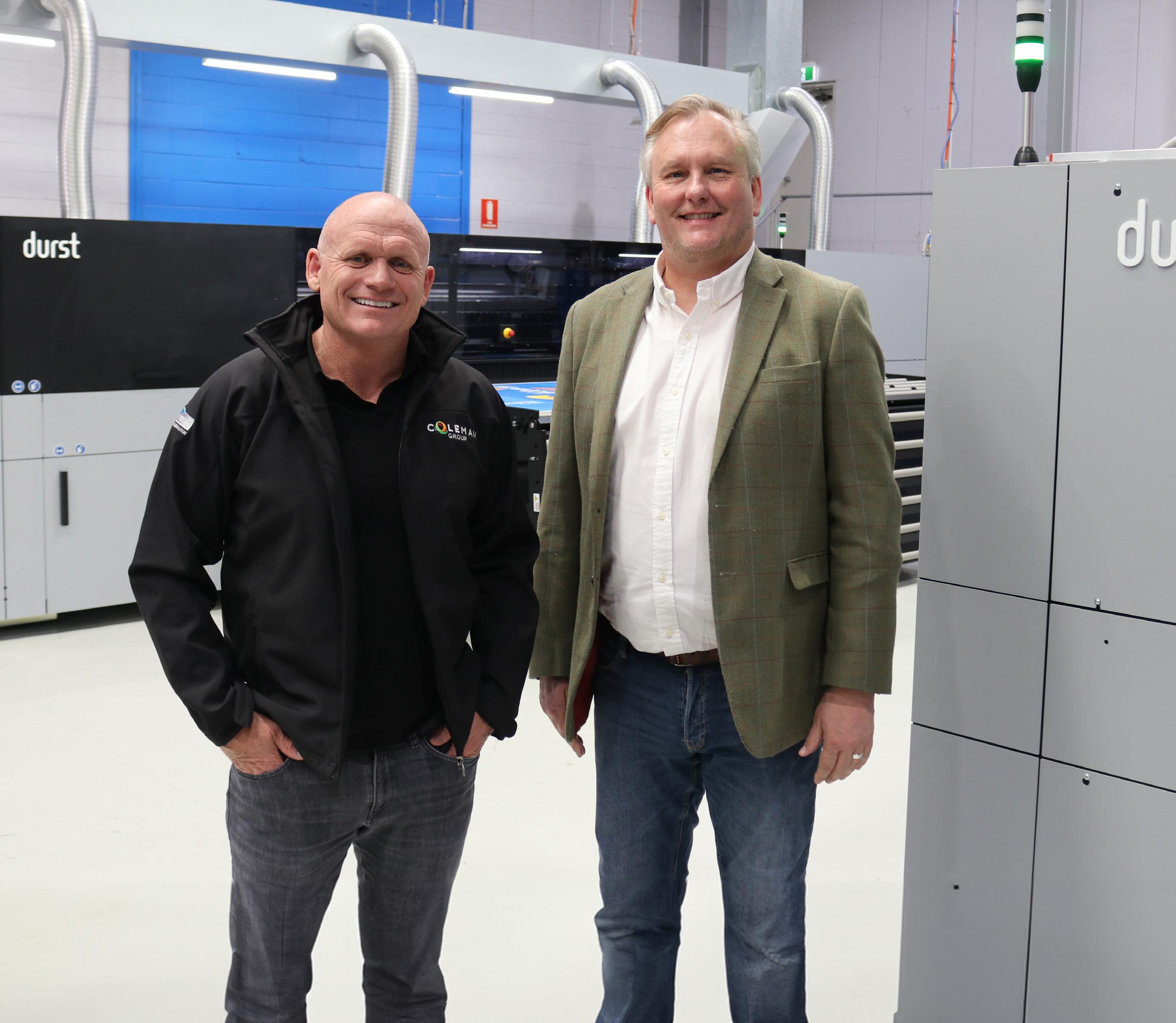
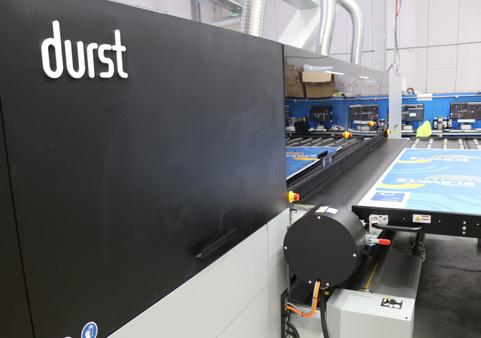
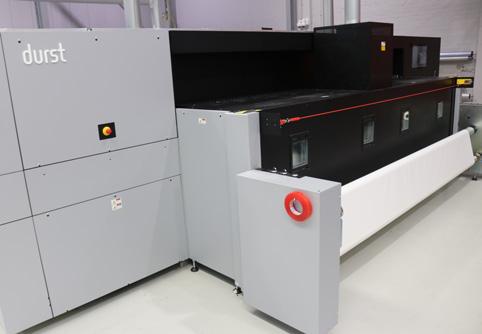
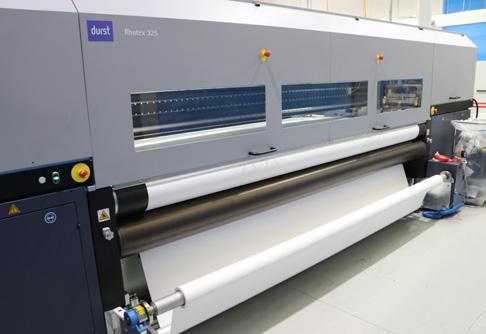
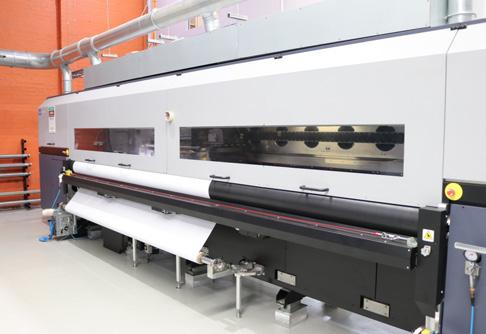
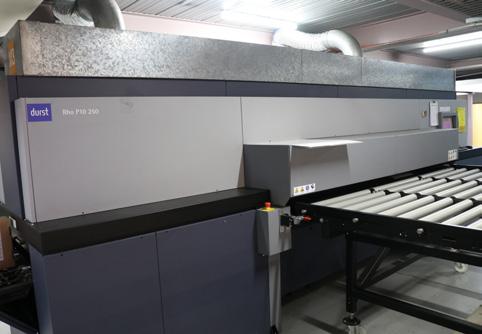
The Vanguard Digital VK300D-HS is the impressive high speed version of our six-time award winning VK300D series.
In this edition of Australian Printer, we’ve rounded up some of the industry’s leading brands to talk about their latest innovations in our inaugural Supplier Showcase. Off the back of the new technologies unveiled at this year’s FESPA Global Print Expo and drupa, the need to stay ahead of the curve when it comes to product innovation has never been more critical.
Not only that, but today’s solutions also need to address the everchanging challenges faced by the commercial printing industry. Whether it be speed, productivity, or delivering on sustainability – those featured in our Supplier Showcase are all the leading the way in their respective fields.
Also in this issue, we speak to Cactus Imaging’s Karen Lawler about social responsibility and how Cactus is leading the way to be green. CMYKhub’s COO Clive Denholm weighs in on the state of the local industry, and entrepreneur Shivani Gupta examines the true cost of having the wrong people in your business.
IVE Group has shared details of a new acquisition completed in May with 40 staff members in Sydney and Melbourne that has already been successfully integrated into the business.
“We stated 12 months ago that we were implementing a strategy to diversify and expand our Creative and Content offering,” IVE CEO Matt Aitken said while delivering the results for the last financial year ending 30 June 2024.
“We felt it was important for IVE to upscale its Creative and Content business to capture additional market share from our customers as well as accessing new revenue streams, markets and customers.
“To accelerate that expansion, IVE acquired Elastic Group at the end of May, an independent creative agency that specialises in video content creation and visual communications. Elastic’s Sydney and Melbourne operations, including 40 staff, have been relocated and integrated into IVE’s existing sites in Sydney and Melbourne.
“Creative and Content has been a core part of our offering for over 20 years. As fragmentation of the media landscape and proliferation of marketing channels has significantly increased the type, volume and frequency of content required for effective omni-channel marketing.
“Our initial focus has been on talent and capability – expanding the breadth and depth of service offering across strategy, creative, content, production and technology. Elastic retains a very impressive portfolio of customers across automotive pharmaceutical, government, sports and entertainment, food and beverage, finance and property.
“IVE now consider ourselves to have an unrivalled in-house marketing agency capability, providing customers with a streamlined and simplified way of producing ideas and content for every marketing channel.”
Aitken said the acquisition was modest in terms of size and was not reported to the ASX, however it does represent a business that is now very strategically important.
IVE Group also reported a revenue of $969.9 million (up by 0.3 per cent from the pcp), EBITDA of $127.8 million (up 7.5 per cent from the pcp) for its FY24 financials.
Managing Director
James Wells / 02 8586 6101 james@intermedia.com.au
Subscriptions / (02) 9660 2113 subscriptions@intermedia.com.au
Subscription rate (5 issues) Australia $79
Managing Editor
Claire Hibbit / 0432 796 384 chibbit@intermedia.com.au
Printed by Hero Print Alexandria, NSW, 2015
National Sales Manager
Carmen Ciappara / 0410 582 450 carmen@proprint.com.au
Mailed by D&D Mailing Services Wetherill Park, NSW, 2164
Design and Production Manager
Sarah Vella / 0406 967 559 svella@intermedia.com.au
Peter Harper, CEO of Visual Connections, has announced he will retire at the end of the year, bringing to a close a career of more than 50 years in the print, sign and graphics sector.
Harper, who founded the original sign industry supplier association some 30 years ago and has been at the helm of Visual Connections for the past 18, said he feels the time is right with a strong board and operational team in place.
“Of course, I have mixed feelings, but I know it is the right decision for myself and for the organisation, to allow fresh leadership as we continue to develop our industry events and other exciting initiatives,” Harper said.
The Visual Connections board was advised of Harper’s decision in January this year at the organisation’s board strategy meeting, giving them plenty of time to plan but, with a number of key projects underway, the decision was made to hold off on the official announcement until after the recent Visual Impact exhibition.
With the hugely successful Brisbane show now concluded, and planning progressing well for the flagship PacPrint 2025 trade show in Sydney, Harper said the time is
right for a smooth and orderly transition to new leadership – a process the Visual Connections board said is well underway.
Mitch Mulligan, president of the Visual Connections board, said Harper embodies the Visual Connections’ mission, which is to contribute to a sustainable future by supporting its members – the industry’s suppliers – and the industry more broadly, through education, exhibitions, sponsorship, grants and networking opportunities.
“As well as cementing the success of the Visual Impact expos, Visual Connections has, under his leadership, also successfully taken on the organisation of PacPrint, which is co-owned by Visual Connections and Visual Media Association, significantly improving the value for exhibitors and the returns to industry through these associations’ funding of initiatives and resources,” Mulligan said.
“He has proven to be an exceptionally talented negotiator and a kind and steady leader through some of the most challenging times the industry has ever faced, not only bringing the organisation through but, in the process, strengthening its effectiveness and resilience.
