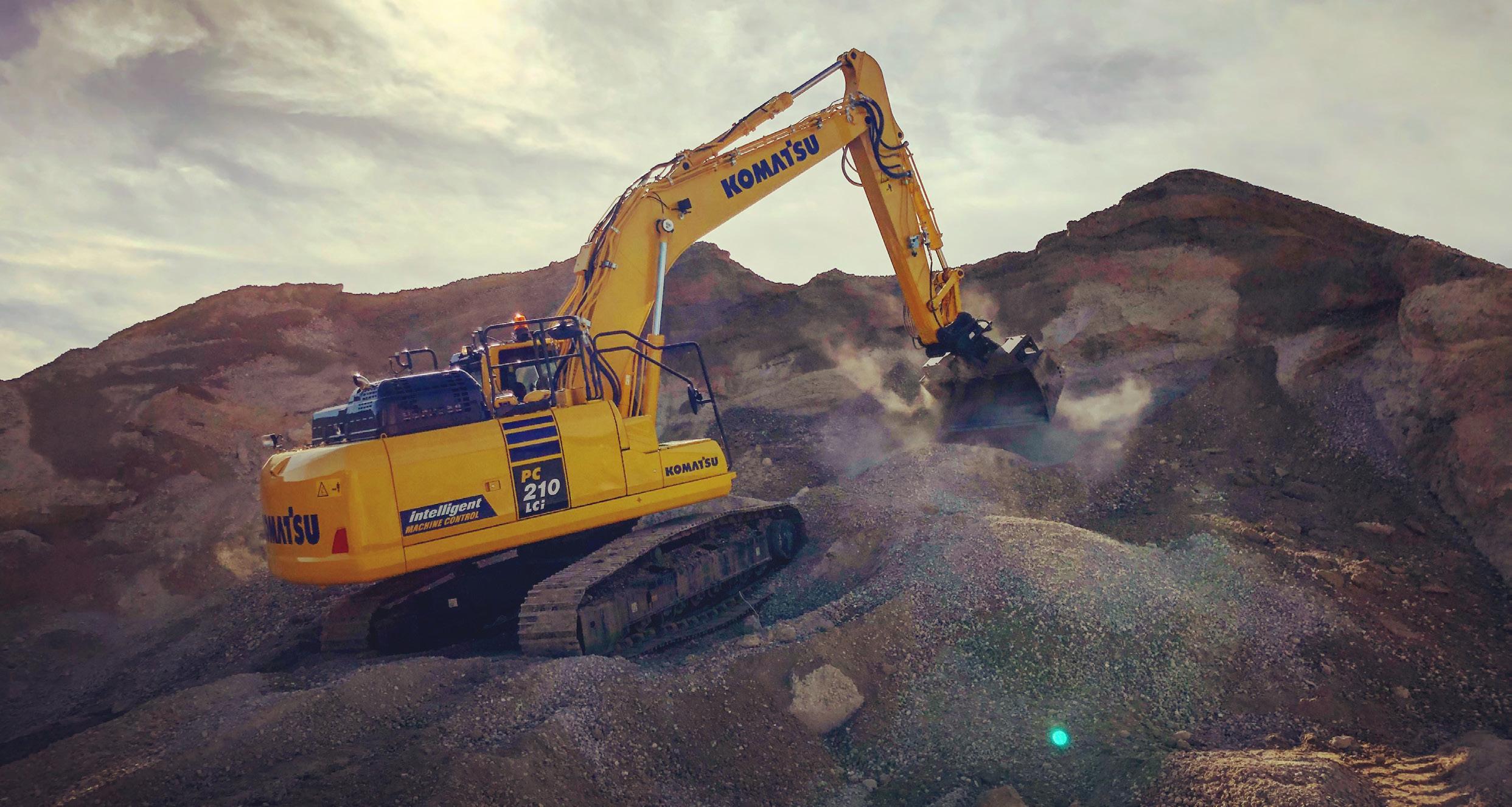
17 minute read
Autonomous Machines
Komatsu’s World of Autonomous Operations
Companies like Google’s Waymo and Elon Musk’s Tesla make it look like autonomous vehicles are something of the near future. With concept cars being tested out on the road people are starting to wonder why has this technology not found its way to other industries like construction?
Advertisement
Komatsu’s Richard Clement, deputy general manager Smart Construction delves deep into the reality of autonomous machines… Currently there is no existing road ahead on how autonomous operation can be integrated into the construction industry. But we at Komatsu believe that just creating autonomous machines isn’t going to be sufficient. Having a total overview not just visually but also in the form of data is needed to bring safety, efficiency and great implementation to the jobsite.
In the past decade, our Autonomous Haulage System (AHS) has been responsible for moving over two billion tons of material. It’s an achievement that has proven the practicality of autonomous operations. With the experience and knowledge we have gained creating this system - which started six years before GPS was commercially available - we want to start focusing on the next big innovation in autonomous operations.
AUTONOMOUS HAULAGE Technically, our Autonomous Haulage System isn’t meant for construction. It was created specifically for the repetitive operations in the mining sector. Where the production process is relatively predictable and there is consistency of haulage routes etc. On these job sites there are strict rules and measures in place to keep pedestrians and non-production vehicles out of harm’s way. Mining is an industry where autonomous technology was able to be deployed for use in an enclosed, tightly managed environment. Construction is not. For that reason, it’s not possible to simply transplant the AHS technologies to the very different circumstances of the construction world.
So, we are not attempting to directly do this. We are taking a different approach. We’re still pursuing technological advancements in autonomous machinery, but at the same time we find it important to investigate how we can evolve the jobsite and processes used in a construction environment.
SMART CONSTRUCTION This way of thinking led Komatsu to the development of a set of Smart Construction solutions. With this innovation we aim to bring a digital transformation of processes to current job sites. One easy to grasp example is drone surveying, an effective way for your employees to measure the terrain safely, accurately and efficiently. There’s also intelligent Machine Control (iMC), which aims to help the excavator or dozer operator to be more accurate and to improve the speed of new recruits being able to operate with their more experienced peers. You can see that beside an increase in safety and efficiency these are tiny but strong steps towards the digital transformation of the construction environment.
By combining our experience from the development of products for autonomous operations with what we learnt from developing the Smart Construction solutions, we at Komatsu developed a strategic roadmap for the transformation of (autonomous operation) products and (digitally transformed) job sites. Following this vision, products, on the horizontal axis, will be designed to operate with increasing autonomy. At the same time, the job site will undergo a transformation. It will become increasingly digitalized. The core message of this approach? The road to optimal performance incorporates a combination of autonomous product development and digital transformation.
Level 05
Optimisation of
Construction
Level 0«
Automation of
Construction lanning
Level 0Ç
3 Dimensional
Construction lanning
Level 0â
3 Dimensional
Topographic Map
Level 0
3 Dimensional
Design Data onstruction)
C
Process (Optimisation Level of
00 Level
Con*entional
www.komatsu.eu/smart-construction Level 0
Limited Operational
Support
Komatsu’s vision of ‘Work Places of the Future’
Products (Level of Autonomous Operation)
Level 0âLevel 0Ç
Ad*anced Operational
Support Ad*anced SolF
Automation Level 0«
Ad*anced Colladorati*c
Autonomous Operation Level 05
Ad*anced Decision makinl
Autonomous Operation
THE ROADMAP We believe in a synchronous digital innovation of the construction jobsite and machinery. The proof is in the pudding, our intelligent Machine Control Level 2 products can be found on thousands of today’s job sites, iMC dozers and excavators are helping operators work on complex surface designs as we speak. Now this is just Level 2 machinery, but we are currently working on all kinds of prototypes we aim to launch in the future. The moment when job sites reach Level 5, the digital transformation of the job site will have created an environment that allows customers to use the autonomous capabilities of the products to their full potential.
We’ll see an environment that offers benefits similar to those of the mining world. The technology will be able to perform to its full potential because the job site environment will be tuned into the needs of this technology. The increased accuracy will allow for better insight into job costs. The use of increasingly autonomous machines will allow the operators to avoid working in the higher risk areas around machines and potentially treacherous terrain. Customers will have the safety, efficiency and insight they need to optimize the benefits of autonomous operations. One common denominator to achieve this is communication. Customers use many different tools and machinery - that aren’t Komatsu products - on a job site to deliver the highest quality construction output. And we want to support our current and future customers in the most efficient and safe way of working. We care about construction productivity so we will focus on both the process improvement as well as product usage.
Komatsu has now put Smart Construction and intelligent Machine Control into effect on more than 8,000 sites worldwide. The lesson learned from this? A job site must complement the technology being used. Otherwise the vehicle automation technology will not perform at optimal efficiency. Take a look at intelligent Machine Control. It offers benefits in any situation. But if you want to optimize the potential? You need to work with 3D data (Design and Terrain). Once you’ve managed this, you’ll be able to look at moving even further forward to perform to even higher standards.
