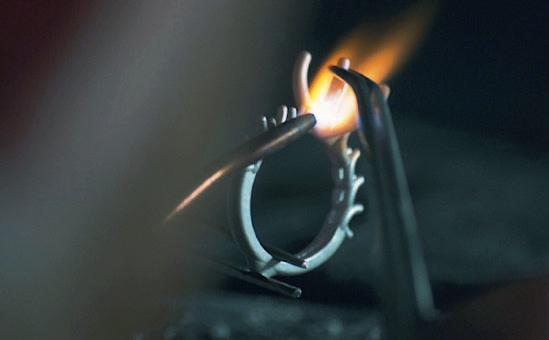
1 minute read
WORTH ITS
from TCT Europe 31.1
by TCT Magazine
How Diamond Centre Wales is incorporating 3D printing into its jewellery manufacture operations.
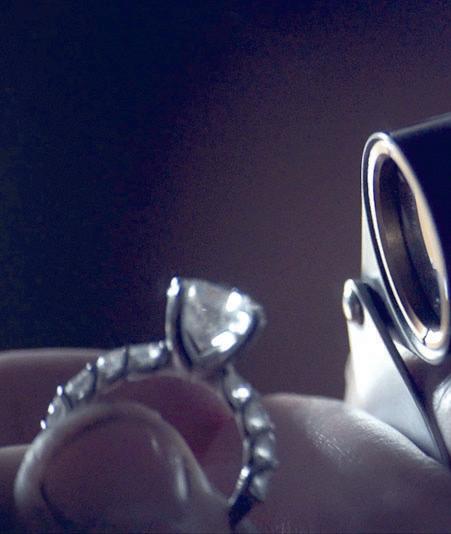
Halfway through an undergraduate degree at the Birmingham School of Jewellery, a future additive manufacturing lead at Cooksongold and an associate of Innovate UK’s Knowledge Transfer Partnership (KTP) programme, comes to a realisation.
“I was a terrible jeweller and I needed to do it all in CAD and print it,” Maria Paparozzi-Shipman modestly tells TCT.
From that point until the end of her degree, Paparozzi-Shipman proceeded to make her collections without touching a single piece of jewellery: Designed in CAD, the pieces would then be printed, polished through a third party, and stones set by someone else.
“I’m a bit of a magpie and then the science comes afterwards,” PaparozziShipman says of her penchant for jewellery aesthetics, and less so the technical aspects of jewellery manufacture. “It’s like, ‘let’s create the Mona Lisa.’ – ‘Okay, well how are we going to do it?’ It’s more about the design aesthetic for me and then the engineering comes in afterwards, and we’ll solve the problems in how to get there.”
This has been her vocation ever since – first at Cooksongold, and now Diamond Centre Wales (DCW), as she implements 3D printing technology within the bespoke jewellery manufacturer through an initial 24-month contract.
“We want to create a really immersive way of designing jewellery that’s completely bespoke,” she tells TCT of her aims at DCW. “It can be made quite simply, we know how sustainable the manufacturing is, we can do it all in house, and we have a massive team of traditional jewellers behind us that then make sure it has the integrity of a traditional piece of jewellery.”