Experience the allure of Highland Park’s Second Phase with an enticing array of new shopping destinations.
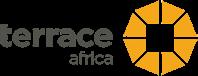

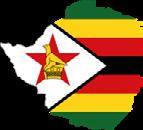

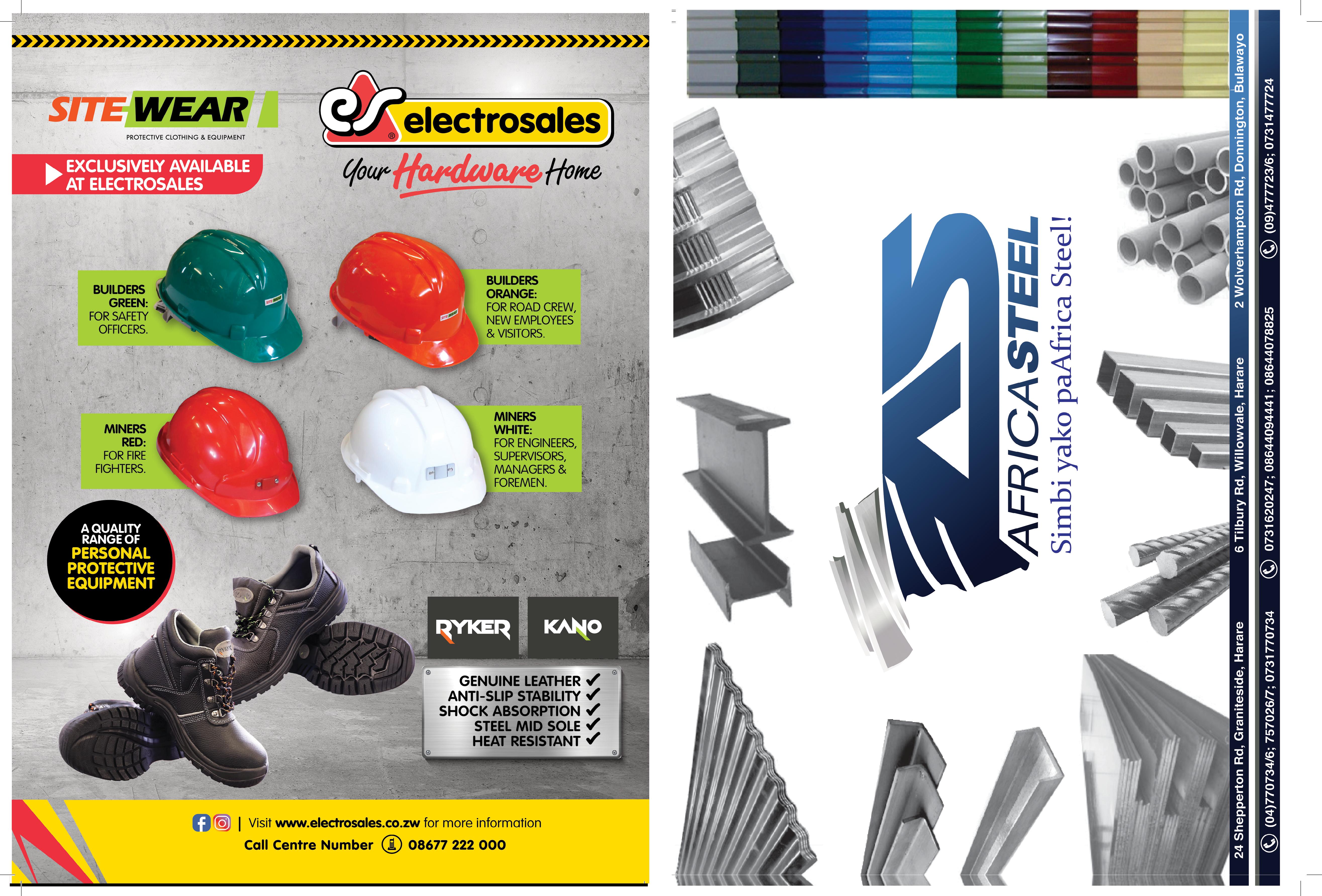
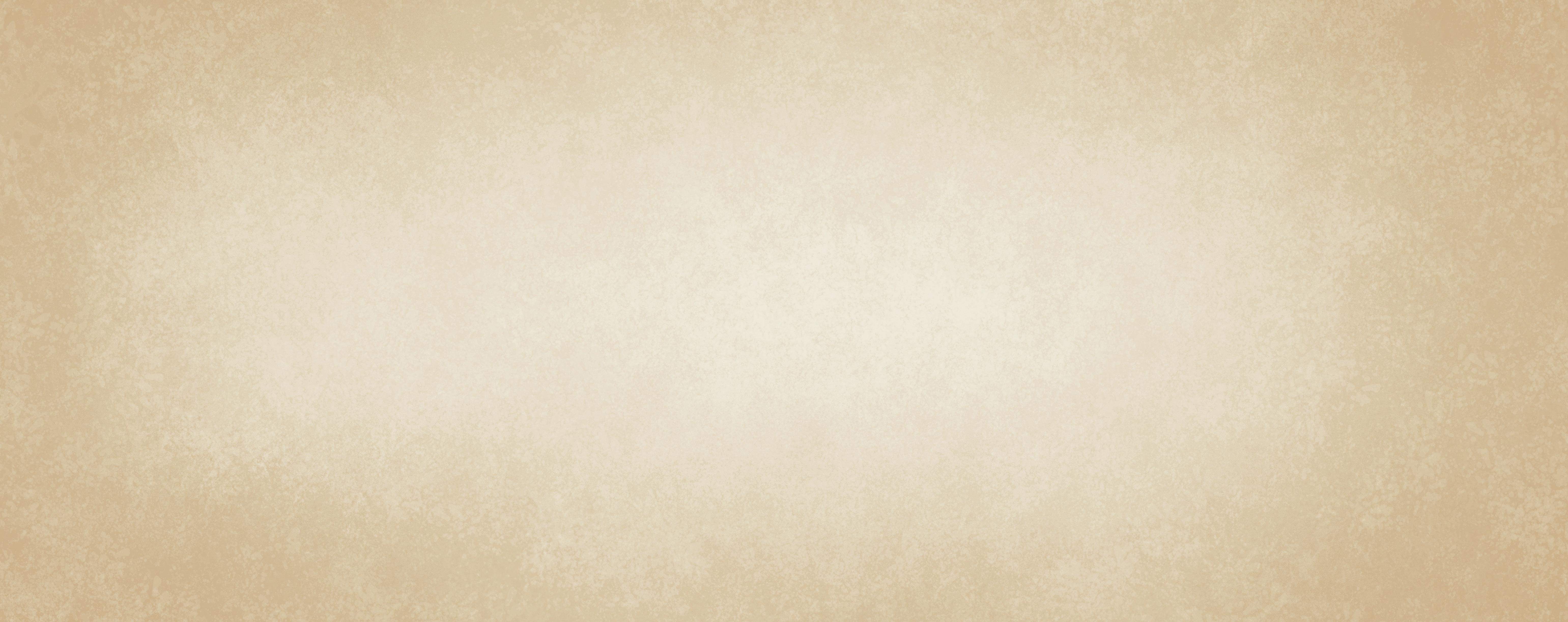

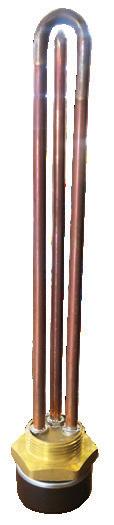
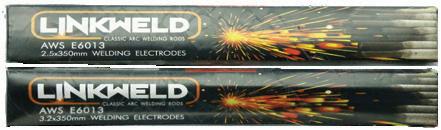
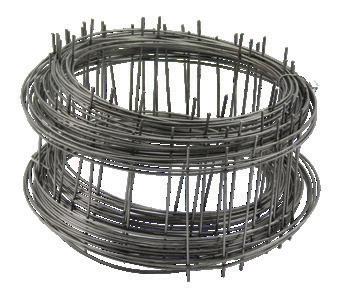
