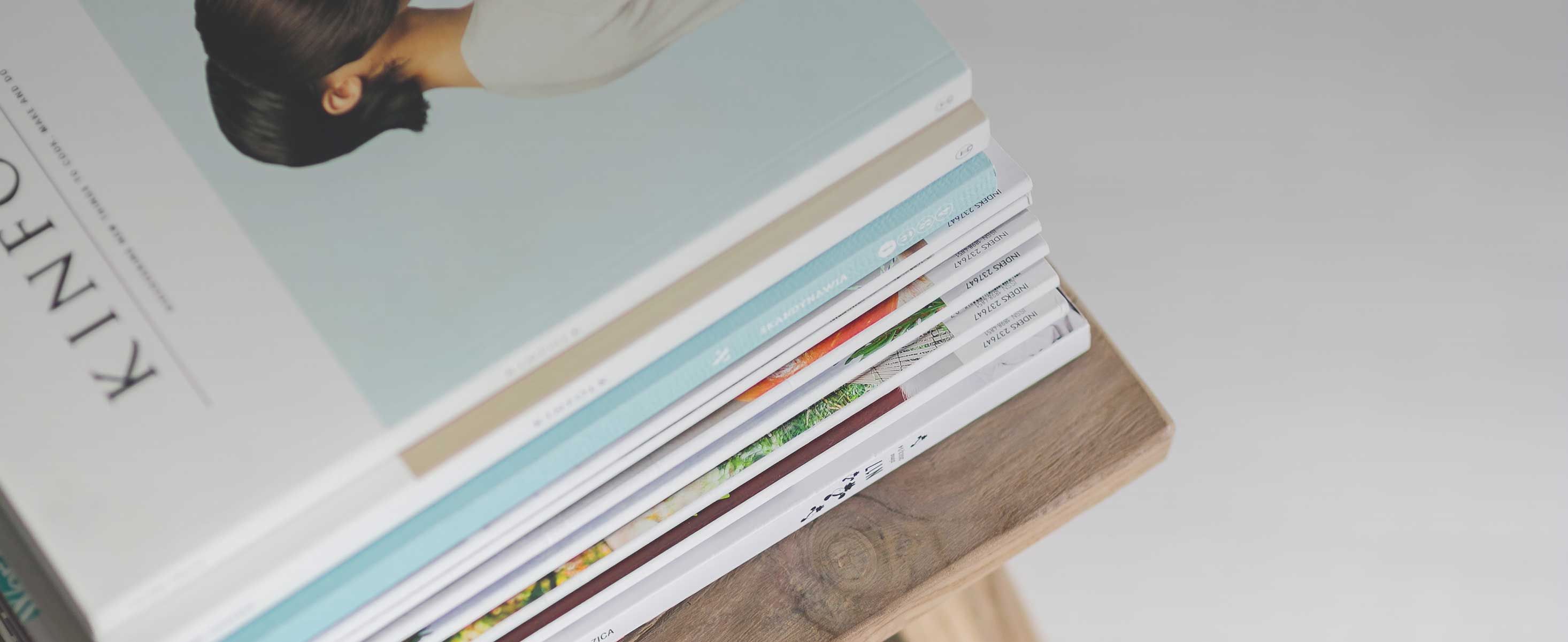
3 minute read
LET’S TALK AB UT STANDARDS
from TCT Europe 31.1
by TCT Magazine
Standardisation, certification, and qualification can pose significant challenges for additive manufacturing. But, as Amanda Allison, Senior Technical Project Leader at TWI tells TCT, they’re also vital to ramping up adoption for critical enduse parts.
As a leading independent research and technology organisation that has been providing knowledge and safety assurance in engineering, materials and joining technologies since 1946 - and the first organisation in the UK to achieve a signed AM facility qualification from Lloyd's Register for the 3D printing of stainless steel parts by powder bed fusion laser beam - TWI perhaps knows better than most the hurdles around AM qualification processes.
“Ten years ago, the development of certification, qualification and standardization frameworks was minimal because of the low readiness of both technology and industry. There was also no priority placed on their development,” Allison said, reflecting on the changing AM standards landscape. “However, as the technology develops and more parts are being manufactured and put into service, there is an increasing pressure to focus and develop these frameworks to ensure the quality and safety of AM products.”
In 2015, TWI embarked on a joint industry project with Lloyd’s Register to explore the certification of metal AM components for adoption in the energy and offshore sectors. As part of the collaboration, TWI worked with a number of Industrial Member organisations to test and certify demonstrator parts for AM production. From this, a set of industry relevant AM certification guidance notes for AM processes (powder bed fusion by laser, electron beam, directed energy deposition by laser, and Wire + Arcbased AM) were created.
“The development of standards is making it easier for industry to look to adopt the technology, but I think there is still a lack of confidence in some quarters because AM can be very disruptive and is moving rapidly. It also does not have a strong timeline of certified parts,” Allison said. “With a strong catalogue of standards, it does help give industry confidence in the use of the technology, and importantly, it standardises the approach to the processes and procedures for implementation, regardless of who is using the AM technology.” different AM systems; or the implementation of digital qualification and certification.
“AM part certification can be quite costly and it can also be a difficult journey, particularly when trying to navigate the AM standards and certification landscape alongside trying to link up with existing industrial sector standards,” Allison explained. “I also think, for facility qualification, the development and use of digital workflows is paramount in order to reliably track all process steps that parts undertake, and to monitor and control progress to ensure alignment with procedures.”
While awareness around AM frameworks is growing, an understanding of the various steps and considerations along the AM value chain takes time and education. According to Allison, "when it comes to investing in AM, certification can often fall last on the list of priorities.”
Allison continued: “We also see a lot more examples of international standards committees collaborating together, which helps eliminate duplication and maximise resources. This is particularly important because the landscape is so huge, involving a vast number of stakeholders across multiple industrial sectors. Bringing expertise and knowledge together to harmonise the approach is something that I've seen develop quite rapidly in more recent years, and something I encourage.”
Allison points to the work of ASTM (which published the first AM standard in 2009) and the ISO committees which have been instrumental in the development of standards for AM processes. However, barriers and gaps remain: the need to avoid repeat testing for parts that might only have small design differences; standards that can support qualifying
“This can lead to problems further down the line,” Allison said. “For me, certification starts at the design stage. Organisations need to be looking into the requirements for certification at the beginning because it can have strong implications on the AM process chain.”
As AM adoption accelerates, part volumes increase, and the promise of distributed manufacturing materialises, frameworks must be in place to support such ambitions.
“The key is dissecting requirements in a methodical manner and understanding how you work through all the process steps to achieve part certification,” Allision added. “At the moment, the certification journey is part-focused, and it is challenging to certify a family of similar parts. Having a means to standardise the process more rapidly, whilst providing confidence in the quality, safety and performance of parts, would help to advance the uptake of AM for industry.”