
12 minute read
The Way We Were A retired farmer looks back at beet harvesting and autumn drilling
LEFT: A Fowler Challenger 22, just like the one operated by the Longfoots, pressing on with autumn ploughing with a Ransomes TS69. BELOW: A County crawler could just about manage a set of 10ft 6in Pettit in 4th (2nd high) gear. Left turns were made most of the time as closing the discs for a right turn did not work very well.
beet comes up Corn goes in,
Advertisement
Turning the clock back to the early 1960s, retired farmer Peter Longfoot recalls some of the key machines his family were using to drill winter cereals and lift sugar beet on their farm in Huntingdonshire.
Well, autumn and now winter are upon us once again and the work continues. Back in 1963, the autumn drilling, which had taken place during October and just into November, was wrapped up and, as always, it was a relief to get all the planned winter wheat in the ground. That is except for the beet land which was ploughed, worked down and drilled as the beet was lifted.
It was unheard of to drill wheat in September back then, maybe the winter barley in the last few days of the month, but definitely not wheat. The first wheat to be drilled in early October was on the ‘seeds’ ground that had been worked as a bastard fallow since the seeds hay crop had been taken. If it had remained dry then
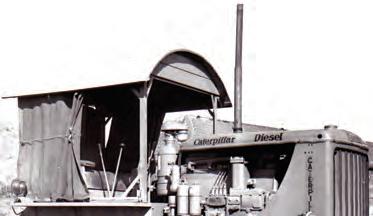
RIGHT: This Caterpillar D7 is like the one that a local contractor used to do some heavy cultivating on the Longfoots’ farm. “Flat out at 1000rpm, it was impossible to rush these old girls, which plodded on at their speed regardless,” says Peter.

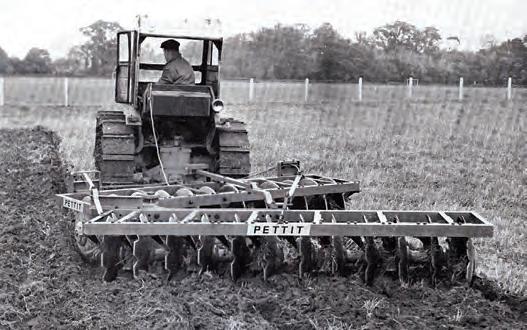
on our farm this ground would have been pulled through several times with an old steam cultivator behind a Caterpillar D7, both owned by a local contractor. These steam cultivators would face anything, no matter how hard the ground. Even the road itself was no contest if the thing happened to drop down on the way to the next field! No one bothered about crawlers running down country roads in those days! If there had been a wet period of weather then the clover in the aftermath from the seeds mixture would have grown well, maybe to over a foot high, and this was then ploughed in. It was first rolled down and care was taken to roll it in the same direction as the
Beet harvesting the mechanised way using a Standen harvester behind a Ferguson TE-20. On level ground and lovely black Fen, soil the job was a doddle, says Peter.
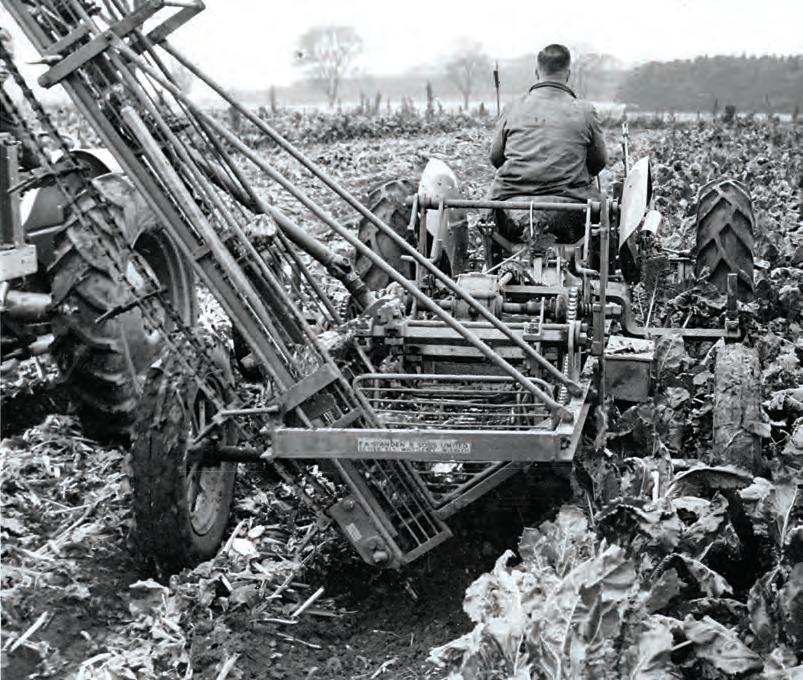
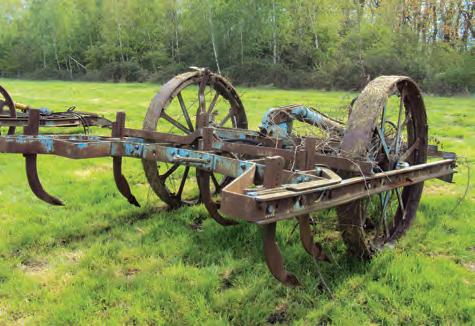
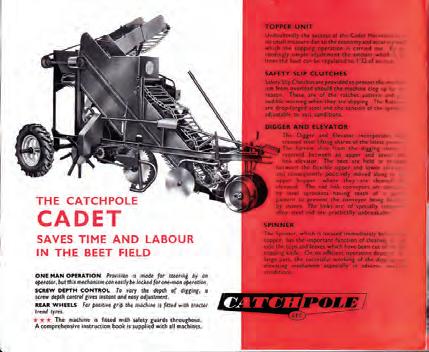
plough was going to take. That way it would go through the plough with few problems, but try going against the rolling and very soon the plough would get bunged-up. All the winter corn land was ploughed and then disced down with a set of 12ft Pettit discs behind a Fordsonbased County crawler. The drilling was then done by a 20-row Massey-Harris 728 drill pulled behind another County crawler.