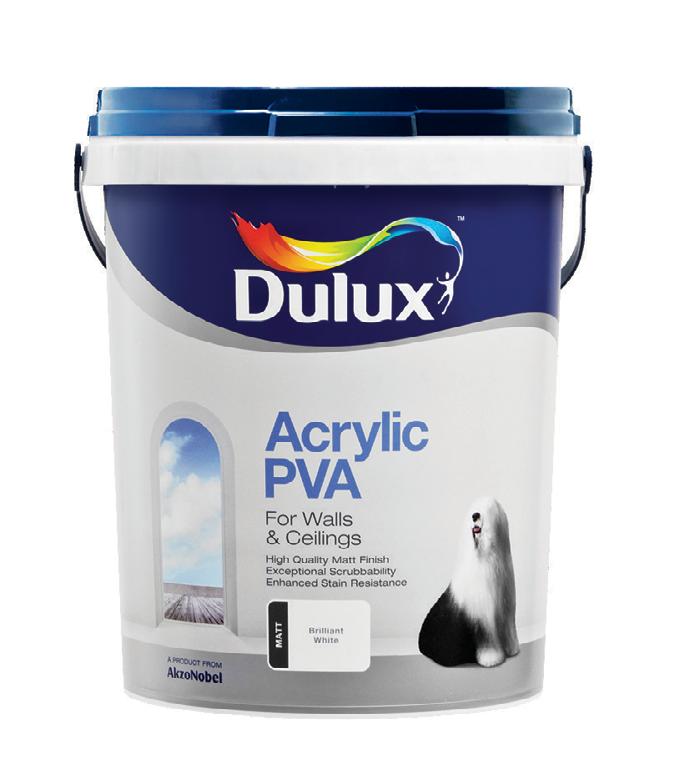


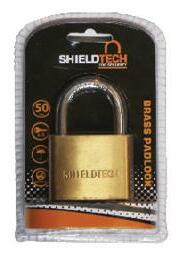
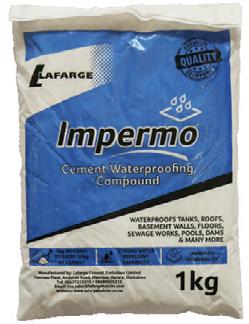
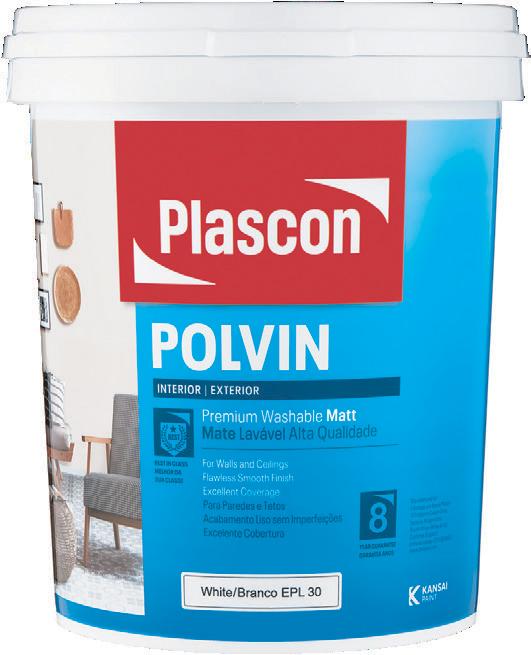
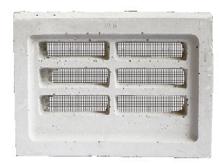

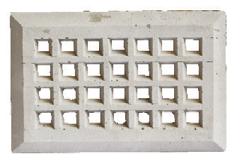

Experience the allure of Highland Park’s Second Phase with an enticing array of new shopping destinations.
