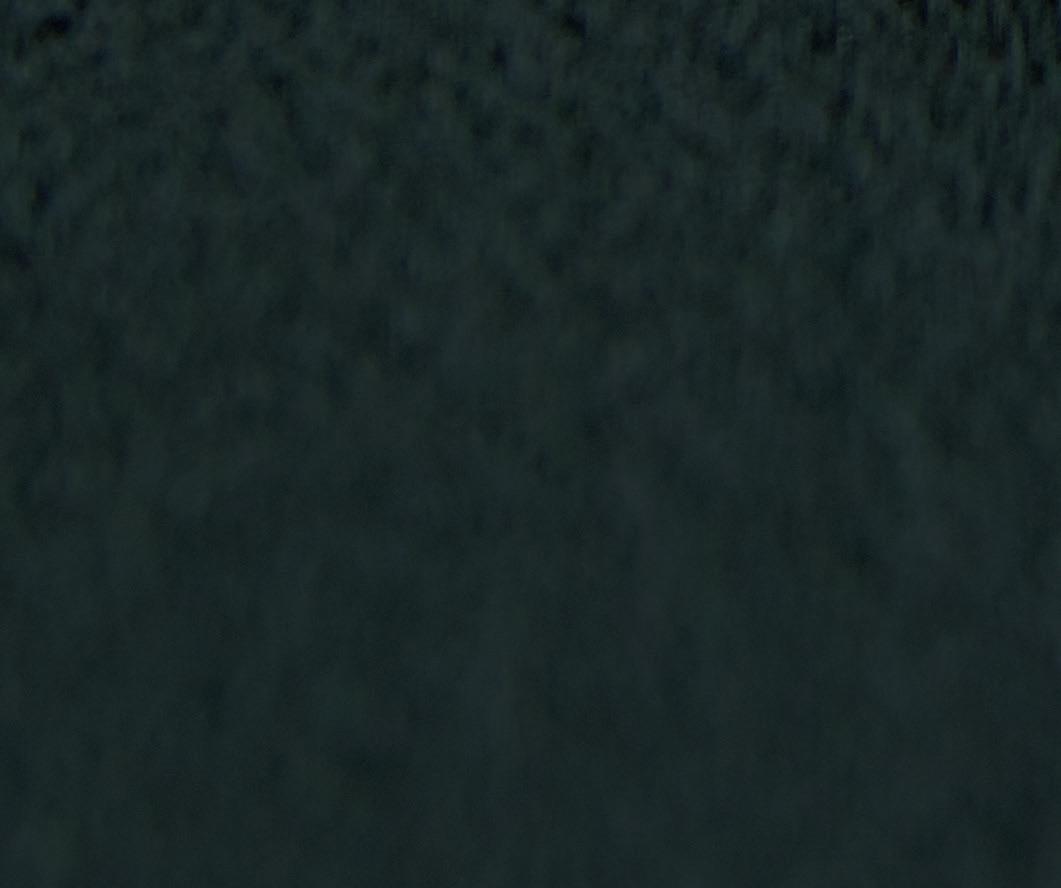
2 minute read
Built on Experience. Proven Solutions.
With over 30 years pioneering integrated additive manufacturing