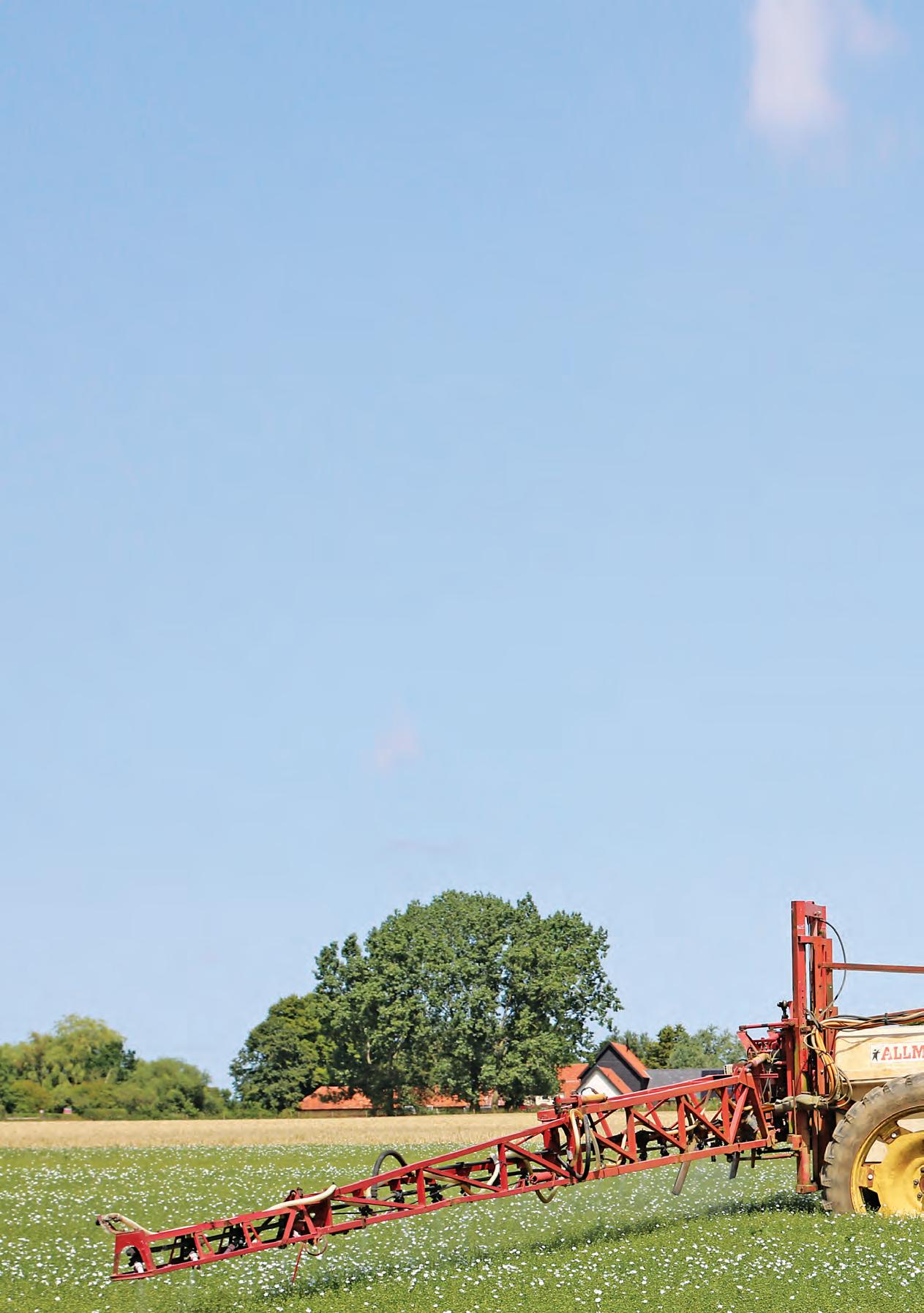
18 minute read
Farming Diary
PRE-HARVEST PROCEEDINGS
Normally there’s a lull just before harvest, but that hasn’t been the case with the Suffolk Bunch – our group of modern classic farm machinery enthusiasts – whose activities in July included spraying, mole-draining, fitting new track chains, fettling a Ford 70 Series and operating a Cat crawler with a scraper box. Coverage of all the action is once again provided by group member and journalist Chris Lockwood.
Advertisement
JON HAYNES’S unique John Deere 2250 based self-propelled sprayer was in action again in midJuly, spraying host farmer Angus Hamilton’s spring linseed, which he established back in April using big classic power (CLASSIC TRACTOR August 2021).
The sprayer had already been fitted with Standen 12.4R46 row-crop wheels in readiness for this work, allowing it to run down the tramlines without damaging the crop. The row-crops have a bigger diameter than the sprayer’s wide wheels so they also increase its ground clearance when working in taller crops from late spring onwards. This time it was being used by Jonathan Tunmore, who spent much of this spring operating a sprayer for local contractor Rob Cannell, to apply a late flowering fungicide to the linseed, primarily to prevent botrytis infection.
“It’s an interesting little thing,” says Jonathan, about the sprayer. “It’s based on a nice little tractor, which sounds good. It’s nimble on its feet and handles well. The steering is rather interesting – you’ve got to get your head around it a bit, how it reacts – and I found that it’s better to go slowly when turning on the headlands and steadily steer round the curve. ”The steering lock isn’t quite as good as that of Angus’s Bateman RB26, which does turn really tightly, but being articulated, Jon’s sprayer turns in such a different manner that you can’t really expect it to be as sharp, although it’s not that far off,” he observes. “The boom rode really well, although I noticed that if you went a bit too hard it would flap slightly, although it was good while travelling at 11kph. You wouldn’t think it has done 16,000 hours as it has been very well looked after, especially inside the cab.
