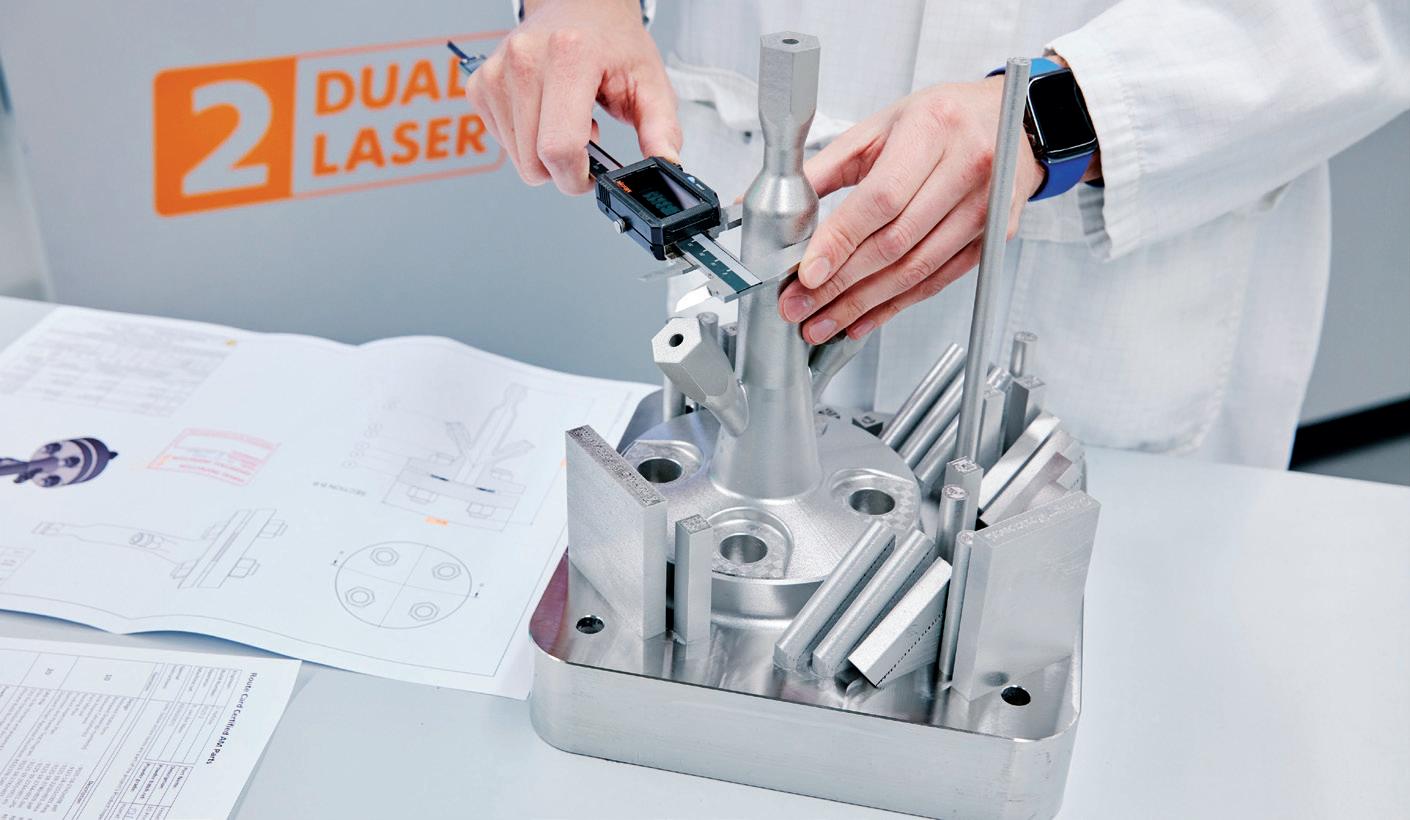
4 minute read
PRESSURE’S ON
from TCT Europe 30.1
by TCT Magazine
WORDS: LAURA GRIFFITHS
Standards remain one of the most predominant challenges in additive manufacturing (AM), particularly in those highly regulated industries the technology best serves. Speaking to TCT Magazine last year with regards to the energy sector, Shell’s 3D Printing Technology Manager Angeline Goh shared how organisations responsible for setting international standards and legislation are “still playing catch up” when it comes to AM parts, but a recent milestone with LRQA (formerly Lloyd's Register) could help to speed things along.
