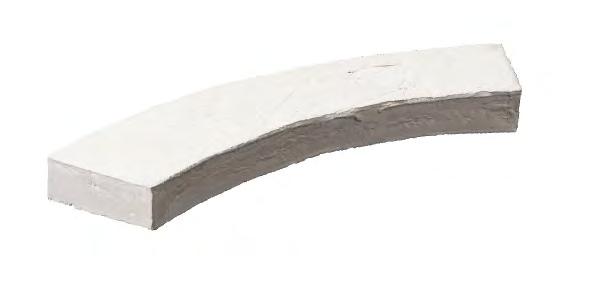
15 minute read
Housing
from Custom Bricks
Villa Platan, Aarhus, Denmark
Client: Private
Architect: ADEPT
Completed: 2015
Brick: K91 + two custom format bricks in the same clay
Photos: Anders Sune Berg, Jakob Lerche
Multi-purpose brickwork
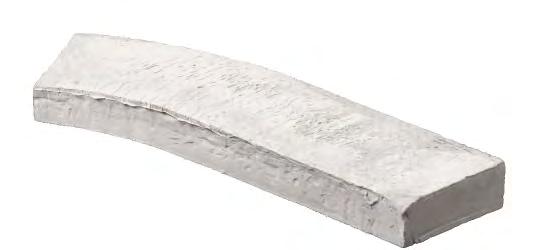
Just two customised bricks were enough to produce precisely the curved forms the architect wanted.
The house comprises just four rooms, each with its own function. Each room is almost an entirely separate structure, carefully positioned to protect privacy, preserve existing trees, frame the view and provide shelter from the wind. The four structures merge at their corners, and short passages create transitions between the rooms without the need for doors. The curved walls, made with customised bricks, mean that the passages are easily traversed.

“Since all the bricks in the façades are handmade, it was a simple matter to supplement them with the curved customised bricks we needed, which are, of course, also made by hand. The design of the façade means that all the curves have the same radius, so we only needed two types of custom brick –one that is curved on all sides and one that has both curved and straight edges. They merge naturally into the brickwork’s wild bond by alternating the two, resulting in a beautiful, harmonious surface. In addition, the long lines of the house are emphasised by the joints – the horizontal ones are retracted, while the vertical ones align with the façade,” explains the architect, Anders Lonka of Adept.
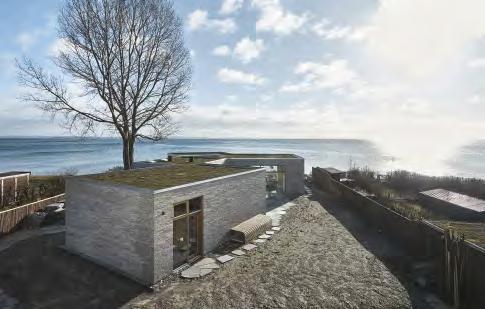
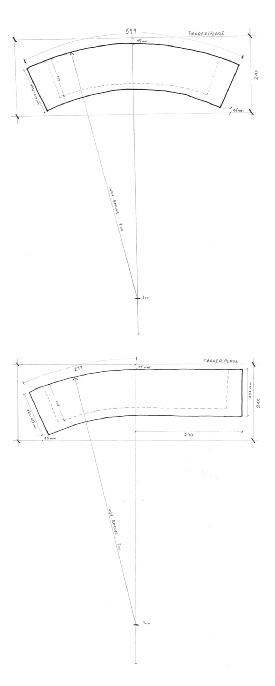
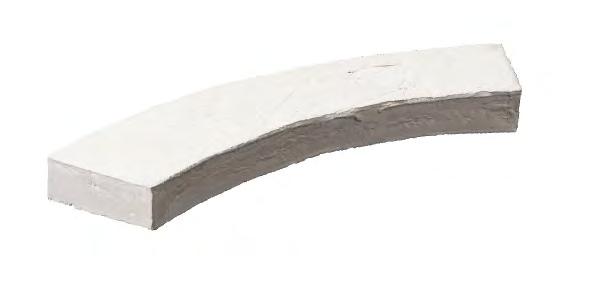

About Villa Platan
Lonka adopted the mantra ‘As little as possible, as well as possible’ when designing a new home for his retired parents.
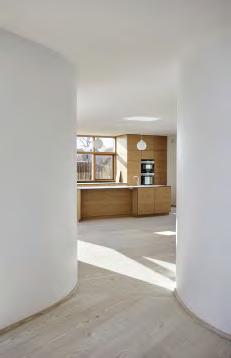
“It means that we use fewer resources, which lets us design more flexibl buildings and, not least, leaves time to add subtlety and refinemen to the architectural elements,” Lonka explains.
Both the clients and the architect knew from the outset that the house would have brick façades that require minimal maintenance. Kolumba was the obvious choice because of the building’s horizontal profile and several brick variants were considered. Lonka and his parents took several types of grey Kolumba to the beach before opting for K91, the greywhite shades of which best capture the colours of the sand and the rocks.
“The house is only feet from the beach. Given the area’s unforgiving conditions, it’s surprising that many of the houses along the coast have plaster facades,” Lonka adds.
Villa Platan was nominated for the Wienerberger Brick Award in 2018.
