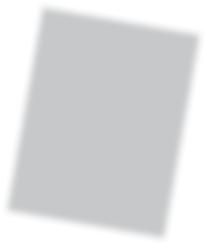
15 minute read
Professional Issues
Deferred Submittals
Part 2: When is Final…Final?
By Dean D. Brown, S.E.
In Part 1 of this series, the importance of proper routing review of a deferred submittal was highlighted. Pre-engineered wood trusses were used as a case study and, while this topic is obviously an issue directly affecting the Engineer of Record (EOR), it impacts the Building Official and their ability to properly enforce the building code. We, as building designers, typically assume building officials properly understand their respective responsibilities and that their adopted policies are compatible with the engineered system. That is not always the case and this issue has puzzled the author for many years as he has dealt with a multitude of Building Officials. As a rule, we make explicit statements, sometimes in the general notes or on the building detail sheets that deferred submittals are to be reviewed by the EOR before construction proceeds. In spite of these instructions, often times the designer is not afforded an opportunity to review Truss Design Drawings and is forced to adjust assumptions made during the initial design. One can suppose contractors get busy and forget to follow protocols. One can also suppose many Building Officials think an EOR’s involvement in the design ends once the stamped set of construction documents has been submitted for permit. This can be a difficult issue to enforce, as most designers have no direct contractual link to the contractor or the truss designer. To satisfy his own curiosity, the author conducted a brief simple written survey of five questions with chief Building Officials across a relatively small state (which shall remain anonymous and to which will be referred to as the “Survey State”). The survey considered all of the main city and county jurisdictions, and the state was one in which the author was not licensed. Also, pre-engineered wood trusses are commonly used throughout the Survey State and would be an engineered system with which Building Officials had experience. The main goal of the survey was to determine any common state-wide consensus (call it “standard-of-care”) on review procedures among Building Officials. Below, the responses are summarized along with the author’s commentary.
Question 1: Are Deferred Submittals required to be listed on contract documents and/or on the permit application?
Responses to Question 1 • “Yes, Deferred Submissions are to be listed on the contract documents and the building permit.” • “Typically our city does not allow
Deferred Submittals. Deferred
Submittals are to be provided at the time of building permit application.” • “Deferred Submittals are not allowed.” Commentary – if deferred submittals are not allowed, are pre-engineered wood trusses not being used? This engineered system is commonly used on residential and commercial projects. How can deferred submittals be completed “at the time of building permit application?”
Question 2: Does the (EOR), when stamping plans, typically provide any notation adjacent to the stamp that the design is ‘Preliminary’ (or comparable notation) indicating that the design needs to be later checked by the EOR?
Responses to Question 2 • “When the building permit is issued, all plan documents must be construction ready.” • “No…no notation is provided indicating that the information is
‘Preliminary’. Any revisions to plans would require resubmittal of changes.” • “Yes, a note is provided that submittal design is for ‘Design Purpose Only’.” Commentary – “Construction ready” implies that the design is final. For “Design Purpose Only’ infers that the submitted design is an interim design.
Question 3: Are Final Deferred Submittals provided at the time of building permit application?
Responses to Question 3 • “Deferred Submittals are not allowed.” • “Submittals are to be provided at the time of building permit application.” • “A preliminary deferred submittal is to be submitted upon a building permit application. Many manufacturers will not provide P.E. stamp on the Deferred Submittal design until the PRODUCT has been paid for.” • “No, the Deferred Submittal documents are provided at the time of inspection.” • “Deferred Submittals are never submitted upon building permit application. They are listed as a Deferred Submittal. Framing inspections are not provided until all the Deferred Submittal documents are received, reviewed, and approved.” • “Proposed Deferred Submittal packages are required to be submitted for plan review, to verify loads are being addressed. Inspections of the structure are made from stamped Deferred Submittal
Package. There are occasional deviations from the ‘Preliminary’ vs. ‘Final’.” Commentary – Regarding the 3rd bullet point, trusses are often purchased after the building permit has been issued and are not finalized until a purchase order has been received from the contractor. Anything submitted prior to this time would be considered ‘preliminary’ or ‘proposed’. The last bullet point does verify that there can be “deviations” between that of the original design to the final design.
Question 4: How does the EOR provide indication that they have provided (independent) Responsible Charge review of the Deferred Submittal documents?
Responses to Question 4 • “EOR typically provide generic details not stamped except for larger commercial projects, bracing and erection details are stamped.” • “EOR are responsible to provide correct details upon submission for building permit application and will often use Truss Plate Institute truss industry bracing details.” • “The building department does not require independent analysis of Deferred Submittal design (i.e., permanent bracing), but the EOR is asked to make Responsible Charge review where requirements are above the building code minimums.” • “The city generally has the structural inspector briefly review the truss engineering and then the inspector compares it to the structural engineer’s stamped drawings. In cases where the
truss engineering doesn’t appear to be compatible or if something doesn’t seem correct, the inspector would notify the plan reviewer and the design professional in responsible charge would be contacted.” Commentary – The building official in the last comment implies that the EOR’s review role is completed upon building permit application. In other words, it’s up to the building official’s discretion to decide when to involve the EOR, contrary to IBC 107.3.4.2.
