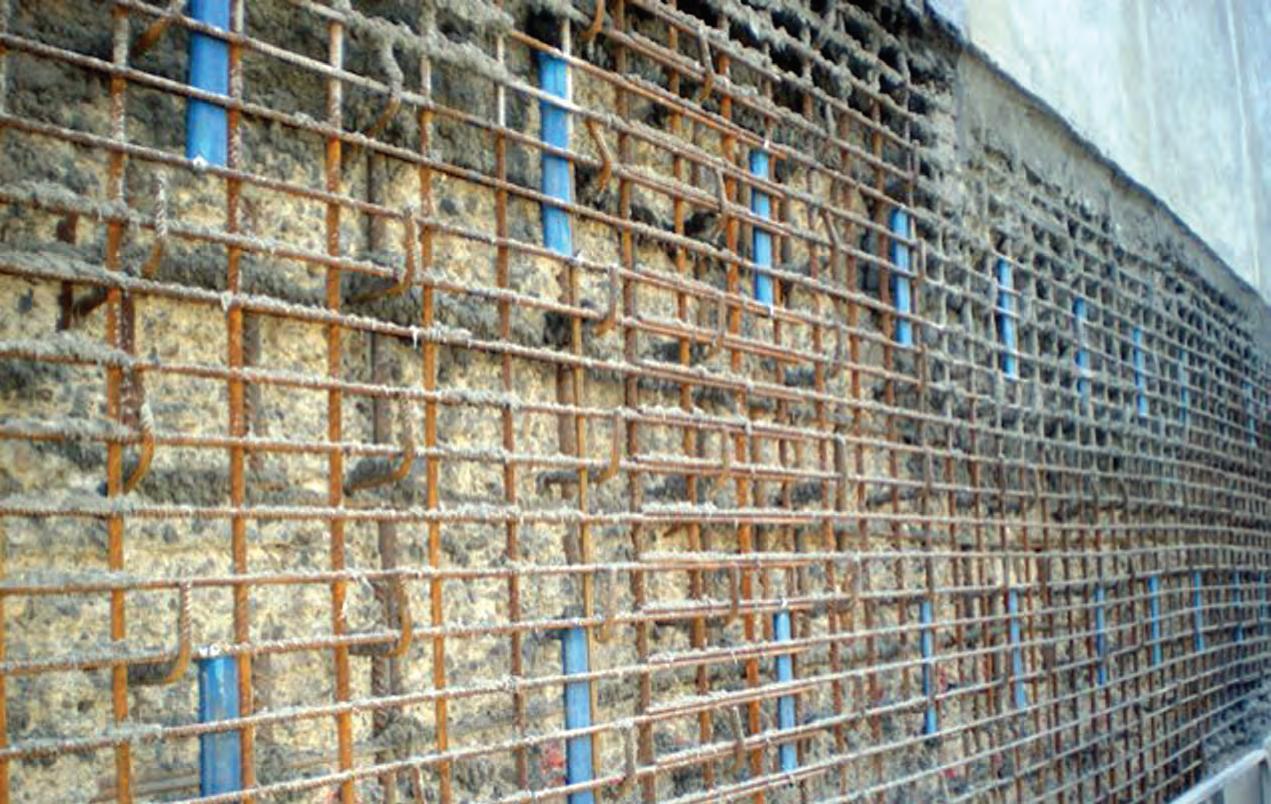
14 minute read
La gestione dell’invecchiamento delle infrastrutture
tecnologie&sistemi
Ugo Dibennardo(1) Paolo Mannella(2)
Advertisement
LA GESTIONE
DELL’INVECCHIAMENTO DELLE INFRASTRUTTURE
La gestione sicura dell’invecchiamento delle infrastrutture ha assunto nel corso degli ultimi anni un ruolo strategico anche a causa dell’“età” costruttiva del parco infrastrutturale attualmente in esercizio. La sensibilizzazione a questo tema condotta nell’ultimo decennio ha stimolato lo sviluppo delle tecniche di misura, della sensoristica e della prognostica che ad oggi offrono grandi possibilità per estendere il tempo di esercizio delle infrastrutture. In questo ambito, una tematica annosa ma sempre attuale è rappresentata della corrosione delle armature nel calcestruzzo. Tale fenomeno si manifesta spesso attraverso attacchi localizzati, detti “pit” o vaiolature, che dalla superficie penetrano attraverso lo spessore del metallo con velocità dipendente del potenziale elettrico dello stesso. Volendo descrivere il processo a livello microscopico, ciò che accade è che la stabilità chimica dell’acciaio al carbonio all’interno dell’elemento strutturale è garantita dall’ambiente fortemente basico determinatosi all’interno del calcestruzzo indurito durante il processo di idratazione del cemento, e ciò grazie alla formazione dell’idrossido di calcio Ca(OH)2 o calce idrata. La presenza dell’idrossido di calcio rende l’ambiente fortemente alcalino (pH 12,5-13,5) e in tali condizioni sulla superficie della barre d’acciaio si forma un film di ossido di ferro insolubile passivante, compatto ed aderente alla superficie del tondino, che protegge il ferro dalla corrosione. La porosità del calcestruzzo e la presenza di eventuali fessure consentono all’aria di penetrare, più o meno lentamente, all’interno della matrice di calcestruzzo indurito. L’anidride carbonica (CO2), presente nell’aria in percentuale dello 0,038% in volume, ha la capacità di combinarsi con l’idrossido di calcio Ca(OH)2 dando luogo a una reazione chimica che ha come prodotti carbonato di calcio (CaCO3) e acqua (H2O), secondo la formula
