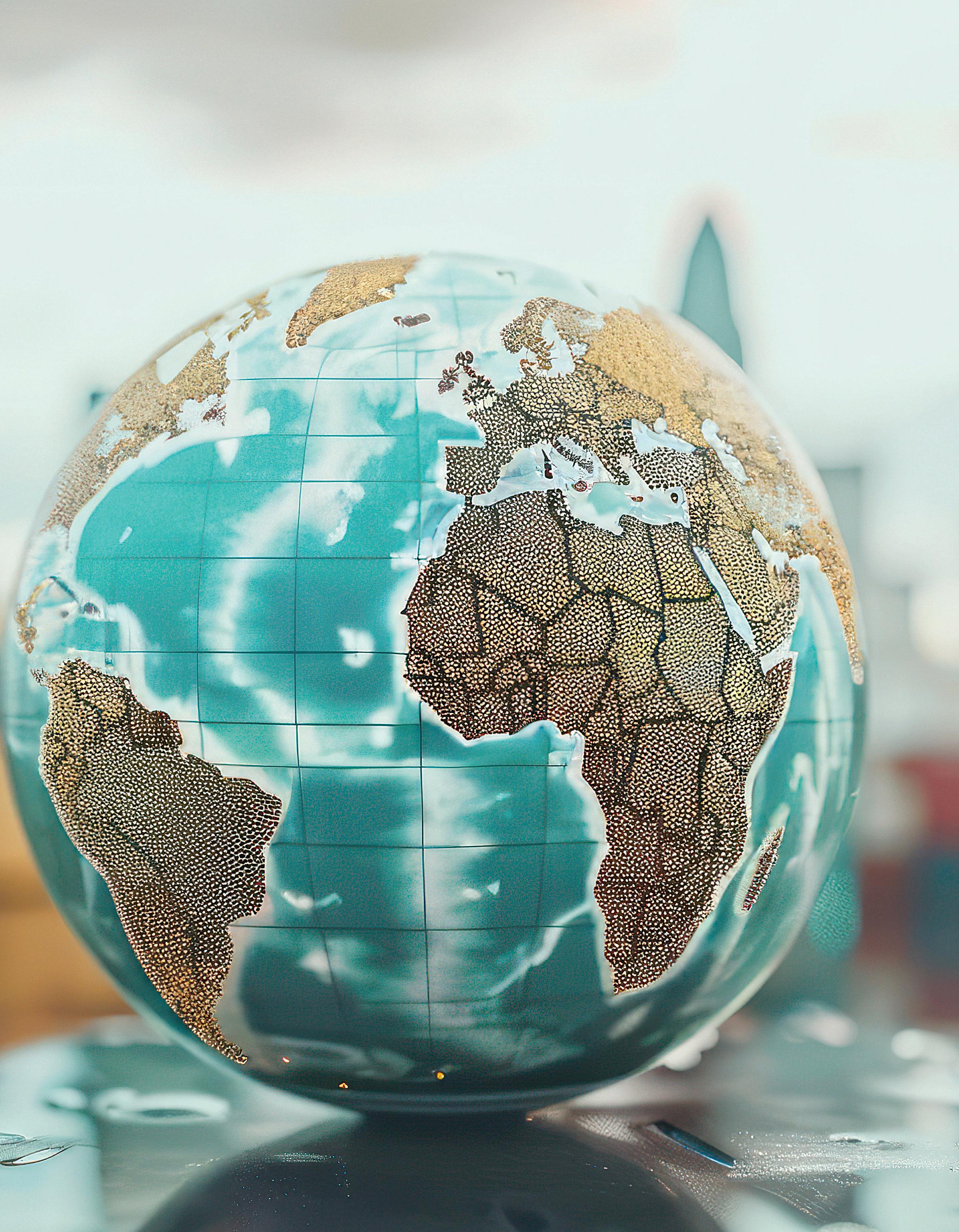

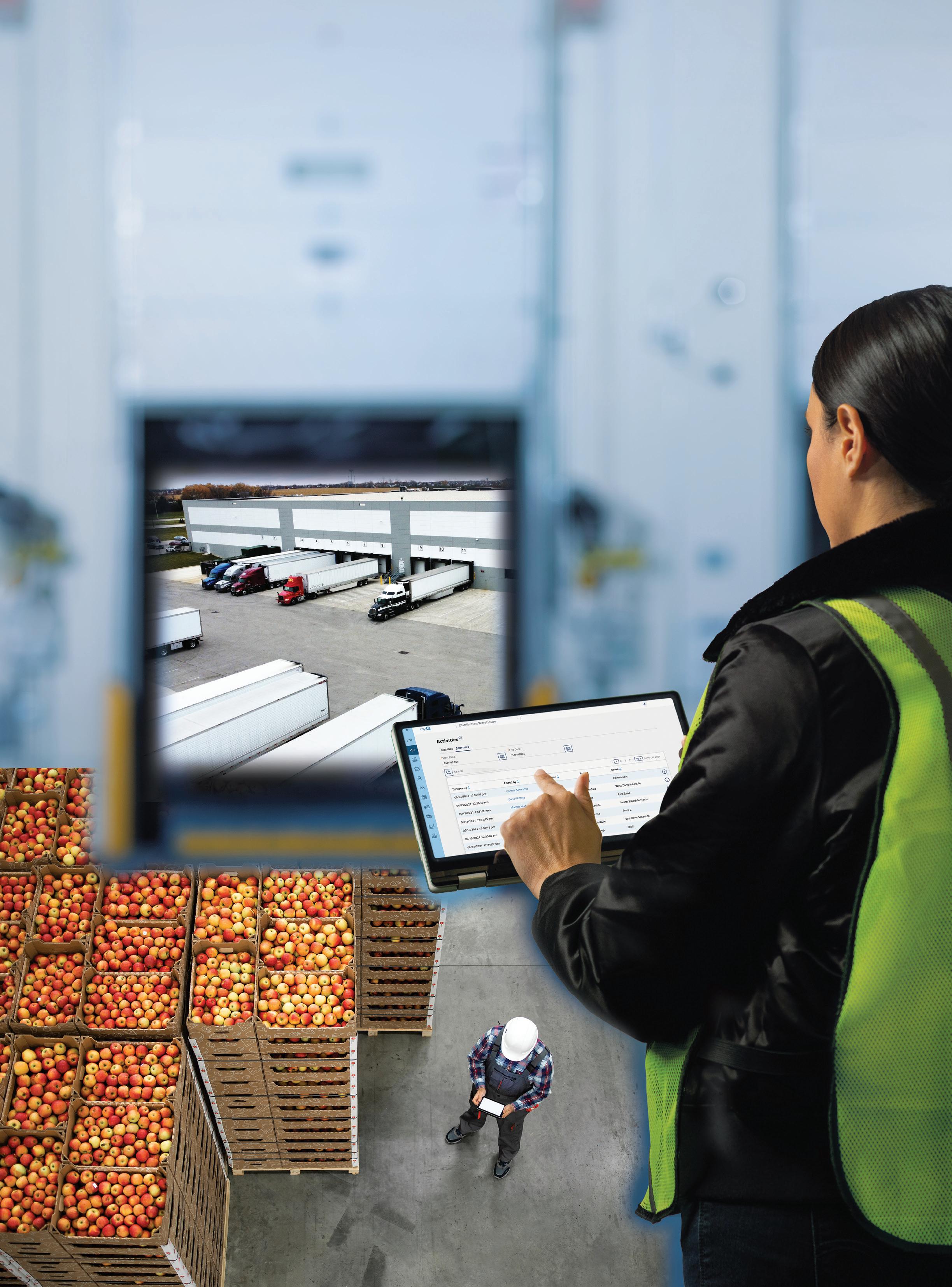
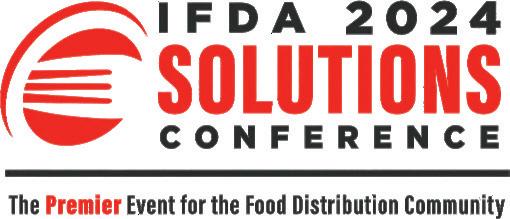
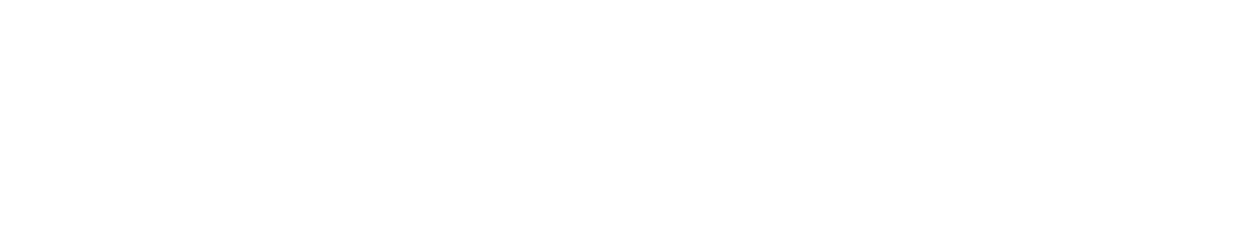

Why Supply Chains Always Win in the End
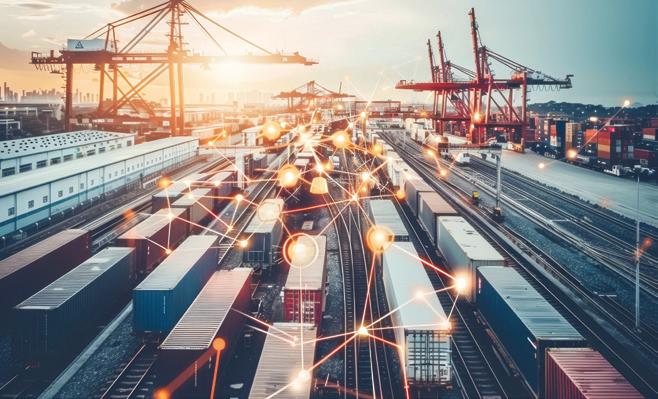
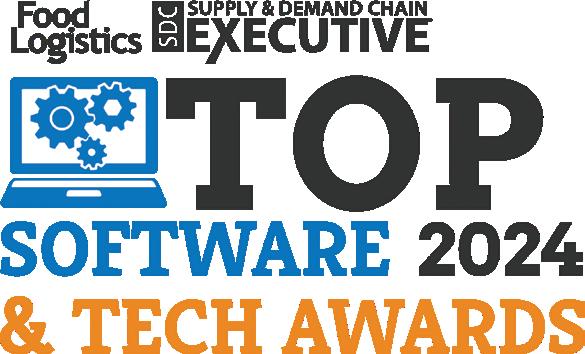

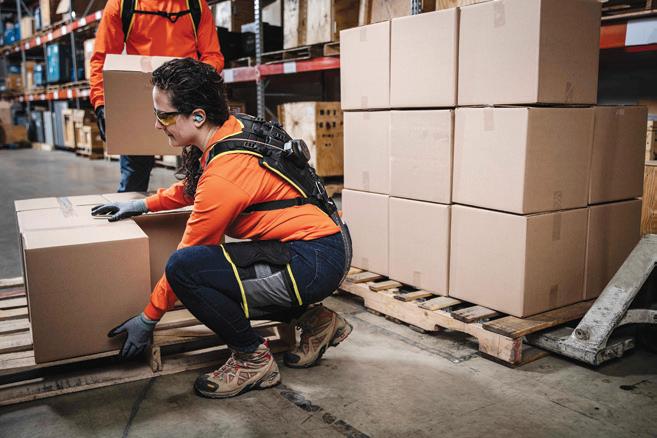
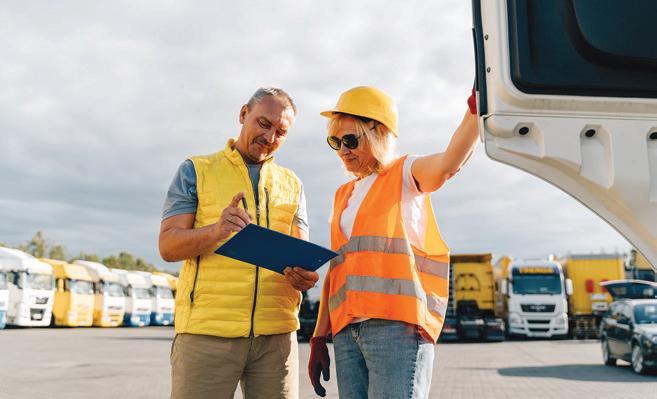
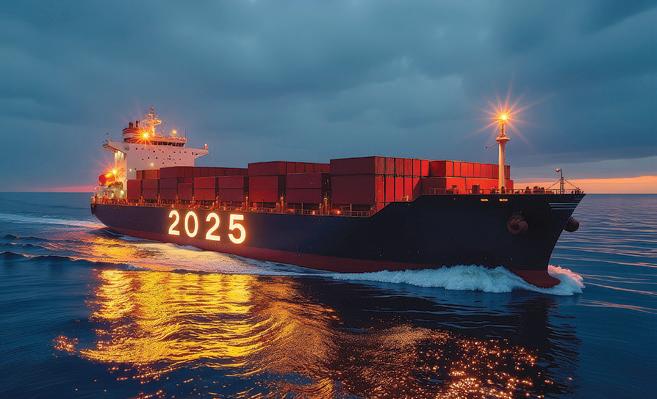
When it comes to new products, new innovations and new ways of doing business, the supply chain industry has it covered. But what some may forget is that it’s the superb supply chain leaders behind those new products, innovations and ways of doing business that turn ideas into reality. Take our Top Software & Tech award, for example. Close to 43% of submissions to this year’s award pertained to supply chain visibility solutions, followed by WMS/TMS software (23%), warehouse automation (18%), procurement/ERP software (12%) and robotics (4%). Fifty-five percent of the entries were enhancements to already existing solutions, where 45% came are new-to-market technologies. Further, 58% of submissions came from small businesses, under $50 million, and 42% came from Enterprises, over $50 million.
For our Top Tech Startup award, a majority of this year’s winners (49%) describe themselves as being in the artificial intelligence (AI) category, with AI-powered automation coming in at No. 2 (47% vs. last year’s 46%). And, winners range in
revenue from $1 million to $20 million-plus, with startups beginning operation as early as 2007.
This is on the heels of our coveted Women in Supply Chain award, which had 305 winners. And comes ahead of our other coveted award, Rock Stars of the Supply Chain, with nominations closing as of press time.
While these awards are designed to honor and celebrate the greatest of the great—whether they be startups, solutions or the executives behind both—they also exhibit the progress the supply chain space makes every year to make the world go ‘round.
These leaders embody passion, drive and mentorship. They’re championing efforts and initiatives to move product through the cold chain in a safer, more efficient manner. And I’m honored every day to facilitate an avenue for these leaders to be recognized.
Head to https://www.foodlogistics.com/awards to check out all of Food Logistics’ award.
And, we’re currently assigning out interviews and contributed content for 2025. Visit our digital media kit to download our editorial calendars (both print and digital).
Here’s to the supply chain leaders that make the world go ‘round. Thank you for ensuring safe food, for upholding regulations that protect the safety of our nation’s drivers and workers, for instilling quality values in the workplace, for protecting our farms and environment, and for being the example to today’s youth.
EDITORIAL
Editor-in-Chief Marina Mayer mmayer@Iron.Markets
Managing Editor Alexis Mizell-Pleasant amizell@Iron.Markets
AUDIENCE
Audience Development Manager ...............................Angela Franks
PRODUCTION
Senior Production Manager Cindy Rusch crusch@Iron.Markets
Art Director Flatworld Solutions
ADVERTISING/SALES
Brand Director Jason DeSarle jdesarle@Iron.Markets
Account Executive Brian Hines bhines@Iron.Markets
Account Executive Jay Gagen jgagen@Iron.Markets
Account Executive Mark Pantalone mpantalone@iron.markets
IRONMARKETS
Chief Executive Officer.......................................................... Ron Spink
Chief Revenue Officer Amy Schwandt VP, Finance Greta Teter VP, Audience Development Ronda Hughes VP, Operations & IT Nick Raether VP, Demand Generation & Education Jim Bagan
Corporate Director of Sales Jason DeSarle
Brand Director, Construction, OEM & IRONPROS Sean Dunphy
Content Director Marina Mayer Director, Online & Marketing Services Bethany Chambers Director, Event Content & Programming Jess Lombardo
CIRCULATION & SUBSCRIPTIONS
201 N. Main St. Ste 350, Fort Atkinson, WI 53538 (877) 201-3915 | Fax: (847)-291-4816
circ.FoodLogistics@omeda.com
LIST RENTAL
Sr. Account Manager Bart Piccirillo | Data Axle (518) 339 4511 | bart.piccirillo@infogroup.com
REPRINT SERVICES Brian Hines (647) 296-5014 | bhines@Iron.Markets
Published and copyrighted 2024 by IRONMARKETS. All rights reserved. No part of this publication may be reproduced or transmitted in any form or by any means, electronic or mechanical, including photocopy, recording or any information storage or retrieval system, without written permission from the publisher.
