
4 minute read
ENABLING CMF WITH 3MF
from TCT Europe 29.1
by TCT Magazine
ENABLING CMF WITH 3MF WORDS: SAM DAVIES
It can be deflating, stressful and exhausting. To exert so much effort, brain power and creativity over a sustained period of time, only to realise there’s still much room for improvement. Or you can take it in your stride, collaborate with the right partner and open the door to new opportunities.
For decades now, design engineers have leant on 3D printing’s ability to rapidly print parts to assess the form and fit, maybe the function too, of an application that will soon go into production. But they’ll probably do so in a different material, colour and surface finish.
Companies don’t want to spend too much money on expensive materials, only for the design to be iterated a dozen times, especially when tools to simulate performance and behaviour are now so readily available. It means colour, materials and finish (CMF) simulation, in which designers get a true insight into how their part looks, feels, and performs, is often carried out only towards the end of the product development phase.
“The problem is they don’t trust the digital design and some of them are using animation tools, rendering tools, CAD tools and so on, so the workflow isn’t smooth,” Michal Diga, Director of PolyJet Software Solutions at Stratasys, begins. “We wanted to enable our customers to have a smooth workflow, to capture the design intent and hold the physical model in their hands.”
Diga is explaining the motives behind Stratasys’ partnership with software company Luxion, which has resulted in the former’s multi-material, multi-colour J Series of PolyJet 3D printers and GrabCAD Print software being made compatible with the latter’s KeyShot 10 rendering platform. It is recognition from Stratasys, one of the oldest companies in the 3D printing space, that even after 30 years, there is still room for the technology’s prototyping capabilities to grow. In particular, the company sees CMF simulation as a key part of the design phase that is currently too costly, time-consuming and complex.
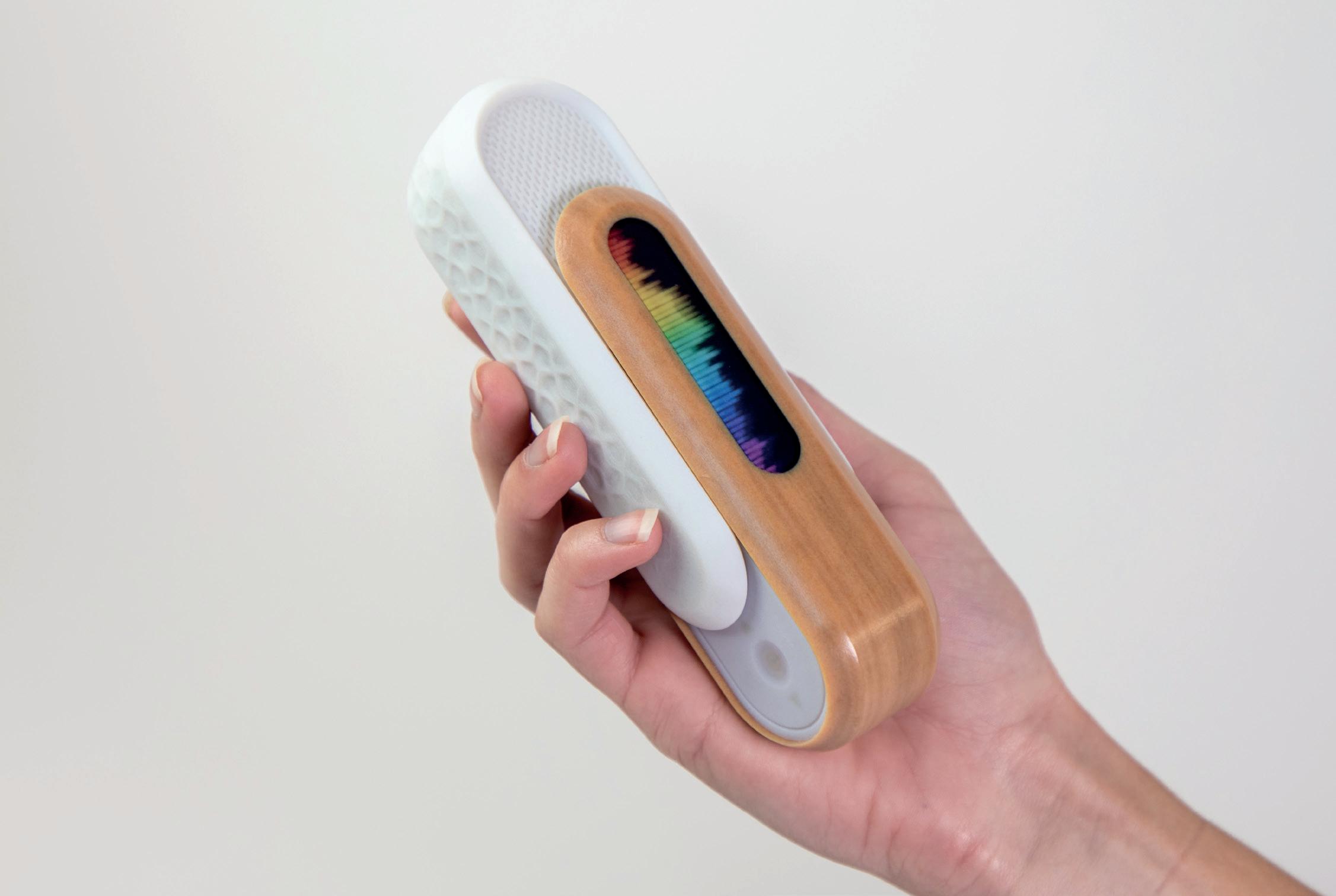
“The screen is good enough for some things,” offers Lior Elgali, Product Manager, Design at Stratasys, “but you don’t touch it, and this means you don’t really know how it’s going to behave in the real world. Even if you think you do, you don’t. It’s like seeing a scenery on National Geographic and being there, it’s a completely different experience.”
