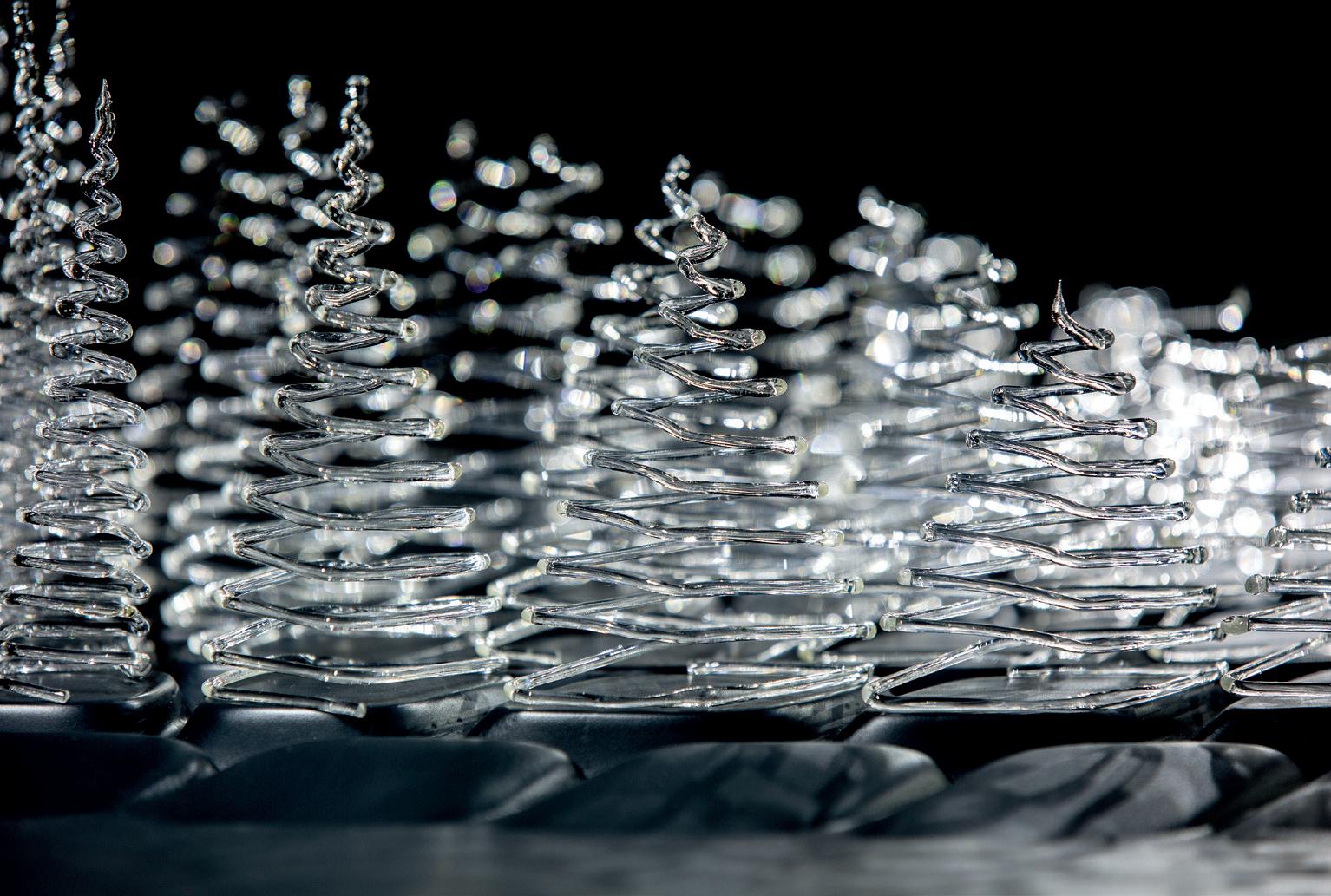
6 minute read
UNIQUE AESTHETICS
from TCT Europe 30.1
by TCT Magazine
WORDS: SAM DAVIES
UNIQUE AESTHETICS
SHOWN:
CRYSTAL GLACIERS
SHOWN:
3D STELAE SCULPTURE
To me, the most important thing is that I achieve something which looks unique, so it has a unique aesthetic embedded in it, something innovative and novel, which sets itself apart from anything that we have seen before.”
The standards were set more than six years ago. Julia Koerner founded JK Design in 2015 in Austria, with a new brand, JK 3D, being established last year with her partner Kais Al-Rawi. In that time, Koerner has found success in architecture, fashion design and product design, leaning on her specialities that span 3D printing, robotic technologies and computational design.