Food Logistics (USPS 015-667; ISSN 1094-7450 print; ISSN 1930-7527 online) is published 5 times per year in March/April, May/June, July/August, September/October, and November/December by IRONMARKETS, 201 N. Main Street, Fort Atkinson, WI 53538. Periodicals postage paid at Fort Atkinson, WI 53538 and additional mailing offices.
POSTMASTER: Send address changes to Food Logistics, P.O. Box 3605, Northbrook, IL 60065-3605. Subscriptions: U.S., one year, $45; two years, $85; Canada & Mexico, one year, $65; two years, $120; international, one year, $95; two years, $180. All subscriptions must be paid in U.S. funds, drawn from a U.S. bank. Printed in the USA.
N. Main Street, Fort Atkinson, WI 53538 (800) 538-5544 •
Delivering Freshness Every Step of the Way
DID YOU KNOW? Every year, 14% of food produced is lost between the time it is harvested to when it hits store shelves.
At Trailer Bridge, we understand the importance of maintaining the quality and safety of your products throughout the supply chain. That’s why we focus on delivering every shipment to its final destination on time and in peak freshness - offering you peace of mind and a seamless experience.
Whether it’s produce or any other type of freight, we give you the power to take what you need for your freight’s supply chain from a single-source transportation provider.
DeltaTrak launched the UBQ Network, an all-in-one platform tailored for the North American produce and grocery markets. This digital marketplace initially connects 25 leading service providers with 5,000 North American and 25,000 global customers to simplify cold chain management, ensure regulatory compliance and enhance sustainability
“We created the UBQ Network to meet the changing demands of the produce industry, ensuring that even the most demanding produce categories arrive on time in optimal condition to maximize consumer satisfaction,” says Karl McDermott, chief SaaS officer of UBQ Network. “By addressing these new challenges, our platform not only reduces waste but also supports sustainability goals and positively impacts costs and working capital—a key consideration for executives in the produce industry.”
Scan the QR code to learn more https://foodl.me/lboy1el2
Many thefts go unreported or are reported too late to help recovery efforts. There’s a growing push for standardized, industry-wide reporting systems that would allow for quicker dissemination of theft information. Increased data sharing between companies, industry associations, and law enforcement agencies could help identify patterns and hotspots more quickly.
Danny Ramon, intelligence and response manager at Overhaul, explains that one of the biggest challenges in combating cargo theft is the lack of comprehensive, timely data.
Food Logistics ’ and Supply & Demand Chain Executive ’s 2024 Top Tech Startup award highlights top software- and technology-based startups in the supply chain and logistics industry.
Today, the logistics industry faces many challenges that affect efficiency, transparency and cost. This award showcases those startups making a difference in the supply chain space. Meet the winners.
Scan the QR code to learn more https://foodl.me/osebwvsk
The rise of strategic theft highlights the need for more robust verification processes for carriers and drivers. This includes thorough vetting of new carriers, implementing multi-factor authentication for digital platforms, regular audits of existing carriers, and training shipping facility staff to spot red flags.
Scan the QR code to learn more https://foodl.me/ne4m9qle
The latest PwC Global Workforce Hopes and Fears Survey paints the picture of a workforce that is open to the future and new ways of working, however, present-day pressures are clouding their perceived optimism toward change. This juxtaposition needs to be balanced with leaders trying to keep their companies economically viable over the long term, especially in the face of immense competition and technological evolution.
From a business standpoint, Jon Bernstein is VP of product management at Motus, says it makes sense. As technology becomes increasingly important across all aspects of our lives, those who drive for work will increasingly expect their employers to provide modern technological tools that enhance their experience.
