
8 minute read
Together in electric dreams
After a short postponement due to COVID, last October’s Bauma 2022 was almost a return to normality. A majority of OEMs exhibited, and visitor numbers were just 20% shy of the 2019 level. Alex Woodrow, managing director, KGP Powertrain Intelligence reports for Construction Worx…
A noticeable trend at the show was the significant increase in fully electrified zero emission machines as the construction segment seeks to decarbonise. From 2023, legislation will require many major companies to quantify carbon emissions from both their operations and from their goods and services in use. Reducing Scope 3 emissions, in particular from fuel and energy used in their machines, will be a major challenge. However, companies’ plans to reduce emissions will increasingly be supported by legislative and related policies – thus incentivising the upgrade of zero and low emission machines.
Advertisement
KGP's database of xEV Non-Road models included specific construction machines totalling 100 zero emission or alternative machines at the show. In 2018 our first review of electrified NRMM, excluding forklift trucks, included just 60 machines, of which 36 were construction and mining machines. Back at Bauma 2019 there were a number of electric excavators, Liebherr’s drill-rig, and compact electric wheel loaders, plus one or two pieces of electric underground mining equipment launched. However, at this Bauma there were considerably more, plus entrants in new segments. Just over 30 machines had been publicly shown before, meaning almost 70 were new to the market. Not just from major global OEMs, but increasingly global Chinese OEMs, including Sany, Sunward and XCMG, had electric machines on show. In total there were over 100 electric, hybrid and umbilical models across 34 OEMs that we visited. Compared to 2018’s 36 construction and mining machines that were electrified, as of November KGP’s data tracks 248 electric and hybrid construction and mining machines on the market or near production i.e. 500% growth in four years.
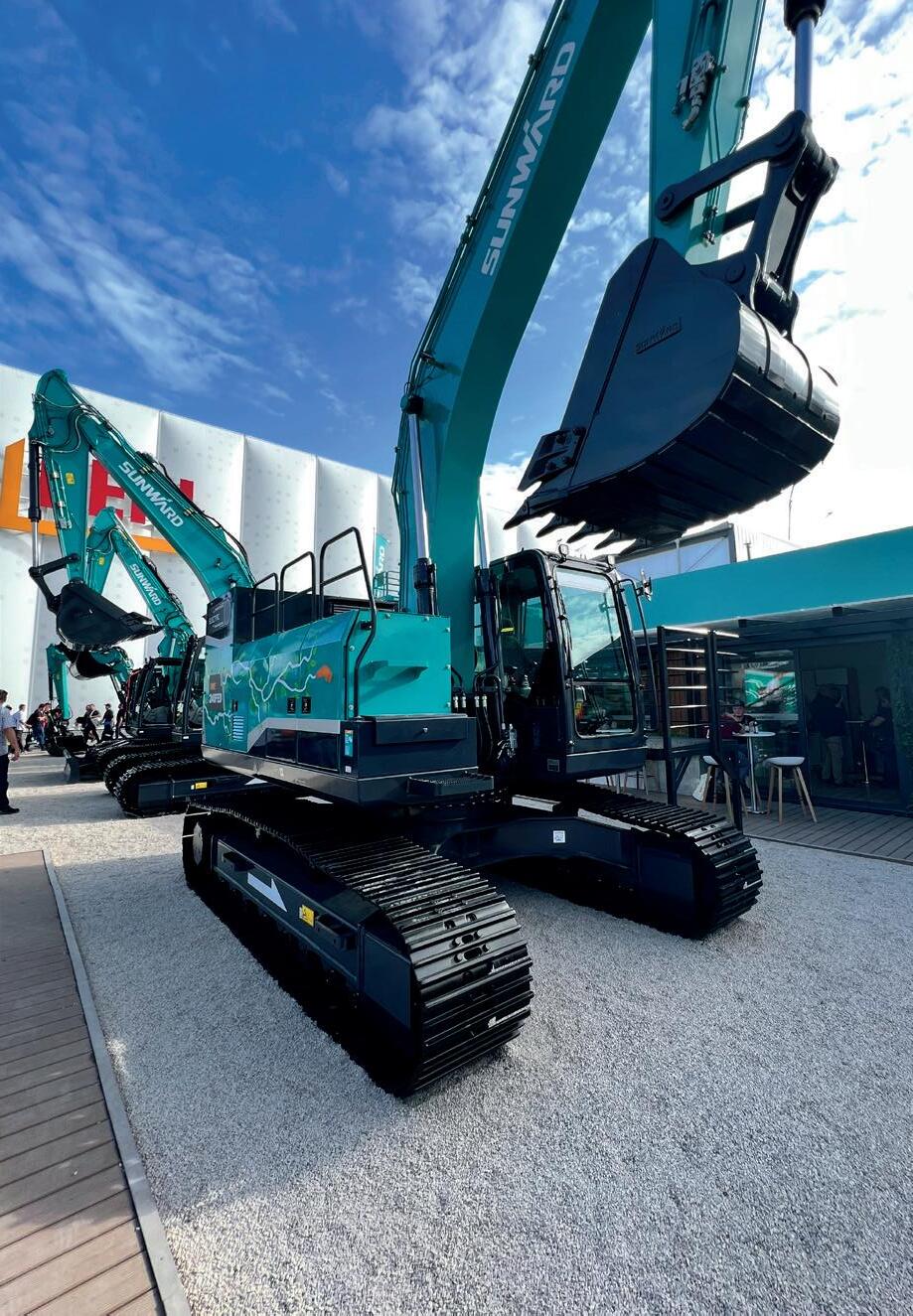
For smaller equipment, 48V has been widely adopted. For larger machines, the voltage level depends on OEM and machine type. However, 48V systems are not widely compatible with existing vehicle charging systems, and therefore require their own either onboard AC or onside DC chargers. Many can be plugged into existing wall sockets, while others may have dedicated chargers connected to the 400V AC or wider grid.