“While the events are a very visible sign of his achievements, one of his greatest
legacies will be an initiative which is set to deliver significant benefit to the industry for many years to come – the Sign & Print Career Connections program.
“Conceived and piloted initially with the Australian Sign & Graphics Association (ASGA), this is now, through Peter’s hard work and collaborative style, an industrywide initiative which is actively recruiting new talent to the sector.
“Peter has always been an inspiration to me and many others, and has always set an incredibly high standard.”
– Keith Ferrel, Cactus Imaging
“Peter is highly valued not only by the Visual Connections board and membership, but by his staff for his constant leadership, encouragement and generosity. He is also widely respected across the industry for his pragmatism and outstanding effectiveness in ‘getting the job done’, and his willingness to consider – and drive – innovation to deliver value to the industry.
“While his steady leadership and many talents will be greatly missed, the Visual
Connections board is excited about the future, with a strong team in place and several strong candidates in the running to take on this pivotal industry role,” Mulligan said.
According to Visual Connections, Harper is keen to focus on the future, with six months of hard work still ahead of him before handing over the reins.
“Peter will be deeply missed by the Visual Connections Association and its board, but also the entire industry. His legacy will continue to inspire and guide us. I can only wish him all the best in his retirement as we move forward in this new chapter.”
– Andrea Trumble, Pozitive Sign & Graphics Supplies
“I have been in the industry for some 50 years and have enjoyed every one of them,” he said.
“Over the past 18 of those years, I have worked with some great teams at Visual Connections, but none better than the current team who I know will continue their great work under the new leadership. I look forward to watching them, and the industry, continue to go from strength to strength.
“Whoever takes on the role will have an amazing team, and great support from one of the best Boards in the business. I am forever grateful to all the board members that have supported me during my years with VISA and Visual Connections, to our
members who consistently demonstrate their loyalty and commitment to our industry, and to the wonderful people who have worked for, and with, me over those years.
“I am still here till the end of the year, and am very much hoping I will get a chance to say thank you and goodbye to as many people as possible, as we continue to work towards a brighter future for the print, sign and graphics sector.”
Industry pays tribute to Harper’s legacy in print and signage
The printing industry also paid tribute to Harper’s contribution to the industry following his retirement announcement.
Kellie Northwood, CEO of the Visual Media Association (VMA) said Harper has offered a strong leadership across merged associations (GAMAA and VISA), trade show development and flexible navigation through COVID.
“He carries a legacy of engagement and leadership to the suppliers across our industry that will be missed. I, and the Visual Media Association board and members, wish Peter the very best in his next life chapter and thank him for his contribution to the industry,” said Northwood.
Mick Harrold, president of the Australian Sign & Graphics Association (ASGA), thanked Harper for his contribution to the industry.
“Congratulations Peter and thank you for all your hard work. The sign and print industries are in your debt for your efforts over many years. I and the ASGA will miss your support and advice.”
Keith Ferrel, co-founder and general manager of Cactus Imaging, said Harper’s leadership of the Visual Connections Association, its events and exhibitions – particularly during Covid – has been extremely important to the growth and sustainability of this sector and has delivered enormous value to the printing industry.
“Peter has always been an inspiration to me and many others and has always set an incredibly high standard,” said Ferrel.
Andrea Trumble, marketing manager at Pozitive Sign & Graphics Supplies and Visual Connections board member, said Harper has shown exceptional leadership, unwavering dedication, and visionary contributions that have helped to shape the sign and print industry.
“Peter will be deeply missed by the Visual Connections Association and its board, but also the entire industry. His legacy will continue to inspire and guide us. I can only wish him all the best in his retirement as we move forward in this new chapter.”
Mark Canavan, marketing and vendor relations manager at Graphic Art Mart and Visual Connections board member, said Harper is a calm, experienced, and pragmatic leader who has always been willing to support the industry and its members.
“The signage and wide format digital print landscape has evolved enormously over the last 25 years, and Peter has helped guide the association and deliver successful exhibitions and education programs over this period of time,” said Canavan.
“His experience and guidance will be greatly missed, but I feel that Peter leaves the industry in a strong position as we move into the next phase of its evolution. I want to personally wish Peter and his family all the very best for his retirement and for what the future holds in store for them.”
Tony Dalleore, secretary of the FPLMA, said Harper has always been an extremely ethical, passionate, and well networked icon for the industry.
“This is exemplified through his recent drive to expand the highly successful education initiative to a significantly broader scope within our industry with the aim of attracting talent. On behalf of the FPLMA, we congratulate Peter on his wide range of achievements which will continue to foster into the future.”
Harper will officially retire at the end of December, with the board expected to announce his successor well before this date.
The Durst Group has celebrated the 25th anniversary of its branch in Lienz, Austria.
“Durst Austria GmbH is an essential part of the Durst Group, and we aim to continue growing in the coming years,” said Christoph Gamper, CEO and coowner of the Durst Group.
“Our branch in Lienz is a shining example of technological innovation and commitment to the highest quality standards.”
The 25th-anniversary celebrations include a special exhibition of group portraits and street banners by renowned South Tyrolean artist, Klaus Pobitzer.
The exhibition is a continuation of the successful “Inside-Out” project previously implemented in Brixen, South Tyrol. Pobitzer’s artworks, which will be displayed in both the city of Lienz and on the premises of Durst Austria, feature large-format individual and group portraits, as well as technical details of the manufactured printing systems.
“Since its founding 25 years ago, Durst Austria GmbH has developed excellently as a subsidiary of the Durst Group in the
sunny city of Lienz,” said Elisabeth Blanik, mayor of the city of Lienz.
“It is a driver of research and innovation, a hidden champion with an international orientation. In addition to its research and production activities at the site, Durst Austria has also sustainably integrated itself into the socio-political fabric.
“The company acts as a generous supporter and continuously promotes art, culture, and social institutions in the region. As a community, we are very proud of Durst Austria’s achievements, congratulate them on this wonderful anniversary, and sincerely thank them for their outstanding social engagement. We wish them continued innovation, economic success, and a thriving economic environment for the future.”
Headquartered in Brixen, South Tyrol, the Durst Group comprises more than 20 subsidiaries and joint ventures worldwide. Since its establishment, the branch in Lienz has developed into an important production site for digital inkjet printing systems, according to the company.
Over the years, the site has been continuously expanded and modernised. A significant milestone was the construction of the research centre in the form of a
“mountain crystal” in 2009, which is one of the world’s leading laboratories for inkjet printing technology.
In the past 25 years, Durst Austria has brought forth numerous innovations. Notably, the co-development of Durst inkjet technology, setting new standards in print quality and efficiency. Another crucial factor for the Durst Group’s success is the integration of state-of-theart software solutions developed by the subsidiary PrePress Digital GmbH (PPD) in Lienz. This software significantly improves the usability and efficiency of the printing systems, enabling better control and management of the printing processes.
More recent developments focus on eco-friendly printing solutions for the packaging industry and the integration of digital technologies to optimise production processes.
Gamper said the 25th anniversary of Durst Austria is an occasion to proudly look back on past achievements while optimistically looking forward to the future.
“Our branch in Lienz is a symbol of the Durst Group’s progress and innovative strength. We look forward to many more successful years.”
FESPA Australia has announced renowned entrepreneur and former executive director and CTO of Lonely Planet, Gus Balbontin, will be the keynote speaker and workshop facilitator for the FESPA Australia Annual Conference on 25 October at Sydney’s Shangri-La Hotel.
The FESPA Australia Conference is co-located with the 2024 ProPrint Awards, which will be held on the evening of Friday 25 October 2024 at the Shangri-La Sydney. The ProPrint Awards, the largest industry event of its kind in Australia, celebrates and honours excellence in the Australian printing industry.
Nigel Davies, president FESPA Australia, said the association is excited to welcome Balbontin to its annual conference in Sydney, where attendees will have the unique opportunity to learn from his vast experience and innovative approach.
“His keynote address and facilitation of the leadership workshop promise to deliver invaluable insights and practical advice that will inspire and equip participants to tackle their own business challenges and drive success.
“Gus’ storytelling prowess and passion for making a tangible difference in people’s lives have made him a sought-after speaker, so we are delighted that he will set the scene for our conference,” said Davies.
Sponsors of the FESPA conference include: Diamond Sponsor – Orafol, Gold Sponsors – Durst, Visual Connections, Silver Sponsor – HEXIS, IVE Group, Cactus Imaging, Bronze Sponsors – Ball & Doggett, Pozitive, HVG Graphics Media, and Kissel & Wolf.
Sponsors of the 2024 ProPrint Award include: Platinum Sponsor – Durst, Gold Sponsors – Ball & Doggett, FUJIFILM Australia, HP, IVE Group, Omnigraphics, and Pozitive Sign & Graphic Supplies, Silver Sponsors – ABC Copiers, Böttcher Systems, Cactus Imaging, Graph-Pak, Konica Minolta, Kurz Australia, Lamont Sustainable Sign Solutions, PAKKO, Ricoh Australia, Spicers Australia, Xeikon, EFI, Auditing partner – PKF.
Women in Print has announced Sharna Beck, HP Indigo Digital Press operator from Southern Impact, as the winner of the 2024 HP Dscoop giveaway.
Beck will travel to APJ Dscoop in Cebu, Philippines, where she will join a global community of HP Graphic Arts users, industry leaders and innovators for a unique opportunity to network, learn and grow alongside some of the brightest minds in the printing industry. HP will cover all related travel, accommodation and seminar entrance costs for her to attend.
The prize was awarded following a comprehensive process. Entries from around the ANZ region were evaluated by a trans-Tasman panel, including Ruth Cobb, PrintNZ; Charlotte Gorham, P.O.S Visual Solutions; Lorraine Fox, On Pack; Samantha Thomson, Prima Printing; and Kimberley Skinner, Total Digital Solutions, and WA Patron for Women in Print.
Beck’s digital print journey began in 2018 in the mail room at Southern Impact in Victoria, where she trained on several digital presses before later joining the company’s digital department as an HP Indigo digital press operator.
Within a year, Beck completed training on the HP Indigo Series 3 and Series 4 digital presses, making her the only digital operator at Southern Impact with the ability to run all four digital presses, which include three Indigo Presses: an HP Indigo 7600, HP Indigo 7800 and B2-sized HP Indigo 15K Digital Presses.
“During my time with Southern Impact, I have found a real passion for the printing industry while learning from other technicians and advancing my skills on the job and gaining great pleasure from seeing the results of my print production efforts,” Beck said.
“When I was fortunate enough to be offered a new role in the digital department, I jumped at the chance to work alongside a fantastic digital team, where I’ve quickly become entrenched as the only operator in the department who can operate all four digital presses, validating my love for printing and for achieving customer satisfaction.
“I love my new career, where I have industry-leading technology at my fingertips, and I feel as if the opportunities I have been given have actually changed my world.”
Stephanie Gaddin, chair of the Women in Print board, said the organisation was thrilled to partner with HP to provide this opportunity.
“As anyone who has attended Dscoop will attest, the experience is a gamechanger and we know the opportunity will deliver immeasurable potential impact for Sharna,” Gaddin said.
“We are confident that taking part in APJ Dscoop Cebu will not only not support Sharna’s career development by providing unparalleled insights and information, but will help expand her horizons and grow her professional network as she makes new connections from across the globe.
“This aligns perfectly with our mission to support and uplift women in our industry.”