“It is a very well thought-out machine,” adds Jonathan. “You can see it really would have had a place back when it was made in 1989/90, and it still does have a place, even today. It will be wellsuited to spraying off stale seedbeds before drilling and for pre-emergence work post-drilling, when you just want to travel lightly without making a mess, plus it wouldn’t matter so much where you turn. Even if it sat on its big wheels all year just for that sort of work it would be a handy tool. I’m really looking forward to having it out in the autumn.
“I’ve done a lot of spraying with hydrostatic-drive sprayers for years,” he continues. “You get used to going at a sensible sort of pace in the field and slowing down on the ends, but without a rate controller on the 2250 you haven’t got that ability, which you have to take into account. So you can understand why spraying speeds were not that fast in the 1980s, before hydrostatic transmissions became popular.
“I can also understand why people used to spray twice around the headlands as well, as there’s quite a lot to do on the ends
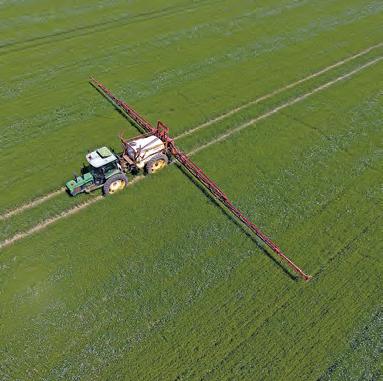
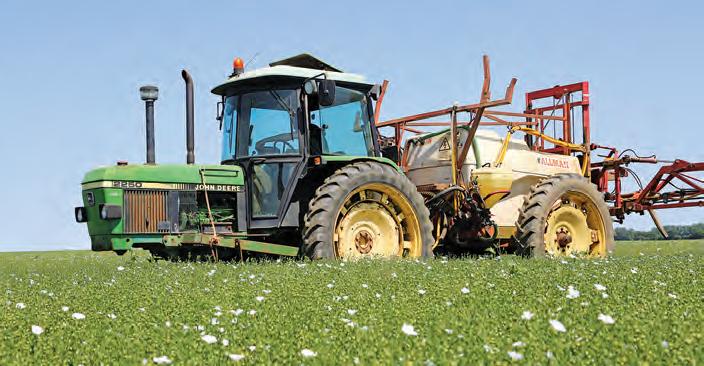
Left: Swapping the sprayer’s standard wheels for its narrower set of Standen 12.4R46 row-crops enabled it to run down tramlines without damaging the crop of linseed.
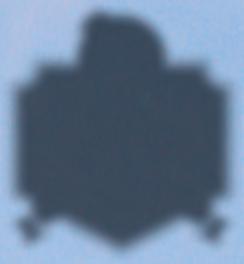
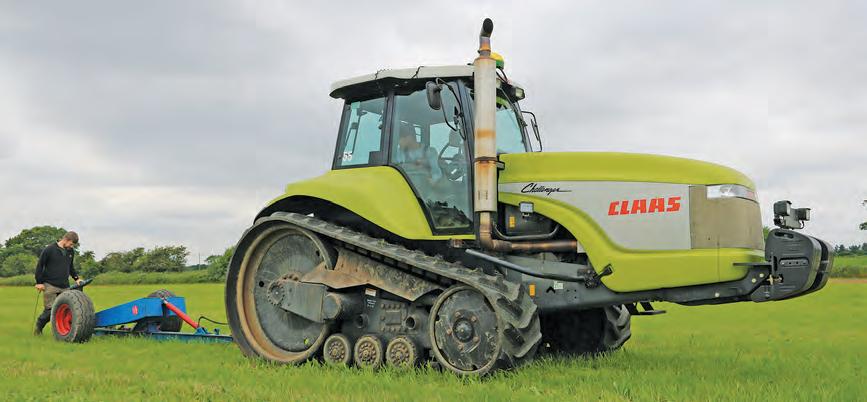
with the throttle, section control and Hi-Lo splitter all being on separate controls rather than one joystick, so you’re quite busy. The whole ethos of spraying has changed so much in the last 20 years. Back then, a 3000-litre machine was a big sprayer, now you see 8000- and even 12,000-litre monsters. But it’s come at a cost.
“I remember when I first drove a combine we never had problems breaking the lifters, because the spraying was done with a relatively lightweight Bateman RB15,” notes Jonathan. “Now I’m following a 36m Agrifac, which is considerably heavier and leaves deeper tramlines that you can’t always see, especially on headlands, and as a result you start breaking lifters and knife sections.”
