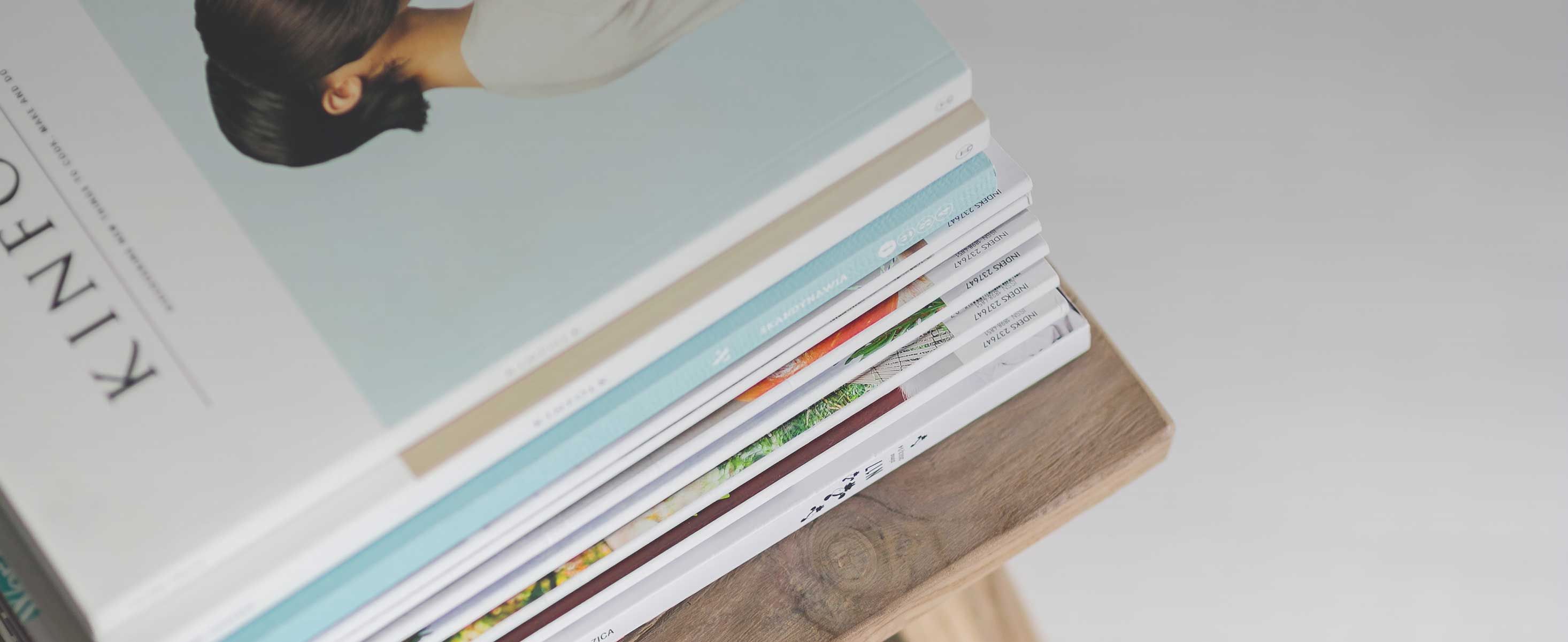
10 minute read
THE ROLE OF 3D PRINTING
from TCT Europe 29.1
by TCT Magazine
THE ROLE OF 3D PRINTING IN FUTURE SUPPLY CHAINS
Sam & Laura speak to several industry personnel to understand the potential role of 3D printing technology in more agile manufacturing supply chains.
In California, a collaborative effort involving Forecast 3D takes just three months to go from design development of a nasopharyngeal swab to additively manufacturing a million FDA-approved units.
In South Carolina, Johnson & Johnson’s (J&J) Ethicon brand works with PRISMA Health to additively manufacture an FDAauthorised ventilator expansion splitter that enables a single ventilator to be used for two rescuable COVID-19 patients until individual ventilators come available.
In Texas, Essentium designs a 3D printable face mask that is additively manufactured tens of thousands of times over ten weeks before its injection moulding tooling is ready, and a more traditional method can shoulder the burden. And then it keeps printing supplementary masks alongside.
There were many more examples all over the world of 3D printing filling gaps of stretched supply chains as the COVID-19 pandemic caused disruptions from the Far East to the West Coast. It quickly sparked conversations about the need for more agile and resilient supply chains, and in this industry, how important 3D printing is to the transformation of these supply networks.
