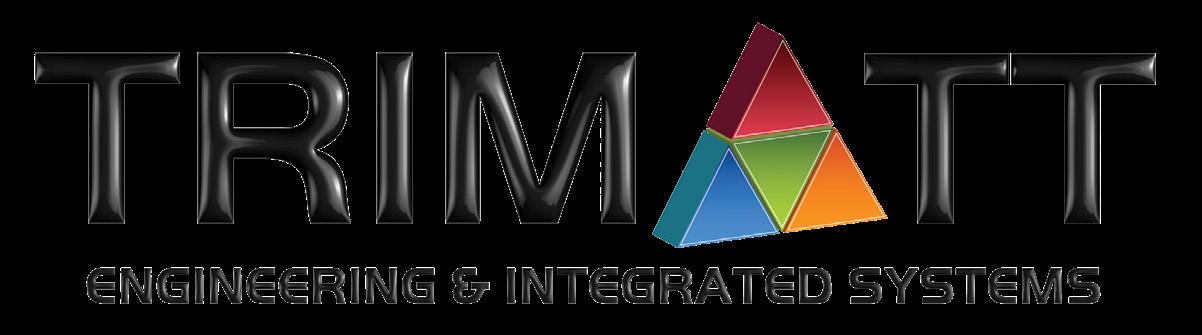
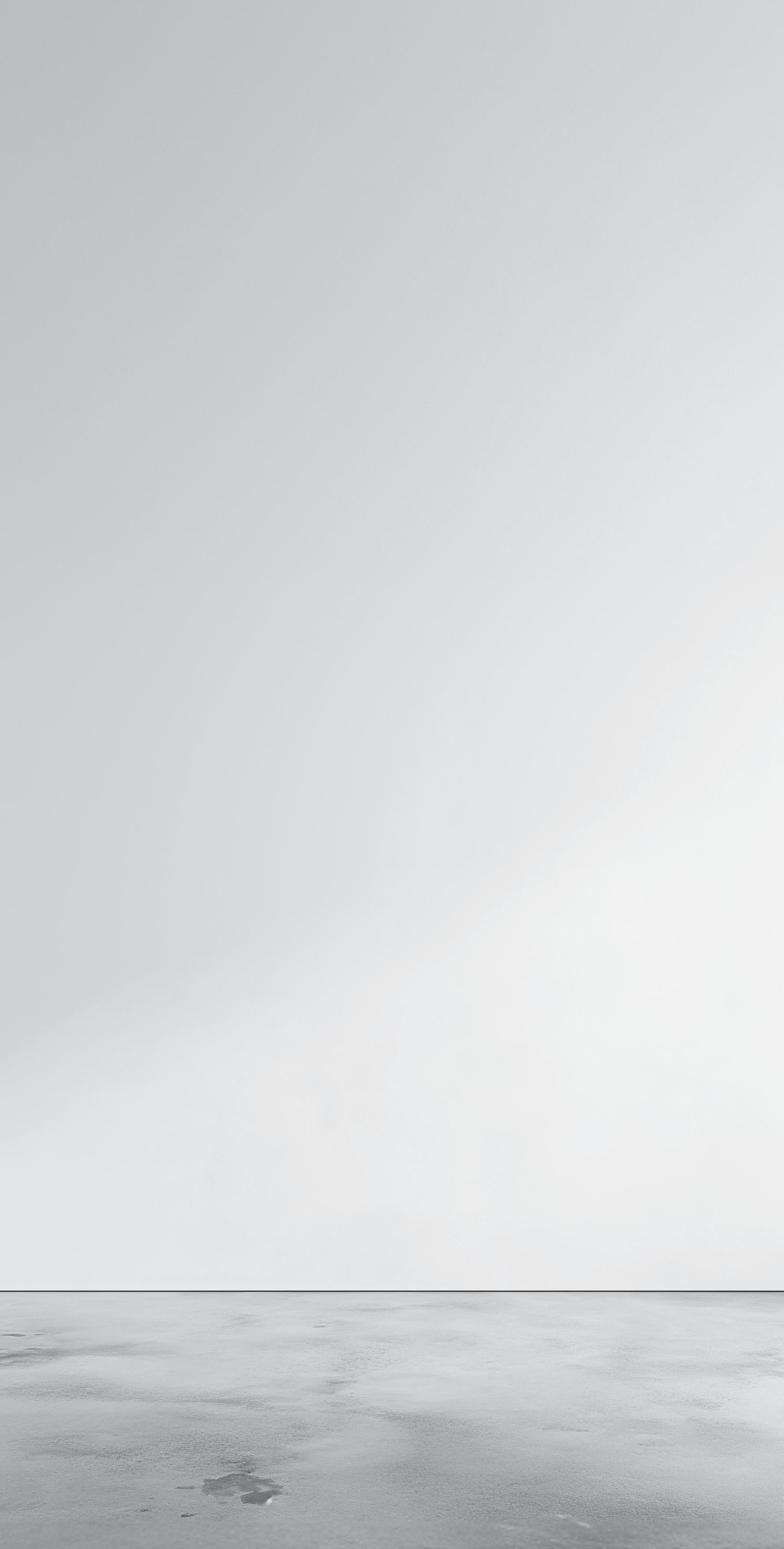
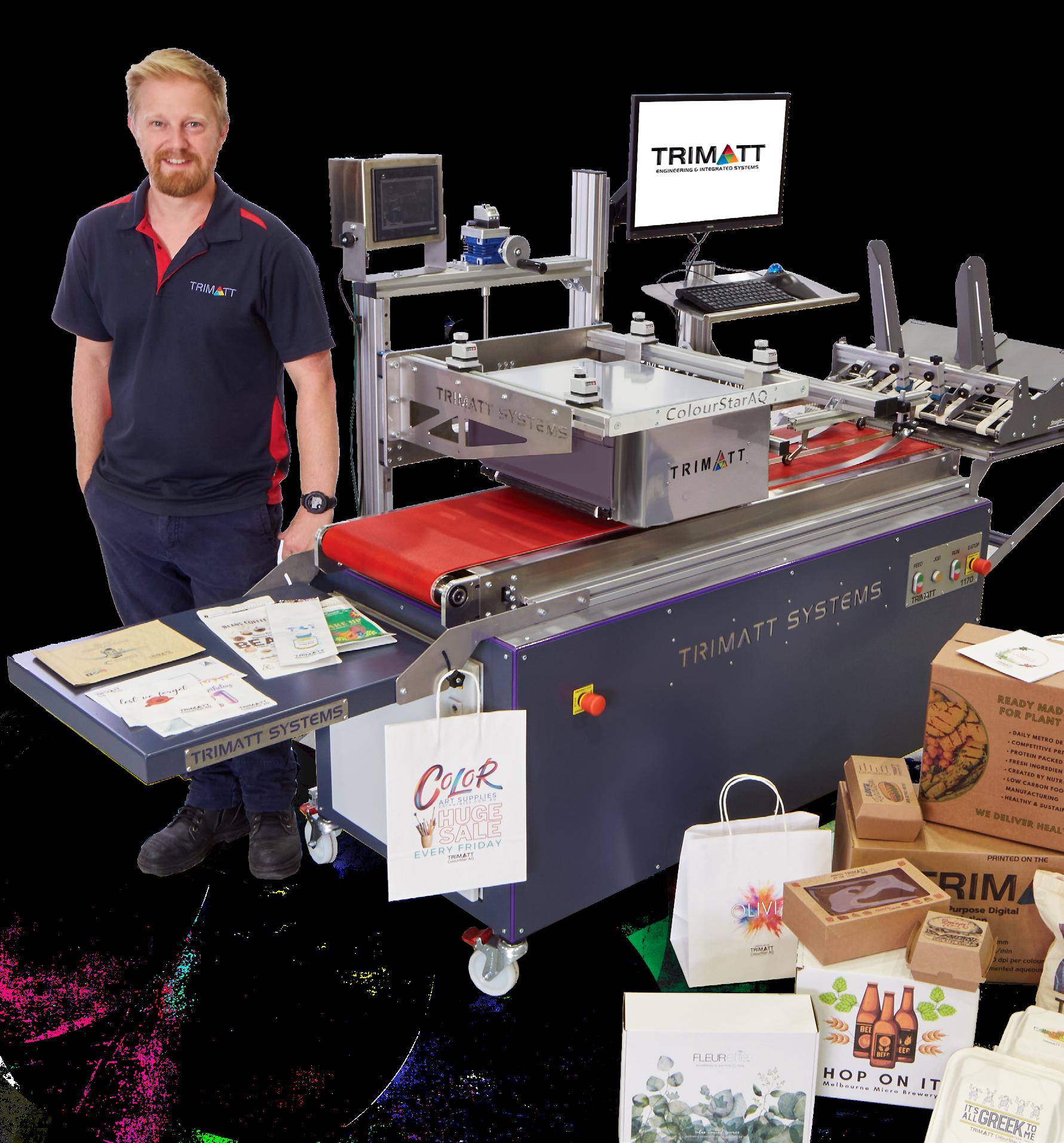
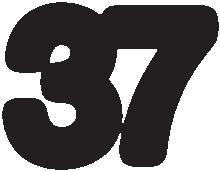
Commitment to excellence confirmed with award-winning solutions.
Offering a formidable portfolio of innovative solutions for the printing, packaging and Smartcard industries, Trimatt Systems continues to produce high quality machinery and technology. Its custombuilt solutions not only exceed customers’ expectations but also help them succeed across a range of industry sectors such as commercial printers, label printers, packaging companies, and coffee roasters.
Matt Johnson, director of Trimatt Systems, founded the company in 2005 He says, “Our focus on staying abreast of industry trends allows us to develop solutions with our customers’ business needs in mind. For Trimatt, customer support is paramount.
“Whether providing solutions to a large company or a small or medium sized business, local or international, our approach to consulting with you to find the right solution for your requirements confirms our commitment to excellence. As your business grows, we continue to support you.
“We understand that as the business environment continually evolves, you need to adapt your business accordingly. Trimatt’s ongoing focus on excellence helps our customer-focused solutions exceed the expectations of our clients across several sectors.”
Award-winning: Matt Johnson, centre holding the award, with members of his Trimatt team
He points out that consumer attitudes have shifted in favour of purchasing locally manufactured printed products over formerly cheaper imports. He says, “They can see the advantages of quick turnaround times and the reliability of local production. As short to medium run digital printing continues to grow, Trimatt’s customers benefit from the company’s immense knowledge and expertise.”
Innovation shows the way
An industry leader, Trimatt’s innovative solutions for fibre-based packaging printing are changing the landscape. Matt says, “Our customers work in a fast paced, ever-changing business environment and we are here to help them adapt quickly to it, developing solutions to keep them ahead of the game.”
Redefining sustainable printing for paper and cardboard packaging, the Trimatt ColourStar AQ range provides a versatile and economical solution for eco-friendly packaging needs. Applications include coffee bags, retail paper bags, packing boxes, and takeaway food packaging. Trimatt offers an integration module (IM), a mid-range entry-level desktop conveyor model (LT), and the most popular Versatile (V) model.
The all in one, customisable, industrial digital colour printing solution makes in
house package printing fast, economic, and profitable. It offers printing for sustainable paper and cardboard packaging as an automated solution that utilises an integrated feeder, a conveyor and an adjustable receiving tray.
Its HP print engine produces waterproof and scratch resistant prints, using aqueous, organic and pigmented CMYK inks, at up to 27 metres per minute. Printing on flat or erected cartons and thick cardboard up to heights of 100mm makes it ideal for food packs. Other applications include boxes, padded envelopes, papers bags and serviettes.
Matt says, “Consumers now expect to see sustainable packaging, especially since the advent of single-use plastic bans. This makes the Trimatt ColourStar AQ perfect for companies looking to remain relevant in today’s increasingly environmentallyaware marketplace.”
Western star
Based in Western Australia, MJ Goods has not looked back since installing a Trimatt ColourStar AQ 18 months ago. Matt and Julie Marchese, who own MJ Goods bought the system to support customer demands in relation to their growing range of products such as food packaging, coffee cups, bags, bottles, shop supplies, and catering boxes.
Matt Marchese says, “The positive effect the ColourStar AQ has had on our business is huge. We are a primarily a packaging supplier, but it has given us a massive value-add for our customers in the printing side of our business.
“We can print runs of any length, on demand. Our volume and turnover have both increased. We have the capability to do 20 boxes or 25,000 boxes in one run. For example, right now we have 70000 pizza boxes on site. We are doing 20,000 pizza boxes per month. The applications are endless; you name it: Uber eats, Woolies bags, and we have our gift shop next door. We now do design as well.
“We have expanded the business since we bought the Trimatt ColourStar AQ, moving into stickers and labels and digital cutting. Now we are branching out into printing for packaging. We have become a one stop shop for our customers. Trimatt has helped us move on that direction. It all adds value for our customers. Other areas of expansion include our purchase of a box machine.
“We have a great relationship with Trimatt, which provides excellent support and service. Matt Johnson is always available. We have also installed a Trimatt Cup Pro 600. It has slotted into our operation with ease. It is another Trimatt machine that is helping us to expand our business as we can offer more value to our customers with it.”