Alongside the machines a number of exhibitors were showing innovations to charge machines on site. There remains a long way to go before these become standard. And the standards are for charging, batteries and other equipment systems are not yet fully defined, unlike in the automotive segment. For automotive applications Level 1 and Level 2 AC chargers can be installed for domestic use, with levels 2 between 3 and 19KW, Level 3 DC fast charger are being widely installed for passenger cars and light commercial vehicles at up to 350kW in public and commercial locations. Charging solutions for the construction site may be brought on site containerised, plugging into an existing 400V grid connection where available. These may contain batteries, charging the batteries constantly at lower power rates, spreading the electricity demand cost through a 24 hour day. These then allow charging of equipment at high rates on demand, overnight.

Larger Battery Packs being developed
Batteries will remain critical to all of the technologies however. Even hydrogen engines may benefit from larger batteries, and may be hybridised in larger machines, as both may be optimised for hydrogen consumption and the latter for emissions, using stored energy for power boosts and engine idling periods. Lithium ion chemistries prevail in the segment. There are a number of smaller applications using Lead Acid, carried over from the forklift truck segment. Lithium batteries are being sourced from many different suppliers, as well as OEM’s in-house capabilities. Caterpillar/Perkins showed their prototype battery pack, with 48V and high voltage versions, albeit with limited detail. Deere showed its Kriesel acquired pack and FPT Industrial its Microvast packs, which are being used already in its parent’s truck applications.
For larger machines, above the 6t mini excavators and compact wheel loaders, other solutions apply. Hitachi, a market leader based on the number of excavators, had four at the show, produced partly in partnership with Swiss Kiesel (KTEG). The largest ZX85 sported a 100kWh battery at 800V. Hitachi’s ZE135 electric, developed between Suncar, KTEG and using an Akasol 200kWh battery can be charged at 150kW using a CCS2 connector. Sunward also showed its 24t excavator, with a 618V system, 120kW motor and battery of over 400kWh according to its spec sheet, the biggest in a machine at the show (although not all pack sizes were made public). Other large packs above 300kWh (3 or 4 Teslas worth) included Caterpillar’s electric excavator with 320kWh, HBM-Nobas’ Motor Grader with 320kWh, Liebherr’s Piling Rig with 400kWh and Sany’s Mobile Crane with 300kWh.
These batteries remain fairly small compared to the latest trucks coming to market (Tesla’s Semi is understood to have 900kWh), but there is a lot wider spread of sizes needed in the Construction segment. The smallest mini-excavator shown was Komatsu’s 1t machine with 1.3kWh; with up to 49.2kWh in Kubota’s 3.6t Mini. For wheel loaders the largest, Caterpillar’s 950 GC has a battery of 256kWh. Compaction Equipment was also a growth segment, but details of battery size and run time from Bomag, Dynapac, Hamm and Vogele was limited. These larger machines follow the smaller ramming plates launched by Wacker Neuson at previous events. At Bauma we also saw the first electric compact tracked loader launched in Europe by Bobcat, bringing the model already launched in the US. The T7X is rated at 460V and has a 60kWh battery. We expect to see larger batteries launched over the next 12 months, following larger applications in adjacent segments. For example, UK based WAE Technologies (formerly Williams Advanced Engineering and now part of Fortescue Metals Group) launched its 1.4MWh pack. The battery is being tested in a Liebherr mining truck.

