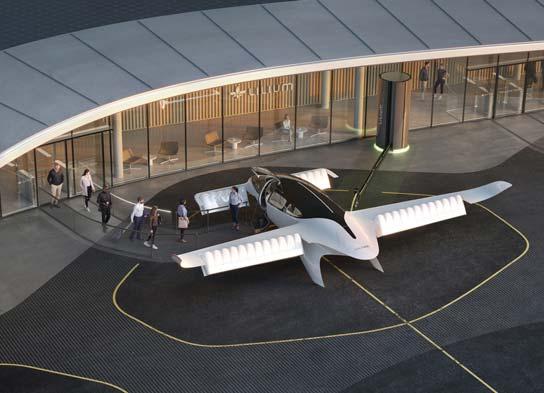
15 minute read
AEROSPACE & DEFENCE
Electric VTOL jet maker Lilium has partnered with Honeywell and DENSO to co-develop and manufacture the electric motor that will power its engines.
Honeywell is already developing the Lilium Jet’s avionics and flight control systems and invested in Lilium in 2021. A leader in aerospace technologies with over 100 years of experience, Honeywell also has an alliance with automotive giant DENSO to develop aerospace electric propulsion solutions. Through this collaboration, the Lilium Jet’s emotor will benefit from Honeywell’s aerospace expertise as well as DENSO’s experience in high-quality volume production.
The Lilium e-motor is a proprietary, high-performance system, on which Lilium, DENSO and Honeywell teams have been working for nearly two years. It is expected to bring exceptional performance and reliability with zero operating emissions typically associated with commercial jet engines. An air-cooled design offers structural simplicity and ease of maintenance compared with traditional liquid cooling systems, and therefore has the potential to significantly reduce aircraft operating costs.
The e-motor has its rotor and stator in a centrifugal or ‘radial’ configuration, compared to traditional axial designs. This lowers the component’s weight, manufacturing costs and susceptibility to foreign object damage. It also boasts industryleading power density, with the first prototypes designed to extract over 100kW of power from a system weighing just over 4kg.
Yves Yemsi, Chief Operating Officer of Lilium said: “Lilium’s Procurement strategy is to engage with the technology providers with the most suitable expertise. We are already making great progress with Honeywell on its Honeywell Anthem integrated flight deck and flight control computers, and we are delighted to deepen our relationship by also partnering with Honeywell and DENSO on our e-motor. The collaboration with these two powerhouses takes us further along the path to revolutionizing regional air mobility.”
Stéphane Fymat, vice president and general manager of Urban Air Mobility, Honeywell Aerospace said: “Honeywell has been at the forefront of innovation in aviation for a century, and we are proud to closely collaborate with DENSO and help usher in the age of electric flight. Lilium’s innovation, combined with our experience in aerospace, will help to bring about cleaner, more sustainable ways for people to travel for centuries to come.”
Koji Ishizuka, senior director of the Electric Sora-Mobi Business Promotion Department at DENSO, said: “DENSO’s focus is powering the shift to a green, safe and seamless mobility future for all. We’re grateful to work with Honeywell and Lilium on making air travel cleaner and more efficient, and in doing so, we have the opportunity to apply our electrification expertise to vehicles on land and in the sky.” 8 lilium.com
Electric jet partners
Strategic data partnership
The trade body representing the UK’s aerospace, defence, security and space sectors, ADS, has appointed management consultancy, Vendigital, as its strategic data partner.
As part of the collaboration, Vendigital will be working with ADS to extend support to its more than 1,100 members; providing access to reliable industry and market data, combined with robust analysis and supply chain intelligence.
In particular, Vendigital is supporting a number of ADS’s aerospace manufacturing members in responding to the industry ramp up with databased insights to assist them in areas such as capacity planning, supply chain management and labour strategies.
For ADS, the decision to appoint Vendigital as its strategic data partner has come at an important moment for its members who work across the aerospace, defence, security and space sectors.
Kevin Craven, CEO, ADS, explained: “The current operating environment is very challenging, and it is important that businesses harness the power of data and understand the strategic benefits it can bring in supporting organisation reach and develop their business objectives.
“Vendigital’s experience in the delivery of data-based insights to support businesses and industries through time of change can provide valuable support to ADS members.”
