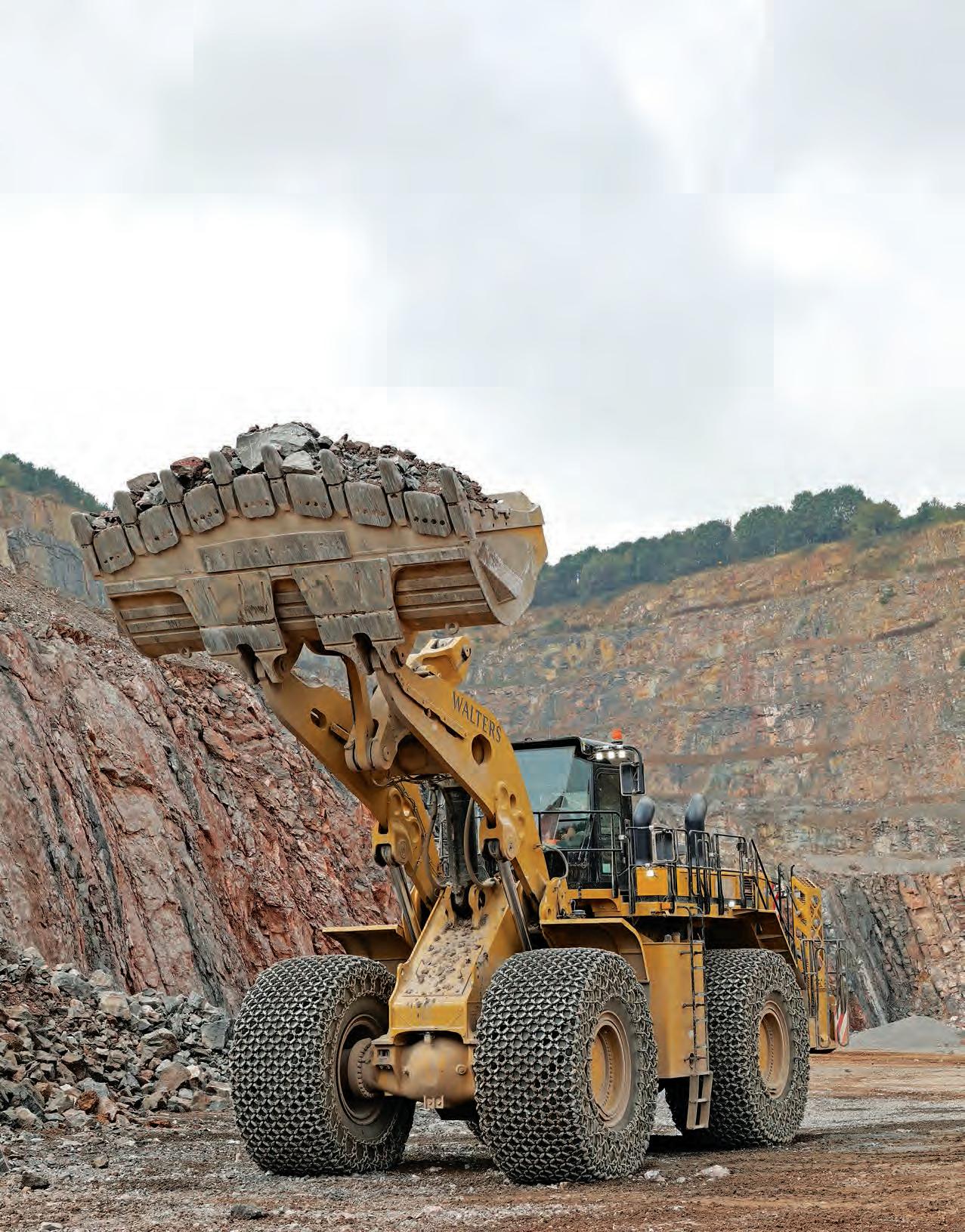
14 minute read
EXTREME MACHINE
DRIVING DOWN TOTAL COSTS PER TONNE
David Wylie visits Hanson’s Whatley Quarry in Somerset to see the fi rst 105-tonne Cat 992 wheel loader in the UK, which is owned and operated by the Walters Group
Advertisement
Based at Aberdare in South Wales, with offi ces across the UK, the Walters Group was founded in 1982. The group’s fi rst Caterpillar machine was a D4D dozer, bought from local dealer Bowmakers in Cardiff. Today, Walters operates what is reported to be the largest independently-owned heavy plant fl eet in the UK. Their on-going investment plan covering 2021 to 2023 is for around 300 large machines, resulting in an estimated £100m spend with Cat distributor Finning.
