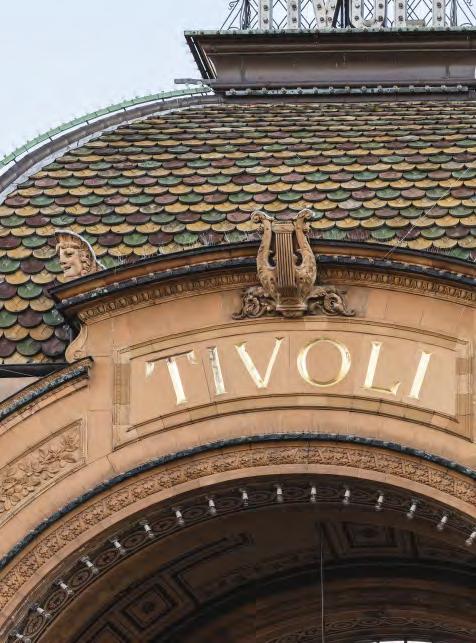
5 minute read
Introduction
from Custom Bricks
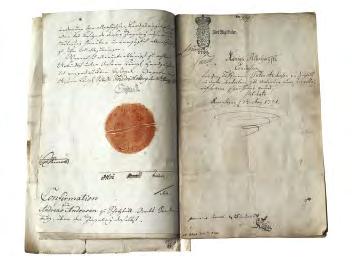
Timeless craft, endless possibilities
Brick has a great many qualities. Made from the purest elements imaginable – clay, water and fie – it has an almost infinit lifespan and requires no maintenance. Bricks laid in lime mortar can be taken down and reused. Or they can be crushed, and the grains used to make new bricks or to build roads, squares and other facilities.
As a building material, brick also has another almost unique quality. It can be produced in exactly the shape you need. All it takes is a brickworks capable of making them by hand. Like Petersen Tegl.
When the company was founded at the present address at Nybølnor in Broager in 1791, handmade bricks were the norm. The Industrial Revolution changed all that, and by the early 20th century, the entire Western world was using machines to produce bricks. They looked mass-produced – uniform, smooth, very few colours.
But not at Petersen Tegl. It was one of the few brickworks to return to its roots.
In the early 1980s, Petersen invented and built machines designed to imitate manual processes, endow the water-brushed bricks with their original, uniformly uneven look and provide four equally presentable surfaces. Ever since then, those same machines have accounted for a significan proportion of the company’s production.
Tivoli in Copenhagen, the second oldest amusement park in the world, celebrated its centenary in 1990. To mark the occasion, it commissioned Petersen Tegl to produce new terracotta ornamentation for the original main entrance. Christian A. Petersen immediately threw himself into the project, and the Custom Brick Department was born.
In the late 1990s, when the architect Peter Zumthor won a competition to design the Kolumba Museum in Cologne, he asked Petersen Tegl to develop a special brick for the project. The Custom Brick Department had the requisite expertise, and the museum was built in the new, handmade Kolumba brick and inaugurated in 2007. Handmade standard bricks have been a hallmark of Petersen Tegl ever since.
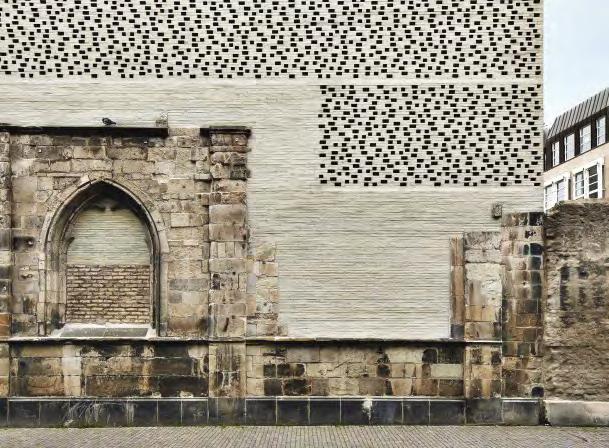
A large part of the company’s production now consists of the standard bricks Kolumba and Cover. They are produced 100% by hand in wooden moulds. However, custom bricks for special projects also account for an ever-increasing proportion of turnover.