Beck is supported by her employer, Southern Impact, who provided a glowing reference in the entry process.
“Sharna is a passionate member of our digital family here at Southern Impact, and we love her enthusiasm,” said Rod Mills, production manager – commercial digital, Southern Impact.
“We value our people and the culture we have created here, and we are so proud of Sharna’s achievements – to be trained on the largest press in the digital fleet within a year of moving into the digital family is
a credit to her dedication and skill. She’s a superstar,” Mills said.
Wendy Coss, committee chair for Women in Print Special Projects, presented the prize to Beck at Southern Impact.
“This giveaway is a testament to the collaborative spirit of Women in Print and our commitment to professional development for women of all levels within our industry,” said Coss.
“We are grateful to HP for their support and thrilled for Sharna, who we know will use this experience to go on and do amazing things in this industry.”
For their part, HP said they are delighted to sponsor the initiative, saying it is an important way not only to further career opportunities for the winner, but to shine a spotlight on the achievements of women in the sector.
“HP is proud to partner with Women in Print to support this initiative. Dscoop is all about community and innovation, and we believe Sharna will bring back invaluable knowledge to share with her peers,” said Craig Walmsley – HP South Pacific Industrial country manager.
“Our goal is to empower professionals in the graphic arts industry, and we are excited to see how this opportunity will inspire and impact the Women in Print community.”
The Visual Media Association (VMA) has announced the resignation of board president, Matt Aitken, at its recent board meeting, with the association also electing new board officers and office bearers.
Aitken has been president of the VMA for two years following significant industry board director roles with his initial appointment to the former Print & Visual Communication Association (PVCA) in 2016, the treasurer, deputy chair, then chair office bearer positions on the Australasian Catalogue Association (ACA), and chair of The Real Media Collective.
“Having given over eight years of service to the industry, as well as supporting two major mergers initially with ACA and TRMC, then TRMC and VMA, I feel now is the right time to step down and for the board, and the association, to enter its next lifecycle evolution,” said Matt Aitken, president, VMA and group CEO, IVE Group.
Kevin Pidgeon of Lithocraft, and former deputy president, has been elected president with Stuart Fysh of The Label Factory, elected to deputy president from his secretary role held for four years. Kirsty Woodhead, Breen Printing, has been elected secretary with Rodney Frost, retaining his role as treasurer. Simon Bailey, IVE Group, GM – NSW, was also recently elected to join the team to fill the casual vacancy.
Heidelberg has started the new financial year 2024/2025 with strong growth in incoming orders following a successful drupa.
According to Heidelberg, the company’s incoming orders in the first three months (April 1 to June 30, 2024) exceeded its own expectations of around €650 million at €701 million (previous year: €591 million). The best order value since 2016 thus forms a strong basis for the entire financial year with a high order backlog of €923 million (March 31: €652 million).
The regions of Europe (+25 per cent) and the Americas (+30 per cent) recorded
Aitken has overseen significant evolution across his leadership of all industry associations he has been involved with, including, but not limited to merging several organisations to form a single peak industry body under the VMA.
According to the association, ”building board diversity and skillset unmatched in previous history, and current practice, across the industry was another significant achievement.”
Double digit year on year membership growth, engagement and stability, of TRMC through COVID was also credited to Aitken.
“The recent TRMC and PVCA merger into the VMA is absolutely the best way
particularly strong growth. Growth was only slightly weaker in Asia (+3 per cent), as the previous year had been particularly strong due to Print China.
“The strong recovery in our order intake allows us to look to the full financial year with great confidence,” said Jürgen Otto, CEO of Heidelberg.
forward, the united board has a common dedication to how one industry body is the best for all of industry,” said Aitken.
“I want to thank each and every board officer for their support and I know I leave the organisation in very safe hands in the leadership of Kevin Pidgeon,” said Aitken.
”I also want to thank Kellie [Northwood, CEO of the VMA]. Over much of my industry board roles, she has held the executive position and always worked with dedicated passion to the members and industry, pushing every opportunity and I believe she will continue to deliver for the industry with the association in a much stronger place.”
Pidgeon is no stranger to market, working across many roles in the sector for some 60 years and within industry associations for 20 years.
“I thank Matt for all his years of service and appreciate his significant contributions whilst also having a very large role across the IVE business. I thank my fellow board officers for their support in electing me as president and look forward to working with the industry across the association’s new programs and commitment to the industry,” said Pidgeon.
“Thank you to all I have worked with in the industry roles, I will remain a strong supporter and assist where I can. I continue to support a single industry association for our industry and urge any companies not members to contact the team and get involved, we can achieve so much more together with a united stronger approach,” said Aitken.
“The pleasing order backlog from the drupa trade fair will lead to rising sales in the following quarters compared to Q1. At the same time, we are working on our cost situation and personnel costs, which are generally too high.”
As expected, sales in the first quarter of €403 million were below the previous year’s level (€544 million) due to the reluctance to invest ahead of drupa.
In the print solutions segment in particular, Heidelberg recorded strong drupa-related growth in incoming orders of around 21 per cent. In contrast, sales declined by around 23 per cent from April to June due to the low order intake in the third quarter of the previous year.
Incoming orders in the packaging solutions segment improved by 17 per cent, while sales in this segment fell by 29 per cent as expected.
The Visual Media Association (VMA) has launched a new insights program to promote the role of the letterbox, and the print within it, to consumers across Australia and New Zealand.
Following a collaborative approach from industry, government, Australia Post, and key stakeholders, the VMA will lead the transTasman project focusing on how Aussies and Kiwis use their letterboxes and the print they receive within it – from letters to bills, statements to catalogues, magazines to flyers.
The program, Open Up to Mail, will build quantitative metrics and qualitative responses developed from focus groups and consumer surveying. Research content will be developed and shared with government, brands, retailers, and key stakeholders, providing insights into the role of the letterbox across societal balances and consumer trends through regular industry insight events being hosted
Wildstone has made two significant hires in its recently launched venture, which is headed up by Noel Cook, who was appointed managing director in May.
The owner of outdoor media infrastructure across the UK and Europe has now added Mitch Cook as its commercial director for Australia and Amber Burbidge as a commercial executive. Both previously worked for oOh!media.
Mitch Cook’s 18 years in the industry have been split between Australia and the UK, with stints at Ocean Outdoor in the UK and in the advertising team at London City Airport. His most recent role was product director for small format at oOh!media. At Wildstone, he will focus on leveraging partnerships between landowners and media partners, driving revenue growth, and advancing the company’s goal to further digitise Australia’s OOH sites.
He will work with Burbidge, whose 20-year career prior to Wildstone
The program will build quantitative metrics and qualitative responses developed from focus groups and consumer surveying
across Melbourne and Sydney, with livestreaming to other states and territories.
“We know from our recent focus groups that younger people now call ‘junk mail’ the emails they receive in their Inboxes, further, people working from home use the ‘trip to the letterbox’ as a ‘break’ from being inside,” said Kellie Northwood, VMA CEO.
“These shifting trends in media consumption are reflected in how we interact with the letterbox, and as digital saturation levels are reached, the letterbox is a powerful and effective channel for government, banks, telcos, utilities and retailers to reach each and every home.”
The research will run across three years and be independently conducted by research agency, The Source.
Open Up to Mail will explore the views of cyber-security and digital scam concerns to personal information, the usefulness of catalogues and magazine advertisement through letterbox distribution, consumer sentiment to switch off from digital, and the societal balance the letterbox plays across Australia and New Zealand.
“The industry has long been campaigning the benefits of the letterbox and never more so than throughout the consultation to the modernisation into the postal service,” said Northwood.
“This process working with government, Australia Post, and key stakeholders, identified the need to develop an exploration of the role of the letterbox across our regional communities, educational channels, financial management and general societal balance.
“Our industry is one of the largest manufacturing employees across the country and a significant contributor to the economy across. We are sovereign manufacturers, delivering a 100 per cent recyclable product and proudly part of the societal schematic. We welcome the educational insights to share with major mail users and our communities as a whole.”
was at oOh!media. Her most recent role was senior commercial executive, where she was responsible for driving innovation and expansion, primarily in the realm of digital billboards. She will have a similar remit at Wildstone, and will be involved in strategic planning and market analysis.
Wildstone also recently announced its entry into Australia’s A$1.07 billion OOH market in May as part of the company’s international expansion. The overseas drive follows its growth across Europe, where it has acquired and developed more than 5000 static and digital OOH assets since 2010.
Damian Cox, founder and CEO of Wildstone said, “Our entry into the Australian market got off to a flying start when we secured Noel Cook as managing director earlier this year. We’re thrilled he’s now brought some of his most trusted and experienced former colleagues into the business.
“Mitch’s experience in both the UK and Australian markets will be invaluable as we work to replicate our European success in Australia. Meanwhile, Amber’s two decades of expertise gleaned from various roles across the sales, operations and commercial divisions of the OOH industry will significantly enhance our capabilities.”
The Sign & Print Career Connections initiative enjoyed its final major outing for the year in Sydney, where hundreds of students engaged with the team at the Sydney Careers & Employment Expo at Hordern Pavilion, Moore Park.
The expanded and improved 2024 program, hosted by Visual Connections, coordinated by Australian Schools Industry Partnership (AusSIP), has proven to be a success, travelling to careers expos in five states this year.
The program, which is designed to help attract new talent to the print, sign and graphics sector, was conceived more than 10 years ago and designed and piloted by Visual Connections and AusSIP in partnership with ASGA. Earlier this year, it was expanded to include the entire print and graphic communications sector, when FESPA Australia, FPLMA, LIA, and VMA came on board.
Sarah Moore, general manager of Visual Connections, said the Sydney
Close to 100 attendees participated in ASGA’s annual Queensland Golf Day at the Brookwater Golf & Country Club in Brisbane.
With 88 registered players, and quite a few more industry personnel attending to cheer from the tee offs, it was a strong turnout for one of the most eagerly anticipated events on the ASGA calendar.
Damian Nielsen, ASGA member and events manager and Queensland state president, said it was a fantastic day of fun and networking.
“Brookwater is a fantastic venue, and it was an absolute pleasure to see the connection and camaraderie made within, and between, the teams who took part today, so I’d like to send a huge thank you to everyone who took part,” he said.
The format of the day was an Ambrosestyle competition which prioritises fun and team participation over skill levels.
event is proving, once again, that visual communications careers can be a career of choice for senior students considering their future.
“There is no more pressing issue in our sector than the need for new talent, but we know that ‘if you can’t see it, you can’t be it’,” Moore said.
“Sign & Print Career Connections is designed to make our often-overlooked sector visible, and to showcase the diverse and exciting range of careers which are available across creative, technical, practical, sales, administration and management areas in print,signage and visual communications.
“The response of students, parents, teachers and careers counsellors at the Sydney Careers & Employment Expo has once again proven that, when young people can see the options available, they respond very positively, with many following up via the Sign & Print Career Connections online or talking directly to training providers to explore training and apprenticeship opportunities,” Moore said.
Joining Tina Mavris and John Watters from AusSIP on the stand in Sydney were representatives from TAFE NSW, TryA-Trade sponsors Bounce LED, Pozitive, Techie Tools and Prytec Solutions, and other industry volunteers. The AusSIP team also took part in the Girls Tech Day, introducing hundreds of primary school aged girls.
