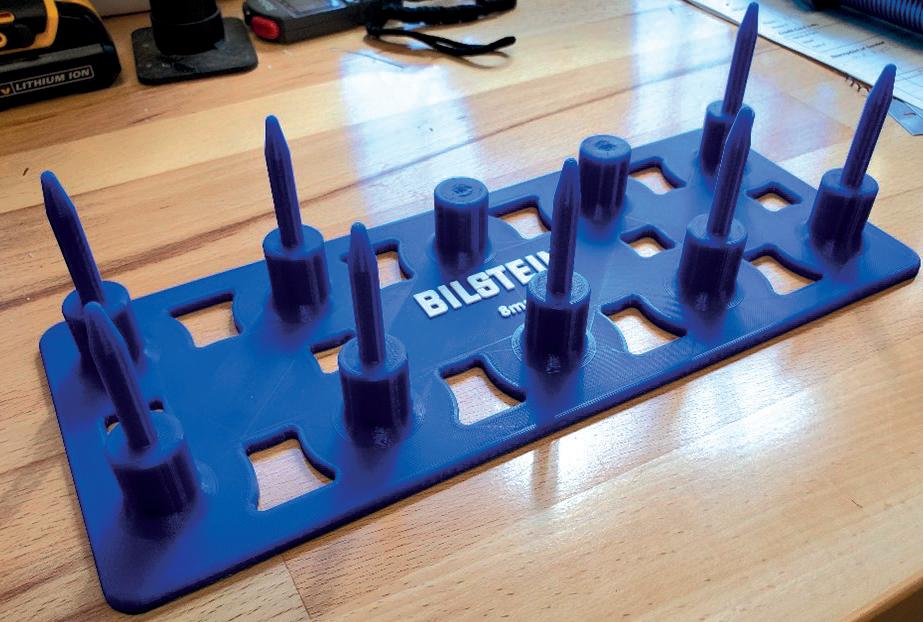
3 minute read
PRINTING SMART
from TCT Europe 30.1
by TCT Magazine
PRINTING
WORDS: SAM DAVIES
SHOWN:
PISTON TRAY
In North Carolina, the US’s NASCAR racing capital, a manufacturer of race car components was stuck in a cycle of print a part, have it break, print a part, have it break, become extremely stressed, and then just print it solid.
This less-than-ideal workflow is what Teton Simulation was founded to resolve when it came to market with its SmartSlice software platform in 2020.
SmartSlice, which is available as a plug-in to slicer platforms like Ultimaker Cura, has been designed to optimise the slicing phase as companies like RE Suspension additively manufacture parts like piston trays. Piston trays, which hold the internal shim stacks and pistons for serviceable shocks, are used by race teams when disassembling, rebuilding and tuning shocks for high-performance vehicles. Before adopting SmartSlice, RE Suspension was hearing from customers that the printed piston trays were breaking. The easiest option was to reprint it solid and ship it back out.
“Then we brought in our software and said, ‘look, we’re showing you on the part where it’s going to break,' which is exactly where it was breaking,” Teton CEO Doug Kenik retells the story. “Instead of changing it to solid everywhere, we just changed the print settings in a very local region where it was breaking and we saved them days of print time, which allows them to get more throughput on those 3D printers.”
RE Suspension is said to use Ultimaker S3 and S5 machines. In its supply of printed parts for its racing team clients, RE Suspension has been looking to free up its 3D printing capacity as much as possible, while also reducing its usage and waste of material. Hence, moving away from the print, break, print, break routine was paramount.
That, however, takes time. In any slicer platform there are a whole host of parameters of a printed part that can be altered, and without the requisite simulation tools, the results of which can only be determined once the part has been printed. With SmartSlice, however, RE Suspension is now able to have the numbers churned automatically in the cloud, with the platform returning a thumbs up or thumbs down response in quick time. stronger materials’ offered by Ultimaker. SmartSlice is able to access the material profiles of the machine vendor’s extensive portfolio and factor their respective properties into its slice simulations. It means users no longer need to buy materials to try them out, just like they don’t need to print their parts to make assessments of them.
“The number of slicing parameters in Cura alone is like 200 plus,” Kenik says. “Which ones do I tweak? Where do I go? You need tools to help you explore that space rapidly. You don’t want to do it manually, even virtually manually, you want to do it in an automated fashion. The software can say, ‘go in this direction, don’t go in that direction.’”
This was of particular help when RE Suspension was moving through iterations of a rear suspension bracket prototype, which would be later manufactured via milling. Rather than printing each prototype to test its load bearing capabilities during fitment testing – the part needed to be able to support the weight of an entire rear axile while being cycled through suspension travel – SmartSlice used modifier meshes to locally reinforce the part where extra walls and infill density were needed. Achieving a thumbs up, RE Suspension could save weeks in time and more than 400 USD in cost when compared to outsourcing the machining for a metal counterpart.
Moving forward, RE Suspension is intending to explore more end-use product applications with the aid of SmartSlice. When they get there, that will be job done for Kenik.
“You need confidence as a user that what you’re printing is what you want at the end of it and if the printer manufacturers and the material suppliers can help supply that confidence, that creates an ecosystem where people are so successful that they want to print more,” Kenik finishes. “That’s where we are as an industry in Teton’s viewpoint. There’s a whole bunch of material innovation, there’s a whole bunch of machine innovation, but there’s a confidence issue right now where one, I don’t know where to put this, what areas it can go in, and two, I don’t know if I print it, it’s going to work. We need to continue providing these ecosystems which are providing users trust and confidence in their parts.”