Independently, the KeyShot 10 software boasts extensive material, texture and colour libraries. Users can access metal, plastic and wood materials; Pantone and RAL colours; and bump, colour, displacement and roughness textures, rendering models to encompass all this detail on screen. With the J Series and its own proficiencies in colour, materials and surface finishes, as well as its compatibility with the 3MF file format, they can also fabricate the design in 3D form.
“3MF was actually the enabler,” Diga explains, “because the special thing about it is that it doesn’t just hold the geometry, but also the colour, the materials and finish. You have much more information in one package.”
Being able to transfer the capabilities of KeyShot 10 through to the J Series and hold so much data, Diga and Elgali believe, is set to have a massive impact on the speed and quality of product design for J Series users. In the past, they’ve seen designers use CAD platforms with limited CMF tools, using textures and colours as placeholders – even labelling parts ‘green’ rather than designing in the shade they desire – because of the lack of available options. It means that often, the fully formed and fully detailed design isn’t prototyped until the very end. But the combination of KeyShot 10 and the J Series, Diga believes, can change that.
“It accelerates the design process so they can start early with CMF,” she says. “They get [the prototype overnight], the quality is better because they don’t have to imagine too much, you can hold it and touch it, and you can give it to the decision makers so that early in the process you have the right direction.”
Having enriched the capacity of 3D printing as a prototyping tool with their partnership, Luxion and Stratasys promise there is more to come. They want to add an option to print directly from KeyShot 10 to their nearby service provider, control and specify shore value within the 3MF file, carry out research into how to translate transparencies from the computer to the real world, and support bump maps to enhance surface finishes.
“It has been a pleasure working with Luxion in the past year, and we’re so happy we have the opportunity to continue working together in 2021,” Diga finishes.
SHOWN:
BLUETOOTH SPEAKER MODEL FEATURING ADVANCED SIMULATED TEXTURES SUCH AS WOOD. PRODUCED BY PRIORITY DESIGNS ON THE STRATASYS J55 3D PRINTER USING KEYSHOT 10