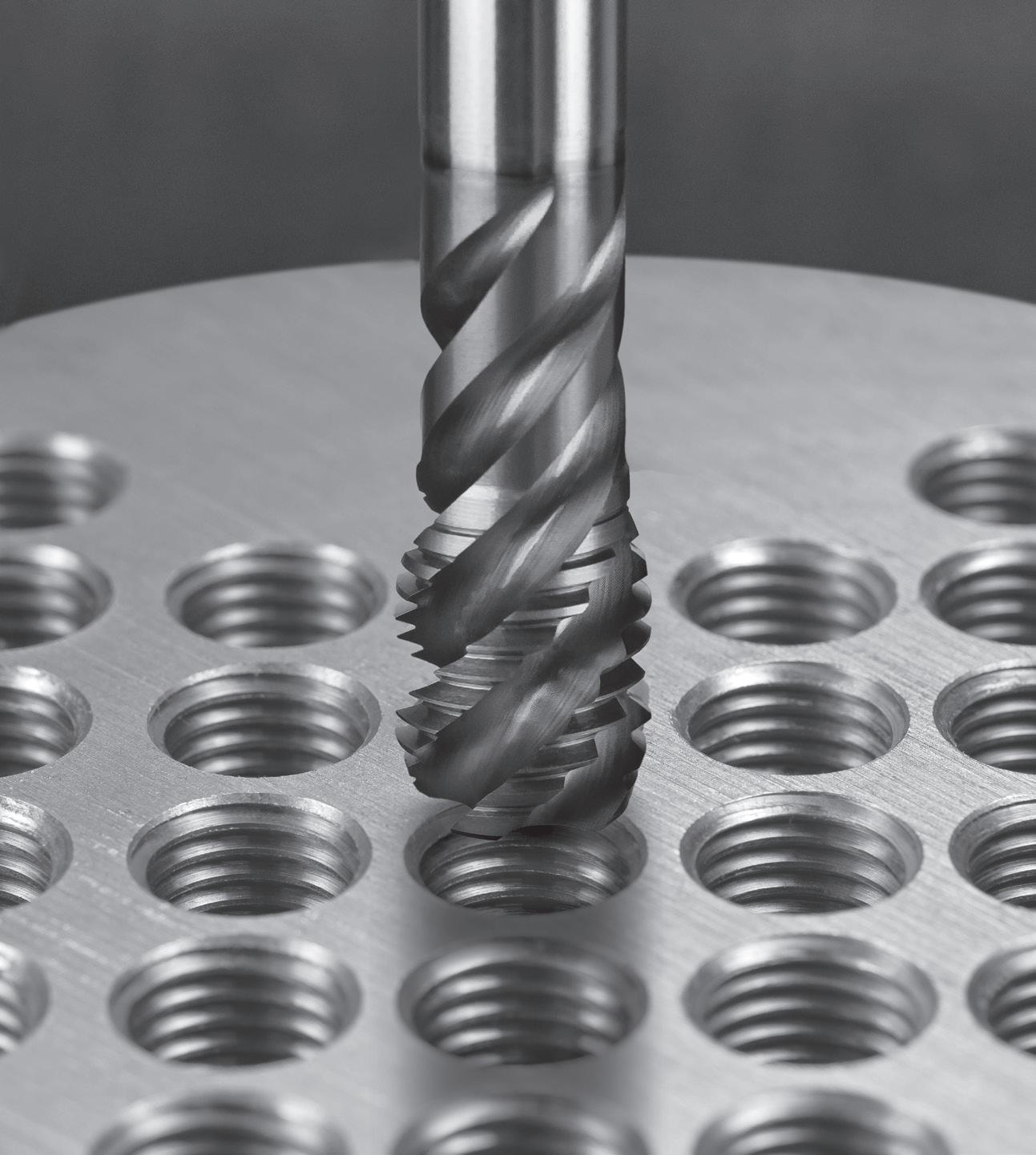
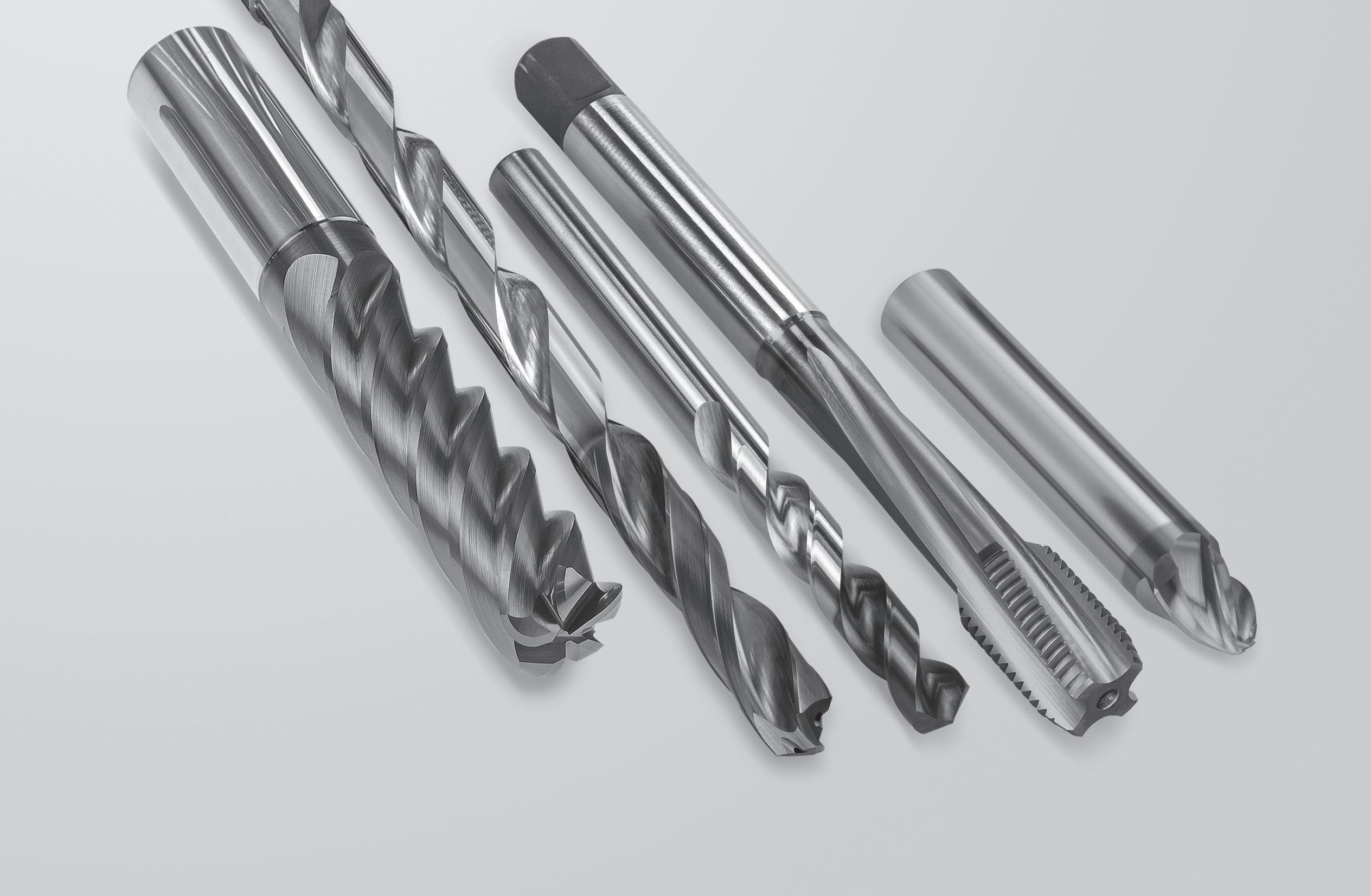
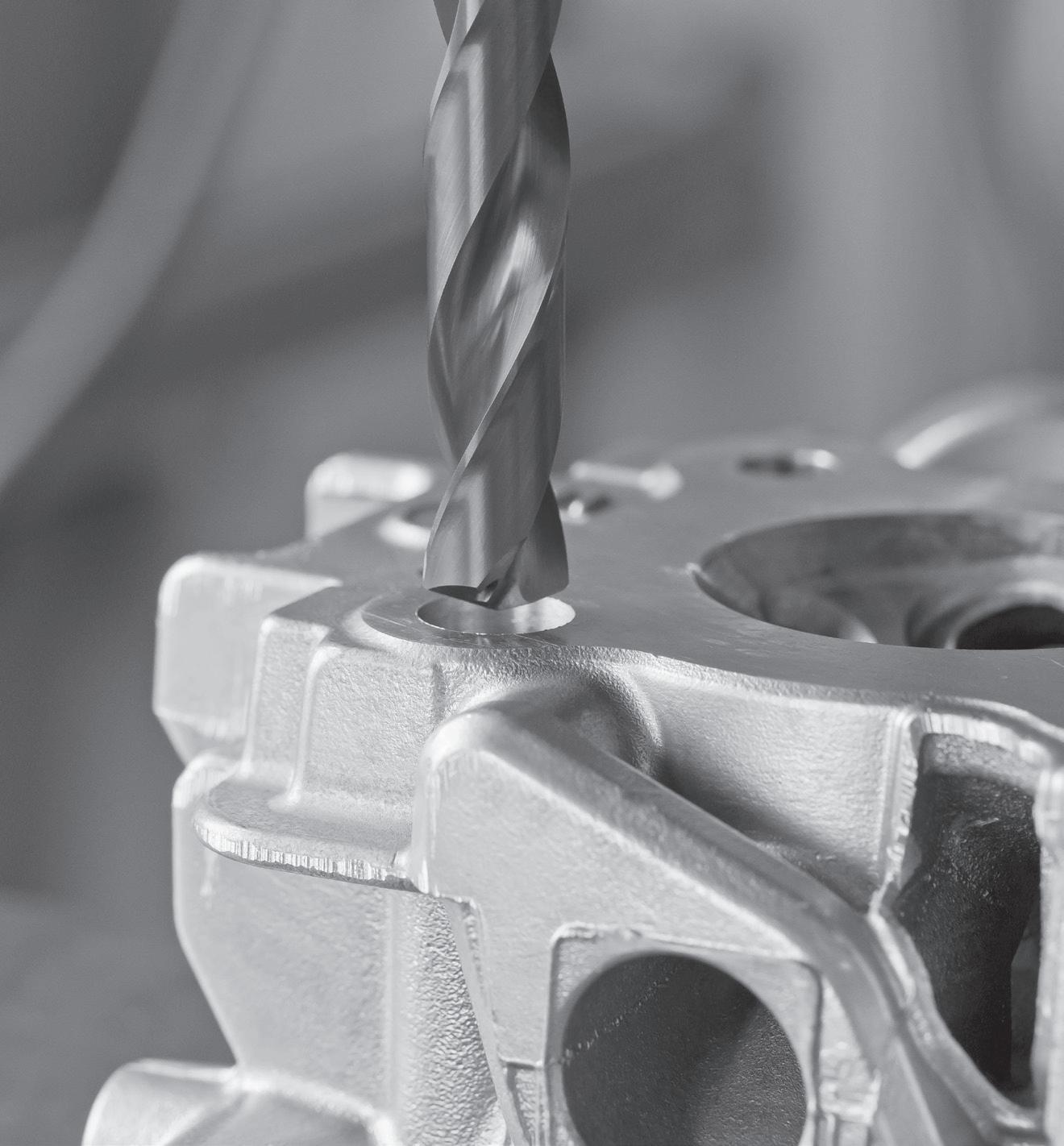
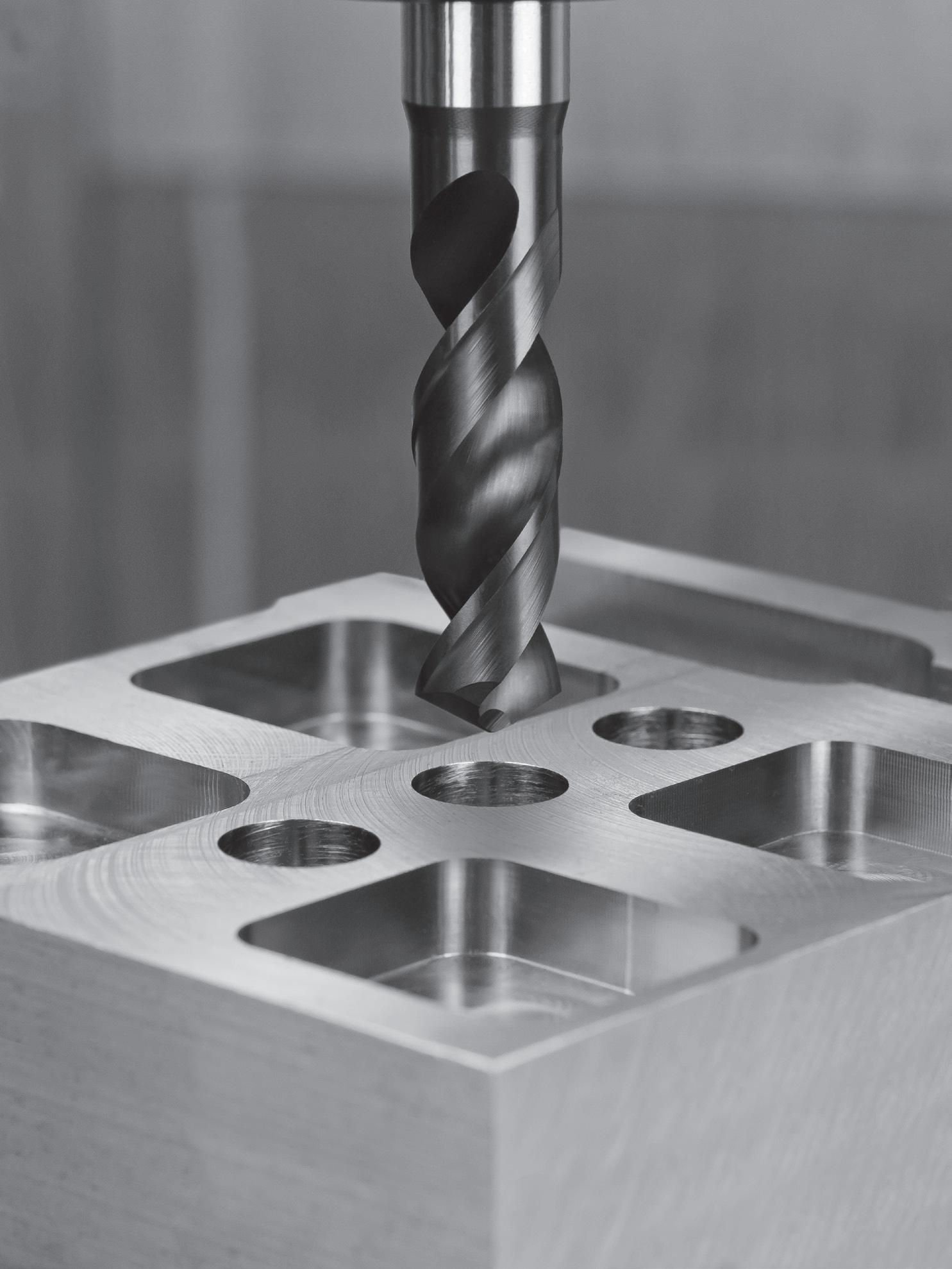
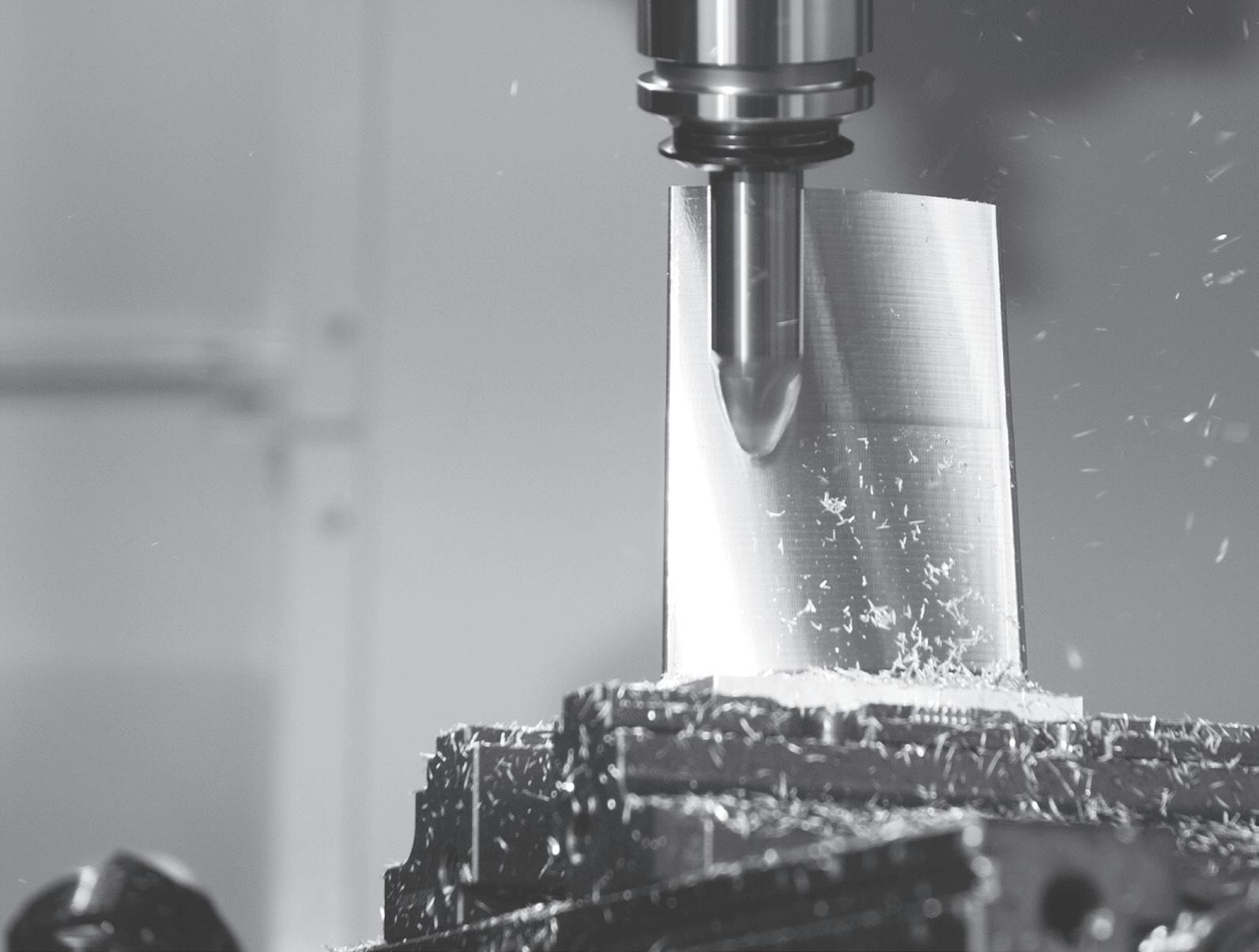

English
• Suitable for materials up to 1400N/mm²
• Strong core
• Micro geometry & surface conditioning for optimal chip control
• AlCrN for maximum tool life
Forets carbure 3xD, hélice 30°, type UNI
• Convient aux materiaux jusqu'à 1400 N/mm²
Noyau renforcé
Micro géométrie et traitement surface optimisé pour un bon controle des copeaux
Revêtement AlCrN pour une durée de vie maximum
Punte Metallo Duro, 3 x D, R30 UNI
• Ideale per materiali fino a 1400N/mm²
• Nocciolo rinforzato
• Micro geometria & rivestimento tagliente ideale per un ottimo controllo truciolo
• AlCrN per massimizzare la vita utensile
Brocas de Metal Duro, 3 x D, R30 UNI
Adecuado para materiales hasta 1400N/mm²
Núcleo Reforzado
Micro geometría y acondicionamiento de la superficie para un control
óptimo de la viruta AlCrN para una máxima vida útil de la herramienta
Founded in 1917, Sutton Tools began as a family enterprise, manufacturing threads and gauges, and over time has expanded its expertise into a broader portfolio of cutting tools. Today, Sutton Tools remains an Australian family business that is renowned for its high-quality power tool accessories and cutting tools for the hardware market and a wide range of specialised industrial applications.
Sutton Tools manufactures cutting tools at three sites across Victoria, both for the domestic market and for export. The bulk of general production occurs at our head office site at Thomastown, in Melbourne’s northern suburbs, with more specialised operations centred at our Maryborough facility. We also have overseas production plants in Auckland, New Zealand, and in the Netherlands.
Sutton Tool’s state-of-the-art production processes begin with raw material preparation. High-speed steel is imported from France and Switzerland in 3.5m-length bars, as Sutton Tools has found the quality of this European-manufactured steel is superior to raw material sourced from Asia. This steel is cut to length and turned, using computer controlled machines that are able to complete a number of turning operations in a single manufacturing stage.
