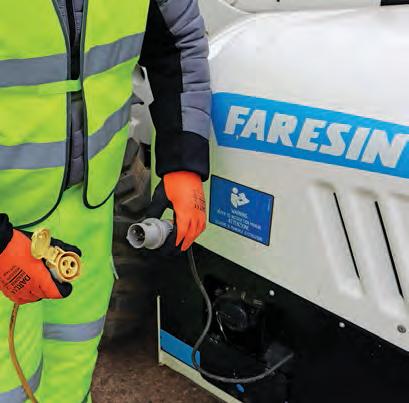
7 minute read
TECHNOLOGY
REAL-WORLD ELECTRIC TELEHANDLER
Peter Haddock reports on the initial success of Faresin battery-powered telehandlers, which have been on the fleet of Flannery Plant Hire since 2020
Advertisement
Inset above and below: The Faresin is constantly topped up during the day, which is enough to keep it available around this busy depot for the whole shift.
n June 2020 Flannery Plant Hire
Itrialled their first Faresin battery-powered telehandler, which was used to help establish the HS2 Tarmac Compound at West Ruislip. They now have six Faresin telehandlers on their fleet, and more are to come. The Faresin 6.26 model offers a 6m lift height and a maximum lifting capacity of 2600kg, plus a maximum forward reach of 3.1m, at which it can handle 900kg. The Italian-made Faresin is powered by a lithium-ion battery pack, of which there are three options delivering up to 10 hours of operation, sold and supported in the UK by the GGR Group.
SITE BACKGROUND
Having worked on various projects during 2021, this Faresin has been with the Morgan Sindall team for the past year to support the delivery of the new £42m bus corridor in the West Midlands. It will improve journey times and provide more reliable services linking Walsall, Birmingham and Solihull. The first section to be completed was used by visitors to the recent Commonwealth Games.
