
28 minute read
CODES AND STANDARDS
updates and discussions related to codes and standards
When done rationally, maintaining and repairing existing buildings represents an efficient use of resources that should be promoted. Also, reusing and repairing existing construction becomes increasingly important as sustainability becomes a higher priority (SEI 2013). Model building codes change over time, with hundreds of changes every few years. Given such revisions, existing buildings would either require frequent modifications or need to be treated differently. Fortunately, lawful existing building conditions are typically “grandfathered,” which means they can be used without modification. Various incidents such as fires, accidents, and storms cause damage to buildings that often requires repair to maintain conformance with applicable requirements. When damage occurs, the minimum required scope of work must be determined in many cases. Can the building be maintained as it was? What upgrades, if any, must be added to the repairs? Answers to these and simiCurrent Code and Repair of Damaged Buildings lar questions can be found within the code provisions that govern repair of existing buildings. The intent of code repair provisions can be Are Upgrades Required? better appreciated by studying their evolution.
By Zeno Martin, P.E., S.E., Brian Tognetti, R.A., and Howard Hill, Ph.D., P.E., S.E.
Zeno Martin is an Associate Principal at Wiss, Janney, Elstner Associates, Inc., Seattle, WA. He can be reached at zmartin@wje.com. Brian Tognetti is an Associate Principal at Wiss, Janney, Elstner Associates, Inc., Bingham Farms, MI. He can be contacted at btognetti@wje.com. Howard Hill is a Senior Principal at Wiss, Janney, Elstner Associates, Inc., Northbrook, IL. He can be reached at hhill@wje.com.
The 50% Rule & Upgrade the Entire Building
The very first model codes in the U.S., the Uniform Building Code (UBC 1927), Southern Standard Building Code (SBC 1946), and Basic Building Code of the Building Officials Conference of America (BOCA 1950), contained specific provisions applicable to existing buildings. These stated what was required to be done depending on the type of work performed (i.e., repair, alteration, and change in use) and its cost. For repairs, if the anticipated cost exceeded 50 percent of the building’s value before the damage, then all aspects of the entire building, not just portions affected by damage, needed to be upgraded to meet new construction requirements. Some of these earlier codes included an additional 25 percent repair cost threshold. When the anticipated cost of repair was between 25 and 50 percent of the building’s pre-damage value, then unaffected portions of the building did not have to be upgraded to meet new construction rules. If the cost of the proposed work was less than 25 percent, then in-kind repair was typically allowed. The three model codes maintained these costof-repair based upgrade triggers until the late 1970s. At that time, these percent-rule upgrade triggers were deemed an obstacle to the re-use of existing buildings (Mattera, 2006) and so were largely eliminated.
Upgrade Only What Was Affected
After removal of the general percent-rule triggers, and starting with the 1979 UBC, 1981 BOCA, and 1982 SBC, the extent to which new construction provisions were triggered by repair work was no longer dependent on cost. Instead, the intent was to leave undamaged, unaffected elements alone, and apply new construction rules only to elements of the construction that were affected by the damaging event. This upgrade only what was affected philosophy was promulgated by each of the model codes until they were consolidated into the International Building Code (IBC) in 2000.
Current Code – Repair with No Upgrades?