Scan the QR code to learn more https://foodl.me/ckcwlyi3
Tejas Rane, VP of operations, Eden Green Technology, explains that the American fresh produce supply chain is out of balance. Most crops can only thrive in a specific region or climate. For instance, Arizona and California account for nearly 90% of all leafy greens grown in America by weight while others rely heavily on overseas supplies of certain fruits and herbs to keep grocery shelves stocked.
Investing in regional solutions through new forms of technology and streamlined distribution is all about access, but also, awareness. A fresher, more reliable supply can and should alter customer expectations around what goods are affordable and readily available for them and their communities. Expanding access is no small feat, but by considering each step from farm to shelf to simplify a crop’s journey, we can begin to envision, build, and maintain a more sustainable food system for all.
Scan the QR code to learn more https://foodl.me/51378lgi
Boplan introduced the Boplan Impact Calculator, an online calculation tool designed to empower safety coordinators, facility managers, and health, safety, and environment (HSE) professionals to accurately assess the impact resistance required for their workplace safety and collision protection equipment.
“At Boplan, safety is our top priority, and the Boplan Impact Calculator is the latest example of our commitment to providing innovative solutions to protect lives and assets. With this user-friendly tool, our customers can confidently take steps toward a safer and more secure workplace,” says Xavier Ramon, CEO of Boplan.
Scan the QR code to learn more https://foodl.me/8nyvujxo
@A Stockphoto.stock.adobe.com
Three transportation company founders, friends, and mothers— Sharon Siar, VP and CFO of Talon Freight Services LLC; Nicole Glenn, founder and CEO of Candor Logistics Management; and Kristy Knichel, president, CEO and owner of Knichel Logistics— joined forces to create Gift of Freedom, a forum that partners with a referral network of organizations and counselors to provide specialized care and rehabilitation for victims of sex trafficking.
“Numerous organizations save trafficked children from their abductors and abusers. However, after a rescue, there are not enough facilities or mental health professionals available to provide counseling services. As a result, many victims return to the streets because it’s all that they know,” Siar says. “We started Gift of Freedom to focus on survivors and help them to reclaim and restart their lives.”
Scan the QR code to learn more.
https://foodl.me/rgzz1hug
The U.S. container trading market is experiencing heightened volatility due to several influencing factors. The recent strikes at East Coast ports have left a lasting impact on supply chains, while focus shifts to the U.S. elections.
“The recent strikes may have ended, but the storm is far from over. With unresolved issues surrounding automation, we are on the brink of another disruption come January 2025,” says Christian Roeloffs, co-founder and CEO of Container xChange. “Given the unresolved issues around automation, I believe there are strong chances of another disruption in January. The unions strongly oppose any form of automation, and this unresolved matter raises the likelihood of another strike in January.”
Scan the QR code to learn more.
https://foodl.me/3n6xpp8z
Samsara Inc. launched its Drowsiness Detection feature into general availability, using Samsara’s comprehensive artificial intelligence (AI) models—trained on its large-scale dataset—to proactively detect when signs of drowsiness occur. Then, it triggers real-time in-cab audio alerts for drivers, while notifying managers via text or email to triage fatigue-related events in the moment.
The Drowsiness Detection feature provides insights that can be viewed as aggregated reports within the Samsara Platform, allowing managers to analyze patterns of fatigue across their fleet, focus on driver coaching, and ultimately reduce drowsy driving to improve road safety.
Scan the QR code to learn more.
https://foodl.me/mf195dz7
Continuous education in logistics is essential for professionals aiming to stay competitive and relevant. Food Logistics details how ongoing education helps professionals keep pace with new trends, tools and best practices.
Whether through formal education, certifications or on-the-job training, continuous education empowers logistics professionals to drive efficiency, improve decision-making and contribute to the overall success of the supply chain.
Scan the QR code to learn more. https://foodl.me/19ezn6we
As devastating and cumbersome as some of these disruptions can be, the supply chain always wins in the end.
What a time to work in the supply chain industry. From port strikes and rail strikes to environmental, social, governance (ESG) regulations, electrification mandates and natural disasters shutting down major roads and ports, it’s a wonder any food and beverage moves through the cold chain.
But have no fear, it’s not all doom and gloom. Every disruption or hiccup in the cold food chain proves to be a lesson learned with emerging technologies, additional safety and security measures and more. And, as devastating and cumbersome as some of these disruptions can be, the supply chain always wins in the end.
Case in point: Motive’s Holiday Outlook Report shows optimism in the
transportation and logistics space, with moderate growth to return in the first quarter and long-term growth trends of 5.7%, year over year, to be restored by the end of 2025.
Transborder freight between the United States, Canada and Mexico experience a slight uptick across all modes, according to a report released by the United States Department of Transportation’s Bureau of Transportation Statistics.
A return to consistent decreases in fuel prices remains the biggest factor in better market conditions for carriers, according to FTR’s Trucking Conditions Index.
And, online grocery in the United States experienced robust growth in Q3, with total sales rising by 13.8% to $27.4 billion
compared to $24 billion for the same period in 2023. This increase was largely propelled by significant year-over-year growth in delivery, according to a report powered by Brick Meets Click and Mercatus.
See? Not all doom and gloom.
Here’s a breakdown of Top 6 trends to watch in 2025.
As of press time, the 47th President of the United States will have been named. And, while both parties provide opportunities and challenges to the supply chain space, the common denominator is that regardless who fills the presidential seat, economic uncertainty remains.
Cost reduction, for instance, remains the No. 1 priority, “but it’s not affecting every industry equally,” says Jenny Vander Zanden, COO at Breakthrough. “We’re seeing industries like durable goods manufacturers—think building products and automotive suppliers—facing more challenging economic conditions than others because of energy and raw material costs and rising interest rates. This adds an extra layer of complexity to their decision-making and makes transportation cost reduction that much more important for these shippers.”
“On top of that, ongoing political dynamics, particularly with China, have manufacturers rethinking their supply chain strategies and footprints, balancing operations internationally and domestically,” Vander Zanden adds.
Wha’s more, financial and economic worries are weighing heavy on the minds of food and beverage business owners, according to an Expert Market report sponsored by Toast.
“This could indicate that a period of inflation in the United States, initiated by COVID-19, may well have impacted small businesses in this industry. Though inflation peaked at 7% in 2021 and has since decreased to 2.97%, it is yet to reach prepandemic levels of around 1.9% in 2018,” the study reveals.
Despite this, predictions for 2025 suggest that concern about economic uncertainty will drop from 20% to 16%.
“As our research has shown, these have been tough times for business owners in the food and beverage market,” says Expert Market’s editor, Chris Maillard. “Inflation has been particularly difficult to deal with, and in a sector that is particularly reliant on energy-intensive kitchen equipment and the rental of prime sites, the rise in these bills has been tricky too. It’s great to see that optimism is still alive, though, and the smarter operators have dealt with the squeeze by making processes and systems leaner and more efficient, which will help them bounce back more quickly as the economy picks up.”
A report from Sphera shows that more than one-third (36%) of the financial risk notifications warned of worsening revenue and growth outlook. High inflation rates eroded suppliers’ purchasing power, with insolvency under self-administration going
@reshidea.stock.adobe.com
Supply chain experts say 2025 will bring a mixed bag of both opportunities and challenges.
up 23% and bankruptcies increasing 42%. Additionally, site relocations or closures increased by 26%.
“Sphera’s Supply Chain Risk Report shows that a broad range of risks, increasing ESG regulations and compliance failures can stress businesses,” says Paul Marushka, Sphera’s CEO and president. “Risk exposure is dynamic, and constantly evolving supply chain risks cause ever-increasing market volatility.”
From artificial intelligence (AI) and machine learning (ML) to data analytics, transparency, visibility, sustainability and electrification, the digitization of supply chains is real life.
That’s because shippers want more agile and resilient cold chains.
Yet a Tive study found that 47% of companies don’t have access to real-time technologies to monitor their shipments, but 75% of respondents say they’re investing in technologies to support supply chain/shipment visibility.
“In today’s complex global marketplace, real-time visibility is the holy grail for food shippers and their providers. It’s no surprise that 75% of leaders are investing in real-time visibility as a focal point for their broader digital transformation strategy. End-to-end monitoring—especially of temperature, light exposure, and location—is crucial for ensuring product quality, minimizing food waste, reducing excursions, and improving
delivery efficiency,” says Krenar Komoni, Tive founder and CEO.
Predictive analytics remains essential for demand forecasting, route optimization, inventory management, and automated decision-making.
“[These technologies are] already deeply embedded in procurement operations at large shippers and brokers, especially in perishable freight. In the coming year, these tools will become more feasible and level the playing field for operations of virtually any size, which is important in food distribution, where you have a lot of small carriers,” says Jeff Clementz, CEO and president, DAT Freight & Analytics.
“The differentiator in predictive analytics is information. The best analytics services have the most comprehensive data sets in addition to delivering customer service and technical support.”
More agile and resilient cold food chains also help reduce carbon footprints, expedite recovery from route disruptions and provide more accurate ETAs, says Margaret Selid, senior product marketing manager at project44.
“As the industry continues to move in this direction, we will see the adoption of technology increase exponentially in the next year,” she adds.
2025 will also bring an increased use of telematics and digital services for carriers and shippers alike, says Alice DeBiasio, VP and general manager, truck trailer Americas and digital solutions, Carrier Global Corp.
“If you haul food, pharmaceuticals and
AI, machine learning, and GenAI are considered to be top digital supply chain investment priorities.
other high-value, high-demand perishable loads, you want to know when there’s a deviation from temperature setpoints or a low battery or fuel level,” DeBiasio says. “Telematics on the TRU can notify you when something is happening inside the vehicle, where the freight is. And it can take a step further by helping you proactively assess and schedule the service you need with a qualified dealer.”
And, the next generation of transportation management systems (TMS) “are leveraging AI and machine learning to build systems and platforms that drive higher productivity and efficiency,” says Rishi Mehra, VP of commercial mapping and routing technology at Trimble. “A 2023 survey about what carriers were doing to ‘weather the storm’ showed companies were (and still are) highly focused on automating manual tasks, reducing paperwork and manual documentation, optimizing load scheduling and routing systems, and streamlining other areas of their business.”
Data is also supporting the emergence of emerging technologies, with AI at the forefront, Mehra says.
“We already see AI dramatically changing the transportation industry, and the next five years will be monumental—especially when it comes to safety, operations optimization, efficiency and productivity. AI-powered video systems are already enhancing safety by detecting hazards on the road, analyzing and predicting risky driver behavior and alerting drivers to take
preventive action,” Mehra adds.