While Sutton Tools supplies tools to a broad spectrum of industriesincluding general manufacturing, electronic manufacturing, automotive, medical, mining and power generation - most advancement in material technology it experiences are occurring in the aerospace, defence and oil/gas industries. The development of so-called ‘super alloys’ for these sectors is constantly pushing material performance boundaries. However, the tougher these materials become, the tougher the tools need to be to work the new generation of alloys.
The good news for tradies and DIY enthusiasts is that the cutting technologies developed for these state-of-the-art cutting applications filter through to the tools Sutton produces for the hardware industry. All of Sutton’s tools are manufactured from high-speed steel and are ground-from-solid, regardless of whether they are destined for the hardware market or for a specialised industrial application. In the same way that a car manufacturer utilises technologies developed through motorsport to improve the reliability and performance of the family cars it produces, so Sutton Tools is able to use its specialised industrial experience to deliver optimised tools for the hardware market.
For easy tool reference, you will find an extensive application based index at the start of each section.
These icons below can be found on the product pages throughout the catalogue, and at a glance the characteristic features of the tool can be identified.
We have been manufacturing quality cutting tools in Australia since 1917 and the fact that we are manufacturing in Australia is becoming an important part of our message.
Third-generation family member Jim Sutton
Sutton Tools is the only production manufacturer of cutting tools in Australia. Promoting Australian Made tools is about more than raising awareness of quality products — it’s about encouraging growth in the Australian Manufacturing Industry.
Sutton Tools supports and promotes Australian made products, with the aim of creating more opportunities for all Australians. Every dollar invested in products made here benefits our country in terms of jobs created, goods and services purchased, taxes paid and welfare payments reduced. When buying Sutton Tools products that carry the Australian Made logo, you can buy with confidence, knowing they are made to Australian standards, exceeding expectations.