Starting with the 2015 versions of IBC, matters governing the repair of existing buildings are addressed almost exclusively by the International Existing Building Code (IEBC). The IEBC has three optional approaches to repair, per Section 101.3: “…to provide flexibility to permit the use of alternative approaches to achieve compliance with minimum requirements…” The applicant is required to select one of three compliance methods, which are termed: Prescriptive, Work Area, and Performance. However, not all alternatives may be available in all circumstances. The Performance Compliance Method is detailed in IEBC Chapter 14. It is the most lenient compliance alternative in that it merely requires repairs to be consistent with pre-damaged construction. It contains no requirements associated with particular building code provisions, regardless of the extent of the damage. According to the associated commentary, it was written in this fashion to accommodate treatment of buildings that cannot be associated with any particular code, and yet were considered suitable for occupancy and use before the subject damage. This situation occurs when a building
pre-dates the jurisdiction’s adoption of codes and there is no documentation as to what standards were used in its construction. The Applicability section of Chapter 14 (1401.2) provides a “prior to” date that defines what structures can be evaluated using its provisions. This section recommends that the date in question “coincide with the effective date of building codes within the jurisdiction.” There is a recommendation that the Performance Compliance Method only apply to buildings constructed before there were any identifiable code provisions being enforced. This makes sense since buildings constructed after codes were put into effect have defined provisions as benchmarks, while buildings that pre-date code enforcement typically do not. In spite of the recommendation to limit application of the Performance Compliance Method to buildings that pre-date code enforcement, some jurisdictions make it effective to a much broader category of buildings, even all existing buildings. In such cases, it is certainly appropriate to use the Performance Compliance Method, which usually comprises the minimum requirements for repairs. Consider the following excerpt from Chapter 14: “An existing building or portion thereof that does not comply with the requirements of this code for new construction shall not be altered or repaired in such a manner that results in the building being less safe or sanitary than such building is currently.” [2015 IEBC, Section 1401.2.4] The only stated requirement for a repair is that the repaired condition be no less safe or sanitary than it was before the damage being addressed occurred. This is based on the entirely rational premise that, as long as the building was considered safe to use before the damage, restoration to the pre-damage state should be sufficient for continued use. The Prescriptive and Work Area compliance methods also allow like-kind repair of damage, with certain exceptions. For example, the Work Area Compliance Method, in Section 601.2 states, “The work shall not make the building less conforming than it was before the repair was undertaken.” The method then has separate sections outlining requirements for Building Elements and Materials, Fire Protection, Means of Egress, Accessibility, Structural, Electrical, Mechanical, and Plumbing. With the exception of Building Elements and Materials, Structural, Electrical and Plumbing, each of these specific sections repeats the general requirement that the repair shall not make the building less conforming than it was before the repair was undertaken. The
ADVERTISEMENT–For Advertiser Information, visit www.STRUCTUREmag.org Building Elements and Materials, Structural, Electrical and Plumbing sections also indicate when pre-damage conditions can be recreated or when like materials can be utilized, but also describe situations in which repair to something other than the predamage state is required. Each of the IEBC compliance methods has provisions that dangerous (2015 IEBC Sections 401.3 and 606.1) or unsafe (2015 IEBC Section 1401.3.1) conditions be abated. So if the damage was related to a hazardous or unsafe condition, as defined in 2015 IEBC Section 202, then in-kind repair that would restore such a condition would clearly not be allowed. Substantial Structural Damage Starting with the first IEBC (in 2003), the concept of Substantial Structural Damage (SSD) was introduced as a means for defining when structural repair to something other than the pre-damage condition might be required. In the 2015 IEBC, SSD is defined in Section 202 and is used in the repair provisions by both the Prescriptive (Section 404) and Work Area (Section 606) compliance methods. The SSD threshold is used, in part, as follows: “For damage less than substantial structural damage, the
STEEL BUILDING SYSTEMS MAKE THEIR GRAND ENTRANCE
Optimize your building design and construction
We are your nationwide resource for the broadest range of custom-engineered structural steel building systems. To reduce total-project costs, bring us in early on your project to evaluate and determine the best solution for your application.
