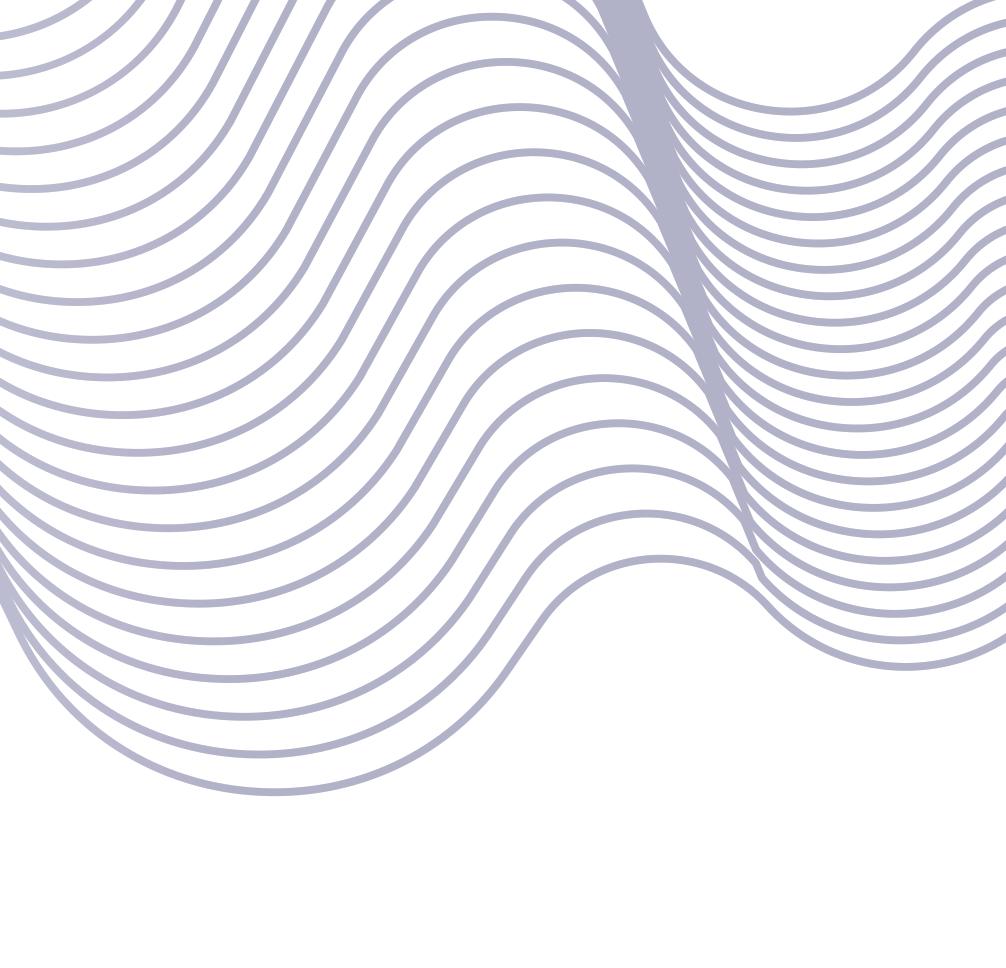
3 minute read
Paging Dr. O
Kip Hanson Contributing Editor
What he will share is that A) automotive is but a small piece of his customer base, B) for now, at least, KAM only prints metal parts, and C) most of what his team produces is bound for aerospace and defense applications.
When asked to explain how “machining 3D-printed metal parts is much different than traditional machining,” Keselowski ticked off several differentiators. First on the list is that virtually no CAD files come to KAM in print-ready condition. Engineers must design build supports and add material in strategic locations for fixturing reasons. Printed parts are typically at or near net shape, leaving little room for positioning error.
The parts also are quite expensive, even without machining and other post-print finishing processes. This means programmers and operators must take special care to avoid scrapping a part that might have taken days to build and be worth tens of thousands of dollars before the first cut.
KAM engineers might also need to work with a customer to make parts more printable, a task with which many in the AM community are familiar. And given that most components are flight critical, the materials used to make them are quite challenging. Inconel 939, Haynes 282, Ti64ELI—Keselowski’s staff routinely prints and machines these and similarly troublesome heat-resistant superalloys (HRSA).
Yet, complexity trumps all of these speed bumps. Keselowski noted that AM opens unprecedented doors to greater gas turbine and rocket engine performance. Because of this, additive parts not only boast extremely convoluted geometries but often contain critical flow paths and internal passageways, making them sensitive to FOD (foreign object debris) contamination that requires complicated mitigation strategies to avoid.
As with chasing the pole position on the Talladega Superspeedway, Keselowski aims to lead the additive pack. “Many people think that 3D printing is going to replace other types of manufacturing such as machining and casting,” he said. “We don’t see it that way. We’re making components with unique materials and unique geometries, while achieving higher levels of quality than is otherwise possible.
Olga Ivanova Master networker RAPID + TCT Director of Technology Mechnano
Olga Ivanova has 3D-printed plenty of interesting parts during her time in manufacturing.
