
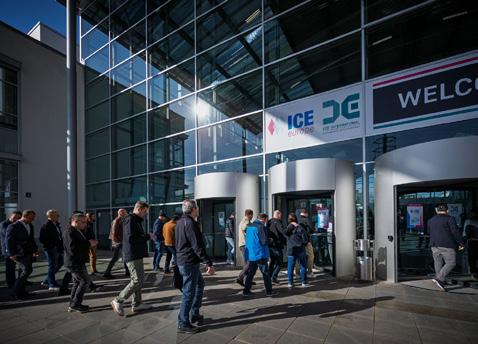
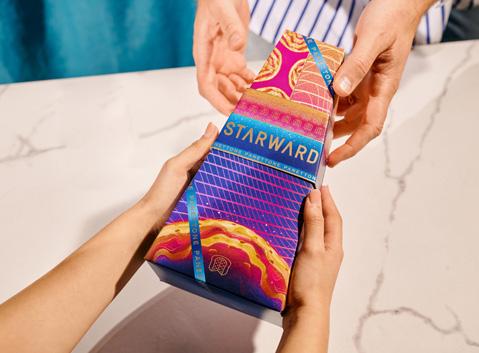

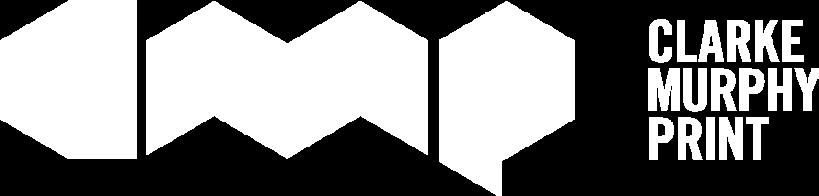
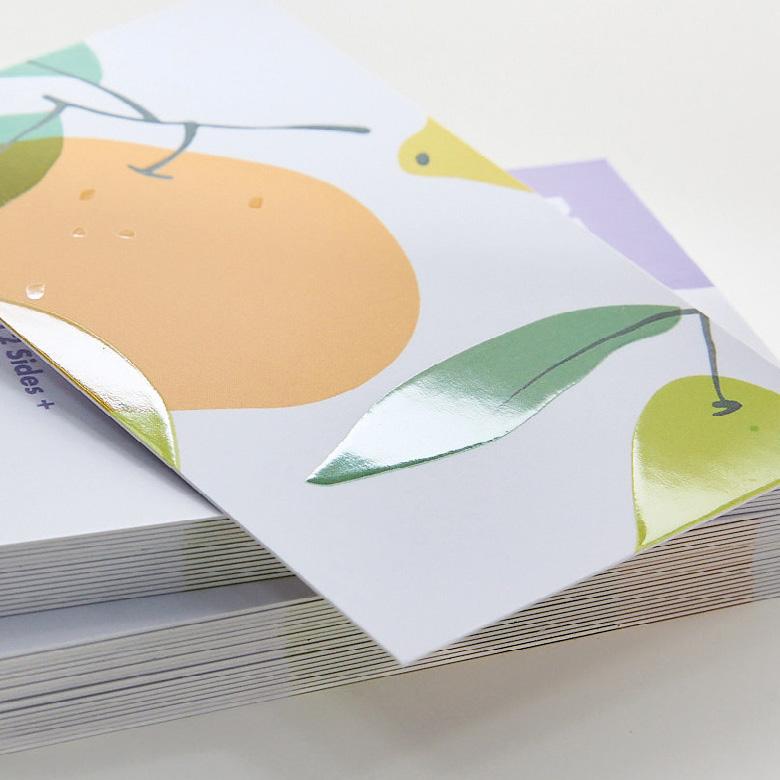
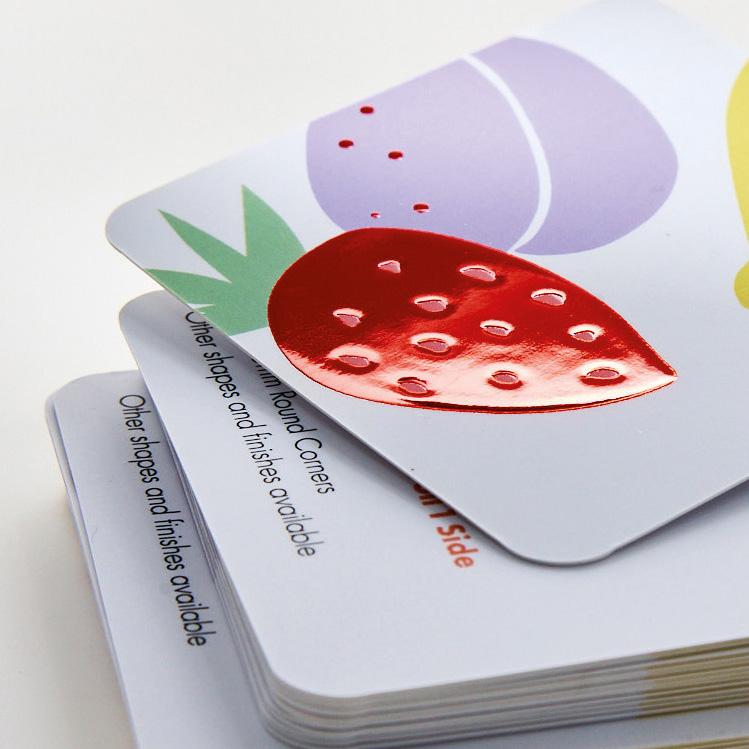
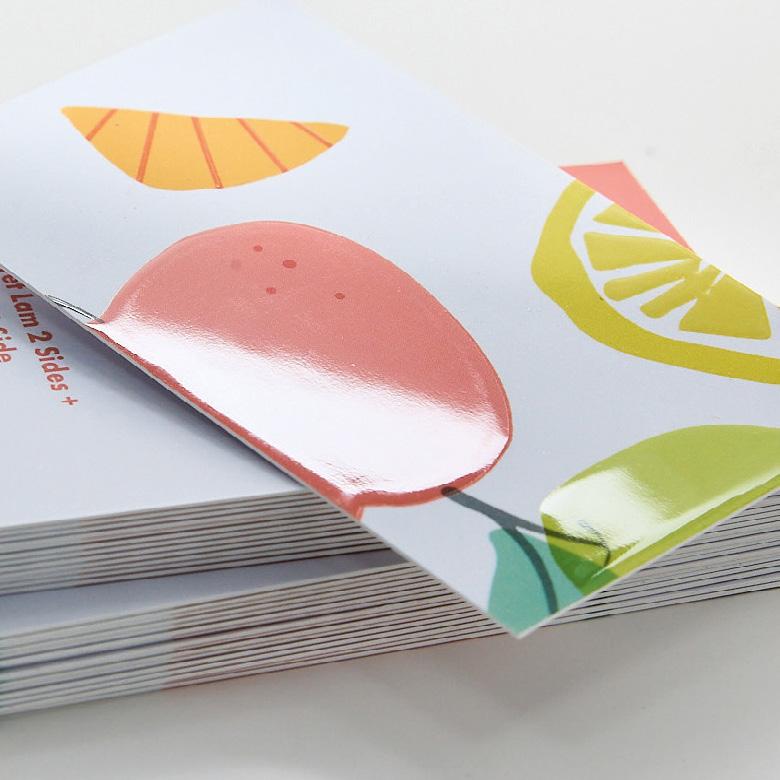
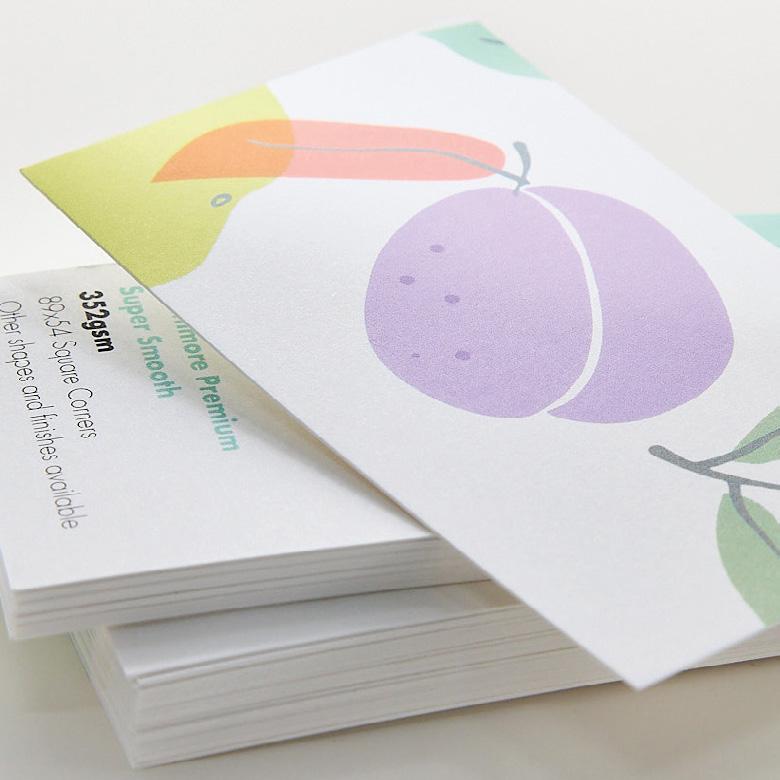

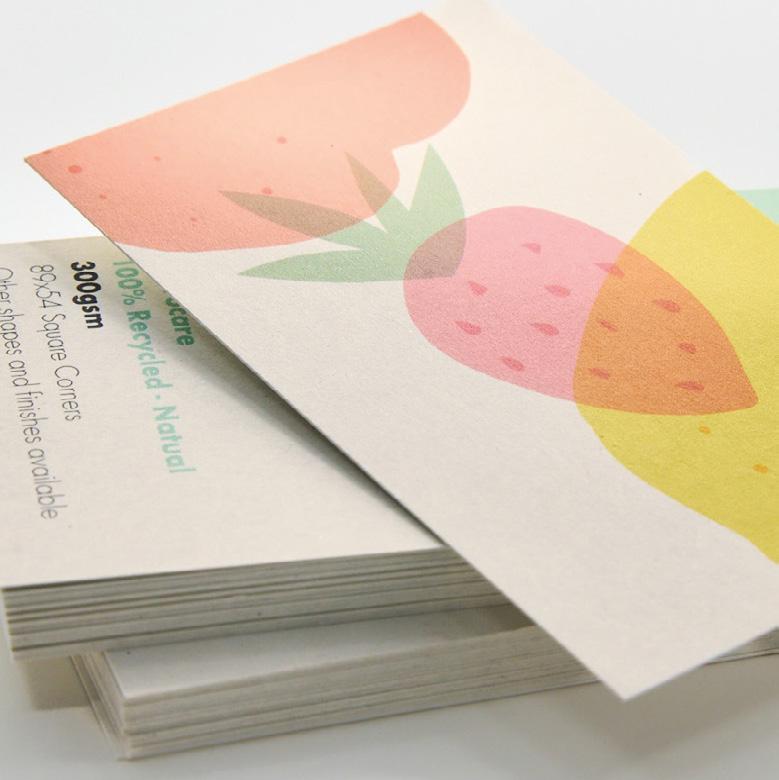
From uncoated to laminated to UV or foils - Hero Print has you covered
AUSTRALIA’S BEST TRADE PRINTER
IVE Group eyes acquisitions P05
The company is keen on more acquisitions
Abel Labels gets Truepress P06
Buys the Screen press from Jet Technologies
Amcor, Insymmetry team up P06
Partnership inked for innovative retort bottle
Reproflex3, Hybrid partner P08
Combine expertise for prepress workflows
CERM buys OMIKAI Systems P08
Deal accelerates cloud product development
Orora shuts Gawler G1 P10
Site transitions from three furnaces to two
Viva Energy innovates P10
Turns used cooking oil into foodgrade plastic
Pact and BlockTexx partner P11
MOU inked in feasibility study
Pro-Pac 1H25 revenue slips P11
Sees 10.1 per cent decline in revenue
Affinity Print invests in folding carton machinery P12
The purchases from Graffica strengthens its in-house end-to-end packaging capabilities
Pozitive installs Felix Gluer at Clarke Murphy Print P14
Clarke Murphy Print improves business processes with the machine from Pozitive
Bindex solutions aim to boost finishing for businesses P16
Graph-Pak and Pressnet partner for high quality finishing solutions
Embracing the future of packaging with innovation P18
DieLine Solutions says smarter automation ensures a safer, more productive workplace
A spotlight on labels and packaging at PacPrint25 P20-21
See labels and packaging solutions at PacPrint
Labelexpo gears up for Southeast Asia tradeshow in May P22-25
Three days of live demonstrations to come Innovations showcased at CCE International 2025 P26-28
Key players in corrugated and carton board production were brought together
IVE crafts stunning packaging for Starward Whisky P30
Partnership creates a distinctive packaging
Orora’s Saverglass executes Papa Salt’s vision P32 Orora elevates the bottle’s aesthetic
It’s tradeshow season and the name of the game is innovation. With some of the biggest events lined up in the coming months – including Labelexpo Southeast Asia, PacPrint 2025, and ProPak Asia 2025 just to name a few – it’s no secret labels and packaging technologies will be front and centre at these fairs.