FREE whitepaper: www.newmill.com/systems
NASCC BOOTH # 7047

damaged elements shall be permitted to be restored to their pre-damage condition.” (2015 IEBC, Section 606.2.1; and similar in Section 404.4) If damage greater than SSD has occurred, then an evaluation is triggered. The outcome of the assessment determines the required scope of the structural-related repairs. If the evaluation establishes compliance of the pre-damage building with the associated criteria, then repairs are allowed to restore the building to its pre-damage state. If the evaluation does not establish compliance of the pre-damage building with the associated criteria, structural-related repairs to something other than the pre-damage state are usually, but not always, required. An important aspect of the SSD provision is to recognize that if such upgrades are necessary as a result of the evaluation, the extent of the upgrades are limited to the structuralrelated work and do not alter the previously discussed scope of the provisions within the IEBC that address the other aspects of the building (i.e., fire protection, means of egress, etc.) Flood Hazard Areas and the Redacted Percent Rule Although the historic general and wide-reaching percent-rule cost thresholds are not in the IEBC, a limited version is still present within all three IEBC compliance methods when addressing damage to buildings located in identified flood hazard areas. When a building, damaged by any means, is located in what Section 202 of the 2015 IEBC defines as a “flood hazard area,” and the cost of restoring it to the pre-damage state exceeds 50 percent of the market value of the pre-damaged building, then all aspects pertaining to flood design for the building shall be brought into compliance with requirements for new construction. Similar to the limitations of the SSD upgrades, eclipsing the 50 percent threshold of the flood provisions does not require other non-flood design aspects of the building to be brought into compliance with new construction provisions.
Too Much Damage to Qualify as “Repair”?
Sometimes people reach the wrong conclusion that replacing damaged materials is not a “repair” but rather new construction or an alteration, or that too much damage has occurred to use the repair provisions. This interpretation is incorrect because it is contrary to the code provisions themselves. The 2015 IBC and 2015 IEBC definition of repair in their respective Section 202 is, “The reconstruction or renewal of any part of an existing building for the purpose of its maintenance or to correct damage.” Repair work then, by definition, reconstructs, renews (i.e., restores), or otherwise maintains what was previously there. Within the 2015 IEBC, Section 502 states that repairs “…include the…replacement of damaged materials, elements, equipment or fixtures...” There is no limitation that correcting damage (repair) pertains only to a certain amount of damage. In fact, both the Prescriptive and Work area compliance methods contain provisions to repair buildings that have sustained substantial damage, such as SSD. A description is offered by NCSEA (2014) that is: “essentially, if the work only ‘fixes’ what was previously there, then it is classified [in building codes] as ‘repair’ work.”

Meeting Current Code
Meeting current code in the context of repairing an existing building means to meet the code provisions that control such work. Upgrades to improve aspects of buildings beyond the explicit requirements of the applicable code provisions that apply to the repair of existing buildings (e.g., the 2015 IEBC discussed above) may be recommended, prudent, or a good idea – but are not required in order to repair and maintain buildings. For excellent reasons, the concept of grandfathering has been applied to the repair of damaged buildings since the inception of building code provisions dealing with repair, and continues today. This practice is based on the reasonable and rational notion that the “victim” of an unfortunate event should not have to bear substantial costs to provide a better structure than what would have existed had the event not occurred. The code provisions for repair of buildings have evolved since their beginning almost 90 years ago. There are now fewer upgrades required. For example, for approximately 50 years (from 1927 to the late 1970s) when repairs in excess of fifty (50) percent of the pre-damage value of a building were made to any building within any period of twelve months, the entire building was then required to be made to conform to all requirements for new buildings. In the 2015 IEBC, repair that does not make the building less conforming than it was before the damage occurred, is, with few exceptions, allowed for nearly all aspects. The significant repair-related upgrade requirements are now limited in the 2015 IEBC as follows: • A 50 percent repair cost threshold, which only pertains to flood hazard areas and only triggers upgrade for flood design features. • If SSD occurs, at most, upgrades are limited to specific structural aspects.▪
This article summarizes an ASCE published Technical Paper written by the same authors (Martin et al., 2015). Reprinted with permission from ASCE.
The online version of this article contains detailed references. Please visit www.STRUCTUREmag.org.
