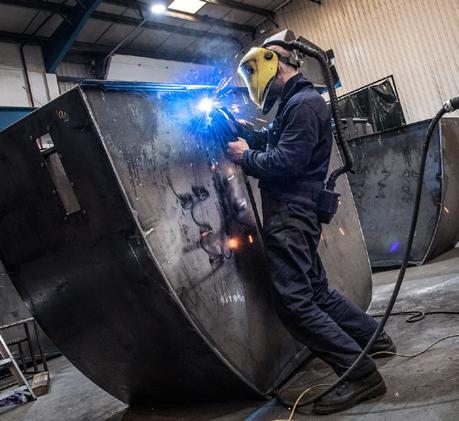
1 minute read
Worksop focuses on products and practices
The Terberg Matec UK manufacturing facility in Worksop, Nottinghamshire, produces a range of recycling vehicles covering all the main waste streams, collection regimes and operators’ needs.
Efficiency and reliability are both the hallmark of these products and also at the heart of their customers’ needs. So a sustainable approach to the entire operation is essential.
“We have customers coming and looking around the factory, seeing how the products they’ve ordered are made,” said Operations Manager Andrew Coulson.
“So it is essential, if we are to create the right impression, that we practice what we preach.”
With this in mind, the Worksop plant has, for several years, been working to reduce its carbon footprint and unit costs.
Welding gas efficiency
The use of gases for mild steel welding has been transformed in the last five years.
Gases were originally stored in cylinders and in a silo beside the building, a common set up in factories throughout the UK. But this is inefficient and significant amounts of gases are lost through leakage, while partempty cylinders were scattered around the factory.
This was replaced by a system of interchangeable gas banks from which the gas is piped into the building. The system is automated so that new banks are ordered and delivered before active ones run out. Two sets of banks are also used – one for mild steel and another for stainless steel.
The whole system has been run by a third party –Ayton Gas – since 2018. They ensure supply, delivery and maintenance as well as detailed reports and analysis of performance.
This system has drastically reduced the loss of gases through leakage. It has also reduced the carbon footprint of the operation by more than 100 tonnes of CO² in less than five years.
Waste management
A new contract began in 2022 for the collection and recycling of waste from the factory.
The new system was put in place 10 months ago and ensures better segregation of different waste streams in both the offices and factory. These are collected in different bins which are then emptied into larger containers for collection.
Electricity savings
The installation of LED lighting in the entire factory in August 2018, heavily reducing our electricity usage each month since.
Further plans
Plans have also been developed for solar panels to power the Worksop operation along with other options to reduce electrical consumption by improving efficiency. Similarly, plans to drastically reduce gas consumption have also been drawn up and are currently under consideration.
In addition, we are currently planning a system to use surplus waste heat from a neighbouring power generation plant to heat our workshops and offices. Further, the power plant makes use of carbon capture technology to yet further reduce their and our carbon footprint.