This issue reviews the recent CCE International, Europe’s key event for the corrugated and folding carton industry, exploring the latest trends and products that will define the future of this space. It also previews Labelexpo Southeast Asia and the Label and Packaging Expo at PacPrint25, providing a sneak peek into some of the technologies that will be on the floor.
We hope you enjoy the read and we look forward to seeing you at some of these upcoming events.
IVE Group managing director Matt Aitken has confirmed he is open to further packaging acquisitions in the local market.
In 2023, IVE Group acquired JacPak for $35 million, with the company confirming plans to become a $150 million player over the next five years in the local $800 million folding carton packaging industry.
Aitken confirmed to ProPack IVE Group regularly receives approaches from companies looking for an exit strategy and any additional packaging acquisitions would need to be complementary to the future growth of the company.
“In terms of packaging acquisitions, we would look at folding carton converters, but we would not be averse to something outside of folding carton if the opportunity made sense,” Aitken said
During his presentation of IVE Group’s half year results to 31 December 2024, Aitken was asked whether the company will be concentrating on the delivery of the next stage of the company’s supersite strategy or whether the company will be focused on additional acquisitions. Aitken said he was keeping an eye on potential acquisitions while also completing the new capital expenditure investments.
“For us, it is a combination of both. It’s clearly really important that we execute on both the 3PL move in Victoria and the supersite move in Sydney
to drive out those efficiencies that we are looking to deliver for that next level of customer experience that we know we are able to deliver following the Braeside supersite three years ago,” he said.
“There is no doubt from a balance sheet perspective that if the right acquisition was to come along, we would definitely consider it. It’s one of the reasons why we have kept the balance sheet strong, so that we have the ability to look at any growth opportunities that might present themselves to the group – not just in the content and creative space – but maybe across other parts of our business and our value proposition too that we would consider acquisitions accordingly.
“There is nothing in play at the moment, so we remain focused on the capital management initiatives that we have called out, including share buyback and to pay down senior debt.”
Tasmanian label producer, Abel Labels, has strengthened its digital printing capabilities with the installation of a Screen Truepress L350UV inkjet press from Jet Technologies.
Abel Labels said this strategic investment enables it to deliver high-quality labels with faster turnaround times, meeting the increasing demands of its customers across the state.
As the label printing industry continues to shift toward digital technology, the L350UV stands out for its speed, precision, and efficiency, making it an ideal solution for medium- to longer-run jobs. The press’ advanced inkjet technology has enabled
Amcor has partnered with Insymmetry to develop an innovative 2oz retort bottle, addressing the growing demand for durable, shelf-stable packaging. Designed to meet the needs of brands seeking high-performance packaging for low-acid, shelf-stable products such as coffee and dairy-based beverages, this packaging solution is the first to leverage Amcor Rigid Packaging’s proprietary StormPanel technology.
Designed to withstand high-pressure retort sterilisation processes while maintaining product integrity, the bottle aims to provide manufacturers with a reliable and scalable alternative to aseptic processing.
Stellify, a beverage brand owned by Insymmetry, is the first company to introduce the StormPanel technology with its energy nootropic Dulce de Leche Energy and Espresso Energy wellness beverage shots.
Engineered with StormPanel technology, the bottle maintains shape and structural integrity under the extreme heat and pressure fluctuations of retort sterilisation, ensuring reliable protection and an extended 12-month shelf life with no refrigeration. The design incorporates features that preserve the round shape, while other areas are specifically designed to flex.
Utilising finite element analysis (FEA) and Amcor Rigid Packaging’s virtual reality capabilities to streamline the process, the teams refined the StormPanel design
Abel Labels to expand its service offerings, while maintaining the high standards for which it is known.
The Hobart-based Abel Labels team collaborated closely with Jet Technologies training specialists to ensure a seamless transition to the new press.
Beyond supplying the Truepress L350,
Jet Technologies remains a trusted partner for Abel Labels, offering technical expertise and ongoing support to ensure smooth operations.
“Having reliable support is just as important as having the right technology.
Jet Technologies and Screen have provided exceptional guidance and service, ensuring we can maximise the potential of our new press. Knowing we have expert backup whenever needed is invaluable,” Abel Labels managing director Trent Cowen said.
Jet Technologies director Jack Malki said Abel Labels’ dedication to mastering this technology underscores its commitment to innovation in the label printing sector.
“Jet Technologies is excited to see Abel Labels elevate its production capabilities with the Screen L350UV. As the industry embraces digital innovation, this press ensures Abel Labels remains at the forefront, delivering superior quality and service to its customers across a wide range of sectors from wine to dairy and everything in between,” Malki said.
to maintain structural integrity during the retort sterilisation by selecting a co-polymer resin and optimising a one-step molding system, they ensured efficiency and scalability.
“At Amcor, we are committed to driving innovation that addresses the evolving needs of the food and beverage industry,” Amcor rigid packaging strategy and marketing vice-president Greg Rosati said.
“Our StormPanel innovative packaging allows beverage brands to elevate shelfstable, low-acid products in a compact, ready-to-use bottle.”
Rosati added the retort process also offers a more cost-effective and time-
efficient solution for manufacturers compared to aseptic processing, reducing upfront equipment investment and streamlining production timelines while maintaining product integrity.
“Amcor’s expertise in packaging innovation enabled us to develop a solution that meets our unique needs,” Insymmetry chief innovations officer Josh Cua said.
“By leveraging its advanced manufacturing technology and material science capabilities, we were able to create a bottle that not only performs exceptionally in the retort environment, but also aligns with growing consumer demand for preservative-free nutritional shots.”
durst-group.com/label
Reproflex3, a provider of prepress services for the packaging industry, has partnered with Hybrid Software UK, bringing together Reproflex3’s expertise in flexographic printing with Hybrid Software’s technology solutions for the industrial printing sector.
According to Hybrid Software, the partnership will redefine prepress workflows by integrating advanced technologies that enhance efficiency, accuracy, and collaboration for global brands and commercial printers.
The collaboration leverages a Cloudbased platform with API integration to provide secure access across all six Reproflex3 sites worldwide, including New Zealand. This means tasks can be executed seamlessly, delivering optimised and consistent results regardless of location.
Through this collaboration, Reproflex3 and Hybrid Software said they are not only tackling existing challenges but also creating opportunities for cost reduction, workflow optimisation, and revenue growth.
“As a global leader in prepress services, we are committed to equipping our clients with the latest tools and innovations.
CERM, a provider of MIS solutions for the labels and packaging print industry, has acquired OMIKAI Systems from Sweden.
OMIKAI offers a cloud native MIS solution for the print and packaging industry. Since regaining its independence through a management buyout in 2020, CERM said it has significantly grown its global presence and market share.
Based on that growth, it has invested in developing a next-generation cloud platform since 2022 that will offer label and packaging converters the option to evolve from the current CERM product portfolio to a cloud-based MIS solution.
The company said it acquired OMIKAI with a view to accelerating its cloud product development that will be commercialised in the coming years. Through this acquisition of the OMIKAI technology platform, CERM
Partnering with Hybrid Software allows us to streamline workflows, enhance automation, and support the evolving demands of modern printers and converters. Their ambition to grow and deliver excellence aligns perfectly with ours,” Reproflex3 CEO Andrew Hewitson said.
“This partnership further positions us as a serious contender in the global flexo prepress industry. We are a technology company enabling our customers to benefit from the very latest toolsets, data, and
expects to shorten its time to market for its labels and packaging specific Cloud MIS.
CERM will continue to offer its current range of MIS solutions, that aims to provide versatility, industry focus, continuous product evolution, and integration capabilities with industry partners.
The acquisition will not result in any changes for existing OMIKAI customers and partners or for CERM customers or prospects
expertise to maximise their productivity and quality.”
Hybrid Software UK and global accounts sales manager Paul Bates said, “Reproflex3 has a long-standing reputation for innovation in flexographic printing. Our solutions complement their vision to set new standards in prepress workflows. This partnership reinforces our commitment to the industry and enables us to deliver the next generation of tools that will transform how packaging graphics are managed and produced”.
as the Cloud MIS development is still ongoing.
“We have been strongly impressed with the cloud MIS product and service offering of OMIKAI and believe our companies have a similar vision, customer focus and culture,” CERM CEO Jan Heyse said.
“Joining forces will strengthen our cloud product development and create additional value for our customers. We welcome the entire OMIKAI team to CERM and eagerly look forward to further accelerating the business, growing our joint team, and expanding our product offering.”
OMIKAI founder Mathias Erlandsson said, “I am incredibly excited about this new chapter for OMIKAI. As an entrepreneur, I’ve always believed that innovation and a personal commitment to our customers are at the heart of success.
“Together with CERM, we now have a unique opportunity to accelerate our mission and deliver even more innovative digital solutions to the printing, labels, and packaging industry.
“I look forward to building on our legacy of excellence and creating even greater value for our customers, partners, and friends. This is not just a business move –it’s a shared journey towards an even brighter future.”
Enterprise workflows
Native PDF editors
Color management
3D prototyping & visualization
High-speed RIPs and DFEs
Printheads electronics
Orora has announced that its Gawler site in South Australia will transition from three furnaces to two, with the G1 furnace closing in the second half of calendar year 2025.
The company said this move will result in a very small volume of production getting redirected to the Ras Al-Khaimah site in the UAE to meet customer demand, in the event of oversupply. It added that a two-furnace operation will be a good model to keep servicing demand for Australian wine, in addition to improving utilisation and efficiency at the site and lower costs overall.
Orora managing director and CEO Brian Lowe said the G1 furnace closure comes as the Australian commercial wine market has been in structural decline for several years, with declines greater than growth opportunities from exports to China or new products such as food jars.
Considering this, it undertook a review of production capacity in Australia and decided on the G1 furnace closure.
“Orora has managed softness in commercial wine and beer volumes in Australia for several years, and in light of this has undertaken a review of glass capacity across the Australasian market. This has resulted in the decision to
Viva Energy has successfully produced its first ISCC+ certified mass-balanced bio-based polymer (recycled food-grade plastic) at the Geelong refinery, using a batch of used cooking oil (UCO).
The development marks the first time UCO has been processed through the refinery’s catalytic cracker and polypropylene plant to create recycled food-grade plastic.
The UCO was sourced from Intersnack A/NZ in New South Wales, where it had been used to cook snack brands including Kettle Chips, CC’s, Natural Chip Company, Thins, and Cheezels. Later this year, Intersnack A/NZ will use the recycled material to manufacture plastic packaging for some of its products.
Cleanaway collected and processed the UCO before it was delivered to the refinery. Viva Energy has made infrastructure upgrades to accommodate the use of alternative feedstocks in its operations.
Lachlan Pfeiffer, chief strategy officer
move from a three furnace to two furnace operation at Gawler, and close our oldest furnace, the G1 furnace, in the second half of calendar year 2025,” Lowe said.
“In turn, some existing production volumes will be redirected to our manufacturing site in the UAE.”
The closure of the G1 furnace is said to reduce capacity by 100kt and avoids an estimated rebuild capex of more than $100 million in 2029.
Plus, with the completion of its G3 rebuild and oxygen plant construction in December 2024, the company expects higher furnace utilisation to result in improved productivity
Intersnack A/NZ will use the recycled material to manufacture plastic packaging for some of its products
at Viva Energy, said the project serves as a proof-of-concept to assess the feasibility of such processes.
“Over time, the plan is to expand the scale of the processing, create new roles for the
and emissions, lower unit costs, and improved margins compared to continuing the operation of all three furnaces underutilised.
The Global Glass (Gawler) segment revenue for 1HFY25 was $655.5 million, up 143.1 per cent. Its EBIT was $71.4 million, up 41.3 per cent.
Orora expects an increase in wine volumes from Chinese exports but claims the domestic commercial wine market will remain challenging, given the structural decline in demand, for FY25 and beyond.
However, it added there is potential for an additional $20 million in onerous contracts resulting from the G1 closure in future.
refinery, and transform the site into a broader energy hub.