Mel McFarlane, marketing coordinator at Trimatt, says, “An astounding 80 per cent of Trimatt’s customers return after their initial machinery success to order further complementary solutions.
“The generation of profit on labour from their first investment positions them to invest further in automation, again propelling their competitive success. We partner with companies that understand that, in this global economy, the best
time for automation and in-house manufacturing is always now.”
Matt Johnson adds. “Seeing Matt, Julie and the MJ Goods team growing their business in such a sustainability focused manner is a great example for other businesses looking to break through.”
Melbourne-based specialty coffee roaster Ranges Coffee has also installed a Trimatt ColourStar AQ V, using it to provide customised coffee bags to contract roasting customers.
Specialising in bespoke coffee roasting and hospitality packaging supplies with sister company Re-Stox, a newly launched website branding4bags.com.au offers custom printing services for coffee bags, wine bags, and carry bags for retail purchases, corporate gifts and takeaway food. Gavin Williams runs the two companies.
Gavin says, “We had been printing on hand-applied labels, or outsourcing print jobs for our contract roasting clients and regional wineries, restaurants, cafés, and any business requiring carry bags.
“The Trimatt ColourStar AQ V enables us to give a bespoke solution while adding value to our coffee and packaging products. We now offer quicker turnaround times and shorter runs. It has helped us improve our coffee packaging and we keep more work and profits in house as we no longer need to order custom printed bags offshore.
Using the Trimatt ColourStar AQ V, the company has refreshed its packaging for Ranges Coffee with a design inspired by its location near the Dandenong Ranges in the Yarra Valley. As a family run business in the local community, Ranges has paid tribute to its heritage. A local packaging designer created the design. The new packaging also features additional
Onshore production: Ged Ryan, from Espressology, is impressed with Trimatt’s ability to design and build its own machines
information for customers on how best to store their beans, and easier identification of whether it contains whole beans or the type of grind for ground coffee. Mel says, “Lydia Williams, operations manager, picked up the mechanics and the software quickly and has trained her colleagues how to drive the Trimatt ColourStar AQ V.
“Partnering with Ranges and Restox is a delight, and we are proud to support them on their journey. As a local machinery manufacturer, Trimatt is in a position to help local companies manufacture in house to improve their profit margins.”
Cutting lead times
Another company benefiting from installing the Trimatt ColourStar AQ V is Espressology, based in Seven Hills, New South Wales. The company uses its machine to produce coffee bags, targeting quick turnaround times and short print runs.
Espressology chief operating officer Ged Ryan visited Trimatt’s Melbourne operation and was impressed by the company’s ability to design and build its own machines as well as its local service and support.
Matt, says, “Until the arrival of the Trimatt ColourStar AQ V, coffee companies faced long lead times when customers wanted personalised products. The automation built into the ColourStar AQ enables Espressology to print short run, customised coffee bags, packaging cartons, and takeaway bags efficiently and economically.
“We are proud to partner with these forward thinking companies. Our printing systems go beyond saving time and resources; they contribute to enhanced productivity, ultimately resulting in improved return on investment for businesses. Our ColourStar AQ range facilitates fast, economical, and profitable in-house package printing.”
Positioning itself as a preferred supplier in the sustainable packaging industry, Trimatt Systems has confirmed its reputation as a leading manufacturer and supplier of high quality machinery with multiple awards recognition over the past three years.
At the 2022 Australian Packaging and Processing Machinery Association (APPMA) Awards of Excellence, Trimatt earned the prestigious title of Machinery Manufacturer SME of the Year. That award recognised Trimatt’s absolute commitment to innovation and the success of its CardLine 7000.
In 2023, the Trimatt ColourStar AQ took out the Melbourne International Coffee Expo (MICE) 2023 Product Innovation Award.
Continuing to design and innovate across the board, Trimatt Systems has released several acclaimed industry solutions. Recent developments include:
Trimatt CupPro 600
In 2023, the Trimatt team showed the Trimatt CupPro 600 to coffee roasters and suppliers at the Melbourne International Coffee Expo (MICE.
The Trimatt The CupPro 600 changes the way owners can provide customers with personalised branded paper cups in short runs and on demand.
Using 100 per cent compostable inks, this system eliminates the need for outsourcing, minimum order quantities, and long lead times.
Matt says, “Now, you can effortlessly print QR codes, words with various
Mel McFarlane, marketing coordinator and Josh Johnson, general manager sales and service with the Trimatt ColourStar AQ V
MICE is Australia’s largest dedicated coffee event showcasing the latest technology, products, and services to hit the coffee. It attracts over 15,000 attendees and connects café owners, roasters, equipment manufacturers, service suppliers and more. At MICE, Trimatt Systems presented its cutting-edge colour digital packaging printing systems, with the ColourStar AQ V receiving the coveted Product Innovation Award for coffee accessories.
Earlier this year, Trimatt Systems repeated its APPMA Awards for Excellence win for its ColourStar AQ for customising a wide range of sustainable packaging products.
Matt says, “Securing these awards and gaining industry wide recognition is exhilarating. We attribute these
Trimatt Systems offers printing for numerous applications across a range of industry sectors
fonts, numbers, symbols, and simple logos on paper cups with full automation. The Trimatt CupPro 600 fills a gap in the market, and we look forward to talking to our New Zealand customers about this exciting innovation.”
This year, at the APPEX show in March, Trimatt Systems unveiled a first of a kind, ultra-wide, short run, on demand single pass print press offering up to 891mm print width: the Trimatt ColourStar AQ BoxPro.
The experts at Trimatt have meticulously designed and crafted this digital CMYK system for paper
achievements to the value people place on innovation, coupled with the relatability of supporting a local equipment manufacturer.
“As pioneers in the engineering domain, we spot opportunities, invest considerable effort, channel resources into research and development, and subject our equipment to rigorous testing. It’s an intensive undertaking by the entire team, and the results are evidently remarkable.”
Mel adds, “Participation in these events has been an overwhelming triumph for Trimatt, with substantial market interest. This recognition stands as a testament to the team’s alignment with the right course of action.”
Following Trimatt’s award wins, the ColourStar AQ V is flying high with global enquiries coming in from Spain, the UK, India, Argentina, and New Zealand.
Trimatt has expanded operations with a second factory to keep up with the increasing print machinery orders, and with its track record for innovation, it won’t be long before another award-winner emerges on its production floor.
and cardboard boxes, shippers, pizza boxes and multiwall bags, to name just a few of this machine’s suite of possible applications.
At the show, interest came from manufacturers of boxes, multiwall bags, food ingredient manufacturers, the parts manufacturing sector and printers with the increasing demand for short runs.
Matt says, “The Trimatt ColourStar AQ BoxPro offers a means to reduce warehouse inventory through on demand SKU printing, freeing up costly warehouse space and keeping manufacturing local. It caters to the evolving needs of manufacturers looking to enhance operational efficiency and reduce warehouse costs. Many products can now be printed long edge leading at over twice the speed, meaning double the capacity for profit.”
Trimatt continues to thrive, recently announcing the opening of their first overseas office, in Malaysia catering to their enormous sim card packaging and card personalisation market to which their machinery is considered ‘gold standard’ throughout SE Asia.
www.trimatt.com
2-5 Trimatt: Offering a formidable portfolio of innovative solutions for the printing, packaging and Smartcard industries, Trimatt Systems continues to design and manufacture high quality machinery and technology.
10 Comment: Ruth Cobb pays tribute, on behalf of the industry, to one of our stalwarts, Tony Sayle.
12-13 Helping Hand: Printed publications are showing a resurgence locally and globally, says Iain MacIntyre.
14 Konica Minolta: Production inkjet technology holds the key to commercial production printing’s future.
16 Ricoh: Broderick Print & Design has upgraded its digital print production with a new Ricoh Pro C9500 press.
18 Pressnet: The new Dapeng Rotacut 5575 is making die-cutting easy at Foyer Printing.
26 Recruitment: Shivani Gupta discusses the true cost of hiring the wrong people and how you can avoid this pitfall.
32 Think Laterally: Your fight or flight response can affect the way you work, says Mick Rowan.
38 Recruitment: Richard Triggs says you need to consider these five points to attract the right talent.
20 Currie Group: The HP Indigo 200K Digital Press is leading the charge to a greener future.
22-24 Durst: PrintLounge has diversified its offering with a new Durst Tau 340 RSC E LED label press from Durst Oceania
28-29 Nekkorb: Bar Graphics (BGM), Rutherford Graphic Products (RGP) and X-Rite solutions are available now from Nekkorb Solutions.
32 Aarque: The Canon Colorado M-Series and Arizona flatbed printers will help you level up your game.
34-35 Computaleta: Arlette Farland says HP Latex R series printers deliver a raft of benefits across the board.
36-37 NZSDA Update: The NZSDA is fulfilling its commitment to connect with members, says Mikayla Hopkins.
EDITORIAL: 021 631 559
Bruce Craig, Editor - bruce@newzealandprinter.co.nz
CONTRIBUTORS:
Ruth Cobb, Shivani Gupta, Mikayla Hopkins, Iain MacIntyre, Mick Rowan, Richard Triggs
CIRCULATION: brian@newzealandprinter.co.nz
DISPLAY ADVERTISING SALES & SERVICE:
Brian Moore - brian@newzealandprinter.co.nz +61 410 578 876
CLASSIFIED ADVERTISING: Brian Moore - brian@newzealandprinter.co.nz
DESIGN & PRODUCTION: Sarah Vella - sarahvelladesigns@gmail.com
New Zealand Printer is mailed to members of the printing, packaging and graphic communications industry in New Zealand 11 times a year, February-December.
New Zealand Printer is a member of the Printer Media Group
New Zealand: New Zealand Printer Asia Pacific: ProPack.pro Australia: Australian Printer, ProPrint
MANAGING DIRECTOR: James Wells - james@intermedia.com.au
GROUP PUBLISHER: Brian Moore - brian@newzealandprinter.co.nz
© Copyright 2024: Contents of this magazine are subject to copyright and cannot be reproduced without
organised by the Label Academy on digital embellishment and self-adhesive materials. www.labelexpo-americas.com
Wayzgoose
Wayzgoose 2022
September 17, 2022
September 17, 2022
Napier
Napier
and Auspack
www.inkianapress.co.nz
Foodtech Packtech
September 20-22, 2022
Auckland
Labelexpo South China 2024
December 4-6, 2024 | Shenzen, China
Labelexpo Americas
March 12-15, 2024 | Melbourne Convention and Exhibition Centre
September 13-15, 2022
Chicago, USA
The Association of Handcraft Printers has a full day programme including visits to Havelock Neighbour’s Press in Hastings; a swap meet; as well as a barbecue dinner at the Napier RSA. This is a must attend event for all interested in letterpress and the craft. www.inkianapress.co.nz
The Association of Handcraft Printers has a full day programme including visits to Imprimo in Havelock North and Neighbour’s Press in Hastings; a swap meet; as well as a barbecue dinner at the Napier RSA. This is a must attend event for all interested in letterpress and the craft. www.inkianapress.co.nz
Heimtextl
People in Print Awards
The country’s largest food manufacturing, packaging and processing technology trade show brings industry professionals and decision makers together providing a forum for education, discussion, as well as sharing knowledge and expertise.
www.foodtech.packtech.co.nz
South China remains a significant market for the label and package printing industry and Shenzhen is a vibrant hub for business and innovation. Organisers promise visitors an inspiring three days where they will see the latest technology and machinery shaping the future direction of the industry. www.labelexpo-southchina.com
All in Print China
October 11-15, 2022
Shanghai
Auspack has transitioned into APPEX, the Australasian Processing and Packaging Expo. Organisers aim to truly represent all sectors of the industry: machinery, ancillary equipment, materials and packaging, food processing, and industry services. It will provide a comprehensive range of all processing and packaging equipment and services under one roof. www.appex.com.au
January 14-17, 2025 | Frankfurt
Foodtech Packtech
March, 2023 | Auckland
Foodtech Packtech
Apart from the latest technology and solutions, Labelexpo Americas this year features a full two-day conference programme and two masterclasses organised by the Label Academy on digital embellishment and self-adhesive materials. www.labelexpo-americas.com
September 20-22, 2022
September 20-22, 2022
Auckland
The global event for interior textiles, interior design and interior trends will play host to a range of industry professionals and will feature new products and trends for textiles and their applications. www.heimtextlmessefrankfurt.com
Auckland
Wayzgoose 2022
Nominations will soon open for the People in Print Awards and Rising Stars of Print Awards. Do you know someone who is consistently achieving excellence in their work in this industry? Of course you do, so when the time comes, put their name forward for these awards so they can receive recognition for their efforts.
www.newzealandprinter.co.nz
People In Print Awards
March, 2025 | Auckland
Fespa Global Print Expo
March 19-22, 2024 | Amsterdam
The country’s largest food manufacturing, packaging and processing technology trade show brings industry professionals and decision makers together providing a forum for education, discussion, as well as sharing knowledge and expertise. www.foodtech.packtech.co.nz
The country’s largest food manufacturing, packaging and processing technology trade show brings industry professionals and decision makers together providing a forum for education, discussion, as well as sharing knowledge and expertise. www.foodtech.packtech.co.nz
September 17, 2022
Napier
More than 1300 exhibitors will demonstrate their solutions across the 120,000 square metres of show space at the Shanghai New International Expo Centre. Organisers expect more than 160,000 visitors from all over the globe as they open the “Oriental Window of the World Printing Industry”.
www.allinprint.com
Letterheads
Organisers will soon call for nominations for next year’s People In Print Awards and Rising Stars of Print Awards. These awards recognise people in our industry who achieve outstanding results for their work, for their community, and for the environment; people who work alongside you. www.newzealandprinter.co.nz
All in Print China
All Print
October 21-23, 2022
The Association of Handcraft Printers has a full day programme including visits to Imprimo in Havelock North and Neighbour’s Press in Hastings; a swap meet; as well as a barbecue dinner at the Napier RSA. This is a must attend event for all interested in letterpress and the craft.