The Walters Group operates across many industry sectors, and some of its largest machines work in contract load-and-haul quarry applications on behalf of the UK’s major aggregate producers. The client base increasingly demands reduced emissions, improved fuel consumption, greater levels of productivity and the highest levels of site safety – all while trying to minimise the cost per tonne delivered to their crusher.
Below: The fi rst new generation Cat 992 wheel loader in the UK is on the fl eet of the Walters Group, working on their load-and-haul contract with Hanson Aggregates in Somerset.

THE IMPORTANCE OF TYRE CHAINS
The new Cat 992 at Whatley Quarry has been fi tted with Pewag Square Tyro 18 tyre chains, which are ideal for this limestone application. The same chain type is fi tted to their old 992G and have now recorded an astonishing over 23,000 hours of use. Apparently, a few links and rings break now and again, but even with this extended lifespan they are still serviceable.
The second 992, currently being commissioned for the Walters Group contract at the Bardon Hill Quarry in Leicestershire, will be fi tted with Rud FELS Granit Plus X 23 tyre chains. Walters has successfully used Run chains in this granite quarry since they started working there in December 2012.

Below, right and far right: This Cat 992 is currently consuming diesel at a rate of between 80 to 85lph, compared with 120lph from an older 992G model that previously undertook this application.
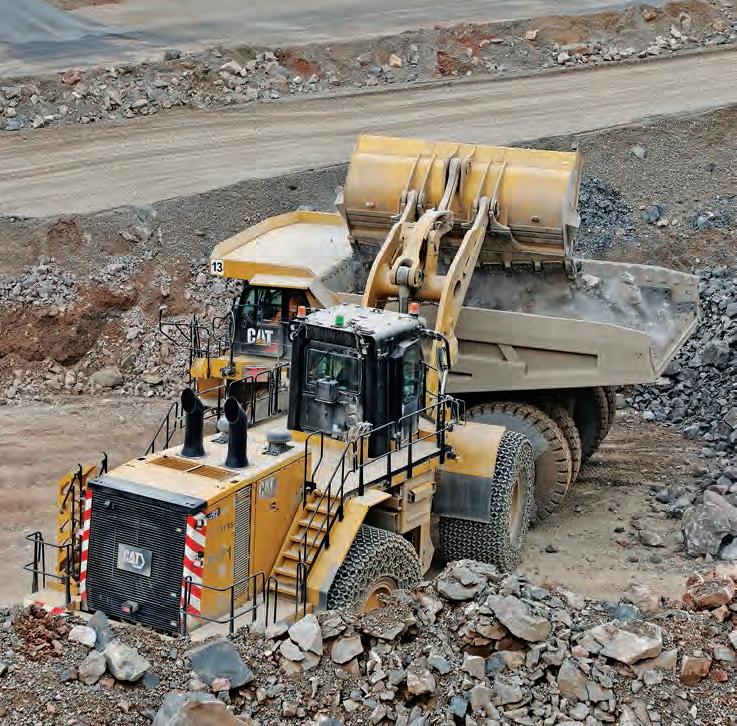
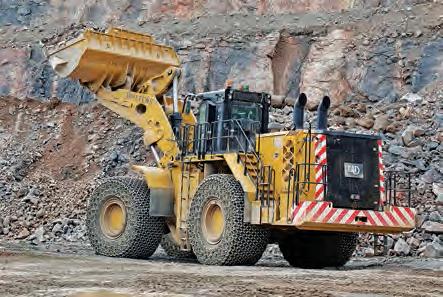
WHATLEY QUARRY
The limestone reserves in the east Mendips area of Somerset are considered a nationally signifi cant resource, serving major infrastructure projects such as Hinkley Point C and HS2. The Whatley Quarry has been operating since the 1960s, supplying crushed limestone aggregate to local markets by road, in addition to bulk shipments to depots in London and south-east England via a dedicated rail head.
