ADVANCED MANUFACTURING MACHINE GUIDE
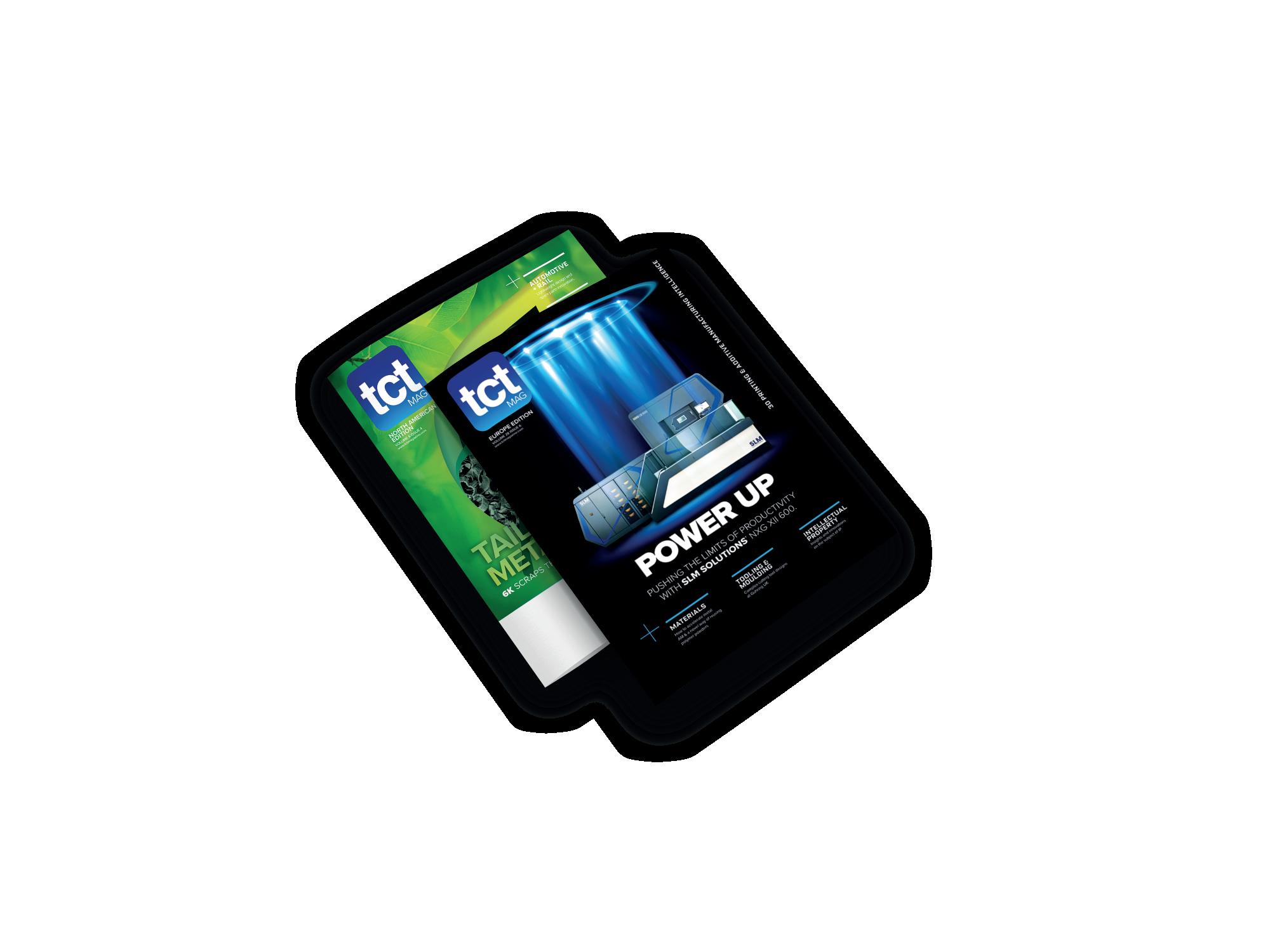
Whether it’s end-use components in automotive, manufacturing aids on consumer-facing production lines, or medical models in life changing healthcare applications, it isn’t such a stretch to say there isn’t an industry that additive manufacturing hasn’t touched in some way.
Since you’re holding a copy of or digitally scrolling through this year’s Buyers Guide, you’re probably wondering how the technology fits into yours.
Since the pandemic, widespread industry challenges around supply chain constraints and sustainability demands have turned the spotlight onto AM in new ways. Perhaps that‘s why you’re here? What could have easily been shrugged off as another so-called hype curve has transpired into continued adoption and developments across the AM gamut as the technology has proven itself as a viable, and oftentimes unique, solution to such challenges.
But choosing the right technology for your application is vital, and more than ever, businesses are being more cautious about where to place their capital expenditure. If you decide to invest in a new technology, you want to maximise its potential –dormant machines do nothing for a business, nor this industry’s street cred!
And despite what past mainstream marketing may have once told you, there is no one size fits all solution. Sorry!
The good news is, you’ve come to the right place to find one that suits your application. Whether you’re looking for information on build volumes, material capabilities or print speeds, the TCT Buyers Guide provides you with a simple, digestible guide to the additive manufacturing options available on the market today.
Whether you’re evaluating how AM might fit into your business, actively adopting for a specific application, or optimising your capacity with the addition of new hardware, the TCT Buyers Guide is where you’ll find the information you need to make the right purchasing decisions and get started.
LAURA GRIFFITHS HEAD OF CONTENT3D Systems launched the 3D printing industry in 1986 and has been leading additive manufacturing innovation ever since. Our broad portfolio of hardware, software, and material solutions spans from plastics to metals, and is backed by industry-specific engineering expertise housed in our Applications Innovation Group. We take a consultative, application-focused approach to solving your most difficult design and production challenges. The combination of our solutions, expertise, and innovation helps our users defy conventional manufacturing limitations and maximize the value of additive manufacturing.
Headquartered in Rock Hill, South Carolina, with offices, manufacturing facilities, and Customer Innovation Centers around the globe, 3D Systems has the expertise and
Figure 4™ Standalone
Printer 426 x 489 x 971 mm 124.8 x 70.2 x 196 mm
Figure 4 Tough 60C White, Figure 4 Tough 65C Black, Figure 4 High Temp 150C FR Black, Figure
4 Rigid Gray, Figure 4 Rigid White, Figure 4 JEWEL MASTER GRY, Figure 4 RUBBER-65A BLK, Figure 4 FLEX-BLK 20, Figure 4 HI TEMP 300-AMB, Figure
4 EGGSHELL-AMB 10, Figure 4 PRO-BLK 10, Figure 4 TOUGH-BLK 20, Figure 4 MED-WHT 10, Figure
4 MED-AMB 10, Figure 4 JCAST-GRN 10, Figure 4 TOUGH GRY 15 - UV Curable Plastics
Figure 4 Tough Clear, Figure 4 Tough 60C White, Figure 4 Tough 65C Black, Figure 4 High Temp 150C FR Black, Figure 4 Rigid Gray, Figure 4 Rigid White, Figure 4 RUBBER-65A BLK, Figure
0.02 to 0.1 mm
Up to 104 mm/ hr vertical build speed
Figure 4™ Modular 3D Printer Configuration dependent 124.8 x 70.2 x 346 mm
4 RUBBER-BLK 10, Figure 4 FLEX-BLK 20, Figure 4 HI TEMP 300-AMB, Figure 4 EGGSHELL-AMB 10, Figure 4 PRO-BLK 10, Figure 4 TOUGH-BLK 20, Figure 4 MED-WHT 10, Figure 4 MED-AMB 10, Figure 4 TOUGH GRY 15, Figure 4 TOUGH-GRY 10UV Curable Plastics
0.02 mm min.
Up to 104 mm/ hr vertical build speed
Figure 4™ Production
3D Printer
Configuration dependent 124.8 x 70.2 x 346 mm
Figure 4 Tough Clear, Figure 4 Tough 60C White, Figure 4 Tough 65C Black, Figure 4 High Temp 150C FR Black, Figure 4 Rigid Gray, Figure 4 Rigid White, Figure 4 RUBBER-65A BLK, Figure 4 RUBBER-BLK 10, Figure 4 FLEX-BLK 20, Figure 4 HI TEMP 300-AMB, Figure 4 EGGSHELL-AMB 10, Figure 4 PRO-BLK 10, Figure 4 TOUGH-BLK 20, Figure 4 MED-WHT 10, Figure 4 MED-AMB 10, Figure 4 JCAST-GRN 10, Figure 4 TOUGH GRY 15, Figure 4 TOUGH-GRY 10 - UV Curable Plastics
0.02 mm min. Up to 104 mm/ hr vertical build speed
NextDent™
ProJet®
ProJet®
Broad selection of
curable Plastics 0.03 mm min.
VisiJet®
0.1 mm 28mm/hr max. vertical build speed
PPSU, CF-PEEK, GF-PEEK
Filaments: ABS, PLA, PETG, PP, ASA, TPU, TPE, TPC, PC, Nylons, CF-ABS, CF-PETG, CF-PP, CF-PC, GF-PC, CF-Nylons, GF-Nylons, HIPS
Pellets: ABS, PLA, PETG, PP, ASA, TPU, TPE, PEBA, TPC, PC, Nylons, CF-ABS, CF-PETG, CF-PP, CF-PC, GF-PC, CF-Nylons, GF-Nylons, CF-PEI, GF-PEI, CFPEKK, GF-PEKK, PPS, PPSU, CF-PEEK, GF-PEEK
Filaments: ABS, PLA, PETG, PP, ASA, TPU, TPE, TPC, PC, Nylons, CF-ABS, CF-PETG, CF-PP, CF-PC, GF-PC, CF-Nylons, GF-Nylons, HIPS
Pellet
Extruder: 0.4mm - 6mm
Filament Extruder: 0.15mm - 1mm
Extruder: 0.4mm - 6mm
Filament Extruder: 0.15mm - 1mm
Up to 30,000 mm/min
Up to 30,000 mm/min
ProJet®
Sapphire, e-Stone™
Accura® 25, Xtreme, Xtreme White 200, ABS Black, ClearVue, 48HTR, Phoenix, Sapphire, e-Stone™
0.025 to 0.125 mm
0.050 to 0.125 mm
Accura AMX Durable Natural,
AMX Rigid Black, Accura
Phoenix,
White 200,
Xtreme, Accura Bluestone, Accura CastPro, Accura ABS White, Accura ABS Black, Accura ClearVue Free, Accura ClearVue, Accura 48HTR, Accura
White
Accura®
(widest
0.05 to 0.15 mm
0.05 to 0.15
to
9T Labs, a spin-off of ETH Zürich, was founded in 2018. The company has created a new way of building composite parts, one that combines 3D printing technique and filament with continuous carbon fiber reinforcement and compression molding to create strong, light components. The multi-step method delivers parts that can be both cheaper and less wasteful than either conventional composite or machined parts, with less porosity and more repeatability than other continuous carbon fiber 3D printing solutions can provide. The AFT solution is targeting serial part manufacturing for yearly volumes between 1‘000 and 100‘000 parts.