Great vibrations for structural growth are always present in and around our stunning nation.
With the official launch of Phase 2, Highland Park has solidified its position as the jewel in Harare’s modern retail crown. Since its debut, Highlands—a neighbourhood primarily composed of single-family detached homes and Edwardian row houses—has seen even more transformation, growing in popularity as a posh and distinguished neighbourhood. Phase 2 contributes to the widely held belief that, even with a number of affluent neighbourhoods in Harare, Highlands is still maybe the wealthiest area!
Recently, The Steel Building Company (TSBC) expanded into residential steel-framed buildings. One of the newest projects for which they supplied the steel skeleton together with the wall and roof coating is the new Driptech branch in Belgravia. In addition to these many recent projects, they have worked with wellknown hardware stores, food processing industries, shopping centres, a motor service and parts centre, and grade-A tobacco warehouses.
Once again, Rulom Steel, a young and expanding business with a solid name in Zimbabwe’s and southern Africa’s built environment, has succeeded. At Poppa’s Mall, which is located in Borrowdale, immediately across from Trade Centre on the intersection of Hoggerty Hill and William Powllet Road, the entirely locally owned enterprise is currently finishing up massive steelworks.
In Zimbabwe’s cutthroat automotive engineering industry, Lotus Auto Tech, the expert car trade technicians, skilled engine rebuilders, and distributors of motor parts, have established unparalleled flexibility and dependability. With two locations in Masvingo and Harare, they have been a reliable source of topnotch services for more than thirty years.
Brown Engineering is proud to continue with their renowned steel structure solutions at two of their latest projects in the Borrowdale and Msasa areas. The steel fabrication company has established itself as an industry leader in the creation of superior steel structures. They have manufacturing and distribution centres in both Harare and Bulawayo and subsidiary concerns across the country.
Behemoth FMCG maker National Foods recently refurbished their old flour milling plant in Bulawayo as part of their continual growth plan. This is a huge investment for a large group whose origins date back to 1920 and who are just fresh from celebrating their centenary. The Zimbabwe Stock Exchange-registered company has, over the years, expanded exponentially.
We are confident that this cross-section of news will satisfy your appetite for the latest in local structural development!
Enjoy the read!
Structure and Design team.
follow us at SDMagzim
PUBLISHER
Caast Media Group
MARKETING
Ashley Bangamu
Newton Musara
+263 775 062 088
+263 08644 275 856
DESIGN & LAYOUT Masimba “Massiv” Gamira Tevin Tewo
WEBSITE & SOCIAL MEDIA
Nichodimus Anesu Ndagurwa
JOURNALISTS
Michael Nott
Martin Chemhere
DISTRIBUTION
Joshua Govati
PHOTOGRAPHY Fotohaus
CONTRIBUTORS
EMAIL marketing@structureanddesign. co.zw adverts.structureanddesign@gmail. com
www.structureanddesignzim.com
FIND US AT 31 Alexander Rd, Highlands, Harare
MAIN FEATURE
08 | Highland Park Phases 2 awaits you
TECHNICAL PROFILE
18 | The Steel Building Company-creating Driptech’s new premises in Belgravia
CIVIL WORKS PROFILE
24 | Another stunning steelwork project by Rulom Steel
AUTOMOTIVE PROFILE
30 | Lotus Auto Tech-the go to automotive engineers
SPACE OF THE MONTH
34 | Brown engineerings’-steel structure solutions
COMMERCIAL NEWS
While every effort has been made to ensure the accuracy of its content, neither editor nor publisher can be held responsible for any omissions or errors: or for any misfortune, injury, or damages which may arise there-from. All rights reserved. Copyright 2024
Structure and Design Magazine:
No Part of this magazine may be reproduced or transmitted in any form or by any means electric or mechanical, including photocopying or recording.