Situated between the villages of Mells and Chantry, four miles west of Frome, Whatley is Hanson Aggregates’ largest quarry, currently producing up to six million tonnes of material a year. Within the 173-hectare site there is a ready-mixed
Above and below: The new Cat 992 replaced a mono-boom Cat 992G model with 24,600 hours on its clock, which is now a standby machine at Whatley Quarry.


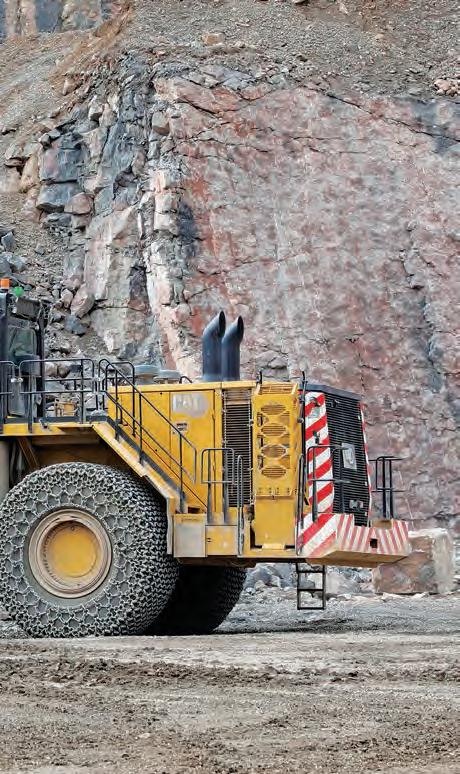
concrete plant and an asphalt plant, where the majority of the limestone extracted on site is consumed. The quarry area itself covers some 120 hectares and holds estimated reserves of a whopping 100m tonnes.
The Walters Group was originally awarded a load-and-haul contract with Hanson for their fl agship Whatley Quarry in 2013. This resulted in a signifi cant investment by Walters in a fl eet of new equipment to serve this project, including Cat 992G wheel loaders, Cat 777 quarry dump trucks, together with a Cat 390 excavator and a range of smaller auxiliary equipment. Walters’ operators used this fl eet to deliver more than 5m tonnes per annum to their client’s primary crusher, which operates on futuristic mono-boom, replaced by a continuous choke conventional Z-bar linkage arms. The feed basis over two working method at the face of Whatley shifts. It is estimated Quarry is ultra-effi cient V-pattern loading, that over the six years which places much stress on the rightof this initial hand side of the bucket, as the wheel contract, Walters loader turns into the pile of blasted hauled over 32 material. On the mono-boom 992G, these million tonnes forces act upon a single bucket pin and, of limestone. more expensively, on the single boom pin. The renewal A replacement boom pivot pin for of the Hanson a 100-tonne Cat 992G costs an astonishing contract in £30,000, plus rebushing and associated 2020 resulted in another labour costs. signifi cant investment by Walters. In addition to upgraded site offi ce and OPERATOR FEEDBACK welfare facilities, it included fi ve new Walters’ operator Shane Grant has been Cat 777G haul trucks, together with what working on this site since 2018, initially on would turn out to a Cat 966 loader be the fi rst new before stepping up generation Cat 992 “WHATLEY IS HANSON to the 992G. He said, wheel loader in the UK. AGGREGATES’ LARGEST “The new 992 is a brilliant piece of LARGE WHEEL QUARRY, CURRENTLY equipment and the best wheel loader LOADERS PRODUCING UP TO SIX I’ve ever driven by A stand-out feature of Walters’ working MILLION TONNES OF far. It has amazing performance and method at Whatley MATERIAL A YEAR” digs really well; it has Quarry is their use lots of power to get of a large wheel loader in addition to the job done. The cab is exceptional too, a mining class excavator to feed the fl eet as it’s a lot bigger than the previous 992G of quarry dump trucks. In other parts of model. It’s very well laid out for the the world, including North America, operator and the three big LCD screens a wheel loader is the preferred loading cover everything you need to know about method, but it is relatively rare to see machine health, payload management one in such an application in the UK.
