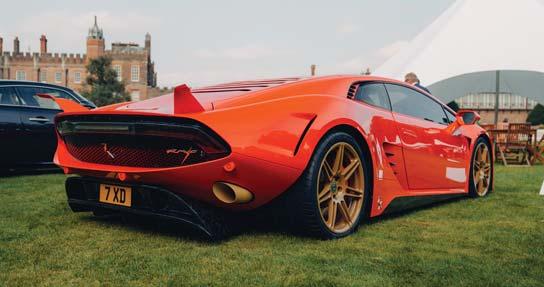
11 minute read
COMPOSITES
Making a Lamborghini faster
Envisage group has helped 7X design create a 270mph carbon fibre-bodied hypercar, the Rayo, takes as its starting point a Lamborghini Huracan.
The finished car took to the track for the first time at this year’s Supercar Fest: The Runway on 29 May.
Translating as ‘lightning’ in Spanish, Rayo is the latest project from bespoke vehicle creator 7X Design. The super-enhanced 1900bhp Lamborghini Huracan LP 610-4 took to the 1km runway reaching 190 mph as the coachbuilt carbon fibre body, engineered by Envisage Group, stood out as an exemplar of hypercar engineering.
Now in its third year, Supercar Fest is the fastest growing supercar event in the UK. Much of the focus was on the everpopular First Point Hypercar Zone where the Rayo went headto-head with more than 50 unique vehicles, impressing the audience with its combination of speed and striking aesthetic.
Rayo’s twin-turbocharged V10 engine produces an incredible 1900bhp – compared to the standard car’s 610bhp. Yet the true differential is the aerodynamic body with a drag coefficient Cd of just 0.279 – a significant 28.5% better than the original. Envisage’s coachbuilding expertise has supported the extensive improvements to performance.
Envisage is known within the automotive sector for supporting vehicle development for everyone from start-ups to OEMs. 7X Design is a specialized automotive designer and project manager that creates one-off vehicles of the highest standard. The team at Envisage had previously worked with 7X Design on a project in 2019 and was first choice to coachbuild the Rayo.
Envisage collaborated with 7X Design throughout the process, providing engineering on the provided 3D designs after handscanning the base vehicle to produce a full 3D model. The team then set to work engineering each individual panel, manufacturing the carbon fibre components and assembling the vehicle to match the design to sub-millimetre accuracy, and the integrity needed for 270 mph plus speeds. Before the final build, the advanced paint technologies division painted all components in Sport Orange.
Since being established in 2009, Envisage Group grew on the back of its ability to respond to changing customer requirements. With four sites in Coventry, together with offices in India and the US, the group has become a coachbuilder for automotive clients around the world.
Tim Strafford, Envisage Group CEO, said: “Supercar Fest was a fantastic event and highlighted just what we’re capable of. The Rayo is a remarkable vehicle and we’re very proud to have played such a key role in its creation. Our relationship with 7X Design goes from strength to strength and we relish every challenge.”
After reaching a top speed of 278 mph in testing, the next goal is to hit 300 mph. 8 envisagegroupltd.com
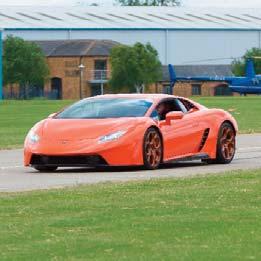
Difficult duplex components
At CIRC Manufacturing in Westbury, Wiltshire, Low Frequency Vibration (LFV) technology on its Citizen sliding head turning centres ensures productivity and quality on difficult materials.
A tubular Duplex stainless steel weld collar for the oil and gas industry is a good example of how the benefits of LFV can be utilised. The high strength material has a tendency to work harden as it is being machined, the impact of which can be reduced by taking deep cuts to remove the work-hardened layer from the previous pass.
The problem is that taking deep cuts in such tough, ductile materials inhibits chip breaking and normally results in a bird's nest of swarf wrapping itself around the component and tool, to the detriment of both and perhaps even rendering them useless. LFV prevents this from happening, so every part produced is perfect and tools last longer. In the case of the weld collar, LFV is switched on for facing the bar and turning a chamfer, then to maintain a high production rate it is switched off for simultaneously boring and turning the OD.
Company owner Tom Pearce explained, "Sliding-head lathes when used with the guide bush in place have an inherent drawback. It is not really feasible to rough and then finish turn a part, as the smaller diameter of the roughed section when drawn back into the guide bush would cause vibration and impair the finishing pass. "It is therefore necessary to turn to size in one operation, but that tends to produce long, stringy swarf when machining certain malleable materials. The LFV software prevents this from happening by lifting the tool tip away from the surface of the material periodically for a few microseconds. "The frequency of the oscillation can be adjusted in the part program to control the size of the much shorter chips, added to which the LFV function can be turned off by G-code when it is more expedient, i.e. slightly quicker, to cut without it. "Overall, productivity is increased by enabling reliable unattended operation, eliminating the need to include axis shuffles in programs to shake swarf off components, especially from grooves, and avoiding the need to stop the machine to clear swarf."
