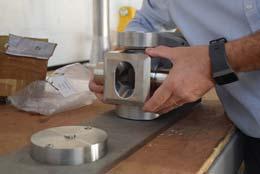
7 minute read
CASTING FORGING
Copper Alloys has developed a lead-free material for use in food and beverage industry. applications such as valve fittings, pumps and gears.
Achieving FDA approved GRAS status, the material is a food-safe alloy with low friction and anti-galling characteristics in contrast to stainless steel.
The alloy’s composition means it offers high corrosion resistance in both acidic and caustic environment and it’s specially developed to prevent galling when in contact with stainless steel, even in high-speed contact applications. What’s more, its alloyed-in lubrication avoids the need for externally supplied lubrication, and it holds uniform properties in all directions.
Ben Turner, Managing Director of Copper Alloys said: “Through the inclusion of a specific mix of minerals and elements we created a fine dispersion of soft globular phases distributed throughout the alloy structure. These phases provide the alloy’s inbuilt lubricity and exceptionally low friction and anti-galling characteristics against austenitic stainless steels.”
To ensure stringent certification and documentations, every piece is hard marked with a cast and bar number so that it can easily be traced back to the relevant material certification.
Each batch is also subject to indepth assessment of chemical composition, liquid penetrant, tensile and hardness properties
All certification is produced in accordance with BS EN 10204 3.1.
Copper Alloys exercises precise control over alloy composition and using advanced process technology techniques, the firm has developed a range of high-performance alloys designed to give engineers greater options for a variety of significant applications in the food and beverage industry.
Traceability from source to customer is guaranteed. 8 copperalloys.net
New alloy for food sector
Leading UK aluminium die casting foundry, MRT Castings Ltd, has been honoured with a Queen’s Award for Enterprise in International Trade, for the second time in six years. Following its previous award in 2016, the Andover based manufacturer has experienced a further period of exceptional growth in export sales.
MRT produces aluminium die castings and machined components for a wide range of UK and international customers. These components are used in applications as diverse as hi-fi equipment to supercars, and designer lighting to military control systems. One of the company’s largest markets is in medical devices, and in particular, critical care ventilators.
When the Covid-19 pandemic struck, hospitals around the world were in desperate need of additional ventilators to treat critically ill patients. Since 2014, MRT has worked with one of the world’s leading manufacturers of these ventilators, supplying 21 components in each unit. Prior to the pandemic, MRT produced approximately 4,000 kits of these
MRT Castings wins Queen’s Award

precision engineered and finished components each year, but between April 2020 and March 2021, MRT dramatically scaled up operations to manufacture over 26,000 sets, enabling its customers to supply life-saving ventilators to every corner of the globe.
This year MRT celebrates its 75th Anniversary. The familyowned business was originally established in London, then relocated to its current production base in Hampshire in 1965. It has steadily expanded the scale and complexity of their production facilities over the years, and just prior to the pandemic, opened a new, purpose-built, state-of-theart diecasting foundry to accommodate future growth.
The company wasn’t expecting to fill it quite so quickly, but with the challenge of rapidly scaling up operations to respond to the Covid-19 crisis, the business invested in additional two diecasting cells and seven additional CNC machining centres over just a few weeks. It added a second shift, and almost doubled the workforce, instantly transforming the new foundry into a hive of productivity and innovation. It is now one of the most technically advanced diecasting facilities in the UK.
The new foundry has been designed with digital

