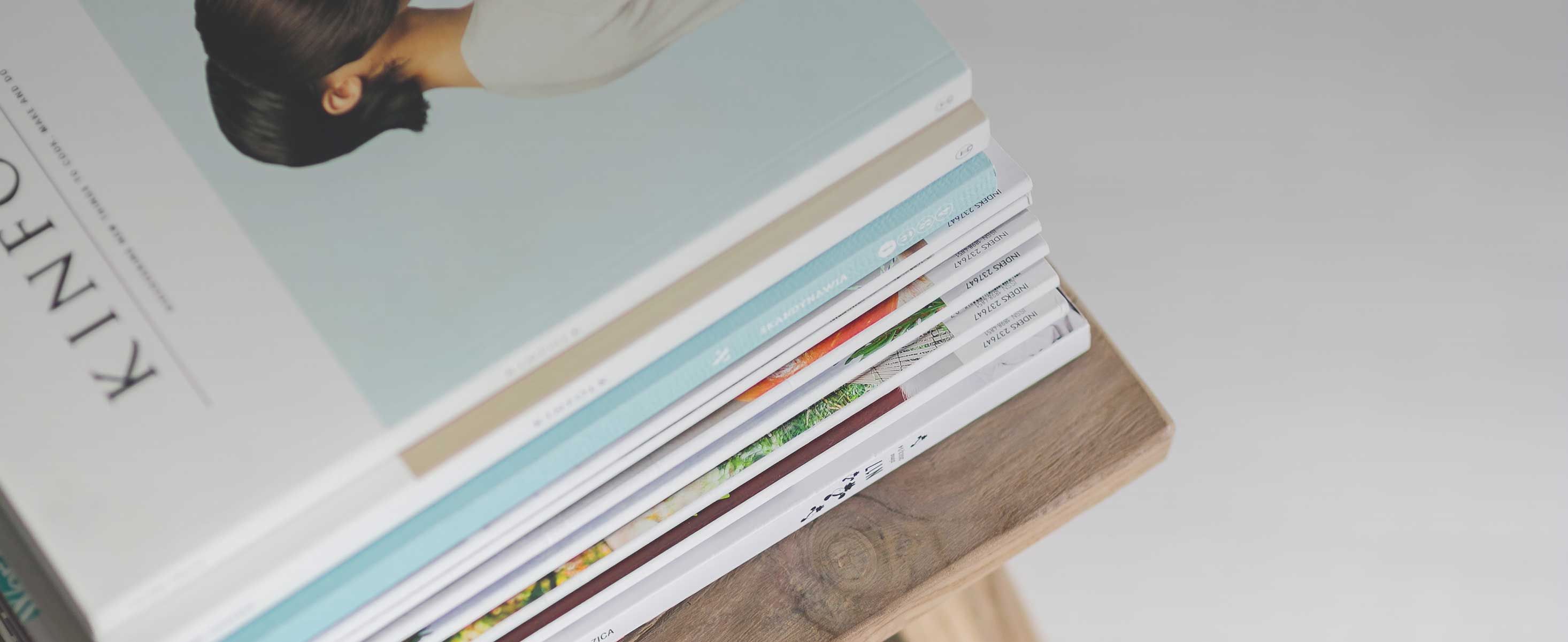
2 minute read
IT'S ELECTRIFYING
Oli
industry, where the process of polishing is done manually, but thanks to eBlast it can be done automatically.”
According to the company, the main benefits of DLyte eBlast are that a user can allocate the polishing wherever they want without masking. Sarsanedas explained that users could polish an insert coming from a big mold and focus the projection where they want, and that there are no limitations in weight and size. A robot system can be implemented, and big structures can be projected. Sarsanedas added: “The final result is smoother and with lower roughness than any other technology, and in only one step we are doing the whole job.”
GPA Innova, a Barcelonabased company, won the TCT Post-Processing Award with its DLyte eBlast technology in June 2022 at the TCT Awards in Birmingham, an event coinciding with TCT 3Sixty. The eBlast technology is based on projected electropolishing, and was created specifically for surface finishing of large, heavy metal parts, or parts with complex geometries which, according to the company, are typically difficult to polish by immersion or require a localized finishing, such as welded areas.
The DLyte eBlast works by projecting a non-conductive liquid and free solid polymer particles, which conducts the electric current between the electrode and the surface, to produce an electrochemical reaction. According to GPA Innova, the non-conductive liquid protects the surface from uncontrolled oxidation during the process, as the liquid replaces atmospheric oxygen during the electropolishing process.
Sarsanedas told TCT: “In the beginning, it was difficult to apply it because we are using a solution that is purely dry, where the particles are the only ones active in the system. This is the DryLyte technology. To project the media and not lose contact between each particle, you need to add a conductive liquid during that process to be sure that each particle is interconnected. But we don’t like conductive liquid because when you add it, you create oxidations, you create super reactions, which is a typical problem of electropolishing technologies. Then in eBlast, we needed to add a conductive liquid only when we project. When the liquid is projected, it immediately becomes non-conductive, it’s an emulsion. It’s very interesting for polishing specific geometries that we are not able to load and unload in our standard machinery for the molding industry, or the welding
Another benefit is the range of materials that can be polished using the eBlast technology. Sarsanedas told TCT that the electrolyte composition is what allows this, as it makes it a flexible solution, and that the eBlast is more a tool for polishing than a machine for polishing. The robot that is included in the eBlast process is necessary according to the CEO as it makes sure the gun is moving with the right speed and the right trajectory, and without the robot the parts would be overpolished.
Sarsanedas told TCT about 3D printing companies using the eBlast technology: “3D printing companies are interested because in 3D printing, sometimes it’s necessary to only polish some parts of the geometry, not all.”
Speaking about the future of the eBlast technology, Sarsanedas said: “We are developing a lot of different electrolytes because here we don’t use the same electrolytes as our standard machinery, we are testing a lot of different electrolytes. But the future is installations, big rooms for polishing where you can allocate big parts mainly for welding technology or stainless steel. When the installations are ready, it will be very easy for customers to approach that technology and to accept it. This means that we need to improve electrolytes and we need to develop more industrial solutions to be easier to implement.”
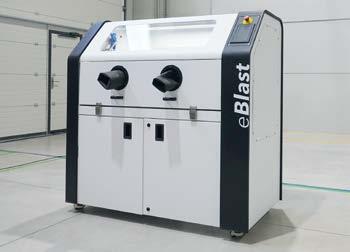