
6 minute read
TOP TEAMWORK
Having recently upgraded its harvester and forwarder to the latest Ponsse specifications, Eoghan Daly revisits Tottenham Timber and discovers a productive machine pairing working on large volume clearfell contracts
IMAGES EOGHAN DALY
Advertisement
Despite the company having broad interests that embrace forestry consultancy, timber sales and marketing, coupled with the supply of animal bedding and forest residue-based products, timber harvesting and extraction have always been crucial activities for Tottenham Timber Ltd. While this aspect of its operation has been served by a variety of different machines since the company was established in 2003, the most recent machine choices have seen standardisation on units from the Finnish manufacturer Ponsse.
Having upgraded its two original Ponsse machines to maintain the highest levels of performance and reliability, Robin Tottenham of Tottenham Timber remains extremely upbeat about his past and present experiences with Ponsse forest machines. This high level of approval is based on a range of factors, not least of which is the level of performance they are capable of delivering in tandem with positive aftersales service and strong resale values when it comes to machine replacement.
Now in his sixth year using Ponsse machines, the initial Wisent came when a Timberjack 1110 stepped aside as the company’s front-line forwarder. Since then, faith in the marque has become even stronger, and when the move came to become self-suf cient in conducting harvesting too, the choice was relatively easy, as Robin Tottenham explained, “Based on the reliability of my rst Ponsse machine and the service we got from the manufacturer whenever problems did arise, looking beyond Ponsse when I was in the market for a harvester was not an option. To reduce the cost involved, I decided a used machine was the best approach, and in 2020 took delivery of a Ponsse Ergo harvester with an H7 harvesting head.”
Running the machine along with his existing Ponsse Wisent forwarder, Robin continued focusing on clearfell harvesting mainly in Counties Clare and South Galway, which is an area known for its challenging terrain. Nevertheless, the machines coped well with the challenges presented, as Robin continued, “The used Ergo was the rst 8-wheeled model of this machine to go into service in Ireland and proved very effective for us. I like the whole Ergo concept, and even with 12,000 hours worked, this machine was still very productive, with the main factor driving my decision to upgrade being the need to run a larger harvesting head since tree volume seemed to be increasing in many of the clearfells we are harvesting.”
Two Of A Kind
With his rst pair of Ponsse machines working particularly well, Robin was mindful of the need to take the longer-term view and not hold onto the machines too long, despite their exemplary service. In addition, the approaching upgrade was used as an opportunity to achieve an even greater level of machine speci cation re nement to ensure the most ideal match with his harvesting needs.
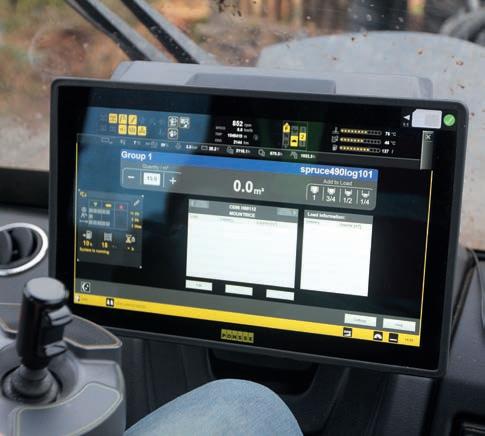
Even though both replacements occurred during 2022, they were conducted on a phased basis, with the forwarder receiving priority status as he explained, “The Wisent had worked 7,000 hours and was a very reliable forwarder for us. Based on the need to increase productivity in larger clearfell sites, we decided to upgrade to the higher size class of the Buffalo, which is a much more powerful 6-cylinder machine with greater tractive force, load capacity and a more powerful crane.”
In contrast to the former Wisent, the Buffalo, which coincidentally is Ponsse’s biggest selling forwarder worldwide, offers greater power through a 6-cylinder Mercedes-Benz OM936 LA Stage 5-compliant engine that develops a power output of 210kW. However, the machine’s real advantages lie in its greater load capacity and higher tractive force, which make it a very attractive machine while it still remains relatively compact with a favourable unladen weight to payload ratio, and remains essentially terrain-friendly, as Robin explained. “John, who operates the new
Buffalo, is really impressed by how well it performs on wet ground. It’s as groundfriendly as the Wisent, even though the Buffalo has much greater load capacity.”