Sutton Tools growth into the global market began over 20 years ago. About 40% of Sutton Tools products are sold overseas, with integrated logistics and warehousing in Europe. Sutton Tools export strategy further proves the quality of Australian Made product and strengthens local jobs and manufacturing in Australia into the future.
1917 - the start to an iconic Australian family brand, manufacturing cutting tools for distribution throughout Australia...
William Henry Sutton arrived in Australia
William Henry Sutton, a British Immigrant, opened a tool room at Thompson’s Foundry at Castlemaine. He was recognised as one of the leading tool engineers in England before his departure to Australia.
Patience and Nicholson (P&N®) in Australia
The P&N ® brand was founded, providing cutting tools for the professional and serious DIYer in Australia.
Start to an iconic Australian family brand
Nearing the end of World War 1 in 1917 after been seconded back to the UK to help with the war effort, W. Henry Sutton at the age of 54, established the Sutton Tool & Gauge Manufacturing Co. at Plant Street Westgarth, Victoria.
Thread production
Sutton Tool & Gauge commenced the manufacture of Thread Tooling, expanding its product portfolio.
Business quadrupled
It soon became evident to local manufacturers’ they could now buy domestically produced tools of equal or better quality than those from overseas! With the original factory ‘bursting at the seams’, Sutton Tool & Gauge moved to a 13,000 square foot factory in Northcote, Melbourne.
A broader market goal
The next generation
Both sons of W. Henry, Henry George Sutton and Leslie Sutton became managing directors of the business whilst William Henry at age 77 continued to take an active interest.
Sutton Tool & Gauge first export was to New Zealand, a consignment of reamers.
Frost (Tools) Engineering
Frost started manufacture, sourcing and supplying hand tools and power tool accessories in Australia.
William Henry Sutton, born 1863 - died 1950, a highly regarded tool and gauge engineer prior to the founding business owner of Sutton Tool & Gauge. William was a pioneer of the Australian Engineering Industry.
A team of engineers were sent across the globe to investigate the best method of producing the finest drill in the world. They came back with the “Ground-from-Solid” process. All endmills, slot drills and taps up to ½" diameter were produced by this method. Sutton Tools purchased and installed specialised equipment and was considered to have one of the most modern facilities in the world.
