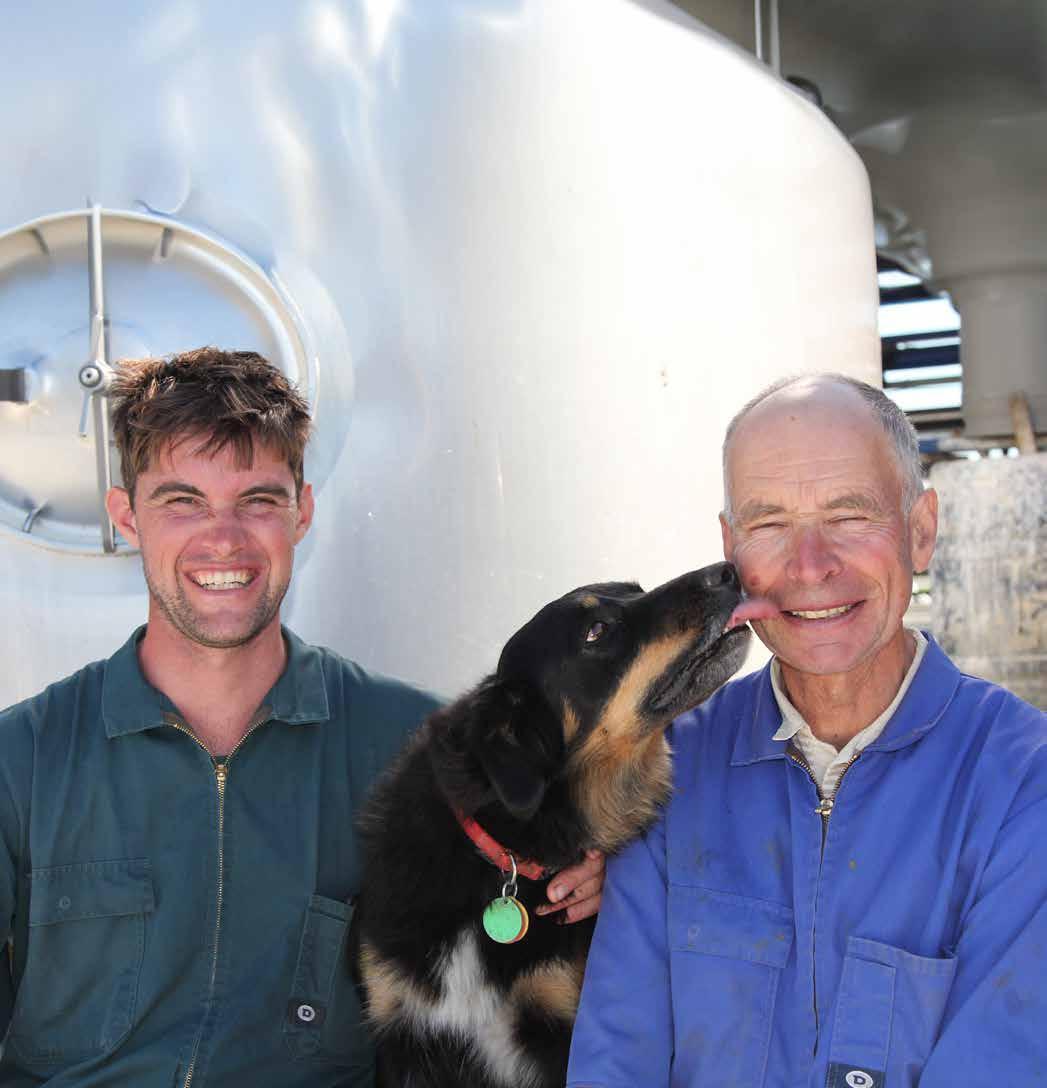
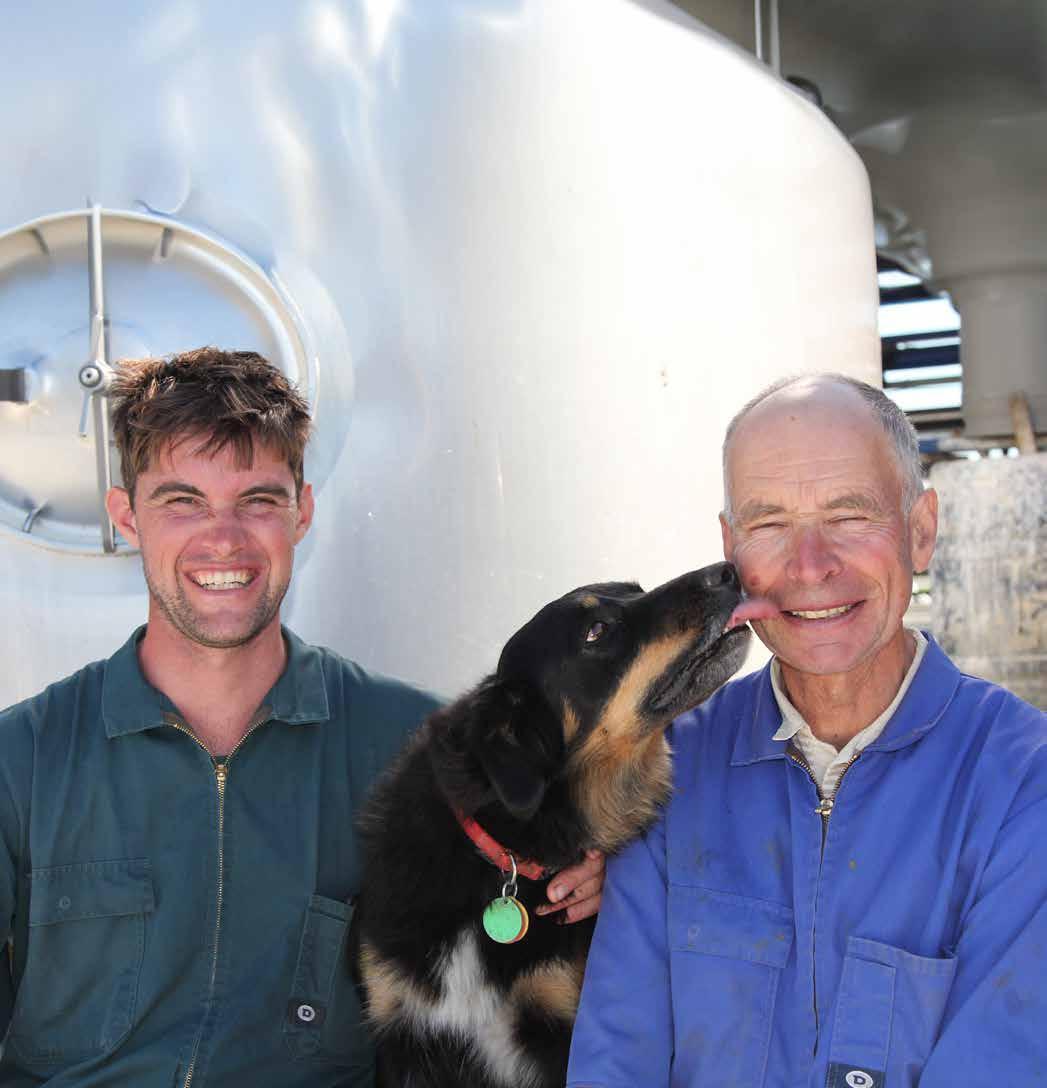
New dairy delights

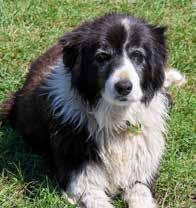

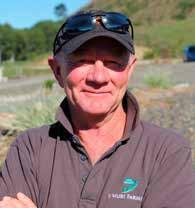
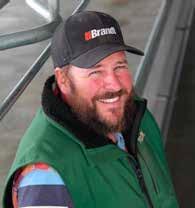

Farmer Andrew de Groot and his father Aad de Groot are very happy with their new no-frills 26-aside herringbone on their Morrinsville farm. Even ‘Flax’ the dog congratulates Aad on the new build! Read about their successful project on pages 54-55. Photo: Clare Bayly.
New Farm Dairies is New Zealand’s most comprehensive guide for farmers planning a new farm dairy construction.
Showcasing a range of the newest dairy farm projects throughout the country. This gives farmers a vital, in-depth reference tool for their own dairy projects for years to come.
Distributing over 30,500 copies throughout New Zealand FREE to all dairy farmers and rural supplies stores, reaching all corners of the country’s vast dairying industry.
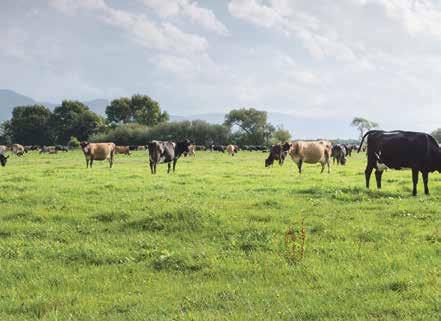


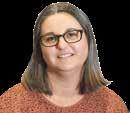
Nothing has changed!
Welcome to the 19th edition of New Farm Dairies – the annual supplement of Coast & Country News, which profiles new dairy builds around New Zealand.
This edition – a truly comprehensive study of 28 individual farm and/or dairy developments –arrives with spring.
In the last year – just like dairy farmers continually do – New Farm Dairies has faced change.
Sun Media publisher Claire Rogers, who owned the paper for 18 years with late husband Brian, sold New Farm Dairies and fellow publications Coast & Country News and The Weekend Sun to NZME in March 2024.
But rest assured – NZME sees the incredible value of this publication, which assists farmers in making one of the biggest on-farm investment decisions in their lifetime – a new dairy build or renovation.
And so, nothing changes. We’re still talking to dairy farmers who are finding and utilising new options to better the way they farm by interviewing – you guessed it – fellow dairy farmers.
New Farm Dairies gives those thinking of building new or upgrading facilities the chance to hear from fellow farmers to agricultural experts on the most up-todate information, products and services.
Everything from earthworks, building
construction, milking plants, to refrigeration, electrical needs to feed systems, equipment and storage facilities to animal housing feature in this guide.
Plus, the technology – that measures, monitors and manages nearly all aspects of a new dairy from the comfort of your home, office or the other side of the world in real time – keeps getting better.
There’s innovative ways to store and apply effluent, chill milk, run water systems that deliver efficiency and cost-savings – there’s even robotic milking systems.
Animal health, comfort and production continues to be at the forefront of new equipment and facilities – as is health and safety, and retainment of staff.
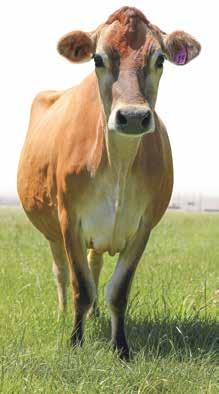
There’s no.8 wire ingenuity packed in, and bespoke ideas flavoured by previous years of this publication – as many farmers we interview have used New Farm Dairies as part of their research into crafting a new facility.
A big thank you goes to 2024’s contributors for welcoming us onto your farms and sharing your stories.
Those wanting to feature in next year’s edition – please get in touch today with our advertising consultant Lois Natta on 027 281 7427 or send her an email: lois.natta@nzme.co.nz Lois has project-managed NFD since it’s conception 19 years ago, and can help with all advertising needs. Be quick –space fills fast!
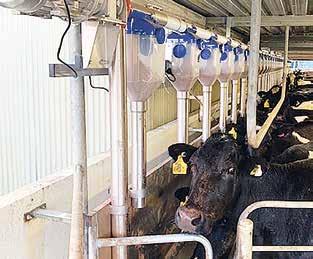
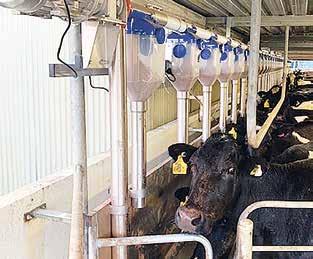
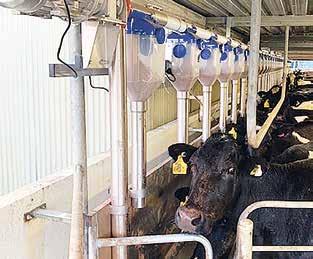
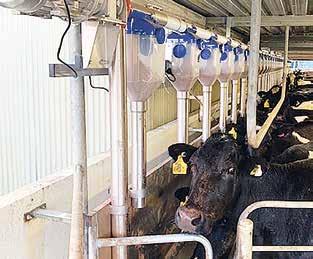
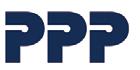
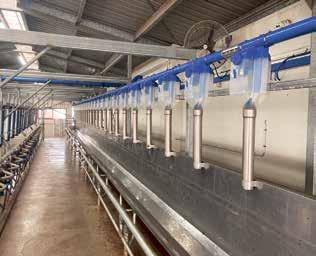
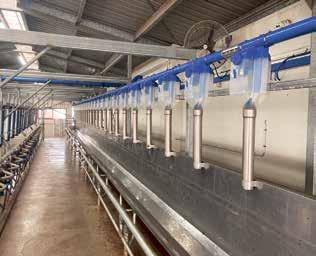
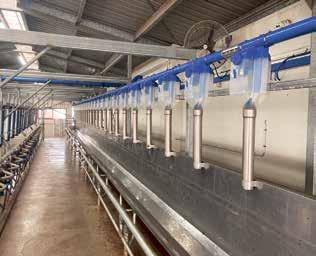
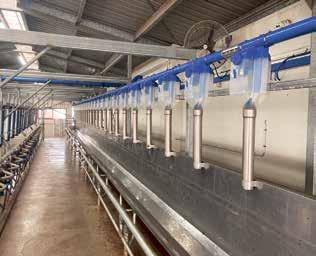

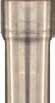
A microcosm of what’s happening on farm
On the face of it, New Farm Dairies promotes investments in the infrastructure which assists the New Zealand dairy industry. But it’s much more than that.
The clamour of opinion and conjecture reached a crescendo during the Covid years – a time when we were isolated from our friends, families and communities. The “news” tended to consist of daily reports of the devastation the pandemic was having around the world with predictions of its impact on our economy.
Most of the developments profiled in this 19th edition of New Farm Dairies were in their infancy during those times – the fact that those plans continued to percolate confirms the resilience that farmers are renown for.
That is what New Farm Dairies does –takes you down the farm race and into the homes and dairies of a small sample of farmers whose investments speak volumes for their confidence in the future of dairying. It provides you with insight to what is really happening on farm – direct from the farmers themselves.
Perhaps it was their geographic isolation from much of the noise that dominated the news which sharpened farmers’ focus on strengthening their farm’s infrastructure so it would be ready for the recovery. Or perhaps it was the simple reality of farming life that is inescapable – animals and land which needed to be cared for.
Whatever it was, this edition of New Farm Dairies bears witness to the confidence and optimism which has shaped our industry,
and which is, once again, raising it to a level of production and quality which is the envy of the world.
It’s a generalisation, but “cockies’” are a modest lot – they don’t go looking for profile and most of those profiled within these pages needed the wider perspective of the value their insight would bring to contemporaries, before they agreed to be profiled. But even then, in every case, their concession was attached to the profile being more about their commitment to building
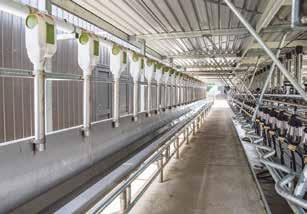
a future for their families than to them as individuals. And, again in every case, they wanted to profile and acknowledge the expertise of the people who they opted to work with to realise the project.
Investing at the levels evident on these pages is a demonstration of belief, ability and bravery in the best of times – but following “the pandemic years” it is nothing short of exceptional. But that is an outside observation; if asked, each of the farmers profiled would say that each project was

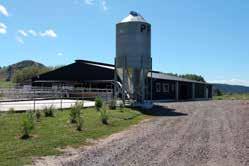
undertaken after rigorous evaluation of every option and every aspect. “Expert” opinion was sought, and many yarns held over fellow farmers’ fences and yards talking about what worked, and what didn’t. It is also fair to say that past editions of New Farm Dairies were referred to for ideas on what could be done.
Another common theme to our stories is the team aspect which under-scored every project. In most cases loyalty was a driving
force, contractors appointed based on “past experience”. And that loyalty went both ways with the vast range of contractors –earthmoving, engineers, yard designers, builders, electricians, plumbers, milking supply companies, water and effluent specialists – collaborating and working with and around each other to deliver the dream. And the result is a palpable pride which is shared across “the team” – in the project and the part each has played, as much for the rewards it has delivered to their families, their businesses, their community and the dairy industry.
In summary, this edition of New Farm Dairies is a microcosm of what’s happening on farm; the resilience, optimism and, at the end of the day, bloody-minded determination to get ahead which no pandemic can dim. It also provides insight to some extraordinary innovations which are adding value, and which could equally have a place on your farm.
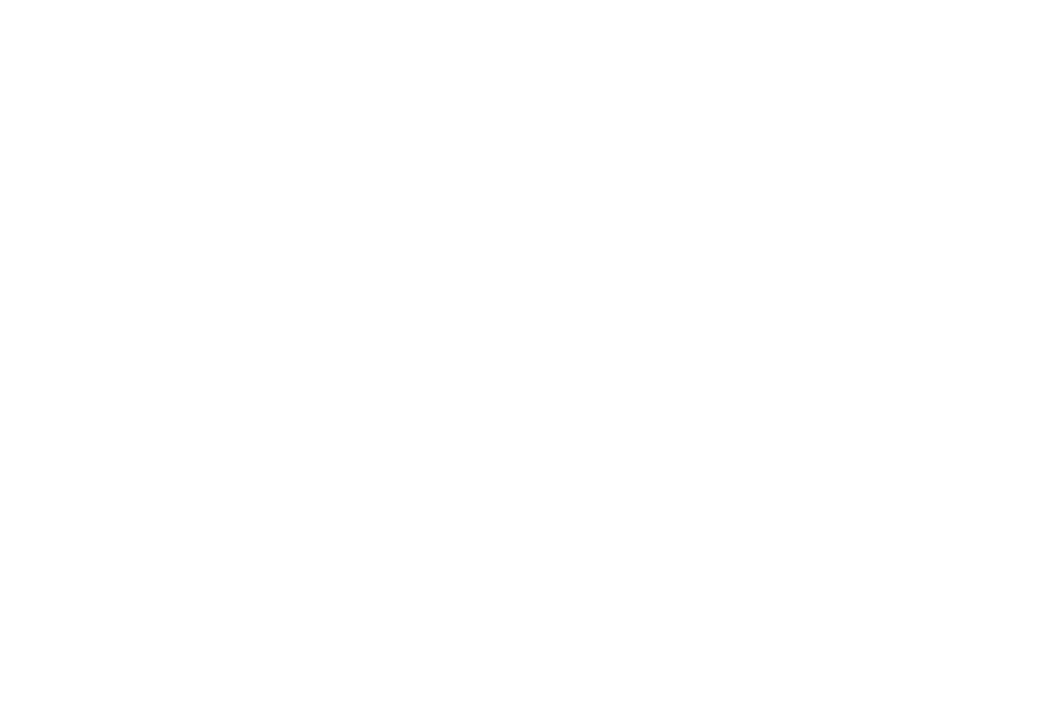
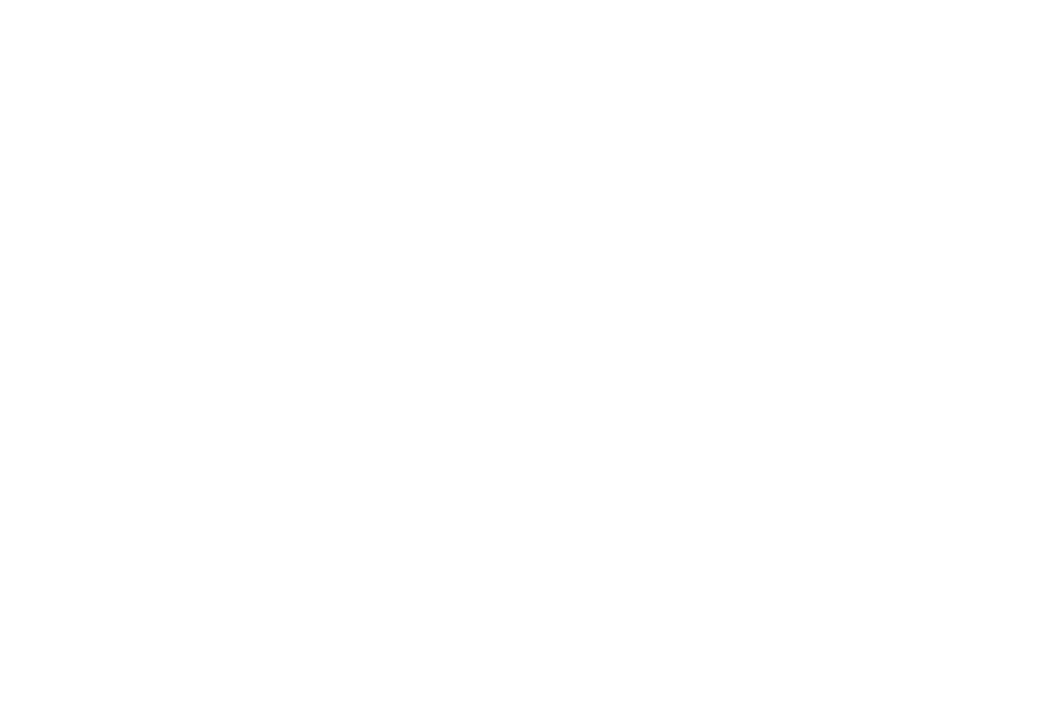
Clare Bayly
RIVERSIDE FARMS
An extra two hours a day…
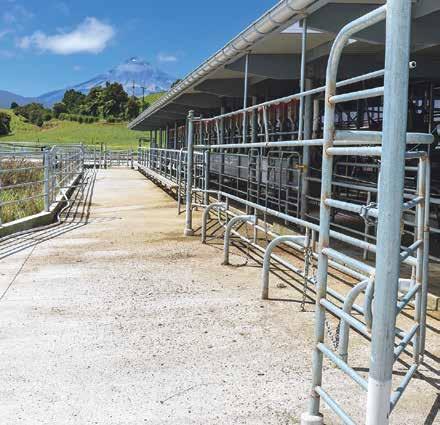
The timing may have been less than perfect – but the team involved, and the result was.
Bruce and Katrina Warren, together with their son Danny his wife Sarah, put the finishing touches to their new 30-aside herringbone cowshed in the spring of 2022 – off the tail of Covid-19.
It was a tough time to push forward with a significant investment, but the family has ‘no regrets’ as they stand inside their heavily automated result –nestled at the base of Mount Taranaki.
Riverside Farms
They milk 315 F16
Friesians at Riverside Farms – averaging 430kgMS per cow – off 200 hectares – which includes 160ha effective with a 130ha milking platform. All of the young stock are carried on the property. It is rolling to steep country, culminating in some river rock that sits 274m above sea level – along Okato’s popular coastal strip – 20 minutes south of New Plymouth.
The dryland operation, outside of effluent irrigation, has 26ha available to make hay and silage. With a 2.5ml annual rainfall this part of the coast is also located in one of New Zealand’s lee wind zones. Lee wind zones are areas where the landforms create localised wind acceleration, resulting in higher wind speeds

than the rest of the region. The old 18-aside cowshed used to swallow five hours a day, and the cows often had to stand with their necks turned to fit into the bail. Bruce says when Danny returned to the farm after working as a builder for a decade, the former mechanic knew it was time to change things.
Playing into the decision was that they didn’t employ any staff – and that Bruce is a Type 1 diabetic, Danny’s wife a schoolteacher, and Katrina and Bruce along with their daughter Jasmin own and operate Sentimental Flowers in New Plymouth.
Automation a must
Automation was the secret sauce they needed, and they
were also mindful of staying ahead of looming potential environmental challenges. It put the decision into a ‘musthave’ territory. It also dictated a greenfield site for effluent management.
“When we purchased the top block, it was always in the plan to do something about the shed,” says Bruce. “The old shed was so close to the river; we knew we would have to address the effluent to safeguard the farm environmentally at some point.”
Danny says building had been a great early outlet and a foundation that allowed him to work for others and to pursue rugby. However, when he started to turn towards home the cowshed quickly came up in the conversation.

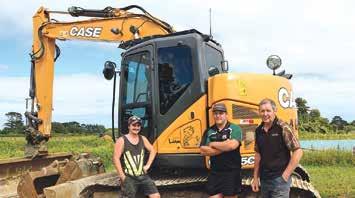


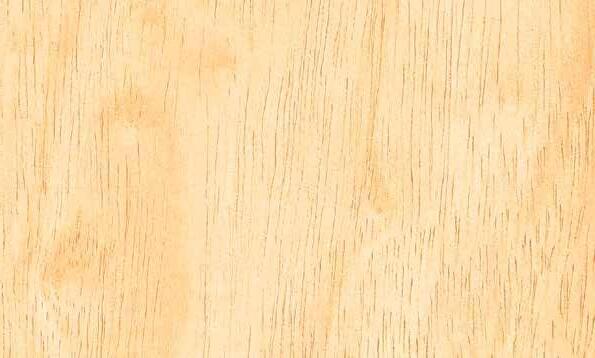


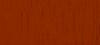

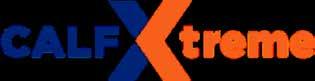


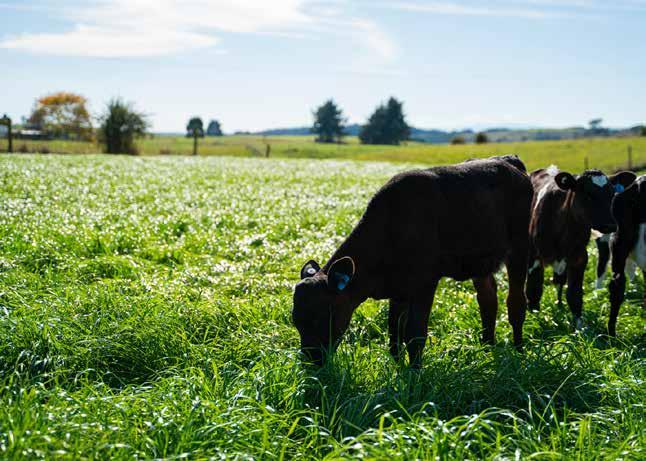
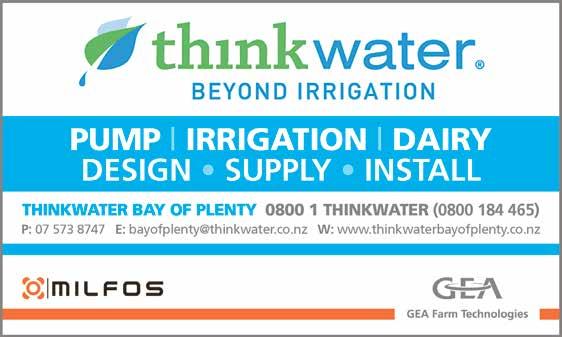
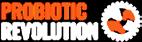
The views aren’t bad – both inside and outside this dairy.
Liam Gibson of SAG Earthworks Ltd has been an integral part of the site preparation for Riverside Farms’ new dairy. Liam also completes regular earthwork maintenance around the property and tracks for Danny and Bruce Warren.
RIVERSIDE FARMS
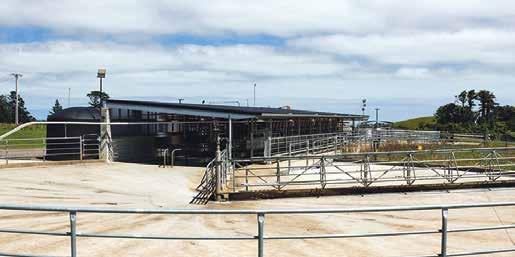
“It was so tiny,” says Danny. “I felt massive in it. I was hitting my head on the clusters, and it was made for Jersey cows.”
Fathers and sons
This farming family was never going to look outside their local connections for a new build. Notably, there were three father-and-son partnerships from three businesses in their community working alongside one another on the project through post-Covid challenges.
“As the dads, we can pull back a bit and let our sons make the calls,” says Bruce of the intergenerational relationships. “We put our point of view in if we’re not happy. But if it looks good, we all run with it.”
Danny adds: “It comes down to communication. You’ve got to be able to give and take”.
Danny leads day-to-day operations at Riverside Farms these days. His building background naturally put him in the
DAIRY WALL COATING SYSTEMS
building mix too. There are some bespoke designs – including a concrete ledge along the entire the AI race – because Danny and Bruce aren’t the tallest men in Taranaki.
The round yard includes interwoven holding pens with clever gate placements for safe drafting, and a hoof trimming crush with a powerful light that allows for safe handling or late-night vet visits.
Both father and son say the cornerstone of this build’s success came down to the people. It principally included Brian Hill Builders, Coastal Welders, Mitre 10 New Plymouth, Think Water New Plymouth and SAG Earthworks Ltd.
“We are so rapt with the team we put together,” says Bruce. “We picked who we wanted, and Brian Hill was our main touch base.
“All these guys sponsor the local community, so it all swings in roundabouts. We’ve known Brian for a long time. We knew his work, he’s built a lot of sheds, and now his son, Jono, is in the business too. It
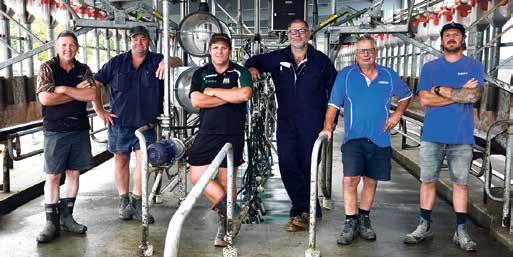
was a no brainer.
“Steve Gibson contracting does a lot of work on our farm, and their team moved the dirt at the start.”
New grazable paddock
The new dairy is not only equidistant between Bruce and Danny’s homes, it was a strategic greenfield site that offered the most efficient effluent management.
SAG Earthworks Ltd carved off the top of a hill on-farm to add and compact an additional 2m.
Bruce says the father-and-son earthworks business – which also owns a local quarry – are familiar faces on their farm. Liam Gibson, 23, was integral to the site preparation.
“I think Liam has been in the digger since he was four,” smiles Bruce. “He’s an awesome operator and he also does our tracks around the farm. We never question him.”
Liam says taking fill from a “big, pointy
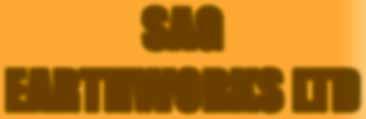

hill” was a good way to “kill two birds with one stone”. It’s given the family another grazable paddock.
Effluent big push
A weeping wall and the one million litre bladder that holds the effluent water has changed the environmental conversations – including negating dealing with excess rainwater in an open effluent pond.
“Although initially it wasn’t a cheap exercise to bring in the bladder from Italy, it’s a modern set-up that will still be compliant in 10 to 30 years,” says Danny. “A lot of traffic goes through this road. It’s a tourist route and instead of having a smelly, and massive pond, this now gives dairying a good name.”
Milking in the new cowshed takes 1.5 hours plus the wash-up, and the Automatic Cup Removers, the automatic teat spray in the exit, and the automatic wash have not only saved time but have added repeatable consistency. The herd’s Somatic Cell Count is 120,000.
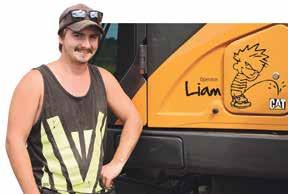
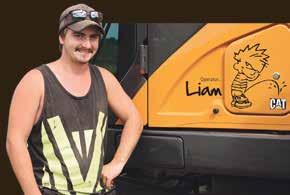
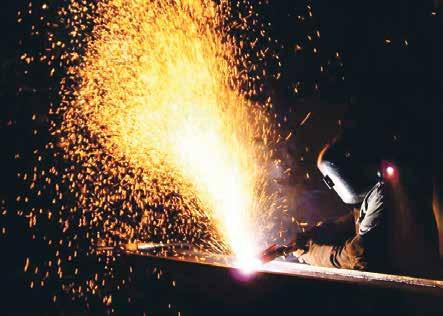

Acraflex Dairy Wall Coating Systems save hours in cleaning, seal against bacterial build up and create a bright, hygienic working environment.
The A-team for the build included Bruce Warren, Andrew Wood of Coastal Welders, Danny Warren, Steve Bevan of Think Water, and builders Brian and Jono Hill.
A lot of thought went into the pipework that promotes cow flow.
RIVERSIDE FARMS
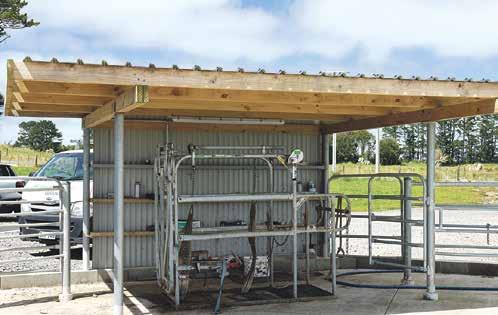
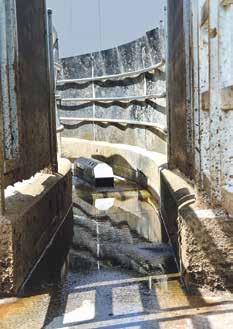
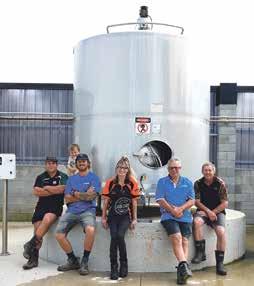
The in-shed feeding has also allowed the family to avoid production crashes when nature doesn’t play the game.
Think Water’s director Steve Bevan was responsible for installing the in-shed feeding, clusters, water conversations, the autodrafting, ACRs, auto-teat spray and he was also involved in calculating the storage and design for the effluent and the weeping wall.
“This is probably one of the most hightech herringbones we’ve done,” says Steve. “We’ve done a number of auto additions in other herringbone builds, but not always as a whole package.”
The revelation
Danny says the automatic wash has been the revelation. “Because when you’re milking by yourself, you can set the pre-rinse, the auto wash-up, and walk away – or be hosing down – and the plant switches itself off. You’re not worried about turning taps off when you leave, and every wash is the same. It’s allowed one person to do the job well and to do it quicker.”
One of the quiet achievers in this build is Mitre 10 New Plymouth, with trade account manager Heather Stewart saying she had wanted to work with Brian Hill for years. When she joined Mitre 10, she finally got her wish. Brian says Heather is exceptional to deal with.
“It’s all about better prices and good service,” says Brian. “Mitre 10 are our main suppliers because they are a great team to work with. They did really well on this build through a tough time.”
Cow flow
Coastal Welders’ Andrew Wood’s role started early in the planning process – in tight consultation with his clients – to make sure the yard design meets their needs
and achieves peak efficiency in cow flow. The fabrication and installation of the steel work is completed before the yard build starts.
Andrew says cow flow is at the heart of every successful project. After a lifetime in the business, he has a number of secret weapons which set his clients up for a positive and practical long game. He regularly collaborates with Brian Hill. The Wrangler crush is another staple that is worth its weight in steel. And Surfatex, which specialises in Acraflex dairy wall coatings – in addition to industrial coatings, anti-slip solutions and protective flooring –gives the dairy it’s easy-clean finish. Surfatex is the only licensed applicator of Acraflex from Taupo southwards, and its high-build paintwork is specifically designed to shield cowsheds from corrosion from manure and chemicals. It is guaranteed for a decade on a new build.
Lifestyle and opportunity
As Bruce looks around, there is a quiet but unmistakable pride in what his family has achieved after selling their house in town to buy a herd of cows and start sharemilking 35 years ago. The rest of Bruce and Katrina’s children include Marcus, who works as a landscape architect in Melbourne, and Michael, a Doctor of Political Science who works in the Wellington Ministry of Buildings.
With his health a constant management consideration – together with his desire to help Katrina and Jasmin with flower deliveries when they are busy – there is now some welcome flex in this operation.
Bruce says: “We also have a presentable and saleable farm that is compliant if we ever wanted to sell”.
Dianna Malcolm
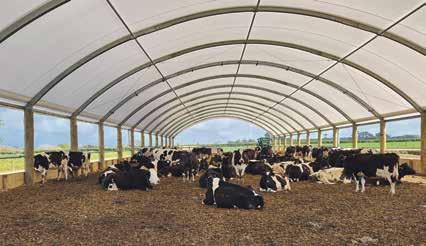
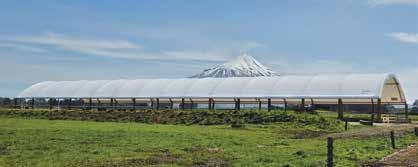
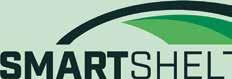

Having full control of cows when treatment is needed is a welcome addition.
Getting supplies through Covid was navigated by Mitre 10’s Heather Stewart, centre, joined, from left, by Danny Warren, Ardie Warren, aged 5, Jono Hill, Brian Hill and Bruce Warren.
The automatic teat spray is taken care of in the exit.
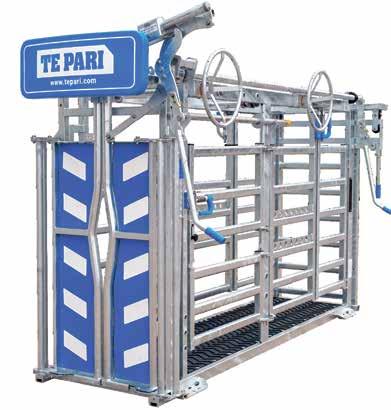

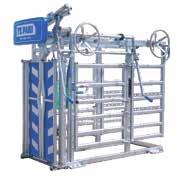
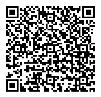
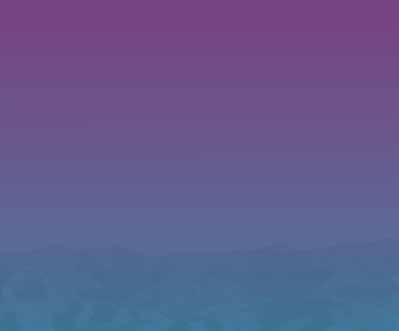
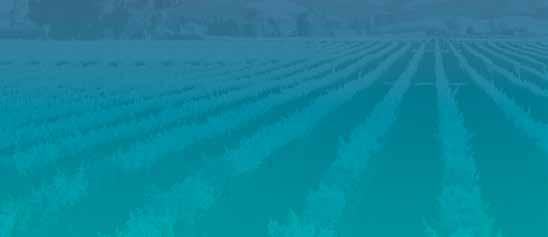
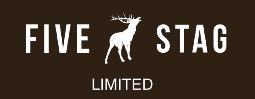
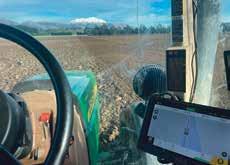
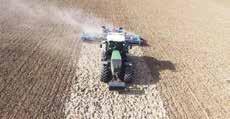
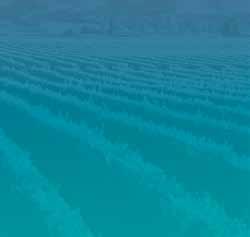

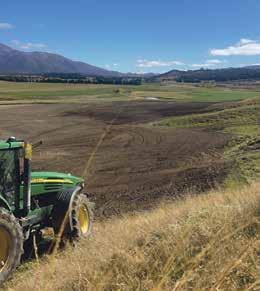


Re-purposing saves thousands!
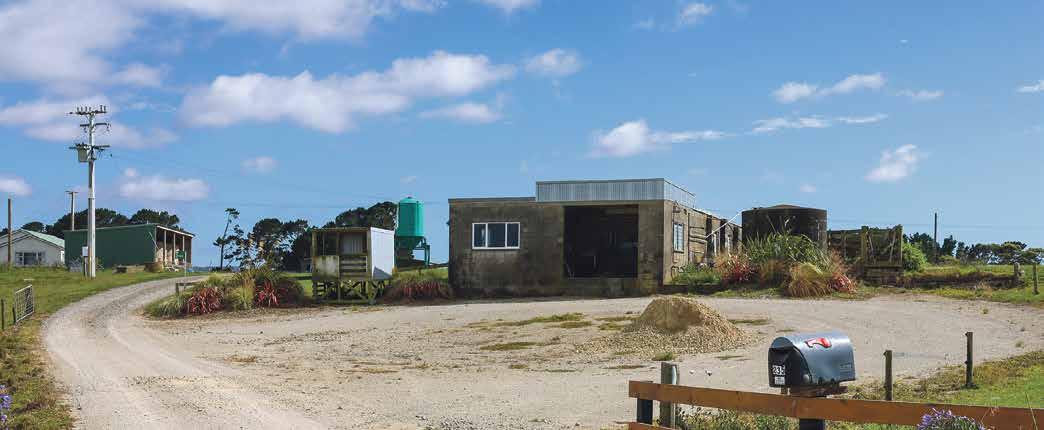
Matthew Lupton sliced a significant number of zeros off the price of his new dairy build when he replaced one of New Zealand’s oldest rotaries with a herringbone last year.
Driving into Collingwood Farms at Waverley, there is no doubt you’re pulling up to a brand new cowshed. What’s not so obvious is that there have been some clever inner decisions that allowed Matthew, 43, and his wife, Hannah, to create a new working space and exceptional cow flow on a greenfield site for an economic price which came in on budget.
This 32-aside herringbone dairy with De Laval Automatic Cup Removers has the latitude sewn in to expand to a 40-aside. For now, Matthew is milking 300 cows
on 120 hectares with an additional 60ha leased. The operation also carries 90 young and carryover stock, and 120-160 head of Hereford beef – with most sold at 100kg-120kg, with about 20 carried through one winter to be sold as yearlings. On-farm, they also make 400 bales of balage and 150-200 bales of hay.
Painful decision
Matthew was already working with Better Dairy Solutions when they started talking about a new cowshed.
“I’d bought the farm eight years ago, and we’d been battling away in the old dairy and dealing with constant breakdowns, [milk] grades, and it’d had been a struggle to get staff,” says Matthew.
“It was enclosed and dark – milkings took up to seven hours a day – and it was
often pretty stressful.”
Hannah is deputy principal of Waverley Primary School, and with their own young family, time is always a priority. Matthew called on his trusted service providers to find the solution. That included Darren Luff Contracting, Better Dairy Solutions, Bruce Clifton Builders, Dairy Technology Services, DeLaval and Surfatex.
It’s who you know
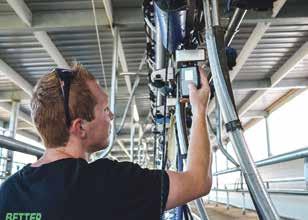
The ingenuity in this project came from whether to buy new or to re-purpose some of the existing plant.
“These guys have years of experience,” says Matthew. “You don’t build a cowshed every day, so it’s good to have their knowledge to reference.”
Better Dairy Solutions’ Gary Wallace and Gary’s son, Base, knew about a cowshed on another property that had been decommissioned six months earlier.
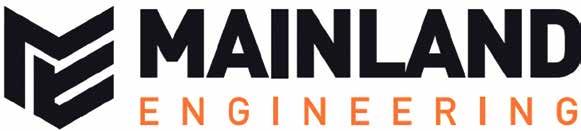
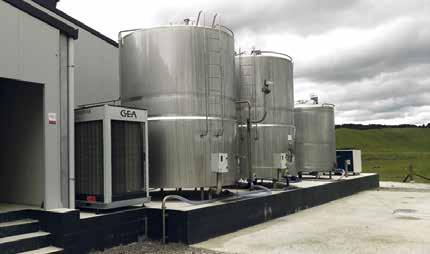

The old cowshed is a reminder of how far the Luptons have come.
Better Dairy Solutions’ Base Wallace makes sure everything is operating at the right settings.
COLLINGWOOD FARMS
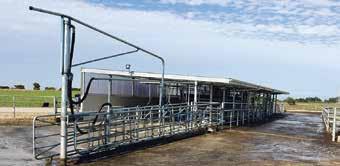
“I mentioned it to Matt, gave him the valuation I’d put on it and stood back and let him work it out with them,” says Gary.
“Then we went in with Matt and his crew, gutted the shed, stripped it, and brought it back – and Matt got all the parts cleaned up.
“There is no reason why things can’t be retrofitted – a 100mm stainless milk line today is a 100mm stainless milk line forever.
“Most of that other cowshed had a modern blower, milk lines, and its vacuum and milk pumps were up to spec,” says Gary.
“When we moved it over into Matt’s cowshed, we simply upgraded it to the size it is now. Matt’s decision to take on the background work that entailed has saved them thousands and thousands of dollars.”
The retrofitted items included the vacuum pump, the milk pump, 20 swing arms, three quarters of the milk line, the receiving can, the cooler – after it was reconditioned, stripped, repainted, and reassembled to match the rest of the plant.
They also re-purposed Matthew’s old hot water cylinder and vat. Their front 20 jetters are re-purposed. The back 20 are new. The front 20 clusters have the original shells, but a better claw bowl was added.
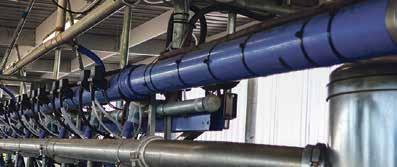
“You can still do things on a budget and get a new one-man cow shed. But there are some things within a new dairy – mostly things that revolve around technology –where we do advise choosing new,” says Gary.
Some things should be new
The ‘go new’ advice included the pulsators, the DeLaval MPC150 Automatic Cup Removers, the P3 automatic detergent dispenser, the bowls on the clusters, some jetters, and rubberware.
The MPC 150 ACRs are a simple, compact, and durable integrated inclusion which has helped whittle milkings down to an easy two hours morning and night.
“Probably the key things we like with the DeLaval ACRs is that we have a lot of programming options,” says Gary. “Our goal is to make them work as close to the way you would milk your cows yourself, and we have enough range within that technology to do that.
Matthew adds: “There is no doubt the ACRs and the autowash system itself have made milkings easy”. “On the auto wash there are not a lot of taps that need changing either, which is easy for staff.”
Dairy Technology Services, known as
DTS, was involved in the refrigeration decisions which also included working some of their magic blending the old with the new.
“We’ve been working with Collingwood Farm for many years, and we understood the farm’s refrigeration needs well,” says a DTS representative.
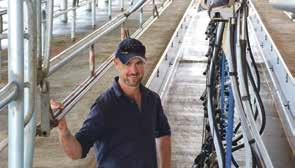
many years – and this isn’t the first time he’s completed a project for the family.
Collingwood
“Instead of installing a new fit-out, we were able to relocate the existing refrigeration equipment from the old shed to the new one, saving the farm a significant amount of money.
“DTS prides itself on delivering highquality refrigeration solutions that are both efficient and cost-effective. We only recommend buying new when it is needed.”
Darren Luff Contracting is one of the unsung heroes of this project and they regularly complete earthworks at Collingwood Farm. Like the ingredients in a cake – their work isn’t obvious once the shed is finished but that result hinges on their groundwork.
Positive experience
Matthew has known builder Bruce Clifton, of Bruce Clifton Builders, for
“Bruce is always really competitive on price, and he did a really great job,” says Matthew. “As soon as we got the consents through, his team just gunned it and worked rain, hail or shine.”
Farms Farms
Surfatex, which specialises in Acraflex dairy wall coatings, in addition to industrial coatings, anti-slip solutions and protective flooring is another daily hero.
The high-build paintwork includes seven coats of paint, creating a protective barrier which makes it easy to clean.
A new car
Next season Matthew will install in-shed feeding, lift cow numbers to 350, and aim for 130,000kgMS.
“Doing it this way doesn’t put too much pressure on us – and, as we can afford those additions – we will,” says Matthew.
“Every day, milking is like getting in a new car, and it frees up a lot of time for me to get on with other jobs or spend more time with my family.”
Dianna Malcolm
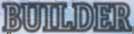
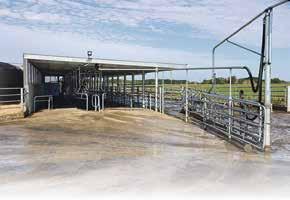
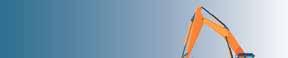
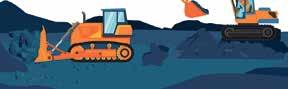



