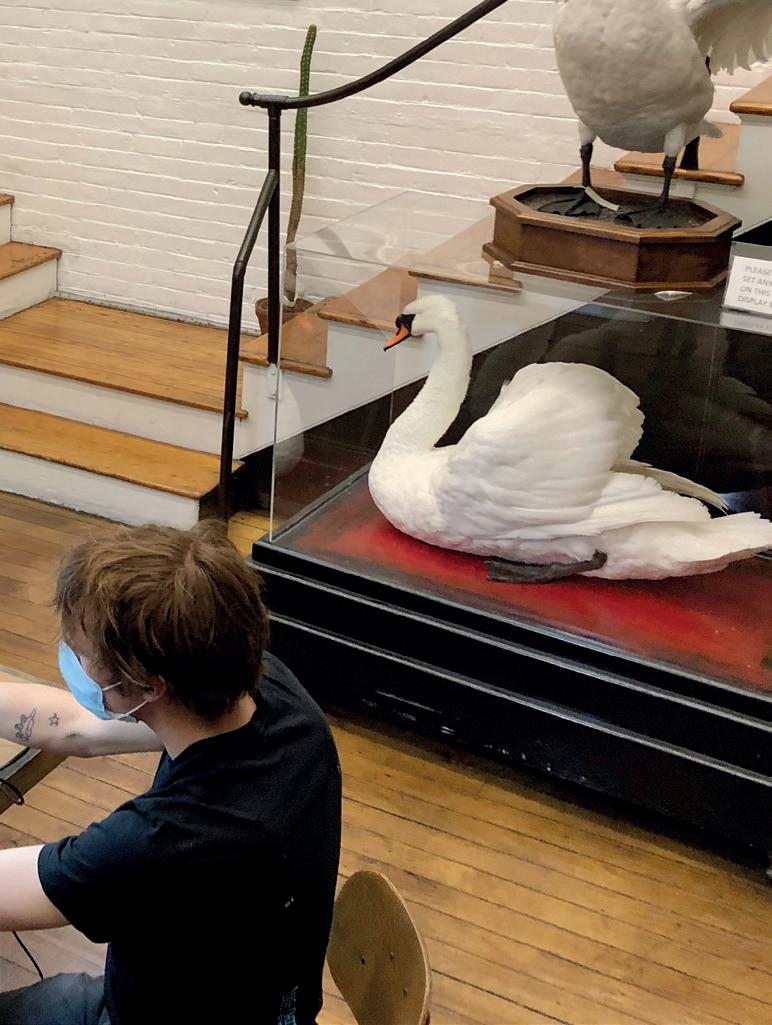
1 minute read
OF ARTEC 3D
from TCT Europe 31.1
by TCT Magazine
For damaged parts or products, applying the 3D-scan-and-print method means you only need to reproduce the damaged area rather than replace the entire part and waste the functional parts of it. This process is much more sustainable than traditional methods which involve conveyors, an overproduction of spare parts, and unnecessary waste due to trimmings or material excess. This enables completely new workflows that are economically and environmentally sustainable. Another application is quality control. 3D scanning provides a faster, more accurate method of ensuring products are up to par throughout every stage of the manufacturing process. Accurately identifying imperfections via 3D scanning early on saves time and costs further along the processing supply chain.
TCT: With that in mind, you recently introduced the Artec 3D Metrology Kit, which is being shown in some huge, heavy industry projects. Where’s the sweet spot for this technology?
AY: Our Metrology Kit is essentially a hightech measuring system for high-precision industrial applications. The applications include anything from deformation analysis to testing to inspection. The Kit is flexible enough to integrate into a user’s workflow, delivers perfect results both in you’re a workshop and outdoors, and is compatible with major software like Control X and PolyWorks.
It can operate as a standalone optical measurement solution, or as a referencing tool for even higher 3D scanning accuracy over distance. Using the Metrology Kit plugin, you get the entire 3D scanning and photogrammetry workflow right inside Artec Studio. This is an excellent solution for scanning large objects – say, a helicopter or a car – when you need to accelerate the process without sacrificing quality or precision. That’s really the sweet spot for this technology: as a complementary tool for the Leo or other scanners, helping users make digital twins of big objects much faster than either tool alone.