Her name has appeared in this very magazine before, after she produced 3D printed garments and accessories for Marvel’s 2018 Black Panther movie, while a fashion collaboration with Stratasys and Ganit Goldstein also filled the column inches of many a 3D printing publication in 2021.
Last spring, Koerner was reaching another professional landmark. Commissioned to develop two art sculptures measuring up to six feet tall, that would be put on public display in Santa Monica, California later that year, she was embarking on her very first public art endeavour. it), things didn’t go exactly according to plan on her '3D Stelae' project.
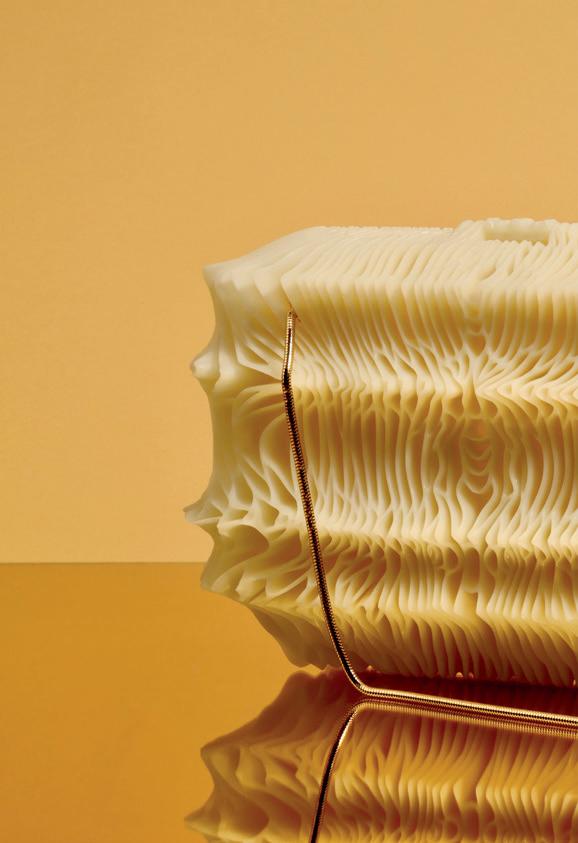
The plan at one time was to hand the production of the 3D Stelae sculptures to a service provider that operated large-format 3D printing systems. With the costs deemed prohibitive, Koerner then explored CNC milling, which was a little more affordable. But by the time she was ready to place her orders with a digital fabrication shop suited to her needs, they were all either closing down because of COVID-19 restrictions or swamped by the demand for faceshields and other Covid-related applications.
At this point, the deadline was just months away, with the first 3D Stelae installation slated for July 2020. The only way forward was to turn to JK Design’s in-house Fused Deposition Modelling (FDM) platforms, 3D printing the two sculptures in four-to-six sections measuring around one metre tall and 30 x 30 cm in diameter.
“We started printing it and it worked without adapting the geometry largely,” Koerner tells TCT. “It was so fascinating because all of a sudden we were able to print these large sections at 1.5 millimetres thick without any support material, so it’s super lightweight and the material can withstand outside environmental forces, such as sun and heat.
“We started to produce this in our studio, and it was revolutionary because I realised what we can do in-house and how we can make our own products with very limited resources.”
SHOWN:
HY CLUTCH
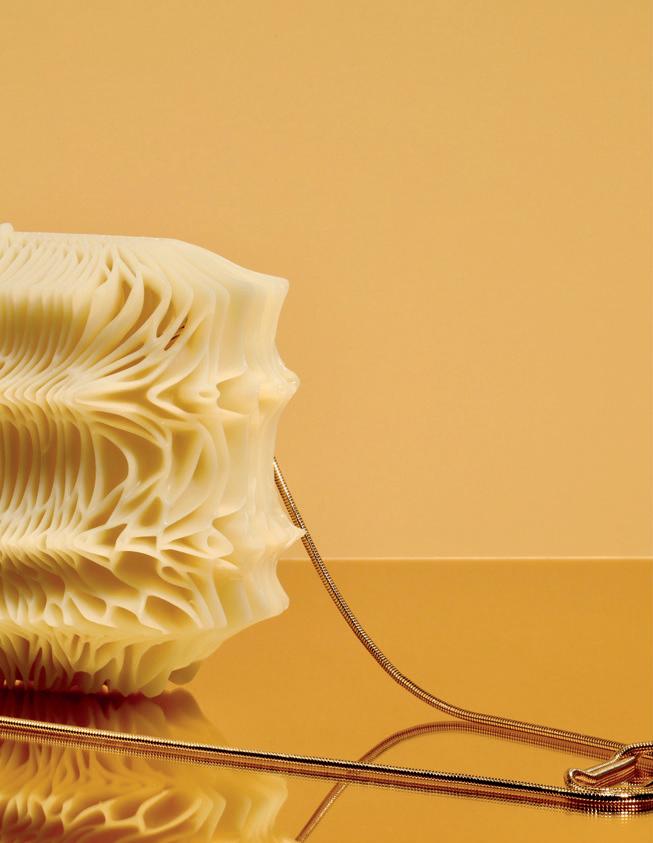
Koerner first came into contact with 3D printing at the University of Applied Arts in Vienna in 2005 and maintained an interest as she passed through the Architectural Association (AA) in London. Here, she not only met Al-Rawi, but she also became involved with the AA’s visiting school programme.