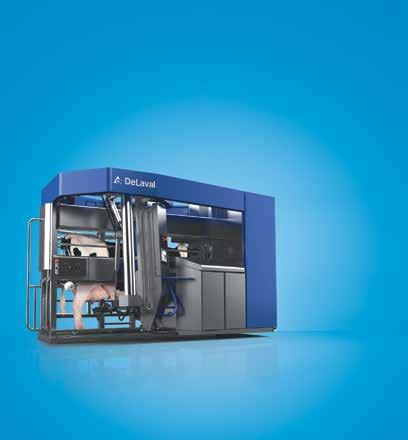
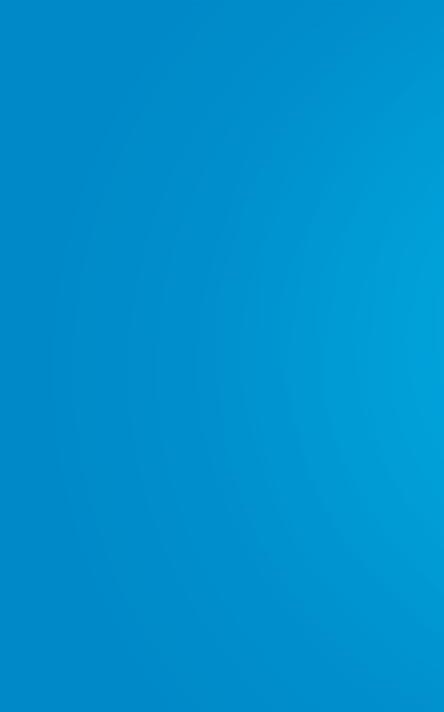
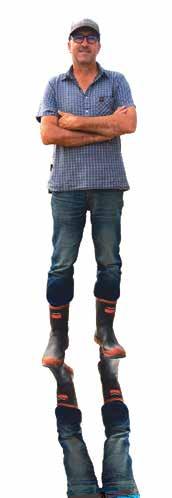
The new dairy has saved hours in the cowshed every day. Working in the old with the new is a clever way to stay on budget. Matthew Lupton says his new cowshed has exceeded his expectations.
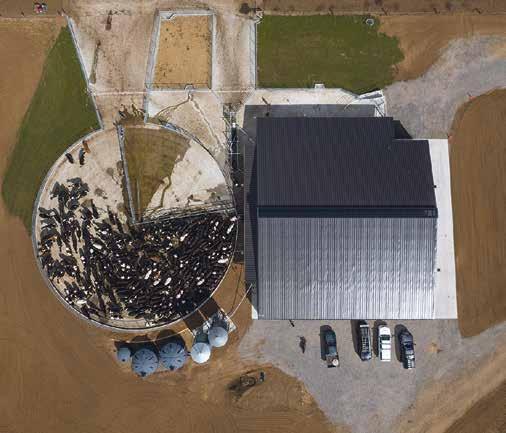
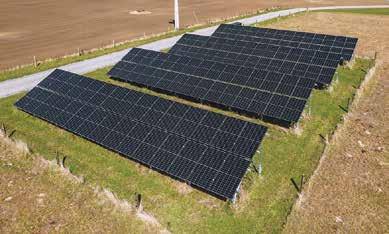
This 50kW solar system includes 120 panels on north-facing ground-mounted racking. The initial investment is expected to pay itself back within six years.
A signature dairy at Stratford
Merging two herds through a centralised new cowshed on a Stratford dairy farm has transformed the dayto-day runnings for a third-generation family operation.
Cornwall Park Farms Ltd, owned by the Lightoller family, is a specific build because they didn’t spare the horses when it came to designing their 60-bail rotary.
Their first big move was to employ Gibson Construction to build it – the company’s first new dairy shed commissioned in Taranaki. Their other bold choices include incorporating solar panels, housing their milk vat, dedicating a room to their imposing 110kVA generator, and adding wider entry steps down to their cupping up area. Their accumulated detailed choices have contributed to an elegant finish, in a lightfilled cowshed for the Ngaere property, which milks 550 cows on 225 hectares for an average production of 520kgMS. The farm is owned and operated by Paul Lightoller, together with his parents, Jay and Raewyn, and Paul’s daughter Brooke, aged 18. The team also includes husband-and-wife duo, James and Carla Bugtong.
Two rolled into one
The family used to milk two herds through two cow sheds on adjoining properties
– through a 32-bail rotary which milked 350-head, and a 19-aside herringbone milking 200 cows. However, both dairies were fading fast, and the family decided to decommission them and invest in a single new solution on a centralised greenfield site.
Paul had seen and liked Gibson Construction’s work in New Farm Dairies, and so contacted its director Blair Atkinson, to talk through their options.
“When I called him, I didn’t realise they worked countrywide,” says Paul. “I was more after plans for a local builder. But Blair said he’d come down and have a look at it – and we visited some cowsheds they’d built, and it went from there.
“I’m not a builder, and it was the first time I’ve done anything like this. These guys do it all the time. I needed to look after what’s happening on the farm, and I wanted someone to oversee the build.”
Jay says: “We also wanted someone that when they started, they were here. We didn’t want them coming and going”.
Blair committed to step out of the office and project manage the build, even though it was three hours from his home. During construction the Lightoller family decided to combine their two herds in preparation for what was to come – milking 550-head through the 32-bail rotary – in a gruelling finale for their old dairy.
The new structure loomed as the promise of
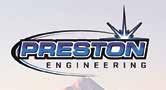

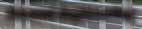
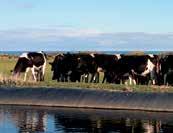
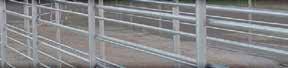


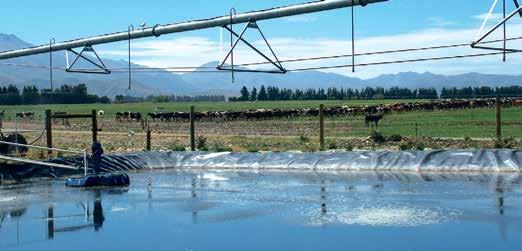
The double backing gates mean they can split the herd, run the backing gate in reverse, and wash the yard more thoroughly with one pass a-piece. Photos: Cayden Searancke.
Proudly Taranaki owned & operated
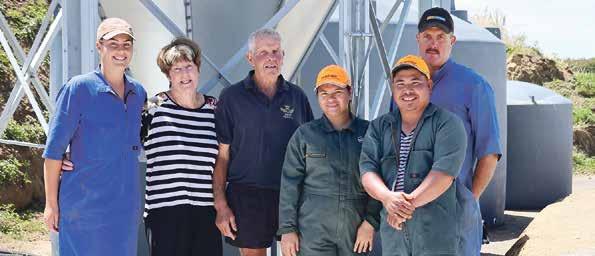
things to come, and Blair says there was no stone left unturned in the new build.
“Everything is special and different,” smiles Blair. “We had a design we were using and then Paul changed everything.”
Paul counters: “What attracted us to Blair was the quality of his workmanship, and it allowed the whole process to progress nicely”. “There are no decisions I’m regretting at this stage. Everyone seems to be happy. We try and keep the farm nice. You spend a lot of time there, so you may as well have it nice and tidy.”
A roof over the vat
Housing the vat room was a departure from most of Gibson Construction’s clients.
“A lot of the time people want to save money by not covering the vats, but as you can see it does look good. It’s out of sight and these guys are out of the weather when they’re working. It was Paul’s idea to put the wall in as well.”
Paul adds: “It was something we chose to do”. ”It keeps a lot of the weather off that area, it means the chiller unit is covered, it gives us a covered parking area, and just finishes the build off nicely.”
DAIRY WALL COATING SYSTEMS
The wider steps – highlighted with Surfatex safety grip – were Brooke’s idea and they now have a ringing seal of approval from the whole team.
Extra ceiling height
The distance from the platform to the shed’s peak height is key to achieving a light-filled working space with meaningful airflow.
Gibson Construction routinely has an additional 800m to the apex of the roof than other contractors.
“We do it for the air flow, because it can get pretty hot in there once it’s full of cows,” says Blair. “Ideally, we aim for 4.2m from the operator floor to the centre of the knee joint with a 10 degree pitch to the roof.”
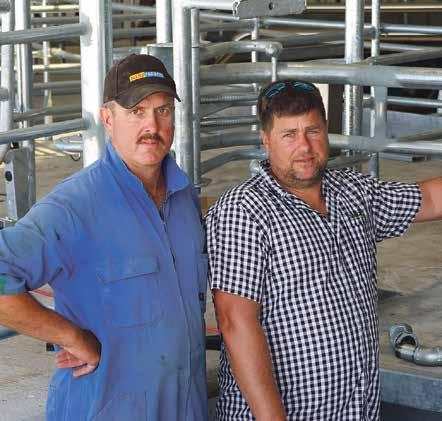
Cornwall Park Farms
Paul says humidity can be a problem in their region, and airflow in the cowshed was important – as is the shorter walking distance to the dairy. The cows used to have to walk up to 2km one way to the dairy. That same walk will no longer exceed 1.6km on any given day.
Their milking time now is two-and-a-half hours’ shorter every day –and, combined with the shorter walk, it opens the opportunity to lift production because there will be more available time for the cows to eat and to rest.
Blair says the Lightollers have been a pleasure to work with, and he’s proud of the finished article. “This is the standard that we
expect,” says Blair. “There is a reason these guys came to us and wanted us to build their shed.”
No high jumps!
When it came to the yard work, Cornwall Park Farms had an easy choice to make. Preston Engineering is based 15 minutes from the farm and was already doing work for them. Director Gary Preston is a skilled engineer with the trophy cabinet to prove it. He says it’s always
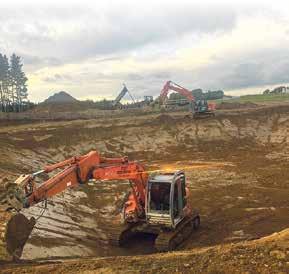



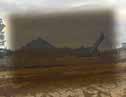
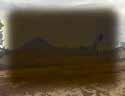
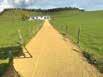
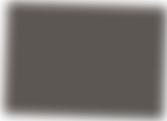
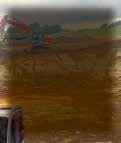

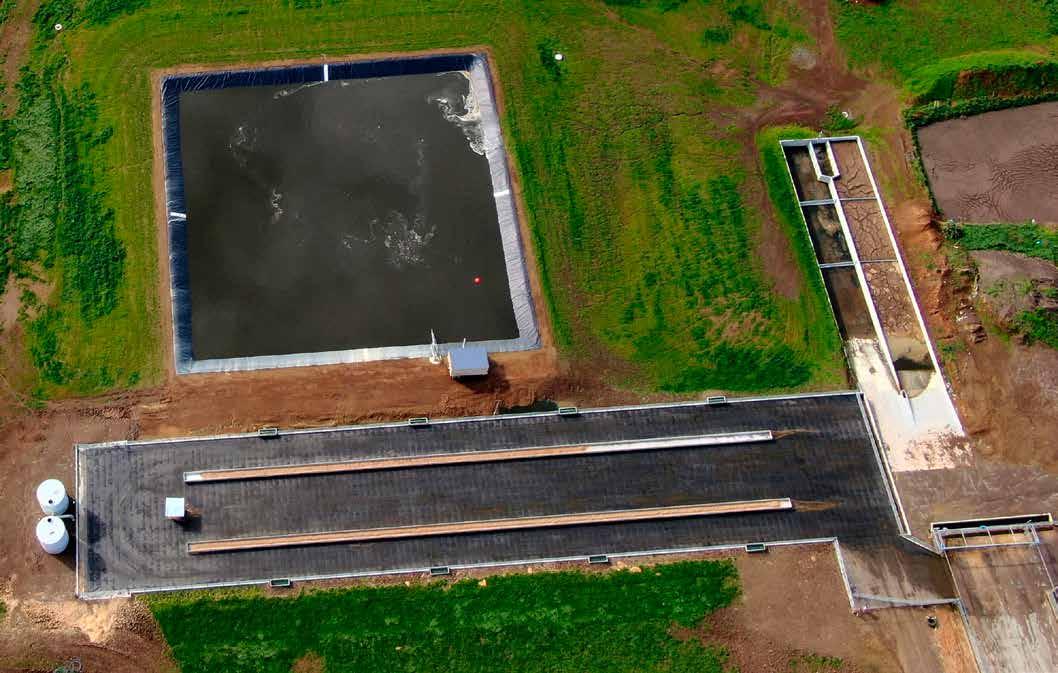
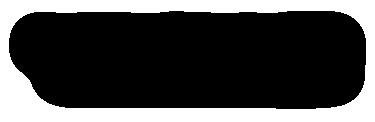

Acraflex Dairy Wall Coating Systems save hours in cleaning, seal against bacterial build up and create a bright, hygienic working environment.
Paul Lightoller and Gibson Construction’s Blair Atkinson understood each other’s vision.
Brooke, Raewyn, Jay and Paul Lightoller are joined by their employees at front: James and Carla Bugtong.
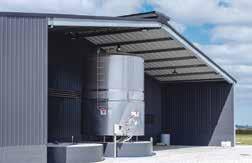
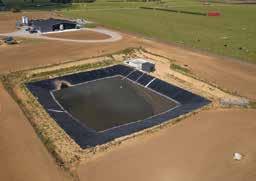
positive to work at Cornwall Park Farms –and the notable difference in the engineered yardwork was that they added an additional rail on the holding yards, yard, and backing gates – taking them all to 1.6m high –300mm higher than usual.
“I think if they think they can jump, they might,” says Gary. “This isn’t as high as we normally do, but it makes everything extremely safe.”
They also installed double backing gates, with the scrapers and jets fitted –which were made in-house by Preston Engineering.
“It seems to be the way farmers are going now in Taranaki,” says Gary. “They are enjoying the double backing gates, because they can split the herd, run the backing gate in reverse, and they both wash the yard more thoroughly in the one pass.”
The other difference was the decision to add eight spring-loaded man gaps.
“It’s not common, but it’s definitely more beneficial than the squeeze gaps,” says Gary. “If there is a squeeze gap, heifers will sometimes try and get through, or if the farmer has eaten too many pies, it can be hard for them to get through. Being
spring-loaded means it’s safe and easy for everyone.”
Solar panels
Another new addition is the solar panels at the farm’s entry, feeding power directly to the cowshed. The 50kW system includes 120 panels on north-facing groundmounted racking. Solar One’s Regan Fairley says this is company’s first dairy installation. He says the initial investment is expected to pay itself back within six years, and the panels and racking are covered by a 25-year product warranty.
Regan sees massive relevance for dairy farms given their high energy demand.
“The biggest struggle for us is getting the information to the farmers, so they see the numbers and data and understand how it can help their business,” says Regan.
Paul says the solar decision seemed logical.
“I can’t remember if I saw some advertising or not, and there was an initial outlay. But we could see the benefit it could have a few years down the track. Our power bill at the cowshed was around $2500 a month so it will be interesting to see how that plays out.”
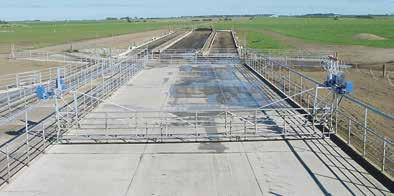
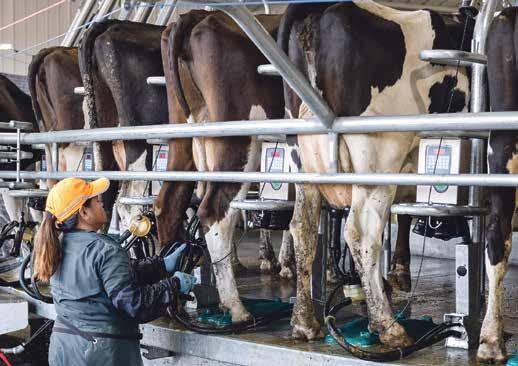
Paul says one thing they hoped not to use was the generator. “It’s a big unit, and originally it was going to be outside, but the room we decided to put it in didn’t have much use, and it made sense to use it because it was going to be in a cramped position by the vats.
“Now, it’s out of the weather and hopefully that generator will be a waste of money and we won’t have to use it.”
Reducing effluent
Davieth Verheij, of AgFirst Engineering, completed the full effluent system infrastructure together with Delaval Coastal Agri Services and supporting contractors Viking containment, and Gibson Construction. It completed the pond, irrigation and
green water recycling design, supply, and build – in addition to designing and supplying the electrical control system. It also completed all council consenting to make sure the system was compliant.
The effluent system is made up of four key system components. The stone trap and solids bunker removes solids through a stone trap and solids storage bunker. A key feature of this component is the AgFirst solids retention screen, which holds the wet solids in the bunker – allowing them to drain and dry.
The effluent storage pond is 40m x 40m x 4m deep, with a total holding capacity 4,181,000 litres. It is lined with Viking Containment High Density Polyethylene. Third on the list is the green water recycling. Its 11kW green water washdown
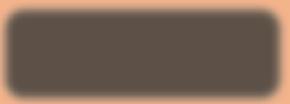
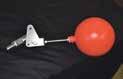
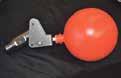
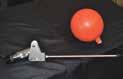
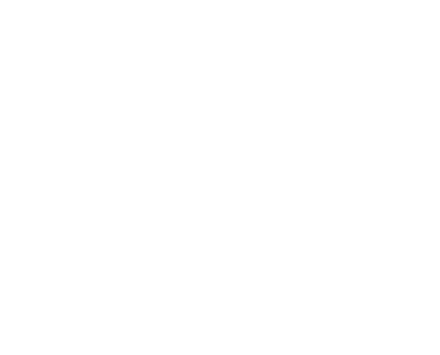
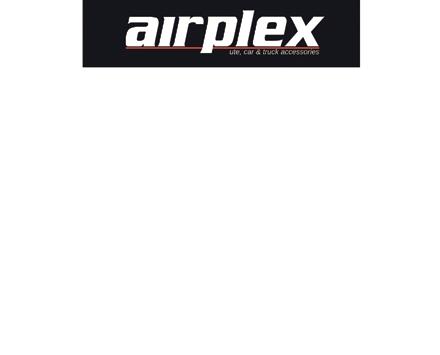
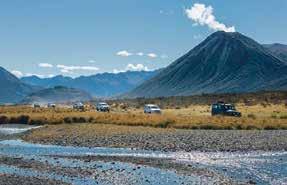


Covering the vat helps keep the sun off it and makes the finish tidier, and allows everyone to work in the space comfortably regardless of weather.
Carla Bugtong putting cups on in the new dairy.
The effluent storage pond is 40m x 40m x 4m deep, with a total holding capacity 4,181,000L.
system draws from the top of the effluent pond, reducing dairy shed water use by approximately 70 per cent. It equates to a water saving of 30m3/day – or 9,150,000L per annum. By reducing the effluent, it –in turn – saves Paul 458 irrigation hours a year, including saving power, time, water and money. Lastly, the effluent Irrigation comprises an industry leading AgFirstdesigned 7.5 kW pond stirrer, a 7.5 kW Wangen PC pump and a Weta low-rate travelling rain-gun irrigator.
Feed a priority
Feed pinches on the shoulders of the season meant that in-shed feeding was always going to be a priority for the family to sustain production and their days in milk, regardless of the season. PPP Industries was responsible for installing it.
“We had already been in-bail feeding for four years in the old dairy,” says Paul. “It keeps our production more consistent through the season to fill in the gaps outside of our pasture growth. We can get dry in summer here, so we do feed turnips and grass silage in late-summer and autumn.”
Lights out
Mike Robinson, of Robinson Electrical, has always done Cornwall Farm’s electrical work and roughly 30 per cent of his business is dairy-related. This job was his first brand new install in seven years, and a baptism of fire with the extensive automation involved.
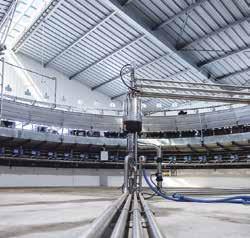
irrigation system, for example.” The detail continues right down to the lights all having sensors which automatically switch on when someone comes in.
Milking is certainly a breeze now
Percy Contracting was responsible for the earthworks, Preston Engineering manufactured the yardwork, and Hunt Farm Services took care of installing the Waikato plant, which included a concrete platform. The Wrangler hoof trimming system completed the install.
The way forward
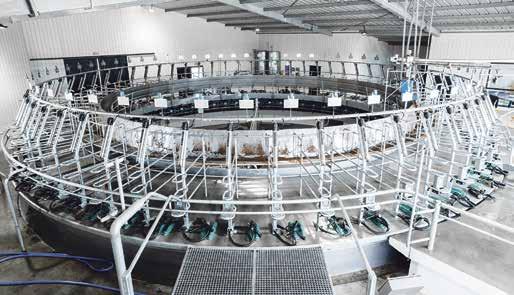

“It was just a matter of doing my homework,” says Mike. “With the solar power we also set up timers to run as much as we can during the day when the sun is out to take advantage of that, like the
Paul says they never hesitated to choose a rotary after working in one for three decades, but he also wanted to make the most of the technology that was available.
“A rotary is what we know and it’s a good way of milking a lot of cows reasonably quickly.
“Like everyone says, this build is about
futureproofing the operation and having a shed that will attract quality staff.
“It’s also about capturing technology that we can use to make informed management decisions around what we’re trying to do.”
Paul says the new working result – which started up for the first time in March – is everything they hoped it would be.
“Milking is certainly a breeze now because the new shed has made it so
straightforward,” says Paul. “It’s an absolute pleasure and milking is certainly a one-person job. But because the facility is expansive, we do like to have an additional person there to help with cleaning up at the end of milking.
“From the outset it hasn’t missed a beat. We’d been told to expect teething problems, but everything has gone pretty smoothly.”
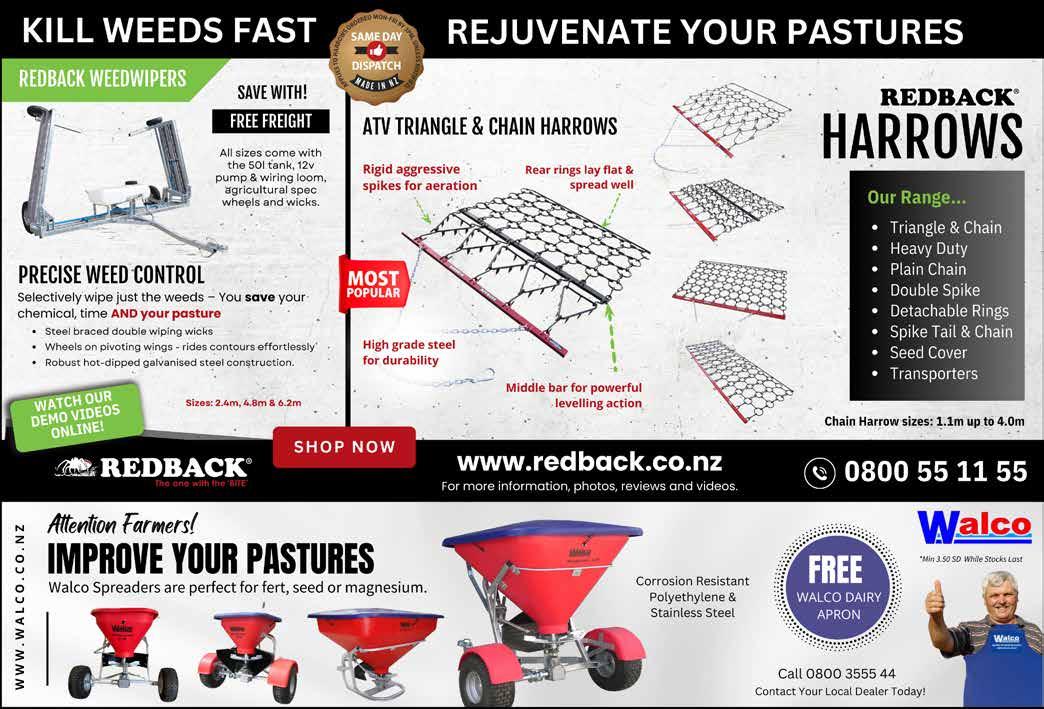
The Lightoller family didn’t spare the horses when it came to designing their 60-bail rotary.
The expansive yard includes an additional rail which is 300mm higher than most yards.
The ceiling is 4.2m from the operator floor to the centre of the knee joint, with a 10-degree pitch to the roof.
Dianna Malcolm
Going robotic
In just six weeks a Taranaki herd achieved what it has taken overseas herds two years to achieve.
When the Greensill family first contemplated converting their conventional Taranaki dairy farm to robotic milking they were told that, anecdotally, cows could take months – if not years – to transition to being in control of the decision to go to the cowshed to be milked.
Within six weeks of commissioning the new robotic milking barn on their 28-hectare property, cows were “voluntarily and consistently coming up to the barn to be milked,” says Layne Greensill.
The Greensill family – farm owners Layne and daughter Helen Loren, who is farm manager, and son Lachlan operate two farm properties in the Oakura district.
Layne says they’d been milking 250 cows at their nearby 80ha property, and 70 cows on the 28ha farm.
“We needed two new cowsheds across both properties and so, eight years ago, we decided to concentrate milking on
the smaller home farm, converting the 80ha farm to drystock.

“That change was enabled by a huge amount of research – starting in New Zealand and then extended in Europe – which confirmed that converting the home farm to robotics and running just 100 cows would enable us to equal or better the production we’d been doing, under conventional systems, on both farms,” says Layne. “It was also cheaper to go robotic than construct a rotary or herringbone dairy with corresponding levels of technology.”
Robotic-ready cows
Farm manager Loren Greensill says deciding to go robotic “affected our genetic strategy and we began breeding ‘robotic-ready cows’ – cows with fabulous, even udders and quick letdown. They also had to have good feet because, with an average 2.5-3 milkings per day, they spend more time walking and standing on concrete – milking and eating.”

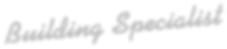
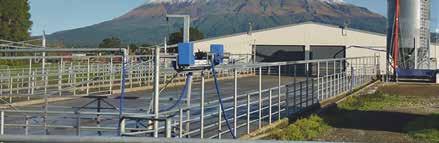

Loren says their past production averaged 480kgMS under a conventional system “but our goal in the 2024/2025 season is 650kgMS per cow”. “A lot of that production increase will be down to the new milking system, and our ability to feed them in the barn during the lower grass growing times of the year.”
The heart
Layne says the new eight-bay barn on a raised site in the centre of the farm is “literally the heart of the business, housing the robotic milkers, feed and drafting lanes with room for a wintering barn”.
Layne and Helen’s son-in-law Rhys Longstaff, of RLC Contracting, commenced earthworks in September 2022 and the shed was commissioned one year later in December 2023.
Specialists in the design and building of dairy wintering sheds, Winton Engineering supplied the new barn which was erected by Layne and Helen’s eldest son, Nick Greensill’s NSG Construction. And it was operational when





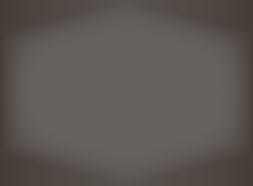




New Farm
Dairies visited in May 2024 with fitout continuing for service rooms, and auxiliary pens and animal bedding.
All concreting was carried out by Freestyle Concrete & Earthmoving of New Plymouth. Pipework for the new dairy was supplied as part of the Lely package, featuring Texas-style one-way gates, and was installed by Layne working with local Tataraimaka business
The Garage.
Robotic system
Layne says their plan is to ultimately milk 180 cows across three robots “but we started with two”.
Lely’s area sales manager Graham Petrie says the Lely Astronaut A5 robotic milking system, coupled with the Lely Astronaut management system, revamps the traditional system with
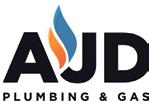
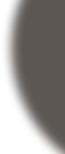
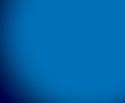
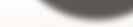
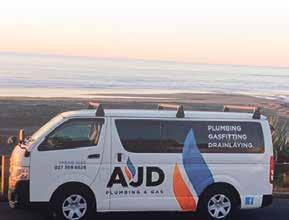

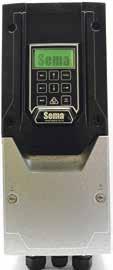

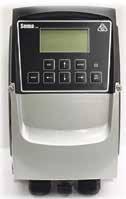
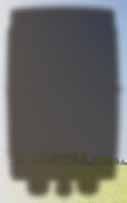

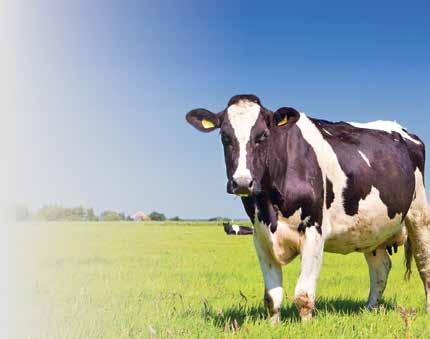
The new barn sits proudly on a central site overlooking the farm.
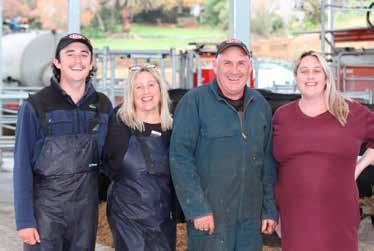
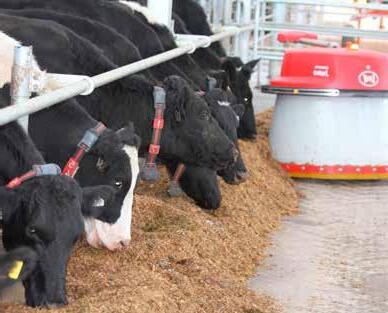
tailored milking “and an incredible amount of insight/data to maximise each cow’s potential”.
“At any time we can see yield in litres, protein percentage, milk fat percentage, liveweight every time they stand on the scales, Somatic Cell Count, milk conductivity and rumination and get alerts for mastitis etc.”
Graham Petrie says natural milking and free cow traffic are not only about the cow’s freedom to choose when to eat, drink, rest or be milked – “they are also about the cow’s wellbeing and comfort during milking”.
“A layman’s overview of the process is the cow voluntarily comes to the barn and approaches each robot – which either admits her for milking or, in the case of her having been milked within a set time period, sends her through and back to the paddock without access to the feed lane.
“Once accepted, the cow enters the
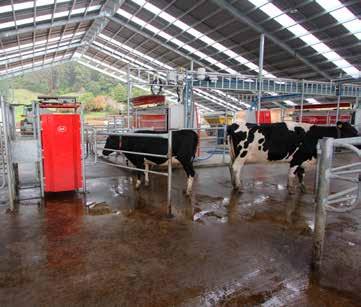
milking zone and the robot commences pre-milking, assuming normal vacuum when the cow lets her milk down.
"Her liveweight is measured as she milks. Each cow is fed a prescribed diet while milking and, once finished, gains access to the feed lane.”
Graham says again, each cow decides when she leaves the feed lane, passing through a drafting gate which directs them to one of three grazing areas – which are preplanned and entered by Farm Manager and nutrition specialist, who is Loren.
“Automatic washing of each robot takes place two hours in every 24 hour period.”
The Lely Astronaut robotic milking system was installed by Bromley Dairy & Pumps of Feilding, which is the Lely franchise in Taranaki and Manawatū.
Ben Bromley of Bromley Dairy & Pumps says his team installed the robots and some of the vat and cooler plumbing. “All milk lines are insulated and milk is taken down
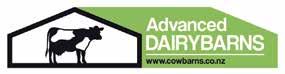
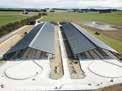
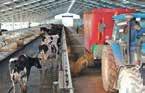
to four degrees Celsius before it goes into the vat.”
All plumbing, sumps, concrete culverts, gates, washdown and the new effluent system – including sand trap – were installed by AJD Plumbing of New Plymouth. Feed systems and pumps were installed by Moa Milking & Pumping of Inglewood.
The transition
Transitioning the cows to the new environment as the barn was nearing completion, Layne says the team spent a week prior to commissioning letting the cows come up and go through the shed “and have a nosey and get comfortable and then another week being here twice-a-day”.
“The first week of milking we reduced available feed in paddock to increase their interest in coming to the barn to get a feed,” says Layne.
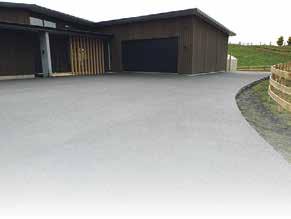

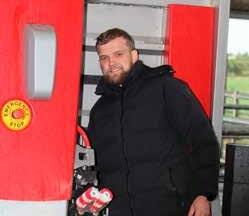
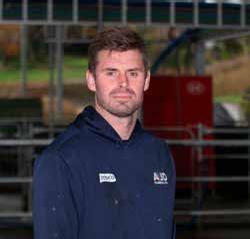
“Our feed supplier tailored a particularly enticing feed mix for the robot and they soon learned that they needed to walk into one of the two robots before they would be fed and then they also got unrestricted access to feed in the raceway.
“Within six weeks we didn’t have to get a single cow out of the paddock – they were all coming up to be milked of their own volition. The cows are happier, quieter and milking like champions. We couldn’t be happier.”

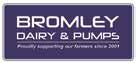





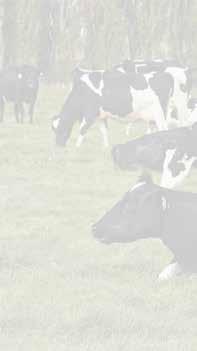
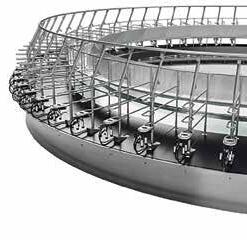

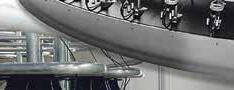
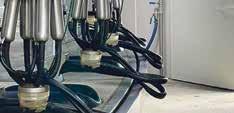

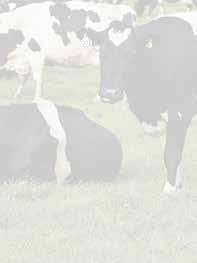
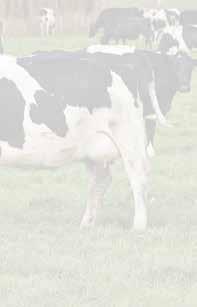
“Effluent made easy”
Ben Bromley says Bromley Dairy & Pumps responds remotely to any issues and ensures same-day service if required.
Alec Dravitski of AJD Plumbing is the son of friends of the Greensill family.
Clare Bayly
Interior of the barn showing cows in feed lane on the left, the exit drafter/weigh scales to the cow’s right, two robotic milkers, additional yards and room for development of wintering barn.
The Greensill family: Lachlan, Helen, Layne and Loren Greensill.
Family’s dreamcome true
The dairy taking shape inland from Rahotu in Taranaki, in June 2024, is a tribute to a family legacy of dairy farmers and, fittingly, the first of its kind in New Zealand.
In 1911 Rob Willcox’s great grandfather purchased the original 140 hectare farm known as the “bush block” while farming on the coast at Rahotu since 1898. “So we’ve got a lot of history here,” says Rob. Rob’s grandfather purchased the bush block from his father’s estate in 1928 but unfortunately suffered a massive stroke in 1940, meaning Rob’s father had to leave school and help his mother – who had come to New Zealand as a war bride in 1919 – to run the farm as his older brothers were away fighting in World War 2. This was the start of a very strong feminine role in the running of the farm.
Rob’s father Frank purchased the farm in 1959 from his father’s estate after running the farm with his brothers. Rob and his wife Gwen came home to the farm in 1971 and in the 1980s began taking over the farm. Their daughter Tina Worthington joined them in 2007. In 2012 Rob, Gwen and Tina formed Willcox Farms Ltd, all three being shareholders.
Three years ago Willcox Farms Ltd was able to purchase the neighbouring farm from the long-standing Fleming family, taking the
farm up to 317 hectares. Tina, her cousin Scott Chadwick and his wife Jacqui run the home farm and contract milker Buddy Sharpe runs the new farm.
Rob says the old shed “was an internal rotary and there was a 40-aside herringbone on the new farm”. The expiry of effluent consents in 2025 and new Fonterra regulations led us to take on the massive decision to build a new dairy in the middle of the combined farms, halving the distance the cows have to walk.
‘Start to finish’
Rob says the family has a long association with Brian Hill builder and approached him to design and build the new dairy. Brian recently sold the business to his son Jono but remained involved in most aspects of the design and build. Corbin Mills was on-site foreman.
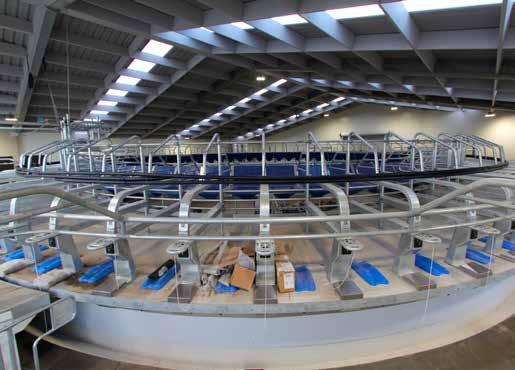
Willcox Farms
client. The Willcox dairy has a larger footprint, providing a spacious interior for the platform and service rooms. “The building has a steel portal frame with timber purlins, a colour steel roof and freezer panel walls,” says Jono.
Brian Hill Builders has been building in the Taranaki region for 50 years, Jono saying they are ‘start to finish’ builders doing everything from design to building including concreting across the spectrum of needs –residential, commercial, agricultural, and repairs and maintenance.
“We have a range of designs for dairies which we then tailor to suit the needs of each
Mitre 10 New Plymouth Trade has a long-standing trade relationship with Brian Hill Builders and was the chosen provider to supply products needed to construct the Willcox dairy. That relationship enabled the close collaboration needed to ensure everything was ordered and delivered on time.
Mitre 10 New Plymouth supplied all structural steel and mesh used in the floor through to all yard areas along with steel for the blockwork in the pit and access areas,
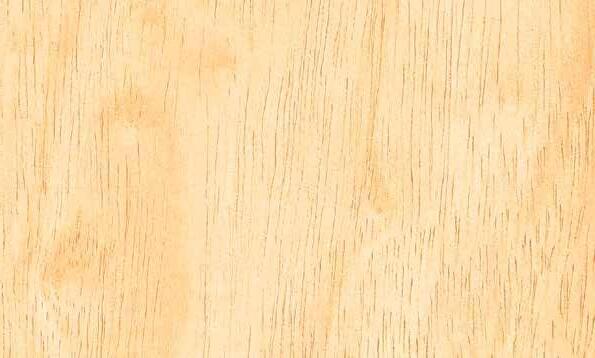

and structural timber ply for the building platform and all fixings. Framing and roof structure timber and correct bracing components with all associated fixings were also supplied on time and to spec.
First for NZ
Entrenching the legacy philosophy, the new dairy will be a showpiece for a revolutionary milking system from DeLaval – the first of its kind in New Zealand.
DeLaval’s technical specialist for Oceania, Graeme Middlebrook, says Flow-Responsive milking speeds up the milk-extraction by lifting the vacuum level when high milk flow is available and then reducing level again once high flow has ended.
“This replicates what happens in nature when a calf’s initial sucking stimulates
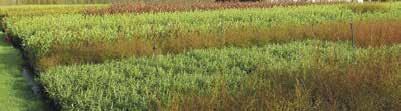

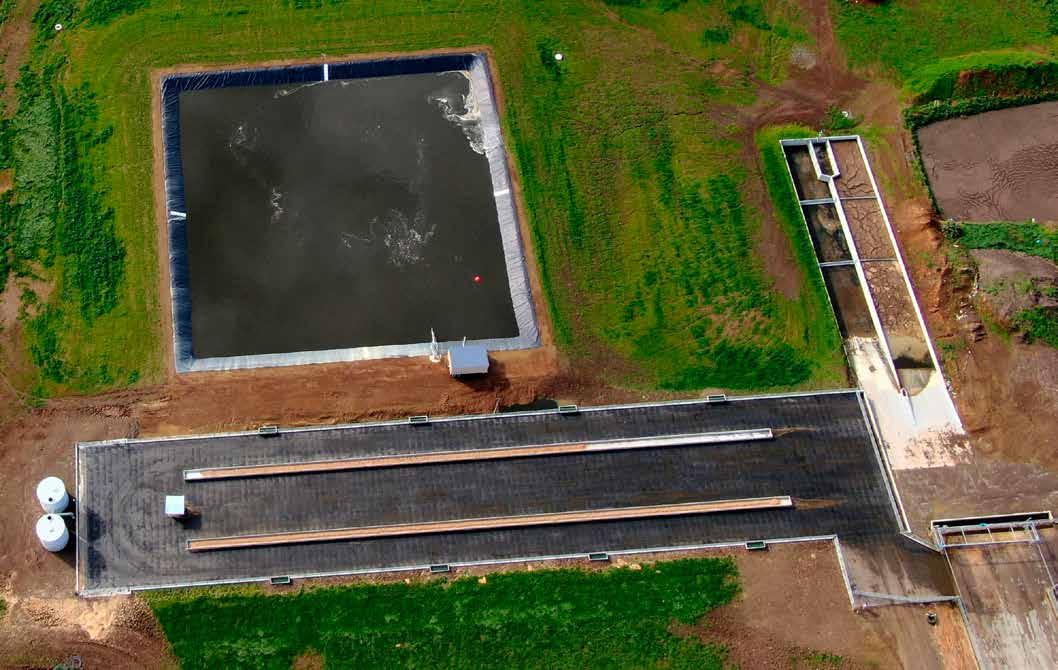
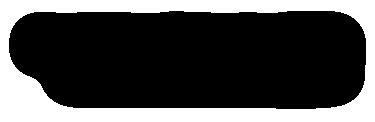

The new 60-bail E100 DeLaval rotary platform features DeLaval ComfortBails where wires, pipes and technology are integrated into the design of the bail.
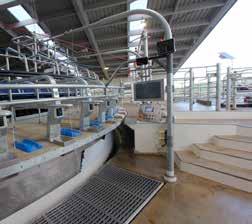
let-down and prevents the inevitable trade-off between udder-health and productivity that occurs in a traditional fixed vacuum level over the entire milking process.
“DeLaval has been producing FlowResponsive milking systems overseas for many years, there are two in Australia and this is the first in New Zealand,” says Graeme.
“Pulsation and vacuum respond to the milk flow in real time and adjust accordingly. To stimulate the cow for milk release at the start and then to balance how quickly milk is released with how quickly the milking machine can harness it.
“Farmers know that flow changes during milking – milk release timing and speed varies from cow-to-cow and this unique system tailors vacuum and pulsation to each and every cow in the herd.
“Additionally, the system senses when flow reduces at the end of milking and accordingly tails off – preventing overmilking,” says Graeme.
Rob says Flow-Responsive milking appealed on at least two fronts – animal welfare and speed of milking. “Stimulating and responding to each cow’s milk flow reduces
The exterior of the dairy has taken shape with internal fitout taking place.
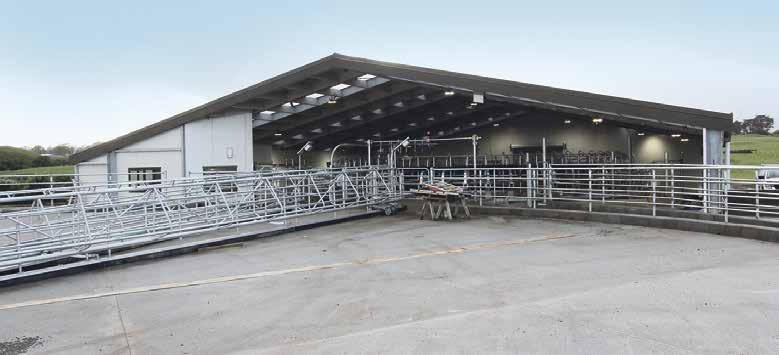
or eliminates the contribution of milking machines to teat damage, and potential mastitis, enabling her to reach her potential and increasing her health and life in the herd. Overall milking time is 20 per cent faster than traditional systems.”
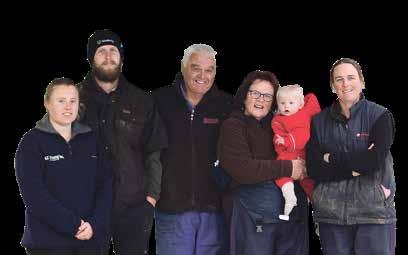
Flow-Responsive milking is just the start of the DeLaval ‘firsts’ installed in the new dairy by Coastal Agri Services of Opunake.
Clusters first
Coastal Agri Services’ Simon Foley says the new Willcox dairy features the revolutionary DeLaval Evanza clusters which come with TopFlow claw and a unique cartridge replacing the traditional liners making milking faster and more efficient.
“The new 60 bail E100 DeLaval rotary platform features DeLaval ComfortBails
DAIRY WALL COATING SYSTEMS
Acraflex Dairy Wall Coating Systems save hours in cleaning, seal against bacterial build up and create a bright, hygienic working environment.
where wires, pipes and technology are integrated into the design of the bail.
“The dairy has a high degree of automation with DeLaval’s MA200 automatic cup removers, body condition score camera, on-deck teat spray and Delpro FarmManager.
“The new dairy also features DeLaval Sort Gates which when combined with the DelPro herd management system efficiently drafts cows according to drafts set either before or during milking.
“Cupping will be effortless in the new dairy thanks to a milker platform the height of which can be adjusted to suit the height of the
milker,” says Simon.
There are no bail restraints in the new dairy as culling has taken place to remove slow milkers. Rob is confident this will be complemented by Flow Responsive milking “which will mean the cows milk out well, and faster”.
Andrew Wood of Coastal Welders built the galvanised steel portals for the building along with consulting to design and fabricate the yarding. Cow flow was paramount in this, and any yard design work. The backing gates feature wireless solar panels which send a signal to solenoids to turn on the water which drives the gate. The design of the yards saves water and hosing time, if any is needed. Personal safety was also important in the design, keeping stock separated from the operators.
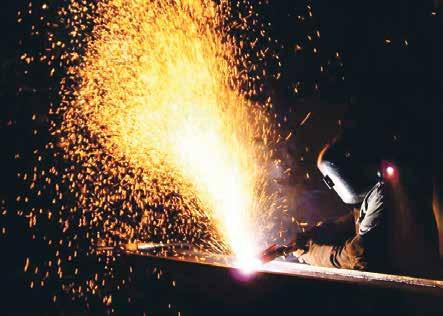


Left: The Willcox family: Jacqui and Scott Chadwick, Rob and Gwen Willcox with Marni, and Tina Worthington.
The dairy features DeLaval’s MA200 automatic cup removers, body condition score camera, on-deck teat spray and Delpro FarmManager.
A minimalistic approach to concrete areas and containment was a priority.
The interior walls of the dairy are coated with the seven-layer Acraflex paint system applied by Surfatex 2019 Ltd, providing a hard-wearing, easily cleaned surface. Tina’s husband Bryan Worthington fitted out the farm office and kitchen with joinery.
Animal handling, veterinary and AB facilities include a Wrangler Cattle Crush, which can quickly and simply be adjusted to accommodate varying size cows, will add comfort and efficiency to the treatment of lame cows.
Effluent research
Rob admits he probably put as much research into a new effluent system as he did to the new dairy, duly appointing Davieth Verheij from AgFirst Engineering in collaboration with DeLaval Coastal Agri Services to complete the full dairy effluent system design and build on a greenfield site close to the new dairy.
Effluent from the dairy flows to a weeping wall system via a rainwater diverter. The AgFirst weeping wall design was constructed from custom-built precast concrete panels by Brian Hill Building. The weeping wall design provides passive solids separation via gravity with no moving parts. It also offers significant solids storage for targeted land application only twice per year. This simplistic design provides peace of mind for troublefree effluent management by removing the risk of solids build-up in the pond and risks commonly associated with effluent solids and irrigation equipment.
From the weeping wall the filtered effluent flows by gravity to the new lined effluent pond.
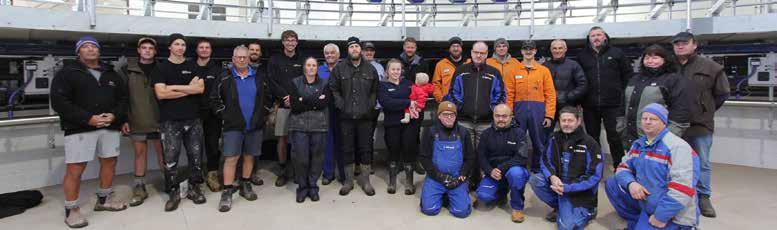
Trapezoid pond
The pond is built in the shape of a trapezoid to suit the landscape, minimising earthworks requirements and maximising land use. Rob expresses appreciation to Jonathan Price from Campbell Contracting for digging the pond with help from his father John, who came out of retirement to operate a hired 30 tonne digger. Typically, a square pond would be desired for pond stirring efficiency. However, as the solids are removed by the weeping wall, regular pond stirring is not required. This is a big saving on system operating costs.
The new pond has a total volume of 4,800,000L and was lined with High Density Polyethylene by Viking Containment. The HDPE liner has a 20-year product warranty and comes in 8.0m wide panels, which allows efficient deployment and installation.
The seam welding process is also unique incorporating an air channel within the seam, which can be pressure-tested to ensure its integrity.
All welding and testing is documented in a comprehensive Quality Assurance Report. Viking Geoladders were incorporated to provide safe access for emergency evacuation
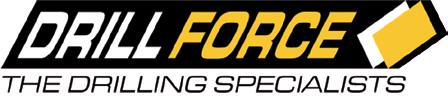
of the pond or for maintenance when servicing pumps or control equipment.
Irrigation design
A large part of the effluent system design is the effluent irrigation system. A Wangen progressive cavity pump reticulates effluent around the property with effluent applied to land via the AgFirst ‘Weta’ Low Rate Travelling Rain gun irrigator. The Weta achieves large irrigation volumes at low rates and is the only irrigator in the world that simply maintains its selected travel speed – no matter where it operates on the farm –ensuring a controlled and uniform nutrient application. The irrigation system was built by AgFirst Engineering and installed and commissioned by Coastal Agri Services.
When New Farm Dairies visited in earlyJune 2024, the start of calving the 750-cow herd was just six weeks away, so the building site was a hive of activity as contractors focused on getting it operational well before the target date.
The whole family say completion of the dairy will be a dream come true.
Futureproof farm
“This is a family farm,” says Rob. “Three generations of my family have farmed this land and our hope is that our investment in this new dairy will futureproof the farm and hopefully ensure that future generations of our family continue to live and farm in Rahotu. This is our legacy.”
Tina agrees. “My cousin, Scott, and his wife Jacqui, are as passionate and committed to the farm as I am. “I’ve also got a couple of kids who I hope will eventually join me on the farm so the future’s bright – thanks to Mum and Dad’s forsightedness and commitment to the family.”
Tina is not fazed by the prospect of transitioning the herd to the new dairy.
“They are used to being milked and fed in a rotary, albeit an internal rotary – where the cows face outward – so we understand there will be a settling phase. But I’m sure the allure of on-shed feeding will resolve that.
“We plan to run the entire herd through the dairy a few times before they calve – hence while calving is due to start July 15. We are aiming to start running cows through around the beginning of July.”

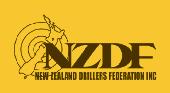
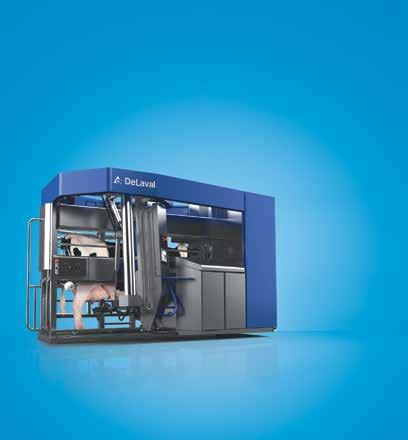
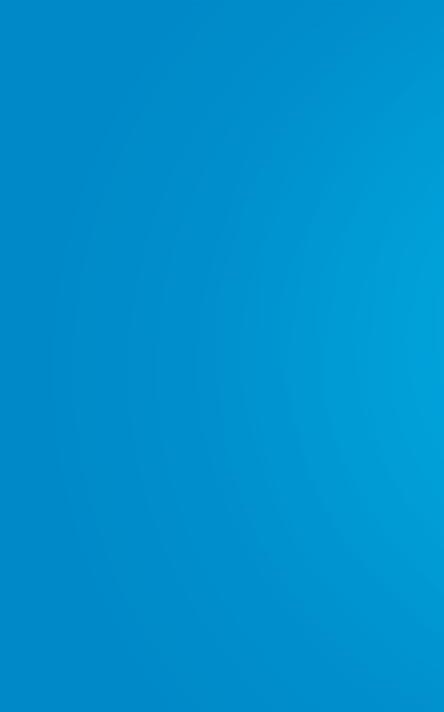
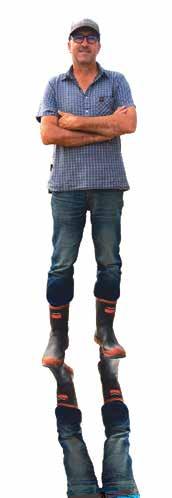
Clare Bayly
Weeks before the dairy was completed, the construction team found time to stop for a photo.