LOOKING TO THE FUTURE
Although it is specifically for the mining world, the Autonomous Haulage System has given us a window into the future. It’s encouraged us to imagine what’s possible in construction. However, the Autonomous Haulage System has already been around for ten years. A decade in which technology has moved ahead in leaps and bounds. It’s perfectly fine to dream of a similar level of autonomy in the construction industry. There’s no saying exactly what other doors will be open to us when we reach that level. ■
Drone surveying is an effective way for employees to measure the terrain safely, accurately and efficiently
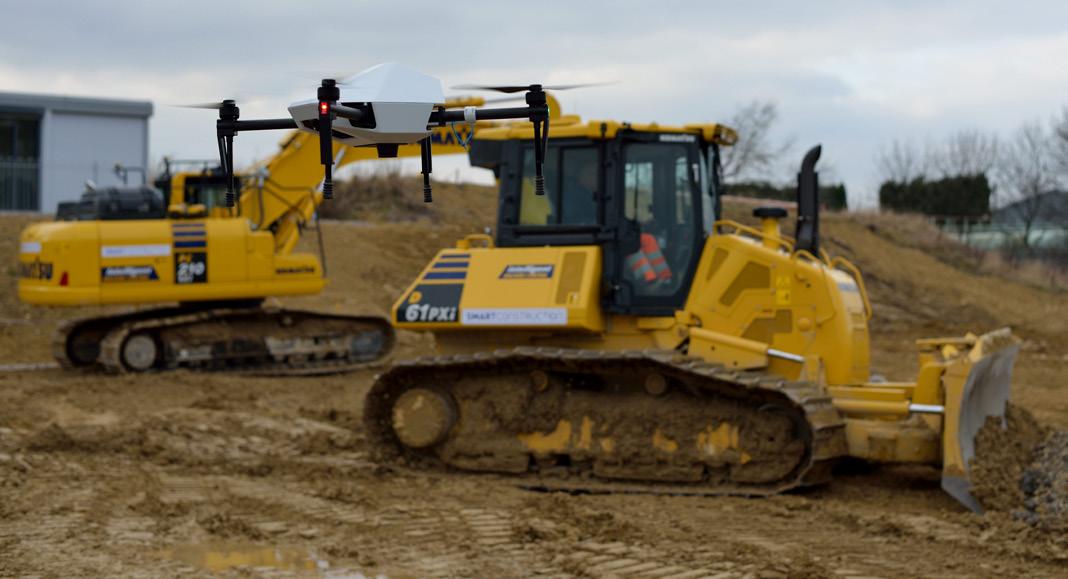
For more information contact: Richard Clement, Deputy General Manager Smart Construction Telephone: +44 1914925444 | mobile: +44 7734684671 Email: richard.clement@komatsu.eu
Dig, form, maintain and clearditches, drainage and watercourses, quicklyand easily, with ourrange ofexcavatorattachments. with Drainage & Ditches