A main contractor on the project, Morgan Sindall invested heavily in its supporting infrastructure, including establishing a main depot on the outskirts of Birmingham city centre. In addition
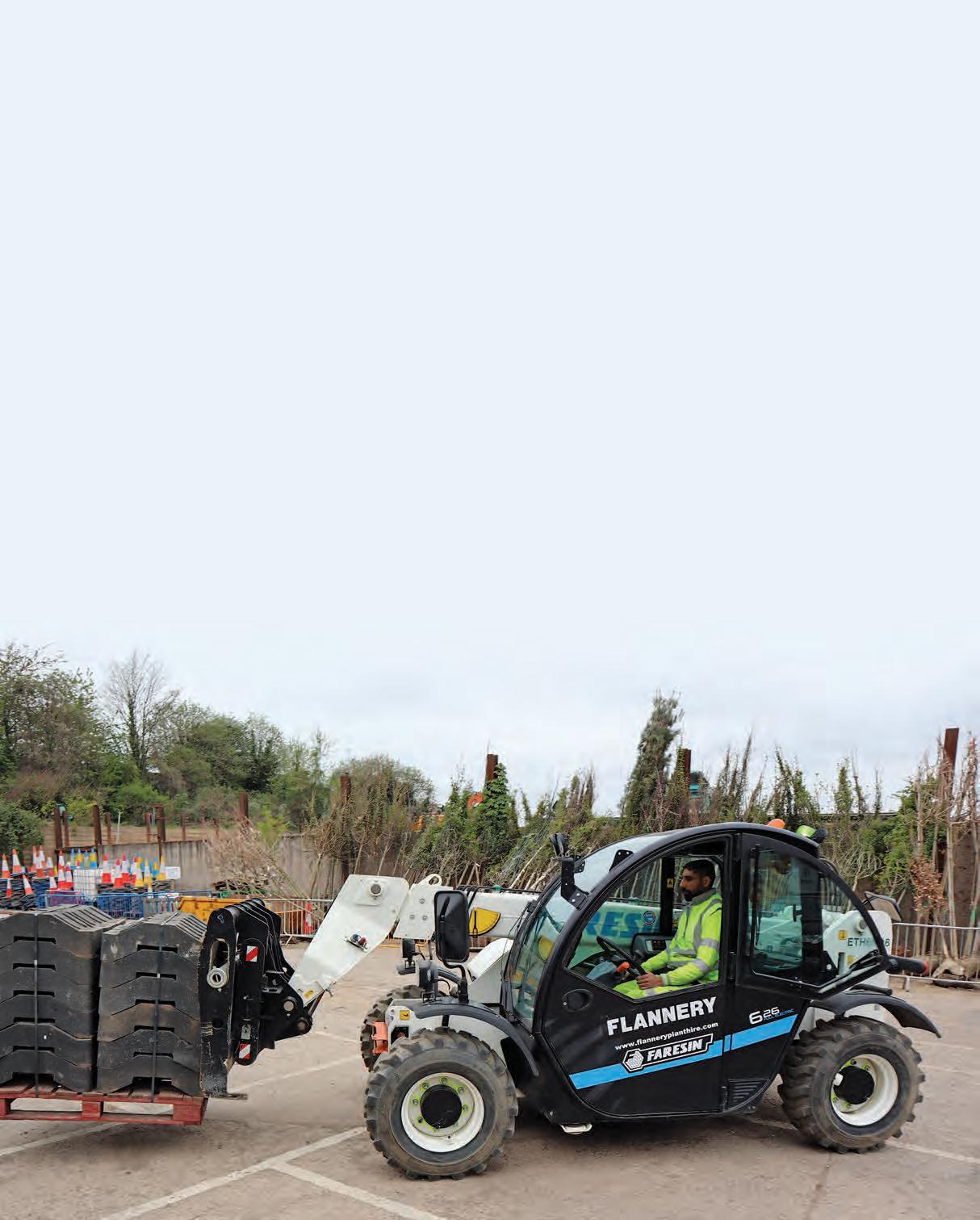
The Faresin telehandler features two electric motors, one for drive functions and one for hydraulic services.

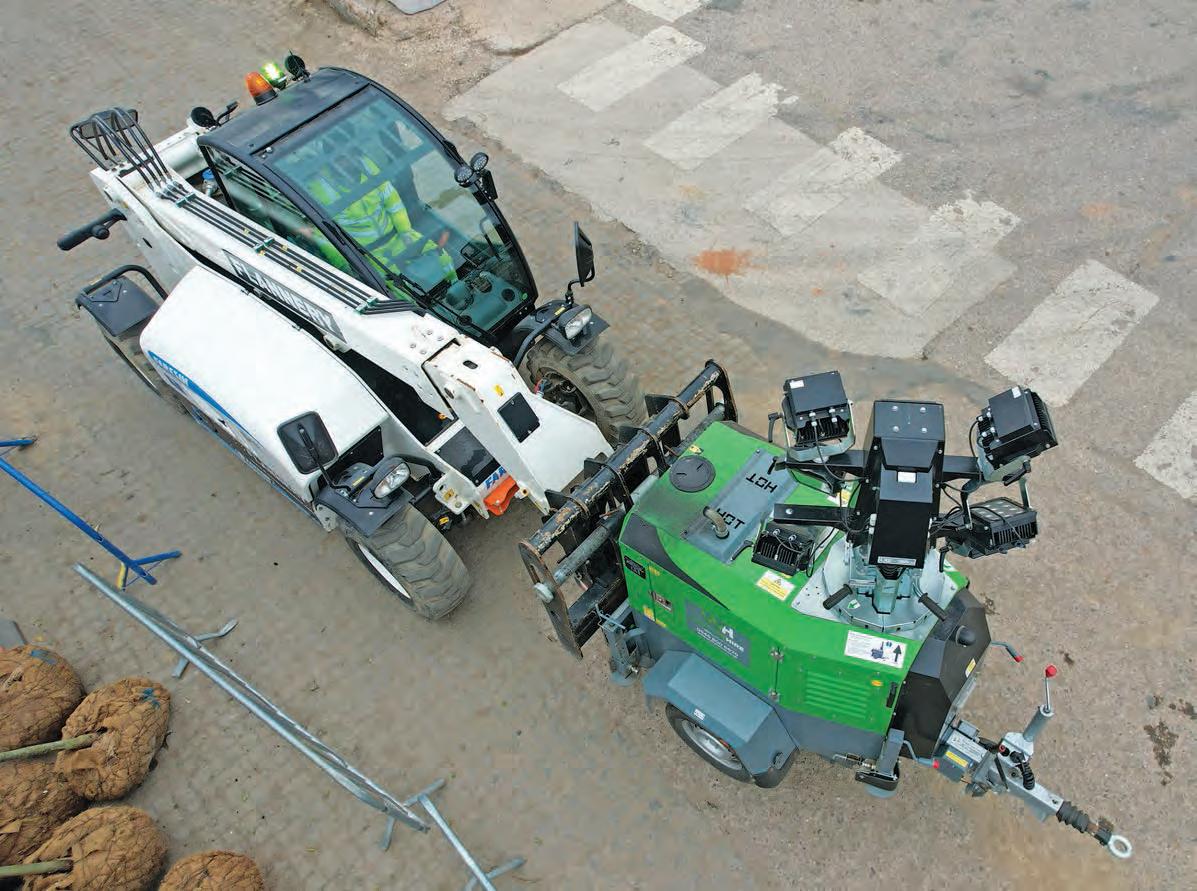
to offices and welfare units, it includes indoor and outdoor storage for a wide range of materials and other assets, including traffic management systems, lighting towers and generators.
The space was also used to support the planting of over 3000 trees during the project. As part of a more sustainable approach to temporary occupation of this site, Morgan Sindall invested in a fleet of electric vans, hired in the battery-powered compact equipment and used low-emissions fuels.
Senior works manager Eddie Anderton said, “For Morgan Sindall’s A45 section of the route, we were required to work in and around the new Green Emission Zone in Birmingham. So, even at the tender stage, I was working with the team on how we could deliver a greener approach. It also allowed us to have some early engagement discussions with the Flannery Plant Hire team to explore our fleet options. They provided the Faresin 6.26 telehandler and some electric excavators for this project, and for all of the other equipment we used HVO fuel.
“These greener choices helped us to secure the work from Transport for West Midlands, while also providing us with the data on carbon emissions and proven use cases for different greener solutions. This information has been monitored throughout the project and will support us in our own goals to be net zero by 2030. We installed a total of 16 charging points at our depot, including a designated charger for the telehandler. The others are used to charge our electric vehicles. They were joined by solar welfare units, lighting and battery-operated CCTV solutions.
“Working with Flannery, we could also have our equipment dashboard using the MachineMax system, which connects all of the Flannery fleet throughout our project. The team and I could access this at any time and see where the plant was, what work it had been doing and, therefore, what carbon impact it generated. It also included information from the telehandler. I was a bit sceptical at first about the performance and longevity of the battery.
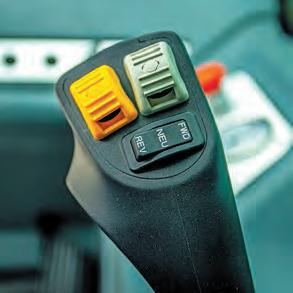

Battery options range from 330Ah to 560Ah, which can be charged through the built-in charger, or from an external fast charger.

