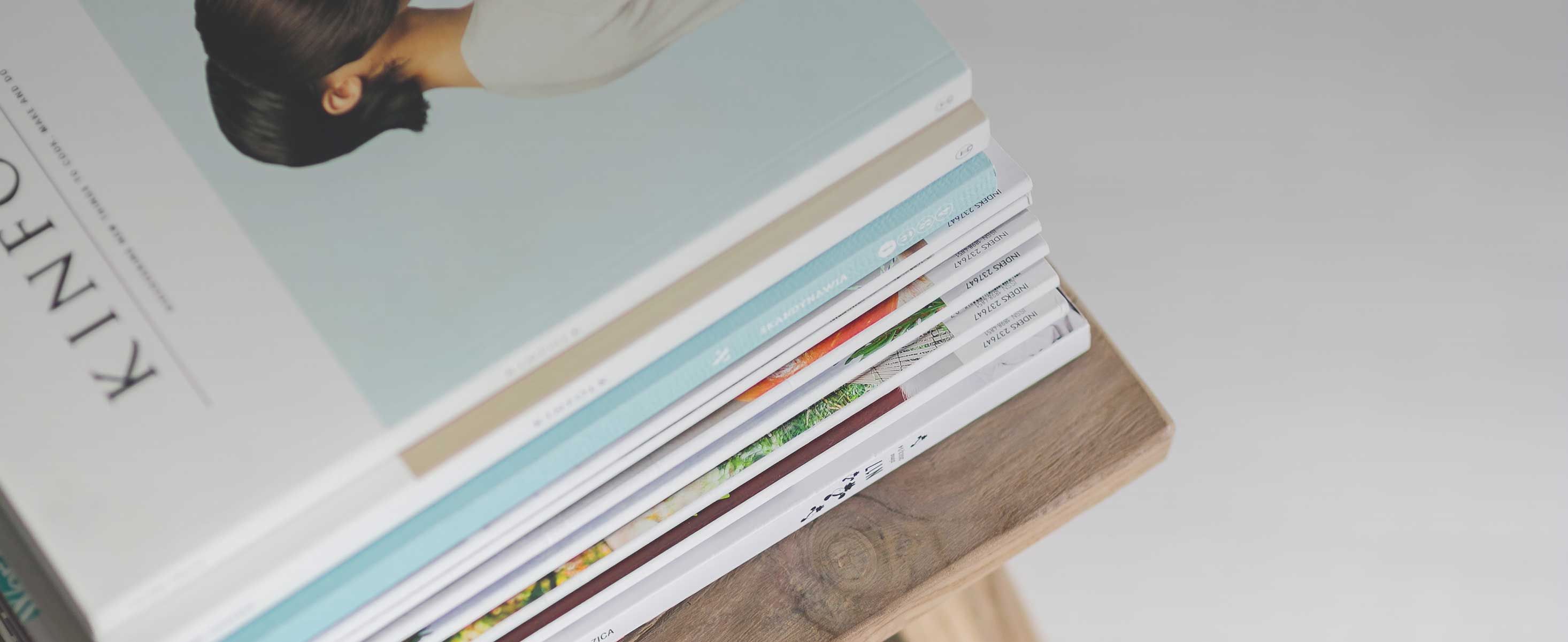
2 minute read
Paging Dr. O
Meet the Director
Kip Hanson Contributing Editor
Thanks to Seepersad’s ingenuity and devotion, UT opened the Center for Additive Manufacturing and Design Innovation (CAMDI) in March 2020, appointing her as its director. And even though her new job title came “right at the beginning of COVID,” Seepersad didn’t let that slow her down.
lga Ivanova has 3D-printed plenty of interesting parts during her time in manufacturing. Rocket nozzles. Turbine blades and impellers. Neonatal tracheostomy tubes. There are more, which we’ll get to in a moment, but to Star Wars fans, it’s the Static Dissipative Yoda that’s most intriguing.
“We printed a bunch of Yoda and Groot (Guardians of the Galaxy) figurines for high school students who visited our facility recently,” said Ivanova, director of technology at Mechnano, an additive manufacturing materials
OCAMDI brings students, researchers, and faculty together under one roof, expanding the school’s commercial AM capabilities and resources. These include a Metal Powder Bed Fusion Lab with EOSINT M280 and Renishaw AM250 Direct Metal Laser Sintering printers, a Liquid Polymer Lab that’s home to a Stratasys J750 Digital Anatomy Printer and 3D
Systems SLA 5000, along with a Metrology Lab boasting structured light scanning, load-testing equipment, and a Zeiss Spectrum coordinate-measuring machine.
Such facilities are crucial to meeting industry challenges. Considering her multiple patents and papers, it’s ironic that Seepersad points to better design capabilities as one of the more urgent needs. Recent advances in topology optimization and generative design notwithstanding, it’s a sad fact that “we can print a lot more than we can design,” she noted.
“Think about the ability to place materials exactly where you want them, or even to modify their composition and mechanical properties from place to place,” Seepersad continued. “Our current design tools are still playing catch-up in many respects.”
Breaking the Conventional Mold
People interact daily with products made via traditional manufacturing technologies, limiting our ability to “think additively,” she said. Until the next generation of designers enters the workforce—young people unfettered by preconceived manufacturing notions and able to wrap their heads around the spatial and material complexities that come with 3D printing—the industry will fail to fully leverage AM’s immense design freedoms.
Thanks to Seepersad and others, that paradigm is shifting. “I think that’s probably been one of our biggest bottlenecks, but the good news is, many of our students have grown up with 3D printing. They’ve used it in high school. Some have even used it in middle school. And aside from our center, UT Austin has a huge maker space called the Texas Inventionworks where students can spend time with 3D printers and laser cutters and similarly advanced technology. We’ve begun to incorporate that into our curriculum, giving students multiple opportunities for hands-on experience.”
Olga Ivanova Master networker RAPID + TCT Director of Technology Mechnano
developer near Phoenix. “It’s our way of getting young people interested in additive manufacturing.”
Padawan Learning
She also challenges students, wherever they are, to design products that can’t be made via conventional means. “More than one student has told me they completed the assignment on their personal 3D printer,” she said. “So despite my earlier comments about bottlenecks and the complexities of additive design, I think the next generation of designers is already here to a certain extent. It’s our job to nurture them and give them all the tools they need to succeed.”
She’s quick to point out that those educational giveaways were made of a gray-colored base resin, not the more expensive static dissipative material (which is black) that she spends much of each day working with—and yes, which she occasionally uses to print Yodas that are just as resistant to electrical charge as they are to the Dark Side of the Force.