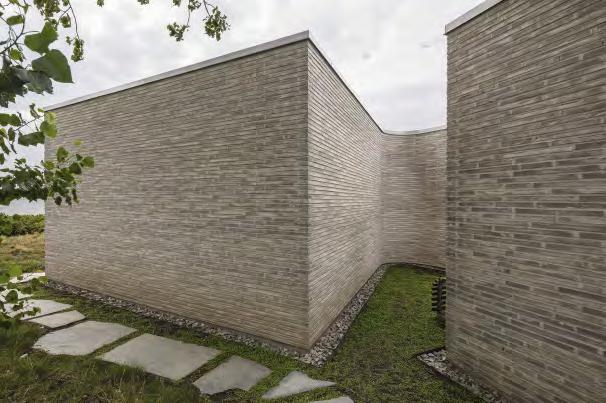

Private home in Groenekan, The Netherlands
Client: Private
Architect: Zecc Architecten
Completed: 2013
Brick, façade: Kolumba K60 + custom format bricks for corners, window niches, sills and lintels
Brick, roof: Custom Cover format in German clay
Photos: Paul Kozlowski
Livable monolith
Well-designed brickwork and exemplary craftsmanship give the desired monolithic air.
The desire for a house with a monolithic look drove the project and led the architect and clients to Petersen Tegl, who they knew could produce the custom bricks that would deliver the all-important, seamless aesthetic.
For the roof, the architects chose a custom-made fla version of Cover with holes to make it easy to mount. Zecc Architecten also designed several custom bricks for the corners, window niches, sills and lintels – all made from the same clay as the standard K60 used on the rest of the façade. Every detail on the new home, including the brickwork, was designed at 1:1 scale, and the craftsmanship is exemplary.
In addition to the 11,040 standard K60 bricks, Petersen Tegl produced 1,070 roof tiles and 1,271 custom bricks. Every brick is handmade and hard-fied in reddish-brown colours, with sand and light slurry on the surface.

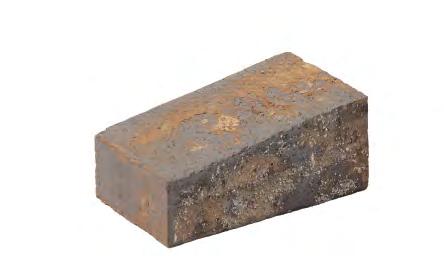
Zecc Architecten designed a brick in K60 clay, 528 x 330 x 37 mm, for the roof. They also designed a series of different moulded bricks to allow the roof and façades on the sharply define construction to meet in perfect harmony.


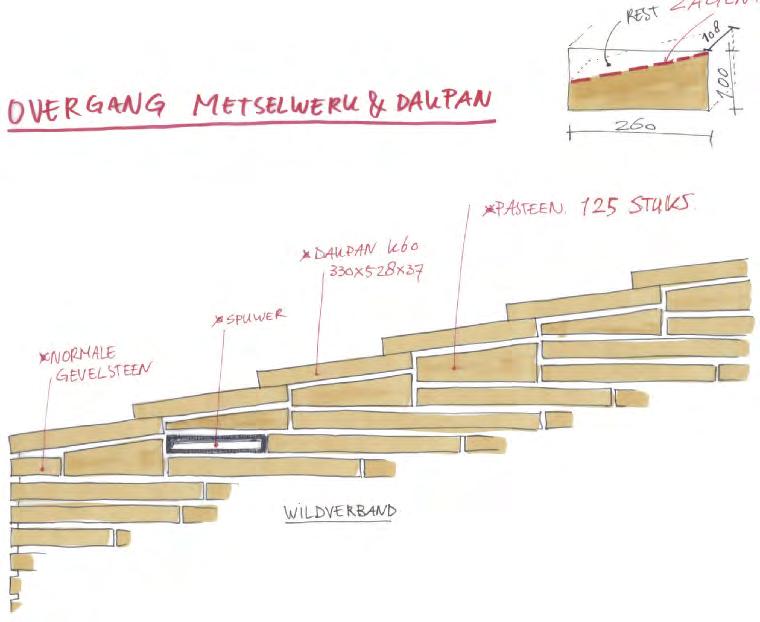
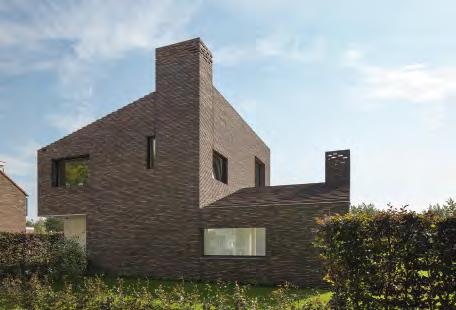
About the private home in Groenekan
The house is on the outskirts of a village, close to a rural area. Most of the surrounding buildings have a simple design, with tiled roofs, plaster façades and partial wood cladding. It made sense for the new building to adopt the same look but with a contemporary feel.
The house consists of two angular, interlocking blocks covered in dark brick and with sharp edges. Both main blocks have roofs of different heights – the lower forming the transition to the adjacent rural area, where the maximum permitted construction height is one storey.
The bricks flo seamlessly around all corners, spreading over the surfaces in the window recesses, up over the roof and outwards to form the paving on the two terraces. A chimney on the roof of each block acts as an anchor point for the vertical grooves that run down through the brickwork on the sides, inlaid with bands of Kolumba that act as expansion joints. At the top, the chimneys dissolve into fiigree patterns that allow you to look through them, softening the transition to the sky.
The concealed gutters are built into the eaves, and no downpipes spoil the exterior – instead, internal pipes drain off the water. The flashing along the roof edges are in brownish lead and perfectly match the homogeneous brickwork.