Lone Tree Bridge By Scott Lomax, M.Eng, C.Eng, MICE and Kelly Dunn, AIA, LEED AP BD+C
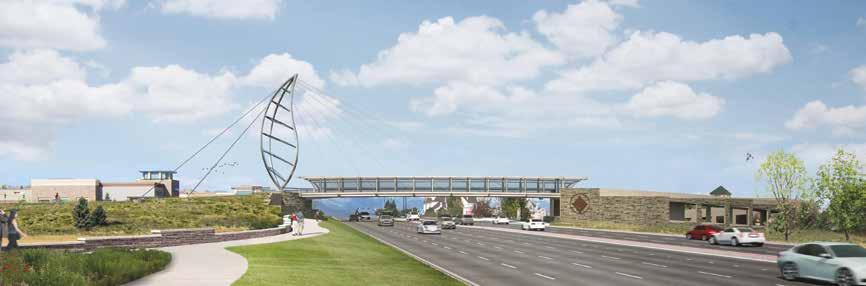
Pedestrian bridges capture the imagination and have the potential to transcend conventional design. There is a long history of landmark bridges created by some of the industry’s greatest engineers and architects. However, the overarching aesthetic demands an integrated approach. This article discusses the historical context of signature pedestrian bridges and showcases the tools and processes that facilitate an integrated design approach, using the example of the Lone Tree Bridge in metro Denver, Colorado, designed by Fentress Architects and Thornton Tomasetti.
Background/Historical Context
Throughout history, bridges have been seen as pivotal links in infrastructure, the means for the consolidation or expansion of a community, a testament to progress in terms of design and materials, and above all, landmarks. The raw nature of these objects appeals to a wide audience, and enormous civic pride is captured in the expression of a crossing. While there are many historic precedents such as Pont des Arts in Paris or Venice’s Ponte dell’Accademia, in more recent times, there has been a significant increase in the design of signature or landmark pedestrian bridges. Projects such as Gateshead Millennium Bridge in the U.K., Langkawi Sky Bridge in Malaysia, or the Puente de la Mujer in Argentina have raised the profile of pedestrian bridges, and owners are aware of the impact such designs may have on the urban fabric. Aesthetic through expression of the structural behavior is not a revolutionary concept. The work of artists such as Nervi, Candela, Dieste, and Calatrava, among others, resonate through a deeply rooted integration of architecture and structural engineering. Indeed, as Candela once stated, “Structural design possesses more art than it does science.” The attraction of the purity of bridge design has fascinated many famous designers, and the most successful projects are a result of an integrated approach combining architecture, engineering, and an appreciation of constructability.
Approach
The success of a project depends on clearly identified goals and objectives, which is more difficult that it sounds. Each project has its unique circumstances and challenges that must be analyzed on a project-specific basis. It starts with basic requirements such as length of span, followed by clearance envelopes, a discussion of cost and schedule, and then on to intangibles such as an improved quality of life and a catalyst for development. From the outset, the challenge is a combination of practicalities, such as constructability or the contextual design of a signature component. The process demands varying skill sets and experience, as well as integration between architect and engineer. For the Lone Tree Bridge, the most
Bridge rendering by Fentress Architects.
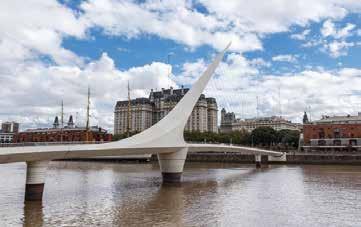
Puente de la Mujer.
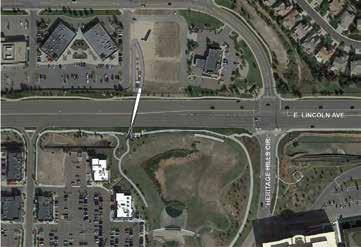
Context plan by Fentress Architects.
basic requirement was to provide a 170-foot crossing over Lincoln Avenue in Lone Tree, Colorado. A closer look showed the need to connect communities and provide an essential link in a network of cycling trails. A more aspirational outlook was to create a landmark that would represent the ambition of the city and be respectful of the amazing natural beauty and vistas of the nearby Rocky Mountains, yet be functional, practical, and within budget. Several concepts were developed, and designs pushed, pulled, and tested. Sometimes this led to minor tweaks, while other times to seismic shifts in the form. Some of the tools available, such as advanced computational modeling (ACM) and 3D printing, were useful during the early stages. However, the principal mode of communication was through hand sketching, preliminary hand calculations, and a mutual respect for the experience and insight that each team member brought to the table.