“There is growing interest in plastic with recycled content and in a more sustainable solution to Australia’s plastic waste challenges, particularly from food manufacturers like Intersnack A/NZ.
“We believe there will be a strong market for food-grade packaging made from recycled materials, but we recognise there is a need for regulatory support for this to be a success.”
Kurt Preshaw, CEO of Intersnack A/NZ, said the initiative aligns with the company’s sustainability goals.
“We are excited about this important first step for Intersnack A/NZ and its potential to address the broader industry challenge of plastic waste. Our customers and consumers expect us to reduce our reliance on virgin plastic, and this initiative is a critical first step toward that goal,” he said.
Viva Energy plans to assess the environmental benefits of its bio-based, recycled, and lower-carbon products over the next year. The refinery, which is part of the Viva Energy Hub, supports energy security, the energy transition, and the circular economy.
The company also intends to explore other alternative feedstocks, including plastic pyrolysis oil and tyre pyrolysis oil, in the coming months.
Pact Group and clean technology company BlockTexx have come together to jointly explore the development of a garment collection and recycling operations for fashion brands and clothing retailers in Australia.
The two companies have signed a memorandum of understanding to determine the feasibility of establishing an end-to-end solution for discarded polyester and cotton-blend clothes.
The proposed operations would involve the collection, sorting, and pre-processing of used garments, and the recycling of polycotton, polyester and cotton garments into raw materials which could be used to make yarn for new clothes, non-food grade plastic packaging products or other sustainable applications.
Pact has expertise in the fashion industry supply chain through its retail accessories division, which collects and redistributes used plastic garment hangers from retail stores in Australia and internationally.
The hangers are sorted, inspected, and distributed to garment and accessory suppliers so they can be reused multiple times instead of being sent to landfill.
Pro-Pac Packaging Limited has released its 1H25 financial results, reporting a decline in revenue from continued operations of 10.1 per cent across the group at $142.9 million.
The company said this included the material impact of a $13.6 million reduction in sales to its major customer in the Middle East and a three per cent reduction in other volumes in the flexibles business.
Pro-Pac CEO and managing director Ian Shannon said, “Our revenue for the half year was $142.9 million, 10.1 per cent lower than the corresponding period of $158.9 million. This decline in revenue included the material impact of reduction in sales to our major customer in the Middle East of $13.6 million.
“Volumes across the flexibles business excluding the sales to our major customer were down three per cent, reflective of the challenging market conditions and weather conditions in Australia and New Zealand which impact on our agricultural volumes.
“Volumes in our specialty packaging business were up 0.6 per cent (excluding
Hangers not suitable for reuse stay in the loop because the material is recycled and used to produce new hangers.
Pact’s packaging division manufactures rigid plastic packaging for everyday products in the food, beverage, and dairy industries, as well as industrial products such as paint and AgriChem containers.
BlockTexx has developed a chemical recycling process for hard-to-recycle polyester and cotton blends to produce recycled material and is currently recycling textiles at its Loganholme facility south of Brisbane.
The BlockTexx recycling technology supports fibre-to-fibre for new clothing, fibre-to-product manufacturing, and fibreto-agriculture applications, ensuring textiles are given a second life, promoting resource efficiency and sustainability throughout the industry.
The feasibility study will look at the garment collection supply chain in Australia, the technical requirements needed to meet
the BlockTexx recycling processes, and the suitability of using the recycled raw materials within Pact’s packaging portfolio and other applications.
Pact Group CEO Sanjay Dayal said, “Pact’s existing presence in the global fashion supply chain through our retail accessories business enables us to expand our expertise across the garment supply chain beyond just hangers. This initiative with BlockTexx demonstrates our commitment to leading the circular economy through partnerships and collaboration to offer sustainable solutions for our customers.”
BlockTexx co-founder Adrian Jones said, “This project aims to accelerate the fashion industry’s shift towards more sustainable products by combining Pact’s capabilities in sustainable retail supply chains with BlockTexx’s textile recycling innovations.
“This could enable businesses in the fashion and textiles sector to transition to more sustainable and circular practices and assist in the reduction of CO2 emissions and prevent unwearable textiles from going to landfill, both here and overseas.”
According to Australia’s clothing product stewardship scheme, Seamless, the Australian clothing industry manufactures and imports about 1.4 billion items of new clothing every year, most of which is made from non-renewable and environmentally problematic materials.
More than half of this clothing ends up in landfill in Australia, which amounts to 200,000 tonnes per year.
Pact and BlockTexx are aiming to complete the feasibility study by the end of FY25.
exited market categories), which is pleasing in a challenging market. EBITDA (pre AASB16) was a $6.4 million loss versus $1.2 million profit for 1HY24, however this was an improvement from 2H24 loss of $8.7 million.
Within its flexibles business, revenue decreased by 12.8 per cent to $108.6 million (2023: $124.5 million) during the half-year.
As for its industrial specialty packaging segment, revenue decreased by 0.6 per cent to $34.2 million (2023: $34.4 million), which included a $0.4 million reduction relating to non-core market segments.
The company said it looks to improve profitability in the face of challenging market conditions.
“Market conditions remain challenging with exchange rate movements likely to continue to impact on our results for 2H25,” Shannon said.
“The current trading results continue to perform below our expectations, and accordingly we are currently working with advisors to undertake a strategic review of our businesses and to explore and execute on plans for improved profitability and longer-term funding arrangements.
“We are pleased to have the ongoing support of our major shareholder, who provided a $13.0 million facility during the period, with the termination date being extended to 1 March 2026.”
Affinity Print recently purchased an 850 CartonFold folding box gluer and a 1060 fully optioned Century die cutter from Graffica, bringing its capabilities fully in-house
Victoria-based Affinity Print has bought two folding carton machines from Graffica, strengthening its in-house end-to-end packaging capabilities. The company, which recently also celebrated 50 years in operation and moved into a new, larger facility, invested in an 850 CartonFold folding box gluer and a 1060 fully optioned Century die cutter from Graffica, offering clients high-end packaging solutions.
Affinity Print owner Steven Todisco said “The move to a bigger premises allowed us to execute on our strategy of bringing our production in-house. This involved the purchase of the 850 CartonFold folding box gluer and a 1060 fully optioned Century die cutter.
“Affinity is now one of the few printers in the country to run a full in-house packaging solution, with foiling, embossing, coating, and UV capabilities. What we can offer the market is of the same level, if not better, than some of the ‘big boys’, which is fantastic for a family-run company.”
Todisco said he chose the machines for their automation, optimised speed, accuracy, and diverse range of functionalities, adding that the units work seamlessly with the company’s other machines.
“The machines have allowed us to boost our productivity multifold. Our turnaround
times have also multiplied, allowing us to take on more jobs than before,” he said.
The 1060 fully optioned automatic flatbed Century die cutter is known for its die cutting, stripping, and creasing of high-end coloured cardboxes. Equipped with the latest Siemens PLC technology, a top feeder system, and a high running speed, the machine is highly efficient.
The machine, which is built for quick setup, safety, wide stock range, and reducing damage to print sheets, can handle solid board (90gsm to 2000gsm) and corrugated board of single flute up to 4mm.
A pneumatic lock up and centerline system are used for a fast-cutting die set up and job changeover. Precise control over the die cutting process is achievable on the electrical control system.
It also has a full stripping function (triple action stripping system and lead edge waste removal device) to save on labour costs and shorten delivery times.
With a maximum mechanical speed of 7,500 sheets per hour, it also has a sheet blowing system and brush system at its delivery section for solid board perfect collecting.
“The die cutter is high-end equipment. As Affinity Print generally does high-end, short-run work, its fast turnaround times meets the company’s requirements,” Graffica director Neil Southerington said.
As for the 850 CartonFold folding box gluer, it features speeds of up to 500m/ min. It allows for a wide stock range –with 200gsm to 800gsm cardboard and corrugated board.
Its full configuration includes a pre-fold unit, straight line, crash-lock bottom, and four- and six- point corners. Optional additions include: a pre-feeder, precrease, braille system, CD boxes, bump turn, auto-set and job recall functions, plasma device, grinder with dust extraction, cold glue system, hot glue system, tape application, and box packer.
“The 850 CartonFold folding box gluer’s capabilities covers the whole gamut of box folding. It’s a very fast machine and adds a lot of value to Affinity Print’s packaging needs,” Southerington said.
“Graffica is thrilled to have Affinity Print as a customer, especially in such a significant purchase from a medium-sized company. It’s very well-established in the market and plays in the high-quality space. Affinity Print’s investment in machinery from Graffica speaks volumes about our offerings as it’s a testament to the quality of our products and service.”
The Felix Gluer has improved operations at Clarke Murphy Print as the machine has enabled the business to use it for a range of applications, including point-of-sale
Pozitive sign & graphic supplies has installed the first Felix Gluer in Australia at Clarke Murphy Print (CMP) in Sydney.
The deal was confirmed at drupa in Düsseldorf in mid-2024, following the appointment of Pozitive as the exclusive distributor in Australia and New Zealand.
“We have a longstanding relationship with Philip Trumble at Pozitive. We have bought seven swissQprint machines over our journey. Phil has seen the growth in our wide format business and the Felix Gluer was a natural progression for us,” CMP director Benn Murphy said.
“After taking on the distribution, Pozitive came to us with an opportunity to be the first in the country with a Felix Gluer table. It was a no-brainer for us, and it’s always such an easy purchase process when you see the quality of the product and you are working with the team from Pozitive.
“This is first time we have had an automated gluer in our business, and it’s a gamechanger. The build quality of the machine is outstanding. It was up and running in a day and a half, and the entire process from end-to-end has been seamless.
“We are still in the early days of working with the product, but the Felix Gluer will be used for our point-of-sale work, all our
corrugated work, and we can change the glue configuration so it can also be used for corflute and polypropylene products.
“We are also starting to see how it can be used in other applications that are not in our wide format business such as short-run presentation folders, making boxes, or even joining one-sided board to make a large cube.
“The benefit of the Felix Gluer is it can offer the application of both hot and cold glue – hot for the initial contact and cold for the extra strong strength. If you are creating a point-of-sale item that needs to be sent all around the country – from Tassie to Far North Queensland – you must ensure that the job is able to withstand humidity and temperature differences.
“With fast setup, not only can our wide format division send a cut file, they can also send a glue CAD file straight to the machine – or we have the option of setting up the glue lines on the table directly.
“Another innovative feature of the Felix Gluer is the table has a camera mounted on the top and we can manually setup the glue lines with its innovative software. The machine can apply the glue in the perfect amount – consistently, piece after piece. It can be dots, as a spray, or as lines – and most importantly, it can be hot or cold glue, or both.
“With the Felix Gluer now installed, this allows us to on-shore more business that we sometimes send to China. Sending work offshore leads to a longer turnaround for our clients. At CMP we are also providing our team with the tools to do things faster, easier and more cost effectively.
Pozitive founder and owner Philip Trumble said the companies’ relationship has been built on the way they have worked together to solve problems and support each other.
“Benn has been a partner in our business for many years and was one of the first printers to buy a swissQprint machine in Australia. Aside from purchasing machines from us, the thing that makes Benn very special is the support he has shown us –and the appreciation of the support that we show him,” Trumble said.
“At Pozitive, we don’t just sell machines; we supply the right machine to the right client, at the right time. I often say to my team that sometimes the best thing you can do is not sell anything at all – because a client will treasure that good advice more than selling them the wrong product.
“I have learned a lot from Benn by asking him whether the Felix Gluer would make a difference in his business, and that helped me to understand the challenges he faced and how a machine like the Felix Gluer solves these issues.”
Trumble said with printers in Australia still hand gluing or taping hundreds and thousands of items per day, the Felix Gluer provided Pozitive with a distribution opportunity in an untapped market for this type of solution as it allows Australian manufacturers to remain competitive and on-shore more business.
“Our mission at Pozitive is to keep Australian manufacturers competitive and performing at their best. We need to keep our local businesses efficient and competitive because if they are not, they’re just going to offshore more work – and that kills our local manufacturing industry,” Trumble said.
“If we can find ways to keep our industry competitive – through use of equipment and automation, we can make sure that people who are employed are re-skilled to ensure they are productive, efficient, and cost effective.”
Industry suppliers Graph-Pak and Pressnet share a common interest in supplying high quality solutions that help their customers improve their bottom lines.
Industry veterans Charlie Scandrett, managing director of Pressnet, and Tom Ralph, managing director of Graph-Pak, have a massive depth of knowledge and experience, which they are only too happy to share with customers.
Recently, the companies entered into a marketing and sales arrangement to provide Bindex PUR binders, HXCP folders, HPM guillotines, and Bin Bao sheeters.
Scandrett had previously visited Bindex and became its Australasian agent.
