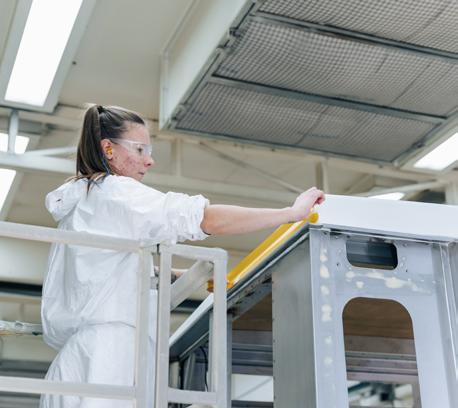
1 minute read
Sustainability mirrored at Blackpool
The close working relationship with our facility at Blackpool, where our cabs are made, have meant many of the improvements at Warwick have also been implemented in Blackpool at the same time. Others have been based on their own initiatives and opportunities. Among them are the following:
Electricity savings
A completely new roof over the factory has made a massive improvement to the heating with significant reduction in both carbon emissions and costs thanks to better heat retention.
Skylights in the new roof have also improved lighting. This, along with the fitting of LED lights throughout the factory and offices, have enhanced the workspace while reducing electricity usage.
Even more electricity has been saved by ensuring the new lights were controlled by both light sensors and movement sensors throughout the facility. This means that lights switch off when natural light levels are high enough and also when there is nobody in a particular area.
Building improvements
Water metering has reduced usage. Old piping, plumbing, fixtures, and fittings have been replaced with more efficient versions which have reduced consumption.
Speed door and emergency doors have also been replaced with more efficient doors. This has improved speed of movement and efficiency around the facilities as well as saving energy through better hear retention.
Ecotile flooring has also been installed in busy working areas. This not only provides better temperature control but is also more comfortable for people to walk on than the concrete floors they have covered.
Supplies waste reduced
Cardboard and plastic waste has also been significantly reduced. Like Warwick, new and bespoke stillages are being introduced and plans to increasingly reuse packaging materials are being implemented.
Equipment upgrades for efficiency
An ongoing programme to reduce energy consumption of air lines has been introduced. Around 60% of power tools are now battery powered. These are not only more efficient but also quieter, improving the environment for staff to work in.
On-tip extraction systems are now used throughout the Fabrication Shop for welders. These are not only more cost-effective and energy efficient but also more flexible than other options. Their introduction coincided with the arrival of new, more efficient welding machines.
Consistently improved efficiency
The Blackpool manufacturing facility now produces more than 1,000 units a year. Variety has increased too, with the new Elite+ cab going into full production in the last year and four new cabs for the North American market being introduced in the last three years.
Despite this increase in complexity and scale, Blackpool has reduced both the output time and the cab production time year-on-year for at least the last 10 years thanks to constantly improving efficiency.