New emissions standards for heavy-duty trucks are accelerating the switch to more emission-friendly vehicles, Mehra adds, “with forensic carbon accounting and measurement a potential legal necessity for shippers and carriers. Hurdles such as mileage range and charging infrastructure are among the limitations preventing fleets from greater adoption of electric vehicles.”
This all leads to further compliance measures and regulations surrounding ESG.
“The ESG category of risk is important to watch as the U.S. and the EU have concurrently introduced legislation to combat environmental and human rights issues in supply chains and many of the proposed changes, like the EU Deforestation Regulation for example, are expected to impact critical products like palm oil and cocoa,” says Jena Santoro, senior manager of global risk intelligence at Everstream Analytics. “These regulations come with compliance requirements that could increase operating costs for F&B companies and run the risk of reputational disruptions if companies are unable or unwilling to adhere.”
Emissions measurement is also becoming increasingly important.
“Since one of the largest contributors to many companies’ carbon footprint is their Scope 3 supply chain emissions,
companies will have no choice but to implement stronger reporting processes and technology to help manage their carbon footprints,” says Selid. “As emissions reporting becomes mandatory, consumers are also increasing pressure on their favorite brands to deliver on their sustainability promises. More than half of consumers plan to prioritize brands that demonstrate a commitment to sustainability during their holiday shopping this year. In 2025, brands that don’t make progress toward their goals will fall behind competitors who are actively working to reduce emissions.”
The No. 1 issue facing the freight brokerage industry is cargo fraud, a growing epidemic that’s costing the industry over a billion dollars on an annual basis, according to Chris Burroughs, president and CEO of Transportation Intermediaries Association (TIA).
“The types of fraud take many forms, including cargo theft, identity theft, unlawful brokerage activities, etc. Additionally, the industry is hampered in the motor carrier selection process as 92% of motor carriers are unrated due to an antiquated safety rating process. This lack of clarity from the Federal Motor Carrier Safety Administration (FMCSA) potentially allows unsafe carriers to continue to operate on the nation’s highways and creates confusing in the selection process leading to less safe roads and frivolous lawsuits,” says Burroughs.
CargoNet, a Verisk business, recorded 771 theft incidents in Q2 of 2024, representing a 33% increase compared to the second quarter of 2023. However, theft activity decreased by 10% from all-time highs established in Q1.
The report also shows behavioral shifts in the country’s most prolific organized cargo theft groups operating in Southern California. Across the board, these groups evolved to be more discriminating in their shipment targets, stealing high-value freight
Meanwhile, an Overhaul report recorded a 49% surge in cargo thefts first half of 2024 compared to the same period in 2023, with the average loss per incident skyrocketing to $115,230, an 83% jump from the previous year.
“Inventory replacement costs for shippers and insurance costs for carriers are just two examples of the negative impacts of freight fraud. Across the industry, shippers, brokers and carriers are seeing a wide range of fraud instances,” says Mehra. “In addition, food fraud impacts an estimated 1% of the global food industry at a cost as high as $40 billion a year, according to the Food and Drug Administration. Product safety, supplier safety and transportation safety are of the utmost importance in reducing fraud in the supply chain.”
Nearshoring has become a go-to strategic approach to supply chain optimization for many U.S. cold food processors and distributors.
For the first time in nearly 20 years, the United States imports more from Mexico than China, with Mexico comprising 16% of total U.S. trade in October 2023 compared to China’s 12.7%.
A study by Flatworld Solutions reveals a significant and sustained increase in interest in manufacturing in Mexico over the past five years as a result of trade policies, labor costs, and supply chain considerations driving the growing interest in manufacturing in Mexico.
The proximity to markets also remains one of the main benefits of nearshoring for the food and beverage industry. Alan Bebchik, country manager for Nowports, outlines in this expert column that “businesses can readily reach new markets and customers by moving operations to a nearby nation without incurring significant transportation expenditures. Businesses that depend on perishable goods and need to maintain the quality and freshness of their products may find this to be very beneficial.”
“As global disruptions continue to impact shipping lanes, I predict nearshoring and supplier diversification will grow since these strategies can help brands avoid massive disruptions. For brands looking to avoid compounding impacts from multiple disruptions at once, bringing manufacturing closer and diversifying sourcing can help reduce pressure on vulnerable or recovering supply chains,” adds Selid.
What’s more, “both severe weather and regulatory changes could disrupt the sourcing continuity of critical food and beverage inputs due to supply shortages, impacting production of end-user products,” says Santoro. “Lastly, when supply shortages complicate or disrupt sourcing efforts, countries have historically engaged in more trade protectionism to safeguard domestic supply for consumption.”
Like the saying goes, when it rains, it pours. Such is the case for supply chain disruptions, as overlapping incidents such as labor strikes and natural disasters continue to plague logistics organizations.
For instance, on Aug. 22, Canadian National and Canadian Pacific Kansas City Southern shut down operations, locking out 9,000 members of the Teamsters union who operate the trains. These two companies account for an estimated 90-95% of all rail shipments in Canada, meaning disruptions can have widespread effects on supply chains across North America.
The Maritime Employers Association announced a three-day strike at two terminals, beginning Sept. 30, affecting close to 350 members.
Close to 45,000 dockworkers at 36 ports along the East Coast went on strike as a result of the International Longshoremen’s Association (ILA) and United States Maritime Alliance failing to reach an agreement prior to the Oct. 1 expiration date.
Not to mention disruptions resulting from drought impacts on the
Panama Canal, geopolitical crises in the Middle East disrupting trade through the Red Sea, impacts and recovery efforts from Hurricane Helene and more.
“When these risks take place concurrently, as has also been the case this year, global supply chains experience an unprecedented level of chaos,” says Santoro. “Vessels blocked from transiting the Suez Canal, for example, had to absorb the added time and costs of diverting around the southern tip of Africa, while still facing an uncertain arrival at U.S. East and gulf coast ports amid looming full-scale port strikes. The main challenge to ensuring continuity of supply chains is in mitigating the scale of disruptions when alternative options are not necessarily readily available due to competing risks.”
Here’s a brief overall outlook into 2025.
of transportation
Overall, industry experts say the State of Transportation deems a positive outlook for 2025. Transportation will be characterized by a complex interplay of labor dynamics, regulatory pressures, technological advancements and economic conditions, Burroughs says. And, the global container shipping industry continues to witness an increase in freight demand for U.S.-bound shipments.
State of software and technology
Emerging technologies, like AI-powered insights, cloud-based solutions, traceability functionalities and more are critical for improving supply chain agility and resilience. As detailed earlier, the digital shake-up is here and ready to transform the cold food chain.
That’s why, AI, machine learning, and generative AI (GenAI) are considered to be top digital supplychain investment priorities, according to a survey by Gartner, Inc. And, to enhance efficiency and improve service, shippers are increasingly leveraging advanced technologies, Burroughs says.
ESG strategies will no longer be optional for businesses. And, over the past five years, pressure from investors to improve supply chain sustainability has grown
by 25%, making it the fastest-growing driver of sustainability efforts, according to a new report from the MIT Center for Transportation & Logistics (MIT CTL) and the Council of Supply Chain Management Professionals (CSCMP).
Supply chain experts say 2025 will bring a mixed bag of opportunities and challenges
Regardless of the challenges many of today’s cold food chains face, supply chains always win in the end.
Go to https://foodl.me/y8yg4ws6 to read the remainder of this article along with exclusive interviews detailing the State of the Supply Chain Industry in 2025.
With a world-class labor force, fast turn times, superior customer service, and quick connections to major roads and rail hubs, the Port of Long Beach is the premier West Coast gateway for trans-Pacific trade.
On the brink of 2025, third-party logistics (3PL) providers will find themselves at the center of an industry thrust into revolution. As businesses lean on 3PLs to streamline operations, technology adoption, rising consumer expectations, sustainability pressures and an unpredictable global market will influence the path forward.
Here’s a look at the trends shaping the future for 3PL providers, the likely challenges they will face and how providers can position themselves for long-term success.
The rise of technology in logistics is nothing new, but 2025 could bring a new wave of adoption for 3PLs. Automation, data analytics, AI-driven decision-making, and tracking technologies will continue to grow to support compliance with regulations like FSMA.
Mathew Moore, VP of market development at Americold, explains that AI and automation will continue on as strong areas of focus to drive efficiency at a lower cost.
“Adoption of AI has been relatively slow in temperature-controlled warehousing, mostly due to lack of understanding of what it is and what it can
actually do,” says Moore. “That is all changing pretty rapidly and we anticipate adoption begin exponentially increasing in 2025 as companies re-assess all aspects of their business through an AI lens.”
Similarly, Radhika Mulastanam, director, international services at AFS Logistics, says 3PLs will be defined by this AI technology, describing that, “The adoption of AI technologies (at least for the large companies) will help drive efficiencies in their processes, warehouses and other operations. The 3PLs that are likely
to stand out are those that can not only provide better solutions, but also exhibit the expertise needed to manage them. We see instances, far too often in my opinion, where companies that provide AI solutions struggle with the front-end folks being unable to explain the features and functionalities.”
Even in areas for upskilling where e-learning helps organizations provide cost-effective training tailored to their industry and individual needs, explains Mulastanam. Educating employees will help bridge the skills gap that’s seen quite
often and also helps address the demand for niche expertise in business areas.
Specific to the cold chain, 2025 will bring continued growth in temperature-controlled technology.
As Sara Stickler, CEO and president of the Global Cold Chain Alliance (GCCA), explains, strong year-on-year increase in demand for cold storage is expected to continue well past 2030, with the industry responding with substantial investments into the construction of new sites as well as the expansion and modernization of existing facilities.
“Another key trend in 2025 will be continued investment into cold store energy efficiency, helping refrigeration-based businesses reduce exposure to volatile energy costs. We can expect continued focus on energy efficiency measures such as improvements to insulation, refrigeration system data collection and analysis, and on-site renewable energy generation (mainly roof top solar),” says Stickler.
Meeting consumer expectations for speed and transparency
E-commerce growth continues to redefine consumer expectations, with buyers now demanding near-instant deliveries, real-time tracking and a seamless purchase experience.
As markets and consumer patterns change, Stickler explains the necessary evolving of services to be a full supply chain solution for customers. This includes increased involvement in e-commerce to support customer needs.
“Fluctuations in consumer demand in 2024 have brought the pressures associated with volatility in volumes, but if inflation continues to decline and consumer confidence rebuilds the food industry, as a whole, can look to greater stability,” says Stickler. “Overall, the increased importance placed on supply chain resilience by the food industry following the disruptions of the past five years is set to continue.”