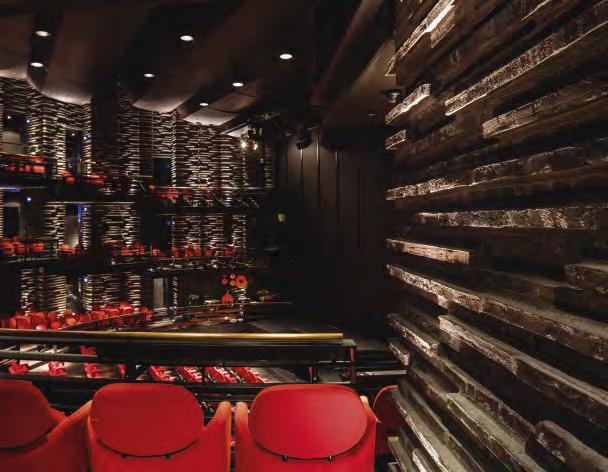
Special formats
The fact that so much of Petersen’s standard production is by hand makes it easy to comply with requests for special formats. The processes and equipment are all there. The customer and brickworks discuss the specificaions for orders. Then a wooden mould is made. An order can range from a single brick for a restoration project to large-scale new construction.
Demand for special formats has been increasing in recent years. It gives an obvious freedom to architects and designers during the creative process that brick can be custom made.
In some cases, special formats are used for ornamentation and complicated detailing. In others, they make the brickwork look as harmonious as possible, for example by using angled bricks on corners. Or bricks can be produced in exactly the lengths needed in order to fi the planned length of the row in the most elegant way.
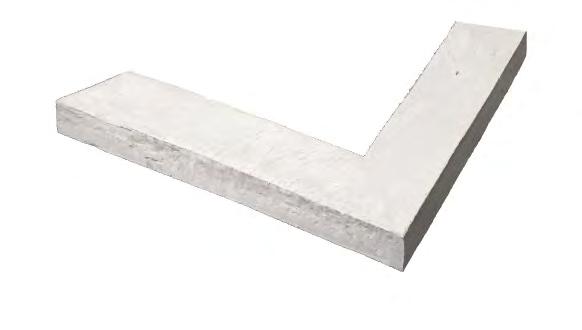
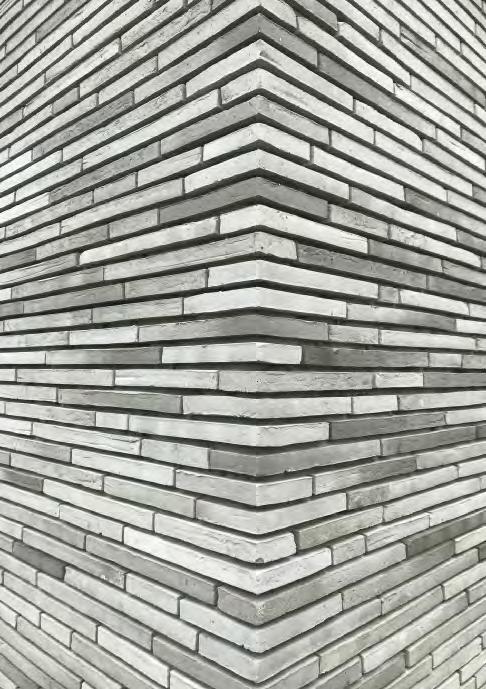
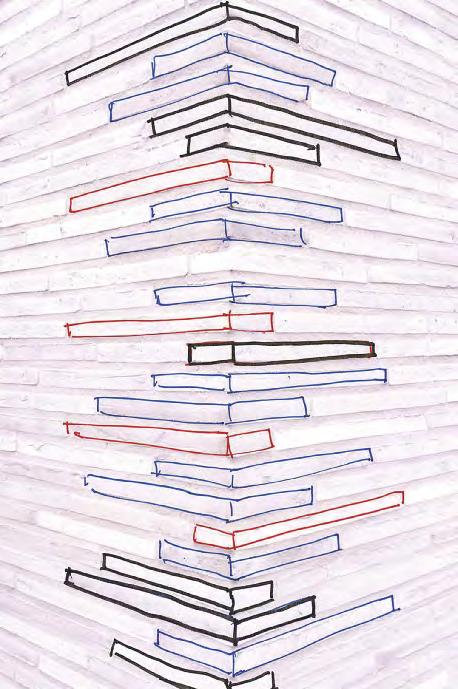
Preparation of clay
Petersen Tegl adapts the production methods according to the actual type of brick. At Petersen Tegl, the clay is pugged, formed and pressed by means of techniques imitating the procedures used when also this part of the work was done by hand. The method gives the clay its optimum texture with capillars and air pores allowing the water to expand when it freezes to ice without spoiling the brick. The fact that the brick may absorb water does not entail risks of frost damage, and Petersen Tegl’s bricks are 100% frost resistant.