For Steve Richardson, Forecast 3D’s Business Development Manager who focused on supply chain development on an international scale while in the electronics industry, there’s much that needs to go into a supply chain to make it agile – “you have to have visibility throughout the value stream, knowing that you have one focal point, normally the OEM, orchestrating all the different pieces, and we have to have data-driven decisions.” – but having seen up close the capabilities of 3D printing, he is in no doubt that it has its place: “What I really took away from the pandemic was how dynamic the supply chain can be with additive manufacturing.”
Speaking to TCT in the autumn of 2020, having surveyed 2,000 manufacturing business leaders about trends in digital manufacturing, HP’s World Wide General
Manager of 3D Printing, Ramon Pastor, noted how the ‘resiliency of a supply chain is the resiliency of the worst part of said supply chain.’ Around 12 months ago, as offshore factories closed down as a result of the spread of COVID-19, manufacturing organisations around the world learnt that the hard way.
COMPLEX CONSIDERATIONS
In the 2019 Global Services Location Index, which lists the most attractive locations to produce goods, India, China, Malaysia, Indonesia and Vietnam topped the rankings, with Thailand joining the United States and United Kingdom in the top eight. Notably, though the US and UK excelled in ‘people skills and availability’, ‘business environment’ and ‘digital resonance’, they lacked in ‘financial attractiveness’.
Because so much emphasis has been placed on lowering costs within many manufacturing organisations, the effectiveness and resiliency in many cases had been neglected. As Richardson pointed out, “If a company has a mindset of, ‘we’re going to be low cost’, every decision that supply chain makes is based on having the lowest cost product in the market.” Companies and entire industries were rocked upon the spread of COVID-19. In a Deloitte survey carried out last year, 59% of respondents said they saw a slowdown in sales and challenges to their cash flow, with 22% noting their inability to directly serve customers was the main negative impact on their business during the pandemic.
“COVID caused every company in the world to look at their supply chain and say, ‘I can’t tolerate this, I have to have more flexibility,’” said 3D Systems CEO Jeff Graves in a recent interview with TCT.
“Nobody could have anticipated COVID,” LEO Lane Co-founder and VP, Business Dr Lee-Bath Nelson offered, “but after COVID nobody can say that failures are not anticipated. You have to take measures for that.”
The strategy of manufacturing parts offshore is carried out with cost at the forefront of the mind, rather than control, visibility, or even ethics. Using the cheaper locations of the world to manufacture goods at high volumes is a cost-effective way for many manufactures to run their business and, with no incentive to do otherwise, rearranging a supply chain to ‘reshore’ manufacturing is likely much too complex and much too time-consuming to do.
Yet, many consider there to be hidden costs involved with this model that only rear their ugly heads in times of crisis. Richardson gives the generic example of a part that is integral to one’s manufacturing line, or integral to the function of their customer’s assembled product, something that, “if you don’t get that part, it’s going to cost you more than anything. Is it worth having it manufactured thousands of miles away where you have no visibility of it just because it costs you ten cents?”
The same idea crossed Xometry CEO Randy Altschuler’s mind in April 2020. Talking to TCT, he stressed: “We need to start quantifying the cost of supply chain disruptions and of risk. It may look like something from a location overseas might be 50% less expensive than domestic, but if you factor in some percentage chance that there could be a supply chain Black Swan event like we’ve had now where there’s no supply available, that’s worth something and that needs to be put into the equation.”
Those considerations are certainly more likely to be made off the back of the pandemic and the disruptions that came with it. But as Dr Jennifer Johns writes on page 14, the reshoring of manufacturing is a political discussion. Indeed, Altschuler conceded that the concept needs the backing from governments, with subsidies being offered, as they have been in countries like Japan, to ‘bring manufacturing home.’ Without them, manufacturers are likely to put cost efficiency first. This point was highlighted by 3D Hubs CEO Bram de Zwart who, in writing for Business Insider last year, said: “From our experience, the balance between cost and the quality of manufacturers is often much more favourable when sourcing overseas, which is a very harsh reality but something we can’t ignore, especially during a period when most businesses are particularly stretched on resources.” He went on to suggest that a combination of both onshore and offshore production is an effective way of enabling supply chain flexibility, citing the fact that when Asian factories opened up again last year, many of those in Europe and North America were shutting down.