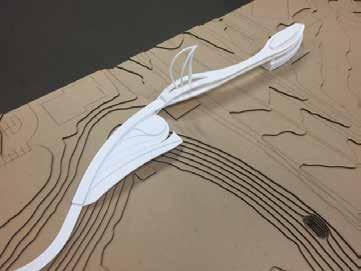
Overall massing model by Fentress Architects.
As the core form of the bridge – an asymmetric cable stay – began to take shape, the analysis and sculpting advanced further. With an efficiency of form founded in the basic layout, the design team focused on the sensitivities of the cable and pylon geometry to create a balance between structural efficiency and art form. Paying homage to the symbolism of the client (the City of Lone Tree), the team refined the pylon to an elementary leaf while retaining the structural integrity. The pylon is essentially a three-dimensional lattice truss, constructed of industry standard elements with a twist in the geometry to create a sculptural form. As the form and vision were consolidated, a number of studies were undertaken to investigate member and material options. The benefits of a lightweight, slender yet stiff structure led to the selection of a steel pylon and deck with a precast concrete walkway. The main legs of the pylon are 24-inch-diameter and 18-inch-diameter for the front and rear legs, respectively. The use of pipe section helped reduce the amount of welding on the project, proved convenient for the intersection of the nodes, and provided a softness to the pylon in keeping with the aesthetic intent. A wall thickness of one-inch was selected to avoid changing thickness, which would incur a splice, and to avoid local stiffening or high stresses at the anchorage connections. This balance of artistry, engineering efficiency, and practical construction was a recurring theme throughout the design and design-assist process. Twin backstays anchor the pylon and the forestay cables splay to support the deck at 24-foot spacing. The 12-foot wide deck is connected to the cables via outriggers that cantilever from the deck sufficiently to ensure the cables do not conflict with the enclosed walkway. The deck is defined by an in-plan truss created by longitudinal edge beams, crossbeams, and diagonal bracing – all using conventional rolled steel members. The main span has an enclosure to protect users in severe weather yet enables one to enjoy the open air and direct sunlight on nice days via a stainless steel mesh on the sides and an ETFE roof. A simple portal frame, supported on the main span deck, provides the infrastructure for the enclosure. As with many pedestrian bridges, the final sizing was a balancing act between strength to carry the imposed loads, stiffness to yield acceptable movements under use, economy through efficiency of sections, type of member and detailing, and attention to the aesthetic vision. The pylon is a signature component, and the member selection and connections were honed with architectural input. The deck was required to be slender for both aesthetics and to maintain the clearance envelope without added depth, which would have a knock-on effect of increasing the approach spans. However, the member types could be conventional, which helps the overall economy. The cables help to yield a lightweight structure, but both redundancy and dynamic behavior became key criteria in the design and were studied in detail. The dynamic behavior, in particular, required time-history analysis of user-induced vibrations to simulate occupancy and determine acceleration levels.
Tools
To work fluidly and communicate effectively, the team used a number of different software packages as the project advanced. From early Sketch-up files through to Revit and then Tekla for the fabrication process, the geometry was developed and shared among the team. The team also developed parametric models to create multiple analysis models and test global configurations to optimize the form. The design team used software to import geometry files into analysis models and then export from analysis models back to the geometry files. This enabled direct communication between the architectural and engineering team, and facilitated a smoother process. Tools and ACM were an integral part of the process; however, it is important to note that they did not drive the design intent. The design was conceived, developed, and finalized through sketches, physical models, and drawings. It was an artistic process rather than a mechanical one.
