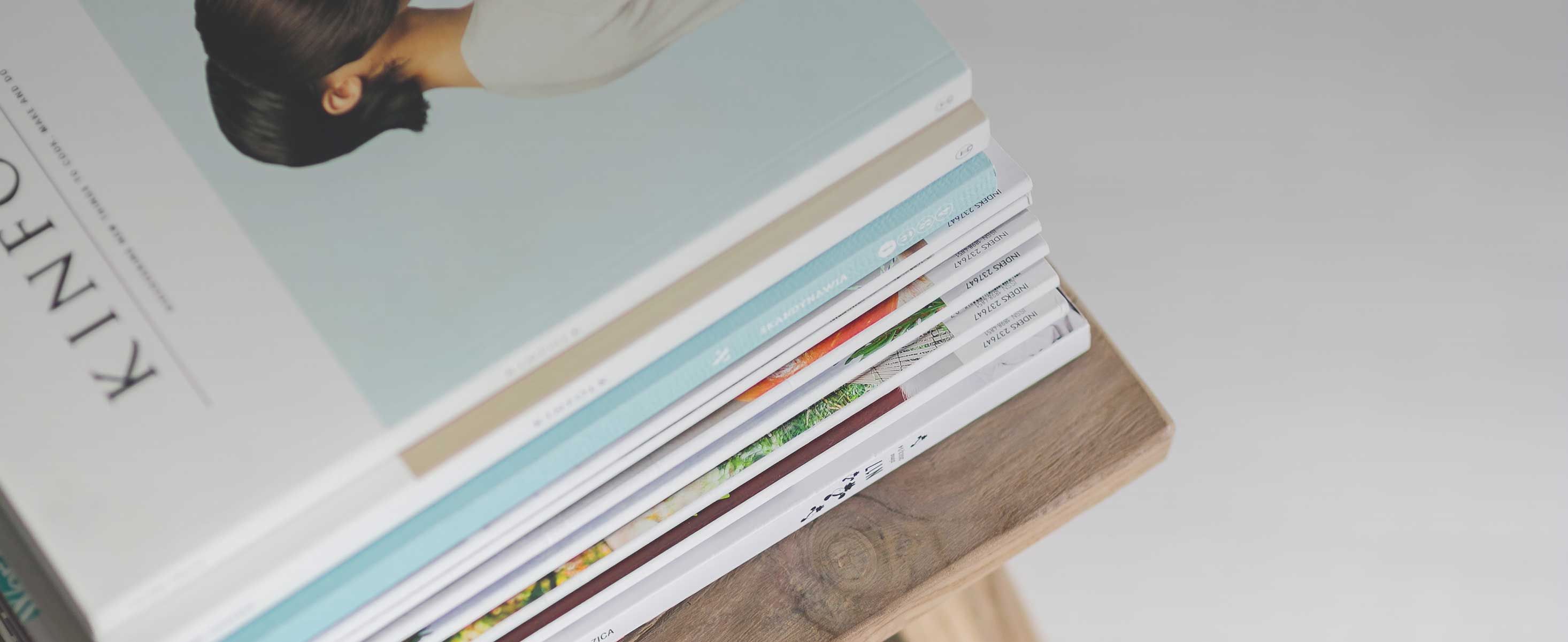
6 minute read
AM Community Shows Off at RAPID + TCT
Mechanically similar to fused deposition modeling (FDM), the process uses a two-part thermoset polymer (like some commercial epoxies) that is mixed on demand, then squirted onto a substrate or build plate. Any similarities to FDM end there, however, because REAM is about two orders of magnitude faster than desktop printers. For example, printing one of the school’s signature Longhorn-shaped test pieces— measuring 230 mm from horn to horn and 16 mm thick—took less than three minutes, compared to “hours” using traditional FDM methods and materials.
These include an LED/LCD curing and patterning system that delivers “lots of light” and a variable tensioning device that gently separates parts from a Teflon film sitting atop the build plate. The latter works much like “peeling away a Band-Aid,” she said, noting this was necessary to eliminate any chance of damaging delicate or elastomeric parts during the build process. The unique light system, on the other hand, circumvents an even more troublesome event: melting the LED/LCD light source.