Mr Pearce is enthused that the chip breaking software also reduces problems and raises productivity when machining other materials such as pure copper, exotic alloys, other stainless steels and most plastics, especially nylons.
Commenting on his Citizen Cincom machines, Mr Pearce concluded, "The three Cincoms are the bedrock of our subcontract machining service. All feature main and sub spindles, full length bar feeds and a multitude of tools for driven cross working, end face milling and off-centre drilling. "They enable us to offer economical done-in-one manufacture, without the need for secondary operations. This in turn allows us to run our machines unmanned, so we can offer competitive prices and hence fantastic value to our clients. 8 circmfg.co.uk/
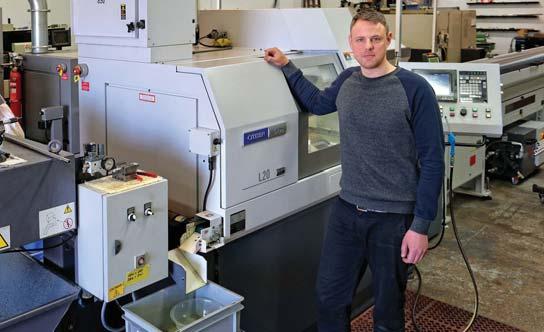
A new moulding machine at Advanced Plastics has doubled output on a key range of products.
The FANUC ROBOSHOT S450iA injection moulding machine, the first in the UK, was installed in combination with an integrated FANCU robot. The success of the installation led Advanced Plastics, a supplier of precision-engineered parts to OEMs in the automotive, medical, packaging, defence and consumer goods industries, to invest in a second machine/robot combination cell.
Rob Anderson, Managing Director of Advanced Plastics, said: “The combination of the FANUC robot and moulding machine allows us to seamlessly integrate our processes. This has resulted in a dramatic increase in our output from around 600,000 parts on a particular range up to a planned 1.3 million.”
Based in Hull, Advanced Plastics undertakes everything from initial design concepts to volume production of plastic mouldings and assemblies, structural plastic components and technical automotive components. The company has almost 10 years’ experience of using FANUC equipment, as Rob explains: “Our injection moulding machines produce high-level engineering parts in various grades of plastic. Since we purchased the first FANUC robot back in 2012, we now have nine ROBOSHOT machines and over 40 FANUC robots. We are proud to be the first company in the UK to purchase the FANUC ROBOSHOT S450iA. We purchased this machine on the back of our experience with FANUC, as we needed a bigger machine that gives us the sensitivity to protect very delicate tooling. This machine perfectly fits the bill.”
The ROBOSHOT S450iA injecting moulding machine operates with a clamp force of 4,500kN, a double platen die height of between 350mm and 1m, and a clamping stroke of 900mm. Weighing 29.7 tonnes, it boasts a rated maximum injection speed of 180mm/s.
FANUC’s M-20iD35 robot offers fast and efficient movement in all six axes with a maximum load capacity of 35kg, which is more than sufficient for lightweight plastic injection moulded components.
The system at Advanced Plastics has a range of intelligent, digital features. In this instance, one of the key smart benefits is the FANUC AI-Protect system for both mould and ejector. This provides unparalleled mould protection, which in turn neutralises an important potential cause of downtime.
“AI-Protect allows the moulds to open and close at fast speeds with full protection of the tooling. The tooling can often be just as expensive as the moulding machines so we must protect it,” said Ed Darling, Advanced Plastics’ Process Manager.
To highlight the effectiveness of this feature, Ed outlines an incident when an apple was dropped between two surfaces of the mould: “Because of the accuracy of the AI-Protect, the apple wasn’t crushed. That shows the precision that we need on these moulding machines.”
Other automated features include Clamp Force Adjustment, which checks and adjusts the minimum clamp force to provide increased security, eliminating the need to manually modify this
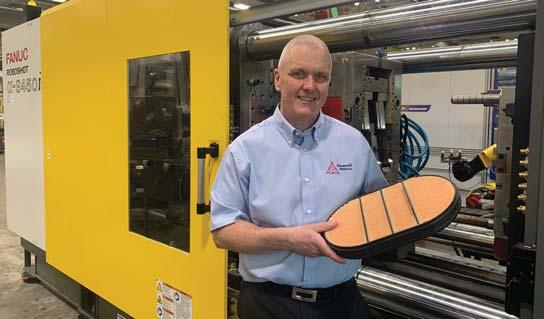
Moulding output doubled
critical parameter. Optimising clamp force also minimises mould wear and increases machine life, cuts component defects, reduces energy consumption and compresses start-up times.
As a result of the close integration of machine, robot and software, exceptionally fast cycle times can be achieved.
Ed Darling explained that this is a key benefit to Advanced Plastics: “I particularly like FANUC moulding machines because, being all-electric, they are economical to run; but mostly, I like them because we are a cycle time-oriented business.”