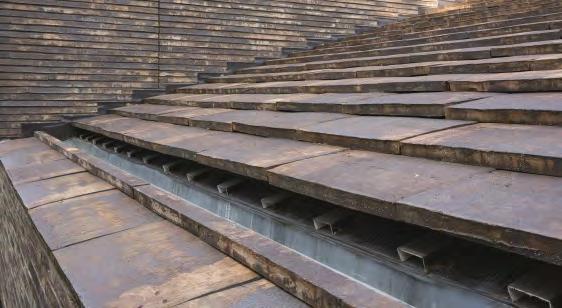
Private home in Utrecht, The Netherlands
Client: Private
Architects: Hilberink Bosch Architecten

Completed: 2014
Brick: K44, K47 + K49 in custom lengths
Photos: Paul Kozlowski
Forest shades
The woodland setting inspired varied lengths of Kolumba in a private home in the Netherlands.
The client wanted a seamless transition between the building and the landscape, a house in dialogue with its surroundings. Accordingly, the architects opted for colours and materials that would create a sense of connection between place and building. The requirement was for a modern home, but not an arrangement of white boxes. The house is in a forest, so the architect chose natural materials, with sand-coloured concrete and bricks that reflec the bark on the pine trees.
In order to give the walls a natural-stone look, three different lengths of brick were used. The longest measured 1 m – the maximum Kolumba length. The deep joints emphasise the horizontal lines, and the use of dark mortar makes the bricks appear to have been loosely stacked rather than precisely placed by a bricklayer.
Overall, a simple and precise dynamic of horizontal and vertical lines has been created architecturally. The sand-coloured concrete deck was cast in situ and has a matte surface, offering a calm contrast with the bricks’ rich play of colour.

“The concrete is the colour of the sand dunes. The bricks are from the Petersen Kolumba range, in shades from black to green and orange. We wanted a minimal look, so went with concrete, brick, glass and cedar, in rustic and toned-down finishes.
Hilberink Bosch Architecten
About the private home in Utrecht
Major changes of level in the terrain are rare in the Netherlands, but north of Utrecht is a ridge of sand formed in the Ice Age and covered by forest. This special location, with a vertical drop of six metres, inspired the design of the new home. It stands on the northern and eastern edges of a square site, with the house along the northern and eastern perimeter and a long horizontal wall extending from the garage to the south.
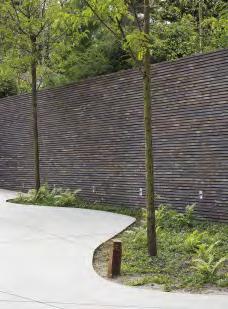
Visitors arrive via a double-height hall, in which the owner exhibits some of his art collection. Most of the living spaces are on the firs floo, connecting the building to the dune and optimising the view of the lush garden. The large windows and sliding doors make the transition between interior and exterior as flui as possible. Interaction with nature is a constant, and it is easy to follow the passing of the seasons.
Brick has been used inside and out, including for the big fieplaces, which infuse the home with warmth and cosiness as the days grow shorter and colder. The strong textural effect of the bricks emphasises the homely feeling and results in an unpretentious aesthetic.

Cabin in Hvaler, Norway
Client: Private
Architect: PUSHAK
Completed: 2020
Brick, façade: C56, 170 mm
Brick, roof: C56, 240 mm custom made
Photos: Ivan Brodey
Custom format makes roof steeper
Cover roof tiles designed in L-format rather than C allow for a steeper incline.
The roof and façades of this cabin in Hvaler are clad in Petersen Cover. Its shimmering, grey-brown shades echo the surrounding boulders, pine trunks, heather and other vegetation.
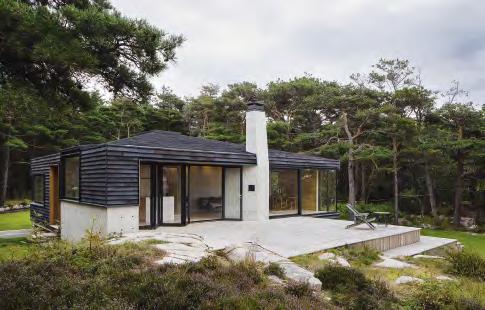
In their detailing, the architects used both Cover formats – 170 mm wide on the façades, 240 mm on the roof. Although broader, the roof tiles look the same size when seen from the ground.
“It is also an advantage that Cover is made by hand, which means it is easy to modify,” says architect Gyda Drage Kleiva of PUSHAK. “The roof tiles are in a specially moulded L-format, rather than C. This allows for a steeper incline, which was both a visual and practical advantage for this project.”
C56 in a special L-shaped edition, which allows for a steeper incline and has both visual and practical advantages.
About the cabin in Hvaler
The cabin lies on an island in Hvaler, on the edge of a forest, with views of the sea and the uniquely beautiful Ytre Hvaler National Park. The previous cabin on the site was built in 1962 but had fallen into disrepair and had an impractical floo plan, so the owner decided to rebuild.