e come effetto quello di abbassare il pH della pasta cementizia. Tale fenomeno prende il nome di carbonatazione. Nei calcestruzzi densi e compatti la carbonatazione può fermarsi a pochi millimetri dalla superficie dell’elemento in calcestruzzo, ma in quelli porosi e fessurati può penetrare in profondità interessando l’intero copriferro se non addirittura spingersi oltre. Una volta che la carbonatazione arriva a interessare la pasta di cemento che avvolge il tondino, lo stesso viene a trovarsi in un ambiente non più fortemente alcalino con la conseguente perdita del film passivante che lo proteggeva dalla corrosione.
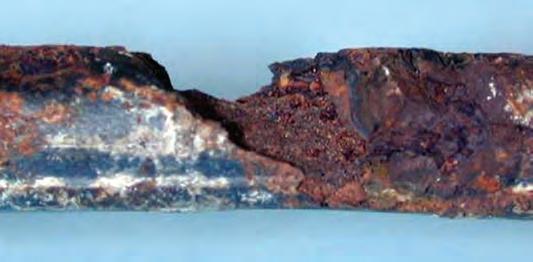
1. L’attacco localizzato per pitting su una barra d’armatura rimossa da un calcestruzzo contaminato con cloruri [1]
CORROSIONE DELLE ARMATURE
La carbonatazione in sé non danneggia il calcestruzzo e nemmeno direttamente i ferri di armatura: essa crea soltanto le condizioni affinché possa innescarsi il processo di corrosione, spianando la strada ai veri responsabili, ossia l’ossigeno e l’umidità. In assenza del film passivante, le molecole del ferro (Fe+) si combinano con l’ossigeno (O2) e l’acqua (H2O), dando come prodotto l’idrossido di ferro Fe(OH)3 (la ruggine):
La reazione appena descritta innesta all’interno della miscela cementizia un circuito elettrico (scambio di elettroni) costituito da un catodo e da un anodo, quest’ultimo costituito dalla porzione di armatura soggetta a corrosione, che si “consuma” con una velocità proporzionale all’intensità della corrente risultante. Più precisamente, non si ha corrosione se il potenziale del metallo (zona anodica) assume valori al di sopra, cioè più nobili, di un potenziale di soglia, detto potenziale critico di pitting, o di rottura Epit, che dipende dal contenuto di ioni cloruri. Si dice che gli ioni cloruri variano il potenziale di auto-passività dell’acciaio stesso, per cui l’aumento del loro tenore in una zona specifica dell’elettrolita (calcestruzzo) che circonda un pezzo di acciaio può innescarne la corrosione senza alterazioni nel campo elettrico [2 e 3].