VISIT: structureanddesignzim.com and issuu.com/structuredesign for the digital editions of every issue
40 | National foods-Renovates and mordenises
These days, entering Highland Park Mall evokes a profound and tangible sense; the grand opening of Phase 2 has enhanced the mall’s status as Harare’s crown jewel of contemporary shopping.
Prime location:
Highlands, a community made up mostly of single-family detached homes and Edwardian row houses, is becoming an increasingly sought-after area of luxury and distinction. The elegant Highland Park Mall, which has expanded into Phase 2 and represents a first-class lifestyle, is proudly located in the area.
Despite the fact that Harare has a number of upscale districts, Highlands is still arguably the wealthiest. One gets the impression that Highlands is unlike any other area, whether it is because of its unique natural setting, breathtaking views of downtown Harare, or its more appealing and tranquil features that make it the perfect place to live. This location has been enhanced by Highland Park Phase 2, which has transformed dining and shopping there into an idyllic experience.
The Highlands suburb welcomed its most prestigious new development and the beautiful gentrification of the area with the inauguration of Highland Park Mall Phase 1 in June 2022. The area’s residential properties are being purchased and demolished more frequently to make room for prestigious
office complexes and apartments, giving the suburb’s constantly evolving skyline a vibrant new look.
Flagship stores:
Tenant occupation is happening quickly at the Highland Park Phase 2;
the majority of the stores have already opened for business. At the time of Structure & Design Magazine’s visit there (middle of February), a couple of shops had not yet opened but had posted “Opening Soon” signs.
The overall number of stores, eateries, and other enterprises in Phase 2 is about twenty-five new shops. Spur, Ocean Basket, and Roco Mamas are among the Simbisa businesses that have flagship stores at the complex. First Capital Bank, Booties Pharmacy, Liquor Supplies, Safari Trading Company, and others add
to a roster of tenants that will support Highlands and its surrounding areas. The tenants’ diverse range of sectors and offers is primarily made up of food outlets, followed by stores selling adult and child apparel, books, pharmacies, and banks.
“Highland Park Mall Phase 2 has been developed with contemporary amenities, with Spurs having a large play area for children, and then lots of coffee shops and food outlets, and a fountain area for playing,” said Mark Gardiner, Managing Director at African Horizon Construction, the building contractor for the project.
In addition, he mentioned that children can play on an artificial turf field with creatures resembling jungle gyms and climb on them. The majority of restaurants provide designated green spaces for outside sitting.
The building design:
Accessibility for individuals with impairments was given priority in the design, as is typical of the majority of contemporary structures in the country. At Phase 2, an elevator is being erected
to provide access to the first-floor stores and Buffalo Ridge Spur. In addition, there is a parking space designated for drivers with disabilities and accessible walkways for the convenience of those with impairments.
Large windows and storefronts demonstrate how the design uses ventilation and natural light to let light in overall. It’s a simple yet creative idea to use sunscreens installed for dual purposes—to hold advertising and protect the stores from the intense afternoon sun.
Materials used for the buildings:
Phase 2 incorporates a number of distinctive design features that stand out, such as a water fountain, an elevator on the outside of the building, and walkways constructed from imported Bosun pavers.
In contrast to imported materials, the developer, African Horizon Construction, has chosen to obtain the majority of steel, concrete, cement, bricks, aggregates, plumbing supplies, and other items locally. Materials such as electrical components, aluminium, and sheeting were imported.
The structures have recycled elements like sunblock integrated within them. Day or night switches on all external lighting systems and solar backup for certain stores are further sustainable features.
The building’s overall utility and beauty are enhanced by the materials that were selected. The design of the unique mall, which represented the mall’s great location and target demographic of Highlands suburb, made use of highquality materials.
Gardiner admitted that the selection of materials was indicative of broader patterns in Zimbabwean building, especially in upscale areas. “Modernising the designs is definitely in style because most Zimbabwean structures are over 20 years old and in need of renovation,” said Gardiner.
Landscaping:
Following the design guidelines of Phase 1, native plants were used, evaporationreducing landscaping was completed, and trees were preserved in original gardens. In this manner, the landscaping plan enhances the building’s usefulness and blends in with the overall architecture.
“The shopping complex and parking lot were planned around the existing trees from the original garden. Additionally, trees that impeded the construction were relocated to more advantageous locations so they could keep growing,” he said.
The upmarket area’s profile has further increased thanks to Highland Park Mall Phase 2, and as the mall develops into a new centre of affluent living, real estate values will rise. The community’s growing property prices and local rentals all make reference to the mall’s close proximity, one of the most significant and closely observed aspects of the real estate industry.