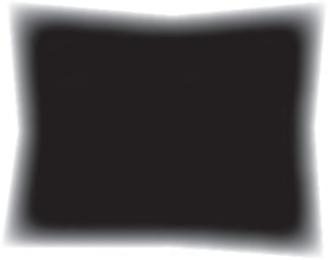
Another major job we had to deal with besides drilling was lift ing sugar beet. About 30 acres of beet were grown then and lift ing it seemed to take forever in those days. In the
1950s the crop was always handlift ed by seasonal labour, which was about as reliable as the weather. When these herberts were on the farm it was father’s continuous job to keep them ‘at it’. The crop was pulled and knocked, the beet fi rst being loosened in the ground by lift ing shares mounted in an old Ransomes tool-bar. Then it was pulled up by the labourers who banged two roots together to knock the soil off . The roots were then laid in a row, all facing the same way, and the tops were chopped off by another person armed with a beet knife. LEFT: Pulled behind a Caterpillar D7 (or D8), an Some of the tops were even loaded IHC TD18, Allis-Chalmers HD14 or even a into the Land-Rover and given to Vickers, these steam-era drags would face the sheep. What a palaver that all anything, no matter how hard and dry the land. was. Nowadays 30 acres of beet is nothing and can be lift ed and BELOW: The Catchpole Cadet sugar beet heaped in a few hours.
harvester was a godsend, notes Peter. “A simple
machine, it saved so much work and the hassle By 1963 the beet harvester with seasonal labour. You soon learnt that the had arrived! A second-hand topping knife had to be razor sharp.” Catchpole Cadet joined the fl eet and what a godsend it was; no more problems with seasonal more problems with seasonal labour. It was now just possible labour. It was now just possible to lift one acre a day, but it had to be a good day! When the harvesting started in early October the Fordson Diesel Majors could cope with the conditions. The start of lift ing depended on the allocation of permits by the beet factory in Peterborough. Whatever happened, a permit could not be missed! Somehow that load had to be delivered because later in the season the issue of these permits could be restricted, especially if there were problems at the factory, which were quite common. As the season progressed, and if there had been a lot of rain, the Majors couldn’t cope. Spud-wheels were tried but the one that ran in the crop
would dislodge the beet and then the topper on the machine just pushed the roots over and didn’t cut the leaves off properly. The Countys came to the rescue again! We had one with hydraulic lift and PTO and that went on the harvester. The track that ran in the crop was cut down to about 10in wide and with another County towing the Major on the trailer the problem was solved. Not quite, because when our clay soil was wet more of it went through the beet harvester than actual beet.