solutions, we have mastered the interactions between lasers and powdered materials, and go above and beyond purely technical capabilities.
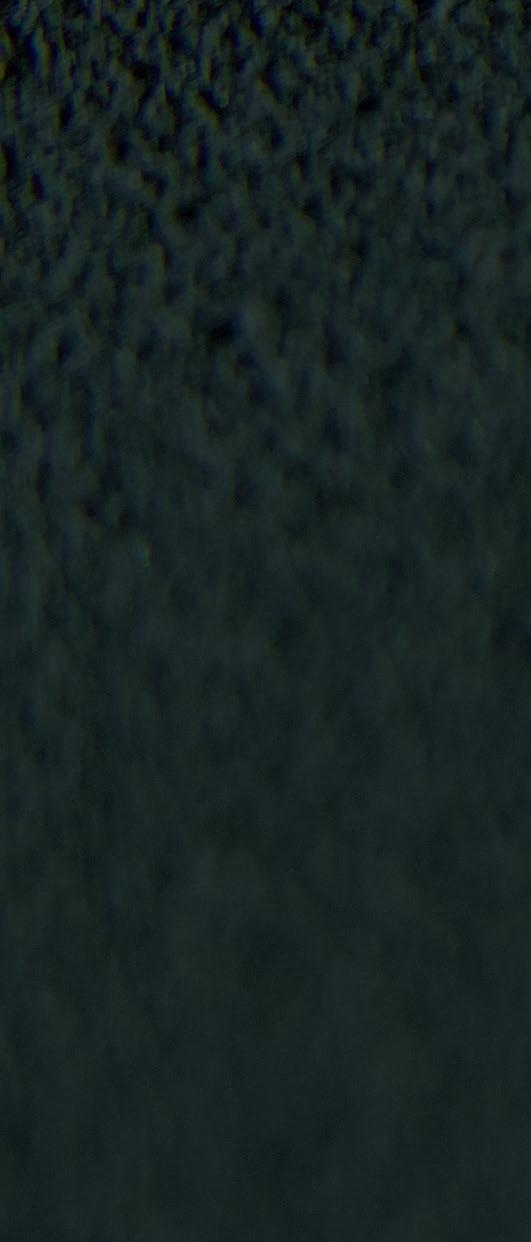