V-Ditchers
t: 01889 503020 8am to 5pm, Mon to Fri Hydraulic Tilt-Ditchers
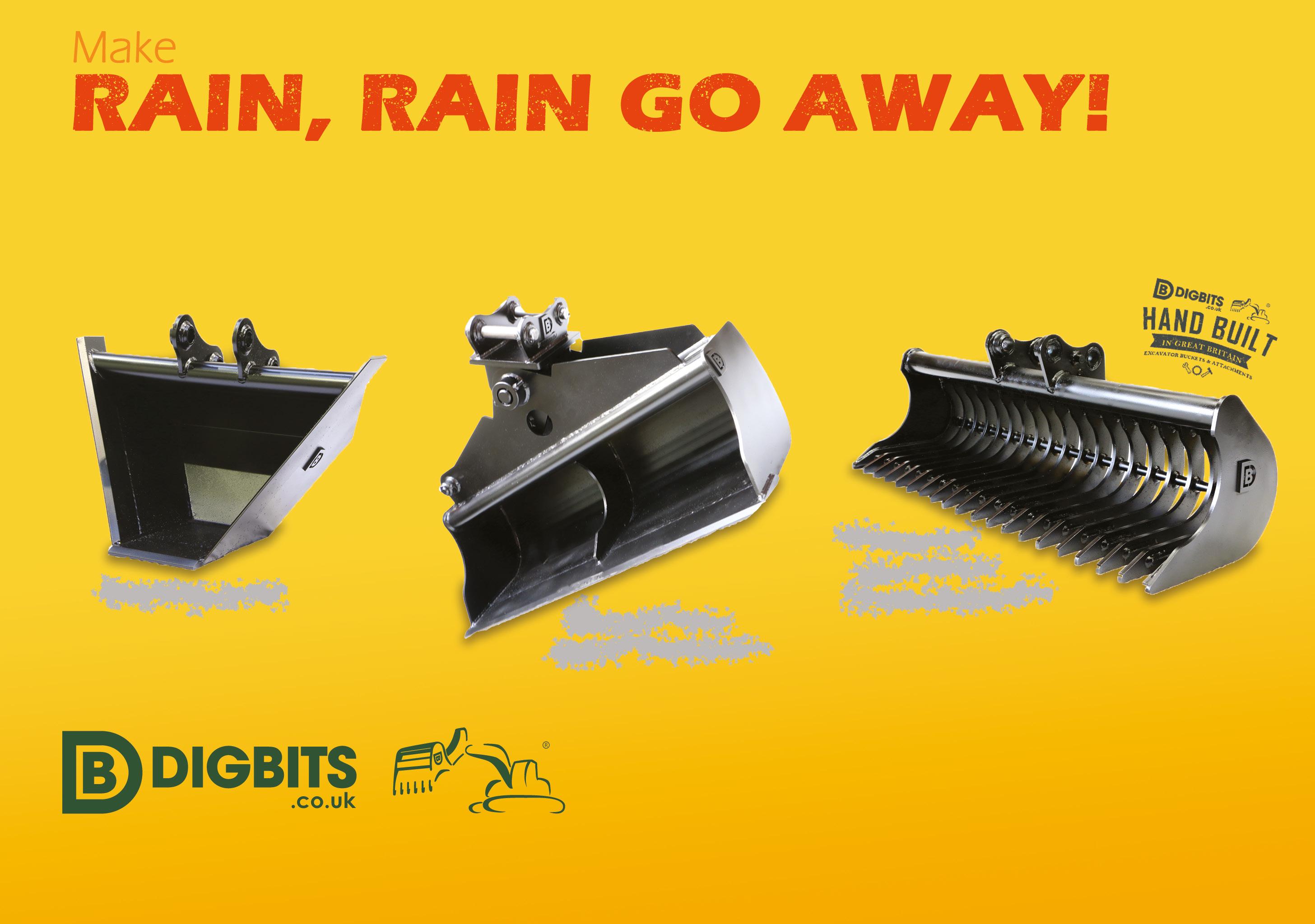

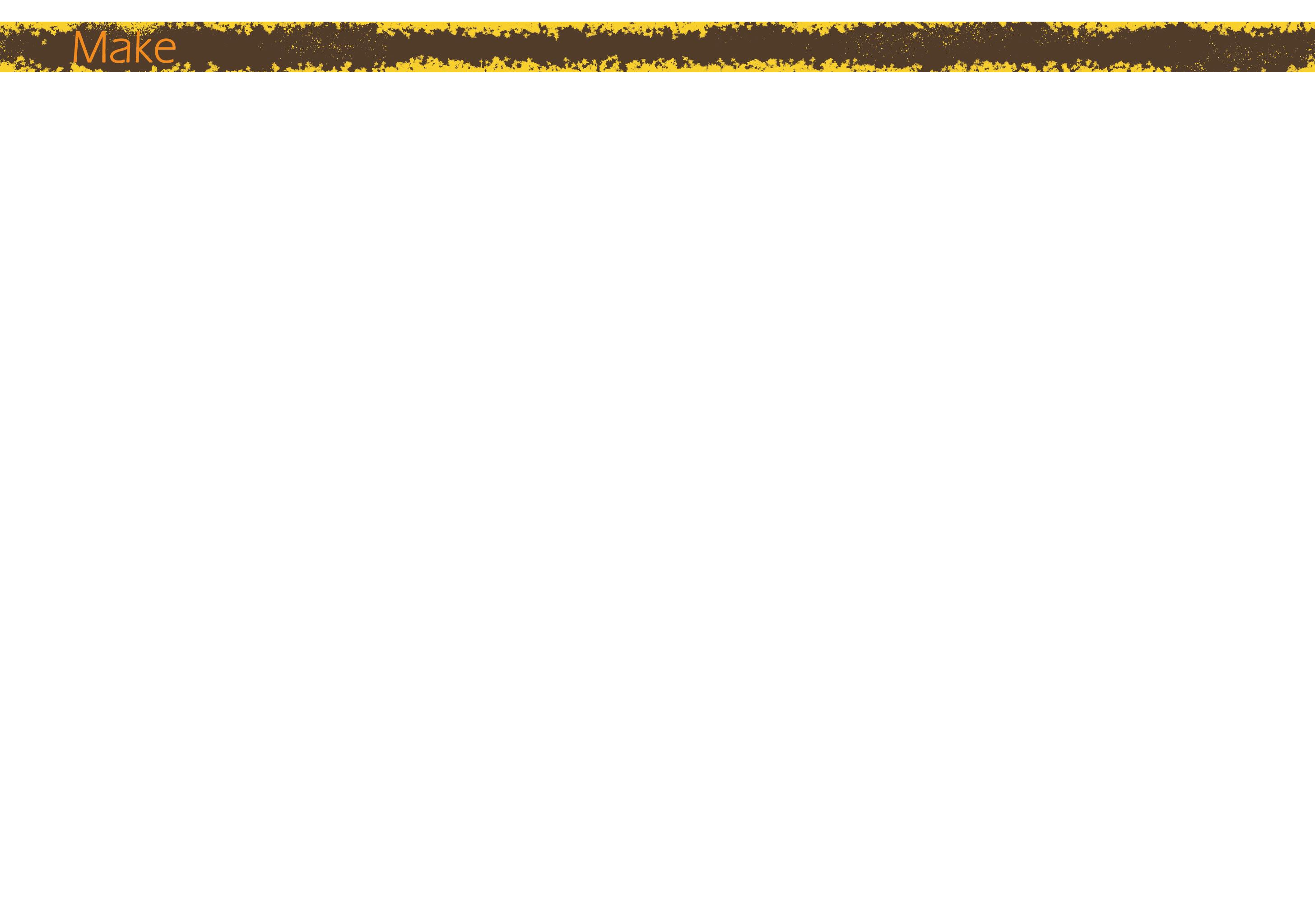
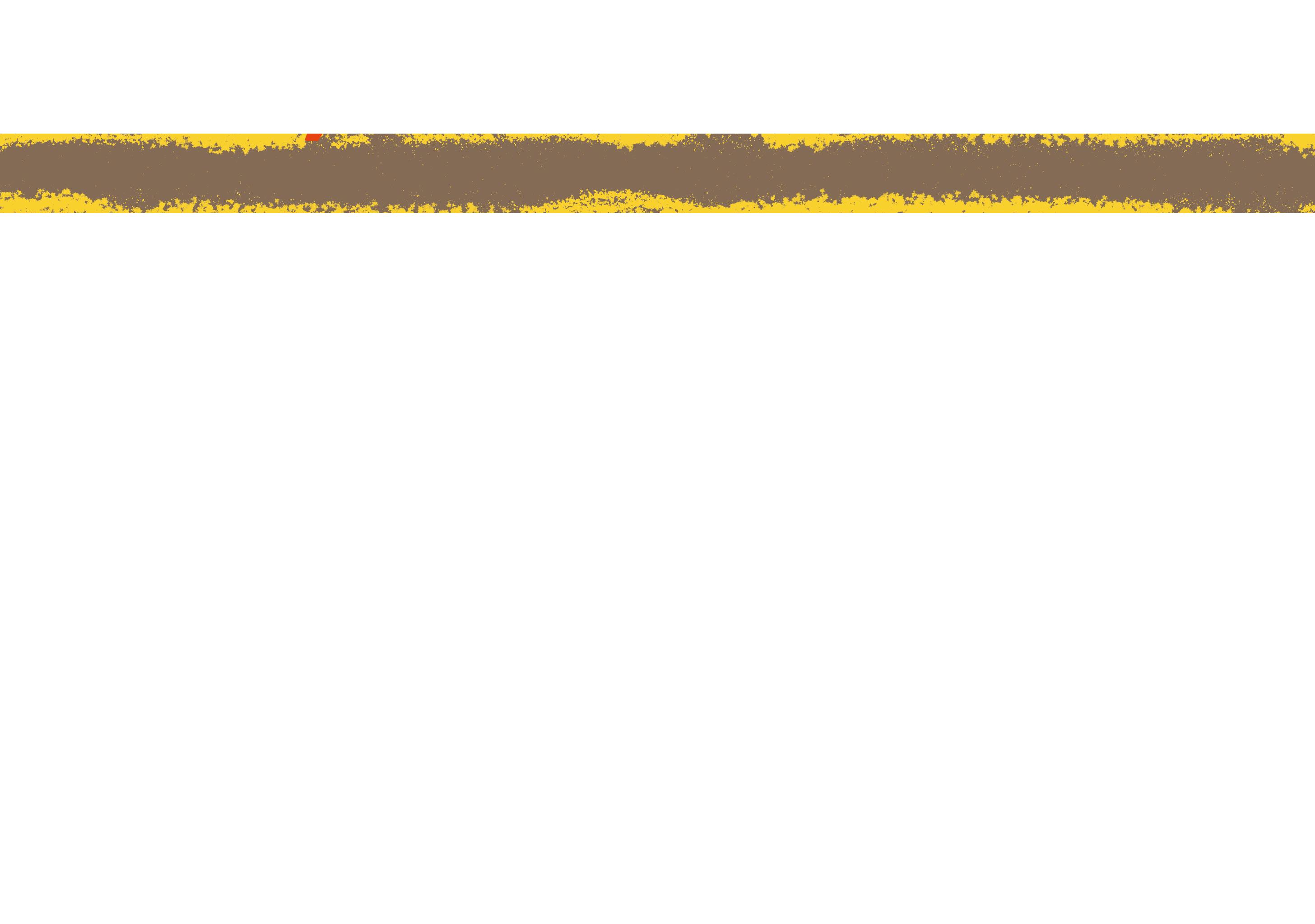
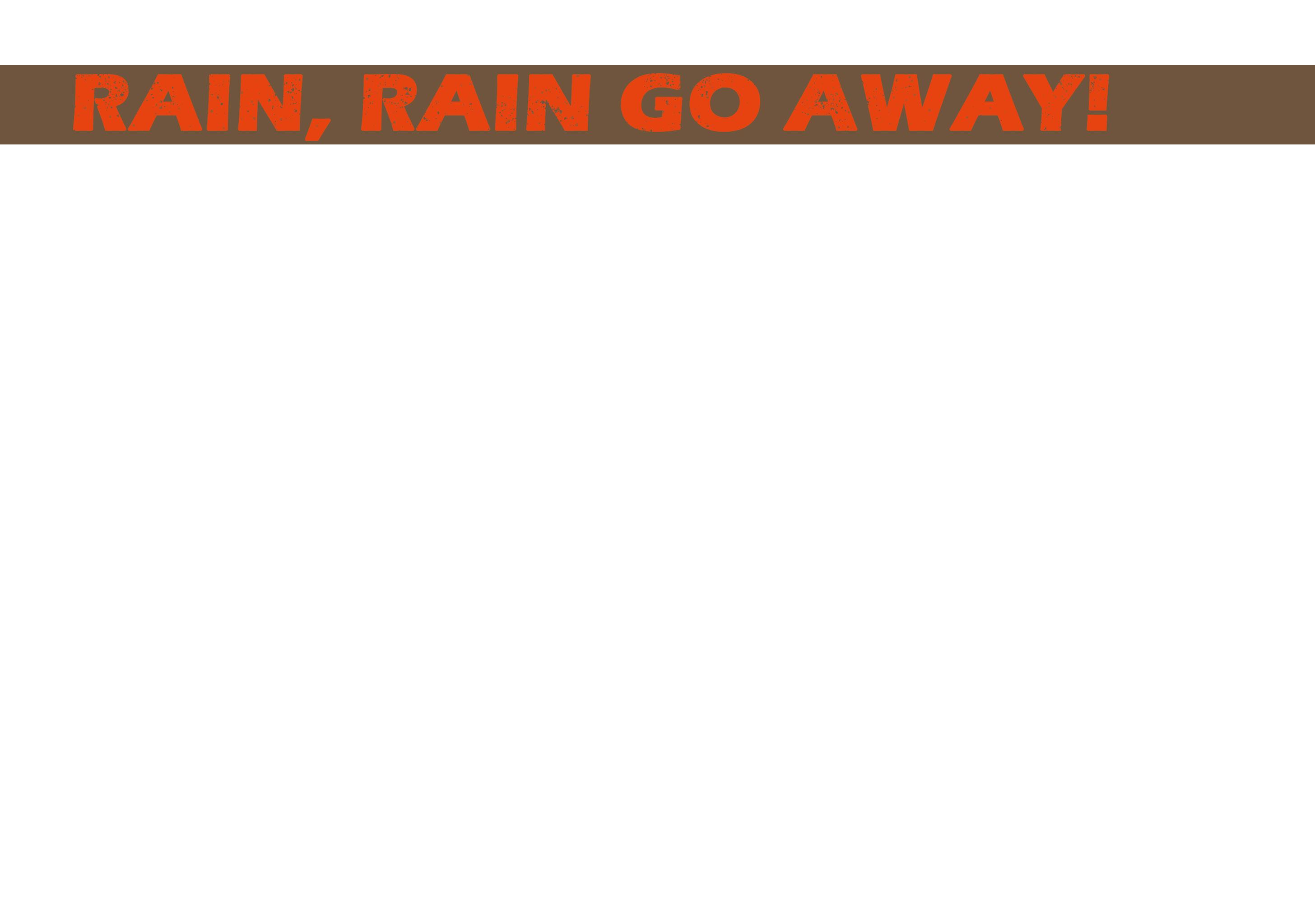
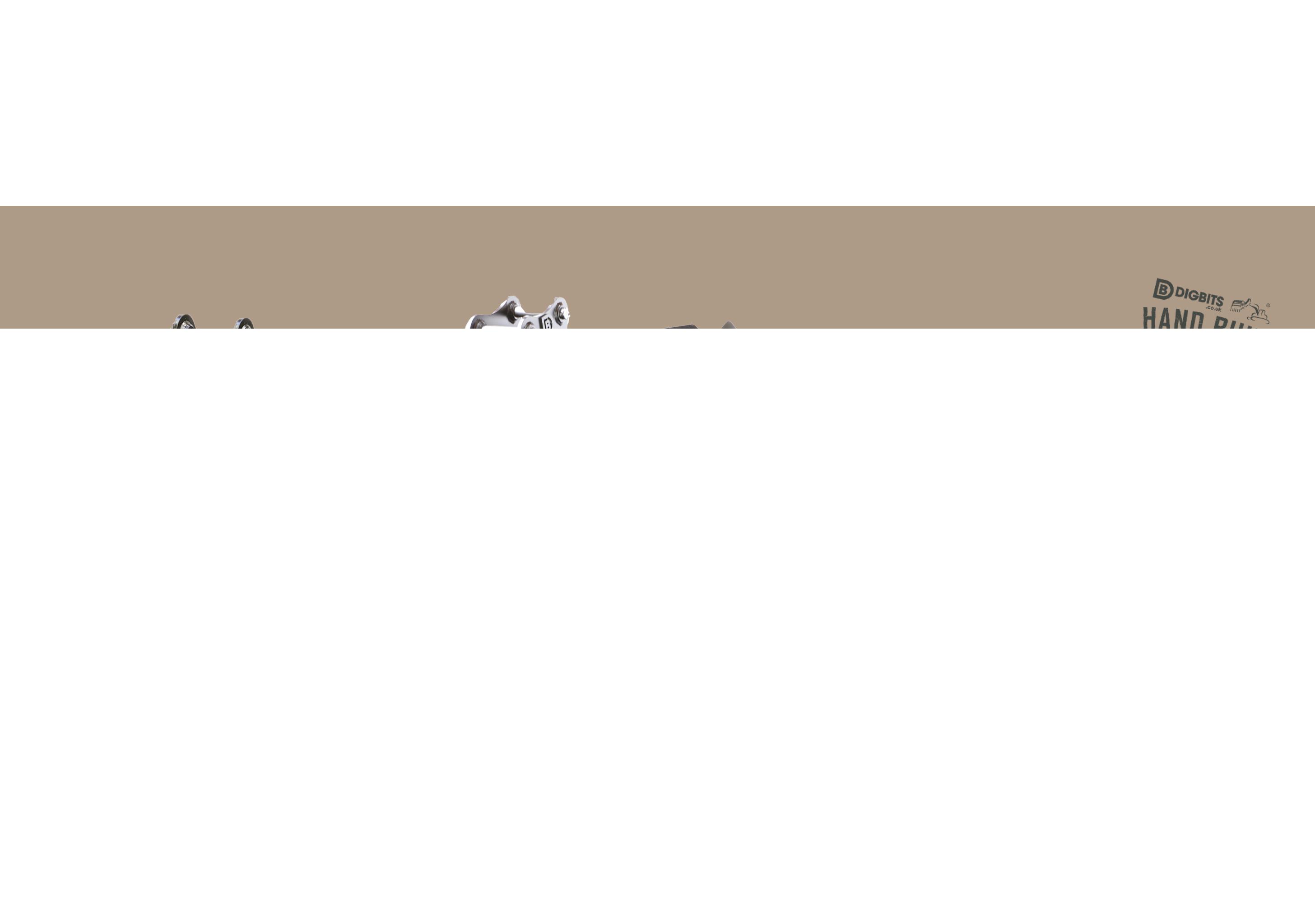
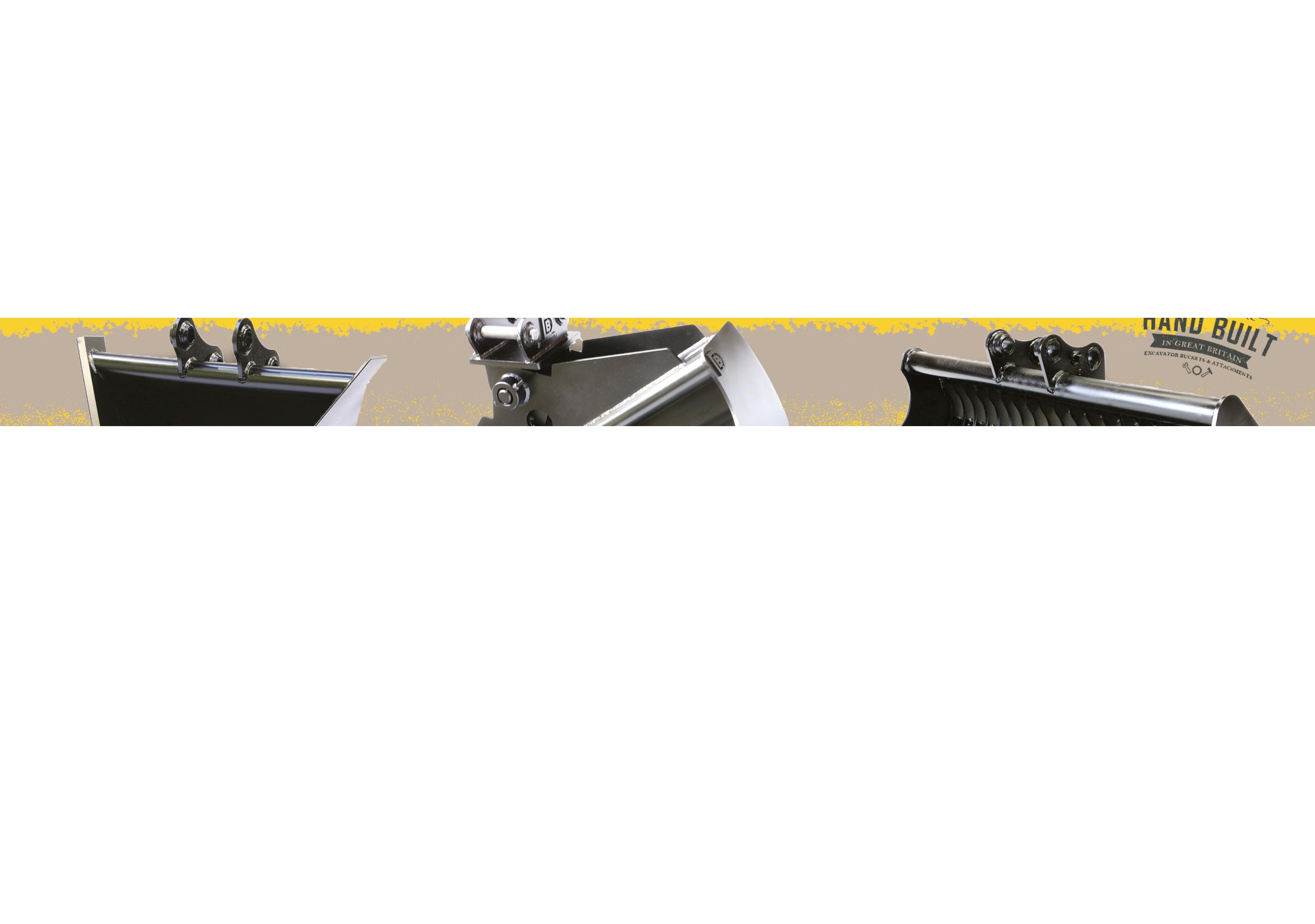
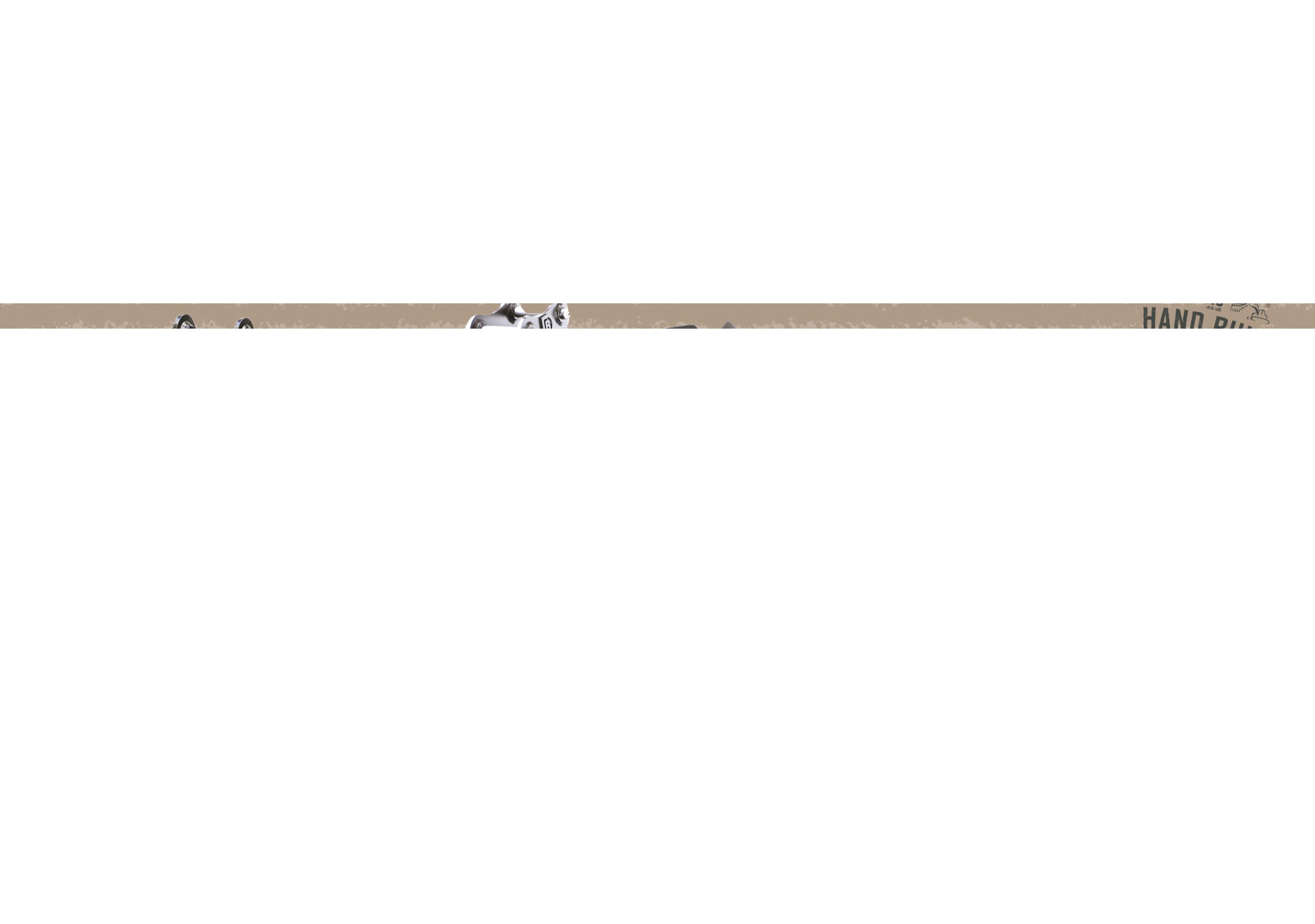
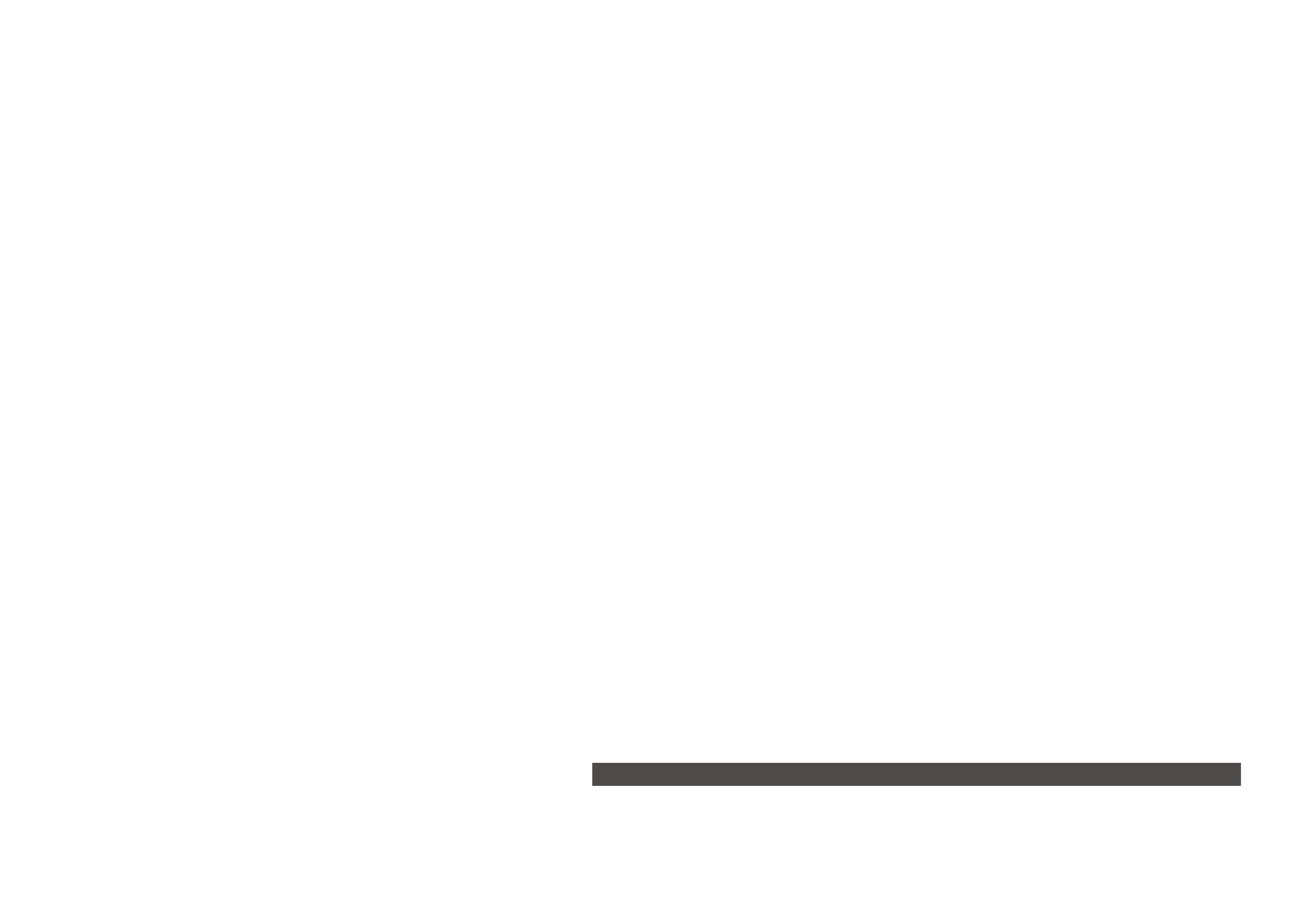



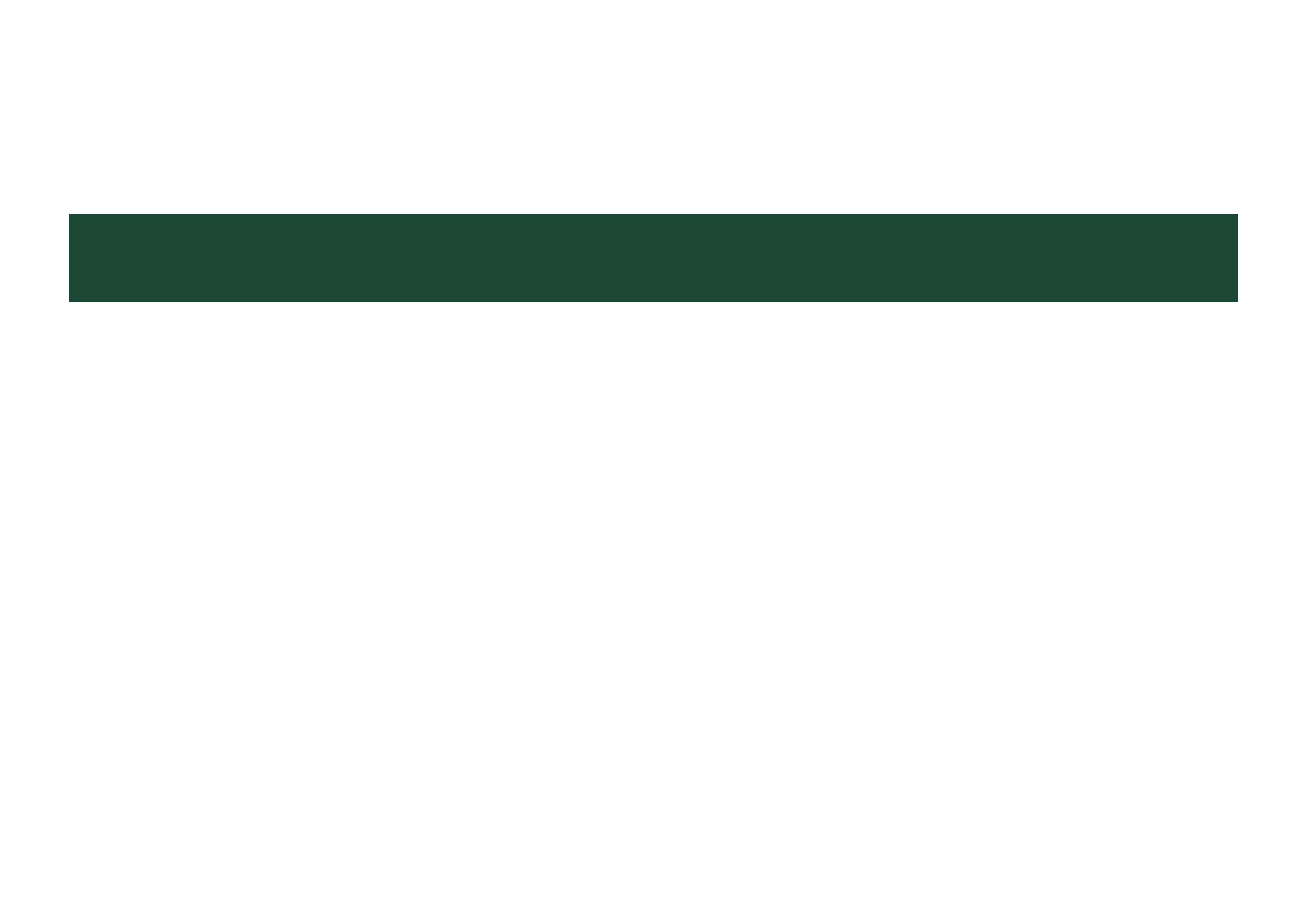
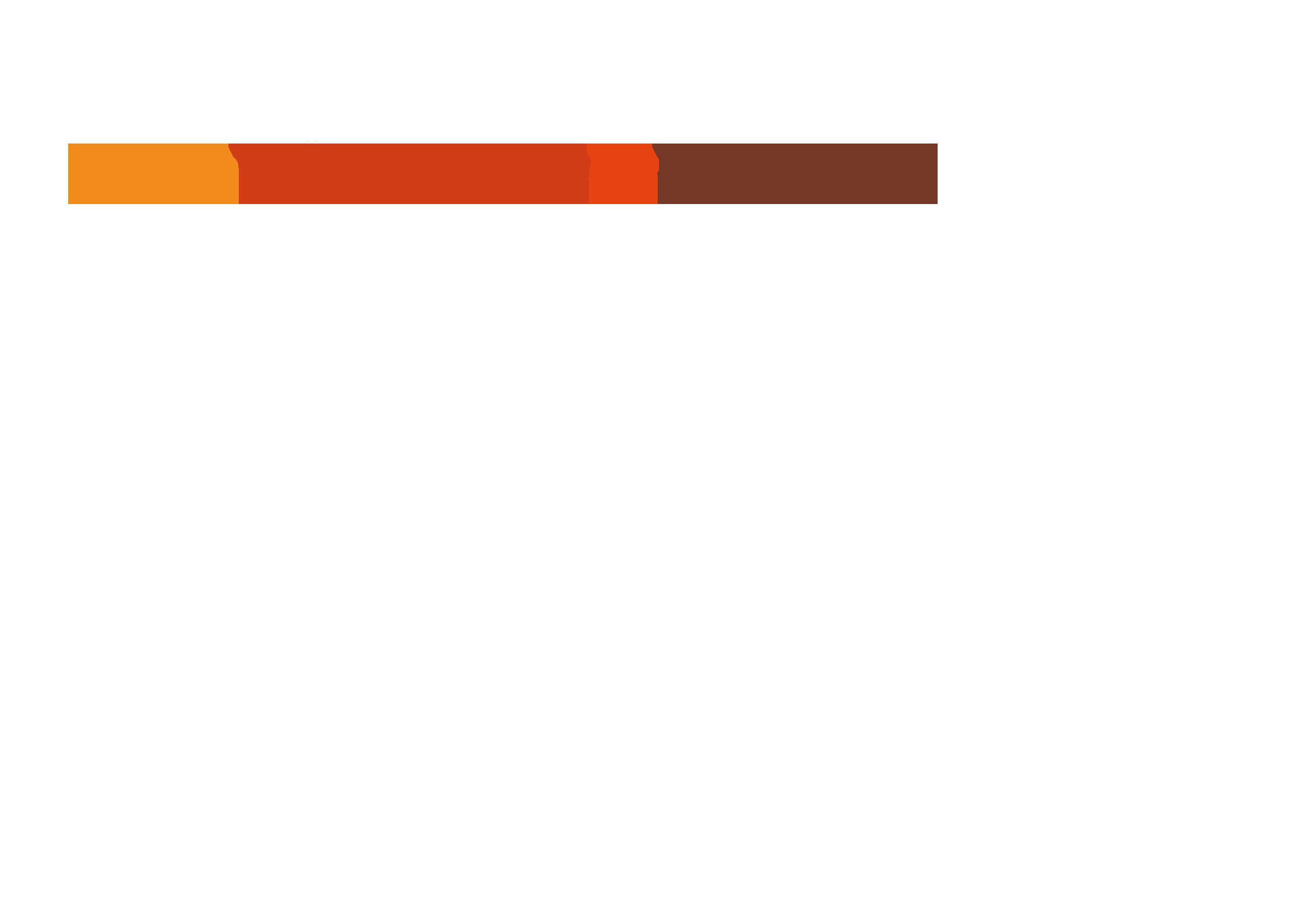
General Purpose Rake Buckets
E X C A V A T O R P A R T S & A T T A C H M E N T S
e: sales@digbits.co.uk w: www.digbits.co.uk
Our core business: • Modular buildings • Office cabins • Sanitary cabins • Storage containers • Shipping containers
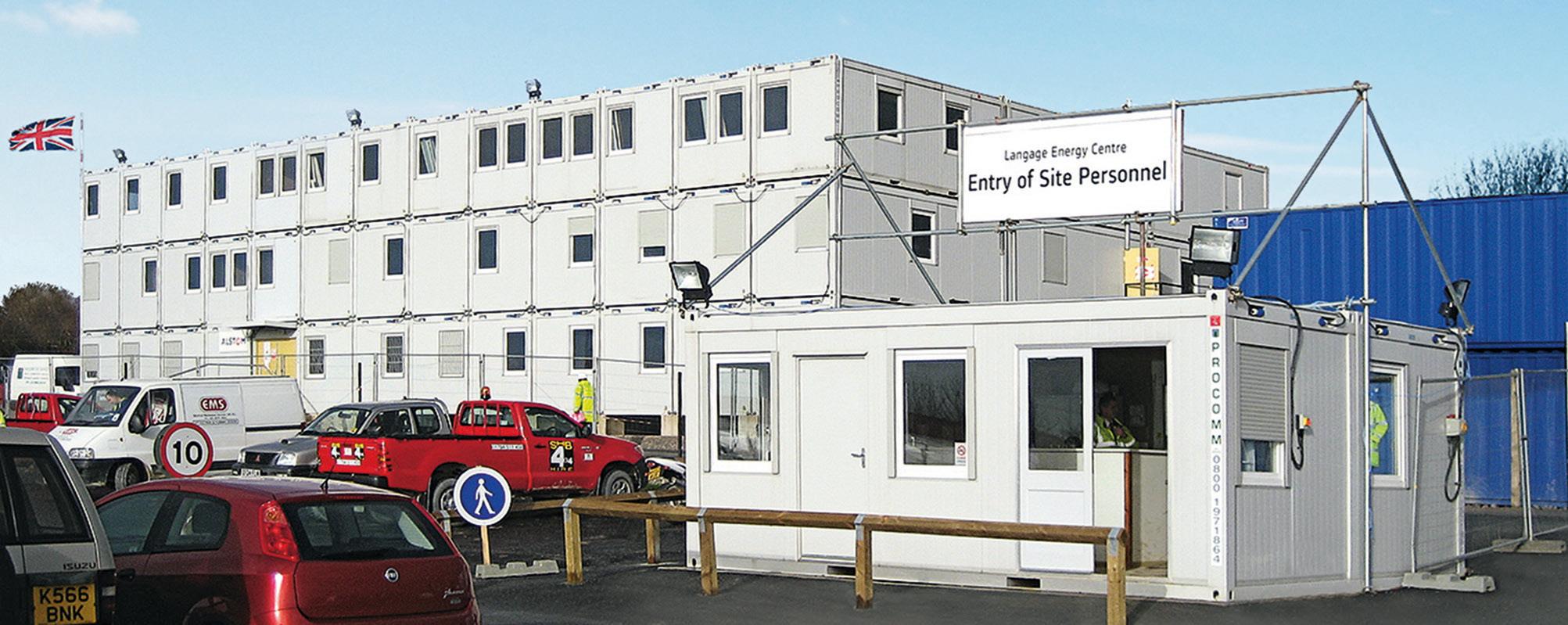
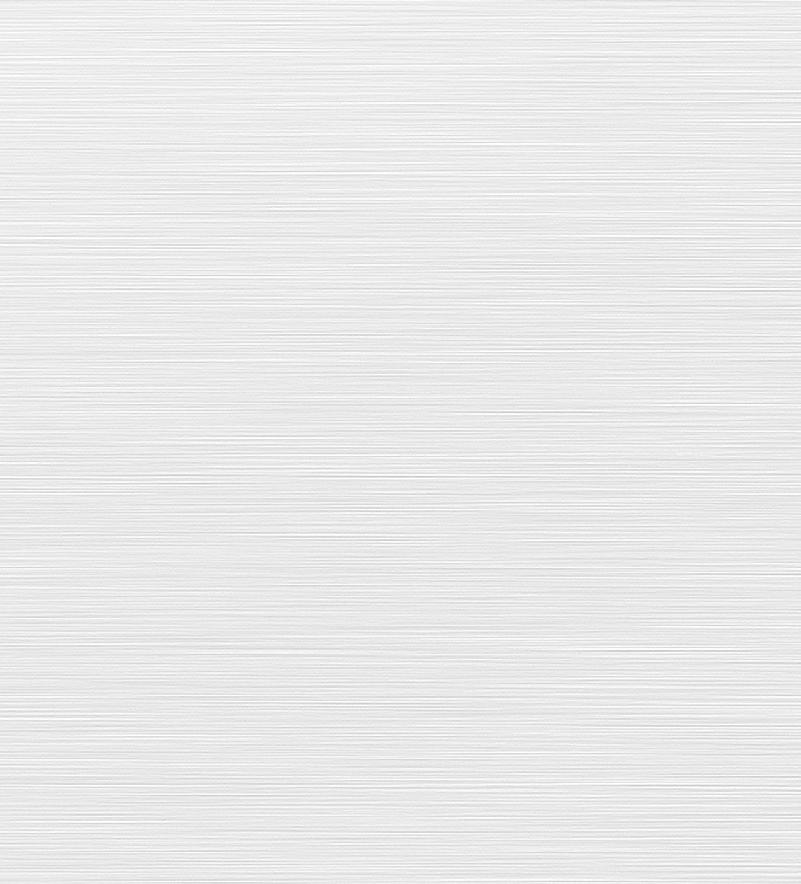

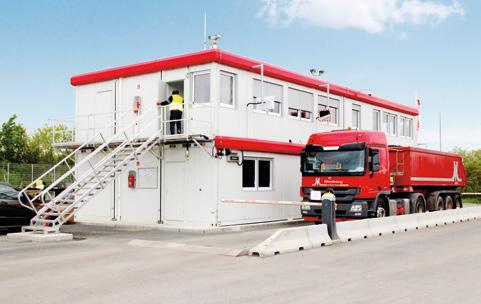