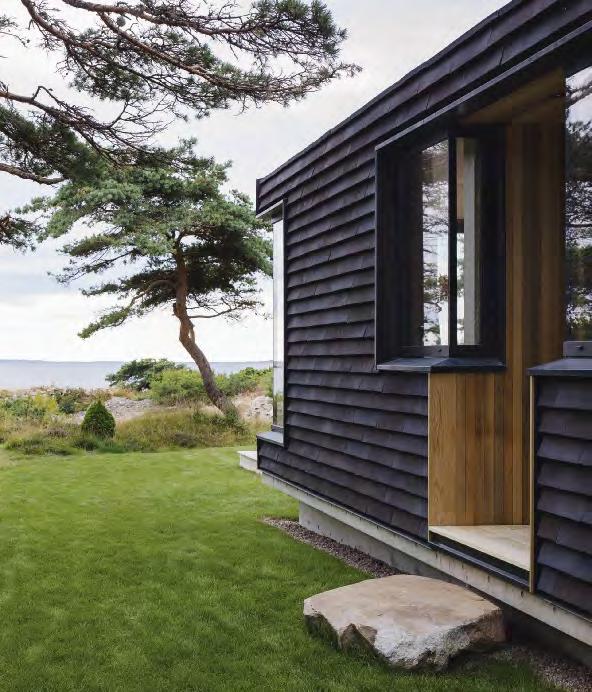
It was crucial for the architect and client that the site remained as intact as possible. The cabin was designed and positioned with the greatest possible respect for the surrounding landscape and vegetation.
Local building regulations allowed a maximum façade length of 12 metres on the side facing the sea, which is why the building is so compact – almost square. It does not spread out but is a simple, well-define volume that clings to the site on the hill overlooking the water.
The cabin has an asymmetrical, hipped roof that allows water to drain off in four directions. This distinctive roof shape also means it was possible to pull the cornices down toward the ground at each corner. All external doors, including the front one, are in recesses sheltered by the large roof. The recessed façade sections are clad with untreated cedar, which will turn silky grey over time.
“It is also an advantage that Cover is made by hand, which means it is easy to modify,” says architect Gyda Drage Kleiva of PUSHAK. “The roof tiles are in a specially moulded L-format, rather than C. This allows for a steeper incline, which was both a visual and practical advantage for this project.”
Holiday home in Tisvilde, Denmark
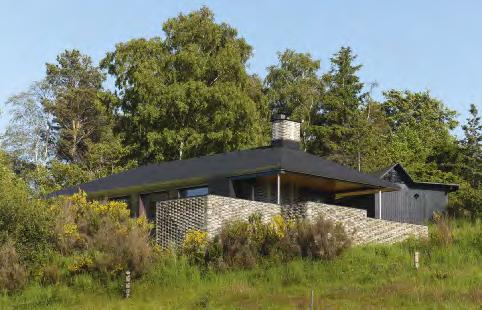
Client: Steen F Lindbergh
Architect: Tage Lyneborg
Brickwork: Sculptor Bjørn Nørgaard
Completed: 2010
Brick: D48, D54 and D72 DNF + custom format bricks in the same clay
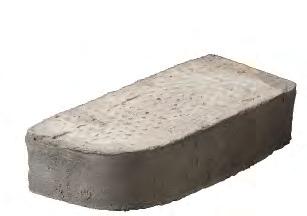
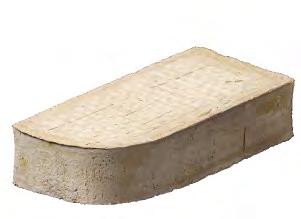

Photos: Anders Sune Berg
Draped in brick
An architect and a sculptor worked together to build this holiday home with undulating brick façades in earthy hues.
The overall idea was that the body of the building should form a softly rounded monolith that merges gently into the landscape. The roof has no gutters, so its curves are uninterrupted. The central concept is also reflecte in the big wall section, the rounded corners which extend around the two façades.
The rounded edges are formed by a number of customised bricks produced by Petersen Tegl, using the same clay as the standard ones used on the project. This gives the brickwork the appearance of plastic sheeting draped around the house. Also the chimney has round corners.
The wall section combines D48, D54 and D72 in a variety of different bonds, and each elevation has its own pattern. Close up, the bricks have an enchanting texture and rich colour. From a distance, what stands out are the refine patterns and the perforated, three-dimensional effect created by offsetting the bricks. They are offset in a consistent pattern – all of the grey bricks are flus with each other, while the red and yellow ones either protrude or are recessed by 16 mm.
About the holiday home in Tisvilde
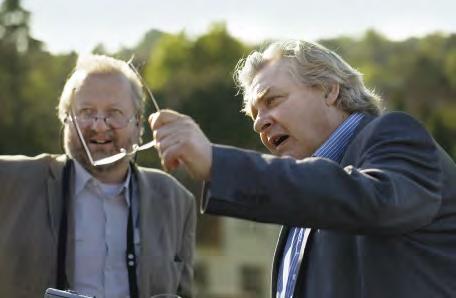
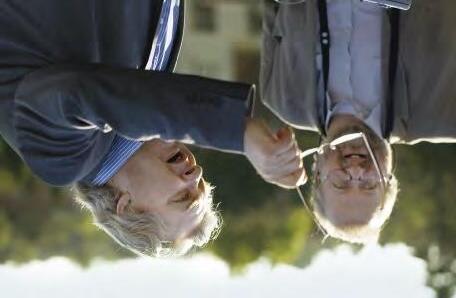

Art and architecture work best together when the borders between the two are fluid In the Tisvilde holiday home, jointly designed a few years ago by sculptor Bjørn Nørgaard and architect Tage Lyneborg, the two art forms achieve a complementary synthesis. The architecture has been artistically processed, while the ornamentation has architectural merit.
The home is on a north-facing hillside in the beautiful, protected Tisvilde countryside. It stands on a plateau that evens out the height difference across the site.
