
9 minute read
Pipedream Come True For Brandt Pipelayers
Pipeline professionals wanted a safer pipelayer. Brandt & John Deere delivered.
When we reached out to pipeline professionals for feedback on what makes an ideal pipelayer, the response was that safety was number one. And two. And three. The team took it to heart—and to market.
Five years ago, after decades of serving the oil and gas pipeline industry, Brandt entered the pipelayer market, collaborating with the engineering team at John Deere on a dedicated pipelayer. We designed the machine with an innovative low-mount side- boom, which delivers a wider stance for the lowest ground pressures and highest stability ratings.

In addition to unrivalled stability (read: safety), Brandt pipelayers boast the exclusive and industry-leading SmartLift™ Dynamic Stability Monitoring system. This system delivers real-time dynamic stability feedback, ensuring the operator always knows the lifting ability at all boom angles over various slopes and pitches. More safety.
“We look at the load, the slung load, how far it’s out, what the ground condition is like, and we combine that into a real-time readout, so from moment to moment the operator knows what’s going on,” says Dan Bonnet, Engineering Manager—Electrical & Hydraulic at Brandt.

SmartLift™ features patented technologies that automatically account for the effect of side slope (roll) and front/back slope (pitch) on the carrying capacity of the tractor while moving, displaying the percentage of the max load in the current location. The system also warns operators when there is a tipping scenario, so they can react quickly to prevent accidents.
John Deere’s Hydrostatic drive is another major advantage that we leveraged to give our pipelayers unmatched maneuverability. With infinite speed variation and effortless zero-radius turns, operators can focus their full attention on the load rather than on driving their machine. Even more safety.
“This is the toughest, safest, most stable pipelayer in the industry,” says Jason Klassen, Senior VP Sales—Manufactured Products at Brandt. “These machines are purpose built for performance on the diverse North American landscape—that means all terrains and all seasons, as challenging as they can be. This is a pipelayer you can count on to get the job done safely and efficiently.”
How did we end up with such a superior machine? By listening to our customers’ frustrations with competitors’ models and incorporating this feedback into the design.
“Everybody talks about wanting to be customer focused, but customers will only share with you if they trust you. Because of the service we’ve delivered over the years, our customers have come to trust us, and know that when we ask, we listen,” says Chris Semple, President — Manufactured Products at Brandt.
Brandt engineers heard that customers wanted lower operating costs, so they created a unique low-mount boom-side winch placement that delivers increased cable life due to the industry’s lowest angle of reeving. They also designed the sideboom to work with John Deere’s proportional hydraulics and ECO Mode, providing full functionality and proportional control at engine idle. Plus, winches can still run at full speed, even with the tractor idled down, resulting in less wear and tear on the engine and lower fuel consumption.
“Safety comes first, last, and always, but you also need a machine that offers maximum uptime and a lower cost of operation, and we are able to deliver it all with Brandt pipelayers,” concludes Klassen. And that’s a pipedream come true.