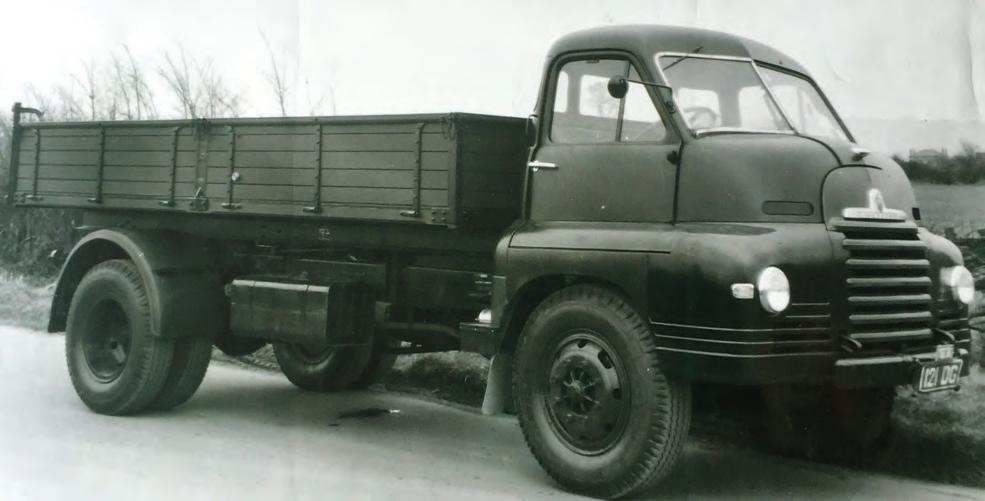
The only way to deal with this was to clamp the beet and wait until it had dried out, then put the whole lot through a cleaner/loader, which got most of the now dry clay off . The soil had to be almost dry before it went through the cleaner/loader otherwise the machine just rolled the set clay into balls and loaded it with the beet. When it was wet, the opal
BELOW LEFT: In the early days of mechanical beet lifting, reference to Catchpole Cadet’s instruction book was advisable, but the machine was so simple to understand it was rarely used.
wheels fi tted to the harvester were next to useless as they just took the beet and soil up in a strip, leaving a small trench where the row of beet had been!
Once the beet was in a heap it then had to be sent to the factory. Right from 1947 our farm had always run a lorry. The fi rst was an ancient Thorneycroft , but that was before my day. The next was a Canadian Ford, complete with fl at-head V8 engine, petrol powered, of course. I can just remember this lorry and usually managed to hitch a lift to the beet factory on a Saturday when there was no school. It had no tipping gear so we had to go through the wash-out, which was always seemed to me to be good fun at the time. With all that wash-out water under pressure it went everywhere and even got in the cab with the windows closed.
By the time all the beet had been washed off , the
During the 1960s, the Longfoots hauled beet to the factory using a Bedford S Type. According to Peter, its Perkins R6 engine wouldn’t start and ran like a bag of nails when ticking over. ABOVE: A 1967 weighbridge ticket from the Peterborough beet factory. The Longfoots’ Bedford S Type truck had a tare (empty) weight of 4t 5cwt and on this load it carried almost 8t.

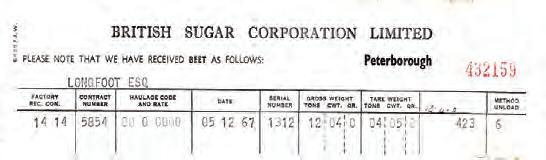
CHOICE OF GRAIN DRILL
After we had been over the ploughing with discs, the winter crops were drilled using a 20-row Massey-Harris 728 pulled by a County crawler. The 20-row version of this drill on steel wheels was too much for a Fordson Major so it was a crawler job (the Majors could only manage a 15-row Massey-Harris 728).
Harrows were always pulled behind the drill but there were times when a cobbly seed bed required an extra rolling and harrowing after the drill, again all done with County crawlers. The corn was always combine-drilled and the fertiliser went down the spout with the seed.
Damp mornings could be a nightmare because the dust in the fertiliser would absorb moisture and then stick to the inside of the drill seed tubes and block them up. It was essential to have a man riding on the drill to watch for problems. If they weren’t spotted there would soon be some missed rows as the blockage would stop the flow of seed too. 20-ROW MODEL The Massey-Harris 728
(20-row) drill had two gearboxes, one for each 10 rows, so there were two trip ropes to pull each time. They were good machines.