9T Labs’ Red Series system consists of its Fibrify software and two different machines, the Build module and the Fusion module. The Build module is essentially a 3D printer with two filament guides to place thermoplastic filament (to date, bio-based PA, PA12, PPS, PEKK, and PEEK) alongside continuous fiber-reinforced filament (to date, glass, basalt, carbon). The platform is open source, and customers are free to use whatever filament they wish with some adjustment to print parameters. 9T Labs sources continuous fiber tape and has it split into 1-mm - 4-mm widths and respooled; this flat tape is fed into the Build module. The
printhead itself features two material deposition guides to selectively apply the thermoplastic and continuous fiber filament. Importantly, the reinforced filament need not follow the same path as the neat plastic; instead, this capability can be turned on and off as needed. The Fibrify software provides user-adjustable intelligent fiber layup suggestions and integrates with commercially available FEA simulation packages such as ANSYS to verify and optimize these patterns. Out of the printer, the parts’ voids and dimensional accuracy preclude them from most of the high-performance production applications 9T Labs is truly after. To achieve their final density and dimensions, these “preform” parts go through a compression molding step in the Fusion module, capable of reaching temperatures up to 400°C and active pressure regulation of greater than 20 bar.
This step uses a mold tool unique to the part — typically machined aluminum for a short-run job, or stainless steel for higher volumes — to compress the printed layers and fiber together, resulting in a low-porosity, dense and strong final composite piece. Parts are said to achieve less than 1% void content through the Fusion process. As an added benefit, bushings, bearings and other inserts can be added to parts during compression molding and secured into place during this step, reducing assembly on the other side. The process also allows multiple sub-parts to be assembled and fused into one part with a complex fiber orientation as well as preform reshaping.
The full-stack solution runs under the name Red Series® Additive Fusion Technology. It includes the software - fibrify ® - the 3d-printer - Build Module - and the compression molding unitFusion Module
350 mm x 270 mm x 250 mm (the Fusion Module can consolidate all parts coming from the Build Module)
Polymers (neat and choppedfiber): bio-based PA, PA12, PPS, PEKK, PEEK
Continuous fiber tape: glass, basalt, carbon
Polymer filament (neat and chopped fiber): up to 150 g/h
Continuous fiber tape: up to 90 g/h
Addiblast® product line by FerroECOBlast® Europe presents the most advanced postprocessing solutions for the additive manufacturing industry, combining 3 key post processing solutions within the same product line: de-powdering, powder recovery & conditioning and surface treatment of 3D-printed parts. Addiblast® line is compatible to post process all main brands of 3D printers existing on the market.
MARS01 is designed for manual de-powdering. The base plate with the 3D parts attached is loaded into the workspace on the hand-held rotating table on which the operator has the option of removing the powder with compressed air. The workspace is airtight and prevents any leakage of the powder. It is equipped with openings and built-in gloves, allowing the operator to clean and remove support structures in a controlled environment. Powder can be collected in the bin bellow or connected to the powder extraction unit for reuse.
MARS02 is designed for automatic plastic powder removal together with surface finishing of complete printed batches. User loads complete batch into the rotating drum, which is located inside the workspace. Blasting and removing the powder is carried out by a process stored in the PLC unit.
MARS03 is designed for a fully automated metal powder removal process for extremely complex metal structures. The whole system is explosion-proof and fully complies with the ATEX Directive, so the treatment of titanium and aluminum powder is not a problem, as the system can produce and maintain a controlled inert atmosphere, keeping oxygen levels below 2%. Fully programmable recipes for rotation movements in X and Z directions along with vibration enables collection of non-sintered metal powders. For the safe loading of heavier jobs, stations are equipped with a unique automatic top lifting door, which allows easy and safe manipulation.
BAM blasting cabinets are suitable for various manual processes such as surface smoothing, roughing, unifying and removing of excess sintered powder. Cabinets can be used also for removing support structures and precise removal of powder from extremely complex structures and internal cavitites. It is made of stainless steel and is suitable for all types of shot blasting media. It consists of both injection-suction and pressure blasting systems, giving users extreme flexibility.
STAR02 is designed as a central station that continuously and automatically provides pneumatic transfer, recycling, and conditioning of powder from various sources. It provides a direct connection to the 3D-printer, de-powdering station (MARS03), and can also be used to purify the virgin powder before it is used in the 3D-printer. Powder recovery and conditioning provide significant improvements for serial additive manufacturing production.
L: 800 W: 800 H: 1700
Smoothing, roughing, unifying, removing support structures, precise powder removal
Stainless Steels, Tool Steels, Cooper Alloys, Titanium Alloys, Nickel Alloys, Stellites, All Nylons, PLA, ABS, TPU, TPE, Ceramic,
650 x 500 x 500 mm
L: 1500 W: 1200 H: 2050
Manual metal powder support structures removal
For reactive or/and nonreactive metal powders: Stainless Steels, Tool Steels, Cooper Alloys, Titanium Alloys, Nickel Alloys, Stellites
Accept build volumes up to 400 x 400 x 400mm and up to 150 kg
L: 1600
1800
2050
Automatic batch plastic de-powdering and surface finishing. PA + TPU material groups Rotary drum diameter 400mm
L: 2000
1200
2050
Fully controlled and automated metal powder removal.
For reactive or/and nonreactive metal powders: Stainless Steels, Tool Steels, Cooper Alloys, Titanium Alloys, Nickel Alloys, Stellites
L: 2000
Automated powder transfer, conditioning and collection. Recycling and conditioning of powder Purifying virgin powder.
For reactive or/and nonreactive metal powders: Stainless Steels, Tool Steels, Cooper Alloys, Titanium Alloys, Nickel Alloys, Stellites
Accept build volumes up to 400 x 400 x 400mm and up to 150 kg
40l powder collection bin
Additive Industries is the technology leader in large frame industrial metal AM solutions. MetalFABG2 provides our customers with the highest productivity, best print quality large frame metal AM solution for manufacturing metal component solutions. Headquartered in the Eindhoven / Brainport region of the Netherlands, and with Process & Application Development Centers in Filton UK, Camarillo, CA, USA, and Singapore, we are here to co-develop your business case and application. Among our blue chip customer base are industry leaders such as VW, BMW, AcelorMittal, K3D, Addman, F1 Team Alfa Romeo Racing ORLEN, to name a few.
We offer services to help you develop and deliver compelling business cases that add value and drive your company strategy, to lead you in the design of solutions and develop and define your process and application development to deliver best in class AM solutions. As your partner, we offer services to drive continuous improvement and drive OEE measures to maximise utilization and asset utilization.
“Additive Industries is the only company providing industrially integrated scalable metal additive manufacturing solutions that we can acquire today”
Mike Curtis-Rouse, Head of Manufacturing for Space at Satellite Applications Catapult
As productivity leaders we often get challenged to push the boundaries of what’s possible in metal additive manufacturing. The first important part of being productivity leaders is the hardware of our MetalFABG2 systems. The MetalFABG2 has automated the manual steps of conventional printers to ensure highest productivity, resulting in the lowest total cost per printed part. With our Powder Load Tool we extend the automation even further, eliminating time needed to fill the system with powder, in a fully inert and safe way. The fully automated process ensures high throughput and reduced operating cost, all focused on achieving the lowest cost per part possible.
For industrial-quality production, the part reproducibility of the MetalFABG2 is assured through solid machine design in combination with advanced laser calibration technology. Predictability is achieved by combining part build simulation, scripted process controls and in-process quality monitoring.
The closed and automated MetalFABG2 system puts the needs & safety of the operator first. The goal of Additive Industries is to make systems and solutions that are easy to integrate into industrial environments. That means: no need for long operator trainings, connections to existing workflows, minimum personal protection equipment and complying with local safety standards.
Please contact us if you want to find out what this can mean for your productivity: sales@additiveindustries.com
Focus on large part production and application development. The first step into fully automated production.
Build volume in mm 420 x 420 x 400 (width x depth x height)
Continuous series production over multiple print cores in one system. Print up to 8 sequential jobs autonomously.
Titanium (Ti6Al4V), Aluminum (AlSi10Mg/ AlSi7Mg0.6), Stainless Steel (316L), Nickel Alloy (IN718, IN625), ScalmAlloy™, Tool Steel (1.2709), M300. Maximum 4 materials are possible in one system
Build speed Up to 150cm3/hr
LOOKING TO SCALE YOUR AM PRODUCTION? Is your Additive Manufacturing output growing, do you need to scale up your AM production facility, and do you want to reduce the cost-per-part?
Workflow automation will get you there as automation will impact time efficiencies, and above all cost reduction which will have a positive effect on your business.
Lowering 3D print cost price & lead times helps you leverage factory investments and scale your business, prevent offshoring, challenge injection molding where possible, and accelerate further adoption of 3D printing.
AM-Flow is the world’s leading AM workflow automation supplier and delivers building blocks to end-to-end automate your industrial 3D-printing process.
We combine expert knowledge in the field of 3D-shape identification, industrial machine vision and AI software, together with the integration of AM production-line hardware and MES software.
THE FUTURE: IS NOW: PAPERLESS WORKFLOW The core of the AM-Flow system is the ability to identify any 3D printed part within 0,2 seconds. And because you can identify parts, you can now sort parts according to the bill of materials (BOM) for each individual part.
With our proprietary workflow software, AMLOGIC, we also provide digital tracking, and tracing creating paperless AM-factories.
The benefits are clear: increased workflow efficiency, tracking & tracing, certifiable production process, automatic data entry, automatic counting, and Industry 4.0 Digital Thread.
Geometry-based 3D printed part recognition within seconds. Automating high mix and high volume - one piece flow & custom series - identifying parts, reducing labour costs.
High-speed, gentle touch sorting conveyor. In combination with the AM-VISION, the AM-SORT forms a complete sorting unit.
Fully automated Bagging, Sealing, Labelling, ready for shipping
Customized part and order information printed on the bag.
With over 80 years of cross-industry knowhow, Rösler is among the worldwide leading suppliers of innovative solutions in the field of surface finishing. In recent years, we have been increasingly dealing with requests for the surface finishing of 3D printed parts. In this sense, we have concluded quickly that, compared to traditional manufacturing processes, additive manufacturing poses entirely new challenges for post processing. Often, these are still solved manually, but this has a negative impact on costeffectiveness and reproducibility.
To meet these requirements in the best possible way, we founded the brand AM Solutions - 3D post processing technology, which will be responsible for developing and offering tailormade equipment, process technologies, and consumables for the automated post processing of 3D printed components. Regardless of material, printing process or production volume, we will find the best quality and most economical solution for your post processing requirements. For this purpose, we also gladly advise you already during the design phase of your parts.
