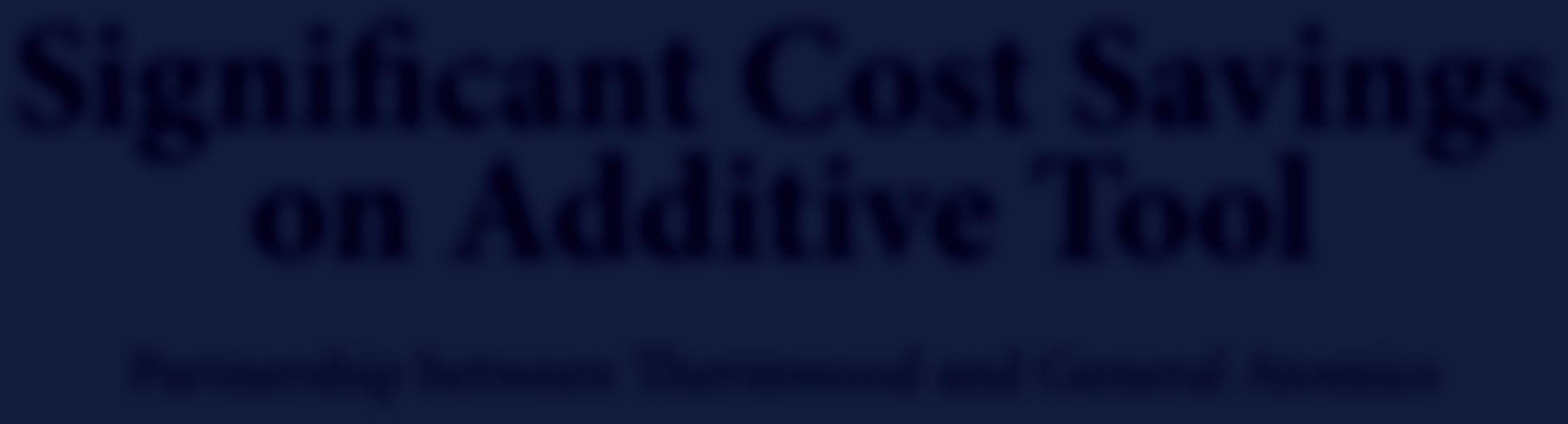
20 minute read
SUPPLY ON DEMAND
Laura Griffiths and Sam Davies explore the impact of AM on supply chain.
Since 2020, the theme of supply chain has dominated additive manufacturing (AM). In turn, we’ve dedicated many column inches and conference sessions to the technology’s deployment as a solution to pandemic-related challenges, and the longer-term implications of its apparent heightened adoption. Two years later, it’s still top of mind, and with emerging use cases, data, and government involvement, it’s not showing any signs of disappearing.
At this year’s TCT 3Sixty conference, a panel of experts including the University of Bristol’s Jennifer Johns, Boston Consulting Group’s Wilderich Heising, and Equinor’s Pantea Khanshaghaghi, discussed the “transformation” that’s happening around AM in supply chain. While it was suggested that AM applications during the pandemic showed “the beginnings of a utopian ideal” where AM steps in to solve our supply chain woes, the common narrative across industry, academia, and end-users, was the cruciality of knowing when and how to implement the technology, and extending that knowledge to the right people.
“Trying to do this top down and saying, here's my catalogue of 150,000 SKUs, let's go out and start making things using 3D printing – that will break people,” Len Pannett, Supply Chain and Operations Transformation expert and author of ‘Supercharg3d: How 3D Printing Will Drive Your Supply Chain’, told TCT. “The other part, of course, is that if you try to do it that way, the rest of the value chain won't be ready. To use an additive approach needs a different way of doing procurement, it needs a different way of doing contracting. In some cases, it needs qualification of those suppliers, as much as you would any other supplier. You also need to convince the engineering teams that the quality of what they're going to get is at least as good as going the traditional route.