There is much to ponder for manufacturers making these decisions, particularly at a time when supply chain disruptions and cash flow problems are impacting the business in an intertwined way. Again on page 14, Dr Johns notes that she generally doesn’t expect manufacturers to shift production from one location to another in a ‘like for like’ way because of the complexities involved,
but instead there may be changes to the ‘status quo’ and that could be good news for additive. Especially given some of the potential wins that are available.
The fundamental thing that a supply chain must do, Pastor emphasised last year, is match demand with supply. And the best way of doing that, he reckons, is on-demand manufacturing with limited physical inventory. Scott Sevcik, Stratasys’ VP of Aerospace, agreed in July 2020, pushing forward the idea of ‘one on the shelf’, allowing there for less wait time upon ordering the part, and less scrap should the Customer Solutions at J&J. “We operate in a dynamic marketplace where consumer preferences are constantly shifting and demands are only increasing, meaning we must be able to quickly pivot to meet the needs of customers in specific markets. [This] can only be provided through a sustainable, flexible supply chain aligned end-to-end with our commercial R&D teams.”
Richardson too, in referencing Forecast 3D’s additive manufacture of testing swabs, eulogised about the demonstration of “collaborative planning, collaborative design, focusing on your strengths, trusting
demand for it never come. Both suggest 3D printing has an obvious play here, while Pastor said HP is working with customers who are already starting to implement the strategy.
In responding to a statistic that came out of HP’s aforementioned survey – that 75% of respondents suggested 3D printing may be useful as a back-up technology to traditional means of manufacture – Essentium CEO Blake Teipel analogised 3D printing with a fleet of water pumps that operate in New Orleans, a city just below sea level that gets hit every year by hurricanes. In normal times, those pumps might be at 20-30% capacity to keep the ocean back, while the rest sit idle. Yet, when a hurricane arrives, they all spring into action to quickly reduce the flooding.
“AM is just like those pumps,” Teipel said. “You’re able to produce parts and then you’re also able to have that surge capacity when you need it.”
Essentium also thinks there’s scope to, as they did with the face masks earlier in the pandemic, use 3D printing to supplement traditional manufacturing. Similarly, from J&J’s experiences, the company is backing the sheer ability it displayed to turn on a dime last year and produce something it wasn’t expecting to a few days earlier.
“As a global company operating in markets all over the world, there is no such thing as a ‘one size fits all approach’,” said Sam Onukuri, Head of 3D Printing &
your partners and then trying to get that real time data from the market of where shortfall was.”
There’s an array of opportunities for 3D printing, some being proved out during the pandemic, while others are currently more speculative. But those that are proffered generally revolve around the technology’s capacity to produce end-use parts, particularly as its capabilities continue to grow. Often overlooked when discussing 3D printing’s potential within flexible supply chains is its rapid prototyping proficiencies. This is where, Richardson suggested, the technology will have its biggest and quickest impact. Graves agreed, asserting we could be about to see “an explosion in the designing of components made by additive manufacturing.”
Yet, Richardson maintained that ‘every production opportunity starts with a prototyping opportunity.’ Indeed, he and Forecast 3D saw as much just under 12 months ago. The naval swabs project started out as a way of validating design; it became a bona fide AM production application scaling into the millions. Key, as ever, to opening up such opportunities with AM remains finding the right business cases, whether it be down to volumes required or complexity. Not every agile and resilient manufacturing supply chain will rely on 3D printed parts, but in a period when all will be carrying out in-depth assessments of their supply networks, there’s a belief across the board that additive has a big role to play.
“Supply chains take a long time to reengineer,” Teipel evaluated. “It’s going to take another 1, 2, 3, 4 years to see the evolution of supply chains to the point where there’s a new type of optimisation because the supply chains have been optimised for the manufacturing technologies of the 80s, 90s and early 2000s. But now, because of additive manufacturing and the buzzy bits of smart factories and the rest, you’re starting to see a new type of efficiency emerge.”
“We anticipate that 3D printing is a mainstay of supply chains,” Onukuri added. “We always want to ensure that we can meet the needs of customers in different markets while also pivoting quickly. By re-imagining the way that we create and deliver products and services, we truly move one step closer to innovation that can change health for humanity.”
“Additive manufacturing with trust and collaboration can take you to the next level,” Richardson finished. “Case in point is the nasal swabs. We did it in a short period of time, accelerated under the gun and were very reactive. Now, think if you were proactive, and had a big supply chain goal or vision in your head, and then you take the time to implement an agile supply chain with time, I mean, the sky’s the limit.”