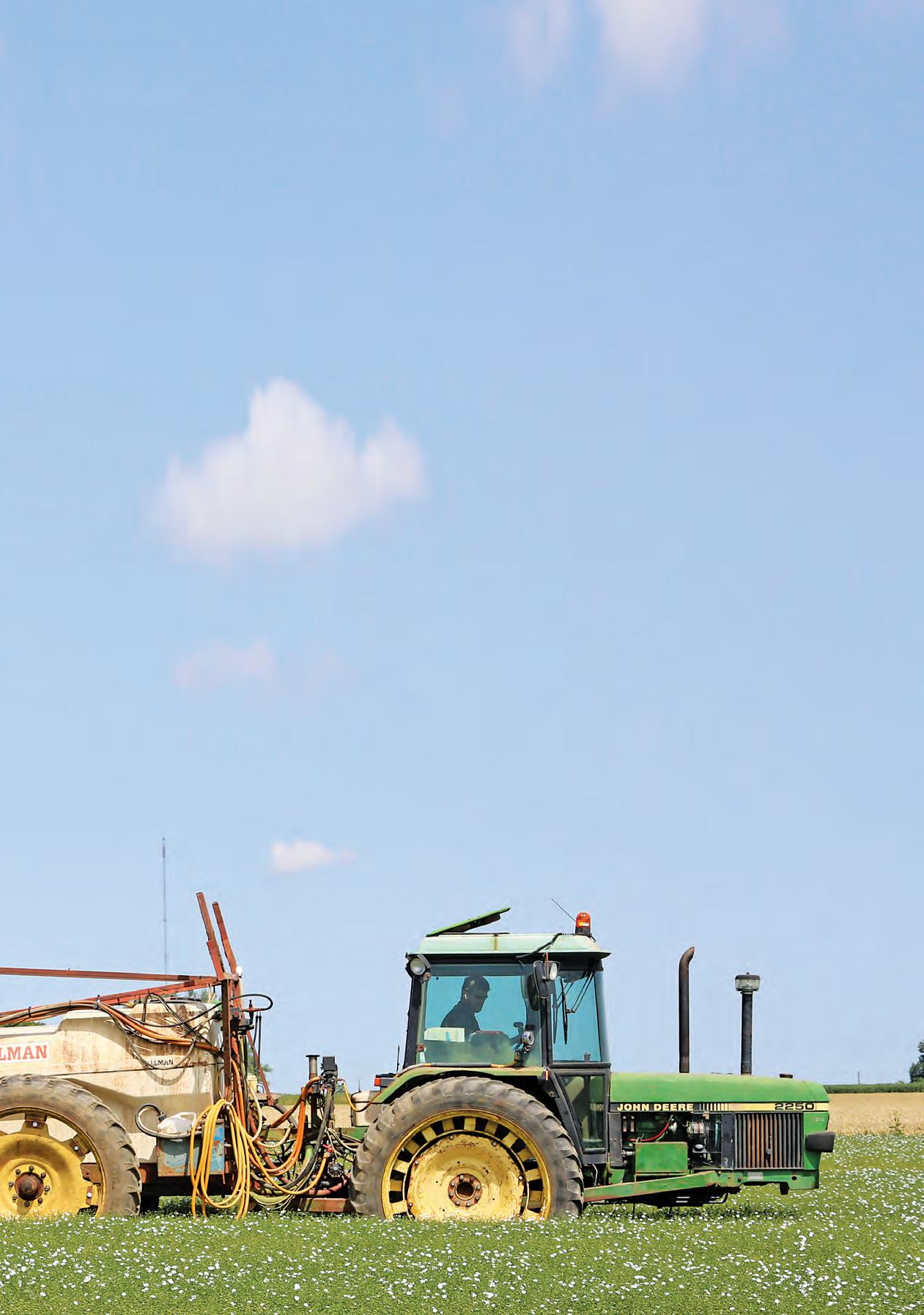
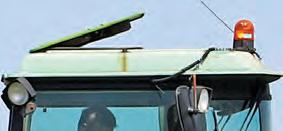
Left inset: Jonathan Tunmore, who was driving the sprayer on this occasion, said its 24m Hardi boom rode very well at a forward speed of around 11kph. Below: Jon Haynes’s unique John Deere 2250based self-propelled sprayer went to work again in mid-July, spraying host farmer Angus Hamilton’s spring linseed.
Moling the marshes
Rory Poacher using Jonathan Tunmore’s Claas Challenger 55 with a Miles single-leg mole drainer on some marshes near the Suffolk coast. Jonathan can be seen walking behind to check that the mole is catching the gravel backfi ll of the drains.
Above: To mitigate the Claas Challenger’s nose-heavy balance and maximise its grip, an additional weight block was carried on the rear linkage. Above right: Jonathan opted for his Claas Challenger 55 for working on the marshes, rather than his larger fl attrack Challengers, due to its lighter weight and shorter track length, with the overall aim being to minimise the damage to the grass.
SUFFOLK BUNCH
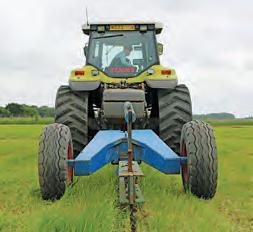
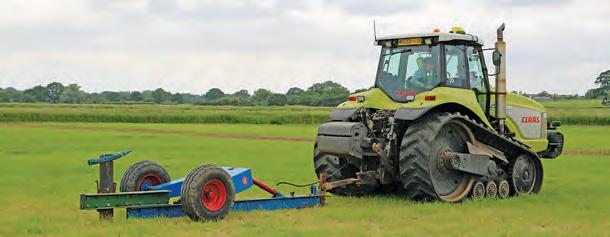
Left: From the air, this sprayer looks relatively conventional, until you notice that this John Deere 2250 has no front axle. Thanks to a set of wide 750/65R26 tyres, it WITH A NUMBER OF CHALLENGER rubber-track crawlers now in his ownership, Jonathan Tunmore is planning to undertake a reasonable area of contract mole draining this season. His campaign kicked-off in early July with some grass marshes. travelled very lightly across the surface of The combination chosen for this task was Jonathan’s a just-drilled fi eld of linseed. W-registration, 270hp Claas Challenger 55 and Miles single Below: The 2850 was working with Angus’s leg mole drainer. The operator for most of the time was Suffolk 3m Ransomes SK300 power harrow, the pair Bunch’s increasingly regular helper, Rory Poacher. recreating a scene that would have been “I was asked to mole drain some marshes at Butley, near the typical in the late 1980s and early 90s. Suffolk coast,” explains Jonathan. “The customer was concerned about weight; he didn’t not want to hammer down and compact the tender soils, and wanted a single-leg machine to do the job. So we opted for the Claas Challenger 55.