TCT: Where does 3D scanning go next?
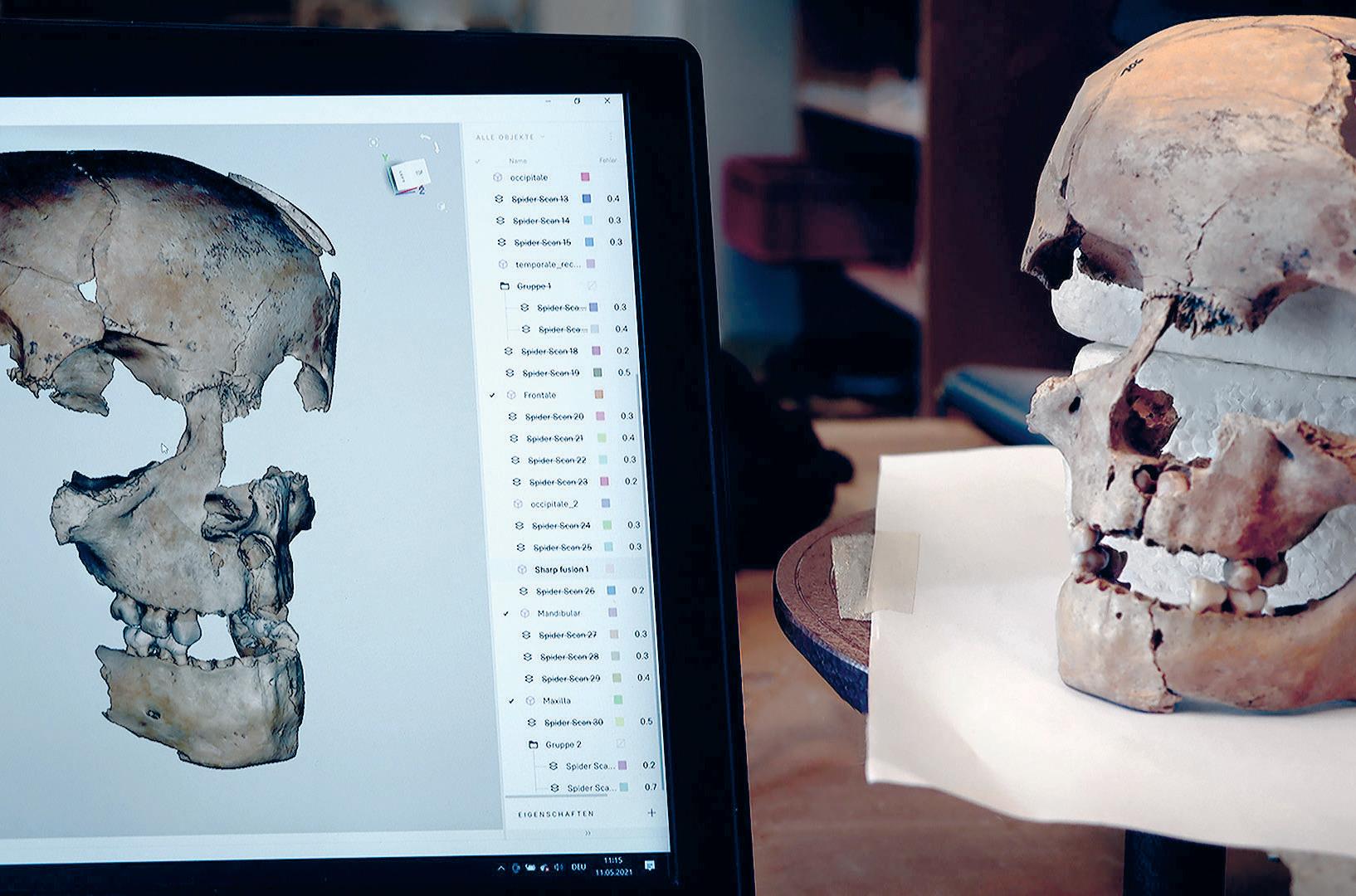
AY: One area we see the industry leaning more into is artificial intelligence. Applying AI is key in processing and interpreting the data a scanner collects, and Artec is fortunate to have had a very strong AI team from the beginning. We helped Apple to create their proprietary Face ID technology, so we’ve been on the turning point of AI technology from the get-go.