In 2025, 3PLs will face even greater pressure to provide fast, reliable and transparent services.
“There have been multiple studies showing that e-commerce retailers
require three times as much total warehouse space as traditional warehouse clients. The big question is how fast will e-commerce continue to grow? On the retail grocery side, online shopping represents almost one-third of the $11.9 trillion in global consumer spend in this space, so it’s already a massive channel,” says Moore. “The next question is how much of the additional warehouse space needed will be outsourced? If the trend towards outsourcing continues on a similar path to traditional retail distribution and e-commerce growth continues to outpace store channels, then 3PLs stand to be big beneficiaries in the coming years,”—questions that may need to be examined sooner rather than later.
While 3PLs have ample opportunities for growth in 2025, challenges come and go every year.
Start with supply chain disruptions, for instance, which as Moore points out, are obviously problematic because (1) they’re unpredictable and (2) expensive to plan for or hedge against.
The incremental costs associated with
disruptions and labor shortages have to be passed on as quickly as possible. Moore says it’s when those costs are no longer able to be “priced in” that companies get squeezed and earnings suffer. Reducing exposure to labor disruptions through automation and AI will be a key focus area for companies with large workforces.
Managing labor shortages, cybersecurity and mitigating risks have been at the top of every 3PLs’ list after 2024s litany of disruptions.
Mulastanam outlines these two points as major concerns in 2025:
• Labor shortages. Lack of qualified candidates with the necessary expertise in different areas of the business will hinder the ability to grow. Without teammates taking on ownership, middle management and supervisors get sucked into micromanaging the day, leaving them with no time to work on strategy or handling customer expectations. This means focused, ongoing investment in training and skill building will be a huge challenge for companies.
• Supply chain resilience. Ongoing disruptions such as the recent East Coast port strike, geopolitical events and/or other natural or manmade disasters will be challenging to 3PLs and their ability to be agile and responsive to customer requirements. The best way to deal with this is to leverage technology to provide more real-time visibility and decision making at different levels, within reason of course. Diversifying sourcing strategies and managing the business effectively particularly in areas of risk management will also be a contributing factor in dealing with disruptions.
Challenges also stem from geopolitical issues including the outcome of the U.S. election and the policies put in place thereafter.
“With the 2024 Presidential Election in the United States, there could and will be considerable unknowns for some time about the full policy implications, as well as the impacts of the election result for the U.S. and global economies. At the same time, we can expect ongoing uncertainty in 2025 regarding international politics and the impacts of war and unrest on global supply chains. Extreme weather events will likely affect U.S. food supply chain operations, either directly or as a result of weather-driven disruptions in other parts of the world,” says Stickler.
Sustainability will remain a top priority as consumers, governments and stakeholders demand greener supply chains.
In 2025, 3PLs will need to demonstrate a commitment to environmental sustainability and adopt practices that reduce their carbon footprint. That, Moore says, starts with an approach from several different angles—three of which include fleet electrification, built environment and energy efficiency.
“3PLs will move more towards fleet electrification, especially as the technology is getting better and better, costs are coming down, and there are federal, state, and local incentives that help to
make the returns on investments better.
The built environment too will continue to decarbonize, whether that be through on-site renewable energy, community solar, further transitions to LEDs, incorporation of variable frequency drives on motors, improved roofing insulations, roofs moving to more white or pale colors to reduce heat island effect, smart building controls that really help manage the energy efficiency of sites. There will be more net metering down to the asset level, and we will see many more existing facilities closing the gaps to get green building and energy efficient building certifications,” explains Moore.
“Energy efficiency employee-led programs and energy waste walks have always been part of the 3PLs, and as we move into 2025, many 3PLs have 2030 decarbonization goals that will require increased skill sets and technology (acoustic imagers for leak detection, IR scans for thermal loss,) to identify energy losses and improve energy intensity,” adds Moore.
Utilizing the aforementioned AI tools and other technology might be the key to unlocking more efficient ways of meeting sustainability goals. Stickler says, expect
to see greater use of AI-driven innovations in, for example, refrigeration system monitoring and data analysis.
An actionable checklist for 3PLs, Mulastanam says, should include optimizing routes and modes, investing in fuel-efficient vehicles and alternative energy sources (not just for transportation but also in warehouses and distribution centers), including their supply chain network of suppliers and carriers in the quest for greater sustainability and always being transparent in their reporting, and above all, avoiding ‘greenwashing.’
The outlook for 3PLs in 2025 is both promising and challenging, and that’s to be expected. On the one hand, technology offers new ways to streamline operations and meet expectations, all while fostering sustainability growth. On the other, 3PLs will face growing demands for transparency and speed while navigating everything from regulations to labor shortages.
Success in 2025 will ultimately depend on doing what supply chains do best: adapt. Those providers who embrace technology, build resilient and sustainable operations, and stay aligned with evolving consumer demands will be best positioned to lead the future of logistics.
Footprint WMS will give you confidence to say “YES” to more customer requests, giving your business the ability to grow faster.
Built on a low-code platform, Footprint WMS is crafted uniquely for 3PL, cold storage, and pharmaceutical warehouses. It brings simplicity to complex processes, enabling you to easily handle intricate requests and workflows, ensuring reliable profitability and efficiency for your operations.
Just say “YES” to
• More configurability including an intuitive, role-driven interface.
• Streamline temperature control to avoid spoilage or contamination.
• Easier tracking and reporting to meet strict food safety standards.
• Improved space optimization without compromising product quality.
Take a look at the warehouse management software that will have you saying “YES” –today, tomorrow, and in the future.
From robotics and warehouse automation to procurement and enterprise resource (ERP) software, warehouse management systems (WMS), transportation management systems (TMS) and supply chain visibility solutions, the supply chain software and technology sector continues to boom.
Case in point: By 2026, 30% of enterprises will automate more than half of their network activities, an increase from under 10% in mid-2023, according to Gartner, Inc. And, composite artificial intelligence (AI) and supply chain data governance are the highest impact technology trends for supply chain planning leaders, as outlined in a separate Gartner report.
Additionally, more than three-fourths (83%) of industrial leaders are investing more in AI in 2024, up from 63% in 2023, according to an Augury study. AI aside, other emerging technologies and solutions continue to modernize many of today’s supply chains.
So, it’s no surprise then that automation, sustainability, smart technology, supply chain optimization and risk management were the major themes of this year’s Top Software & Tech award, presented by Food Logistics and Supply & Demand Chain Executive.
Fifty-five percent of the entries were enhancements to already existing solutions, where 45% are new-to-market technologies. Further, 58% of submissions came from small businesses, under $50 million, and 42% came from Enterprises, over $50 million.
This award is designed to showcase new-to-market and enhancements to existing software and technology solutions that provide automation, efficiency and visibility to the supply chain space. The new software/technology solution must have been introduced or gone through a major update between October 2023 to September 2024.
These new products and enhancements are upping the ante in modernizing how product moves through the chain.
Close to 43% of submissions to this year’s Top Software & Tech award pertained to supply chain visibility solutions, followed by WMS/TMS software (23%), warehouse automation (18%), procurement/ERP software (12%) and robotics (4%).
ORO Labs
www.orolabs.ai
Name of Solution/Technology: Procurement Orchestration Platform
Product Description: ORO Labs launched several enhancements to its procurement orchestration platform that leverage the latest advancements in GenAI to focus on simplifying the procurement intake process. The new GenAI-powered features employ natural language understanding and predictive analytics to enhance the user experience. Additional new features include:
Intent detection. When a user submits a request in natural language, ORO is able to determine a user’s intent and provide the most appropriate response, like initiating the most relevant workflow, providing a status update, or answering a question.
Category recommendations. Business users are often asked to categorize their requests according to the organization’s complex category tree. ORO is able to automatically map a natural language requisition to the correct category.
Buying channel guidance. ORO considers intent and category alongside things like role, region, and company policies in order to determine the best and most efficient buying channel for a particular request. The result is a vastly improved and dynamic user experience, faster processing, and less manual effort.
Supplier recommendation. ORO looks at a company’s preferred supplier list, past transactions, and performance data to suggest the best supplier(s) for a given use case. By doing this, ORO simplifies the selection process, minimizes the need to onboard and maintain new suppliers, and speeds up the requisition-to-pay process.
Smart PO/PR creation. ORO is able to create purchase requisitions and purchase orders by extracting key information from contracts and proposals, The result is a single or multi-line PR/PO that complies with business rules (i.e. CapEx, OpEx, Time-based).
Smart proposal reviews. ORO extracts data from vendor proposals and checks to ensure consistency with the buyer’s intent, buying channel, and category.
Torc Robotics
https://torc.ai/
Name of Solution/Technology: Torc Robotics Virtual Driver
Product Description: Torc’s Virtual Driver is designed for commercialization based on its singular, foundational knowledge of trucking companies’ complexities and needs. Torc collaborated with Aeva and others for sensors, Foretellix for virtual verification and validation and several additional partners, including Algolux, which Torc acquired in 2023 , to integrate cameras, long and short-range LiDAR, and long and short-range radar to detect its surroundings. This sensor suite uses each component’s strengths to provide a 3D picture of the environment, detect objects, and calculate the movement of vehicles around the truck for better prediction and decision-making. Torc’s advanced localization and prediction algorithms provide autonomous trucks with the data to determine the next safe move on busy and unpredictable roadways by planning and updating the truck’s location in real-time. Torc’s Virtual Driver also embeds safety into every aspect of its technology—aligning with USDOT and NTSB principles, creating a safer and more reliable ecosystem for transporting goods. These abilities transform off-the-shelf driver assist technology into true autonomy.
Trimble www.transportation.trimble.com
Name of Solution/Technology: Transporeon Visibility
Product Description: Transporeon Visibility is a state-of-the-art real-time transportation visibility solution designed to enhance the efficiency, security, and customer service of logistics operations across various transportation modes, including road, ocean, and air. This solution leverages advanced AI capabilities to provide precise shipment ETAs and integrates seamlessly with Trimble TMS applications and other visibility solutions. Key features and capabilities include:
Global end-to-end visibility. Comprehensive real-time visibility for all in-transit shipments across all modes of transport up to SKU (order item) level.
Real-time freight tracking. Live tracking and map display of vehicles and shipments, giving operators and stakeholders full control over their shipments. This real-time tracking helps eliminate delays caused by faulty addresses or vehicle license plates.