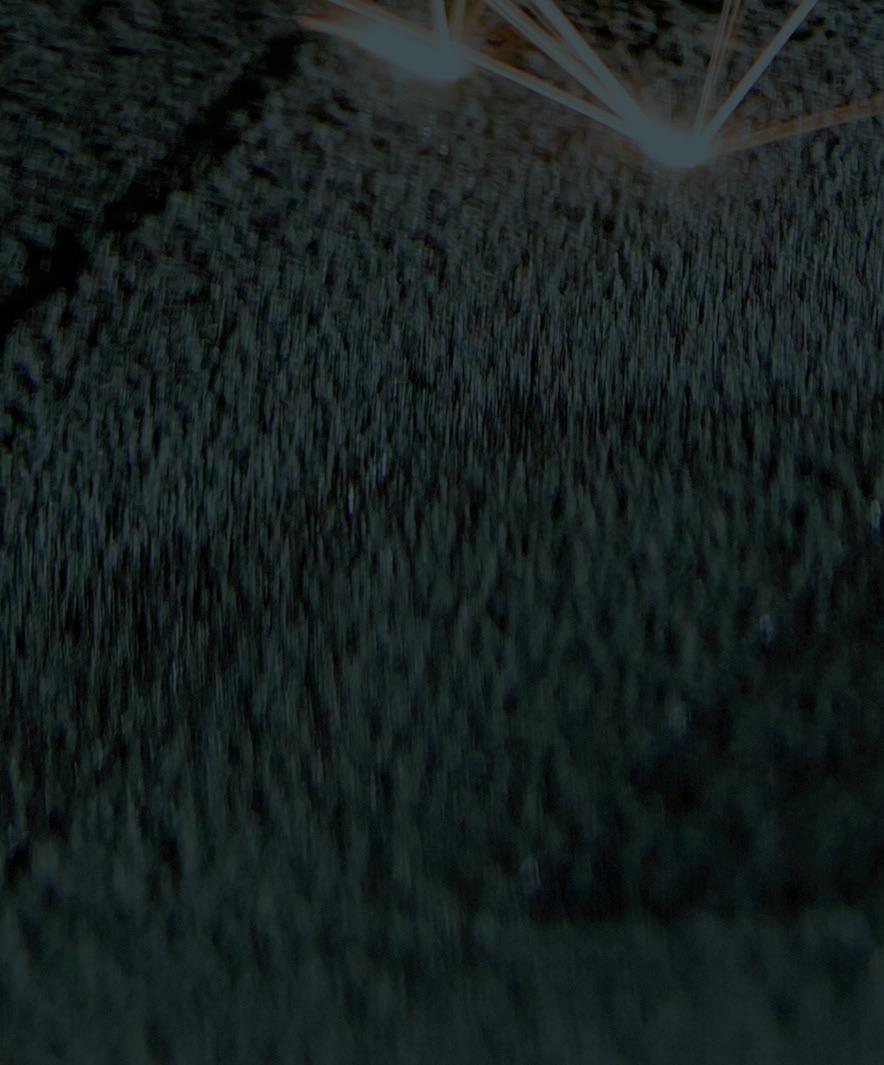
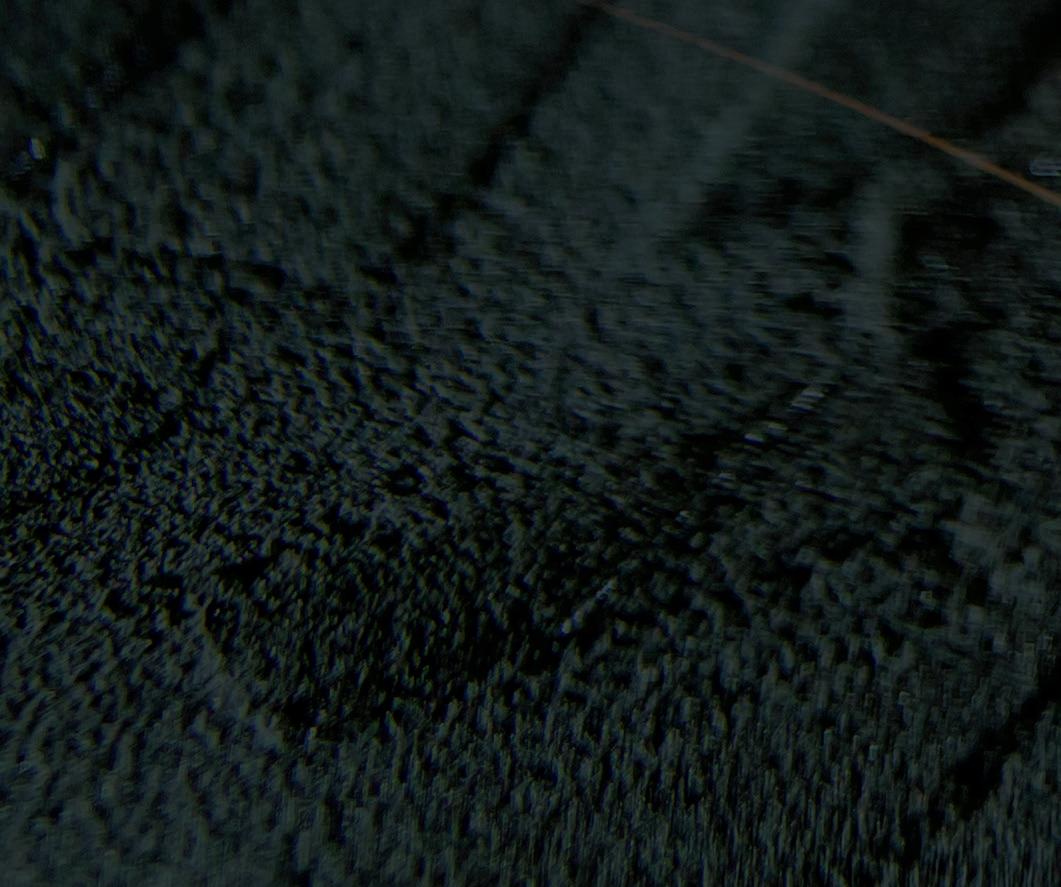
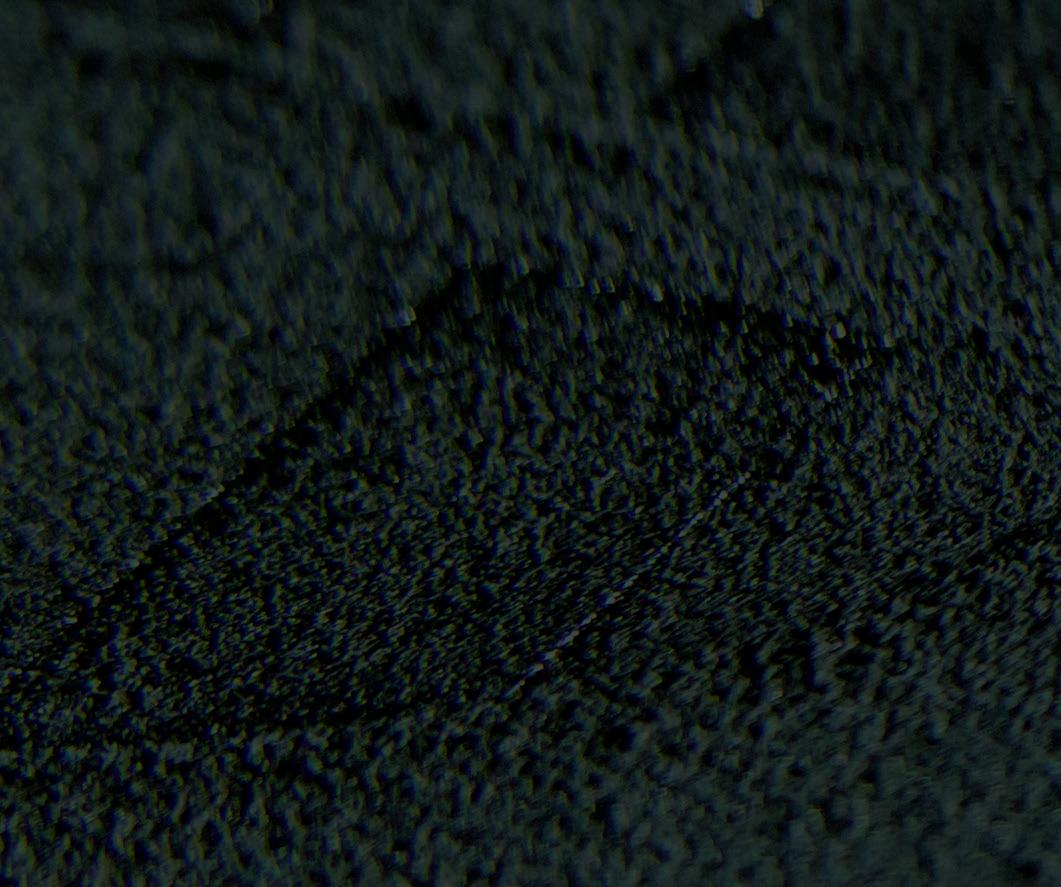