Question 5: For projects containing Deferred Submittal submission, does the EOR typically make amendment (or changes) once they have reviewed the Truss Submittal Package?
Responses to Question 5 • “No.” • “There are a few instances where the
EOR makes changes to the original building design (when using a preliminary truss design). The EOR does review changes to the design before submittal to building official.” • “The EOR is required to re-review the original design with respect to load bearing. Issues identified during field inspection are brought to the attention of the registered design professional.” Commentary – How is it that in some jurisdictions there are no revisions to the Structural Design Drawings and then in others, there are? Disparities in these responses were alarming, given that these individuals are tasked with enforcing the building code. A Building Official’s simple directive is to enforce the code, provide interpretations as to the intent of code, and to adopt policies as to the code’s application. They are not authorized to override the design intent as rendered by the EOR. (2009 IBC, Section 104.1) For one city surveyed (4th question, last bullet point), the author subsequently informed the building department of their deficient practice and was initially met with push-back (i.e., no agreement with the conclusions). The mayor was then contacted to apprise him of the situation and he responded with, “Based on a review of the City…adopted building code and our current practices, we have asked all of our building plan reviewers and inspectors to now require that a letter be stamped by the engineer in responsible charge indicating that the deferred submittals from truss manufacturers and others are in general conformance to the design of the building before any Certificate of Occupancy is issued.” It is obvious that there is no state-wide consensus among Building Officials regarding the use and review of deferred submittals. Most of these submittals have a direct impact on the Lateral Force Resisting System of a building and are therefore part of the Life/Safety mandate of the IBC and the state’s Rules of Professional Practice. This affects the practice of professional engineers (i.e., does not the practice of Building Officials …at least on this issue…impact the professional engineer in responsible charge duties?). Perhaps, if there has been any ambiguity on roles and responsibilities with engineers, it has been, in part, because some Building Officials do not fully understand their role. Standard-of-Care (for Professional Engineers) in the Survey State is defined as, “Each Licensee and Certificate Holder shall perform in accordance with the standard of care for the profession and is under duty to the party for whom the service is to be performed to exercise such care, skill and diligence as others in that profession ordinarily exercise under like circumstances” (emphasis added). Given that practices differ from building department to building department, is standard of care confined to local regional practices (i.e., city-to-city or county-to-county)? Obviously the statute is defined for state-wide practices, but in reality standards of practice can vary more locally. When it also states “…as others in that profession…”, is that what others in that state are currently practicing or what they “should be” practicing by building code and truss industry standards? Given the conflict that occurs among Building Officials, this was brought to the attention of the respective Survey State’s Board of Professional Engineers. Their brief response alarmed the author even further, stating “The Board is under no obligation to inform a building official of any conflict. This is so because the building official, in and of itself, does not practice engineering. The processes, practices, or methodology that the building official employs regarding plan approval …for metal or wood trusses or any other matter has nothing to do with the practice of engineering by engineers. If there are discrepancies in plan approvals, those discrepancies are the policy of the building official. Further, there was no information that exists suggesting ... that the health, safety or welfare was a risk due to a systematic failure of the review process.” They went on to elaborate that they did not see any deficiencies with current state statutes or that of building officials requirements for professional engineers (i.e., the status quo properly defines an engineer’s role and responsibility). Ironically, this state’s regulations reads, in part, “All Licensees … shall at all times recognize their primary obligation is to protect the safety, health and welfare of the public in the performance of their professional duties.” If and when a city contracts with a Professional Engineer for peer review services (involving deferred documents), the State Board informed the author that the engineer is under “no obligation to remedy the city (client)” plans review process or practices. If there are discrepancies of some kind in the plans review and approval processes, those discrepancies are the policy of the city and building officials and not the responsibility of the peer review engineer. Does not the proper practice of building officials impact that of the professional engineer? Are not the two roles tied together? If building officials are not properly enforcing the review of deferred submittals, does that not reflect on the engineering community at large and a professional engineer’s responsible charge and primary obligation? In this one case, a city mayor (who is a non-industry individual) clearly understood the issue with his own building department and acted to align policy with practice. The State Board chose to ‘kick the can down the road’ and Building Officials couldn’t see the existing problem. As engineering professionals, we can’t afford to design within a bubble any longer. In this age of integration, there needs to be faster and more efficient alignment between all stakeholders. State Boards regulating Professional Engineers need to work with Building Officials on a state-wide basis. There needs to be an examination as to conflicts between state statutes and building code language. Each state’s structural engineering association would do well to lead this effort and thereby serve their own interests. In Part 3 of this series, the author will discuss a specific conflict … using the Survey State as an example.▪
Dean D. Brown, S.E., is a Professional Structural Engineer in the state of Utah. He works as a senior structural engineer for Lauren Engineers & Constructors in Dallas, TX. He can be reached at browndean57@yahoo.com.
Are Sustainable Structures Compactible with Common Sense?