•
Unpacking of work pieces
• Removal of support structures
• Removal of loose and sintered powder from the component surface
• Smoothing and cleaning of internal passages
• Surface cleaning
• Surface homogenization, surface grinding & smoothing and (high gloss) polishing
• Surface preparation for subsequent manufacturing steps, e.g. coating and painting
• Liquid color smoothing
• Decades of experience in the processing and finishing of surfaces for a wide range of industries
• Broad portfolio of machines for surface processing/finishing specially developed and adapted for AM
• Individually adapted process development for every workpiece and every process step
• > 80,000 m2 production and development at the German site
• > 400 m2 Customer Experience Center at the German site
• Many years of experience in automation / process interlinking
• Competent after sales support and worldwide subsidiaries as direct local contacts
ABOVE: S1: The smart multi-talent for cleaning, smoothing, and homogenizing
LEFT: C1: Fully automatic and efficient support / resin removal from 3D printed plastic components
The German family-owned company ARBURG is one of the world‘s leading manufacturers of plastic processing machines. ARBURGadditive was founded in 2021 in order to bundle together activities in the additive manufacturing area. The product portfolio comprises the freeformers from ARBURG and the 3D-printers from innovatiQ, an ARBURG family member.
The freeformer using ARBURG Plastic Freeforming (APF) is an open system, which operates on the basis of standard granulates. The APF process opens up completely new applications.
It enables the processing of three components to produce resilient and complex functional parts in a hard/soft combination. This is unique to date within the industry. A new addition to the range is the freeformer 750-3X, whose part carrier of 750 cm² is around 2.5 times larger than that of the freeformer 300-3X.
The APF process is suitable for the additive manufacturing of prototypes and industrial functional components in particular. With the
freeformer 200-3X for two components and the freeformer 300-3X and freeformer 750-3X for three components, ARBURG covers a wide range of applications. Custom-made plastic parts for consumer goods, medical implants and spare parts made from the original material are only three of the many areas for which the freeformer is predestined.
The open system offers great geometric and material freedom. Users can apply their own original materials and optimise droplet size as well as process regulation. The ARBURG material database documents qualified standard granulates such as ABS (Terluran GP 35), PA10 (Grilamid TR XE 4010), PC (Makrolon 2805), TPE-U (Elastollan C78 A15), Ultem and PP (Braskem CP 393) as well as special plastics for
freeformer
Volume
Materials
154 x 134 x 230 (x, y, z) max.
234 x 134 x 230 (x, y, z) max. mm
330 x 230 x 230 (x, y, z) max. mm
APF is an open system, that offers great freedom in terms of materials. It is based on qualified original plastics in the form of standard granulates (e.g. ABS, PA10, PC, PP, TPE, PMMA, Ultem).
particular applications such as a PC approved for aerospace use (Lexan 940). The range of qualified materials is continuously being expanded.
The freeformers are in great demand for applications in medical technology, including for use within the human body. They are suitable for additive manufacturing of individual orthotics, implants made from original biocompatible material and models for surgical preparation. The system can process for example medical PLLA (Purasorb PL18), very soft TPE (Medalist MD 12130H) or Resomer LR 706 that imitates human bone to produce implants.
In the ARBURG Prototyping Center (APC) at the German headquarters in Lossburg, several freeformers produce benchmark parts for prospective customers. Further machines are used for the same purpose at the company‘s subsidiaries throughout the world. Preliminary trials can be conducted to determine whether the freeformer is actually suitable for the desired part, material and application.
Max. melting temperature in the plasticise cylinder
Max. build chamber temperature Support Material
up to max. 450°C up to max. 200°C
(water soluble support, e.g. Armat 11, 12) break away support
Carbon is a 3D printing technology company helping businesses to develop better products and bring them to market in less time. The Carbon DLS™ process combines versatile printers, advanced software, and best-inclass materials to deliver functional parts with end-use performance and aesthetics, helping engineers and designers to create products that outperform expectations. From prototyping and low-volume production to production-at-scale, global organizations use the Carbon process to create a wide range of functional end-use parts and print them reliably wherever and whenever they need them through Carbon’s production network partners. Carbon is a venture-backed company headquartered in Redwood City, CA. To learn more, follow Carbon on Twitter, LinkedIn and Facebook.
Make the widest range of real, functional parts with the broadest portfolio and highest performing polymer materials for 3D printing
Ideal for functional prototyping and all production levels
Offering speed, accuracy, and an effective build platform size, the M2 is well suited for a wide range of applications.
75 µm, 25, 50 or 100 µm Layerless, isotropic parts
Up to ±70 μm + 1 μm per mm dimen sion size
Up to ±0.003 in + 0.001 in per in dimension size
7.4 x 4.6 x 12.8 in 189 x 118 x 326 mm
The M3 printer is the cutting edge of DLS printing, ideal for customers looking for faster printing, a simpler print experience, an expanded design space, and a more consistent surface finish.
75 µm; 25, 50 or 100 µm
Layerless, isotropic parts
Up to ±65 μm+ 1 μm per mm dimension size
Up to ±0.0026 in + 0.001 in per in dimension size
7.4 x 4.6 x 12.8 in 189 x 118 x 326 mm
The M3 Max printer offers the benefits of next-gen DLS printing with a true 4K light engine, enabling double the build area with the same pixel size and density.
75 µm; 25, 50 or 100 µm Layerless, isotropic parts Coming soon 12.1 x 6.4 x 12.8 in 307 x 163 x 326 mm
The L1 printer is a sophisticated, proven tool for product designers, engineers, and manufacturers who need to produce at high volumes consistently.
Powering innovative, enduse products like adidas Futurecraft
4D midsoles and Riddell Diamond helmets, the L1 provides the reliability and quality needed for ondemand production.
160 µm, 25, 50 or 100 µm
Layerless, isotropic parts
Up to +0.003 in + 0.001 in per dimension size
Up to +70 µm + 1 µm per mm dimension size
15.7 x 9.8 x 18.1 in 400 x 250 x 460 mm
Machine Name Description XY, Z resolution Layer thickness Accuracy Build volumeDigital Metal®, is a global leader in highprecision metal binder jetting systems for industrial use, and the world’s first company to commercialize state-of-the-art 3D metal printers for production of components with advanced geometries. The proprietary binder jetting technology enables the production of complex objects with superior surface finish and accuracy, which is not possible with competing technologies. When going into mass production of printed components, automation is key. Digital Metal® is continually evolving the automation of binder jetting processes.
Companies from all around the world and from many different industries such as Energy, Medical, Dental, Luxury, Automotive, Aerospace and Industrial, rely on components printed with Digital Metal printers.
Digital Metal® also offers printing services in small volumes as well as larger series in the +50 000 range.
The high-precision metal binder jetting printer DMP/PRO is built for real production with a robust stable platform. All moving parts have an accuracy down to single micron which is important to minimize deviation and secure consistent repeatability from one build to another.
Some of the features are:
• Typical dimensional tolerance of ± 0,5 % (2σ) and at best ± 50 µm
• Resolution of 35 µm
• Surface roughness on average Ra 6 µm without post processing
• Wall thickness >0,3 mm and holes >0,2 mm as a guidline.
Digital Metal® is headquartered in southern Sweden, was founded in 2003, started to offer printing services in 2012 and printers in 2017. Digital Metal® is a Markforged® company
As a global full-liner with over 20 years of experience in the ADDITIVE MANUFACTURING of metal parts, DMG MORI represents innovative manufacturing technologies and a worldwide service. With powder bed and powder nozzle technology, DMG MORI combines the two most important processes under one roof and in addition offer a comprehensive portfolio of CNC machines for post-processing of additively manufactured components from a single source. The portfolio consists of the LASERTEC SLM models and the LASERTEC DED series and thus enables four complete process chains for additive manufacturing using powder nozzle or powder bed technologies.
The Directed Energy Deposition (DED) with the powder nozzle is characterized by a very high build-up rate. The LASERTEC DED / DED hybrid machines are therefore particularly suitable for components with large volumes. The flexible change between laser and milling / turning machining enables the direct machining of component segments and the integration of the complete production chain in one machine. A twin powder feeder allows multi-material applications and also graded materials.
The Selective Laser Melting (SLM) process is particularly suitable for highly complex components with functional integration or internal structures such as cooling channels. Lightweight structures also enable parts and assemblies to be significantly reduced in weight. The integral software solution for CAM programming and machine control CELOS rounds off the process chains for the LASERTEC DED and LASERTEC SLM series.
With its consulting approach, the DMG MORI Academy pursues the goal of supporting companies in developing the required design know-how and establishing the process chains around the LASERTEC DED and LASERTEC SLM series. The consulting portfolio includes services along the entire process chain of additive manufacturing, including the AM Quickcheck as a perfect entry point for exploiting these potentials. In a two-day workshop, experienced DMG MORI engineers support companies in the industry-specific and needs-based introduction of the technology.
DMG MORI is the provider for integrated solutions in the manufacturing environment. With Dynamic and Excellence DMG MORI advances future technologies. The portfolio comprises turning and milling machines, the Advanced Technologies ULTRASONIC, LASERTEC DED and LASERTEC SLM for Additive Manufacturing as well as consistent automation and digitization solutions. Its customer-focused services covering the entire life cycle of a machine tool include training, repair, maintenance and spare parts service.
EOS is the world’s leading technology supplier in the field of industrial 3D printing of metals and polymers, with a focus on responsible and sustainable manufacturing. Connecting high quality production efficiency with its pioneering innovation and sustainable practices, the independent company formed in 1989 is shaping the future of manufacturing through its innovative and comprehensive solutions. Its product portfolio of EOS systems, materials, and process parameters gives customers a crucial competitive advantage in terms of product quality and the long-term economic sustainability of their manufacturing processes. Supported by its broader ecosystem, EOS facilitates customized manufacturing solutions across the entire value chain – from the initial idea to design and engineering, production, post-processing and ultimately the finished part.
Today, industrial production is in the throes of a fundamental change. EOS is certain the future belongs to digital manufacturing, with industrial 3D Printing being one of the key drivers. At the same time, additive manufacturing can play an important role in overcoming the limitations of current manufacturing techniques that are restrictive, wasteful, and inefficient. EOS is leading the way in AM techniques such as metal support-free part printing and creating production workflows that enable easy integration with existing production lines, while accelerating the part design process.
As a market leader, EOS wants to lead by example on sustainability. This has for a long time been part of its company DNA, with a strong focus on customers and their applications. EOS nurtures an ecosystem, actively engages its community, and network, and empowers its people to strive for results that increase energy efficiency, reduce
ABOVE: Support-free hip replacement (source: EOS)
waste, and use resources conscientiously at every step of the process. All with the very clear intention of establishing Responsible Manufacturing as the ‘new normal’ – and to support customers in achieving their own sustainability goals.
EOS, its customer YOU MAWO, and Fraunhofer EMI partnered up for a comparative lifecycle analysis. The result: eyewear 3D printed on EOS technology shows up to 58 percent lower carbon footprint than conventional eyewear. As the technology enables the design and manufacturing of highly individualized eyewear, it also helps to avoid overproduction, minimizes supply chains, and enables on demand production where it’s needed.