Covering digital printing, screen printing, textile printing, garment decoration and signage, Fespa Global Print Expo will mix all the latest technology and solutions with events like the World Wrap Masters and Fespa Party Night alongside features such as its Sustainability Spotlight; Personalisation Experience, and Sportswear Pro.
The Association of Handcraft Printers has a full day programme including visits to Imprimo in Havelock North and Neighbour’s Press in Hastings; a swap meet; as well as a barbecue dinner at the Napier RSA. This is a must attend event for all interested in letterpress and the craft. www.inkianapress.co.nz
www.fespaglobalprintexpo.com
October 11-15, 2022
Fespa Global Print Expo 2025
October 11-15, 2022
Sign Foundry, Welling
www.inkianapress.co.nz
Shanghai
Shanghai
May 6-9, 2025 | Berlin
Printopia
Foodtech Packtech
Foodtech Packtech
May 3-5, 2024 | Corbans Estate, Henderson
www.fespa.com/en
PacPrint 2025
Craig Paul 027 655 4267
September 20-22, 2022
Auckland
The call has gone out for all signees to grab their brushes and head to Lower Hutt for the annual Letterheads event. This year’s theme is ‘Red and Blue’. Your hosts this year are Lydia Reeve and Duncan Rourke.
www.letterheads.co.nz
Covering screen, digital, wide format, and textile printing, the giant show brings hundreds of exhibitors to showcase their latest innovations and product launches across graphics, décor, packaging, industrial and textile applications. It features the World Wrap Masters Final 2025; the Sustainability Spotlight; and the Fespa Party Night.
Now into its third year, the Printopia Festival of Original Print promises a fun, inspiring, print-filled weekend of artist talks, demos, workshops, live printing and of course our print fair. International artist Jenny Robinson will give the keynote presentation on May 4 and a masterclass the following day. www.printopia.nz
Interpack
drupa
More than 1300 exhibitors will demonstrate their solutions across the 120,000 square metres of show space at the Shanghai New International Expo Centre. Organisers expect more than 160,000 visitors from all over the globe as they open the “Oriental Window of the World Printing Industry”. www.allinprint.com
More than 1300 exhibitors will demonstrate their solutions across the 120,000 square metres of show space at the Shanghai New International Expo Centre. Organisers expect more than 160,000 visitors from all over the globe as they open the “Oriental Window of the World Printing Industry”. www.allinprint.com
May 20-23, 2025 | Olympic Park, Sydney
May 28-June 7, 2024 | Dusseldorf, Germany
Craig Paul 027 655 4267 sales@curriegroup.co.nz m
May 4-10, 2023
The country’s largest food manufacturing, packaging and processing technology trade show brings industry professionals and decision makers together providing a forum for education, discussion, as well as sharing knowledge and expertise.
www.foodtech.packtech.co.nz
Düsseldorf, Germany
Letterheads
Letterheads
• Consulting and Machine Recommendations Sourcing
October 21-23, 2022
October 21-23, 2022
The most comprehensive and relevant business to business event serving the evolving needs of the print, sign and graphics industries in our region, PacPrint will welcome around one hundred leading suppliers showcasing their latest products and services to thousands of industry professionals. www.pacprint.com.au
All in Print China
• Export/Import Sales
The world’s leading trade fair for printing technologies has opened registrations to again welcome the industry’s main players, and quite a few minor ones. All will show their latest solutions. Visitors can stay on trend with the technology and seminars featuring topics from sustainability to digitisation. www.drupa.com
Sign Foundry, Welling
Sign Foundry, Welling
Foodtech Packtech
Visual Impact Brisbane Expo
July 17-19, 2023 | Brisbane
• Machinery Inspections & Valuations
October 11-15, 2022
Shanghai
September 2-4, 2025 | Auckland Showgrounds, Auckland
The call has gone out for all signees to grab their brushes and head to Lower Hutt for the annual Letterheads event. This year’s theme is ‘Red and Blue’. Your hosts this year are Lydia Reeve and Duncan Rourke.
• Plant Relocation OFFICE: 09 8367577, ALEX MOB. 021 975 477 sales@apm.co.nz www.apm.co.nz
The global packaging industry will meet in Düsseldorf with a focus on packaging materials, packaging machines and related process technology for the food, beverage, confectionery, bakery, pharmaceutical, cosmetics, non-food and industrial goods sectors.
www.interpack.com
www.letterheads.co.nz
The call has gone out for all signees to grab their brushes and head to Lower Hutt for the annual Letterheads event. This year’s theme is ‘Red and Blue’. Your hosts this year are Lydia Reeve and Duncan Rourke. www.letterheads.co.nz
New Zealand’s largest food manufacturing, packaging, and processing technology trade show brings industry professionals and decision makers together providing a forum for education as well as sharing knowledge and expertise. It will attract more than 250 local and international exhibitors and around 4,000 visitors.
www.foodtechpacktech.co.nz
Visual Connections Australia will host visitors and exhibitors at the Brisbane Convention and Exhibition Centre. The Exhibition hopes to attract over 2,500 visitors interested in the signage, print, graphic and engraving industries and featuring digital printing, personalisation, signage, sublimation, design, routing, display solutions, and vinyl applications. www.visualimpact.org.au
Interpack
Interpack
newzealandprinter.co.nz
More than 1300 exhibitors will demonstrate their solutions across the 120,000 square metres of show space at the Shanghai New International Expo Centre. Organisers expect more than 160,000 visitors from all over the globe as they open the “Oriental Window of the World Printing Industry”.
Printing United
May 4-10, 2023
May 4-10, 2023
www.allinprint.com
Düsseldorf, Germany
Düsseldorf, Germany
Las Vegas, USA | September 10-12, 2024
Letterheads
October 21-23, 2022
Sign Foundry, Welling
Showcasing the latest innovations and applications in specialised printing, the event attracts thousands of visitors from across the printing industry, serving as an exhibition and as a knowledge hub, where experts share their expertise and stimulate discussions about the future of the industry. www.printingunited.com
The global packaging industry will meet in Düsseldorf with a focus on packaging materials, packaging machines and related process technology for the food, beverage, confectionery, bakery, pharmaceutical, cosmetics, non-food and industrial goods sectors. www.interpack.com
The global packaging industry will meet in Düsseldorf with a focus on packaging materials, packaging machines and related process technology for the food, beverage, confectionery, bakery, pharmaceutical, cosmetics, non-food and industrial goods sectors. www.interpack.com
Craig Paul 027 655 4267 sales@curriegroup.co.nz
The call has gone out for all signees to grab their brushes and head to Lower Hutt for the annual Letterheads event. This year’s theme is ‘Red and Blue’. Your hosts this year are Lydia Reeve and Duncan Rourke.
www.letterheads.co.nz
newzealandprinter.co.nz
Interpack
May 4-10, 2023
Düsseldorf, Germany
The global packaging industry will meet in Düsseldorf with a focus on packaging materials, packaging machines and related process technology for the food, beverage, confectionery, bakery, pharmaceutical, cosmetics, non-food and industrial goods sectors.
www.interpack.com
COLOR-LOGIC has announced an update for the user manuals it provides to printers and graphic designer customers. Mark Geeves, director of sales and marketing for Color-Logic, says, “The update gives licensed users detailed video instructions for quickly producing ColorLogic metallic print files and embellishments. The manuals now support 133 languages using Google Translate, enabling graphic designers to use ColorLogic metallic colour palettes and embellishments for each of the metallic colours..”
EFI subsidiary, EFI Cretaprint has licensed its Building Materials digital printing business to its current global strategic partner, DPI. Scott Schinlever, chief operating officer for EFI’s global inkjet business, says, “This strategic partnership strengthens DPI’s role as the exclusive provider of service and support for EFI’s ceramic digital printers and spare parts, leveraging EFI’s renowned know how, trademarks, and uncompromising quality standards. DPI will manage both current and future product and service needs, ensuring that customers continue to receive high quality support.”
ESKO has commissioned a study examining the potential return on investment businesses may realise in deploying its WebCenter packaging and label artwork management solution. Key findings from the report include quantified benefits such as productivity gains of 30 per cent for core team members of the packaging process and 40 per cent for supporting team members of the process; revenue gains due to increased speed to market; and cost savings through vendor consolidation.
Epson has entered into an agreement with affiliates of Siris Capital Group, including Electronics for Imaging, to acquire all interests in Fiery.
Subject to customary closing conditions including required regulatory approvals, the deal will see US-based Fiery become part of the Epson Group but retaining its current name and organisational structure. It will continue to operate from its existing offices.
Epson and Fiery say Fiery’s software, server, and workflow solutions will complement Epson’s strategic vision and hardware leadership
Durst Group has placed its Workflow software with its 1000th customer, US large format specialist Forge Graphic Works.
The milestone marks a significant achievement for Durst Group, highlighting its rapid growth and dedication to providing cutting-edge solutions to the printing industry. Forge Graphics has a reputation for innovative and
to accelerate the growth of digital printing around the world.
Yasunori Ogawa, Epson’s president, says, “We are delighted to welcome Fiery into the Epson Group. We are confident that this agreement will not only drive further growth in our commercial and industrial printing businesses but also accelerate the digital transformation of the analogue printing market in
high quality graphic solutions and joins a distinguished list of customers benefiting from Durst Workflow’s advanced capabilities.
Forge Graphic Works specialises in large format printing and graphic manufacturing, installation, and fulfilment services for retail, events, interiors, and experiential marketing programmes. Previously using a third party RIP, Forge Graphic Works found the process labour intensive with limited automation, often leading to errors. Todd Ebersole, strategy director of Forge Graphics, explains, “We wanted a more advanced workflow solution with integration in other parts of our business like scheduling,
innovative way.
“Together with Fiery, we remain committed to contributing to our customers’ success and enhancing corporate value as we pursue new opportunities in the evolving printing landscape.”
Toby Weiss, chief executive at of Fiery, adds, “Epson’s acquisition of Fiery showcases the important role we play in enabling success across the entire print industry. Fiery has built a legacy of empowering original equipment manufacturers to deliver the best possible results for customers, and that legacy will be enriched under Epson’s strategic vision.
“Epson is a legendary company in the print industry, and we are thrilled to join the Epson family to drive the growth of digital printing around the world together.”
pricing, and automation of common tasks that save us time and prevent rework.”
At the recent Printing United trade show, they discovered Durst Workflow and Durst Lift ERP. Impressed by a vendor partner’s success with these solutions, Forge Graphic Works was particularly drawn to the vertical integration with Lift ERP and key modules within Durst Workflow, such as Verification, Impose Editor, and PDF Proof Approval.
Configurable as an all in one solution integrated with Lift ERP, Durst Workflow provides a single point of contact for implementation, training, and troubleshooting. It will drive all the company’s printing systems.
Jet Technologies has launched the Jet iQ range of finishing solutions for the label and packaging markets.
Designed and built in partnership with Polly Automatics, the collaboration brings together the intellectual property and expertise of both companies, positioning Jet Technologies to deliver a comprehensive suite of finishing solutions. Jack Malki, director of Jet Technologies, says, “Together with its range of digital presses by Screen GP, the Jet iQ range will provide local businesses with access to a fully integrated end to end solution, enhancing productivity and innovation in the digital print space.
“The Jet iQ range covers everything from slitting, rewinding, and inspection to shrink sleeve processing and digital finishing equipment.
“One of Jet iQ’s standout innovations, the optional inclusion of the Vesatex Print Bar by Xaar, enables you to add substantial value to your print, utilising the Print Bar to add digital effects such
Organisers have stayed true to drupa’s four-year cycle, scheduling the next event for 2028, but as a nine day event instead of eleven.
They say that, as the world’s leading platform for printing technology, the trade fair must adjust to the changing needs and expectations of exhibitors and visitors. The next drupa will run from May 9-17, 2028 in Düsseldorf.
Wolfram N Diener, chair and chief executive officer of drupa organiser Messe Düsseldorf, says, “drupa 2024 was more international than ever, and the positive atmosphere throughout the halls reflected our industry’s determination to drive profound change to make the printing and packaging industry more sustainable through automation, artificial intelligence and strategic partnerships. And these are exactly the kind of important goals that will continue to require a reliable platform such as drupa in future.