“Over a decade ago, the Chinese binding machine manufacturer Bindex entered into a manufacturing and licensing agreement with Wohlenberg of Germany. Now, every Wohlenberg book clamp and Sprinter s or s/XL gathering machine in the world is manufactured at Bindex in Pinhu, in the Hengzhou district of China,” he said.
“Wohlenberg’s name is on the main factory front, and Wohlenberg has supplied technology and reviews of Bindex technology to the Li father/son team who own Bindex.
“Bindex have a range of machines from the single clamp Explore at 500 books per hour, through to the 12,000 books per hour Galaxy 12,000e.
“All Bindex machines are automatic setup with servo motors.”
Also in the range, the Ecobinder offers speeds of up to 2,000 books per hour.
Scandrett said, “This PUR model is ideally suited for the on demand market”.
Graph-Pak and Pressnet have already sold the first Eco binder model to a printer in Melbourne.
“We immediately found problems with safety lights, stacker speed, and the integration of the Nordson PUR supply unit with the Bindex Ecobinder. Ang Li, the general manager and part owner of Bindex, flew to Melbourne with his engineers to supervise the rectification. Nordson in China ran some tests at the Bindex factory, and the problem was resolved,” Scandrett said.
“This first installation is running well now. Although we had this initial issue, the subsequent actions from Bindex have proved how very responsive the company is with its technical support.
“We have a bilingual engineer’s support chat group, where we can talk to Bindex engineers in English, and they read Chinese at their end.”
Ralph and Scandrett have four proposals for Galaxy 6000e machines out in the Australian market already.
Pressnet is also co-operating with Bindex to design roll-to-bind solutions for the emerging inkjet web market.
Ralph said, “We are confident these affordable and technically excellent
machines will achieve significant market share. We are excited about bringing this technology to the local market and we look forward to discussing with you how these solutions can help your business.”
The Bindex Ecobinder, a fully automated five-clamps perfect binder is an ideal solution for flexible and quick binding of small and medium book quantities.
Equipped with an automatic book delivery, which ensures that the book falls smoothly from the clamp, the Ecobinder can connect to the digital three knife trimmer, forming a digital perfect binding line to meet various production needs.
Ecobinder features:
• Automatic thickness measuring device
• Book clamps, opening and closing automatic adjustment
• Professional independent notching section for superior spine preparation, width automatic adjustment
• Double spine glue units with independent temperature control; and an automatic spine glue cut-off with a PUR glue unit option
• Side glue section, width automatic adjustment
• Cover guides/scoring on the cover feeding section, width automatic adjustment
• Cover guides (both front and side) on the nipping section, width automatic adjustment; and heavy duty double cam mechanism for superior spine nipping quality
• Book positioning guides, automatic adjustment
• Delivery channel, width automatic adjustment
• Integral casting and strong rigidity.
Australia’s packaging producers face a tough challenge. Labour is expensive, and repetitive manual tasks – like lifting heavy boxes all day – make jobs at the end of the folder-gluer line difficult to fill. Did you know that a single worker can lift and pack up to nine tonnes in a single day? That’s a massive strain on the body. But what if we could make these jobs more attractive, safer, and more productive?
Automation is key. It doesn’t just lighten the load, it removes the most physically demanding tasks, making jobs more ergonomic and engaging. Instead of lifting cartons all day, workers operate and oversee automated systems.
And the benefits go beyond individual well-being: staffing shortages and absenteeism due to injury are real concerns, and hand-packing with a skeleton crew means slower speeds and lost efficiency. When automation steps in to do the heavy lifting, finishing lines can maintain peak output – even with fewer people on the floor.
In the folding carton and tray-forming sector, speed limitations at the packing stage have long been a bottleneck. While full automation works for some, other producers need the flexibility to do many box types on a single finishing line. Recognising these issues, IMPACK has developed innovative semi-automatic solutions such as the ERGOSA.
These systems bridge the gap between full automation and manual labour, providing flexibility, fast changeovers, and ergonomic benefits.
The impact of these solutions is remarkable. One local packaging producer installed an ERGOSA and, after a short training session, put it to work. On its first run, a single worker packed 40,000 boxes per hour of a specific box type. I suggested they test its full potential, and after increasing the speed of their folder-gluer, they hit 60,000 boxes per hour without breaking a sweat. Before the ERGOSA, two workers packing manually could only manage 20,000 per hour of this box type. This isn’t a one-off case – facilities worldwide are seeing similar gains after implementing IMPACK solutions.
Fast payback, lasting benefits
Automation isn’t just about improving working conditions – it’s about boosting profitability. With production numbers and labor costs, it’s easy to calculate
the payback period on automation, and in the case of IMPACK solutions, it’s a matter of months before the machine starts delivering pure profit.
Innovation meets the tray forming line
I’m always on the lookout for cutting-edge solutions that give my clients an edge. For years, I’ve supplied Gietz Tray Formers and until recently, there weren’t any solutions to help with end of line tray packing. But this year, IMPACK is introducing the TRAYVA, a semi-automatic packing system designed for tray formers, unlocking higher productivity and improved labour utilisation. It’s so efficient that a single operator can pack for two tray-forming machines.
Value through superior solutions
My commitment has always been to provide packaging producers with high-quality solutions that address industry challenges and maximise longterm investment value. I also represent MARBACH flatbed/rotary die-cutting tooling in the A/NZ market – a premium, German-engineered product renowned for its performance and durability.
Another standout innovation is Policart Anvils, which significantly extends the lifespan of cutting tools while enhancing precision for the fibre/corrugated converting market. By improving cutting accuracy and lasting longer, these Anvils help businesses reduce costs and increase efficiency, delivering tangible benefits in a highly competitive market.
Innovation is the driving force behind industry advancement. The right automation does more than boost output; it revolutionises operations, making packaging producers more resilient, efficient, and profitable.
By Ian Gillanders, DieLine Solutions.
Labels and packaging professionals looking to innovate, optimise, and expand their capabilities should not miss this opportunity to discover and explore the future of the industry first-hand
PacPrint 2025, one of the premier events locally for the print, sign, and graphic communications industries, will take place in May with labels and packaging at the forefront.
As the sector embraces digital innovation, sustainability, and automation, the event will bring together industry leaders, cutting-edge technologies, and thoughtprovoking discussions to shape the future of labels and packaging.
A hub for labels and packaging innovation
With an impressive lineup of exhibitors catering to the labels and packaging market, PacPrint 2025 will explore the latest advancements.
Major brands such as Epson Australia, Screen GP Australia, Fujifilm Business Innovation Australia, HP PPS Australia, Konica Minolta, and Koenig Machinery will showcase their printing technologies designed to improve efficiency and quality in label production.
Beyond hardware, PacPrint 2025 will also highlight key players in workflow automation, sustainability, and finance solutions.
Exhibitors including Accura MIS, CERM, M-Power Software, and Quote & Print Software will present automation solutions that streamline production.
Finance@work will provide financial solutions tailored to the industry’s evolving needs. EcoChan Sustainable Packaging will bring a sustainability focus, showcasing eco-friendly alternatives that align with global environmental priorities.
Konica Minolta’s immersive stand will showcase the AccurioLabel, amongst other printing and embellishment machines. The AccurioLabel is Konica Minolta’s digital label press line-up that offers high productivity and high speeds, whilst still ensuring maximum quality. It is also compatible with a range of media, meeting a variety of needs.
Konica Minolta chief marketing officer Melissa Dempsey said, “We are excited to demonstrate how our high-performance solutions help businesses boost productivity, expand their capabilities, and maximise profitability”.
Screen GP Australia: The future of digital packaging
Screen GP Australia will feature its Truepress Jet L350UV series, which is an advanced UV inkjet press known for high-speed, high-quality label production. Additionally, the Truepress PAC 520 and Truepress PAC 830F will showcase sustainable packaging solutions with recyclable, paper-based wraps and pouches as an alternative to plastic.
Screen GP Australia managing director Peter Scott emphasised that Screen’s technology eliminates the need for plates, ultimately reducing waste while maintaining print excellence.
“Flexible, short-run packaging solutions are becoming a necessity in today’s market and we’re delivering digital solutions that meet this demand,” Scott said.
Fujifilm BI Australia: A complete label and packaging solution
Fujifilm Business Innovation (BI) Australia will introduce an end-to-end approach to packaging print production that is combining analogue plates, specialty inks, and digital workflow solutions.
By bringing together Fujifilm BI Australia and Fujifilm Graphics Communication, the company aims to provide one-stop solutions for printers looking to optimise their operations and expand their capabilities.
The company will have on show four new mid-range production presses in the Revoria Press series, including the Revoria Press EC2100S, Revoria Press SC285S, Revoria Press EC2100, and Revoria Press SC285.
The Revorias can do a small range of label and soft packaging prints at A1 size maximum. They are more suitable for print-on-demand/personalised labels and soft packaging instead of roll-to-roll label production.
Fujifilm BI Australia head of Oceania and graphic communications senior general manager Yoshitaka Nakamura said, “As industry demands continue to evolve the efficient printing process, we are thrilled to introduce the nextgeneration machines, bringing even greater possibilities to the local market”.
Graffica: The latest in packaging and display equipment
Graffica will be exhibiting at PacPrint 2025, providing attendees with more information about its range of folding box gluers, board, slitters, creasing machines, auto loaders, and cutting tables.
Some of Graffica’s key products include:
• The Century range of die cutters –Automatic flatbed die cutting machines that are applicable for cutting corrugated boards, laminated paperboards and carton boards used in the printing and packaging industry, with a maximum sheet size of 2500mm by 1620mm. These reliable and highprecision flatbed die cutting machines aim to meet the growing demand for manufacturing corrugated boxes and POP/POS displays.
• The CartonFold Pro – A carton folding machine that comes in 650, 850, and 1100 models with auto-set and job recall. Some of its features include crash-lock and 4/6 point gluing. An optional pre-feeder/packer, which operated at 450m/min, is also available.
• The CorrFold range – A selection of corrugated folder gluers that are
available in 1450, 1700, and 2300 formats.
• The GuoWei guillotines – Equipped with AC digital servo controlling technology and a 10-inch colourful touch screen, the machines’ data resolution rates are 0.01mm. Its other features include self-diagnostic functionality, 100 program units, more than 10,000 different cutting positions, and dynamic follow-up. The guillotines come in a range of models – from 52cm to 300cm.
Beyond the exhibition floor, PacPrint 2025 will feature an extensive forum program offering valuable insights into emerging trends, sustainability best-practice, and global market shifts.
Key sessions will include:
• Leaders in Labels & Packaging Panel – Wednesday, 21 May
Industry leaders will discuss technological advancements, market opportunities, and challenges in label and packaging production with a focus on automation, sustainability, and hybrid printing solutions.
• Sustainability, Packaging, & Global Paper Trends – Keynote by Stephanie Strassburger, vice -president Asia and Pacific, Gmund Paper – Thursday, 22 May
Strassburger will delve into sustainable packaging innovations and global paper trends, offering insights into how businesses can stay ahead of regulatory and consumer demands.
• Leaders in Trade Panel – Thursday, 22 May
This panel will explore trade and supply chain considerations, particularly relevant to the labels and packaging sector in which global sourcing and material sustainability are critical factors.
As environmental responsibility becomes a central priority for the industry, PacPrint 2025 will highlight cutting-edge
sustainable materials, low-energy printing, and waste-reducing technologies.
Exhibitors such as Spicers Australia, EcoChan Sustainable Packaging, and Epson will showcase solutions ranging from biodegradable substrates to waterbased inks and energy-efficient machinery.
Kirsten Taylor, chair of PacPrint 2025, said, “Sustainability is a critical part of the future of our industry. Our exhibitors are bringing innovations that allow businesses to make meaningful environmental improvements, while aligning with both regulatory pressures and consumer values”.
PacPrint 2025 offers unparalleled opportunities for professionals in the labels and packaging industry to:
• Experience live demonstrations of innovative label and packaging print solutions
• Gain insights from industry leaders on automation, sustainability, and future trends
• Network with key suppliers, printers, and packaging professionals
• Discover cost-effective and sustainable alternatives for packaging production, and
• Stay ahead of global trends impacting the label and packaging industry.
PacPrint 2025 will take place from 20-23 May at the Sydney Showground, Sydney Olympic Park.
Labels and packaging professionals looking to innovate, optimise, and expand their capabilities should not miss this opportunity to discover and explore the future of the industry firsthand. Visit the official registration portal today.
For more information about exhibiting at PacPrint 2025, contact the events team at exhibitions@visualconnections.org.au or call +61 2 9868 1577. For more information about the show and all the latest news, go to www.pacprint.com.au.