March 2014
The March 2014 Structural Forum column ba ed me. e author has not documented the basis of his assertion that “sustainable” buildings are only one percent better than “standard” buildings, nor did he explain why he “ignored the energy used to run buildings” even though, of the total energy used to construct and maintain a building over its lifetime, operation typically accounts for about half. We are left with the somewhat self-congratulatory argument that anything an engineer touches is better than prior designs because of increased structural e ciencies; or perhaps that what some call “sustainable” design really is not sustainable. It’s been a couple of years since the last semi-credible “climate skeptic” examined the evidence and said that not only was he convinced, but things are worse than originally thought. While public agencies are preparing for rising sea levels, more frequent droughts, etc., maybe we should examine the de nition of “common sense” as well as “sustainable.” Instead of designing an “e cient” new bridge to widen a highway, we could replace the highway with a mass transit system; instead of state-of-the-art and “e cient” McMansions, we could design multi-family housing with equally e cient structures, preferably using truly renewable materials. We have enormous challenges ahead of us. LEED won’t meet them in time; that does not mean we should abandon the goal of sustainability, but rather that we should reset our entire outlook on what we should build, and how. or Matteson, S.E. Berkeley, CA
Response from the Author My admittedly outrageous statement that current “sustainable” structures are little di erent from normal structures is based on the following assumptions: • It is essential that engineers lead the way in reducing impact on the environment and depletion of non-renewable resources. See Building for a Sustainable Future: An Engineer’s
Guide, published in February 2014 by the Institution of
Structural Engineers. • My comments were limited to what engineers can do once the decision has been made to construct something; i.e., their normal job. • e energy used to operate buildings is not part of structural design; also, the end of a structure’s life and potential for recycling are not within the engineer’s control. • Structural engineering design codes, augmented by value engineering, generally result in near-minimum-weight and -cost structures. • For a typical large building, say 50,000 square feet, the choice is between steel and concrete frame, with similar oor structures. Stripped to structure only – foundations, cores, columns, beams, oor slabs – there is virtually no di erence, in terms of cost, weight and embodied energy, between steel and concrete options; rather, the di erences are smaller than those that arise out of project-speci c and commercial circumstances – the precise sources of construction materials, their transport to site, required speed of construction, preferences and experience of contractors, etc.
Many studies have demonstrated this. • e outcome of whole-life embodied energy calculations depends entirely on the assumed life of the structure, which is generally arbitrary; this always lies in the assumptions given in the small print of such calculations. Bill Addis, Ph.D., MCIOB
Closure anks to Mr. Addis for clarifying this, and for his other contributions toward sustainable design. His rst point, that engineers should lead the way in reducing environmental impacts, suggests that we need to shift our approach to his other ve points by in uencing the following: • Deciding what we construct – e.g., suburbs, exurbs, and freeways vs. well-planned, high-density housing areas with no need for private automobiles. • Using materials that result in lower operating energy – e.g., steel-framed houses with poor thermal performance vs. wood-framed. • Measuring on a “per need” basis, not a per square-foot basis – e.g., the couple who asked me to design a 5,000-square-foot retirement home, glowing about how energy-e cient it was, should have been guided toward a much smaller home or apartment. • inking beyond the structural core – e.g., can the structure be adapted to future uses, or can components be easily reused or recycled? • Designing for true resource e ciency, not just to meet arti cial goals subject to rede nition for the convenience of the owner or design team. Every building material sector tells you how theirs is the most sustainable to use. e truth is, unless some 7 billion other people can build just the same way you are, and never reduce the supply of raw materials, your building is not sustainable. e last time we practiced truly sustainable construction was before we started mining coal. We don’t need to regress, but we de nitely need to change course swiftly, while we still can. or Matteson, S.E. Berkeley, CA
Vertical Turbine in an Urban Environment
February 2014
I just came across this article in STRUCTURE magazine. Drum turbines do have some of the best turbine coe cients (Ct). ey do produce more e cient power then horizontal turbines in urban areas. ey will capture up to 95% of air mass going through, while horizontal turbines at best will capture 40% of air mass going through. But there are a few down sides, such as: vertical assembly has weight issues, the entire assembly sits on one gear box which carries both the weight and rotation of the turbine. And secondly, wind ows both on the force and drag side of the turbines; blades have to be aerodynamically shaped to capture wind on the one half and reduce drag on the other side as blades are rotating into the wind. Bahari Energy, LLC, has developed a new technology which overcomes all the issues with both vertical and horizontal. It is called the Wind Tower technology. is is a game changer technology in capturing wind energy for the urban environment. Regards, Habib Bahari Rockville, MD
Design Defi ciencies in Edge Barrier Walls in Parking Structure
April 2014
ank you for your excellent article in STRUCTURE magazine on “’edge barrier walls” in parking structures. We need more of these type practical articles – this is especially important for young structural engineers. In Figure 1, the #4 standard hook is not developed in a six inch wall – reference CRSI Reinforcing Bars: Anchorages and Splices. In the past twenty years or so, I have investigated parking structure problems and found most serious structural issues to be related to connections. anks again and good luck. Larry G. Mrazek, P.E., S.E. Chester eld, MO
ADVERTISEMENT–For Advertiser Information, visit www.STRUCTUREmag.org