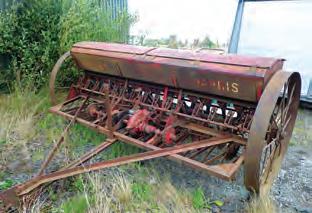
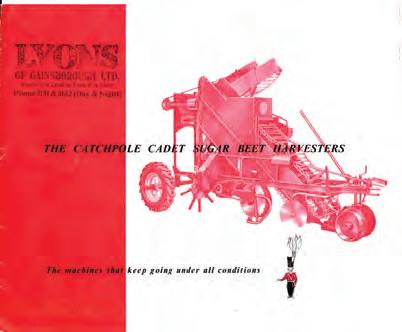

water had found its way into the engine’s ignition system. I wondered why father always had plenty of revs on! Sure enough we would limp out of the torrent of water on anything from four to six cylinders. Six out of eight wasn’t too bad, but with four cylinders out, power was a bit short. There was no point fl apping so we would just pull to the side and sit and wait until the warmth from the engine had dried out the plugs and wires. When the engine went back to at least seven cylinders we were away. At no time was the engine stopped on purpose. You have to remember these Ford V8s only had 6v electrics, which struggled at the best of times, never mind with wet plugs.
When Father decided that petrol had become too expensive, a big move up was made to a diesel lorry. Various makes were tried but it was a big Bedford that replaced the old Ford. The lorry was up to the usual Bedford standard but its Perkins R6 engine, oh dear, what a pain. It might decide to start on a warm summer’s morning, but in the winter beet season more times than not it refused point blank to start before the batteries were run fl at.
Once warm it was OK, and this lorry had hydraulic tipping gear so there were no more trips through the wash-out. Another feature of the Perkins R6 was that at tick-over it rattled the lorry so much that if the doors were left open they gave every impression that they were going to fall off .
So this is how it went. The vehicle was loaded the aft ernoon before the day the permit was due. Now when I say loaded, I mean loaded. The plan was that as long as there was a gap between the rear tyres and the mudguards you kept piling the We ran an army of County crawlers, the first being an E27N Major with a Perkins P6. Father bought complete tractors, parts machines and any spares that turned up in farm sales. Steering clutch problems were endemic until the old type shoe clutches gave way to the later disc type. They were little bother provided the tractors were not used for ploughing, which they weren’t up to. We usually had three Countys operational, plus a spare ready to take over when one broke down. The ploughing tractor at this time was a Fowler Challenger 22.
beet on, greedy boards accepted! Then the lorry was parked on a suitable slope and a County crawler placed at the ready with a chain. In the morning the thing was towed off and, with the engine cover open in the cab, copious amounts of Easy Start were sprayed into the air cleaner. Eventually the thing would decide to start, not that it had A second-hand Catchpole much choice in the matter. We grew beet until the season of 1968, Cadet joined the fleet and which if you remember was a very wet harvest and autumn. That year lift ing what a godsend it was beet became almost impossible on our clay land and aft er a continuing battle with the conditions Father suddenly ABOVE: decided enough was enough. He turned the sheep A 1960s on to the remaining 12 acres of un-lift ed beet and Catchpole tore-up the beet contract. That was the end of our Cadet sales sugar beet growing years. Not a bad move I brochure. thought because it did away with the job I most What it doesn’t hated. Tractor-hoeing sugar beet on a freezing cold mention is the day was mind numbing.
amount of soil that, on heavy land, was lifted with the beet or what was required of the tractor in wet conditions. Multiple Countys
CRAWLER POWER COULTER CHECKING It was standard practice to have a man riding on the drill to check that all the coulters were running with no blockages. The Longfoots ran a number of County crawlers very similar to this one. “They were cheap to buy and could be used later for spares,” says Peter.
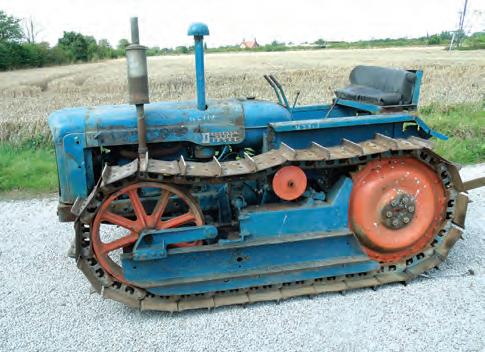
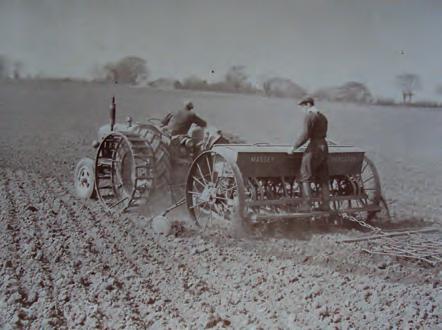