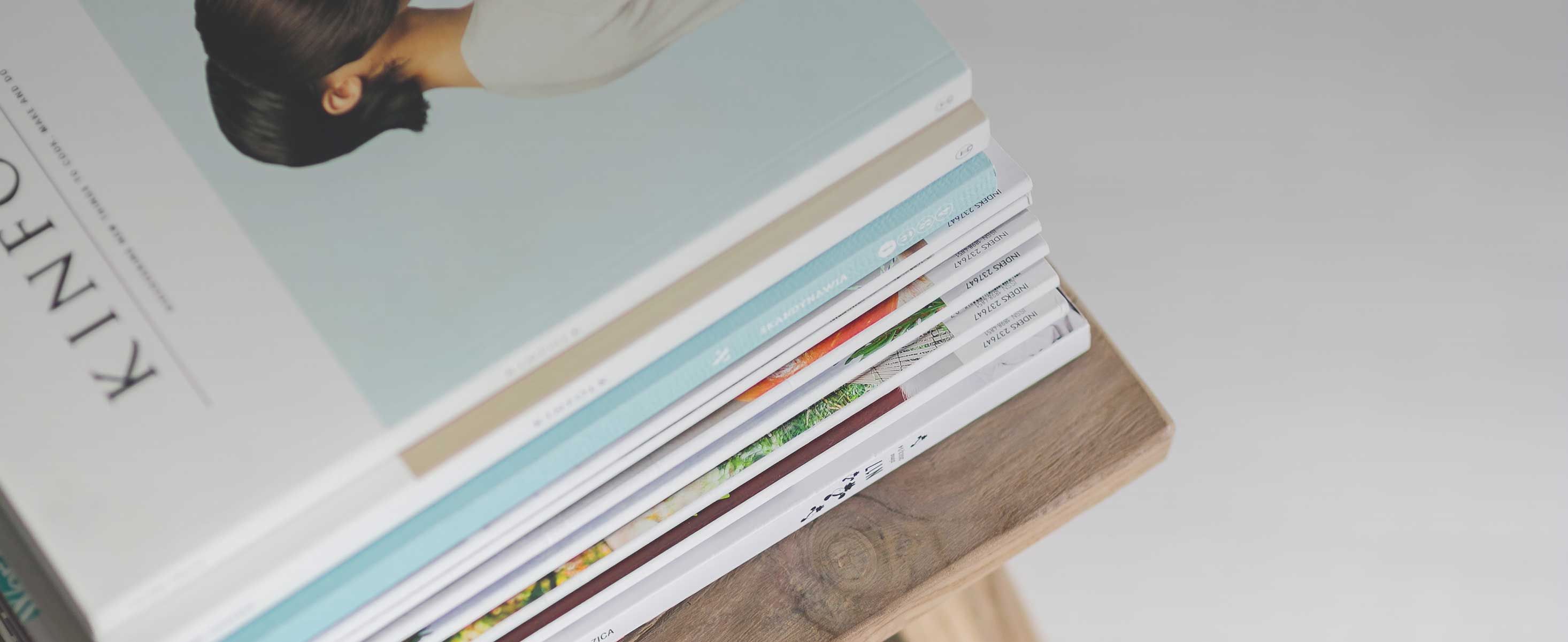
2 minute read
LEAPS AND BOUNDS
from TCT Europe 31.3
by TCT Magazine
On a recent Additive Insight podcast, we were welcomed to the headquarters of Evove, a UK-based company leveraging 3D printing technology to enable precise filtration membranes.
Evove is developing its own binder jet 3D printing platform, which it intends to scale up to develop enhanced membrane technologies at volume for the desalination, water, green hydrogen, and food & beverage markets.
Below, Evove CEO Chris Wyres [CW] and Senior AM Engineer Richard Finch [RF] explain why 3D printing and computational fluid dynamics are integral to its membrane products.
What would we need to know about your technology to understand what the aims of Evove are?
CW: We have two technology platforms. Our Enhance range of products improves the performance of existing membranes. That includes the graphene oxide coatings that the business was originally founded on. Spacers, which we 3D print, are inserted in between membrane layers to manage the fluid flow and inserts, which are spiral shaped 3D printed products, are inserted into tubular membranes to manage the fluid dynamics. All retrofittable to existing membranes and in terms of performance gains we see everything from a doubling in selectivity to a 5X increase in throughput to an 80% reduction in energy consumption for processing a given volume of fluids. Pretty transformational performance gains.
The second range of products we call Separonics, and that's wholly 3D printed membranes where we're precisely engineering the architectures for a specific purpose. Separonics was really where it all started. We recruited the team specifically to help drive that programme forward.
RF: Separonics is a reactive binder jet process. So, instead of a conventional method of printing a polymer binder, we're printing a reactive binder. We're printing ceramic onto ceramic. The binder then contains particles which fill the interstices within the powder bed. So, not only do we end up with a denser green part, we also reduce the thermal budget required for sintering, which also improves the commercial viability of the process. And it reduces the postprocessing time, which makes it very commercially applicable.
A couple of the application examples you have here are spiral inserts and spacers. Could you outline the impact 3D printing is having on those parts?
RF: With the spacers in particular, we’re able to change the features down to tens of microns, [from] which you will see a dramatic performance gain. And we're shifting it over to a high throughput process, which we've managed to do with additive manufacturing. So, not only have we been able to increase the performance, we’ve also been able to then change it to make it customer specific to their own applications and compared to a conventional spacer or mesh structure. We're leaps and bounds ahead.
CW: And if we look at one of our big applications for this in desalination, we’re able to reduce the energy consumption in the desalination process by up to
30%, and given that there’s an increasing requirement globally for desalination, this could have a really big impact.
Talk me through the significance of computational fluid dynamics and what that enables you to do.
RF: So if we go to conventional spaces, they are basically a filament that is extruded and there is no other feature for that than just to provide a flow channel between two membrane sheets. We've got a very talented CFD engineer who's looked into how we can model these existing spacers and he's identified areas where we can improve. So, we're printing hydrofoils onto the spacers that improve the flow [and] reduce the pressure drop across the membrane.
And we're talking about struts, these hydrofoils are about 200 microns tall, with a curve profile that can actually guide the flow through it. We’ve then spent several months correlating what we get with the CFD performance, the printing performance, and then our CFD model can then influence what we're printing.
CW: And that whole generative design process has really accelerated our time to final product. We're busy investing now and scaling that technology.