The Sign & Print Career Connections program is made possible with the cooperation of industry associations ASGA, FESPA Australia, FPLMA, LIA and VMA. It is also supported by major sponsors: Amari Visual Solutions, Ball & Doggett, Cactus Imaging, Fujifilm Graphic Systems, Graphic Art Mart, Mulford Australia, ORAFOL, Pozitive Sign & Graphics Supplies and Sign-a-Rama, and partnering sponsors Böttcher, FPLMA, Hero Print, MacDermid Graphic Solutions and Spicers.
A range of prizes were also up for grabs, from ‘Nearest the Hole’ to the hotly contested ‘Survival Ball’, keeping everyone on their toes. Following the game, prizes were presented over lunch at the course’s prestigious Club Rooms.
This year, Tri Vision took out the winner’s trophy for the first time, after their team scored an outstanding 55.62 adjusted to take home the first place in a very close competition. They were followed by HVG at 56.37 adjusted, and then SEQ Signs at 57.12 adjusted. The everpopular ASGA members draw went to Miles Plastics.
A highlight this year was the introduction of a new ‘Best Dressed’ award, with Maurice O’Sullivan from team KRZ and Darron
Ryan from Tri Vision, announced as joint winners of the inaugural prize.
Sponsors of the event included: Principal sponsor, HEXIS; ORAFOL, who sponsored lunch drinks and prizes; Graphic Art Mart for the Survivor Ball and Franco Brotolin Tropy (NTP); Visual Connections who sponsored drinks and the on-course drinks cart, and to Novelty and Individual Hole sponsors ASMI, Bounce LED/Lettertech, Bentleigh Sign Group, CV Media and Signage, HVG, Mulford, Rowmark, SA LED, Shann, Signarama, SMIB Insurance and Spicers.
“We are looking forward to our next Golf Day in Melbourne on 2 October and are already well underway with planning for similar events on our 2025 events calendar,” Nielson said.
Mimaki Australia has undertaken a restructure of its channel management roles to grow its business further in the local market.
Under the changes, Mimaki national sales manager, Jason Hay, has relocated from Sydney to manage the business from Queensland, and as a result, well-known industry executive Chris Morrison has been appointed to join the channel management team based in Sydney.
Morrison joins Mimaki with over 20 years of industry sales experience including 11 years with Fuji Xerox, six years with EFI and three years with Fujifilm Business Innovation.
“I was looking for a new opportunity and I have always admired Mimaki as a brand as well as its great product range,” Morrison said.
“I visited Visual Impact recently and I spoke to a number of companies in the room. I had a great conversation with Kohei and Jason, and it just so happened that they were looking for a new channel manager – so I guess it was serendipity.”
Hay has confirmed that Morrison will take over channel management responsibilities in New South Wales, South Australia and Western Australia.
“With Chris coming on board, it strengthens the industry knowledge of our organisation and I think he will be a very important addition to our business and the growth of our brand,” Hay said.
“It is important that we recruit the right people to key roles within our organisation to take Mimaki to the next level of growth. We play in six different ink technologies and we are always creating something new and different for our customers – in the dealer network and our end users – the people who use the machines.
“Over the past 11 years, our growth has been astronomical – starting at 1.8 per cent market share of the 1.6m and below category and we are now averaging 25 per cent share in this category. For us to grow further, we are introducing innovative industrial products to the market, including the new TRAPIS textile printing technology with significant wastewater savings launched at Drupa earlier this year.
“We have four important national dealers – Spandex, Spicers, Graphic Art Mart and Fujifilm – and they do a great job across our Signage & Graphics, Industrial and Textile & Apparel products. This national dealer network is supported by a secondary network of satellite dealers with state-based responsibilities. We have three separate showrooms located at Rydalmere
in Sydney, Morningside in Brisbane and Mulgrave in Melbourne that house over $1 million worth of Mimaki hardware.
“We now have 25 staff members and half of these are service and support staff that have a very clear understanding of our customers’ needs, wants and time frames.
“Our growth is the reason why we have had to recruit more people to the business. I doubt you would be able to find a manufacturer in our industry over the last two to three years that has hired more channel managers and six engineers.”
The three state offices for Mimaki Australia now consist of six staff in Queensland, with Jason Hay supported by a marketing manager and three engineers; there are eight staff in Sydney with two channel managers – Chris Morrison and Roger Corby and seven engineers; and in Melbourne there are four staff members with channel manager Cameron Bongartz supported by three engineers.
Mimaki Australia recently showed off the latest and greatest of its technologies –including its recently launched Mimaki UCJV330-160 – at the company’s recent Brisbane Open Day in Morningside.
Mimaki national sales manager, Jason Hay, who will soon relocate from Sydney to Brisbane, said the UCJV330-160 is part of the company’s 330 Series that offers high image quality, high production, and application versatility.
The UCJV330 Series is a print and cut UV-LED inkjet printer that combines productivity and image quality with Mimaki’s UV printing technology. This flagship model is also equipped with advanced UV-LED technology.
While inheriting the conventional two through five-layer printing functionality, this is Mimaki’s first roll-to-roll product that supports 2.5D printing. This machine is also equipped with unique features such as watermark printing.
“The Brisbane Open Day has allowed us to showcase our latest technologies to our customers and dealers. Mimaki is a very innovative business. We’re the only company in six different ink technologies
in the market. And at Mimaki Morningside, we’re trying to showcase as many of those as possible,” Hay said.
“Sustainability is huge for Mimaki – all of our machines on this showroom physically run off a 10 amp or a 15 amp single phase power point, which enables our customers to have far better power saving than our existing models, or even our competitors’ models.
“For example, the UCJV330-160 would probably use almost eight times less power than a conventional solvent printer or latex printer.”
Mimaki Morningside’s other equipment on display included its UJV100-160, its JV100-160, its CG-130AR, CG-160FXII Plus and CG-60AR cutters, its CJV300160 Plus, its UJF-6042MkIIe, its JFX2002513 EX, and its 3DFF-222 3D-printer.
The UJV100-160, which was launched about three years ago, is an entry-level UV-LED model with excellent operational performance. With two newly developed heads, NCU (Nozzle Check Unit), NRS (Nozzle Recovery System), MAPS4 (Mimaki Advanced Pass System4), and DAS (Dot Adjustment System), the machine reduces workloads on an operator.
The company has since launched the Plus model to this machine, which allows for three-layer printing and a new, unique ink saving function that’s available on its new current models – the UCJV330, JV300 and JFX600.
As for the JV-100-160, it is an eco-solvent inkjet printer that also consists of NCU, NRS, and MAPS4 technology. Mimaki Australia has developed a new ink set with a 35 per cent saving over the existing model. This entry level starts from $19,995
excluding GST and ink cost per cartridge is $165 for a 600ml bladder.
Mimaki’s CJV300-160 Plus is an older model that prints about 11 sqm an hour (sellable output), while the newer CJV-330 Plus models print at 21-30 sqm an hour in the same in colour configuration.
Its CG-130AR and CG-160FXII Plus cutters offer through cut and kiss cut capabilities, at different speeds. They both now work with Mimaki’s ID Cut feature.
Mimaki’s UJF-6042MkIIe is a flatbed UV inkjet printer for promotional products. This has further improved image quality and machine stability, while maintaining the
operability that was highly acclaimed in its predecessor UJF-6042MkII model.
As for the Mimaki JFX200-2513 EX, it is the company’s fastest selling UV flatbed. It is a large format flatbed UV inkjet printer that combines high-value-added printing and high productivity, while being an entry model.
“This is the fastest selling four by eight flatbed in Australia. Today, it has the fastest return on investment for a machine that only uses three head technology. Our competitors use 10 heads for the same speed. It’s just the way we’ve got our print heads configured, which enable us to print at 35 sqm an hour and on anything up to 50mm in thickness for substrates,” Hay said.
In addition, it had on display its 3DFF222 3D-printer, which is a desktop 3D-printer using Fused Filament Fabrication technology, and forms objects of sizes up to 200mm by 200mm by 200mm (W x D x H).
“Our growth in Queensland has been exceptional. We started Mimaki Brisbane in a small 45sqm office about eight years ago. Since then, we have gone from strength to strength – moving into a 125sqm unit in Murrarie, then relocating from there to our current Morningside unit. We’ve got about 250sqm of floor space here,” Hay said.
“The showroom is also good for our dealer networks as well. We use it as an education centre, an experience centre, an application centre, and use it to offer training courses for service engineers.”
Mimaki Australia has a national dealer network consisting of Spicers, Spandex, Graphic Art Mart and Fujifilm. Its localised satellite dealers are Sign Essentials, Velflex, G2 PSD and Charti.
Wayne Chapman has been appointed to manage the national textile business for Mimaki, based in Brisbane.
According to Hay, Wayne’s extensive experience with Konica Minolta, Fujifilm, Sensient Inks and Sun Chemical will provide additional benefits for the business.
“Wayne will be an important addition to the team with over 20 years of experience in the textile segment, and we expect he will strengthen our relationships even further. With the recent launch of TRAPIS, Mimaki will continue to be a key player in the textile market,” he said.
“In the Brisbane office, Wayne will be joined by both myself and Craig Dainty (Qld service manager, Stephen, Bevan (engineers), as well as Chris Dutkowski in marketing.”
Coleman Group recently added on a Durst P5 350 HS large format printer and Durst P5 TEX iSub dye sublimation printer to sit alongside its Durst Rho 325, Rho 512R and Rho P10 250 machines.
Glenn Coleman can’t remember exactly when he bought his first Durst as it was so long ago, but since then he has bought another five machines that are all operating on the floor of his event and exhibition signage business in Sydney.
“We bought our first Rho 800 in either 2007 or 2008 when Durst was managed in Australia by PES. Nine years later we upgraded to the Rho 325 and Rho 512R and that was six years ago. We also have a Rho P10 250 – and they all continue to operate today,” he said.
Last year, Coleman added more firepower to his business with the introduction of a P5 350 HS and a P5 TEX iSub dye sublimation machine. After a significant reorganisation on the floor of his factory, Coleman now has two Durst textile
“We have found the new Durst P5 TEX iSub has been great – it can print direct on to certain fabrics and creating jobs directly is a huge advantage. We also print to paper on this machine as well. I would recommend it for people that maybe don’t want to invest in a separate finishing machine for dye sublimation.
“The P5 350 HS was a machine we loved as soon as we saw it at the Durst factory in Brixen in February 2023 after attending the Euroshop exhibition at Düsseldorf. It has been going very well since it was installed late last year.
“We put similar work through the older Durst machines as the new machines,” Coleman said.
“Our customers are very deadline driven – we just can’t not deliver – it is not an option and that is why we have Durst, why we chose Durst originally and why we have stuck with Durst.”
While some companies have only recently started seeing a move towards more sustainable materials including fully recyclable exhibition materials –Coleman claims this trend is not new.
Durst Oceania managing director, Matt Ashman, is not only the supplier of machines and consumables to Coleman Group, but has also experienced what it is like to be a customer as well.
“It is great to continue the relationship we have with Glenn, Rod and Coleman Group. We chose Glenn and Rod ourselves to launch Durst Oceania at PrintEx in 2019.
“Coleman Group built our stand and created all of the graphics and they did an amazing job – the entire stand was erected and installed by the team. And sometimes the concept doesn’t always meet the expectation from a design perspective – not from a printing perspective. And when it needed to be changed – it was reprinted within hours.
“They use their five Durst machines like Ferraris – and they have a superb garage featuring high performance equipment ready to go to meet a deadline.