Learn more about Brandt pipelayers at brandtpipelayers.com. SP
Source: Brandt
Aggregate Equipment
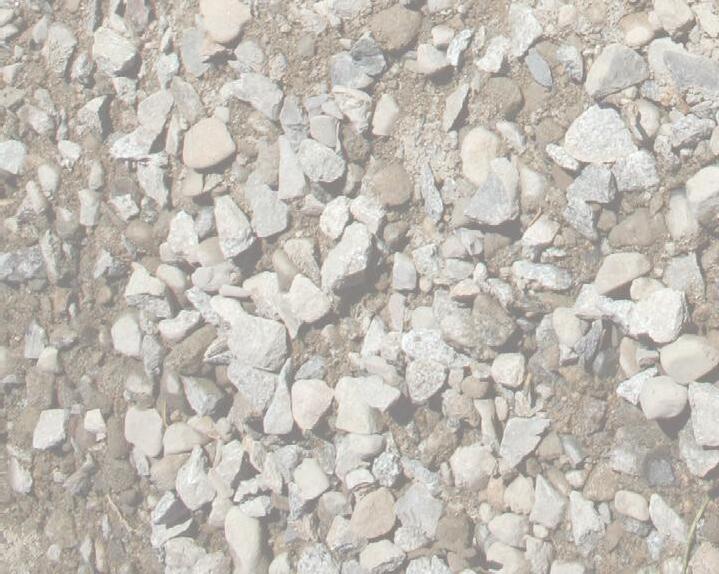
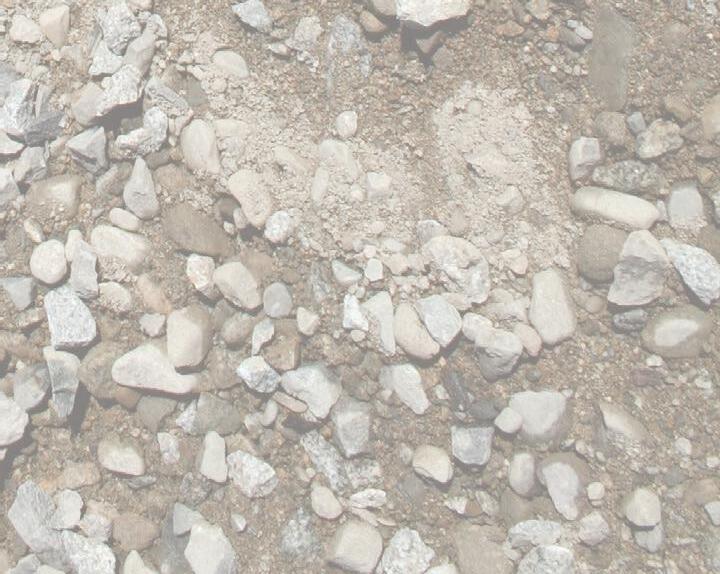
Superior Updates Belt Cleaners
Superior Industries, Inc., a US-based manufacturer and global supplier of bulk material processing and handling systems, made some tweaks to its Exterra Conveyor Belt Cleaners, which will reduce time required to maintain the popular scraping systems.
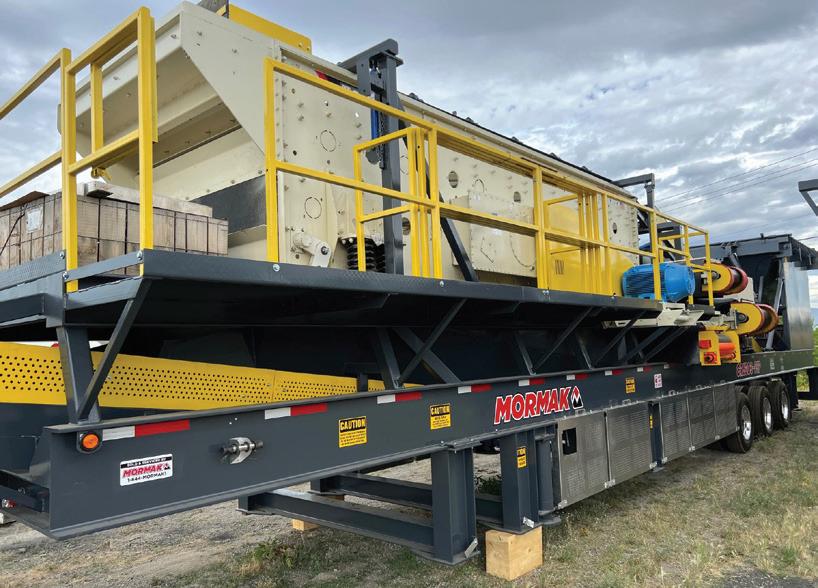
First, a new fast-acting click tensioner is available for the primary and secondary models. After installation, operators simply twist the tensioning unit for a prescribed number of times to set proper force. Click count instructions are conveniently labeled on the aluminum housing that protects the springs.