“The marshes are in grass and are used to produce haylage, and obviously when they’re cutting close to the ground they don’t want to be raking up stones and soil, so I thought the Challenger 55’s shorter track length would make less of an impact when turning. We also used the GPS guidance so that we could work in lands, missing two or three bouts, to reduce the tightness of the turns and stop the tracks scuffing.
“We lifted the mole out while it was still in a straight line,” he adds. “By doing this, the heave caused by the leg and expander emerging was minimised and the tracks were pulling equally without any slip. We then reversed, making sure one of the tracks ran over the heaved area to push it back down, and turned under minimal load.
“We also carried a weight block on the linkage to help balance the tractor, as they do tend to sit a little nose heavy,” notes Jonathan. When working through a green crop, like grass, there is a tendency for a track to slip, and the extra weight helped maximise the grip. Another reason for choosing the Challenger 55 was because it has the best set of tracks. It pulled it without any issue at all in sixth gear at about 1500rpm. This allowed us to travel about 4.6kph, which was nice and steady, and just right for forming a good mole channel.”
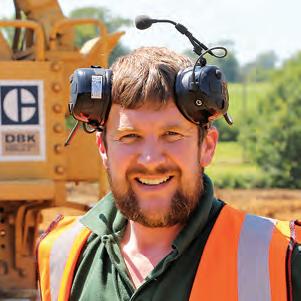
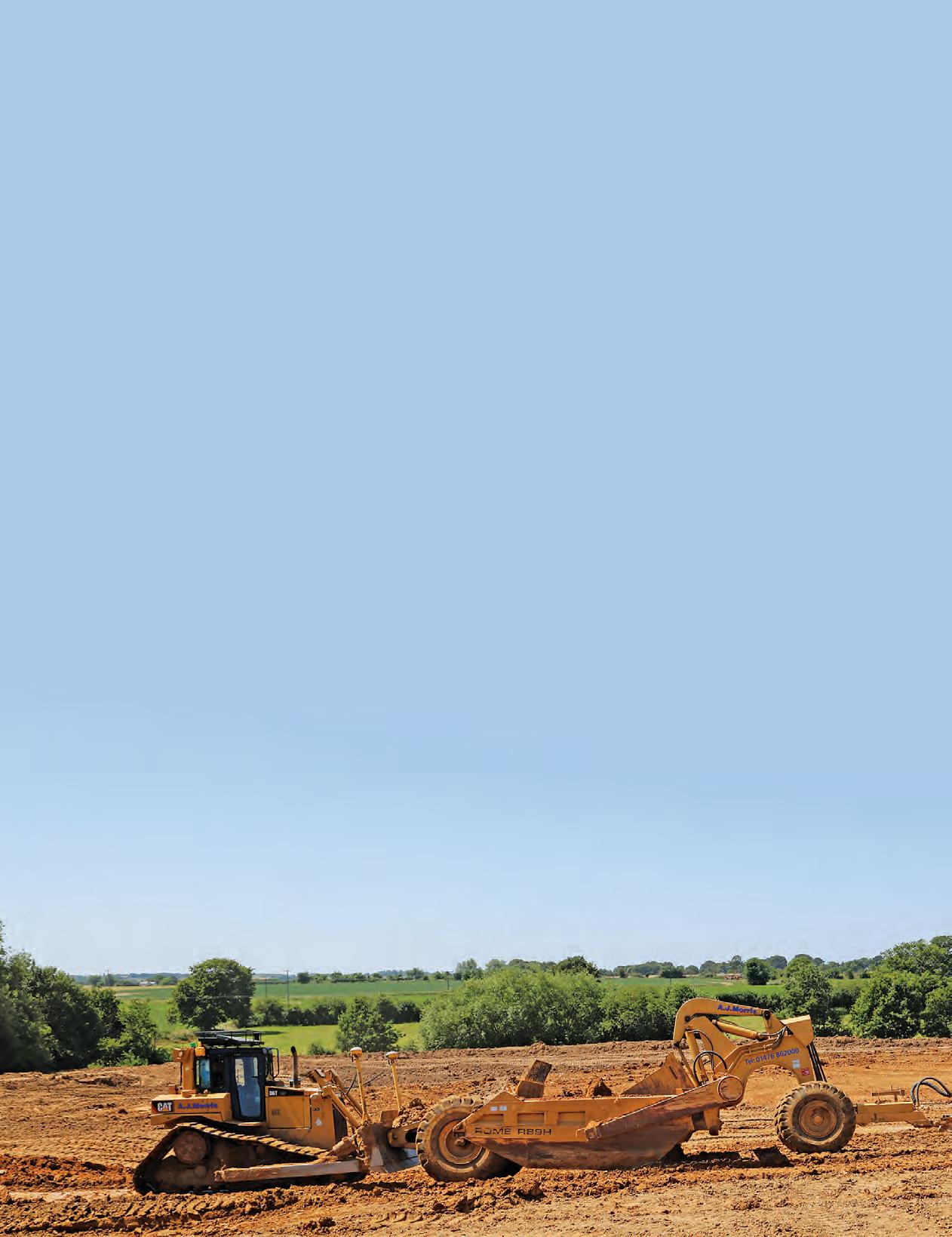

Right: Back in mid-July, Jonathan Tunmore spent a fortnight operating a Caterpillar D8K and Rome R89H scraper box for earthmoving contractor A. J. Morris, helping to construct an irrigation reservoir.