Main Contractor AFRICAN HORIZON CONSTRUCTION
Piling PILE AFRICA
Building Material Supplier NEVSEN LTD
Electrical Subcontractor L-ELECTRON
Reinforcement Steel RULOM INVESTMENTS
Aluminium & Glass ALUMIN STRUCTURES
Shopfitting GLOBAL SHOPFITTERS
Paving JTL
Cement PPC
Bricks TIGER BRICKS
Painters STAR PAINTERS
Plumbing LESOP PLUMBERS
Waterproofing AFRICAN HORIZON CONSTRUCTION
Steel Installation KINGSON INVESTMENTS
Sealants & Adhesives INTERNATION COATINGS COMPANY
Steel Sections KINGSON INVESTMENTS
Steel Frame Supplier KINGSON INVESTMENTS
Doors & Windows AFRICAN HORIZON CONSTRUCTION
Lighting L-ELECTRON
Concrete Premix SCRIBANTE LIMITED
Palisades POMONA FENCING
Air Con Systems THERMACOOL LTD
Roof Seets SUPERSTRUCTURES LIMITED
Staircases & Balustrades KINGSON INVESTMENTS
Wall & Floor Tiles AFRICAN HORIZON CONSTRUCTION
Agristructures and Superstructures are divisions of The Steel Building Company (TSBC). They have 40 years of experience in design, fabrication and installation of a variety of steel framed structures including warehouses and factories, shopping malls and residential projects. They have completed numerous projects across Zimbabwe as well as in Mozambique, Zambia and the DRC. As the name implies Agristructures tends to focus more on agricultural projects like storage sheds for farm equipment, workshops and poultry sheds, whereas Superstructures focuses more on commercial, industrial and mining projects. Recently TSBC has diversified into steel framed residential projects like the house featured in S&D issue 61. In issue 62 we featured the new Driptech branch in Belgravia
for which TSBC provided the steel skeleton as well as the roof and wall cladding. They have recently completed projects for prominent hardware outlets, food processing companies, shopping malls, a motor service and parts centre, as well as a grade-A tobacco warehouse. Current ongoing projects include a new 15 000sqm tobacco warehouse along Simon Mazorodze, a mixed property Masvingo Development and an upcoming retail centre in Borrowdale. Their work in conjunction with design and construction companies across the region has enabled them to gain valuable experience and keep abreast of current global building trends. TSBC has a very optimistic outlook for future developments in Zimbabwe and the region.
Their newly completed project for Driptech in Belgravia includes retail outlets and storage space for Driptech and their sister companies, One Stop Solar and TyreZim all conveniently incorporated into a single steel frame structure. The building has a Chromadek bull nosed roof and Chromadek wall cladding attached to the steel frame. TSBC also installed a mezzanine floor around three sides of the interior space – mostly for storage of the client’s extensive stock.
For the Belgravia project TSBC worked closely with the client’s architect and the civils contractor. The architects provided conceptual architectural drawings which TSBC then processed using their Tekla BIM (Building Information Modelling)
programme. The programme helps provide construction detailing and quality control as well as providing 3D models for clients to look at before manufacturing commences. The programme divides the structure into convenient sections which, together with the architect, can be rationalised to suit and if needed adapt the concept. TSBC is flexible and adaptable to work with different section layouts, particularly when designing and building residential projects.
The Belgravia project is 36m long by 40m wide and 5.5m high at the lowest eaves. The mezzanine floor extends around three sides of the internal space like a gallery with open space in the centre.
It was designed and erected in different load bearing capacities – heavy duty for storing tyres for TyreZim, medium duty for storing solar panels for One Stop Solar and light duty for lightweight, bulky goods. The mezzanine is a steel skeleton with steel decking panels fixed on top and finished with 19mm shutter ply board.
They co-ordinated closely with the building contractor to specify where the concrete bases should be positioned to support the steel columns – both around the perimeter and internally, so that the prefabricated sections could be properly and easily installed. They worked c with the civil contractor so that as each individual Chromadek roof section was completed, the work on the floor progressed accordingly in a systematic and synchronised manner in a waterproof and sheltered environment.
As usual, much of the framework for Belgravia was premanufactured at their workshop in Willowvale. TSBC has a 6,600sqm factory serviced by overhead cranes, forklifts and
with a substantial backup generator for ZESA power cuts. The workshop can produce around 400 tonnes of structural steel and roofing, each month to meet project demands. They have the cutting, rolling, welding and jig equipment to manufacture fabricated I-beams, castellated beams, heavy rolled plate structural tubes, conventional angle iron lattice trusses and portal I-Beam structures.
TSBC has an impressive fleet of crane trucks and site equipment to transport and install fabricated steel components and roofing. Materials were transported to the Belgravia site in one of their 30 tonne tri-axle flatbed crane trucks. Site equipment included one of their three telehandlers with a 4.5 tonne capacity, 17m reach. Steel components delivered to site are handled with care, offloaded, and safely and neatly stacked onto dunnage in designated zones. Wherever possible, the steel work for each structural area of the building is to be stored in one location and is laid out for ease of erection.
TSBC rolls their own roof sheets at their factory into IBR profile, wide-span profile, or Seamlok 745 concealed fix roofing system.
The sheeting for Driptech Aberdeen was processed at their factory using 0.58 mm Dark Dolphin Chromadek. The coil was purchased by TSBC in 4/5 tonne rolls and processed into an IBR profile. The bull nosed profile on the roof (manufactured at their workshop) meant there was no requirement for rain water gutters – another time and cost saving design feature. TSBC installed Alububble insulation below the roof for thermal insulation to keep the place cooler in summer and warmer in winter.
Since most of the framework was pre-fabricated only a small crew was needed to complete the construction on site for
such a large project. Excluding site supervisors and related engineering experts there were six members of the steel installation team and 10 members of the roofing and cladding team.