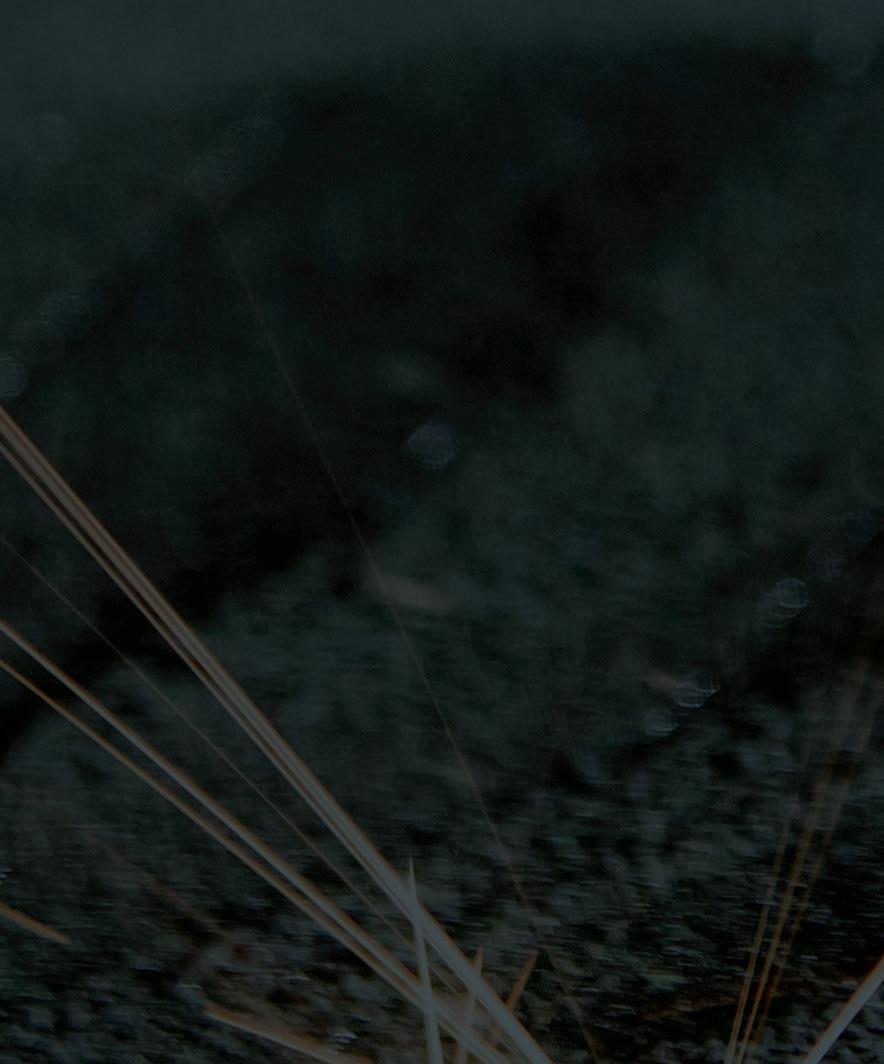
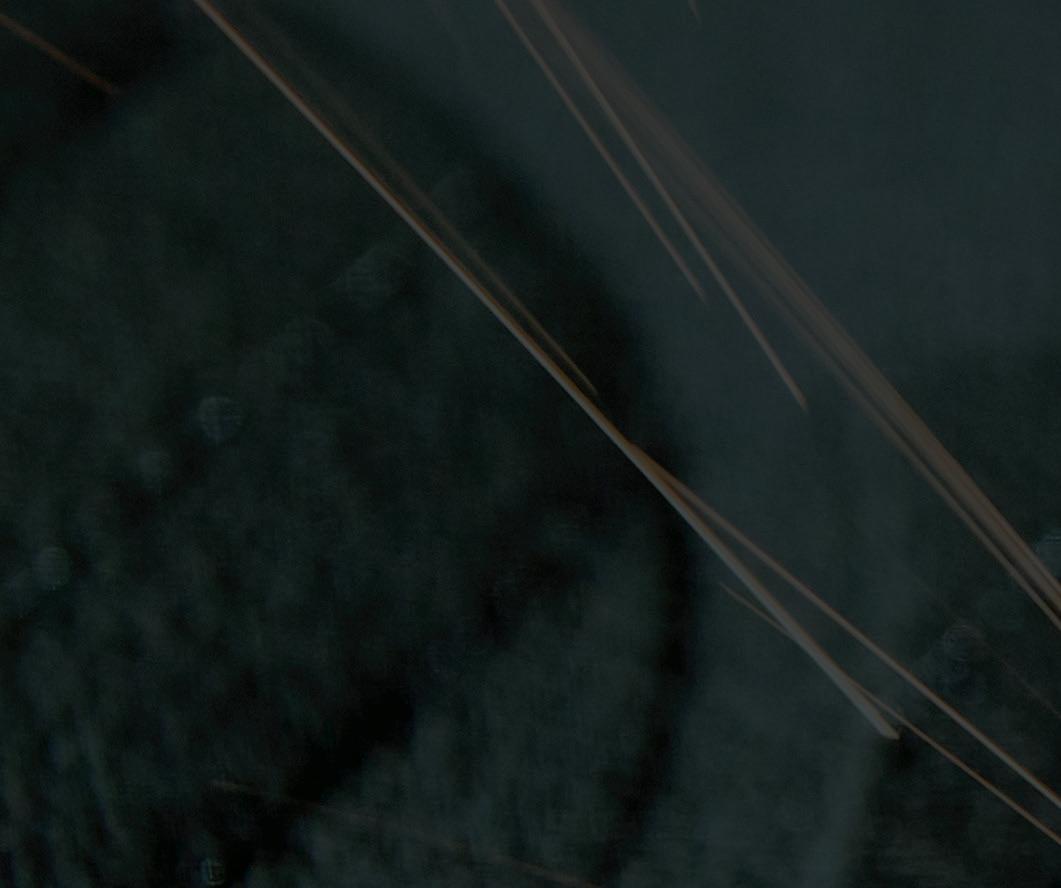
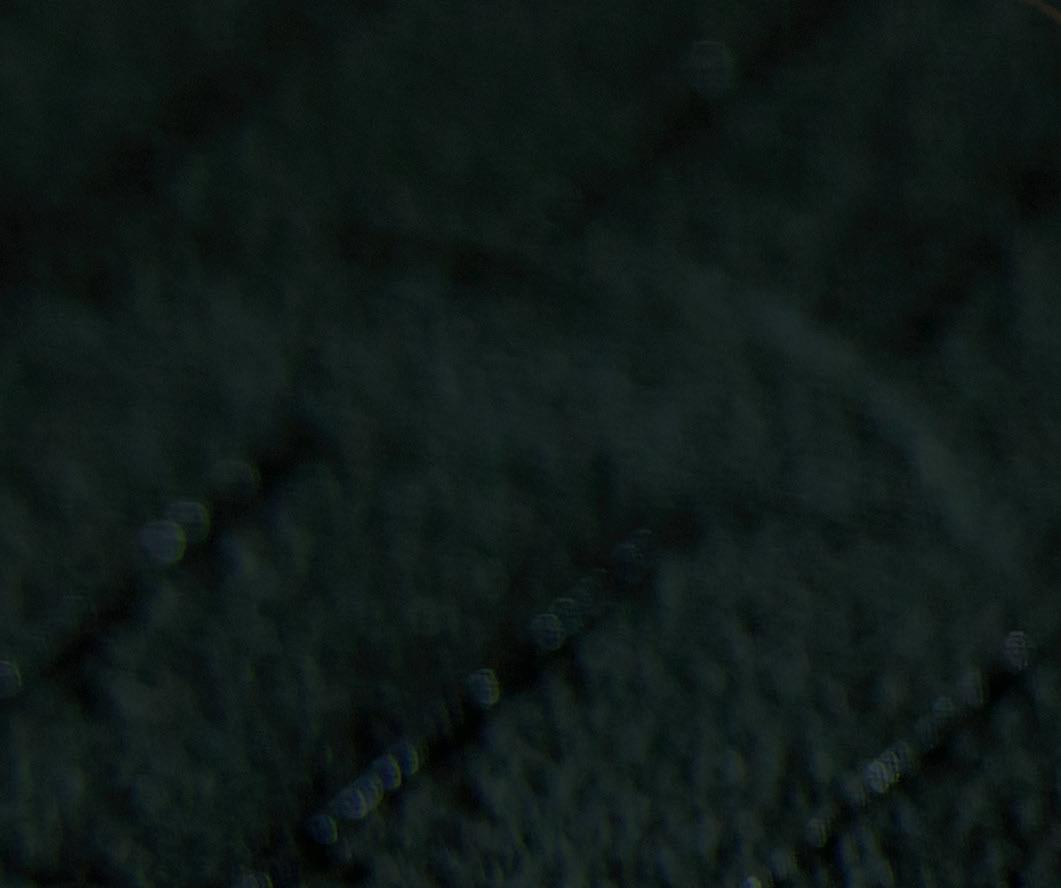
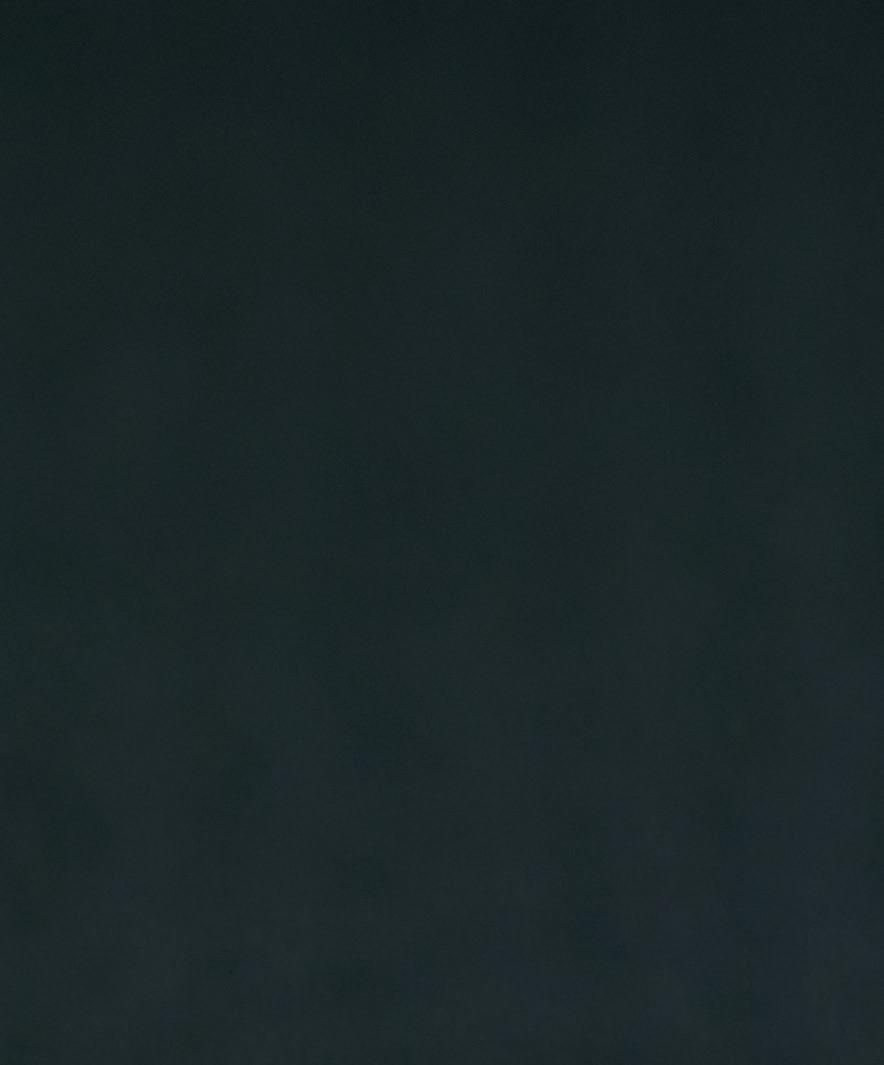