manufacturing at the heart of its operations. As machines from the original facility were transferred into the new building, each was fully refurbished and upgraded to incorporate the latest robotic ancillary equipment, and full networking capabilities for data transfer and real-time monitoring. Indeed the facility itself was designed in partnership with the Manufacturing Technology Centre, utilizing 3D virtual reality representations of the building and the machinery to optimize the efficiency of the layout.
The investment has not been limited to MRT’s foundry operations though. The company’s extensive in-house machine shop now boasts 26 Brother high efficiency CNC machining centres, and three CNC turning centres, including a new Biglia 620YS installed just last month. All of the machines have been selected for their lightning speed, accuracy, flexibility, and one-hit machining capabilities for maximum productivity.
This impressive array of manufacturing technology has attracted an increasingly complex range of new projects from international and UK-based customers. MRT supports those projects with a collaborative design support service. In-house
Solidworks CAD and Magmasoft casting simulation capabilities complement MRT’s 75 years of engineering experience to ensure that component and tooling designs are optimised for the ultimate functionality, repeatability and productivity.
MRT's current export markets now cover Western Europe, Eastern Europe and North America. Overseas sales have grown by 437% over the past three years and the proportion of sales exported has increased to 85% of total sales.
Managing Director, Phil Rawnson, explained “A Queen’s Award for Enterprise is the ultimate accolade for a UK business, and to have won two just six years apart is testament to the relentless energy and enthusiasm of our team. To receive this honour during the company’s 75th anniversary year is particularly special.” 8 mrt-castings.co.uk
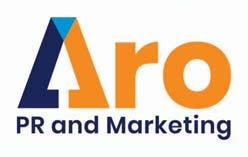
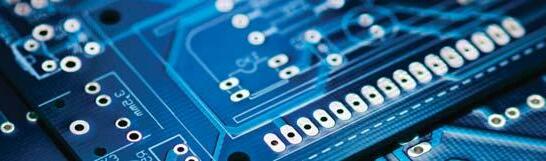

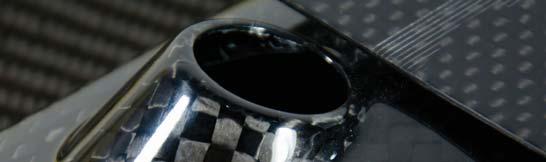
Doncasters, which manufactures high-precision alloy engineering components, has acquired UniPol, a global business specialising in the manufacture of superalloy cast parts.
The company says the acquisition places it amongst the largest manufacturers of highprecision alloy components in the global supply chain, enhancing the future for the group, its employees, and customers.
The precision parts market is expected to reach revenues of $300 billion by 2025, growing at a CAGR of over 10% between 2019 and 2025. Doncasters has seen the industry develop since 1778, when the company’s founder, Daniel Doncaster applied the crucible steel-making process to the manufacture of hand tools. From creating forging tools, Doncasters developed a reputation for quality craftmanship, reliability and metallurgical knowledge.
Since it was established, Doncasters has grown to be a leading international manufacturer of high-precision engineering components. Each of its eleven advanced production facilities across Europe and the US has specialist capabilities and serves a broad blue-chip client base, including Siemens, GE, RollsRoyce, Ansaldo, BorgWarner, Garrett Motion and Cummins.
Established in 2005, Uni-Pol has four manufacturing facilities in China, India, Mexico and the UK. This acquisition means that Doncasters will have an annual revenue of over $500 million and employ nearly 3,000 people across 7 countries.
“Some time ago, we identified Uni-Pol as a natural fit with the Doncasters group of businesses,” explained Mike Quinn, CEO of Doncasters. “The additional support from the group gives Uni-Pol extensive opportunities to further develop its offering and, in turn, Doncasters will benefit from Uni-Pol’s additional expertise and technology. It also broadens Doncasters’ product offering, benefiting existing and new international customers, particularly those in Asia and South America.
“This is an exciting time for the Doncasters group of businesses, as we invest in upgrading our operating equipment, technology platforms and capabilities, so that we can be more efficient, accurate, timely and can compete on a wider scale. We’ll also be strengthening and developing our talent, who will benefit from the opportunities created by this acquisition,” concluded Quinn.
David Orr, Chief Executive Officer of Uni-Pol commented, “This is a fantastic new chapter in our history. This synergy is great for our people and for our customers as we focus on supplying complex, high-quality competitive products for the automotive and aerospace industries on an international scale. I’m looking forward to working together as one team, towards what looks like a bright future for us all.”
Doncasters says that the uniting of these two companies will augment its mission to supply complex, high-quality, competitive products for the aerospace, automotive and industrial gas turbine industries on an international scale. 8 doncasters.com
Cast parts acquisition
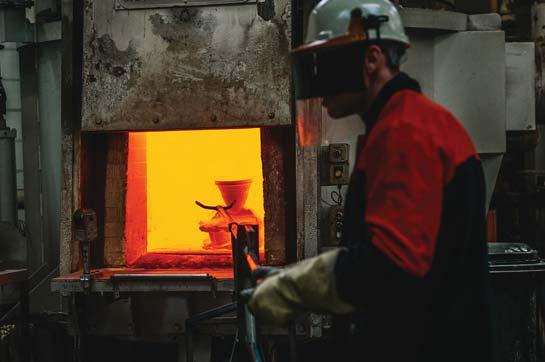