Accurate ETA predictions. Reliable estimated ETA predictions allow planners and operators to stay ahead of disruptions and proactively manage exceptions with automated triggers and customized sets of rules. This leads to cost savings by reducing demurrage and detention penalties, and optimizing the deployment of equipment and driver resources.
Data sharing and security. The solution ensures data security by sharing data only when consent is given, a vehicle is allocated, and data sharing criteria are met. This feature is particularly attractive for smaller carriers that need to use a single visibility tool regardless of multiple shippers’ requirements.
Wider business opportunities. Facilitates the expansion of carrier networks for shippers and provides visibility into the performance of those carriers.
Security and safety. Real-time visibility enables precise monitoring of shipment routing and location, addressing unexpected deviations and efficient resource allocation quickly.
Interconnected transportation modes. The solution covers intermodal visibility, including changeover points such as ports and airports where disruptions are more likely to occur. This visibility extends to intercompany flows when shipments transfer from one carrier to another.
Integration and deployment. Transporeon Visibility integrates seamlessly with Trimble TMS products such as TMW. Suite and Innovative, with additional integrations like TruckMate expected by the end of the year. This seamless integration allows carriers to automate their data sharing and network connectivity.
Enhanced efficiency. By automating transport processes and providing actionable analytics, Transporeon Visibility helps companies improve their logistics operations. The solution offers the highest ETA accuracy in the market, reducing check calls by up to 80% and increasing sales revenue by up to 2%.
Sustainability. The solution helps reduce empty miles by up to 10% and CO2 emissions by up to 7%.
Customer satisfaction. Real-time visibility improves customer satisfaction by enabling better communication and proactive problem management. Customized notifications keep all stakeholders informed about the status and progress of shipments.
Improved on-time delivery. Accurate ETAs empower users to better predict and anticipate in-transit issues.
ArcBest www.arcb.com
Name of Solution/Technology: Vaux Smart Autonomy
Product Description: Vaux Smart Autonomy is autonomous material handling technology that combines autonomous mobile robot (AMR) forklifts and reach trucks, intelligent fleet management software and remote teleoperation capabilities to autonomously handle materials movement within warehouses, distribution centers and manufacturing facilities while keeping humans in the loop. Here’s how it works:
1. WMS dispatches work to fleet management software.
2. Fleet management directs the vehicle to drive autonomously to a pickup destination.
3. Teleoperator is assigned a mission to pick materials.
4. Autonomy takes over, and the forklift self-navigates to the destination.
5. Teleoperator is assigned a mission to drop materials.
The forklifts and reach trucks move independently within the warehouse while teleoperators monitor and operate multiple vehicles in multiple locations from a remote location. Operators only have to step in when an AMR encounters a problem the autonomy can’t solve, or reaches its destination. The counterbalance forklift is used for trailer load and unload, cross-warehouse transfer and bulk storage, while the reach truck is used for rack pick and putaway. Both forklifts and reach trucks are equipped with advanced software, sensors and cameras that help the robots safely navigate warehouse facilities and create efficiencies in warehouse operations. Vaux Smart Autonomy uses state-of-the-art 3D perception technology to perceive its environment and optimize path planning in real time. Additional capabilities include advanced 2D barcoding functionality, cameras with barcode scanning capabilities and easy integration with customers’ WMS.
Datex
www.datexcorp.com
Name of Solution/Technology: Footprint WMS
Product Description: Datex Footprint WMS is a premier Software-as-a-Service WMS designed to empower cold storage warehouse operators with technology that can accommodate multi-temperature environments. Hosted on Microsoft Azure and fully powered by Datex’s Wavelength low-code application platform, Footprint offers intuitive drag-and-drop simplicity and zero downtime updates. Built for harsh environments, the mobile interface is highly customizable and easy to use, helping cold storage operators to achieve both operational efficiency and simplicity. Benefits include:
Scalability. Scales effortlessly with the growth of the business.
Visibility. Provides complete data transparency and total operational control.
Flexibility. Whether a company needs a simple solution or a complex setup, an intuitive drag-and-drop interface lets users tailor their instance without hassle.
Seamless integration. Footprint connects to critical business and supply chain systems, ensuring streamlined operations and maximum efficiency.
Footprint WMS seamlessly integrates to other systems, allowing for e-commerce, shipping and manifesting, EDI, and the latest technologies such as flexible automation, AI, and robotics. Footprint’s unique data and technology structure allows better data management, real-time visibility and the ability to meet rapidly changing needs with quick feature updates that don’t require massive system updates. Further, the company’s emphasis on usability during development translates to faster onboarding and intuitive operation by system admins and simplified mobile interface for warehouse associates. Other features entail restriction of inventory to specific temperature zones; stores inventory in primary or secondary locations; provides specific temperature-controlled functionality; enables catch/variable weight; captures temperatures; enables lot control and serialization and excels in managing multiple levels of package serialization and inventory aggregation. It offers detailed identification by genealogy, lot/batch, serial number, unit of measure, disposition, and historical activity trace.
Go to https://foodl.me/kmr2r068 to view the full list of winners.
Penske’s game-changing Catalyst AI ™ decision engine combs through billions of data points from hundreds of thousands of trucks so you can compare your fl eet to similar fl eets and gain insights to help manage your business like never before.
Kaleris www.kaleris.com
Category: WMS/TMS Software
Name of Solution/Technology: Kaleris TMS + YMS
Product Description: Kaleris TMS + YMS is a co mprehensive yard and transportation management solution, created by combining the CAMS Prospero Transportation Management system with the Kaleris yard management system. The former CAMS Prospero TMS, now Kaleris TMS, following Kaleris’ acquisition of CAMS Software , manages all aspects of trucking operations for grocery retailers and wholesalers, providing dispatch, backhaul, driver payroll calculation, and vehicle tracking for all inbound, outbound, and return trips. Electronic logging devices (ELDs) in the truck cab provide drivers with complete information for their shift, including destination information, turn-by-turn directions and remote re-dispatch information in the event of real-time changes. The ELD also tracks drivers’ Hours of Service to ensure compliance and for IFTA reporting. The Kaleris yard management system, formerly PINC, optimizes and streamlines yard operations for all types of yards, including finished goods and manufacturing sites. The Kaleris YMS provides real-time tracking and visibility of all assets within the yard, including trailers, containers, and equipment. It automates various yard processes, such as gate check-ins, trailer moves, and dock assignments, reducing manual intervention and improving efficiency. It also facilitates the scheduling and planning of yard activities, ensuring that resources are optimally allocated and operations run smooth.
Luma Brighter Learning
https://lumabrighterlearning.com
Category: Supply Chain Visibility Solutions
Name of Solution/Technology: Luma Navigator
Product Description: Luma Navigator is an advanced learning tool that harnesses data and multiple interaction types to create individualized coaching plans for each learner. By delivering just-in-time training through multiple types of interaction over a period of time, this technology helps build a meaningful connection between the driver and the driver’s manager. Luma Navigator brings in custom data from the fleet, FMCSA data on driver performance, telematic data from the trucks, workman comp data, etc., and then based on performance, assigns coaching plans to each individual, which includes different interaction types that can be automated or manually assigned on a cadence. Fleets can assign any type of AI-generated custom learning or choose one of Luma’s 1,300-plus microlessons. Key features include:
Live online synchronous instruction provides real-time, interactive learning experiences that allows for immediate feedback and personalized guidance.
Immersive learning experiences , or 2D learning experiences, create realistic scenarios that enable learners to see an actual environment that is meaningful to the fleet, leading to improved retention and performance.
Motivational surveys help identify individual learners’ goals, challenges, and preferences, allowing for the creation of tailored learning paths that optimize engagement and achievement.
Phone evaluations offer a personalized, one-on-one approach to assessing learners’ progress, providing targeted feedback and coaching that addresses specific areas for improvement, ultimately supporting individual growth and success.
Nulogy
https://nulogy.com
Category: Supply Chain Visibility Solutions
Name of Solution/Technology: Materials Management Capabilities
Product Description: Nulogy introduced new materials management capabilities within its two key products—the Supplier Collaboration Solution (Materials Visibility Module) and the Shop Floor Solution (Materials Ordering Tool)—to provide brand owners and their external supply chain partners with the resources needed to reduce material supply risks, ensure continuous operations, and take a collaborative, proactive approach to effective materials management.
The Supplier Collaboration Solution’s Materials Visibility Module is a materials monitoring report that can show the impact of material shortages on demand. This module provides a real-time view into the impact of material shortages and enables brands to proactively work with customers or suppliers to resolve potential issues. As a shared view, the data is available to both brands and external supply chain partners to enable rapid alignment and corrective action.
The Shop Floor Solution’s Material Ordering Tool streamlines and simplifies material ordering processes. It combines information on current inventory levels, received orders, work orders, and bill of materials to identify expected material deficits and provide material planners with all relevant information to make optimal material order decisions. Additional features and benefits include efficient material shortage identification, timely order recommendations and streamlined order creation.
ORTEC
www.ortec.com
Category: Supply Chain Visibility Solutions
Name of Solution/Technology: ORTEC Load Building and Final Mile Optimization Suite
Product Description: ORTEC Load Building and Final Mile Optimization Suite is designed to optimize load building processes and streamline final-mile delivery operations for companies operating in the supply chain and wholesale delivery sectors. Enhanced features include:
Dynamic load building. Leveraging advanced algorithms, the suite enables dynamic load building to create optimal load plans that account for various constraints, including vehicle capacity, delivery time windows, and product compatibility.
Multi-stop consolidation. Companies can consolidate multiple orders into efficient routes, minimizing the number of vehicles required for delivery and reducing overall transportation costs.
Real-time adaptability. The system can adapt to real-time changes in orders, vehicle availability, and traffic conditions, ensuring that load building remains optimized in dynamic operating environments.
Final-mile route optimization. Provides robust route optimization capabilities to ensure that final-mile deliveries are executed in the most efficient and cost-effective manner, considering factors such as traffic patterns and delivery time windows. Time slot management. Companies can efficiently manage delivery time slots, allowing for flexible scheduling based on customer preferences and operational constraints.
Dynamic dispatching. Enables adjustments to delivery routes based on changing conditions, ensuring timely and efficient deliveries.
ERP and TMS integration. Streamlines data flow and process alignment, enabling end-to-end visibility and control.
Real-time visibility. Offers real-time visibility into load building and final-mile operations, empowering companies with actionable insights for proactive decision-making and improved customer communication.
Performance analytics. Robust analytics and reporting capabilities allow companies to track key performance indicators, identify operational bottlenecks, and make data-driven decisions.