Suzy Marzano Senior Manager Industry Development and Technical Activities SME
It’s official. Additive Manufacturing is thriving and continues to gain momentum with successes across diverse applications. In addition to ongoing technology advances, AM’s growth is fueled by a host of engaged companies, organizations, and dedicated professionals, all of whom are energized and passionate about developing, implementing—and sharing—new ideas and best practices throughout a collaborative community of innovators.
The recent RAPID + TCT conference, which was held May 17–19 in Detroit, is proof positive as to how far AM has come in recent years. The 31st edition of the industry’s marquee event featured more than 400 exhibitors, hundreds of speakers and expert panelists, dozens of technical sessions, networking opportunities, and attendees from 38 countries.
Even more impressive is the fact that the Longhorn and other REAM parts have much less anisotropic mechanical properties (varying in magnitude according to the direction of measurement), due to the inter-layer crosslinking of polymer chains. “We can also mix in additives—magnetic particles is one example, as is carbon fiber—that give the part additional strength or functionality,” Seepersad explained.
The AM community took center stage throughout the show. This includes the passing of the baton in two key leadership positions. John Barnes assumed the chair of the Additive Manufacturing Technical Community Leadership Committee, succeeding Christopher Williams; and Sarah Rimini now chairs the Medical AM Advisory Committee, succeeding Amy Alexander. I’d like to thank Christopher and Amy, who provided exemplary leadership and vision during their tenures, and welcome their replacements.
3D-printing services. At RAPID + TCT, she moderated a panel discussion on 3D printing for point-of-care medical applications. The panel was one of several during a special town hall hosted by the Medical AM Advisory Team.
Other highlights included the winners of the 2022 SME Additive Manufacturing Community Awards: Slade Gardner, founder of Big Metal Additive (Industry Achievement); VELO3D and IMI Critical Engineering (Aubin AM Case Study); and Virginia Tech students Daniel Chirvasuta, Nathanael High, Matthew Martin, Benjamin Nguyen, Omkar Shinde, and Nicolas Tomanelli (Digital Manufacturing Challenge).
Seepersad’s group is collaborating with Penn State University on an NSF-funded LEAP HI project (Leading Engineering for America’s Prosperity, Health, and Infrastructure) to produce functionally graded “active” materials via REAM. The joint effort will allow them to build smart parts that change their shape based on specific stimuli, a capability she suggested is suitable for a range of applications, including the creation of medical devices that adjust to a patient’s anatomy, increasing comfort and reducing the risk of infection.
The AM community took center stage throughout the show. This includes the passing of the baton in two key leadership positions. John Barnes assumed the chair of the Additive Manufacturing Technical Community Leadership Committee, succeeding Christopher Williams; and Sarah Rimini now chairs the Medical AM Advisory Committee, succeeding Amy Alexander. I’d like to thank Christopher and Amy, who provided exemplary leadership and vision during their tenures, and welcome their replacements.
To help foster the next generation of innovators, the SME Education Foundation’s Bright Minds Program welcomed nearly 1,000 middle and high school students to RAPID + TCT. There also was a special networking lunch for young professionals and a Career Forum Panel. The initiative is led by Ellen Lee and Jennifer Coyne, who are both advisors on the Additive Manufacturing Technical Community Leadership Committee.
There also was a special networking lunch for young professionals and a Career Forum Panel. The initiative is led by Ellen Lee and Jennifer Coyne, who are both advisors on the Additive Manufacturing Technical Community Leadership Committee.
The high-viscosity stereolithographic printing process uses polymer resins that are thick “like peanut butter” and a wire grid polarizer that reflects energy rather than absorbing it.
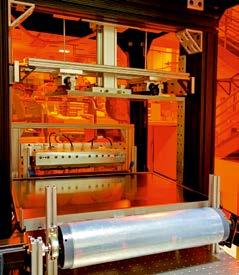
John, who heads The Barnes Global Advisors and Metal Powder Works, has been involved in metal additive manufacturing throughout a distinguished career. He’s led teams that qualified the aerospace industry’s first series production metal AM parts, and developed a pilot metal production facility.
John, who heads The Barnes Global Advisors and Metal Powder Works, has been involved in metal additive manufacturing throughout a distinguished career. He’s led teams that qualified the aerospace industry’s first series production metal AM parts, and developed a pilot metal production facility.