Second, Superior’s SFL scraper models are now manufactured with a special extruded tube. It’s designed to house the patented springs and seal them from fugitive material. The abbreviation SFL means “Set for Life”. Exterra Belt Cleaners with this SFL option require tensioning just once at the time of installation. Accurate tension is maintained automatically — with no required maintenance — for the entire life of the blade.
Third, Superior’s conveyor components engineers recently completed lab and field testing on a proprietary new mix of polyurethane, which is poured into molds to form the blades. This longer-lasting material is also more flexible, which endures beating from belt splices and wears more effectively. All blades are developed in-house by Superior. There are several models of Exterra Belt Scrapers in both aggregate and mine duty constructions. Blade widths are available up to 102-inches (2,590mm). SP
Source: Superior Industries
How To Regulate Systems In A Portable Compressor
Why are regulation systems so vital in a portable compressor?
And how do they differ to those suitable for a stationary machine? Guy Laps, Technology and Innovation Manager at Atlas Copco, explains.
Integrated within a compressor are systems that play an essential role in regulating the machine’s flow, pressure, power and speed to name a few. The equipment keeps a compressor – and thus an overall project – running optimally, without any setbacks.
The regulating systems offered by Atlas Copco are designed to afford efficient operation and high performance, while helping to avoid any unnecessary running costs for the user. But before we look at the specifics in closer detail, it is vital to clarify that the systems in place for a portable compressor can differ a lot from its stationary counterpart.
Mobile vs Stationary Stationary compressors are – by definition – im - mobilised, and typically remain in a factory or allocated compressor room. They feed compressed air into multiple destinations/ tools, which is first routed through a piping system with a large buffer in place. Some use a simple ‘on-off’ regulating system, meaning once the desired level of pressure has been achieved the system will shut off or go into ‘no-load’ state (idle without producing air). It will remain this way until the pressure in the system drops below a threshold, or air demand increases.
For mobile compressors however, the requirements greatly differ. They typically feed a single application; have one user; and a much smaller buffer compared to the stationary application. Mobile machines can have an extremely varied demand in air, and therefore require regulating systems that can cope with such variations.
VSD is key
Having a regulating system that can efficiently react on fluctuations will lead to meaningful energy and cost savings. Thanks to its state-ofthe-art Variable Speed Drive (VSD) technology, Atlas Copco’s mobile compressors adjust their operating speed in order to match air production to demand in real-time.
The VSD technology uses a combination of two regulation parameters: first is speed regulation, which is the most efficient means to control air demand; and second is ‘throttling’ – closing the air inlet of the compressor element –which is less efficient. Atlas Copco VSD compressors always prioritise speed regulation, and only use ‘throttling’ when it is no longer possible to go down in engine or electric motor speed, in order to adjust the final percentage of required capacity.
Fixed speed compressors, on the other hand, are incapable of adjusting their speed. They can only operate at full capacity and are obliged to control air demand via the inefficient ‘throttling’ process. Using this type for operations where demand for compressed air fluctuates will lead to a significant amount of energy being consumed and wasted when compared to a VSD machine.
