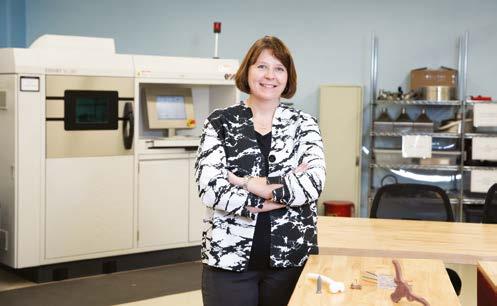
1 minute read
Printing Longhorns Paging Dr. O
Kip Hanson
Kip Hanson Contributing Editor
espite widespread and growing popularity, it’s important to realize that additive manufacturing (AM) is still a young technology—and that most of its potential remains untapped. Carolyn Seepersad spends her days exploring such possibilities.
DOlga Ivanova has 3D-printed plenty of interesting parts during her time in manufacturing.
Rocket nozzles. Turbine blades and impellers. Neonatal tracheostomy tubes. There are more, which we’ll get to in a moment, but to Star Wars fans, it’s the Static Dissipative Yoda that’s most intriguing.
“We printed a bunch of Yoda and Groot (Guardians of the Galaxy) figurines for high school students who visited our facility recently,” said Ivanova, director of technology at Mechnano, an additive manufacturing materials developer near Phoenix. “It’s our way of getting young people interested in additive manufacturing.”
A mechanical engineering professor at The University of Texas (UT) at Austin, Seepersad is taking this decades-old technology in novel directions while attempting to solve some of its thorniest problems. Reactive extrusion. Volumetric powder-bed fusion. Large-scale, high-velocity stereolithography.
These are just a few of the AM technologies that Seepersad, her students, and fellow faculty members are developing at the university’s Cockrell School of Engineering.
Padawan Learning
She’s in good company. One of her mentors and colleagues is Joe Beaman, the 3D-printing pioneer who coined the term “solid free-form fabrication,” and, with student Carl Deckard, developed selective laser sintering during the mid-1980s.
She’s quick to point out that those educational giveaways were made of a gray-colored base resin, not the more expensive static dissipative material (which is black) that she spends much of each day working with—and yes, which she occasionally uses to print Yodas that are just as resistant to electrical charge as they are to
“We have a long history of additive manufacturing at UT Austin and continue to do extensive research into the printing of polymers, metals, and ceramics,” she said.
REAM Team
Blazing her own AM trails, Seepersad is mostly focused on endowing materials with unique properties that can only be achieved through 3D printing. But she’s also active in developing new technologies. For instance, she and her colleague Mehran Tehrani are working with their graduate students on reactive-extrusion additive manufacturing, or REAM.