Roy Williams, CEO at Vendigital, added: “Using accurate data to guide decision making is critical and could help businesses to direct their own digital and cost transformations, while greening operations and thriving as a result.” 8 Adsgroup.org.uk
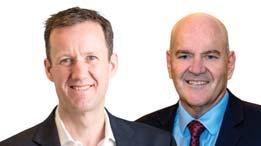
8 Roy Williams of Vendigital and
Kevin Craven of ADS
THE SPECIALIST SUPPLIER OF METALS & PLASTICS TO THE AEROSPACE INDUSTRY
For commercial and aerospace alloy applications, Righton Blackburns has been a trusted supply partner for over a century. Our experience and expertise extends across a wide range of materials, including:
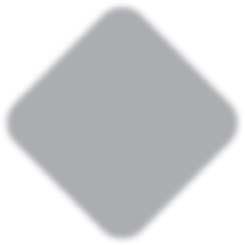
Copper Alloys Aluminium Alloys Stainless & Alloy Steels Bearing Steel Titanium Nickel Alloys Special Alloys Hardiall® (AMS4596, AMS4597, AMS4598) Powder Metals Cronidur® 30 Engineering Plastics
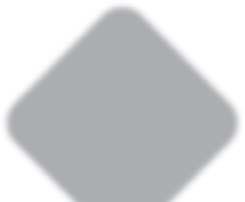
To find your nearest Service Centre visit www.rightonblackburns.co.uk

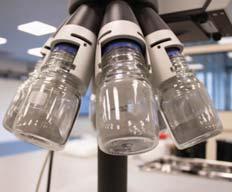

Kilkeel, Northern Ireland aircraft seating manufacturer, Collins Aerospace has been recognised in three separate industry awards for its innovative products, processes and excellence.
The company was awarded the Automotive, Aerospace and Rail award at the recent Insider Media Made in Northern Ireland Awards, where it was shortlisted in four categories. The judges noted Collins’ commitment to using the local Northern Ireland supply chain as being an important part of its success.
The Made in Northern Ireland Awards, which were held at Titanic Hotel in Belfast, showcased the high quality and excellence of the region’s manufacturing and engineering businesses, and recognised the resilience of the companies operating within the sectors.
The company has also been announced as a finalist in the respected Crystal Cabin Awards for 2022, which recognise and award excellence in aircraft interior innovation. It has been shortlisted in the ‘New Cabin Concepts’ category for the innovation shown in the design and manufacture of the Finnair AirLounge seat, which was one of this year’s most widely discussed entries.
Manufactured by the team in Kilkeel, the AirLounge business class seat was created in cooperation with Finnair, PriestmanGoode and Tangerine. It has been described as “more like a piece of classic Nordic furniture than a simple airline seat” for its features, which include a contoured shell design that provides passengers with more living space and freedom to relax, as well as offering added privacy.
Collins Aerospace in Kilkeel, part of Raytheon Technologies (RTX), which has over 300 sites globally, was also recently announced as the winner of the RTX/Collins Environmental Health and Safety (EH&S) Award for Large Site Excellence.
The award recognised the Kilkeel facility for demonstrating excellence in EH&S management over the preceding two-year period through significant performance improvement or long-term sustained performance excellence. 8 collinsaerospace.com
Jaltek has increased its manufacturing space by 50% and is recruiting in production, engineering and account management, to meet increased demand for electronic assembly.
The additional facility is next to the original factory near Luton, and will be ready to start production of electronic
Triple award for Collins
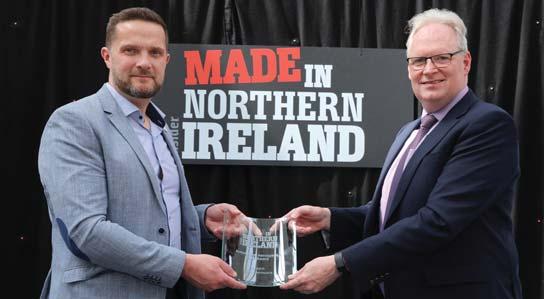
Meeting electronics demand
system assembly and test in the coming months.
Jaltek’s Steve Blythe said, “We continue to see sustained growth in a number of sectors including in Aerospace, Medical and EV related products. More clients require full system assembly and test which has led to some great opportunities.”
Steve Pittom, Managing Director added, “Essentially this investment enables us to continue delivering our vision towards world class competitiveness and productivity for our customers.” 8 jaltek.com
EDM outsourcing partnership
Strategic manufacturing outsourcing specialist PP Control & Automation has signed a new deal to support the development of what is said to be the world’s most productive EDM drilling machine.