The demand for high quality tools made by Sutton’s continued, and to meet with increasing sales the firm opened another 45,000 square foot factory in Thomastown.
Sutton Tool & Gauge commenced manufacturing Jobber Drills in Thomastown.
Sutton Tool & Gauge acquired an adjoining factory in Thomastown.
The third generation Suttons, Bill and Jim, consolidated and extended Sutton Tools’ position in the market, through their absolute commitment to quality, innovation and persistence.
Sutton Tools established Surface Technology Coatings and for the first time could offer physical vapour deposition (PVD) coatings on their products. Previously any coated tools sold in Australia were imported.
With the expansion into a greater range of products the company officially changed its name from ‘Sutton Tool & Gauge’ to ‘Sutton Tools’.
During the 1990’s Peter and Robert Sutton joined the family business. Their combined experience and passion in cutting tools has positioned Sutton Tools as an Australian champion in manufacturing.
...of course, after a proud history spanning over 100 years it’s always tempting to keep looking to the past. However, it is just as important, if not more so, to look to the future.
Manufacturing and Distribution Centre in New Zealand
Sutton Tools purchased Patience & Nicholson New Zealand (Evacut) to increase manufacturing capacity.
Asia Distribution Centre
To provide a greater level of service to the company’s South East Asian customers, an office and distribution centre was established in Singapore
Australian Made License
Sutton Tools becomes licensee of the Australian Made campaign, reaffirming our commitment to Australian Manufacturing.
1993 1995 2000 2006 2008 1994
Achievement of ISO 9001
Accreditation
Sutton Tools achieved quality accreditation ISO 9001. The structure of controls and checks throughout the manufacturing process ensures that we continually manufacture products that will exceed customer expectations.
A Global Vision
Robert Sutton was appointed Sutton Tools first Export Manager. His vision leads to rapid expansion into the ‘high performance’ product category to compete in the global market.
Export Milestone
Sutton Tools sold the 5 millionth drill bit to Germany.
Sutton Tools Europe
Sutton Tools Europe was established with an office and warehouse based in the Netherlands.
The Tech Centre
Facilities for specials and regrinding services were established to support the market in high performance cutting tools, with a specific focus on carbide.
Victorian Manufacturing Hall of Fame
The Vic. Government, in partnership with the Victorian Industry Manufacturing Council, inducted Bill and Jim Sutton into the Victorian Manufacturing Hall of Fame Honour Roll for their outstanding contributions to manufacturing excellence.
DMTC Partnership
Sutton Tools becomes a member of Defence Materials Technology Centre (DMTC) a collaborative venture between industry, universities and government research agencies.
4th Generation
Suttons took the helm
Peter and Robert Sutton took the helm to move Sutton Tools into the next century.
USA Warehouse and Distribution Centre
Sutton Tools USA was established. With a Warehouse and Distribution Centre in North America, Sutton Tools can now be recognised as a global company providing world class cutting tools.
Purchase of Carbitool Pty Ltd
Sutton Tools acquired Australian manufacturer Carbitool Pty Ltd to expand the carbide tools and wood working range.
Sutton Tools Celebrate 100 Years Awarded Manufacturer of the year at 2017 Victorian Manufacturing Hall of Fame.
Purchase of Fenn Tool Ltd
Sutton Tools acquired leading UK cutting tool manufacturer and distributor Fenn Tool Ltd to increase presence in the UK market.
P&N® Celebrate 100 Years Iconic Australian tool brand Patience & Nicholson celebrates 100 years in Australia. What a fantastic milestone!
Launch of the Thomastown Smart Centre
Sutton Tools
S.M.A.R.T Centre (Supporting Manufacturing Advances, Research and Technology) was built.
Sutton Tools endeavours to minimise impacting factors that will reduce its carbon footprint and environmental impact.
A well-managed structured system embracing all manufacturing processes from the floor up, driven with a continuous improvement policy ensures that our customers can be completely satisfied with the quality of our products. This includes all aspects of the purchasing process, with full traceability from the moment customers place the order to delivery.
Sutton Tools is a leader in the field of the conventional grinding and advanced super abrasive grinding. This Grinding Technology ensures that our cutting tools are of the highest accuracy and performance. Modern CNC machines give pick-and-place robot handling functions, that not only give repeatable quality operations but a safer work place environment.
The structure of controls and checks throughout the manufacturing process, backed by documented procedures and support personnel ensures that we continually manufacture products that will exceed customer expectations.
We are here to help you
Stock requirements and needs can vary from customer to customer and Sutton Tools has implemented varied ordering systems to receive orders and seamlessly process them.
We combine the latest logistic technology (freight management systems) with personalised customer service to ensure that you get the products you order, when you need them on time, every time.
Our comprehensive customer service comprises:
• EDI and internet ordering
• Fully integrated ERP system
• Automatic delivery and order confirmation
• Quick backorder response
My Sutton is an online customer portal where you will be able to gain 24/7 online access to Sutton Tools. My Sutton provides you with secure and easy access to:
• Your Orders
• Pricing and stock availability
• Invoicing and delivery information
For more information, contact your Sutton Tools sales representative.
We have over 20,000 SKUs and our stock availability consistently averages in the high 90%
Our International Distribution Centre uses modern radio frequency scanning technology coupled with the latest carousel and stock replenishment systems which allows accurate stock control and efficient warehouse operation. We have over 20,000 SKUs and our stock availability consistently averages in the high 90%. From a customer perspective, this provides confidence in breadth and depth of stock cover and reliable delivery service.
Our Distribution Centre comprises:
• Modern radio frequency scanning technology and latest carousel and stock replenishment systems
• Computerised dispatch system
• Warehousing over 20,000 SKUs
• Picking over 10,000 items daily
• Dispatch of over 1,000 consignments daily
• Order and dispatch within one hour turnaround
• Global Storage Area in excess of 5,000m²
Sutton Tools use state-of-art CNC tool grinding equipment, and manufacturing processes to produce specialised cutting tools, distribute to industries such as plumbing, electrical, automotive, aerospace, marine, transport, construction, surgical, manufacturing and agriculture.
We use only the very best European grades of materials including powder metallurgy, HSS cobalt and ultra-fine grain carbide. Materials are complimented by the latest generation of thin film PVD coatings, providing many advantages in tool life, component surface finishes and the ability for the tools to operate in low or minimum coolant environments, making them more environmentally friendly.
All tools are subject to stringent quality and performance checking and testing to ensure best results. Our customers can benefit from the advantages of our reliable cost effective world’s-best practice manufacture, supply and support capabilities, now and well into the foreseeable future. Our Special Tools division offers express service on non-standard taps and other cutting tools.
Australia’s only company to provide regrinding, coating and heat treatment on the one site.
The regrinding service significantly reduces tooling costs over buying new tools. Our customers benefit from Sutton Tools advanced super abrasive grinding expertise providing high accuracy and quality. All tools are subject to stringent quality and performance checking and testing to ensure best results.
Complementing our regrind facility, Surface Technology Coating (STC) provides a Physical Vapour Deposition (PVD) coating service, and is at the forefront of heat treatment and surface engineering technology.
In addition to providing PVD coating, STC provides plasma nitriding and vacuum heat treatment for various tools and components. Our unique position enables us to provide tailored solutions to a wide range of friction and wear problems.
Suitable for materials up to 1400N/mm²
• Strong core
• Micro geometry & surface conditioning for optimal chip control
• AlCrN for maximum tool life
Forets carbure 3xD, hélice 30°, type UNI
• Convient aux materiaux jusqu'à 1400 N/mm²
• Noyau renforcé
• Micro géométrie et traitement surface optimisé pour un bon controle des copeaux
• Revêtement AlCrN pour une durée de vie maximum
Punte Metallo Duro, 3 x D, R30 UNI
Ideale per materiali fino a 1400N/mm² Nocciolo rinforzato
Micro geometria & rivestimento tagliente ideale per un ottimo controllo truciolo AlCrN per massimizzare la vita utensile
Brocas de Metal Duro, 3 x D, R30 UNI
• Adecuado para materiales hasta 1400N/mm²
• Núcleo Reforzado
• Micro geometría y acondicionamiento de la superficie para un control óptimo de la viruta
• AlCrN para una máxima vida útil de la herramienta
Sutton Tools item # system makes it easier to identify a product. The codes are based on a universal prefix and suffix system.
Prefix (Catalogue Code) – is alpha numeric, and is unique to a specific product range. The letter is relevant to the type of tool, and the number refers to a product range.