This programme took Koerner and Al-Rawi to the Wadi Rum desert in Jordan, renowned for being the closest environment on Earth to that found on Mars. While there, Koerner spent a lot of time at the Nabataean city of Petra, which was once a thriving trading centre carved into the sandstone cliff faces by the Nabataeans in the second century A.D. Over time, the carved stone columns at Petra have been eroded, but would serve as Koerner’s inspiration for a project entitled Columns to Crowns.
“We looked into this change over time, and we developed 25 columns which represent this change in a series,” Koerner says. “With 3D printing, you can produce unique custom elements, you can personalise, you can customise, and the idea was to showcase these morphologies in physical form.”
Columns to Crowns was exhibited at Amman Design Week in 2019, with the work being carried out between 2014 and 2018 and the pieces being created with 3D printed PLA and acrylic tubes. It was this work that would later lead Koerner onto the 3D Stelae sculptures, advancing the research that came in Jordan and again returning to 3D printing technology.
For Koerner, 3D printing is a means to push the boundaries of her creativity, reinterpreting how we typically think about products and creating distinctive pieces with unique geometries and aesthetics. It all dates back to her time at the University of Applied Arts in Vienna.
“My thesis was about superhuman enticement. I was inspired by the anatomy of the human body, by biological morphologies, growth systems, and abstracting the mathematical logics, what you would find in nature into geometries, which are only possible to be 3D printed,” Koerner says. “There was a certain fascination which came along where no other fabrication technique would be able to do it.”
Fifteen years on from concluding her studies, and with her JK Design and JK 3D brands progressing well, Koerner splits her time between California and Austria. On one notable return to her homeland, Koerner was invited to Swarovski’s headquarters which sits amidst a mountainous landscape in Wattens. The glass company had requested not only a keynote presentation from Koerner, but for her to also contribute to an element of its glass 3D printing research and development.
As she stood side by side with a Swarovski design team, she reinforced 3D printing’s capacity for outputting different variations of a part using the same algorithm in the same build process. This idea was manifested in a JK Design project entitled Crystal Glaciers, a series of 24 customised glass spirals that were inspired by the topology of the mountains surrounding Swarovski HQ.
“With Crystal Glaciers, we wanted to showcase that across a series of these [glass spirals] there is a shift in size and scale, in intensity and the looks,” Koerner explains. “I think it had quite an impact on how they develop the technology further thereafter.”
As an Austrian native, to work with Swarovski, and gain the company’s trust as an external designer, is a career defining moment and one that represented a significant shift. After years' working with polymer 3D printing, there were new size limitations to get to grips with while working with glass printing. She also had to adjust to a slower feedback loop since she wasn’t overly familiar with the glass printing technology that Swarovski are so far keeping under wraps.
Crystal Glaciers was a project that primarily intended to represent Swarovski’s continued spirit for innovation, but it did a good job of highlighting Koerner’s own ambition too. Her most recent work saw a return to more conventional 3D printing techniques, but another step forward in inspiration.
Manufactured with locally sourced plantbased materials, the HY CLUTCH bag features an integrated closure clasp, partial opening hinge and an interior pocket, all of which is 3D printed. Available in black, offwhite bone and transparent colours, the HY CLUTCH products are produced on-location, on-demand within a single day, before being distributed in packaging that is made from vacuum formed recyclable plastic.
While meeting a prerequisite for sustainability, it also nails Koerner’s need for originality and innovation. Featuring intricate and complex organic forms that resemble the natural hymenium lamella structures found on some species of mushroom, the HY CLUTCH bag won the Red Dot Design Award for 2021 and was Long Listed for Dezeen’s Product Design and Wearable Award 2021.
It is bold, it is distinct, and it meets the brief.
“We’re excited about it,” Koerner finishes. “I see a lot of future opportunities with this product. There is no similar product right now on the market. It’s something really unique and cutting edge.”