Rocket nozzles. Turbine blades and impellers. Neonatal tracheostomy tubes. There are more, which we’ll get to in a moment, but to Star Wars fans, it’s the Static Dissipative Yoda that’s most intriguing.
“We printed a bunch of Yoda and Groot (Guardians of the Galaxy) figurines for high school students who visited our facility recently,” said Ivanova, director of technology at Mechnano, an additive manufacturing materials
“Of course, I’m fascinated by additive manufacturing and recognize its potential in the racing world, but what I’m most interested in from a KAM perspective is our role in developing future solutions that will make the world a better place,” he enthused. “For example, some of our parts are found in reusable rockets, which serve to launch critical telecommunications equipment that helps bring people around the planet closer together. We’re leveraging and promoting technology I’m honored to be associated with, and that will serve future generations for decades to come.”
“Some of that is due to part consolidation,” he continued. “We’re able to eliminate a lot of brazed joints, for instance, increasing part strength while reducing assembly costs. Machining these parts, however, is not easy.” developer near Phoenix. “It’s our way of getting young people interested in additive manufacturing.”
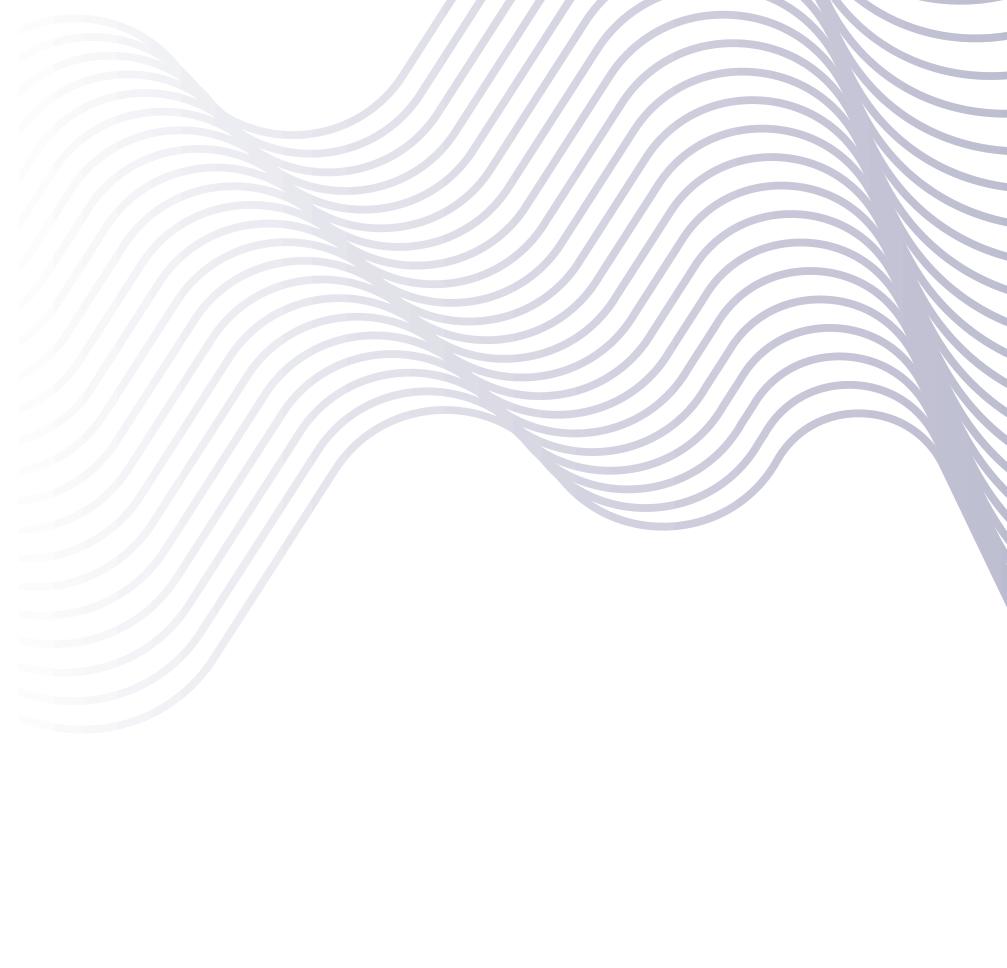
Waving the Green Flag
Padawan Learning
She’s quick to point out that those educational giveaways were made of a gray-colored base resin, not the more expensive static dissipative material (which is black) that she spends much of each day working with—and yes, which she occasionally uses to print Yodas that are just as resistant to electrical charge as they are to the Dark Side of the Force.
Another job falling into the not-too-easy bucket is gaining customer confidence. As with the ability to design print-ready parts that fully leverage AM’s immense capabilities, buyers and engineers are often playing technical catch-up and have reservations about its use. “They know that what they have right now works to some degree and they’re afraid to change,” Keselowski said. “Even if we offer them a solution that’s proven to be either more cost-effective or of higher quality, there’s still that apprehension. That’s probably our biggest external challenge.”