LA PROTEZIONE CATODICO-GALVANICA
Tra le tecniche d’avanguardia dell’asset integrity, emerge la protezione/prevenzione catodico-galvanica, il cui scopo è appunto quello di proteggere l’acciaio strutturale dalla corrosione dovuta all’azione degli agenti aggressivi ambientali. Tale tecnica si basa su regole elettrochimiche e può essere realizzata imprimendo una corrente continua fra un elettrodo, definito anodo e il metallo che si vuole proteggere, che diventa quindi il catodo (Figure 2A e 2B). Questo circuito genera l’abbassamento del potenziale dell’elemento metallico e ne riduce la sua velocità di corrosione, di fatto contrastando la corrente generata dal processo corrosivo. Il processo catodico può essere innescato in due diverse condizioni: • qualora il fenomeno della corrosione dell’elemento metallico sia già in atto, ci si trova in condizioni di protezione catodica, che ha lo scopo di ridurre l’attività fino al suo arresto; • nel caso in cui il fenomeno della corrosione non si sia ancora verificato si può definire il processo di prevenzione catodica, che ne impedisce l’innesco. Le tecniche per realizzare un intervento di protezione catodica sono sostanzialmente due: • sistema a corrente impressa; • sistema ad anodi galvanici. Il sistema a corrente impressa, non trattato in questo articolo, utilizza un alimentatore esterno per sviluppare la corrente necessaria. Il sistema ad anodi galvanici ha invece il principale vantaggio di non utilizzare nessun alimentatore di energia esterno. Quest’ultima tecnica si basa infatti sul principio secondo il quale, quando due diversi tipi di metallo collegati tra di loro sono annegati in un adeguato elettrolita, il metallo con il potenziale elettrico più negativo ossiderà proteggendo il metallo con il potenziale meno negativo. Per la protezione dell’acciaio generalmente vengono utilizzati l’alluminio e lo zinco qualora l’elettrolita sia l’acqua di mare o il calcestruzzo, il magnesio
per gli elementi immersi nei terreni e nelle acque dolci e il ferro per le leghe di rame o gli acciai inossidabili. Per quanto riguarda le armature annegate nel calcestruzzo, la protezione catodica-galvanica viene realizzata andando ad apporre elementi di zinco in forma di “panetti” (Figure 3A e 3B) direttamente sulle armature o mediante anodi laminari fissati con un gel elettrolitico adesivo (Figure 4A e 4B), sulla superficie della zona da proteggere. Esiste anche una terza modalità, meno dif-
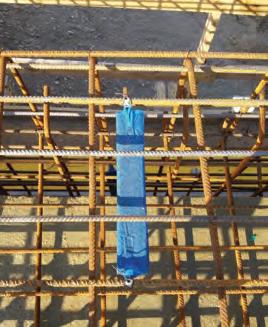
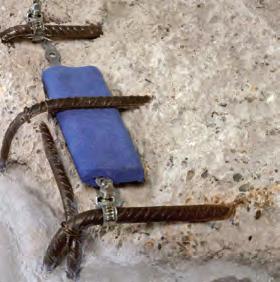
3A e 3B. Esempi di collegamenti tra armature e anodi di zinco
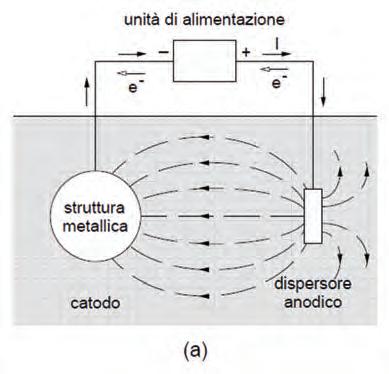
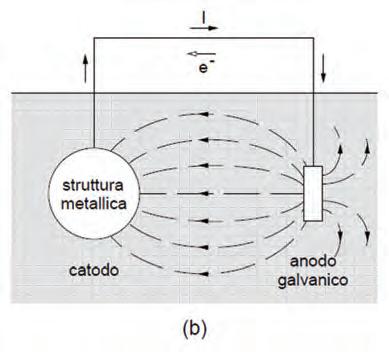
2A e 2B. I sistemi di protezione catodica: mediante correnti impresse (2A) e con anodo sacrificale (2B) [1]
tecnologie &sistemi
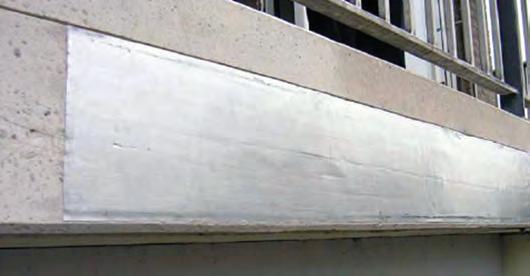
4A e 4B. Lamine autoadesive di zinco per protezione catodica