“What was also apparent, however, was that, as a B2B trade fair with a very high proportion of decision makers from
The Jet iQ range covers slitting, rewinding, inspection, shrink sleeve processing, and digital finishing equipment
as digital foil as well as a combination of gloss and high build varnishes in a single pass. In the past, these were only possible via conventional print techniques.
“The results have been outstanding. To be able to print a high build varnish of around 100 microns directly onto uncoated wine stocks is an absolute game changer. No primer, no limitations and outstanding results on a wide range of locally supplied materials.”
“The entire Jet iQ range will be available to New Zealand customers, addressing a long standing demand for well supported digital print and finishing solutions. We support our range of equipment is supported across Australia and New Zealand, providing customers with factory-trained service options.”
all over the world, the length of stays at drupa has become shorter. That’s why we want to facilitate trade fair visits with maximum efficiency.
“At this year’s drupa, 76 percent of visitors came from top and middle management. We believe that this adjustment is also confirmed by the experience we have gathered at our leading global trade fairs in the fields of machinery, plants and equipment, interpack and K, that address comparable customer profiles and do very well with a similar duration.
“The presentation of cutting edge technology and machines in operation remains a unique selling proposition of drupa. The new rules for trade fair duration will continue to allow exhibitors to effectively present and stage wide ranging product portfolios, machines and workflows as well as an impressive stage programme.”
“We expressly welcome the new trade fair duration starting in 2028, as it will meet changing industry requirements without limiting the international scope of the trade fair. This is also demonstrated by the fact that visitors from 173 countries attended drupa, emphasizing the global appeal of the event. No other format generates such a high level of interest from the industry.”
Messe Düsseldorf will present the conceptual direction and new key visuals for drupa 2028 to the industry in 2025.
P (09) 444 5523 M 021 190 1305 E info@bookbindingpress.co.nz www.bookbindingpress.co.nz
An unswerving commitment to the industry and a passion for training from an industry legend.
Tony Sayle retired from Jenkins Group on September 30, and I wanted to take the chance to acknowledge the incredible contribution he has made to our industry, not only through his work at Jenkins, but for both our Industry Training Organisation (CMITO) and PrintNZ.
After university, Tony briefly tested a couple of career options including Irish Seaman and Whale Trainer but decided neither of those were for him. It was the horticulture industry and that set his career pathway which in turn morphed into the printing industry as managing director of Jenkins Group, but even then, still retaining those links to horticulture through their fruit labelling side of the business.
Tony’s career in horticulture started with Bay of Plenty Fruit Packers and then he went on to Fruitfed Export, the training ground of many of today’s horticulture industry leaders. Under their auspices, he transferred to Nelson, then to Auckland and subsequently the UK.
With the formation of the Kiwifruit Marketing Board in 1989, it was back to New Zealand where he held senior international marketing and management roles. During his previous time in the UK, he had come across the founder of Sinclair International, a UK company specialising in automatic fruit labelling and his relationship with the self-adhesive industry began there.
In 1994 he joined Sinclair, and subsequently returned to the UK to take up the position of international marketing director. In 1999, he eventually returned to New Zealand and joined Jenkins, the New Zealand /Australian Agents for Sinclair. At that point, Jenkins produced not just fruit
labels, but a broad range of other self-adhesive and shrink wrap labelling.
Tony oversaw the Auckland and Australian operations and was responsible for the transition of the business to focus solely on fruit labelling and the transfer of their production plant to Tauranga, closer to their core market. At the same time, they diversified to include a full range of packaging and handling systems, and consumables.
Tony had a great passion for training and in 2010 he was shoulder tapped to join the board of CMITO, our Industry Training Organisation. He served on that board until CMITO merged with Competenz in 2014.
Tony was part of the project team that went through the assessment of prospective partners when the government indicated that it wanted to reduce the number of Industry Training
Organisations they were funding. This was an extensive task that took the best part of a year, requiring substantial additional input and Tony’s expertise in assessing the options was invaluable.
Following the disestablishment of CMITO post-merger, when Tony thought he may be able to move quietly into the background, he was again shouldertapped to join the Board of PrintNZ and he very generously served as a Board member from 2014-2017, then as president of Print from 2017 – 2021, and remained on the Board as Immediate Past President until he stood down at the AGM in 2024.
Tony’s commitment to CMITO and PrintNZ has been outstanding. His passion for training, his understanding of business and his considered approach have made his contribution invaluable.
While he may not have made a career as an able seaman he has certainly steered the ship with a steady hand through some quite difficult times, firstly with the merger of CMITO into Competenz, and then the unprecedented challenges presented by Covid, all the while being responsible for driving progress and change at Jenkins Group and facing those same challenges for their own business.
Not willing to let him go just yet, in 2023 Tony was appointed as a Trustee of the Trust4Skills Training Fund and at the AGM in September 2024 has been appointed to the Chair of that organisation. The Trust is responsible for allocating grants to PrintNZ members for workplace training and providing opportunities for individuals and businesses to improve their skill base. Again, Tony’s sage advice, alongside the other Trustees, will be well placed in ensuring that the Fund continues to fulfil its purpose.
On behalf of the industry, I take this opportunity to wish Tony, and his wife Sandy, all the best for his retirement and if he misses the horticulture industry too much, I am sure that there are plenty of orchards looking for a helping hand during picking season.
resurrection and NBA success emphasise the enduring value of print.
Recently, community and business demand drove the printed return of East Auckland newspaper, the Times. This reflects the ongoing and deep value widely-held for printed publications.
Founder Reay Neben closed the 53-year-old newspaper in April to enter retirement. Soon after, businesswoman Bo Burns stepped forward to acquire Times Media’s assets and relaunch the publication in an initially online format.
She says, “I always intended to have something in print. While I had planned it for 2025, huge community and business
support enabled me to bring that decision forward.”
Beacon Print produces the Times printed publication. Its twice-monthly frequency in mid-August saw “all bins emptied within two days”.
Bo says, “We have already increased our circulation by a few thousand after our first run and it will continue to increase with demand. Our current print distribution is 10,000. We have an expected readership of print of 30,000 as we are in strategic locations. The digital paper has a readership of 10,000.”
While she says the publication’s printed version readers include people biding time when sitting at doctors, cafes, takeaways, hairdressers, bus stops and on boats, she points out how device fatigue contributes to its popularity as well. She says, “People get sick of staring at their phones. They want a tangible product to hold. Also, if you have the right balance of
news, lifestyle, events and competitions, the lifecycle is far greater.”
Times Media must now navigate its way through several recent challenges including a changing media landscape; the pandemic; difficult economic conditions; rising living costs; and forced recessions.
Bo says, “I came in with a strong advertising and marketing background and had an intention to revitalise the hero, which was the online Times.co.nz. I wanted to engage with our community, who love and support the brand.
“Initially the digital platform was all I had to work with, whilst in the early stages of reconfiguring the business and merging it into my other business systems. Once I could come up for air, I heard the community loud and clear: it wanted the print version back.”
She describes the company’s readership statistics as on a huge upward trajectory. She says, “The digital paper is around 10,000 reads already, so this combined with our printed editions is a fabulous integrated reach and approach to all demographics. We also have increased our socials to an impressive five channels.
“We must be doing something right.”
Employing eight people, the business anticipates further growth as it continues to reach residents across in Pakuranga, Highland Park, The Peninsula, Howick, Botany, Meadowlands, Cockle Bay, Golflands, Flatbush, Ormiston, Dannemora and Highbrook.
Bo says, “Times Media services a huge audience of 160,000 East Auckland residents. We are the most culturallydiverse area in Auckland. As for the future, we have very big plans. Watch this space.”
Times print return lauded
In a recent Times opinion piece, past PrintNZ Board member Charles Miller strongly praised the strategic decision to reinstate the printed version of the publication.
He wrote, “This move highlights the paper’s commitment to engaging with its community, particularly those who
find online access challenging, and is a great credit to Bo Burns and the dedicated team who’ve worked so hard to make this a reality.
“In a world increasingly dominated by digital content, there’s an important segment of the population that prefers the tactile experience that only a physical newspaper can provide.
“For people not raised in an online world or those in rural areas with limited Internet connectivity, the return of the printed paper is more than just a convenience. It’s an essential service that ensures they remain informed and connected to their networks.”
“The printed publication provides an additional channel for advertisers to showcase their products and services, in a format to which new readers will be drawn and which often etches greater recall.
“In settings like motel rooms, cafes and waiting areas, print materials are shared among multiple readers, amplifying each copy’s impact as it reaches several individuals who spend time engaging with the content.
“This shared, extended interaction increases the effectiveness of print, leading to a wider audience and a more in-depth experience, where articles and advertisements are more thoroughly absorbed and retained.”
In a similar development, as reported in New Zealand Printer last month, the Newmarket Business Association (NBA) continues to boost the circulation and readership of its Newmarket.magazine as a key means of positioning the precinct as the must-visit shopping destination in New Zealand.
The magazine has undergone a boost in print circulation to achieve a readership of 180,000 readership. It plays a specific role in promoting Newmarket and attracting domestic tourists. Mark KnoffThomas, chief executive at NBA, says, “By putting out top-notch editorial content and stunning visuals, we showcase the best that luxury and design in New Zealand has to offer. Promoting the precinct has been an amazing plus.
“From our high fashion editorial shoots to thought-provoking opinion pieces by leading chief executives, it is all about offering something engaging for everyone and, in doing so, supporting our local businesses.
“Kiwis still crave high quality, entertaining media that appeals to their
interests, despite the widespread desire for short-form digital content. The magazine has attracted attention from both local and international brands and businesses, and its strong offerings have cemented Newmarket as the premier precinct for retail, hospitality and art, with a strong undercurrent of heritage and supporting local.
“Print is alive, and we feel proud to play a small part in that ongoing media battle.”
Meanwhile, Rolling Stone magazine has recently undertaken a comprehensive redesign.
According to reportage by India-based Flip The Media, the collaboration of its creative designer with external graphic and type designers has delivered a reimagining of “what a print magazine can be in the modern age”.
“The result is a publication that not only looks different but feels different, thanks to a new paper stock that gives it a grittier, more tactile quality,” reported Flip.
“The redesign process was extensive and meticulous. Exclusive fonts were crafted specifically for Rolling Stone, and the entire layout was reshaped to pack in more stories, add new franchises and bring back some classic features.
“The magazine is now emphasising its criticism, expanding long-form features
and delving deeper into various topics. This comprehensive overhaul aims to capture the enthusiasm, exuberance, and depth of knowledge that Rolling Stone is known for.”
“It is a bold statement in a digital age. “It reaffirms the value of print media and the unique experience it offers. The redesigned magazine is a celebration of Rolling Stone’s rich history and a nod to its future. It invites readers to slow down, turn the pages, and immerse themselves in the stories that matter.
“In a world filled with endless digital distractions, Rolling Stone’s new look is a reminder of the enduring power of print. It’s a testament to the magazine’s ability to evolve while staying true to its roots.”
Recently, Texas-based financial services specialist Vericast completed a study showing that direct mail plays a “critical and emotional role in how consumers choose to engage with and purchase from brands”.
Vericast’s survey found consumers:
• Create an emotional connection with direct mail ad, according to 33 per cent of respondents.
• Find print ads trustworthy (58 per cent)
• Spend an average of 1.6 minutes with a direct mail ad
• Save direct mail ads to refer to later (88 per cent)
• Are likely to buy after seeing a direct mail ad (50 per cent)
Building upon findings from research for the United States Postal Service (USPS) by Pennsylvania’s Temple University, Dr Martin Block, professor emeritus in Medill’s Integrated Marketing Communications programme at Illinois’ Northwestern University analysed the study.
He said, “My assessment and conclusion of the study finds that consumers who use print ads are happy, confident and consistent
“Why is this significant? Years of conducting and reviewing this type of research shows a predisposition for happier people to shop and spend more.
“The concurrent validity demonstrated across separate studies conducted by Vericast and the USPS supports the continued need for media plans that include direct mail messages to optimise consumer engagement. What gives print ads their edge, according to the studies, is they are more effective at leaving a lasting impression.”
Production inkjet technology holds the key to commercial production printing’s future.
One of the largest manufacturing sectors in New Zealand, Print has almost 12,000 employees and more than 1,800 businesses with an annual turnover in excess of $2bn. Despite steady employment growth in the sector, changing market demand has caused a significant level of disruption, pushing many businesses to consider investing in inkjet technology as part of their digital transformation strategy.
So, what can we look forward to?
According to Smithers’ 2021 market report, the next decade for the global printing industry will focus on adjusting to print buyer demands for shorter and faster print runs. This will not only reshape the cost dynamics of print; it will also increase the pressure on businesses to automate their print production workflows to remain competitive and increase profit margins.
Chris O’Hara, national production print manager for Konica Minolta New Zealand, says, “The printing industry is set for a future of shorter print runs, innovative technology, and growing product personalisation and we are ready to position Kiwi printers to take advantage of that.”
He believes the investment in switching to an automated workflow is well worthwhile. He says, “In addition, new technology in the form of digital inkjet and toner presses will help businesses transition to shorter run lengths as well as supporting the drive to greater variety in packaging print. This outcome for your business is a higher quality of output, faster running speeds, less inventory overhead, and numerous financial benefits.”