Artec 3D is committed to making its technology ever-more pervasive in fields that can benefit from reliable, easyto-use, yet still ultra-precise scanning. We collaborate with organisations that use our scanners to help people – whether that be in the form of lifechanging prosthetics, crime reduction and prevention, or accessible education. We look forward to continuing this work and seeing how 3D scanning continues to open up endless opportunities in the realms of science, history, medicine, archaeology, and sustainability.

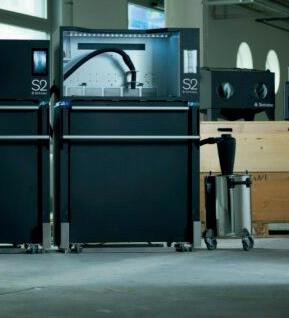
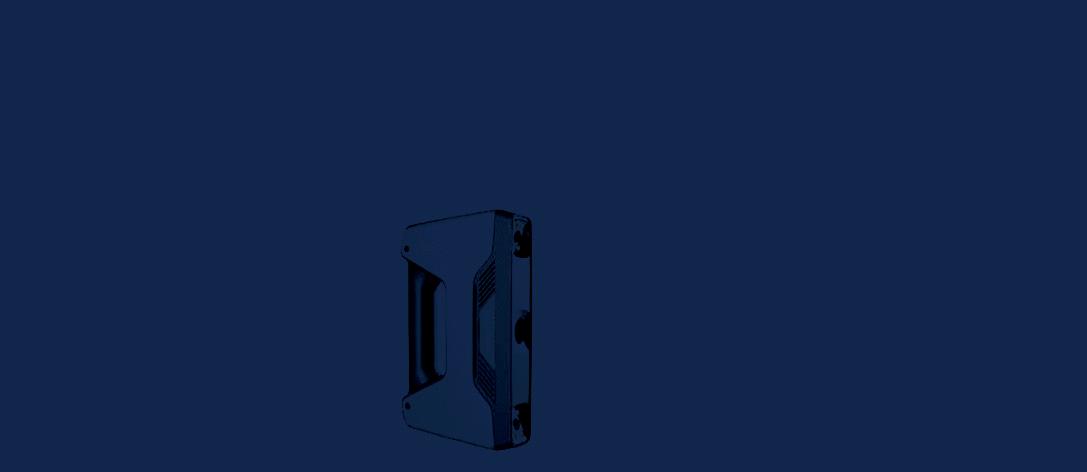
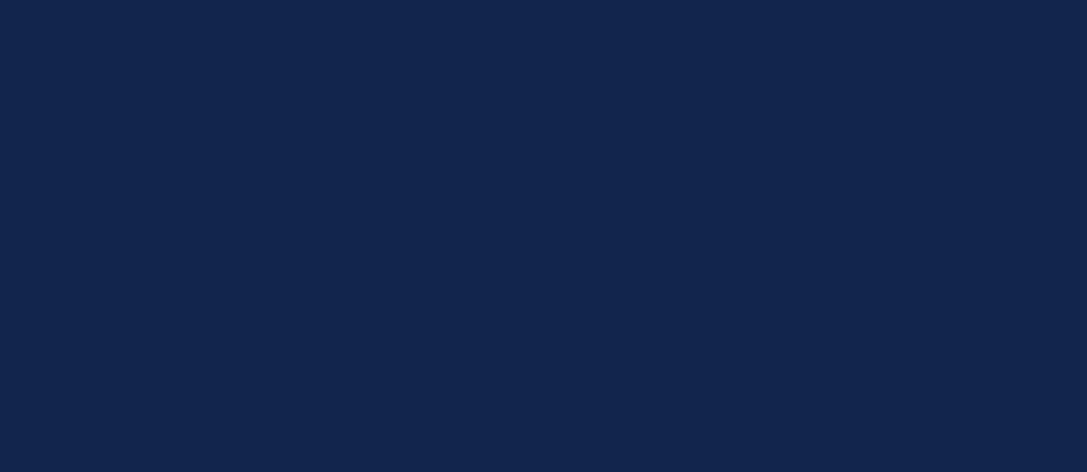
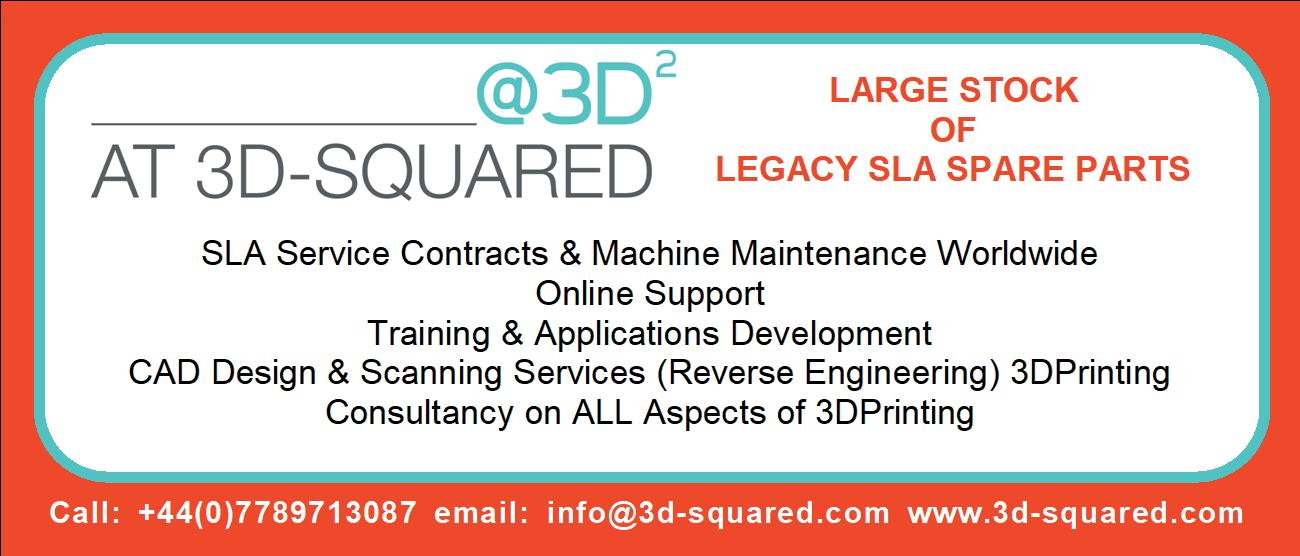
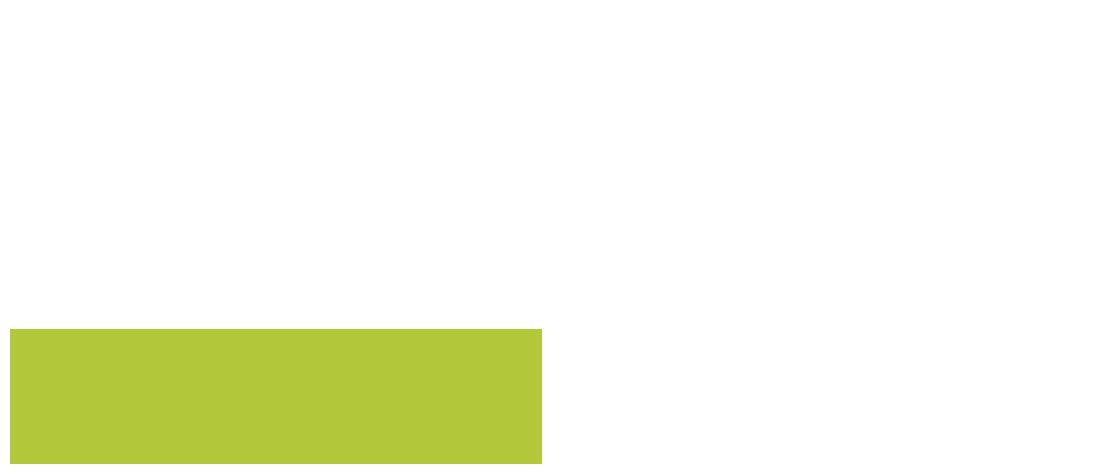