fusa nel nostro territorio, e consistente nella creazione di uno strato esterno di zinco sulla superficie del calcestruzzo tramite spruzzatura. Ad ogni modo, qualunque sia la tipologia di anodo galvanico utilizzato, è indispensabile che i due metalli (zinco dell’anodo e acciaio delle armature) siano a diretto contatto tra loro oltre che con l’elettrolita (calcestruzzo) così che il circuito galvanico si possa chiudere.
LA METODOLOGIA DI INDAGINE
La problematica principale nel definire un intervento protettivo delle barre di armatura in calcestruzzo armato è che la loro posizione e il loro stato di degrado non sono visibili ad occhio nudo. L’obiettivo principale dell’indagine è quello di evidenziare fino a che punto la corrosione, nella zona di indagine, si sia estesa alle barre di rinforzo e se abbia aggredito eventuali barre di precompressione o i loro sistemi di ancoraggio. Per fare ciò si eseguono in genere prove di tipo elettrico e chimico come ad esempio: • indagine pacometrica, per il rilevo della posizione e del diametro delle armature; • la mappatura del potenziale di corrosione, attraverso la quale vengono acquisiti dati circa il potenziale elettrico delle armature (differenze di potenziale, espresse in millivolt) rispetto a un elettrodo di riferimento. Tali dati vengono poi processati attraverso l’aiuto di software al fine di poter riprodurre su diagrammi a colori la distribuzione delle aree in corrosione, permettendo quindi la loro localizzazione in modo puntuale (Figura 5); • l’analisi chimica in laboratorio del calcestruzzo per la misura del tenore di cloruri.
GLI INTERVENTI TIPOLOGICI
Gli interventi tipologici si suddividono in due principali famiglie: gli anodi interni (sotto forma di “panetti”) e gli anodi esterni (sotto forma di “lamine”). La scelta tra i due tipi di intervento dipende da diversi fattori, quali il tipo di elemento strutturale che si intende proteggere, la facilità di applicazione di uno o dell’altro metodo, la necessità o meno di eseguire demolizioni e scarifiche profonde. L’intervento con lamine esterne è preferibile quando la superficie del calcestruzzo presenta un degrado non troppo profondo, tale da non necessitare la messa a nudo di armature. Quando invece il ciclo di lavorazione previsto include il trattamento a vivo delle armature esistenti o l’aggiunta di reti integrative, è possibile utilizzare la tecnica degli anodi esterni. Gli esempi che seguono presentano un caso per ognuna delle due tipologie di intervento e riguardano due degli elementi più sensibili e spesso ammalorati che costituisco i ponti in c.a. e c.a.p., ovvero le selle gerber e i pulvini. Altri elementi che usualmente sono soggetti a corrosione delle armature e che quindi possono essere candidati ideali per una protezione catodica galvanica sono ad esempio i cordoli di impalcato, le teste delle travi in corrispondenza dei giunti, e in alcuni casi i fusti delle pile.