Process + Design Assist
The client made a decision to follow a design assist approach and engage a contractor early in the project. Once the design concept was consolidated by Fentress Architects and Thornton Tomasetti, and vetted by the public via consultations, the next hurdle was to ensure the vision was realized within the schedule and budget constraints. The overall project cost was set at $6.8 million, with a design period of eight months and a construction schedule of 12 months. By integrating the contractor into the design process and using Guaranteed Maximum Price (GMP) milestones, the client reduced cost and schedule risk. For a long-span signature project, the design assist process was also invaluable to develop and finalize the design with input from the industry. Conventional project milestones of SD, DD and CD were replaced with IGMP, GMP, and Mill Order. The design team worked live and directly with the contractor/fabricator to develop options and select details, and received immediate feedback on how they would impact schedule and budget. The process helped control the quality of the final product and reduced risk across the project. Design assist is a loosely defined process and can be of enormous benefit if correctly applied. Some key requirements include: • Engagement of the contractor at the correct stage of project development. Balancing sufficient design development to show feasibility, intent, and consolidation of principal


Local FEM of the pylon base pin.
requirements, yet allowing enough latitude for the construction team to have influence. • Selection of the most appropriate construction partner. In addition to cost and experience, the understanding and willingness of the contractor to engage in design assist in a collaborative manner is paramount. The contractor must understand the design goals, and the entire team must be committed to achieving the balance of cost, schedule, and quality. • Respect for the experience and skill set of the various parties.
Essentially, for design assist to be successful, the design and construction teams must work toward common goals and value input across the board. Clarity of the objectives and challenges is key, followed by effective communication. For Lone Tree Bridge, general contractor Hamon Construction and steel fabricator King Fabrication joined Fentress Architects and Thornton Tomasetti during Schematic Design. Their input,

2016 Commercial Real Estate Award
Portland Business Journal
Citation Award
AIA Portland 2016 Architecture Awards
Seattle Tacoma Lacey Portland Eugene Sacramento San Francisco Los Angeles
KPFF is an Equal Opportunity Employer.
www.kpff.com Long Beach Pasadena Irvine San Diego Boise St. Louis Chicago New York
The Cosmopolitan Condominiums
Portland, OR Stress contour map.

knowledge, and expertise were fundamental to advancing the project. A series of charrettes and workshops created a common understanding of the issues, and open lines of communication facilitated the platform to work through solutions. An example of this was the pylon base – a joint that was not only of huge engineering and architectural significance but would also be influenced by the fabrication process and the erection requirements. The use of a sculpted pin connection provided a strong yet artistic architectural expression, and was in keeping with the contractor’s preferred erection scheme whereby the pylon would be assembled flat and rotated into position. The engineering team worked closely with the fabricator and developed local finite element models of connections to optimize the configuration and sizing. Design assist is not necessarily the correct approach for every project; however, in the case of Lone Tree Bridge, where an outstanding team was assembled at the critical project milestones with experienced, committed, and passionate individuals, it has been a success to date.
Summary
The most successful pedestrian bridge designs are often pure in their concept. There is an elegance to their simplicity and form that transcends conventional architecture and engineering. To deliver such a project requires an integrated process starting at conception and continuing through the design development and construction. It is essential that the design is influenced by architectural, engineering, and construction principles. Lone Tree Bridge is a wonderful example of an educated client; a balanced, experienced and focused design team; the exchange of ideas and tools to communicate effectively between parties; and integration of constructability with the design process.▪
Scott Lomax, M.Eng, C.Eng, MICE, is a Principal with Thornton Tomasetti in New York, NY. Kelly Dunn, AIA, LEED AP BD+C, is an Associate Principal with Fentress Architects in Denver, CO.