C - Countersinks
D - Drills
E - Endmills
L - Literature
R - Reamers
T - Taps
Z - Tool Holders / Chucks
Suffix (Size Ref.) – in most cases is relevant to the diameter or size reference of an item and is based on a metric value.
For example 5mm = 0500, and 1/4" = 0635 (inch converted to decimal).
Suffix can also refer to set code or number of pieces in a set.
Benefits of the coding system
• Range identification simplified.
• Go online to suttontools.com and search by range.
Product Group (A0202 – Z1108)
These codes enable our distributor partners to identify their pricing structure on any particular product.
Material
This highlights what the product is made of. (e.g. VHM = Carbide, HSS = High Speed Steel) For the full list of explanation, refer to page 75 of the technical information section.
Surface Finish
Many of our products have various surface coatings to improve the performance. Surface coatings improve productivity by increasing speeds and feeds and reducing friction related problems.
Symbols
For all of our product pages you will find symbols which depict what specifications these products were made to. Symbols have been used to simplify product identification.
A full list of symbols can be found at the start of this catalogue.
Some common examples are:
Vc Page # - Speed & Feed Data
Vc Page #: 58
This graphic indicates what page number to reference in the Technical Information section of this catalogue for the speed and feed data of the tool.
DIN Taps UNC, Spiral Flute, R50 Black Magic
DIN Taps UNC, Spiral Point (Gun), Black Magic
DIN Taps UNC, Spiral Point (Gun), NH+
DIN Taps UNC, Spiral Point (Gun), VA
DIN Taps UNF, Spiral Flute, R45 VA DH
DIN Taps UNF, Spiral Flute, R50 Black Magic
DIN Taps UNF, Spiral Point (Gun), Black Magic
DIN Taps UNF, Spiral Point (Gun), VA
Drills
D323 7 A0210 Drill, 3xD, R30 UNI, Shank Form HA
D326 11 A0210 Drill, 5xD, R30 UNI, Shank Form HA
D329 7 A0210 Drill, 3xD, R30 UNI, IK, Shank Form HA
D332 11 A0210 Drill, 5xD, R30 UNI, IK, Shank Form HA
D335 14 A0210 Drill, 8 x D, R30 UNI, IK, Shank Form HA
D356 7 A0210 Drill, 3xD, R30 VA Black Magic, HA Shank
D358 11 A0210 Drill, 5xD, R30 VA Black Magic, HA Shank
D371 15 A0210 Drill, 12xD, R30 UNI, IK, Black Magic XL
D372 17 A0210 Drill, 15xD, R30 UNI, IK, Black Magic XL
D373 17 A0210 Drill, Extra Long, 20xD, R30 UNI, IK, Black Magic XL
D375 17 A0210 Drill, 20 & 30xD, R30 UNI, IK, Black Magic XL
Form C VHM Pertura Tip -
Form C VHM Pertura Tip
Pertura Tip -
Form C VHM Pertura TipEndmills Catalogue
T332 34 D0408 Tap, Forming, With Multi Coolant Groove, NH
T350 53 D0408 Tap, Spiral Point (Gun), VA PM
T685 31 D0410 Tap, Spiral Flute, R50 Black
(Gun), Black Magic
T689 35 D0410 Tap, Spiral
• 3xd1 to 30xd1 hole depths • Ultra fine grain type carbide
ISO VDI Material Group
P A Steel N
M R Stainless Steel VA
K F Cast Iron GG
N N Non-Ferrous Metals, Aluminiums & Coppers AI W
S S Titaniums & Super Alloys Ti Ni
H H Hard Materials (≥ 45 HRC) H
^ VDI 3323 material groups can also be determined by referring to the material cross reference listing in the application guide at the back of this catalogue.
• D323/D329 - Suitable for materials up to 1400N/mm2
- Micro geometry & surface conditioning for optimal chip control
- AlCrN for maximum tool life
• D356 - Excellent solution for stainless steels & difficult super alloy type materials
- Optimised geometry ensures no work hardening and high productivity
- HELICA for outstanding oxidation resistance and hot hardness
• D323/D329 - Suitable for materials up to 1400N/mm2
- Micro geometry & surface conditioning for optimal chip control
- AlCrN for maximum tool life
• D356 - Excellent solution for stainless steels & difficult super alloy type materials
- Optimised geometry ensures no work hardening and high productivity
- HELICA for outstanding oxidation resistance and hot hardness
D323/D329 - Suitable for materials up to 1400N/mm2
- Micro geometry & surface conditioning for optimal chip control
- AlCrN for maximum tool life
• D356 - Excellent solution for stainless steels & difficult super alloy type materials
- Optimised geometry ensures no work hardening and high productivity
- HELICA for outstanding oxidation resistance and hot hardness
• D323/D329 - Suitable for materials up to 1400N/mm2
- Micro geometry & surface conditioning for optimal chip control
- AlCrN for maximum tool life
• D356 - Excellent solution for stainless steels & difficult super alloy type materials
- Optimised geometry ensures no work hardening and high productivity
- HELICA for outstanding oxidation resistance and hot hardness
• D326/D332 - Suitable for materials up to 1400N/mm2
- Micro geometry & surface conditioning for optimal chip control
- AlCrN for maximum tool life
• D358 - Excellent solution for stainless steels & difficult super alloy type materials
- Optimised geometry ensures no work hardening and high productivity - HELICA for outstanding oxidation resistance and hot hardness
Application
Shank Form (DIN 6535) HA HA HA ISO Materials
• D326/D332 - Suitable for materials up to 1400N/mm2
- Micro geometry & surface conditioning for optimal chip control
- AlCrN for maximum tool life
• D358 - Excellent solution for stainless steels & difficult super alloy type materials
- Optimised geometry ensures no work hardening and high productivity
- HELICA for outstanding oxidation resistance and hot hardness
Vc Page #: 69
Catalogue Code D326 D332 D358
Product Group A0210 A0210 A0210
Material VHM VHM VHM
Surface Finish AlCrN AlCrN HELICA
Application N N VA
Geometry R30 R30 - IK R30 - IK Point Type 140° Form C 140° Form C 140° 4 Facet Form C Shank Form (DIN 6535) HA HA HA ISO Materials
• D326/D332 - Suitable for materials up to 1400N/mm2
- Micro geometry & surface conditioning for optimal chip control
- AlCrN for maximum tool life
• D358 - Excellent solution for stainless steels & difficult super alloy type materials
- Optimised geometry ensures no work hardening and high productivity
- HELICA for outstanding oxidation resistance and hot hardness
Product Group A0210 A0210 A0210
Material VHM VHM VHM
Surface Finish AlCrN AlCrN HELICA
Application N N VA
Geometry R30 R30 - IK R30 - IK Point Type 140° Form C 140° Form C 140° 4 Facet Form C Shank Form (DIN 6535) HA HA HA ISO Materials
• - Suitable for materials up to 1400N/mm2
• - Strong core with internal coolant supply
• - Micro geometry & surface conditioning for optimal chip control
• - AlCrN for maximum tool life
A0210
VHM
AlCrN
0450
4,6 81 43 6 D335 0460
4,7 81 43 6 D335 0470
3/16 95 57 6 D335 0476
4,8 95 57 6 D335 0480
4,9 95 57 6 D335 0490 0500 5,0 95 57 6 D335 0500 0510 5,1 95 57 6 D335 0510 0516 13/64 95 57 6 D335 0516 0520 5,2 95 57 6 D335 0520 0530 5,3 95 57 6 D335 0530 0540 5,4 95 57 6 D335 0540 0550 5,5 95 57 6 D335 0550 0556 7/32 95 57 6 D335 0556 0560 5,6 95 57 6 D335 0560 0570 5,7 95 57 6 D335 0570 0580 5,8 95 57 6 D335 0580 0590 5,9 95 57 6 D335 0590
15/64 95 57 6 D335 0595
6,0 95 57 6 D335 0600 0610 6,1 114 76 8 D335 0610 0620 6,2 114
•
Group A0210
• • Suitable for materials up to 1200N/mm²
• Strong core with internal coolant
• Micro
• Pertura for
• - Suitable for materials up to 1200N/mm2
• - Strong core with internal coolant supply
• - Micro geometry and surface conditioning for optimal chip control
• - Pertura coated tip for maximum tool life
Code D372 D373 D375 Product Group A0210 A0210 A0210
ISO VDI Material Group
P A Steel
M R Stainless Steel
K F Cast Iron GG
N N Non-Ferrous Metals, Aluminiums & Coppers AI W
S S Titaniums & Super Alloys Ti Ni
H H Hard Materials (≥ 45 HRC) H ^ VDI 3323 material groups can also be determined by referring to the material cross reference listing in the application guide at the back of this catalogue.