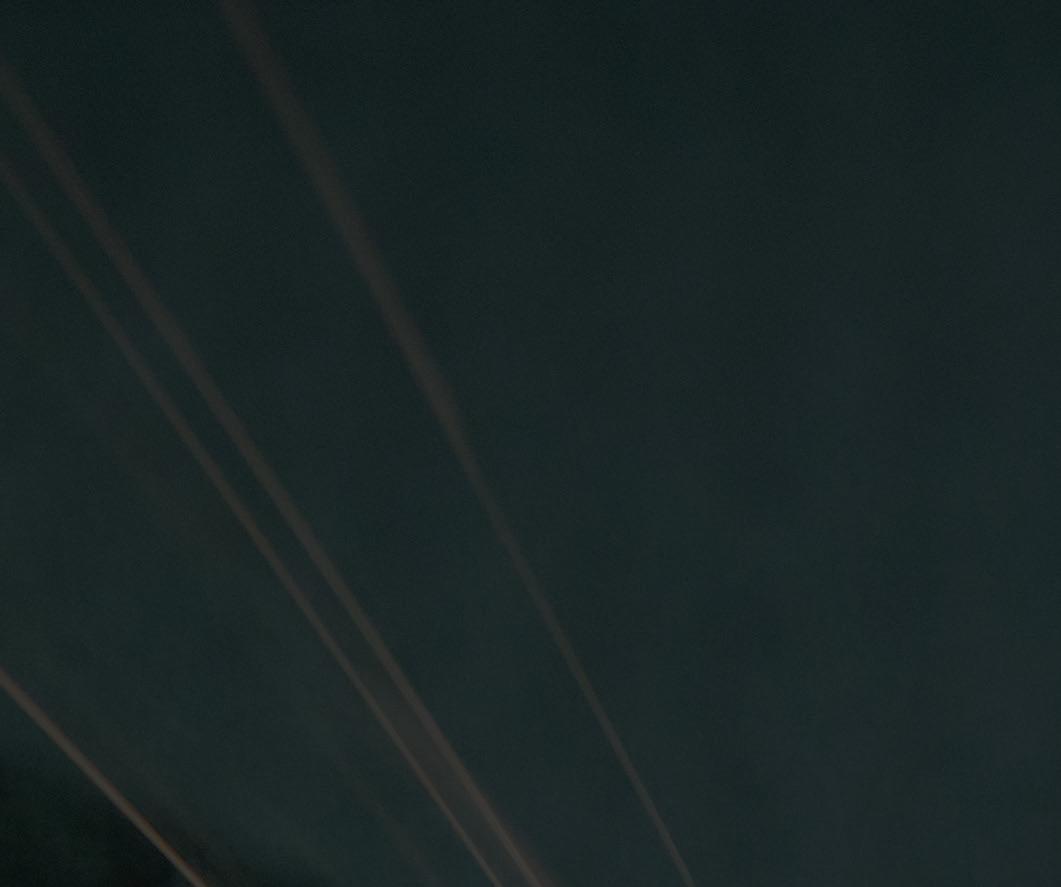
Offering comprehensive and reliable solutions, we support each customer through their entire development and production process.