“The tough nut to crack is not the engineering, it's the data side, it's how do you identify which of your 150,000 SKUs makes sense to go down this route? And that requires much more than just doing physical assessments and the assessment of physical characteristics. It means also looking at the supply chain characteristics.”
Pannett offers Deutsche Bahn up as an example of a company that has successfully demonstrated “the art of what’s possible” for AM in supply chain. Perhaps one of the most well-known adopters of AM for spare parts production, the company relies on a mix of in-house 3D printing capabilities and service providers, primarily, to produce polymer and metal components for the railway sector, from rail stops to hand-rail signs featuring braille. Cosmetics giant L’Oreal is another, and is currently using HP’s Multi Jet Fusion (MJF) to create adjustable components for its packaging production line with plans to further leverage the technology via HP’s Global Production Network to “build a truly global supply chain” that will enable more localised manufacture.
“The use of additive manufacturing, notably in a hybrid configuration with other technologies, allows us to react extremely quickly to supply chain fluctuations,” Matthew Forrester, Head of Transformation & Recycling Science at L’Oreal, told TCT. “Empowered teams, deploying their intimate knowledge of manufacturing processes, integrating the specificity of our goods, and even iterating during production, is the perfect combination to create best-inclass, agile tooling.”
FITTING IN
While examples like this from major brands and manufacturers show promise, just how much is
AM really being talked about with regards to
AZOTH 3D USE CASE: TAKE ONE MAKE ONE
Manufacturing service provider Azoth is utilizing 3D printing technologies to support its Take One Make One (TOMO) digital inventory strategy. Through TOMO, Azoth empowers its users to convert physical inventory to digital inventory and produce parts as needed without a minimum order quantity to justify up-front tooling or setup costs. When X number of parts are taken out of inventory, the same amount are made to replace them. Azoth considers this to be the leanest supply chain possible.
The company has proved out this concept by deploying Desktop Metal’s binder jet Shop System to additively manufacture bolt placement grippers that are installed onto a robot arm to pick and place bolts on an assembly line. Using the Shop System, Azoth is able to produce 1,400 of these end-use parts per day in 17-4PH. 3D printing is deployed because of the components’ intricate teeth design.
“These grippers are the perfect TOMO example,” commented Cody Cochran, co-founder and General Manager of Azoth. “They are more cost effective with binder jetting and can be delivered with a ten-day turnaround vs an eightweek lead time.”
supply chain outside of the AM bubble? According to Mark Cotteleer, Managing Director - Supply Chain and Operations Consulting Deloitte, “a lot.”
“We are seeing across our client base both in the public sector and in the private sector, I would say, an upsurge in discussion,” Cotteleer told TCT. “And that has a lot to do with the fact that additive manufacturing is, in my opinion, the quintessential example of digitally distributed manufacturing. What that means is that it brings together all the interesting attributes of digital distributed manufacturing; the ability to engage in the model-based enterprise, the ability to work across the supply base and distribute production to the point of demand at the time of demand, to bring in ideas around things like digital thread and digital twin, which are very hot topics. Additive is not the only solution. There are lots of solutions and we recommend that our clients take a portfolio approach to it.”
It's true, additive is not the only solution, and sometimes, it’s not the right one either. It’s about finding that sweet spot, developing a business case, and as our TCT 3Sixty panellists agreed, choosing when to apply it, whether that’s on a permanent basis or as an emergency stop gap in times of crisis. The latter, a more temporary outlook, might sound like a negative for an industry that appears to be confidently going after supply chain, but for Cotteleer, that’s actually its USP.
“To me, that's a feature not a bug,” Cotteleer explained. “In the sense that one of the core value propositions of additive is surging production at the point of demand, geographically and in time. Can we deliver production where we need it, when we need it?” He notes the work Deloitte carried out with America Makes during the pandemic on the Advanced Manufacturing Crisis Production Response (AM CPR) initiative which acted as a digital stockpile of designs that could be surged into production when and where the point of need materialized. It wasn’t just about COVID-related challenges either and the collaborators ran multiple scenarios – what happens if a supplier goes down or an earthquake hits, for example? – taking into account the many players across that supply chain, from designers to regulators and so on.