100% Support-free 3D printing: This metal printed Titanium (Ti64) hip replacement exceeding neck fatigue testing ISO 72606 was produced on an EOS M 300-4 and EOS M 290 and integrated into a traditional production workflow. By shifting to supportfree 3D printing, the AM process was improved economically and environmentally. Not needing to construct supports during the build means less of the material in the powder bed will be melted, which cuts down production time and saves post-processing resources. This results in a lower level of material waste and reduced energy expenditure.
AMCM, an EOS company that provides customized machines, enables new levels of part performance. Customers like ThyssenKrupp can produce highly efficient copper components thanks to the AMCM M 290 system with 1 kW infrared fiber laser. The new inductor design generates an optimized magnetic field, which leads to a more efficient process. The cost saving is an impressive 60% when the inductor is manufactured using the additive process. The inductor has 2.5 times longer service life and, in addition, the power consumption during the heating process can be reduced by 50%.
ABOVE: Dual function inductor (source: thyssenkrupp)
Machine Name Machine Size (mm; w x d x h)
Build Volume (mm)
Plastic systems: more under www.eos.info/plastic
FORMIGA P 110 Velocis
additional technology version with CO laser available for FineDetailResolution (FDR)
1,320 x 1,067 x 2,204 mm (51.97 x 42.01 x 86.77 in)
EOS P 396
1,840 x 1,175 x 2,100 mm (72.4 x 46.3 x 82.7 in): system incl. switchgear cabinet
200 x 250 x 330 mm (7.9 x 9.8 x 13 in)
Nylon 11: natural, black, climate neutral Nylon 12: white, natural, glass-filled, aluminum-filled Thermoplastic Polyurethane: unfilled
EOS P
3,400 x 2,100 x 2,100 mm (133.9 x 82.7 x 82.7 in)
340 x 340 x 600 mm (13.4 x 13.4. x 23.6 in)
Nylon 11: natural, black, flame-retardant hal., carbon fiber filled, climate neutral Nylon 12: white, natural, glass-filled, aluminum-filled, flame-retardant hal. & non-hal. Thermoplastic Polyurethane: unfilled
EOS P
EOS P
2,250 x 1,550 x 2,100 mm (88.6 x 61 x 82.7 in)
500 x 330 x 400 mm (19.7 x 13 x 15.7 in)
Nylon 12: white
2,500 x 1,300 x 2,190 mm (98.4 x 51.2 x 86.2 in)
700 x 380 x 580 mm (27.6 x 15 x 22.9 in)
Nylon 11: natural, black, climate neutral Nylon 12: white, natural, glass-filled, aluminum-filled, flame-retardant hal. & non-hal.
Thermoplastic Polyurethane: unfilled
700 x 380 x 380 mm (27.6 x 15 x 15 in)
PEKK: carbon fiber filled
Machine Name Machine Size (mm; w x d x h)
EOS M 290
Build Volume (mm)
Metal systems/Direct Metal Laser Sintering (DMLS): more under www.eos.info/metal
2,500 x 1,300 x 2,190 mm (98.4 x 51.2 x 86.2 in)
EOS M 300-4
5,221 x 2,680 x 2,340 mm (205.6 x 105.5 x 92.1 in)
EOS M 400
4,181 x 1,613 x 2,355 mm (164.6 x 63.5 x 92.7 in)
EOS M 400-4
4,181 x 1,613 x 2,355 mm (164.6 x 63.5 x 92.7 in)
250 x 250 x 325 mm (9.85 x 9.85 x 12.8 in) incl. build platform
Cobalt chrome, titanium, stainless steel, maraging steel, tool steel, nickel alloys, aluminium, case hardening steel, copper
300 x 300 x 400 mm (11.8 x 11.8 x 15.8 in) excluding build plate
Aluminum, Nickel alloy, maraging steel, titanium and further materials under development
400 x 400 x 400 mm (15.8 x 15.8 x 15.8 in) including build plate
Nickel alloy, aluminum, titanium, maraging steel, copper
400 x 400 x 400 mm (15.8 x 15.8 x 15.8 in), including build plate
customized machines via AMCM (1KW, Dual Laser) www.eos.info/responsible-manufacturing
Nickel alloys, maraging steels, stainless steel, aluminium, titanium
Farsoon Technologies is a global supplier of industrial-grade polymer laser sintering and metal laser sintering machines. In addition to our established 3D printer portfolio, Farsoon is focused on maximizing productivity with multi-laser technologies on large-format platforms, to open up potential markets and applications by lowering operational cost and enabling true industrial-scale series manufacturing. We offer:
Farsoon offers high-quality, industrial grade metal and plastic powder bed fusion machines that features a wide range of build envelope size and process capability.
Powered by a strong material R&D team, Farsoon develop and manufacturing high performance PA12 and PA6 based materials for your additive manufacturing needs.
Package includes versatile build preparation software BuildstarTM and powerful machine control software MakestarTM. Advanced 3rd party software such as Siemens and Autodesk can also be integrated with the machine.
Farsoon’s dynamic support teams are globally diversified, professional engineers are ready to collaborate and provide a dedicated level of support that tailored to customer’s needs.
here
help!
Machine Name Laser Type
Envelope
FLIGHT HT1001P Dual Fiber Lasers, 2 x 300W, or Quad Fiber Lasers, 4 x 300W 1000 x 500 x 450 mm (39.4 x 19.7 x 17.7 in)
HT1001P-2 Dual CO2 Lasers, 2 x 100W 1000 x 500 x 450 mm (39.4 x 19.7 x 17.7 in)
FLIGHT HT403P Single Fiber Laser, 1 x 500W, or Dual Fiber Lasers, 2 x 300W
403P SERIES CO2 Laser, 1 x 100W (HT/SS) CO2 Laser, 1 x 55W (HS)
252P SERIES CO2 Laser, 1 x 100W (ST)
400 x 400 x 450 mm (15.7 x 15.7 x 17.7 in) or 400 x 400 x 540 mm (15.7 x 15.7 x 21.3 in)
400 x 400 x 450 mm (15.7 x 15.7 x 17.7 in) or 400 x 400 x 540 mm (15.7 x 15.7 x 21.3 in)
1 x 55W (HT) 250 x 250 x 320 mm (9.8 x 9.8 x 12.6
• PA6
Processable Material
material platform)
• FS3201PA-F, FS3401GB-F
• Elastomeric Materials
• PA6
• Diverse selection of PA materials including carbon fiber fill, glass bead fill, and mineral fiber fill
PA6
• FS3300PA-F, FS3401GB-F
• Elastomeric Materials
• PA6 (HT/ST), PA66 (ST), PPS (ST)
• Diverse selection of PA materials including carbon fiber fill, glass bead fill, and mineral fiber fill
• Elastomeric Materials
• PP
Up to 20.0m/s (65.6 ft / s)
Up to 15.2m/s (49.9 ft / s)
Up to 20.0m/s (65.6 ft / s)
Up to 15.2m/s (49.9 ft / s)
Up to 10.0m/s (32.8 ft / s)
316L,
316L,
HX, HAYNES
Ti6Al4V, AlSi10Mg,
to
AlSi10Mg, ST1, Maraging Steel Grade
more
Up to 15.2m/s (49.9
Up to 10.0m/s (32.8 ft / s)
316L,
TA15, Ti6Al4V, AlSi10Mg, AlMgScZr, IN718, HX, AlMgScZr, Maraging Steel Grade 300, H13,
W, Ta, CuCrZr, more materials to
Up to 15.2m/s (49.9
Since its founding 2013, Fusion3 has delivered on, its commitment to provide our business & educational customers with affordable, high-performance 3D printing solutions.
The new Fusion3 EDGE is the 3D printer of manufacturers in aerospace, automotive, metal fabrication, and many other industries. The fourth iteration of the ‘F-Series’ motioncontrol platform builds upon our reputation for performance and quality, providing the speed and detail to prototype parts large & small at even better quality than prior Fusion3 3D printers. With its larger 14.5″x14.5″x13.5″ build area, EDGE is excellent for making jigs & fixtures using engineering-grade materials that are tough, durable, and withstand high-temperature environments. Thanks to our categoryleading speed and large build area, many of our customers frequently engage in volume production of many different types of parts, too expensive to injection mold.
For EDGE, we’ve updated the ‘F-Series Platform’ with upgraded motion control components, including all-new linear rails, Gates 2GT2 belts, and specially tuned stepper motors. Through these changes, Fusion3’s EDGE 3D printer has attained even faster speeds at standard print settings with tremendous improvements in print quality and enabled unique features such as a new “Fast” 3d printing mode for printing certain materials at 200MM/sec using a .4MM print head.
Fusion3’s patent-pending ANVIL print head system combines precision-milled print head components with an inexpensive surgical steel print tube in place of the traditional screw-in 3D printer nozzle.
The ANVIL print head, which heats up to 320°C, utilizes precision milled components, a highquality, high-temperature heater cartridge, and a PT-1000 temperature sensor.
The use of a single, interchangeable, surgical steel print tube, enables faster 3D printing and is wear-resistant for use with abrasive filaments such as carbon fiber or fiberglass-reinforced filament.
The print tubes come in .4MM, .6MM and .8MM sizes and are easy to swap out, or customers may decide to purchase extra ANVIL print heads and swap print heads out on the carriage.
The single tube design is more reliable, eliminating the chance of leakage found in a traditional screw-in nozzle print head, and inexpensive and easy to replace, translating to lower operating costs.
EDGE will build massive parts, quickly with its total build area of 14.5″ x 14.5″ x 13.5″ (1.64 cu ft). Passively heated from the multizone print bed (max temp 145*C) and print head (max temp 320*C) , the enclosure heats up to 70*C.
This heated build area ensures excellent print results when printing high-temperature, engineering-grade materials such as ABS and Polycarbonate.
New control systems are powered by a dedicated 64-Bit ARM processor, separate from the 3D printer’s control board. Powering a 7″ touch screen, more useful information and robust remote management tools, including maintenance reminders are available to the operator.
Fusion3’s rigorous material testing and certification process ensure that our customers can print the widest range of materials purchased from a variety of quality suppliers. Using the ¼” aluminum tool plate print bed with glass print surface (standard), our customers can print materials from all major categories including (but not limited to): PLA, ABS, ASA, Reinforced Materials including Carbon Fiber, Kevlar, and Fiberglass, Flexible, Nylons, PET/ PETG and Polycarbonate.
With the addition of an optional magnetic tool plate and various optional magnetic print surfaces, customers can now print new materials, including Polypropylene, PVDF, and 316L Stainless Steel. Fusion3 provides customers with optimized settings for these materials within our bundled REACTOR 3D printing software, ensuring certified materials print successfully “out of the box.”
engineering-grade materials such as ABS and Polycarbonate
and
speed 500 mm/sec
Intech Additive Solutions was founded in 2012 and has been a pioneer in Additive Manufacturing since then. Our portfolio includes LPBF Metal 3D Printers, AM Software, DfAM Consultancy, and 3D Printed Flow Reactor System. In 2018, DMG MORI came on board as an investment partner.
With a management team having over three decades of rich experience in metallurgy and component machining, Intech has transformed into a leading solutions provider in Metal Additive Manufacturing (AM) systems and AM Software. We are revolutionizing AM by providing a complete eco-system right from concept design, material selection to printing, post-processing, and testing of metal parts, thereby accelerating the adoption of Metal 3D Printing in Manufacturing.