Guy Laps, Technology and Innovation Manager at Atlas Copco, elaborates:
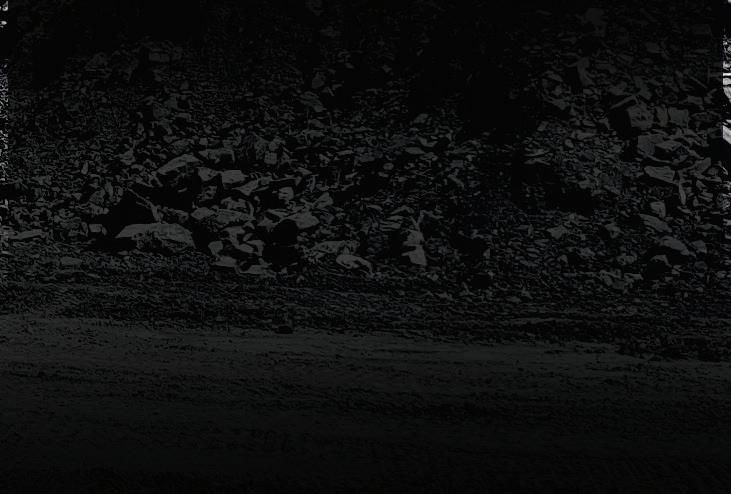
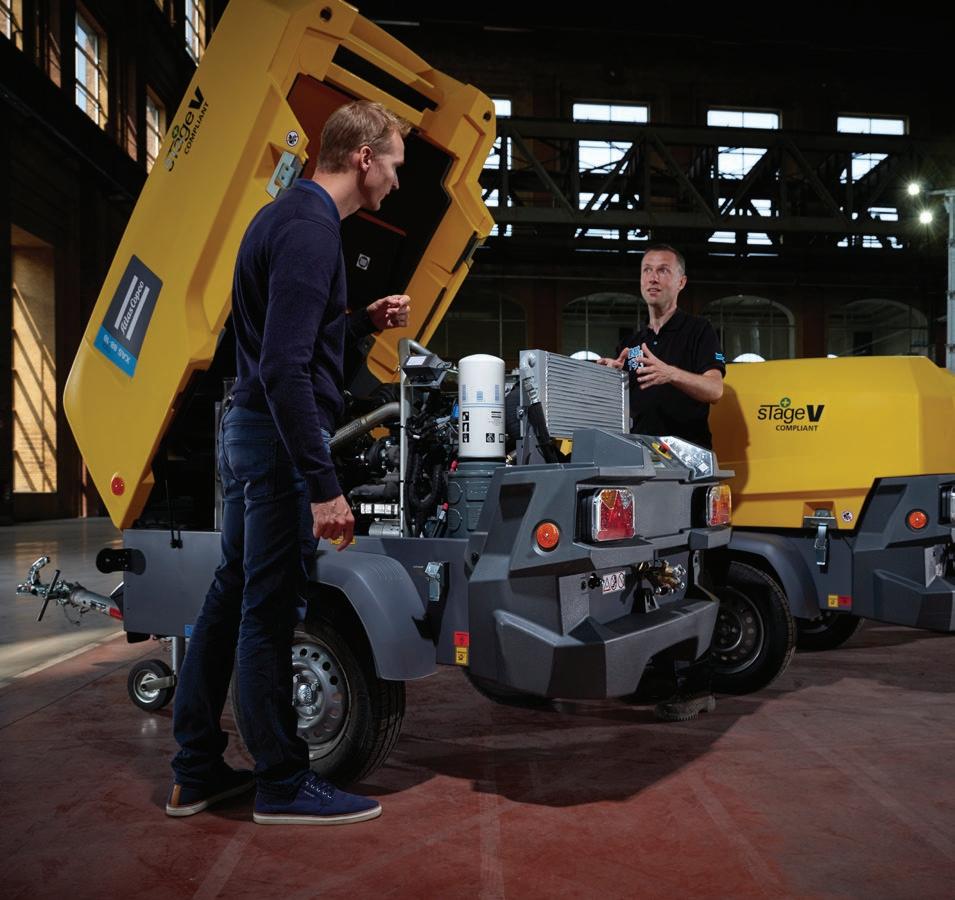
“Fixed speed may be suitable for applications where demand variation is minimal, but this is most often not the case with mobile compressors. Being able to match the speed of the mobile machine’s element with the required flow is vital. Atlas Copco was first to offer this ability in portable compressors, and to this day our VSD technology continues to offer unparalleled efficiency, unmatched reliability, and future-proof connectivity.”