In September, Deloitte issued a report in partnership with the Manufacturers Alliance looking at how traditional manufacturing supply chains are evolving to balance costs, efficiency, and resilience. While the term ‘additive manufacturing’ is referenced just once in the 26-page document, in a chart showing the biggest impact on manufacturer’s supply chains, the top three responses - shipping delays (59%), part shortages (56%) and transportation delays (56%) - are key areas where the benefits of AM truly shine. Yet while additive’s value proposition as an enabler of distributed, on-demand manufacturing is evident, challenges remain.
“All of the old concerns still exist: quality, materials, cost, repeatability,” Cotteleer said. “I think what is changing is that, while the concern exists, many of the technical solutions are increasingly available so people need to be constantly revisiting the state of the art because things are changing quite rapidly. There are instances where we are seeing people quite effectively being able to distribute production, particularly at the lower end. At the higher end, with exotic materials and very expensive machines and very high-end uses, we still see, and in fact recommend, more centralized production models, but even there, you could still solve the time problem, you're just not solving the location problem.”
Interestingly, that singular nod to AM in Deloitte’s report ties into another industry trend: mergers and acquisitions. The report notes the strong M&A activity in manufacturing with 52% year-on-year growth in such deals in 2021,
STRATASYS USE CASE: CIRCUIT BOARD BRACKET
When Stratasys was first manufacturing its H350 Selective Absorption Fusion (SAF) 3D printers, the company ran into the same problem many other manufacturers did. A PCB Stepper Controller Board had originally been ordered from a supply chain vendor, but as COVID-19 hit, the product was discontinued.
The H350 Production Team then decided to utilize a new electronics board, which could be sourced easily, but required a mounting bracket to implement a necessary cooling function. For the solution, the team looked inward and bet on the technology they were working to bring to market. With the H350 machine, they designed and printed a circuit board bracket which could secure the fan to the electronics board and then safely mount the board within the printer.
The bracket, which doesn’t require any screws or tools, is said to occupy a minimal amount of space. Stratasys can nest 132 brackets within the same build with a cost per part of 4.15 USD. The company has implemented the circuit board bracket in every H350 3D printer and has continued to apply SAF technology to its SAF systems. “This was one of those examples that ‘ticked many of the boxes of additive manufacturing,’” Neil Hopkinson, VP of AM Technology at Stratasys, told TCT. “The challenge arose from supply chain issues, which are becoming more frequent in manufacturing these days and the solution came from AM technology that actually allowed the team to develop an improved product with easier assembly. In this instance, it was very gratifying that SAF technology itself was the solution for a SAF product development issue. The team has since built on this and each H350 printer has 30 parts produced by SAF technology.”
and suggests some instances of vertical integration can be seen as a tool for achieving supply chain resilience. For instance, earlier this year, aerospace and defence manufacturer Safran, which recently opened a new dedicated 3D printing campus, completed its acquisition of metal AM powder supplier Aubert & Duval, bringing its supply of metal powders inhouse. It’s an extreme example, and bringing AM into your supply chain doesn’t necessarily mean investing in an entire company or bringing in expensive hardware. Manufacturing service providers offer an alternative route to sourcing parts on-demand, and Pannett suggests finding a supplier to produce products with the right QA processes already in place as a “very easy, quick win.”
Joshua Parker, US 3D Printing Supply Chain Manager for Hubs, provides further insight into the benefits of additive. As an online manufacturing platform, Hubs provides engineers access to a network of 3D printing suppliers. The Amsterdam-based company was acquired by Protolabs in 2021, signaling further market consolidation in distributed manufacturing. The platform allows users to upload designs, instantly receive quotes and send their files for production via a network of AM, CNC machining, injection molding, and sheet metal fabrication partners. To date, the service has manufactured over 7 million parts. As part of its annual 3D Printing Trend Report, Hubs spotlighted more robust supply chains and localized on-demand manufacture as the most important AM trends for 2022.