SME Media also interviewed dozens of AM leaders during RAPID + TCT as part of its Voices AMplified initiative that showcases the people behind the technology. This month’s Voices AMplified report profiles two such visionaries: Olga Ivanova and Carl Dekker. Known as “Dr. O,” Olga has worked on innovative projects for the medical and defense industries, and is a tireless crusader for advancing AM.
SME Media also interviewed dozens of AM leaders during RAPID + TCT as part of its Voices AMplified initiative that showcases the people behind the technology. This month’s Voices AMplified report profiles two such visionaries: Olga Ivanova and Carl Dekker. Known as “Dr. O,” Olga has worked on innovative projects for the medical and defense industries, and is a tireless crusader for advancing AM.
Let There Be Light
As senior manager of Ricoh’s Healthcare Center of Excellence, Sarah is developing a curriculum for the company’s Learning Institute that focuses on medical managed
As senior manager of Ricoh’s Healthcare Center of Excellence, Sarah is developing a curriculum for the company’s Learning Institute that focuses on medical managed
Another evolutionary AM project involves the stereolithographic (SL) printing of high-viscosity resins, a technology developed in partnership with Lawrence Livermore National Lab by Seepersad, her colleague Rich Crawford, and their graduate students Nick Rodriguez and Hongtao Song. The process is similar to the “bottom-up” approach common with several brands of commercial SL machines, but with several adjustments to compensate for the peanut butter-like viscosity of the polymer resins.
“Curing high-viscosity resins requires significant amounts of light energy,” Seepersad said. “But, unfortunately, the film polarizers typically used to create the patterns in this type of SL printer absorb much of that energy. So to avoid overheating and possibly destroying the LCD light patterning device, we switched to a wire-grid polarizer, which reflects energy rather than absorbing it.
Carl puts the emphasis on people. He leads a talented team at Met-L-Flo, which produces a wide range of 3D-printed products. He also chairs the Direct Digital Manufacturing Advisory Team and moderated a panel at RAPID + TCT.
Carl puts the emphasis on people. He leads a talented team at Met-L-Flo, which produces a wide range of 3D-printed products. He also chairs the Direct Digital Manufacturing Advisory Team and moderated a panel at RAPID + TCT.
“This way, our LCDs don’t heat up as much and we get greater illumination,” the professor continued. “It also allows us to print reasonably large parts, at least by stereolithography standards. Our current machine, which I believe is one of a kind, has a build area 20 inches square.” Laughing, she added, “It’s almost big enough to print an entire herd of Longhorns.”
Carl and Olga represent the spirit behind Voices AMplified. I hope you enjoy their stories.
Carl and Olga represent the spirit behind Voices AMplified. I hope you enjoy their stories.
Heavy Hitter
Although their movie counterparts possess awesome superpowers, the 3D-printed Baby Yodas (at left) and Groots (right) that Olga Ivanova gave to visiting high school students are unable to do so much as dissipate electrical charge--but they’re still very popular with the kids.
Seepersad, who is named on the patents for these and several other inventions, began her studies at West Virginia University in 1992. She was named a Rhodes Scholar at the University of Oxford, then earned a Ph.D. in mechanical engineering at the Georgia Institute of Technology. In 2005, she took a position with UT Austin as an assistant professor, and has been there ever since.
In addition to AM, Seepersad works on engineering design research and topology optimization, both of which have gradually taken on an additive flavor. One of her current projects involves interactive design exploration, where users can adjust and “play with” 3D-printed structures to see the effect changes have on performance.
“I’ve also done quite a bit of work in meta-materials design, which looks at how a material’s structure—as opposed to its composition—affects its functional properties,” Seepersad added. “That work was in collaboration with fellow professor Mike Haberman, and led to one of our first patents.”
That patent describes “negative stiffness honeycomb materials,” which are ideally suited to 3D printing in metal or plastic and should be of particular interest to anyone with a child in Little League baseball. That’s because these 3D-printed constructions “snap through” on impact, providing recoverable energy absorption capabilities that could one day be applied to motor vehicles, spacecraft instrumentation, and, yes, sports helmets and other forms of personal protection equipment. “We can engineer these to reduce an object’s acceleration threshold by an order of magnitude,” Seepersad said.