Inkjet technology offers features that unlock productivity and efficiency
The future of inkjet printers looks bright. The global inkjet print market has a current market value of US$80.4bn ($130bn) and is expected to reach US$118.2bn by 2025.
The increased interest in production inkjet technology for mainstream document applications is due to several factors. Legacy business models that are not sustainable in the current landscape combined with significant improvements in ink technology and pre-coat fluids are the main drivers behind its adoption.
Inkjet technology offers several features that unlock productivity and efficiency across the print production process and is the key to securing future business growth. Chris outlines the major benefits:
Superior quality – High-speed inkjet technology is more productive than digital colour toner presses. For example, Konica Minolta’s high-speed inkjet technology has a resolution of 1200dpi x 1200dpi print quality at rated speed. It can print finer, smoother details through higher resolution with little to no warmup time.
Outstanding flexibility – Flexible packaging is a significant part of the packaging market; however, there are many challenges when it comes to flexible packaging, including food safety and de-inking capability. Inkjet technology can print on standard offset print media, meaning there is no need for specialist materials. It also offers easier customisation and rapid changes
and is compatible with many packaging materials and substrates that are not possible with Traditional off-set or toner based print production.
High productivity: - Konica Minolta’s highspeed UV LED inkjet technology can print at 3,000 sheets per hour simplex and 1,500 sheets per hour perfecting. This enhances business productivity levels by delivering content and quality at higher production speeds, which also increases the costeffectiveness of the entire print process.
Commercial print is rapidly changing with data-driven personalisation and faster and shorter run lengths set to shape the industry over the next decade. Production inkjet technology forms a core part of this future and its growth as an innovative technology is bringing a new level of costeffectiveness, productivity, and long-term success to the print industry.
Chris says, “At Konica Minolta, we understand the demanding nature of printing and the role emerging technologies play in shaping future business success. To ensure print businesses thrive in a digital landscape, we provide innovative solutions that add extra value, outstanding flexibility, and superior quality.
“Our UV LED inkjet technology provides the best speed, quality and uses state-ofthe-art Konica Minolta print heads and sensing technologies.
“We look forward to discussing the ways that our how our high-speed inkjet technology can help take your business to a new level of performance.”
The new AccurioLabel 230 offers enhanced productivity, job flexibility, operability and excellent image quality at an affordable system cost, making it the perfect solution to ensure you always deliver high quality labels on time, every-time. Printing at an impressive 23.4 metres per minute and with a compact footprint, this label press is perfect for label converters looking to convert to digital technology as well as those entering the label market.
To rethink label printing, simply visit: konicaminolta.co.nz/AccurioLabel-230
From its Glenfield base, on Auckland’s North Shore, Broderick Printing & Design pumps out a range of printed products. Its customers have come to depend on Broderick’s ability to provide high quality printed collateral, from offset and digital printing to wide format and packaging solutions.
Recently, the company installed a Ricoh Pro C9500. Managing director Jonny Broderick says, “We first connected with Ricoh just prior to drupa 2016; that ultimately lead to the purchase of our first high speed production machine, the Pro C9100. We have maintained our relationship with Ricoh and we are always keen to see their latest offerings.
“To maintain our outstanding reputation in the market, we must ensure we’re delivering on the quality and service our clients have come to expect. After sighting and comparing prints from the Ricoh Pro C9500, through Ricoh’s Darren Daffern, it was a no brainer. That was enough for me to start the process of crunching the numbers.
Jonny has a critical eye. He says, “The Ricoh Pro C9500 delivers phenomenal prints; I would argue that of offset quality. The solids are beautiful. We are doing large runs, and it handles them easily. It is quite a hungry machine.”
With a maximum speed of 135 ppm (A4) and high productivity on mixed media jobs, the Ricoh Pro C9500 uses twin toner bottles for uninterrupted, continuous printing. You can add up to three vacuum feed units to increase the feeding capacity to 18,100 sheets. It supports media from 40gsm to 470gsm and offers an extra length sheet of 960mm.
The engine controller, the Ricoh GC OS, is a completely new and intuitive UI designed for production printing customers providing enhanced media settings; integrated management capabilities for multiple printers; as well as higher integration with remote diagnostics and service systems.
An optional unit automates quality, registration, and colour fluctuation
inspection. This provides flexibility to choose how the printer operates after inspection according to requirements. The unit performs colour diagnosis automatically, alongside real-time monitoring and colour stabilisation during printing. This includes inspection of image quality imperfections such as spots and streaks; front-to-back registration for image position alignment; and colour fluctuations.
Jonny adds, “Overall, the increase in speed and general print quality are impressive. Also, there is less battling to make jobs work. And there are lots of other features that help production, for example, we have brought a lot more shorter run packaging in house because it can handle much thicker one-sided boards.”
Other features that set the Ricoh Pro C9500 apart include VCSEL technology which emits 40 laser beams simultaneously, resulting in 2400dpi × 4800 dpi image resolution. The press achieves crisp text, fine lines, smooth gradations and realistic image reproduction with its Active Toner Density Control. Its digital front end is still Fiery based, but on a more powerful platform. There are two options, for midrange production and VDP requirements.
“The service and support from Ricoh is very responsive. The techs are well
educated on the machine, and we have our own Scotty Durham, who is excellent on the Ricoh machines. He knows the ins and outs and has actually taught the Ricoh guys some things. We still run our Ricoh 7200 SX. It complements the Pro C9500; they are calibrated, and we can swap jobs between them.”
For a smaller print company, Broderick Printing & Design completes a significant amount of work. Jonny says, “As a team of only 12, it’s not uncommon to see half the crew involved in a single job, where that is required. For the work we do, planning is key – getting an end date and working backwards with our clients. We take the time to educate our clients, so they know what is involved and understand the processes.
“Let’s be honest, this is a business, and we’re here to make money. So, having jobs well planned from start to finish gives us the best chance of doing that. Obviously, we need to have the ability to adapt to changing circumstances and we do that when we need to.
“One of the best parts of what we do is making our customers happy, especially on the difficult jobs. Delivering on intricate jobs and promotions that exceed the customers’ expectations makes all the hard work worthwhile.”
Dapeng Rotacut 5575 rotary die-cutter strips waste in one pass.
Pressnet offers an extensive range of products encompasses printing machines, die-cutting equipment, paper cutting machines, binding solutions, laminating machines, and more, catering to diverse requirements across various sectors.
The leading provider of cutting edge machinery solutions for the printing and packaging industry has expanded its portfolio with a new Rotary die cutting solution from manufacturer Dapeng.
Charlie Scandrett, managing director at Pressnet, says, “Dapeng, situated in Rui’an China, is primarily a paper guillotine manufacturer. However, 11 years ago, Dapeng began to develop rotary die-cutters.”
Pressnet suggested to Dapeng that it could increase its machine’s sheet size to 550mm x 750mm to suit the medium printer die cutting market and “to replace the aging Heidelberg SBGs”. Charlie says, “The result is the Dapeng Rotacut 5575, which is a servo-motor setup machine capable of die-cutting and stripping the waste in one pass. Its
gearing and side frames are as heavy duty as an SBG.”
Suitable for small batch and long run production, the integrated Rotacut5575 rotary die cutting machine uses a flexible die forme which is easy to replace.
Features include automatic paper lifting, automatic paper feeding, double sheet detection, chasing mark alignment die cutting, automatic deviation correction, automatic waste discharge and other functions.
The separator section can be directed to blow away waste, and adjustment does not require tools. The separator section and collection section can be pushed away as a whole for changing the die forme.
The wheel of the separator section is electrically controlled, timed up and down to deliver the final product smoothly to the receiving table smoothly
Applications include stickers, tags, wine labels, playing cards, small boxes and so on. It handles coated paper, cardboard, PE film, and other media.
It handles sheet sizes from 240mm x 280mm up to 550mm x 750mm at speeds of between 1,000 and 6,000 cycles per hour. It handles a range of media from 0.15mm to 1.0mm in thickness.
Foyer the first
Recently, Pressnet completed its first Dapeng Rotacut 5575 regional installation at Foyer Printing on the Gold Coast. Charlie says, “They are already die cutting and stripping drink coasters at about 100,000 pieces per hour.”
Foyer Printing director Ron Rankin says, “We have run the Dapeng Rotacut 5575 for about a month. It is the first in the country, so we are the guinea pigs for the machine, which is proving to be a good workhorse.
“Obviously, there is a learning curve when you have a new machine, but we have smoothed it out and the Rotacut 5575 is ploughing on. There is still more refinement to come as we want to get it to its full potential. At the moment, we are die-cutting, but we are looking forward to using the other capabilities that it has such as scoring and kisscutting. We do have plans for that later down the track. As yet, we haven’t run it at its maximum speed of 6,000 cycles per hour, but it is handling everything we can throw at it.
“Charlie and his engineer have helped us sort out any teething problems and concerns that we had. For instance, they gave us advice on getting the correct angles for the feeding suckers. We were also initially concerned that we might not get good longevity from the knives, but they are also performing. The Rotacut 5575 is quite gentle on the knives.”
Foyer Printing has had a long relationship with Pressnet. Ron says, “I have known Charlie for many years and over the last 12-15 years, he has supplied us with several machines. He is very knowledgeable, and he is a man of his word.
“We wanted some custom elements added to our Rotacut 5575 and he managed to get those done at a fair rate. Charlie always does his best to make sure we are happy. If we need anything, he is only an hour away,”
The affordable future of general die-cutting, using rotary, flexible, magnetic dies
SPECIFICATIONS:
Size: 240 x 280mm to 550 x 750mm
Speed: 1,000 - 6,000 sph
Thickness: 0.15 mm to 1.0 mm stock
Waste: Automatically stripped into bin underneath
Swing Tags: Holes stripped on the run
OPTIONS:
• Programmable individual product stacker
• Ladder conveyor of waste to a large wheelie bin
• Sheet stacker for the unstripped sheet
• Magnetic lower cylinder for embossing die
Installed in Australia die-cutting drink coasters
Built with heavy side frames like a cylinder die-cutter, all Western electronics and very user-friendly.
HP Indigo offers the most sustainable and efficient way to produce on-demand flexible packaging as seen with the HP Indigo 200K Digital Press.
Sustainability efforts have been influencing the printing industry and radically changing business operations and models for many years now.
At HP, the company is committed to constantly improving every aspect of its ambition to positively impact the lives of people and communities around the world.
“As leaders of the print and packaging industry, we are always driving efforts to improve energy efficiency, increase circularity, reduce waste, and help our customers reduce the environmental impact of their businesses,” HP Indigo and Scitex vice-president and general manager Noam Zilbershtain said.
A new era of sustainable print with HP
The shift from analogue to digital print production, exemplified by HP Indigo, heralds a sustainable transformation in the printing industry.
Digital printing eliminates the need for printing plates, reducing waste associated with production, storage, and disposal. It offers flexibility with on-demand printing, minimising inventory waste and enabling quick responses to market demands.
HP Indigo’s sustainability commitment extends to carbon emission reduction and
circularity, prioritising energy efficiency and material reuse. Practices include using recycled materials, designing presses for reuse and recycling, and adhering to regulatory standards.
As brands increasingly make public targets and commitments to work toward making packaging 100 per cent recyclable or reusable, partnering with HP puts you in a position to be the go-to print service provider for brands that are working toward fulfilling their commitment.
In a world where customers demand highly crafted solutions, only HP Indigo technology gives you and your business the ability to meet any need across any type of commercial printing, labels, or packaging job.
The HP Indigo 200K Digital Press has been developed to give digital flexible converters a competitive edge with better productivity, on-demand delivery, no minimum orders, unique designs, reduced energy consumption and minimal waste.
The press is based on digital technology for digital flexible packaging and has a successful install base of more than 300 series 4 HP Indigo 25K digital presses worldwide.
The series 5 HP Indigo 200K Digital Press prints up to 56 m/min increasing the productivity of high-margin, sustainable short runs of digital flexible packaging to be delivered in days.
“The HP Indigo 200K is a mid-web digital press especially designed for converters addressing the needs of brands in flexible packaging, but it also serves the growing requirements of the label and shrink sleeve industries for higher productivity and wider format,” Zilbershtain said.
“Flexible packaging is a growing market, and as HP Indigo customers are growing much faster than the market, I have no doubt that the HP Indigo 200K Digital Press will open the door for more flexo converters who want to join the success and reign in industry 4.0.”
The HP Indigo 200K offers a 30 per cent increase in speed and a 45 per cent boost in productivity compared to the HP Indigo 25K.
Featuring gravure-matching colour quality based on the HP Indigo Liquid Electro Photography (LEP) and One-Shot Color technologies, the press also offers the broadest range of ElectroInks.
It is designed to print high-coverage packages with white on most industrial substrates, both surface and reverse. Additional business opportunities include unique brand protection elements.
The HP Indigo 200K features HP Indigo’s PrintOS software automation capabilities for batching, ganging, and variable data, as well as faster, accurate colour match and workflow.