“As additive becomes more of a low volume production solution, there has been increased interest with customers using technologies like SLS and HP’s MJF to either provide a short-term production solution or to switch to 3D printing altogether,” Parker told TCT. “We have seen a lot of success in the EV sector, especially with companies that are highly iterative and innovative and want to stay nimble with their design. With the increased lead times of going overseas for molds, 3D printing provides a quick alternative while tooling is being created.”
PRACTICE WHAT YOU PRINT If 3D printing is the silver bullet in supply chain resilience, are 3D printer manufacturers taking note?
AM FORWARD & SUPPLY CHAIN
THE AM INDUSTRY WEIGHS IN ON THE AM FORWARD INITIATIVE DESIGNED TO SUPPORT US-BASED SUPPLIERS’ ADOPTION OF AM CAPABILITIES.
DIDIER DELTORT | PRESIDENT, PERSONALIZATION AND 3D PRINTING | HP
“We believe the initiative is a bold step forward for additive manufacturing, particularly if it revitalizes the US supply chain by enabling more companies to take advantage of the intrinsic benefits of AM. Our hope is the program helps the many small and medium-sized businesses working to unlock new business opportunities and scale sustainable production with AM.”
LAUREN TUBESING | DIRECTOR OF OPERATIONS, MILITARY PROGRAMS | GE ADDITIVE
“Public-private initiatives like the recently announced ‘AM Forward’ initiative will help to address DoD’s sustainment and readiness challenges head on. Strengthening US supply chains by encouraging small and medium sized manufacturers across the United States to adopt metal additive technology will create a nationwide network of qualified additive manufacturing suppliers.”
ELLEN KULLMAN | CHAIR OF THE BOARD OF DIRECTORS | CARBON
“We're at an undeniable inflection point — bringing digital manufacturing to U.S. businesses will be a critical component to the success of the American economy both now and into the future. The administration's acknowledgment of 3D printing to boost the economy is a solid step forward and a proof point that digital manufacturing is critical in addressing our ongoing supply chain challenges and beyond.”
JOSH MARTIN | CO-FOUNDER | FORTIFY
“I think it's still early and I think a lot of people I work with are still wondering what that means. But I think, if anything, it could chart a path towards additive manufacturing playing a more significant role in supply chain resilience. And if there's anything that the last 36 months has taught us, it's that there's vulnerability there and additive can play a role.”
Signi cant Cost Savings on Additive Tool Signi cant Cost Savings on Additive Tool
Partnership between ermwood and General Atomics Partnership between ermwood and General Atomics
e Details
Using a ermwood LSAM 1020, the tool e Details was printed from ABS (20% Carbon Fiber Using a ermwood LSAM 1020, the tool Filled) in 16 hours. e nal part weighing was printed from ABS (20% Carbon Fiber 1,190 lbs was machined in 32 hours. Filled) in 16 hours. e nal part weighing 1,190 lbs was machined in 32 hours.
Cost Savings of around $50,000 vs traditional methods Cost Savings of around $50,000 vs traditional methods
Total lead time for the part decreased from 6-8 weeks to less than 2 weeks by utilizing Total lead time for the part decreased from the powerful LSAM system. 6-8 weeks to less than 2 weeks by utilizing the powerful LSAM system.