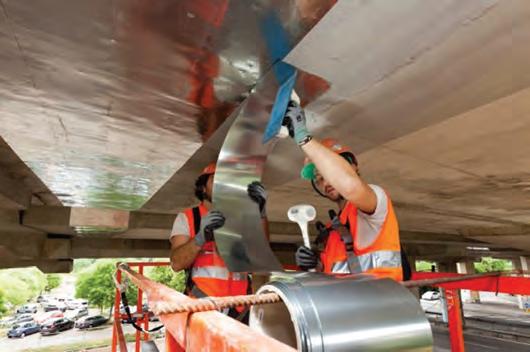
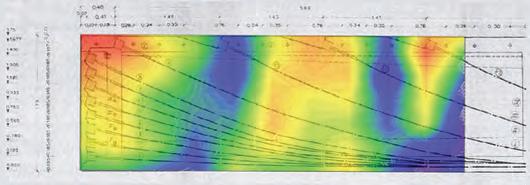
5. Un esempio di mappatura rispetto a un elettrodo di riferimento di una trave: le aree rosse rappresentano quelle dove il potenziale è più negativo e quindi la corrosione è potenzialmente più sviluppata, a causa di locali deficienze nell’impermeabilizzazione dell’impalcato [4]. Sulla base dei risultati ottenuti dalle prove sopra menzionate nonché della geometria e dell’effettiva fattibilità si va a scegliere e dimensionare il tipo di intervento da realizzare, in funzione dei parametri esposti di seguito [4 e 5]
6A e 6B. Un intervento di protezione catodica con lamine di zinco in corrispondenza del giunto gerber: in zona di appoggio (6A) e in campata con tampone (6B)

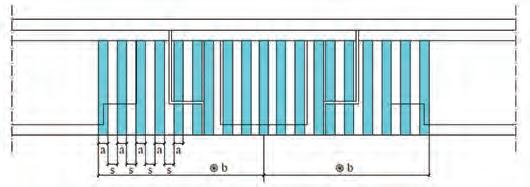
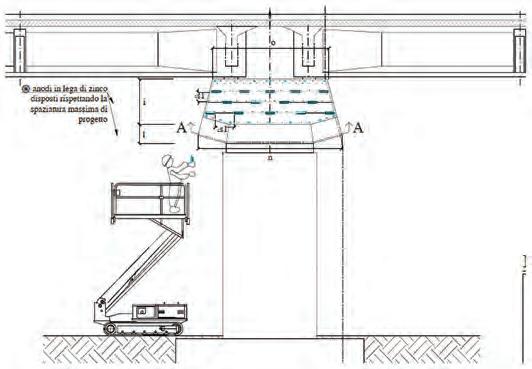
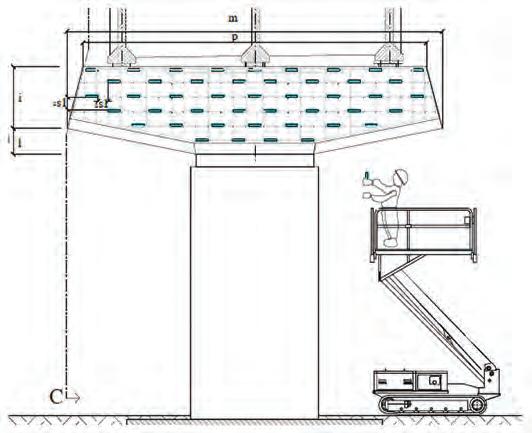
7A e 7B. L’intervento di protezione catodica con anodi interni in corrispondenza di un pulvino in calcestruzzo armato
È mostrato un intervento di protezione catodica con anodi interni in lega di zinco di un pulvino in calcestruzzo armato, di forma tipologica con dimensioni in altezza i e l, e dimensioni principali in pianta (m x n) e (p x o).
