
9 minute read
Audits
Every Audit tells a Story
Every audit that is undertaken should be done to provide information about performance. If it is not going to tell us anything, we should question why it is even being done. Whether an audit identifies numerous non-conformances, or ideally none at all, it should still tell us the things we need to know.
The most common approach to health and safety management is the ‘Plan, Do, Check, Act’ approach. This is favoured by the Health and Safety Executive (see publication HSG65, Managing for Health and Safety), and forms a core principle of the ISO standards 9001 (quality management systems) and 45001 (occupational health and safety management systems). This approach also forms the basis of licence renewal assessment by the Asbestos Licensing Unit.
A site audit should evaluate how thoroughly a job has been planned (‘Plan’), that the control measures detailed in the plan have been implemented on site (‘Do’), and the inspections, measurements and other checks made to demonstrate the effectiveness of those control measures throughout the job (‘Check’). The ‘Check’ stage includes the frequent inspections and measurements made by the site supervisor, air testing by the appointed analyst, and site audits whether conducted ‘in-house’ (an internal audit) or externally by an independent organisation such as ARCA.
The value of the information obtained from audits is dependent on a number of factors, including: w the relevance of the ‘question set’ w the competence of the auditor w the reliability of the information generated w the consistency of approach w the extent to which the findings are acted on
The Relevance of the ‘Question Set’ The Plan of Work should be a practical and useful document, compiled prior to the 14-day notification period for the work, describing a safe working method for staff to follow. It should include details of the work, and the appropriate actions to control risk and prevent
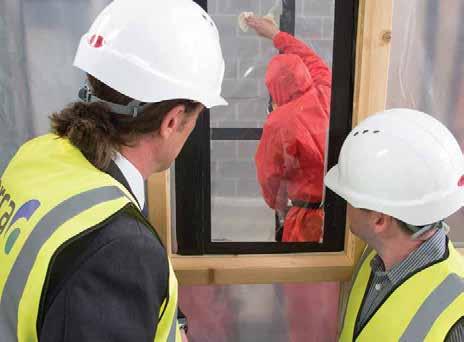
harm. The audit should thoroughly assess the Plan of Work’s fitness for purpose, as the Plan of Work is a tool to measure how effective a business is in managing their work with asbestos.
The audit of the Plan of Work element should assess its completeness in addressing the key requirements, that the chosen methods and control measures are suitable for the asbestos containing material being worked on, and are in sufficient detail relating to the complexity of the job and the risks present and likely to be encountered. It should present clear, precise and unambiguous instruction to the site team, and the audit ‘questions’ should be of sufficient relevance to explore these key requirements. An example ‘question’ would be one to establish that “the selection of negative pressure unit in use is correct and fully demonstrated within the Plan of Work”.
Likewise, the audit should explore the extent of compliance by the site team in following the details contained in the Plan of Work, which by default should demonstrate full legal compliance. Following a suitable and sufficient Plan of Work is one of the standing licence conditions for the licensed asbestos removal contractor, and so the audit needs to be thorough in establishing compliance or otherwise. An example question could be one that records whether “waste is properly and promptly bagged”.
Similarly, the audit should establish that the required checks have been made and recorded (most of these will be by the site supervisor), and to establish, by a representative number of auditor checks, that the records are complete, reliable and accurate.
Hopefully, an audit will tell us the story we would want to hear, being an accurate and in-depth representation of what was found on site. Occasionally it may tell us a story that we don’t particularly want to hear, but nevertheless we need to hear so that required actions can be taken.
Asking the right questions goes a long way towards establishing the true story that unfolds on site.
The Competence of the Auditor
There is currently no qualification available relating to demonstrating competence as a site auditor for asbestos work. Therefore, any asbestos related qualification will at least help to demonstrate familiarity with the industry, though relevant experience is that major factor in demonstrating competence. An auditing qualification, such as one relating to ISO9001:2015 or ISO45001:2018 would also be beneficial.
The fact that licensed contractors need to prepare site specific Plans of Work, rather than just generic method statements, confirms how individual each job is likely to be. The auditor will need sufficient experience to be able to audit the full range of jobs that could be encountered, all of the different scenarios that could be presented, and be aware of any situation where better planning would have resulted in a better selection of site arrangements and procedures. Ideally, there should also be a comprehensive standardisation process in place for organisations conducting audits to ensure consistency of auditors in approach, in drawing conclusions and in recommending actions, such as ARCA has implemented within the audit programmes provided for ARCA members.
A competent auditor, with the relevant support from a reputable organisation, will go a long way towards ensuring the audit story told is accurate and conducive to raising and maintaining the high standards expected of the permissioning regime of licensed asbestos removal.
The Reliability of the
Information Generated
The relevance of the question set and the competence of the auditor are major factors in giving an accurate account of the performance of the licensed contractor, both in planning and executing the plan. The competence of the auditor, and the support system of their organisation, are also a major factor in ensuring reliability of the information generated, and thus the reliability of what the audit findings are telling us.
For instance, the ARCA audits are graded against a standardised marking scheme which has been developed and regularly reviewed over many years by asbestos industry influencers and leaders, including licence holders, analytical companies and enforcing authority inspectors. The audit scheme is also embedded into ARCA’s ISO9001:2015 quality management system certification, which is audited annually by a UKAS accredited certification body.
