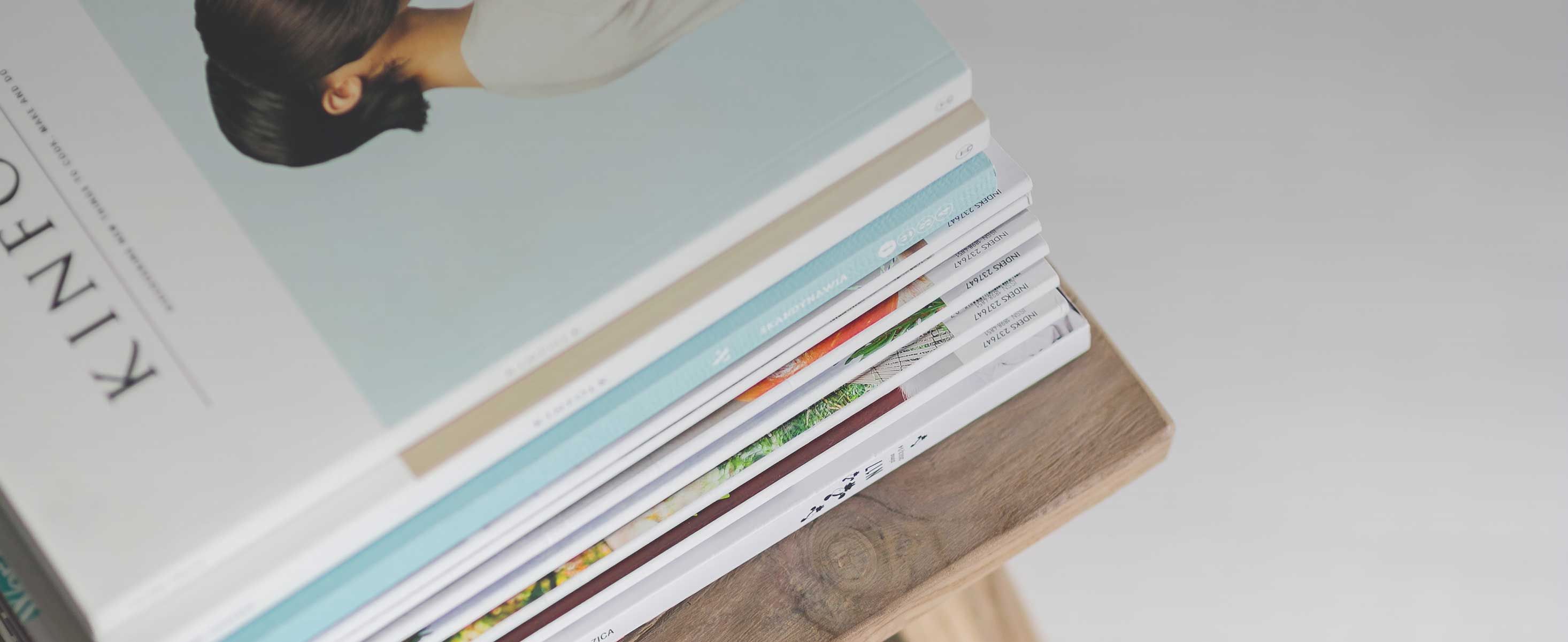
5 minute read
STACK THE ODDS
MedScan3D & Corrib Core Lab on an aortic root CTO surgical planning model developed with 3D printing.
At a desktop 3D printer, a 15-year-old loads a design from software to hardware, presses print, and turns in for the night. From nothing but digital data and a material feedstock, he will have a new Star Wars figurine ready to add to his collection by morning.
The capabilities of this technology aren’t lost on his cardiologist grandfather either. Dr. Patrick W Serruys, who manages the Corrib Core Lab, has been practicing since the 1970s but he too has embraced the capacity to materialise plastic models from digital input in a matter of hours.
Working with MedScan3D, a specialist in converting medical scans into STL files for the 3D printing of medical models, and Capbuster, the makers of a balloon catheter and guidewire combination device, Serruys has developed an aortic root chronic total occlusion (CTO) model with patient-specific coronary arteries. The model, printed as a single multi-material part, is designed to help surgeons prospectively and retroactively gain understandings on how to best approach the aortic CTO procedure.
“You’re not going to go into the patient without knowing what you’re going to do,” Serruys told TCT.
“You’re going to put all the odds on your side and have training, planning, and simulation before [operating].”
The model was developed using patient data from a CT scan, with the data being sent to MedScan3D for segmentation using its FDA-approved DICOM to Print software. This yields a rough digital model which is made suitable for 3D printing after post-processing in Autodesk Meshmixer and parametric design, in which a tank and conformal holder were engineered, with Siemens SolidEdge. Leaning on the Stratasys J826 Prime multi-material PolyJet 3D printer, MedScan3D then printed the model before distributing it to the Corrib Core Lab.
