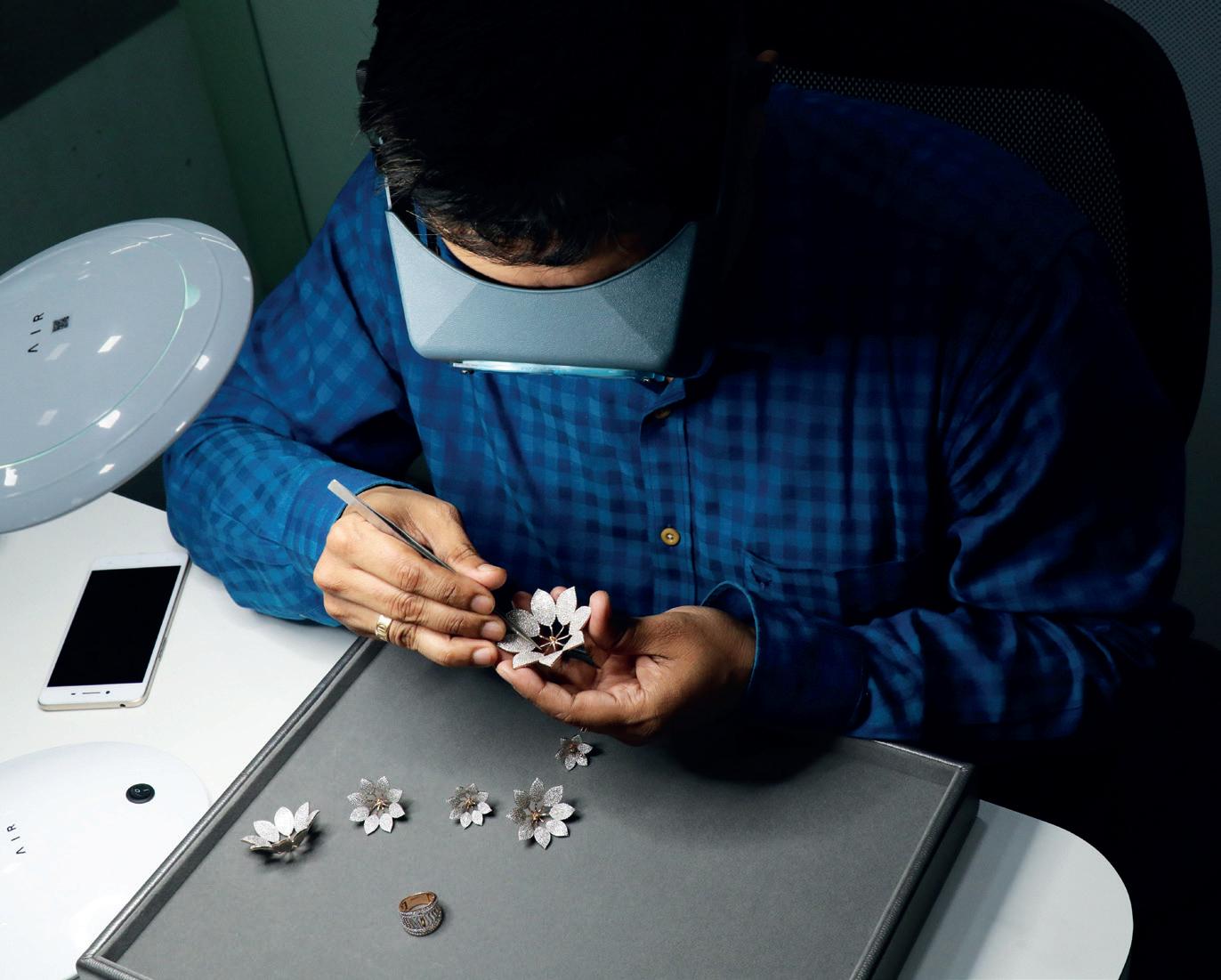
3 minute read
DIVINE DESIGN
from TCT Europe 29.1
by TCT Magazine
WORDS: SAM DAVIES
SHOWN:
SKILLED JEWELLER SETTING DIAMONDS ON THE DIVINE – 1801 BRAHMA VAJRA KAMALAM RING
In Mumbai, India, a world record certifying authority representative sits and counts up to 7,801. Imaginarium and the Diamond Store by Chandubhai have gone for the world record of most diamonds set in a ring and wait patiently to have it confirmed. Watching the representative manually count nearly 8,000 diamond pieces across two whole days with nothing but a jeweller’s loupe, the partners are thankful they had digital technologies to hand when embarking on the Divine – 1801 Brahma Vajra Kamalam project.
The piece, which broke the Guinness World Record in August 2020, only to be usurped in November, was inspired by the natural design of the Himalayan Camellia flower. It features seven parts – a gold shank and six rows of petals – all assembled around a stigma crew to allow thousands of diamonds to be set by one of Imaginarium’s skilled jewellers within prongs on each component with the highly precise micro pavé technique. But such were the intricacies of the design, the partners decided to leverage Imaginarium’s 3D printing capacity to iterate multiple versions of the ring before heading into production.
“The precision and tolerances are impossible in the conventional way of making jewellery,” Tanmay Shah, Head of Innovations at Imaginarium, tells TCT. “The convention that I refer to is where all of this would have been the work of a craftsmen who starts with
a block of [material], and they have only two-dimensional sketches to refer to, so even the curvature [of the petals] in three dimensions, the way it fills that volume, was something that had to be in their head. Only a select few skilled artisans could have pulled this off.”
Imaginarium was well-placed to take on this project. At its headquarters in Mumbai, it has dozens of employees working on jewellery manufacturing and finishing every day while it was able to leverage Digital Light Processing technology from Rapid Shape, who has products designed specifically for jewellery projects. Using the vendor’s S30+, Imaginarium utilised its 405 nm UV LED light source, HD 1920 x 1080 px resolution and resin temperature control capabilities to produce iterations in a quick-print, high-resolution general-purpose material that helped Imaginarium visualise the design and spot defects. The company then harnessed Rapid Shape’s direct casting material to allow the ring to be cast in gold.
“When it comes to this level of precision,” Shah explains, “we needed a laser-based printer because of the tolerances. Rapid Shape comes closest to an SLA. The interesting evolution of technology is that projector-based system, because of its high resolution and high definition, is now giving parts at a par with a high-end laser-based SLA machine. But the added advantage for the DLP is speed. Whereas an SLA machine would have taken six hours to make this prototype, a DLP would take one hour to do the same.”
Jewellery is one of Imaginarium’s four main business activities, with 3D printing regularly being leant on to help the company tackle complex designs, reduce the time to manufacture and print one-off or customised goods. All were at play in this record-breaking project. Shah estimates that this design, approached in a conventional way, would have taken months because of the complex shape and need to assemble multiple pieces. And that is just the first iteration, without considering the size of the prongs that differ for every diamond they hold.
“That’s the standard,” he says. “So, enter 3D printing. What that does is one, all of your simulation, validation etc is done in the CAD software; we could modify the design as many times as we wanted, and even after making the first prototype, if we find something not working, it’s a matter of one hour or two hours to tweak the CAD design and start again. Two, of course, it’s impossible to achieve otherwise. And the third is when you can play with multiple materials, you’re not trying to replicate a prototype into some other conventional form, it’s part of the same workflow. It’s just one workflow.”