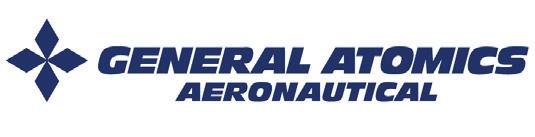
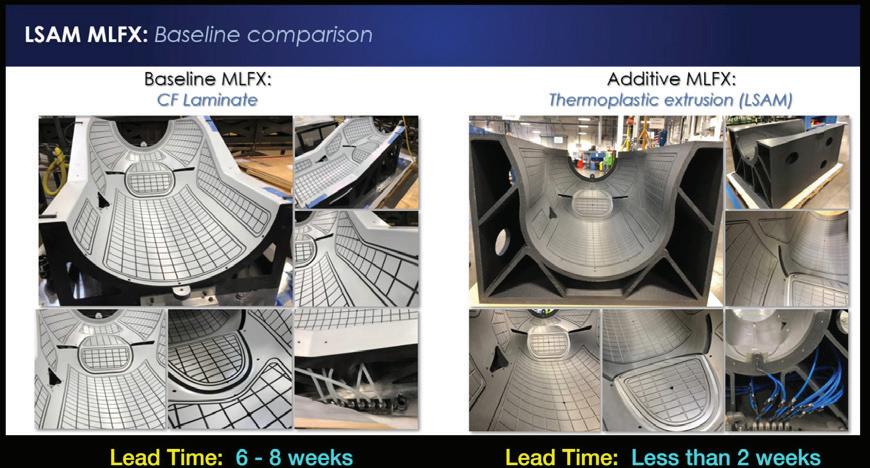
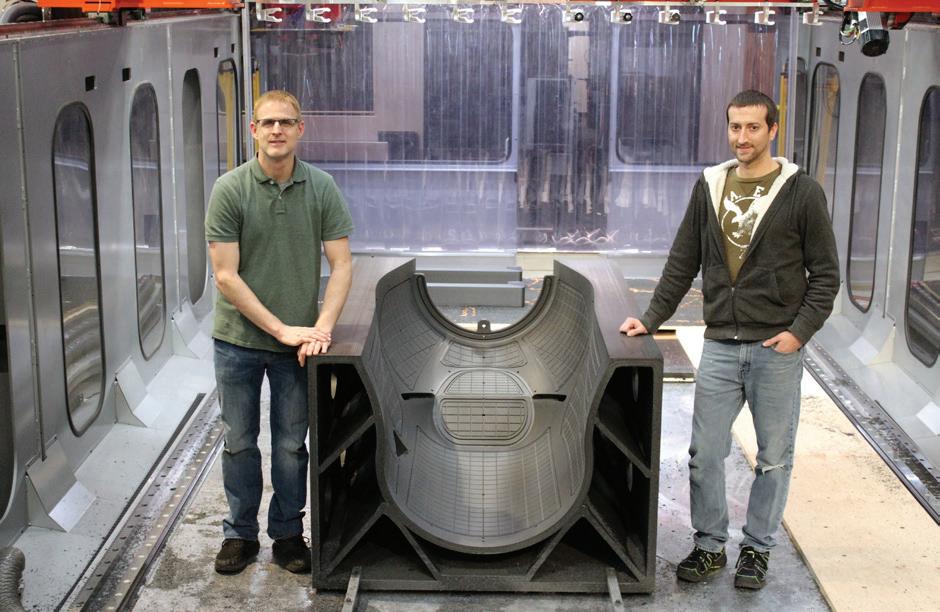
e Results
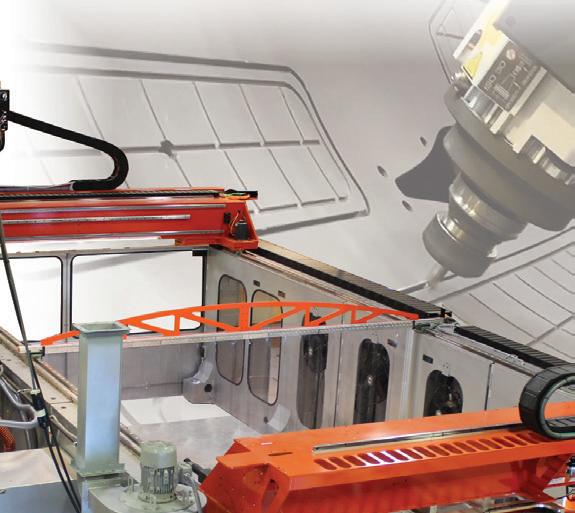
Scan QR code to view a video of the LSAM and Scan QR code to view a General Atomics process. video of the LSAM and General Atomics process. • Cost Reduction: 2-3 times e Results •Faster Development: 3-4 times• Cost Reduction: 2-3 times •Production Capable Tool • Faster Development: 3-4 times •Vacuum Integrity • Production Capable Tool •Suitable for Large, De• Vacuum Integrity ep 3D Geometries, Backup Structures • Suitable for Large, Deep 3D & Vacuum Piping Geometries, Backup Structures & Vacuum Piping
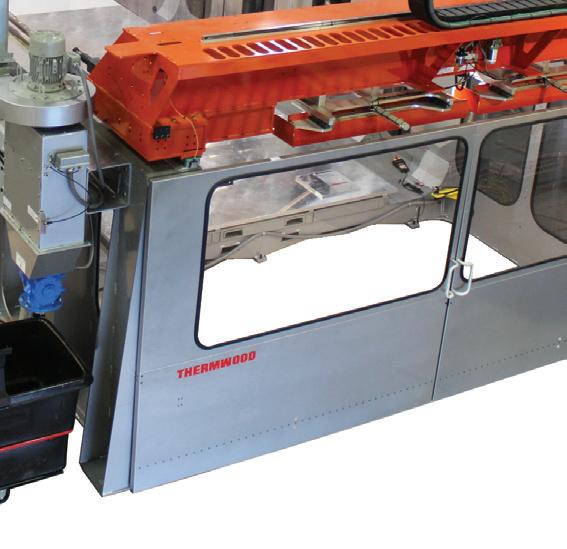

Megan Liu, Supply Chain Engineer at Formlabs, works within the global sourcing team, looking after supply chain for Formlabs products. In fact, several Formlabs machines feature a range of components manufactured with its own printers.
“We, I think, definitely understand that there is a good application for 3D printing in supply chains,” Liu said. “At the same time, most of our printer is not made out of a 3D printed material so there are definitely limitations on 3D printing parts for production. I think the best use cases are really small parts, in terms of geometry, things that nest well in our printers.
“I joined Formlabs because I am super interested in how we can use 3D printing in all different types of industries. It's super exciting for me to see Formlabs practising what we preach.”
The sourcing team’s job is essentially to find suppliers to make and deliver parts to its contract manufacturer on time. When Formlabs launched its Form Wash L and Form Cure L systems during the pandemic, for example, the team was able to mitigate supply chain issues and material delays by ramping up print production from its materials production facility in Ohio and Somerville HQ.