• General purpose machine tap
• Bright finish ideal for non-ferrous metals
• Suitable for materials up to 1000N/mm2
• Through holes
• Depths up to 2 x d1
• Blu finish ideal for ferrous metals and stainless steels
• Also suitable for materials up to 1000N/mm2
• Through holes
• Depths up to 2 x d1
• Suitable for general steels up to 35 HRC
• Through holes
•
• Use in stainless steels and high strength steels
• Suitable for materials up to 850N/mm²
• Through holes
• Depths up to 3 x d1
DIN 371 REINFORCED SHANK
• Universal high performance tapping
• PM-HSSE V3 offers superior tool life
• Use in stainless steels and high strength steels up to 850N/mm²
• Through holes up to 3 x d1
• Suitable for synchronous tapping in machine operations
• Suitable for harder materials up to 42 HRC
• Through holes
•
• General purpose machine tap
• Bright finish ideal for non-ferrous metals
• Also suitable for materials up to 1000N/mm2
• Blind holes
• Depths up to 2 x d1
• Blu finish ideal for ferrous metals and stainless steel
• Suitable for materials up to 1000N/mm2
• Blind holes
• Depths up to 2 x d1 Catalogue Code T832
• Suitable for general steels up to 35 HRC
• Blind holes
• Depths up to 3 x d1
• Suitable for controlled tapping in deep holes
• Use in stainless steels and high strength steels up to 850N/mm²
• Blind holes
• Depths up to 3 x d1
• Suitable for controlled tapping in deep holes
• Use in stainless steels and high strength steels up to 850N/mm²
• Blind holes
• Depths up to 3 x d1
Catalogue Code T202
Discount Group D0408
• Universal high performance tapping
• PM-HSSE V3 offers superior tool life
• Use in stainless steels and high strength steels up to 850N/mm²
• Blind holes up to 3 x d1
• Suitable for synchronous tapping in machine operations
•
• Suitable for
•
• For use in grey cast iron (GG)
• Through & blind holes
•
• SPM for superior performance
• Suitable for materials with restricted ductility
• Application specific geometry for harder materials (GGV)
• Through or blind holes
• Depths up to 2 x
• Universal high performance tapping
• PM-HSSE V3 offers superior tool life
• Use in stainless steels and high strength steels up to 850N/mm²
• Through holes up to 3 x d1
• Suitable for synchronous tapping in machine operations
• Suitable for harder materials up to 42 HRC
• Through holes
• Depths up to 3 x d1
• Universal high performance tapping
• PM-HSSE V3 offers superior tool life
• Use in stainless steels and high strength steels up to 850N/mm²
• Depths up to approx. 3 x d1
• Suitable for synchronous tapping in machine operations
• Suitable for
•
•
• HSSE, for use in grey cast iron (GG)
• VHM, for use in Al >10% Si & cast iron (GGG)
• Through & blind holes
• Depths up to 3 x d1
• SPM for superior performance
• Suitable for materials with restricted ductility
• Application specific geometry for harder materials (GGV)
• Through or blind holes
• Depths up
• Use in stainless steels and high strength steels up to 1000N/mm²
• Through holes
• Suitable for machine operations
• Depths up to approx. 3 x d1
• Universal high performance tapping
• PM-HSSE V3 offers superior tool life
• Use in stainless steels and high strength steels up to 850N/mm²
• Through holes up to 3 x d1
• Suitable for synchronous tapping in machine operations
watch the video
Catalogue Code T693
Discount Group D0410 Material PM-HSSE V3 Surface Finish HARDLUBE
• Suitable for harder materials up to 42 HRC
• Through holes
• Depths up to 3 x d1
• Use in stainless steels and high strength steels up to 1000N/mm²
• Blind holes
• Suitable for synchronous tapping in machine operations
• Depths up to approx. 3 x d1
• Universal high performance tapping
• PM-HSSE V3 offers superior tool life
• Use in stainless steels and high strength steels up to 850N/mm²
• Through holes up to 3 x d1
• Suitable for synchronous tapping in machine operations
V3
•
•
•
• Use in stainless steels and high strength steels up to 1000N/mm²
• Blind holes
• Suitable for synchronous tapping in machine operations
• Depths up to approx. 3
• Universal high performance tapping
• PM-HSSE V3 offers superior tool life
• Use in stainless steels and high strength steels up to 850N/mm²
• Suitable for synchronous tapping in machine operations
• Blind holes up to 3 x d1
• Use in stainless steels and high strength steels up to 1000N/mm²
• Through holes
• Suitable for machine operations
• Depths up to approx. 3 x d1
• Universal high performance tapping
• PM-HSSE V3 offers superior tool life
• Use in stainless steels and high strength steels up to 850N/mm²
• Suitable for synchronous tapping in machine operations
• Through holes up to 3 x d1
• Use in stainless steels and high strength steels up to 1000N/mm²
• Blind holes
• Suitable for synchronous tapping in machine operations
• Depths up to approx. 3 x d1
• Universal high performance tapping
• PM-HSSE V3 offers superior tool life
• Use in stainless steels and high strength steels up to 850N/mm²
• Suitable for synchronous tapping in machine operations
• Blind holes up to 3 x d1
• Use in stainless steels and high strength steels up to 1000N/mm²
• PM-HSSE V3 offers higher edge hardness than standard VA series
• Through holes
• Suitable for synchronous tapping in machine operations
• Depths up to approx. 3 x d1
Catalogue Code T350
Discount Group D0408
Material PM-HSSE V3 Surface Finish TiCN
• Universal high performance tapping
• PM-HSSE V3 offers superior tool life
• Use in stainless steels and high strength steels up to 850N/mm²
• Suitable for synchronous tapping in machine operations
• Through holes up to 3 x d1
P A Steel
M R Stainless Steel
K F Cast Iron
N N Non-Ferrous Metals, Aluminiums & Coppers
S S Titaniums & Super Alloys
H H Hard Materials (≥ 45 HRC) H
^ VDI 3323 material groups can also be determined by referring to the material cross reference listing in the application guide at the back of this catalogue.
• Highly efficient finishing
• Form tolerance ±0.01 mm
• Suitable for high-strength materials
• Suitable for HSC finishing Vc Page
Catalogue Code E700
Discount Group B0210 Material VHM-ULTRA
Surface Finish AlCrN
Sutton Designation UNI Geometry R30
Shank Form (DIN 6535) HA / HB Shank Tolerance h6
•
•
•
Catalogue Code E701
Discount Group B0210
Material VHM-ULTRA
Surface Finish AlCrN Sutton Designation UNI Geometry R30 Shank Form (DIN 6535) HA Shank Tolerance h6
• Highly efficient finishing
• Form tolerance ±0.01 mm
• Suitable for high-strength materials
• Suitable for HSC finishing
•
• Suitable for
• Suitable for HSC
2
2
4
4
4
4
4
4
5
6
6
6
6
6
6
6
6
6
6
6
6
6
6
6
6
6
6
6
12
12
12
12
12
14.1
14.1
14.1
14.1
14.2
14.2
14.2
14.3
14.3 1.4542 X5CrNiCuNb16-4
S31803 / S32205 (SAF2205)
31 1.4558 X 2 NiCrAITi 32 20 NA 15 N 08800
31 1.4562 X 1 NiCrMoCu 32 28 7 N 08031
31 1.4563 X 1 NiCrMoCuN 31 27 4
31 1.4864 X 12 NiCrSi 36 16 NA 17 Z 12 NCS 35.16
31 1.4958 X 5 NiCrAITi 31 20
31 2.4668 NiCr19NbMo NC20K14 AMS 5544
32 1.4977 X 40 CoCrNi 20 20 Z 42 CNKDWNb
33 2.4360 NiCu30Fe NA 13 NU 30
33 2.4610 NiMo16cR16Ti
33 2.4630 NiCr20Ti HR 5,203-4 NC 20 T
33
33 2.4858 NiCr21Mo NA 16 NC
34 2.4668 NiCr19FeNbMo
35
35 3.7115 TiAl5Sn2
36 3.7025 Ti 1 2 TA 1 R
36 3.7225 Ti 1 pd TP 1
37 3.7124 TiCu2 2 TA 21-24
37 3.7145 TiAl6Sn2Zr4Mo2Si R 54620
37 3.7185 TiAl4Mo4Sn2 TA 45-51; TA 57
37 3.7195 TiAl 3 V 2.5
37 TiAl4Mo4Sn4Si0.5 37
40
40
ISO VDI Material Group
P A Steel
M R Stainless Steel
K F Cast Iron
N N Non-Ferrous Metals, Aluminiums & Coppers AI W
S S Titaniums & Super Alloys Ti Ni
H H Hard Materials (≥ 45 HRC) H
^ VDI 3323 material groups can also be determined by referring to the workpiece material cross reference listing. Refer to main index of this section.