The upcoming Labelexpo Southeast Asia tradeshow promises three days of live demonstrations and innovative technology from industry-leading suppliers
Labelexpo Southeast Asia 2025 is due to take place next month in Bangkok, Thailand, showcasing the latest technologies and technical advancements – live – from some of the world’s leading manufacturers and suppliers.
The event, which promises three days of industry knowledge, partnership building, and technology showcase, aims to provide attendees with the tools necessary to strengthen their business.
Aimed at connecting printers/converters, brand owners, label and package printing technicians, and buyers and design specialists, the event is a platform for attendees to engage with the latest technologies.
With the Asia Pacific region named as the fastest growing self-adhesives label
market globally, it’s no wonder that manufacturers are increasing their play in this region.
A report released recently by Global Technology Intellect forecasts substantial growth in the Asia Pacific label market, indicating significant opportunities for market expansion.
The report states that technological advancements and shifting consumer preferences will fuel innovation and drive demand. Favourable regulatory landscapes and increasing awareness will further contribute to market growth.
Market Research Intellect predicts a steady CAGR during this period, indicating a positive outlook for industry players. By capitalising on emerging trends and adopting strategic approaches, companies
can position themselves to thrive in this evolving market environment.
A similar report by Mordor Intelligence identified that Asia Pacific is expected to grow at a CAGR greater than 6.3 per cent until 2029 and is estimated to reach almost US$16.23 billion by the end of this year.
The report indicates that, over the short-term, significant factors driving the market are the growing e-commerce industry in the region and the increasing demand for packed goods from the food and beverage industries.
In Asia Pacific, lifestyle changes, the growing disposable income of people, an increase in the number of working professionals, and the growing preference for fast food are said to propel the demand
for packaged food, especially in countries such as China, India, and Japan.
The shifting focus towards bio-based self-adhesive labels will also likely act as an opportunity.
Thai consumers are demanding a shift to circular packaging – more than 90 per cent of consumers in Thailand, in the 2024 Q2 Consumer Survey conducted by GlobalData, stated they choose sustainable packaging when making purchasing decisions.
Thailand’s food and beverage industry is undergoing a significant shift towards sustainability as regulatory pressures and consumer demands for eco-friendly packaging continue to rise. With sustainability increasingly at the forefront of business strategies, industry leaders are taking significant steps to drive the adoption of circular packaging.
In response to growing environmental concerns, the Thai government has also implemented stronger regulations targeting waste reduction and promoting circularity. The Second National Action Plan on Plastic Waste (2022-2027) and the Sustainable Packaging Act are part of the government’s broader effort to tackle plastic waste and improve recycling rates.
These regulations compel food and beverage manufacturers to adopt Extended Producer Responsibility (EPR) frameworks, ensuring that packaging is responsibly managed from production through disposal. As a result, the Thai market is high on the radar of manufacturers in packaging.
When choosing machinery or materials, it’s vital to feel confident about a decision. Probably, the best way to do this is to
see all the options together in one place. Here is a snapshot of the products to be showcased by some from the major exhibitors at the tradeshow:
Durst will showcase its Tau 340 RSC E in a six colour (CMYKW+Or) configuration. The Tau 340 RSC E is a key model within the Tau RSC platform, offering performance, quality and scalability. Its adaptable design allows printers to start with a powerful product tailored to their current needs, while maintaining the flexibility to expand capabilities as their business grows and market demands evolve.
Delivering production speeds of up to 52 m/min (upgradeable to 80 m/min) and true 1200dpi by 1200dpi resolution, the Tau 340 RSC E meets industrial production requirements without compromising on quality.
Some of its other features include: a Dimatix Samba G3L best-in-class printhead, 2pl minimum drop size for smooth gradients and sharpness, and automated nozzle compensation. Automated print head cleaning reduces time for daily maintenance and ensures high up time. In addition, its Tau RSC UV inks are BS5609 and UL compliant, and enable light fastness and heat resistance for outdoor applications.
It is also equipped with Durst Workflow Label, prepress and production software, Durst Analytics, and now Durst Hawk AI.
Hawk AI is Durst’s latest innovative technology that utilises camera vision systems with the aim of automating print quality, resulting in significantly reduced waste and overall improved print quality. Durst Hawk AI is not only an inspection system; it goes one step further as it is correcting print mistakes, such as missing nozzles, inline and in real-time, without any setup needed and without any operator intervention.
UK-based curing systems manufacturer GEW will be exhibiting at Labelexpo Southeast Asia alongside its exclusive distribution partner for the region, Press Systems Group.
GEW will highlight its next generation LED products at the show: AeroLED2 is a refined successor to GEW’s air-cooled AeroLED UV curing system, while the LeoLED2 takes LED performance to new heights over the already highly acclaimed, water-cooled LeoLED system.
The AeroLED2 delivers an increased power level when compared to the original AeroLED model, for faster printing across more applications. It is also newly available for web widths of up to 70cm, to cater for more presses in the narrow web market.
AeroLED2 maintains the key attributes of the earlier model: it is ArcLED compatible, meaning that it can easily be interchanged with GEW’s Arc lamp systems, and it maintains GEW’s unique centralised fan cooling architecture.
As for the LeoLED2, it introduces two power level options to GEW’s acclaimed watercooled system. The regular power option offers modest gains over the original LeoLED, while maintaining backward compatibility. The high-power option, however, brings increases in UV irradiance and dose over its predecessor, delivering unprecedented performance for the most extreme curing challenges in the packaging market.
LeoLED2 maintains the key attributes of the earlier model: it is ArcLED compatible,
meaning that it can easily be interchanged with GEW’s Arc lamp systems, and the same level of temperature control and condensation protection. It is also fully backward compatible with LeoLED, featuring the exact same connections and external dimensions.
GEW director of international sales Marcus Greenbrook said, “With the introduction of AeroLED2 and LeoLED2 to our range, we have the highest performing, most reliable LED systems in the market. We believe that AeroLED2 will become the default UV curing solution for label and narrow web, both in Southeast Asia and globally, as its capabilities are now extended to cater for the entire market.
“We look forward to welcoming customers old and new to our stand at Labelexpo Southeast Asia, and having the opportunity to show off these ground-breaking new products.”
Jet Technologies will be exhibiting at Labelexpo Southeast Asia for the first time
this year, bringing to the region its expertise in digital and labels printing, specialty films, and cutting-edge print technologies.
“Visit us at Labelexpo Southeast Asia and discover the latest digital printing solutions to expand and boost your market, and experience our easy change die-cutting and high-build finish technology,” the company said.
The company is an official partner of Xaar and will showcase the Jet iQ M370 finishing machine. Attendees will get a chance to explore the Jet iQ with Versatex Print Bar, delivering high-build varnish, digital foil, and spot varnish on even uncoated papers. With two semi-rotary flexo units and semi-rotary die cutting, it offers a versatile and powerful finishing solution for any digital press.
Also on display will be the Polly SRI 450, demonstrating its high-speed label inspection, slitting, and rewinding capabilities. With a dual rewinder system and speeds of up to 450 metres per minute, this advanced machine ensures precision, efficiency, and seamless label finishing.
Finally, the OMET iFLEX label press will be launched in Asia. Jet Technologies is OMET’s distributor in the Southeast Asian region. At the Jet Technologies stand, attendees will have the exclusive opportunity to see the iFLEX in action.
Featuring advanced technologies like iLIGHT laser-guided plate alignment and iVISION real-time register control, the iFLEX optimises label printing with superior quality and fast setup times. Jet Technologies will be running live demonstrations on this machine, where people can see its seamless job change capabilities firsthand.
Find Jet Technologies on Stand D2 at the event.
As an interactive state-of-the-art exhibit, Kurz will have on display information about the DM-UNILINER 3D. Although the machine itself won’t be on the floor, it offers a technology deep dive into 3D
inkjet-on-substrate technology for label and roll applications.
The DM-UNILINER 3D is a digital spot coating and metallisation in narrow web machine that is a stand-alone unit for pre- or post-printing embellishment.
Event participants will learn how this technology produces fascinating effects and exciting creations in just one work step, through digital metallisation and coating. The flexibility of the machine enables flat and tactile effects with impressive quality on an industrial scale.
With the DM-UNILINER 3D, users can metallise and varnish in just one work step. Thanks to the ‘inkjet on substrate’ technology, the machine offers individual flexibility for finishing processes and allows users to create flat and haptic effects.
With different ink lay downs from four to 100 μm, users gain maximum design freedom from conventional, flat 2D surfaces that are typical for digital printing. Finished with a wide range of metallisation effects, high-gloss, or matte designs, applications from the DM-UNILINER 3D will catch the eye of customers at the POS.
With the DM-UNILINER 3D, users can finish up to 100 m/min, depending on the substrate. Roll diameters of up to 800mm allow them to work in a time-optimised manner without having to change the reel. Designs can be metallised before or after the printing process, and an additional quality aspect is the possibility of protecting the digital metallisation with digital UV spot varnish.
“The DM-UNILINER 3D redefines digital embellishment with its ability to produce exquisite, high-precision effects that elevate labels to a new standard of luxury,” Kurz Thailand head of sales Warichsaphorn Thongyang said.
“Delivering intricate, shimmering details with unparalleled clarity and brilliance, it enables converters to create visually striking, premium labels efficiently –without compromising on speed or cost-effectiveness.”
Nilpeter will showcase the state-of-the-art FA-17 flexo press at the event. The FA-17 is designed to meet the evolving needs of the label and packaging industry, offering flexibility, automation, and print quality.
Designed to accommodate a printer’s evergrowing requirements, and built around the modern print operator, the machine has an intuitive user interface conveniently positioned within operator reach.
A benchmark of flexibility and modularity, the FA allows printers to enhance the performance of their press with valueadding units and automation features according to application requirements and budget. Future customisations are often done with a simple press of a button.
Some of its key features include:
• Advanced automation – Reduces setup times and enhances overall production efficiency
• Exceptional print quality – Ensures high precision on a variety of substrates, including self-adhesive labels, and flexible packaging
• Operator-friendly design – A streamlined interface and intuitive controls make the FA-17 easy to operate.
Live demonstrations will take place throughout the exhibition, allowing visitors to see the FA-17 in action and discuss how it can benefit their production.
“Labelexpo Southeast Asia is an important event for Nilpeter as it allows us to connect with customers and partners in one of the world’s fastest-growing markets. We look forward to showcasing our latest innovations and discussing how our solutions can help printers optimise their production,” Nilpeter Asia sales director Erik Blankenstein said.
“We invite all industry professionals to visit the Nilpeter stand, F32, to explore the FA-17 and discuss how we can support your business. Our team of experts will be available to provide insights and personalised recommendations.”
OKI will be showcasing a range of innovative printing solutions designed to meet the needs of graphic arts professionals, label producers, and businesses seeking high-performance printing with exceptional media versatility.
Key highlights at the stand include its Pro9542dn light production printer for high-impact graphics, its Pro1050 5-colour short-run label printer, and its Pro330S LED colour label printer.
The Pro9542dn is designed for high-impact graphic arts and light production use, delivering outstanding CMYK plus highdensity white-under single-pass printing. Its advanced LED technology enables vibrant, standout results on a wide range of light, dark, and transparent media.
It is an A3 colour printer with 5-station single-pass (CMYK + white), has print speeds of up to 50 ppm (A4), 45 ppm with white, is network-enabled with PCL support, and features flexible media handling for a variety of substrates.
As for the Pro1050, it is a professionalgrade narrow-format label printer offering CMYK + white printing, perfect for on-demand label production. Capable of printing on white, black, or transparent media, it enables brands to produce waterproof, alcohol-resistant, and greaseproof labels with ease.
Its added opaque white printing enables enhanced visibility on transparent and coloured media, and the machine is
designed to reduce lead times and costs for in-house label production.
The Pro330S, which the company says is the world’s smallest LED dry toner colour label printer, aims to bring colour label printing to a new level of accessibility.
The compact and efficient 3-colour label printer aims to allows businesses to produce versatile and professionalgrade colour labels and tags, maximising advertising impact compared to standard black-and-white thermal prints.
With a strong focus on quality, versatility, and innovation, OKI Southeast Asia marketing manager Steven Ong said the company’s printers empower businesses to enhance their print capabilities while maintaining efficiency and costeffectiveness.
“Southeast Asia’s diverse and dynamic business landscape demands print solutions that offer versatility, efficiency, and cost-effectiveness. OKI’s latest innovations, including the Pro9542dn, Pro1050, and Pro330S, empower customers with high-impact colour printing, durable label production, and flexible media handling,” Ong said.
“From graphic arts to food packaging and industrial labelling, our printers help companies reduce costs, streamline operations, and bring their creative visions to life – all while meeting the region’s growing demand for short-run, on-demand printing.”