“These machines are all top-quality examples of European engineering and Italian manufacturing that have been specifically chosen and calibrated to do a job. Even if they are not operational
all day every day like other businesses, they are sitting there just waiting to be ready to win the race for not only Coleman Group, but for the customer.”
When asked if this will be his final Durst purchase, Coleman reluctantly disagreed.
“We expect to have another Durst when we upgrade again in a few years from now.”
The P5 350 HS large format printer
The P5 350 HS is a hybrid solution for roll and board printing of up to 3.5m and a productivity of up to 708 square metres per hour. Fast media change, easy maintenance handling and full safety are only a few of the reasons that Coleman Group render the printing process way more efficient.
The P5 350 HS is a fully integrated machine that makes the increasing complexity in large format printing more manageable. The printer is equipped with the Durst Print Workflow software and the monitoring tool, Durst Analytics. Coleman Group finds that the P5 350 HS provides optimum performance, from pixel to output.
The P5 TEX iSUB is a dye-sublimation printer with an integrated inline fixation (iSUB) for a one step direct to fabrics printing process. The Durst P5 TEX iSub’s contactless fixing technology ensures excellent colour consistency, as well as sharpness of detail in images and text. Blurring or bleeding of colour is also eliminated.
A wide range of applications on polyester material can be implemented with the new dye sublimation printer, such as light box and decorative fabrics including difficult media as blackback and flags.
However, the printer is not limited to direct printing. Transfer papers can also be printed and further processed in the usual way – a plus for the needs of Coleman Group.
The Rho 512R is a super-wide 12 picolitre roll-to-roll UV inkjet printer with Variodrop technology. With a print quality of up to 1200dpi and at speeds of up to 385 square metres per hour, the Rho 512R has allowed Coleman Group to print a variety of large format advertising materials by handling three 1.6m rolls simultaneously.
The Rho 512R is equipped with Variodrop technology and uses multiple impulses for modulating the droplet size.
Thus, the exact amount of ink is placed, which prevents drop satellites that are more common in conventional grey-scale printing. Unattended printing and very low production costs have also enabled the Rho 512R to be one of the most economical printers for the business.
With the 3.2m Rho 325, Coleman Group can utilise a dual-purpose printing system that combines directto textile printing with dye sublimation transfer printing technology. Depending on the application and fabric, this printing system can alternate between paper transfer and direct printing on polyester-based materials quickly.
This is possible because of Durst’s WTS printhead technology, which achieves an exceptionally highquality print using water-based, environmentally friendly dispersion inks for various printing materials, and a print speed of almost up 390 square metres per hour.
The Rho 325 is also equipped with an integrated hot air dryer, automated nozzle cleaning system, and additional features for 24/7 production reliability.
The Rho P10 250 inkjet printer enables Coleman Group to deliver quality work within industrial print production.
The printer combines speed and quality without compromising either. Furthermore, just like previous flatbed and roll-to-roll printers, its ability to print on the widest range of rigid and roll media provides Coleman Group with the ability of unrivalled and convincing versatility.
Equipped with the Durst Quadro Array 10 print head technology, this system achieves a print quality of 1000dpi without loss of speed. This also applies to the use of light colours. The compact and robust print machine for industrial production is also designed for non-stop printing with minimum downtime.
Friday 25 October 2024
Scan to purchase your ticket
Photographer turned printer Colleen Raven Strangways shares her print journey and what she is doing to help create more career pathways for women in print.
Colleen Raven Strangways first started her Adelaide-based business, Nharla Printing, in 2019 after entering the world of print as a side business to support herself and her young family.
Prior to Nharla Printing, Raven Strangways was working full-time as a social worker for Life Without Barriers,
and as a part time photographer. A proud Arabana Mudburra Wirlpiri mother of two young boys living on Kaurna country in Adelaide, Raven Strangways soon found working multiple jobs and being away from her young family wasn’t very sustainable. Moving into print was the answer, allowing Raven Strangways to use her existing skills in photography and Adobe products to
create Aboriginal artwork for printing and sale.
“Ever since I was a kid, I have always been creative,” Raven Strangways told Australian Printer
“I first got into photography around 2010, and a few years later decided to take the leap and make it my full-time job for
a better work/life balance. But I soon learnt that photography can be seasonal – it ’s either a feast or a famine – and I needed something else to support my family.
“I first got into printing using a Cricut at home, and then eventually moved into sublimination. However, I was starting to get frustrated because I was limited to the size of an A4 print area.”
It was then that Raven Strangways first met the team at Adelaidebased Graphic Arts Supplies.
“We first met Colleen in 2021 when she came into Graphic Arts Supplies and bought a small dye sublimation printer and a heat press,” Steve Murphy, sales director at Graphic Arts Supplies, told Australian Printer
It took Raven Strangways no time at all to master the dye sublimation printing, and she quickly reached out to The Circle, a First Nations entrepreneur hub, funded by the Federal Governments’ National Indigenous Australians Agency, in partnership with the South Australian Government. The Circle supports and collaborates with First Nations entrepreneurs, businesses, and emerging First Nations business owners.
As the business was still small and the budget was tight, it was agreed by Raven Strangways and the team at Graphic Arts Supplies that the Roland VersaSTUDIO BN20A Solvent Printer (small entry model) was the right machine.
“That really opened up a lot of opportunities for me and printing soon started to overtake my photography business. I could print and cut stickers, heat transfer, dye sublimation, and produce small signage,” she said.
By mid-2022 Raven Strangways had purchased two additional machines from Graphic Arts Supplies: a Roland GS24 Cutter and Epson F2160 DTG/DTF to help keep up with demand. This allowed the business to also offer even more services, including direct to garment, direct to film printing, as well as faster cutting.
For the next two years, Raven Strangways focused on building her business and expanding her offering. The equipment she started with when the business first began was the right solution for her capacity at the time, but she was now seeking an upgrade for her growing business.
Continuing to work with The Circle, Raven Strangways was providing printing services for several large enterprises. However, for her to really capitalise she knew she needed to upgrade her equipment. She again turned to the team at Graphic Arts Supplies to find the right solution for her business.
She needed to print larger stickers, wall art, wall papers, floor decals and larger signage. She, and the team from Graphic Arts Supplies, settled on the Mutoh 1341.
“This compact solvent printer with serious quality and capability was the answer for Colleen and her business needs,” Murphy said.
This allowed Raven Strangways to go from printing 500mm wide to 1341mm wide. Also having a separate cutter maximised her workflow and increased her speed and output nearly 10-fold.
“Her new Mutoh 1341 solvent printer, paired with a Mutoh VC21300 cutter, has allowed Colleen to print much larger prints up to 1300mm wide x 50 metres and cut files to the same width. This is in line with business expectations allowing her to support larger more demanding clients and provide commercial grade printing and applications in house rather than outsource,” Murphy said.
This has helped improved turnaround times, proofing, and overall service offering. Raven Strangways can now also print small stickers 5cm in size all the way up to car wraps, floor and window decals and even building signage.
“Having better equipment has enabled me to secure larger jobs,” said Raven Strangways.
“I ’m now working with government agencies and a major retailer in Adelaide. My long-term plan is to expand the business and bring others in to take on some of the work. I want to be able to tender for more government contracts as well as be able to provide a pathway for more women to get into the print industry.
“I learnt from late nights watching YouTube and learning through my own mistakes. Graphic Arts Supplies have supported me, and I want to be able to offer other women the same opportunity and guidance.
“I’m of the belief that there is no competition. It’s all about collaboration and I believe that’s the key to being sustainable and successful in this industry. I feel like there’s enough work here for everyone so having partnerships and sharing the workload only helps us all succeed.”
Murphy said Raven Strangways’ success story means so much to everyone that knows her.
“For us at Graphic Arts Supplies, we could not be happier to watch someone start with the smallest of printers and work to where she is now. It is nothing short of spectacular. Colleen is the most wonderful person, a mentor to her community, and a successful woman in print,” he added.
Cactus Imaging business development manager Karen Lawler discusses her career highlights, the importance of social responsibility, and how Cactus Imaging is leading the way to be green.
Can you tell us a little about your career and how you started in print?
Before working in print, I worked in hospitality and event management. I worked for seven and a half years for a major hotel group in Sydney’s CBD and loved it, but it burnt me out. I then worked for an IT company, but it wasn’t the right fit for me. I joined Cactus Imaging in my current role in 2017. I did have a very short stint as a pre-press assistant with Torch [Publishing] when I was younger, so I came to the role with a very basic understanding of print, but not of digital print, so it was a steep learning curve. The great thing about this job and the print industry is that there’s always something new to learn. My role changes quite a bit on a day-to-day basis, with different jobs coming through – it can be anything from a birthday sign to a large-scale building wrap. I also have a substantial client base, between 300 and 350 clients the last time I counted, which also keeps it interesting.
What have been some career highlights?
For me, what comes to mind when it comes to career highlights are some of the projects I’ve been involved with and the impact these projects have had. One project that stands out is the Woolworths Indigenous art building wrap on George Street in Sydney’s CBD that we did in 2022. The largescale artwork, ’Ancient Tracks’, which was also designed by
Indigenous artist, Toby Bishop, was made from mesh and wrapped around scaffolding on the façade of the Woolworths building across from Town Hall. Social responsibility, both personally and professionally, is something that is important to me, so I was proud to have been involved with that project.
Another highlight was Cactus’ involvement with the ASEAN-Australia Special Summit this year, which saw leaders from ASEAN and Australia all come together in Melbourne. It was more than 150 individual fabrics and 2200sqm of work for one event. It was hectic, but seeing all those leaders standing in front of fabric that I worked towards getting there was very cool. Another rep I work with did a large mesh print during the NRL’s Indigenous round for the Brisbane Broncos. Seeing that on the field on the TV was also exciting To be involved in some capacity with events like these, that have an impact on people, is a very rewarding part of the job.
The ProPrint Awards is always a great night. It’s great to catch up with everyone in the industry and for all of us to let our hair down and celebrate our hard work. There are so many amazing people in this industry, so to have been previously nominated was also special.
What do you enjoy most about your role and the print industry?
The people – not only the people that I work with, but also the people that I meet
across all aspects of the industry. One of the things that I love about working at Cactus Imaging is our team. We have a small sales team – there’s four of us in Sydney and one in Melbourne – and I know that if I’m away, I can always rely on the team. When I first started, Nigel [Spicer] told me Cactus Imaging is like a family-run business, and it really does have that feeling. What I also love is how many aspects there are to the print industry and going to events like the ProPrint Awards opens your eyes to how big this industry is.
What do you think the industry can do to help attract, engage, and retain more people?
A lot of people think printing is a dying art, but I think there’s always going to be a need for print. I think it’s important for us as an industry to continue to raise print’s profile. While there’s also a place for digital, there’s a real art when it comes to traditional printing, which needs to be celebrated. If we’re looking at ways to get more people in the industry, then we need to sell it with its biggest asset – the people. It’s such a great community to be a part of. I grew up around motorsports and there were instances where you were made to feel excluded as a female, but you don’t get that in this industry. There are more women entering the industry too, which is great to see, but I think we still need to do more to encourage that.
What’s next for you and the team at Cactus Imaging?