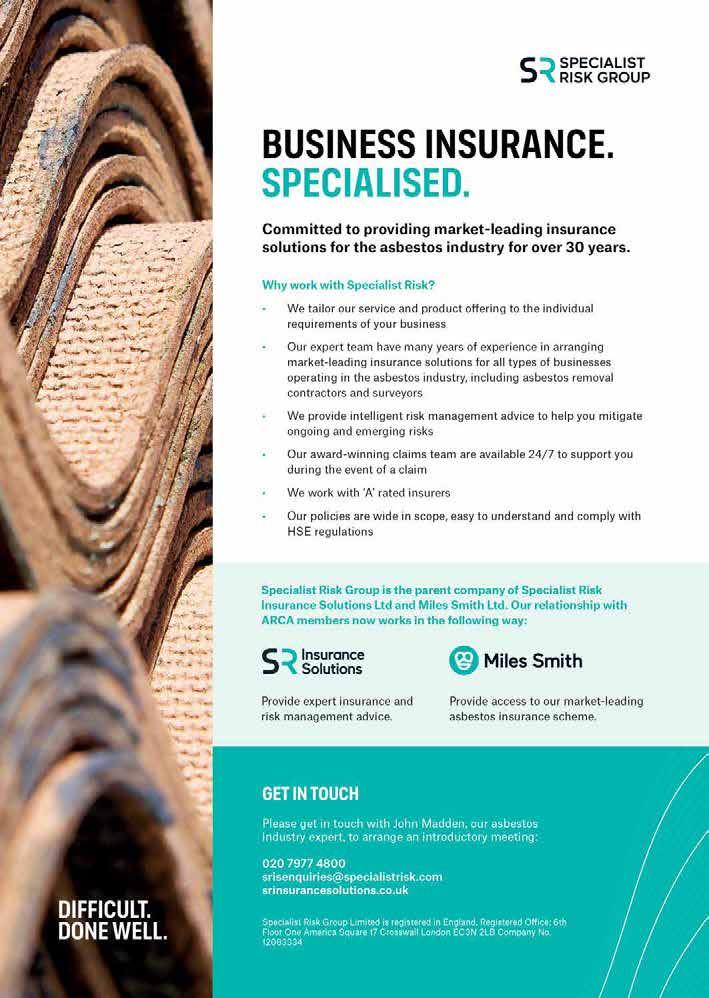
The Consistency of Approach
In addition to the consistency required of the auditor, the auditee can also contribute to the consistency of their broader audit programme. If every audit tells a story, then a set of audits in combination may speak volumes.
Should the three audits per year required for ARCA membership not happen to cover some activity types that you undertake, or not cover all of your site teams, you can arrange additional audits to cover these. Additional ARCA audits are conducted to the same exacting requirements of those under the Site Audit Accreditation Scheme.
For your licence renewal, the Health and Safety Executive will want to know: w your audit strategy w how often audits (internal or external/independent) are carried out w How you ensure that audits are as effective as possible, e.g. whether they are announced or unannounced, and that they are asking the right questions w how you audit your own work internally.
Your own quality system should ensure consistency in your planning, which should extend to site implementation of the subsequent Plan of Work and associated Standard Procedures. Your management system should also provide consistency in the way audit findings are addressed and closed out, looking at both immediate and root causes to prevent future recurrence.
The Extent to which the Findings are Acted On
During the licence renewal process, you will be required to describe to the assessing inspector how you review your performance and develop action plans. The inspector will want to see that all the findings have been actioned, and the extent to which this has been done. In other words, the inspector will be scrutinising numerous audit findings, together with findings from their own inspections, and formulating their own story of how effective your business is in managing work with asbestos. Difficulties arise when discrepancies are found when comparing their interpretation with yours. It is crucial that your audit reviews are as in-depth and thorough as would be undertaken by an assessing inspector.
Even the best companies use audits to tell their story, sometimes albeit a short story, but nevertheless a valuable one based on accurate and credible observations and findings. It is inevitable that, from time to time, the story may introduce an unexpected twist that needs to be unravelled, so robust auditing will tell us by providing early signs that some further actions are required.
This is the essence of the ‘Plan, Do, Check, Act’ approach – that it doesn’t end after the ‘Act’ stage, but that the story continues into the planning of the next job, thus being a platform for continuous improvement.
Every audit tells us a story if we are willing to listen.
ARCA has always taken the view that each audit should produce a report that clearly and accurately conveys how a job has been planned, that plan implemented, records kept to show control measures maintained, and that any further actions required are introduced. This approach leads to improvements being made during the works whenever required, and subsequently for future similar works.
ARCA’s Membership Compliance Manager, Geoff Silver, has commented that “an audit should inform any stakeholder exactly what the state of the job was at the time of the audit, whether exemplary, deficient or anywhere in between. It should leave the reader in no doubt as to what has been done well, and where improvement needs to be made if an element of the audit did not meet the expected standard.”
One ARCA member recently took an in depth look at some of their recent audit findings. As a result, they identified some procedural changes that needed improvement, and some training needs. These were all actioned, and several additional audits arranged to measure how effective these changes had been embraced at site level. In response to an excellent audit result, one of the directors provided feedback that they were very pleased with both the findings and auditor’s comments, and that the audit grade demonstrated how the recent changes they made had a positive impact, and had been well received by the supervisors.
The management team of another ARCA member company courageously identified where they themselves had fallen short in supporting one of their supervisors, following some findings identified in a site audit. Instead of blaming the supervisor, their introspective stance identified some root causes beneath the site findings and put these right. As a result, the supervisor was better equipped to run sites, and a subsequent audit clearly demonstrated how the company’s actions had enhanced site performance.
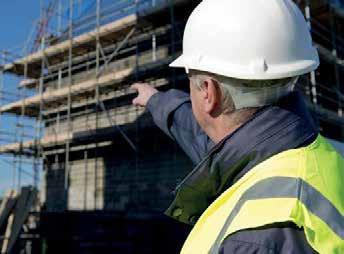
For more information about how ARCA can provide for all your auditing requirements, including how to get the most from your audit findings, contact the ARCA Membership Department on 01283 505776 or email audit@arca.org.uk