The two main advantages of using a wheel loader over an excavator are much greater mobility and the reduced need for support machines. Using a wheel loader, the operator can be far more selective on how to manage a face and far more easily move from one face to another, or get quickly out of the way for a blast. More importantly, a wheel loader has the ability to clean up after itself, virtually eliminating the need for a dozer and operator to remove any spilled rocks and maintain the pit fl oor. The Walters Group currently runs fi ve THE RIGHT BUCKET FOR THE JOB 100-tonne class wheel loaders from the Cat 992 family, not only in quarry applications, but also to load hot slag in a steel works. Much consideration was given to replacing the original 992G at Whatley Quarry with an updated 992K model. However, with a brand-new design from Caterpillar on the near horizon, which promised signifi cant fuel and maintenance savings, the decision was taken to wait until the all-new 992 model was in production. The most signifi cant design change in the 992 over its immediate predecessors Both Walters’ 992s have been specifi ed with Cat’s new 12.2cu.m bucket, which features a dual radius shell plate design, allowing the centre of gravity of the full bucket to be pulled back, providing improved stability and material retention. The standard bucket is reinforced with horizontal and vertical Hardox steel plates at Walters HQ depot at Hirwaun. Regarding wear parts on these two new loaders, Walters has progressed from the K-series to the new Cat Avensis tooth and shroud system. is its working equipment. Gone is the
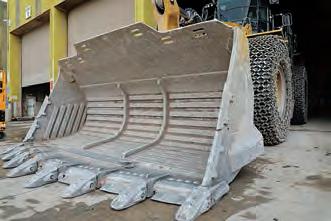
Left, below and far right: Operator Shane Grant states that the Cat 992 is a brilliant piece of kit, which has amazing performance and lots of power to get the job done.
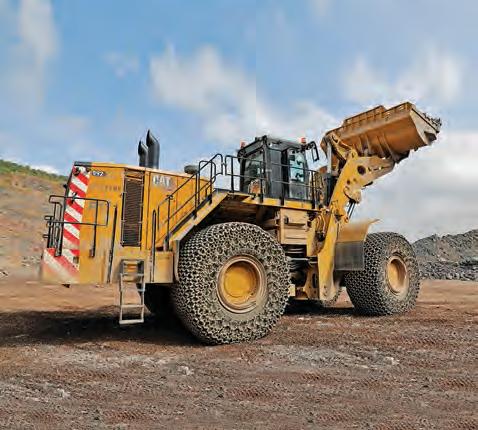
and 360-degree camera systems. The visibility through the larger front screen is outstanding, as is the smooth joystick steering and lightweight controls for the front-end equipment.”
Shane feels the new design of lift arms has actually improved his visibility, as he’s now looking down on the bucket during the dig phase, rather than looking along the mono-boom. He reports that the most noticeable performance difference is muchimproved stability at full reach: “Stability and lack of sway of the lifting arms on the new 992 is in a different class compared to the old 992G. It’s just so much better and therefore more pleasurable to drive; I absolutely love operating this new Cat 992.”
Shane explained that he received fi rst class training from Finning’s John Blackett on the all-new 992, which has a host of features to help the operator get the best from the machine. This includes an integrated payload management system, where the contents of every bucketful of material is weighed. This helps to achieve the optimum number of passes to consistently reach the target payload of the haulers. Shane reports that, if the shot material is well fragmented, he can load a Cat 777G hauler in just four big
“STABILITY OF THE NEW passes, but most of 992 IS IN A DIFFERENT the time its 95-tonne target payload is
CLASS TO THE OLD 992G. achieved in fi ve quick IT’S JUST SO MUCH BETTER passes, taking a total of 2.5 minutes.
AND THEREFORE MORE In addition to the PLEASURABLE TO DRIVE” 992 wheel loader, Walters’ contracts manager Jon Lisk also has a new Hitachi EX1200 excavator deployed at Whatley Quarry. Three of the fi ve Cat 777G haulers are usually assigned to the wheel loader, while a pair serve the large excavator. However, when working with a well-fi red blast on a wide bench, Jon will switch one of the haulers from the excavator to the 992, as the big wheel loader will keep four trucks busy all day long in such conditions.