Sustainability is a big focus for the Cactus team and we’re always looking at new ways of how we can implement more sustainable and socially responsible practices into the business and our operations. It’s not only important to us, but it is also increasingly important to our clients. Last year, we won the Outstanding Achievement in Sustainability Award at the ProPrint Awards for our development of Ecobanner, in conjunction with oOh!media and Gale Pacific. Ecobanner is a fully recyclable material that is manufactured in Australia using cleaner and more sustainable processes than PVC. Winning the award was a really proud moment for the whole team to be recognised for our work in this space. It’s important to us that as a company, we are leading the way in to be greener.
1800 Projects’ Ben Browning and Brent Nassibian have evolved their business to not only keep it well ahead of the curve, but to also deliver on innovative and premium branding solutions for their clients.
Founded in 2006, 1800 Projects was initially created to produce branding solutions for action sports events. It has since grown to become a multiple award-winning company that produces premium branding solutions for brands large and small.
1800 Projects managing director Ben Browning tells us more about the business and what keeps it going.
Q: How did you end up in this industry?
Ben Browning (BB): My corporate background started while I was working in action sports events. I gravitated to the branding side of events and found myself communicating with brands and ensuring they got great coverage at the event or on TV. I came up with the idea to create 1800 For Promo (what 1800 Projects was formerly known as) when I was in action sports events. I would watch companies give away stubby coolers and t-shirts to promote their brands, and thought that if they are giving it away, then they must want to buy more.
1800 For Promo introduced me to many corporate companies over the years.
1800 Projects came to life when I partnered with Brent Nassibian. Brent and I have known each other for well over 20 years through Red Bull – at that time, Brent worked at Red Bull and I was working with the brand through action sports events. Brent has brought his extensive corporate knowledge to 1800 Projects through his work with corporate organisations such as Red Bull, Australian Turf Club, Wonder Creative Agency, Red Rooster and Oporto.
Q: How has 1800 Projects grown since its inception?
BB: 1800 Projects started in a rented apartment in Cronulla. The name 1800 Projects is an evolution of the business, and is an opportunity for us to let our customers know that we are more than just a promo company. 1800 Projects still offers branded merchandise and uniforms, which was the foundation of the business, but we have found ourselves producing large scale printing and signage related projects more and more in the recent years.
Today, the business produces premium branded merchandise and signage material for the likes of Channel Nine and Stan. We can produce just about anything to brand or promote a business –vehicle graphics to giant sardine cans and keyrings. If it’s branded, 1800 Projects is the place to get it done. 1800 Projects now also employs over 15 people and services clients Australia-wide.
Q: What machines does the company own?
BB: 1800 Projects has an arsenal of printing and sign making equipment that we use to create our work. When I started the business 18 years ago, I bought a Roland Versa Studio cutter to make transfers and then quickly progressed to a Roland wide format print cut machine so that I could move into the print/cut world.
I never expected to do signage, but with so many clients wanting us to build bespoke-style brand activation pieces, it became apparent that signage printing and fabrication was the direction that our business needed to follow.
Since then, we have purchased many printers and cutting machines. Printing solvent is done on our Roland TrueVIS VG3640 and Roland SOLJET Pro4 XR-640. UV printing roll-to-roll is carried out on the Canon Colorado M-series and direct printing is done on our Océ Arizona GT.
Cutting shapes happen on the Summa F1832 Series cutter and Multicam CNC machine. Finishing is done on the trusty RollOver table. We also have DTF printing in-house for our uniforms side of the business – this allows us to produce textile transfers without limitation.
Q: What are some of the biggest growth areas for the business?
BB: In recent times, our wide format printing and profile cutting segment has taken centre stage. We have printing power on the Colorado and the cutting speed on the Summa. Beyond the machines, we have a dedicated and skilled team of printing professionals that help Brent and I steer the business in the right direction.
Hard work is the catalyst to the upward momentum of 1800 Projects, and that is delivered by our team – from client
interactions to the print room and onto the installation or delivery. Our team genuinely cares about the finished product, and delivering on a premium result is ingrained into the working culture of the business. It is something that we are all proud of.
Q: What are some of the most unique projects the company has worked on?
BB: We’ve produced so many great projects over the years, but one that comes to mind is the Camilla projects that we recently worked on. We are blessed to work with her impressive designs and bring them to life in a retail setting. One standout Camilla project was a can of sardines that we made – it stands proud at the entrance of her head office. A project like this uses just about all of our sign making equipment and the end result makes your head turn!
Stan and Nine Paris Olympics branding and merchandise was also memorable as it was a milestone for the business, allowing us to use all segments of 1800 Projects. We delivered metres of print along with branded uniforms and merchandise, down to the Olympic pins worn during the Olympic broadcast from Paris.
Other projects would include the Giant Dragon Egg for BINGE’s launch of Game of Thrones, and the Super Bowl Field floating down Sydney Harbour that gained a minute of airtime during the Super Bowl broadcast.
Those interested can see more of our work, including custom printed tiles, printed and profile cut plywood, wallpaper and window displays, on our website.
Q: What are some of your future plans for 1800 Projects?
BB: For 1800 projects, the next six to 12 months will be focussed on servicing our regular clients and showcasing the new look business to the wider community. We have so much to offer as a company and we are not afraid of expanding to service the needs of our growing clientele.
Long-term, we’d like to see 1800 Projects continue to deliver on high-end branding solutions and marketing tools to our customers. We want to move with the times and welcome new technology, like AI, and the exciting prospects they bring to our team, so that we can deliver on better branding experiences that are memorable and effective for all of those who use our services.
HP Indigo offers the most sustainable and efficient way to produce on-demand flexible packaging.
Sustainability efforts have been influencing the printing industry and radically changing business operations and models for many years now.
At HP, the company is committed to constantly improving every aspect of its ambition to positively impact the lives of people and communities around the world.
“As leaders of the print and packaging industry, we are always driving efforts to improve energy efficiency, increase circularity, reduce waste, and help our customers reduce the environmental impact of their businesses,” HP Indigo and Scitex vice-president and general manager Noam Zilbershtain said.
A new era of sustainable print with HP
The shift from analogue to digital print production, exemplified by HP Indigo, heralds a sustainable transformation in the printing industry.
Digital printing eliminates the need for printing plates, reducing waste associated with production, storage, and disposal. It offers flexibility with on-demand printing, minimising inventory waste and enabling quick responses to market demands.
HP Indigo’s sustainability commitment extends to carbon emission reduction and circularity, prioritising energy efficiency and material reuse. Practices include using recycled materials, designing presses for reuse and recycling, and adhering to regulatory standards.
As brands increasingly make public targets and commitments to work toward making packaging 100 per cent recyclable or reusable, partnering with HP puts you in a position to be the go-to print service provider for brands that are working toward fulfilling their commitment.
In a world where customers demand highly crafted solutions, only HP Indigo technology gives you and your business the ability to meet any need across any type of commercial printing, labels, or packaging job.
The HP Indigo 200K Digital Press has been developed to give digital flexible converters a competitive edge with better productivity, on-demand delivery, no minimum orders, unique designs, reduced energy consumption and minimal waste.
The press is based on digital technology for digital flexible packaging and has a
successful install base of more than 300 series 4 HP Indigo 25K digital presses worldwide.
The series 5 HP Indigo 200K Digital Press prints up to 56 m/min increasing the productivity of high-margin, sustainable short runs of digital flexible packaging to be delivered in days.
“The HP Indigo 200K is a mid-web digital press especially designed for converters addressing the needs of brands in flexible packaging, but it also serves the growing requirements of the label and shrink sleeve industries for higher productivity and wider format,” Zilbershtain said.
“Flexible packaging is a growing market, and as HP Indigo customers are growing much faster than the market, I have no doubt that the HP Indigo 200K Digital Press will open the door for more flexo converters who want to join the success and reign in industry 4.0.”
The HP Indigo 200K offers a 30 per cent increase in speed and a 45 per cent boost in productivity compared to the HP Indigo 25K.
Featuring gravure-matching colour quality based on the HP Indigo Liquid Electro Photography (LEP) and One-Shot Color technologies, the press also offers the broadest range of ElectroInks.
It is designed to print high-coverage packages with white on most industrial substrates, both surface and reverse. Additional business opportunities include unique brand protection elements.
The HP Indigo 200K features HP Indigo’s PrintOS software automation capabilities for batching, ganging, and variable data, as well as faster, accurate colour match and workflow.
It adds automation tools for operator efficiency, coupled with sustainable production, circular packaging and food packaging safety.
All enquiries can be directed to Currie Group, the authorised HP distributor in Australia and New Zealand.
FUJIFILM Australia Graphic Systems continues to support the Australian commercial print and packaging industry with solutions for both lithographic and digital printing.
F or the past 20 years, FUJIFILM Australia has supported the Australian commercial print and packaging industry. FUJIFILM also proudly supports and believes in Australian manufacturing with its facility in Melbourne producing a number of pressroom consumables including founts and coatings. FUJIFILM currently produces more than 20 tonnes of chemicals per week which service the web, sheetfed, and flexographic markets. In addition to producing batches of up to 9,000 litres, FUJIFILM has an in-house colour-matching service for UV offset ink to a minimum batch size of one kilo.
With a research and development laboratory on-site, FUJIFILM tests, modifies, develops and creates a range of products to suit the needs of the individual
normally despatching finished product within 48 hours of receiving an order.
FUJIFILM Australia also offers a complete and comprehensive range of wide format solutions, be it roll-to-roll, flatbed, or hybrid platforms to suit the needs and budgets of any business. With automation, high quality, speed and an attractive total cost of operation (TCO) proposition, a number of these devices have made their way to strategic partners across Australia looking to diversify their businesses, with results certainly being delivered. FUJIFILM has installed several large format devices utilising industry-standard robotics to bring efficiencies and repeatability to its partners in this space.
Globally, the FUJIFILM corporate philosophy is “Giving our world more smiles” which encompasses the objectives within each division of the business, underpinned by a commitment to a reduction of the impact to the environment.
customer, partnering with them to deliver the best operational efficiencies possible.
FUJIFILM has invested heavily into the research required to support its locally developed and manufactured UV coatings, focusing on low-migration properties for food compliance purposes. These products are readily available and perform across a number of partners, their equipment as well as the final, sellable print.
The company’s Melbourne manufacturing facility includes state of the art blanket cutting and barring facilities. This allows FUJIFILM to cut, bar and assemble its European imported blanket polymers according to the bespoke requirements of customers and the various sizes required for any of their presses. FUJIFILM can respond to orders quickly and with efficiency,
At Drupa 2024, FUJIFILM Group’s message to the industry was “Discover the Difference”. Showcasing the latest versions of its equipment, consumables, and solutions, that provide greater efficiency, less power consumption and a total cost of operation more favourable to its partners. FUJIFILM’s commitment to the Print-on-Demand (POD) market, as well as industrial platforms in commercial cutsheet, roll-to-roll as well as grand format were on display, and the company also demonstrated new technologies in wide format that will soon be made available in the Australian market. FUJIFILM’s Superia ZX processless printing plate range was also shown on the stand, showcasing benefits of this technology, including its quality of output without the reliance of process chemicals.
While FUJIFILM utilised the Drupa 2024 event in Düsseldorf to showcase its impressive range of products and solutions globally, FUJIFILM Australia Graphic Systems is unique within the Australian market with not only access to these industry leading products, but also a team that can deliver the right solution for Australian industry.
The Acuity Ultra R2 is a modular system with scalable architecture, meaning it can grow and change as your business evolves.