Deciding to specify the machine with standard non-balanced bogies, the option of the long rear bogies was also resisted based on the belief that the machine in standard con guration was a better all-round extraction solution. With the machine’s double extension K100 crane, a wide working range is afforded, which comes into its own, especially when stacking on road verges off the adjoining embankment.
While the Buffalo may meet with both owner and operator approval, positive operator reaction to the Ergo harvester also comes as a major endorsement of the machine’s design, speci cation, and working capabilities. Operated by Adrian O’Donoghue, who has served as an operator on the previous generation Ergo with Tottenham Timber and could immediately see major improvements that culminate in greater output. While this may be encouraging, of even greater signi cance are Adrian’s views on the design format of the Ergo harvester.
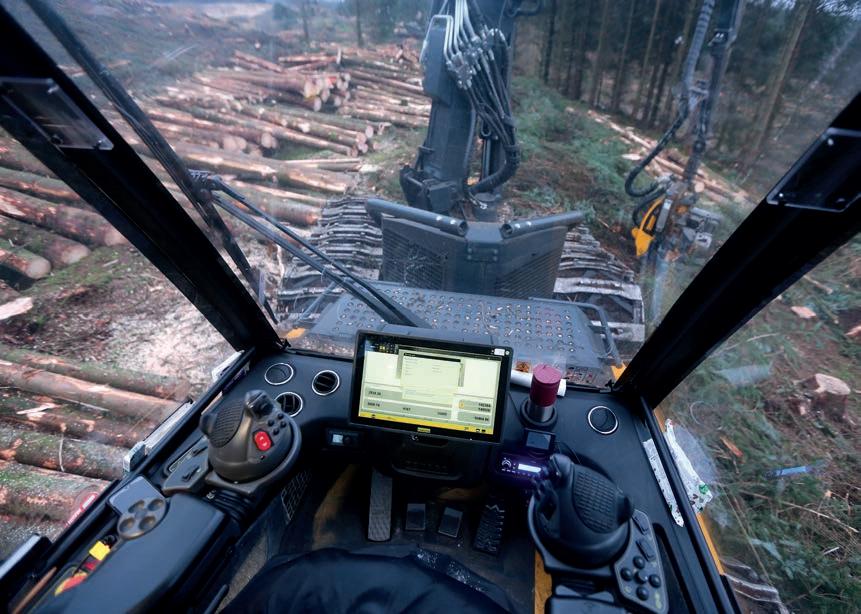
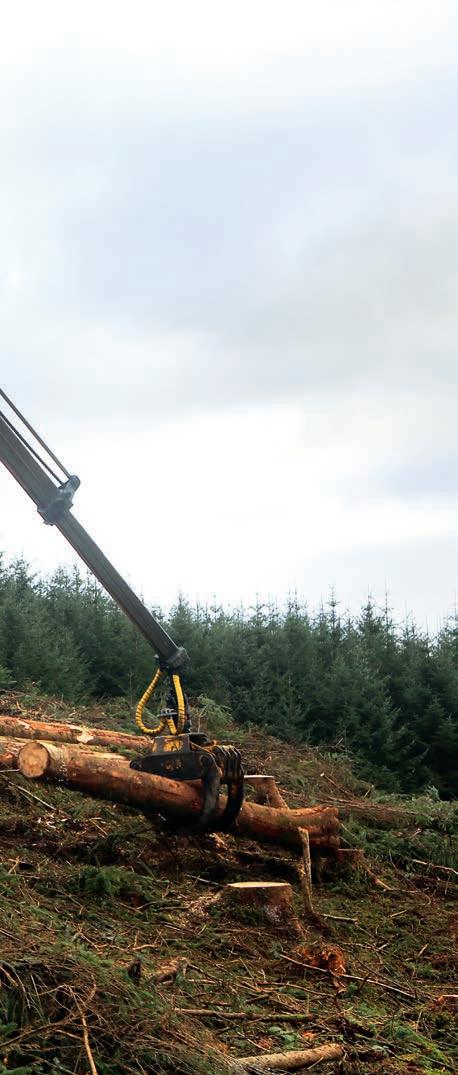
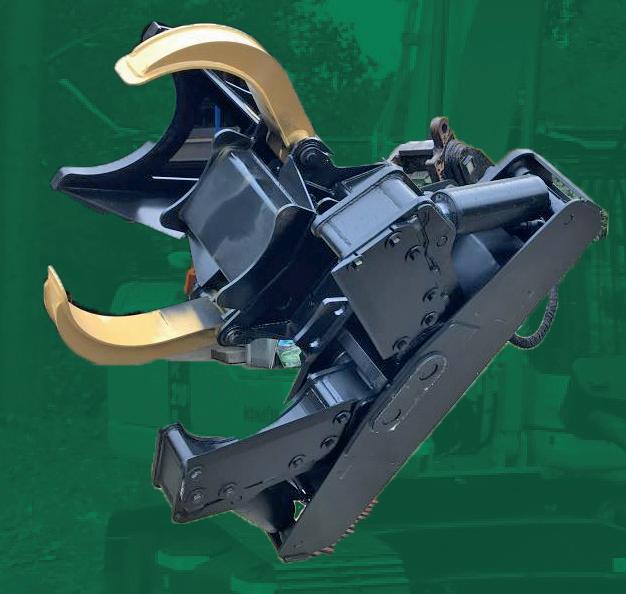
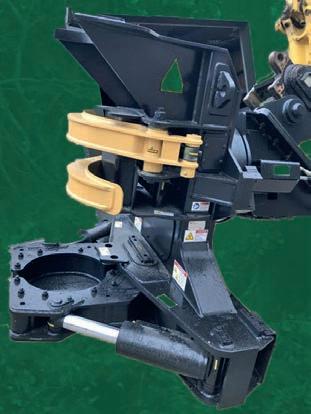
Prime Position