“Something that has been super exciting to see is, and I know this is kind of a buzzword, but we are able to decentralize our supply chain a little bit by using 3D printing,” Liu said. “If we are ever short on components or things like that, we can use a 3D printer right at the spot to print components to keep production going.”
In addition to a shift in customer applications, which now go beyond prototyping to tooling or production parts on the Fuse and Form 3L, and extend to even more industries, Liu says the last few years have also produced more awareness and interest in the technology.
“I think a lot of things probably have contributed to that extra interest,” Liu said. “I think the technology has improved and grown a lot over the last couple of years, but then also COVID with all the supply chain issues that brought was also definitely a wake-up call for a lot of people who are relying on traditional manufacturing methods.”
If the wake-up call was missed the first time around, the announcement this past Spring around the Biden Administration’s AM Forward initiative should ring a little louder. The initiative was setup to support the adoption of AM amongst SMEs, with large manufacturers like Siemens Energy, Honeywell, Lockheed Martin, GE Aviation and Raytheon, all longtime users of the technology, committing to purchasing additively
FAST RADIUS USE CASE:
STREAMLINING SPARE PARTS
As 3D printing continues to mature, and applying the technology for productiongrade parts becomes more of a reality, Husqvarna has aligned with Fast Radius to implement an advanced manufacturing approach.