Top right: As well as push-loading the scrapers, A. J. Morris’ 200hp Caterpillar D6T LGP dozer was also levelling the deposited soil on the banks of the new reservoir. Above right: Even with 300hp under the bonnet, to get a full load on the scraper, especially when working in harder clay, the Caterpillar D8K needed some assistance. On this occasion, the shove was provided by a Cat D6T LGP dozer. Below: The Caterpillar D8K and scraper box that Jonathan was operating is one of three almost identical set-ups in the A. J. Morris fleet. This D8K has done an estimated 60,000 hours, but is in exceptional condition, having previously had a thorough rebuild.
THEY SAY THAT a change is as good as a rest. In midJuly, Jonathan Tunmore spent two weeks operating a Caterpillar D8K with a Rome R89H scraper box. The outfit was one of three identical combinations that earthmoving contractor A. J. Morris was using to construct a 55,000cu.m. irrigation reservoir. It allowed Jonathan to fulfil a longstanding desire to use a large steel-track crawler with a scraper box. This ambition stemmed from memories of a reservoir being constructed during his time as farm manager for Foskett Farms on the Suffolk coast.
“In 2007 we had a reservoir installed at the Kirton Estate,” recalls Jonathan. “I think Pryors did the work, and they had a pair of Cat D9Gs and a smaller Komatsu on scraper boxes. The D9s were absolutely massive. I remember taking a photo of my Toyota Hilux parked beside one, and it looked so small in comparison. I thought at the time that it would be nice to have a go on one, and thought the same when I saw Adrian Morris working at Blaxhall a few years ago. Adrian has a reputation for keeping everything smart and doing a good job, so when I saw he needed a driver for a D8 and a box locally, it was a good opportunity to give it a go, especially with harvest being a few weeks later.”
Caterpillar introduced the first Series K version of the D8 in 1974 to replace the long-running D8H. At the time, Cat claimed that the D8K could easily out-perform early D9s in many applications, and that its field studies had shown it offered a 10 per cent dozing production advantage over the D8H. Compared to the previous version, the D8K boasted more power (300hp) from its 20.5-litre D-342 engine, a larger capacity radiator, steering clutch and brake control combined in the same levers, a thicker main frame and an uprated transmission. The exhaust was re-routed with the muffler mounted on the bonnet further away from the cab. A modular ROPS cab was offered, which was more comfortable and could be specified with air conditioning. Later versions benefitted from spacer plate engines, with an additional plate between the cylinder block and cylinder head instead of counter-bores machined into the block to support the cylinder liner support flange. Powershift and direct-drive transmissions were offered. The trio operated by A. J. Morris are all powershift 66V Series models, made at Caterpillar’s Glasgow plant in 1981.
“Adrian’s three D8Ks are very tidy machines,” notes Jonathan. “They’re certainly a lot quieter in the cab than my D8H. They are 40-year-old tractors, yet they feel absolutely fine. They handle really well, especially with the power-assisted brakes and you don’t actually have to touch the brake pedals. And with a torque converter as well, they are just so incredibly forgiving.
“I think I would rather be driving something like this than a modern machine, as it’s just pure power,” he adds. “They’ve each got something like 60,000 hours on them, so they’ve done their fair share of work and it’s a real testament to how well they’ve been looked after.
“Although I had some D8 experience from my own tractor, I was completely new to running a scraper box,” points out Jonathan. “The D8Ks are big machines, but the scraper box is just under 4m wide and will hold almost 20cu. m., and it can draw you to an absolute standstill. When you first see a D8K up close and personal, it seems just monstrous. They’re big huge brutes, and you would honestly think it would pull a house down, and in agricultural terms they will pull almost anything.
“But of course, everything in farming is designed to let soil flow through it, soit’s nowhere near as brutal,” he states. “When you see a D8, which weighs over 20t, just stopped – physically standing still with its tracks scraping – it’s pretty epic. You leave it in second gear the whole time and just need to get the depth right when you’re filling the scraper. If you let it in too deep it will just stop, so you lift it out a bit and she will keep on going. The window to see into the box is quite small so it’s not really very easy to judge how much you’re getting in, but you get more used to it, and I guess someone who is incredibly experienced would know exactly.
“To get a big load on you need to be pushed by a dozer,” notes Jonathan. “In good going, you can get a good load on without a push, but you have to be strategic and set your runs out in a nice straight line and gradually fill it up with a continuous flow of nice thin layers, otherwise it doesn’t want to come out again at the other end.