Restoring New Haven’s East Rock Road Bridge
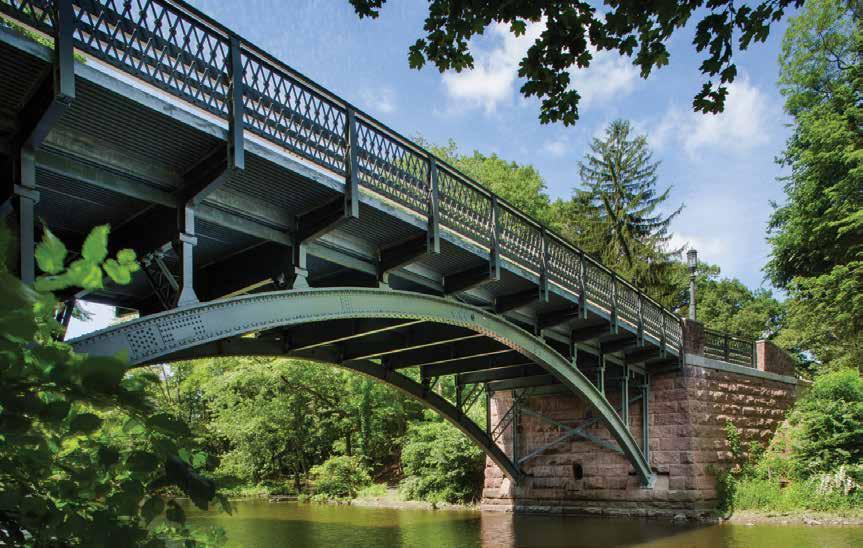
By Thomas Strnad, P.E.
Apopular community destination in New Haven, Connecticut, East Rock Park is listed on the National Register of Historic Places. The 427-acre park, which attracts visitors year-round for hiking, picnicking, bicycling, boating, and cross-country skiing, features a number of historic buildings, gardens, and structures that date to the late 19th and early 20th centuries. Among these is the circa-1900 East Rock Road Bridge, a steel arch bridge that crosses the Mill River on the west side of the park. The 84-foot-long, single-span bridge carries a two-lane roadway with a 20-foot curb-to-curb width. The bridge is also used by many hikers, runners, and bicyclists, and has two five-foot-wide sidewalks. The superstructure consists of a steel grid deck with infill concrete supported on steel floor beams, columns, and deck arches. The arches are part of the original construction; the remainder of the superstructure was replaced during a rehabilitation project in 1984. The original abutments and wingwalls are gravity-type walls with brown, cut-stone masonry facing. These elements were modified during the 1984 rehabilitation by adding a concrete cap to support the new sidewalk and railing on the wingwalls. The east and west abutments are supported on spread footings and timber pile foundations, respectively. In 2007, the Connecticut Department of Transportation (ConnDOT) performed a routine biennial inspection of the East Rock Road Bridge that led to ratings of “serious” for the bridge deck condition and “poor” for the superstructure. Based on the state’s inspection, the City of New Haven determined that the bridge required a major refurbishment.
Historical Research, Modern Analysis
The city selected the firm of Dewberry as the prime consultant to perform an in-depth inspection and design of the bridge rehabilitation. The consulting team also included William Kenny Associates, LLC, for Wetlands delineation, Martinez Couch & Associates, LLC, for the site survey, and Archeological & Historical Services for archeological consulting. City officials challenged Dewberry’s engineers to develop a design that complied with Federal Highway Administration (FHWA), ConnDOT, and AASHTO guidelines and specifications, and in particular the AASHTO LFRD Bridge Design Manual with the HL-93 design vehicle. This led to the final design capacity of 36 tons, as compared to the previous weight limit restrictions of 17 tons and 24 tons for trucks and tractor-trailers, respectively. In conjunction with these design standards, the design was required to emphasize aesthetics and incorporate historical elements into the process. The process began with a review of the original, circa-1900 engineering plans and an effort to supplement information missing from those plans. Dewberry also inspected the bridge to document section losses and current conditions. This required the use of a specialized tracked vehicle to inspect the bridge from the riverbed, as the bridge’s weight restrictions prohibited the use of an under-bridge inspection vehicle located on the bridge deck. Geotechnical investigations included excavating test pits in front of the abutments, verifying existing foundation details, and performing non-destructive testing on the original timber piles to assess their condition and verify their adequacy for design scour events. The excavations extended down to the bottom of footings to observe the tops of the timber piles, which were still in excellent condition. The testing enabled Dewberry to verify the capacity of the original foundation and its ability to carry increased loads. The firm also performed hydrologic, hydraulic, and scour analyses. The design team obtained the required permits from city and state regulatory agencies. Throughout the duration of the project, the

The rehabilitation replicated the ornamental pedestrian rail system and added decorative lighting.
city and the consulting team maintained a robust public outreach program, including a project-specific website and three public information meetings. An initial proposal to widen the roadway by four feet to comply with current AASHTO standards met with some concern from community members and the Connecticut Commission on Culture and Tourism, which sought to maintain the historic character of the bridge and limit speeding. Dewberry successfully obtained an exception from FHWA to keep the existing roadway width.