It adds automation tools for operator efficiency, coupled with sustainable production, circular packaging and food packaging safety.
All enquiries can be directed to Currie Group, the authorised HP distributor in Australia and New Zealand.
After two decades as an offset printing specialist, Auckland-based PrintLounge is embracing the new business opportunities available from digital diversification including its recent investment in a Durst Tau 340 RSC E LED label press.
Just weeks after installation in June this year, PrintLounge owner Steve Sheppard is already seeing an immediate return on investment from his new Durst Tau 340 RSC E LED label press.
“When we bought the Durst we wanted to upgrade our existing toner based solution to a machine that would produce quality labels at 1200dpi with a wider colour gamut and would allow us to market ourselves to pretty much anybody who came to us looking to put something on a supermarket shelf.
“Unfortunately the equipment we had before the Durst didn’t have white ink, so this meant we were saying no to a lot of jobs when we were quoting – and I hate saying no to work.
“Since we installed the Durst we have brought back in-house a number of customers that we previously had to outsource to other label companies. We have also been winning new work from many sources, including social media, where we have always been active.
“Just this morning we received an order from a client that wanted 2000 labels within a week as their current label company was unable to do it. Later in the morning we received a second job from the same company – and these jobs will be perfect for the Durst.”
Upgrading to the Durst
Durst head of sales for labels and packaging, Graham Blackall, first discussed a label solution with
PrintLounge over five years ago. Although Blackall was unsuccessful with the sale on that occasion, he has maintained a close relationship with Sheppard and the PrintLounge ever since, so when he joined Durst at the end of last year, he knew the Tau would suit their business perfectly.
“I have been working with Steve for the last 25 years after he gave me a phone call about some second hand equipment and since then I have sold him nothing but new equipment. He is an entrepreneurial businessman as well as a craftsman that has a strong understanding and appreciation of the machines,” Blackall said.
“About five years ago, Steve recognised he needed to diversify his business due to the pressures on offset and the reduction in
order volumes. What I was offering at the time was too big a step for his company and he bought another machine that was more cost effective. I told him to buy a very good finishing unit, as he would only be buying it once.
“PrintLounge quickly outgrew their previous label press, and after a lot of consideration he went with the Tau 340 RSC E LED because he wanted to have the ability to talk to anybody about any quality of labels with no limitations – whether it was about colour gamut, quality, productivity as well as support and service. The process of upgrading to the second machine was a nine-month discussion. It was a serious investigation into the labels category from day one five years ago about a very deliberate diversification process from dipping the toe into the category through to now purchasing the Durst label press.”
Sheppard finally settled on the Durst Tau 340 RSC E LED within the last hours of the final day of Labelexpo Brussels in September 2023 after numerous discussions and researching the market on both sides of the Tasman.
“We were looking for a machine that could advance us from our original label press we had at the time that was only running CMYK and had a limited colour gamut.
We had to choose something that everyone else wasn’t doing and this is why we have gone down this path and that’s why it has been successful,” Sheppard said.
“By upgrading we wanted to increase our colour gamut and we wanted white so we could print on clear and silver polypropylene stocks and really open up the label market for us to a wide range of
other jobs. We had come to a certain point with our previous machine where it was going well, but we were missing out on jobs because it didn’t have the orange and green that the Durst can do and we also need white ink as well.
“Before we bought the Durst, we were pretty much decided on another machine that was 600dpi and we thought
the Durst was out of reach for us. Even though the price was a little higher, the Durst ticked a lot of boxes for us – build quality, 1200dpi resolution, colour gamut and white ink. Plus the Durst is upgradeable to 80 linear metres per minute, so the machine can grow with us!
“We had done plenty of homework over about nine months including travelling to Australia and inspecting various machines in Melbourne and Brisbane. I visited a number of different printers with similar Durst machines in Australia including the 1200dpi machine and a slightly older machine. They all had very good things to say about the Durst technology.”
“We are definitely trying to diversify here at PrintLounge – if we look back 10 years ago we didn’t have a digital offering and now it represents a solid double digit percentage of our turnover. You have to diversify your business – you can’t go on doing the same thing otherwise you will not survive,” Sheppard said.
“Like a lot of other businesses, we started off as a conventional printer and now we offer commercial print, packaging, digital printing and rolls labels. Our diversification into roll labels has been one of the best things we could have done as the label market is growing –particularly here in New Zealand.
“There are a lot of label printers with an old school mentality where they are only offering lead times of two to three weeks.
We are seeing this as an opportunity for our business. Now we have the Durst, we have started to print labels using white ink as well as clear work and all of the different colours. The quality is great and we can also add varnishes on top. We recently ran a 3400 metre job in just over an hour with three role changes on the Durst – and that wasn’t even at the top speed. This means we can almost compete with flexo over shorter runs which is very exciting. We have also invested in an LED offset press, so it seemed like the correct path to invest in LED with the Durst as well over a conventional mercury lamp – less power and less heat and it also delivers a nicer drying system that works very well.”
With over 42 years of experience as an analog printer and letterpress specialist, PrintLounge digital operator Mike Anderson was recently trained up to become the operator of the Durst Tau 340 RSC E LED label press.
“I’m seeing a much bigger range of nice bright strong greens and pinks from the colour gamut on the Durst that I have not seen on any other label printer. And when you compare the Durst to other machines – the analog or offset machines are not even close. It is especially notable when you profile the material and see the full range of colours it can do. Since I have had an analog printing background already, the transition to the Durst was not very complicated. The key for me is to know what to do when you need to make a colour adjustment and my conventional
background has made my transition quite easy.”
Brittney Anderson, who has worked with PrintLounge as pre-press digital supervisor for over four years has recently started working with the Durst software including the Workflow Plus modules.
“The Durst label press software and Workflow Plus software has been amazing to work with. Every day after I started playing around I would find more features and say ‘Oooh that’s cool’ – such as being able to create a die-line as well as the white in the software. There is so much in it and we essentially don’t even need to use Pitstop or anything beforehand – you can drop the file in and do everything within the software. The way everything is laid out makes it very easy to understand. Things that can be quite difficult with pre-press with other software is a click of a button on the Durst software.”
Durst Oceania managing director, Matt Ashman, said he is very pleased to have another label press installed in New Zealand.
“I am very proud that an innovative business such as PrintLounge has invested in the Durst Tau 340 RSC E LED. This is a company that has always tried to push the boundaries of what was considered the norm. They have always tailored their business to focus on what their customers need and this a testament to their continued success and growth in a very competitive market.”
Why understanding and minimising the true cost of hiring wrong people is important.
Professional service businesses are challenging to run for its leaders and owners. The costs of hiring the wrong person can amount to between two and five times the person’s salary. Understanding and minimising the true cost of hiring wrong people is important.
The most visible cost of hiring the wrong people is financial recruitment and training costs being the main ones. Every new hire comes with recruitment expenses, advertising, interviewing and onboarding. When a new person leaves or we ask them to leave before we have realised the benefits of that person, the investment is lost, and the cost repeated.
In service-based businesses, efficiency is key. People who are not a good fit may struggle to perform their job leading to reduced productivity. This can slow down operations, increase workloads and impact customer ratings.
Poor hires often lead to higher turnover rates. High turnover can be costly as it means constant recruiting, hiring and training which is common in this industry. This means there is a feeling of survival at times just to deliver the service, rather than move into a feeling of thriving where you are making more profit.
Customer experience is what makes and breaks a business. People are the face of the business who shape customer perceptions. Poor hires can impact many areas. People who lack the right skills, attitude or training give poor customer
The costs of hiring the wrong person can amount to between two and five times the person’s salary
service. This might mean failing to care for customers, which may lead to negative reviews and a damaged reputation.
Consistency is key in building a trusted brand. People who do not act with the business values can create terrible customer experiences.
The wrong people can significantly affect the culture and the morale of your business. When a person is not performing well or fits poorly within the team, they not only affect their output but also affect the morale and output of other people in the team.
The saying ‘one bad apple spoils the cart’ is true when it comes to people. High performing people can get demotivated if they have to do extra hours and manage workload for the people that underperform. This leads to a decrease in productivity and in the worse case, high performers leave who are harder and more expensive to replace.
Every business has its own culture. People who do not fit well within this culture cause more conflict which can create a toxic work environment.
Hiring the wrong people can also have issues that affect the vision you are trying to achieve. Wrong people slow the growth of the business. For example, a low performing manager can impact the retention of people who report to them, which means that it takes longer for you to realise the growth of your business.
“The wrong people can significantly affect the culture and the morale of your business. When a person is not performing well or fits poorly within the team, they not only affect their output but also affect the morale and output of other people in the team.”
Poor hires lack skills to find or act on new business opportunities. This results in the business falling behind competitors who are better positioned with the right people. Here are some strategies to help get the right people:
1. Slow down the hiring processes: Hire for attitude and train for skill. Do not rush through the hiring process because you are busy, especially for key roles such as management.
2. Ongoing training: Even though training is expensive, what is the cost of not training and people impacting your culture? Keep investing in training so your people are getting the repeated message on what you are trying to achieve.
3. Positive culture: A strong culture can help retain top people and create a place of work where people want to work and recommend that place to others also.
4. Performance management: If you do not have the right people in place, move them out fast from your business. Manage non-performance early and set the standards for the right behaviours early on.
By focusing on these strategies, businesses can minimise the costs of hiring the wrong people and create a more productive and positive work environment. And the right people in the right jobs can make a big impact on your bottom line.
Shivani Gupta, author of Getting Your People to Step Up, is a speaker, trainer and facilitator. www.askshivani.com
Stop
Bring new life back into your old printing machine
Nekkorb Solutions supplies Rutherford Graphic Products (RGP) and X-Rite in Australia and New Zealand
User friendly and engineered to reduce time, labour, paper and ink costs, it assists with colour management and improves colour accuracy, making it an excellent companion for every printer and print job.
• Save money
Bring new life back into your old printing machine
• Ink
Energy
• Save money
• Save money
Bring new life back into your old printing machine
• Ink
• Paper
• Best in class colour consistency
Ink
• Energy
• Save money
• Paper
Paper
• Seamless integration with most rips
• Energy
• Best in class colour consistency
• Ink • Paper
• Best in class colour consistency
In addition, IntelliLoop handles both standard press runs and the more sophisticated, high gamut presswork that requires light cyan and light magenta inks. The system easily manages spot colours, including metallic and white inks.
This closed loop colour measurement solution delivers fast make ready and gets the machine into production quicker than ever before.
.fr your old printing machine
Acombination of RGP’s IntelliLoop system, which automates pressside colour setups and X-Rite’s IntelliTrax, a fully automatic scanning system, can reduce ink and paper costs on all print runs, said Nekkorb Solutions managing director Frank Brokken.
Printwell’s 15,000 square metre shop houses three Heidelberg full-web, six-colour heatset (with ribbon deck) presses; one Heidelberg Harris M-110, six-colour heatset web press; a six-unit Heidelberg non-heatset web press; as well as two, Heidelberg sheet-fed presses and digital equipment.
Because of the time, ink and paper required for web press colour setups, Printwell has tended to forego short print runs in the past. However, with the RGP and X-Rite retrofit solution, Printwell has reversed its short-run print strategy.
Printwell president Paul Borg said, “To be profitable with short run work on web presses, Printwell has to get colour right the first time, every time.
This closed loop colour measurement solution delivers fast make ready and gets the machine into production quicker than ever before.
• Seamless integration measurement solution delivers fast make ready and gets the machine into production quicker than ever before. Ready or
Energy • Best in class colour This closed loop colour measurement solution delivers fast make ready and gets the machine into production quicker than ever before.
Ready or considering the upgrade?
He pointed to the experience of awardwinning commercial print company Printwell. Based in Michigan, US, Printwell runs several of the IntelliLoop systems retrofitted to its Heidelberg presses. These systems adjust and maintain colour accuracy throughout the print process, quickly and easily.
Rutherford fr
Ready or considering the upgrade?
Ready or considering the upgrade? Contact us now
Ru
Get in touch with our partner Contact details: Frank:
RGP engineers and manufactures its colour console and closed-loop system as a straightforward, uncomplicated retrofit to most makes of offset printing machines, enabling them to achieve higher print standards, greater print consistency and increased profitability than in the past. The RGP colour console allows quick and easy adjustments. It ties into X-Rite and Pantone systems and maintains colour accuracy throughout the printing process.
“The job control, colour accuracy and colour consistency using the Rutherford and X-Rite process is simple. Make a scan, feed the data to the press, and get consistent results. We enjoy not having to make constant press checks and the subsequent paper cost savings. It is fast and it is accurate. We’re happy, and, even better, our customers are happy. Our job opportunities have increased exponentially, especially in the once difficult short-run area. Rutherford Graphic Products and X-Rite has helped get us to this point.”
Brokken added, “Please contact us at Nekkorb Solutions to discuss how these advancements can help your business improve its profitability.”
New Zealand label and packaging manufacturers can now add Bar Graphics solutions to their armoury.