Methods of formatting
Three methods of formatting are used to produce the special formats, wooden moulds, templates or plaster moulds.
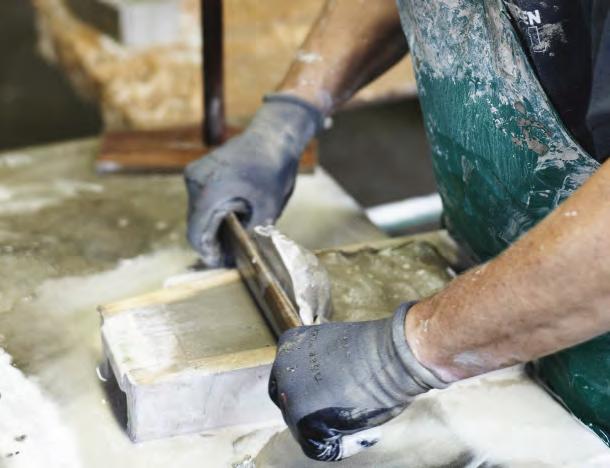
Wooden moulds: Bricks have been produced in wooden moulds for thousands of years. They are hand struck by pressing a lump of clay into a wet form. The clay is then compressed and any surplus material struck off. Water or slurry is used as a lubricant to slide the lump out of the mould and onto a plate to dry. It is then fied in a kiln.


Photos: Anders Sune Berg
Templates: A lump of clay bigger than the fina product is pressed into a wooden mould and left to dry for a few days. It is then clamped between two pieces of indented wood and cut with a wire. The excess clay is removed, and the brick is rubbed down. After the wooden template is removed, the clay is dried and fied.

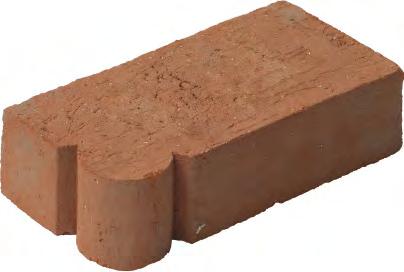
Plaster moulds:
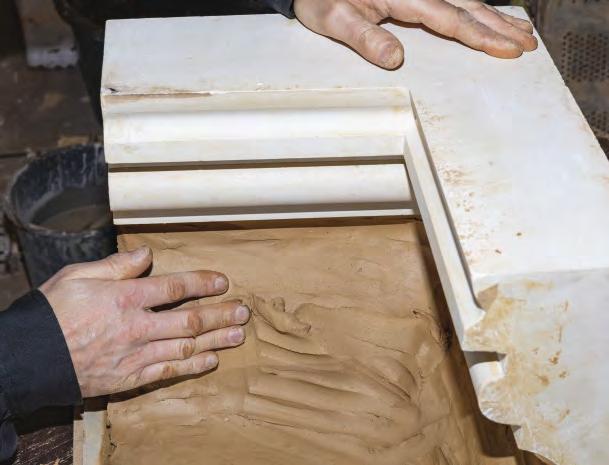
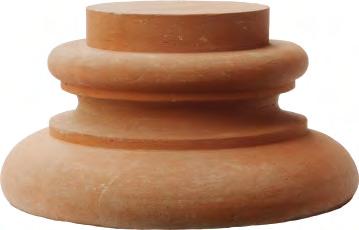