Let’s build the future together.
+1 877 388 7916 of Ф200mm × 700mm was designed to replicate the main features of a landing gear system, with WAAM deposited features extruding away from a forged rod to connect braces and actuators. The deposition work was conducted in a global shielded inert environment with argon, 7 kg of material was deposited at a deposition rate of 1.3kg/hr and took 16 hours to finish, including setup. The BTF ratio was decreased from 5.9 to 2.0 for the demonstrator when compared with conventional subtractive manufacturing, reducing the material used by 65%. This demonstrated that WAAM can not only produce geometrically accurate features without any defects on radial forged substrates but also greatly increase coste ectiveness and reduce lead times.
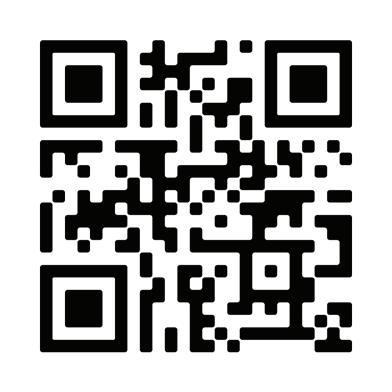
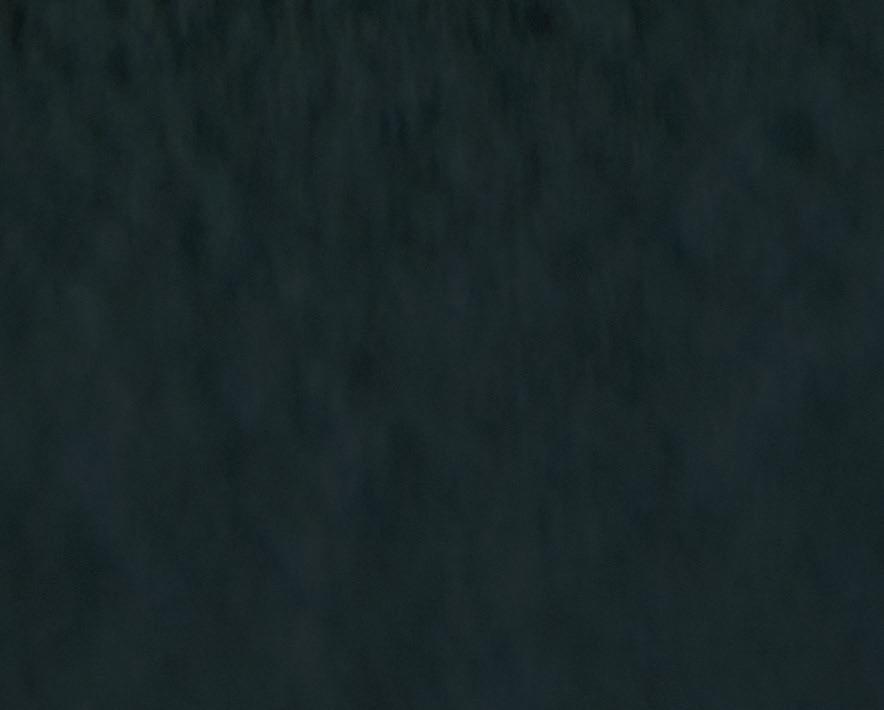
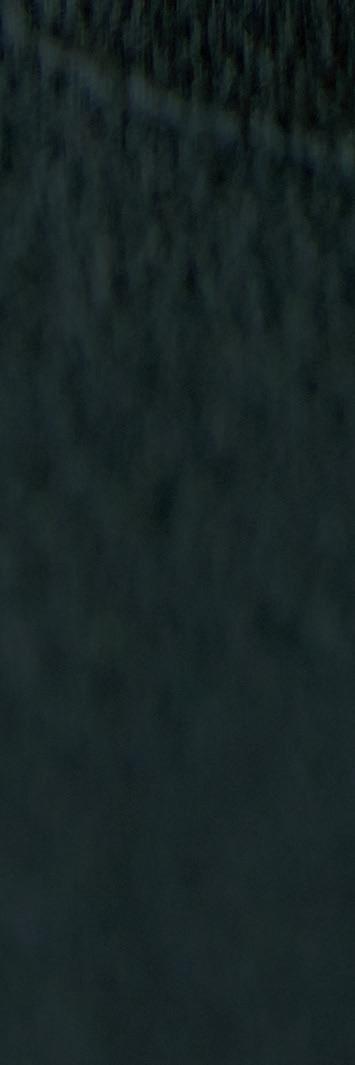
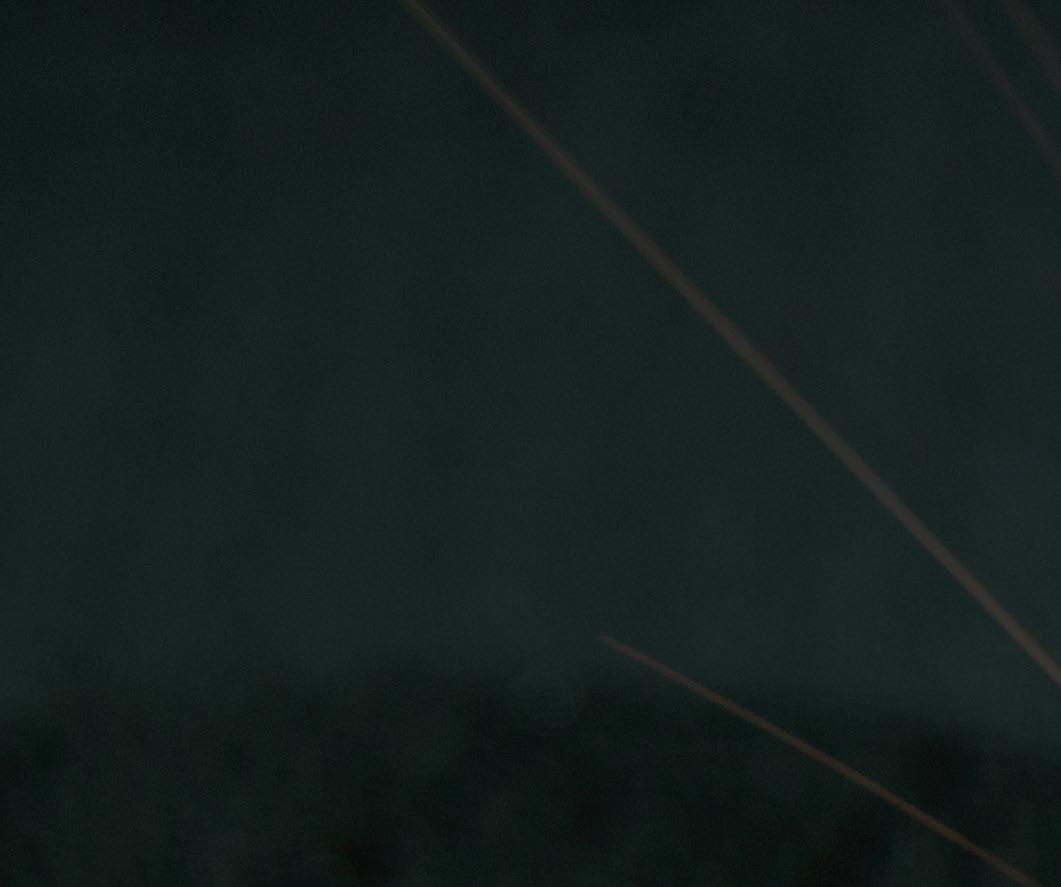
An environmental impact assessment study based on a “cradle-to-gate” life-cycle approach (including the cumulative e ect from raw materials extraction until the shipment of the component to the customer) has shown very promising results. Dr Emanuele Pagone, researcher in the Sustainable Manufacturing Systems Centre at Cranfield University, observed: “Our study shows that producing the landing gear component with WAAM rather than traditional, subtractive approaches reduces significantly the required amount of raw materials to be extracted and refined. This also has a knock-on e ect on all manufacturing processes with less material to be heat treated, machined, and transported. We have estimated that the carbon footprint of the component can be roughly halved when substituting traditional machining with WAAM. Embodied energy consumption estimates show similar results and suggest that, approximatively, other environmental impact indicators (including emissions to air, water and land) are roughly halved as well. Furthermore, WAAM creates the opportunity to repair a damaged part re-depositing only what is necessary, an option not available by traditional means. Our studies in this area have shown that repair with WAAM can reduce the environmental impact by orders of magnitude, even including the additional transportation required to repair.”