Cost analysis. Conduct comprehensive cost analyses of load building and final-mile operations.
Penske Truck Leasing
www.gopenske.com
Category: Supply Chain Visibility Solutions
Name of Solution/Technology: Catalyst AI
Product Description: Catalyst AI delivers real-time insights into fleet performance and optimization, and empowers fleet managers to make actionable decisions to optimize fleet performance using dynamic comparative data.
The first of its kind in the transportation industry, the platform entails a patent-pending algorithm that identifies the most similar fleets by evaluating key dimensions of fleet operations and composition. This process creates a unique “fleet DNA,” enabling highly customized operational KPI benchmarks tailored to each fleet’s specific performance needs. Catalyst AI empowers leaders to benchmark their fleets using apples-to-apples comparisons, unlock fuel efficiency opportunities, optimize fleet utilization, and improve business performance using targeted insights.
Rygen Technologies
www.rygen.com
Category: Supply Chain Visibility Solutions
Name of Solution/Technology: X1 Integrations
Platform-as-a-Service (iPaas)
Product Description: X1 is a cloud-native integration engine that empowers users to create and manage integrations faster and more efficiently, decreasing the level of involvement needed from IT resources. With a focus on user experience, X1 increases the speed and value of business integrations while reducing implementation time and cost for supply chain experts. It’s AI-enhanced platform allows for data-mapping with effortless diagnostics so users can implement integrations in days, rather than weeks or months. Key benefits are:
Interoperability across disparate systems. Supports a wide range of protocols and formats, enabling easy data transformation, and simplifying partner onboarding.
Visibility and traceability of transactions.
X1’s document-centric message processing provides a full lineage and audit trail of each transaction. Detailed event logging allows users to quickly identify and resolve bottlenecks.
Speed of integration and deployment. Operates without the need for developers or code deployment, thorough AI-assisted configuration, and instant scalability.
VIA Technologies, Inc.
https://viatech.ai/forklift-overview
Category: Supply Chain Visibility Solutions
Name of Solution/Technology: VIA Mobile360 Forklift Safety System
Product Description: The VIA Mobile360 Forklift Safety System is a multi-camera safety system that eliminates blind spots and increases visibility around the vehicle, simplifies fleet management, improves operator training and strengthens safety protocols. The system’s cameras detect pedestrians accurately, records video footage of each alert event, and configures work areas to track vehicle status and receive alerts when vehicles enter or exit designated zones. Additional features include:
Pedestrian detection. Smart AI cameras accurately detect people approaching the vehicle, minimizing alert fatigue and preventing accidents before they happen.
Dual alerts. With a detection range of up to 8 meters, audio and visual alerts deliver timely warnings when pedestrians are detected, which gives operators ample time to react to potential hazards.
Multiple camera configurations. Choose from multiple camera placement configurations with up to three cameras around the vehicle. This allows for flexible detection zone arrangement tailored to the work environment and specific detection needs.
Driver Safety System (DSS). Detects fatigue, smoking, or phone usage, prompting operators to take breaks while fostering a culture of care and safe driving practices.
vCare. This cloud-based online platform provides fleet operations data, driver information, and safety analytics such as vehicle usage and alert rates with a 24-hour trend chart.
Seatbelt Sensor. Detects whether the driver’s seatbelt is fastened or not.
Wireless Speed Sensor. Tracks vehicle speed and direction to ensure each alert is accurate and necessary.
BY ALEXIS MIZELL-PLEASANT, MANAGING EDITOR
In the warehouse, robotics extend a helping arm to fill labor gaps while wearables transform processes for the better.
In the frozen food sector specifically, robots are proving to be invaluable. Many of these systems operate flawlessly in sub-zero temperatures. Automated guided vehicles (AGVs) and robotic arms navigate through freezer aisles, retrieving and transporting products with precision.
Mark Richardson, CEO at Ocado Intelligent Automation, says temperature-controlled storage can hinder human workers, requiring them to take breaks for their own safety. This is where robotics has a niche need to operate in stride with the human workforce.
Heather Chapman, head of ergonomics at Soter Analytics, says employers must empower workers with tools to understand their movements and individualized safety risks.
“After all, all bodies are different. There’s plenty of technology, like computer vision or wearable sensors,
out there that can help employees understand how they are increasing their risk of injury before they get hurt. This is an easy way to give employees more oversight when it comes to how they’re moving their bodies on the job, without making them feel psychologically unsafe,” explains Chapman.
Collaborative robots (cobots) work alongside human employees, enhancing productivity and streamlining workflows. In tasks like order picking and packing, cobots contribute to increased accuracy and speed, mitigating the impact of workforce shortages once again.
ABB describes how industrial collaborative robots are bridging the gap by providing ease-or-use for those non-robotics specialists. This is key when considering the introduction of technology to a workforce that may not be in the midst of upskilling yet.
Dave Food, head of product supply chain at Board International, predicts that in 2024, supply chain companies will need to reevaluate training and upskilling strategies, as the shift from manual to digital fulfillment continues to accelerate.
From smart glasses to exoskeletons, wearables are enhancing the capabilities of human workers.
According to ProGlove research, over half (56%) of warehouse and logistics leaders are currently utilizing industry wearables to improve efficiency in the warehouse.
@amorn.stock.adobe.com
“The potential is huge for human-machine collaboration,” says Stefan Lampa, CEO of ProGlove. “Undoubtedly, the number of organizations relying on automation will increase in the coming years. It’s an enormous undertaking that will bring with it a significant change in people’s work. However, there are many different boxes to be ticked in a warehouse’s total operations. As a result, the mental acuity, agility and problem-solving skills human workers provide will have a significant part to play for years to come. Over the next decade, connecting those human qualities with the power of automation technologies will be a key part of success.”
Smart glasses, another example, provide real-time information to warehouse workers, improving order accuracy and reducing errors.
Brian Calus, director of sales at Vuzix Corporation, says smart glasses allow technicians to tap into an unlimited set of resources by communicating their situational point-of-view with remote experts and receive instruction, in real-time, to solve issues in the field.
Whether it be through robotics, wearables or a combination, technology is revolutionizing the warehouse sector and filling critical labor gaps.
Go to https://foodl.me/ zynbtkte to read the remainder of this article.
Overexertion may cause workers to suffer a number of musculoskeletal disorders (MSDs) that impact their quality of life, and in some cases, their ability to continue working. The injuries also take a toll on companies, as more than 264 million workdays are lost each year because of back pain. As companies seek ways to rotect workers and improve operational efficiency, wearable technology—specifically exosuits—is emerging as an innovative solution to mitigate these risks.
MSDs are among the most common workplace injuries in the logistics and warehousing sectors. These injuries don’t just come from moving heavy items. Much of the strain comes simply from supporting the worker’s own upper body weight through many high-frequency bend and lift cycles. Employers who adopt safety and health programs can expect reduced workplace injuries and associated costs such as workers’ compensation, medical bills, and productivity losses.
Many companies in the logistics and warehousing sectors are turning to wearable technologies like exosuits to protect the well-being of workers. The exosuit is an innovative wearable technology designed to assist with demanding physical labor. They offer physical support by reducing the strain from repetitive tasks, such as lifting or bending.
Studies and user surveys have shown that exosuits can reduce worker fatigue and muscle strain by up to 40%. Some lightweight exosuits can mimic biological back muscles, offloading physical stress from crucial muscle groups and allowing workers to perform repetitive tasks with less strain and fatigue. For warehouse workers, wearable exoskeleton technology should feature a lightweight, non-motorized design that provides ergonomic support without restricting workers’ movement or requiring additional power sources and weight. These types of exosuits use passive mechanisms, such as elastic bands, and have been shown to be
as effective—and often more effective—as motorized models in offloading strain from crucial muscle groups, especially the lower back.
Exosuits reduce muscle fatigue and the risk of injury, and their lightweight nature means workers can wear them comfortably. If the exosuit has a low-profile design, as some do, they can even be used with other PPE.
These devices have also been shown to positively impact productivity.
Enhanced safety and increased productivity make wearable technologies like exosuits an investment worth exploring for many companies. The benefits of fewer claims in worker compensation and productivity gains help companies maintain efficiency in labor-intensive sectors.
While exosuits offer clear bene fits, their success ful integration into the operations of workers in the field depends on careful planning, partic ularly regarding training and fit for maximum benefit. To successfully im plement wearable technology, it is crucial to provide ongoing support at various stages of the implementation process, including evaluation and training on its proper use.
while reducing costs, the role of technologies like exosuits is likely to expand
Exosuits offer an ergonomic solution to provide optimal comfort, efficiency, and safety for workers, unlocking heightened overall performance, superior outcomes, and a more satisfied workforce.
Go to https://foodl.me/ os00ztml to read the rest of this column.
JENNIFER
Helps
Helps
As companies continue to face pressure to improve performance
Looking ahead to 2025, the global ocean freight market shows no signs of slowing down. From ongoing disruptions in the Red Sea and the Panama Canal, to broader geopolitical tensions and shifting global trade patterns, shippers face more complexities than ever.
Here are five predictions for how the ocean freight industry will play out in 2025. Supply and demand dynamics continue to evolve. The big picture of supply and demand is a cautiously optimistic prediction: supply and demand remain relatively equal heading into 2025, despite longer lead times and supply pressures caused by Cape of Good Hope (COGH) diversions. Without much additional capacity, the market would likely see more volatility across rate levels and space availability in the event of any large, unexpected disruptions. However, the market is expecting an 8% increase in capacity in 2025 and only a 3% increase in demand, which will help ease volatility.
Volatile rate levels and space availability are expected to continue on key routes like Asia to Europe and Asia to the United States. Meanwhile, other trade lanes, such as those from Europe to the United States and Europe to Asia have remained relatively stable—a trend that’s expected to continue.
But when it comes to navigating fixedrate contracts, both carriers and freight forwarders have moved quickly to adapt to more uncertainty.
Rates can fluctuate wildly, and currently, routing to the East Coast is nearly as affordable as routing to the West Coast, though this may change if an International Longshoremen’s Association (ILA) strike occurs on the East Coast around Jan. 15, 2025.
For most of 2024, blank sailings were driven by a lack of vessels. This has resulted in more extreme volatility, as carriers have experienced reduced capacity during peak season.
Ongoing disruptions add uncertainty and longer transit time. The Suez Canal diversions and an early peak season are setting the stage for a turbulent 2025 in
ocean shipping. Many lingering issues in 2024 show few signs of letting up in the New Year: for example, the Suez Canal.