Mainly used in restoration projects to recreate the original bricks. Based on a 3D drawing, a plastic or wooden model is produced, 8-10% larger than the original. This is then used to make a plaster mould. High-quality clay is pressed carefully into the mould to avoid air pockets forming. Once the mould has been filed, a cavity is carved out to ensure that the clay dries evenly. The plaster draws water out of the clay for a few hours, and then the mould is removed. The brick is left to dry before firing Photo:
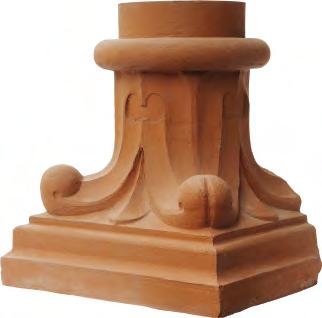

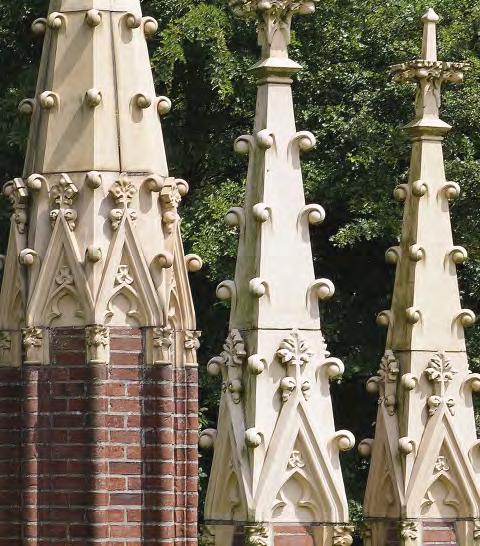
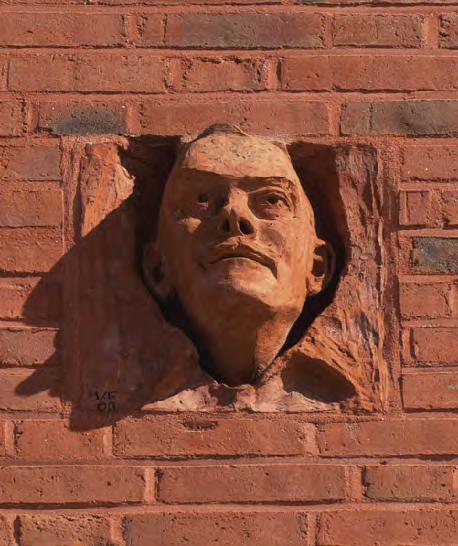
Custom bricks made in wooden moulds create the illusion that the façade is made of pine logs.

Semi-circular bricks positioned in a pattern were recreated to replace existing ones when the wall around a 19th-century property was restored.
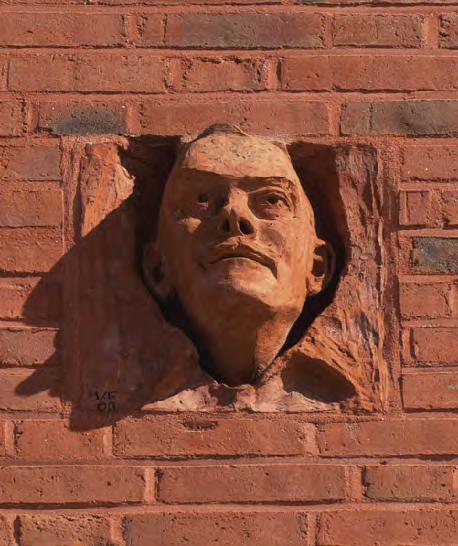
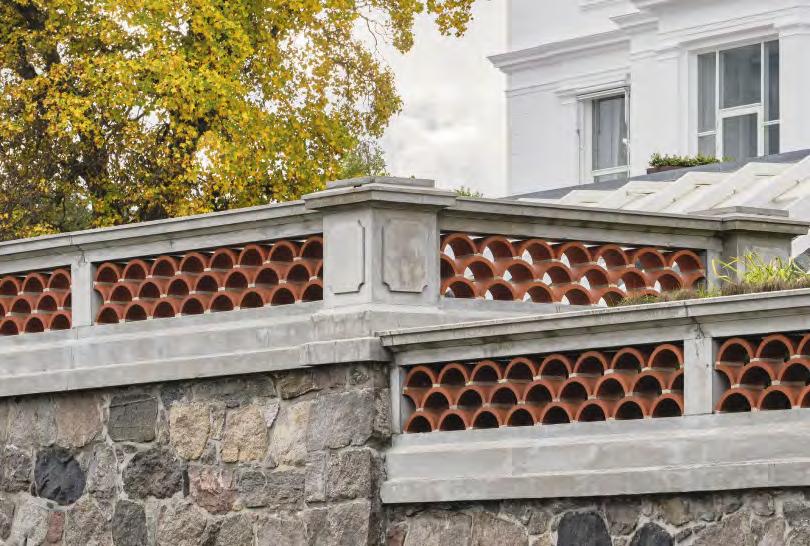
Special colours
To meet the rising demand for custom shades and tones, the brickworks has its own dedicated colour department, which constantly conducts experiments. As a result, several specially coloured bricks originally developed for specifi projects have later been added to Petersen’s standard range.
