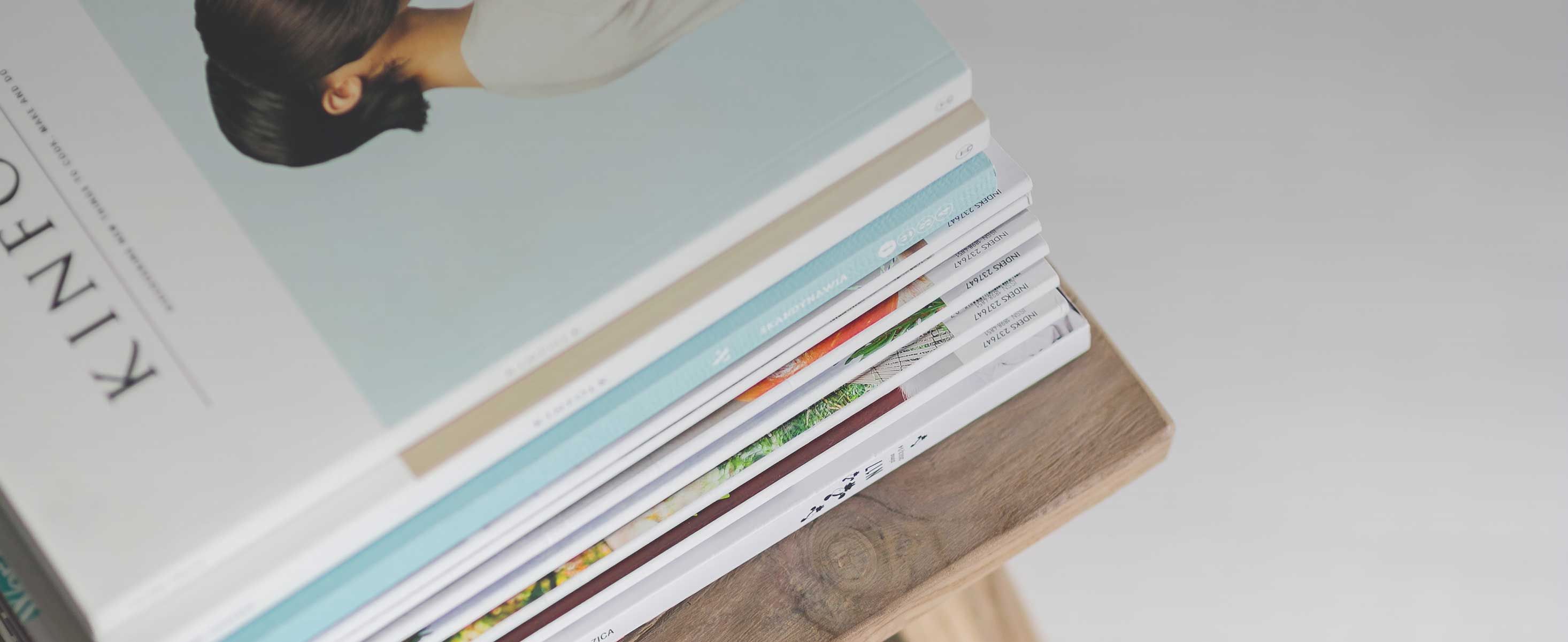
2 minute read
Paging Dr. O
Kip Hanson Contributing Editor
lga Ivanova has 3D-printed plenty of interesting parts during her time in manufacturing. Rocket nozzles. Turbine blades and impellers. Neonatal tracheostomy tubes. There are more, which we’ll get to in a moment, but to Star Wars fans, it’s the Static Dissipative Yoda that’s most intriguing.
“We printed a bunch of Yoda and Groot (Guardians of the Galaxy) figurines for high school students who visited our facility recently,” said Ivanova, director of technology at Mechnano, an additive manufacturing materials
OIn each of these positions, El Desouky “came in on the ground floor,” meaning his employer was just getting started on its 3D-printing journey, and looking for ways to turn the technology into a mainstream manufacturing process rather than a prototype-only development tool. He was at Eaton when the company printed its first flight-approved component in 2019, which “was a great achievement for the entire team,” according to El Desouky, and he assisted powder metallurgy specialist Carpenter in creating its Additive Manufacturing division.
El Desouky also has spent many years in academia, including positions as an adjunct professor and postdoctoral scientist at George Washington University, graduate researcher at University of California San Diego, lecturer at San Diego State University, and assistant professor at the Egypt-Japan University of Science and Technology (E-JUST). His areas of study focused on materials processing and additive manufacturing, making him well-equipped for his chosen profession.
Into the Clean Room
Bringing additive to a certain level of manufacturing maturity has turned out to be “kind of his thing,” and El Desouky is now working to give Veeco the same competitive edge he’s helped bring to others.
Along the way, he’s learned that the semiconductor industry presents unique opportunities and challenges for additive. “As you might imagine, cleanliness is a top priority, with requirements that are orders of magnitude higher even than those of the medical community,” he noted. “This is why, when you’re designing a component for semiconductor use, there’s more to it than making it printable, but designing it so that the part can be thoroughly cleaned afterward.”
Olga Ivanova Master networker RAPID + TCT Director of Technology Mechnano
developer near Phoenix. “It’s our way of getting young people interested in additive manufacturing.”
Padawan Learning
Additive’s immense design freedom is a wonderful thing, he explained, yet such considerations tend to detract somewhat from this freedom, since the tiniest speck of dirt or an errant bit of powder can have serious repercussions when you’re producing capital equipment that will go into a clean room. “The biggest fear is having a micron or sub-micron-sized particle stuck to a component’s inner wall that breaks free six months into service,” El Desouky said. “That would be a killer, so we take all the necessary measures to ensure this never happens.”
She’s quick to point out that those educational giveaways were made of a gray-colored base resin, not the more expensive static dissipative material (which is black) that she spends much of each day working with—and yes, which she occasionally uses to print Yodas that are just as resistant to electrical charge as they are to the Dark Side of the Force.
Contamination concerns aside, Veeco enjoys the same benefits as other AM practitioners. Part consolidation, supply chain simplification, reduced design and production costs, along with faster time to market—these are just a few of the reasons why metal and polymer printing are consuming an ever larger slice of today’s manufacturing pie.
And while El Desouky can’t share exactly which components are emerging from the build chambers of Veeco’s partners’ laser powder-bed fusion (LPBF), directed-energy deposition (DED), and stereolithography (SL) printers, he will say that semiconductor processing equipment requires all manner of manifolds, gas delivery and mixing systems, cooling plates, housings, valves, and bellows.
“Additive and semiconductors are a perfect match,” asserted El Desouky. “That’s especially true for equipment manufacturers like Veeco, which has a high mix, low volume of parts, and is happy to customize its offering based on the customer’s specific needs.”