Intech is among the few manufacturers globally to integrate its iFusion series of Metal 3D Printers - iFusion SF1, iFusion MF, iFusion LF, with its in-house build processing software –AMBuilder and parameter optimization software -AMOptoMet.
We have been at the forefront of innovation that can transform the manufacturing industry through digital technology. Software, Design(DfAM) and Hardware capabilities make us one of the very few all-encompassing Additive Manufacturing OEM Solutions company in the world.
As a company of many firsts, we are pioneers in offering solutions that empower customers to adopt additive manufacturing efficiently and effectively. Driven by the philosophy of ‘first time right’, it is our endeavour to uphold the needs and business interests of our customers all the time.
Our dedicated team of engineers, out-of-the-box thinkers and problem solvers are in a constant quest to revolutionise the manufacturing processes with the help of Additive Manufacturing. Our mission is to enable faster adoption by keeping the innovation alive and influence digital transformation through additive technology in a sustainable way.
Parameter
150mm x 180mm 1 laser 500 watt
AlSi10Mg, 18Ni300, 13Ni400, SS316L, 17-4PH, IN718, IN625, CoCrMo, Ti64, CM247LC
325mm x 325mm x 420mm
1/ 2 laser(s) 500/ 1000 watt
AlSi10Mg, 18Ni300, 13Ni400, SS316L, 17-4PH, IN718, IN625, CoCrMo, Ti64, CM247LC
450mm x 450mm x 450mm
1/ 2/ 4 laser(s) 500/ 700/ 1000 watt
AlSi10Mg, 18Ni300, 13Ni400, SS316L, 17-4PH, IN718, IN625, CoCrMo, Ti64, CM247LC
INTAMSYS 3D Printing all-in-one solutions offer users infinite and customizable Additive Manufacturing possibilities. Meeting the most demanding industrial standards, INTAMSYS 3D printers are optimized for applications in industries as diverse as Automotive, Aerospace, Oil & Gas, Medical and Education.
You can easily unlock infinite applications with INTAMSYS FFF printers. Co-founded by a team of engineers with years of precision equipment development and high-performance material research, INTAMSYS strives to bring high performance materials and open-source control at an affordable price. lNTAMSYS is headquartered in Shanghai and has established 2 regional offices in Stuttgart Germany and Minneapolis Minnesota. These three offices support a global network of partners in sales, marketing, applications, and technical support.
INTAMSYS has developed a complete line of industrial FFF printers for all applications that benefit from high performance engineering plastics, ranging from the hard PEEK materials to ABS. It has successfully launched FUNMAT PRO 610HT, FUNMAT PRO 410 and FUNMAT HT industrial 3D printer to the market. The company’s first product is the FUNMAT HT, the
FUNMAT HT comes with a single extruder with a 450 °C nozzle, 160 °C heated build plate and the entire build room is heated, it is capable of printing both high-performance as regular engineering polymers. With a 610 x 508 x 508mm build volume, the FUNMAT PRO 610HT is INTAMSYS’ largest and most feature-packed 3D printer. The FUNMAT PRO 610HT is in many ways a superior alternative to the few existing larger format higher temperature printers currently available on the market in terms of temperature, build volume, certified materials and productivity features. In this year Formnext, INTAMSYS will release the latest addition to its AM solutions portfolio, the FUNMAT PRO 310 to respond to the growing demands from professional engineers. Let’s stay tuned!
INTAMSYS is also featured with the easy user experience with its Open Material system. INTAMSYS cooperates with mainstream material manufacturers to constantly expand the printing material choices to its customers. The printers are not restricted nor locked on any filament brand on the market allowing the customers to control their costs efficiently. In order to offer “ready-to-print” settings on its 3d printers, materials are being continuously tested and compared to provide the most accurate printing profiles when paired with Intamsuite, INTAMSYS’ slicer software.
PA6/66,
PC-ABS, ABS, ASA, PLA, HIPS,
PEEK, PEEK-CF, PEEKGF, PEKK, PEI 9085,PEI 1010, PPSU, PPS, PC, PC-ABS, PA6/66, PA6CF, ASA, ABS, HIPS, Carbon Fiber-Filled, Glass Fiber-Filled, ESD-Safe
PEEK, PEEK-CF, PEEKGF, PEKK, PPS, PC, PCABS, PA6/66, PA6-CF, ASA, ABS, HIPS, PVA, Carbon Fiber-Filled, Glass Fiber-Filled, ESD-Safe
PEEK, PEEK-CF, PEEKGF, PEKK, PPS, PC, PC-ABS, PA6/66, PA6CF, ASA, ABS, Carbon, Fiber-Filled, Glass Fiber-Filled, ESD-Safe
Several third-party filament manufacturers are part of the CAEP program, INTAMSYS’ customer application enabling program. The program allows INTAMSYS customers to enjoy the right printing settings on popular and well-known material brands preventing them to waste time adjusting profiles before printing.
max. 120mm/s
max. 120mm/s
max. 120mm/s
max. 120mm/s
INTAMSYS 3D printing all-in-one Solutions bear the ambition to make future lives fully customizable due to the infinity of possibilities the Additive Manufacturing Industry offers. Meeting the most demanding industrial standards.
Impossible Objects CBAM-2 machine delivers industrial strength 3D printed parts.
Its revolutionary Composite Based Additive Manufacturing process (CBAM) delivers part that are stronger, faster with better dimensional tolerances than any other polymer process.
With high performance materials like PEEK and carbon fiber it produces parts that are up to 5X stronger than FDM, SLS or MJF. It can make parts with no warpage and little shrinkage. Flat parts which are difficult to make in other processes can be reliably made with Impossible Objects. With a 50-micron voxel size part have outstanding surface finish. With materials like PEEK with a melting point 350 C and high chemical resistance parts can be used in industrial environments like solder pallets. Because we use inkjet printing and parallel methods, we are faster than
other polymer processes. With the use of lowcost materials like fiberglass we can produce parts at lower costs than other processes.
Carbon fiber allows for strength to weight ratios that are better than aluminum. Because of the use of fiber reinforcement, we make industrial strength parts that can be used in aerospace
and drones. Propellers and fans don’t fall apart when spun at high speed and as compared to FDM parts can be built up to 10X faster.
Impossible Objects provides both parts services and machines.
JuggerBot 3D manufactures industrial-grade 3D printers that are uniquely capable of processing performance materials. Since first being introduced in 2020, manufacturers have equipped their teams with the Tradesman Series™ to produce large format tooling and end-use parts.
Industries Served:
Transportation Design
Oil & Gas
Power Generation
Mold and Die
Aerospace
Automotive
Defense and Military
Medical Equipment
Machine and Equipment Manufacturing
Heavy Industrial
Construction
JuggerBot 3D’s industrial product line featuring large build volumes, industrial controls, and self-contained architecture. Empowering manufacturers in the studio, shop, or on the production floor.
Boasting state-of-the-art filament and pellet extrusion technologies, JuggerBot 3D’s printers offer the most versatile capabilities in their class. Every machine fit for filament extrusion comes standard with JuggerBot 3D’s Interdependent Drive System, deploying push and pull forces to optimize control over material.
Pellet-fed Tradesman Series™ models feature top-notch extrusion technology capable of extruding material up to 300 times faster than traditional 3D printers. Active research and development is coupled with strong technology partnerships, including Oak Ridge National Laboratory, to deliver polished innovations that give operators more process control and streamlined interaction with their pellet-fed machines.
Choose from thousands of readily available materials in either pellet or filament form. Manufacturers can access materials that fit their application best at market price, as JuggerBot 3D maintains an open material system. Their close relationships with material suppliers provide operators with additional support for successful development and implementation.
party materials in 1.75mm filament, including:
Commodity thermoplastics
Flexible thermomplastics
Engineering thermoplastics
Reinforced thermoplastics
High temperature thermomplastics
Third party materials in pellet form, including:
Commodity thermoplastics
Flexible thermomplastics
Engineering thermoplastics
Reinforced thermoplastics
High temperature thermomplastics
Third party materials in pellet form, including:
Commodity thermoplastics
Flexible thermomplastics
• Engineering thermoplastics
• Reinforced thermoplastics
• High temperature thermomplastics
kg - 9 kg (0.5 lbs20 lbs) per hour
Up to 30 lbs/hr (13.6 kg/hr)
LulzBot is the premier American-made desktop 3D printer brand thanks to our award-winning reliability, repeatability, and performance. Each day, we strive to produce easy-to-use machines that allow you to create high-quality 3D prints right out of the box. Since 2011, we have proudly served Fortune 500 companies, Small Businesses, Military Branches, Universities, Libraries, and Makerspaces. Military and Government users; find us on GSA with Contract Number 47QSMA22D08NT.
If you’re looking for professional results, the LulzBot TAZ Pro platform delivers in a variety of ways. Many of our customers have shared how the TAZ Pro made 3D printing easy to adopt. Whether it’s 1.75mm or 2.85mm filament compatibility, dual-extrusion, backlash compensation, specialized build volume, or other application-specific requirements, the LulzBot TAZ Pro platform has the power, durability, and versatility needed for any project.
The LulzBot Bio is optimized for Freeform
Reversible Embedding of Suspended Hydrogels (FRESH™) printing. Out of the box, users can print unmodified collagen, alginate, and other bioinks. This brings researchers closer to recreating human physiology for in vitro testing and regenerative medicine than ever before. Equipped with an ultra-precise syringe pump extruder, the LulzBot Bio is the perfect addition to any lab!
Ready to scale your 3D printing output? At LulzBot, we operate a Print Farm of over 300 TAZ 3D Printers daily to keep up with our production needs. Lean on our experience to help plan your own LulzBot print farm catered to your needs, facility, and resources.
FOR MORE INFORMATION Call 701-809-0800 Email sales@lulzbot.com
www.massivit3D.com
Massivit 3D Printing Technologies Ltd. www.massivit3D.com (Tel Aviv Stock Exchange: MSVT) is the leading provider of large-scale 3D printing systems, serving a range of industries including Automotive, Marine, Rail, Architecture, and Scenic Fabrication. The company was established with a vision to overcome existing limitations in 3D printing production speed, size, and material versatility. Massivit 3D’s patented Gel Dispensing Printing (GDP) technology enables ultra-fast production of large-scale parts, prototypes, and molds – at up to 30 times the speed of existing 3D printers. The build volume of Massivit 3D printers facilitates parts up to 1450W x 1110D x 1800H mm.
Massivit 3D manufactures and sells proprietary interdisciplinary systems comprising hardware, advanced photo polymer thermoset materials, and sophisticated software. To date, the company provides 8 printing materials developed to suit a range of applications and industries.
The company provides end-to-end services to its global customers in 40 countries. Founded in 2013, Massivit 3D is headquartered in Lod, Israel with additional offices in Atlanta, USA and Belgium.
The Massivit 5000 is an industrial-grade, largescale 3D printer that empowers manufacturers to produce large parts, prototypes, and molds within hours, instead of days.