Multi-roll capability maximises productivity for smaller jobs
Auto media thickness and position measurement
Our Acuity Range is known for its excellent high quality, productivity and reliability on a massive industrial scale. Engineered with the operator in mind, LED configurations work in harmony with specialist inks to support the printing of exceptional near-photographic interior graphics and the high speed printing of banners and PVC signage.
With a throughput of over 600 m² per hour, the machine has the potential to produce huge volumes of work when printing on three rolls simultaneously, as well as printing superwide format graphics up to five metres in width.
The Acuity Ultra R2 is equipped with a media detector mounted on the carriage. This is used to determine the position and thickness of the media.
To discover more, scan below:
The SADF-540B is a double sided fully automatic laminator equipped with electromagnetic heating, 3 tonne of pneumatic pressure and with speeds of up to 30 mts/min you might start seeing double.
A
new initiative that utilises world-first recycling technology is aiming to help the out of home billboard advertising sector reduce waste and be more sustainable.
Climate One, a new Australian initiative aimed at reducing PVC waste, has officially launched.
It is understood that in Australia, the soft PVC industry disposes of 22,000 tonnes of waste into landfills annually, with the advertising and media segment contributing more than 1,500 tonnes of this, with an estimated 115,000 tonnes of soft PVC in circulation.
“Climate One was created to avoid putting PVC into landfill by recycling end of life soft PVC,” explains David Walton, cofounder of Climate One.
Utilising world-first technology, Climate One’s mechanical separation recycling process, located at its Queensland factory, the company is able to recycle billboards printed on PVC banner and save them from
going into landfill. Climate One’s patented technology and process has also been thirdparty verified by the globally recognised accreditation company, Global Greentag.
“This [accreditation] enables Climate One to supply data back to our clients on their campaigns once they have been recycled. Being verified allows this data to be used for their own ESG reporting,” said Walton.
Out of home media companies JCDecaux, QMS, and several large media groups have shown immediate support for the initiative.
Climate One is now quoting recycling as an option for all out of home billboard campaigns for Dentsu and other wellknown media companies. Climate One has also recycled and booked campaigns for Woolworths, Dan Murphy’s, Mercedes, TAC, Milkrun, Medibank, Nike, and Taxibox.
Climate One’s plant in Queensland has the capacity to recycle 4,000 tonnes of soft PVC annually, with plans to introduce more complex plastic separation longer term. Its world first technology enables Climate One to remove plasticisers and adhesives from PVC – increasing the products it can recycle and expand the number of products that can be repurposed.
Climate One also plans to improve its operations through the introduction of green power, solar and is looking into EV trucks for transport.
The next phase is the roll out of Climate Crates going out to all key billboard installers across Climate One’s network.
“Following interest in other sectors we are aiming to increase collection points and offer drop off points.”
The introduction of Duplo’s first B2 Die Cutter, the DSM-1000, exclusively from SMARTECH Business Systems, represents a significant leap in die-cutting technology.
In the competitive world of commercial printing, staying ahead is essential.
The introduction of Duplo’s first B2 Die Cutter, the DSM-1000, represents a significant leap in die-cutting technology. Exclusively offered by SMARTECH, this machine is set to transform the industry with its advanced automation, enhanced safety features, and intuitive technology.
A key advantage of the DSM-1000 is its potential to unlock new revenue streams. By broadening service capabilities, printers can tap into the rapidly growing digital packaging market. Its versatility and ease of use make it an ideal solution for addressing the rising demand for high-quality printed and packaging products.
The DSM-1000 is a versatile and user-friendly solution for any commercial printing business
As businesses scale, the DSM-1000 effortlessly adapts, enabling companies to take on larger, more complex projects. Whether expanding product offerings or entering new markets, this machine provides the flexibility and power needed to succeed.
Engineered to optimise material usage and minimise waste, the DSM-1000 B2 enhances profit margins. Its precision cutting reduces errors, saving time and materials, leading to a quicker return on investment.
Consistently delivering superior quality output, the DSM-1000 ensures every finished product meets the highest standards, boosting customer satisfaction and encouraging repeat business.
With the ability to handle various substrates and produce diverse products like packaging, POP displays, and pocket folders, the DSM-1000 is a versatile and user-friendly solution for any commercial printing business.
The CPC375 XPRO from Multigra f performs professional creasing , perforating, cutting and foldin g Time perforation in both direction s Expandable with folding machin e your prints into user-ready your prints into user-ready formats with our efficient finishing solutions, formats with our efficient finishing solutions, perfect for both offset and digital projects. perfect for both offset and digital projects.
Handle a wider range of application including booklets up to 50 sheets with square spine Delivers range of applications such as A4 landscape, catalogues, textbooks and calendars with automated precision
MULTIFINISHER
CPC375 XPRO
Scan me to learn more
Designed with customer feedback in mind, the Ricoh Pro C7500 and Pro C9500 address key printing challenges with quality, versatility, productivity, ease of use, and sustainability.
The commercial printing industry faces numerous challenges, from managing diverse media requirements to maintaining consistent quality and maximising productivity. Print Service Providers (PSPs) are often caught between the demands of meeting tight deadlines and delivering impeccable results. To address these challenges, Ricoh has introduced the Pro C7500 and Pro C9500 digital presses, both designed with direct input from customers. These machines represent the peak of print technology, offering solutions that tackle the most pressing needs of commercial printers.
When it comes to quality, consistency is key
The quality of printed materials is crucial for commercial printers, as their reputation and client satisfaction depend on it. Recognising this, Ricoh has engineered the Pro C7500 and Pro C9500 to deliver superior print consistency. Both machines ensure that the first print is as precise as the last, with consistent colour and clarity throughout the print run. The Pro C7500 features new neon colour profiles, expanding the colour gamut for richer, more vibrant prints. Meanwhile, the Pro C9500’s fusing unit enables precise handling of thin media, supporting complex projects such as booklet printing, where uniformity is critical.
Versatility to meets diverse printing needs
The ability to work with a wide range of substrates and stocks is a significant advantage for commercial printers looking to expand their service offerings. The Ricoh Pro C7500 and Pro C9500 shine in this area, offering some of the broadest media support available. The presses can handle paper weights from 40 gsm to 470 gsm, opening up opportunities for applications ranging from lightweight pharmaceutical notes to packaging and intricate greeting cards. This versatility empowers printers to expand their offerings, meet diverse customer demands, and future-proof their businesses by tapping into new revenue streams.
Both the Pro C7500 and Pro C9500 have the capability to produce long-length
double-sided prints up to 1,030 mm, making them ideal for creating specialised brochures and banners.
For PSPs, productivity isn’t just about speed – it’s about reliability and efficiency. Downtime can lead to significant financial losses and impact customer satisfaction. The Pro C9500’s new Auto Colour Diagnosis Unit represents a significant leap forward in automation, reducing the need for manual colour checks and enabling continuous, uninterrupted production. This unit automatically inspects and stabilises colour instantly, ensuring that each print meets the required standards without slowing down operations.
Coupled with Ricoh’s Graphic Communications Operating System (GCOS), both the Pro C7500 and Pro C9500 streamline operations, allowing jobs to be queued and managed with minimal intervention. These advancements ensure that PSPs can meet tight deadlines with confidence, knowing that their equipment is up to the task.
A major challenge in the printing industry is the shortage of skilled labour, making ease of use an essential feature in printing equipment. The Ricoh Pro C7500 and Pro C9500 are designed to be user-friendly with advanced automation and an intuitive user interface.
The new GCOS provides an all-in-one screen for managing print jobs, scheduling maintenance, and monitoring machines
remotely. Operators are trained to perform more maintenance tasks themselves, reducing the need for service calls and maximising production uptime.
Ricoh’s commitment to sustainability is reflected in the design of the Pro C7500 and Pro C9500. Both machines incorporate features that reduce their environmental impact, from energy-saving motors to low power consumption to minimise emissions. Both print engines meet Japan’s strict Green Printing certification with a three-star rating, reflecting their ability to reduce resource consumption, waste, emissions, and environmental pollutants.
Furthermore, the materials used in both machines are recyclable. There is no hazardous waste or specialised materials handling nor any need for specialised ventilation, ensuring a safer working environment for operators. Finished products are recyclable and can be safely disposed of. The Pro C7500 and Pro C9500 are presses that align with the increasing demand for environmentally responsible printing practices.
Screen’s latest inkjet technology, including two new presses, drew plenty of crowds at drupa 2024, with the innovations soon set to hit local shores.
The drupa exhibition in June saw much interest in Screen’s latest inkjet innovations. Two new presses in particular raised eyebrows, one for its superb image quality on standard offset papers and the other for its ability to disrupt plastic ‘soft’ packaging and replace it with more eco-friendly papers.
Screen’s new Truepress JET560HDX is a natural evolution of its highly successful JET 520 continuous-feed press series of colour and mono inkjet devices, first introduced in 2006. While the 520 series has seen many variants and developments including high-definition inks, its core markets have been the transactional, marketing collateral and book sectors. The new 560HDX moves the continuous feed range up several levels.
Screen GP Australia managing director Peter Scott, explains: “The new press is not just a 560mm web width version of the 520mm series. It’s engineered from the ground-up with the high-quality commercial print sector firmly in its sights. The print samples running at drupa showed that offset quality on standard offset stocks can be achieved, or exceeded, using our new SC2 inks on the 560HDX running at 1200dpi.”
Scott points out that the 560HDX uses the latest cutting-edge inkjet heads, the newly formulated SC2 inks, a smart drying system and top-level automation, with the result delivering faster production rates and higher-resolution prints with amazingly vibrant colour at a lower cost.
“From a cost perspective, customers tell us that they want to offer the same paper stocks used on offset presses, on digital devices but this has been a challenge until now because of ink adhesion and drying factors,” says Scott.
No primer or pre-treatment needed
“Solutions involving pre-treatment or priming of offset stocks to accept waterbased inkjet have been explored but –here is the remarkable thing – no primer or pre-treatment at all is needed with the 560HDX. Together with AI-powered ink management that reduces waste and the best colour management in the business, the 560HDX is the perfect candidate for the most demanding book, magazine, brochure or catalogue work where the
benefits of short-to-medium digital print runs are called for.”
Availability in the ANZ market is expected to be from the first quarter of 2025 but two 560HDX installations are already underway in the USA, both with customers also running earlier 520HD models. These customers have cited the speed and easeof use to set up jobs as important factors is this era of operator skill shortages. ANZ customers are invited to have test files printed at other installations in Kyoto, Amsterdam, or Chicago.
“As always, local support and training will be well up to Screen’s legacy reputation here in our region,” adds Scott.
“People put trust in Screen equipment, and we won’t let them down.”
Another industry-changing technology that drew crowds at drupa was Screen’s Truepress PAC520P. The PAC520P was demonstrated with Mondi FunctionalBarrier 95/5 heat-sealable barrier paper. Screen has also announced a partnership with SAPPI and EMSUR for barrier papers and lidding solutions that are inkjet-printable with outstanding results.
Screen’s packaging technologies are distributed by Jet Technologies in Australia
and New Zealand, whose sales director David Reece says: “Paper is resurgent in flexible packaging. Consumers are voting with their feet and actively selecting paperbased flexible packaging options over plastic and manufacturers are adjusting rapidly to ensure that their packaging meets consumer expectations as well as provides the necessary functions including barrier properties that are required for their content.