Complex Issues
The $2.1 million rehabilitation of the East Rock Road Bridge required that the superstructure be completely removed. ROTHA Contracting Company, Inc., led the construction effort, aided by several specialty contractors. The historic arches and the circa1984 columns were transported to Boston Bridge and Steel, Inc., Massachusetts, where they were dismantled, blast cleaned, repaired, strengthened, and painted. Southington Metal Fabricating Company provided the rail fabrication and ADF Industries, Inc., served as the rail erector. The strengthened bridge elements were then transported from Boston back to the site, where they were erected in their original location. The bridge construction was completed with the installation of new floor beams and a steel grid deck partially filled with concrete, which was selected to reduce loads on the arch while at the same time providing a paved riding surface. The project addressed several complex issues, including: • The existing arches were riveted I-section members consisting of a web plate, flange angles and cover plates, with lower steel material properties resulting in insufficient capacity to meet current standards for legal loads. When the bridge was disassembled, the arch pieces were sent to Boston
Bridge and Steel, where the contractor removed the rivets and cover plates and installed thicker cover plates on the top and bottom flanges to increase their capacity. The contractor blast cleaned all of the pieces, removed lead paint, repaired deteriorated steel, and painted each piece. The shop fabricated the new floor beams to support the bridge deck and shipped the pieces back to New Haven for reinstallation.
All of the original arch pins were replaced as part of the reconstruction. Because the arch strengthening resulted in a deeper section, ROTHA Contracting Company took
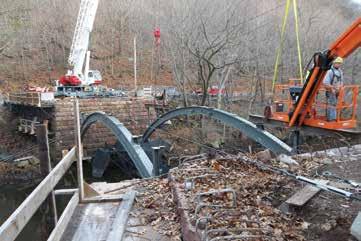
Construction views showing erection of rehabilitated steel arches.
many careful measurements to determine the thickness of shim plates required to install the floor beams at the proper roadway elevations on top of the bridge. • Some fragile elements, such as the original arch cast iron bearing assemblies, could not be re-used as they were damaged during removal operations. These elements were replaced in kind with new steel bearing assemblies. Also, after blast cleaning, the team determined that the deterioration in some steel members was significant. These discoveries required quick action to develop repairs or new details to accommodate these elements. • The design combined the ornamental pedestrian rail system, containing lattice bars and rosettes, with a crash-tested bridge rail system. This resulted in a safe and aesthetically pleasing solution. The contractor also took many measurements and installed shim plates to ensure that the railing posts were installed vertically, and the railing was aligned properly.
Award-Winning Design
The rehabilitation of New Haven’s East Rock Road Bridge over the Mill River, as the structure is formally known, reopened in 2015 and was well received by city officials and community members. The bridge continues to contribute to the historic ambiance of East Rock Park. In addition to the engineering solution that preserved the ornamental rail system, the project incorporated decorative lighting designed by city staff as well as new wayfinding signs, landscaping, and brownstone masonry facing on the concrete surfaces of the new lighting pedestals and bridge rail end walls. The project was awarded a 2016 Engineering Excellence Award from the American Council of Engineering Companies (ACEC) of Connecticut, in recognition of the engineering challenges addressed during the rehabilitation as well as the care taken to maintain the structure’s historic integrity. Identical plaques on either side of the bridge credit the design and construction team, noting that the project was undertaken to “meet modern traffic loads and return the bridge closer to its original splendor… Care was taken to respect the historical setting of East Rock Park in the shadow of East Rock itself.”▪
Thomas Strnad, P.E., is a Senior Bridge Engineer in the New Haven, Connecticut, office of Dewberry.