A (Annealed), AH (Age Hardened), C (Cast), HT (Hardened & Tempered), QT (Quenched & Tempered)
= Optimal | Regular = Effective
Notes on Drilling
1. Step feeding or pecking is required for drilling greater than 3 x Ø.
2. When drilling cast surface & black (ie: not machined surface), reduce drilling speed by 20%.
3. For optimal positional accuracy and hole size, the use of spot drills is recommended prior to drilling desired hole, refer to our standard range (D175).
4. For hole depths greater than 7 x Ø, pre-drill initially to pilot start for more accurate hole position and eliminate drill wandering. The pilot can be drilled with short rigid drill, approx. 3 x Ø in depth and reduced feed to ensure accurate pilot hole.
reference listing. Refer to main index of this section.
A (Annealed), AH (Age
C (Cast), HT (Hardened &
Bold = Optimal | Regular = Effective
Notes on Milling
QT (Quenched &
1. Above values are guidelines for the size and type of cut nominated.
2. For long series tools, reduce speed by 40% and feed by 20%.
ISO VDI Material Group
M R Stainless Steel VA
P A Steel N UNI
K F Cast Iron GG
N N Non-Ferrous Metals, Aluminiums & Coppers AI W
S S Titaniums & Super Alloys Ti Ni
H H Hard Materials (≥ 45 HRC) H
^ VDI 3323 material groups can also be determined by referring to the workpiece material cross reference listing. Refer to main index of this section.
Condition: A (Annealed), AH (Age Hardened), C (Cast),
= Optimal | Regular = Effective
Notes on Tapping
(Hardened & Tempered), QT (Quenched & Tempered)
1. The speeds listed above are a recommendation only, and are based on depth of thread listed, speeds can be adjusted on application. As a general rule; -If hole depth required is less than above mentioned = increase speed -If hole depth required is more than above mentioned = reduce speed
2. Taps must be driven by the square to eliminate slippage, eg, ER-GB collets (square drive).
3. When using spiral flute taps with length compensation tapping attachment, it is recommended to short pitch the feed 95%, to eliminate tap cutting oversize, eg. M6x1 @ 1000RPM, Feed rate= 950mm/min.
4. Forming taps are suitable for materials with >10% elongation
ISO VDI Material Group
P A Steel
M R Stainless Steel
K F Cast Iron
N N Non-Ferrous Metals, Aluminiums & Coppers
S S Titaniums & Super Alloys
H H Hard Materials (≥ 45 HRC) H
^ VDI 3323 material groups can also be determined by referring to the workpiece material cross reference listing. Refer to main index of this section.
Notes on Tapping
1. The speeds listed above are a recommendation only, and are based on depth of thread listed, speeds can be adjusted on application. As a general rule; -If hole depth required is less than above mentioned = increase speed
-If hole depth required is more than above mentioned = reduce speed
2. Taps must be driven by the square to eliminate slippage, eg, ER-GB collets (square drive).
3. When using spiral flute taps with length compensation tapping attachment, it is recommended to short pitch the feed
to eliminate tap cutting oversize, eg. M6x1 @ 1000RPM, Feed rate= 950mm/min.
4. Forming taps are suitable for materials with >10% elongation
Code Problem
1 Thread is oversize
2 Axial miscutting of thread
3 Thread is undersize
4 Thread has bellmouthed entry
5 Thread surface is rough and unclean
6 Low tool life
7 Partial or complete tap breakage on FORWARD or BACKWARD movement
1 2 3 4 5 6 7 Possible reason
•
•
• •
• Wrong tap, cutting geometry of the tap is not suitable for this operation
• • Tap hole diameter is undersize
• Misalignment - tap hole position, or angle is not correct
• The axial machine spindle movement is not free and easy
• Cold welding on the thread flanks of the tap
• Poor guidance of the tap because of little thread depth
•
•
•
• • Speed is too high
• • Chip clogging
• • The lubrication wrong, additives or the coolant supply is not sufficient
• Spiral fluted taps are over pressured in the initial cutting phase (retracting pulling force)
• Spiral pointed taps (gun taps) are not receiving enough pressure in the initial cutting phase
• •
•
Tolerance on the tap is not identical to the tolerance on the drawing or on the gauge
Wrong initial cutting pressure has been used or the machine spindle is not moving along its axis free and easy
• • Tap is over loaded, either from coarse pitch and/or tough material
• Cold welding, material build-up (pick-up)
• • Hardened walls in drilled hole
• Over loading of teeth in the chamfer area
Solution
Use correct tap for the material group (see Expert Tool System, at www.suttontools.com)
Tap hole diameter should be in accordance to DIN336 or respective standard. For cold forming taps, a special hole diameter is needed.
a) check workpiece clamping
b) check machine settings
a) use mechanical feed
b) use tap holder with length compensation
a) use a new tap
b) improve and check lubrication
c) remove cold welding area from tap
d) use tap with surface treatment or coatings
a) use mechanical feed
b) use tap that has better guiding characteristics
a) improve lubrication
b) lower speed
a) use tap with different flute form
b) use coated taps
c) use tap set
Make sure that the coolant is correct and that the supply is sufficient
Spiral fluted taps should only be lightly pushed into the tap hole until it begins to cut. The tap holder should immediately begin to apply tension to the tap.
Spiral pointed taps and even left hand spiral flute taps must have a stronger pressure until they begin to cut. The tap holder should immediately begin to apply pressure to the tap (pushing force)
Use a tap which has a correct tolerance
a) use mechanical feed
b) use tap holder with length compensation
Use set of taps
a) improve coolant supply, use taps with surface treatments or coatings
b) check if surface treatment is correct for this application
a) use drill best suited to material being drilled
b) use new drill or boring tool
c) resharpen drilling or boring tools
d) if possible, heat treatment and coatings should only be made after threading
a) use a longer chamfer (check if the tap hole is blind hole or through)
b) use increased number of teeth in the chamfer area by selecting tap with increased number of flutes
• Tap hole chamfer is missing or wrong Countersink tap hole chamfer with correct angle
• Tap crashed against the bottom of tap hole
Use tap holder with length compensation and over load clutch
Alcrona (AlCrN) Aluminium Chromium Nitride Mono Layer 3200 HV 0.35
Durana AlTiN/ TiSiXN
• For general purpose applications
• For ferrous metals
• Prevents chip build-up on the cutting edges, especially in low carbon steels
• Oxide layer protects surface Good carrier of lubricants
For high-performance machining of aluminum and aluminum alloys
• ASX prevents the formation of built-up edges to a particularly large extent
• Reduces friction on the face and makes machining easier
• High degree of hardness also guarantees excellent wear protection
• Cutting and forming of copper, nickel, and monel metal
• Enhanced thermal stability and oxidation resistance Excellent corrosion resistance
• Low internal stress of coating results in excellent adhesion under high loads
• General purpose use
• Wide range of materials
• 3 to 8 times longer tool life than uncoated tools
• Higher tool speeds and feeds than uncoated tools
• High performance applications
• Difficult to machine materials
• Abrasive materials - cast iron and aluminium alloys Adhesive materials - copper and copper based alloys
• Abrasive materials – cast iron and heat treated steel Difficult to machine materials, such as stainless steel
• Higher speeds and feeds
• Reduces or eliminates use of coolants
• For challenging conditions
• Highly resistant to crater wear and oxidation
• Ideal for wet and dry machining
• Versatile application in high end drilling
High tool lifetimes
• Trouble-free chip transport
• Reduction of cutting forces
• Extremely high service life, even with deep-hole and dry drilling
• Hard materials
• Difficult to machine materials, eg. Ti alloys, Inconel
• High speeds and feeds
• Dry or MQL machining Machining of hardened steels (>52HRC)
Low alloy steels and high tensile steels
• Hardened steels up to 54 HRC
• Ideal for carbide tools
AlTiN-based and TiSiXN layers gives Durana a high degree of ductility and superior abrasive wear resistance
• Hugely improved performance during demanding machining operations. Helica Alcrona based Multi Layer
• Longer tool life
Higher cutting speeds and feeds
• Superb chip evacuation
• Greater number of regrinds
• Improved drill hole quality
• Excellent performance in abrasive material TiSiN TiSi based Multi Layer
• Suitable for high speed (wet / dry) and hard machining for difficult materials above 52 HRC.