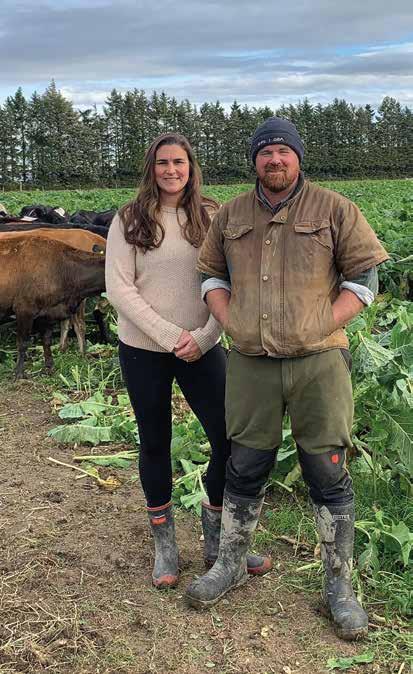
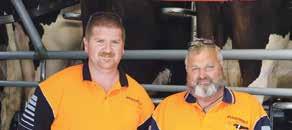
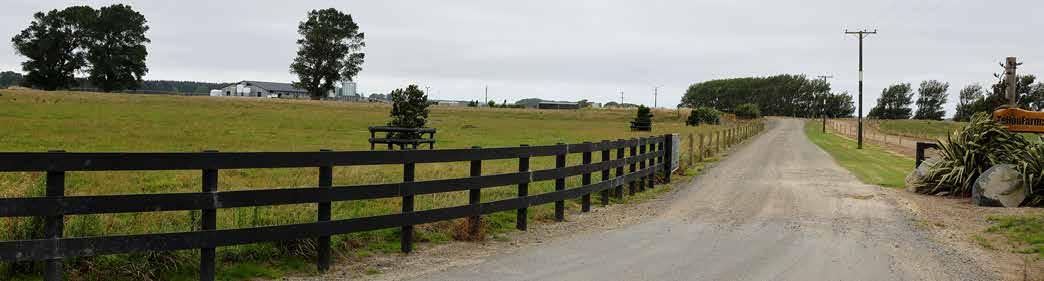
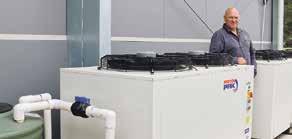
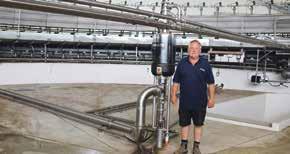
Even from a distance the Te Hou Farm’s new 80-bail rotary is imposing – and the team responsible for it remain intensely and collectively proud of the fresh heartbeat it’s given this Rangitikei operation.
Located 12km from Bulls, Te Hou Farm milks 1600 cows – with 300 autumncalving – on 1324 hectares, which has a 580ha milking platform.
Production is 520kgMS per cow, which equates to between 800,000 to 832,000kgMS for the season.
They are split into three herds based on age, weight, and stage of lactation, in addition to a sick herd.
Te Hou Farm is managed by Jarred Clode, who relocated from Hinds in Mid-Canterbury in 2017, bringing with him new ideas for one of the biggest single-site dairy producers in the lower North Island.
As the partnership has acquired neighbouring properties, the business model has steadily changed for Jarred and its owners, Ngā Wairiki Ngāti Apa from Marton with 67 per cent, and the Ātihau-Whanganui Incorporation owning 33 per cent.
In 2020 Jarred’s role expanded to operations manager, and it was clear to him at that point the 50-bail rotary was holding the farm back.
Jarred presented the idea to his board that building a new cowshed on a greenfield site would be a logical and efficient choice. He wanted to mirror a cowshed he had worked on in Canterbury. The board supported the decision – and a monumental shift was initiated.
“Our milkings used to take five hours a day,” says Jarred. “The old cowshed was just…old, and there was a lot starting to go wrong with it and I knew if we were staying, we would have to change things.”
That shift included demolishing the
50-bail rotary – because that site was still central to the farm – and transitioning the entire herd into a 36-aside herringbone, which they had inherited on a neighbouring 100ha buy for the duration of the build. The earthworks had been completed a month earlier. They then had to endure another switch back to the new rotary at completion.
“It was a lot of cows and a lot of stress on the staff at that time,” remembers Jarred with a grimace.
During that time, Jarred and his wife, Bronwyn, also welcomed their son, Will. It has made the last three years a blur of action, decisions, and work for Jarred, aged 40, and his team of five dairy staff, a drystock head stockman, two calfrearers, and administration staff which includes Bronwyn.
Milkings clipped by three hours Managing the new construction within a cowshed that operates 365 days of the year has been a testament to their
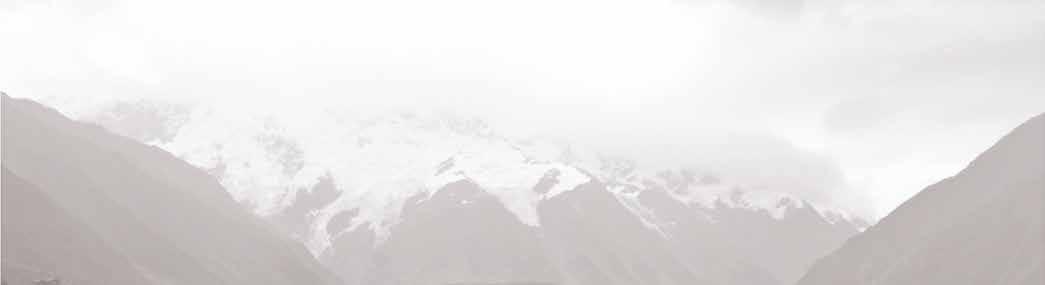

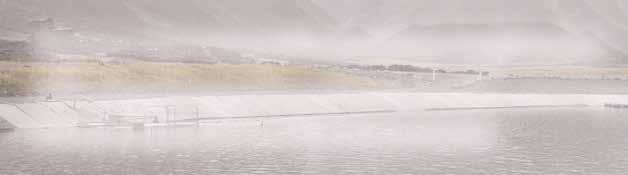
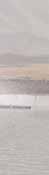
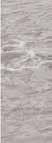

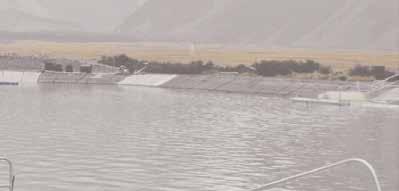
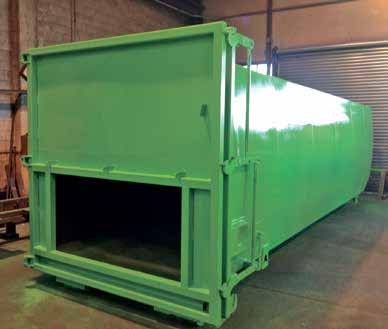



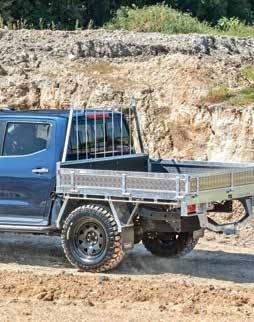

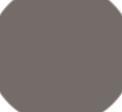

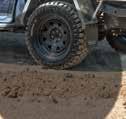
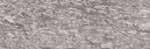

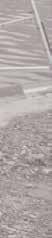
APB Electrical’s senior sparky Barry Penny-Baker and chief executive Andrew Boustridge.
Dairy Technology Services’ Aaron Evans says Te Hou installed a Glycol chiller and vat wraps.
Steve Bromley, of Bromley Dairy & Pumps, was responsible for the water tanks and stainless steel plumbing for water for the plant.
commitment. The final result is they have lifted cow numbers, and shortened milking times by three hours a day.
“The greatest thing is the time and the efficiencies of cow flow with the new yard, and cow comfort,” says Jarred. “I’ve replicated some things from a cowshed I worked at in the South Island at Rangitata Dairies, which is a little different to North Island dairies.
“We have included a big open 5m apex here at the North face. That was one of my biggest pushes, because it offers better light and ventilation. We also allowed a 3m overhang for more shelter at cups-on and at cups-off.
“We added a massive sprinkler system on the yard, and we have more space in the yard. The cows like the shed better. It’s brighter, lighter and the technology is great too. It’s all auto plant, vat, and floodwash with the auto yard clean on the backing gate. Everything adds up to time savings, efficiencies, and consistency.”
Being able to preserve their 2018-built feed pad, effluent system, and exit from the old dairy and merge it into the new build was a welcome saving – in addition to their Wrangler hoof-trimming set-up.
From the ground up
The enormity of the earthworks is one of the big early impressions on the driveway approach. They had to lift the site by 3m to allow enough room for the drainage and effluent management. It meant ground zero on the new cowshed was at the same level as the roofline of the old cowshed.
The earthworks fell to Sutherland Contracting. Alan Sutherland says when his son, Logan, dumped the first 24-tonne dump trailer-load he realised the enormity
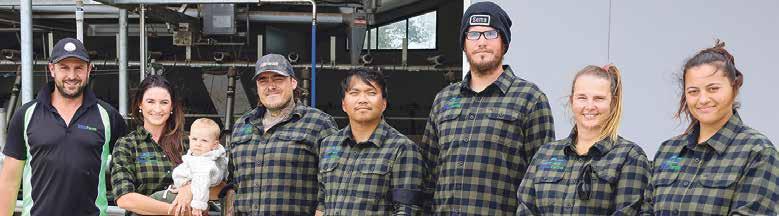
of the mission.
“The challenge was the sheer size of it,” says Alan. “Logan did thousands of loads for two months non-stop. I think he saw the same butterfly and the same rabbit in front of him every day for the entire time.”
Alan adds that establishing the foundation turned into so much more.
“It brought a lot of us contractors together in various things and built relationships that we’ve carried on post-build. We were all sort of locals, but we hadn’t worked this closely for this long before.
“There were definitely a lot of laughs. We did pull some late nights, and the odd evening a little fairy lady [Bronwyn] came out with a few meals. Normally when we do a contract, we do it, and that’s it.
“But for this one we were fully involved throughout, so we got to see the completed job. Every time I come here now; I think about how we built it.”
Jarred says they chose a Waikato plant and Moa platform for a straight-forward reason: “Because they build a basic, easymaintenance, good shed”.
The Orbit 5500 concrete platform installed by Moa Rotary Platforms features an automated lubrication on a double beam with nylon rollers. The 100mm deep reinforced concrete deck has a 2.7m platform – which is ideal to protect machinery, and for better cluster alignment and application – a heavy duty galvanised sub-frame and Automatic Cup Removers. The outward sloping deck allows for easy entry and exit and sends manure to the outside of the platform.
Modern technology
Steve Bromley, of Bromley Dairy & Pumps, at Feilding says they were already servicing Te Hou’s existing machines. He was also responsible for all of the water tanks, and the stainless steel plumbing for water for the dairy plant.
“The cool thing about it is that the platform and the milking plant are from the same people, and it’s a tried-and-true New Zealand-made product that is very reliable,” says Steve.
“It’s also very customer-focussed. We like that. The features of the Waikato ECR-S
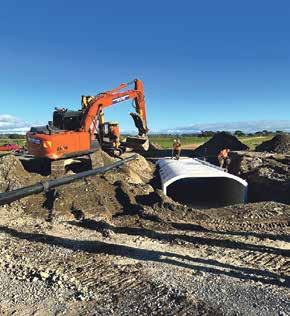
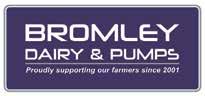

[Electronic Cup Removers] are the new touch buttons where the light reflects what’s going on with the milk and you can see that at a glance from a distance.
“They also include the ‘lift-to-start’ function; it controls the cow restraints and the SmartSPRAY at the end of milking.”
Steve says the whole idea of this plant is to go forward with modern technology.
“The shed is the blueprint for every new shed now. It also has a multi-port centre gland, so all the milk, compressed air, wash water and teat spray goes through underneath the platform. Running over the top is increasingly an OH&S [Occupational, Health, and Safety] issue, and bird problem.”
Steve is particular about his workmanship and favours stainless steel and medium density alkathene pipe with a 50-year rating.
“I like a nice job, and farmers are paying a lot of money for their new sheds so why shouldn’t it be nice, reliable, and easy to service?” he asks. “The water here is very hard on galvanised pipe, so we were mindful of that.”
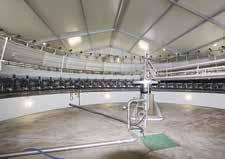
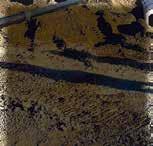

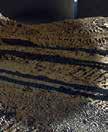
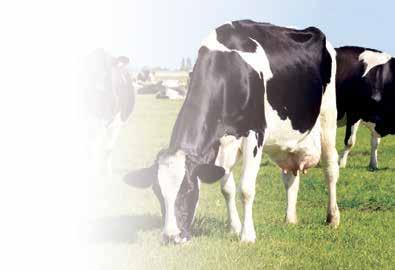



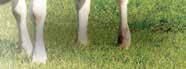















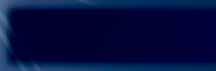





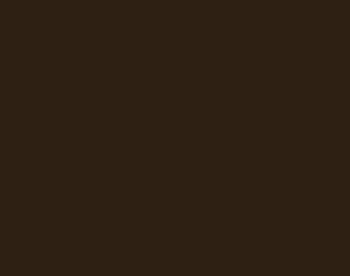
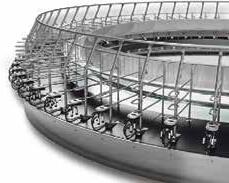

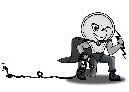
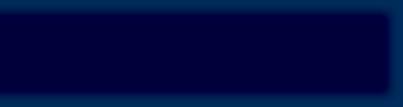


Te Hou Farm Te
Jarred Clode and wife Bronwyn holding their son Will, with the Te Hou team of Dillan Baird, Glenn Cuenca, Brad Curtice, Jasmine Thomas, and Rachael Laurenson.
80 bails of new technology
The farm is 70 per cent irrigated by five centre pivots – the biggest one covering 65ha. The paddocks have all been subdivided into six to nine hectares, and the cows receive 1.2 tonne of supplement a year, fed on the shoulders of the seasons. The cowshed includes individual in-bail feeding and auto-drafting.
Wrapping up chilling
Chilling milk has become a clever and innovative area to be involved in. Dairy Technology Services’ Aaron Evans says Te Hou pays significant attention to how it handles their product. Not only did they invest in vat-wraps for the 21,000L and two 30,000L vats, they also installed a Glycol chiller so the milk hits the vat at six to eight degrees Celsius, and is chilled to 4.5 to five degrees Celsius by the end of milking. Vat wraps can drop vat refrigeration energy consumption by up to 25 per cent, by reducing the vat’s environmental heat-gain.
“It’s all good to get the milk into the vat cold,” says Aaron. “But exposed stainless steel heats up pretty fast on a summer day, and it takes a lot of power to keep that milk cool without the vat-wraps.
“We find the chiller won’t start at all during the daytime if the vats have those wraps on them. They also help with the temperature pull-down, because the vats don’t have the heat load from the sun on the stainless steel. We can wrap any vat, of any size.”
Aaron says the rising price of refrigerant gas now makes investing in new units the smart choice if the units are aged 10 years or older. For Te Hou, everything was new. “We’re the last ones here at the end of the
project to install this part of it, so there is always pressure then to get everything up and going before the shed starts. It’s always nice, when everything is lined up, and it looks neat and organised.”
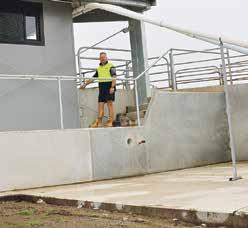
Power it up
This was a monster installation for the electricians on-site, APB Electrical. The company’s chief executive officer Andrew Boustridge says APB Electrical had worked with Te Hou for eight years in day-to-day runnings and was happy to be involved in the new build.
“It’s a great achievement to be standing here at the finished cowshed with it in full swing,” says Andrew. His words are echoed by senior electrician Barry Penny-Baker. “Knowing what the previous cowshed was like to where they are
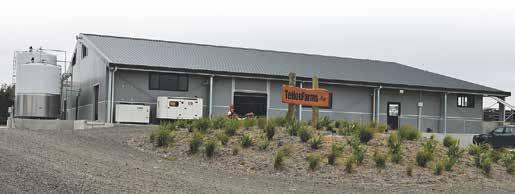
today is so different by leaps and bounds,” says Barry. “Everything is now plug and play. The challenges were putting the infrastructure into the ground prior to pouring the concrete. Within that we were anticipating the future – so instead of running two conduits, we run three because at some stage we all know there will be another addition. We try to always do that, but it’s not always allowed for in the budget. This time it was.”
What is he most proud of?
“Everything. This is the first cowshed of this size for me. To come away and the first day and everything worked great was a big tick.”
Barry says the size of the project meant the team had plenty of time to get to
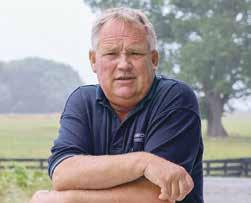
know one another. Standing beside the 110kVA generator with the cows behind him, he reflected on the experience.
“You can’t go into a project like this not being able to work together. There is no room for big attitudes. We will be here for ongoing repairs and maintenance and general upkeep to keep this huge enterprise going.”
The only thing that is not automated at this point is the cows don’t have collars, and heat detection is still manual.
Surfatex, which specialises in Acraflex dairy wall coatings, in addition to industrial coatings, anti-slip solutions and protective flooring plays a big role in keeping this cowshed safe and clean.
The high-build paintwork includes seven coats of paint, creating a protective barrier which makes it easy to clean.
For Jarred – now in his eighth season with Te Hou – the changes have completely changed his day-to-day life and made it easy to retain team members.
“The board were very supportive throughout and took everything I’ve suggested and never turned anything down. I’m really grateful for the faith they’ve shown in me.
“The cowshed is awesome, our team love it, and we are all very excited for what the future holds for the herd and for our business.”
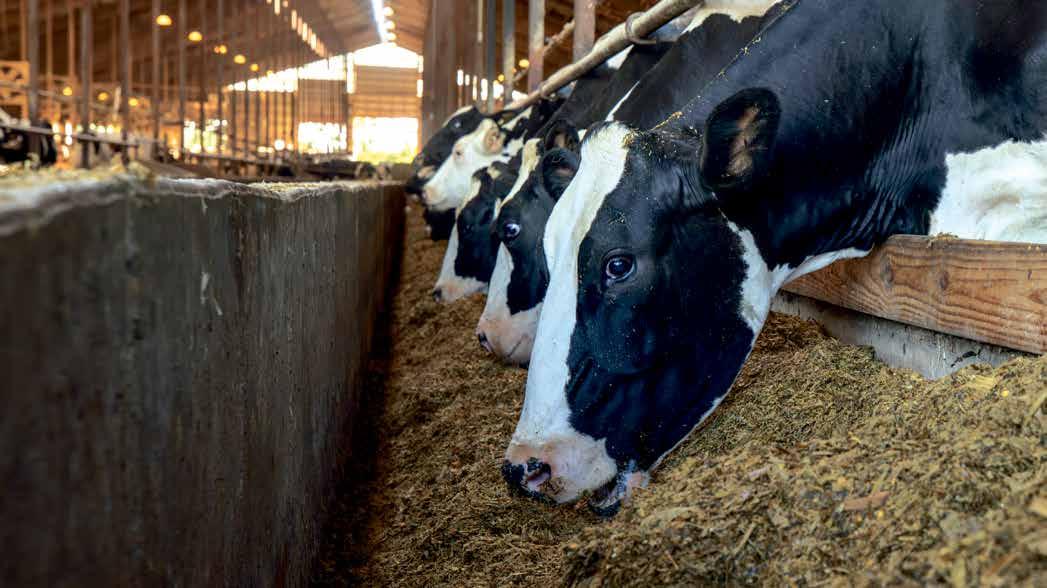
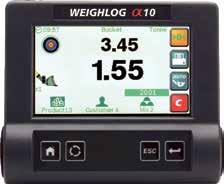
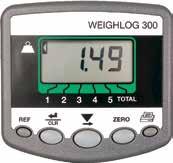
Alan Sutherland, of Sutherland Contracting, had to lift the greenfield site by 3m to allow room for drainage and effluent management – here he gives perspective to the earthworks.
The new operation houses an 80-bail rotary on this Rangitikei farm, 12km from Bulls.
Steve Bromley, of Bromley Dairy & Pumps.
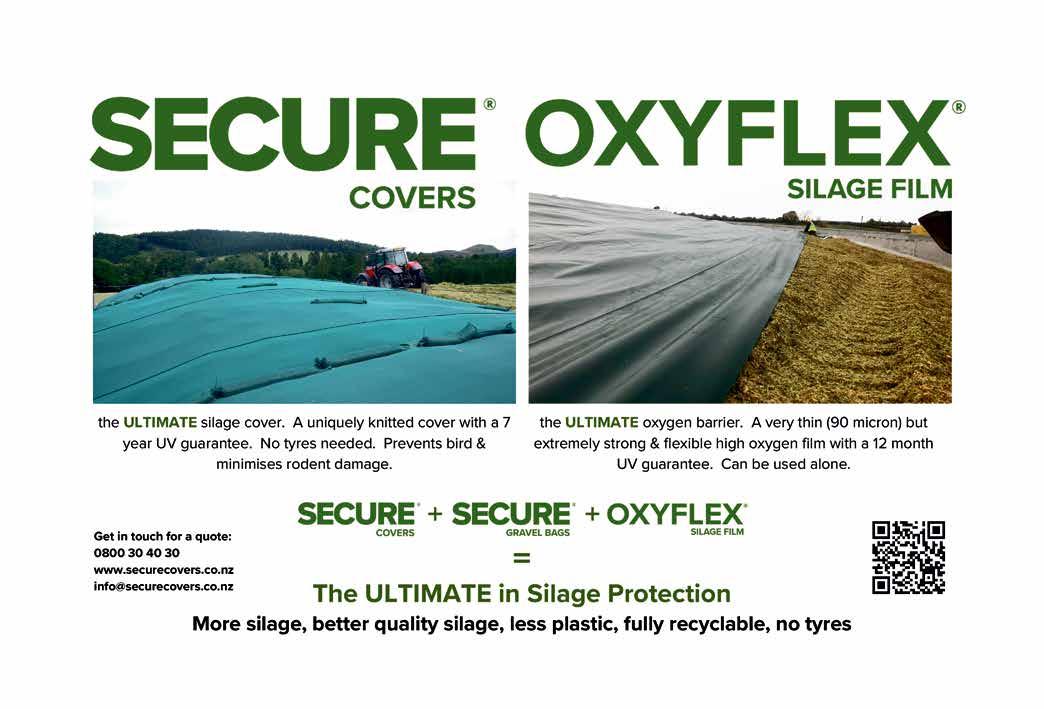


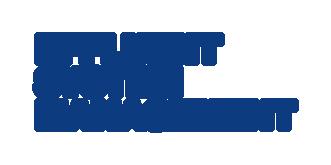
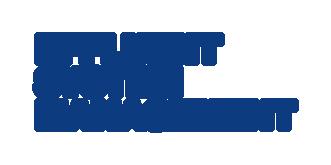
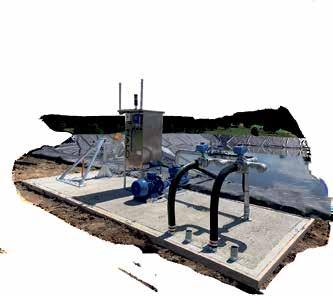

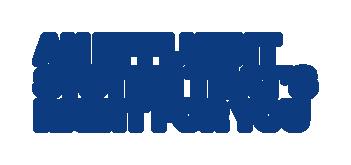
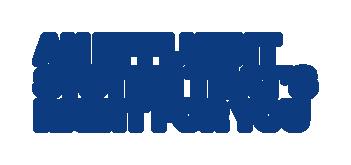
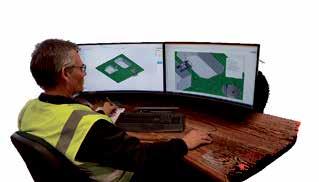
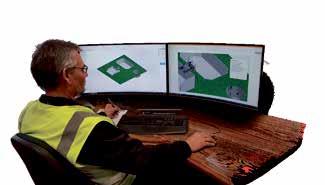

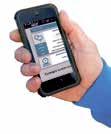
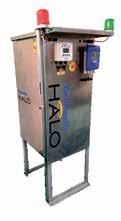
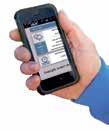
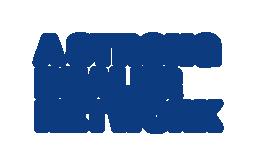
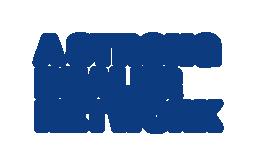
























































































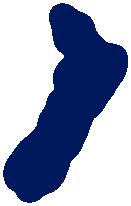
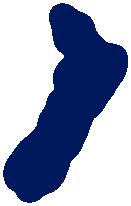





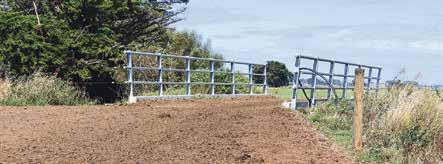
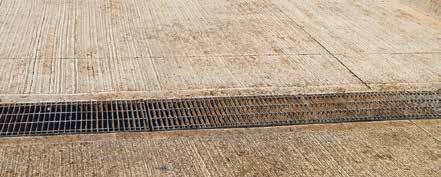
Making days
When Jim, Dave and Emily Malone tore down their cowshed, they looked at each other and took a deep breath…because the clock was ticking.
They had eight weeks to rebuild a 30-aside herringbone before calving started, Emily was pregnant, and there weren’t a lot of Plan Bs.
The couple milk 270 cows in an equity partnership on 93 effective hectares with Dave’s father, Jim, at Sanson about 30 minutes west of Palmerston North.
To create the window, they needed to achieve the build, they dried off three weeks early and dropped the start of their spring calving back by 10 days.
“That demo moment when you’ve no longer got a cowshed was pretty confronting,” admits Dave. However, there were some enviable professional advantages within this family when it came to the rebuilding. Emily is a draftsperson for Resonant – multi-disciplinary engineering and surveying services. Dave was a former residential builder who’d come home eight years earlier when his mother, Elaine, was fighting cancer. It has tied the three together in a partnership founded on deep respect and care.
Fiscally responsible
None of them wanted to over-capitalise on the flood-prone property, but they all wanted a classy result that would make their working days easier. Their old cowshed was born as an eight-aside in 1963, before stretching into a 12, 14, then 20-aside by 2000 under Jim’s stewardship. Dave was ready for the next step.
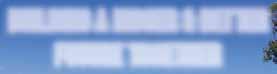
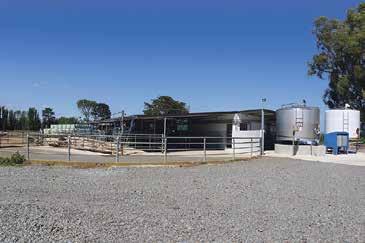

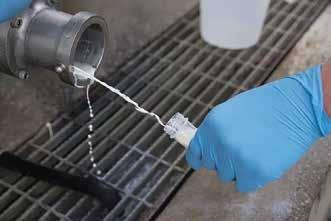
“I’d been milking for eight years, cupping up and daydreaming about what I’d change,” says Dave. “We’d looked at heaps of sheds around the area as we got more serious about it and plucked ideas from everything.
“But the biggest thing for us was – if we were going to do it – we needed to do it once, and we needed to do it right.
“This wasn’t about potential resale; it was for our future sanity. We had made the commitment to be here, and we decided to take on some debt and do it properly.”
The initial plans came in over budget, and instead of cutting corners the three of them rolled up their sleeves and did a significant amount of the grunt work themselves – painting late at night, laying conduits through the weekend, running alkathene and water lines, hooking up hoses, and completing brickwork together.
A game-changer
Emily proved to be a game-changer and a big saving for the partnership with her connections and knowledge in the planning. She handled all the council consents, which were more complicated because they are on a flood-prone property. It allowed them to spend less than they had originally asked the bank for. They did drop two storage rooms from the build to save costs. “Looking back now, I’m glad we didn’t put them in. We didn’t need them,” says Dave.
The new toilet almost got flushed too, but its inclusion has been a popular save.
“The toilet was an additional $12,000 because it needed a full septic system,” says Dave. “We didn’t realise how much of an inconvenience it used to be for everyone who came to the farm that there was no toilet available at the cowshed.

Steve Bromley of Bromley Dairy & Pumps, farmer Dave Malone with wife Emily holding Archie, Jim Malone, and Alf Downs Contracting Ltd’s Johan Hayward.
The new bridge was a necessity.
Two stone traps save time during hosing down.
easier
“It’s been a surprise just how useful that single decision has been for the operation.”
Teamwork
The main team involved in the build included Rural Building Engineering, Alf Downs Contracting, and Bromley Dairy & Pumps. They started May 20, 2023, and the new cowshed was completed by July 25, 2023.
Milking still takes 2.5 hours, but the stress levels are gone – and there are some nifty personalised design hacks in this cowshed.
“We’ve saved a labour unit,” says Dave. “Before we had to have two people milk because we had to push every row in. That was the main reason we needed to change. In the old shed the wall was literally at the end of the cows’ noses, and they just didn’t want to go in.
Emily adds: “We do have weekend relief staff, and the new shed has also definitely made getting staff easier”.
The new cowshed is six metres wide with a 1.5 metre pit, Electronic Cup Removers, and it is now a one-man job. Cow flow is seamless, and production is 20 per cent ahead this season. They deliberately didn’t install a wing wall on the exit. Dave says it works well because there is a direct line of vision for the cows exiting the cowshed to the paddocks. Three windows in the wall in front of the cows is also a nod to allowing more light into the structure. The Wrangler crush forms the end of the AI race.
Dave says their contractors were impeccable. RBE also put in a new bridge over the creek directly out from the cowshed because the old bridge was in the way of the new build.
“We didn’t realise how bad that bridge was until we pulled it down,” says Dave.
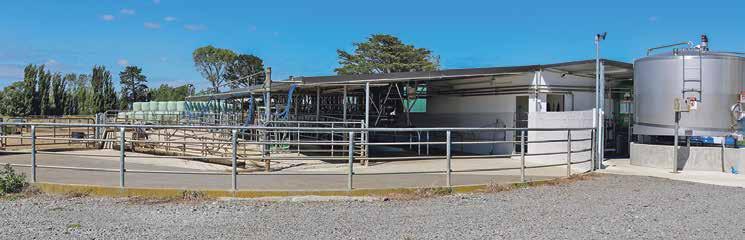
“RBE did a fantastic job across the board, and they were so organised. We know they have built 90 per cent of the sheds in this area in the last 30 years. That’s why we picked them. They had everything prefabricated, ready to go, and they pulled finger when they needed to.”
Smart installation
Steve Bromley, from Bromley Dairy & Pumps, was responsible for the plant and he made lots of practical suggestions and didn’t waste anything. Right down to the simple things like making sure they had multiple taps so they could easily deal with water challenges, and stainless-steel TriFerrule clamps for durability, and easy access to the pumps for any repairs.
“When we pulled everything out of the old cowshed, we were careful how we did it and we put it all in the hayshed,” says Emily. “Steve worked out what could be re-used, and we got rid of the rest. We re-used all our claws, pulsators, and milk pump.”
Dave adds: “We upgraded to a Blower Vacuum pump with a variable speed drive one”. “It matches the airflow, so we are using less power. Our power bill has dropped slightly. I expected it to rise, because we have gone from a 7.5KW
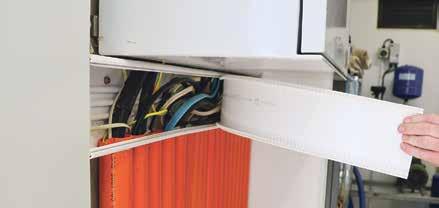
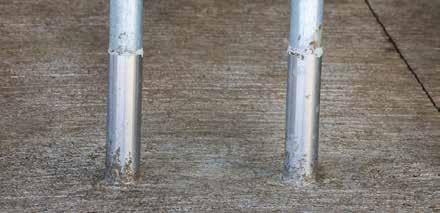

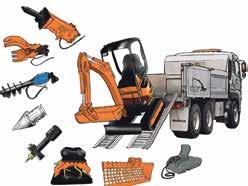

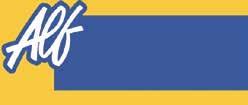
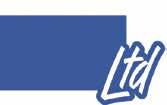
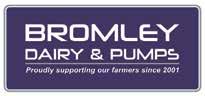




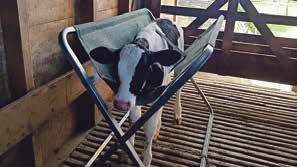
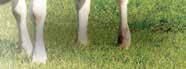
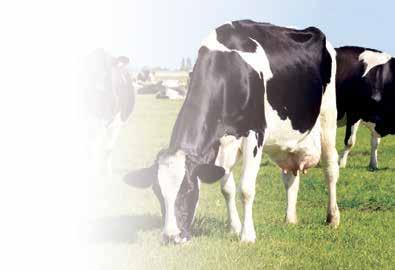














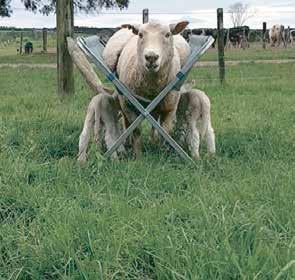
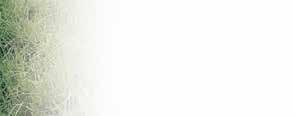
Stainless steel collars around the galvanised pipe will add life to the cowshed.
The power is all neatly packed away, but accessible.
The attractive dairy has made finding relief milkers much simpler.
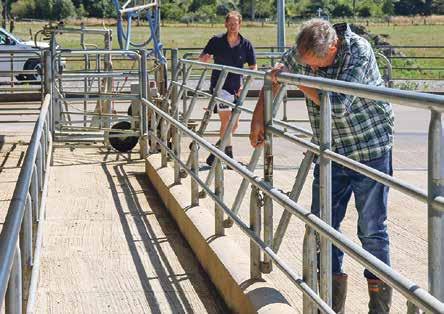
An ingenious and simple drop-down lane design has allowed a two-for-one use with Malmak Ltd’s drafting race doubling as an AI race.
Getting the right results
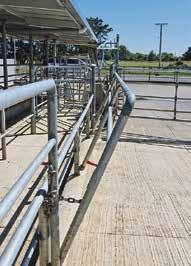
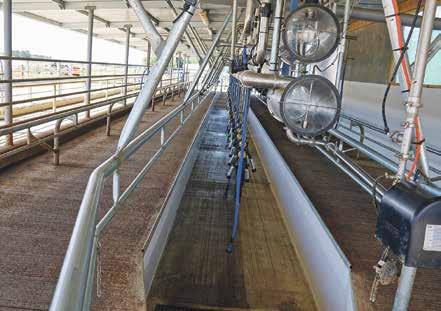
pump to a 15KW pump. We have a new vacuum pump, new washdown pump, a new farm pump, a new filter, and a double-bank cooler to meet regulations. Our milk is going into the vat at 10 degrees Celsius and the chiller is off within an hour of milking.”
The inner workings of a cowshed were in Steve Bromley’s wheelhouse, and the Waikato distributor is thrilled with the result. The herd’s Somatic Cell Count is at 105,000.
“It’s almost a new plant and Dave, Emily, and Jim did a great job of keeping everything organised and moving forward,” says Steve.
Installing Waikato ECR S Automatic Cup Removers have been a popular inclusion for Dave too.
Steve also notes that the backlit touch switches on each cluster give a quick and clear visual on each cow’s milking status from any position in the pit.
Surfatex, which specialises in Acraflex dairy wall coatings, in addition to industrial coatings, anti-slip solutions and protective flooring was also in the mix. Glen and Leianne Sinclair own Surfatex’s lower North Island franchise.
The high-build paintwork usually includes seven coats of paint, which stops manure and chemicals breaching its protective barrier. It is guaranteed for a decade on a new build.
Malmak Farm’s old shed also had Acraflex dairy wall coatings, and Dave didn’t hesitate to choose Acraflex again, because it had stood the test of time.
Lightbulb moment
Their electrician choice was a slightly off the grid for cowshed builds. Alf Downs Contracting used
to do a lot of work on cowsheds but the 70-yearold Marton-based business – with 36 staff – has become well-known for its expertise in industrial, commercial, and domestic factory maintenance, Programmable Logic Controllers computerised systems, lighting and lines. At one point, it was New Zealand’s biggest street lighting contractor.
“We’d had one-off sparkies over the years, and having a bigger firm in the mix was part of our thinking so if we have a call out, we can get someone,” says Dave.
Their on-site electrician was Johan Hayward, who says it was a pleasure to be involved. Alf Downs’ manager Ashley Williamson acknowledged the impact of the group’s teamwork.
“It made a big difference having Dave who was so hands-on,” says Ashley. “Their communication was great. Dave knew exactly what he wanted, where he wanted it, and how he wanted it. Together with Steve’s knowledge as a milking systems specialist, it’s worked out perfectly.”
Steve adds: “It’s always good when someone wants to be involved, and we were thrilled Dave, Emily, and Jim gave us the project, and put their trust in us”.
Sliding doors
Jim reflected quietly that his life could have looked very different at this point.
“Without Dave and Em, I probably would have sold out. I’m very lucky to have them here.
“It’s been an exciting project to share with them. While we had to be careful to not over-capitalise, everyone involved worked hard and we are so pleased we got the right result.”
Dave’s advice to anyone considering a new build? “Within reason, take your time and plan it properly.”
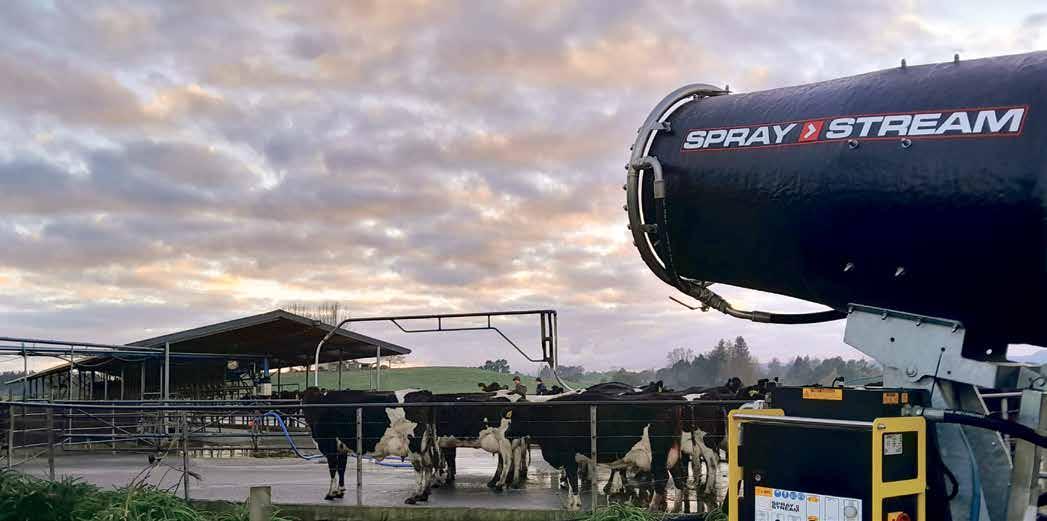
Dave Malone added a window along the inside wall for additional light.
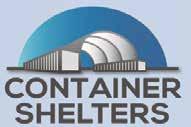
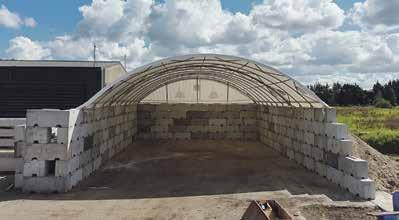
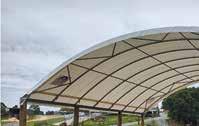
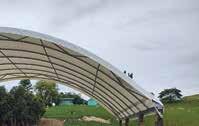
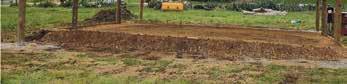

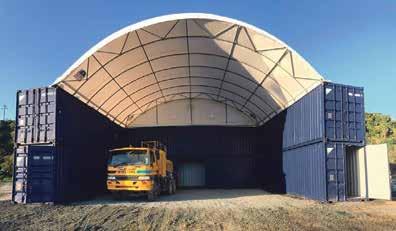
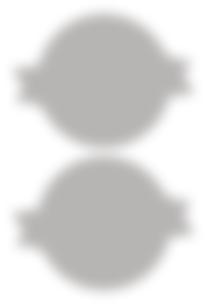
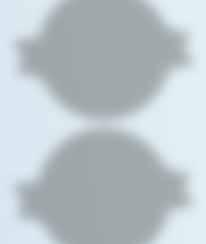
‘Delighted’ with new dairy
One person is comfortably able to milk 300 cows per hour in the new 54-bail rotary on Kernohan Farms’ dairying property at Koputaroa in the Horowhenua district.
It’s a throughput which meets one of the family’s objectives for building a new shed.
Farm owners Peter and Pam Kernohan have lived on the 220 hectare property for 50 years with, in recent years, son Mathew and his wife Megan 50/50 sharemilking 470 cows.
“Milking that number of cows through a 24-aside herringbone was time-consuming,” says Mathew. “The shed was old and wornout so three years ago we started planning a new dairy.
“We wanted a one-person shed although we always have two people on-board, the ideal for the new shed being one person milking while a second got the next mob in.
“Achieving that objective called for a relatively high level of automation which led us to begin looking at rotaries,” says Mathew.
“We started off thinking a 40-bail would be ideal but the more we looked at other sheds and talked to farmers the more we realised that going bigger actually
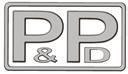
streamlined milking and didn’t compromise one person’s ability to process the cows so we increased the platform size to 54 bails.”
Preparation of the site, which is adjacent to existing buildings, began in 2022, with Peter and Mathew Kernohan doing the majority of the site development. Achieving the optimum height for gravity feed of effluent called for “thousands of metres” of grey face metal – which was transported to the site by Shannon Bulk Haulage. Once in place, the site was consolidated.
Larger footprint
Construction of the new dairy began in January 2023, with the footprint larger than standard for a 54-bail rotary to provide plenty of room around the deck to make it easier to keep the walls clean. The extra room also enabled large service rooms and what must be one of the most spacious underpasses in the industry! Clearlite panels feature in apex walls at each end of the dairy, allowing flooding natural light into the dairy. The grey concrete tilt panel walls are softened by red joinery chosen by Pam Kernohan to “brighten the exterior”.
The interior walls of the dairy are coated with the seven-layer Acraflex paint system applied by Surfatex 2019 Ltd. This provides a hard-wearing, easily cleaned surface. Service rooms are painted with

Dulux paint. By design, the collection yard is rectangular for optimal cow flow and features two linear backing gates; the front one automatically sensing and sweeping cows in at 80 a time with the back gate bringing up the next group.
The yard is cleaned by floodwash and hoses are fed from raised water tanks – one fresh and the other green – to one side and adjacent to the animal handling yards.
The animal handling facility features two head bails, load-out ramp and a Wrangler cattle crush to ensure fast and efficient hoof care.
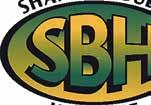
Comfortable cupping
Mathew says they looked at 12 different sheds – all with different height platforms – and “being tall we opted for a 915cm height platform which makes for comfortable cupping”.
The new 54-bail concrete rotary platform and the feed bins were installed by Moa Rotary Platforms. The rotary features a multi-roller twin-track system, the 2.7 wide deck providing optimum protection for milking and electronic equipment, and features a stainless-steel skirt that directs water away from milkers.