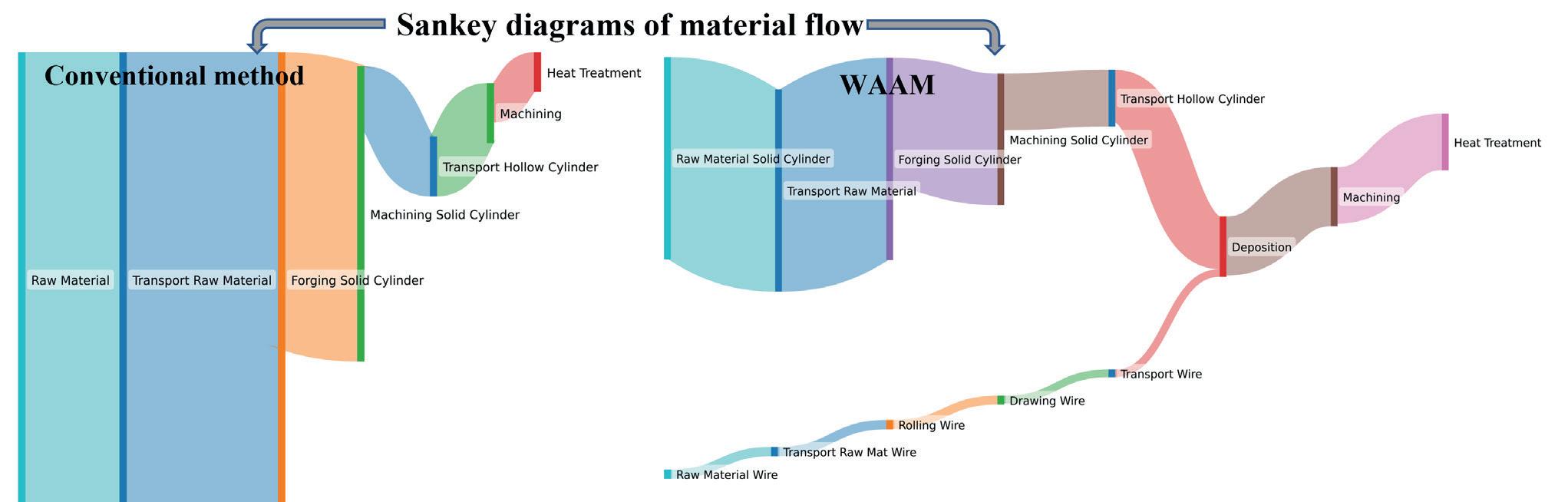
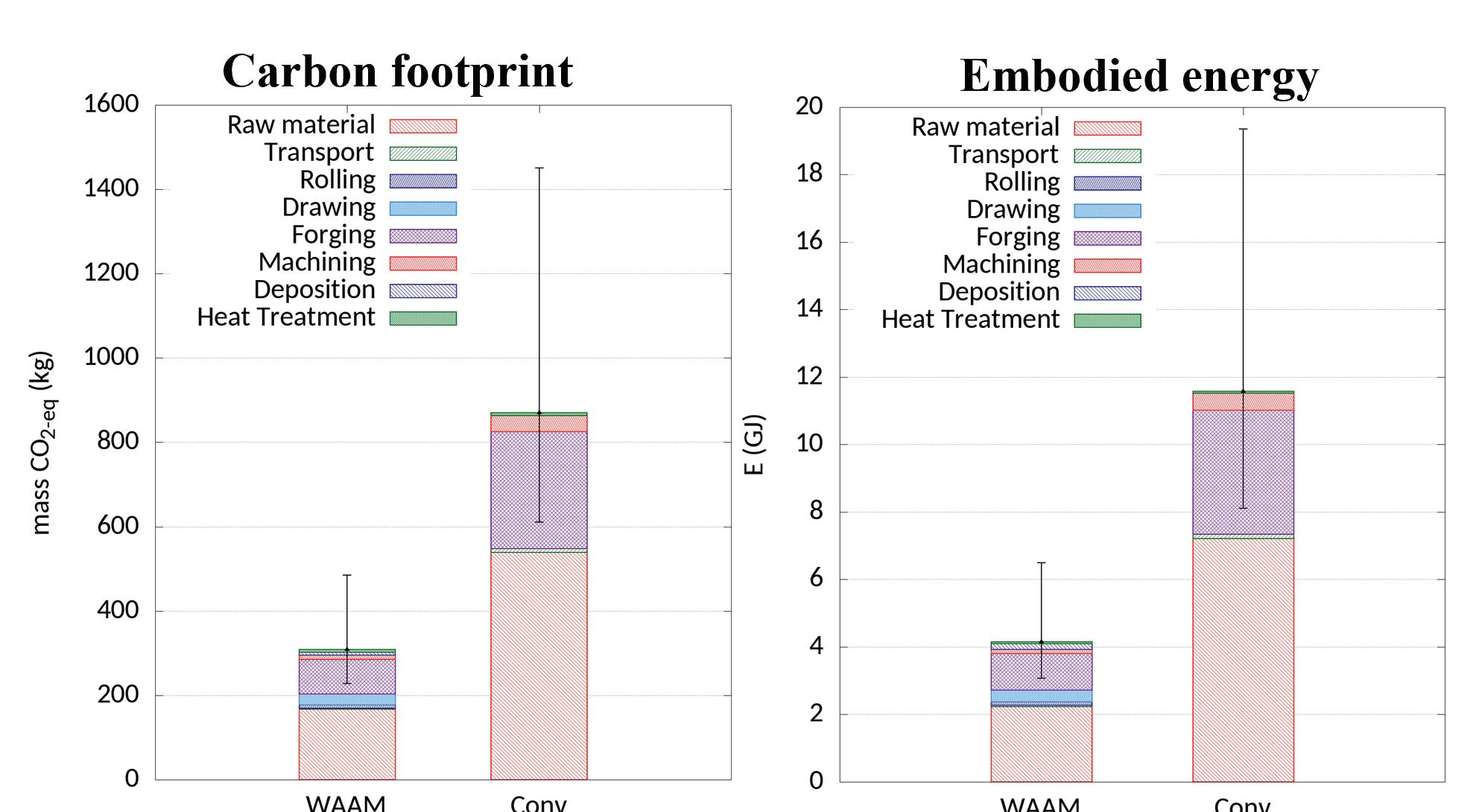
Therefore, WAAM appears as one critical technology to significantly reduce the environmental impact in manufacturing and to support the industry in the ambitious, yet absolutely important race to Net Zero.
Overall, this investigation will promote many opportunities and benefits for the whole aerospace industry as we incorporate additive manufacturing into a hybrid solution that can realize significant savings and achieve a pathway for critical component manufacturing to access more sustainable modern technologies.
For the next step, Prof. Stewart Williams, the Director of the Welding and Additive Manufacturing Centre, added: “We are currently applying our newly developed CW-GMA process to the manufacture of aircraft landing gears. This process can achieve high deposition rates of up to 15 kg/h whilst providing precise thermal control with a wide heat input range.”
Beyond that, a further exciting new development in WAAM technology is the RoboWAAM coherent hardware-software ecosystem developed by WAAM3D. It generates programmes seamlessly with any CAD model and oversees the whole deposition process, providing process monitoring and governance over the many health and safety capabilities, as well as a fully auditable process trail.