The West Midlands-based company will assemble the EDM generator module that is at the heart of Winbro Group Technologies’ new HSD-351 model.
A new production cell has been set-up to complete the build, with work on the first 25 units set to begin shortly. These machines will be used for drilling holes in complex aero and industrial gas turbine blades and nozzle guide vanes.
The relationship has spanned a decade and ten different model variants, with the decision to outsource continuing to provide production ‘flex’, reduced assembly time and improved supply chain management for Winbro.
Tony Hague, CEO of PP C&A, commented: “If you are going to write a book about strategic manufacturing outsourcing and how it can work, I’d like to think this relationship would be in the case study section.
“To work with a company that operates in such a demanding field for ten years is some achievement and we are delighted to be entering our ‘testimonial year’ with a new machine tool to help them build.”
He continued: “The HSD-351 is an EDM machine that packs so much power in so little space and we have been instrumental in helping produce the heartbeat of the model – the EDM generator module.”
Manufacturers are increasingly looking to deliver more productivity per square metre of shopfloor space, and this drove Winbro Group Technologies’ decision to develop and launch the HSD-351 system.
With a footprint of just 2.5m2 , Winbro says it is the world’s most productive EDM drilling machine and boasts a capacity of almost 700 electrodes, across a range of diameters giving unprecedented lights-out machining capability.
Gary Robinson, Vice President of Sourcing at Winbro, said: “The HSD-351 is proving that a small footprint can also be powerful, delivering more performance than our previous best-in-class model.
“At the heart of this capability is the EDM Generator module, which is assembled and built at PP Control & Automation to ensure we get the same repeatable quality in every unit.
“This machine really illustrates the strength of our relationship… it’s business critical. Together, we sat down and looked at the design for manufacture for the generator and, using the expertise of both firms, we were able to come up with an assembly process that is faster and more efficient.”
He continued: “It also has the benefit of being fully UL 508A approved for the American market, something we now take for granted after working with PP Control & Automation for so long.”
Engineers at PP C&A’s world class manufacturing and assembly plant are just getting started on the first of 25 units over the course of the next twelve months, with design for manufacturing contributing to an assembly time reduction. 8 ppcanda.com
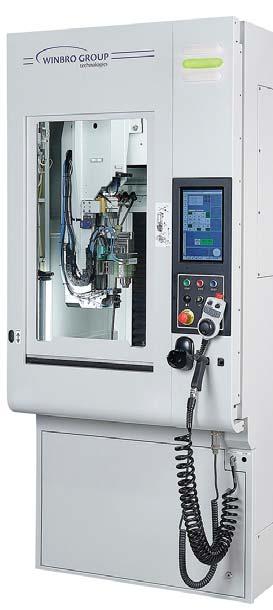
Lesjöfors has developed a new wire form for fishing lure manufacturer Salta Lure.
The component is for a newly developed trolling product line, MagPower, that includes a quick release system that allows lures to be changed over very quickly. The new part is a stainless steel component for the lure’s locking system.
From the very beginning, the customer had a clear picture of what the component would look like and what specifications it needed to meet. After internal discussions, it was clear that the Lesjöfors company in Nordmarkshyttan was best equipped to help out with designing and producing the wire form.
To begin with, the customer's representative Georgios Toris received samples of how the wire form could be designed. When he was content with the dimension, the technicians at Lesjöfors continued with the requirements for strength, the component needed to withstand a weight of remarkable 136 kilos. Lesjöfors' technical expert Mattias Hartvigsson performed a FE analysis on the ring diameter in question and it turned out to work excellently.
The choice of wire material was the stainless steel Duplex EN10270-3-1.4462 as it is hard and can withstand a lot of load. "Unfortunately, the wire form will probably never break so the only way we will have the opportunity to sell more is if the fishermen drop the fishing box in the lake," says Christian Larsson,
New customer hooked
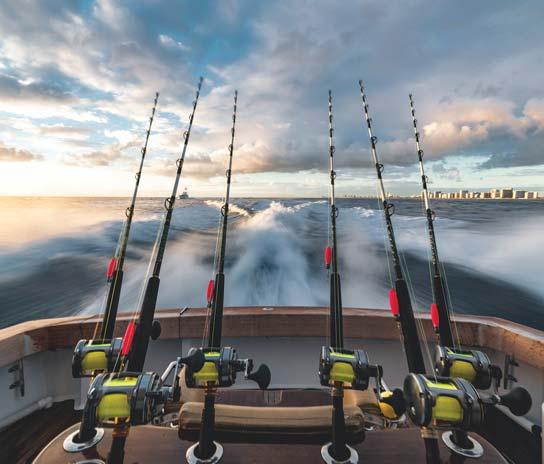
technical sales at Lesjöfors Industrifjädrar in Nordmarkshyttan. 8 lesjoforsab.com

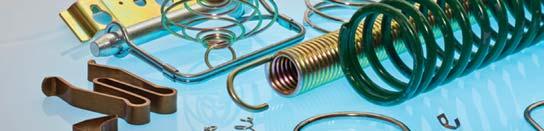
From design, sampling and technical support to manufacture, Simpson Springs & Pressings Ltd provide the complete service.