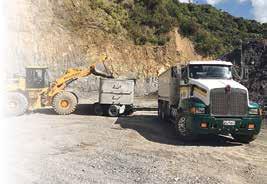
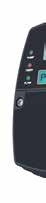

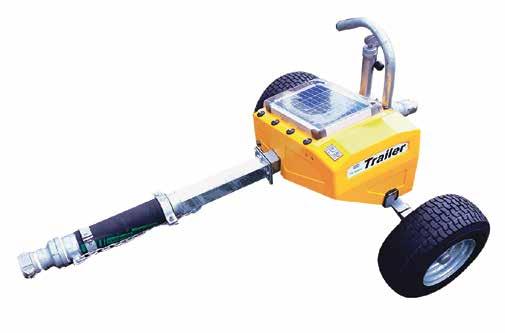
Peter Kernohan, Lynda Sinclair and Chad Hinga, Megan, Pam and Mathew Kernohan, Brian Gattsche of Shannon Bulk Haulage and Glen Sinclair of Surfatex.
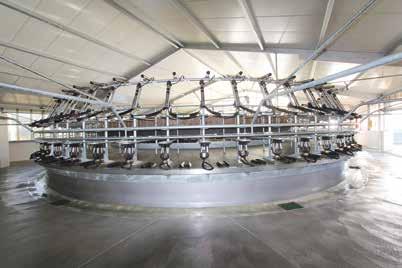

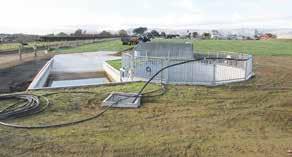
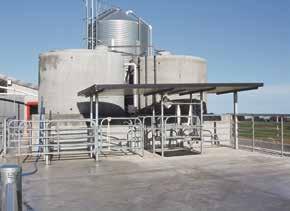
The milking system, automated drafting, shed water and effluent system were supplied by Bromley Dairy & Pumps of Feilding.
Director Steve Bromley says fast and efficient milking is ensured “with Waikato electronic cup removers, bail marshall, automatic teat spray and automated plant and vat wash”.
“The centre gland streamlines the centre of the dairy with no overhead pipework.
Comprehensive cow and herd data is collected and available via the parlour ID system and drafting is programmable either remotely, before or during milking thanks to the draft gate.
“Bromley’s also supplied and installed a custom shed water system with above-
ground stainless plumbing, ensuring ease of maintenance and long life,” says Steve.
“The effluent system consists of a Bromley’s custom effluent pontoon, Doda effluent pump and stirrer.
“The Bromley team is on call to provide round-the-clock service for all aspects of the dairy,” says Steve.
The new dairy was commissioned in March 2024, with Mathew recalling they were still milking twice-a-day at that time.
“The herd transitioned to the new shed after pregnancy testing.
“They were used to being fed in the dairy but we made up an extra-enticing mix for the first few feeds in the new dairy to encourage them onto the platform.
“We had six people on hand to encourage








them on and off the rotary; the first milking took a few hours but over the following three milkings they settled and we were down to 2.5 hour milkings within a week.”
90 per cent
Kernohan Farms Kernohan
Peter has a saying that he applies, good naturedly, to the new dairy when he says it is “90 per cent finished with 90 per cent left to go”.
“We are delighted with the new dairy. It’s better than I expected but the work continues with landscaping, building tracks etc to enhance the exterior,” says Peter.
“Our farm team – Chad Hinga and Lynda Sinclair – have found the new dairy






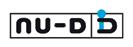

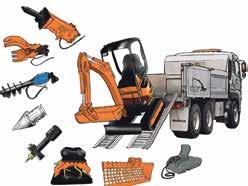

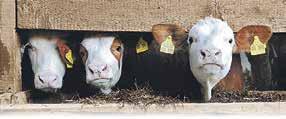

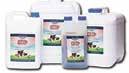
logical and easy to operate, despite the upturn in innovation,” says Mathew. “One person is easily able to milk the herd in around 1.75 hours with a second person bringing the second mob in and helping with clean-up at the end of milking.”
The Kernohan farm has been in the family for more than 100 years. Mathew’s great-grandfather came out from Ireland and bought the original property in 1921 – at that time the farm ran dairy cows, pigs, grew potatoes and harvested flax.
The family agrees that the new dairy has futureproofed the farm for future generations.
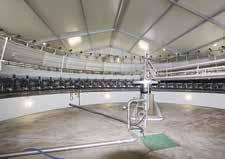




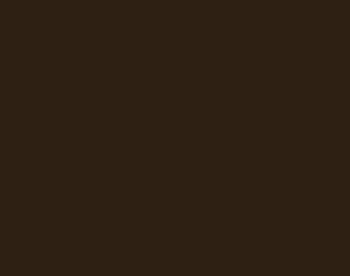
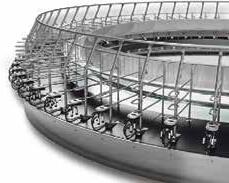

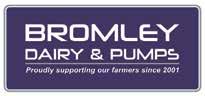
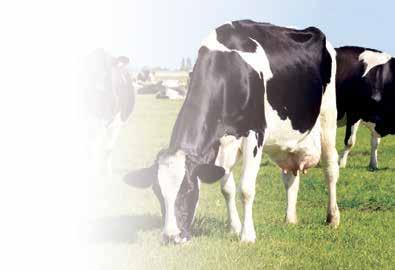
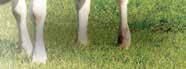














Clare Bayly
The interior is spacious thanks to the large footprint.
The Race Wrangler animal handling facility to one side of collection yard and beside raised washdown tanks.
Bromley’s custom effluent system features a pontoon, Doda effluent pump and stirrer.
Pam, Peter, Megan and Mathew Kernohan are delighted with their new dairy.
RIVERDALE FARM TRUST
Automated drafting makes life simple!
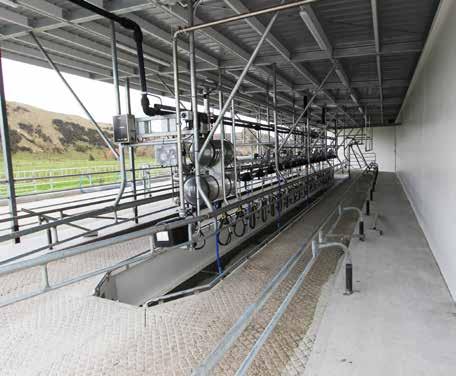
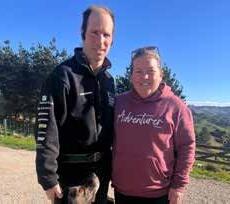
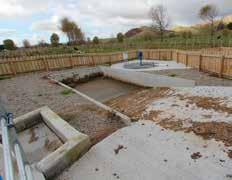
“Effluent made easy”
Archaeology is described as the study of historical human activity through material remains – and the excavation of the site for Riverdale Farm Trust’s new dairy certainly met that definition.
Michelle Brown and husband Duncan picked the site for the new shed “because it allowed our sharemilker to continue milking in the old shed”.
“The site for the new build is further down the road from the existing shed, adjacent to the road for easy tanker access. Choosing this site allowed them to continue milking until the new shed was finished,” says Michelle.
“There was an old implement shed on the new site and we knew there’d been at least one dairy on the site, but the excavation revealed there had been two sheds – making this the third dairy to be built on this site.”
Long and narrow
The Riverdale Farm Trust property is 600 hectares with an 80ha effective dairy platform. “The farm is long and narrow – bordered on one side by medium hills on which we graze drystock, and the river on the other. The dairy unit, which occupies the flat land, milks 200 cows.”
Until 2023 the herd had been milked through an “old, tired” 20-aside herringbone located “down the road” from the new shed.
“It was worn-out so we decided to replace it with virtually a replica of the old one, with the addition of automated drafting,” says Michelle.
“We wanted a basic, easy to operate herringbone with sufficient space so we could, at any point, add technology and in-shed feeding if this is ever warranted,” says Michelle. “Adding automated
drafting at this point in time makes it a oneperson shed.”
Construction of the new 20-aside herringbone dairy began in November 2022 with a goal to have it completed and commissioned before calving 2023. In reality, the new shed was finished and operational on September 29, 2023.
External milk-room
Emphasising the focus on simplicity the milkroom is located outside, freeing up room inside the dairy, under a verandah and behind the vats. The shed is designed for efficiency with easy access from and to the milking area from the service rooms which consist of staff room, bathroom and pump/storage room.
The 20-aside Waikato swing-over milking system was supplied and installed by Dannevirke Dairy Supplies which also installed the washdown, plant wash and water feed for the new dairy.
Dannevirke Dairy Supplies director Sean Borlase says the milking system is powered by a BP200 vacuum and a Sema Variable Speed Drive.
“Every aspect of the dairy is designed to be simple, easy to use and highly efficient. We tailored some aspects – like the positioning of the plate cooler beside the vat and the custom-made hot water cylinder stand. The VSD milk pump is also set up with a milk recovery unit which blows air up the line before each wash to push milk into the vat and prevent production loss which, over a season, can add up to 18,000 litres of milk saved from going down the drain.
“The only automation in the dairy is the drafting unit, which makes it easy for one person to draft cows,” says Sean.
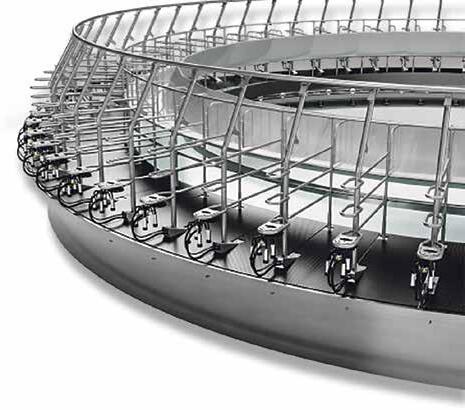

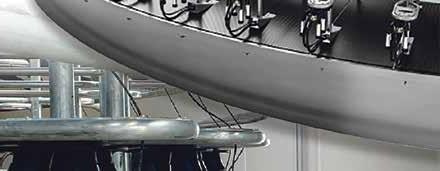

“Effluent made easy”
Farmers Duncan and Michelle Brown.
The bum rail is heavier than standard and all steel trusses and beams are galvanised.
The new effluent system, consisting of a stone trap and bunker, feed to the existing Kliptank.
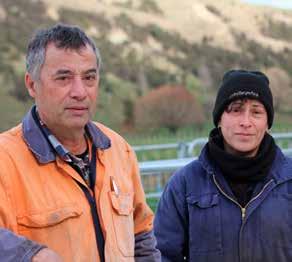
All-in-one precooling
The dairy’s DTS 50 Heavy Ice bank from Dairy Technology Services provides a compact and complete all-in-one precooling and refrigeration solution, which enables significant energy savings. DTS ice banks utilise off-peak power to build up a mass of ice between milking. As milk enters the vat, it is precooled between four-six degrees Celsius. Additionally, the refrigeration system within the ice bank maintains the vat’s cold temperature, ensuring optimal milk storage conditions. This advanced technology creates energy efficiency gains while maintaining high-quality milk production.
A new effluent system, comprising of a sand filter and bunker, feeds effluent to the existing Kliptank.
Wall and floor surfaces feature Acraflex dairy wall coating system, which creates an easy to clean and maintain attractive finish that’s hard wearing and warranted
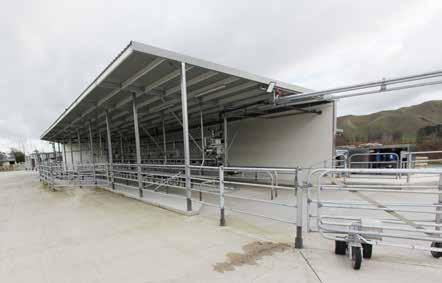
The dairy, from the collection yard showing the auto
for 10 years. Surfatex director Glen Sinclair says floors in the service rooms are also treated, providing an anti-slip surface that’s chemical resistant while the walls are painted with Dulux.
All steel, pipework and 30 gates were designed by Tony Peeti Engineering of Dannevirke and manufactured by engineer Maureen Camden.
“The varying quality of steel saw us beef up the size and strength of the pipework in the dairy,” says Tony Peeti. “The bum rail is heavier than you’d normally see and all the steel trusses and beams are galvanised.”
The animal handling and AB races are adjacent to rows and protected from the weather by a roof.
No pressure
Michelle says construction of the new dairy commenced before Christmas 2022 and the sharemilker, as planned, was able to continue milking in the old shed.
“Beyond the new shed being ready for calving at the start of 2023/2024 we were under no pressure to get the shed finished but there were some challenges and delays during the building process which meant the new dairy wasn’t commissioned until September 29, 2023.”
Michelle says the result is a “true one-person shed”. “We’ve incorporated elements, like automated drafting and an additional rail at the end of each row to deter cows from jumping the breast rail, which enhance one person’s ability to efficiently milk and handle animals.
“All aspects of the shed have been designed to be logical and easy to use, from a milker perspective, and have great cow flow.
“The varying price of steel, while we were building, compromised the ability to budget precisely but we are pleased with the final figure – it is a simple, basic, robust dairy that will be efficient and pleasant to work in.”
Clare Bayly
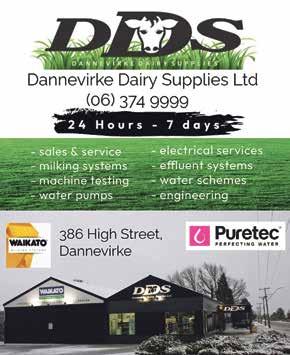
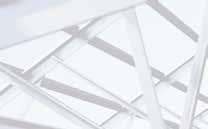
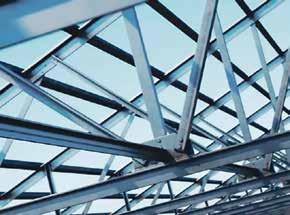

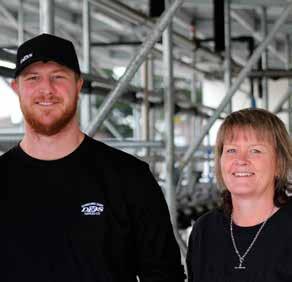
Above: Sean Borlase and Nicola Phillips of Dannevirke Dairy Supplies.
Below: Glen Sinclair of Surfatex.
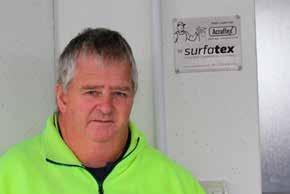
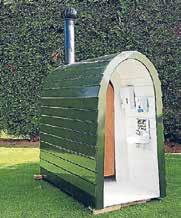
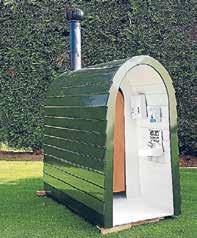
These toilets are the good looking, sensible answer to human organic waste management. Environmentally friendly, they are economical, easy to install and require little maintenance.
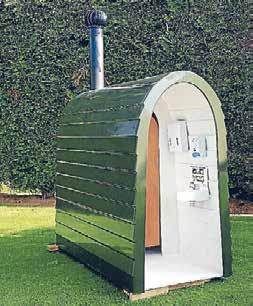
Toilets are vented so there are no unpleasant odours, no need for toilet cleaners or room deodoriser.

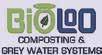
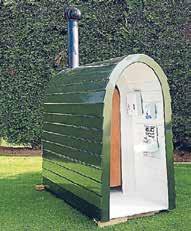
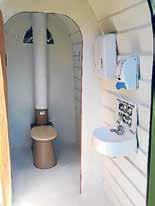
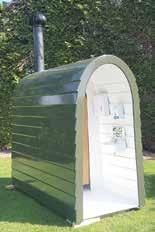
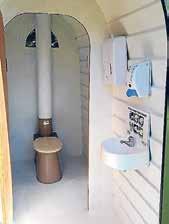
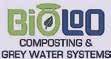
are the good looking, sensible answer to human organic waste management. Environmentally friendly, they are economical, easy to install and require little maintenance.
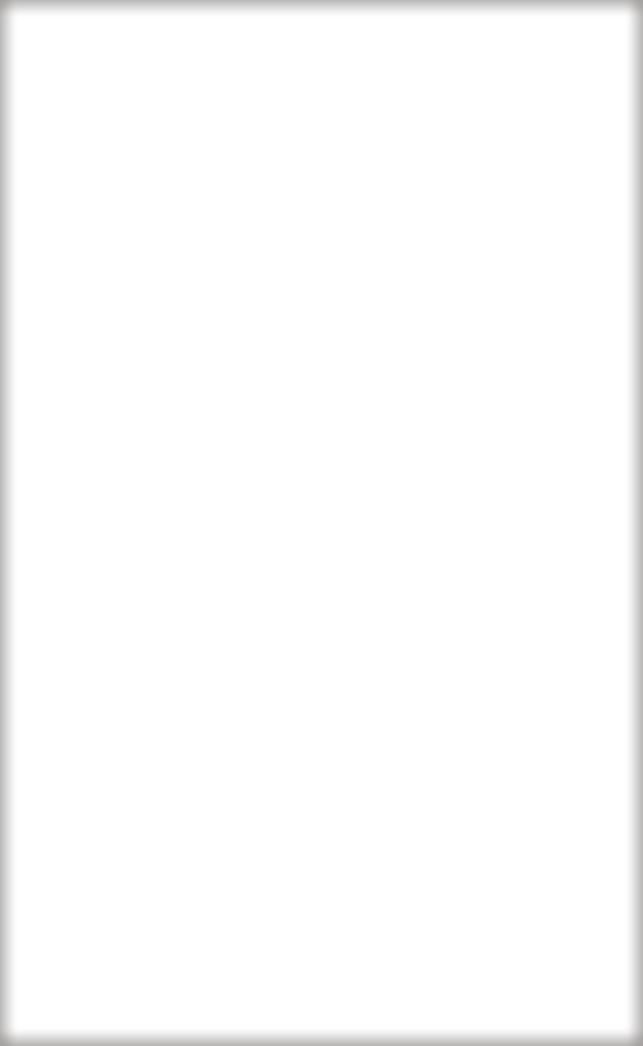
Toilets are vented so there are no unpleasant odours, no need for toilet cleaners or room deodoriser. They meet all required NZ Standards and building codes and are in use by DOC and regional councils. Right from the

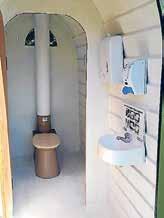
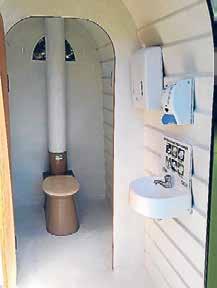
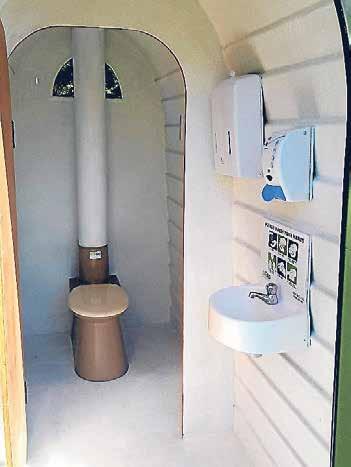
Tony Peeti and engineer Maureen Camden.
drafter at exit.
VALLEY VIEW FARM
A mirror build at Mokoreta
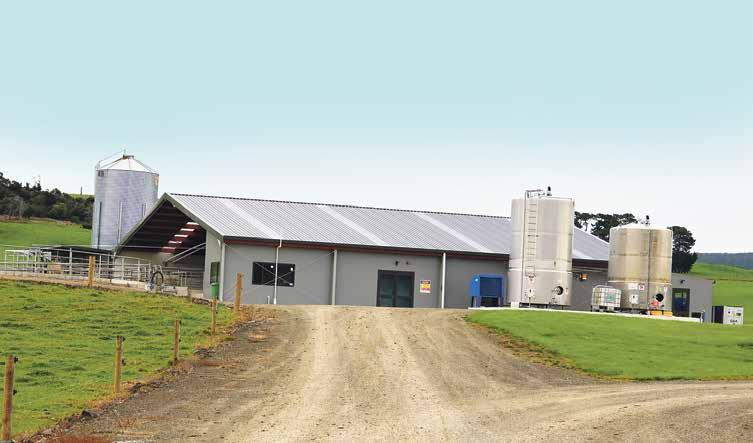
When Stu and Brooke Cameron bought a neighbouring property and decided to build a second cowshed, they didn’t hesitate to mirror their first build.
The Southland couple own Valley View – a property that has swelled to 1050 hectares – at Mokoreta, 55km east of Invercargill.
The property is fully self-contained, also carrying the operation’s replacement heifers, and 100 bulls annually that are reared and/or traded – depending on the prices and the season.
Buying an additional 350ha in 2022 changed the weighting of their business. At that time, Valley View was milking 1600 cows – averaging 480kgMS – through a GEA 64-bail rotary cowshed with a team of seven staff.
Their business has since been split into two contract milking operations milking 1700 cows through two cowsheds for Valley View.
They are milking 1000 cows through the original shed, and 700-head through the new GEA 54-bail DairyRotor T8500 rotary, which was commissioned in August 2023 for contract milkers Harminder and Girija Singh. The cowsheds sit 1.5km
apart, on a milking platform of 560 effective ha and a runoff area of 370ha.
Each herd has a stock underpass for the cows to cross under the road.
The blueprint
The original 64-bail rotary – built in 2014 – formed the blueprint for the second. The new 22m x 20m cowshed includes rooms for the office, milk room, pumps, storage, and electrical systems. A raised vet area with a fold-down working platform makes mating easier. It has been built with box section rafters using stained timber purlins, which not only look classy but also stops birds from

perching/nesting and help make the cowshed quieter to work in.
A T-underpass allows their milking staff to cut across from cups-on to cups-off without circumnavigating the platform – also giving them access to the centre without having to vault the platform.
Stu says it was a no-brainer to double-down on a GEA plant. He wanted to make it easy for the operators, and for the cows to potentially switch between the two cowsheds.
“We liked the way our other one functioned, and we appreciate that cowsheds need to be well set-up to attract and retain good staff,” says Stu.
“We also wanted to increase our cash flow, and with the extra cows we’re running now, we’d like to think it will get that done.”
Quiet platform
They chose GEA’s concrete platform with twinbeam nylon rollers – making it quieter-running with auto greasers. He also liked the GEA IC330 cluster, which includes a sight glass that visually alerts the operator if there is a split liner.
The plant was fitted with iCR+ automatic cup removers (ACR), which were important for Stu because they negate the risk of over-milking. They also allow the rotary to be operated by one person,
FA RM M APPING
Our team of GIS technicians produce accurate farm
maps tailored to your unique farm features.
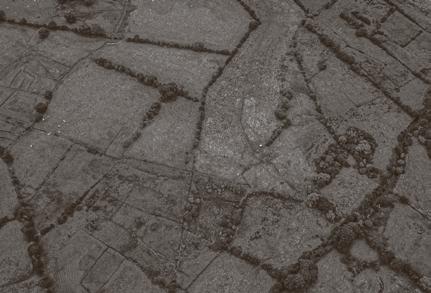
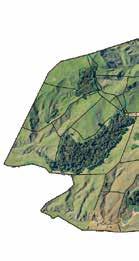
PRINTED PRODUCTS
GPSit offer a wide range of printed products so you can access your map anytime and anywhere.
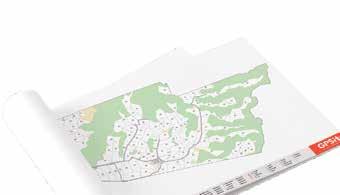
EXPERIENCE
At GPSit we know farms. Many of our team come from farming backgrounds so we understand a farm map is the foundation of your entire operation.
HEALTH & SAFETY
Our maps are an effective and easy way to communicate farm layout and hazards to staff and visitors to ensure you comply with all health and safety regulations.
RETURN ON INVESTMENT
A GPSit farm map is an investment that provides immediate and long-lasting returns. It will improve your farm’s productivity and support the decisions you make.
ENVIRONMENTAL PLANNING
An accurate map is critical for any Freshwater Farm Plan (FWFP) to identify waterways, fencing, riparian planting, and slopes.
ACCURACY
Our in-depth knowledge about orchards and surveying allow us to generate precise maps to help you make important decisions about your orchard with confidence.
DAIRY FARM MANAGEMENT
Maps are a powerful tool to assist with day-to-day farm management. This includes planning, budgeting, tracking fertiliser applications, and allocating stock rates/movement.
One of the quiet achievers in this cowshed is the concrete platform with twin-beam nylon rollers – making it quieter-running with auto greasers. GEA’s Andrew Smith checks the clusters.
Stu and Brooke Cameron’s new 54-bail DairyRotor T8500 rotary, which was commissioned in August 2023 for contract milkers Harminder and Girija Singh.
VALLEY VIEW FARM
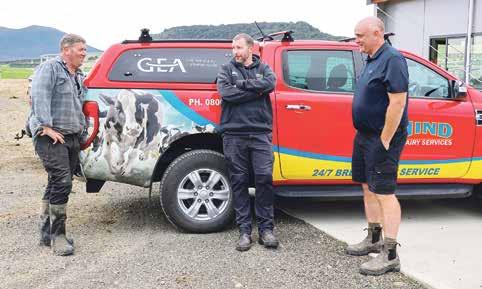
if needed. They opted for a cluster dropdown so the clusters could pass under the bridge at the exit and rise again at cups-on – freeing the exit and entry of all hoses and clusters.
A secondary point of difference on the clusters is that the pulsation operates front to back – rather than left to right – so the milk-out can be adjusted to finish together, acknowledging there is 20 per cent more milk carried in the rear than the fore quarters.
“It’s another feature that can help avoid overmilking,” says Nind Dairy’s Logan Barnett.
The automated cluster lift-to-start function protects staff from milking fatigue.
A lock-out remote is an exclusive function. “It means if the cow is still milking when she gets to the bridge the cluster automatically stays on, and the retention bar doesn’t release her until she is past the operator,” says Logan.
“I don’t think we talk about that feature
enough. Once people experience it, they love it.”
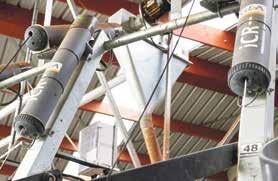
local business that Stu was already working with. They carved out the new 6000m3 effluent pond, and the stock underpass.
Valley View Farm Valley View Farm
Other automated functions include the iSPRAY4 on-platform teat sprayers, and the FIL
Intelliblend automatic teat spray mixing –negating waste and adding consistency.
The installation of a LD240 aquaCHILL adds Glycol cooling within the double bank plate cooler, so milk enters the vat at six degrees Celsius.
Builder and excavators
Stu’s builder, Baz Janssen, is a popular Southland business. Stu says Baz was an easy decision.
“I knew Baz and I had already dealt with him. He’s honest and reliable, and he worked in with us. He knew what we wanted, and if he needed to check anything, he just went and measured the other shed.”
Central Southland Excavating is another
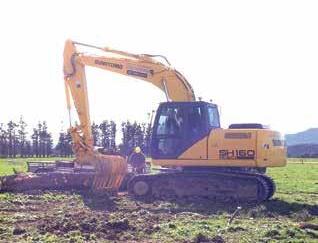
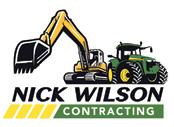

“The effluent pond is a simple and robust system,” says Stu. “It also helped turn a gully into a paddock because that’s where we put the excavated dirt.”
Invercargill’s Hecton Products supplied a full feed system, feed trays with robbing bars to stop cows steeling feed, a 12-foot five-ring fully galvanised silo, and a mineral dispenser.
Nick Wilson Contracting takes care of the farm’s baleage and cultivation.
“He’s a helluva good bloke to work for,” says Nick.
Changing roles
Stu says while it’s nice to be out of the daily grind of the cowshed, he remains busy in the day-to-day operations.
“Well, it doesn’t seem to be a whole lot different to before, but I do spend a little longer in bed in the mornings and I see a bit more of the kids.
“It’s nice that our contract milkers now employ their own staff. We’ve been lucky in
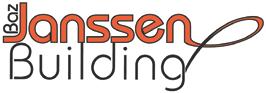
Invercargill’s Hecton Products supplied a full feed system, feed trays with robbing bars, a 12-foot fully galvanised silo, and a mineral dispenser.
that we’ve always had really good staff, but it’s another thing I don’t have to worry about anymore.”
Stu says it’s too early to quantify production gains because they have more cows, the herds don’t walk as far, and Southland’s season has been kind.
Panic slowly
When it comes to advice for anyone considering building a cowshed, this veteran of five conversions – three on their own tab – says it’s a standing joke with their bank that every time they build a new cowshed the payout crashes.
“Whilst building the first cowshed on the property, the payout went from $8.40 to $4.20 [2015] followed by $3.90 the following season, and then in 2023 our season opened at $6.75 [from a season close that was close to $9]. “It ‘pays to panic slowly’,” he smiles.
“You don’t build cowsheds to get rich overnight.”



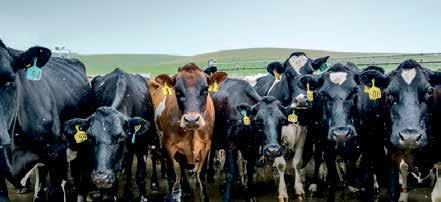

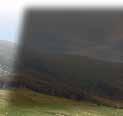
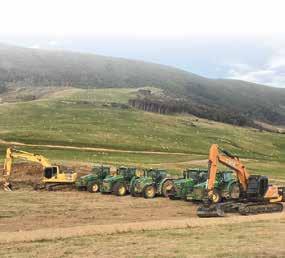
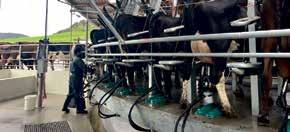
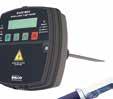

This cowshed includes box section rafters using stained timber purlins.
Stu Cameron trusted Nind Dairy’s Logan Barnett, who is supported by GEA’s Andrew Smith.
Dianna Malcolm
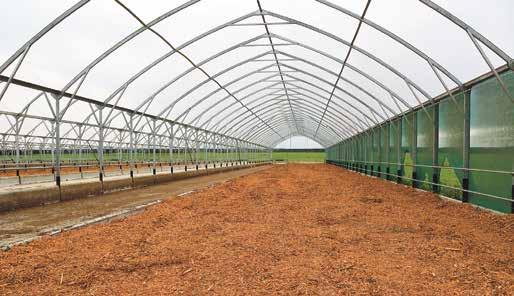
‘It’s
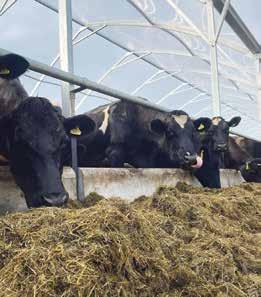
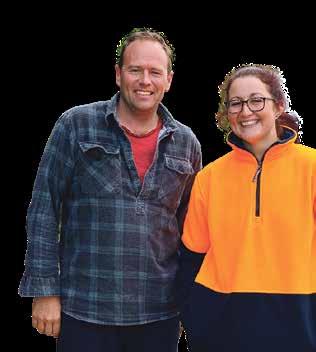
changed the way we farm’
Sometimes when things get overwhelming, the only way out is to make a big call.
So it was for Southland dairyman Joel Burns in the spring of 2021. With atrocious weather and 900 cows calving in the cold and the mud outside, his drive to make calving and the transition easier for his cows and his staff reached a breaking point.
Clover Bell Limited milk four herds on 315ha, with 292ha effective, through a 50-bail rotary cowshed at Waihopai Downs, about 20 minutes from Invercargill.
“It was so cold, and we never got any drying during the days,” says Joel. “No matter where we sent the cows, they muddied their pasture within the hour.
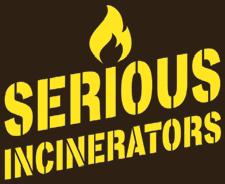
"I’d put them in a fresh paddock overnight only to find what looked more like a crop paddock the next morning.
“For somebody who has a passion for animals and the land…that sight hits you on every level.
“When you’re taking care of a lot of stock, it only takes one or two things to go wrong before it snowballs. Even the team on the farm saw me break down at one point.”
Protection imperative
The cost of surviving spring challenged their budget, and their status quo. “We lifted our in-shed feeding so the cows got to the paddock as full as we could get them. We sped up the grazing rotations – which came with other consequences – and we
spent a lot of money. We were forced to reflect on why we were farming and the cost of controlling spring.
“Also in that mix were Covid lockdowns, price increases for wintering off, and increased fertiliser costs.”
Joel and Linnet called a round table summit with their landowners, and now equity partners, Andrew and Linda Gunn –along with Joel and Linnet’s advisor – Tony Robertson. They wanted to winter and calve their cows on-farm.
Between November 2021 and July 2023, the partnership added a 93.6m x 99m (9266m2) Redpath Shelter that collectively holds a minimum of 750 cows. The clear film roof cladding allows 91 per cent sunlight through – drying the bedding and
warming the cows without the windchill. And windbreak shade cloths add ventilated protection.
“Redpath offered us the most options in terms of a large cow farm,” says Joel.
“We’ve kept away from the technology, so we’re still very much a manual operation – scraping lanes ourselves – because that is also a part of farming. I don’t want to be on my phone all day just to see what my cows are doing.”
Production up
From 2020-2021 their production has trended upwards from 373,000kgMS to 470,000 kgMS for the 2023-2024 season – that’s 97,000kgMS higher, and 522kgMS per cow. They are gunning for
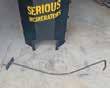
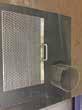

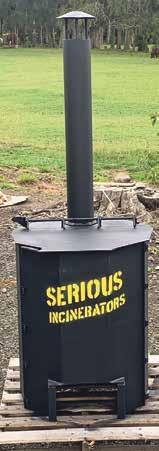
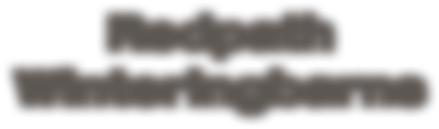
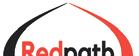
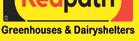
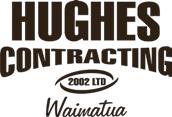

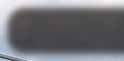
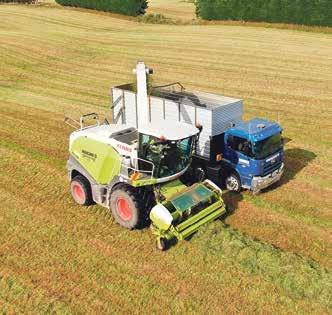
Bark chips form the bedding for the structure.
Clover Bell’s Joel Burns and his 2IC Vicky Short, who has been with the operation for eight years.
500,000kgMS this season. Joel says the shelters have changed their world.
“Our last calving was amazing. You could sleep knowing there was no mess being made overnight, and no matter what storm or weather event came through it wasn’t going to stop the cows from going into survival mode and not calving.
“Checking them was a breeze because they were all in one undercover location 1km from our house. We’re around them a lot, so we naturally pick things up earlier.”
To that end, they had 75 per cent less milk fever incidents last spring and their empty rates after 11 weeks of mating was nine per cent, which has always been historically strong and is achieved with tail paint and manual observation by Joel and his trusted 2IC Vicky Short.
“We’ve always had low empty rates, but that is the second-best result since we’ve been here, and you’d have to think the barn has had an influence.”
Peace of mind
Joel says the value of wintering in the shelters over grazing off-farm is cumulative. The cows were grouped on body condition score and fed 50 per cent dry matter silage during their dry period.
“If they were grazed outside off-farm, we’d still have to travel to check them. That takes time. Then, there are the things that are harder to quantify – like the stress and expense we used to have trucking in-calf cows to graziers.
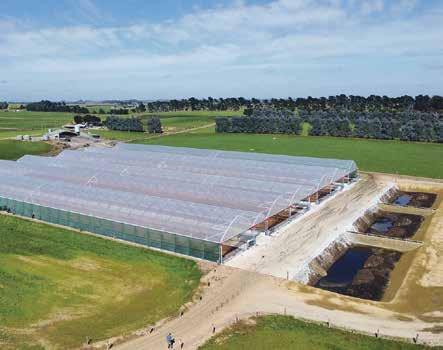
The team
Redpath Pacific Ltd’s owner Glen Williams says Joel and his partners were easy to work with.
Clover Bell Ltd Clover Bell
“Their pre-planning and vision through the entire job made the process of supply and installation seamless,” says Glen.
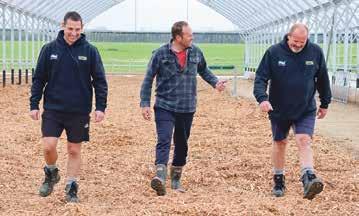
tipping systems so they automatically flipped over, releasing roughly 200 curbs without impacting the concrete.
“We had an advantage in that we could strip them really early, because we were not really putting any pressure on the concrete that way,” says Baz.
“That was a huge time-saver,” says Joel.
“At home you control the feed, and there is less feed wastage undercover. It takes 45 minutes to feed everything. Yes, it’s changed the way we farm, but I don’t believe it’s made more work for us.
“As long as there are two or three senior staff on-farm, we can feed, scrape pens, and simultaneously check the cows.”
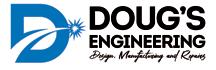


Joel says within that conversation he was grateful to Dairy Green Ltd at Invercargill, which provided the drawings and plans for the environmental planning and compliance.
Local builder Baz Janssen completed all the concreting and pre-cast feed curbs. Baz came up with an ingenuous way to turn the curbs out quicker. He designed two seven-metre moulds with weighted
Doug’s Engineering completed the engineering, pipework, rails, and gates. This allowed Joel to divide the area into six large pens, or 12 smaller ones.
Nind Electrical’s Barry Tomlins and Scott Glover – responsible for the electrical work and pumps – say the roof cladding made their job easier. “To have that natural light still on the cow’s back during winter when it’s cold out, but still sunny is a huge benefit for lighting,” says Scott.
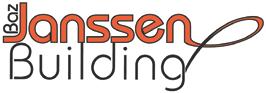



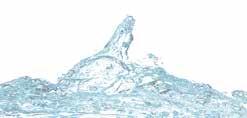


Hughes Contracting supplies Clover Bell with 700 tonnes of baleage and silage every season, in addition to the farm’s groundwork. “This year we did buy in more silage than usual because we hadn’t done a full transition in the shed, so it’s good to have that relationship,” says Joel. They have had a trusted Wrangler animal handling system for many years, and Joel says it owes them nothing.
Futureproofing
For their four full-time staff members – including Vicky who has been with them eight years – the shift to the barns has been exciting. “Whether we like it or not, change is coming,” says Joel. “We have to find a way for this generation to want to farm.”
Dianna Malcolm
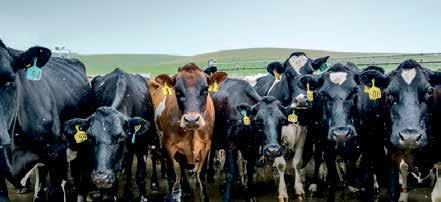
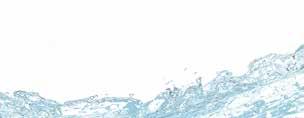





Above: Nind Electrical’s Barry Tomlins, farmer Joel Burns and Nind’s Scott Glover enjoy a quick walk through the shelter.
Left: The aerial view gives perspective to the area dedicated to wintering Clover Bell’s 900 cows. Photo: supplied.
FAIRLEIGH DAIRY FARM
Unafraid to do things differently
Change and independent thinking has been the constant for the Eade family at Fairleigh Ayrshires and Holsteins during three decades.
This family operation at Greenvale – 30 minutes from Gore – is run by Bruce and Tanya Eade, with Bruce’s parents Ken and Nancy.
Ken and Nancy converted the rolling property 30 years ago, and the family’s progress has culminated with installation of four DeLaval robots for their high production cows, which operates alongside a 40-aside herringbone with no automation for the balance of the herd.
They milk 560-head. The robots will milk 280-head by September 2024. The balance will continue to be farmed outside, after calving in the barn, and milked through the herringbone. The farm carries a winter contract of 27,000kgMS.
A thunderclap
It’s a combination that – on the surface – appears to muddy the advantages of automation. But Bruce and his parents are clear about their motivation.
This family converted the 405ha property and starting milking with a two-cow plant in a hayshed until their herringbone was completed.
They later built a barn of sorts to weather Southland’s brutal winters.
Their first big step towards fully housing cows came in 2012 when they built a 150m x 38m barn.
Bruce says the decision to fully house cows came like a thunderclap.
“We’d had four or five wet springs in a row, and I
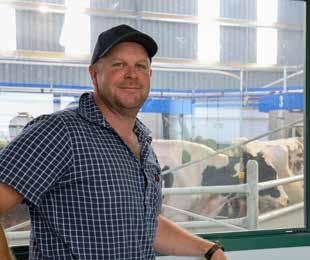
Bruce Eade says combining four robots and their herringbone cowshed works for their operation.
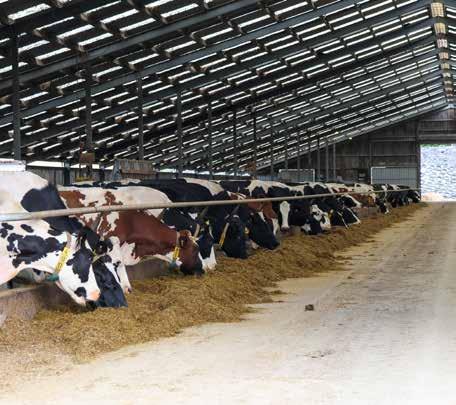
first significant step
remember feeding out on a particular paddock on September 25, and a snowstorm came in. I had to sit there for 15 minutes because I couldn’t find my way back to the gate. I was like: ‘There’s got to be a better way’.
“The cows do so much better in the barn. We have a calving pen at one end. Everything calves inside. You’re not getting calf deaths and you’re not getting down cows. We also grow more grass because the cows aren’t wasting feed or ruining pasture. You’d never go back.
“If the spring is wet, we can keep the entire herd indoors at night.”
Playing into their decisions is that they milk registered Ayrshires and Holsteins.
LETS

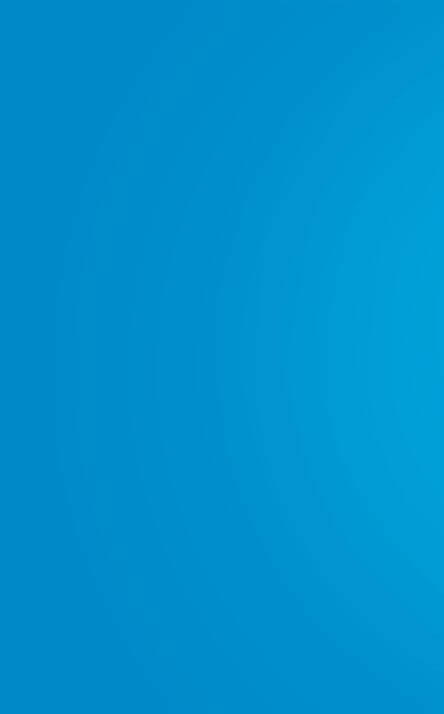
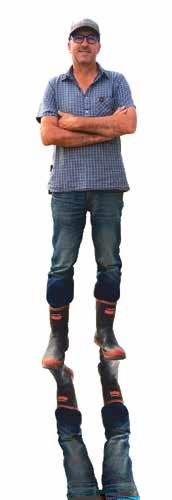
UK inspiration
Bruce’s confidence in installing robots came after listening to a UK farming blog on Evening Holsteins at Carlisle. The Cumbrian operation had combined six robots with a manual cowshed. As Bruce listened, his mind started ticking.
“They had pedigree cows, they loved showing, they had trouble with unreliable staff, and they did all their own cultivation and silage.
“It was basically us in England. Within three or four days, Tanya and I were driving to Invercargill and we started talking about it with Mum and Dad.”
Three weeks after Bruce sent a first text
to Mark McMillan – DeLaval’s Southland distributor, who co-owns Southland Farm Services – the deal was done.
The Eade family already had an established relationship with SFS, and were the first in Australasia to install DeLaval’s feed pusher in their barn.
Between December 2022 and May 2023, a 20m apron shed and office was fused to the existing barn for the robots –built by Comfort Cow Barns.
An early advantage Fairleigh Farms had was Grant Stalker – who used to co-own Lucernvale Holsteins in Canterbury – had shifted to Gore. He came on-board in a herdsman role – focussing on the robots.

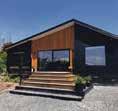

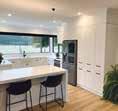
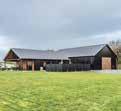
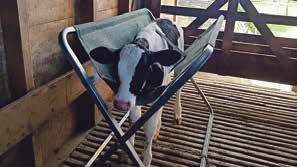
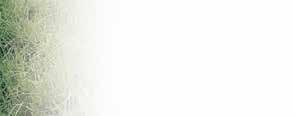
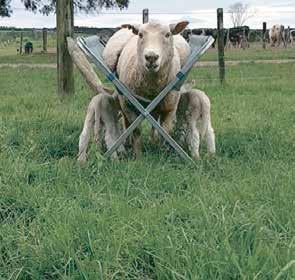
The
towards fully housing cows came in 2012 when the Eade family built this 150m x 38m barn.
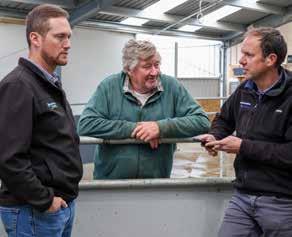
Southland Farm Services is co-owned by Mark McMillan and Donald Vermeulen. It includes 70 staff and three divisions – the milking machine side of the business –Southland Electrical & Refrigeration Ltd, and a plumbing and effluent team. Mark clearly remembers Ken’s emotional response to his family’s decision to move forward with the robots.
“We thought the Eade family were good candidates, and I knew if they were asking the question, that they were serious.” They chose four new DeLaval VMS V300s. “We now have two farms in Southland with robots because we’ve been easing into it,” says Mark. “It was a massive thing for them, because they were the family that originally converted this farm, and for them to make the call to go this far into technology is significant and a credit to them.”
Bruce says the tipping point with DeLaval was about so much more than the 3D
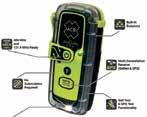
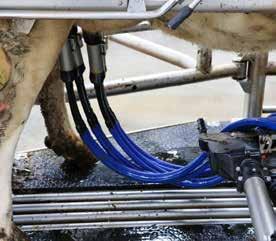
camera, for more accurate and faster cup attachment, and having four dedicated International Committee for Animal Recordingapproved milk meters where the vacuum, pulsation and takeoff are adjusted automatically for each teat. It was about accumulating the speed that delivers a 50 per cent faster attachment time with a 99.8 per cent attachment success.
Biggest impact
Fairleigh Dairy Farm Farm
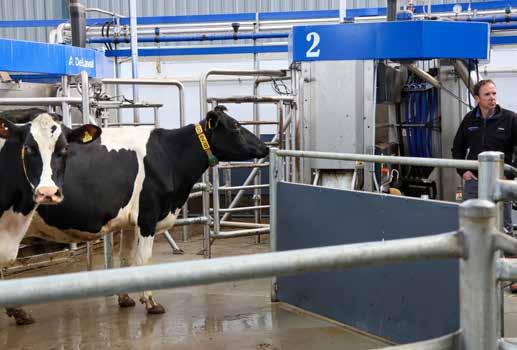
delivered to them undercover, and that was a big shift, which allowed us to finish the season strongly.”
The robot cows are averaging 2.7 voluntary milkings a day – some milk seven times in two days. The top grain ration is 4.5kg per cow per day, with a base rate of 3kg.
Part of the sum
The biggest impact on production today includes the cumulative improvement in genetics, management, technology, and extending their Days In Milk because of the barn and robots.
“By having some [cows] inside all the time, and the rest of the herd inside at nights it’s cut down their walking and damage to tracks. Plus, they were getting good feed
As much as they love what the robots have brought to their operation, Bruce doesn’t see them milking their whole herd this way.
“If we did that we’d have to go back to outdoor wintering or build another barn, and that’s not an option for us.”
They are supported by strong Southland suppliers. SGT Dan Stockfoods has been delivering supplementary feed to Fairleigh Farm for 12 years. Bruce says it’s been a great relationship, and they’ve never let them down.
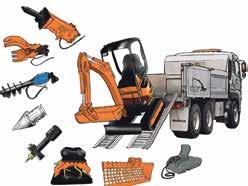
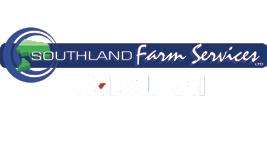
Hecton Products installed Fairleigh’s robotic meal feed system fuelled by a 16-tonne silo. They also installed the farm’s augers and supplied its electrical control box.
The Wrangler cattle crush for hoof care has been there 18 years. “It ticks all the boxes for us,” says Bruce.
Calving intervals
The next step is to see exactly what the cows are capable of. “The more you feed, the more they milk,” says Bruce. “In the past we had to get them in-calf, calve them, get them peaking, then get them back in-calf within a very small window.
“The robots and the barn will help us get the maximum efficiency out of those cows. Because now we can give them everything they need, and they can go for it.”
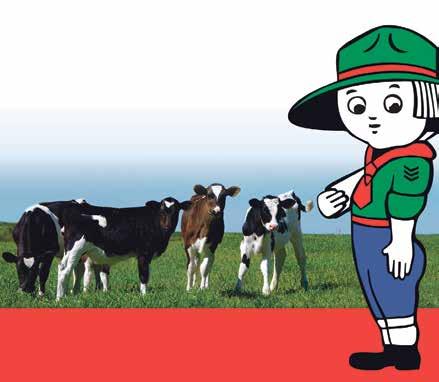
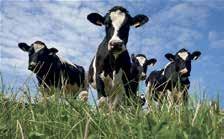
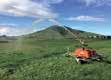
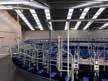
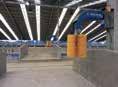
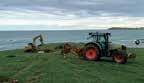
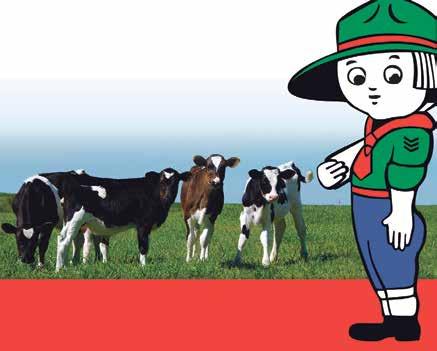
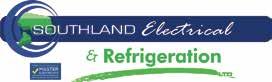
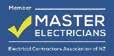

Each robot includes four dedicated ICAR-approved milk metres.
Southland Electrical & Refrigeration Ltd’s Gerhard Lategan, Ken Eade, and Southland Farm Services co-owner Mark McMillan.
The cows assess their next move with DeLaval’s Southland distributor from Southland Farm Services, Mark McMillan, at Fairleigh for a visit.
Dianna Malcolm
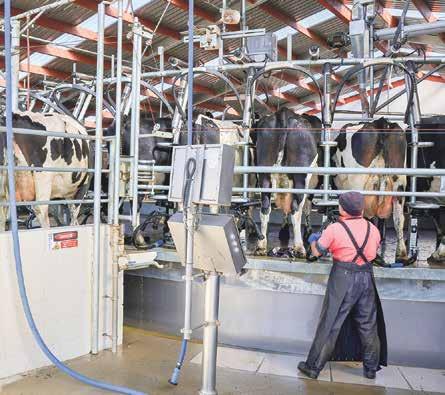
I wanted a farm…
Few dairies in New Zealand have three metres of underfloor heating at the cups on.
Southland farmers Todd and Fleur Anderson have. The Winton couple milk 850 cows on 300 effective hectares, plus 30ha for wintering the milking herd or calving, at Kauana. Their new 64-bail rotary is housed in a shed sized for a 70-bail rotary, and they have several other points of difference for their 21 per cent contract milkers Eric and Judith Retana, who have a safety net with a set floor.
Kauana Dairy Ltd Dairy

This cowshed is an important juncture within Todd’s self-made career through banking and real estate. Todd always wanted to farm, but he didn’t have a family farm. He progressed to ownership after a decade in banking and 16 years selling real estate for PGG Wrightsons. His professional resume seems at odds with his passion – and subsequent ownership – of registered dairy cattle, sheep, dogs, and deer. He says it’s all played into their journey.
“Bankers are usually quite conservative,” acknowledges Todd. “Someone said to me that it’s tough when you’ve been in the bank because you’re always looking at why you shouldn’t be doing something. But because I haven’t had a family farm, I’ve always looked at how we could do it.
One or two?
“I haven’t travelled the world like some of my friends. I haven’t got a sports car in the garage, or an extreme personal lifestyle. I’ve never done things for the money. I’ve done it because I was passionate about farming, and I wanted a farm.”
Fleur was in human resources for Sky City and
TVNZ in Auckland before they met, when she joined the bank. Their decision for Fleur to take charge of their biggest asset in the early days – their children – meant her career shifted to also helping manage their divergent businesses.
They toyed with building two cowsheds so they could potentially split the farm for marketability down the track. But, in the end one cowshed takes prime position on this stunning holding.
Eric and Judith say they had joined knowing the new cowshed would be built. They spent one headspinning season in the old twin herringbone that could milk 50 cows at a time.
“You need more labour, and when you’re looking for a cow, you have to go up one side and down the other and there is no space between the runs,” says Judith. “Especially at herd testing and mating.”
Now, they are milking in the Rolls Royce of cowsheds, Judith couldn’t be happier.
“I love dairying and I love cows,” she smiles. Eric adds: “We love animals”.
Todd finishes their thinking. “This is a long-term relationship.”
Generous design
Todd and Fleur were happy to invest in detail –like underfloor heating at the cups-on – to make sure their team enjoys working in this cowshed.
“We did that solely for our staff, because in a herringbone you’re moving all the time. In a rotary on a cold Southland morning at cups-on, it super cold when you’re stationary,” says Todd.
To establish the cowshed’s base Neville Stirling Excavating was called in. Neville expected to bring in about 2000 tonnes of gravel. In the end, he delivered 10,000 tonnes and it took him six months – and 20,000km – to get the cowshed’s
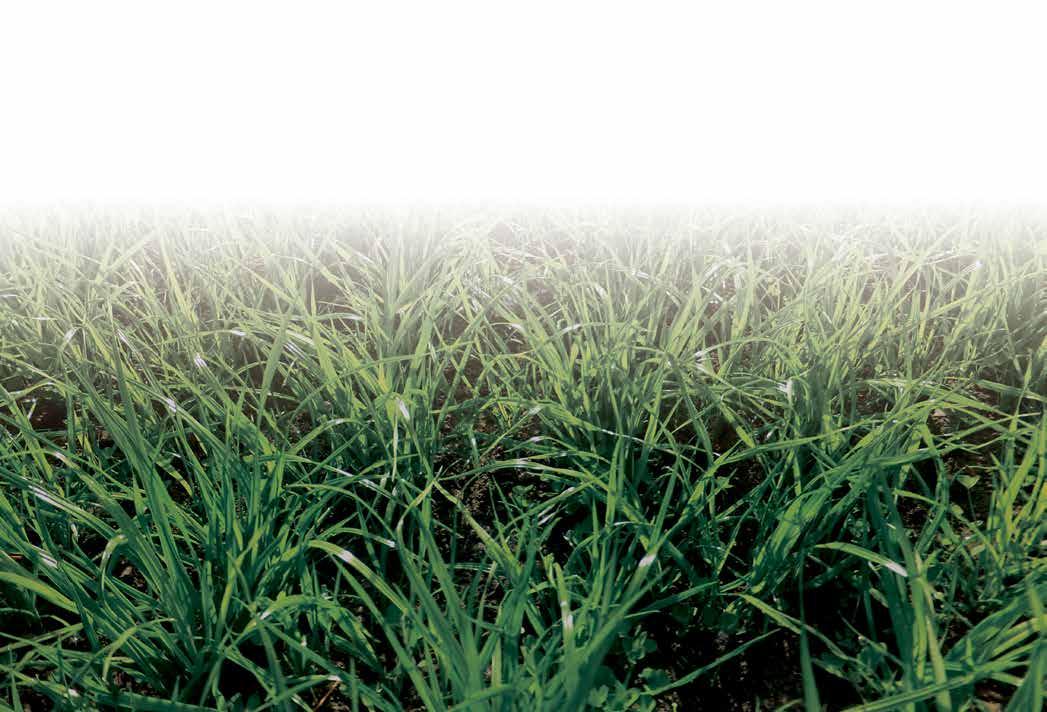
Three metres of underfloor heating gives the cups-on operator a measure of comfort through the cold Southland spring.
Owner Todd Anderson enjoys breeding registered dairy cows, sheep, dogs, and deer within this commercially-run operation that has to pay the bills.