Available from Nekkorb Solutions, Bar Graphics designs and manufactures a wide range of finishing solutions for the label and packaging sector. Nekkorb Solutions commercial manager Tash Brokken said, “With these solutions, you can enjoy highspec features commonly found on more expensive machines”
Their advantages include:
BGM Elite 410/450 iSR Label Inspection Slitter Rewinder
BGM Elite 410/450 iSR Label Inspection Slitter Rewinder
Boasting automatic unwind braking with an adjustable roll end stop, as well as reversible rewind and machine diagnostics, this machine lives up to its reputation as the most cost-effective, compact, robust and free-standing Label Inspection Slitter Rewinder on the market.
With running speeds of up to 300m/m, and requiring just a 230v/13amp supply, this is a highly efficient machine. Roll end wastage is as little as 1.2m. A colour HMI touch screen allows the operator to setup the machine quickly and efficiently. Plus, no operator intervention is needed with the automatic unwind and rewind tension control system once set, thus maximising productivity.
BGM Elite eDSRt Die Cut Slitter Semi-Automatic Turret Rewinder
With speeds of up to 250m/m, this is the fastest, free-standing, semi-automatic turret die-cutting machine on the market.
For loading, the weight of the die is supported by a bottom guide rail, meaning the operator can quickly and effortlessly load dies into the machine. This feature vastly improves operator setup and handling times, and it helps to reduce damage caused by incorrect loading (a common problem in conventional die stations).
The easy loading die station accommodates most styles of dies, utilising existing dies, and minimising any tooling costs. A twospindle semi-automatic rewinder enables you to pre-load cores on to one spindle, while the second spindle is rewinding. The turret also incorporates an automatic tail cut and applier.
With the aid of an integrated support attachment, it is possible to run 12.7mm cores. Users of this system have claimed an increased productivity output by as much as 60 per cent.
BGM Elite Label-i Automatic Inspection Slitter Rewinder
BGM Elite Label-i Automatic Inspection Slitter Rewinder
Cost-effective, compact, robust and free-standing, this machine enables you to inspect, slit and rewind unsupported and supported substrates as thin as 15 microns at speeds of up to 300m/m.
Simply key in the rewind shaft size and the machine will automatically adjust the acceleration and deceleration times. It offers automatic unwind braking with an adjustable roll end, reversible rewind and machine diagnostics. Plus 100 per cent inspection and defect detection of the printed web is possible when fitted with an Esko AVT Helios inspection camera system from Nekkorb Solutions.
BGM Elite Label-i Automatic Inspection Slitter Rewinder
Free-standing label inspection slitter rewinder suitable for paper labels, transparent clear-on-clear & films
BGM Elite Comflex Compact Digital Converting Finishing System
A fully offline entry level digital converting finishing solution suited for any digital print house
BGM Elite Digiflex Digital Converting Finishing System
Use as a spot register station or a simple flood coating station. Available in both full or semi-rotary die cutting versions
Suitable for paper labels, transparent clear-on-clear and films, the Label-i Automatic Inspection Slitter Rewinder will increase your productivity. Get in touch with our partner
Stress is ever-present in today’s fast-paced world, particularly in the modern workplace. From tight deadlines to high-stakes negotiations, business can often feel like a battlefield, with many stuck in a fight or flight cycle. This ancient response, once necessary for survival in the wild, now manifests in our professional lives, making it critical to understand and manage stress effectively.
First described by Walter Cannon in the 1920s, the fight or flight response is the body’s automatic reaction to perceived threats. When triggered, stress hormones such as adrenaline and cortisol flood our system, preparing us for action. In the past, this reaction helped humans outrun predators. Today, it might push someone to power through a late night deadline or tackle a challenging business presentation.
While this response can provide a short-term performance boost, chronic activation leads to adverse outcomes like burnout, decreased productivity, and various health problems. Recognising when the fight or flight response is helpful and when it’s harmful is critical to navigating modern business challenges.
Fight or flight can help
There are situations where the fight or flight response can be advantageous in business. In moments of crisis, this heightened state can enhance focus and decision making, essential for handling unexpected challenges. In competitive settings, such as high-pressure sales or negotiations, the energy surge can drive professionals to perform at their peak, sharpening instincts and fuelling creativity.
For some, stress even sparks innovation and problem solving, particularly when deadlines loom. Leveraging this response
wisely in certain situations can provide a critical edge in the business world.
However, problems arise when the fight or flight mode becomes a default state. Chronic stress disrupts decisionmaking, shifting thinking from strategic to reactive. Teams suffer with stressed individuals more prone to conflict, hindering collaboration and damaging workplace relationships.
The serious long term health effects of constant stress include increased risks of cardiovascular problems, weakened immune systems, and mental health challenges. These factors reduce individual performance and impact the organisation’s productivity, creating a toxic cycle of stress and underperformance.
In response to these challenges, progressive companies are implementing comprehensive stress management programmes with initiatives ranging from stress awareness training and mindfulness programmes to restructuring work environments with flexible schedules and de-stress zones.
Leadership plays a critical role in setting the tone for stress management. When executives model healthy approaches to stress, it encourages employees to do the same. Effective strategies often include educating teams about recognising and managing acute stress, creating opportunities for rest, and fostering a culture that balances performance with well-being.
Investing in comprehensive wellness programmes addressing physical, mental, and emotional health can see tangible returns: increased productivity, reduced absenteeism, and improved employee
retention. This is not just a feel-good strategy; it’s a smart business move. Progressive companies are redefining success itself. While financial metrics remain essential, they’re no longer the sole measure of a company’s worth. Employee satisfaction, work-life balance, and well-being are crucial indicators of a company’s health and future potential.
As businesses evolve, so do the approaches to managing workplace stress. Technology, environmental design, and policy changes are shaping more harmonious work environments. For example, wearable devices that track stress levels allow employees to monitor and manage their stress in real-time, enabling proactive stress reduction.
Biophilic office designs—integrating natural elements such as living walls and natural light—are becoming more common, as research shows that exposure to nature reduces stress and enhances well-being. Additionally, some companies are implementing mandatory downtime policies, requiring employees to disconnect during off-hours or vacations fully. This approach directly challenges the always-on culture that contributes to chronic stress.
By recognising how stress influences the body and mind and cultivating a workplace culture prioritising performance and wellbeing, businesses can empower employees to survive and thrive. This transformation elevates individual well-being while fuelling innovation, creativity, and long term prosperity.
The future of business doesn’t lie in a constant state of fight or flight but in mastering the art of navigating the modern work landscape with agility, resilience, and mindfulness. As we continue to think laterally and embrace a more holistic approach to the challenges of today’s workforce, the key to unlocking our full potential will be harnessing the power of our primal instincts on our terms, for a future that thrives beyond survival.
Mick has spent the past decade building printIQ into one of the most recognised software brands in the printing industry, and with over four decades of experience, Mick truly has ink in his veins.
The ideal solution for handling a high mix of work, including many types of short-run jobs, multi-board and double-sided production.
Enabling you to offer near-photorealistic quality and fine-art applications on a vast range of media, particularly on unusual applications. With the Roll Media Option installed you can print on flexible media.
With more than 8,000 installations worldwide, the Arizona series, made in Germany, has earned a reputation as a robust and reliable workhorse that you can depend on.
The latest PRISMAelevate XL is an easy-to-use software application that enables a printing height to 4 mm (0.157”) to help you create stand-out, tactile artwork for elevated print applications that enhance and expand your product offering. You can now unleash a broad range of high-margin applications like high-value signage, décor materials, disability signage, package prototyping and tactile art reproductions.
Benefit from Advanced Image Layout Controls for last-minute adjustments at the printer, reducing material waste, and PRISMAservice tools for predictive maintenance and remote assistance.
Current Arizona 1300 with FLOW technology owners can upgrade to the latest version with FLXflow functionalities, including Float and Instant Switch functionalities, and new Advance Image Layout Controls.
FLXflow in a nutshell
Hold, Float and Instant Switch – to enhance media handling.
The Hold function uses patented airflow technique to secure various media types in place with minimal masking, while the optional Float function creates an air cushion to easily position heavy or challenging substrates, reducing media damage risk and enabling smooth registration. The Instant Switch feature allows for easy transition between Hold and Float modes using foot pedals, simplifying printer operability and media removal.
Designed with circularity in mind
Reducing waste and energy consumption – FLXflow minimises the need for masking underlays, while UV-LED printing cuts energy use by at least 15% compared to previous models. Featuring power-saving options like first-time-right printing and instant-on functionality. Its UL GREENGUARD Gold certified inks make prints safe for use in sensitive environments.
PRISMAelevate XL Pro for tactile prints up to 4mm
PRISMAguide XL – Pro Arizona
ONYX Thrive RIP Software to increase pre-press efficiency
White Ink for a Month to grow new markets
steve.wiltonjones@aarque.co.nz
Level up your game
LEVEL UP YOUR
CREATIVITY
Wide, unique application range including white ink
LEVEL UP YOUR
PRINTER
Modular design, field-upgradeable as you expand BUSINESS
With the Colorado M-series, 1.6m roll-to-roll printers powered by the patented UVgel technology, you’ll level up your business, your creativity and your profitability.
Say ‘yes’ to more jobs, no matter how challenging, and meet your high productivity and turnaround standards at the same time. Create unique applications with matte and glossy elements in the same print, without varnish. Maximise your profit potential with a smart financial investment in the large-format graphics business. What’s even better: this nextgeneration Colorado M-series is upgradeable in the field, allowing you to level up your machine as you level up your business.
The power of UVgel, now with white ink!
Use unique UVgel technology to print large-format jobs with white ink, with speeds equivalent up to 3 times faster than comparable technologies. No maintenance or printhead treatment needed.
FLXfinish+
FLXfinish+ is the unique ability to print matte, gloss or mixed matte and gloss in one go, shaking up the world of large-format graphics.
FLXture+
With FLXture+, you can add subtle surface detail to your prints, creating a luxurious and intriguing feel for your products. Design beautiful, high-value packaging, attention grabbing labels and easily enhance your products with new surface textures without complicated material combinations.
LEVEL UP YOUR Low total cost of ownershipa smart financial investment
LEVEL UP YOUR
Productive and sustainable by nature
PRISMAguide XL – Pro
FLXfinish+
FLXture+
ONYX Thrive RIP Software to increase pre-press efficiency
White Ink for a month to grow new markets
Equipment Sales Consultant, Aarque Group 021 719 634 steve.wiltonjones@aarque.co.nz
*Conditions apply
Arlette Farland discusses the benefits of the HP Latex R series printers.
As environmental sustainability becomes a priority for businesses worldwide, the printing industry is rapidly evolving to meet the demand for greener, more responsible production methods.
The HP Latex R Series printers, with their innovative water-based technology, stand at the forefront of this change.
For New Zealand businesses looking to reduce their environmental footprint without compromising on quality, HP’s R Series printers offer an ideal solution.
They are available through Computaleta, HP’s trusted corporate partner in New Zealand, so businesses can also benefit from local expertise, local support and exceptional customer service.
The sustainability advantage of HP Latex technology
HP’s commitment to sustainability is evident in the design and function of the HP Latex R Series. These printers are
engineered to deliver high quality results while minimising environmental impact, making them a responsible choice for businesses in industries ranging from signage to interior decoration.
Water-based HP Latex Inks reduce harmful emissions
One of the most significant sustainable benefits of the HP Latex R Series is its
use of water-based HP Latex Inks. Unlike traditional solvent or UV-curable inks, Latex inks are free from hazardous air pollutants. This makes them safer for operators and the environment, reducing harmful emissions and promoting better air quality in the workplace.
For industries looking to meet stringent environmental standards, HP’s waterbased Latex technology provides a viable alternative to traditional printing methods. Prints produced with Latex inks are also odourless, making them suitable for use in sensitive environments such as healthcare facilities, schools, and retail spaces.
Energy efficiency and waste reduction
In addition to utilising eco-friendly inks, HP Latex R Series printers are designed with energy efficiency in mind. The printers come equipped with thermal printheads, as a result, businesses can reduce their energy consumption and lower their operational costs while maintaining high production speeds and quality.
HP’s commitment to reducing waste is also reflected in its use of recyclable materials and packaging. HP offers robust recycling programs for used ink cartridges and printheads, making it easier for businesses to minimise their waste output.
This closed loop system, supported by Computaleta, offers a take-back programme that allows users to return used ink consumables for recycling helping businesses contribute to the circular economy. In addition, HP Latex Ink is produced in a facility that uses reclaimed water.
Because HP Latex R Series printers do not use harmful solvents, there is no need for specialised ventilation systems, further lowering installation and operational costs.
This is especially beneficial for small to medium-sized businesses looking to expand their printing capabilities without incurring significant overhead.
Durable and versatile printing for a longer product lifecycle
Sustainability extends beyond production processes to the lifespan of the printed materials.
HP Latex prints are known for their durability and resistance to scratches, weather conditions, and fading. This means that outdoor signage, banners, and vehicle graphics created with the HP Latex R Series can withstand the elements for longer, reducing the need for frequent replacements. As a result, businesses can minimise their material use and waste over time.
New Zealand businesses across various industries are already benefiting from the HP Latex R Series printers’ sustainability and versatility. Some of the key applications include:
The durability and weather resistance of HP Latex prints makes them ideal for New Zealand’s outdoor signage and advertising industry, where vibrant, longlasting graphics are essential.