Two factors determine a brick’s colour –the type of clay and the firin process. Petersen uses Danish, German and English clay, either in pure or mixed form. When clients request particularly unusual hues, small amounts of natural clay minerals are added to the mixture.
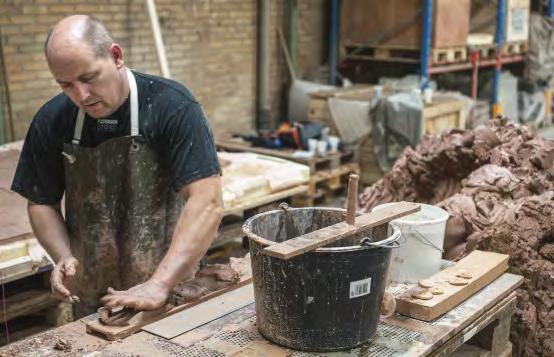
The bricks are fied at 1,000-1,150°C. Different temperatures influenc the fina colours and appearance. The firin process can also be adjusted by adding to or reducing the amount of oxygen in the kilns. These processes – known as ‘reducing’ and ‘oxidising’ – provide extra colour options.
The variations in clay type and firin processes can be combined in various ways to produce an almost infinit array of colours in the fina product.
For Petersen Tegl, the colouring process can be part of fulfiling a major order for bricks that all have the same tone and play of colour. However, and just as often, it can also be for a project that calls for a batch of bricks all of which have different colour variations.
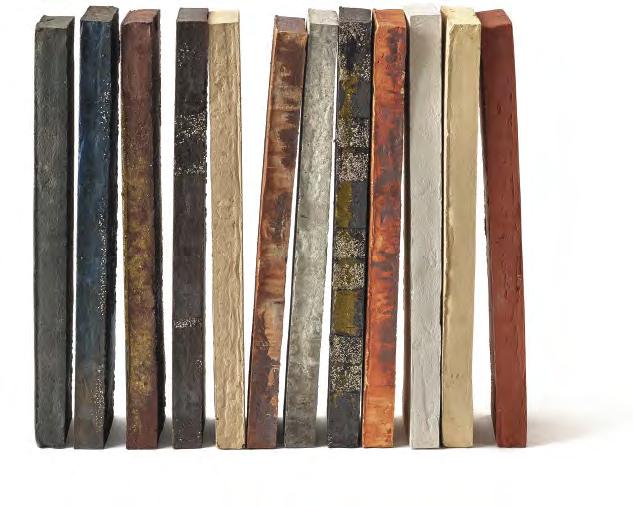
Special glazes
Glazed brick has been around for millennia. For example, remains have been unearthed in Mesopotamia of buildings with glazed brick façades built hundreds of years BCE.
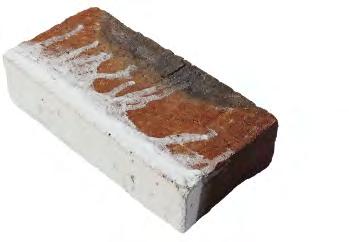
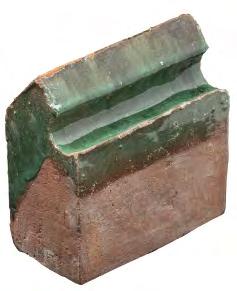
Architects have loved the glazed look ever since. It catches and reflect light and can be used to emphasise certain details, sections or colours on the façade.
Petersen Tegl has a special glazing department, which – like the colour department – is constantly experimenting to meet clients’ requirements.
Glazed bricks are produced by applying a liquid glaze after the firs firing The bricks are then fied in electric or gas kilns at varying temperatures so that the glaze melts without affecting the character of the brick. Sometimes, an underglaze is necessary, in which case the brick needs to be fied several times.
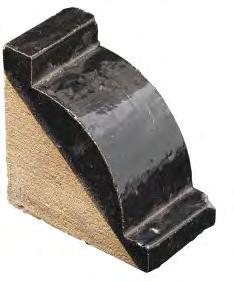