Yupo Corporation
Yupo Corporation will showcase CleanSort, a next-generation in-mold technology that allows easy label separation from the container, which can then be recycled to low-contamination form.
The labels used in the CleanSort system are specially designed to be easily separated during the recycling process, carrying away contaminants like inks, foils and coatings. This allows packaging materials such as PP, PET, and HDPE to return to their low contamination state, ready to be reused in manufacturing.
This way, CleanSort minimises contamination in recycled materials, increasing the quality of the PCR content and expanding demand for these recycled products. The result is a more sustainable and efficient recycling process that benefits everyone involved, from plastic reclaimers to brand owners.
The CleanSort labels suit white, light or natural bottles and containers. By removing labels during recycling, CleanSort reduces solid waste and improves the overall recycling experience.
The tradeshow brought together key players in corrugated and carton board production to present and discuss bespoke processing solutions for today’s evolving markets
Attendees of the recent CCE International, one of Europe’s premier trade fairs in Munich, discovered the future of corrugated and folding carton packaging.
The tradeshow brought together key players in corrugated and carton board production to present and discuss bespoke processing solutions for today’s evolving markets.
Over three days, visitors explored an impressive variety and showcase of live machinery and high-tech equipment while engaging with leading suppliers.
Many of the 100 specialist exhibitors brought their live machinery to Munich, showcasing a new generation of highspeed equipment packed with advanced automation and digital features to boost connectivity and workflows.
Sustainability remained a key focus and theme at the event, with energyefficient machinery helping
manufacturers cut waste and shrink their environmental footprint.
As the international meeting point for sourcing efficient and cost-effective production solutions, CCE International 2025 embraced resilience and innovation, connecting industry stakeholders to the latest technology developments and international producers in the sector.
Industry leaders used the opportunity to unveil cutting-edge solutions and provided attendees with strategies on how to navigate a landscape primed for growth, with projections indicating a steady rise in demand and significant investment in capacity.
Visitors included professionals from corrugated board plants, sheet plants, corrugated sheet feeders, folding carton converters, packaging designers, specifiers, rigid carton manufacturers, honeycomb board manufacturers, core board and core tube manufacturers, and trade agencies.
As a highly specialised marketplace, CCE International provided exclusive access and networking opportunities with international brands including: Vice, Officina Meccanica Sestese, Tien Chin Yu Machinery, Talleres Serra, Macarbox, Baysek Machines, Höcker Polytechnik, Messersì Packaging, Bahmüller, Pentatech, Balemaster Europe, Robatech, Solarco Machinery, Kolbus Group, EDF Europe, and CUIR Corrugated.
“Every production line has unique requirements, making off-the-shelf solutions rare. Investing in custom-built machinery is a long-term commitment, and having a reliable supplier ensures not only seamless integration but also ongoing technical support and innovation,” RX paper and print events event director for converting Patrick Herman said.
“CCE International provides a hands-on experience with direct access to live machinery and – just as importantly –a collaborative environment to build lasting partnerships that help businesses
stay competitive. Our entire show concept was built around the industry’s three key pillars: tailored solutions, expert guidance, and futureproof technologies.
“CCE International offers a well-known international platform to personally meet manufacturers and see their latest machinery live and in action. Attendees addressed their specific production requirements in a matter of hours rather than doing months of online research.”
RX is the organiser of CCE International.
Exhibits covered the full spectrum of corrugating lines and corrugated converting equipment, folding carton converting equipment, systems for machine and plant control, materials handling and warehousing, waste extraction and baling, consumables, as well as print machinery, systems and solutions.
Buyers had the chance to see live machinery in action, gaining additional insight and opportunity to carefully assess the benefits of innovative solutions for streamlining their production.
From regulatory changes to evolving consumer preferences, this event also identified insights and opportunities that will shape the industry’s trajectory for years to come.
This highly specialised event acknowledged the longstanding role of the corrugated and folding carton sector as a cornerstone of packaging solutions through two conference streams:
The CCE Conference stream offered an engaging programme of technical talks on the latest trends and developments in the corrugated and carton board sector, with a focus on optimising production processes and value creation.
The Print Conference stream covered print applications in corrugated and folding carton production lines, such as direct-to-corrugated digital printing, flexographic printing for high-volume jobs, or premium print solutions for luxury or high-end retail packaging.
Designed as open seminars, sessions featured representatives from Aumann Lauchheim, Brasilata, BST, COMEXI, Dr. Hönle, ENLYZE, Erhard + Leimer, Fraunhofer IVV, Hewlett Packard (HP), INGEDE, Koenig & Bauer, Kurt Zecher, Meteor Inkjet, MICOR, OPTIMA life science, Plastics Europe, PLG-Consultant, Schreiner Group, Seiko Instruments, Tietoevry, Webfed, Xaar, and other leading suppliers.
The broad agenda covered a wide range of topics, including digital and inkjet printing, label production, packaging,
high-speed drying processes, strategic partnerships, sustainability, API-driven communication, e-productivity, automation and digitisation, advanced coating techniques, the circular transition of plastics, as well as new substrates and materials. A dedicated conference stream on ‘Printing for Packaging’ also took place at the show.
HP GTM manager Wolfram Verwuester spoke about hybrid print production in corrugated cardboard printing, and the need to bridge conventional and digital technologies.
As the corrugated packaging industry is evolving rapidly, driven by the changing consumer demands, shorter production cycled, and increasing sustainability requirements, he explored how hybrid print production, combining digital inkjet and conventional flexographic printing, is necessary in today’s environment.
Verwuester spoke about the new HP PageWide T700i build with Koenig & Bauer, and how the company is pushing the boundaries with PageWide technology and the new Gen 5 Printheads, blending digital precision with flexo efficiency for better profits.
Examples of exhibitor showcases
Suppliers brought their latest innovations to their stands, showcasing the capabilities of these machines and solutions.
Graffica was at CCE International showcasing the Century MWZ 1670Q automatic flatbed die cutter. The machine features a highspeed lead edge feeder paired with a robust feeding table, making it suitable for cutting both corrugated boards and laminated sheets. It also has a height-adjustable back stopper for warped sheets feeding.
The die cutter’s automatic self-lubrication system ensures smooth running, while its central positioning system enables fast job changeover and easy machine set-up. Its gear drive system used as a main drive provides high speed operation.
The machine’s stripping section has a central positioning system, simplifying
the stripping die set-up and allowing for fast job changeovers. Its heavy-duty double action stripper efficiently removes waste, ensuring positive stripping. The waste separator at the front removes trim waste from the sheet and transfers it to the machine drive side by conveyor belt.
Graffica installed the same machine at a converter’s premises in South Australia in March.
Messersì Packaging allowed attendees to explore its range of solutions and discuss how these technologies can support their needs.
Messersì Packaging established its position into the market with the production of PP and PET strapping band and now offers a complete range of packaging machines including automatic and semi-automatic strapping machines, wrapping machines, hooding machines, thermo-shrinking system and complete packaging lines.
Its focus is on state-of-the-art technology, process innovation, and on heightening awareness of its products and services. The company most recently installed a new wrapping machine at Robotic Automation, a NSW-based automation machinery manufacturing company, ensuring performance and efficiency for the customer.
BCM Transtech presented its smart storage solutions and efficient tooling logistics for the corrugated, folding carton and flexible packaging industries, educating attendees on how they can transform operations.
The company designs, manufactures, and installs innovative and effective customised
storage solutions for cutting dies, printing plates, and sleeves – from manual handling to fully-automatic systems.
Its wide product assortment consists of flexo stereo storages, printing sleeve storages, and rotary and flatbed die storages. In addition, its complementary products consist of mobilators, trolleys, mezzanine elevators, steel sheet cladding, and fully automatic flexo stereo cleaning.
COMEXI, a global partner for flexible packaging converting, brought to CCE International its expertise in solutions that cover the entire process – from flexo, offset, and digital printing to slitting, laminating and end-of-line systems.
Attendees to the company’s booth discovered how its latest flexible packaging conversion technologies are designed to reduce carbon footprints while delivering exceptional quality. They also learnt more about COMEXI’s Offset CI, a solution that combines efficiency, sustainability and premium print results.
COMEXI has a technological centre in Bangkok, Thailand, which services the Asia Pacific region – COMEXI’s most important region for the flexible packaging market as it represents more than 46 per cent of its global consumption.
Vice, an Italian chemical company founded in 1999 that specialises in the research, production, and distribution of industrial chemical auxiliaries, took to CCE International to inform attendees about its best chemical specialties for corrugated board.
Some of its products showcased were:
DROP ONDA – Vice’s range of biodegradable liquid gluing assistants that are environmentally friendly and can be used in all starch formulations. DROP ONDA aims to increase machine speed, productivity and mechanical properties of corrugated board.
FIX ONDA – Vice’s range of gluing assistants for different starch formulations in liquid form that acts on different levels, improving the quality of glue for corrugated cardboard.
TAKE ONDA gamma – Vice’s anti-friction/ silicone protective lubricant that aims to provide smoothness on the heating plates, minimising friction and increasing machine speed. The TAKE ONDA T range includes cutting blade protectors that provide a high level of protection and smoothness for all types of blades, reducing friction with the corrugated board and extending their life.
German machinery manufacturing company Kolbus Group brought its expertise in special machine construction for packaging production and corrugated board processing to CCE International.
It showcased its Box maker BX Motion Pro, a machine that creates customised short-run corrugated box production.
It enables production of a wide range of folded packaging (FEFCO types) and custom box styles, including wraps, telescopic boxes, trays, lids, sleeves, and interior features such as inserts, layer pads, and dividers in corrugated board.
With inline digital printing and inline gluing, it allows creasing and countercreasing, cutting lengthwise and crosswise, slitting, die-cutting, and printing in one pass, as well as a MultiOut function for multiple corrugated board blanks arranged next to each other.
Officina Meccanica Sestese showcased its latest innovations in the corrugated and folding carton sectors at CCE International, including its ILS1300/1600 in-line strapping
machine, designed specifically for the corrugated cardboard converting industry. This machine aims to offer seamless integration with casemaker and folding-gluing equipment, enhancing the efficiency of strap application in the production process.
The ILS1300/1600 is designed to be installed on the outgoing side of casemaker and folding-glueing equipment for the application of straps in the direction of flow. After the pack of cardboard boxes comes out of the casemaker, it is conveyed, compacted sideways, and kept perfectly squared up to the strapping area. The range includes two basic models, ILS1300 and ILS1600, to process different pack widths.
Established to successfully bridge the gap between traditional rotary and flatbed corrugated paper die cutting, Baysek Machines took to the event to allow attendees to get a closer look at its C190 Die Cutter.
Manufactured in the US, the Baysek C190 Die Cutter requires only one operator to run the machine. A full stack of sheets is fed into the machine and processed, with the nick-free finished die-cut parts exiting the machine, counted, and stacked seamlessly and quickly, ready for immediate shipping.
The company said this machine allows savings on time and additional labour costs, as no further handling is required. The C190 Die Cutter can also process and die-cut all grades of corrugated from single face up to double wall and solid board.
Images courtesy of LinkedIn.
The Insignia is a sheet-fed, rotar y, flexo magnetic die cutter designed for production-driven operation at an a ordable price point.
SMARTFOLD SERVO X
• 500 metres per minute, max outputs make this one of the fastest folder gluers in the world
• Full auto make ready system, allows 10-minute change overs
• Straight line, crash lock, 4 and 6 corner boxes, pocket folds, custom box option
• Available in 65 cm wide, 80 cm or 1100 cm wide
• Cardboard or corrugated.
• Hot melt and cold glue system friendly
• Auto feeder, delivery, carton packing and robotic palletiser options
Megafold Folder Gluer is designed to run max. Speed of 300m/min with solid board ranging from 250-1200gsm and 3 Ply Litho-laminated and 5 Ply corrugated cartons up to 25mm folded thickness
Folding gluing machine with hand feeder and delivery table
Folding gluing machine with hand feeder and delivery table
TECHNOCUT 1050S
MATERIALS
TRUE GUIDE & GRIP REGISTER TEM ENSURE SHEET-TO-SHEET CURACY. SIDE PULL GUIDE ABLE OF PULLING EITHER LEFT OR RIGHT TO MATCH PRESS REGISTER EDGES.
OP SUCTION AIR FEEDER WERED VIA A BUILT OWER PUMP IN THE HINE. AN OPERATOR CAN INDEPENDENTLY ADJUST OLUMES OF BOTH BLOW & SUCTION TO ADJUST FOR THE T RANGE OF MATERIALS POSSIBLE. INDEPENDENT R HEADS CAN BE TED TO SHEET SIZE.