The oil and gas giant recently worked with the global assurance provider to successfully certify a 3D printed pressure vessel in accordance with the European Pressure Equipment Directive (PED). The project, a first for the industry, underwent four stages over four years starting with the design, through to facility qualification and printing, defining acceptance criteria, and culminating last year with testing and inspection.
To date, standards and legislation for AM pressure retaining parts have been lacking, and the need for regulations has generally prevented 3D printed pressure equipment from being permitted. The goal behind this project was to create a proof point that could inform the energy industry’s trust in AM for future applications. It also emphasises the “justin-time as opposed to just-in-case” method of part sourcing Goh also spoke about last year as Shell explores alternatives to the purchasing and storing of spares.
The vessel has been designed for pressures up to 220 bar and was manufactured at Shell’s Energy Transition Campus in Amsterdam using Powder Bed Fusion. While this CE stamp represents a significant breakthrough for the energy sector, in a more recent Q&A with TCT, Goh says there’s still a way to go.
“The knowledge and data that we have gained in this process is valuable for engaging with standards bodies and improving the sector’s trust in additive manufacturing," Goh said. "It will allow us, eventually, to further increase the scope of our inventory for just in time manufacture instead of stocking, as well as increase our scope in novel design and applications critical to our asset’s eff orts to reduce operational emissions of greenhouse gases.”
Shell shared the three main challenges that arose during this project. The first was primary material approval, which meant printing test specimens alongside the pressure vessel to test and approve material properties before formal approval through the Particular Material Appraisal (PMA) process.
Goh explained: “Unlike material bought in batches, tested upfront, with 3D printing, the part is created as the material is printed. Therefore, the formed material must be certified after the pressure vessel is already produced.”
SHOWN:
3D PRINTED PRESSURE VESSEL CERTIFIED IN ACCORDANCE WITH THE EUROPEAN PRESSURE EQUIPMENT DIRECTIVE (CREDIT: SHELL)
“The sector is still lacking general acceptance criteria for defects in 3D printed pressure vessels,” Goh elaborated. “It took a lot of R&D time and effort from Shell and LRQA to be confident with the final product. Still, more data must be collected and shared by part producers for standards setting bodies to define general acceptance criteria for defects in 3D printed pressure vessels which can be adopted by certifiers in Europe and globally.”
Data from this project can be utilised to support efforts to define standards for 3D printed pressure vessels under the EN 13445 - Unfired Pressure Vessels standard. Shell is now exploring the use of printing pressure-retaining parts for its own experimental installation, focusing on R&D and design and process optimisation “to improve the economy of printing critical parts, rather than large scale manufacturing.”
They also had to define inspection protocols that would catch defects caused by AM’s own “unique flaws.” This included printing a dummy vessel featuring deliberate defects and using a range of CT scanning, dye penetrant testing and other non-destructive techniques to observe hard to detect flaws. Due to those unique defects, the usual acceptance criteria for welded pressure vessels was deemed unsuitable by the certifier so the team had to model intentional flaws on the vessel's performance to help define maximum acceptable defects.
While the company says it will have more projects to showcase in the coming months, there are no immediate plans to get more parts certified. For now, more data, and sharing of that data, is required.
Goh concluded: “We hope other companies, research institutes and companies who have invested in similar research also see the value of sharing their learnings with standard setting bodies.”