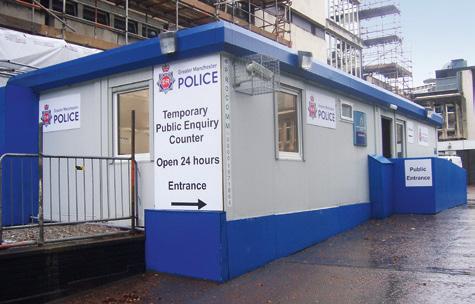
Contact us: Free Phone: 0800 458 0386 • E-Mail: sales@containex.com www.containex.com


Is construction ready for automation?
The controlled environment of construction sites makes them the perfect playground for exploring automation – bringing real-life benefits in terms of productivity, safety and fuel efficiency. But how far advanced is construction automation? Johanna Huggare, manager Intelligent Machine Platforms, at Volvo Construction Equipment (Volvo CE) explains more…
The construction industry has been automating processes for decades. The automatic gearbox and climate control are just two examples, relieving operators of the responsibilities of changing gear or turning the heating up and down. But these are not the processes that spring to mind when we hear the word automation. No, we think futuristic, driverless. As the technology continues to mature at a rapid rate, just how close are we to adopting these futuristic concepts on tomorrow’s construction sites?
IT’S ALL ABOUT THE DATA Over the last few years, we have seen machines fitted with increasingly advanced systems that are less dependent on operator skills but are not yet fully autonomous, ones that support operators with guidance or control primary functions. Take the Volvo Co-Pilot and its range of intelligent Assist applications that help operators deliver higher quality outcomes, in less time and with lower effort. For example, Volvo CE’s excavation machine control system – Dig Assist – allows operators to take measurements from inside the cab. The system automatically calculates exactly what material has been taken, from where, and what the current levels are. This represents savings in time and money, as well as improving safety.
Furthermore, the construction industry has also been drawing on more advanced Artificial Intelligence (AI) to aid automation. AI allows a new level of sophistication to be reached – where machines ‘talk’ to each other in a bid to boost total site productivity. However, AI needs large amounts of data in order to work, which is partly why industries like finance, banking and entertainment have been some of the more successful early adopters.
Yet construction is catching up. The industry is starting to capture more and more data out of machines and that is what is now allowing us to build the infrastructure needed to develop advanced algorithms. At Volvo CE we’ve made huge advances in after-market, customer support and mobile applications. And now with even more data at our disposal, we are starting to use AI for more things, such as automation and driver support systems. Combine this with the controlled environments of today’s jobsites and you have the perfect playground for making automation a reality.