TSBC is passionate about creating well engineered and durable structures to support the economy and the lifestyle of people in Zimbabwe and across the region.
Rulom Steel, a young and growing company with an established reputation in the built environment of Zimbabwe and southern Africa has done it again.
The wholly locally-owned company is currently completing major steelworks at Poppa’s Mall, at the corner of Hoggerty Hill and William Powllet Road, (directly opposite Trade Centre), in Borrowdale.
The steelworks occupy over 1000 square metres and as to date, over 100 tons of steel had been recorded. A lot of steel had to be shaped and cut according to the requirements of engineers. The work-in-progress would still require more steelworks till the project completion.
Most of the challenges encountered during the steelworks were naturerelated, specifically due to the current rains. Other than that, there wasn’t any specific challenge in terms of steel supplies.
Rulom Steel management believes the future trends in reinforcement steel fixing will change, positively impacting their work. Currently, the steel demand is increasing due to the rapid pace of new and upmarket building projects around the country, especially in Harare.
“We have lots of high-profile structural developments in the pipeline. The cluster home trend has caught up with developers in Zimbabwe, in addition to the new towns like the proposed Manhize Town in the Midlands Province and more shows how demand for steel can potentially go up,” they said.
“Poppa’s Mall is one of our major projects to date. We are happy with the swift progress made so far. The target was to finish the project on time and I am glad we were on time,” said Yonita Venn, marketing manager of Rulom Steel.
Work on the project commenced in April 2023 and they hoped to have wrapped up by the end of February this year.
The reinforcement steel fixing on the Poppa’s Mall project perfectly impacted the structural integrity of the building. Steel fixing gave the building stability and resilience. Proper fixing ensured efficient load transfer through the reinforcement cage, ultimately contributing to the building’s ability to withstand various stresses.
All this is happening when Rulom Steel has completed various projects, notably the Highland Park Mall in Highlands among others. Now they are completing yet another exciting project, Poppa’s Mall.
Rulom Steel believes that the future is bright for steel fixing and there will be more work even though it will also then create more competition because everyone would want to tap into the industry.
Founded in early 2016 and officially registered in October 2017, Rulom Steel is committed to building the trust and loyalty of customers.
If you are looking for a reliable supplier of a wide range of reliable steel products in Zimbabwe and the SADC region, Rulom Steel is a great option.
Lotus Auto Tech is the specialist auto trade technicians, professional engine re-builders and motor parts distributors in Zimbabwe. They have built unmatched flexibility and reliability in Zimbabwe’s competitive automotive engineering sector and are unlikely to relinquish that market position any sooner!
Situated at number 22 Kaguvi Street, in Harare and at number 694 industrial road Masvingo, they have always been a trusted provider of high-quality services. On offer are services such as cylinder head reconditioning, block re-sleeving, crankshaft
grinding, line boring, conrod standardizing, cylinder head pressure testing and skimming. With over three decades of excellence in the automotive industry, Lotus Auto Tech has earned an enviable position comparable to none other in Zimbabwe.
They believe in competitive pricing in accordance to the dynamics of the marketing environment. This is backed by advanced machinery and highly skilled manpower. Lotus Auto Tech’s motto is anchored on quick turnaround as well as providing quality services to its customers always. Goodwill is enhanced through offering free technical support to all its customers.
“We always strive to exceed our customers’ expectations through offering unique services such as cylinder head hot pressure testing, unlike any other company. We offer a one-stop shop facility under one roof to our customers’ convenience.
We also collect and deliver jobs timeously. In meeting quality standards we have acquired an advanced washing machine to clean our customers’ products,” commented Hamilton Chingwanga, Lotus Auto Tech Marketing Manager.
Vast experience and expertise have enabled specialization in all types of engines, both new and old models, unlike any other competitor in Zimbabwe.
Thorough performance modifications are carried out to engines to enhance power and efficiency such as block re-boring to the next size to use oversized pistons
(rebore to 0.20 thousandths, 0.30 thousandths, 0.40 thousandths). Servicing of all types of engine components is done but not limited to locomotives, boats, forklifts, mining equipment and agricultural equipment.
To ensure quality and longevity in all engine rebuilds, they employ routine quality checks in all sections before
all the engine components are dispatched. Quality controllers man all checkpoints and are conversant with their line of operations. A dedicated and experienced workshop manager has the mandate of doing final quality checks and inspections before the engine and engine components are dispatched.
After sales services are always carried out through field officers to hear customer feedback about the performance of the serviced engines.
With their meticulous approach to engine rebuild jobs, their reputation is rising and is the cornerstone of their retention of most of
their large and growing client base. World-class standard procedures in an automotive machine shop specialising in reconditioning and servicing engine parts are essential in ensuring quality workmanship, efficiency and customer satisfaction. The robust engine rebuilding process begins by initial inspection. All engine parts
brought in for reconditioning must be inspected thoroughly to check for any damages, wear and tear, cracks or other defects that may affect performance.
The initial condition of each part is then documented. Then carefully disassemble the engine parts following the manufacturer’s guidelines
and using appropriate tools. Taking note of the order of components and their positions to ensure correct reassemble later.