Having worked with other contractors in the past using harvesters such as Komatsu, some may view the Ergo’s cabin position as being unfavourable due to its positioning at the opposite side of the articulation joint to the crane, leaving it quite a distance away from the business end of the machine. In defence of the Ergo design, Adrian admitted it took time to adjust, but once accustomed to the design, there are no real shortcomings.
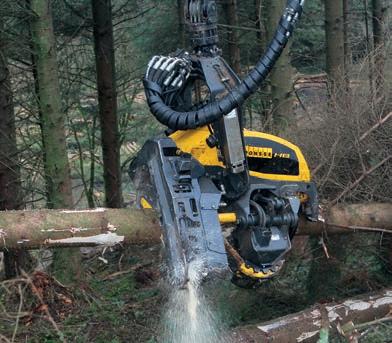

“I have nothing bad to say about the position of the cab on the Ergo. Even though it is completely different from the Komatsus I used in the past, it still has a very good view of the head. The fact that you are a bit further away can have bene ts as the full standing tree can be seen, making tree selection easy. The view of the front bogies is also very good, and there are no blindspots with this cab position.”
However, the real measure of the machine’s capabilities comes in the harvesting of larger volume trees in clearfell applications on challenging ground conditions. At the time of our visit, the Tottenham Timber harvesting team was engaged in the harvesting of an 8,000m3 Sitka Spruce stand with an average tree size of 0.65 at Snaty near Broadford, County Clare, for Glennon Brothers Sawmills.