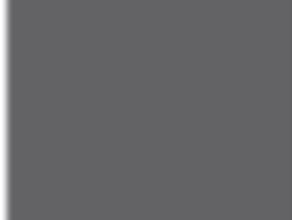

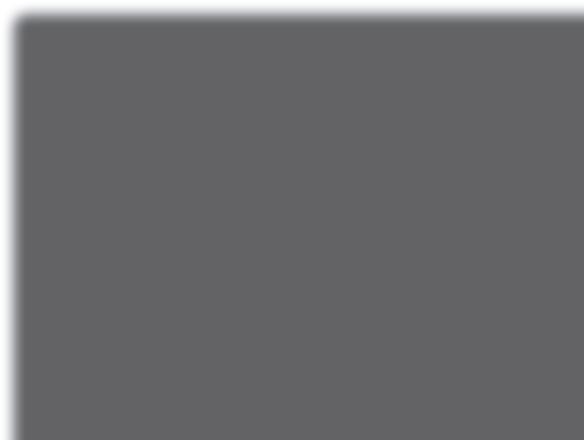
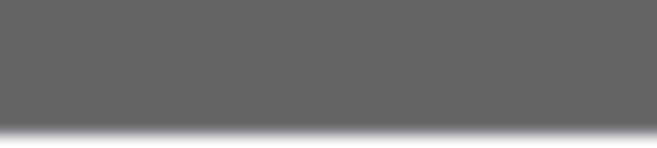
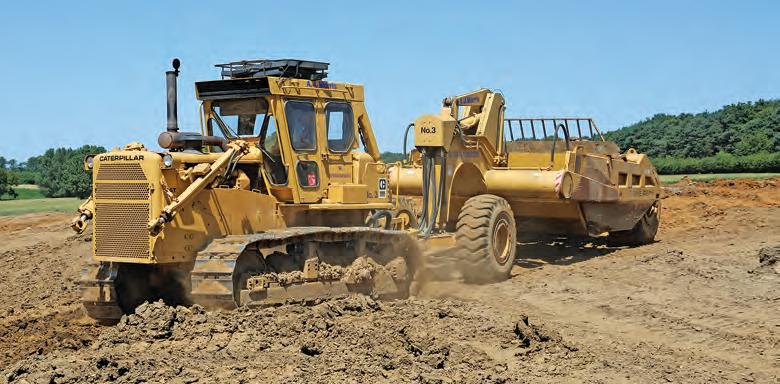
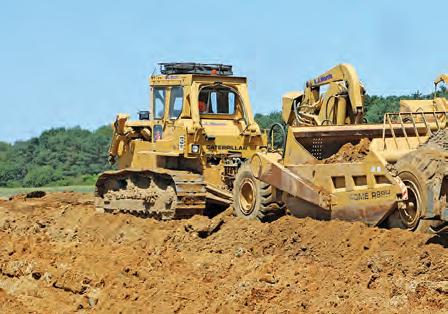

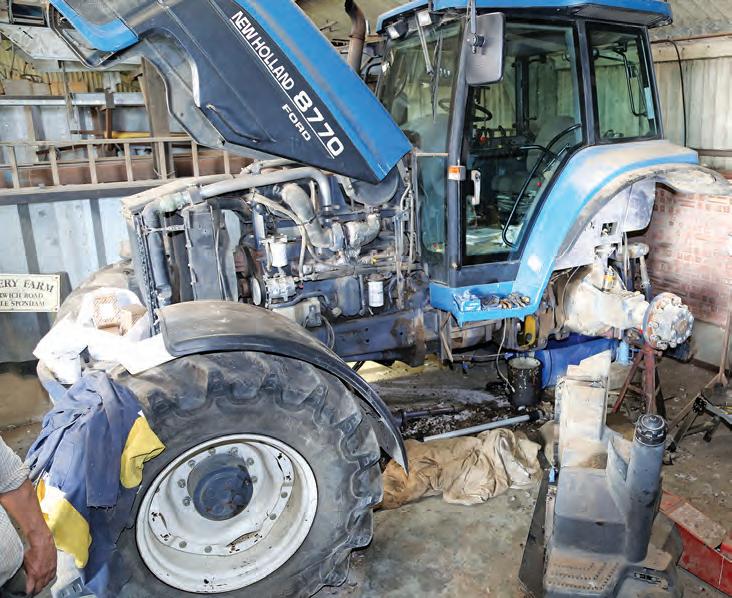

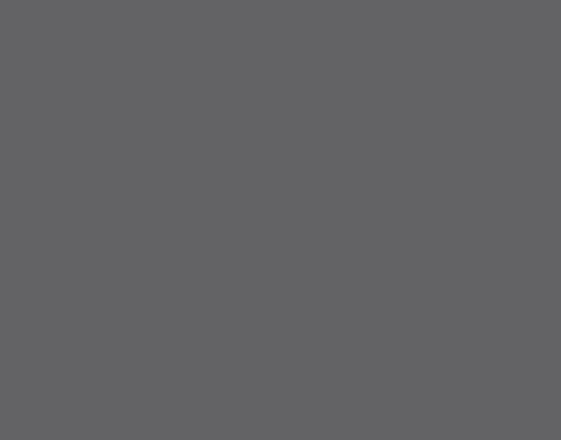

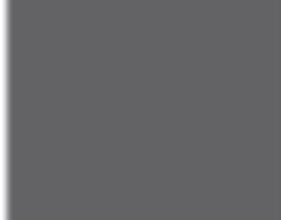
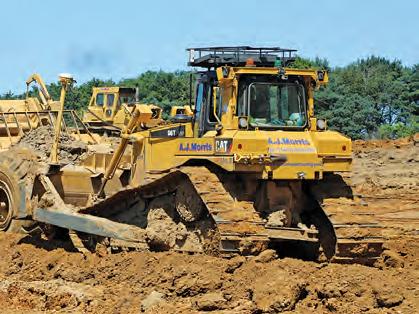
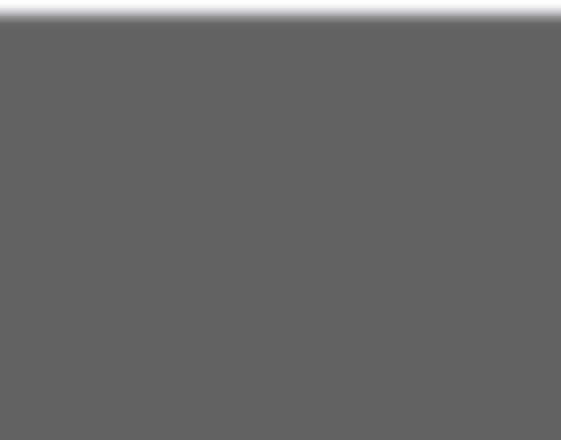
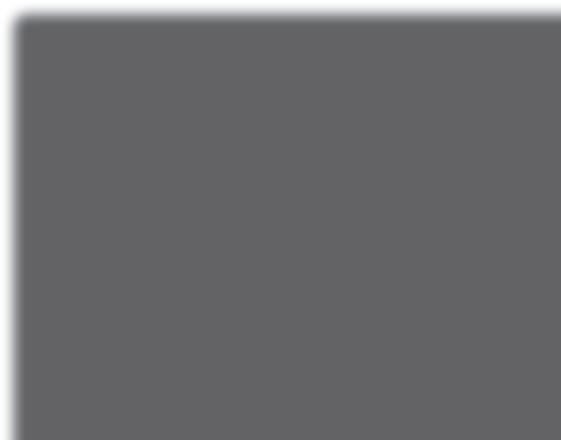
“Many of the same principles carry over from agricultural tasks,” he adds. “You have to give everything you do a bit of forethought, much like using a rubber-tracked crawler. It needs to be going in a straight line, because it won’t pull on just one track if you try to turn – it’s as simple as that.