All engine parts must be thoroughly cleaned using specialised equipment and automotive approved cleaning agents.
Remove any dirt, grease, rust or other contaminants that can impact the reconditioning process.
Magnaflax or ultrasonic testing must be conducted in order to detect any crack or defects that might not be visible to the naked eye. Then identify any potential areas of concern.
State-of-the-art precision machining tools are utilized to recondition the engine parts based on their requirements. Cylinder heads may require valve seat and guide replacement, resurfacing of mating surfaces or injector hole modification. Cylinder blocks may need boring, honing or line boring. Crankshafts could require grinding, polishing, crack test or balancing.
Quality control measures must be conducted through out the entire reconditioning process. Inspect each machined part for dimensional accuracy, surface finish and proper tolerances. Calibrated measuring instruments are used to ensure compliance with specifications.
Final inspection must be conducted to verify that all engine components
are correctly assembled, machined and meet the required specifications. Any discrepancies or issues are then immediately attended to.
Testing of the reconditioned components is mandatory in order to verify their functionality, endurance and performance to ensure that they meet or exceed industrial standards.
All engine parts must be thoroughly cleaned and packaged properly before delivery. This is done to avoid any damage during transportation. Labelling of all engine parts must be done properly as well. Adhering to strict packaging and handling guidelines to maintain the quality of the reconditioned components.
Comprehensive documentation and customer feedback must be conducted throughout the entire process, sometimes including before and after photos, measurements, test results and customer specific requirements. Seeking customer feedback throughout the process, so as to continuously improve quality and services.
Any automotive machine shop specialising in reconditioning and servicing engine parts can consistently deliver high quality precision engineered components that meet the demands of both individual customers and industry standards if it employs these world class standards procedures.
Core values and principles guide them in ensuring customer satisfaction through feedback. They operate with a zero-tolerance attitude to jobs that are returned due to client dissatisfaction. This is achieved through employing a stringent quality culture.
“Our vision is centred on thriving to be the best automotive engineering
company in Zimbabwe and wherever they are called for work in Africa. We want to be the centre of new inventions in automotive technology. We achieve this through acquiring advanced machines,” said the marketing manager.
Lotus Auto Tech’s advice to all aspiring automotive technicians or entrepreneurs is to “Be constantly in touch
The company boasts a team of certified automotive technicians who assist in augmenting the firm’s expertise and experience base. Furthermore, they are proud of their research and development since there are constant changes in the world of technology. The company also invests regularly in training.
with the current and dynamic automotive technology for you to be marketable and survive growing competition in this industry. This is done through employing or acquiring new technology and machines.”
Physical Address:
22 Kaguvi Street
Harare
Land: (0242) 750 959 / 770332
Cell: 0772 948 091
(Operations)
Cell: 0772 710 248
(Workshop)
Cell: 0788778211 and 0776
910 096 (Sales Reps)
Brown Engineering, a proudly Zimbabwean company, has established itself as an industry leader in the creation of superior steel structures.Brown Engineering creates diverse structures, including showrooms and offices. Recent projects include a modern car dealership and offices in Borrowdale for one client and a project in Msasa for Paramount Garments.
Showroom and Offices - Borrowdale:
Brown Engineering’s showroom demonstrates the key benefits of steel structures. Steel’s natural robustness means vast clear-span spaces can be created, and without obtrusive columns, the showroom features large areas ideal for vehicle displays.With clear visibility and without conspicuous and space-demanding columns, the showroom floor feels more expansive,
open and welcoming to customers. The steel structure, which also houses contemporary modern offices, has allowed for greater design flexibility and versatility. Open floor layouts allow for simple installation and have impeccable steel framing.
Also, steel projects are noted for their shorter construction timetables, ensuring the client can occupy their new premises more swiftly.
Garment factory - Msasa:
Brown Engineering’s expertise in steel structure construction has provided the perfect solution for Paramount Garments, a leading garment manufacturer in Zimbabwe. Brown Engineering structures offer several advantages - such as durability and strength, flexibility and expansion, and cost-effectiveness.
Brown Engineering’s collaboration with Paramount Garments goes beyond the steel. Their team worked closely with the client to understand their specific needs, production flow, weight requirements for machinery, and future expansion plans. Working to meet the needs of the client ensures the structure is not only strong but also optimizes Paramount’s production processes, contributing directly to their success.By choosing Brown Engineering’s steel structures, Paramount Garments gained a robust, adaptable, and cost-effective building solution.
This strong foundation allows them to focus on what they do best – creating high-quality garments – while Brown Engineering’s commitment to excellence, precision and using their wealth of experience ensures that their success is built to last.
Showroom and Offices - BorrowdaleSteel structure advantages:
Although strength and flexibility are vital attributes, Brown Engineering’s steel structures are superior in other ways. Steel is a sustainable building material and has high thermal insulation properties, reducing energy costs associated with climate control.
Steel is entirely recyclable; thus, it has no adverse effects on the environment and requires less maintenance and repairs. Due to its longevity and resilience, steel structures represent a prudent choice for businesses seeking modern, long-lasting structures.
Steel Structures allow for large, airy atriums and innovative architectural features. Steel structures are durable and able to withstand strong winds.