base to the required two metres above ground level across a 16m radius plus supporting yard area. The mission was to get enough clearance so the water could have the gradient to travel to the effluent ponds.
“I think it’s pretty impressive now that it’s all finished,” says Neville.
Todd is motivated by efficiency, and to that end they invested in automatic cup removers, in-bail automatic teat spray, liftto-start clusters, in-bail identification and feeding, a double-plate cooler supported by a chilled water calf vat, auto plant wash, and several strategically placed floodwashes in the dairy yard. Milking and clean up takes three hours morning and night and Eric and Judith employ three staff.
The Andersons asked their builder, Baz Janssen, to stretch the measurements further than the 70-bail roofline, so all the service rooms for the cowshed fit under the roof in one neat square.
“I personally quite like it,” says Baz. “It means you can fit all those rooms in the
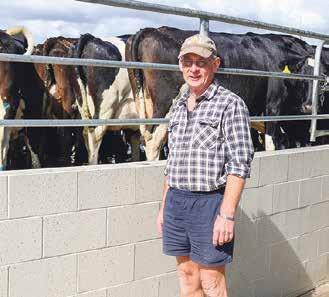
end of the shed – rather than having a side room – and you can configure them a little differently. It also gives the building really clean visual lines.”
They have three vats. Two are 16,000 litres, and the third is 18,000 litres. The 18,000L vat has a two-way underground piped system so milk can easily be transported to the calves, and the line can be cleaned with re-circulated water. After calf rearing, it is used to chill the cooler water.
Two exits and entries
The Andersons have invested in two entries and two exits to the cowshed, so different herds can be coming in and going out at the same time without interference or delays. They have also invested in ‘water pulses’ down the exit lanes.
“The exit race goes quite a wee way so it’s good to have that water pulse alkathene upright hose and be able to push a button which triggers the wash-down pump when
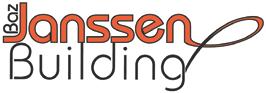



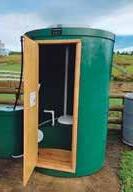
the cows are backed up to encourage them to leave,” says Todd.
They’ve also installed overhead sprinklers for the cows. “On a hot day it might get to 30 degrees Celsius here, but that 30 degrees is hotter than it feels at the same temperature in Canterbury.”
Hecton Products installed their mineral dispenser, and shifted and extended the Anderson’s existing silo from their old to their new shed, plus fitted robbing bars and feed trays.
Todd says their Wrangler hoof trimming crush is a “pretty amazing device” for making regular hoof trimming straightforward and safe for their staff.
Content
Todd and Fleur say they made the right call for a 64-bail shed. “Some people were telling us to go for a 54, some a 60, a mate had done a couple of 64s, and some people put 80-bails in.
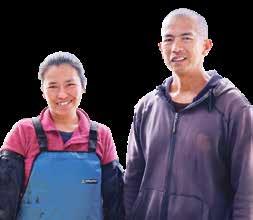
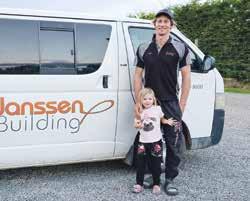
“But the reality is that if you work it out at those bigger sizes, you then need two people cupping up because the platform is going so quick.
“For us, we couldn’t be happier with the 64 with a 70-bail roofline. To also have that extra room between the platform and the shed wall allows more working room and keeps the dairy cleaner. You only do this once.”
Dianna Malcolm
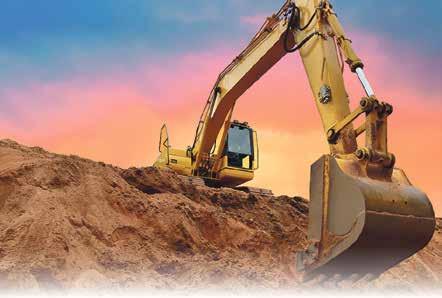

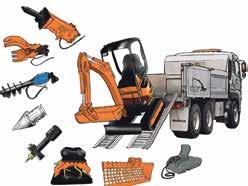

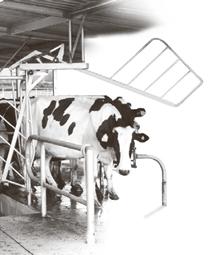
A drone gives this greenfield site perspective. Photo: Neville Stirling.
Neville Stirling brought in 10,000 tonnes of gravel to achieve the elevation needed for the build.
Builder Baz Janssen, and daughter Chloe, enjoyed delivering the finer details that Todd and Fleur Anderson built into their new cowshed.
Contract milkers Judith and Eric Retana love the new cowshed.
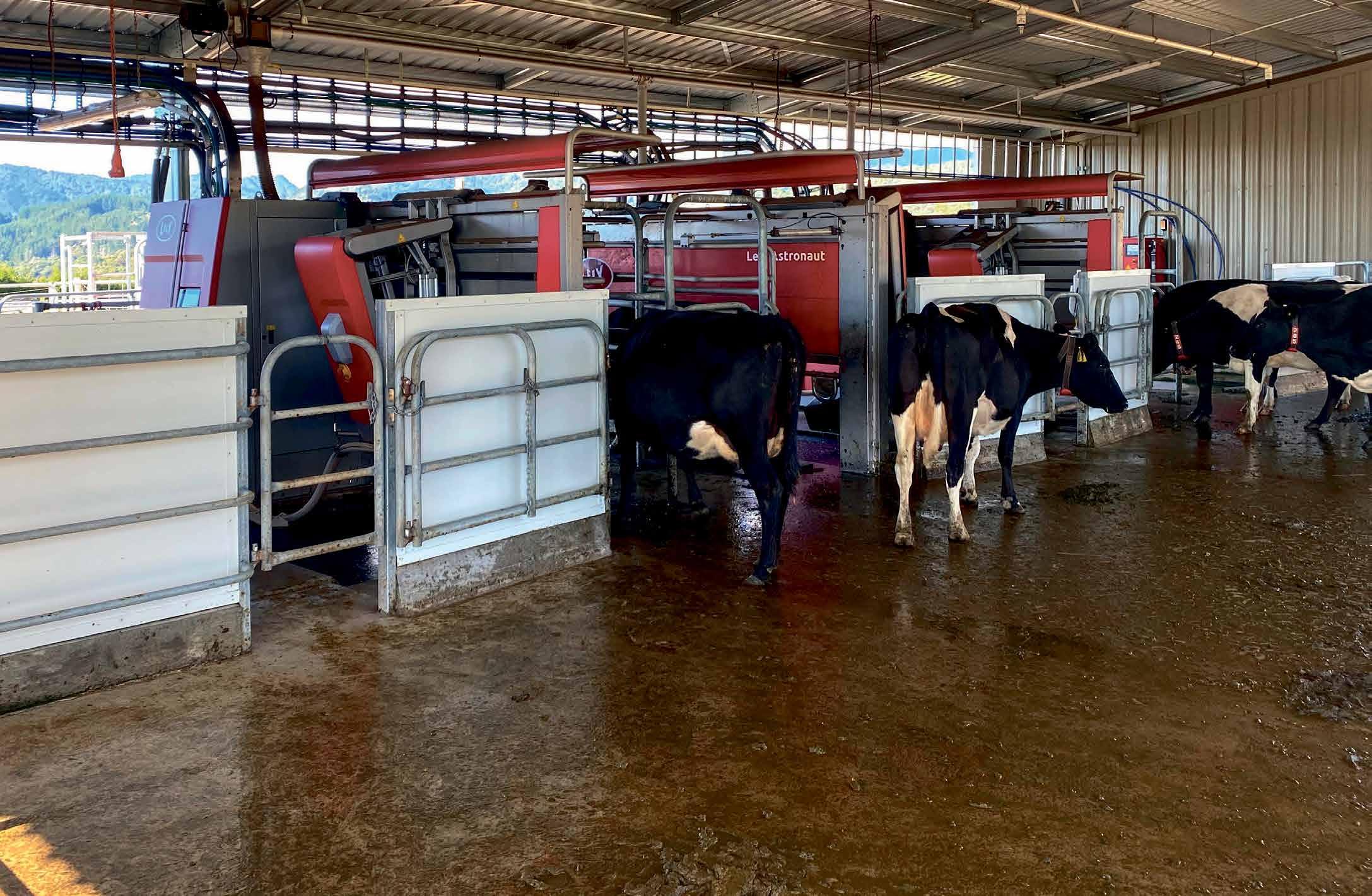
profitability
Are you efficiently identifying cows on heat? robotic milking system, in addition to activity and rumination data, provides determine heat attention more accurate? For example, by estimating and offer other health-related attentions that could impact successful meeting the ‘on heat’ criteria will be waiting for you in the separation yard.
Want to learn more of our technology? Then get in touch!
Bright farming is yours by choice
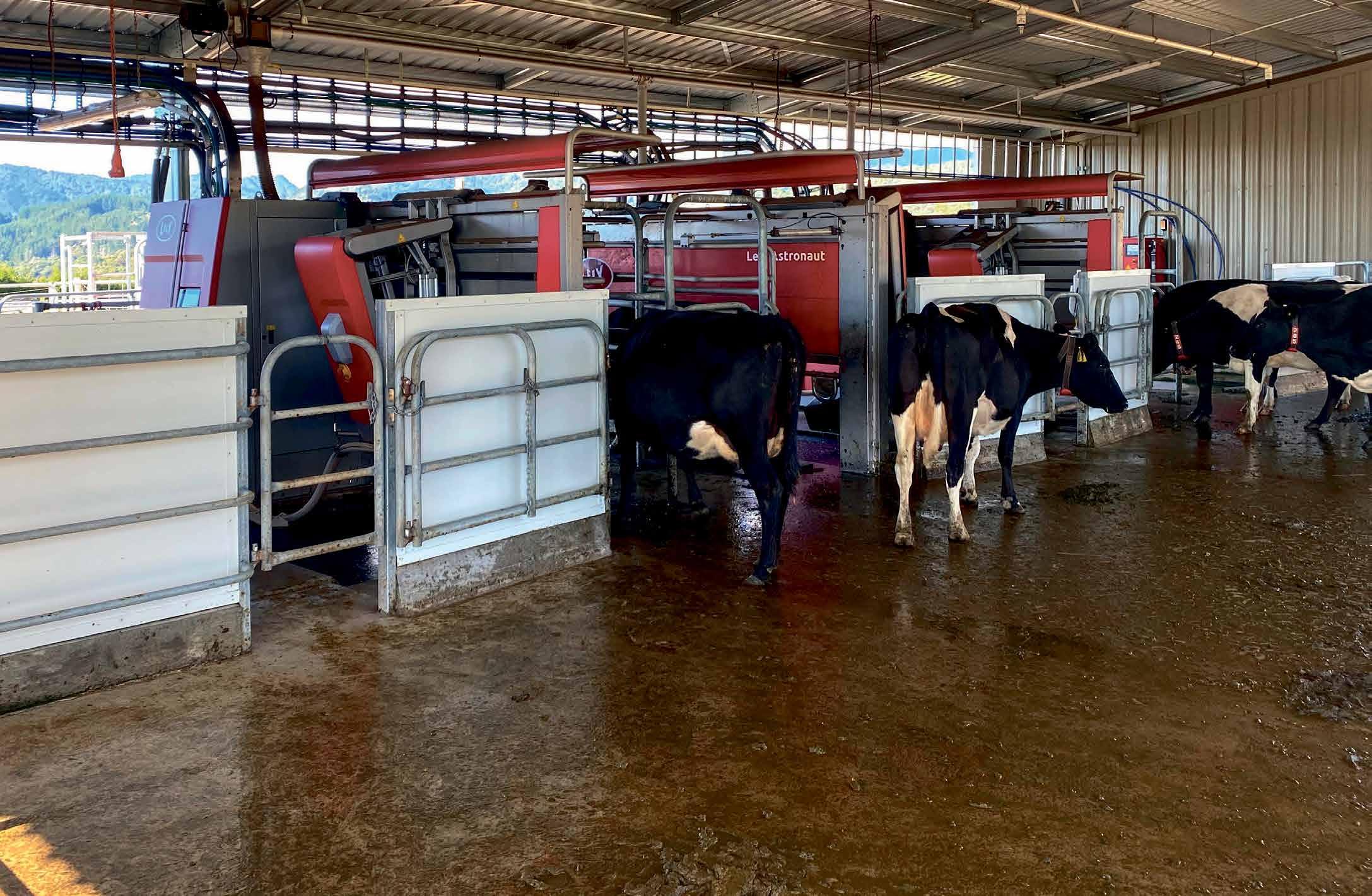
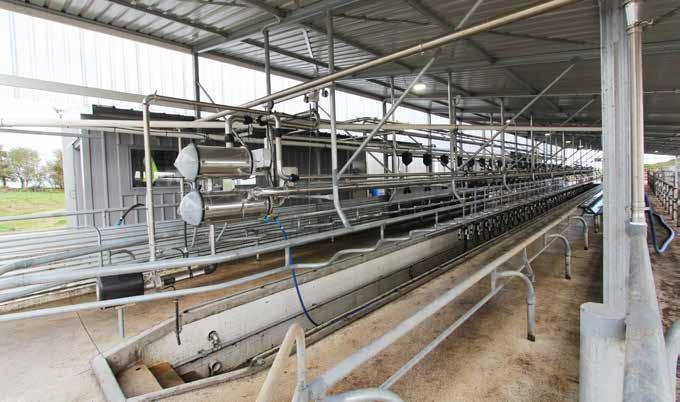


magic! Mamaku 50-aside
Two seasons on, Andrew and Christiane Myers are “very happy” with the ‘new’ 50-aside herringbone on Ngatira Group’s 432 hectare dairy farm at Mamaku north of Rotorua.
The Ngatira Group is a farming partnership between Andrew’s parents and sister, Andrew and Christiane.
The family own and farm a dairy property in Cambridge and in 2012 were looking to grow and saw the Mamaku property.
“It was close enough to the home farm but had a higher altitude and was colder and wetter which complemented the Cambridge farm where we have had some dry summers.
“We took over the farm on Christmas Day 2012 and, for the remainder of the season, milked 300 cows already on the property, building up to 600 cows over winter with cows from the home farm, or bought in. The cows are crossbred tending to Jersey, which are well suited to the typography and soil of the farm.”
Square farm
Andrew says the farm is square – 2km x 2km – with the original dairy and support buildings located in the centre, which was ideal. But the old dairy had had its day –concrete in the yards and shed had been made using rhyolite, which is more chalky
than sand, so over the years the concrete had degraded.
“We worked with the old shed for a few years, upgrading a number of components of the milking system but performance was always compromised by the degrading condition of the concrete.
“Initially we considered replacing all the concrete but, in the end, it made better business sense to build a new dairy adjacent to the old and transfer the recently-installed components across.”
Andrew says the new dairy was always going to be a 50-aside herringbone “but we decided to initially set it up with 44 sets of cups and retrofit the balance sometime in the
future. We wanted a simple, functional and efficient dairy – basic without technology but with great cow flow”.
Steeper roof
“When it came to the dairy’s design we wanted a steeper than normal roof, so we’d have good drainage and avoid algae build-up often seen on flatter roofs, with a covered walkway which is open to but separates the milking area from service rooms. The roof line is repeated over the service rooms – with clearlite panels extending the walls and immediately under the roof to bring light into the dairy. Site works commenced at the start of 2022

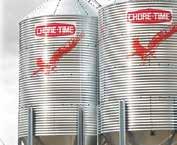
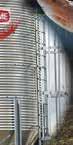
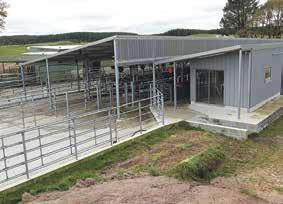



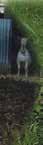
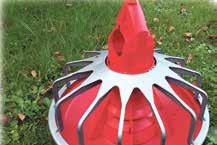
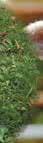


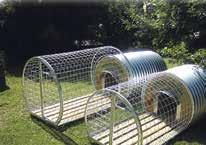
The dairy is light and bright thanks to clearlite panels which extend the walls.
Vats separate the staff and storage rooms from the milk and pump rooms.
The steeper roof line is repeated over the auxiliary rooms.

NGATIRA GROUP
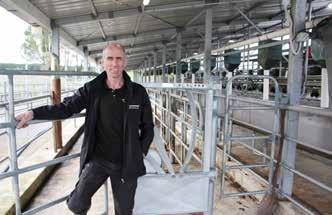
Ngatira Group Ngatira
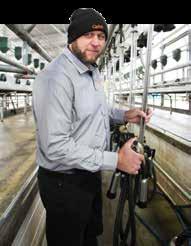
and Andrew recalls they “optimistically hoped it would be completed by August in time for calving”. “In reality, however, due to a range of factors including the building boom and contractor delays, it wasn’t commissioned until September 2022 when we already had 400 cows calved.”
It was, Andrew says, a stressful time. “We had to calve and milk once-a-day in the old shed and then, in one afternoon, transfer across all the vats and plant, connect and wire it into the new dairy – including getting approval of the new installations that night from our milk processor!”
Enhancing the plans
Don Chapman Waikato Ltd constructed the new herringbone and Andrew expresses appreciation for the company’s willingness to work with plans provided by an external party.
“Shanan White, managing director of Don Chapman, reviewed the plans and made several enhancements to improve functionality and ensure compliance with QCONZ and MPI standards. The original plans lacked detail on yarding, pens and animal handling – all of which
Don Chapman Waikato designed and incorporated. We’re highly impressed with their approach and expertise,” says Andrew.
As part of their contract, Don Chapman Waikato engaged Leask Engineering to install pipework, rails, and gates.
Edwin Meek, co-manager of Leask Engineering, says the company has 65 years’ history building and installing animal handling equipment. “We take pride in our innovative solutions that enhance operational efficiency and client satisfaction.
“We fabricated and installed Ngatira Group’s herringbone steelwork, pit step rails, platform entry gates, backing gates with a yard washing system, exit races, holding facilities, AI and vet race setups, and a Leask headbail,” says Edwin.
In-shed feeding
Andrew says the existing Corohawk Feed System was incorporated into the new dairy.
Corohawk director Jamie Hawkings says Ngatira’s feed system features a Chore-Time silo.
“Our dispensers are the strongest on the market and feature a ‘Y’ end which halves the number of dispensers required for
savings to the pocket and allowing more light in the shed.”
The team at Qubik delivered and found a cost-effective way to use existing plant and machinery – many of which were only a few years old, and installing new where needed.
Qubik Putaruru’s operations manager Pete Nelis says the new Waikato Supa 4 milking system offers optimum vacuum control and fast milking. A 100mm milk line, which ensures great milk flow and stable vacuum, maximises animal comfort and minimises risk of mastitis.
“The dairy’s Waikato 320 clusters feature lightweight shells with Quadrant liners and Read slide mechanical pulsators were also installed.
“The dairy has a Fristam centrifugal milk pump and 90L receiving milk can with 60L sanitary trap, a Qubik Variable Speed Drive milk pump controller and milk recovery system. The vacuum system is a BP400 blower system with VSD.
“The Waikato G2 Swingdown Jetter system creates more space in the pit during milking and also reduces RSI by limiting shoulder work with jetters at chest height.
“The dairy features stainless steel above and
below ground pipework, connecting water pumps brought over from the old shed.
“Qubik transferred the milk filter, doublebank plate cooler and vacuum system from the old shed, supplying a new 600L stainless steel jetter tub, a Qubik fabricated hot water cylinder stand and two 600L hot water cylinders.”
Pete says Qubik specialises in offering farmers a one-stop-shop when it comes to renovating or replacing dairy systems.
“We offer the complete package – milking systems, effluent management, refrigeration, feed systems, water reticulation and have our own fabrication team able to design with their 3D CAD software programme.”
The heart
All electrical and refrigeration was undertaken by Philip Smith Electrical and Refrigeration of Rotorua.
Andrew says the new dairy is everything they hoped it would be as the heart of an efficient grass to milk dairy farm investment. “Cow flow is good although compromised to some extent by in-shed feeding because the cows just want to stay and eat!”

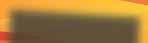
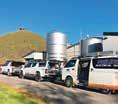

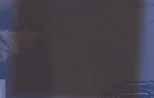


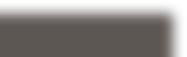
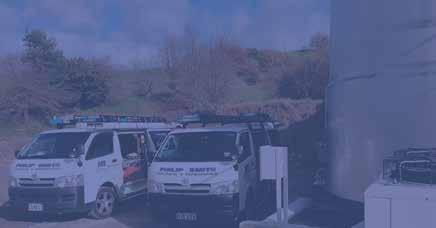
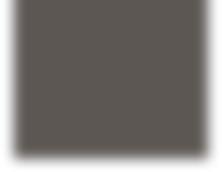
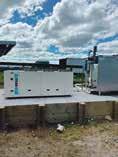

Tailored Solutions, Nationwide
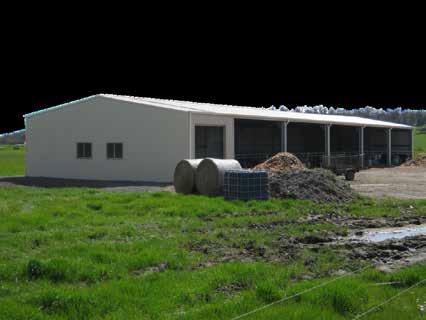
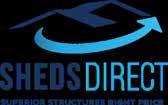
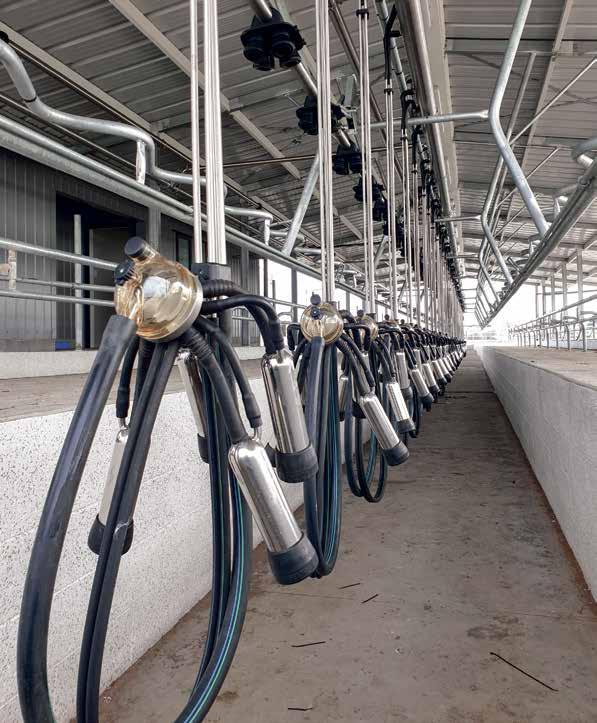
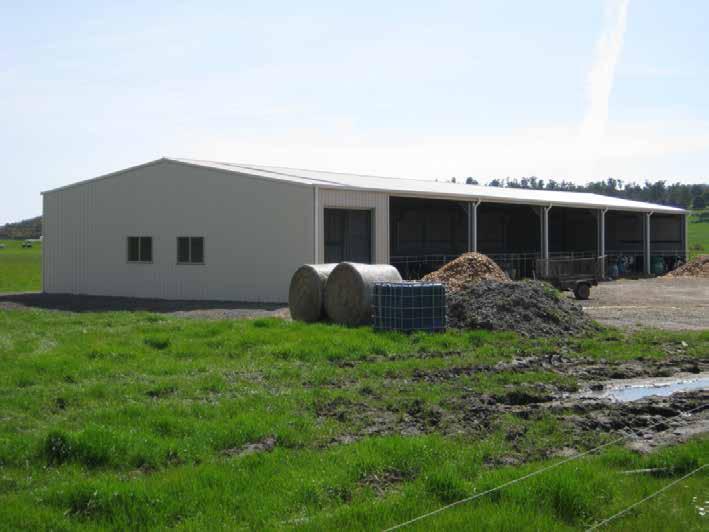
Clare Bayly
Ngatira Group’s Mamaku farm team: Andrew Myers, Phillip Hauser, Paul Fredrickson and Sukhwinder Singh.
Leask Engineering’s Edwin Meek with their head-bail.
Qubik’s Pete Nelis checks the dairy’s lightweight clusters.
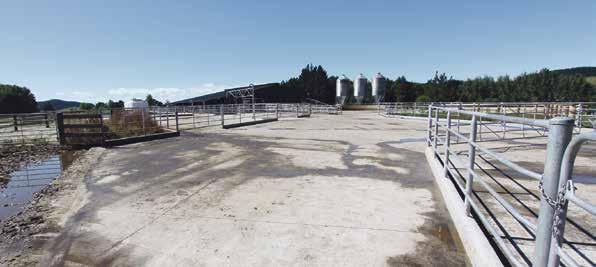
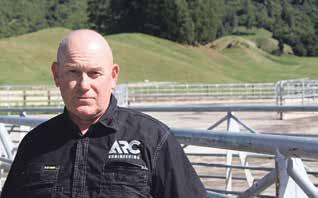

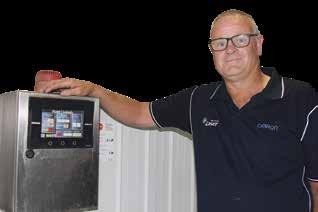
New rotary enables
The driving motivation for replacing a 64-aside herringbone with a 60-bail rotary was to improve the work/life balance of staff at Totara Valley dairy farm north of Taupō.
Roger and Amanda Garland purchased the 540 hectare – 460ha effective – dairy farm about 11 years ago and, over the years, added technology enhancements like automatic cup removers to improve its functionality.
“Contract milkers and farm managers, Matt and Sarah Griffiths, have been with us for 14 years initially on one of our other farms, and moving to this property when we purchased it,” says Roger.
“They have a team of four staff but the 64-aside herringbone was very labour intensive, requiring three people in the shed for up to eight or nine hours a day at peak.
“Given most of the team have young families, we wanted to create an environment which gave them time away from milking so they could spend time with their families,” says Roger.
Quality, efficiency and consistency
The focus of the System 3-4 farm is quality, efficiency and consistency, with Roger saying: “We don’t send off one bobby calf – they are all reared on-farm and then finished to weaner or 100kg on the Y Wuri Trust’s grazing blocks”.
“We also don’t do any artificial breeding – putting Hereford bulls out at the start of mating followed by Friesians so they have markers for replacements.”
It is a system which clearly works with the mainly Friesian herd’s empty rate around eight per cent and average production of 450-470kgMS. The farm milks year-round – around 1100 cows in spring and 250 true autumn cows, plus carryovers, in autumn.
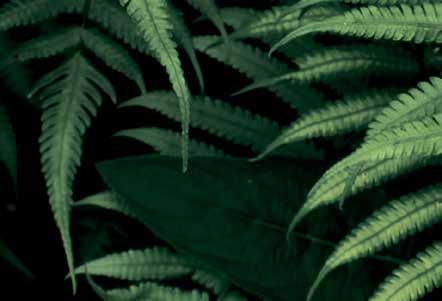
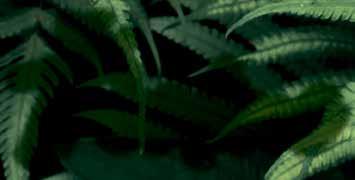
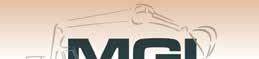


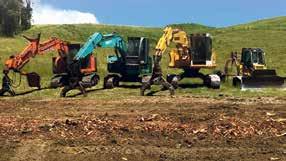
The same philosophy applied to the new dairy – every efficiency to make it a more productive environment. “It was always going to be a rotary because we wanted to reduce the labour quotient of milking,” says Roger.
“Gibson Construction has built a few sheds around the district – we have one on another farm – and the Gibson team are great to work with, producing a quality product, so it was a no-brainer to get them in here.
“Because we milk all-year-round, we needed to keep the old shed functioning so the building site is adjacent so we could tap into existing services.”
Y Wuri Trust has a range of heavy machinery –diggers, scrapers and bulldozer – “so we were able to do the site ourselves,” says Roger.
Concept plan
Gibson Construction director Brent Bird says he met with Roger and Matt to get their wish list for the new shed and this enabled a concept design to be developed.
“This was tweaked a bit around placement of rooms and yard layout based on feedback Matt got from vets and truckies on what worked and what didn’t.
“The shed has a timber frame with colour steel cladding and features a half-moon raised area, which is good for viewing on the platform and when the cows are being milked. The extended roof over the animal handling area provides protection from the elements. It’s a nice flowing shed, well set up,” says Brent.
“Gibson Construction sub-contracted all concreting of the yards, which were extended into the entrance/ exit race to reduce the amount of mud coming onto the yards and into the shed.”
Construction of the new dairy began in November 2022 with the pouring of the yards.
All steelwork, including yards, were constructed by ARC Engineering Taupo. Director Matt Nash
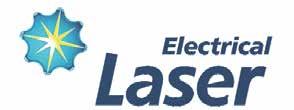
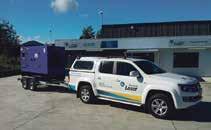

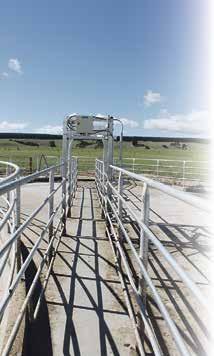
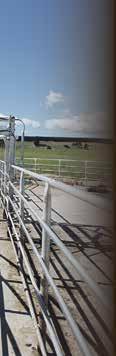
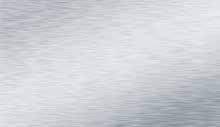
Extended concreting to prevent mud coming into the yards.
Above: ARC Engineering Taupo director Matt Nash.
Above: Laser Electrical’s Darryl Karl, with the plant control board.
Left: Qubik Putaruru’s Chris Maughan and Pete Nelis, checking out the new clusters.
work/life
says ARC does general engineering “from sheet to structural steel”. “We built the skeleton of the shed for Gibsons to complete, built the yards and custommade the gates and backing gates.
“There are staggered drafting gates in the exit race which enhances manual drafting – one gate ahead of the other, giving the operator more time to direct cows.”
The Waikato Orbit Concrete 60-bail rotary platform, which features Multiroller twin track system, was installed by Moa Rotary Platforms.
Optimum protection
Moa’s Shane Arthur says the platform’s 2.7m wide deck provides optimum protection for milking and electronic equipment and the SmartFit mounting system improves the efficiency of equipment installation and maintenance.
“The new platform features a stainless-steel skirt, which directs water away from milkers.”
Qubik supplied and installed all dairy, water and effluent technology.
Qubik’s Pete Nelis says: “Waikato equipment includes 320HP clusters, automatic cup removers, in bail teat spray, bail gate restraints, auto plant and vat wash”.
“In the centre the Multi Services gland runs the milk line in addition to compressed air, skirt wash, teat spray, vacuum and wash water, enabling the platform to continue to turn when the wash is going through. This allows for cows to be AI’d with a wash going through at the same time, helping to reduce time pressure during mating. The Multi Services also allows for the teat spray tank and compressor to be located

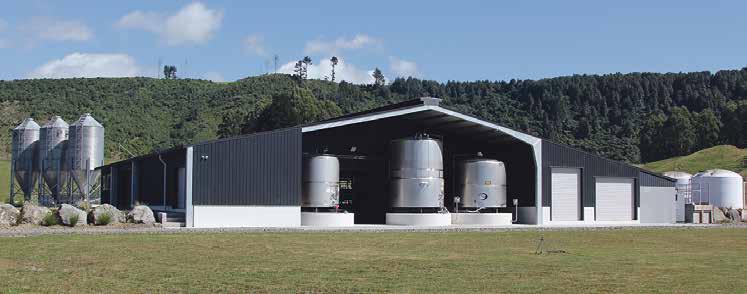
externally of the platform.
Pete says the milk recovery system uses compressed air to force residual milk into the vat preserving milk and preventing water grades. “On the vacuum system we installed a BP400 vacuum pump with a Variable Speed Drive. The milk pump is a 2.2kw Fristam milk pump also on a VSD. All the milk and air lines are stainless steel.
Feed system
The feed system was supplied and installed by Qubik using existing silos. The washdown and cooler water pumps were also provided and installed by Qubik.
“Matt kindly allowed us to stay in a vacant farm cottage, allowing our team to live on the farm during the installation which certainly helped with the speed and efficiency of the project,” says Pete.
All electrical work – dismantling the old shed and setting-up the new – was undertaken by Laser Electrical Putaruru.
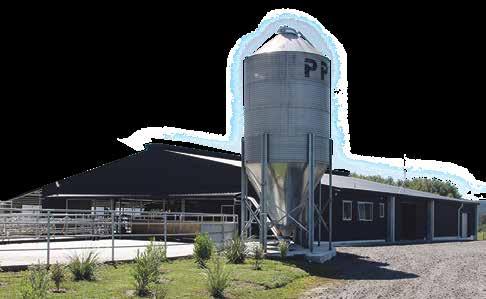
Specific planning
Lead sparkie Darryl Karl says keeping the old shed running while the new dairy was built called for specific planning.
“Laser Electrical installed a new distribution board in the old shed two years ago when it needed upgrading, knowing it would eventually be moved to the new shed – so this was just one element which had to be factored into planning.”
An automation board controls all electrical components in the new dairy –lights, pumps, jetters, sludge and hot water, monitoring the plant wash and issuing an
alarm for faults. “At any time operators can see trends of washing temperatures. The board provides an easily operated overview of all things electrical in the shed ensuring consistency and efficiency,” says Darryl.
Heaters
Other enhancements – which add to operator comfort during cold Taupo winters – include heaters at cups-on and cups-off. Matt says they carried on milking in the old herringbone until the end of May while the new rotary was being built.

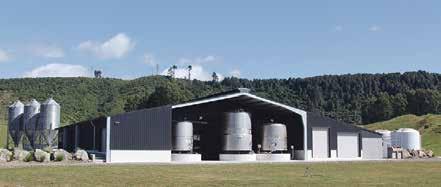

“Effluent
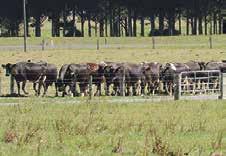
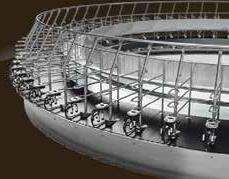
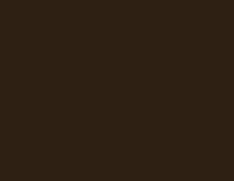
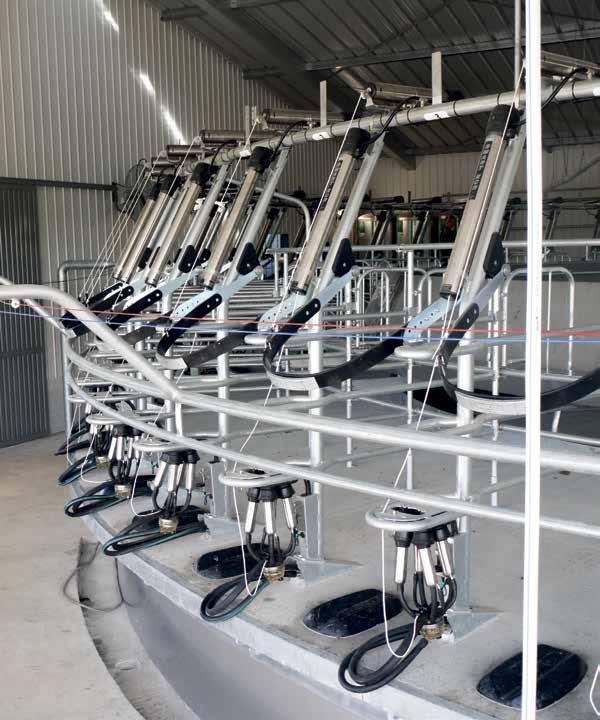
From any angle, a spectacular dairy!

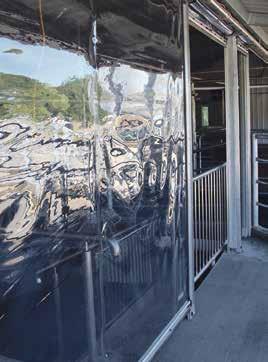
“The only change we made is we didn’t milk on autumn calvers, as we’d normally do, instead trucking them out to one of the trust’s other farms.”
Training ahead of calving
The new rotary was commissioned – on budget and to date – in time for the start of spring calving on July 20, 2023.
Matt and Sarah recall they put the cows through the shed a few days before they calved, and trained all the heifers ahead of them prior to calving.
“The pets were the worst, having to be manhandled onto the platform for the first few days, but after four days the cows were pretty comfortable walking on and off the platform,” says Sarah.
“The feed helps – they were fed supplement in the old shed so it’s part of the enticement and routine of milking. That helped
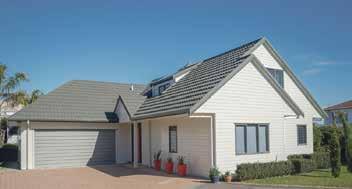


encourage them on and helped them settle to the new environment.”
Three mobs
The herd is milked in three mobs. Two mobs are on twice-a-day and one – the heifers – on once-a-day. Each cow gets the same amount of feed in the shed made up of 50 per cent PKE, 20 per cent soy hull and 30 per cent DDG plus minerals.
Matt and Sarah both say the cows are more settled in the new shed. “There’s no competition for space, each cow has her own area/bail where before they’d be pressed up against each other and they seem more relaxed.
“In contrast to the old shed where we regularly had three people in the shed with another bringing the next mob in, we now have 1.5 to two people. It’s a great shed to milk in – quiet, efficient with good cow flow.”
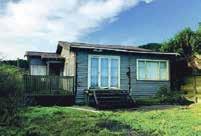
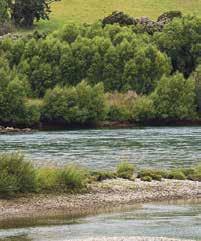
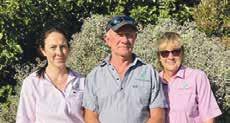
Roger is quick to acknowledge the people behind the dairy’s development. “If it wasn’t for Matt and Sarah it wouldn’t have got done; they project managed it and did a great job.”
“Our three contractors – Gibsons, Qubik and Laser – have all worked together before and this meant the project flowed well –everyone got to do what they needed to do in the right sequence.
“It’s been a great build, there hasn’t been one contractor we had an issue with.
“The hopes we had for the dairy benefitting the work/life balance of our team has been realised. Most have young families so now, instead of their days being dominated by time in the shed, they can get away to school or sport activities for their kids,” says Roger.
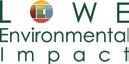

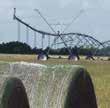
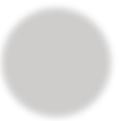
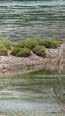
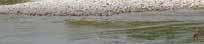
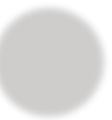
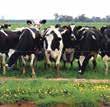

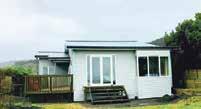



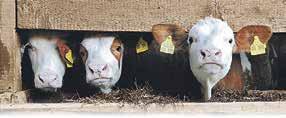

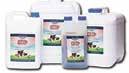
The contractors behind the build: Qubik’s Pete Nelis, Laser’s Marc Camp, Qubik Putaruru’s Chris Maughan, Laser Electrical’s Darryl Karl and the Y Wuri Trust Totara Farm team: Roger Garland, Mike Williams, Jonny Clarke, Wayne Russell, Sarah Griffith, Matt Griffith and Suzanne Burling.
Roger and Amanda Garland with their daughter and business manager, Brooke, on the left.
Clare Bayly
Plastic drop-down blinds installed to protect the milking environment from prevailing wind.
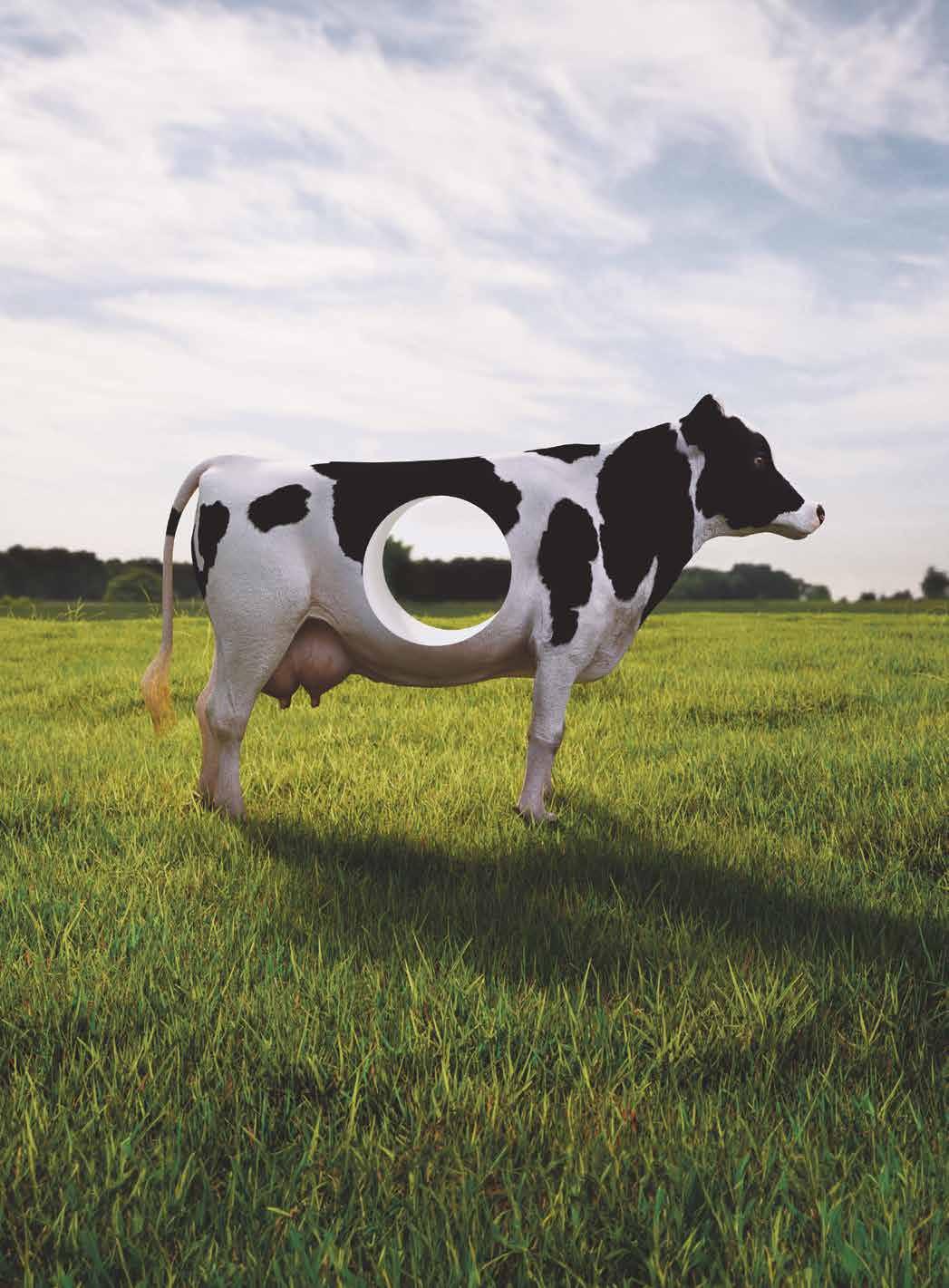
What are your cows missing?
Revitalise your herd with a precise mix of pelletised minerals and supplements that are easy to feed in-shed, 100% utilisable (with zero waste) without wasting another hour dusting. They can’t tell you, but they will show you what Vitalise adds to their health and production. 0508 678 464 cplimesolutions.net.nz/vitalise by CP Lime
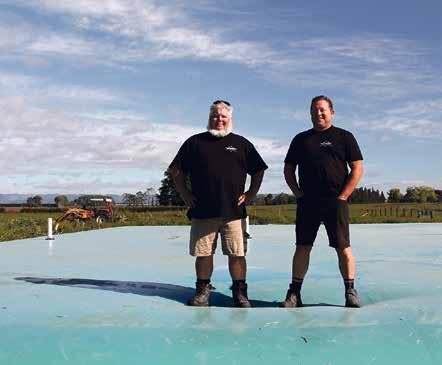
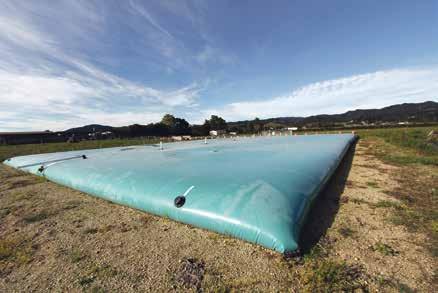
Vortex bladder the
A vortex bladder provides the optimum storage mechanism for effluent on a 71 hectare farm on the outskirts of Whakatāne.
Owned by Janet and Shawn Jenkins, in partnership with Janet’s mother, the property is classified as having high risk soils which do not drain freely in times of high rain.
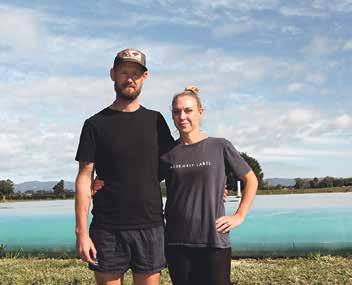
“We built a new 20-aside herringbone in 2014,” says Janet. “At the time we had two unlined effluent ponds which were consented for 10 years, so we had plenty of time to mull over what type of system we would install to replace them.
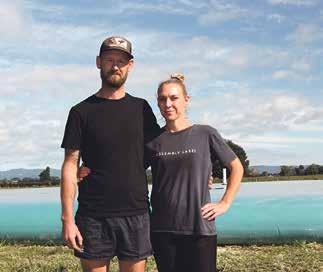
The design
“We looked at a variety of storage systems but the soil type combined with our desire to build a new system – which was economical to install and maintain, minimised smell, and provided optimum storage without the associated health and safety risks of open ponds – led us to an enclosed bladder.”
“In early-2023 we spoke with Bevan Thomas and Mark Boyde from 60/40 Milking who, in



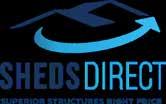
turn, put us in touch with an effluent specialist to produce an accredited design which would match a 15-year consent.
Mark Boyde, who heads 60/40 Milking’s effluent division, says their systems “are based on industryleading FDE Design Codes of Practice and Design Standards so farmers can rest assured that they’ll stand up to even the most demanding conditions”.
“After considering all the options, a vortex bladder provided the optimum solution, ticking all the boxes.
“The bladder was originally designed in France undergoing extensive testing across Europe and the United Kingdom before it made its way to Australasia. In a few short years the bladders have earned a reputation for providing an extremely well-priced and effective option for storing liquids including effluent.”
The material
Mark says the bladder is made of pretensioned reinforced fabric “delivering exceptional strength, no stretch and reduced weight with a 15-year guarantee”. “And because it is not a permanent structure the bladder can be easily moved to another site should this ever be necessary.
“Because the system is contained, you are able to limit the amount of storage required to effluent as, opposed to open systems, the bladder does not collect rain water – just liquid effluent.
“All effluent gravity feeds from the dairy to two stone traps where solids are separated from liquids – solids remain in a bunker for removal and application to pasture, and liquid goes to a bunker or tank.
“The optimum is for liquid effluent to be irrigated to pasture on a daily basis. The Jenkins use a stationary canon, which operates for one
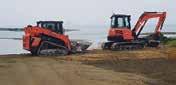

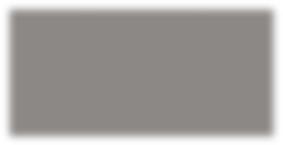
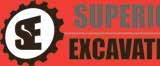
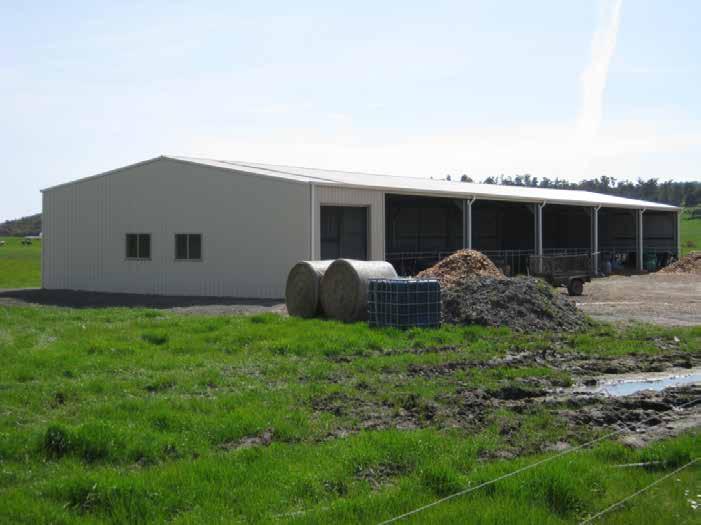
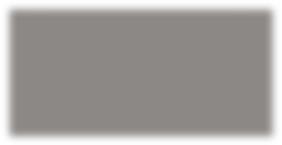
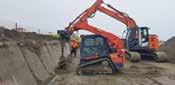





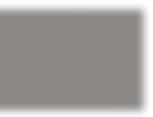

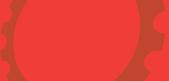
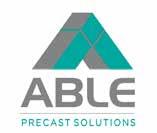
Mark Boyde, head of 60/40 Milking’s effluent division with 60/40 Milking’s owner Bevan Thomas.
The new vortex bladder offers maximum storage for moderate cost.
Shawn and Janet Jenkins say the new effluent system is delivering more nutrient rich effluent.
Wintering Barns | Horse Stables | Farm Sheds | Hay Barns Machinery
optimum solution
hour per day applying 25 cubes per hour at a rate of 7ml.
“In the event of heavy or persistent rain, and/or water saturated soils, liquid effluent pumps from the bunker straight to the bladder.”
Mark says any solids that remain in the liquid when it enters the bladder is collected in the centre of the bladder by virtue of the vortex action where, in much the same way as a whirlpool, the liquid spins in a circular motion drawing any solids into the drain hole in the concave centre of the bladder. From here it’s a simple matter to periodically pump it out.
The site
The installation
Cocquetdale Trust
“The installation of the new bladder, consented for 15 years, was incredibly quick and simple and took place in conjunction with the construction of the stone traps and tank. Once the bladder site had been prepared it was simply a matter of days before the new bladder was up and running,” says Shawn.
“Having an enclosed bladder means we no longer have any concern over the danger of an open pond for people or animals and will never have to worry about build-up of sludge or crust on effluent.
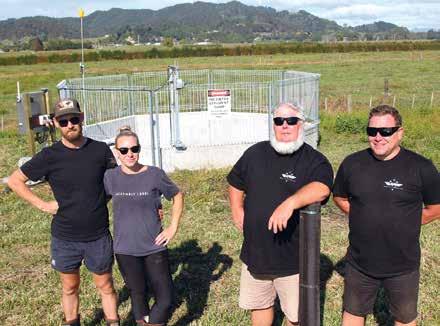
Superior Excavation of Whakatāne was called in to construct the concave site for the new bladder. Superior’s owner Leigh Carter says the site was constructed from sand transported in from a nearby creek bed. “Accommodating the concave nature of the bladder required the centre of the site to be 300mm lower than the outer boundary.
“Superior Excavation is one of the only contractors in the greater Bay of Plenty who have a box grader laser on our posi-track which enables us to, precisely and accurately, develop a building platform which has the required dual grade.”
The new stone traps, storage bunker and effluent tank were built by Able Precast Solutions of Awakeri.
Shawn and Janet say the site preparation took place shortly before Christmas 2023 with the new system operational in the New Year.
“We’ve noticed that the effluent we pump to pasture now – regardless of whether it’s direct from the tank or the bladder – is darker, more nitrogen rich, than it used to be, simply because it hasn’t been diluted by rain water. When you have paddocks which can get saturated from rain, knowing that what you’re applying is ‘pure’ effluent is an important consideration.
The result
“We irrigate directly to farm every day when the weather allows. The canon is positioned so effluent never extends beyond a mandatory 20m buffer zone around the external boundary of the farm. Rain water at the yards is diverted to the old effluent ponds.”
Shawn says effluent lines were extended along with the new system “so we now irrigate to around 15 hectares”.
“We’re really pleased with the new system –other than changing the direction of the pump ie from paddock to bladder, there’s nothing we need to do; just keep milking.”
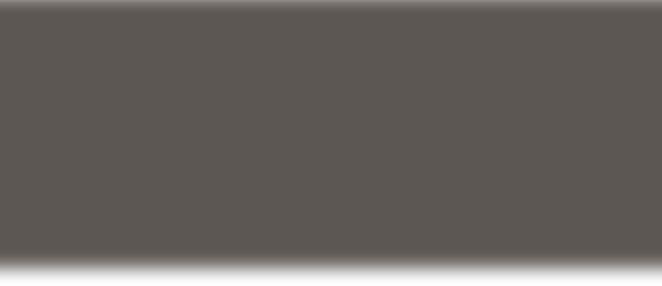