TRUE GUIDE & GRIP REGISTER TEM ENSURE SHEET-TO-SHEET
TRUE GUIDE & GRIP REGISTER ENSURE-SHEET TO-SHEET CURACY. SIDE PULL GUIDE IS ABLE OF PULLING EITHER LEFT OR RIGHT TO MATCH PRESS TER EDGES.
CURACY. SIDE PULL GUIDE ABLE OF PULLING EITHER LEFT OR RIGHT TO MATCH PRESS REGISTER EDGES.
A TRUE GUIDE & GRIP REGI SYSTEM ENSURE-SHEET TO-SHEET ACCURACY. SIDE PULL GUIDE CAPABLE OF PULLING EITHER LEFT OR RIGHT TO MATCH REGISTER EDGES. A TOP SUCTION AIR FEEDER IS POWERED VIA A BUILT IN BLOWER PUMP IN THE MACHINE. AN OPERATOR INDEPENDENTLY ADJUST VOLUMES OF BOTH BLOW SUCTION TO ADJUST FOR WIDEST RANGE OF MATERIALS POSSIBLE. INDEPENDENT SUCKER HEADS CAN BE ADJUSTED TO SHEET SIZE.
A TRUE GUIDE & GRIP REGI SYSTEM ENSURE SHEETACCURACY. SIDE PULL CAPABLE OF PULLING EITHER LEFT OR RIGHT TO MAT REGISTER EDGES. A TOP SUCTION AIR FEEDER IS POWERED VIA A BUIL T IN BLOWER PUMP IN THE MACHINE. AN OPERATOR
A TRUE GUIDE & GRIP REGI SYSTEM ENSURE SHEETACCURACY. SIDE PULL CAPABLE OF PULLING EITHER LEFT OR RIGHT TO MAT REGISTER EDGES. A TOP SUCTION AIR FEEDER IS POWERED VIA A BUIL IN BLOWER PUMP IN THE MACHINE. AN OPERATOR INDEPENDENTLY ADJU VOLUMES OF BOTH BLO SUCTION TO ADJUST FOR WIDEST RANGE OF MATERIALS POSSIBLE. INDEPENDENT
TRUE GUIDE & GRIP REGISTER TEM ENSURE SHEET-TO-SHEET CURACY. SIDE PULL GUIDE ABLE OF PULLING EITHER LEFT OR RIGHT TO MATCH PRESS REGISTER EDGES.
OP SUCTION AIR FEEDER IS POWERED VIA A BUIL T IN BLOWER PUMP IN THE ACHINE. AN OPERATOR CAN INDEPENDENTLY ADJUST OLUMES OF BOTH BLOW & SUCTION TO ADJUST FOR THE WIDEST RANGE OF MATERIALS POSSIBLE. INDEPENDENT KER HEADS CAN BE ADJUSTED TO SHEET SIZE.
Scan to watch
OP SUCTION AIR FEEDER OWERED VIA A BUILT IN BLOWER PUMP IN THE ACHINE. AN OPERATOR CAN INDEPENDENTLY ADJUST OLUMES OF BOTH BLOW & SUCTION TO ADJUST FOR THE WIDEST RANGE OF MATERIALS POSSIBLE. INDEPENDENT KER HEADS CAN BE ADJUSTED TO SHEET SIZE.
SUCKER HEADS CAN BE ADJUSTED TO SHEET SIZE.
INDEPENDENTLY ADJU VOLUMES OF BOTH BLO SUCTION TO ADJUST FOR WIDEST RANGE OF MATERIALS POSSIBLE. INDEPENDENT SUCKER HEADS CAN BE ADJUSTED TO SHEET SIZE.
• Fast processing, speed to 7500 sheets per hour
OP SUCTION AIR FEEDER IS POWERED VIA A BUIL T IN BLOWER PUMP IN THE ACHINE. AN OPERATOR CAN INDEPENDENTLY ADJUST OLUMES OF BOTH BLOW & SUCTION TO ADJUST FOR THE WIDEST RANGE OF MATERIALS POSSIBLE. INDEPENDENT KER HEADS CAN BE ADJUSTED TO SHEET SIZE.
Scan to watch
• Wide size range, 360 x 400 mm to 750 x 1050 mm
• Cutting force 300 tonnes
Same machine as Box 1 but is upgradable to add the automatic continuous feeder PLUS an automatic delivery table
• Paper, cardboard, solid board, corrugated board plastic
• Corrugated board max 4 mm thick
A TRUE GUIDE & GRIP REGI SYSTEM ENSURE SHEETACCURACY. SIDE PULL CAPABLE OF PULLING EITHER LEFT OR RIGHT TO MAT REGISTER EDGES. A TOP SUCTION AIR FEEDER IS POWERED VIA A BUIL T IN BLOWER PUMP IN THE MACHINE. AN OPERATOR INDEPENDENTLY ADJU VOLUMES OF BOTH BLO SUCTION TO ADJUST FOR WIDEST RANGE OF MATERIALS POSSIBLE. INDEPENDENT SUCKER HEADS CAN BE ADJUSTED TO SHEET SIZE. A RECESSED SCRIBE LINE SINGLE MAGNETIC MAC ALLOW FOR FAST, CONSI DIE MOUNTING & ENSURES TOOLS ARE HUNG PARALLEL CENTERED.
• Carton board min 80 g/m2, max 2000 g/m2
Same machine as Box 1 but is upgradable to add the automatic continuous feeder PLUS an automatic delivery table
RECESSED SCRIBE LINE ON SINGLE MAGNETIC MACHINES W FOR FAST, CONSISTENT DIE MOUNTING & ENSURES DIE OOLS ARE HUNG PARALLEL & CENTERED.
A RECESSED SCRIBE LINE SINGLE MAGNETIC MACHINES ALLOW FOR FAST, CONSIS DIE MOUNTING & ENSURES OOLS ARE HUNG PARALLEL CENTERED.
A RECESSED SCRIBE LINE SINGLE MAGNETIC MAC ALLOW FOR FAST, CONSI DIE MOUNTING & ENSURES TOOLS ARE HUNG PARALLEL CENTERED.
RECESSED SCRIBE LINE ON SINGLE MAGNETIC MACHINES OW FOR FAST, CONSISTENT DIE MOUNTING & ENSURES DIE OOLS ARE HUNG PARALLEL & CENTERED.
RECESSED SCRIBE LINE ON SINGLE MAGNETIC MACHINES OW FOR FAST, CONSISTENT DIE MOUNTING & ENSURES DIE OOLS ARE HUNG PARALLEL & CENTERED.
RECESSED SCRIBE LINE ON SINGLE MAGNETIC MACHINES OW FOR FAST, CONSISTENT DIE MOUNTING & ENSURES DIE OOLS ARE HUNG PARALLEL & CENTERED.
Scan to watch
Scan to watch
Same machine as Box 1 but is also upgradable by added second folding unit to fold and glue crash lock bottom and machine
A PIN MOUNT SYSTEM MAGNETIC MACHINES THE ALIGNMENT OF THE SET OF DIE T OOLS. CYLINDERS ALSO HAVE BUILT-IN MIC ADJUSTMENT CAPABILITIES ENSURE MATING.
A PIN MOUNT SYSTEM ON MAGNETIC MACHINES ENSURE THE ALIGNMENT OF THE SET OF DIE TOOLS. CYLINDERS ALSO HAVE BUILT-IN MICR ADJUSTMENT CAPABILITIES ENSURE MATING.
Same machine as Box 1 but is also upgradable by added second folding unit to fold and glue crash lock bottom and machine
APIN MOUNT S YSTEM ON D MAGNETIC MACHINES THE ALIGNMENT OF THE SET OF DIE T OOLS. CYLINDERS ALSO HAVE BUILT-IN MIC ADJUSTMENT CAPABILITIES ENSURE MATING.
PIN MOUNT SYSTEM ON DU GNETIC MACHINES ENSURE THE ALIGNMENT OF THE PAIRED SET OF DIE T OOLS. CYLINDERS ALSO HAVE BUILT-IN MICROADJUSTMENT CAPABILITIES TO ENSURE MATING.
MOUNT SYSTEM ON DUAL GNETIC MACHINES ENSURE THE ALIGNMENT OF THE PAIRED DIE TOOLS. CYLINDERS ALSO HAVE BUILT-IN MICROTMENT CAPABILITIES TO ENSURE MATING.
A RECESSED SCRIBE LINE SINGLE MAGNETIC MAC ALLOW FOR FAST, CONSI DIE MOUNTING & ENSURES TOOLS ARE HUNG PARALLEL CENTERED. A PIN MOUNT SYSTEM MAGNETIC MACHINES THE ALIGNMENT OF THE SET OF DIE T OOLS. CYLINDERS ALSO HAVE BUILT-IN MIC ADJUSTMENT CAPABILITIES ENSURE MATING.
N MOUNT S YSTEM ON DUAL GNETIC MACHINES ENSURE THE ALIGNMENT OF THE PAIRED SET OF DIE T OOLS. CYLINDERS ALSO HAVE BUILT-IN MICROTMENT CAPABILITIES TO ENSURE MATING.
PIN MOUNT SYSTEM ON DU GNETIC MACHINES ENSURE
THE ALIGNMENT OF THE PAIRED SET OF DIE T OOLS. CYLINDERS AVE BUILT-IN MICROADJUSTMENT CAPABILITIES TO ENSURE MATING.
HYDRAULIC PRESSURE
Smartfold Classic Folder Gluer is designed to run at a maximum speed of 400m/min, handling solid board ranging from 170-800gsm and 3-ply litho-laminated cartons up to 15mm folded thickness. It offers many upgrade and automation options, including Braille application, vision inspection systems, and inserting.
HYDRAULIC PRESSURE
HYDRAULIC PRESSURE ASSEMBLIES ARE ADJU VIA THE BL ACK WHEEL. ADJUSTABLE UP TO 3,000 CUTTING PRESSURE IS AV GAUGES ENABLE OPERA DETERMINE MINIMUM TO EXTEND DIE LIFE.
HYDRAULIC PRESSURE ASSEMBLIES ARE ADJUSTED VIA THE BL ACK WHEEL. INFINITE ADJUSTABLE UP TO 3,000 CUTTING PRESSURE IS AVAI GAUGES ENABLE OPERATOR DETERMINE MINIMUM PRESSURES TO EXTEND DIE LIFE.
Scan to watch
HYDRAULIC PRESSURE ASSEMBLIES ARE ADJU VIA THE BL ACK WHEEL. ADJUSTABLE UP TO 3,000 CUTTING PRESSURE IS AV GAUGES ENABLE OPERA DETERMINE MINIMUM TO EXTEND DIE LIFE.
Scan to watch
AULIC PRESSURE ASSEMBLIES ARE ADJUSTED EASI VIA THE BL ACK WHEEL. INFINITEL TABLE UP TO 3,000 PSI OF CUTTING PRESSURE IS AVAIL ABLE. UGES ENABLE OPERATOR TO DETERMINE MINIMUM PRESSURES O EXTEND DIE LIFE.
ASSEMBLIES ARE ADJUSTED EASI VIA THE BL ACK WHEEL. INFINITE ADJUSTABLE UP TO 3,000 PSI OF CUTTING PRESSURE IS AVAIL ABLE. UGES ENABLE OPERATOR T DETERMINE MINIMUM PRESSURES O EXTEND DIE LIFE.
HYDRAULIC PRESSURE ASSEMBLIES ARE ADJU VIA THE BL ACK WHEEL. ADJUSTABLE UP TO 3,000 CUTTING PRESSURE IS AV GAUGES ENABLE OPERA DETERMINE MINIMUM TO EXTEND DIE LIFE.
HYDRAULIC PRESSURE ASSEMBLIES ARE ADJUSTED EASI VIA THE BL ACK WHEEL. INFINITE ADJUSTABLE UP TO 3,000 PSI OF CUTTING PRESSURE IS AVAIL ABLE. UGES ENABLE OPERATOR T DETERMINE MINIMUM PRESSURES TO EXTEND DIE LIFE.
FOR FURTHER INFORMATION PLEASE CONTACT OUR HEAD OFFICE 72 Grady Crescent, Erskine Park, NSW, 2759, email: info@graph-pak.com.au Toll Free: 1300 885 550
ASSEMBLIES ARE ADJUSTED EASI VIA THE BL ACK WHEEL. INFINITE ADJUSTABLE UP TO 3,000 PSI OF CUTTING PRESSURE IS AVAIL ABLE. UGES ENABLE OPERATOR T DETERMINE MINIMUM PRESSURES TO EXTEND DIE LIFE.