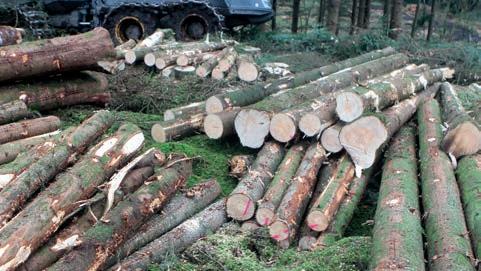

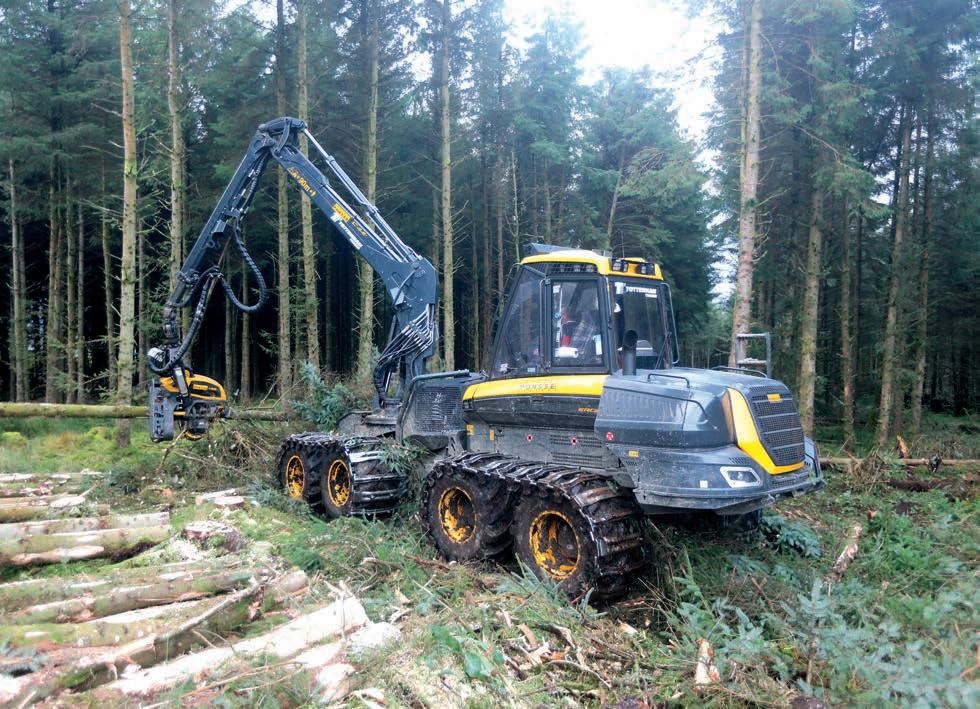
Located on a relatively dry elevated site with a thin skin of peat on the surface, the site had been deep ploughed at establishment, with the ploughed ribbons running across the slope making the ground relatively rough to travel and adding to the importance of laying out the brash mat to compensate for the deviations in the terrain. With the Ergo tted with combination band tracks on both front and rear bogies, its climbing ability and otation characteristics were greatly enhanced.
“The Ergo is a very well balanced and stable machine that allows me to use the full reach of the crane,” Adrian said. “Even when taking down bigger heavily branched edge trees at full reach, it stays rmly planted on the ground. It’s a big plus to be able to use the full range of the crane and means there is plenty of brash, which helps the forwarder travel the site so much better.”
Nevertheless, the real measure of the machine’s capabilities is the power of the crane. The overall geometry of the crane, coupled with its base design, assist in delivering fast and powerful movements with the reassurance of prospective long-term durability. Selecting the C144+ parallel crane option over the alternative C50 sliding boom crane variant based on several key factors, this expectation has proven correct, as Robin noted, “Even though I do like the C50 crane, it is more expensive, and I decided in favour of the C144+ that was well-proven on the used Ergo and gives great power and reach.”
Tip Of The Spear
Offered in three possible reach con gurations of up to 11m, the 10m version was seen to give the best combination of reach without compromising on performance, as it has shown to allow full exploitation of the H8 harvesting head’s working abilities. One of the biggest advantages of the upgrade is that it has brought new levels of working capacity to the harvesting operation while offering a high level of feed force without compromising feed speed, with all essential measurement accuracy preserved.