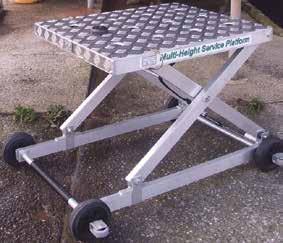

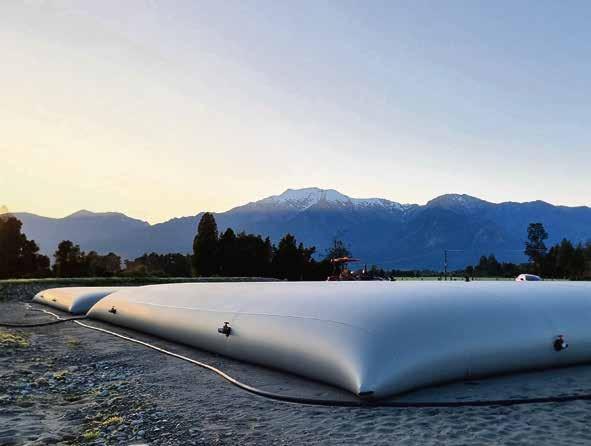





The 25/100 positive displacement pump is capable of pumping 25 cubes per hour at full speed.
Sunglasses are an essential piece of kit in the Whakatāne sunshine.
Clare Bayly
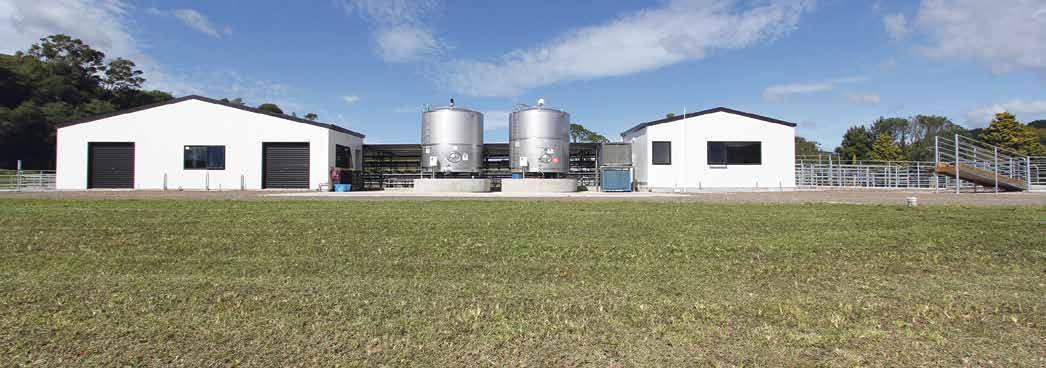
Efficiency the driving force
There’s no missing the Symmans family’s new dairy.
Located at the end of a road not far from Whakatāne, the new streamlined dairy is framed with hills on one side, and trees on the other. The fact that the dairy has been in operation, milking 400 cows twice-a-day for most of the 2023/2024 season, is not evident in the interior, which is, quite literally, sparkling.
Lyn Symmans owns the farm, and her son Sam Symmans and partner Colleen Webb are 50/50 sharemilkers. The trio, who admit the overall goal of the new dairy was compliance, are evidently proud of what’s been achieved.
“My Grandfather and father have owned and operated part of this farm since the 1970s,” says Sam. “[With] Our family adding the portion which now contains
the new dairy in 2018. Accessing the old 30-aside herringbone required the tanker to cross a bridge which the cows also had to cross.
“We would have had to build a second bridge to remain compliant, combined with the need for a new effluent system for the consent renewal.”
Sam says the System 3 farm has three barns where the cows are fed supplements each day. “It made sense to build a new dairy close to the barns to optimise efficiency and reduce the cow’s walking distances.”
Cost-effective option
When it came to the optimum size, Sam and Colleen say herd numbers meant a herringbone was the most cost-effective option. “We didn’t want to be doing more than 10 rows per milking and didn’t want
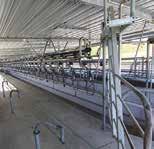


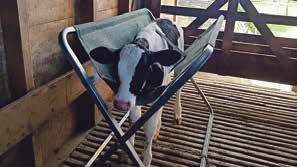
any more than two people in the pit, so we settled on a 40-aside.
“We went with a ‘tweaked’ Chapman design dairy –with open sides behind the vat stand, which separates – at one end –the pump room, supply room and milk room and, at the other end, the office and toilet. There is a covered corridor between the milking area and office block with bench space for such things as herd testing.
it to the south. So far, the open design provides enough warmth and is relatively sheltered from the prevailing wind.”
Symmans
In the second week of January 2023 site development commenced with the groundwork for the dairy and adjacent Klip Tank foundations, constructed by Superior Excavation of Whakatāne.
Sam says the orientation of the building was tailored to suit the site. “Traditionally dairies face the north but if we applied that logic it would have meant the tanker would have to cross the cow path to and from the shed – so we opted to orientate

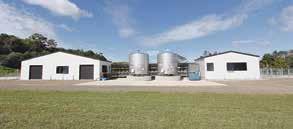
Superior Excavation’s Leigh Carter says: “Significant earthworks were required to excavate and build up the dairy building platform, and the site for the new Kliptank”. “We were able to access a seam of pumice on the farm and, in all, probably transported around 6000 cubic metres to both sites.
“Superior Excavation is one of the only contractors in the greater Bay of Plenty
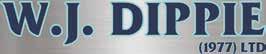
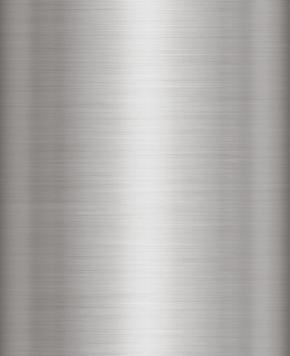




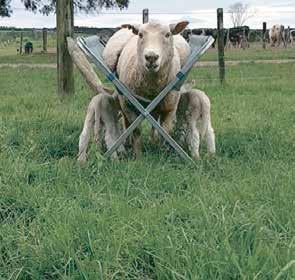
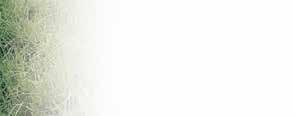
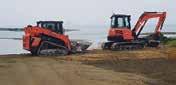

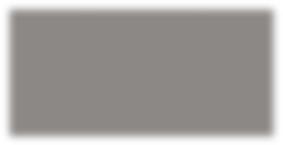
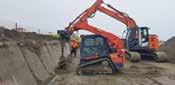
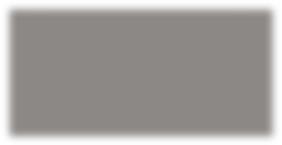

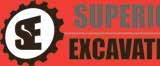




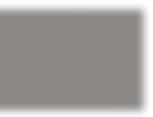
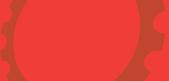


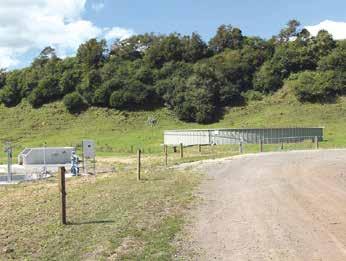
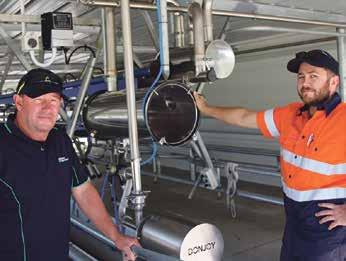
who have a sharp grade laser on our positrack which speeds up and adds a huge degree of accuracy and precision to the final building platform,” says Leigh.
Chiller panel
The new dairy was constructed by Bay Builders, in conjunction with Yates Carpentry & Construction’s Alex Yates of Whakatāne.
“We had a builder on-site from January 2023 for about three months,” says Sam.
“The buildings are clad in chiller panel with a long run iron roof over the milking area. The pit is wide and deep in a modern design, which enhances milker comfort and efficiency. The pump room has also been positioned at the back end of the shed to minimise noise in the milking area and increase vacuum pump efficiency,” says Sam.
King Farm Services of Whakatāne supplied and installed the milking machine, water and effluent systems.
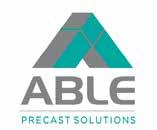
King’s project manager Robbie Hall says the dairy is equipped with a Delaval 40 HL-HB swingover with EP100B electronic pulsation. The vacuum system is a Delaval LVP4500 and the cooling system a doublebank plate cooler with chilled water on one side. “The dairy features full stainless steel washdown and water systems,” says Robbie.
“We also supplied a complete effluent system consisting of double stone-traps and bunker – provided and installed by Able Precast Solutions – leading to a sump with transfer pump to the Kliptank.
“Irrigation to pasture is direct from the Kliptank via a fully automated Varisco pump which applies effluent via a Torpedo rain irrigator.”
Robbie says King Farm Services provide design and installation of all milking, water and effluent systems including fabrication and welding.
Built to last
The yard and milking area steelworks
were completed by WJ Dippie of Tāneatua, who have built a reputation, across more than 76 years, for engineering which is built to last.
Grandson of the founder, Bill Dippie says they “look at every aspect of every job, looking for those little enhancements which will increase the life and/or efficiency of the job”.
“In these yards, for example, we made the rails around the exit yards higher, 1600mm, to discourage cows from jumping out. We also built strengthened galvanised steel posts to support the breast rails in the shed to ensure they last.
We built all yards including the backing gates.”
Sam says they had previously experienced cow lameness which had been “managed” in the drafting race of the old shed.
“Including a Wrangler Cattle Crush was an essential item in the new dairy’s animal handling yards; it’s brilliant. Makes treating lame cows a lot easier, and more

comfortable for the cow.”
The Wrangler’s Wilco Klein Ovink says the Wrangler quickly and simply adjusts to different size cows, adding that in the last year they’ve developed a crush for cows above 650kg.
Comfortable to milk in Whakatāne-based Mathis Electrical did all of the electrical work for the new build – from bonding underground mesh to eliminate stray voltage, to all electrical wiring of the dairy and effluent system.
The new dairy was commissioned in September 2023, with Sam and Colleen saying the cows were challenged for the first milking but quickly settled.
“The swingarms on the cups take clutter out of the pit and improve cup alignment, making it a comfortable shed to milk in. The shed has been set up so in future we can add auto cup removers, auto drafting and in-shed feeding,” says Sam.

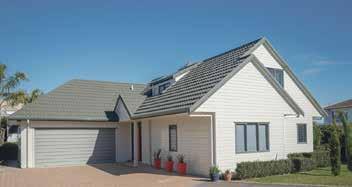


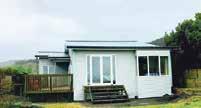
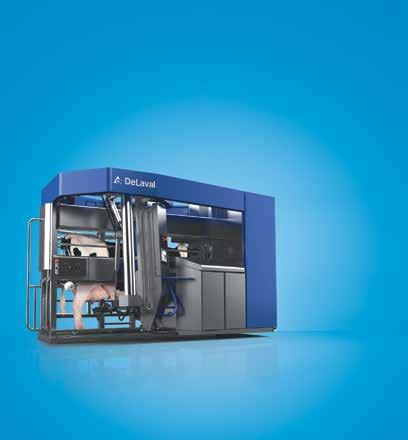

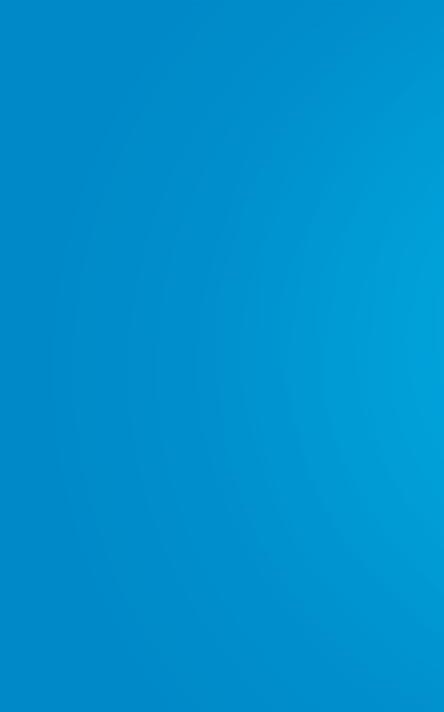
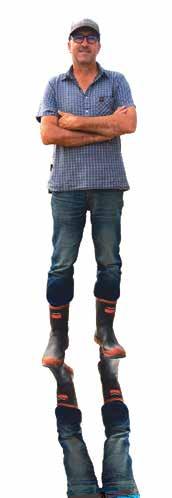
Farm owner Lyn Symmans with son Sam Symmans and partner Colleen Webb.
King Farm Services’ Robbie Hall with technician Marshall Bagnall.
The new effluent system – sand traps, bunker and Kliptank.
Revampvision realised
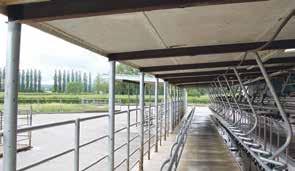
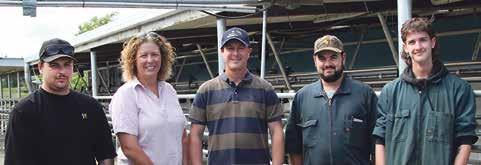
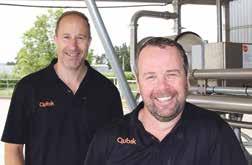
Roof supports were moved to the roof edge to accommodate the wider pit and better aligned herringbone bails.
Hakin Farm
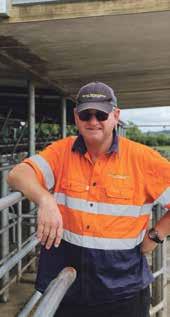
A concrete water trough in the milk room was one of many adaptations which had taken place in an old herringbone on the outskirts of Ōtorohanga.
Tony and Louise Collingwood took possession of the 165 hectare dairy farm – and milking shed – on June 1, 2023, saying that, for their second visit, they bought along friend and earthmoving contractor Paul Wolvers.
“Paul is a visionary; he can look at something and see its potential and as we walked around the shed – which had reached the end of its productive life – he could see its potential,” says Tony.
“The shed was still operational but in a tight labour market we wanted a dairy that
was conducive to attracting and retaining top people.
“Paul has worked with us on the home-farm and understood our goals for the new property and was able to conceptualise a project which would achieve our goal for the new farm,” says Tony.
“We effectively rebuilt the milking platform of the dairy, leaving the walls and roof as they were.”
“Originally a 42-aside, the herringbone had 900 centres meaning the cows had their heads against the wall on one side and were virtually side-on to the pit, which was very shallow.”
Eight weeks
The Collingwoods had a window of eight weeks to revamp the shed with an end date of August 1, 2024. “However, as it turned out, the
first milking actually took place days earlier on July 28, 2023 – testament to the way the team of contractors all worked together to get the job done.”
“Work started on the morning of take-over day – June 1, 2023 – with all pipework and milking plant cut out and removed.
Lead contractor Gibson Construction, led by Hayden Pryor, moved the structural roof poles to the outer edge of the roof to enable them, working with Paul Wolvers Contracting to excavate the old pit and dig a new one 200mm deeper than the previous pit and in the centre of the new posts.
Again working with Paul Wolvers, all of the concrete under the roof line was removed and replaced enabling Gibson Construction to build a new bail area, line the new pit and build a new AI race compliant with new safety
standards on the outer side of the dairy. Qubik stripped out everything in the original milk room, leaving the vats, allowing Gibson Construction to install new underfloor drainage, floor and wall coatings.
Tony says other yarding was not altered with the exception of a new gate, which Paul Wolvers recommended should be inserted into the outer pipework of the collection yard to make it more accessible to machinery if and when needed.
Consistent excellent hygiene
Qubik supplied and installed a 44-aside Waikato Supa4 midline system into the revamped shed. The milking plant consists of 101mm milk line, 63mm pulsation line, SmartPuls electronic pulsation, 44 320 cluster sets, lightweight stainless steel shells and


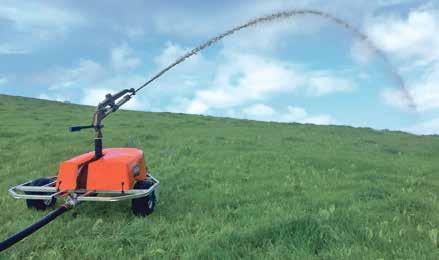

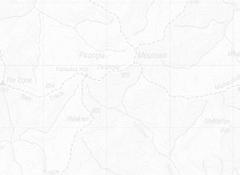
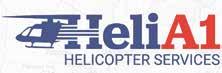


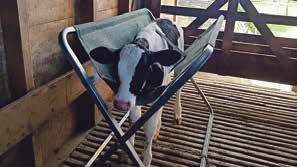
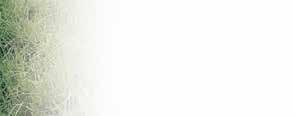
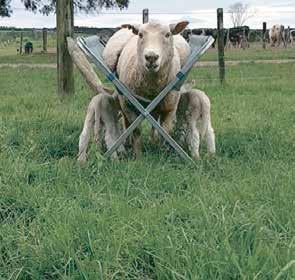
The Hakin Farm team, from left: Farm manager Zac Van Dorston, owners Louise and Tony Collingwood, 2IC Harley Frazer and farm assistant Ethan Thompson.
Qubik’s Nick Heffer and Kyle Osborne.
Paul Wolvers was able to conceptualise and help realise the dairy’s potential.
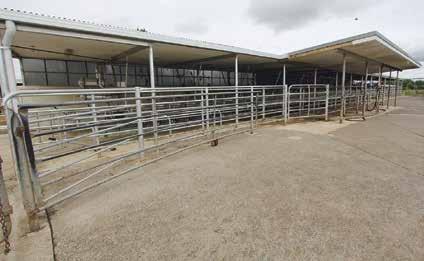
Other than new guttering, there were no changes to the dairy roof that extends over the AI area.
quadrant square liners. The milking system has a 90L receiving milk can, 60L sanitary trap, a Fristam centrifugal milk pump and a BP blower vacuum pump with SmartDrive.
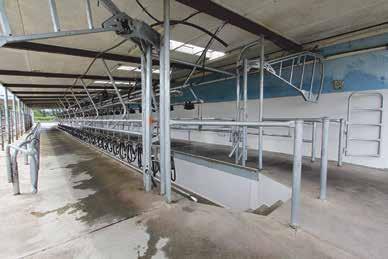
G2 cluster washers were installed to ensure consistent excellent plant hygiene – the washer system is strong, robust and Kiwi-designed and built.
Energy use is optimised thanks to a Qubik Variable Speed Drive milk pump controller and milk recovery system.
The water system at the dairy was updated and replaced by Pumpn. Owner Shane Phillips says his Pumpn team considered working with the old system “but so much had been modified as the years went by and the most efficient approach was to pull it all out and start from scratch”.
The farm’s existing effluent system was tidy but some improvement was needed to improve flow from the cowshed to the stone trap. Paul


The new outlet point for effluent from the
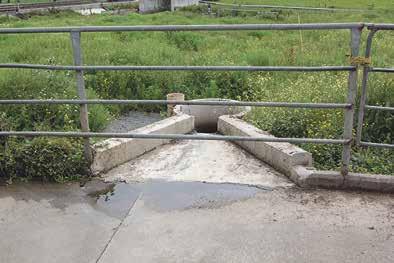
We milk in two herds and the flow is great.
Wolvers, working with Gibson Construction, designed and installed newly-improved exit points for effluent from the shed, and located and replaced damaged piping between the shed and the effluent system so the overall system now works optimally.
A team!
Tony and Louise say at times there were 10 or more contractors working in and around the shed “but they worked as a team, everyone committed to meeting or exceeding our deadline so we can’t speak highly enough of them”.
“The shed was finished on July 28, 2023, and by then we’d already calved half the 470-cow herd,” says Tony. “Thankfully there was a small 10-aside shed on the back of the farm which we utilised, but we couldn’t send the milk off so it was used for the calves.
“We didn’t calve any heifers, which was advantageous with the shed rebuild. Around 350 crossbred cows came from Morrinsville, 50 locally and the balance from the home farm.”
Flow is great!
Tony says the cows settled really well into the new shed. “We milk in two herds and the flow is great; having a modern, efficient milking system is fantastic. There is nothing overly technological in the new shed – our emphasis was on creating a dairy which would be pleasant to work in and highly efficient.
“With the dairy operational we are now turning our attention to the layout of the farm, which spans both sides of the road. Currently things are scattered – for example, feed storage with maize, grass silage and PKE in three different locations

so, with Paul Wolvers’ help, we are consolidating and repositioning them to the side of the farm with the dairy.
“Long-term we will also widen the entry/ exit race and continue to improve the races and paddock layout.”
The last word goes to farm manager Zac Van Dorstan who, along with 2IC Harley Frazer and farm assistant Ethan Thompson, milk in pairs in the new dairy.
“Every set of cups is in the right place and the lightweight clusters really speed cupping. It’s fantastic, great to work in.”
The farm’s name, Hakin Dairies, comes from a village in Wales where Louise’s grandparents lived and means ‘place at the bend in the river’. There’s a big kahikatea tree on the bend in the river, which runs through the farm and the forbear of the previous owners camped there at the end of World War I in 1919 when he was balloted the farm in 1920.


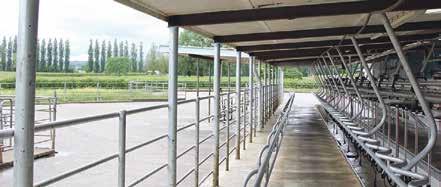

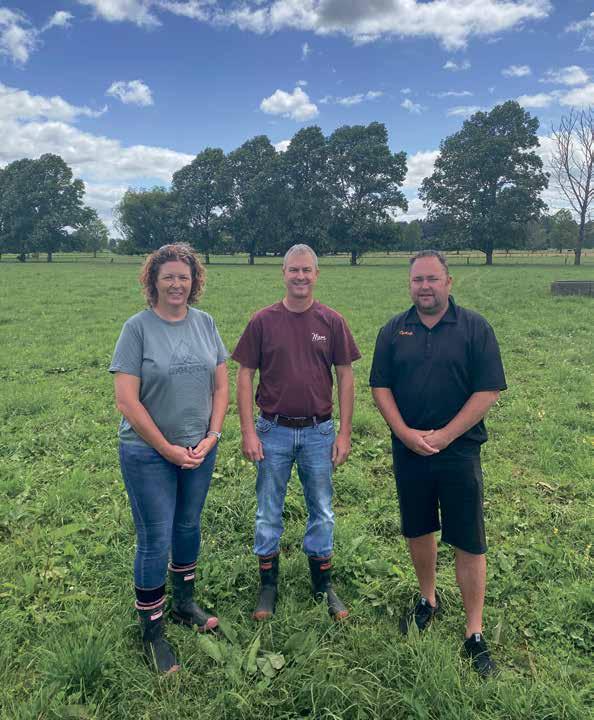
The revitalised interior of the dairy.
The revamped milk room.
dairy to the stone trap –designed by Paul Wolvers.
An old disused yard to the side of the dairy houses the Wrangler cattle crush.
No frills, highly functional
There are no frills in the new 26-aside herringbone on Aad and Jill de Groot’s farm on the outskirts of Morrinsville. And that’s how it’s meant to be – a highly functional environment which facilitates smooth, efficient and fast milking, minimising the time cows spend standing on concrete.
Aad de Groot emigrated from Holland in the early-1980s after growing up on a small dairy farm, attending agricultural college before compulsory military training. “I had Dutch friends who were farming in the Waikato and a short visit with them was enough to convince me that I wanted to make New Zealand my home.”
Initially Aad was a farm worker before progressing through the ranks becoming 50/50 sharemilker with wife Jill on a 35ha farm on Gibbon Rd, Morrinsville. The couple subsequently purchased the farm in 1995.
“The Gibbon/Roache Rd area, like much of the Waikato, was made up of small [by today’s standards] farms and so, in subsequent years, we were able to purchase neighbouring farms as
they came on the market – in 2003 an adjoining 34ha and, recently, a 35ha farm on the back boundary of the farm, which we had leased for 10 years.
“The combined farms are now run as one. A total of 105ha milking 280 crossbred cows, farm system 2 with cows averaging between 400kgMS and 450kgMS per cow and all young stock reared on-farm,” says Aad.
Until 2023 the herd was milked in two mobs through an old 18-aside herringbone on the block they purchased in 2003. Aad says they had “some subsidence under the vat stand which necessitated a new stand, but overall the shed was tired and needed replacement”.
With son Andrew and wife Vivian managing and contract milking, Aad and Jill decided to build a new dairy to provide a more functional environment. “Cow numbers supported our decision to stick with a slightly larger basic 26-aside herringbone with the ability to add technology in the future.”
Initial thoughts were that the new shed would be constructed on the site of the old shed because it occupied the highest point on the farm to optimise drainage and effluent runoff.
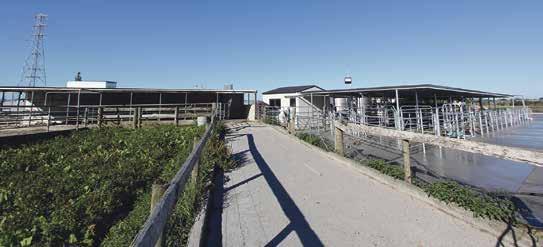
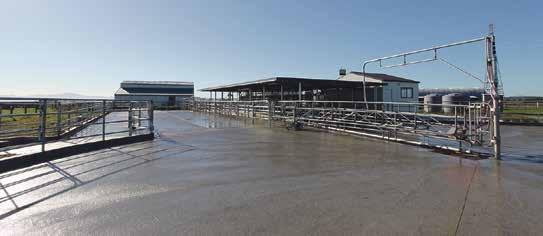
Normal rhythm
“However, building on the same site compressed and potentially compromised the building process,” says Aad. “As the old shed would have to be demolished and the new built while the herd was out, so we decided to develop the land beside the old shed, enabling us to maintain the normal rhythm of the farm while the new shed was being built.”
Aad approached local builder Rob Broomfield of Broomfield Construction. “I’d seen some of
the sheds he had built and his workmanship is great. Rob takes a personal interest in every job, he’s on-site and I appreciate that connection and attention to detail,” says Aad.
Rob Broomfield says Aad wanted a simple, functional shed. “I had built one with a dairy similar to what he wanted in the district so he could satisfy himself that it would meet his needs before we refined the plan.”
Site development was undertaken by Paul Steiner in April 2023. Paul says he “brought in
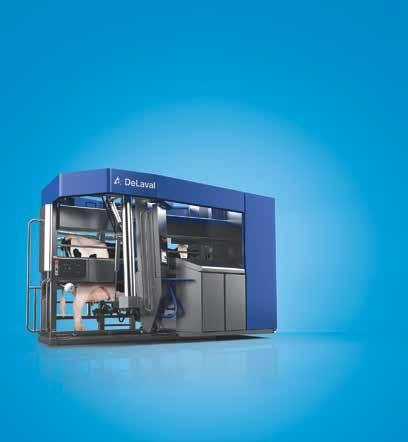




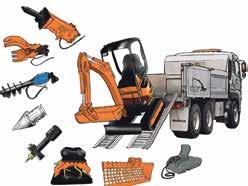

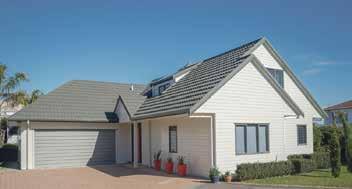

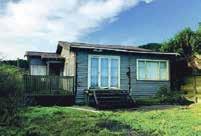
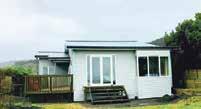

The new collection yard comfortably holds the entire herd which, thanks to faster milking, spend less time standing on concrete.
The new shed on the right was built adjacent to the old, on the left.
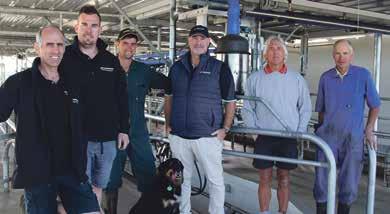
truckloads of brown rock to raise the site for the new shed and yards finishing with a layer of sand”. “We also dug out the new pit ready for the builder.”
Refined yard layout
Edwin Meek, co-manager of Leask Engineering, says they worked with Aad and the builder to refine the yard layout which, due to a delay in demolition of the old shed and yards, required temporary draft pens and exit race.
“We fabricated and installed all the herringbone steelwork, pit step rails, pendulum exit gates, platform entry gates and all livestock handling equipment and facilities to promote optimum cow flow. This included a 10m circular yard with water boom and backing gates – one gate fitted with a wash system – AI and vet races.
“Aad initially wanted overhead piping for wash water in the pit but we convinced him that it would be more efficient for it to be channelled through one side of the pit steps – and he really likes it.

“In relation to the temporary exit yards, we constructed two small pens either side of the exit race until the old shed and yards are dismantled. Then the exit race and drafting yards will be extended,” says Edwin.
Excellent cup alignment
McGregor Farm Services, based in Morrinsville, supplied and installed the DeLaval milking machine.
McGregor’s managing director Daniel Peake says the DeLaval Midiline reinforces that DeLaval’s quality and innovation covers the spectrum – “from simple and efficient, to high-tech and efficient”. “The great thing is that the bridge between the two is achievable and cost effective. If, at any stage, Aad or Andrew want to add technology, it’s simply a matter of retrofitting.
“The dairy has great cow flow, the cluster droppers enabling excellent cup alignment.”
Morrinsville-based Silvester Electrical installed a new mains cable to the old shed two years ago. Graham Silvester says




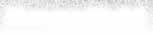
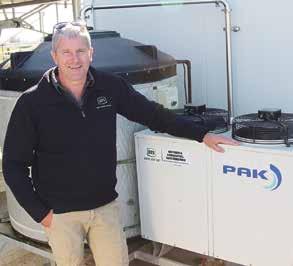
this necessitated a temporary cable to supply power to the new shed during the build.
Once the old shed was decommissioned a generator was used for a few days before the mains was redirected to the new shed.
Silvester Electrical did all electrical wiring for the new shed including water and bore pumps which had to be changed over on the same day – so, one day working in the old shed, next day in the new.
When it came to refrigeration in the new shed, Aad and Andrew were able to harness the existing DTS ice bank in the old shed for pre-chilling.
DTS Waikato and Bay of Plenty regional manager Lawrence Kerr says addition of a second vat called for a new stand-alone refrigeration unit to prioritise the supply vat and keep the calf milk vat cold.
“The DTS ice bank is extremely efficient, minimising power usage while ensuring milk is consistently chilled to around six degrees Celsius as it goes into the vat,” says


Lawrence. Work on the new shed started in April 2023. Aad recalls that with no tight deadline for the new dairy to be completed, he and Andrew were able to milk in the old shed until the new build was commissioned on October 25, 2023.
Very happy
“We milk in two mobs – younger cows and older cows – twice-a-day to end of December and then once-a-day with the young cows. I milk with Andrew in the mornings, mainly to drench the cows for minerals.
“We ran both mobs through the new shed before it was commissioned so when it came to the actual change-over they settled reasonably quickly.”
Andrew de Groot says he and his father are very happy with the new dairy. “The improved cow flow and overall efficiency enhancements means faster milkings, so the cows aren’t standing on the yard as long as they were before.”



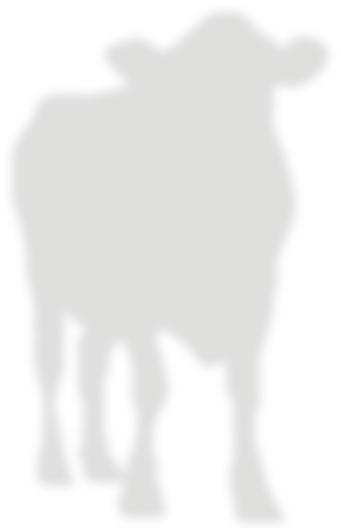

Clare Bayly
ACM & LJ de Groot Ltd ACM & LJ de Groot
The spacious interior of the new dairy.
Leask Engineering’s Edwin Meek and Chris Foster, Andrew de Groot, ‘Flax’ the dog, DeLaval’s Cory Duckworth, Silvester Electrical’s Graham Silvester and Aad de Groot.
Lawrence Kerr of DTS with the DTS ice bank.

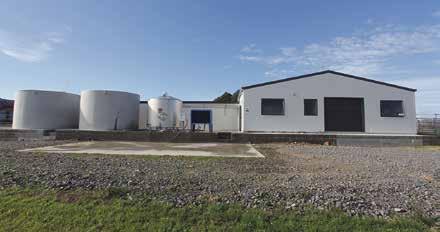
Evan’s farm evolution
Evan Dela Rue admits he considered a number of sites for a new dairy on his Ohaupo farm before builder Shanan White, who is builder and managing director of Don Chapman Waikato Ltd, identified what turned out to be the perfect spot.
“At the time the land was covered with large macrocarpa stumps – the remains of 100-year-old trees which had probably been planted when the farm was originally developed.
“After one falling over during a storm and taking out half of the hay barn I decided to mill the rest of them, leaving only the massive stumps behind.”
Evan has been farming the 61ha property since 1959 initially as a 29 per cent sharemilker with a friend before purchasing it in 1969.
Walk-through origins
“When I first came here, my mate and I milked 180 cows through a six double-up walk-through shed which I converted to a 12-aside herringbone in 1974. At that time we also ran a large number of pigs.
“A few years later, after purchasing adjoining land and increasing the farm to 83ha, I extended the milking shed to 18-aside,” says Evan. “It was a pretty good shed for its day but was worn out after 50 years of milking.
“I’ve had sharemilkers on the farm for the past 20-plus years and wanted to build a new dairy to futureproof the farm and provide them with a
modern efficient herringbone to work in.”
Once the stumps were removed the building site was cleaned and raised with sand and clay, with the build starting in November 2022.
Don Chapman Waikato Ltd designed and built the new 24-aside herringbone dairy for Evan Dela Rue. Evan was really impressed with the way they designed and built the dairy on his son’s farm at Eureka back in 2014.
Shanan White, managing director of Don Chapman Waikato, says Evan wanted a one-man shed that was easy to run and sized to handle his 250-cow herd in 10 rows, which meant a 24-aside dairy setup.
Different layout
Evan and Shanan worked together on different shed layout options to find one that would ensure smooth cow flow and easy access for milk tankers, while also considering the prevailing weather conditions.
“As with most of our newer builds, we included an AI facility and a vet race with a head bail. The basic design was similar to Evan’s son’s shed, but we made some tweaks to fit the site and Evan’s specific needs as well as integrating the latest improvements in shed design and construction that Don Chapman has developed over the past decade.
“Our contract covered everything from the concrete and erecting the building to installing walls, roofs, drainage, pipework, rails, gates, and doing interior painting. We also prepared the





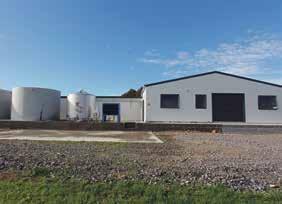
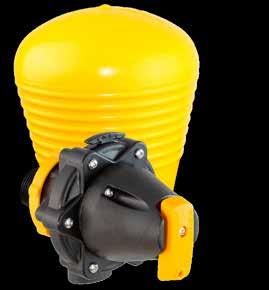
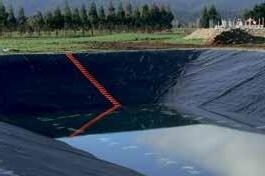
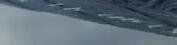
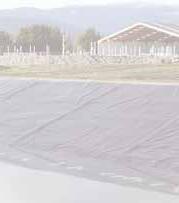
Congratulations to the Dela Rue family on their outstanding new dairy shed.
The new 24-aside herringbone was designed and built by Don Chapman Waikato Ltd.
Farm dog ‘Pup’ with sharemilker Jake Thomson and farm owner Evan Dela Rue in front of the new dairy.
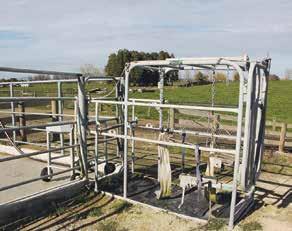
building for the milking, refrigeration, and water systems, and coordinated with electricians,” says Shanan.
As part of their contract, Don Chapman Waikato engaged Leask Engineering for the installation of pipework, rails, and gates, leveraging their extensive 30-year partnership.
Edwin Meek, co-manager of Leask Engineering, says the company has a 65-year history of building and installing animal handling equipment. “We take pride in constantly re-evaluating and innovating to deliver exceptional animal handling facilities.
“Leask Engineering provided and installed the herringbone steelwork, pit step rails, platform entry gates, backing gates with a yard washing system, exit races, holding facilities, AI and vet race setups, along with a Leask headbail,” says Edwin.
Digital pulsation
Qubik Te Awamutu supplied and installed the 24-aside Waikato Supa4 midline swingover system which creates maximum room in the pit while maintaining perfect cluster alignment. The milking plant includes
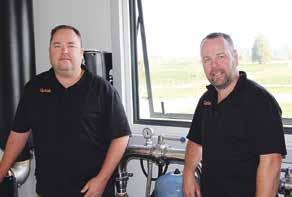
SmartPULS pulsators, a top loading maxi filter, double-bank plate cooler, Qubik milk pump controller, 1.5KW Fristam milk pump and aBP200 Vacuum Pump with SmartDRIVE.
SmartPULS pulsators – which are a digital pulsation system designed to produce accurate results time and time again –were installed. The solenoids inside the pulsators are smaller and have a greater life expectancy, exceeding 200 million cycles.
A Glacier Plus 20kw water chiller chills a 25,000 litre underground concrete tank of water to six degrees Celsius outside milking time. During milking, water is circulated through the second stage of the plate cooler reducing milk temperature to 7-10 degrees Celsius before entering the milk vat. A heat recovery unit complements the water chilling system, with hot water entering the hot water cylinders at a rate of two-three litres per minute at a temperature of 50-60 degrees Celsius dependent on incoming water temperature. An 8hp DX unit was installed for vat refrigeration.
Steel pipework
The dairy’s water system has stainless steel
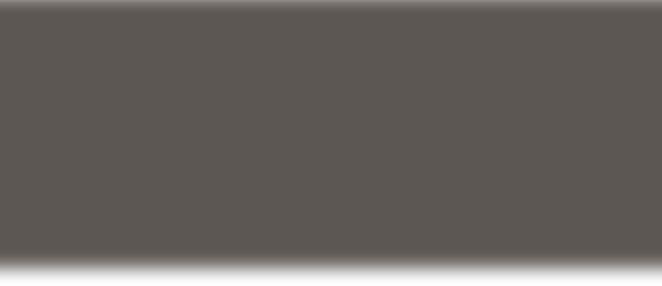

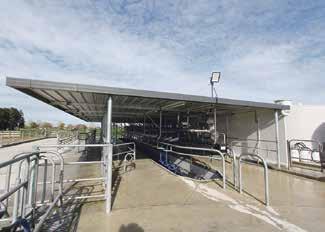
pipework above and below the ground. The water pumps comprise a plate cooler pump controlled by pressure tank system and washdown pump with a Variable Speed Drive. Hot water cylinders sit on a custommade stand alongside a 350 litre stainless steel jetter tub from Qubik’s fabrication division.
The effluent system was connected to a new lined effluent pond constructed below the dairy and the existing effluent pond pump and pontoon were re-used to irrigate to pasture.
Jake and Alana Thomson are about to start their fifth season as 50/50 sharemilkers on the farm located equal distances from Hamilton, Te Awamutu and Cambridge Jake says: “Evan involved me in a lot of aspects of the build, which I appreciated – including the milking system, auto plant wash, cup removers and lightweight clusters”.
“Alana had carpel tunnel syndrome and these lightweight clusters are fantastic, easy to handle and reduce the risk of a recurrence.” Jake also personally added rubber to the floor of the pit for cushioned footing during milking.
Dela Rue Dela
The new dairy was commissioned on July 22, 2023, with Jake saying they started calving in the old shed. He says not having to transfer any gear from the old shed to the new meant that the minute the new dairy got approval, they simply started milking there. “It was very simple and, looking back, very straight forward.
“The cows settled relatively quickly to the new environment, and I believe the yard layout and light and bright interior were significant factors,” says Jake.
“It is very easy for one person to milk in this dairy, each milking taking around 90 minutes plus washing up.”
‘Doing things right’
Many of the original farm buildings remain standing and functional on the Dela Rue farm, which is testament to ‘doing things right’ and also providing tangible evidence of the progress in farming efficiencies.
Evan says when he looks back at what they coped with in the early days, he can appreciate the scale of improvements which have taken place over the years – many evident in the new dairy.
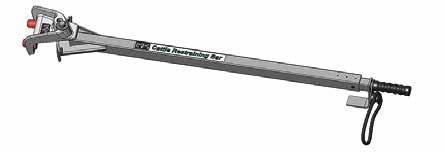
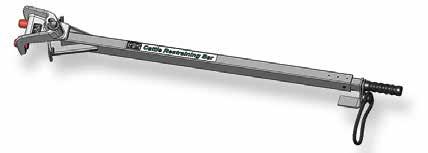

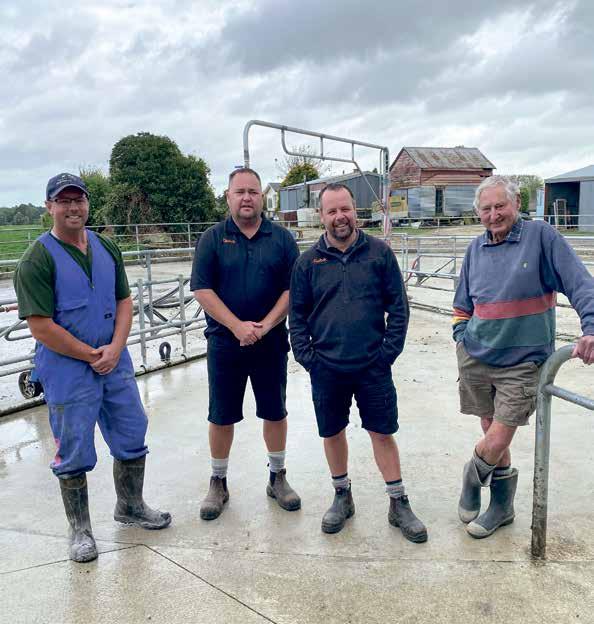
Clare Bayly
The dairy’s roof extends over and protects the animal handling and AB race.
Qubik Te Awamutu’s Jeremy Collett, and Kyle Osborne.
An existing Wrangler cattle crush has been repositioned in one of the three drafting pens.

More family and farm time!
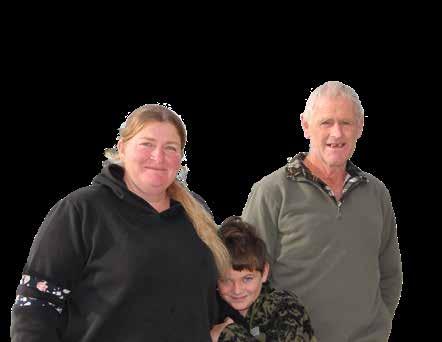
The Thompson family moved to Waikato in 1875 – their place in history recorded in the name of the road.
Brett Thompson is the only member of the family still dairying in the area. Originally a 92 hectare block, the farm was divided between Brett’s father and his two brothers. Brett eventually purchased one of his brother’s blocks and then half of the home farm in 1997.
Braedene Jersey Stud began breeding pedigree Jersey cows in 1973 and today, Brett and his niece Amy milk 300 cows many with bloodlines dating back to those early days.
The old dairy on the farm was a 16-aside herringbone built in 1997 and Brett recalls the frustration of spending more than six hours every day in the shed milking. “That’s a big slice out of every day, so reducing that was the main driver to replacing the shed,” says Brett.
One-person shed
“I wanted a one-person shed, and a rotary with all the bells and whistles enables that. We estimate that with the technology employed in the new shed, each milking should take around one-and-three-quarter hours all up – ie. from the time we walk in till we turn off the lights.
“Even in the peak of the season we’ll halve
the time we’ve been spending milking –allowing more time for other work on and around the farm. The investment in the new dairy will have a significant payback in quality of life.”
The new dairy is a 40-bail Waikato Centrus rotary with auto drafting, mastitis detection, auto cup removers, bail restraints, in-shed feeding and a herd management system that records everything from percow production, through to liveweight, feeding and reproduction.
“I wanted all the bells and whistles – as much technology as possible – to simplify and speed up each milking, ensuring consistency and high standards.”
Brett anticipates per-cow production will
improve in the new dairy. “In the past, minimising time in the shed was a priority so we didn’t focus as much on production as we will now.
“With time pressure off – ie. reduced time in the shed and the high level of individual cow and herd information the shed will generate – we’ll be able to focus on percow production more than we’ve ever been able to.”
No going back
The shed was nearing completion when New Farm Dairies visited. Brett says: “It has to be up and running for when we start calving on or before July 10”. “The old shed’s been decommissioned – it’s been

Manage your winter feed effectively with our Weighlog Alpha10 on-board weighing system designed for telehandlers or loaders. Gain precise insights into your feed distribution to avoid unnecessary overfeeding for better feed management. a a RDS SYSTEMS LTD ., ,, a Phone Nev on

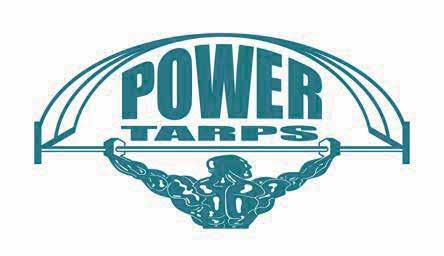
POWERTARPS ARE NEW ZEALAND’S LEADING RETRACTABLE TARP SUPPLIER
We specialise in high quality, mesh and PVC covers to suit trucks, trailers and farm bunkers. All of our covers can be easily operated from the ground using a silky smooth cable system, eliminating health and safety risks.

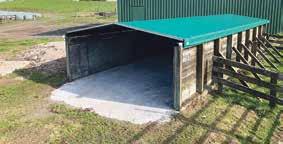
Te Awamutu Construction’s Andrew Smith is proud to have been part of building a beautiful and highly functional dairy.
Brett Thompson says the new dairy futureproofs the farm for more generations of the family – including niece Amy Yates and, hopefully, Amy’s eight-year-old son Blake.
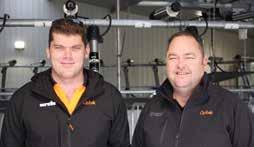
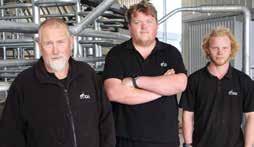
gutted so there’s no going back.
“It will be a big transition for the herd to go from the small 16-aside herringbone to the rotary so we’ll run them through the new dairy a few times before they calve.
“They’re a quiet herd but we know it’ll take a few milkings before they settle down to the new environment – in-shed feeding will help, so the biggest challenge could be getting them to back off the platform!”
The site for the new dairy was pinpointed “years ago” – within sight of the old shed. Brett says they’ve been “talking about building a new shed for around five years” so when it came to replacing the old effluent pond etc they were able to position the new one between the old and new sheds.
The only thing we’ve moved from the old shed, which will be converted to a calf shed, are the chillers.
Earthworks to develop the building site commenced March 2023. Te Awamutu Construction designed and constructed the new dairy. The only change to the standard design was to extend the roof over the Wrangler, and bail entry and exit.
Treated timber walls
Te Awamutu Construction owner Andrew
Smith says the dairy’s walls are 6 by 2 treated timber, wrapped and insulated with low rib steel cladding. “This creates a better looking shed than freezer panels as all the pipes and wiring are within, and not external, to the walls.
“It makes the dairy easier to keep clean and maintain,” says Andrew. The dairy’s roof is long run coloursteel with Te Awamutu Construction’s vent, which lets light in and gets rid of heat from the cows in summer.
“We prep all concrete and have contractors come in and lay it; we’re there from start to finish.
“We also built a lean-to on the outside of the dairy to house compressors and chemicals and designed and custom-made office fittings so Brett has the option of a standing desk – where he can also look into the dairy – or seated. It’s a great shed, and we’re very proud of it,” says Andrew.
More rollers
The 40-bail rotary platform was installed by Moa Rotary Platforms in October 2023. Waikato area manager Shane Arthur says the platform has more rollers than conventional to distribute the weight of the deck. “It’s very low maintenance with a
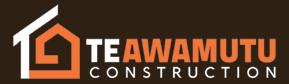
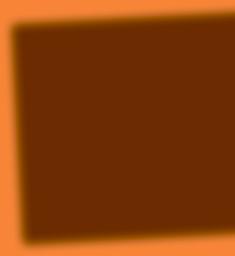
“Effluent
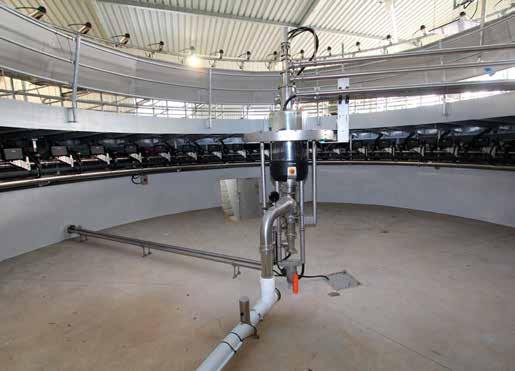
grease set which lasts for six months.”
Qubik advised, supplied and installed the milking, effluent and water systems for the new dairy.
Qubik’s operations manager Jeremy Collett says Brett’s brief was to incorporate every technology – “and we did”. The dairy is fully automated with light weight clusters with no shut off, cup removers, bail marshalls, electronic bail gates, automated drafting, milk cooling and recovery and a full dairy ID system.
“On the water side, again, everything is automated – cluster, platform, face spray and vat wash with automated teat spray. Stainless steel handrails were made by Qubik’s fabrication division. The dairy also features a Qubik infeed system.
“We also connected the existing effluent
system, which we installed two years ago, across from the old shed to the new dairy. Qubik did all water and effluent, connecting to the existing system, pumps and auto vat wash. Everything else is pretty standard – washdown pump with Variable Speed Drive, stainless steel pipes underground, platform wash, face spray, auto teat spray and stainless steel handrails made by Qubik’s fabrication division.”
More time
With weeks until calving starts, Brett accepts that – for the herd and himself –the new dairy will be “quite an adjustment from what we’ve been used to”. “But I’m looking forward to freeing up so much of each day to spend more time around the farm, and with family.”