The ability to produce high-quality prints that withstand New Zealand’s diverse climate means businesses can rely on the HP Latex R Series for eye catching signage that performs well in both urban and rural environments.
With sustainability increasingly important in the packaging industry, HP Latex R Series printers offer a valuable solution for businesses looking to create eco-friendly packaging.
The printers’ ability to work with both rigid and flexible substrates enables companies to produce packaging that is not only visually appealing but also environmentally responsible. Waterbased inks ensure that these products can be safely used for a variety of applications, with minimal environmental impact.
In the competitive world of retail, where first impressions are crucial, the HP Latex R Series provides businesses with the ability to produce high-quality, durable, and customisable point of sale (POS) displays.
The versatility of these printers allows for short-run, customised prints that fit the unique needs of each retail campaign. With vibrant colours and crisp details, retailers can effectively attract attention while staying true to their sustainability goals.
The HP Latex R Series is also making waves in the interior design industry, where businesses and individuals alike are seeking sustainable solutions for custom décor.
From wall coverings and murals to
decorative panels and furniture wraps, the R Series’ ability to print on a wide range of materials makes it ideal for creating personalized, eco-friendly interior elements. The Latex prints are durable, non-toxic, and easy to apply, offering a perfect solution for both residential and commercial spaces.
Environmental certifications and recognition
HP’s commitment to sustainability is further validated by the numerous environmental certifications and recognitions the Latex R Series has received.
HP Latex inks have achieved certifications such as UL Ecologo and Greenguard Gold, which ensure that the inks meet stringent environmental and health standards. These certifications are especially important for businesses in New Zealand looking to align their operations with global sustainability standards, particularly in sensitive environments like schools, hospitals, and retail spaces where air quality and safety are critical.
The R Series printers have also been awarded the Energy Star certification, confirming their energy efficiency and contributing to lower operational costs for businesses.
Advance your sustainable printing with HP and Computaleta
For businesses looking to reduce their environmental footprint, increase operational efficiency, and deliver highquality products, the HP Latex R Series represents a future-focused investment that aligns with today’s sustainability goals.
With their strong environmental credentials and durable, vibrant prints, HP Latex R Series printers are helping New Zealand businesses meet the challenges of the modern market while promoting a greener future.
For more information or a demonstration contact our friendly team at hardware@clgroup.co.nz.
Mikayla Hopkins shares the latest from NZSDA’s regional meetings.
OMIKAYLA HOPKINS
Lead Projects, Events, and Marketing Specialist NZSDA
ne of the NZSDA’s big commitments this year involved making the effort to get out and about and visit as many members as possible.
Last month, we spent a week in Auckland making visits and running two regional meetings. It was such a productive trip, and I really appreciated learning more about the sign shops in the area and sharing with them the new benefits and opportunities we have made available this year. A highlight for me was having the chance to meet many of our associate members and hearing more about what they do and how they support the industry.
We also took the opportunity to present Certificates of Recognition to members, also managing to catch them on camera.
Next on the cards is a trip to the Manawatū/ Whanganui region, followed by a few days spent in Taupō and Tauranga.
I am thrilled to announce the official theme for the 2025 Sign Makers Conference and Awards of Excellence. It is ‘Tradition Meets Tomorrow’.
This event marks the 60th anniversary of the association and we have chosen this theme in honour of the traditional history of the industry and in excitement for the future. We want to reflect the importance of celebrating where we came from, while also supporting the innovation of tomorrow.
The conference will run from June 12-14 June in Nelson. It is such a milestone event that we want to welcome as many members there as possible. Pre-registration for this has opened, so please get in touch to indicate your interest and to book your spot early.
One of our big projects for the year was a complete revamp of the Master Sign Maker accreditation. This accreditation holds incredible value, as the ‘Master Tradesman’ title is easily recognised by the general public as a sign of quality workmanship and integrity in business practices.
The revamped accreditation will prioritise engagement with NZSDA’s
offerings of Learn, Connect, Craft, adding to our core values of Quality, Integrity and Service. It is a badge of honour that celebrates our most engaged and active members, setting you apart as a leader in the signage industry. The new pathway for achieving this accreditation will be released soon. If you are interested, please do let us know now.
Our comprehensive Terms of Service document has recently had a much-needed refresh. We worked closely with a human resources specialist and a legal team to ensure that the new Terms of Service is fit for purpose for our industry. We will bundle the Terms of Service with a guide for use, account application, and guarantee. Next month, we will release the package in the members portal on our website.
Also due for imminent release is our 2024 Pay Rate Guide. This is the second release of the guide, with the first one developed and released back in 2019. The employment landscape has changed considerably since then. Within this 2024 guide are topics and insights such as retaining your best people, offering the right benefits, clarification on pay equity and parity, as well as addressing the skills shortage.
We also conducted a survey among our membership, and from the results, we were able to provide a guideline around the salary and wage ranges for key roles within our industry. This will be released next month.
We have several more webinars planned for the year to provide professional development and sound business advice to our membership.
Our fourth and final human resources webinar addressed the topic of the value of systems, processes, and automation. The webinar outlined the benefits of using apps to assist businesses in remaining compliant when it comes to human resources administration, and the benefits of having processes and policies in place as an organisation.
An upcoming webinar will feature Aaron from Go Taxi. This will cover the details on how the Taxi system can help you leverage your provisional tax payments to secure affordable working capital. Aaron recently presented at our Auckland regional meetings and his message received an amazing response from the attendees.
Our whakatau for October is:
Ka mua, ka muri Walking Backwards into the Future.
If you can’t attract and retain top performers, your business will never achieve its full potential no matter how good your products or services are. Here are five considerations to keep in mind when recruiting new staff.
Having been an executive recruiter for more than 20 years, plus having led teams of up to 750 people myself, I am regularly asked by CEOs and business owners how to best go about attracting and retaining the best people in their organisations. This has been especially true in more recent times where people are talking about the “war for talent” and the “great resignation”. The reality is that organisations live and die based on the quality of their people. If you can’t attract and retain top performers, your business will never achieve its full potential no matter how good your products or services are. Here are five key points to assist you in this regard:
1. What are you doing to build your company brand and your own personal brand as an employer of choice? Most company websites are very focused on their ideal customer, yet very few have any emphasis on why someone would want to join as an employee. Most executive leaders have a LinkedIn profile that is a synopsis of their career history yet gives no indication of why
The reality is that organisations live and die based on the quality of the people they recruit
they would be a great person to be managed and led by. If your people are your greatest asset, then why not invest some time and money in projecting that to your ideal employees through your website and LinkedIn profiles.
2. If you are not recruiting the role directly yourself, make sure that the person you have delegated this to (either internal HR or a third-party recruiter) clearly understands the role and especially the key deliverables. You want to recruit someone who has done it before, done it well, and is motivated to do it again. The clearer the brief as to what success looks like, the more likelihood that the person recruiting the role will deliver appropriately qualified and experienced candidates.
3. Make sure that the person recruiting the role puts their name and phone number on the advertisement (Seek or LinkedIn). Good candidates want to ring a real person and have a real conversation with someone before
applying. If there is nobody to ring, then they are likely to not apply, which will significantly reduce the quality of your candidate pool.
4. Make sure that you headhunt. The best candidates are not actively looking for a new role, they are passive. There are issues with internal recruiters headhunting because they need to identify who they work for. So, if it is a mission critical role, or you are looking to replace a nonperformer, then ideally you will engage an external headhunter to handle this for you.
5. Once someone is employed, it is critical to establish a relationship of love and performance. Too much love and not enough KPIs results in a soft, underperforming team. Too much accountability (KPIs) and not enough love results in team members becoming very self centred (they only care about their own KPIs) and/ or they leave. Employees want to do well, they want to be held accountable, and they want to be loved. It’s a fine balance, however it is the mark of a great leader and it’s something you can easily learn to do.
If you can successfully attract and retain top performers, your business will achieve excellent results. As a leader, you will be able to delegate tasks efficiently and effectively, you will be able to focus on more strategic priorities, and you will be able to have a much greater work/life balance.
In my opinion, both the “war for talent” and the “great resignation” are cliches used as an excuse by recruiters and managers for poor performance. There are simply some companies that are great at recruitment, and the majority who aren’t. Likewise, there are some leaders who are excellent at retaining their top people, and the majority who aren’t. Through implementing these five simple suggestions, you and your business will have a distinct advantage over your competitors. It’s definitely worth it, don’t you think?
Richard Triggs, author of Winning the War for Talent, is the founder and CEO of Arete Executive, an executive search and recruitment company. www.areteexecutive.com.au
Thanks for asking. Nettl is a business system.
It’s a bolt-on partnership. Made for graphics businesses like yours. Keep your existing brand. And add Nettl. To extend the range of things you can do for your clients.
Use your existing team’s skillset to do more. Take advantage of Nettl’s suite of marketing to engage new clients and keep in touch with existing ones.
Nettl is the largest network of neighbourhood web, print and design studios in the NZ. We have hundreds of Nettl locations worldwide, including Australia, United States, Belgium, England, France, Ireland, Scotland, The Netherlands, Wales, and of course, right here in New Zealand.
Nettl helped these businesses diversify to become the go-to place for all the things their clients now need. Websites. SEO. Print. Signage and exhibitions. We’d like you to be a part of it too.
It all starts with the client.
We always think that’s a very wise place to begin. In the old days, clients invested their marketing spend on print-based advertising.
Nowadays, the first thing a start-up business wants is their website. So that’s where Nettl starts too.
But it’s certainly not where it ends.
You’ve probably noticed that business cards aren’t first on anyone’s shopping list anymore. You might still sell lots of them. So do we. It’s just that clients are putting their energy into other marketing channels first.
After their website, they need help with email marketing, social and search engine optimisation. Signage, exhibition graphics and then, probably a heap of print and promo too.
Nettl does all of those things. And a bit more too.
A long time ago, we had hundreds of print shops. We began opening and licensing print shops worldwide, twenty years ago. We franchised them all over the place. Then the world started to change.
It’s not that clients don’t buy print anymore - of course they do.
It’s just that the creative relationship starts with the person who designs the first thing. Since that thing is often a website, nowadays that’s often the web designer.
Admit it. You’ve probably cursed the web guy who sent you a 72 dpi RGB logo to print. Well, now files that might have gone to a print shop are being uploaded every day to online printers. Hurts, doesn’t it?
We know. Because, we were once the print shop. Of course, we delivered clever creative. And magical marketing. But print was our DNA and we had a network of print stores, sprinkled all around the globe.
Gradually, clients stopped coming in. Things got harder. Our margins eroded. And so we changed.
We became Nettl.
They want it all. And there’s been a convergence. Clients don’t want multiple creative relationships.
They hate explaining their brand to a sign guy, a web girl, some expo dude and then a printer.
They want one person to take care of it all. Someone local, who can do their website, then their SEO, then all the printing they need. Could that be you?
Once upon a time, a website was just a homepage, about us and a contact form. Then clients started wanting to do more. To take payments. To sell things online. On the move. On mobile devices. With stock synced to their back office system. Put up online appointment booking forms. With live availability of time slots.
And that’s when this stuff got real.
Design isn’t just design any more. You’re being asked to work with ecommerce or booking systems. To design for stretchy fabric displays or signs. To keep up with new tech and SEO.
Nettl makes it easy for clients to navigate. We simplify. We cut out the jargon.
We don’t patronise people.
Interested to learn how a Nettl partnership can help grow your business and keep your customers sticky? Visit partner.nettl.com/nz to learn more.
Custom Manufacturing
•
Flatbed
1965 Heidelberg SB Cylinder Letterpress 54 x 77cm
1986 Heidelberg GTO 52 Single-Colour Offset Press with Varn Kompac Dampening plus Numbering & Perforating
Buyer must pick up machines from Lower Hutt. Open to offers.
Lanyard Pockets
Mounting/Case Binding
Recycled and Recyclable
Specialists in Finishing & Synthetic Stocks
11b Culperry Rd, Glendene, Auckland 0602
Pre-loved equipment or excess consumables to sell?
Services to offer? Business for sale?
Then THIS is the place to advertise to reach printers the length and breadth of Aotearoa! Call or email Brian Moore to advertise now +61 410 578 876 | brian@newzealandprinter.co.nz
CCS Packaging has taken their business up to the next level of high-value-added shorter to long run packaging printing. Their RMGT 970ST-7+C+LD is powering the Sydney company into a new segment of the print market. Utilising seven colours to achieve the many colour variants required for high quality packaging printing, the new RMGT 970 is built on the rich heritage of the 920 and 1060 series. It combines the small footprint, ease of use, low running cost, superior quality and high productivity of the 920 series with the advanced features, skeleton transfer system and heavy-duty packaging construction of the 1060 series. CCS has built its reputation over 37 years in the demanding media business and is now applying their considerable expertise to service the cosmetic, health and wellness packaging segments. With enhanced productivity and finishing capabilities, CCS capitalises on decades of production experience to offer their customers high quality packaging with short lead times. CCS is expanding the mindsets of customers by deploying JIT (just-in-time) operations to reduce business cost and waste.