“It was nice to do something different and challenge myself,” concludes Jonathan. “And it was nice to see the guys who really know what they’re doing, like Dennis who was on the D6T pushing me. He is absolutely mustard and just a joy to watch. The dozer does exactly what he wants it to do and it seems so effortless.
“As well as helping Adrian out, it was also a useful training exercise for me, as I’ve never had anyone give me any guidance on my own D8H. So it was useful to work with some highly-experienced and respected guys and see how they look after kit. I’m very grateful to Adrian for the opportunity, and I believe he is always keen to hear from potential new operators if anyone wants to work with plant.”

Above: Angus Hamilton has been carrying out some maintenance to his recently-acquired New Holland 8770, in readiness for using it for autumn cultivations. The work has including replacing a front axle driveshaft oil seal.
Below: To gain access to the front axle drivetrain, the 8770’s main fuel tank to be removed.
AS YOU WOULD EXPECT on an arable farm in midsummer, Suffolk Bunch host farmer Angus Hamilton has been busy preparing for harvest by carrying out jobs such as cleaning grain stores and readying machinery for the forthcoming cultivations campaign. In addition to these routine seasonal tasks, he has also been working on his 1996 New Holland 8770, which he acquired earlier in the year (CLASSIC TRACTOR April 2021).
“Most of machinery has now been through the workshop,” says Angus. “We’ve also carted some LimeX out to the field and I’ve mown around the field margins and edges so that we don’t bring any weeds in with the combine.
“As things stand currently, I don’t think I have any wheat closer than three weeks away from being fit,” he notes. “So having been given extra time due to what will be a later-than-normal harvest, we decided to spend some of it getting the 8770 ready for ploughing. This work has included replacing a leaking oil seal on the four-wheel drive prop shaft, access to which could only be gained by removing the tractor’s main diesel tank. We’ve also put the sixth furrow back on the 5+1 Dowdeswell DP7 plough in anticipation of using it with the 8770.”

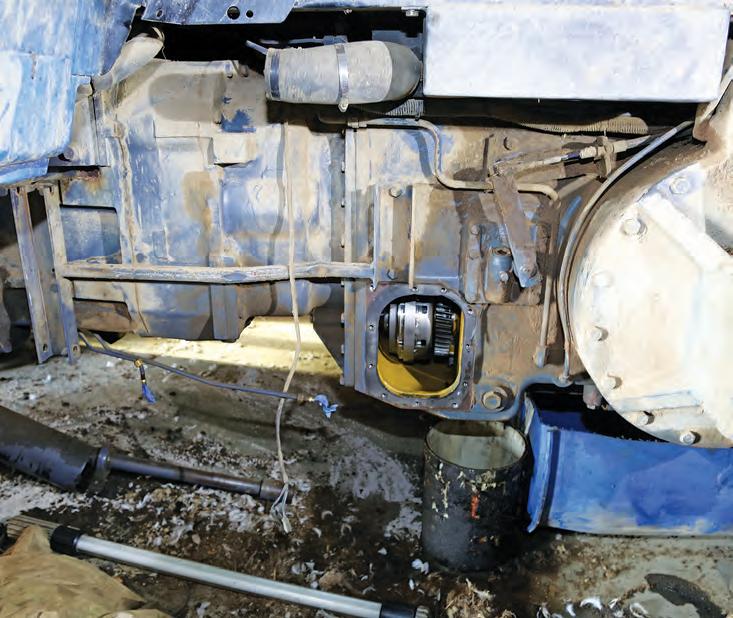
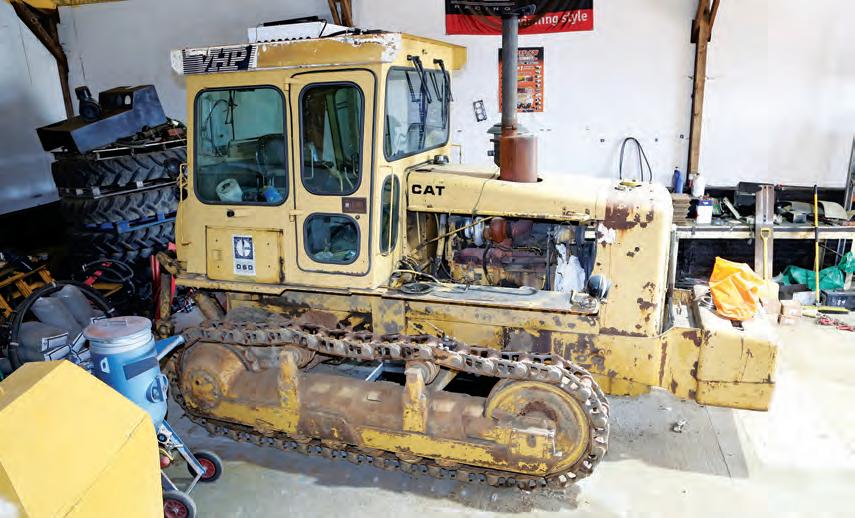
Left: Dave Williams’ 1985 Caterpillar D6D SA VHP looks bare without its track plates, some 36 per side, removed, in readiness for changing the track chains.