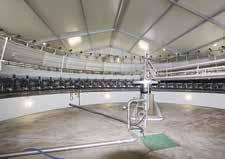
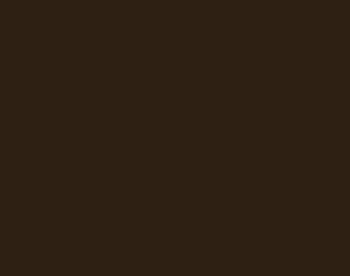

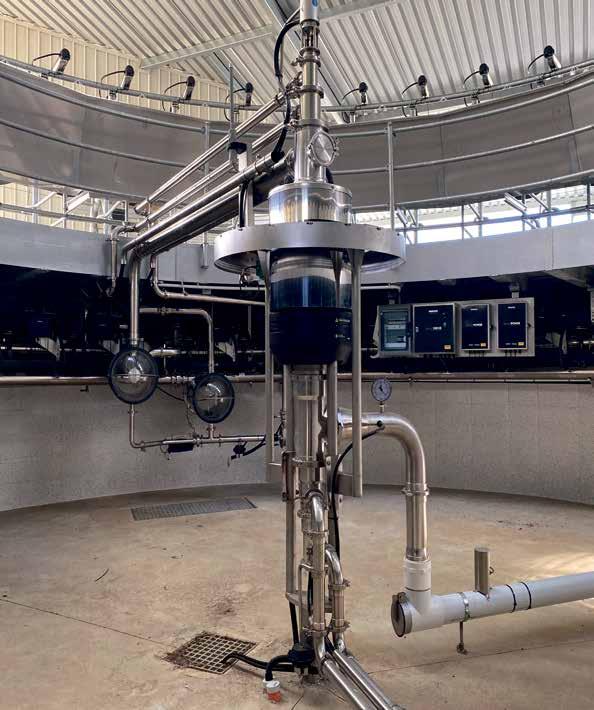
made easy”
Clare Bayly
Qubik’s Liam Cook and Jeremy Collett say the dairy is a showcase for everything Qubik does.
The Moa team: Shane Arthur, Joe Bradly-Arthur and Callum Jarvis-Hall.
The centre of the dairy.
Thompson
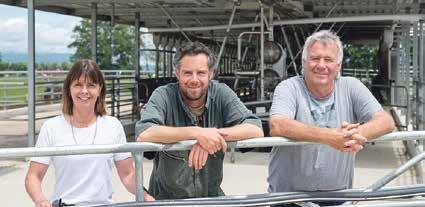
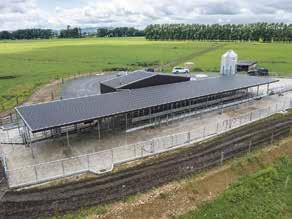

the fifth generation
Cambridge farmers Donna and Lindsay Barton are still milking the descendants of Donna’s greatgrandfather’s Jersey herd established in 1906.
In fact, Donna says Beechlands Jersey Stud is the oldest Jersey stud in New Zealand.
The Auckland-based Beechlands herd passed from Donna’s great-grandfather to her grandfather and then to her uncle where they ended up in Roto-o-rangi, Cambridge.
It was from there that dairy farmer
Lindsay Barton bought the herd in 1985 and met Donna. Self-confessed “absolute townie” Donna married her farmer in 1987 and became the fourth generation of her family to own the Beechlands Jerseys.
Today the couple own two dairy farms and are actively involved but have a farm manager on the 127 hectare farm that they have more to do with. This farm has mainly Jersey cows with the 460-strong herd producing only A2 milk.
Their son Trent and his wife Ashley contract milk on the other 85ha farm,
milking 300 cows of which around 60 per cent are purebred Jersey, and the rest are KiwiCross.
They are the fifth generation to farm with the Beechlands Jerseys. The couple’s other sons are diesel mechanic, Liam, and refrigeration technician, Kurt.
Time to upgrade
On the farm Trent runs, the herd is grass fed with 2-3kg of supplement fed daily.
“I would say we run a production system 3 and feed the cows in-shed,” says Trent. “We also grow 4ha of maize and cut silage.”
An above-ground 1.4 million litre effluent tank was built in 2020, and around 25ha of the flat farm is irrigated using a travelling irrigator; and slurry is applied to some paddocks, blown from a tractor-pulled tanker trailer.
The cowshed on that farm was an old 14-aside herringbone – probably built in the 1970s.
“We extended and upgraded to 20-aside in 2002 and we were going to add on again, but the roof was looking bad and the pipework was starting to rust,” says Lindsay.
The family decided to start from scratch and build a modern shed, with the attitude of: ‘If you’re going to do
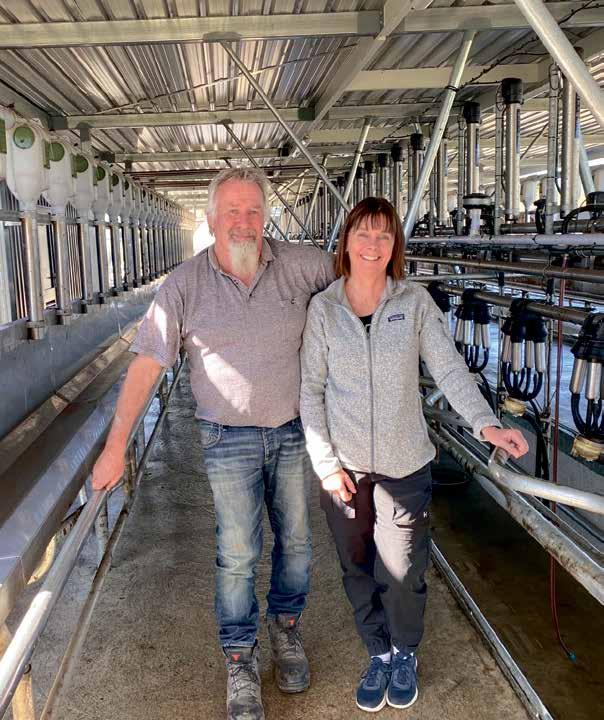
it, you may as well do it properly and futureproof as much as possible’.
Their first point of call was TA Construction, which is now fully owned by Andrew Smith. Ex-owner Pat Gibson was still involved, and the Barton’s shed was the last one he planned and built.
“They were great,” says Lindsay. “They have built numerous sheds and took us to see a similar one before we decided to go ahead and that was really helpful.”
Qubik was engaged to work with the Bartons to plan the plant they wanted for the new 30-aside herringbone.
The build
“Once we gave the green light, everything moved very fast,” says Donna. “We dried the cows off mid-April 2023 and had three months before calving started.”
Qubik removed the old plant, and the electricity and water were disconnected before Haveman Earthworks demolished the old building and prepared the site. Haveman Earthworks owner-operator Chris Haveman has been carrying out work for Lindsay and Donna for the last seven years. “We demolished the site and most of the steel and iron was recycled,”
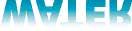

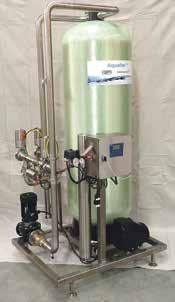
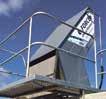
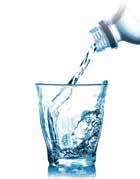
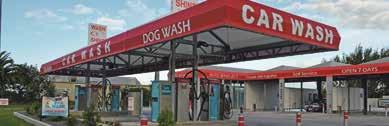
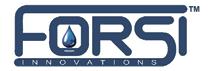
Stainless steel feed bins for the in-shed feeding system.
A new dairy shed to replace the Barton’s 1970s one.
Donna and Lindsay Barton with their son Trent, in the centre, who contract milks on the farm.

says Chris. “The new metal and sand base had a larger footprint to accommodate a covered exit race to house the electronic drafting exit system and auto teat sprayer.”
The soft brown rock entry and exit races were also widened and gently sloped up to the height of the new shed floor to eliminate any stepping up into the shed or stepping down to exit by the cows. The tanker track loop was re-formed and widened to meet Fonterra specifications. “We carried out all the concrete work, block work for the pit, buildings, and railing installation,” says TA Construction owner Andrew Smith. “We were challenged by wet weather, which combined with the already soft peat required us to drive piles between 3.6 metres and four metres deep for the main shed structure.”
The concreting included a round yard, silo pad, vat stand and tanker pad. The new buildings consisted of the 30-aside herringbone shed, plant room and an office, which covered a 314m2 footprint.
TA Construction fitted newly-fabricated yard and pen railings and made-to-measure backing gates.
The Bartons used some key pieces from their old
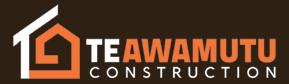
plant in the new shed as well as new equipment too. After milking the cows now walk through a covered exit race over the new automatic teat sprayer. They then pass through the re-installed electronic collar drafting system to leave the shed.
The two new feed silos take 16 tonnes each.
Lindsay says that takes a truck and trailer of feed, which means deliveries are fewer.
‘Must haves’
A Qubik in-shed feed system was installed using 1.2 millimetre stainless steel feed bins with seamless welds, overlapped for strength. Pneumatic air rams were introduced to deliver a slow and steady release of the meal through durable stainless steel droppers.
This also eliminates repetitive strain injury on workers’ shoulders for health and safety purposes.
Feeding like this allows every cow in the herd to have access to the same amount of feed, and individual feeding is far more cost-effective.
“Our ‘must haves’ included AI/vet holding pens within the yard to draft off and hold cows. We made sure that the roof extended over the pens so they were undercover,” says Donna.

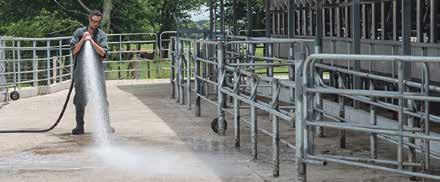

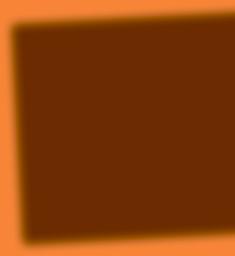

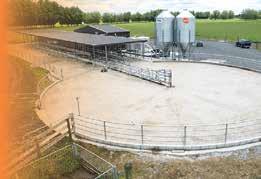
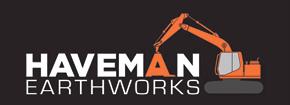
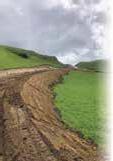
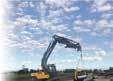
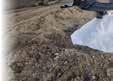
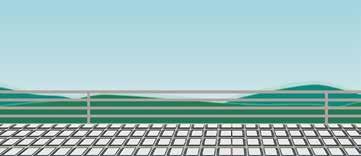
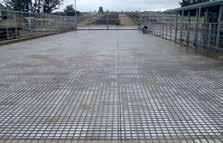
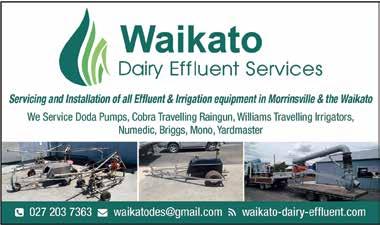
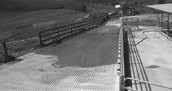


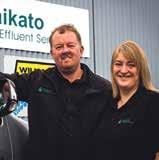
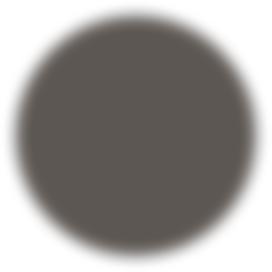

The new 30-aside herringbone dairy at the Roto-o-rangi farm of Lindsay and Donna Barton.
Lindsay and Donna Barton, Qubik’s Nick Heffer, and Qubik Te Awamutu branch manager Kyle Osborne in the new parlour.
A bird’s eye view of the new dairy shed.
Trent Barton using the new washdown system.

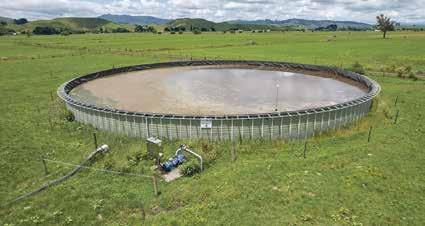

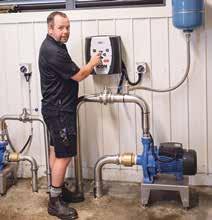
“Another ‘must have’ was a loading ramp in the yard. We use electronic drafting collars, so the ability to draft and hold in the yard then load cows straight from there has been a real convenience.”
New tanks
“We have two new 25,000 litre above-ground plastic water tanks and a new 18,000L in-ground concrete tank with a new Qubik pre-cooling water chiller unit,” says Lindsay. New pipework was fitted throughout. The farm’s water is from the Pukerimu Water Scheme.
All effluent is channelled into a sump initially where solid matter is trapped and the liquid is pumped to the three-year old Kliptank 1.4 million litre, above-ground effluent tank.
Kliptank owner Kim Henderson carried out an analysis of the tank requirements with the Bartons. “Amongst other things we look at cow numbers, the proposed location of the tank and the rainfall in the area,” says Kim. “We are the only tank providers in the country that can install on peat.”
The foundations are put in during the dry season with a base of crusher dust. Kliptanks don’t need a concrete base and their PSI pressure on the ground is very light.
The Bartons chose to install a Klipjet stirrer/ aerator to keep the effluent moving and fluid. Washdown can either use recycled green water from the effluent tank or fresh water. The round yard is fitted with sprinklers to keep the waiting cows comfortable in hot weather.
Plant features
Qubik installed a Supa4 30-aside heringbone plant with some particular features that the Bartons wanted, which increased the bail numbers and milking efficiency compared to the old shed.
“It’s a larger shed and we fitted it accordingly,” says Qubik sales specialist Nick Heffer. “Qubik installed the Waikato SmartPuls system that provides rippled pulsation for excellent vacuum
stability, gentle milking and quiet operation with customisation to suit the herd.”
The BP400 Blower Vacuum Pump is perfect for the larger dairy and when operated by a Variable Speed Drive it quietly performs while maintaining accurate airflow on-demand. This pump doesn’t require oil or water to operate.
Automatic cup removers were a ‘must have’ and the ECR-S Cup Removers reduce labour, improve efficiency and ensure milking consistency.
“The new washdown pump has a Variable Speed i-CON drive, which eliminates the need for large pressure tanks and switches and can supply constant pressure water without manual operation once the parameters are set correctly,” says Qubik Te Awamutu branch manager Kyle Osborne.
G2 Jetter cluster washers ensure the milking clusters are thoroughly cleaned after milking. The installation of a WalkoverSPRAYER teat sprayer in the covered exit lane sprays the cows’ teats as they leave the dairy.
“At normal walking pace the teat sprayer automatically deploys two spray nozzles to accurately spray all four teats. It detects if the cows are moving faster and deploys all four nozzles,” says Nick.
The milk filtration uses the Maxi milk filter, which was built for larger dairies and has a superior top loading enclosure and has been designed for ease of use and quick assembly.
An efficient team
Lindsay describes the initial teamwork between TA Construction, Qubik and Haveman Earthworks as “very efficient and everything was gone in under a week ready to start the build”.
The new shed was up and running for calving and the Bartons were pleased with the outcome and efforts of all involved.
There is a little friendly, family rivalry between Trent and his parents as it’s the farm he is in charge of that has the shiny new milking shed with all the modern conveniences and not Lindsay and Donna’s farm!
SUSTAINABLE LIQUID STORAGE OPTIONS
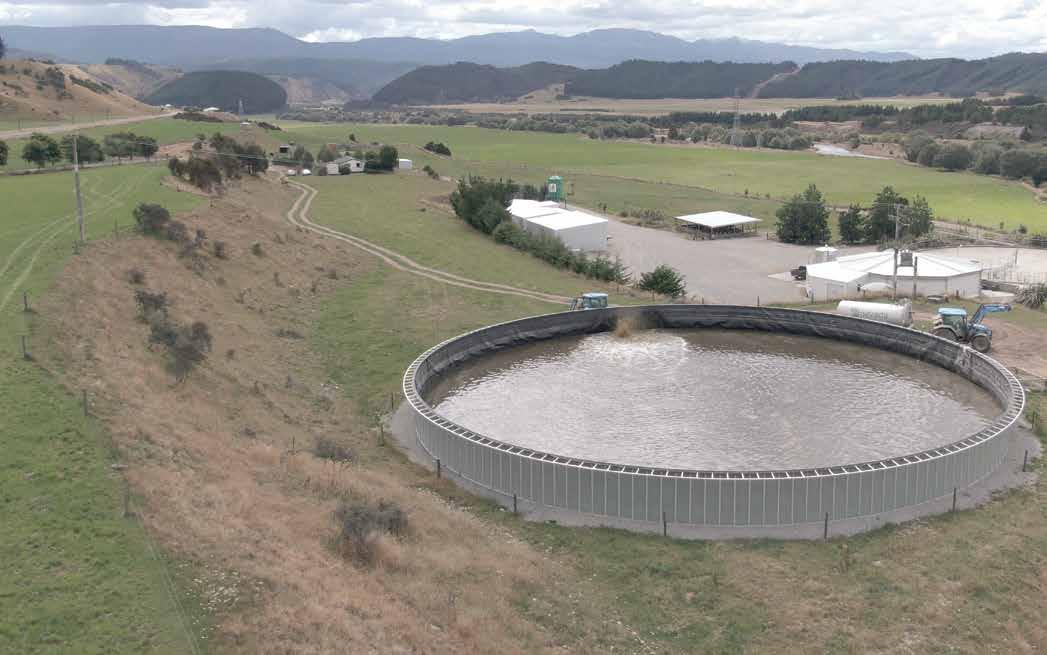
•
•
• Quick installation (normally 3-7 days) 25-year design life
The new loading ramp directly from the yards at the dairy.
Qubik Te Awamutu’s Kyle Osborne, with the Variable Speed i-CON drive.
Kliptank 1.4 million litre effluent tank built in 2021.
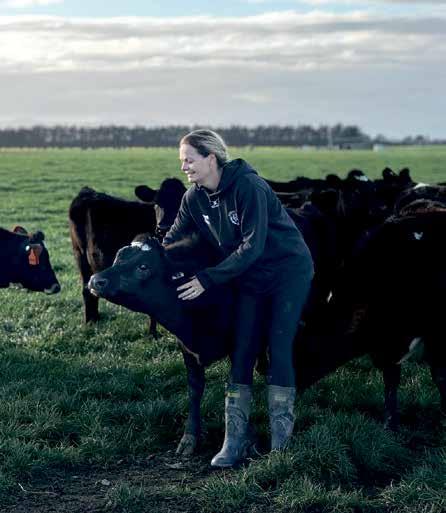
Fit for purpose!

The set-up of the new herringbone dairy on Walsh Enterprises’ farm east of Morrinsville is tailored for contract milking.
Equipped with everything that enhances fast, efficient milking the dairy does not include technologies which Walsh Enterprises’ operations manager Mike Garrud says “are often only variably utilised”.
“Technology tends to be valuable for those who want to use it, but not for technophobes! It’s only as good as the user, so when planning the new dairy our focus was a big, simple, straight-forward shed,” says Mike.
“The pit length and number of cups is factored to the number of cows we are currently milking – at 270 –but we were mindful that we may have the opportunity to add acreage and stock numbers in future, so sized the collection yard to 500 cows. At that point the pit would be extended from the current 30-aside to 40-aside.”
Walsh Enterprises has owned the 100 hectare property since the 1980s. Mike says it was originally two 50 hectare blocks with a functional 15-aside
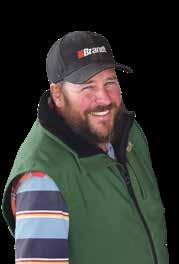
herringbone “which we milked in for a couple of decades but it was at the end of its life”.
Fresh farm layout
“The need for a new dairy provided an opportunity to take a fresh look at the layout of the entire farm and to choose a site which was central, albeit a significant amount of redevelopment of races, paddocks and effluent pond was required,” says Mike.
Paul Steiner Contracting developed the site for the new dairy, new tanker track and farm races connecting the new dairy in addition to a new effluent pond.
The excavated site was backfilled with brown rock and pit sand. The effluent pond was then developed and completed at the start of 2023, ready for Viking Containment to install the pond liner.
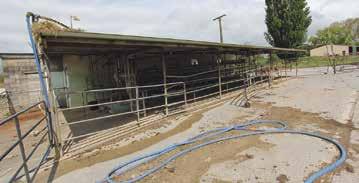
Viking Containment, working closely with AgFirst Engineering Waikato which designed the overall effluent system and installed the 1800m2 HDPE pond liner which has a manufacturer’s warranty of 20 years. The fully-tested liner incorporates a gas venting system and two safety ladders.
AgFirst installed the effluent system which at the pond comprises a stirrer, shore-mounted boom and Wangen positive displacement pump.
AgFirst’s installation technician Morgan Keighley says effluent gravity feeds from the shed through two mega stone traps. “Effluent can easily be diverted to the pond or on-farm irrigation via a weta travelling raingun,” says Morgan. Walsh Enterprises had been operating an AgFirst weta irrigator and pond stirring/pumping system for many years on their other farm and were pleased to adopt
the same system for the new effluent system.”
A safer option than a pontoon, the AgFirst 5.5kw submersible stirrer is easily swung to one side or winched out of the pond. Originally installed at the old shed, AgFirst relocated the pump to its new location inside a shed where it is protected from weather.
Streamlined and quiet
Don Chapman Waikato’s Shanan White says construction of the new dairy commenced early-2023.
“We project-managed the dairy’s construction, building the foundations, laying all concrete and worked closely with Leask Engineering on construction of the yards and gates.”
Shanan says the walls of the dairy are insulated panel and the roof long run

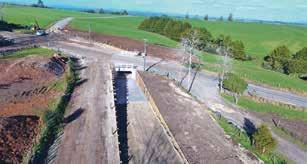

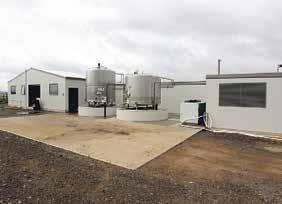
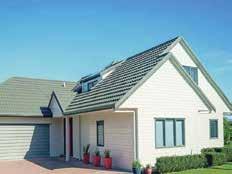



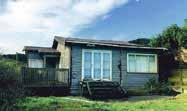

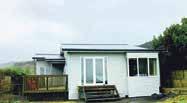

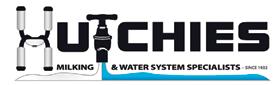
The new dairy.
The old shed is a far cry from the new dairy.
Contract Milker Andrew Ahlers, who milks on his own, says “milking’s a breeze in the new dairy”.
WALSH ENTERPRISES
The futureproofed
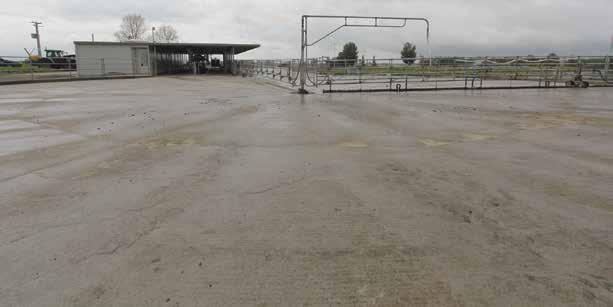
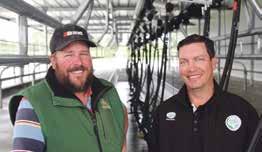
iron. “The pit is wider than standard to accommodate the swing arms and provide plenty of room in the pit. The dairy features a drenching race on both sides providing easy access to the cows.
“The cow entrance and exit to the dairy is also wider than standard to minimise the chance of cows bunching when entering or leaving the dairy. Manual drafting levers in the pit enable easy drafting of individual cows as they leave the dairy.
“The overall design objective was to create a dairy which was streamlined, simple, quiet and a pleasure to milk in. For that reason the pump room is separate – reducing noise in the dairy,” says Shanan.
The new milking system is a Waikato 30-aside Supa4 with swingarm cup removers which create maximum room in the pit for milkers while maintaining alignment of the 320HP clusters that only weigh 1.3kg and are designed for optimum fit and animal comfort.
Installed by Geo Hutchinson & Co, better
The new effluent pond, with the Viking Containment pond liner.
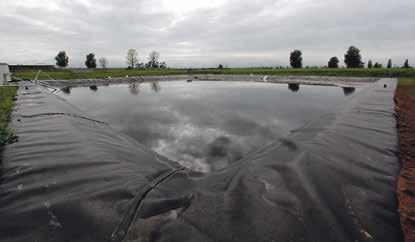

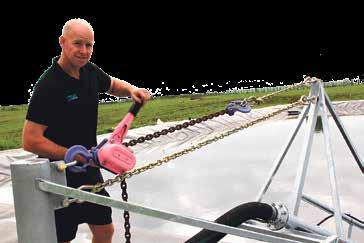
known as Hutchies, the swing arms have an LED light/touch button with the capability of showing eight different colours for selected parameters during milking; these replace the paddle switch to operate the automatic and manual wash modes.
Leask Engineering fabricated and installed the herringbone steelwork, pit step rails, platform entry gates, backing gates with yard washing system, exit races, holding pens and loading ramp along with the AI and vet race with a Camlock Head-bail.
Do it all
Leask Engineering’s site manager Chris Foster says the new dairy features the company’s unique animal handling AI and vet race, which provides a safe, functional environment where one person can “do it all” – load cows, inseminate or provide veterinary assistance, and release.
“For AI, cows stand at an angle and are held in position by a simple locking bar which is easily
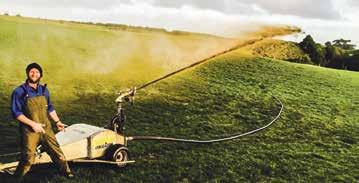
moved. This latches over an adjustable breast rail which can be positioned to accommodate varying cow size. The technician or veterinarian stands in an abutting race with all equipment within arm's reach and when finished activates the unique Leask Engineering gate latch to release the cows,” says Chris.
Dairy Technology Services, known as DTS, was called on – at short notice – to fill the gap left by the originally scheduled refrigeration company and move the refrigeration unit from the old shed to the new dairy.
DTS area manager Dave Gray says despite the tight deadline “our amazing Matamata-based team stepped up to the challenge”.
“Although the refrigeration unit move was not part of our typical inventory, we appreciated the dilemma the farmer faced and understood the need for the unit to be professionally removed and installed in the shortest possible time,” says Dave.
The first milking in the new dairy took place on August 2, 2023. Contract milker Andrew
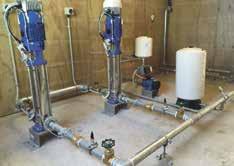
Ahlers says calving had started some weeks earlier with around 150 cows and heifers in.
“I had three additional people on hand for the first few days milking and then one additional person for a week thereafter – but after initially needing some encouragement to go right up to the solid exit gates they soon settled to the new environment,” says Andrew.
“I milk on my own and it generally takes around two hours in the morning – from start to finish – and less time in the afternoon.
A breeze
Andrew says now milking’s a breeze. “I didn’t have automatic cup removers in the old shed and the swing arms create room in the pit.
Additional LED lights mean the whole milking area is bright and the pit step rails make it easy to check cow numbers.
“It’s a shed anyone could milk in – easy to use, logical and highly functional and efficient,” says Andrew.
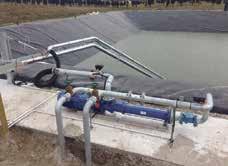
Clare Bayly
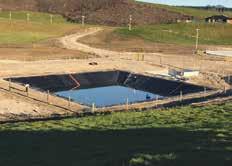
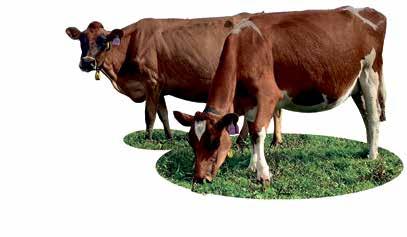
Below: AgFirst’s Morgan Keighley says the submersible stirrer is easily swung to one side or winched out of the pond.
Leask Engineering’s Chris Foster and Edwin Meeke in the new safety-focused animal handling race.
Contract milker Andrew Ahlers with Walsh Enterprises operations manager Mike Garrud.
collection yard easily holds 500 cows.
Walsh Enterprises Walsh Enterprises
No

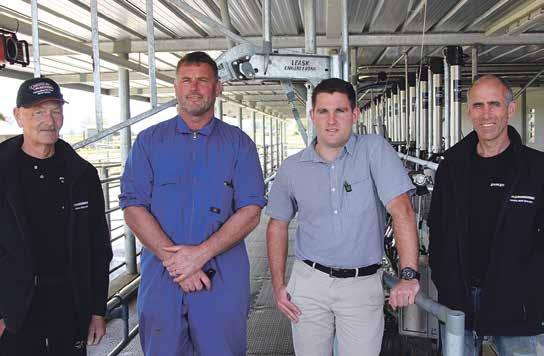
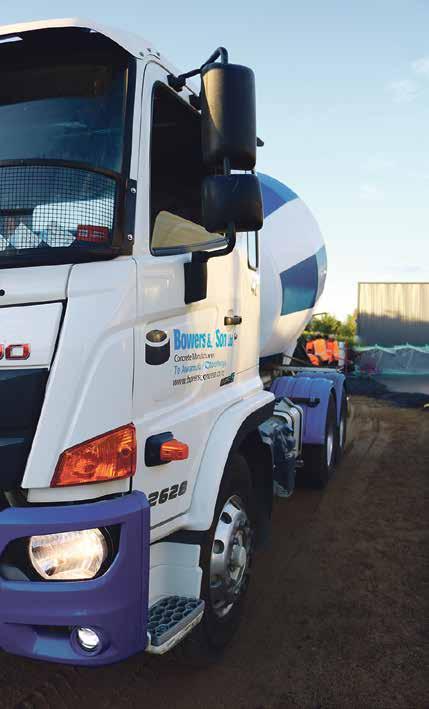
comparison
Cow comfort and health were at the heart of an upgrade to a 50-year-old herringbone dairy on the outskirts of Morrinsville in the Waikato.
The Innes family have been dairying in the area for 51 years. Bryan Innes and sons Craig and Paul are the current generation overseeing a 130ha effective dairy platform. Jason and Angela Wainwright have been lower order sharemilkers on the farm for four years.
“It was originally three farms,” says Paul Innes. “But Dad added neighbouring properties as they became available, ultimately milking out of the most central 38-aside herringbone dairy.
“Rectifying those issues were two of the objectives for the upgrade so, working with Jason – who understood better than anyone the pros and cons of the existing shed – we decided to extend the dairy so it would be a ‘true’ 38-aside herringbone.
“At the same time we would widen the bails and install a zigzag rail in place of the old straight rail so each cow would have her own space. We also decided to build a larger collection yard, which would be covered with rubber matting to provide a cushioned surface for cows to stand on before and during milking.”
In essence the shed was past its ‘use-by date’
“In essence the shed was past its ‘use-by date’ requiring frequent repair and maintenance to keep it operational; we decided to undertake an upgrade in the winter of 2023.”
All the options
Paul says the family considered all the options – including building new in the same or a different location. “But we opted to extend and improve what was already there.”
“The old dairy was originally built to comfortably hold 38 Jerseys per row but cow liveweight has increased significantly over the years and it’s been some years since we were able to fit 38 of our 450 crossbred herd into a row,” says Paul.
“The increased cow size also meant the cows stood at an acute angle with the effect that, on one side, their heads were up against the wall.
Paul recalls the herd was dried off in April 2023, and work began to demolish the old dairy on April 20, 2023 – up to but not including the old milk room and vat stand “which were retained because they were strong and functional”.
40 years plus Shanan White of Don Chapman Waikato Ltd was called on to develop a design for the renovated dairy.
Don Chapman Waikato Ltd, with more than 40 years’ experience delivering turnkey dairy parlours on around 500 farms across the country, was approached to develop a design for the renovation.
Shanan White says through innovation, client experience and new compliance requirements, the company has developed a range of options – for new builds and renovations – which deliver a cost-effective, highly efficient environment for people and cows.
“We had a window of around eight weeks
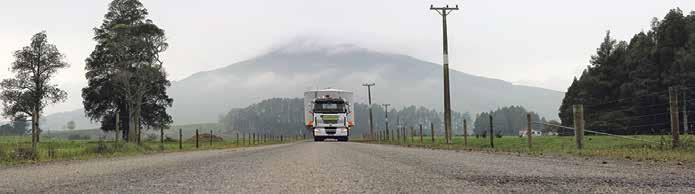
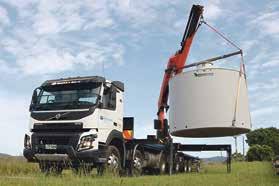
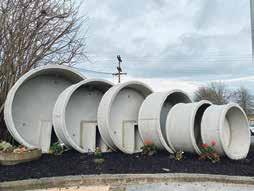
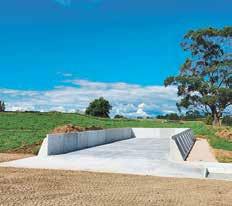
The new dairy is now a true 38-aside herringbone.
Leask Engineering’s Rom Stellingwerf, sharemilker Jason Wainwright, Numat Agri’s Milan Renton and Leask Engineering’s Edwin Meeke.
INNES FARMS
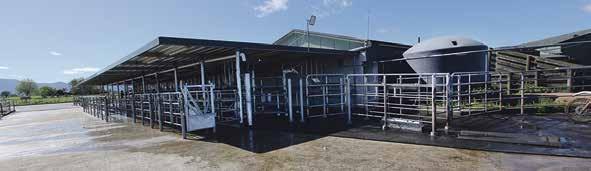
Don Chapman Waikato Ltd project-managed the renovation project to meld old and new in a cost-effective, highly-efficient dairy.
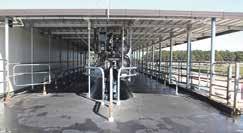
to demolish the yards and shed and get the new dairy up and running for calving,” says Shanan. “Don Chapman Waikato project-managed the entire build but we had a great team of contractors who just got on and got their ‘bit’ done inside the time allowed,” says Shanan.
The zigzag rail and wider bail area means cows are more comfortable.
Cow flow has improved, as viewed at the dairy entry.
Innes Farms
Paul Steiner Contracting demolished the existing yard and bail area – removing the old pit, which was shallow and positioned too close to the wall, and backfilled the site with pit sand ready for Don Chapman Waikato to commence the construction of the extended wall and roof and lay the new yards.
New yards
Leask Engineering, which has more than 65 years’ experience building dairy sheds and installing animal handling equipment, fabricated

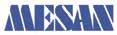


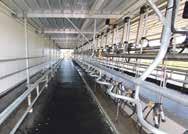
and installed all the herringbone steelwork, pit step rails, pendulum exit gates, all the livestock handling equipment and facilities. This included a 13m circular yard with water boom and backing gates – one gate fitted with a yard washing system –exit races, holding pens, loading race along with AI and vet races with a Leask Camlock Head-bail.
Numat Agri’s Waikato agri consultant Milan Renton says the original dairy had rubber matting in the old collection yard but “over the years it had become degraded due to the concrete underneath breaking up”. “However, the matting remained in good condition so we were able to reuse that, positioning it in the exit area of the new dairy.”
Milan says the renovated dairy – entry race, collection yard, bails and exit race –is extensively covered with Numat Agri’s premium rubber matting. “These mats are

The new roof extends over the animal handling facilities, fabricated and installed by Leask Engineering, include loading, AI and vet races with a Leask Camlock head-bail.

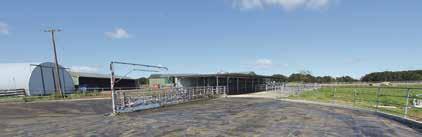
interlocking and 25mm thick, offering a cushioned surface that is easily cleaned.”
All electrical work was undertaken by McMillan Electrical Solutions. Steve McMillan says his team did all the electrical rewiring, installation of the new switchboard, milking machine, lighting, chillers and backing gate controls.
Knock off 45 minutes
Sharemilker Jason Wainwright says the renovated dairy was operational for the start of calving on June 20, 2023, and is “a delight to milk in; there’s just no comparison between the old and new”.
“It took so long to milk in the old shed –basically now, with automatic cup removers and improved cow flow – we can knock off up to 45 minutes at each milking.”
Jason says cupping is much easier thanks to the new pit, which is deeper and positions

milkers at the right level to apply cups and check udder health. “The zigzag rail and wider bail area means the cows are more comfortable, they row up more quickly than before and are milking really well.”
Paul says the family is delighted with the renovation. “It’s all come together really well. We can’t speak highly enough of Don Chapman Waikato Ltd. Shanan White provided fantastic advice and his oversight of the project was a key factor in the shed being finished in the eight-week timeframe.
“Our overall goal when undertaking this revamp was to have an efficient, low-cost, low-impact dairy, which was up to standard, futureproofing the farm. We also wanted to provide Jason with a dairy with the technology and environment he needs to optimise the herd’s potential and to attract and retain great staff.”
Clare Bayly


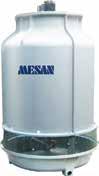
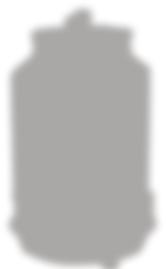
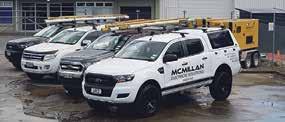





Liz Voorend
P 027 755 6501 | E farmsafety@wfss.co.nz workablefarmsafety.co.nz

Liz Voorend
Liz Voorend
Liz Voorend
Liz Voorend
P 027 755 6501 | E farmsafety@wfss.co.nz workablefarmsafety.co.nz
P 027 755 6501 | E farmsafety@wfss.co.nz workablefarmsafety.co.nz
P 027 755 6501 | E farmsafety@wfss.co.nz workablefarmsafety.co.nz
Liz Voorend LOWEST PRICE
P 027 755 6501 | E farmsafety@wfss.co.nz workablefarmsafety.co.nz
P 027 755 6501 | E farmsafety@wfss.co.nz workablefarmsafety.co.nz
LOWEST PRICE
LOWEST PRICE
The ONLY Health & Safety company that:
LOWEST PRICE
LOWEST PRICE
LOWEST PRICE
The ONLY Health & Safety company that:
The ONLY Health & Safety company that:
Brings the farm up to compliance standard
The ONLY Health & Safety company that:
The ONLY Health & Safety company that:
The ONLY Health & Safety company that:
Brings the farm up to compliance standard
Brings the farm up to compliance standard
Brings the farm up to compliance standard
Organises hazardous substances, safety data sheets, inventory and plan
Brings the farm up to compliance standard
Brings the farm up to compliance standard
Organises hazardous substances, safety data sheets, inventory and plan
Organises hazardous substances, safety data sheets, inventory and plan
Organises hazardous substances, safety data sheets, inventory and plan
Provide easy to use templates
Organises hazardous substances, safety data sheets, inventory and plan
Organises hazardous substances, safety data sheets, inventory and plan
Provide easy to use templates
Provide easy to use templates
Provide easy to use templates
Provide easy to use templates
Provide easy to use templates
Provide on the farm follow-up services
Provide on the farm follow-up services
Provide on the farm follow-up services NO MEMBERSHIP FEES!
Provide on the farm follow-up services NO MEMBERSHIP FEES!
Provide on the farm follow-up services
Provide on the farm follow-up services
NO MEMBERSHIP FEES!
NO MEMBERSHIP FEES!
NO MEMBERSHIP FEES!
NO MEMBERSHIP FEES!


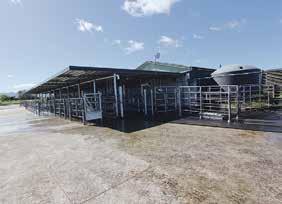

The collection yard, bail area, exit and entrance races are extensively covered with premium rubber matting from Numat Agri.

expectations!
After more than 30 years’ milking, Noel and Debra Hosking happily handed the reins of their 95 hectare Aka Aka farm to a sharemilker – never dreaming that, 10 years on, they’d be back in the pit.
“Debra, and I are the third generation of the family to own the farm,” says Noel. “When the family first came here, the farm was onethird of its current size and was just bare land much of it swamp.
“My parents started building the infrastructure – house, walk-through shed etc –in the late-1940s and they bought neighbouring properties as they came on the market bringing the farm to its current size,” says Noel.
“My parents started off milking around 20 cows by hand through a walk-through shed but as the farm grew, so too did cow numbers. Today we milk 260 cows.”
After three decades milking Noel and Debra opted to put a sharemilker on around 10 years ago. “The old herringbone was nearing the end of its life and a few years ago we began planning a new dairy on a site adjacent to the existing shed – but then Covid came along.
“Our sharemilker deciding to move on fortuitously coincided with our daughter Lisa and her husband Joe and their kids deciding to return to the farm.”
Fresh impetus
The prospect of another generation of the family back on the farm gave fresh impetus to getting the build underway – so Noel bought a digger and began to further develop the building site and races.


on a raised site 1.5m higher than the old shed, with a fall of 250mm to facilitate gravity feed of effluent around the farm or to the existing effluent pond.
“The new site’s adjacency to the old shed meant we were able to continue to use the feed silos we had installed eight years earlier, and to recycle all feed dispensers into the new dairy.
“The greenfields site also gave us the gift of time – for example, the ability to continue milking in the old shed while the new dairy was being built,” says Noel.
Family Farming
“Because we were on or near optimum cow numbers, we opted for a 30-aside herringbone
Specialist earthmoving and site development contractors, GJ Contractors, helped develop the building site. “Developing the new raised site required around 15,000 tonnes of Soft Pit Run metal to be brought in,” says GJ Contractors’ Greg Monteith.
“The first 13,000 tonnes defined the site
NGINEERING EASK
with the balance of 2000 tonnes used to preload, or compact, the site for six months before Don Chapman Waikato began building the dairy,” says Greg.
The new dairy is a Don Chapman Waikato ‘standard herringbone’ proven over more than 40 years by delivering turnkey dairy parlours on more than 500 farms across the country.
Recycle
Don Chapman Waikato’s Shanan White says Noel and Lisa wanted a dairy that would facilitate great cow flow and productivity, while providing the optimum environment for milkers.
“They wanted to recycle a range of items from the old shed, which were in good condition and functional. For example, clips, clamps, clusters and feed dispensers.
“The Don Chapman Waikato team, led by Steve Fowler, did all the building work which included all concreting – yards, ancillary

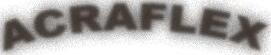


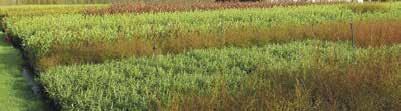


FAMILY FARMING
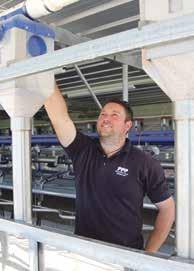
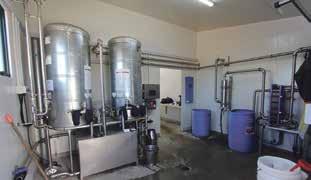
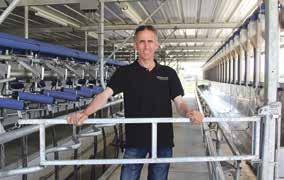
buildings etc – insulated panel cladding, walls, windows, drainage and painting within the building footprint, leaving the building ready for the plant installers and the electrician to fit off,” says Shanan.
Leask Engineering fabricated and installed the herringbone steelwork, pit step rails, pendulum exit gates, backing gate with yard washing system, exit races, holding pens and loading race along with the AI and vet race with a Camlock Head-bail.
Innovations
Noel says the company’s 65 years’ working with farmers is evident in their innovations that add new levels of ease and efficiency.
“The Leask Platform Gate is a case in point, preventing the last cow in the row from backing out, once her feed is finished, and trying to join the new row of cows on the other side! We can slot it into place from the pit and it’s incredibly simple and effective,” say Noel.
The new dairy’s proximity to the old shed enabled utilisation of the existing feed
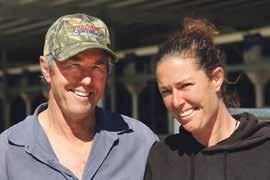
silos and the 30 existing feed dispensers were recycled and repositioned on the inside wall of the new dairy, with 30 new dispensers and a new feed system supplied and installed by PPP Industries.
Bruce Cameron, of Specialised Coatings, applied Acraflex paint finish to the pit walls of the new dairy. Acraflex is a high quality, solvent-based acrylic waterproofing compound that is an attractive, single-coat durable longterm waterproofing solution.
The heart of the dairy is a DeLaval Midiline ML2100 swing arm system which ensures perfect alignment of clusters, EP100 pulsators and automatic cup removers. The milk pump is a DeLaval FMP220 with a SEMA Variable Speed Drive controller. Clusters from the old dairy were in good condition and recycled into the new dairy.
Optimum environment
The previous dairy did not have a swingarm system and the pit was shallow, meaning the milking environment was cramped –
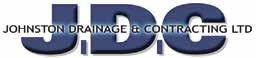
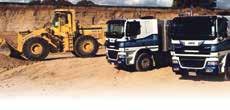
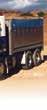
particularly with two or more milkers – and the cupping position was low and therefore uncomfortable for milkers. Noel and Lisa both say the swingarm system and deeper pit resolved those issues creating an optimum milking environment.
Noel and Debra’s daughter Lisa Reilly says her first season back on the farm was in the old shed. “Dad and I milked together, each milking helping refine what was needed in the new dairy.
“We effectively started the 2023/2024 season in the new shed and the new dairy has delivered beyond expectations.”

The new dairy’s proximity to the old enabled utilisation of existing feed silos.
flow is exceptional, the cows are settled and milking well.
“Automated cleaning, of the milking system and vat, is next level and ensures peace of mind.
Everything in this new dairy is easy.
But the final word comes from Noel who, after retiring from milking after 30 years, never thought he and Debra would be back milking.
“We are really enjoying milking,” says Noel. “Everything in this new dairy is easy; there’s simply no comparison between milking now and how it used to be in the old shed. Cow
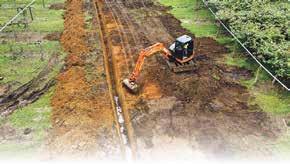
“There are always two people in the shed – Debra and I rotate milking with Lisa and Joe. It’s a flexible arrangement which suits both families and means we get days off when needed.”
Noel says when something like a new farm dairy has been in the planning stages for a long time “your expectations are high for the value which will be generated from building new”.
“This dairy has more than delivered. We couldn’t be happier.”