“Paper can be sourced from sustainable origins and is completely recyclable. With Mondi Functional Barrier, it contains only 5 per cent plastic and is PVDC and PFAS-free. Adding a barrier paper to the mix, from 63 to 136gsm, opens many new markets for paper-based packaging such as frozen foods, fresh foods, dry food, home and personal care and technical packaging,” says Reece.
He adds: “The PAC520P is ready to address this burgeoning market for sustainable soft packaging. Because of Screen’s range of fast-drying ink technologies, production issues using water-based inks are eliminated. It ticks sustainability boxes in other areas too, such as reduced energy usage: 30-40 per cent versus flexo and 60-70 per cent versus gravure, reduced set-up wastage of less than 100 linear metres, 75 per cent less than flexo CI and a massive reduction in set up costs since there are no plates, tooling or solvents – estimated at 85 per cent by an independent survey.
“Since there are no minimum order quantities with digital, redundancy and warehousing of packaging is virtually eliminated, saving a further 25 per cent in wastage,” adds Reece.
The PAC520P runs paper-based packaging at 80 linear metres per minute across a 320-520mm web, using aqueous pigmented inks.
Redefine Commercial Printing Standards and elevate production with Next-Gen High-Speed Inkjet
PRODUCTIVITY
•High productivity
•560mm paper width
•High machine uptime
QUALITY
•New Inkjet 1200dpi PHs
•New saturated ink SC2
•Enhanced image quality
USABILITY
• Energy-efficient drying
•Easy operation
•Offset-coated papers
AGILITY
•Optimised integration
•Precision paper sensing
•Complete New Platform
CMYKhub’s Clive Denholm weighs on in the state of the Australian print industry.
Recent discussions about the fragmented print industry and its competitive capabilities warrant further examination.
The print industry in Australia is far from being merely fragmented. It is a vibrant and competitive sector, characterised by a diverse array of players who are continually innovating and adapting to meet market demands.
The Australian print industry is valued at $6.4 billion (source: IBIS). However, this figure includes food packaging and specialised print services for large businesses, which are managed by well-established companies.
The retail print market is likely closer to $2 billion, depending on what is included. Retail print is primarily serviced by franchised stores and independent design and print businesses.
A recent article asserts that the print industry is fragmented and lacks competitiveness, positioning a web-based mass customisation model as a better alternative.
In Australia, trade printers with advanced equipment and software equip resellers with the tools they need to stay ahead. This approach fosters a competitive environment where businesses can thrive based on their unique strengths and customer relationships.
There are strong franchise networks as well as independent print and design businesses that provide a combination of innovation, specialisation, and customer-centric approaches, driving growth and competition.
In this sector, rather than describing it as fragmented, I would characterise it as distributed – a positive and necessary aspect of the industry.
Consider a few scenarios:
• A design studio in Esperance, WA, collaborates with the local council to produce a newsletter on recycled paper for ratepayers.
• A franchised store in Sydney CBD delivers legal documents within two hours for a law firm.
• An independent printer supports the
local sports team and creates banners for other sponsors.
• A design agency in Byron Bay, which designed the ambiance and fit-out for a local coffee shop, also produces labels for its food offerings.
In each of these cases, local presence, relationship-building, and an understanding of customer needs are crucial.
Take the example of the design agency and coffee shop: a four-person business cannot afford a $3 million digital label solution or automated workflow. However, that’s where we come in, as a trade supplier supporting them with the resources they need.
Australia benefits from a range of highquality trade printers, many of which are reinvesting in the industry.
At CMYKhub, we are so confident in the future of our trade customers that we are investing an additional $6.8 million in wide-format printing equipment and a new eight-colour Komori press for our purpose-built 6,700 sqm facility in Melbourne, due for completion in early 2025. CMYKhub is fortunate to have locations around Australia, which reduces freight times and increases our ability to support local resellers.
The synergy between small, communityfocused design and print businesses with efficient trade printers creates an effective model in Australia.
While online design and web-based ordering have their place, they are best suited for micro-businesses. Although exact figures are unknown, I would estimate that the average order value is under $300.
When it comes to design, try going online and using an AI logo designer or any of the online sites to design a logo. The ability to achieve high-quality design is nearly impossible compared with working with a talented designer.
There are exceptions and hybrid models that use a sales force to target businesses for print while operating online or managing corporate print via a dedicated portal. However, the strength and talent within distributed businesses should not be underestimated.
Being local, talented, and having relationships is powerful when combined with efficient manufacturing.
While consolidation in the market will occur, I believe that small independent businesses supported by trade operators can grow their market share, and the future looks promising.
At CMYKhub, as I am sure is the case with other trade suppliers, we are proud to support a thriving ecosystem of resellers who excel in this competitive landscape, proving that the industry is robust and full of potential.
Clive Denholm is chief operating officer of CMYKhub.
Why understanding and minimising the true cost of hiring wrong people is important.
Professional service businesses are challenging to run for its leaders and owners. The costs of hiring the wrong person can amount to between two and five times the person’s salary. Understanding and minimising the true cost of hiring wrong people is important.
The most visible cost of hiring the wrong people is financial recruitment and training costs being the main ones. Every new hire comes with recruitment expenses, advertising, interviewing and onboarding. When a new person leaves or we ask them to leave before we have realised the benefits of that person, the investment is lost, and the cost repeated.
In service-based businesses, efficiency is key. People who are not a good fit may struggle to perform their job leading to reduced productivity. This can slow down operations, increase workloads and impact customer ratings.
Poor hires often lead to higher turnover rates. High turnover can be costly as it means constant recruiting, hiring and training which is common in this industry. This means there is a feeling of ‘survival’ at times just to deliver the service, rather than move into a feeling of ‘thriving’ where you are making more profit.
Customer experience is what makes and breaks a business. People are the face of the business who shape customer
perceptions. Poor hires can impact many areas. People who lack the right skills, attitude or training give poor customer service. This might mean failing to care for customers, which may lead to negative reviews and a damaged reputation.
Consistency is key in building a trusted brand. People who do not act with the business values can create terrible customer experiences.
The wrong people can significantly affect the culture and the morale of your business. When a person is not performing well or fits poorly within the team, they not only affect their output but also affect the morale and output of other people in the team.
The saying ‘one bad apple spoils the cart’ is true when it comes to people. High performing people can get demotivated if they have to do extra hours and manage workload for the people that underperform. This leads to a decrease in productivity and in the worse case, high performers leave who are harder and more expensive to replace.
Every business has its own culture. People who do not fit well within this culture cause more conflict which can create a toxic work environment.
Hiring the wrong people can also have issues that affect the vision you are trying to achieve. Wrong people slow the
growth of the business. For example, a low performing manager can impact the retention of people who report to them, which means that it takes longer for you to realise the growth of your business.
“The wrong people can significantly affect the culture and the morale of your business. When a person is not performing well or fits poorly within the team, they not only affect their output but also affect the morale and output of other people in the team.”
Poor hires lack skills to find or act on new business opportunities. This results in the business falling behind competitors who are better positioned with the right people. Here are some strategies to help get the right people:
1. Slow down the hiring processes: Hire for attitude and train for skill. Do not rush through the hiring process because you are busy, especially for key roles such as management.
2. Ongoing training: Even though training is expensive, what is the cost of not training and people impacting your culture? Keep investing in training so your people are getting the repeated message on what you are trying to achieve.
3. Positive culture: A strong culture can help retain top people and create a place of work where people want to work and recommend that place to others also.
4. Performance management: If you do not have the right people in place, move them out fast from your business. Manage non-performance early and set the standards for the right behaviours early on.
By focusing on these strategies, businesses can minimise the costs of hiring the wrong people and create a more productive and positive work environment. And the right people in the right jobs can make a big impact on your bottom line.
Shivani Gupta, author of Getting Your People to Step Up, is a speaker, trainer and facilitator. www.askshivani.com
Got an event? Send an email to chibbit@intermedia.com.au with all the details and we will put your event on the page
2024 ProPrint Awards
25 October 2024 Sydney, Australia www.proprintawards.com.au
FESPA Australia Annual Conference
25 October 2024 Sydney, Australia www.fespa.com
Pack Expo International 3-6 November 2024 Chicago, USA www.packexpointernational.com
Heimtextil 14-17 January 2025 Frankfurt, Germany www.heimtextil.messefrankfurt.com
FESPA Global Print Expo 2025 6-9 May 2025 Berlin, Germany www.fespa.com
CCE International 11-13 March 2025 Munich, Germany www.cce-international.com
PacPrint 2025 20-23 May 2025 Sydney, Australia www.pacprint.com.au
Labelexpo Europe 2025 16-19 September 2025 Barcelona, Spain www.labelexpo-europe.com
Pack Print International 17-20 September 2025 Bangkok, Thailand www.pack-print.de
•
•
• Specialised services for non-standard applications
• In-house expertise to help you achieve your production goals
For enquiries, please contact: Carmen Ciappara, National Sales Manager
Direct: 02 9833 4314 or 0410 582 450 | Email: carmen@proprint.com.au
JTS Engineering servicing the industry for all machinery and engineering requirements, has partnered with Longer Machine Industrial Co Ltd to supply a specialised range of paper guillotines systems featuring high speed, precision and safety.
Contact us anytime for all service and guillotine requirements JTS Engineering Services Pty Ltd Jim Strounis, Owner
Mobile: 0433 100 243 Email: jim@jtsengineering com.au
Scott Mohammed, Service & Account Manager
Mobile: 0431 887 501 Email: scottm@jtsengineering com.au Unit 5, 80-82 Seville Street, Fairfield, NSW, 2165 Web: jtsengineering.com.au
•
•
Imagination Graphics is your trusted partner in digital printing, graphic design, A2 posters and CTP (Computer to Plate). We support most press CTP sizes.
CMYK 1 side on 170gsm art starting from A2 x 100 $230
A2 x 500 $310
A2 x 1000 $410
A2 x 2000 $725
CTP (computer to plate)
........................... $55
Please call to discuss pricing on large volume plate production.
*Plus GST and delivery. Prices based on C.O.D.
02 9560 6511 | 33-35 Sydney Street, Marrickville NSW 2204 quotes@imaginationgraphics.com.au | www.imaginationgraphics.com.au/trade
anything Volunteer or Sponsor help us grow! Come and see the extensive
and renovations. Need a venue for a function? Talk to us we can help. Visit https://www.printingmuseum.org.au/
See our range of folding box gluers, board slitters, creasing machines, auto loaders, unloading cutting tables and more.
Revolutionise Your Bookbinding with Our State-of-the-Art Hard Case Solutions.
Print Logistics is proud to offer cutting-edge, hard case binding technology that delivers a new level of durability and sophistication. Our innovative process involves expert casing of the hardcover, resulting in a final product that exceeds the competition in both robustness and elegance.
Elevate your publications, specialty books, and projects to new heights with our superior hard case binding solutions, perfect for customers who refuse to compromise on quality.
• Fast turnaround times
• Competitive trade-only pricing
• Privileged communication
• Family owned and run
• Variety of customisation options to meet your specific needs
“We’ve relied on Print Logistics for years and couldn’t be happier with their service. Their professionalism, precision, and dedication to confidentiality make them invaluable partners. We highly recommend Print Logistics for exceptional printing and binding services.” Principle Design
Print is perception and we treat it accordingly.
Contact Us Today
Phone: 1300 659 029
Email: contactus@printlogistics.com.au
Visit: www.printlogistics.com.au