The house is anchored by its key feature – the large wall section that comprises the west façade. It encompasses the fieplace, chimney and west wall of the house but extends beyond the main structure and around the north-west corner to provide protection against wind, weather and prying eyes. The wall makes the house stand out as something unique in the landscape but also embeds it in its location through the use of natural materials – including handmade bricks – and harmonious, earthy colours.
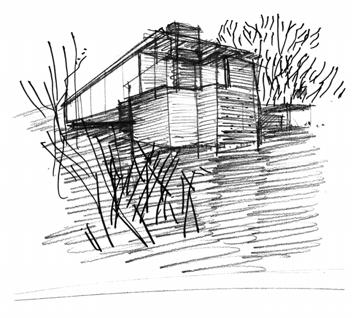
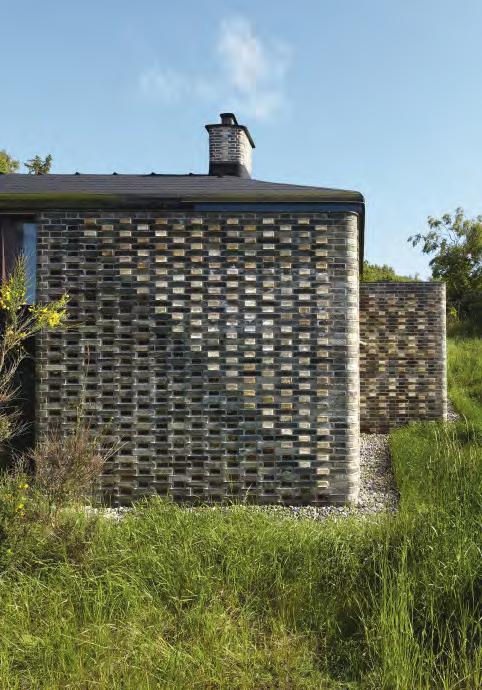
Private home, Prinsen Bolwerk, Haarlem, The Netherlands
Client: Private
Architect: MOPET Architecten
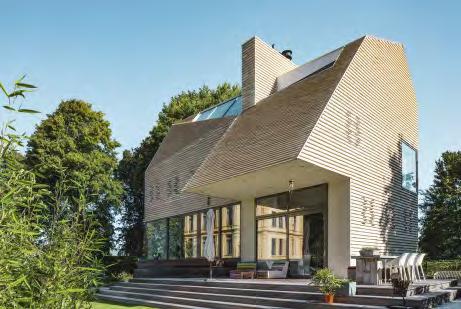
Completed: 2016
Brick: C71 + custom version of C71 with gaps
Photos: Paul Kozlowski
Decorative gaps

Perforated Cover protects privacy and creates a decorative pattern.

According to Joep Mollink from MOPET Architecten, Petersen Cover’s sculptural shape made an obvious choice for cladding the façade of this new home. Not only did it turn out to be a practical and technically straightforward solution for the wooden construction, C71 subtly complements the white and yellow shades of the older houses in the neighbourhood. The brick’s almost luminous surface is a result of the slurry used as a lubricant when the clay is removed from the mould. The same hues found in C71 were also used in the building’s concrete plinth.
A large, unconventionally shaped roof turns the first floor into wide-open and intriguing space. As the path through the park goes right past the house, Mollink opted to use custom Cover to screen off several rooms on both floors. Horizontal gaps in selected bricks form a decorative pattern and let light into the rooms while breaking up the line of sight.
About the private home in Prinsen Bolwerk
The new home designed by J.D. Zocher was built on a 500-m2 plot in De Bolwerken Park, where Haarlem’s defensive fortifictions once stood. Before World War II, a school – now demolished – was built on the site. To avoid damaging the remainder of the fortificaions below ground, the new home had to be built within the foundations of the old school, which are still there.
Several generations in Haarlem have fond memories of attending the school. Mollink’s desire to acknowledge the site’s history and keep the new construction within the old footprint resulted in an unconventional design idiom.
The neighbouring buildings consist of grand homes from the late 19th century, so the architects were keen that the new 350-m2 building should have a solid, monumental look.
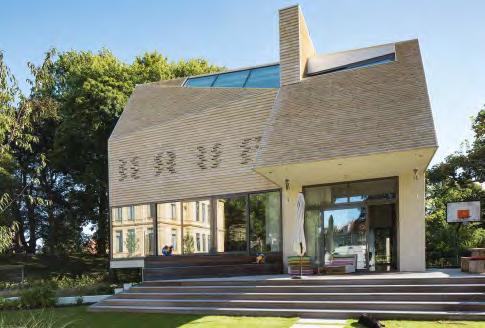
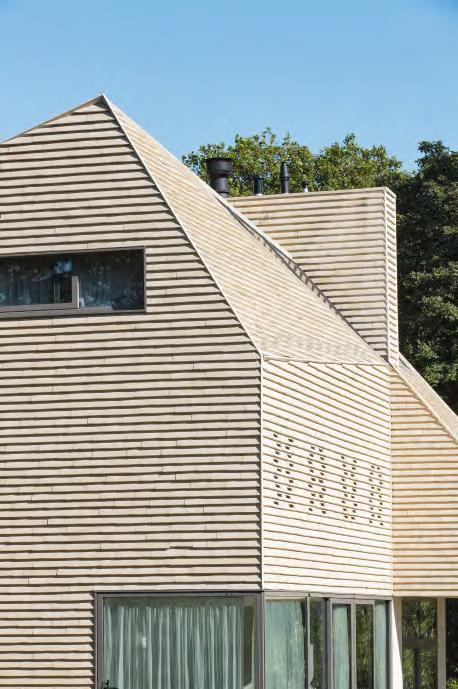
Houttuinen townhouse with two flats, Dordrecht, The Netherlands
Client: Private
Architect: Lugten Malschaert Architecten
Completed: 2017
Brick: K91 + K91 in custom format with a radius of 3,000 mm
Photos: Paul Kozlowski
Reviving forgotten history
A townhouse in Dordrecht features a custom-brick rotunda and echoes a nearby medieval fortificaion.