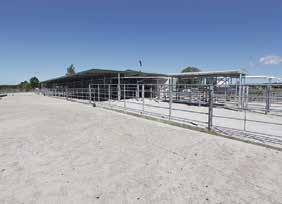

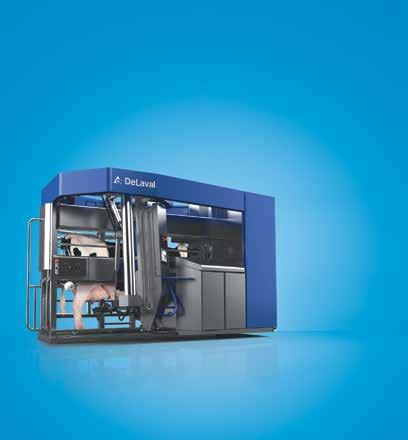
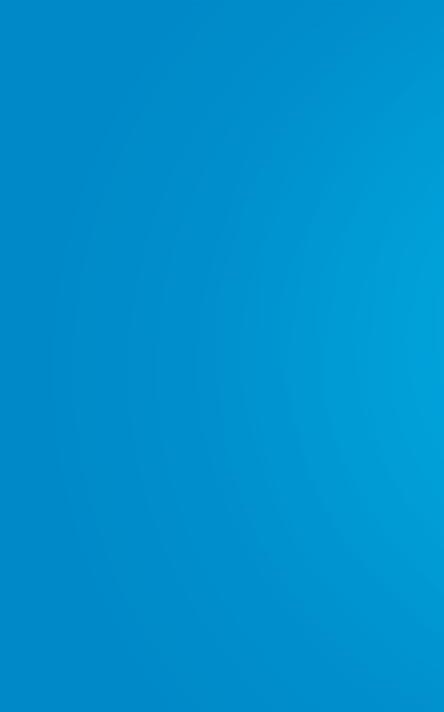
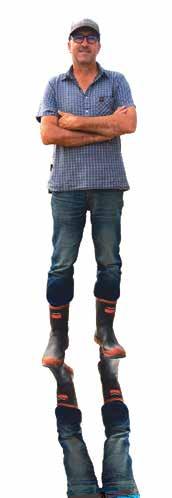
Left: PPP Industries’ Simon Vernon says half of the new dairy’s 60 feed dispensers were recycled from the old shed.
Noel Hosking and his daughter Lisa Reilly.
Taking the bull by the horns
Cantabrians Peter and Kristy Schouten invested in an eye-watering multimilliondollar upgrade to Eyrewell Dairy for a decisive reason.
This couple – who farm a little more than 30 minutes north of Christchurch – has put itself ahead of expected environmental restrictions. And, when Peter decided to take that bull by the horns – he did it in a gargantuan way. More than 1.3 hectares of concrete has been poured with nine different gradient levels. The new concrete covers three feed pad areas and access tracks of 6400m2, an effluent bunker and drying pad at 1400m2, silage bunkers and access tracks of 5800m2, effluent ponds at 867m2 with 1450m3 storage; and another effluent pond at 3550m2 with 8400m3 storage. The 70-bail rotary built in 2008 – covered by an 80-bail building – has also been rejuvenated with new bails and plant installed by Rakaia Dairy Services.
NumatAGRI’s rubber matting covers about 1300m2 of the circular yard and dairy platform. And rolls of NumatAGRI rubber 1.8m wide by 30m long – weighing two tonne each – are laid on the first 200m of the exit tracks. A diesel generator snaffled after the 2011 earthquakes could power the whole farm. Effluent includes fully lined ponds, recycled greenwash for the dairy, and managing solids on-farm.
Pushing ‘play’ again
It’s a lot to absorb, but Peter never secondguessed his decisions for their 2150-cow spring
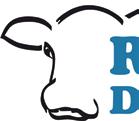
and autumn calving operation. The operation is split into two entities: one milking 1450 cows on the home farm under manager Liam Gray; the second milking 700 cows in a 60-bail rotary 7km away under manager Dev Bohara. The complete farm covers 1150 effective hectares and includes two lease-hold run-offs 4km and 12km away.
Eyrewell Dairy has averaged up to 650kgMS per cow. However, growing pains and some telling winters pushed it back to under 600kgMS last season.
Peter has now completed changes to the home farm, he’s had time to establish a great team, and he is ready to push “play” again.
“The cows can average 700kgMS, no problem, if they don’t have a big walk, you can control their diet, and you have the right people on-board,” says Peter.
“We’ve pushed for a feed pad, so I’ve got control of the inputs and the outputs. If you feed grass silage in a paddock, on a good day you’re probably running at 30 per cent wastage.
“The feed pad has increased our feed efficiency by 25 per cent. We can also add palm kernel, soya bean meal and chipped fodder beet.” A contractor transports the beet, Peter washes and stores it in a concrete bunker, before chipping it every other day so it’s fed fresh and clean.
“We bring the cows on to the feed pad premilking, so they have equal opportunity to access feed.
“The reason we also poured concrete all the way from the feed pad to the silage stack is so
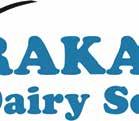
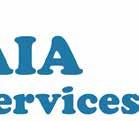
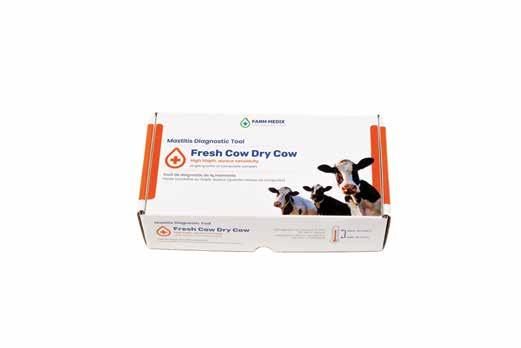
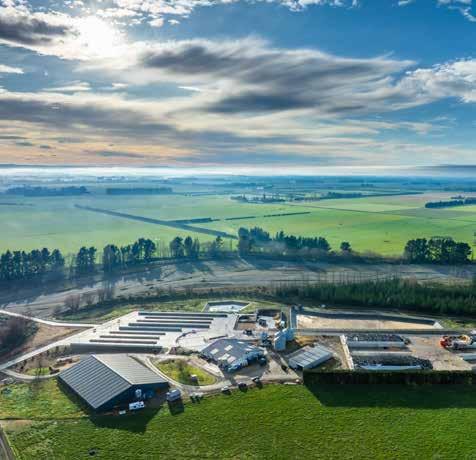
the silage wagon is always travelling on clean concrete, and not dragging mud and stones around.”
• Milking Machine Service, Installation & Repairs
site. The Rural Building Solutions team set up temporary cattle stops, site accessways and signage – moving them with each subsequent stage.
Teamwork
• Milking Machine Service, Installation & Repairs
• Teatspray Servicing
• General Engineering
• Teatspray Servicing
Rural Building Solutions designed, built and project-managed the upgrade.
• Water Reticulation
• General Engineering
• Water Reticulation
RBS director Nigel Hodges says the site was a working farm throughout the build – with all three cow lanes entering the yard through the building
• Chemigation and backflow valve testing
• Chemigation and backflow valve testing
• Authorised agents for Read and Wetit
• Authorised agents for Read and Wetit
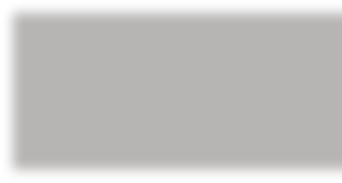


Clark 0274 382 180 tony@rdsl.co.nz
“Things went smoothly because we had a shared vision with Peter – we communicated clearly and often – and we did what we said we would within the agreed timeframes,” says Nigel. Peter says installing NumatAGRI rubber matting was a no-brainer
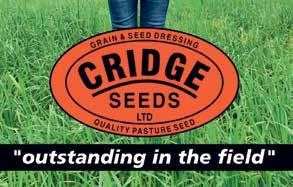
Tony Clark 0274 382 180 tony@rdsl.co.nz
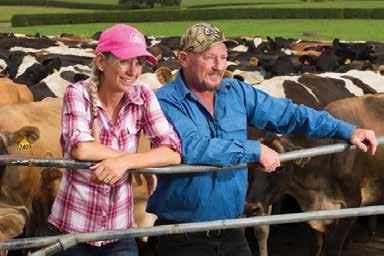
The river boundary combined with cool winter temperatures gives Eyrewell Dairy almost mystical lighting from above in July 2024. Photo: Ollie Larkin.
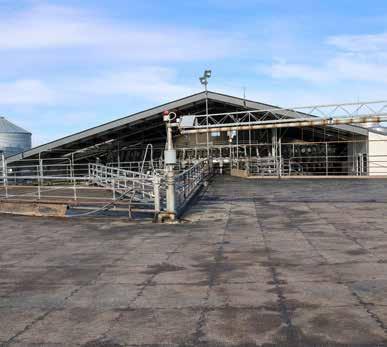
because it forms part of his ultimate push for production.
“It’s reduced lameness, and it’s part of everything that’s going on that’s leading into why our production is climbing too,” says Peter. “When we thought about doing rubber, we immediately thought of Numat.
“We considered the areas that would see the highest amount of traffic. The holding yard and platform get used twice-a-day 340 days of the year. It really only has a couple of weeks off. Also, getting the cows off the yard and onto the track is important. So, we didn’t hesitate to put down rubber in all those places too.”
Densem Contractors was tasked with the earthwork responsibilities. Curating gradients ranging from 1.35 per cent to five per cent over nine different areas was
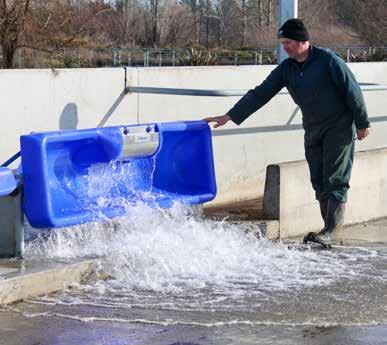
Eyrewell Dairy
made easier for Matthew Densem’s team, because of their smooth connection with Rural Building Solutions.
“The biggest challenges were keeping the offset distances from the river boundary [which borders the farm], which impacted on the shape of the effluent ponds,” says Matthew. “Also, the gravel extraction from the river wasn’t helped by the two or three flood events, but it’s fantastic to see it successfully operating.”
Biggest sold
The effluent system is the biggest single system Ashburton-based business Stocker
Solutions has sold in New Zealand. Shane Stocker says most systems include a single vertical Agi-Pompe pump. Eyrewell Dairy has three. The focus was on turning effluent into greenwash or solids and being able to use the 11 flush valves to floodwash designated areas of the yard at the push of a button.
“Because it’s such a large area – with some of it having pre-existing concrete with different falls – we added more pumps and reception pits to make it all work,” says Shane.
Everything is plumbed beneath the concrete. “It’s quite impressive to watch the lids lift up and blast water out of the valves. It’s effective cleaning large areas of concrete without manpower. It helped that Peter is very innovative, and that we love this sort of work,” says Shane.
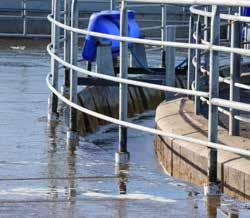
Electrical work was completed by Nairn Electrical. “I don’t think you’d look at anyone else when it comes to electrical for industrial projects like this,” says Peter. “They are on their game, and they already knew our existing layout. We didn’t hesitate.”
Three choices
Peter says this investment makes sense. “As I see it, you have three choices to spend money. You can either spend it frivolously, repay debt, or invest in the farm that you have.
“We opted to invest in our farm because I believe that with environmental regulations coming – you can either control the outcomes, or regulations will catch up to you.
“And, you can’t get the milk we’re looking for unless you do something like this.”
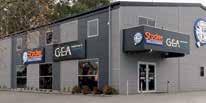
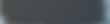

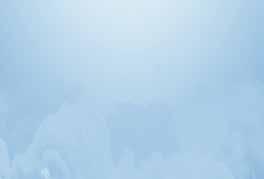
•
•
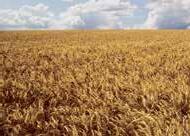

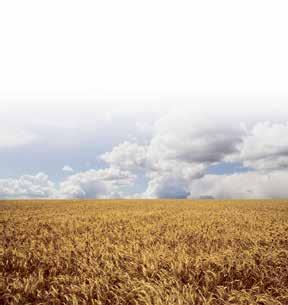
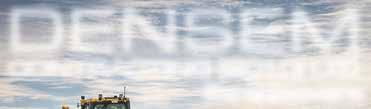
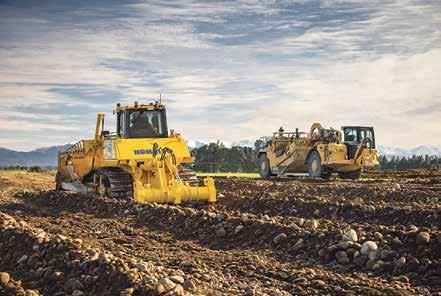
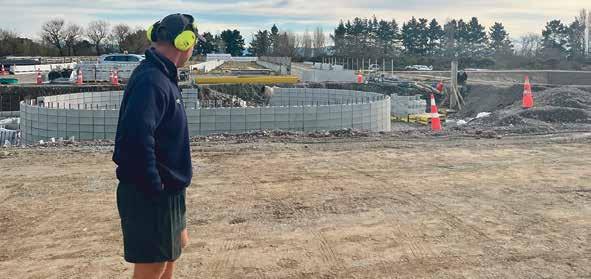

Dianna Malcolm
NumatAGRI’s rubber matting extends across the entire yard, onto the cowshed’s platform, and 200m down the track.
Peter Schouten cleans one of the 14 DeLaval tippable water troughs on the feed pad, making fresh water easy and safe to access.
Greenwash has an efficient exit off the feed pad (left), which is funnelled underground without impacting the cowshed yard.
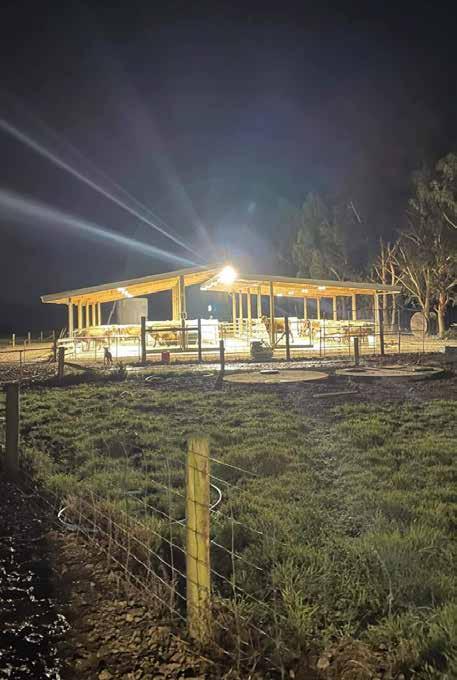
New barn a three-way effort
A herd of 23 Jersey show cows is bucking the trend in Canterbury when it comes to making money from a dairy herd on 5.5 hectares.
Until 2020, Peter and Claire Hansen had run their show herd, Lilac Grove Jerseys, as a passion project – without supplying a processor – alongside their family business, Peter Hansen Drainage.
Milking cows allowed Peter to continue his family legacy in dairy, but with six children and the ownership of a busy drainage and excavation business – which employs 13 to 15 staff working throughout Canterbury – the cows were a monster daily effort with little to no financial payback. The couple reared calves with the milk, but the pricing on both ends of the deal was unpredictable.
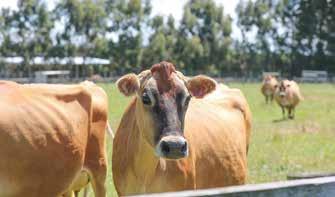

of the wider industry’s public relations effort – not unlike UK television presenter Jeremy Clarkson’s dive into the ‘Diddly Squat’ farm – Fernside Fresh is showcasing and quietly educating its urban customers what beautiful cows living an excellent life looks like.
Fernside Fresh Milk Fernside Fresh Milk
Three-and-a-half years ago, they finally found and bought a small holding at 492 Oxford Rd on the main road between Oxford and thriving North Canterbury hub Rangiora. It was a deliberate move, because it cemented their decision to sell raw milk to the public under their brand, Fernside Fresh.
It also put them in the driving seat of the dairy side of their business – even though it demanded an upfront investment that could overcapitalise the property. However, for the benefit

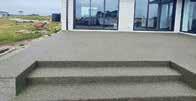

“Obviously we were very intentional with the property location,” says Peter. “It took us quite a few years to find the right spot on a main road, close to town – because no-one is going to visit a dairy that’s 20 minutes down a back road.”
Their customers travel from as far away as Ashburton, about 1.5 hours away.
320L a day
They milk through an uncomplicated eight-aside swingover herringbone cowshed they built in 2021. In 2022, they added two 200L self-serve milk vending machines, which opening to the public that November.
A smaller holding means that when the public drive into their facility, the quiet cows are never far from the cowshed – making the marketing of this family venture as beguiling as it gets.
“We are lucky in that we can get awesome photos with the cows for marketing, because they are used to being handled, we can halter them, and they often wander over to the fence for a pat,” says Peter.
Just over 12 months later, they’ve peaked at 520 people visiting their business a week – buying 320L in a day – at $3.50 a litre plus bottles.
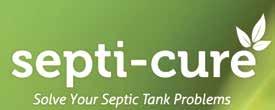
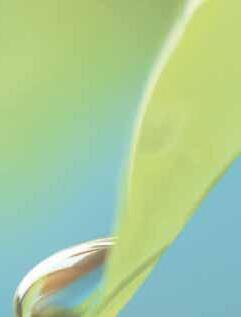
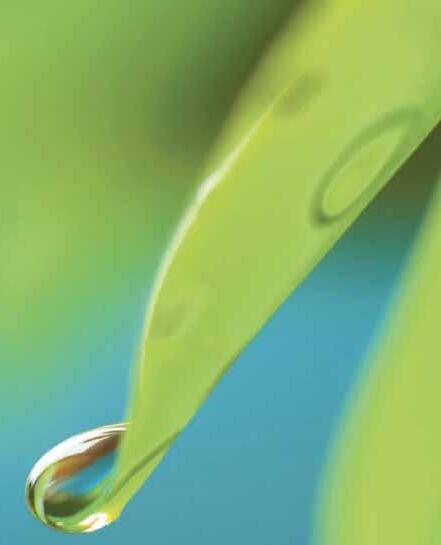

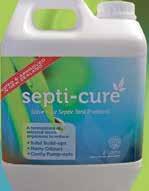
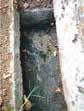
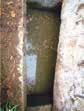


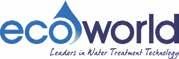


Peter and Claire Hansen like knowing their cows have protection from the elements. Photos: Claire Hansen.
“The barn will allow us to get around 30 per cent more milk from the cows we have”
“It’s exciting to think what we can potentially make off here once we are in full stride,” says Peter.
The barn
In June 2024 they added a 240m2 barn with 30 beds – to make it easier to protect pasture and to manage the cows during a drought or adverse weather.
The decision to add a barn so soon after the cowshed and milk vending service came down to practicality. They lease two runoffs for young stock and dry cows, and it’s always been a juggle.
“It was the pasture damage,” says Peter. “We were losing 25-30 per cent feed at times on this property. I just think when it is wet or dry, we have now have shelter and/ or a feedpad. It’s better for animal welfare and it helps sustain production no matter what the weather is doing. Our first choice is always pasture-based production, but it’s good to know we have an option.
“And, if we were to lose a run-off – which you’re always vulnerable to – we could bring the animals home and run them in the shed here if we had to. One end of the barn can be fenced off into a calving pen too.”
Peter says their focus is on achieving more production from fewer cows. They can milk 30 comfortably year-round.
“The barn will allow us to get around 30 per cent more milk from the cows we have, rather than having to milk more numbers, which our farm isn’t suitable for.
“We considered a bigger farm at different
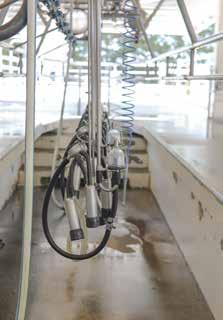
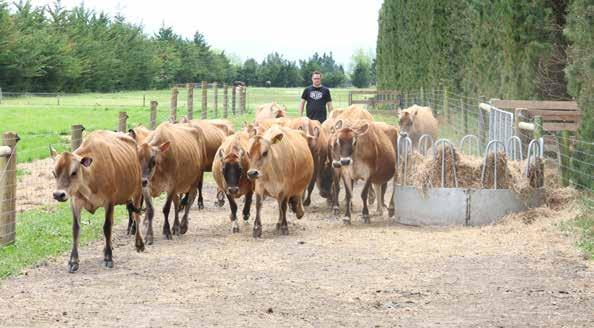
times, but it would have put us under a massive debt load, and it seemed more logical to try and get more from a smaller holding.”
Pressure points
The workload in supplying raw milk to the public involves ongoing pressure. Their Somatic Cell Count runs at around 28,000 – udder preparation is exacting – and a milk test every 10 days by an independent authority will always be part of the equation. Peter says the cowshed is a perfect size, given the detail that must happen inside it.
“We have to go through and wash all the udders well, strip every cow and every quarter, pre-spray them, wipe them down with a clean disposable cloth, and be careful
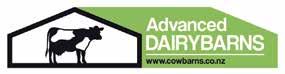
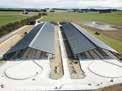
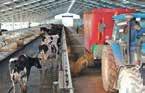
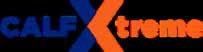
not to touch the udder with our hands when we cup up. If we had a bigger dairy, you’d nearly need another person, so this size has been perfect for what we’re doing.
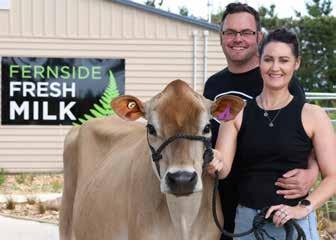
“Naturally everything is very stringent and there is always some stress when you open the email for the test results. But, so far it has been fine.”
They keep ahead of their SCC with a DeLaval Cell Counter on-farm.
“It allows us to be proactive, and it’s simple, accurate and keeps us on-track.”
They have roughly 10-15 per cent excess milk, outside of calf milk, at different times of the season. “We don’t have that extra milk all season. Sometimes it’s just when


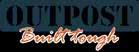
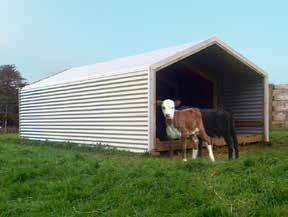



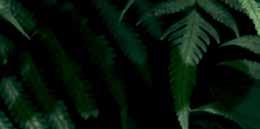
Growers
Growers of quality native plants


we are transitioning between the spring and autumn herds,” says Peter.
Barn details
Building the barn was a three-way effort between Peter Hansen Drainlaying and Forrest Engineering, with the support of Winton Engineering, who supplied the barn’s individual stalls, matting and breast rails.
Blake Forrest, who took over Forrest Engineering from his father Grant this year, was in the thick of things for a

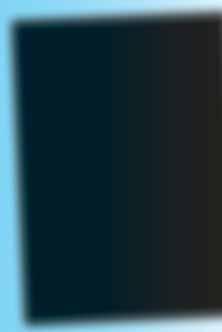
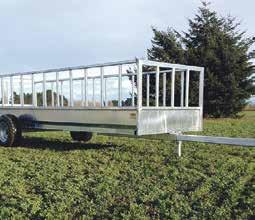

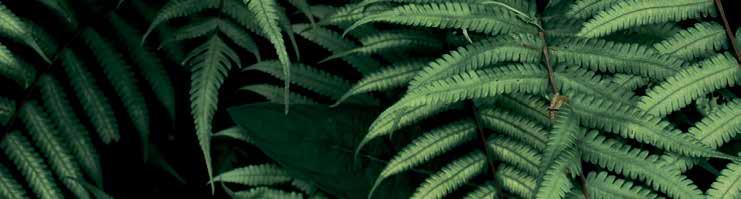
Growers of quality native plants
Hygiene is paramount.
Photo: Evie Tomlinson
Peter and Claire Hansen have found a marketing edge when it comes to selling raw milk to the public from their quiet registered Jersey herd of show cows.
second time. Forrest Engineering built the cowshed. They then installed the barn’s internal structures.
Peter researched information from Jersey Canada regarding free stalls size and settled on 1200mm x 1800mm stalls. The cows – which went into the barn in June – are bedded on Agricow foam cow mattresses, supplied by Winton Engineering. The Italian-made beds include 5cm thick Latex foam encased in polythene with a 3mm polyethylene cover and a woven top surface. The combination offers maximum cow comfort, exceptional slip resistance, and is easily maintained.
The shed is simple, but effective with an outside feed face on both sides and two head-to-head freestall lanes. The shed includes two per cent gradient fall for the recycled and automated flood wash.
Blake says it was their first barn build and install, and he enjoyed the challenge.
“Working on new builds is always good,” says Blake.
“Dairy wintering barns are the bread and butter for Winton’s sister company Advanced Dairy Barns, so it was great to take advantage of their knowledge, and they were a great bunch of guys.”
Advanced Dairy Barns Limited builds full barns for up to 1650 cows. It also supplies hot dip galvanised structural steel kitset sheds. Its full service incorporates all the internal fixtures, bedding, stalls, effluent scrapers, cow brushes, and water troughs.
Showing cows
Peter’s love of registered Jerseys and showing cows has led him to a number of fearless investments in genetics for Lilac Grove Jerseys, which is closing in on







close to 90 years of family history with the breed.
In 2017 they bought four registered Jersey cows in an Australian auction.
Peter and Claire planned to import the milkingage cows, dry, live to New Zealand. Ten days before the cows were to fly – having passed all their tests and completed their quarantine – the Ministry for Primary Industries reported the first outbreak of Mycroplasma bovis in New Zealand and slammed the border shut.
Those cows never left Australia. Peter and Claire have since imported embryos from those individuals – selling one three-month-old heifer calf born in New Zealand at the NZ Dairy Event in January 2024 for $6500. They’ve also proactively bought embryos from profile North American herds.
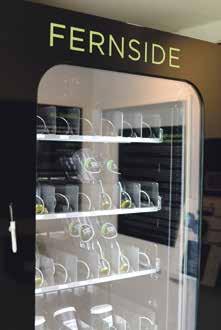

journey hasn’t been without its moments of self-doubt, reflection, and pause, they are glad they pushed through.
In April 2024 Lilac Grove Jerseys invested in genetics closer to home –when it paid the top price of $24,000 for Ferdon Fizz Viyella EXC at the “75 years of Ferdon” sale in Otorohanga. “The Fizz” now calls Fernside Fresh home and has delivered a heifer calf this season.
Eye-watering risk
Peter says there’s been a perfect synergy blending pedigree cattle with the raw milk business. It makes the risk they have absorbed less overwhelming. While the
With Bellbirds singing in the background – his final thought comes easily.
“I milked cows for a long time just for the love of it. It’s nice that they’re now paying their own way, and the registered part of the business complements the commercial side, and helps tell our story for our customers,” says Peter.
“Yes, there has definitely been significant risk. But I’m hoping once everything is running at full throttle and we get a chance to consolidate that this will have been the best decision we’ve ever made… and I think it will be.”
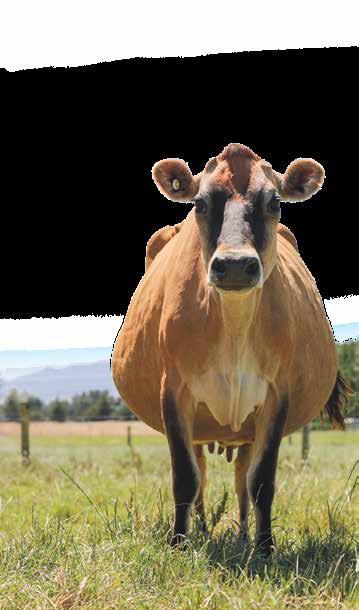




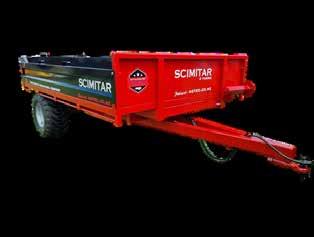
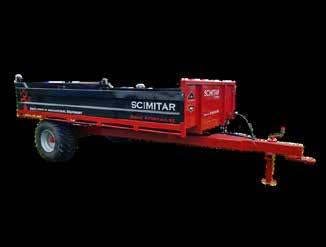
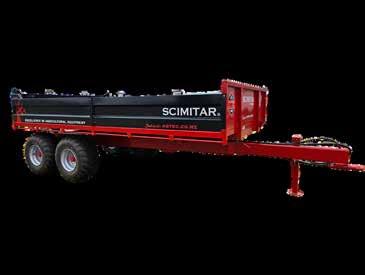




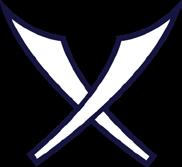
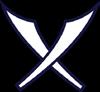

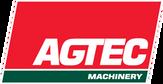
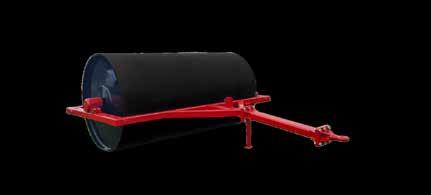
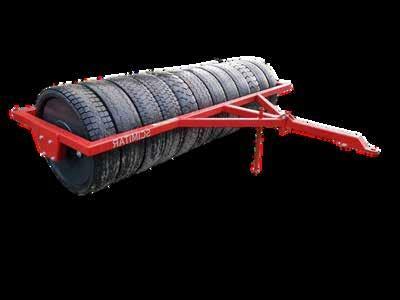

Dianna Malcolm
The self-help vending machine means customers can access fresh bottles easily. Photo: Evie Tomlinson.
Peter and Claire’s children from left: Elijah, Lauren, Ethan, Israel, Brooke and Joseph.
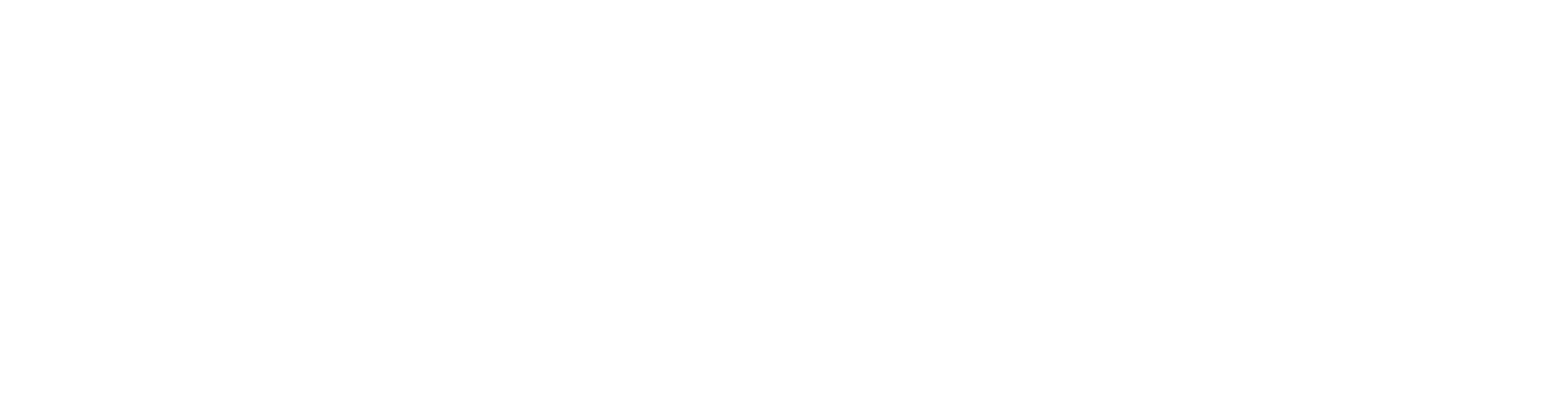



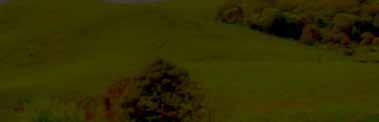



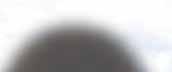


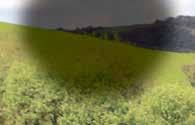


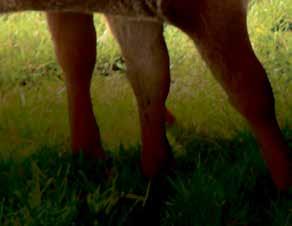
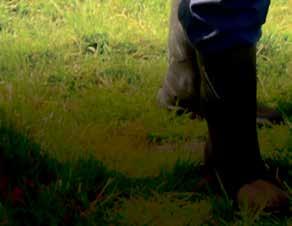




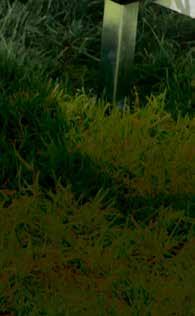
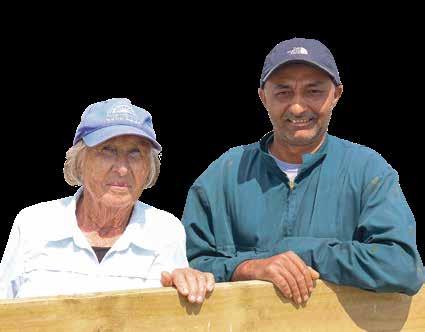

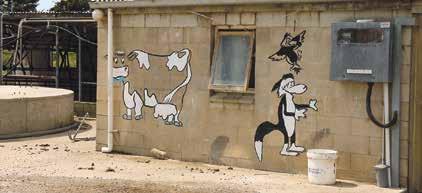
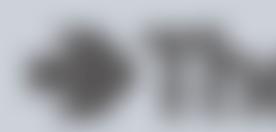

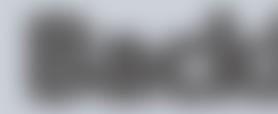
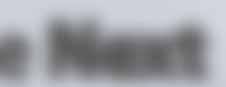
days at Joy’s
While most people Joy Burke’s age are taking life easy, this septuagenarian has just finished building a new dairy on one of her two South Canterbury dairy farms.
The career dairy farmer has run three half marathons – one as recently as seven years ago – and progress rather than her age occupies her mind the most. She swiftly shuts down any questions regarding her birthdate. “I’m not telling you how old I am, because then you’ll treat me as such – and I don’t wish to be,” she quips.
But Joy will tell you why she has pushed on, from where she started, and who helped her get to where she is today.
Her dairying career was founded milking 380 cows on steep country at Kaukapakapa, 40km north of Auckland. After her divorce and the sale of the property, Joy says there was no market to sell the cows at that time in the North Island.
She decided to follow the dairy migration to the South Island – drawn by production gains through irrigation – trucking the herd south. Her initial intention was to farm for “a couple of years” before selling the cows. But it goes down as a “magic time” for her and she remains grateful to a number of people who helped her transition to irrigation, and to the area.
“That time has run my outlook on things throughout my career, and it’s made me realise how marvellous people can be,” says Joy.
“It was a struggle financially, and there must always be a measure of luck and a dollop of desperation. I was a bit fortunate with the bank at the time. They didn’t need to back me, but they did, and I’m grateful.”
Three decades later she’s also still with the Home
Farm 65, supplying Oceania Dairy Limited. She is dairying because she loves the cows, which has created opportunities for her valued staff members. The Home Farm 65 spans 215 hectares, milking 650 cows under sharemilker Nardeep Singh. The old dairy – a 36-aside herringbone – has now been replaced by a new 40-aside herringbone on the new site. Her second sharemilker, Jeff Columbus, milks 640 cows 7km away on 174ha through a 60-bail rotary.
Joy says she knew the dairy on the home farm had run its race a few years ago, but it proved too tough to change then. Everyone was tired of routinely dealing with the flooded milk line during peak production, and the greenfield site she wanted would halve the amount of walking the herd had to do every day down to 2km.
“Modern dairy cows milk more at capacity now, and it was pushing us,” says Joy. “Through September 2023, it was very difficult. That milk line is such a major thing and it impacts on everything else.
“Changing this dairy represented what it would take to look after the cows that much better.
“That’s why it’s here.”
A builder
Her biggest challenge was finding someone to build it. Among the flurry of new builds and dairy upgrades she couldn’t lock down a local builder. She turned to Gibson Construction company in Te Awamutu, in the Waikato. Managing director Brent Bird says they price dairy builds from one end of the country to the other, and they never let distance get in the way.
“Joy wanted it built within a certain timeframe, and there were some conditions that came with it,” says Brent. “I priced it, and Joy was up for it.”
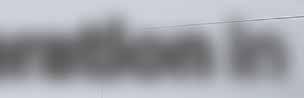
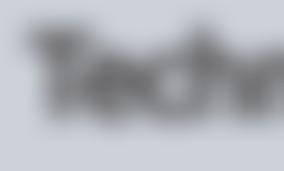


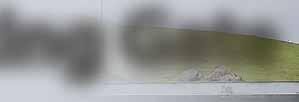
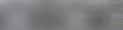
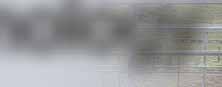



Joy Burke and her sharemilker Nardeep Singh.
The old dairy’s best feature was the Footrot Flats wall art.
Cow flow is now seamless.
new dairy
Brent says their company is habitually busy, so he stepped out of the office himself to drive the build. “I still like being on the tools,” says Brent. “It was a good build. I had a young apprentice, Curtis Friedrich, come down with me, and he proved himself.”
Brent says the local sub-contractors were great to work with and Gibson Construction’s part of the build – including the effluent bunker – was completed ahead of schedule within a monthand-a-half on an established pad. His total time commitment was three months as they worked in with timeframes for local contractors.
Joy adds: “I tried to find someone locally, but they couldn’t start until October”. “Gibsons just got on with it and they had it done within a month or two. It was no time at all. They were highly organised, and their dedication and level of detail was impressive.”
Night-and-day
The result has literally been “night-and-day” for Joy and her team. The cowshed has been built with the potential to push out to a 46-aside, and she chose a herringbone over a rotary because of the price-point difference.
The herd is projected to finish with 300,000kgMS for the season, with a 462kgMS average. There is 10 per cent less lameness, production is eight per cent up month-on-month, the average Somatic Cell Count is 120,000, and the staff are happy.
The dairy looks almost like a new house on the approach, and Brent says they make no apologies for injecting some personality into their builds.
“It is quite common these days. It does help that we have a commercial side to our business as a background. It brings a bit of flair to the old cowshed.

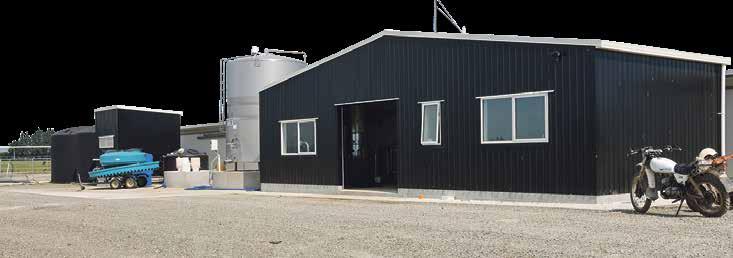
Some stay with the natural colours, but others like Pioneer Red or Denim Blue, for example.”
Joy may have chosen purple had she had the choice, but Gibsons had black and white barges on-hand, so she went with that. She couldn’t be happier.
“It’s even better than I expected it to be. It’s more centralised, the machines are better, and it hit me the other day that we’re no longer reaching up to cup-on, and that makes it so much better for everyone’s backs.”
Nardeep agrees. “The backing gate is also there, but we don’t really need to use it because the cows flow in and out so easily. There is much more light in the dairy, and the cleaning is simple,” he smiles.
Home Farm 65
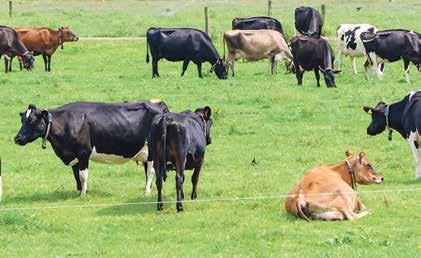
“The herd is looking good because their energy is going in the right direction.”
Keep running…
Joy goes to a personal trainer twice-a-week, and her reason to still be dairying is simple.
“Because I can, I suppose,” she muses.
She’s not planning on retiring anytime soon. “I remember running a half marathon in Christchurch and I was flagging at one point. As we ran past a graveyard someone yelled: ‘Keep going’. I looked at that graveyard, and that really got me going.”
That race speaks to Joy’s general philosophy on life. It’s important to keep running.
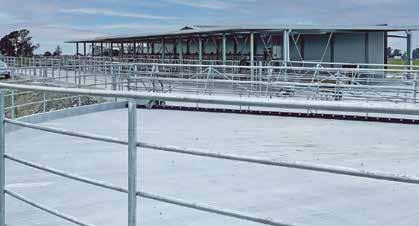


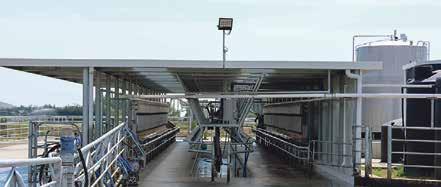
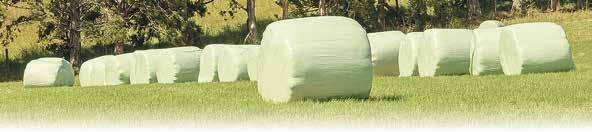
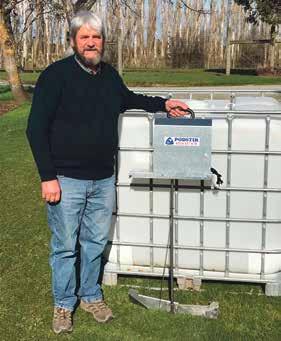

Gibson Construction’s Brent Bird says it’s quite common for cowsheds to resemble residential homes from the outside now.
Production is eight per cent ahead month-by-month on last season.
The circular yard supports cow flow. Photo: Gibson Construction.
You can’t go past fully galvanised silos
Invercargill-based Hecton Products is a down-to-earth manufacturing business with access to world-class materials and networks in agriculture.
Owned and operated by Aaron and Lauren Bremmer, it doesn’t get more “real” than sitting down with this understated and diligent innovator and manufacturer.
Hecton Products found its start during the early-1970s producing sheep handling equipment. Today, its products are exported to Australia, the UK, and the USA.
By 2006 the buzz word in Southland’s agricultural landscape was changing to “dairy”, and – as the region’s sheep farmers started converting their operations –Hecton Products also pivoted. It diversified into dairy, while still servicing the sheep industry. For its dairy customers, it added feed systems, storage silos, custom-made projects, and after-sales service. Today the dairy industry comprises 60-70 per cent of its business.
Hecton Products also offers general engineering, on-farm repairs, and maintenance, Tig and Mig welding and custom manufacturing in addition to being one of New Zealand’s largest manufacturers of single and tandem ATV trailers for calving and lambing, road trailers, and stock crates. Not to mention supplying silos, augers, roller mills, in-line dispensers and meal and molasses feed systems for
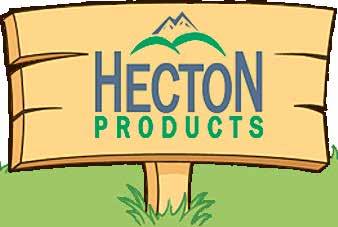
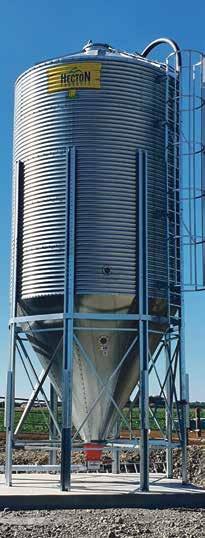
herringbone and rotary sheds. It is the New Zealand agency for Australia’s Feedtech Roller Mills & Pencil Augers.
Hecton’s high-spec ATV trailers have several compelling points of difference, including a clever back door that slides right across, leaving no rail to bump heads on and greater access for loading calves. Its back door also drops down – doubling as a ramp. Suspension on the double tandem trailers can be adjusted to follow a ute or a bike.
“The business is still evolving,” says Aaron. “We’ve always done our own thing, and over the years we’ve just kept getting more efficient and more in control of our supply chains.”
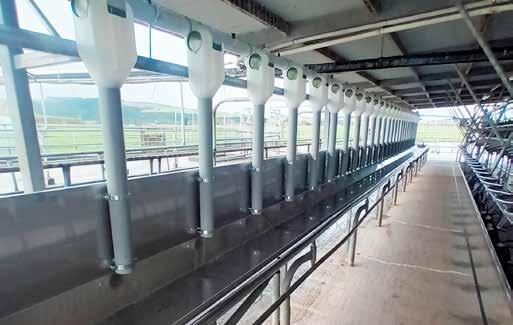
Hecton Products Hecton
it 10 years ago. We assemble them locally, and we’ve always got stock on-hand.”
Eighteen months ago Hecton Products started sourcing its storage silos from Europe through Hamilton-based Agri Systems. Among the game-changing detail these silos offer New Zealand is that they are fully galvanised, and they carry a 10-year warranty – which is 10 times longer than most competitors. They come in any size, and Hecton Products has found a sweet spot with its 12-foot, five-ring, units.
“There were plenty of silos available out there, but they didn’t all have the quality I wanted,” says Aaron. “The European ones are excellent, the supply is good, and they are priced competitively. I wish I’d done
Aaron says his team of 14 staff travel throughout Southland and into Central, and South Otago. However, their silos are available in kitset throughout New Zealand.
Hecton Products is Southland’s biggest installer of in-shed feed systems – sourcing many of its components through Agri Systems. These Kiwi-made systems offer several advantages over their imported counterparts – including being manufactured with a UV stable plastic. When it comes to after-sales service, Aaron is quick to respond. “I’ve always been passionate about making sure we can offer effective after-sales service. We still do a lot of local callouts, and we are happy to service anyone’s feed system.”

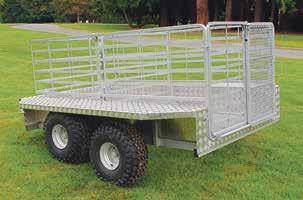
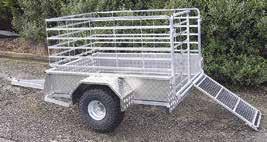

Hecton Products’ Josh Bremner and Corey Gibbs, who install and service the Southland company’s meal feed systems.
An in-shed feed system.
In-shed feed systems for Kiwis by Kiwis
Based in Hamilton, but distributed through dealers across New Zealand, Agri Systems Ltd specialises in products and reliable services for the dairy and poultry industries.
Simon Medd, co-owner with his wife Olivia, says the company was formed in 2021 “to provide in-shed feed system components designed for New Zealand farmers”.
“I had worked in the poultry and dairy industries most of my life, largely working with imported feed systems. The plastic components on these systems were often compromised by New Zealand’s high UV light,” says Simon.
“Farmers bore the cost of this, needing to replace components – like in-shed feed dispensers/volume drops – within a few short years of installation.
“Working closely alongside our South Island distributor Hecton Products, Agri Systems and the design team at ES Plastics Ltd designed and started manufacturing
the AS-22 feed dispenser kit, which resolved many of the shortcomings of imported counterparts.
The AS-22
Simon says the AS-22 feed dispenser kits have been manufactured with UV stable plastic, which has proved to be very popular with more than 9000 units having already been retrofitted to existing systems or incorporated into new herringbone dairy sheds.
“The AS-22 is designed to fit 75mm and 90mm auger systems. It is simple and compact, with an improved sensor position on the control dispenser. The large feed throat minimises blockages, meaning that every animal in the shed gets the right allocation of feed when it’s needed.
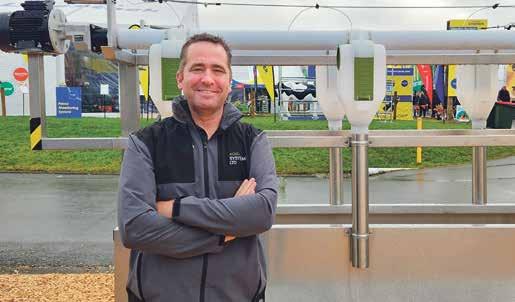
systems which will reliably perform and, most importantly, last.
“In addition to New Zealand designed and manufactured products, we also import and distribute high quality system components like the VAL-CO Flex Auger, which comes in multiple size options, and VAL-CO storage silos with sizes ranging from 2.6 to 48.5 metric tonne.
“We are the NZ distributor for Transtecno gear units and drive systems, and we also have a specific range of fully galvanised silos up to 48 metric tonne which are available from Hecton Products in Invercargill.
Agri Systems Ltd
“The quality of our products, and back-up service we provide has fuelled demand from farmers wanting feed

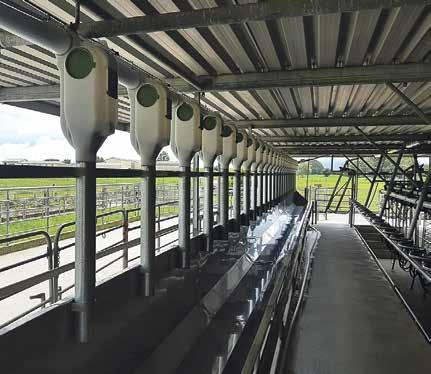
“We stock a comprehensive range of electric motors, drive units, augers, control systems and components for every aspect of in-shed herringbone and rotary feed systems.”
Simon says the company aims to either
provide or develop solutions to feed-system problems faced by dairy and poultry farmers.
Develop solutions
“We are continuously investing in new product design and tooling for the manufacturing of more components in New Zealand and are gearing up to begin exporting our products to the US this year.”
Agri Systems products are available in the North Island from Qubik and Livestock Feed Systems in the Waikato, Central Silos in Palmerston North and from Hecton Products in the South Island.
Simon says growing demand means that the company is currently seeking expressions of interest from distributors in the Northland region. “We have a great working relationship with our distributors and enjoy problem solving and creating new products alongside them.
“Our challenge to farmers and distributors is to bring us a problem so we can solve it.”

Agri Systems Ltd co-owner Simon Medd.
Introducing NumatAGRI Construction Ridgeback Composting Barns
A revolutionary new barn for the dairy industry.
NumatAGRI streamlines the process of constructing feed pads or cow barns, making every step from design to build straightforward and stress-free.
Ridgeback composting barns are a game-changer for the dairy industry. With 20% more air exchanges compared to traditional barns they compost better and provide a healthier environment for cows. Farmers who make the switch to Ridgeback composting barns say they’ve seen a remarkable increase in production output and big reductions in cow health issues.
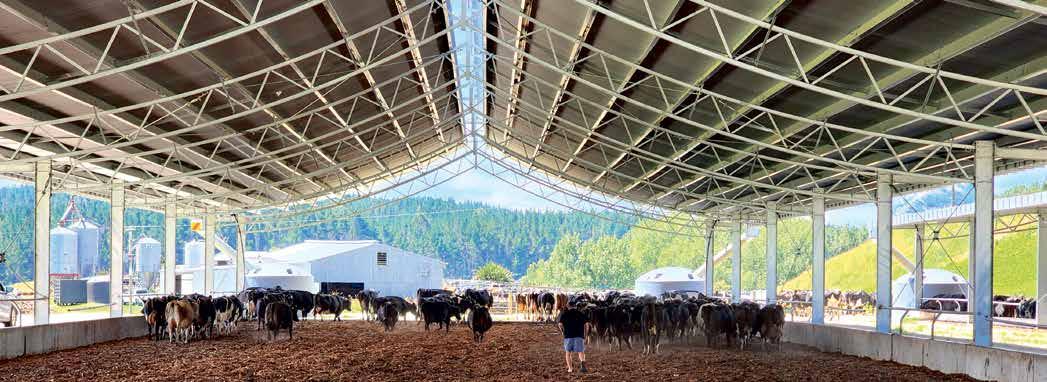
Design & Build Feed Pads
The easiest way to build a feed pad
Have a feed pad design in mind but don’t know where to go next with it? NumatAGRI Construction can help design it and build it too. Check out what one of our recent customers had to say about NumatAGRI Construction’s design and build service:
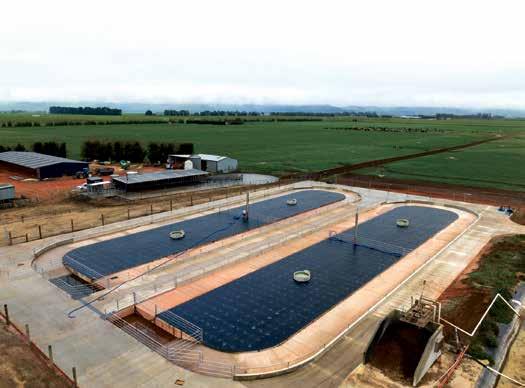
“I’veworkedwithalotofbuildingagencieswithlotsofthings happeningonfarmconstantly.WithNumatAGRIConstruction,the processwasjustverysmooth.We’reveryhappywiththeresults”
Michelle Borrie, North Otago