Keeping operations running smoothly
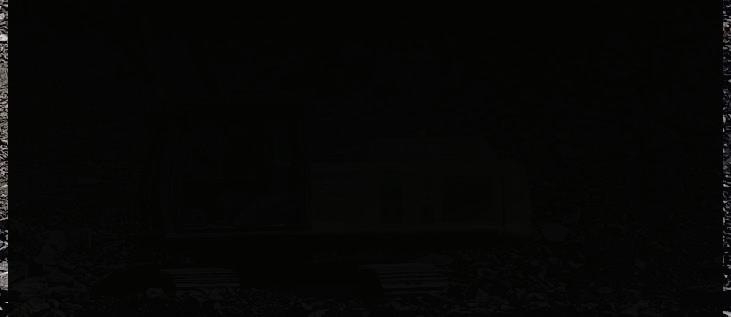
Mobile compressors can also suffer from pressure drops or overshoots. If a pressure drop happens mid-application – while drilling, for example – it can demobilise the tool being powered and halt operations. At the other end of the scale, overshoots can lead to the opening of the safety valve, resulting in a sudden and extremely loud, uncomfortable noise that can hinder both workers and bystanders.
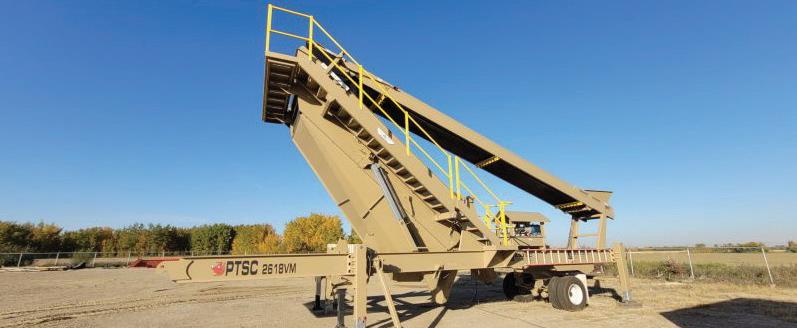
A stable, fast acting regulating system that is designed to handle transients is therefore critical to avoiding pressure drops and overshoots.
Guy concludes:
“Atlas Copco’s expertly designed mechanical and electronic speed regulation systems, AirXpert and Pace technology, make it possible for the operator to define the pressure while the machine automatically regulates the flow. These innovative technologies will stop fluctuations in their tracks, resulting in a stable and highly efficient compressed air output.”
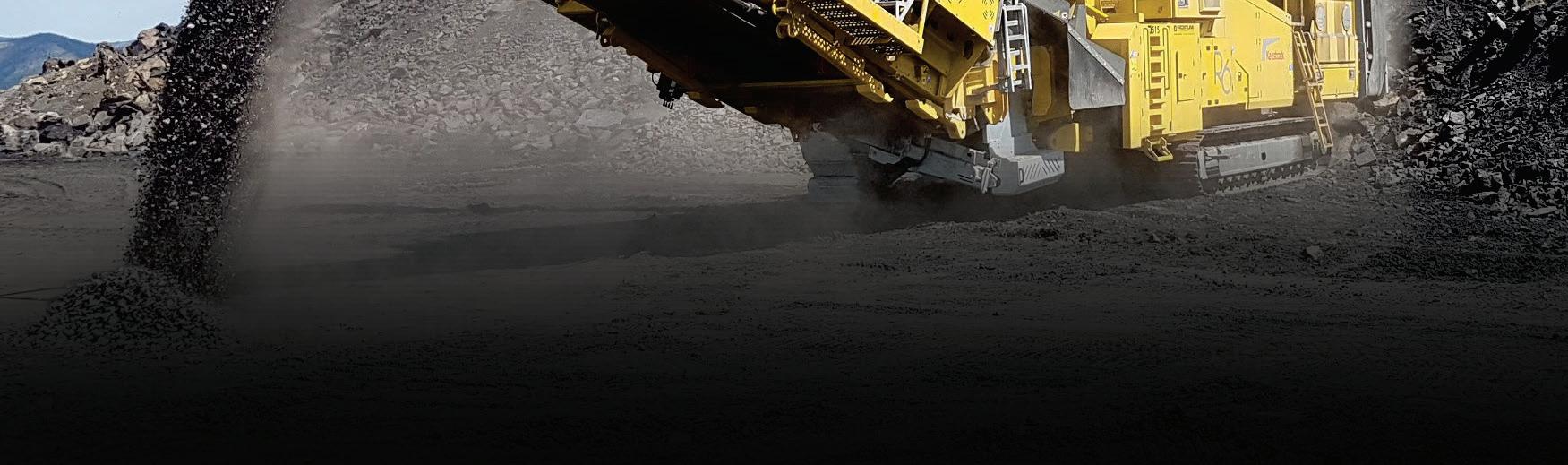
Ultimately, an efficient, versatile and reliable regulation system works wonders in mobile compressor applications. They help save energy, lowers noise and avoids unnecessary running costs –ensuring the user can get the most out of their compressor and project. SP
Source: Atlas Copco
Volvo CE To Produce More Electric Wheel Loaders
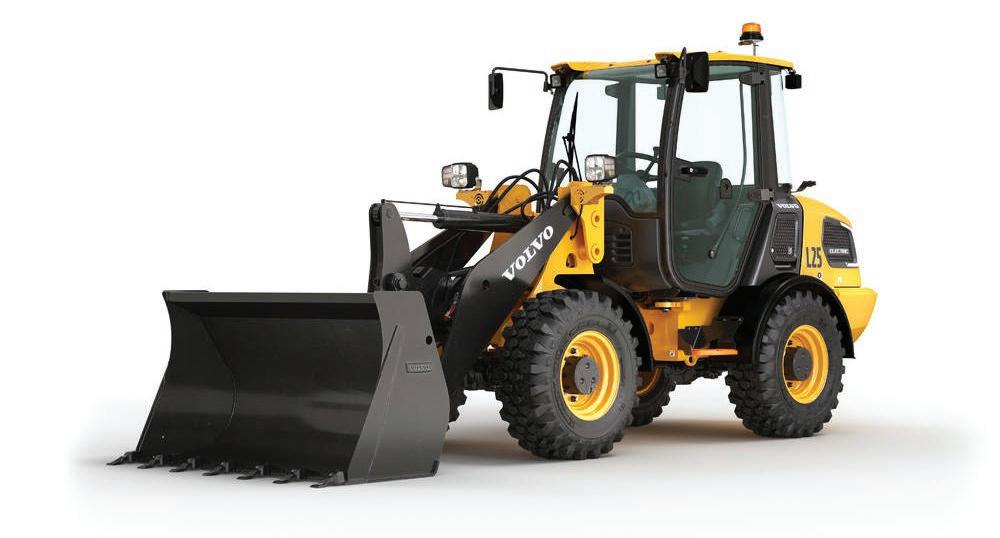
As part of its ambition towards industry transformation through sustainable solutions, Volvo Construction Equipment (Volvo CE) has announced an investment into the production of electric wheel loaders from its plant in Arvika, Sweden.
The SEK 65 million (around $6.3 million) investment from Volvo Group will allow the Arvika factory in Sweden – which specializes in the production of medium and large wheel loaders – to expand its facilities with a new building and allow for the phased introduction of new electric wheel loaders.

It is not only a milestone in the plant’s almost 140-year history, but a significant moment for Volvo CE and its determination to be completely fossil free by 2040 – in line with the aims of the Paris Agreement and as laid out in the manufacturer’s industry leading Science-Based Target goals. It is also a pioneering step forward in its ambition for 35% of its machines sold to be electric by 2030.
Coming soon after an announcement to invest in electric haulers from the company’s production facility in Braås, Sweden, it is also a signpost that Volvo CE is committed to achieving more sustainable solutions for customers across all its product lines – and is dedicated to driving that change forward in the here and now. These announcements are part of an investment strategy that allows Volvo CE to advance electric solutions across its production facilities, including also the Konz facility in Germany, Belley in France and Changwon in South Korea, where other electric machines are made.
Site Manager Mikael Liljestrand says: “This is a clear signal of our commitment to building the world we want to live in. It is more hearts to be part of something bigger in building our future.”