But data is no use if you don’t have the guaranteed network connection to safely and effectively manage this technology. To address this connection issue, we are one of the lucky few to test a 5G network for industrial use. We are currently teaming up with Telia and Ericsson to test remote-controlled machines and autonomous solutions in a real application. This is allowing us to explore the boundaries for automation and see what challenges and benefits arise as a result.
ELECTRIFYING SHOWCASE We first showcased the potential for driverless automation in 2018, when we partnered with our customer Skanska, to create the world’s first ‘emission-free’ quarry. Drawing on the electromobility and automation expertise of the Volvo Group, we electrified each transport
stage of the quarrying process – from excavation to primary crushing, and transport to secondary crushing. As well as electric wheel loaders and excavators, the project also involved eight HX02 autonomous, battery-electric concept load carriers. These machines were fitted with a vision system, which allowed them to detect humans and obstacles in their vicinity and also follow a pre-programmed GPS path.
The Electric Site demonstrated how the level of operator assistance is transforming the overall productivity of machines. And it’s not just productivity that was enhanced – safety increased as accidents caused by human error were eliminated. Autonomous machines also perform repetitive tasks more efficiently and precisely than human operators. And because machines operate in the most efficient way, customers benefit from improved performance, productivity, fuel efficiency, and durability. The results were tangible. During the 10-week project there was a 50% increase in fuel efficiency, 40% reduction in operator cost, a 70% cut in energy costs and a 98% reduction in carbon emissions.
CHANGING ATTITUDES We can clearly see the benefits that automation brings. But what of the challenges? One of the main issues is attitude. In a survey – carried out on behalf of Volvo CE – almost half of construction workers we spoke to feared safety could be put at risk by automating tasks. Here at Volvo CE we are working hard to address these concerns. The Electric Site project highlighted the reduction in accidents when humans were taken out of dangerous working environments. But removing humans from the equation raises other concerns.
For example, the same study highlighted concerns about how automation would affect job security. Machine operator roles were perceived to be most at risk – according to almost half of the respondents (48%). However, experts agree that while the job of an operator will change with increasing automation, some tasks are so complex and unpredictable that the operator needs to feel what’s happening, and in those cases, we will always need operators controlling the machines.
In addition, as machine autonomy increases, the operator will generally act more in a supervisory capacity. In fact, there is actually a shortage of trained skilled operators, so instead of taking away jobs, automation could create safer, less stressful and more interesting work for operators, with perhaps several machines being controlled remotely by one operator at a time, thus boosting efficiency for the customer.
BRINGING AUTOMATION TO LIFE Ensuring our customers are benefitting from our research and development – and working together to test its potential – is the key to making automation a success. From next month, Volvo Autonomous Solutions will deploy a fleet of concept autonomous haulers in a commercial pilot with customer Harsco Environment. Although, the technology is not yet available to the market it is one step closer toward industrialization.
It’s clear that fully autonomous machines will not suddenly arrive. The journey, in the construction industry at least, will come in stages. Currently, we are working on creating machines that can perform a number of simple, largely repetitive, applications fully autonomously, while other applications remain semi-autonomous for the foreseeable future.
It’s not just the machines that are changing. As we move into a more autonomous future, we will see changes in work site layouts and working hours. Autonomous machines will be able to facilitate 24/7

and 365 days a year working. Operators will no longer need to work in harsh and sometimes remote environments – they’ll be able to control machines from the comfort of an office that is maybe hundreds of miles from the site itself. With technological advancements we will be able to customize the behavior of the machines to fit specific applications. Who knows, maybe we’ll see autonomous Volvo CE equipment used for off-earth space mining.