Architect Andries Lugten had long had a clear architectural vision for a site in Dordrecht’s historic harbour area. When the site was put up for sale in 2015, Lugten submitted his proposal to the council building committee, which approved the plan and published the details in the local newspaper. This attracted the interest of two clients, who have lived in the Houttuinen development’s two flat since its completion.
It was crucial for Lugten that the townhouse referenced and paid homage to Dordrecht’s past. The building includes a ro-
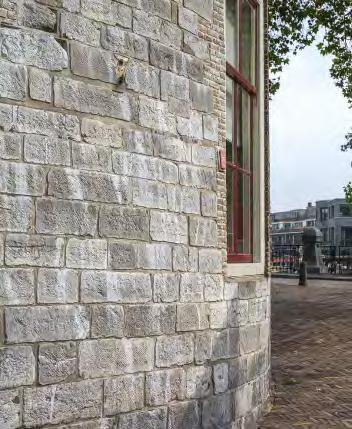
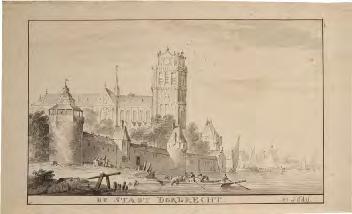
To establish a visual affinit with its medieval neighbour, Lugten opted to clad the façades of the new building in handmade Kolumba. The brick is made from a clay mixture that, after firing resembles the patinated sandstone and slate of the 600-year-old tower. Petersen Tegl also supplied custom bricks with a radius of 3,000 mm to give the tower a regular curved shape.
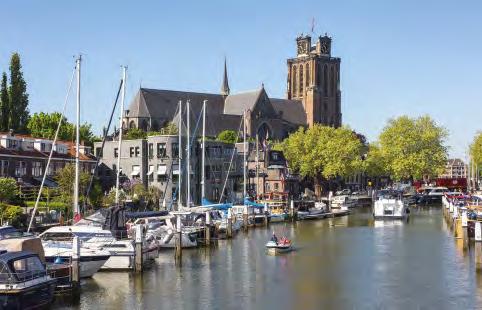
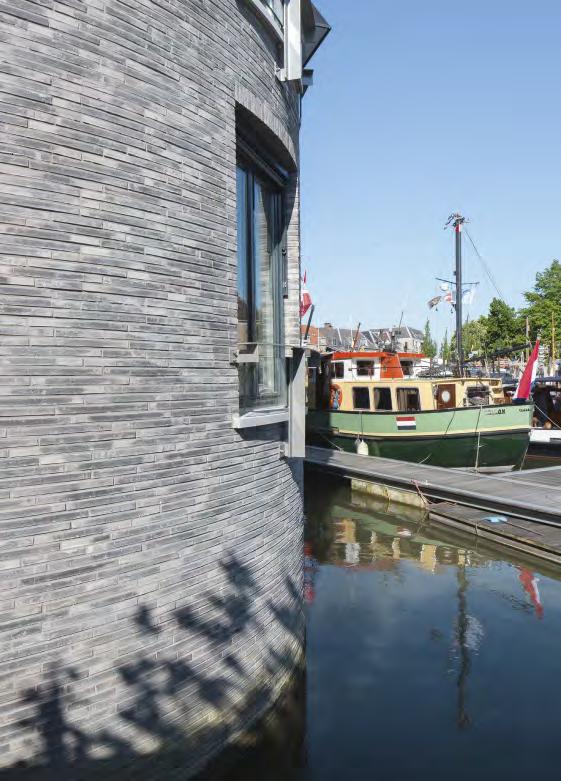
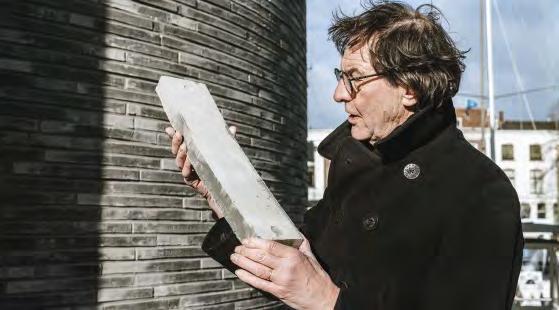
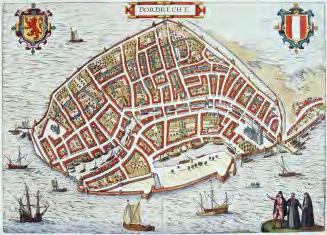
About Houttuinen townhouse
Throughout his career, the architect Andries Lugten has been passionate about the fascinating, historic city of Dordrecht and has played a part in several restoration projects to preserve its cultural heritage. He designed Houttuinen (The Lumber Yard) along with his partner Theo Malschaert, with whom he has shared a studio for almost 40 years.