Tel: 0118 978 6573 Email: sales@simpsonsprings.co.uk
Electron beam welding breakthrough
Sheffield Forgemasters says it has achieved a breakthrough in the industrialisation of Electron Beam Welding (EBW) for thick-section materials.
Using EBW, the company weldjoined two 200 mm thick, threemeter diameter vessel sections in UK-SMR nuclear grade steel. The weld, equivalent to approximately 10m of length, was completed in a single pass and in a dramatically short timeframe.
Completed in 140 minutes, with no reportable defects shown in preliminary non-destructive testing (NDT), a weld of this kind would typically take months and include numerous stages of NDT as well as heat-treatment.
Research, Design and Technology Director, Professor Jesus Talamantes-Silva, said: “This is the most critical milestone in our project to industrialise EBW and to eliminate the requirement for large vacuum chambers typically used in this technology, we have pioneered the use of local vacuum EBW alongside our project partners, Cambridge Vacuum Engineering (CVE).”
“This follows a body of work started in 2015 with support from Innovate UK to establish the basic science for local vacuum EBW, which was successful, producing welds with very favourable mechanical properties.”
The company initiated a subsequent 2019 project: ‘Industrialisation of large-scale electron beam welding for nuclear industry applications’ to further prove the technology, supported by the Department for Business, Energy & Industrial Strategy (BEIS) as part of its £505m Energy Innovation Portfolio.
Sheffield Forgemasters’ aim is to incorporate advanced fabrication techniques, offering significant savings on both processing time and cost through the potential of electron beam welding over the more traditional method of Tungsten Inert Gas welding for thick-section pressure vessels.
The EBW process uses local vacuum and a high power electron gun which penetrates the vessel material with an electron beam, to melt and fuse the two components together in one pass, rather than building up of multiple layers of weld filler wire.
Senior Development Engineer & Project Lead, Dr Michael Blackmore, added: “We completed the weld and carried out the factory acceptance testing of the machine tool, a process that verifies that the equipment is built and operating in accordance with design specifications at CVE's site in Cambridge.
The project, led by Sheffield Forgemasters, underpins the company’s ambitious commitment to the UK’s civil nuclear ambitions as demonstrated through its supply of complex, nuclear-grade demonstrator forgings to the Rolls-Royce SMR programme.
To ensure successful dissemination and awareness of the EBW technology, an industry steering committee including the Ministry of Defence, Rolls-Royce submarines and SMR divisions, The UK Atomic Energy Authority and Cavendish Nuclear, was formed. Engagement with the Office for Nuclear Regulation and Environment Agency was also instigated by BEIS as the project progressed.
Michael concluded: “We are due to start building an X-Ray enclosure to house the EBW equipment, and it will be ready
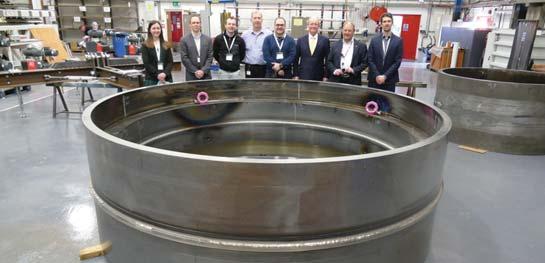
during Q2 2022. We are also planning to fully demonstrate the welding capabilities by fabricating a full-scale nuclear pressure vessel which will consist of five main components, four shells and a nuclear head, to ensure a reliable and repetitive process.”
The project benefits from partner contributions and support from CVE, Arc Energy Resources, The Welding Institute, the Nuclear Advanced Manufacturing Research Centre at the University of Sheffield, and the Universities of Cambridge and Manchester.