GLI ESEMPI DI DIMENSIONAMENTO
Il dimensionamento viene effettuato facendo riferimento alla superficie di calcestruzzo attaccato ed in funzione delle prescrizioni imposte dalla Norma UNI EN ISO 12696. I parametri di input nel dimensionamento degli elementi di protezione per un elemento strutturale in c.a. sono: • estensione desiderata, in anni, della vita utile dell’opera; • tipologia di protezione (lamine, panetti, ecc.); • fattore utilizzo dell’elemento di protezione (fornito dal produttore dell’anodo); • contenuto di cloruri in massa del cemento. Rispettando quanto prescritto dalla Normativa e guardando ai diagrammi di Pedeferri (diagrammi di comportamento dell’acciaio nel calcestruzzo per differenti potenziali e contenuti di cloruro), se si considera ad esempio 1 m² di calcestruzzo con rapporto area di acciaio/area di calcestruzzo Aa/Ac = 1, nel caso sia rilevato un contenuto di cloruri pari allo 0,45% in massa di cemento, si può progettare un sistema che, erogando 20 mA/m² per il primo anno, al fine di garantire la ripassivazione, e 5 mA/ m² per i successivi 19 anni in modo da assicurarsi che il pitting non si possa innescare di nuovo, prolunghi la vita utile dell’elemento di 20 anni utilizzando lamine autoadesive di zinco di larghezza 25 cm (anodi esterni). Il consumo di zinco al primo anno per 1 m² di acciaio sarà dunque pari a:
mentre per gli anni successivi:
Per la superficie specificata, la massa totale di zinco necessaria ad una protezione di 20 anni è pari a:
che corrisponde a un fabbisogno di copertura con lamina di zinco per ogni m² di calcestruzzo (Ac = Aa) di:
Essendo le strisce larghe 25 cm, ciò corrisponde a una spaziatura tra di esse pari a circa 5 cm. Variando di volta in volta il rapporto Aa/Ac è possibile costruire un grafico che, per tale tipo di anodo, fornisca la spaziatura massima da adottare in funzione del rapporto Aa/Ac stesso.
LA PROTEZIONE CATODICA CON ANODI INTERNI DI ZINCO PER STRUTTURA BIDIMENSIONALE
Qualora invece si volesse proteggere un elemento strutturale a sviluppo bidimensionale in calcestruzzo armato non immerso in acqua attaccato da fenomeni di corrosione delle barre di armatura con anodi interni, assumendo: • estensione, in anni, della vita utile dell’opera = 20 anni; • tipologia di protezione = anodi di zinco; • fattore utilizzo dell’elemento di protezione = 0,9; • contenuto di cloruri in massa del cemento = 0,45%.
CORROSIONE DELLE ARMATURE


8. Le spaziature per anodo laminare dal peso di 1,7 kg/m² al variare del rapporto Aa/Ac
tecnologie &sistemi
si avrebbe un consumo di zinco al primo anno per 1 m² di acciaio pari a:
mentre per gli anni successivi:
Per tale superficie la massa totale di zinco necessaria a una protezione di 20 anni è pari a:
che corrisponde a un fabbisogno per ogni m² di calcestruzzo (Ac = Aa) di:
L’area di influenza di ciascun anodo è quindi pari a:
La spaziatura massima (verticale e orizzontale) da adottare fra un anodo e il successivo risulta pari a:
Variando di volta in volta il rapporto Aa/Ac è possibile costruire un grafico che per tale tipo di anodo fornisce la spaziatura massima da adottare in funzione del rapporto Aa/Ac stesso.