Left: After considering various options, Dave purchased a set of brand new DCF sealed and lubricated track chains for this Caterpillar D6D. Below left: As well as fitting new track chains, Dave has been busy MIG welding extensions onto each of his crawler’s 72 track plates, to build up the grouser depth to 70mm. Below: The D6D’s existing track chain were showing considerable signs of wear and would not have lasted for the duration of this summer’s mole draining season.
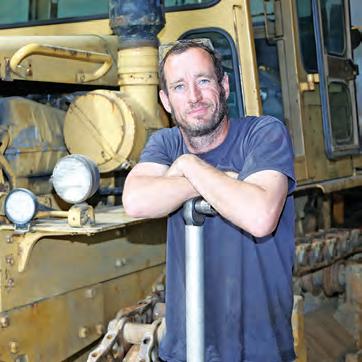
CATERPILLAR STEEL-TRACK CRAWLERS seemed to be a bit of a theme for Suffolk Bunch members during July. While Jonathan Tunmore was off driving a Caterpillar D8K, Dave Williams was busy fitting a brand new set of track chains to his 1985 Caterpillar D6D SA VHP in readiness for this year’s contract mole-draining campaign.
This job involved removing all 72 track plates, splitting the old chains and sliding them out, fitting the new replacement chains and bolting the track plates back in place again.
“The old chains were knackered,” explains Dave. “I bought my D6D knowing that at some point they would need replacing, and after a full season moling with it, here we are. It definitely wasn’t going to do another year as the chains were going to fall apart.
“I decided that trying to turn the pins and bushes would be a stupid waste of money,” he states. “I don’t think I’ll even turn them when the new chains start wearing – I’ll keep running them until they start showing significant signs of wear, so basically running them to death. The purists out there will think that’s mental, and I know I won’t be getting the utmost wear out of them, but I think that the cost of turning them versus just a straight replacement would be detrimental, and I would be better off cutting my losses.
“Every track-plate bolt had to be loosened with a 6ft length of scaffold tube,” adds Dave. “Changing the chains was hard work, but not actually too bad to do. The worst bit was getting the old ones off; because they were so sloppy they wanted to pinch your fingers. The new ones were stiff and not too bad to pull around with a block and tackle. I chose DCF chains because they were the cheapest sealed and lubricated track chains I could find. They are a wearing part.
As well as the chains, the grousers were also not surprisingly worn down, which had started to affect the Cat’s ability to grip. To remedy this, Dave welded an extension onto each grouser to bring the total height to 70mm. This obviously had to be done individually, on all 72 track plates, and it proved to be a timeconsuming exercise.
“It’s one of those jobs that you think you will have all winter to do, but in reality I ended-up doing two days of solid welding,” says Dave. “I don’t think I would do it again. I would just replace the track plates with new ones, as two full rolls of Mig wire have gone into the grousers. I’m hoping it’s going to be time well spent as it should make a huge difference to the grip.”
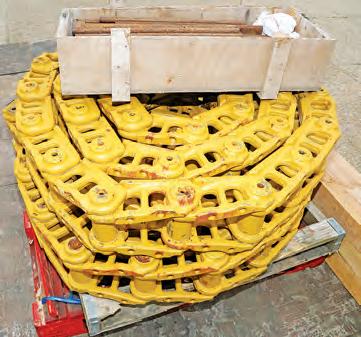

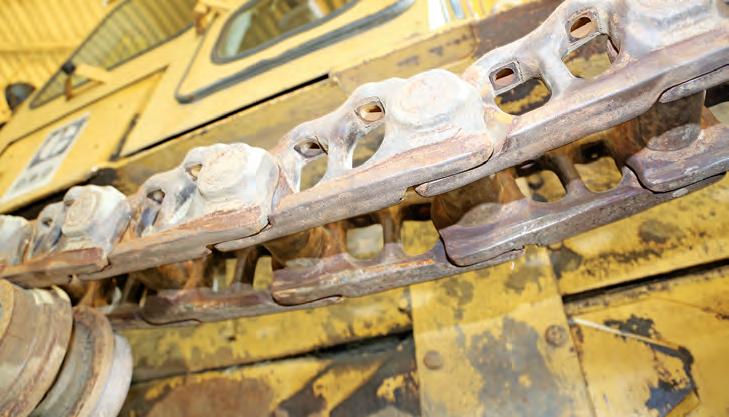