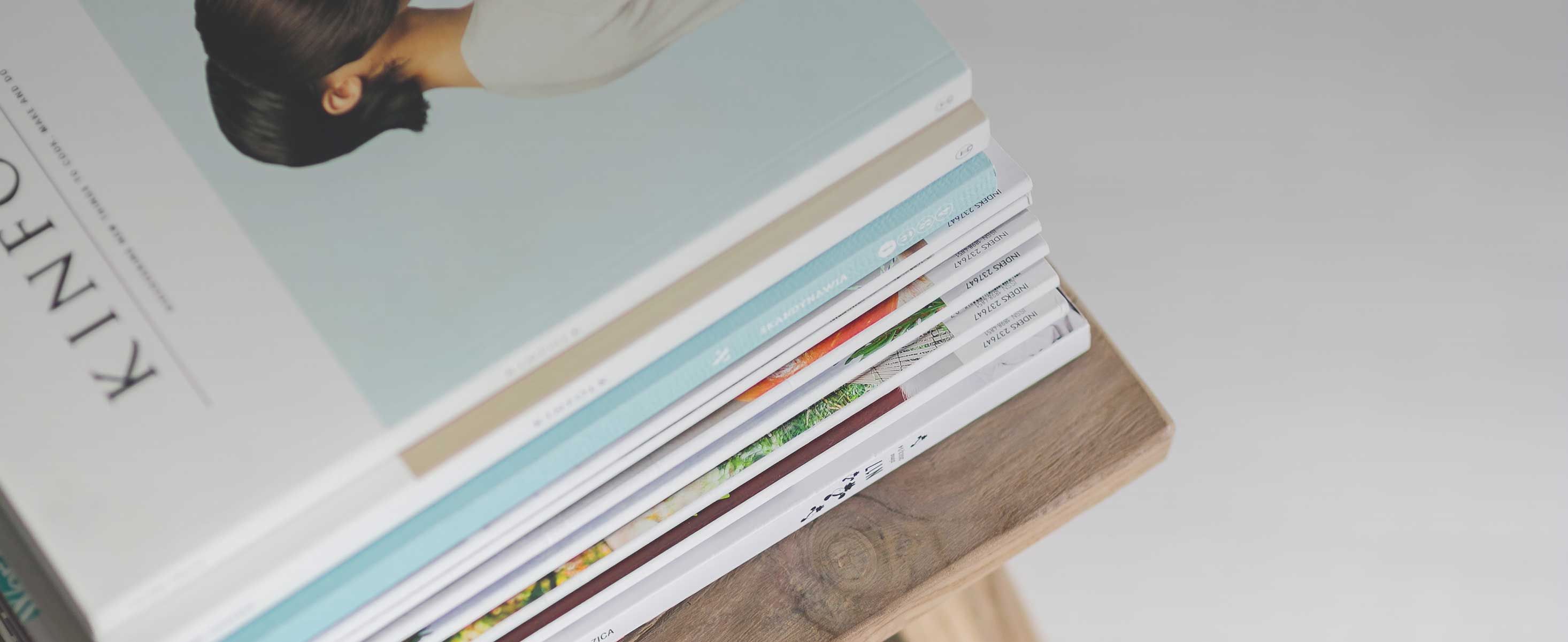
2 minute read
TANIOBIS
Based on our 60 years expertise in manufacturing and development of refractory metals, we have developed AMtrinsic® atomized tantalum and niobium spherical powders and their alloys for demanding additive manufacturing technologies. Our ability to adjust specific intrinsic material properties enables us to push the limits according to the requirements of your application.
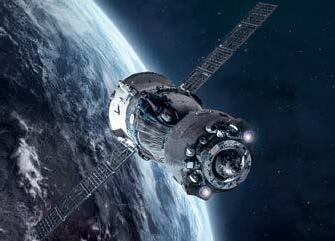
AMtrinsic® spherical tantalum and niobium powders provide outstanding combinations of material properties customized for specific applications. Aligned with 3D-printing technology, AMtrinsic® powders can help overcome hurdles in various high-tech industries. The high temperature stability, excellent corrosion resistance and biocompatibility of AMtrinsic® Ta, Nb powders and their alloys deliver a perfect fit for biomedical (Ta, TNT and TNTZ), chemical (Ta, Nb, Ta-W) and aerospace (Ta-W, C103 and FS-85) applications. In addition, AMtrinsic® Nb with its prominent superconducting properties is ideal for the superconducting industry.
TANIOBIS has recently expanded its AMtrinsic® portfolio adding C103 (Nb-10Hf-1Ti) and FS-85 (Nb-28Ta10W- 1Zr) pre-alloyed powders. High-temperature strength, superior creep properties and their excellent workability with Additive Manufacturing make these alloys great candidates as structural material for various aerospace applications. AM offers design freedom enabling manufacturing of lightweight components with complex features e.g. rocket thruster with integrated cooling channels which is one of the applications of our AMtrinsic® C103 and FS-85 alloys.
DR
PHIL REEVES | Managing Director | Reeves Insight
"When building a business case for AM adoption, the most important thing you need to have is a metric. More than one metric is even better. Having something to measure AM against is the most crucial part of any business case-building activity. For example, that metric could be cost reduction, weight reduction, increased flow rate, reduced operating pressure, or reduced part count. The critical consideration is understanding how the metric impacts business performance and customer value. Does a lighter-weight part cost the customer more to purchase but save money to operate? Does reducing part count through design for AM save money in production but drive up the spare part cost? The other parallel consideration should always be whether this is still the best manufacturing process for this component or whether we should look towards traditional manufacturing processes and supply chains."
ANDY MIDDLETON | Vice President | XJet
Firstly, we must understand the motivation behind bringing in AM. Assuming the aim is not ‘to be a visionary’ with no real business need, most companies we speak to are looking for flexible production –to produce thousands of parts as opposed to the hundreds of thousands of parts generally produced by ceramic manufacturers. AM solves that problem, without the cost of the intensive, labor-heavy processes used by the ceramic industry today. To make the business case, companies must show that AM can meet, or surpass, the quality of parts made by the incumbent technology. For successful adoption, manufacturers absolutely will not compromise on quality. In ceramics, this is often about material properties, such as performance at high temperatures, chemical resistance and electrical insulation. In addition, the process must be as automated as possible. To compete with the standardized methods manufacturers have been using for decades, AM cannot use labor-intensive post-processing, it must be competitive."