The outdoor product manufacturer has worked with Fast Radius to identify parts that could be produced at scale with Carbon Digital Light Synthesis and HP Multi Jet Fusion technology, before establishing a Production Part Approval Process (PPAP) that included UV resistance, chemical resistance, and dayslong cycle tests, as well as an evaluation of real-world performance. Once parts pass the PPAP, designs and production specifications are stored digitally in the Fast Radius Virtual Warehouse, eliminating a lot of the supply chain costs associated with warehousing, minimum order quantities, material waste and part obsolescence.
From this virtual warehouse, parts can be downloaded, produced and shipped in a matter of days, while also affording Husqvarna and its customers the peace of mind that products will never be out of stock again. The reduction or elimination of material waste and part obsolescence is also supporting Husqvarna’s ‘Sustainovate’ sustainability programme, in which the company has outlined CO2 reduction targets for the year 2035.
“For Husqvarna, storing parts in the Virtual Warehouse has allowed them to avoid inventory holding cost, scrap at end of life, and has enabled better customer support by eliminating the need to discontinue production of certain spare part SKUs,” Matt Schroeder, Product Manager at Fast Radius, told TCT.
produced parts from smaller USbased suppliers, providing training, and engaging in common standards development and certification for additive products. It’s a bold move, and emphasizes the recognition of additive and distributed, localized manufacturing as tools to achieve supply chain resilience, something which Deloitte shares a confidence in.
Cotteleer said: “We are very bullish on the concept of distributed digital manufacturing and I think that it will continue to be important for supply chain and operations leaders to stay on top of, and develop strategies for how to deploy these technologies in support of cost, quality, resilience, flexibility, agility – fill in the buzzword – because this, to me, is the way the world is going, and if you're not incorporating these into your strategies, you're very likely falling behind.”
SPEAKING SUPPLY CHAIN From each of these conversations, it's increasingly clear that AM’s success in supply chain also relies on sharing these wins and having conversations with the people that can make change happen. Those already working in or using AM will be aware of the benefits of on-demand and decentralization, and Pannett argues AM companies should be putting themselves in front of supply chain professionals in order to see progress.
“I think the more that we can do to get the AM community in front of supply chain decision makers, the better,” Pannett said. “Those events where the supply chain guys are going to be exposed to new ideas, those are the ones that, I think, if we're going to really peak in our sales, have to be included in the roster.”
Having those conversations means being able speak the right language, to understand the needs of those operating along supply chains, and communicating where the benefits of AM, which may be lesser known outside of the industry, come into play.
“Words matter and I think this is a general challenge in the additive and advanced manufacturing space,” Cotteleer said. “And I'll point no further than the use of terms like digital thread and digital twin, which are crucial for the support of additive manufacturing. We often find ourselves at the beginning of a project or discussion, literally saying, ‘when we use these words,’ fill in the blank, ‘here's what we mean,’ because different people can ascribe different meanings to those words.”
Parker adds that it’s important to put that message across early in the procurement process: “A general lack of education and familiarity are the main reasons we see slow adoption. Our Sales and Engineering teams do a great job working with the customer to understand their needs and help companies steer their design towards the final manufacturing method. If you don’t consider 3D printing as a production method during design, it can be more difficult to change the manufacturing method later in the product design cycle.” That also means educating the right people, not just the engineers who will ultimately be using the technology but personnel along that value chain who need to understand the benefits in order to recognize where and why additive fits, or if it simply doesn’t.
“It's definitely a lot of engineering [people] right now, they're probably the most aware of this technology. [...] When we talk to people in supply chain, they're talking to us about printing spare parts and components and I think that definitely makes a lot of sense," Liu concluded, adding that there is an element of curbing expectations and a learning curve around what 3D printing can currently do in terms of spare parts. "That's, I think, where the knowledge gap starts to show a little bit because I think they're really hoping that 3D printing can solve all their problems in terms of aftermarket parts, spare parts, and things like that. I think maybe there needs to be a little bit more education in terms of the interim. Even though you potentially can't use 3D printing for this grand solution, there are definitely ways in which 3D printing can help aid in that transition, keeping all this excess stock to printing when you need.”