DATA-DRIVEN DECISIONS
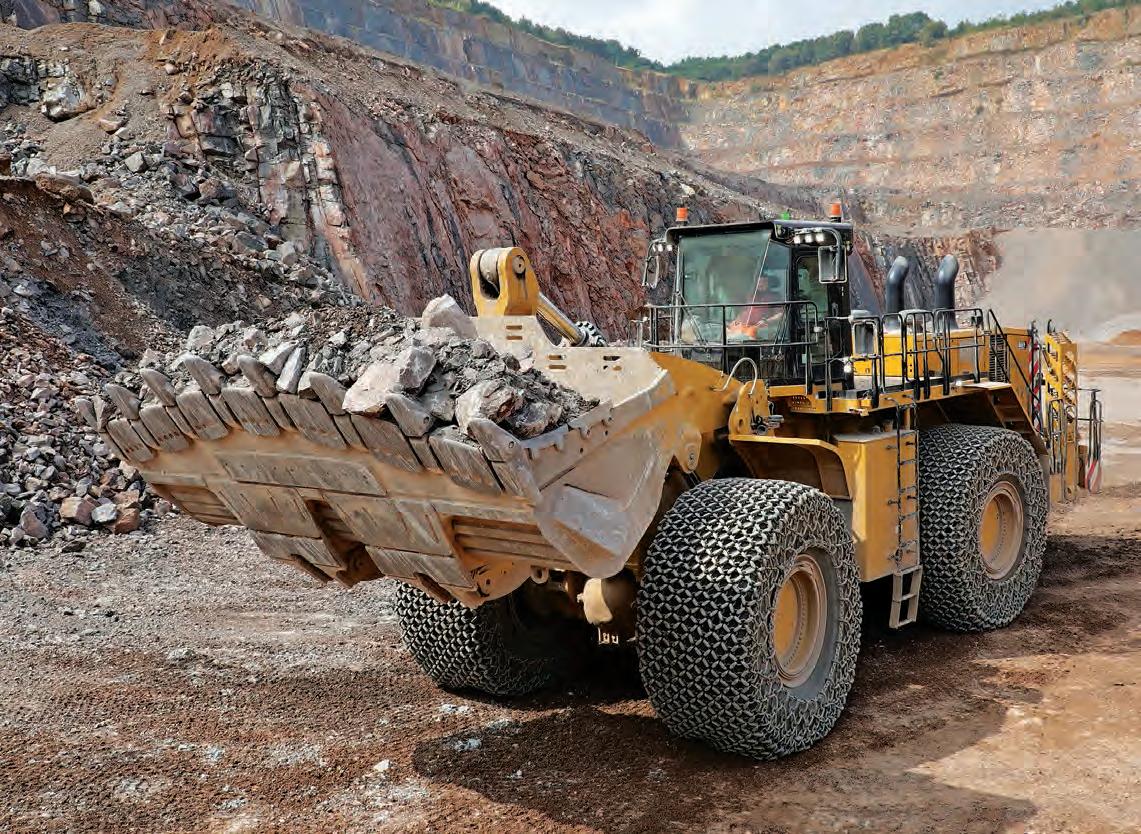
The Walters Group has 40 years of collective experience getting the most from heavy plant, but nowadays this is supplemented by a host of data.
Jon uses Cat’s MineStar system to help manage the connected fl eet and monitor production from detailed daily reports and a weekly summary, which are automatically generated and sent to his laptop. In conjunction with MineStar, Cat’s VisionLink system is used to monitor machine health.
But this is just the start of the process, as the Walters management team has carried out regular appraisals of individual aspects of their work at Whatley Quarry over the years.
This covers working cycle analysis including waiting times, payload optimisation, haul road condition/ maintenance, together with plant availability and use.
The use of dynamic site modelling allows them, for example, to optimise hauler payloads according to local conditions and topography, while minimising waiting times and long-term maintenance costs.