Volvo CE has already successfully introduced compact electric wheel loaders to the global market with the L20 Electric and L25 Electric wheel loaders proving to be efficient, zero-exhaust emission solutions capable of driving down carbon emissions while maintaining high productivity across a variety of customer applications. Together with the ECR25 Electric, ECR18 Electric and EC18 Electric compact excavators and the mid-size EC230 Electric excavator, Volvo CE has one of the largest electric ranges on the market.
Sustainability Transformation
than 40 years since we last invested in a new building and what better reason now than to invest in our future, our planet and the next generation. We know that this is not only important to our customers and stakeholders, who rightly have high expectations on us, but it is also close to our
Thanks to the investment, Arvika will erect a new building, approximately 1,500 sq m, which will allow the facility to free up areas inside its assembly factory to be able to build electric wheel loaders. While it has not yet been announced which models will begin their electric transformation and exactly when, production of both electric wheel loaders and more traditional wheel loaders fitted with combustion engines will continue for now on the same production line.
Volvo CE will ensure a phased introduction model by model, taking into account all aspects of the electric ecosystem as it does so, including infrastructure requirements, charging solutions, battery handling and business models. The result will be reliable midsize and larger electric wheel loaders that can easily be integrated into customers’ business.
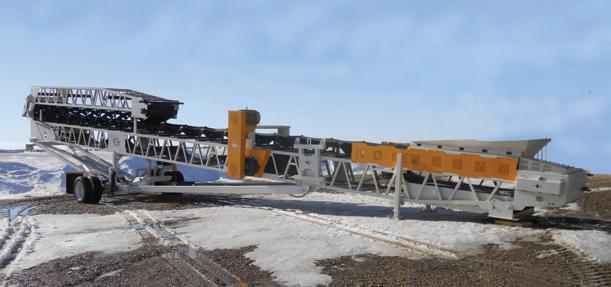
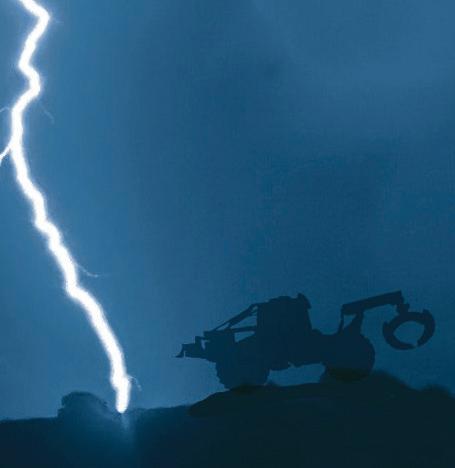
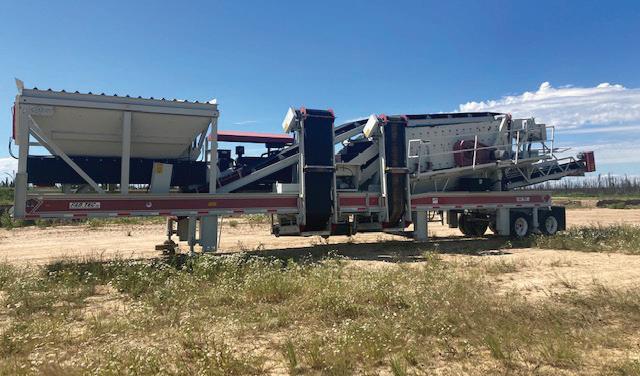
It is not the first sustainability initiative from the Arvika facility. Despite actually increasing production last year, the factory managed to reduce its internal climate footprint by 350 tons of CO2 thanks to a variety of emission reduction efforts.
“Our goal at the factory in Arvika, as well as Volvo CE and the entire Volvo Group is to be climate-smart and to produce fossil-free machines,” continues Mikael.