Leveraging Massivit 3D’s unique Gel Dispensing Printing (GDP) technology, the Massivit 5000 enables production of full-scale custom parts up to 1800 mm in height at unprecedented speed.
GDP technology leverages a range of proprietary, instantly-curing photo polymer gel materials that cure on-the-fly, enabling production of large, hollow models. The end parts are lightweight, durable, and receptive to a variety of post-processing methods.
A range of layer thicknesses are available allowing flexibility for both definition and production speed: 0.5 mm, 0.8 mm, 1 mm, 1.3 mm, and 1.5 mm.
The Massivit 5000 offers a range of features to optimize workflow efficiencies: a Dual Material Mechanism that allows operators to simultaneously print with a different material on each head according to application requirements, and integrated slicing software that enables automated file preparation.
The Massivit 10000 is designed to overcome the bottlenecks of mold production for composites with advanced additive manufacturing.
Based on Massivit 3D’s Cast In Motion (CIM) technology, the Massivit 10000 shortens workflows for mold production by up to 80% – from weeks to just days – for a range of industries including automotive, marine, rail, defense, bath ware, and construction. It is designed to replace existing tooling methods that are slow, expensive, wasteful, and require extensive manual skilled labor.
DIM 400 (High HDT, Impact-Resistant), DIM 110 (High-Definition), DIM 100 (General Purpose), DIM 20-FR (Flame-Retardant), DIM 300 (Transparent), DIM 90 (Cost-Effective), DIM WB (Water Breakable)
DIM WB (Water Breakable) for Sacrificial Shell
CIM 500 (HighPerformance Casting Material)
300 mm/sec linear speed. 35cm /13.7” on Z axis per hour (Printing speed for 1-meter diameter cylinder)
300 mm/sec linear speed. 35cm /13.7” on Z axis per hour (Printing speed for 1-meter diameter cylinder)
Leveraging advanced thermoset materials, the Massivit 10000 enables direct printing of a mold, thereby eliminating the need to produce an initial master, and shortening conventional mold-production workflows from approximately 19 steps down to just four steps.
Massivit 3D’s Cast In Motion process is more sustainable than existing tooling methods, minimizing material waste at several stages of production. The company’s advanced casting material offers a high HDT, a low CTE, and provides the only isotropic 3D printed mold on the market.
The Massivit 10000 reduces skilled laborassociated costs by 90%, decreases manufacturing costs by 75%, and dramatically shortens overall leads times for composite materials manufacturing.
Considered by many in the UK Additive Manufacturing community to be leaders in the field of 3D printing technology, strategies and applications, Matsuura has seen rapid exponential growth of our 3D printing customer base in UK manufacturing.
Operating from a state-of-the-art Additive Manufacturing Centre in Leicestershire, visitors can expect to see the entire 3D workflow – from concept to CADCAM, to preparing the chosen machine and material, to the actual printing & post processing – turning raw 3D parts into high value end user products.
Our product portfolio boasts the leading names in their chosen disciplines and materials, from PA Nylons, to TPU, to Super-polymers and of course the growing 3D catalogue of metals.
Matsuura are the UK’s leading authority and technical reseller of HP MJF Machines, with over 60 machines currently in operation at supported UK customer sites as of 2022. Our Additive Manufacturing Centre in Leicestershire is the only venue where you can see this astounding, game-changing technology, and the entire range of MJF machines in operation. Want to experience the whole process before you invest?
Want to see your components created to give you confidence in the process, machines, and Matsuura as a supplier partner? No problem.
Roboze manufacture the most accurate 3D printing technology in the world for high performance super polymers and composites. Represented and fully supported by Matsuura in the UK, our AMC boasts machines of all capacities from across the Roboze range of handcrafted machines.
Desktop Metal exists to deliver on the ultimate vision of 3D Printing: Mass Production in a diverse selection of metals, carbon fibre, wood, and the rapid onset of dynamic emerging materials. Fully supported by Matsuura in the UK, Matsuura always has Desktop Metal UK stock machines under power and ready to demonstrate in our AMC.
ETEC offers a variety of 3D printing systems with the ability to mass produce polymer parts, with the speed and quality needed for demanding end-use applications. ETEC printers deliver parts with exceptional accuracy, superior part properties, fine feature detail, and
Carbon PEEK, ULTEM AM9085F, Carbon PA, Flex-TPU, PP, Functional-Nylon, Strong ABS, Ultra PLA, ABS-ESD, Helios PEEK 2005
smooth surface finish at a scale and cost that is competitive with traditional manufacturing techniques such as injection moulding.
Always in UK stock at the Matsuura AMC, and ready to demonstrate, like all 3D printer products in our portfolio ETEC are fully supported by Matsuura from our centrally located base in the UK.
To learn more about these products visit www.matsuura.co.uk
Nano Dimension is a provider of intelligent machines that are changing the way the world manufactures.
Our vision is to transform Additively Manufactured Electronics (AME) and precision Additive Manufacturing (AM) by delivering a complete Industry 4.0 solution - transforming digital designs into functioning electronic and mechanical devices - on demand, anytime, anywhere.
Nano Dimension’s focus on AME is oriented on the design and development of HighPerformance Electronic Devices (Hi-PED®s), complemented by a suite of AM solutions that enable multi-dimensional – from millimeters to several centimeters in size with micron precision – production of polymer, metal & ceramic-based applications, and parts.
Through its strategic integration of its portfolio of products, Nano Dimension has served over 2,000 customers across aerospace & defense, automotive, industrial, technology, R&D and academia, and other industry verticals in offering
the advantages of rapid prototyping, IP security, minimal environmental footprint, and the design possibilities that are unleashed with additive manufacturing.
Nano Dimension acquired NanoFabrica in 2021 and thus added precision micro-AM to its portfolio The Fabrica 2.0 reduces the cost, lead time, and inefficiencies that come with precision manufacturing. It also eliminates the need for specialized expertise, so any company can now manufacture precision parts.
Precision micro-AM changes the economics of manufacturing in five key ways:
1. No need for tooling or tooling changes
2. Ability to produce prototypes within hours
3. High-mix, low-volume production enables a variety of parts to be produced simultaneously
4. Profitability not dependent upon economies of scale or MOQs.
5. Faster time-to-market / accelerated delivery
Essemtec is Nano Dimension’s business that leads the industry in adaptive SMT pick-andplace robotics, equipment for both high-speed-
to 60 mm per hour, depending on material
260 x 220 x 280 mm | 10.23 x 8.66 x 11 inches (88 µm) *varies – one example
300 kg
660 lbs
up to 300 layers per hour
96 x 54 x 110 mm | 3. 78 x 2.13 x 4.33 inch (50 μm) *varies – one example
and micro-dispensing, as well as an intelligent production storage and logistic systems. The combination of printed circuit board (PCB) placement accuracy, speed, and high-quality engineering makes our offerings unique.
Nano Dimension’s GIS (Global Inkjet Systems) business is a leading developer of highperformance software, ink delivery systems and printhead drive electronics for industrial print systems. Its modular components are designed to work reliably 24/7 in rugged industrial printing environments. Their scalable and flexible solution inkjet technologies are easy to integrate and can be used in XY scanning, single pass, 3D, and custom systems.
Admatec/Formatec is the newest Nano Dimension acquisition. It is a leading developer
and manufacturer of additive manufacturing and 3D printing systems for ceramic and metal enduser parts. Its industry-grade systems - powered by digital light processing technology - use materials with superior mechanical, electrical, thermal, biological, and chemical properties to produce an array of parts for medical, jewelry, industrial, and investment casting uses.
Nano Dimension’s unprecedented 3D printing capabilities are now integrating with the most advanced factory robotics and the latest developments in hardware and software, including neural-network Deep Learning AI. Our technologies will enable R&D labs new latitude to develop products that are radically innovative.
At Nano Dimension, we’re inventing something completely new – now so can you.
Nexa3D is a global leader in ultrafast 3D printing solutions. Its patented Lubricant Sublayer Photocuring (LSPc®) technology is orders of magnitude faster than traditional polymer 3D printing processes, resulting in up to 20x productivity gains in polymer production applications.
Nexa3D offers a wide range of 3D printers, spanning from the desktop to the factory floor. Its desktop resin 3D printer, the XiP offers a large, 4.8L build volume and print speeds of up to 18cm per hour, resulting in significantly greater throughput than other professional desktop 3D printers.
Powered by Nexa3D patented LSPc® Technology, the XiP’s key features include:
• Self-lubricating Everlast™ Membrane delivering enhanced part quality at superior speed
• Generous 4.8L build volume (190 x 115 x 210 mm)
• Modular, 4K resolution mono LCD and advanced UV light engine delivering uniform and consistent prints
• Open materials platform for ultimate accessibility
• Quick-change resin system for easily swapping resins
• Sleek industrial design with robust components made out of recyclable aluminum
Nexa3D’s flagship industrial 3D printer, the NXE 400Pro series is used by hundreds of customers worldwide to produce functional parts and production components for a variety of industrial applications. Its 17L build volume and unrivaled print speed enables exponential productivity gains on the production floor.
The NXE 400Pro series printer features include:
• Precision and high speeds enabled by the patented LSPc® Technology printing up to 6.5x faster than other SLA or DLP technologies
• Large, versatile build volumes up to 17L, measuring 10.8 x 6.1 x 15.7 inch (275x x 155 x 400 mm)
• Robust, high-performance materials portfolio of validated resin as well as an open platform for the ultimate freedom of resin selection. Currently validated materials include a variety of modeling and functional resins, with both rigid and elastomeric properties.
• Edge-to-edge uniformity and accuracy with 4K resolution enables part-to-part consistency across the full build without light diffusion near part edges.
(plant-based)
(plant-based)
Nexa3D’s newest industrial 3D printer, the QLS 820 is built for high throughput manufacturing applications. This thermoplastic, powderbased technology is able to print 8L per hour at up to 20% job density, making it the industry’s leading powder-based technology for serial production.
The QLS 820 printer features include:
• Highest throughput in its class printing up to 8 liters/hour and delivering an average 20% build density.
• Automation-ready architecture with Siemens PLC factory automation controls and an exchangeable build unit for optimal printer utilization and minimal down time.
• Open platform with inert, high-temperature capabilities you have an abundant material choice and build parameters, including production temperatures up to 230°C.
Oryx, a trusted additive manufacturer providing patented 3D finishing solutions for over 10 years with over 16,000 equipment units out in circulation, takes pride in its devotion to providing customers with trusted solutions that encompass high product reliability, factual product testing data, and exceptional customer service. Notable product families such as the sca product line help to define this company as a leader within the AM Finishing industry, proving their constant pursuit of achieving the full potential of additive manufacturing. Removing support materials is a significant part of finishing, but there’s often more work that needs to be done before a print can be finalized. Using its accumulated 3D printing experience, Oryx Additive specializes in helping manufacturers streamline this process, and ensure the maximization of quality and throughput of their final prints.