Before the model was printed, conversations between MedScan3D, Corrib Core Lab and Capbuster were had to determine which materials were most suitable to mimic which areas of the aortic valve model. Using their experience and the Hounsfield Unit to measure radio density, the partners selected a rigid polymer material for the sections of the model which represented calcified areas of the aorta valve, and softer elastomers for sections such as the vessel wall. With attention to detail of the utmost importance, the partners also took advantage of the CT scan data to ensure the arteries mimicked were specific to the patient.
With this model, the surgeon would then use the semi-transparent model to simulate actions made in the surgery.
“What we will do,” Serruys explained, “is cannulate the ostium of the coronary artery with the guiding catheter. The second step is going to advance the small catheter which has a small balloon and when we get in contact with the cap, we will inflate the balloon [and] we will see if the balloon is nicely anchored. If it is nicely anchored, the next point will be to advance the rigid wire, which is anchored in an helicoidal system and you rotate a quarter of a millimeter, advancing very slowly. There is no problem of flow because it’s totally occluded so the patient doesn’t feel anything. All these steps will be repeated and at each step you can learn ‘don’t do this, but do that.’”
To develop the aortic root CTO model, it required a two-hour segmentation process and a two-hour printing process. Timings that would be palatable for most surgeons preparing for most surgeries, with the overnight additive production of models identified as an opportunity by Serruys.
Before the guidewire and balloon combination was introduced in the 1980s, the only therapeutic intervention for a total occlusion was bypass surgery. Now, the treatment of CTO might be about to take another step forward with 3D printing.
“Through close collaboration with healthcare professionals, engineers, and patients, we can create innovative solutions that address unmet medical needs and enhance people's lives,” said MedScan3D Technical Director Jacqui O’Connor. “We are enthusiastic about the possibilities that lie ahead.”
Why intelligent depowdering means an efficiency booster for postprocessing and the production process of AM parts
Recently, depowdering pioneer Solukon has launched the first depowdering software, the SPR-Pathfinder®. Learn in our short Q&A what makes this software an efficiency booster in postprocessing.
What motivated Solukon to launch the SPR-Pathfinder?
It’s always been Solukon’s ambition to automate and simplify powder removal. In 2018, Solukon CEO Andreas Hartmann discussed the potential for an algorithm-based depowdering mode with Dr. Christoph Kiener, Principal Key Expert on Functional Design for Manufacturing at Siemens Technology. We were sure that metal parts might get too complex to let humans do the programming of the depowdering motion pattern. Developed by Siemens Technology in a joint project with Solukon, the software was unveiled publicly for the first time in 2018 under the name SiDAM.
After a successful testing phase SiDAM turned out to be the game-changer for automated depowdering that we intended it to be. So, Solukon has acquired exclusive rights to the software, developed it into a Solukon product, and brought it to the AM market under the new name, SPR-Pathfinder®.
What are the fundamental capabilities of the product?
SPR-Pathfinder® software uses the build job’s CAD file to calculate the ideal motion in the Solukon system. The SPR-Pathfinder® calculations are based on a flow simulation that analyzes the part’s digital twin. The individually calculated motion sequence is then read by the Solukon system, which in turn runs the programmed paths.
The SPR-Pathfinder® can currently run on SFM-AT800-S and SFM-AT1000-S models.
What are the benefits of using SPR-Pathfinder in real-terms?
• The SPR-Pathfinder® is a fireand-forget software. So you basically load the CAD file in binary format into the software and it does the rest. So, there is no human programming or teaching of depowdering motion sequences required anymore.
• Significant time savingsNo time is needed for programming anymore and users have more time for more valuable working steps in the process.
• With the software you get an optimized degree of part cleanliness especially for components with intricate internal channels.
• The SPR-Pathfinder® paves the way to a true serial cleaning and therefore to serial production. Obviously, SPR-Pathfinder® executes the same cleaning program for the same kind of parts.
• SPR-Pathfinder® is able to calculate the motion sequence for the whole build job, i.e. even for different parts on one build plate simultaneously. This means another booster in efficiency for AM productions with a greater variance of components.
• As soon as the CAD file of the component is ready, SPRPathfinder® can calculate the depowdering motion patters. So, the depowdering can be arranged even when the printing of the part is still in progress. The software also ensures part cleanliness, so designers can freely design their components and do not need to consider any obstacles in depowdering.
Why is creating a digital twin for the post-processing of parts important?
Creating and working with a digital twin in postprocessing makes the process steps after printing predictable and scalable even if the parts are still in production. Before, SPR-
Pathfinder® was launched the digital twin was just usable in the printing process but not in any subsequent process steps. For a total digital manufacturing process, the postprocessing needs to be digital to a certain degree. The digital twin is one tool for that, alongside sensors and digital interfaces.
And how does the software integrate with the rest of the additive manufacturing workflow?
The software itself works not in the Solukon system but on a PC or laptop via any recent windows operating system, giving maximum flexibility.
Via OPC UA you can load and start the cleaning program, calculated by SPR-Pathfinder® in the Solukon system. Just like the Solukon systems themselves, the SPRPathfinder® is compatible with every 3D printing system and peripheral equipment on the market. www.solukon.de