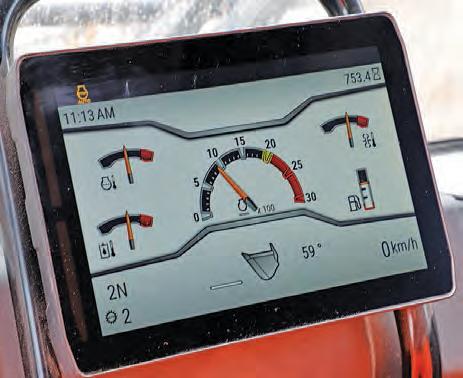
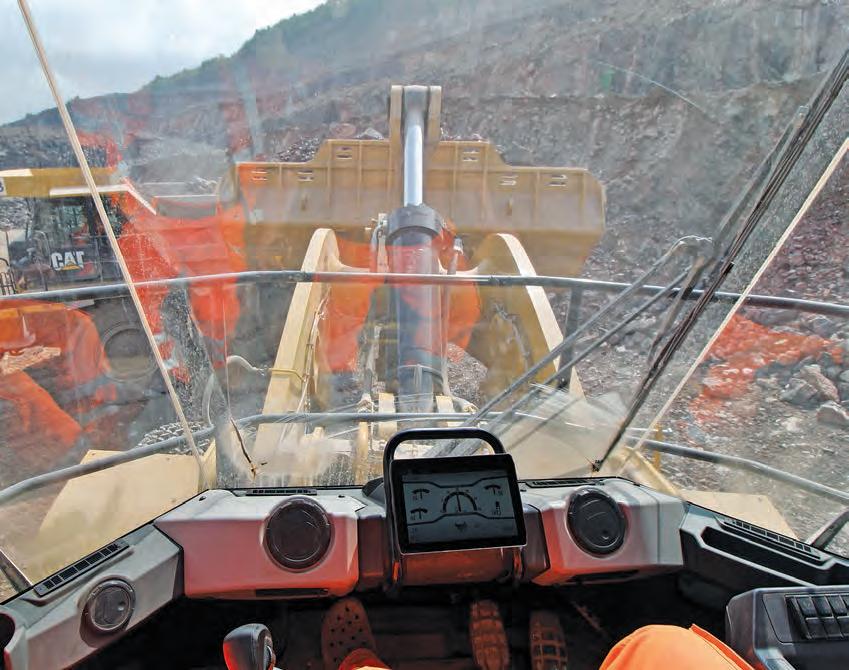
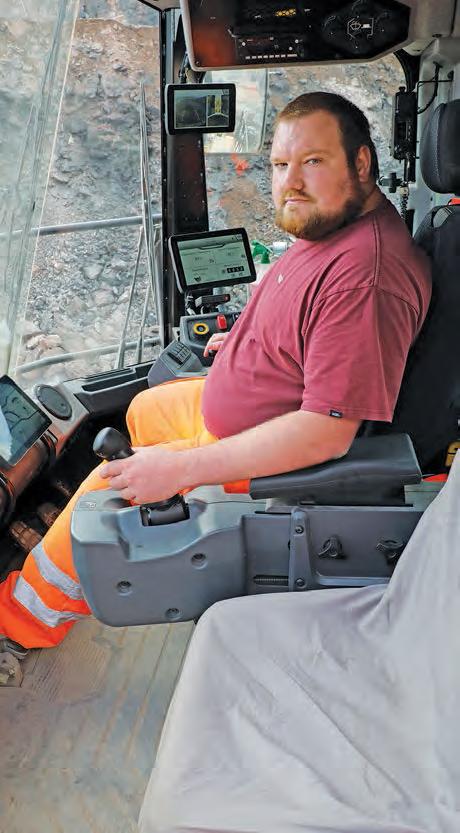
Such a data-rich environment also helps the management team judge the practical impact of such massive investment decisions. For example, they discovered that, in well-blasted limestone, the 992 was around 30 seconds quicker than a 992G to load a Cat 777 dump truck. Even more if the big loader is used somewhat more aggressively to four-pass load 95 tonnes. Over a multi-shift working day, this adds up to around an extra hour of productive time that, on a long-term load-and-haul contract, is of critical importance to the senior management of both client and contractor.
Obviously, one key data set is fuel consumption from the Stage 5 ultra-low emissions Cat engines fi tted to the new haulers and wheel loader. Jon is pleased to report that the new 777G haulers, delivered earlier in 2022, have an average consumption of 45 litres per hour.
Below: There is good visibility to the working area from the operator’s seat, within an over-sized cab with all the latest creature comforts and productivity aids.