• Suitable for high speed machining with hardened steels above 60 HRC to maximum of 63 HRC Vc and Vf = +50%
Latest generation PVD coating for long tool life in difficult to machine materials, such as Super Alloys & Stainless Steels
• High speed machining
Aldura TiAlN + AlCrN Multi Layer
Blue - Grey
Light Grey
• Suitable for minimum quantity lubrication (MQL) and dry machining
• Machining of hardened steels (>60HRC)
• Ideal for carbide tools
Even high thermal stresses hardly effect the superior hardness of the coating
• Its high hot hardness results in excellent abrasion resistance even at high cutting speeds
• Excellent friction and lubricating properties of the
provide optimal chip flow
Tapping and drilling of hard to machine materials
Suitable for minimum quantity lubrication (MQL) and dry machining
• For machining non-ferrous metals as well as composite and plastic materials.
• sp3 content of 60 – 70%
• Hard coating maintains cutting edge sharpness in machining abrasive materials
Abbreviations
HSS
HSS Co
HSSE Co 8%
HSSE
PM-HSSE V3
PM-HSS Co
SPM
VHM
VHM
VHM-ULTRA
Conventional high speed steel
5% cobalt grade of high speed steel
8% cobalt grade of high speed steel
Premium grade of high speed steel
Powdered metallurgy
- vanadium grade of high speed steel
Powdered metallurgy
- 8% Cobalt grade of high speed steel
Powdered metallurgy
- 11% Cobalt grade of high speed steel
Sub-micron grade of solid Carbide (ISO K15-K30)
Sub-micron grade of solid Carbide (ISO K40)
Sub-micron grade of solid Carbide (ISO K40-K50)
Application
Standard tool material for most common applications
High-heat resistance, especially suited for roughing or when coolant insufficient
Increased heat resistance and hardness, suitable for difficult-to-machine materials
Wide range of machine taps
Materials with hardness up to 40 HRC
Difficult-to-machine materials eg. stainless steels
Materials with hardness up to 45 HRC
Special applications, requiring very high edge hardness. Cutting tools with the appropriate geometry can be applied to workpiece materials with hardness up to 55 HRC
Tapping hardened steel
Sutton standard grade for endmills & drills
High performance grade for endmills
Description
Used for the manufacturing of cutting tools such as twist drills, endmills and taps.
Cobalt alloyed, tungsten-molybdenum high speed steel possessing high hardness, excellent cutting properties, high-red hardness and good toughness.
Available for applications that require a strong resistance to softening at elevated cutting temperatures. The ability of the steel to maintain its “red-hot hardness” is provided by the addition of cobalt. The high hot hardness is required for machining difficult materials such as nickel-base, titanium and highly alloyed steel.
Vanadium grade gives high wear resistance and toughness for most tapping applications.
PM-HSS V3 for higher performance tools, incorporates very fine and uniform grain structure allowing a high hardness to be achieved, whilst maintaining good toughness.
The addition of cobalt provides this material with the ability to maintain its strength and hardness level when exposed to extremely high cutting temperatures. This makes PM-HSS Co suitable for heavy duty tapping, in materials such as high alloyed steels to non-ferrous metals like Ni-base alloys & Ti-alloys.
An excellent bridge material between high speed steel and carbide. SPM offers very high red hardness, wear resistance and the highest compressive strength of any high speed steel.
Ultra fine grain type (0.8µm) with maximum toughness & high hardness, therefore especially recommended for rotating tools to machine hardened parts.
Ultra fine grain type (0.6µm) offers the ideal combination of hardness & toughness for high performance drilling & general milling applications
Ultra fine grain type (0.5µm) offers the best wear resistance for high performance milling applications.
All sizes are “suggested sizes” only and may be varied to suit individual requirements
*Taper pipe threads of improved quality are obtained when taper is pre-formed using Sutton Tools Taper Pipe Reamers.
Fluteless taps do not cut threads in the same manner as conventional taps – but actually FORM and FLOW the threads with an absence of chips. Used under suitable conditions, these taps produce threads with a high degree of finish not possible with ordinary taps. Ductile materials are most appropriate for forming of threads and must have a minimum 10% elongation.
Higher speeds and tool life
Reduced possibility of breakage due to no cutting edges and robust tool construction
Figure 1. No chips produced
Figure 2. Higher tensile strength threads produced due to grain structure following the thread form
Figure 3. For use in through and blind holes applications
-Low carbon steels
-Leaded steels
-Austenitic stainless steels
-Alloy steels; typically up to 1200 N/mm2, (36 Rc) with a minimum 10% elongation
Figure 4. New polygon profile
Figure 5. New radiused blend on polygon profile
Figure 6. Thread profile with radius crest
Figure 7. Polished tool surface, surface finish
-Aluminium die castings alloys (low silicon, 10% max;)
-Wrought aluminium alloys (Ductile)
-Zinc die casting alloys
-Copper and copper alloys
Because the thread produced by a fluteless tap is substantially stronger than a conventional thread, greater tool life and efficiency may be obtained when forming up to 65% thread. Threads may be formed up to 80% of depth, but tool life will be reduced and work clamping pressure necessarily increased. Greater tapping speeds allow the metal to flow far more readily, so 60 feet per minute minimum may be used as a guide, but this could increase with the type of material being tapped. A depth of 65% is recommended for the ductile materials mentioned, but this percentage will be reduced for less ductile materials to maintain all-round efficiency.
Refer Tapping Drill Size Chart for recommended sizes (Suitable for Unified, Whitworth and Metric sizes only). The formula to calculate the theoretical hole size for a required percentage of thread is:
It is to be noted that the drill size for fluteless tapping is always larger than the P.D. of the thread. A drill size equal to the P.D. of the thread would produce 100% of thread, but this is NOT recommended.
As the additional driving torque is only up to 50% increase, any conventional driving equipment using the square as a drive is suitable for fluteless tapping
In general it is best to use a good cutting oil or lubricant rather than a coolant for fluteless tapping. Sulphur base and mineral oils, along with most friction reducing lubricants recommended for use in cold extrusion or metal drawing, have proven best for this work. Make sure lubricant is clean, free from chips swarf and filings in suspension, which produce a poor finish and jamming, sometimes breakage – extra filtration may be required.
Because the fluteless tap displaces metal, some metal will be displaced above the mouth of the hole during tapping, countersink or chamfer the hole prior to tapping will reduce the extrusion within the countersink and not interfere with the mating part.
Basic
Thread Cutting
Thread Forming
Existing Method
Uncoated
Component:
Material Group: Material Grade:
Characteristics of Material:
Short Chipping
Long Chipping Hole Type:
Through Hole
Tapping Hole Size: Drilled Cast Punched
Hole Depth:
Machine Details
Machine Type:
CNC
Semi Auto
Manual
Machine Direction:
Vertical
Horizontal
Oblique
Work Piece Holder: Stationary
Rotating
Coolant: Neat Oil Mist / Dry Emulsion >5% Emulsion >10%
Feed: CNC
Mechanical Pneumatic Hydraulic Manual
Tapping Attachment:
Tapping Chuck
Tension
Compression
Tapping Attachment
Tapping Chuck (rigid)
Collet Chuck (length compensating)
Drill Details
Basic Geometry
Tool Type:
Drill
Step Drill
Countersinks
Subland Drills
Core Drills
Centre Drills
Total Length (mm):
Number of Steps:
Without
With steps Step Diameter (mm):
TiAIN
Steam Oxide
other
Point Design
Point Geometry:
Relieved Cone
For Grey Cast Iron
Centre Point
Facet Point Grind
other
Shank Design:
Reinforced
Without Flat
With Flat
Parallel Straight Shank
Morse Taper
other
(specify if known)
Surface finish/coating Uncoated TiN TiCN TiAN AlCrN Uncoated TiN TiCN TiAN AlCrN
Cost per tool $ $
if known)