Very few standards for batteries for NRMM currently exist. OEMs are often seen borrowing systems from automotive, both light vehicle and heavy vehicle, or other segments – for example material handling – forklift trucks in particular. In the automotive segment vehicles are evolving from 400V systems through 800V for passenger cars, as well as the more widely available 48V micro and mild hybrids, but in the truck segment a new standard has been introduced by CharIN, the industry standard for above 1MW charging, now called the MCS – Megawatt Charging Standard. Its new connector was released in 2022 and, although we didn’t see it yet at Bauma, we expect to see it alongside the more regular CCS standard on machines at Bauma in 2025.
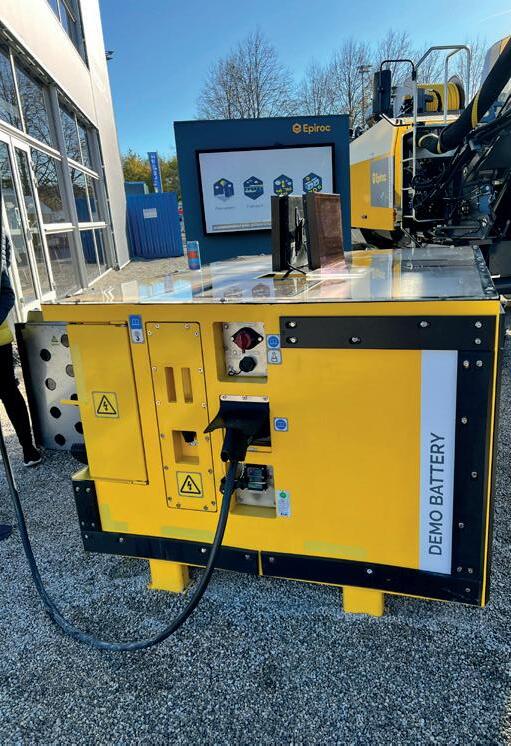
CECE’s PT Electrification is currently reviewing standards for batteries in construction. With the automotive segment increasing demand for batteries significantly investment is flooding into capacity. However, demand from the construction and broader NRMM industry will be a small fraction of the overall market and will need to adopt standards. In the EU’s Battery Directive battery durability has been omitted for automotive applications, pending a UNECE regulation that was proposed in the last quarter of 2022. A similar regulation for the heavy vehicle segment is being considered. These should drive durability of batteries that can be used in Non-Road applications, but with widely differing demands for NRMM applications the sector may need to consider its own durability standards.
Alternative Fuels
And then there are the alternative fuels. Hydrogen is controversial amongst many spectators, that observe significant energy losses, but there is still massive investment, due to the need to time shift energy supplies during less sunny or windy periods.
Most hydrogen interest in the news currently focusses on hydrogen ICE. There were a number of hydrogen ICE models at Bauma and a few more press releases. Notable on display were Liebherr’s H964 and H966 hydrogen engines, using its own fuel injection system. Volvo Penta displayed its 13-litre hydrogen ICE, using CMBTech’s conversion, and Kubota announced a partnership for stationary use with its V3800 converted to hydrogen. Unfortunately, with JCB, Cummins and Deutz absent from the show, but all announcing hydrogen engines none were present at Bauma. The sole hydrogen fuel cell equipment was Hyundai Construction’s HW155H wheeled-excavator.
Let’s see what Conexpo brings…
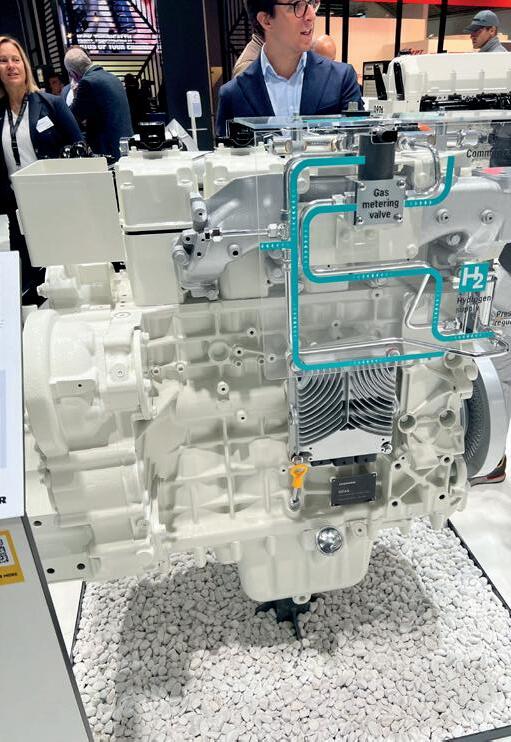