IL MONITORAGGIO
Per valutare l’efficacia della protezione catodica occorre impiegare un sistema di monitoraggio, che come definito dalla Norma UNI EN ISO 12696 deve essere costituito da sensori applicati in punti rappresentativi, disposti nelle zone anodiche da proteggere. Un tipico esempio di sistema di monitoraggio di protezione catodica è quello realizzato sui cordoli dei ponti in calcestruzzo armato. L’installazione del sistema di misura prevede le seguenti fasi: • si isola l’armatura del cordolo per un tratto di alcuni metri; • si posiziona un anodo interno di zinco non a contatto con le armature; • si collega un filo elettrico all’anodo di zinco e uno a una barra di armatua vicina e si collegano i due in una scatola di derivazione esterna a chiudere il circuito. A intervalli di tempo prefissati si effettuano le misurazioni disconnettendo il circuito e connettendo il filo dell’armatura a un elettrodo di riferimento al fine di verificare se la protezione dello zinco è ancora attiva o no. Si rimanda ad ulteriore bibliografia per approfondimenti riguardo lo stato dell’arte e tecniche innovative di applicazione [6, 7, 8, 9, 10, 11, 12 e 13]. n

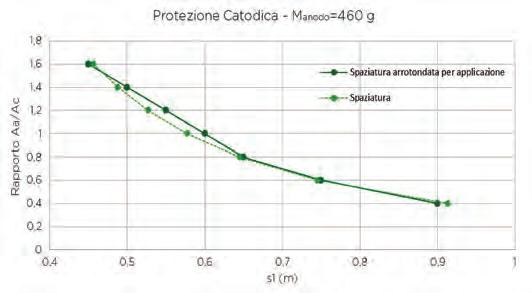
9. Le spaziature per anodo interno dal peso di 460 g al variare del rapporto Aa/Ac per elemento strutturale bidimensionale (1) Ingegnere, Direttore Operation e Coordinamento Territoriale di ANAS SpA (2) Ingegnere, Direzione Operation e Coordinamento Territoriale - Ufficio Ponti Viadotti e Gallerie - Responsabile Centro-Sud di ANAS SpA
Bibliografia
[1]. L. Bertolini - “La corrosione delle armature nel calcestruzzo e la sua prevenzione”, Politecnico di Milano. [2]. B. Bazzoni - “Dispense del Corso “Corrosione e protezione dei materiali metallici””. [3]. P. Pedeferri - “Cathodic protection and cathodic prevention”, 1996. [4]. C.A. Rodopoulos, P. Panetsos, I. Koropoulis - “Application of galvanic cathodic protection using Zink Sheet Anodes according to Ε 12696: axios Bridge”, Section Athens to Thessaloniki, 2016. [5]. M. Belli, R. Giorgini, F. Laino - “La manutenzione dei giunti del viadotto dei Parchi”, “Strade & Autostrade”, n° 119 Settembre/
Ottobre 2016. [6]. D. Agostini, L. Stucchi - “Evoluzione e controllo della corrosione in strutture in c.a. cave a contatto con acqua di mare”, Tesi di Laurea del corso di Laurea Magistrale Ingegneria dei Materiali, Politecnico di Milano, 2011. [7]. A. Della Pergola - “Condizioni critiche per l’innesco della corrosione da cloruri dell’acciaio nel calcestruzzo”, 2012. [8]. M. Dugarte, A.A. Sagüés - “Galvanic point anodes for extending the service life of patched areas upon reinforced concrete bridge members”, University of South Florida, 2009. [9]. R. Giorgini, H. Van den Hondel, J. Gulikers - “Assessment of the throwing power generated by a surface applied galvanic cathodic protection system on a light weight concrete bridge deck soffit”. [10]. A.M. Hassanein, G.K. Glass, N.R. Buenfeld - “Protection current distribution in reinforced concrete cathodic protection systems”, 2002. [11]. S. Laurensa, R. Françoisa - “Cathodic protection in reinforced concrete structures affected by macrocell corrosion: a discussion about the significance of the protection criteria”, 2017. [12]. G. Sergi, C.L. Page - “Sacrificial anodes for cathodic prevention of reinforcing steel around patch repairs applied to chloride-contaminated concrete”. [13]. A.J. Van den Hondel, R.G. Giorgini, J. Gulikers - “Application of a surface-applied cathodic protection system on a light weight concrete bridge”, Part II: “Developments in time of the effectiveness by potential decay values and current densities”.