Brown Engineering’s reputation: Brown Engineering prioritises local expertise.Their highly skilled work force guarantees excellent manufacturing and construction, bolstering Zimbabwe’s economic progress.
Brown Engineering offer complete engineering and design services, working together with clients and architects to bring their ideas to life.The belief in using steel in construction by Brown Engineering has had a significant impact on the corporate and industrial landscape of Zimbabwe.From imposing warehouses to cutting-edge retail structures, Brown Engineering’s innovative methods and core principles of excellence and precision offer a vision of the strength, efficiency, and sustainability of buildings in the future.
Chances are that as you read this you’ve already enjoyed a number of National Foods products today. National Foods manufactures, packages and distributes a broad range of basic foods including breakfast cereals, maize meal, flour (in your morning toast), rice, salt, biscuits, pasta, popcorn and a range of snacks.
Red Seal, Gloria, Mahatma and Pearlenta are just a few of their most well-known brands which can be found in almost every household across the country. They are the leading suppliers of Fast Moving Consumer Goods (FMCG) as well as a full range of stock feeds.
They have manufacturing and distribution centres in both Harare and Bulawayo and subsidiary concerns across the country. Their current headquarters are situated at 10 Stirling Road in Workington, Harare, which include their executive and administrative offices, logistics, milling and processing units, and their bakery research and development laboratory.
National Foods has its origins back in 1920 so they recently celebrated their centenary. Over the years the company has expanded exponentially and is registered on the Zimbabwe Stock Exchange. As part of their continual growth plan they have recently
refurbished their old flour milling plant in Bulawayo. Phase two of their cereal line is complete and National Foods is due to commission new pasta and biscuit manufacturing plants in Harare in early 2024. They are constantly upgrading and modernising their facilities – we reported on the renovations to their laboratory and bakery done by Howes and Homes in 2018. In 2019 Howes and Homes went on to renovate the second floor of the office block including all the offices and the upstairs reception area, the boardrooms and meeting rooms, as well as the boardroom kitchen and the executive ablutions.
Late last year they embarked on building a new entrance and security office. The existing entrance and security set up, including the roof, were demolished and the reception and ground floor were renovated. The ground floor includes a meeting room, ablutions and a kitchenette – again the revamp was undertaken by Liz Howes from Howes and Homes. It not only
improves their corporate image it helps to create a better working environment for the staff. The original décor had become a little dated and tired but it now has a fresh new look throughout.At the entrance a new wall was built up on the right hand side to match the height of the existing walls. It looks neater and more modern. A gentle ramp was installed on one side (with a railing supplied by Inner Living) with steps on the other side. New double doors were fitted at the entrance with a new portico roof. Newer more contemporary signage was supplied and installed by Compusign.
The security area has been revamped with floor tiles from Earthen Fire and a new window to the reception area was installed. The existing internal signage was removed and the walls given a fresh coat of paint. A new cashier’s booth was built next to the security check in. The reception area has floor tiles in black, grey and white in a classical geometric design. One wall has been wallpapered in a Hertex wallpaper – selected and installed by Ivory Palm Interiors and supplied by the Fabric Studio.New ceilings and bulkheads were installed with down lighters.
Next to the reception is a large solid fixed window pane looking out to the busy yard and reminding visitors of the industrial nature of the space.The reception leads to the large open plan sales and marketing office. New pale floor tiles have been installed here and throughout the rest of the smaller offices and most of the rest of the ground floor.
Floor plug sockets were installed so there’s no need for messy and awkward cables and each workstation has access to power. The concrete ceiling has been painted a dark charcoal grey while the supporting bulkhead beams are white.
The slightly dated large format printed banners were taken off and the walls painted giving a more contemporary look and feel to the space. One wall has been painted a sage green which matches the new office chairs. Vertical blinds were fitted by Ashleigh Smith Interiors.
From the open plan sales office, a wide passage leads to offices and a meeting room on one side and ablutions and a kitchenette on the other side. The offices and the meeting room have windows out to the yard in front on one side and glass partitions to the passageway on the other side.The partition walls have frosted National Foods logos supplied by Signs of the Times. The meeting room/boardroom has similar wallpaper to the reception area – the same pattern but in a slightly different shade. Modern square LED panel lights were installed in the acoustic ceiling.
Both the men’s and the ladies’ ablutions were completely gutted and new wall and floor tiles (from Earthen Fire) were installed as well as new sanitary ware and basins on granite counters. The ladies’ ablution area was reconfigured to create a small entrance foyer providing more privacy.
In the kitchen the entrance doors were replaced and cabinet doors were repaired or replaced as needed.
New handles were fitted and an aluminium kick plate was installed around the base of the units for easy cleaning. New wall tiles were fitted to refresh and brighten up the area.Throughout the ground floor the electrics were tidied up and new DB boards fitted as needed necessary.
All the walls and ceilings were painted and new tiles with tiled skirting fitted. Some of the old fluorescent lights were replaced with downlighters or LED panels fitted into the acoustic ceilings.
In addition, the stairs leading to the first floor were refurbished with full body tiles
which are very hard wearing and aluminium edge trim was installed to prevent chips.
Howes and Homes has total totally revamped and modernised the whole ground floor to make it more attractive and functional – all done with in a time frame of four months.