Houttuinen is a three-storey, L-shaped building linked by the rotunda. One wing runs along the riverside, the other along an alley perpendicular to the waterfront. The entrance to the two flat is via the spacious foyer of a listed, single-storey factory building from 1840. At the ground-floo level, the building houses an office which is connected to the lower of the two flat and has parking space for six cars.
With a scale that matches its neighbours, its articulated shape that marks the three volumes – with the rotunda in the middle as a hinge, a simple façade and the subdued grey shades – the new building is a modern and positive addition to the city, not least because it recalls the site’s forgotten history without descending into pastiche.
Paper Island, housing project on Christiansholm, Copenhagen, Denmark
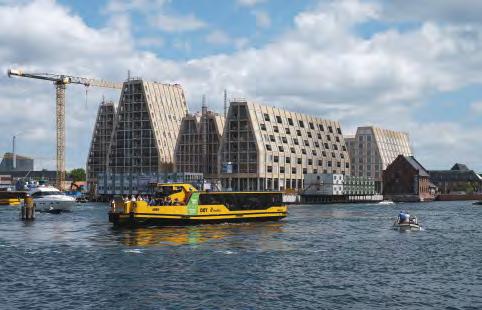
Client: Udviklingsselskabet Christiansholms Ø P/S, consisting of Danica Ejendomme, UNIONKUL and Nordkranen
Architect: COBE
Completion: 2023-2024
Brick: Custom format and colour, Danish clay developed in collaboration with COBE
Photos: Anders Sune Berg
New brick with a sense of history
Structure and textuality give new brick a look that harmonises with the surrounding centuries-old warehouses.
Early in the project, Dan Stubbergaard, architect and owner of Cobe, contacted Petersen Tegl to develop a custom brick for the residential project on Christiansholm. They wanted a brick that had an inherent patina and special textuality that would establish a kinship with the harbour’s old brick warehouses.
The new brick is made at the brickworks in Broager on machines designed to replicate centuries-old, handcrafted techniques.
“We named it the Christiansholm brick, and it has exactly the look we wanted,” says Stubbergaard. “The water-brushed brick is made from Danish blue clay and is coal-fied to achieve its totally unique play of colours. We designed the brick with a four-sided, obliquely chamfered recess, which drains rainwater no matter which way it faces. The recess gives the façades a relief effect that makes playful use of shadow.”
The brick is placed with the mortar side outward. Cobe used a technique developed at Petersen Tegl that adds an additional layer of whitish clay to the side of the brick, giving it a slightly lime-like look after firing The façades are prefabricated, with a light mortar that closely matches the golden hues in the 500,000 bricks used in the project.
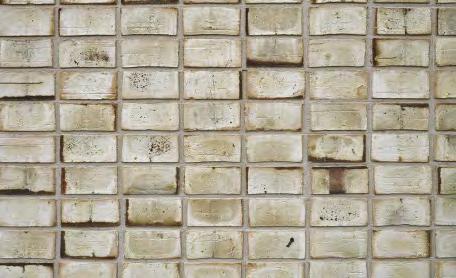
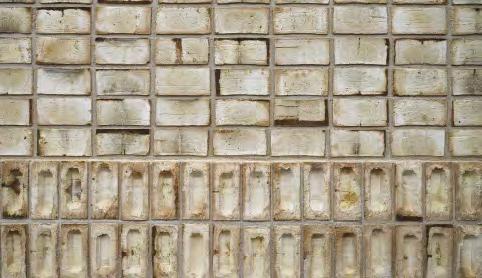
About Paper Island
For well over 300 years, the artificia island of Christiansholm in the Port of Copenhagen housed a number of important functions for the city, including a naval hospital, shipyard and storage facilities for cannons and coal. In recent times, most locals remember it best for storing materials for Danish newspaper production, which earned Christiansholm its current nickname: Paper Island. Right now, the island is undergoing a metamorphosis. Soon, it will be a new urban district that, in addition to housing, will be home to an aquatic centre, a hotel and a new food market which was the latest major activity on the island.
Cobe drew up the master plan for Christiansholm and is also the studio behind the new homes. In total, Paper Island will accommodate approximately 250 homes. It was a precondition that the residences would be highly diverse in terms of both type and size. One third will be affordable housing, the rest private. To promote a sense of community between the buildings, the ground floor have high-ceilinged halls that can accommodate various activities.
The design of the buildings takes inspiration from the old warehouses on Holmen and Christianshavn, as well as the former industrial buildings on Paper Island. They vary in height and create a varied skyline on the harbour front. The firs homes are expected to be ready in 2023, the last in 2024.
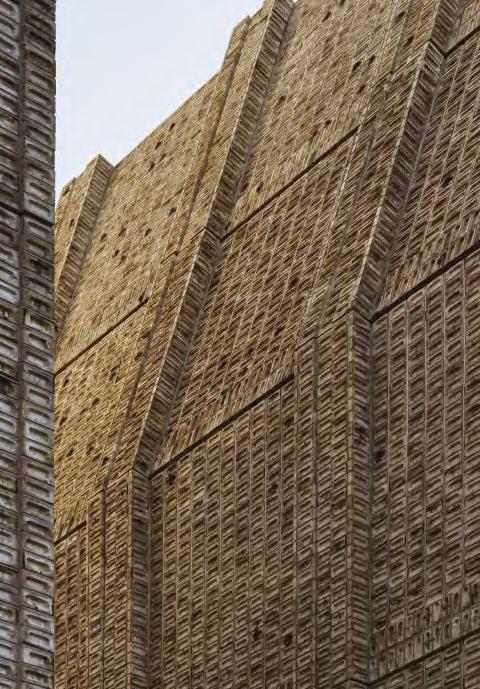
Residential block on Jagtvej 2/Ågade 110, Copenhagen, Denmark
Architect: O. Nærum
Built: Late 19th century
Restoration project: 2012
Client: Andelsboligforeningen A/B Åhjørnet
Architect: Michael K. Andersen
Engineer: A/S Ishøy & Madsen
Brick: 3,000 bricks in 36 different formats, the main part glazed
Photos: Anders Sune Berg
Recreating refinement
3,000 handmade, glazed, moulded bricks were produced for a 19th-century building in the heart of Copenhagen.