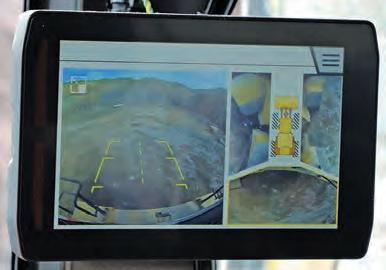
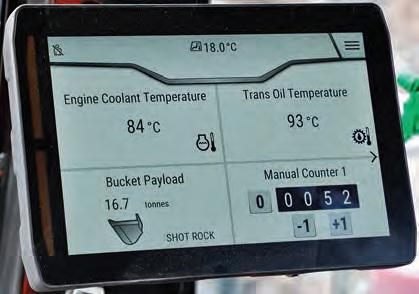
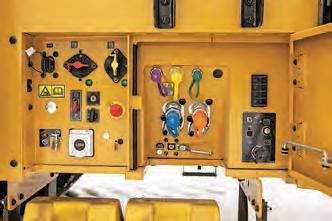
CAT 992 BRIEF SPECS
As well as a radical change of front working equipment, the new Cat 992 wheel loader features a complete redesign of the front and rear frames. Together with a new cab, Caterpillar claims that only two main components are shared with the previous 992K model: the tyres and the engine block. Even the wheel rims are diff erent, to fi t on the heavier-duty axles.
The 992 wheel loader is powered by the latest Stage 5 ultra-low emissions Cat C32B engine rated at 814hp. Together with enhancements to the transmission, axles and fi nal drive, these driveline components are designed to deliver a 20% longer lifespan between planned replacement. Naturally these days, routine service points are safely accessible from ground level.
The 105.8-tonne 992 has gained six tonnes in weight over the previous 992K model, principally thanks to more durable components, which help to better balance its increased payload for improved stability. The tipping-to-weight ratio has increased from 53% to 58% on the standard lift arms of a 992 compared to a 992K, and from 49% to 53% on the high-lift arm variant. This is because the centre of mass of the machine as a whole moved backwards, also improving the machine’s overall stability.
Over 6000 examples of the Cat 992 family have been sold since it was introduced in 1968, making it the most popular large mining wheel loader model of all time. The latest 992 model sets new standards of productivity, plus reduced maintenance costs, off ering up to 48% greater payload fuel effi ciency than the previous 992K model.
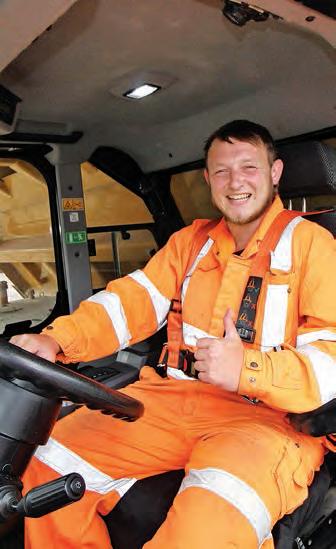
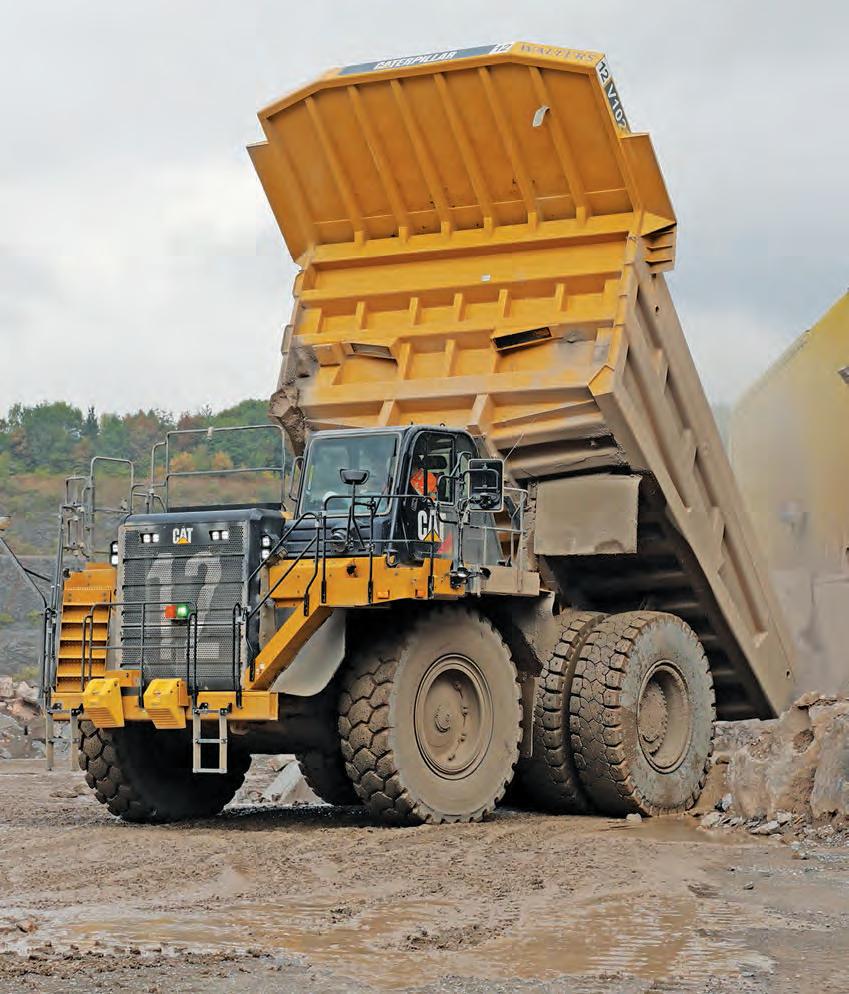
OPERATOR FEEDBACK: CAT 777G