In removing support for FDM/FFF and Material Jetting processes, such as Polyjet or Extrusion Technology, the sca product family provides a wide range of predefined machine settings and is fully compatible with all soluble support material concentrates, from water to caustics. It further provides the user with the appropriate level of agitation to balance the needs of heavy removal while maintaining critical dimensions on delicate or intricate part geometry.
We listened to our customers, understood the needs for industrial additive manufacturing and found that current technology limits the ability to maximize support removal, and with this, src1 was born. CEO Keith Jeffcoat
Src1 is a chemical cleaning agent capable of quickly removing support material from multiple 3D printed models with speed and efficiency. The no mess cleaning agent quickly dissolves and cleans SR30 support material from FDM modeled surfaces. When paired with the sca line or other wash tanks, the prepackaged amount represents a dissolution speed of 2X the leading competing cleaning agent.
The sca Waterjet is a water jetting spray booth capable of coarse and fine support material removal for various AM processes. The capability to be plumbed direct or used stand-alone with an included mobile water tank allows for industrial uses or difficult-toplumb situations such as offices. It features a gasketed window with internal mount wiper blade assembly for clear view of the LED-illuminated work area, ergonomicallyconsidered front cabinet design & gloved ports for operator part handling, with two waterjetting spray wands - both capable of high- and low-pressure operation to fit the needs of support removal for your delicate and rigid parts alike. The covered mobile support frame minimizes collection of shop debris and dust inside the cabinet, while also allowing for a sit/ stand option for operators, with easy access to the pump and holding tank.
Oryx Additive aims to collaborate with others in the development of trusted finishing solutions that meet customer needs. Whether you are looking for a cost-effective semi-automated workflow, or a lights-out, fully-automated system, the team of engineers at Oryx Additive work with clients to deliver value based solutions to fit those needs.
Rapidia, based in Vancouver, Canada, produces metal 3D printing systems for rapid prototyping and demanding end-use applications.
Recognizing the limitations of existing metal AM systems - speed, price, part design constraints, operator safety - founder Dan Gelbart saw an opportunity to build on the significant recent advances in metal 3D printing technology with an entirely new process. The result was the development of Rapidia’s unique and revolutionary water-based system.
This system has several advantages over competing bound metal offerings. Parts go straight from the printer to the sintering furnace, eliminating the lengthy thermal or solvent debinding process, which can take upwards of 50 hours. This allows customers to start printing a part one day and have it ready the next. Loose metal powder hazards usually associated with metal 3D printing are eliminated, as are the solvents normally required for debinding.
Rapidia’s process also enables users to bond ‘green’ (unsintered) parts together by simply using a small amount of water to stick them together. This is useful for creating assemblies which would require extensive support or otherwise be impossible to print. When sintered, the bond is indistinguishable from the inherent layers.
Parts can be produced with any percentage infill for lightweighting, or completely solid when maximum strength is required, without a maximum wall thickness. Rapidia’s proprietary evaporative support technology allows users to create the most complex parts. Choose between automatically generated polymer supports which evaporate during sintering, or hand-removable metal structures when sintering support is required to prevent sagging.
Rapidia’s new, next-gen furnace uses advanced materials to offers partial pressure vacuum sintering in an unrivaled small and affordable package. The system is able to achieve excellent metallurgy in an argon atmosphere with low gas consumption and short cycle times.
From prototyping to final product, Rapidia offers the fastest, simplest, and most versatile bound metal AM system.
Renishaw designs and manufactures world-leading metal additive manufacturing systems for production of components in a variety of metals, using a process called metal powder bed fusion (or laser melting).
Renishaw is a global engineering and scientific technologies company with expertise in additive manufacturing (AM), precision measurement and process control, position and motion control, and healthcare.
Renishaw’s additive manufacturing solutions include metal AM systems, software, metal powders, ancillary equipment, accessories, and expert consultation and training. Renishaw can provide turnkey and optimised additive manufacturing solutions for a broad range of applications in the industrial and healthcare sectors.
Using its experience as a manufacturer and its expertise in process development, Renishaw
supports its AM customers as they explore how metal 3D printing could revolutionise how they design and make products.
From aerospace and medical to oil and gas, a wide range of customers use Renishaw’s advanced AM systems to fulfil a variety of industry applications where productivity, durability, customised parts and precision are key.
All AM components require a degree of finishing and inspection after they come off the build plate. Renishaw is the only company in the 3D printing industry to offer the technologies and expertise that provide both highly productive metal 3D printing AND control of finishing and downstream processes.
Sinterit became well known for introducing the compact version of the most advanced SLS (selective laser sintering) 3D printers. The company’s mission is to support the innovation and creativity of engineers, researchers, programmers, scientists, and visionaries. The system created by Sinterit is present in over forty markets around the world.
Now the product line includes three compact SLS 3D printers - Lisa, Lisa PRO, and Lisa X, as well as one new industrial laser sintering 3D printer - NILS 480 with large build volume, fast printing time, and the best ROI on the market.
Sinterit’s vision, from day one, is to accelerate global development by providing everyone access to this innovative technology. The SLS 3S printing solution by Sinterit is based on ease of use, versatility, and availability, thanks to which the technology of the future becomes available today.
Since 2014, the equipment manufactured by Sinterit has been trusted by engineers, educators, companies from industries such as automotive, prototyping, and product design all over the world.
With nine powders (PA 12 Smooth, PA 11 Onyx, PA 11 ESD, PA 11 CF, Flexa Bright, Flexa Soft, Flexa Grey, TPE, and PP Polypropylene) Sinterit has the widest material portfolio available for compact SLS 3D printers. The Powder Handling Station and the set of additional accessories make Sinterit’s solution multi-application ready.
Sintratec is the leading Swiss developer and manufacturer of precise 3D printers for professional use. The cost-effective and compact systems employ Selective Laser Sintering (SLS) to process high-quality polymer materials.
By means of the Sintratec technology, users can create complex objects with an exceptionally high freedom of design. Whether rigid or flexible, Sintratec materials are highly resilient and temperature resistant. Sintratec systems are in operation worldwide in various industries, research institutes and universities.
Sintratec’s latest machine generation – the Sintratec S2 – is the result of the company’s year long experience in the field of SLS. The S2 is more than just a 3D printer: it is a modular scalable manufacturing platform that combines the processes of material preparation, 3D printing, and depowdering in one single end-toend solution.
The Sintratec S2 provides industrial-grade quality at an affordable price with a compact modular design that can be easily extended according to manufacturing needs. Thanks to the self-contained process material changes are not only possible but can be carried out in only 10 seconds – without the risk of crosscontamination.
The Sintratec S2 delivers parts with great quality at an exceptional speed and allows us to develop much faster at a lower cost.
Valentin Vergnes Prototyping Technician INFACO
At the French company INFACO the next
of
are designed and manufactured with the help of SLS. The R&D team of Valentin
relies on a Sintratec S2 to rapidly
casings, mounts, and covers with resistant PA12 to effectively test and adjust their products before they go to market.
Since 2015 Solukon is the pioneer and technical leader of automated depowdering in additive manufacturing. The company, located in Augsburg, Germany, has extensive experience in the development of AM systems and related peripheral equipment and offers a full range of industrial postprocessing systems. Solukon has installed depowdering systems in 26 countries and is the supplier of choice of leading rocket manufacturers. The systems are approved for safe and reliable processing of powder materials, including tough-to-handle and reactive metal powders. Solukon provides four different systems, each of them optimized for your part size and application. The powder removal systems fit for every laser powder bed fusion manufacturing system on the market.
With the introduction of the unique Smart Powder Recuperation technology SPR®, Solukon developed the state-of-the-art process for powder removal.
Solukon systems clean metal laser melted parts within a sealed process chamber, using adjustable vibration and automated two-axis part rotation.
Through programmable rotation of the build plate around two axes, unfused metal powder is completely removed from complex parts with intricate channels and support structures.
Depending on the build material, the process chamber can be rendered inert with safety monitored inert gas infusion.
For the digital integration of automated depowdering, Solukon is the first manufacturer on the market offering unique digital tools using the digital twin in postprocessing.
The SPR-Pathfinder® uses the build jobs CAD file to calculate the ideal motion sequence in the Solukon system.
The Digital-Factory-Tool is a sensor and interface kit for quality validation and automation integration.
Manufacturing in metal is traditionally very complex, expensive, and inflexible and this contributes to supply chain issues when sourcing metal parts. These supply chain issues have been exacerbated globally by recent events. The world, now more than ever, needs elegant, simple, clean, flexible & reliable metal manufacturing solutions.
SPEE3D are here to help solve these issues with metal printers that enable the most affordable additive manufacturing process in the world. SPEE3D’s 3D metal printers make metal parts
the fastest way possible, leveraging cold spray technology for the production of industrial quality metal parts in just minutes, rather than days or weeks, at production costs. Rather than using heat to melt metal powders, SPEE3D developed ‘Supersonic 3D Deposition’. This is the name given to the patented process in which a rocket nozzle accelerates air up to three times the speed of sound, into which metal powder is injected then deposited onto a substrate maneuvered by a six-axis robotic arm. In this process the sheer kinetic energy of the particles hitting each other causes the powders to bind together to form a high density part with metallurgical properties superior to casting.
SPEE3D technology suits the production of parts otherwise produced using sand or die casting with the added benefits of flexibility and the ability to produce parts on-demand at the point of need.
SPEE3D produces expeditionary metal manufacturing equipment, which has been field tested and proven to be robust enough to be deployed by the Australian Army, who have used SPEE3D technology in several world-leading metal 3D printing field trials since 2020. SPEE3D technology has also been trialled by other defence forces including the Royal Australian Navy, and the US Navy. Most recently, during REPTX as part of ANTX-Coastal Trident 2022, SPEE3D’s WarpSPEE3D was the first in the world to successfully metal 3D print military maritime parts, in several different materials, on a US Navy ship. Headquartered in Melbourne, Australia, SPEE3D is committed to helping manufacturers print their parts, their way, when they need them.
Machine Name Machine Size (mm) Build Volume (mm) Materials Build Speed
LightSPEE3D Machine footprint: 3130 x 1460 x 2325mm 300 x 300mm (4kg)
WarpSPEE3D Machine footprint: 3910 x 2723 x 2742mm 1000 x 700mm (40kg)
XSPEE3D
Machine foot print: 6056mm x 2428mm x 2591mm
1000 x 700mm (40kg)
Copper, Aluminium, Aluminum Bronze and Stainless Steel 100g/min
Copper, Aluminium, Aluminum Bronze and Stainless Steel 100g/min
Copper, High-strength Alumin ium, Aluminum Bronze, and Stainless Steel (in development: Nickel-based Carbides and Titanium).
100g/min
XSPEE3D offers a containerised, ruggedised, deployable metal Additive Manufacturing capability that provides all the necessary functions to build metal parts in one place. XSPEE3D is easily transportable as a standard shipping container with printer and all auxiliary equipment within one box. With XSPEE3D, military forces can maximize productivity, strengthen inventory, and generate parts where and when they are needed quickly.
During the last two years Stratasys has added an additional three 3D Printing technologies to its portfolio, bringing the widest range of polymer materials and application possibilities to industry.