In addition, the machine offers a high level of sophistication and assists greatly in providing comprehensive data on production and machine ef ciency, as Robin emphasised. “I am very impressed by the accuracy of measurement with the H8 head, and the technology the machines offer gives big advantages for monitoring production and machine ef ciency. The Manager 8 system means I know exactly what is harvested and extracted by remotely accessing the system.
Ponsse Ireland also uses the system to schedule machine servicing as we have signed up for a 6,000 service package on both machines, which gives great peace of mind. “Not only do Ponsse design and build excellent forest machines, but they also have premium-level aftersales support to match,” Robin added. “Whenever we need support, the response is very fast, ensuring minimal production losses. The only area that could bene t from possible improvement is addressing the charging of travel expenses to the customer on warranty callouts.”
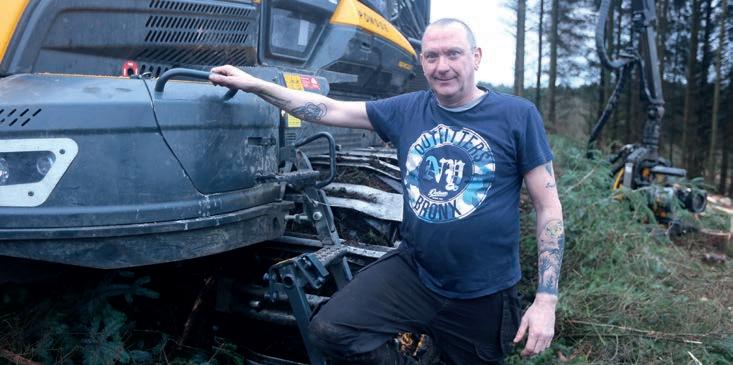
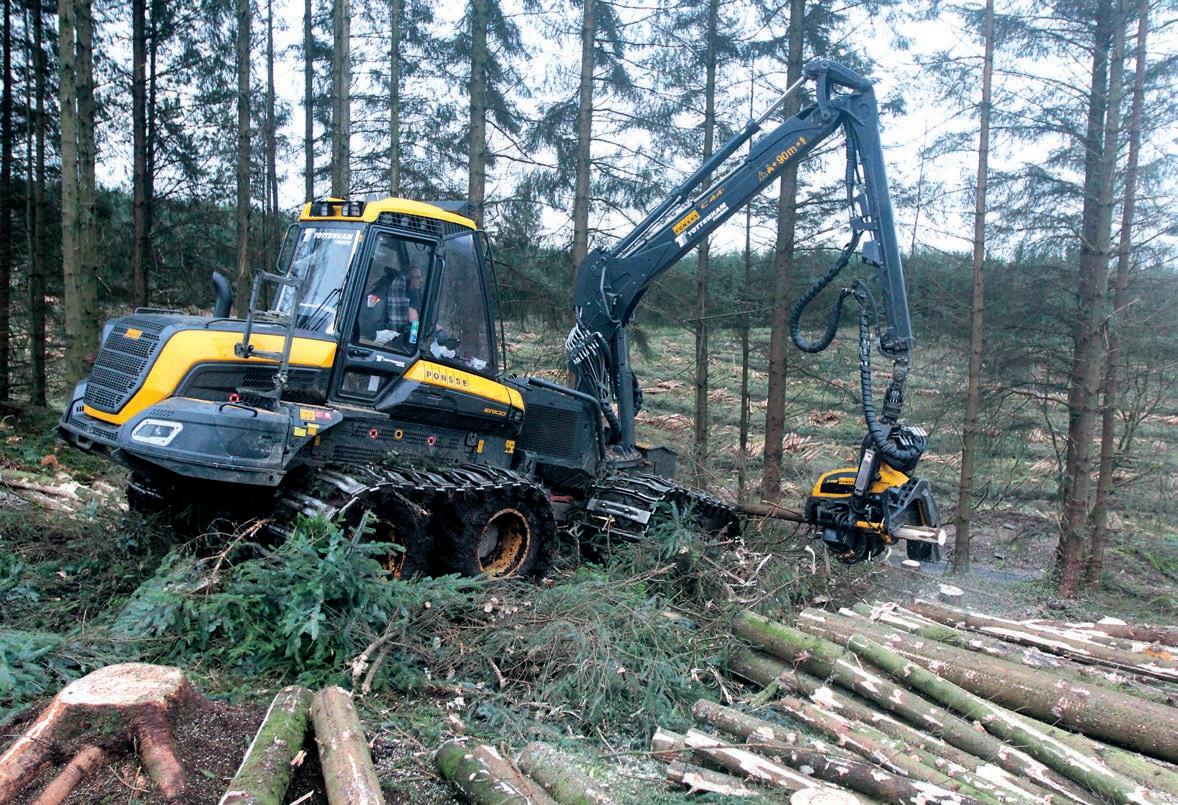
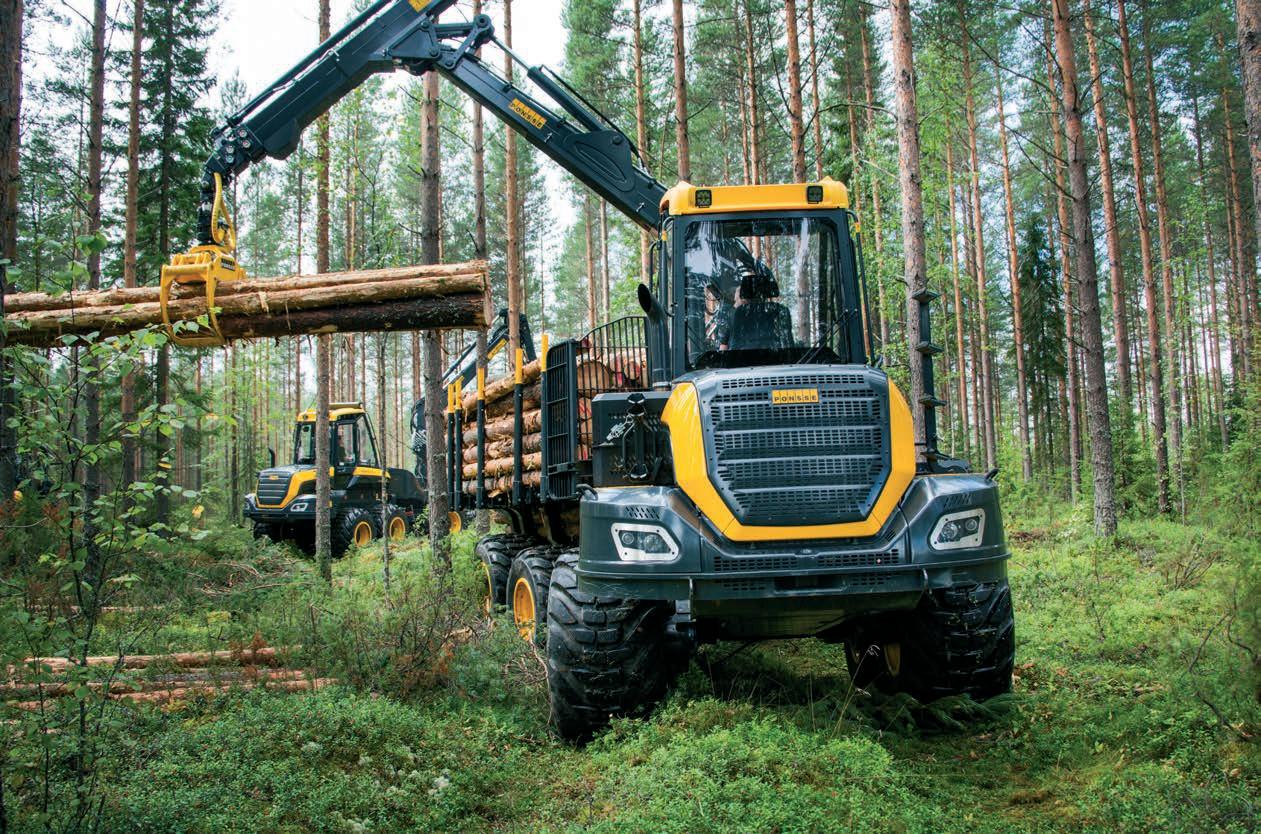
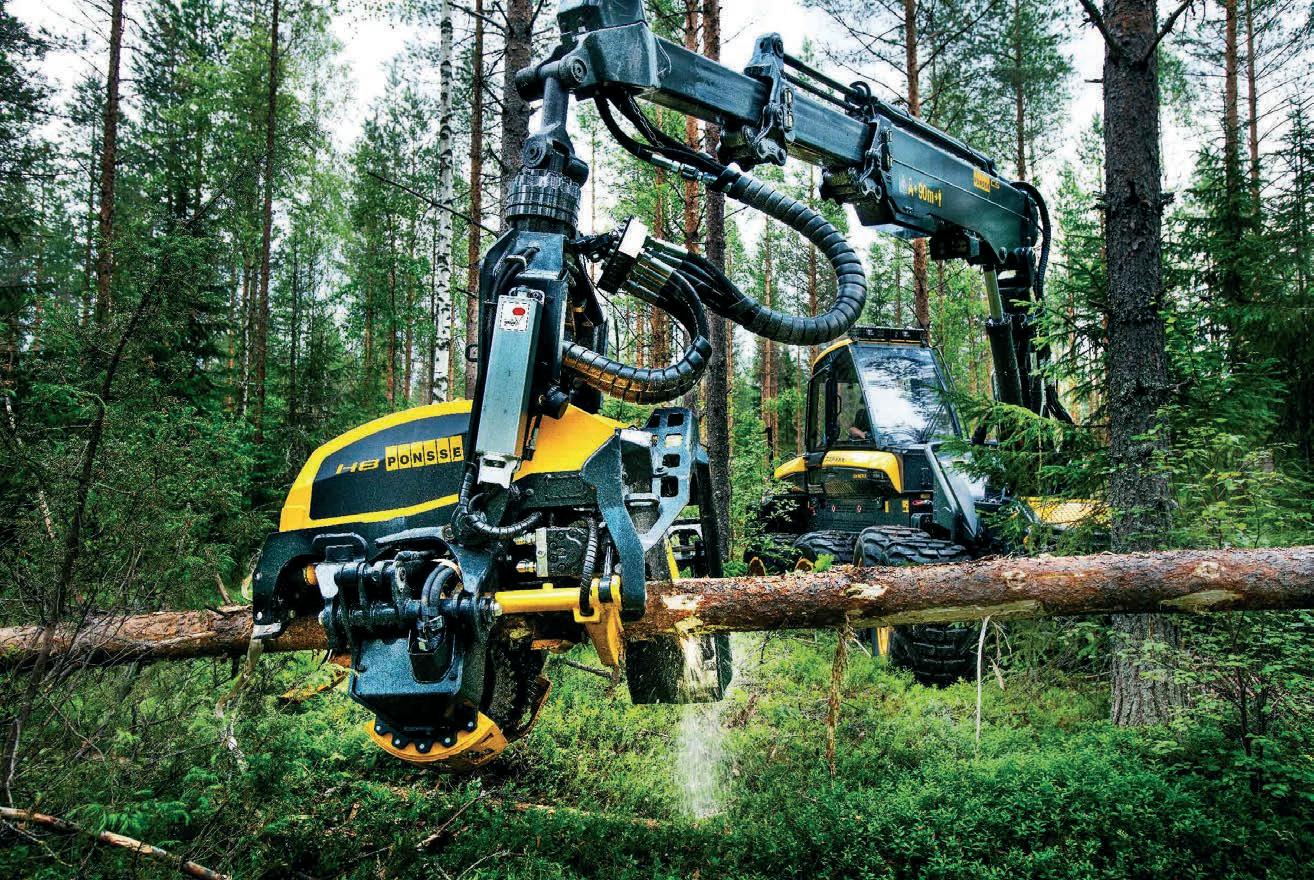