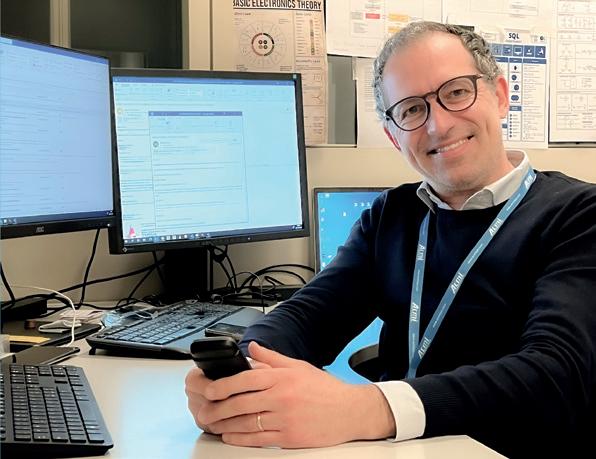
3 minute read
A safe cardboard feeder for a high-performance cartoner
To automate and a make cardboard feeder safer in the cartoning machine Ecopack, ACMI has chosen Pilz certified solution PNOZmulti 2 with optical sensors O300
On the hills of the lower valley of the River Taro, in Fornovo Taro – in the province of Parma, we find the headquarters of ACMI, world leader in bottling and packaging systems featuring high technology for the food and beverage markets.
Advertisement
ACMI has patented numerous systems and presented significant innovation in packaging. Partner of the most important international groups, ACMI designs, manufactures, installs and tests complete turnkey lines for any food and beverage sectors. Long-lasting synergy with Pilz Italia has enabled ACMI to benefit from safety solutions for machines and plants, thus guaranteeing the highest flexibility and productivity.
Ecopack cartoner
Ecopack is a wrap-around continuous cartoning machine for 40 stroke/min that creates packages of products as follows: 4x3, 3x3, and 2x2. ACMI’s latest creation, Ecopack, is part of the company’s product line “GoGreen by ACMI” stemming from the need to offer the market packaging solutions without plastics for packaging operations. Ecopack features robust structure in steel tubes and is activated by ACMI new proprietary OS “AoS”.
Particular attention paid during the design stage has enables creating a machine provided with easy and fast regulation systems, possibly motorized, that can simplify both regulation and changeover operations. The machine-sided items storage can be equipped with an automatic material feeding system. Moreover, to meet the requirements of the food sector, Ecopack features lubricationfree supports, bearings, and chains. This technical choice will turn into less maintenance costs and higher hygiene.
(Gianluca Contesso Automation and Safety Director ACMI S.p.A.)
Certified solution to control cardboard feed with PNOZmulti 2
This ACMI machine monitors the machine storage where the cardboards are fed. When the cardboard feeder has enough packaging material, access to the danger zone is not possible when the machine is running. As soon as there is too little material, the machine will stop to avoid the operator to injure himself. The solution proposed and installed consists of two optical sensors O300 combined with PNOZmulti 2 safety unit. The two optical sensors are evaluated safely inside the PNOZ mB0 module by means of a safe block that verifies that there is always sufficient material in the infeed as to prevent the operators from reaching into the running machine when there is too little material and injuring himself.
The optical sensors O300 with background suppression, sensing distance between 30mm and 100m, offer among others the following peculiarities: lower response time (2.4ms) and sensing detection of objects with diffuse reflectivity ranging between 2% (black surface of the carton) and 90% (white surface of the carton).
This solution to safely control cardboard feed into packaging machines is TÜV SÜD-certified for PL d and/or Cat. 3 in compliance with EN ISO 13849-1 or SIL 2 according to IEC 62061, reducing stopover down to the minimum and increasing productivity.
Thanks to this certification, ACMI has saved on time during planning, design and start-up. In addition, in emergency, it is also possible to simultaneously control different cardboard storages with just one base device.
Possibility to expand safety logics and manage special safety function, such as control of cardboard feed by means of optical sensors O300, makes this Pilz solution high-performance, simple and flexible, thus allowing ACMI machines to keep high productivity.
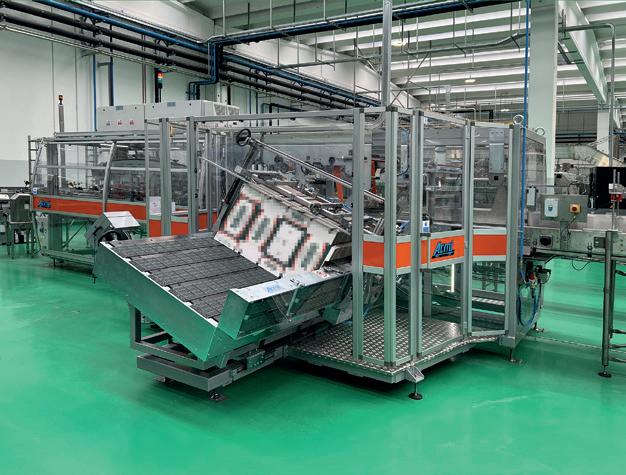
Thanks to this solution, ACMI has been able to control – through PNOZ mB0 – emergency mushroom stop buttons, door sensors, modal selectors and authorization devices. The system is configured by PNOZmulti Configurator software with simple and intuitive block programming.
Expansion module PNOZ m EF PDPlink has enabled creating a safe network of PDP67 F 8DI ION modules (decentralized I/O modules with IP67 protection) with which to go on site and pick the emergency mushroom stop buttons and PSEN code slim sensors delocalized at the doors. Hence, it was possible to optimize the wiring and improve the easiness of installation.
The CRC of the programme that guarantees the univocity and integrity of the project has been archived in the technical folder to be visualized at the start of the PNOZ mB0 module, as well as the name and the date of creation of the project. Online diagnostics by PNOZmulti Configurator enables checking safety status at once and, thanks to error stack and diagnostic word, it is always possible to find the problem immediately.
Interface of the PNOZmB0 system with machine automation system has been completed with busfield PNOZ m ES Profinet, with which we can quickly and easily identify any problem.