In the cab of the latest Cat 777G, (fl eet number 12) is Tyler Pole who said, “The latest 777G is a really nice truck to drive and the repositioned driver’s seat, closer to the door and nearside mirror, provides better visibility for spotting the truck under the 992 loader. This new truck also has everything you could wish for and more: a quiet and comfortable cab, plenty of pulling power on the ramps and loaded with good driver aids, such as its front and rear camera systems.”
Spill boards have also been added to the skips of the new 777Gs to help obtain a more consistent 95-tonne payload in this limestone application. The Walters Group has also gone to the considerable expense and time of rubberlining the skips with 120mm-thick fl oor, side and headboard mats to help keep noise and vibration levels low, both for the benefi t of their operators and the local community.
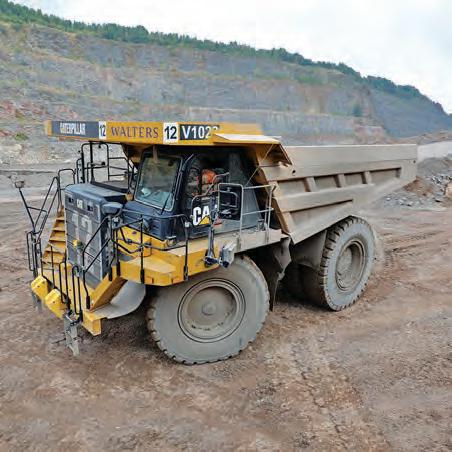
This represents a 15% to 20% improvement over their 2013 versions of the 777, which burn 50 to 55lph. Now with 750 hours on its clock, it is beginning to look as if the new 992 wheel loader is living up to the rather astounding claims made by Caterpillar regarding its projected fuel consumption, which is currently an exceptionally low 80 to 85lph. This compares to an average of around 120lph from their 24,000hr 992G model, which was treated to a replacement engine at 14,000hrs. That’s a huge fuel saving on a machine that is working 18 hours a day. A clean-burning engine that consumes less diesel also represents a signifi cant reduction in carbon emissions.
A second new Cat 992 is currently being commissioned by the Walters Group for their long-standing load-and-haul contract at the Bardon Hill granite quarry in Leicestershire. Jon concluded, “While it’s early days, fi rst impressions of the new 992 are good; it’s meeting our high expectations in terms of extra performance, quick duty cycles and signifi cantly lower fuel burn than our previous Cat 992G model. Of course, one element that is equally important is we’ve got an excellent team of competent, well-trained and enthusiastic quarry face operators to extract the maximum performance from the machine, which has been well received by them.”