But let’s come back down to earth for a moment. To make automation work, customers have to want it. Some of our customers would be happy to use autonomous machines today, while others prefer to wait until the technology is more mature. Until now, it has been difficult to build a compelling business case for automated construction equipment, largely because the technology that sits behind it is expensive. Current trials are highlighting the benefits that automation brings to the construction industry. But for fully autonomous construction equipment to become commonplace, we’ll need to see acceptance and trust in the technology, a reduction in cost and an increase in the pace of technological change.
It’s safe to say this is the same amount of change as when dedicated construction machines were first invented a century ago. It’s at that same level of disruption and it’s a wonderful time to be part of it.
The road to optimal performance incorporates a combination of autonomous product development and digital transformation. ■
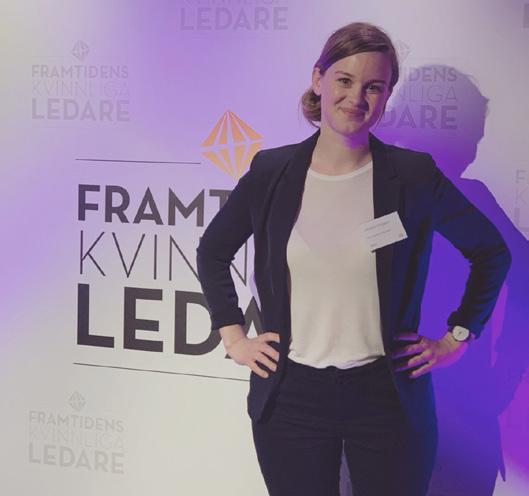
Johanna Huggare is manager Intelligent Machine Platforms at Volvo CE. She and her team of 20 people are working to explore, develop and industrialize the technology of the future. In order to find their way among all the information, Johanna and her employees work closely with a number of universities, research institutes and partner companies around the world. They are in contact with technical experts and futurologists and work closely together with customers and suppliers. They also play a key role in spreading and building knowledge within the organisation.
KEEPING YOU AND YOUR SITE SAFE
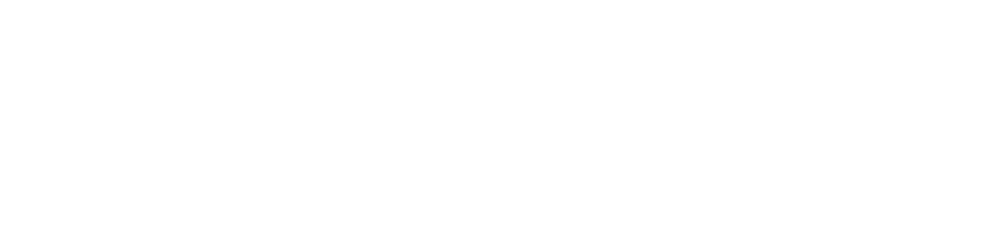
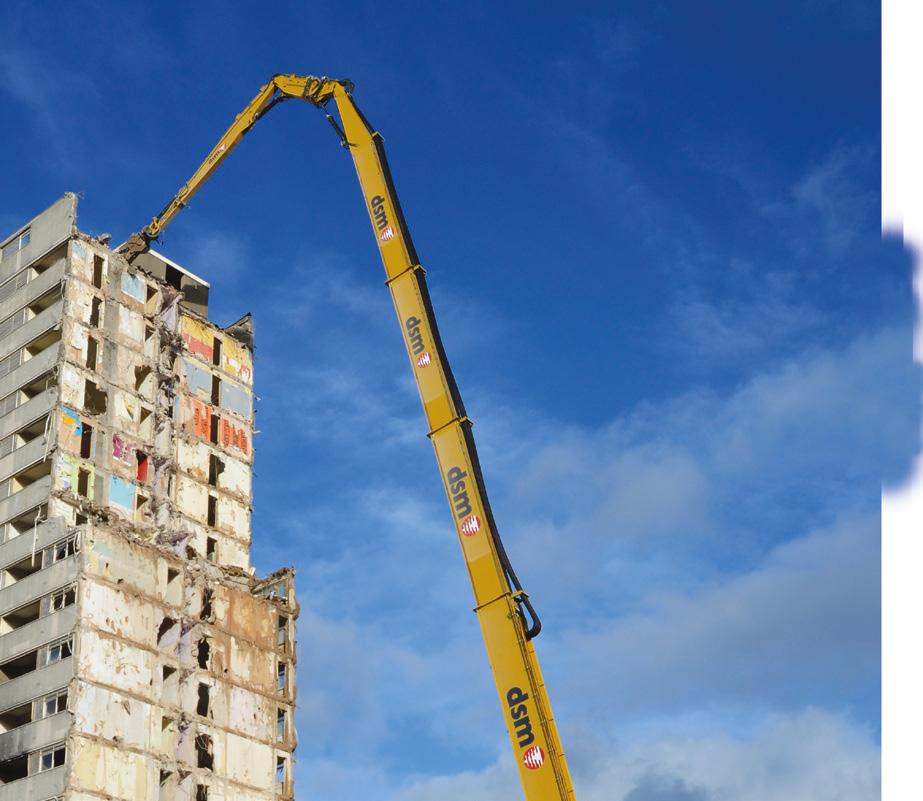
SLEW
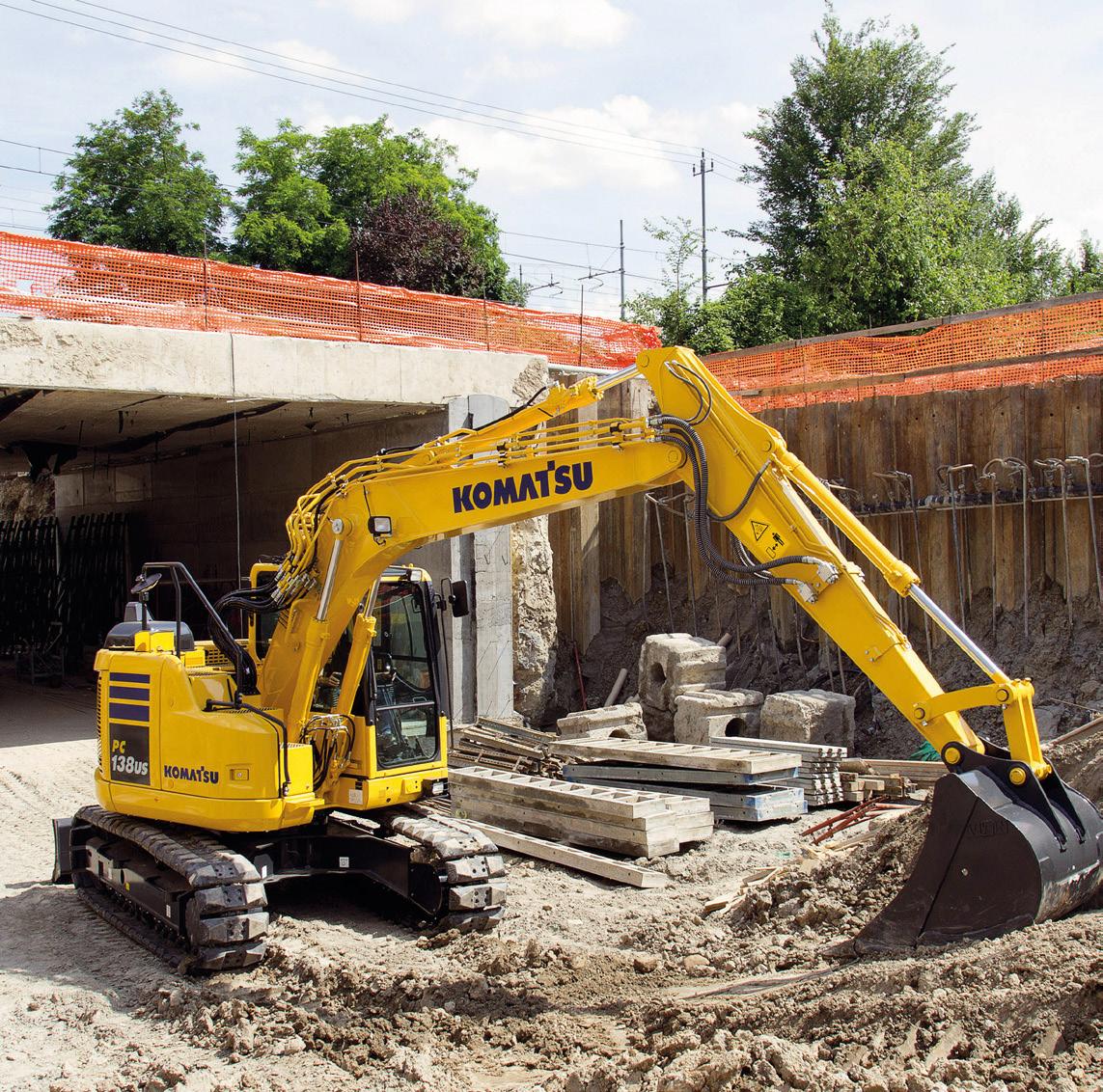
HEIGHT KG LOAD
GKD systems - easy to install and easy to operate.
Manufacturers of the most intuitive motion safety indicators on the market, enabling your operators to work more safely within your site’s height, slew and load restrictions.
Reduce risk and improve productivity by choosing GKD Technologies.
Visit us online at gkdtec.com Call 01202 971 972, E-mail sales@gkdtec.com
TELESCOPIC DEMO
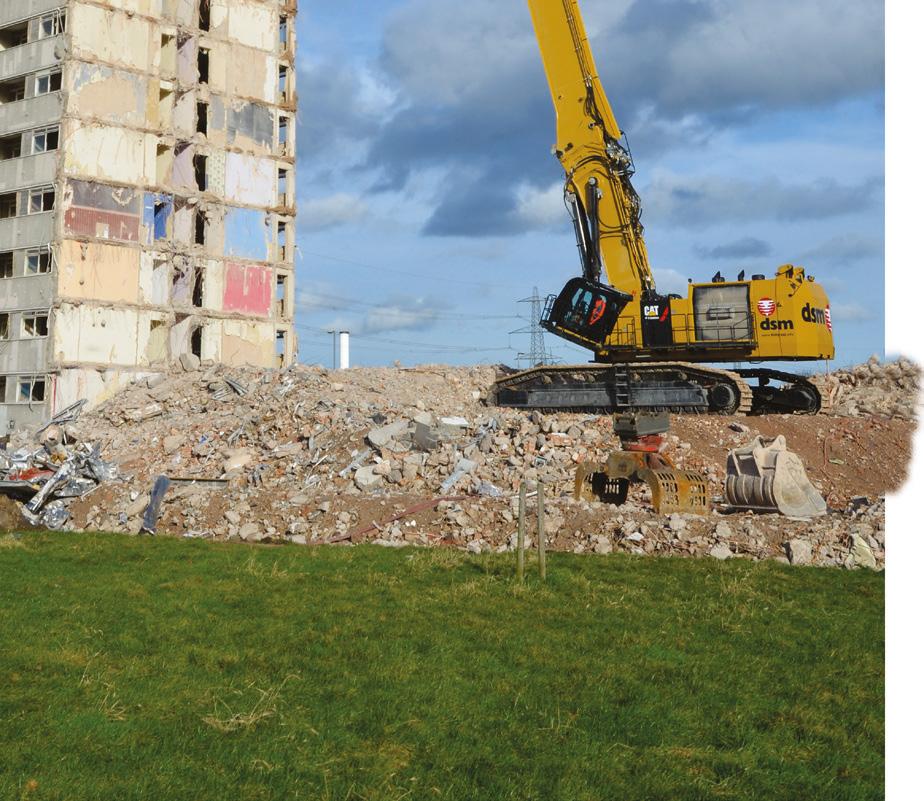
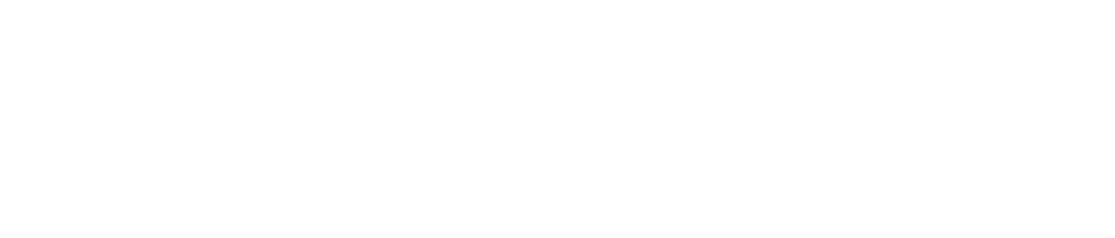
Be sure to get the most out of your demolition equipment with Kocurek Telescopic High Reach Equipment. Operating heights range from 34m up to 70m. Speak to the experts to find out full details on our extensive range. t: +44 (0) 1473 217477 e: sales@kocurek.co.uk www.kocurek.com
Generating financial support for digital investment
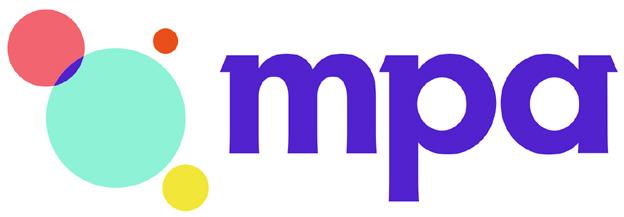
The MPA Group is a CEA partner. Iain Warburton from MPA is looking at ways that they can help members with their R&D and development activity
The impact of technological advancement is changing the landscape for many businesses across all sectors. It’s no surprise that the construction industry is moving under the spotlight as construction equipment begins to face the same digital disruption felt in the automotive and commercial-vehicle sectors.
Machines are becoming increasingly automated and connected, enabling operators to deploy them more efficiently. As customers adopt building information modelling (BIM) this will accelerate the deployment of smart, connected heavy machinery. The challenge is how to fund the investment in this innovation.
Funding help is available As part of the drive to make the UK more competitive globally, HMRC is happy to cut your tax bill or pay you cash if you can satisfy their technical requirements. Over £4.3 billion was ‘paid out’ in R&D tax credits in the last reported statistics with an average SME claim value of £50,000.
Less than 1% of Construction SMEs are claiming Less than 1% of SMEs in the broad construction sector (around 1,800 companies) are claiming R&D tax credits and given that construction represents around 7% of GDP and that there are more than 250,000 construction SME’s this seems too low. Nervousness about what activity qualifies and the risk from HMRC’s quality drive could be at the core of this. Activity qualifiers are covered by simple phrases: “attempting to resolve a scientific or technological uncertainty” and so technical expertise as well as tax expertise is required to make a successful claim.
Expert advice at no cost Irrespective of whether you are claiming or not, we can provide valuable advice to help. If you’d like specialist advice on R&D Tax opportunities in your business at no cost, then contact our advisor Iain Warburton on 07519 070636. Iain.Warburton@mpa.co.uk
TOOL THEFT HAS INCREASED BY 65% OVER THE LAST 2 YEARS
DON’T LET THIS HAPPEN TO YOU!! Protect Your Tools - Protect Your Livelihood - with Tool Defend!
If you own a van and valuable tools, for your business to run efficiently on a day to day basis, you are taking a huge risk if you don’t put extra security measures in place to prevent theft. Consider the effects of having your tools stolen:
• Loss of a day or weeks work – timescale changes affecting other trades • Downtime spent replacing tools and sorting out vehicle repairs • Loss of customer contract • ‘Repeat Target’ - thieves return weeks later – YOU ARE A SOFT TARGET!!!


PROTECT YOUR TOOLS! Contact: Geoff Reyner | 07951 585171 | blaydesales@aol.com
Amber Valley Developments
THE FUTURE IS MBER Europe’s Largest Manufacturer of Reversing & Safety Systems