For Rob Anderson, meanwhile, the success of the first system quickly led to the company placing an order for a second: “We went for the second machine due to the easy installation of the first. The short lead times offered by FANUC meant we could get products to market extremely quickly. At Advanced Plastics, we like to experience new technologies and look at innovative technologies where we can achieve better results for our customers. In essence, the FANUC ROBOSHOT S450iA was the only machine that could do the particular job that we needed it to do – and it does it very well.” 8 advanced-plastics.co.uk
DIRECTORY | Engineering Capacity
8
BROACHING JFL Broaches and Broaching
JFL are broach and broaching specialists with many years personal experience. We offer a comprehensive broaching service covering keyways, squares, hexagons and special forms.
Unit 2, Deethe Farm Industrial Est, Cranfield Rd, Woburn Sands, Milton Keynes, Bucks MK17 8UR Tel: 01908 585103 www.jflbroaches.co.uk
8
Qualiturn are a very modern subcontract machining service. We offer CNC precision Turned and Milled components to your specifications and quantities. We work with all sizes of customers, offering the same service to all. Supplying various market sectors across the world.
7 Fountain Drive, Hertford, Herts, UK, SG13 7UB Tel. +44 (0) 1992 584499 www.qualiturn.co.uk
8
MACHINE TOOL MANUALS
LATHES.CO.UK
Lathes.co.uk
store.lathes.co.uk - where Manuals, Catalogues Drive Belts Books Accessories & Spares are listed The world’s largest machine tool reference archive. Manuals, Catalogues, Books, Pictures Specifications, Technical Guides Wardlow, Tideswell, Buxton, Derbyshire, SK17 8RP Tel. 01298-871633 (from overseas: +44-1298-871633) from 09:00 to 23:00 UK time www.lathes.co.uk
8
CNC PRECISION COMPONENTS G W Martin and Co Ltd
GW Martin are a supplier of precision machined CNC components and assemblies. Recent investments in the latest automated technologies reinforce our strong reputation for high quality parts and service excellence. Contact us for your complete service engineering requirements. 7 Bishopstoke Road, Eastleigh, Hampshire, England, SO50 6AD Tel: 023 8064 2922 Email: sales@gwmartin.co.uk www.gwmartin.co.uk
Get your company noticed with an Engineering Capacity classified profile advert
Call 01737 270648

DAWSON PRECISION COMPONENTS Manufacturing precision machined components since 1965 Services include: CNC milling, CNC turning, turn/mill machining, sub contracted services, finishing and project management.
Greenfield Lane, Shaw, Oldham, Lancashire, OL2 8QP Tel: 01706 842311 8
SUBCONTRACT CNC TURNING
dpc.co.uk
Subcontract mill turned parts up to 65mm in parts up to 65mm in diameter from bar diameter from bar and 300mm and 300mm billet work. work.
– r – – s yol l A repuS ssaB
leetSssel ni a t S nimuAl mui scitsalP
8
PRECISION ENGINEERING
5 High quality precision machined components 5 Trusted technical support service 5 Complete and bespoke service from conception to completion 5 AS9100D & ISO 9001:2015 approved
Oldfield Street, Crosland Moor Huddersfield HD4 5AJ T: 01484 548903 www.thomas-brown-engineering.co.uk
8
PRECISION ENGINEERING Wealdpark Ltd
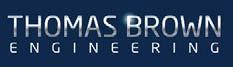
CNC mill-turn facility using Star sliding head lathes with bar capacity up to 32mm diameter. Miyano and Doosan fixed head lathes with bar capacity up to 65mm. Hurco vertical machining centre.
Sutton Road, St. Helens Merseyside WA9 3DJ Tel: 01744 22567 www.wealdpark.co.uk
8
REPETITION TURNED PARTS
8
SPRING MAKING Kirkham Engineering Co Ltd

13 - CNC Sliding Heads up to 1”; 14 CNC Twin Turret Fixed Heads up to 65mm; 5 - Twin Turret Twin Spindle; 5 - Twin Turret with Sub-Spindle and 4 - Twin Turret; 4 - CNC Single Turret Fixed Heads up to 6” Billet. Centreless Grinding & T/rolling. All materials - Stainless Steel; Nickel Alloys and other exotics a speciality. Prestwood Place, East Pimbo, Skelmersdale, Lancashire WN8 9QE Tel: 01695 727401 www.kirkhamengineering.co.uk
Simpson Springs & Pressings Ltd
Precision manufacturers of a wide range of compression tension and torsion springs. Also circlips, wireforms, contacts, antennas and light pressings. Quality approved to BS EN ISO 9001:2000. Unit 1, Latimer Road Industrial Est, Latimer Road, Wokingham, Berkshire RG41 2YD Tel: 0118 978 6573 www.simpsonsprings.co.uk
8
TURNED PARTS Precision Products (Brighton) Ltd
A one-stop-shop for high-quality turned parts
Accredited to AS9100 Rev D