Even though some niche regional carriers have used the canal, many carriers across the broader industry are still diverting vessels around the COGH. Shippers should understand how they are insured, particularly against General Average events, in case they’re shipping on a service transiting Suez: the premium—or lack of coverage—might not be worth the shorter sailing time.
Additionally, tensions between the ILA and the U.S. Maritime Alliance remain unresolved.
New shipping alliances bring major tactical challenges. New shipping alliances set to launch in early 2025 are poised to bring tactical challenges for shippers.
Beneficial cargo owners (BCOs) will need to be more selective in 2025 due to an increasingly complex carrier landscape.
Smaller shippers, who may not be familiar with these nuances, could find it challenging to choose the right service, and might benefit from closer collaboration with freight forwarders to navigate complexities and minimize risks.
Index-linked deals and enforceable contracts become more popular. Index-linked contracts, which link shipping costs to a well-known shipping index, provide consistent access to capacity and reduce administration costs.
While an index-linked agreement is not necessarily predictable in terms of what the
exact cost will be one month from now, it is predictable in that it will follow the market.
Index-linked contracts also save time, as they over time simplify the request for proposal (RFP) process and reduce administration, and help build long-term relationships with carriers and forwarders.
Regulations and tariffs mean shifts in trade patterns.
As the world’s largest goods importer, the United States brought in about $3.8 trillion’s worth of goods in 2023, according to the U.S. Department of Commerce.
Companies are reducing single sourcing, and are diversifying now. Consider doing the same if you’re expanding, and keep in mind that changing sourcing may completely change how you import today.
Go to https://foodl.me/a59gfu1b to read the remainder of this column.
NERIJUS POSKUS VP, global head of ocean procurement, Flexport.
TRINE STORGAARD NIELSEN VP, global head of ocean freight, Flexport.
The commercial transportation industry continues to experience significant growth, fueled by the rise of e-commerce and shifting consumer buying trends. However, this expansion also raises notable challenges, particularly around last-mile deliveries and a persistent labor shortage. These pressures are reshaping how businesses operate, forcing them to confront both immediate logistical needs and long-term regulatory and safety implications.
Some companies have prioritized shortterm solutions, like hiring less experienced or underqualified drivers, to maintain delivery schedules. This shortsighted approach increases the likelihood of accidents, claims, and legal exposure. Along with higher vehicle, technology, and replacement part expenses, the labor shortage contributes to rising claim costs as well.
Claim severity, too, has ballooned, with auto liability claim amounts increasing from an average of $13,000-38,000 over the past two years. This has created a ripple effect, increasing insurance premiums and exacerbating overall industry risks.
A key concern in the industry is driver employment classification as traditional employment models mix with the gig economy’s 1099 contractual agreements. While gig drivers offer a flexible and costeffective solution by saving on payroll expenses, the model has drawbacks. It often leads to a revolving door of inexperienced labor, exacerbating the existing shortage of qualified drivers.
In contrast, businesses that invest in more traditional, structured employment models tend to experience higher employee retention, which is more cost-effective than continually hiring and training new drivers.
Across the board, commercial transportation businesses can expect insurance costs to remain elevated as the overall risk landscape for the transportation industry becomes more complex. Expect to see changes in insurance costs throughout 2025 in auto liability (insurance premiums may rise by 10-20% in 2025); physical damage (coverage may rise by 20-25% in 2025; and umbrella liability (may see premium increases ranging from 10-30% in 2025).
Considering the rising costs and industry hurdles, taking proactive steps to mitigate risk and manage coverage makes good business sense. Stay ahead of these challenges by:
• Maintaining strict safety standards. Implementing safety technologies like collision avoidance systems, telematics, and cameras can reduce the likelihood of accidents and protect against future liabilities. Additionally, underwriters are scrutinizing motor vehicle records more closely, so keep these records clean and up-to-date.
• Monitoring Federal Motor Carrier SAFER scores. Ensure that Federal Motor
Carrier Safety Administration (FMCSA) SAFER scores remain below the national average to secure favorable insurance terms. Scores of 50 or higher require close attention. A score of 65% or above in Crash Indicator, HOS Compliance, or Unsafe Driving can trigger an FMCSA investigation, with the threshold lowered to 50% for those transporting passengers or hazardous materials.
• Exploring alternative coverage options. Instead of reducing coverage to cut costs, consider alternative insurance options such as captives, risk retention groups, or higher deductible programs.
The commercial transportation industry will continue to face significant challenges in 2025.
Working together and prioritizing long-term sustainability over quick fixes can help reshape the industry to be more cost-effective and resilient.
BRIAN JUNGEBERG transportation VP, Risk Strategies ABOUT THE AUTHOR
BY ALEXIS MIZELL-PLEASANT, MANAGING EDITOR
The adoption of artificial intelligence (AI) in supply chain and logistics is revolutionizing the industry, producing efficiency, increasing speed and contributing to resiliency in operations. AI is quickly emerging as a common tool to overcome traditional challenges and enhance decision-making. Central to this transformation is the strategic use of data, which fuels AI models and allows logistics companies to anticipate disruptions.
Michael Hung, CEO at TradeBeyond, explains that, today, AI is driving massive improvements across supply chains by adding accuracy and speed to traditionally manual processes.
Supply chains are inherently complex, and this complexity creates challenges in visibility, accuracy and response time, which are exacerbated by external disruptions such as geopolitical shifts and natural disasters. There are three main spaces where AI is thriving: demand forecasting, inventory management and transportation planning.
Steve Dombroski, director, consumer markets at QAD, says with AI, demand forecasting becomes much more accurate by analyzing various data sources—like social media trends, weather patterns and economic indicators—that influence consumer demand. This helps businesses anticipate what people will need in the future, making it easier to avoid overproducing or running out of stock.
“In demand forecasting, AI analyzes huge data sets—like sales history, market trends and even weather patterns—to better predict customer demand. For the food and beverage sector, this includes seasonal adjustments to account for peak demand during holidays or trends affected by extreme weather events that impact fresh food availability. This allows companies to avoid the risks of overstocking or running out of stock, aligning production more closely with actual demand,” says Hung.
Traceability is a hot topic in the discussion about inventory management, especially where food and beverage is concerned. Hung says AI-enhanced chain
of custody solutions streamline the process by automating documentation review, rapidly identifying inaccuracies or gaps, and consolidating data across all ingredient levels.
For Dombroski, managing inventory means balancing how much stock is on hand without overcrowding warehouses or running short.
“AI can monitor sales, supplier timelines, and even seasonal trends to keep inventory levels optimized, reducing excess stock and preventing shortages. For instance, if AI identifies a sudden spike in demand for a specific item, it can automatically adjust inventory orders to meet that demand without wasting space or resources,” says Dombroski.
Meanwhile, in transportation planning, Hung says AI optimizes routes by factoring in real-time traffic and weather data, cutting costs and reducing delivery times— especially critical for ensuring that fresh and frozen products reach stores promptly, maintaining quality and minimizing spoilage, while reducing fuel cost.
And a modern transportation management system (TMS), for example, could have integrations that produce more accuracy through the use of AI software.
“Transportation planning benefits from AI’s ability to improve routing, predict delivery times, and manage logistics costs,” says Dombroski. “AI analyzes factors like traffic patterns, fuel costs, weather conditions, and even driver schedules to select the most efficient delivery routes. This reduces delays, saves fuel and can even lower shipping costs by choosing optimal routes.”
One of the challenges in AI adoption is integrating with legacy systems. Companies are overcoming this hurdle through real-life application.
Before investing time and money into AI-powered solutions, Thor Olof Philogène, co-founder and CEO at Stravito, says AI leaders must first identify real-life pain points of existing systems and legacy software and understand how AI solutions can benefit them.
“Another aspect to consider is change management. Time should be taken to explain both the limitations and strengths of the technology being integrated to stakeholders, empowering people with knowledge,” says Philogène. “This mitigates anxieties around the results of the change and gives them agency to ask questions and take an active role in participating.”
Oftentimes, companies use multi-enterprise platforms that bridge the gap between older systems and new AI tools. These platforms allow for seamless data exchange without the need to completely overhaul older infrastructure, says Hung.
“Best practices for smooth AI implementation include starting with a data readiness assessment to ensure that existing data is clean and well-organized,” explains Hung. “ Many companies also roll out AI in stages—focusing on specific functions like inventory management before expanding across the entire supply chain. This phased approach helps reduce disruption and allows teams to learn and adjust as they go.”
Why data is the fuel
Data is the lifeblood of AI applications.
As more logistics operations adopt digital technologies, they generate vast amounts of data at every step of the process—from suppliers and manufacturers to warehouses and customers.
“Ensuring high-quality data is foundational to making AI work effectively. Many companies are adopting data governance frameworks to standardize how data is collected, validated, and managed across the organization,” says Hung. “These frameworks ensure consistency and accuracy in data, preventing issues like duplication or outdated information. However, the main challenge often lies not just in legacy systems but in the fragmented nature of data, with crucial information stored across disparate systems that may not interact with each other.”
For example, Philogène says, with the issue of “hallucinations” in some generative AI tools, organizations that rely heavily on accurate market and consumer research should ensure they implement tools that generate insights exclusively from vetted data, not from open-source or publicly available data. Furthermore, Philogène stresses, when integrating the data, the technology should be complemented by a human-run service layer to ensure its effectiveness.
“They also check data regularly to make sure it’s current and accurate. These steps mean AI systems can work with reliable, up-to-date information, which is key for making good predictions and decisions in
the supply chain,” says Dombroski. With advances in machine learning and natural language processing, AI will become even more integrated into supply chain processes.
“Demand forecasting is also set to benefit from AI’s enhanced predictive capabilities. With its ability to analyze and correlate real-time demand signals, AI will play a critical role in the food industry. Accurate, AI-driven forecasting will minimize the likelihood of costly product waste, aligning production with consumer demand and ensuring fresher products on shelves. And in inventory management, AI will drive improvements in key performance metrics like ‘inventory turns’ and ‘days on hand.’ By optimizing inventory based on real-time and predictive data, AI helps reduce excess stock, improve turnover, and ensure fresher products are available to consumers. Its ability to perform complex, multivariate analysis will allow for more precise inventory management, supporting efficient stock replenishment and reducing product spoilage,” says Hung.
With data at its core, AI is helping companies make better predictions, optimize routes, manage risks and improve visibility. As these technologies continue to advance, companies that harness the full potential of AI will gain the most competitive edge in the race toward technology optimization.