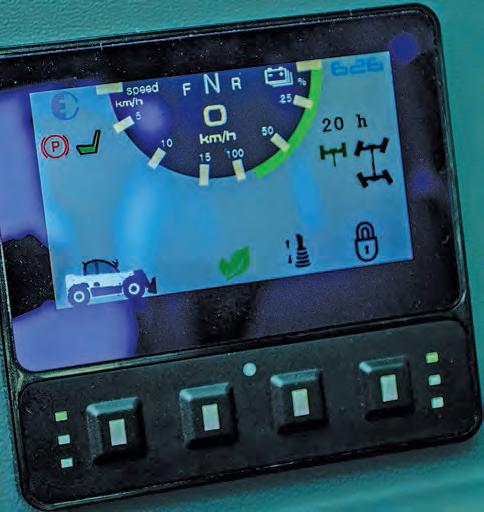
It quickly became very clear from the data and our operator, Happy Singh, that it was ideal for the job. We now know how impactful alternative fuelled machines can be and how we can integrate electric machines into the mix.”
OPERATOR FEEDBACK

Happy Singh used the Faresin 6.26 electric telehandler for general tasks around the depot, including loading and unloading. He said, “It took me a couple of days to get used to the controls and of course how to put it on charge in my breaks. Handling-wise, it’s very similar to a diesel-powered machine, but of course it’s much quieter. As it is all electric, unlike a diesel machine I can also use it across the whole site, including inside our warehouse. This has been very useful when we needed to protect materials from the weather.
“Because it’s electric, the power is also instant, so you have to get used to the sensitivity of the accelerator and the joystick controls, but that’s just like any new machine you get. I definitely think it’s the way forward for sites like this, where you have all the charging available in a designated area. I have never had any problems with charging and the battery on the machine is more than enough to do the tasks I need.”
THE FUTURE
Flannery’s Chris Matthew said, “Since we have been able to analyse the performance of the Faresin telehandler, we now know what type of activities and use cases are suited to the machine. With this information to hand, we have been able to show more customers how they can adopt electric machines, which has led to us increasing our fleet to six units. All of these machines are now connected assets, thanks to the work Faresin and its UK dealer, GGR Group, has done to make the data readily available to our equipment management platform provider MachineMax.
“As we continue to collect and analyse more data, we will also be able to look at fleet purchasing decisions based on real-world activities. This will influence the different battery options from Faresin and, of course, decisions around the purchase of new products in its pipeline. There is definitely a place for electric machines in our fleet mix. That is why we will continue to work in partnership with manufacturers to feed back what our customers’ needs are and how future product developments can support them.”
With zero and ultra-low emissions machinery and vehicles helping to create new infrastructure, it’s fitting that National Express West Midlands has already been running the first of a fleet of zero-emissions buses on the route, which will, in the future, include hydrogen-powered vehicles.
Left, far left and inset: Operator Happy Singh reports that the power is instant, but handling-wise it’s very similar to a diesel-powered machine.
MANUFACTURER’S COMMENTS
Faresin’s product specialist Nicolae Manea said, “Inside the cab to the right of the operator we have a series of buttons that control some of the key functions like the parking brake and Eco or Power operation. The operator can also control the fl ow, boom suspension and fl oating boom features, as well as the LED lights. The joystick mounted to the right-hand side of the cab has a toggle switch for forward, neutral and reverse, and these functions can also be accessed from a lever on the left-hand side of the steering column.
“Embedded into the right-hand side of the dashboard is a 7in LCD display, which shares general information on the hours worked, the charge on the battery and any alerts. It also links to the rear-view camera. Right in front of the operator we have mounted our anti-tipping system display. Using LED lights, this system automatically calculates the load on the front of the machine that is either being carried or lifted. Particularly for lifting, this system alerts the operator to ensure they keep within safe operation.
“We now have a 330Ah, 440Ah and our new 560Ah battery options. They can all be charged from our built-in charger. We have both standard and fast charger options, depending on what charging levels are required. For fast charging, you can charge the battery between an hour and two hours, depending on its size. But for Morgan Sindall on this project, they simply parked up the telehandler and plugged it in when the machine was not operational, topping up the battery throughout the day.”