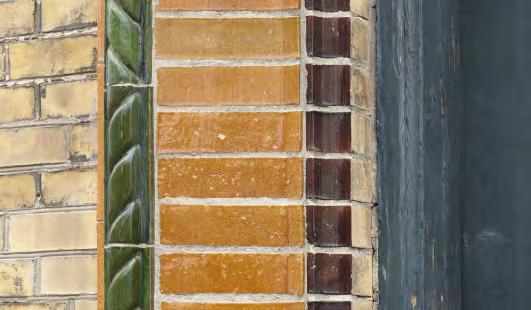
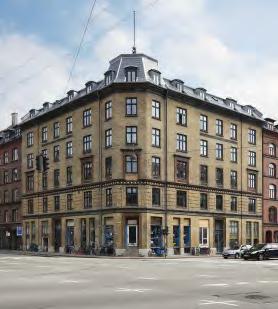
When Petersen Tegl was commissioned to recreate thousands of moulded bricks for a corner building in Nørrebro, the firs step was to make a comprehensive photographic record. Petersen supplied 3,000 bricks for the project, divided into 36 different types. A copy of each type had to be sent to the brickworks before work could commence.
“All of the bricks were hand-cut by knife, but fiv of the types were so complicated that the mould had to be cast in plaster and then imitated by hand. The bricks were glazed in fiv different colours, one green, one white, one a translucent, greenish colour and two different shades of brown. Copying the colours of an existing glaze is no mean feat. Even the most experienced brick-makers have to experiment extensively until they get it right,” explains Erich Mick, head of Petersen’s Custom Brick Department.
The experiments were a success, and it is virtually impossible to tell the difference between the new bricks and the original moulded ones from 1889.
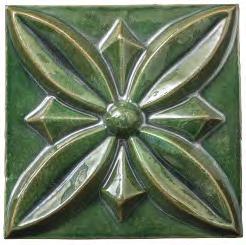
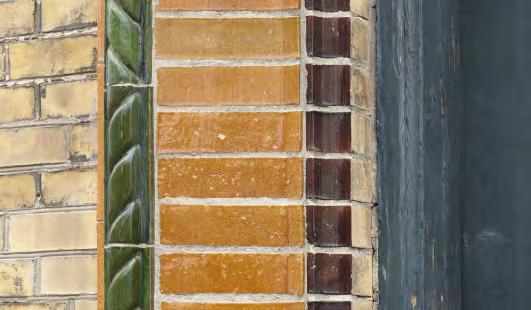
About Jagtvej 2/ Ågade 110
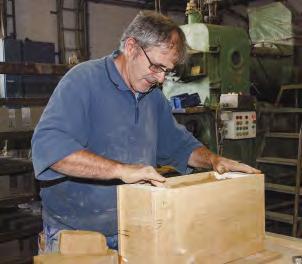


At the corner of Jagtvej and Ågade stands this five-stoey, yellow-brick apartment block of the type found throughout the densely populated inner-city areas in Copenhagen. However, this building is a little bit more sophisticated than most, with glazed bands of terracotta on the ground and firs floors The street doors and windows on the second floo are also framed in glazed, yellow and brown terracotta, and the cornice under the eaves and bands on the third floo also feature terracotta ornamentation.
About a decade ago, architect Michael K. Andersen and engineering company Ishøy & Madsen were commissioned to renovate the dilapidated block and restore its original look. The architects dealt with the descriptions and drawings while the engineers handled building management and supervision – and both contributed to the historical research. In addition to recreating the glazed moulded bricks, the project specificaions included new attics and windows, restoring the tower and spire and replacing the brickwork.


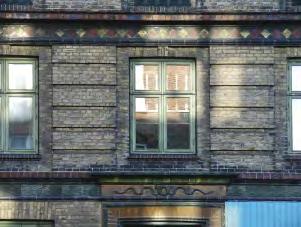
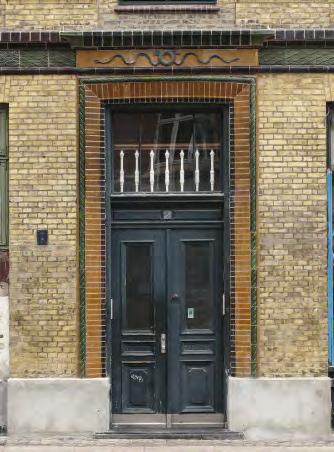
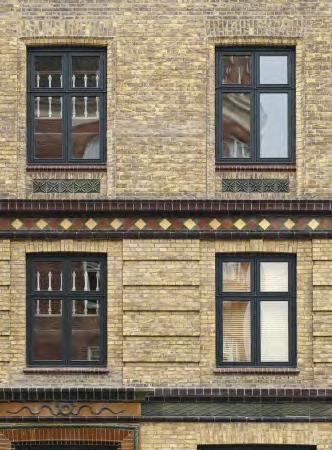