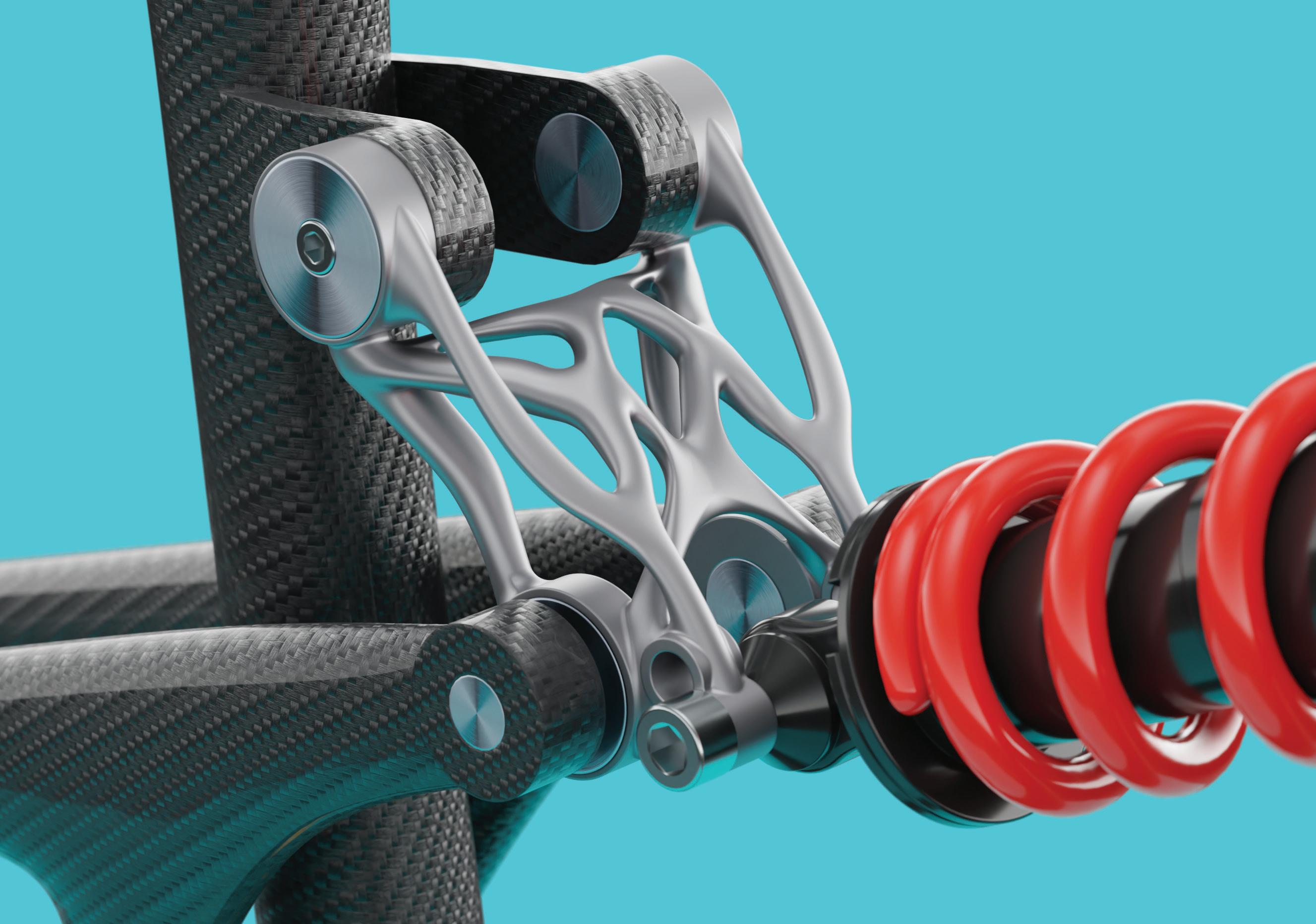
MAKE YOUR PRODUCT RIGHT THE FIRST TIME
DESIGN WITH ADVANCED MATERIALS
When you need to combine peak performance with ultimate lightweight requirements, fi ber-reinforced materials are the solution of choice – no matter what industry you’re in.
From product ideation to certifi cation, Altair solutions give you an innovative, comprehensive, holistic product development approach. With our industry-leading simulation, HPC, and AI tools, you get the power to create lighter, higher-quality, and more sustainable designs with advanced materials. With our intuitive solutions, you can beat project deadlines and deliver on performance metrics like never before.
Surpass the competition and shatter expectations with Altair.
Learn more at altair.com/sustainability-solutions