Managing Director of CVE, Bob Nicolson, said; “We have been proud to host the ONR, EA and BEIS representatives during visits to our Cambridge factory to officially present progress and hardware capabilities to be utilised at Sheffield Forgemasters.”
Sheffield Forgemasters actively supports the development of materials and processes for the nuclear sector. Safety-critical components, i.e. castings and forgings, have been produced using conventional methods. More advanced manufacturing techniques such as Hot-Isostatic Pressing and advanced metalforming have also been successfully implemented at its Brightside Lane facilities.
Although the main core activity of the EBW project is welding, other work packages within the project will also advance Sheffield Forgemasters’ technical expertise in areas such as fracture mechanics and cladding.
The project was part funded under the £26m Advanced Manufacturing and Materials Programme within the BEIS Energy Innovation Programme. 8 sheffieldforgemasters.com
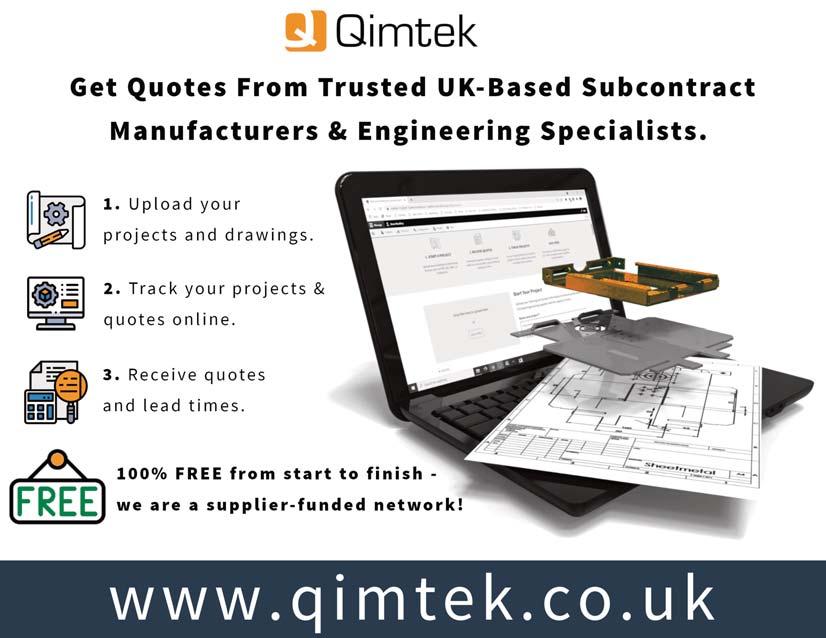
Welded wire success story
William Hughes has become leading supplier of welded wire assemblies, primarily for the automotive industry.
The Company’s expertise in MIG, MAG, TIG, spot/resistance and butt welding processes has led to it establishing a total of 33 welding cells across its three factories in the UK, Poland and Bulgaria.
In the UK, William Hughes Ltd is the only supplier of large volume automotive welded assemblies, a skill it has spent the last twenty years perfecting, still trading.
William Hughes has always been a large volume producer of wires, springs and small welded assemblies for the automotive industry. Twenty years ago, welding was carried out manually or by simple semi-automated machines but Engineering Director Emma Burgon had the foresight to focus on acquiring a contract for 100% rear seat welded assemblies, having correctly recognised a potential gap in the market at the Company’s low cost facility in Bulgaria. The William Hughes engineering department was tasked with understanding the specific tooling required to manufacture this type of product and the investment necessary to bring such tooling manufacture in-house.
After several years of honing their knowledge and developing their expertise, the team in Bulgaria was successful in securing two major contracts. Typically these rear seat welded assemblies have approximately 50-60 welds; however for one of the newly secured projects, each frame had a total of 120 welds! Despite the complexity and difficulty involved, William Hughes rose to the challenge. Using a mixture of in-house design with support from subcontract tool makers, the first William Hughes welding tools were soon being produced. Shortly afterwards, the first-off tool components appeared and were ready to be measured in William Hughes’s high-tech quality department.
After two years of manufacture in Bulgaria, word of the Company’s capability reached the customer base in the UK and it secured its first welded assembly for the home market. By this time, some serious investment in machinery and personnel had led to William Hughes producing its own tooling, allowing more control over design philosophy and greater cost effectiveness.
These early projects have now all gone to end of production but William Hughes growth in this area has meant that they now have a total of 23 MAG robot welding cells and 10 spot robot welding cells over its three manufacturing locations. 8 wmhughes.co.uk