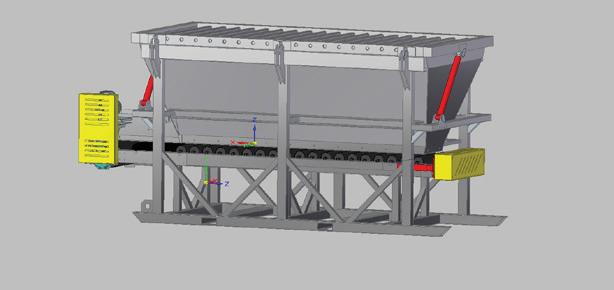
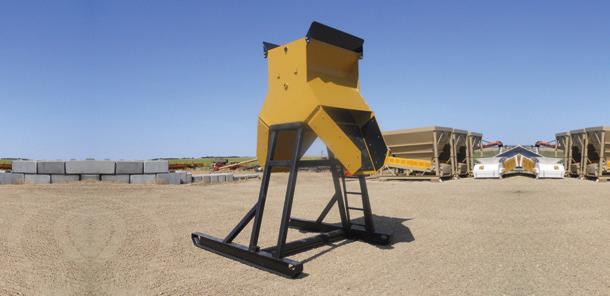
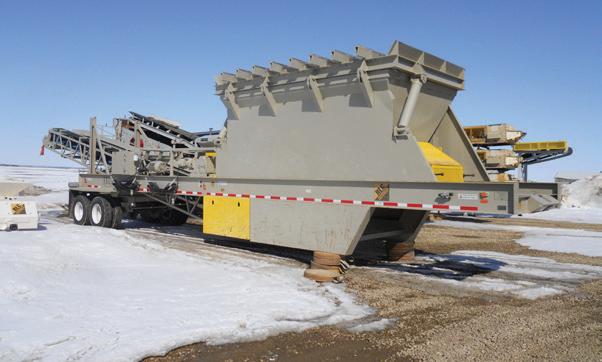
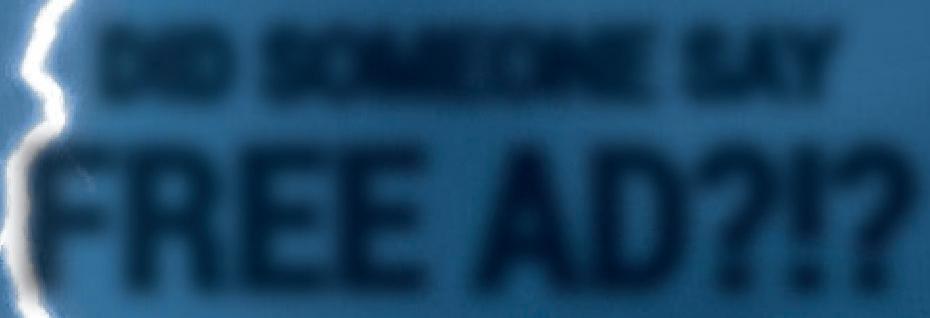
“Together, we are quite clear that we want to lead this transformation and be the driving force of more sustainable ways of working for the benefit of our planet. This investment is Arvika’s exciting first step towards electrification.”
Building work is set to begin later this year, with further announcements on when production will begin to come. SP

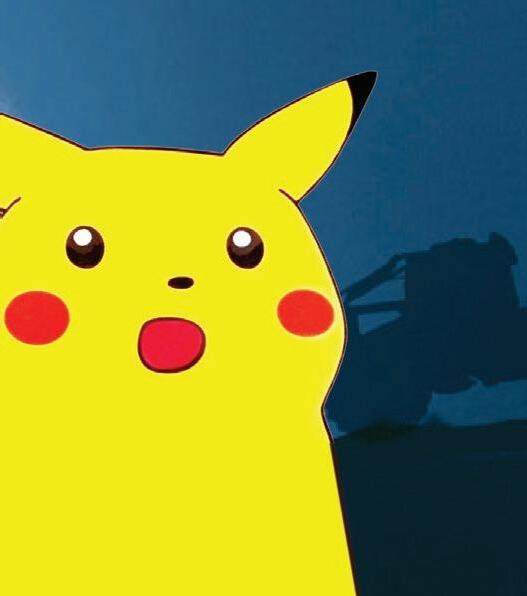
Source: Volvo CE