As well as producing PolyJet and FDM 3D printers, Stratasys has added stereolithography, a digital light processing (DLP) technology called P3 or Programmable PhotoPolymerization, as well as a powder bed process called SAF or Selection Absorption Fusion to its range of 3D printing capabilities.
The addition of stereolithography allows prototypes, tooling and master patterns with the state-of-the-art Neo range.
The reliable and proven Neo prints high-quality parts with superior surface quality, accuracy and detail. It also delivers a reduction in finishing time by up to 50%. An open material system means users are able to access and utilise any commercially available 355nm hybrid resin chemistry.
PolyJet is still largely used by designers for early-stage form, fit and function prototypes to validate early-stage concepts in high fidelity. PolyJet models enable true multi-material (from rigid to rubber) printing in full colour. Stratasys has also recently added the ability to print directly on to fabric, enabling fashion designers to exploit the freedom of additive technologies.
There has been a real shift by manufacturers in the last few years with jigs, fixtures, tooling and end-use parts all widely being produced on FDM 3D printers. FDM offers a huge range of real thermoplastics with ESD, chemical resistance, biocompatibility, low FST and importantly key certifications for use in many industries including aerospace, automotive, rail and defence.
P3 technology is transformative, as it enables functional end-use parts to be produced in a range of high-performance materials. It allows the industry-leading repeatability, accuracy, consistency, detail and throughput, from biocompatible medical devices to aerospace-grade components and everything in between.
The amazing accuracy and surface finish is second to none, and enables a wide range of applications from injection mould tooling to enduse production parts. Origin One’s P3 technology utilises computer vision and 25+ environmental sensors to monitor and respond to every important aspect of the print process.
SAF technology is behind the H350 3D printer, designed for production-level throughput of end-use parts. SAF uses powder-based additive manufacturing to achieve accurate, consistent production at competitive part costs.
SAF technology uses an infrared-sensitive HAF (High Absorbing Fluid) to fuse particles of polymer powder together in discreet layers to build parts. It uses Big Wave™ powder management, a proprietary technology that includes powder distribution across a bed, where industrial-grade Piezo-electric print heads jet the fluid in prescribed areas to create each layer of the part.
The high yield PA 11 is a rugged highperformance polymer that is a 100% bio-based, derived from sustainably produced castor oil.
No other 3D Printer manufacturer can match the end-to-end capabilities of Stratasys machines, with software that enables easy integration with your chosen CAD program, automatic drag and drop file preparation, tick box part build options and easy multi departments / site access to printers with upfront part build cost and print time information.
Stratasys technology scales with you, helps you stay agile and flexible, and will be your partner in training, providing new materials options and application advice to help you unlock the capability of additive manufacturing.
We pride ourselves on delivering systems to professional and industrial customers that depend on repeatability, reliability, uptime, hightolerance and successful builds every time with minimum set up and automatic fast calibration.
410
92A,
– Black
ABS-M30i, ABS-ESD7,
800NA, Antero 840CN03™ ASA, PCISO, PC, PC-ABS, FDM Nylon 12, FDM Nylon 12CF, ST-130, ULTEM™ 9085 resin, ULTEM™ 1010 resin
ABS-M30i, ABS-ESD7 Antero 800NA Antero 840CN03 ASA PC-ISO, PC PC-ABS PPSF FDM Nylon 12 FDM Nylon 12CF FDM Nylon 6 ST-130 ULTEM 9085 resin ULTEM 1010 resin
Thermwood is a US based, multinational, diversified machinery manufacturer that markets its products through offices in 11 countries. Thermwood is the oldest manufacturer of highly flexible, 3 and 5 axis high-speed machining centers known as CNC routers. We primarily market to the aerospace, plastics, composites and woodworking industries, but have found applications in almost every major industry from medical to entertainment.
Thermwood is also the technology leader in large scale additive manufacturing of thermoplastic composite molds, tooling, patterns and parts with its innovative line of LSAM (Large Scale Additive Manufacturing) machines that both 3D print and trim on the same machine. These are some of the largest and most capable additive manufacturing systems ever produced and are marketed to major companies in the aerospace, marine, automotive and foundry industries as well as military, government and defense contractors.
Thermwood has a strong ongoing research and development effort combined with core skills in diverse technical areas such as ultra high-performance control system design, real
time software development, CAD/CAM software development, advanced machine structure design, machine motion dynamics, thermal design and polymer science.
Thermwood was the first company to develop a CNC control system in the 1970s, and today our control has advanced to become one of the most powerful and capable available. It is highly regarded and used by major aerospace, automotive, government and defense contractors for some of their most demanding applications. Thermwood embraces all aspects of the essential technology, the machine, the control and the driving software. This better integrates all aspects of state-of-the-art technology into superb products to meet the most demanding customer requirements.
Thermwood machines are designed to operate in real production environments 24 hours a day, 7 days a week, 365 days a year with minimal maintenance. Many, if not most, customers go years without experiencing a technical issue.
Thermwood’s technical service is ready to help if ever needed. From highly innovative virtual service to the ability to ship almost any part of any machine overnight, to providing updates, upgrades and rebuilds of older machines, to indepth training both at the machine purchase and any time after. Thermwood service is available to anyone who owns a Thermwood machine whether it was purchased from us or on the used market.
Our key guiding principal is to insure that Thermwood users continue to profit as a result of their relationship with us.
Machine
(mm)
LSAM 1520 3048 x 4572 x 6096 (X - Y - Z) 457,200
PSU, PESU, ABS (carbon fiber filled and glass filled), PEI/ULTEM, POLYCARBONATE, PPS, PETG, POLYETHEYLENE, POK
Deposition rates from 200 lbs per hour to 500 per hour depending on the melt core and polymer used.
LSAM 1540 3048 x 4572 x 12192 (X - Y - Z) 1,097,280
PSU, PESU, ABS (carbon fiber filled and glass filled), PEI/ULTEM, POLYCARBONATE, PPS, PETG, POLYETHEYLENE, POK
Deposition rates from 200 lbs per hour to 500 per hour depending on the melt core and polymer used.
LSAM Additive Printer 5’ X 10’ 1524 X 3048 X 1219 (X - Y - Z) 60,960
PSU, PESU, ABS (carbon fiber filled and glass filled), PEI/ULTEM, POLYCARBONATE, PPS, PETG, POLYETHEYLENE, POK
Deposition rates from 200 lbs per hour to 500 per hour depending on the melt core and polymer used.
LSAM Additive Printer 10’ X 5’ 3048 X 1524 X 1219 (X - Y - Z) 60,960
PSU, PESU, ABS (carbon fiber filled and glass filled), PEI/ULTEM, POLYCARBONATE, PPS, PETG, POLYETHEYLENE, POK
Deposition rates from 200 lbs per hour to 500 per hour depending on the melt core and polymer used.
Beijing Tiertime Technology Co., Ltd. (Tiertime) is a leading innovator and 3D printing solution provider in global 3D printing industry. Its product line includes industrial 3D printer, the Inspire series, and the desktop 3D printer, the UP series, with respective 3D printing software and printing material. Tiertime headquarter locates in Beijing, China, and it reaches out the global market with business establishment all over the world.
With advanced technology and quality, ease of use and competitive price, Tiertime 3D printer has been used in various industries, including aerospace, aviation, medical treatment, manufacturing, education, design and fashion, and it is widely engaged in customized production, product sample design and model printing, product display, market research, educational experience and DIY work practice. Tiertime devotes to the commitment of best user experience as top business objective, with continuous elaboration on R&D of new technology and new product.
From prototyping to industrial series production. As a pioneer in additive technologies and laser specialist since 1979, we offer the right technology for every application requirement: Laser Powder Bed Fusion or Laser Metal Deposition. Benefit from complete industrial solutions with intelligent monitoring and smart services from a leading high-tech mechanical engineering company worldwide.
Are you looking for an application that you would like to produce additively? Talk to our AM Consulting.
In addition to performance increase with fullfield Multilaser option, the focus of the TruPrint 3000 is improving process robustness and various operating scenarios. High process reliability due to newly developed gas flow and high part quality are proven with Melt Pool Monitoring.
The 3D printer can be tailored to your production process needs.
Copper, copper
metal
Stainless steels, tool steels, aluminum, nickel-based, cobaltchrome, copper, titanium or precious metal alloys, amorphous metals
1 x 200 W
Multilaser option: 2 x 200 W (TRUMPF fiber laser)
μm
Be curious what will be presented at
Unpacking: Internal Monitoring: Condition, Powder Bed, Performance
New options: - Multiplate for 4 build plates printing without a stop - Preform for printing single abutments on pre-built base parts
Up to 200 °C
Stainless steels, tool steels, aluminum, nickel-based, cobaltchrome or titanium alloys, amorphous metals
1 x 300 W
Fullfield multilaser option: 2 x 300 W (TRUMPF fiber laser)
μm
Unpacking: Internal under shielding gas Periphery: Powder preparation station
Monitoring: Condition, Powder Bed, Melt Pool, Performance
Up to 200 °C
Stainless steels, tool steels, aluminum, nickel-based, or titanium alloys
1 x 500 W or 1 x 700 W Fullfield multilaser option: 2 x 500 W or 2 x 700 W (TRUMPF fiber laser)
80 μm
Unpacking: Internal under shielding gas or external with interchangeable cylinder in depowdering station (optional under shielding gas) or with unpacking station
Periphery: Industrial part and powder management Monitoring: Condition, Powder Bed, Melt Pool, Performance
Preheating: Up to 200 °C (basic machine), up to 500 °C (optional)
Automatic process start: Yes
500 W Fullfield multilaser (TRUMPF fiber laser) 80 μm
Unpacking: External with interchangeable cylinder in depowdering station (optional under shielding gas) or with unpacking station
Periphery: Industrial part and powder management Monitoring: Condition, Powder Bed, Melt Pool, Performance New option: Preform for hybrid manufacturing
voxeljet is one of the leading manufacturers of industrial 3D printing systems for the production of molds and models for metal casting without tools. voxeljet operates facilities in Germany, USA, United Kingdom, India and China.
voxeljet SYSTEMS business division focuses on the development, production and distribution of the fastest and most powerful 3D printing systems in the market. Today, voxeljet has a wellcoordinated product range that reaches from smaller entry models to large-format machines, and therefore offers the perfect 3D print system for many application areas.
voxeljet SERVICES custom parts service centre creates sand molds and plastic models based on CAD data on demand. Small-batch and prototype manufacturers appreciate the automatic, patternless manufacture of their casting molds and 3D models.
The company’s customer base includes wellknown automotive manufacturers and their suppliers, foundries as well as innovative companies from the arts design, footware, construction, movie and entertainment industry.
The intensive exchange of information between the two business divisions and the close linking of development and production create synergy effects that benefit voxeljet and its customers alike. Experience values gained from discussions with customers make their way into both business divisions, where they are implemented into new and trend-setting solutions and offerings. This unique combination of technical know-how and consistent improvements in technology makes voxeljet a globally respected partner for demanding clients from the world of 3D printing.