IVE and Starward Whisky demonstrate how a strong partnership and thoughtful design can create truly distinctive and expertly crafted packaging
Packaging plays a crucial role in shaping a product’s identity, particularly in the premium whisky market. Every element, from structural integrity to finishing touches, must ensure functionality while reflecting the premium quality of the product inside. The collaboration between IVE and Starward Whisky demonstrates how a strong partnership and thoughtful design can create truly distinctive and expertly crafted packaging.
Starward Whisky Distillery is known for pushing boundaries in whisky-making, and its festive release, Panettone in a Bottle, was no exception. Given the sentimental value and premium nature of the release, its packaging needed to be remarkable –designed to feel like unwrapping a luxurious gift while maintaining Starward’s distinctive branding.
Starward envisioned a modern packaging design that opened like a traditional panettone, creating a sense of anticipation, excitement and the ‘wow’ for the gift receiver. It had to be both structurally sound and visually striking, ensuring it aligned seamlessly with the whisky’s refined character and exclusivity.
The challenge was to create a solution that was as special and rare as the product itself – balancing function, aesthetics, and a sense of occasion. To capture this, Starward wanted to go beyond one-sided printing and achieve inside printing on the gift box to create engagement and storytelling.
The design process
The project began with initial discussions between Starward and IVE’s team of packaging specialists. After reviewing a paper mock-up provided by the client, the team quickly transformed the concept into a structural design, producing dieline samples within a day.
Once the structure was confirmed, the final artwork was developed in collaboration with Starward’s design agency, Stranger & Stranger, to ensure the branding was executed perfectly. For the final packaging, a 830um
whiteback board was selected, printed via UV offset on a Heidelberg press. This method ensured crisp, high-quality printing with instant UV curing, bringing out vibrant colours and sharp details. Premium finishes such as gold foiling, embossing, and reactive UV varnish were incorporated to add texture and dimension, enhancing the packaging to reflect the whisky’s premium craftsmanship and distinctive appeal.
As with any complex packaging project, several challenges arose throughout production. One of the first obstacles was identifying a board that provided both the necessary strength and high-end finish. Working closely with Ball & Doggett, a material was sourced that met these requirements while maintaining the desired look and feel.
Another key challenge was balancing the use of foiling and UV reactive varnish, two finishes that don’t always work together seamlessly. Foiling adds a rich, metallic finish, while UV reactive varnish creates a raised, glossy texture.
The challenge was making sure these elements worked in harmony, enhancing rather than clashing with each other. This required precise testing and refinements to prevent any imperfections. As the packaging was produced locally in Melbourne, the Starward team had the opportunity to attend print sessions, allowing for hands-on refinements and real-time problem-solving. This level of collaboration ensured that every detail was fine-tuned before production was finalised.
The completed packaging delivered on both practicality and visual appeal, with a unique opening design that created an engaging unboxing experience. Gold foiling and embossing added a sophisticated touch, while the reactive UV varnish created depth and a dynamic effect.
“The packaging not only looked impressive but also felt luxurious, reinforcing the whisky’s premium status and making it a perfect complement to this limited-edition release,” IVE head of client partnerships – print Chris Terry said.
“The success of this project was a result of the expertise of both teams, with IVE’s deep knowledge of packaging and Starward’s commitment to excellence making for a highly effective collaboration. By producing packaging solutions locally, both companies have been able to collaborate closely, ensuring that Starward’s products receive the level of detail and care they deserve.
“Following this release, Starward Whisky continues to explore new packaging innovations, with several upcoming projects already in development.
“The success of Starward Panettone Whisky has set a new benchmark for future limited-edition releases, demonstrating the impact of thoughtful collaboration and technical excellence.”
Orora’s Saverglass meticulously executed Papa Salt’s vision, applying refined touches to elevate the bottle’s aesthetic and make it fully functional
Crafted in the heart of Byron Bay, Papa Salt Coastal Gin was nurtured by a vision to unveil a unique gin, presented in a distinctly shaped bottle –perfect for sharing with friends or effortlessly nestled into the sand during a sun-soaked beach day.
Papa Salt Gin was born from a shared passion of five friends who, despite their love for gin, couldn’t find one abroad that satisfied them all. After 59 different recipe attempts, the result exudes a flavour profile with a symphony of native botanicals including “zesty wax flower, hibiscus and citrus peel – all wrapped up with subtle hints of nutty wattleseed, the zing of ginger and an unmistakable minerality from a hint of oyster shell,” according to Papa Salt.
Inspired by iconic Australian beach days
The journey to bring Papa Salt’s bottle to life began in 2022, when the Australian brand partnered with Saverglass to produce 700ml bottles at Orora’s manufacturing plant in France. From the start, the collaboration aimed to create a bottle design that was both functional and beautifully crafted.
Saverglass, which joined Orora Group in 2023, produces premium and highly sophisticated glass bottles for beverage brands all over the world. The Saverglass team were briefed on Papa Salt’s vision by Squad Studio, who designed both the bottle and the Papa Salt Paloma RTD can initially.
The key focus of the bottle design was portability and style. Drawing inspiration from the classic hip flask, creating a bottle that fits effortlessly in a beach bag, but brings pride when displayed on the shelves of the most stylish bars around the world.
“Every detail was thoughtfully designed to embody the natural beauty and laidback charm of the Australian coastline,” Saverglass Australia general manager Sally Arnold said.
Saverglass, known for its beautifully designed and created glass packaging, meticulously executed this vision, applying refined touches to elevate the bottle’s aesthetic. The white lettering of the Papa Salt logo is manually stamped on the front of each bottle, adding a sophisticated dimension, while the palm tree logo near the base subtly hints at the brand’s beachside origins.
The bottle’s aqua blue shade, known as a ‘soft acqua’, was inspired by ocean hues, which was a labour-intensive process that Saverdec, Saverglass’ specialist decoration department, meticulously perfected to deliver to our customer.
After numerous trials, the Saverglass team finally captured the dreamy, ocean-inspired colour that perfectly encapsulates Papa Salt.
Papa Salt Coastal Gin is now available in multiple sizes including 50ml, 700ml, and 1L bottles.
A new chapter with RTD gin cocktails
In 2024, Papa Salt expanded its portfolio through a collaboration with CAPI and
Orora Cans. Together they introduced a ready-to-drink (RTD) cocktail: the Papa Salt Paloma, crafted with CAPI’s iconic grapefruit soda.
Packaged in Orora’s 250ml slimline cans, the iridescent metallic blue finish perfectly mirrors the sparkling hues of Australia’s coastal waters.
The Orora Cans team perfectly executed the can design brief which brought to life the iconic reflective blue accents that encapsulates the Papa Salt brand and creates a premium looking finish that enhances the consumer experience.
Papa Salt has launched in both Australia and UK markets, with the Coastal Gin and Paloma now available across Virgin Airlines, BWS, and Dan Murphy networks within Australia.
By the Orora Beverage team.
For leaders in the labels industry, the future lies in building inclusive, dynamic, and innovative organisations that inspire employees and embrace change
One of the sessions from the recent FINAT European Label Forum centered on label leadership, providing an in-depth exploration of effective leadership strategies within the label industry.
The session featured a panel discussion with label industry leaders and a closing keynote by Olympic gold medalist and coach Tim Foster.
The panel, comprising of Laura Bas (Gen Z expert and former UN Youth Ambassador), Tom Baker (Baker Labels, UK), Dana Kilarska (Purgina Labels, Slovakia), Iban Cid (Germark), and Anastasios Politis (IC – International Circle of Educational Institutes of Graphic Media Technology and Management, Greece), tackled critical challenges in attracting and retaining talent while emphasising the unique aspects of leadership within the label sector.
One recurring theme was the pressing need to attract younger generations to the industry. Panelists acknowledged that the label industry often struggles with its image as “not sexy”. However, the consensus was clear: rebranding the sector to highlight its innovation, sustainability efforts, and impact on everyday life is essential.
Suggestions included:
• Enhancing employer branding: Creating authentic narratives around the industry’s contributions to sustainability and innovation. Using digital platforms, companies can showcase how their work impacts global supply chains and consumer experiences.
• Engaging Gen Z and Millennials: As younger generations value purposedriven work, collaboration, and continuous learning, fostering an inclusive and adaptive workplace culture can better resonate with these demographics.
• Educational partnerships: Some companies successfully collaborate with educational institutions, so programmes such as internships, apprenticeships, and job rotations are effective in attracting and developing young professionals.
Visual takeaways from the session
Panelists agreed leadership in the label industry must evolve to meet the expectations of a diverse workforce. The panel stressed the importance of:
• Intergenerational collaboration: Pairing experienced employees with younger professionals fosters mutual learning and innovation. Mentorship programmes that encourage two-way knowledge sharing are highly effective.
• Flexibility and autonomy: Empowering employees with flexible work arrangements and opportunities for creative problem-solving aligns with the values of younger generations.
• Positive workplace culture: Leaders discussed how trust, empathy, and transparency form the foundation of a productive and engaged workforce. They also emphasised creating a culture where feedback is constructive and actionable.
Foster’s keynote on leadership offered parallels for label industry leaders aiming to guide their teams effectively. He used the analogy of his Olympic rowing team to illustrate the following principles:
1. Trust as a foundation: A successful team begins with trust in individual
expertise. Foster described how each rower brought unique strengths to the boat, emphasising the importance of recognising and leveraging individual contributions.
2. Constructive conflict: Foster highlighted how his team embraced open and honest communication. After a rare defeat before the Sydney Olympics, the team held a candid discussion where every member took personal accountability and identified areas for improvement. This meeting transformed their approach, ultimately leading to their gold medal win.
3. Commitment and accountability: Foster stressed the importance of shared goals and relentless effort. His team’s mantra, “Will it make the boat go faster?” served as a guiding principle for decision-making and action, ensuring alignment with their ultimate objective.
4. Adapting leadership styles: As a coach, Foster learned that effective leadership requires understanding and addressing the unique motivations of team members. He stressed the need for leaders to balance technical expertise with emotional intelligence to inspire their teams.
Foster also drew direct connections between sports and business leadership:
• Set ambitious but clear goals: Just as his team aimed to surpass the world record, businesses should define measurable, ambitious targets to drive performance.
• Foster team resilience: Challenges and setbacks are opportunities for growth. Leaders should cultivate a culture where teams view failures as stepping stones to success.
• Promote continuous improvement: Foster described how his team’s training regime involved constant evaluation and refinement. Similarly, businesses must invest in upskilling and innovation to stay competitive.
For label industry leaders, the key takeaway was clear: the future lies in building inclusive, dynamic, and innovative organisations that inspire employees and embrace change.
The packaging sector is progressing at different speeds across this continuum of business improvement. Where does your business sit?
In the February issue of ProPack.pro, I shared my 2025 predictions for the packaging industry and anticipated continued industry consolidation. While three months is a long time in such a fastmoving industry, I’m surprised by how quickly these trends have taken hold in early 2025.
At the larger end of the scale, some of the biggest packaging transactions we have ever seen emerged: Megadeals like Smurfit Kappa acquiring Westrock, Amcor and Berry announcing a proposed merger, and closer to home, Orora disposing of its packaging distribution business to Veritiv (following its major acquisition of Saverglass in late 2023). Whilst most of these assets are offshore, the changing of hands does produce ripple effects on the Australian market.
On a smaller, more local scale, Spicers acquired Signet Packaging, Interpak acquired Orora’s closures business, and Tricor Braun continued its acquisition strategy picking up UniquePak and Alplas, among a list of other packaging transactions.
The strategic drivers are clear, including scale efficiencies and footprint consolidation, and vertical integration and capability expansion. There is both industry and private equity interest in this space.
In the public forum, IVE Group has made its intentions clear that it is open to further packaging acquisitions in the local market. There is already a hive of M&A activity working quietly through the customary processes, and we expect a number of these to transact in 2025. Stay tuned.
Despite some market uncertainty, the general consensus is that uncertainty is a short-term issue, so the key need to refresh capital in the industry continues. Whilst businesses are putting more scrutiny across investment decisions, the key focus areas remain:
• Capital equipment can be a key differentiator
It is time to reassess priorities and ensure strategic alignment for sustained success
• Automation and efficiency gains are key
• Investing in production flexibility to meet evolving customer demands is critical: digital, multi-size, customisations, and more.
Turning into 2025, businesses continue to push cost-out programs to maintain margins, with common initiatives including process optimisation, footprint and supply chain reviews, and tightening discretionary spend.
The challenge is ensuring that cost reductions don’t come at the expense of long-term competitiveness. The best execution strikes a healthy balance between immediate cost savings and maintaining ability to scale and compete effectively.
The next competitive battleground
The natural progression on the business improvement continuum, after investment, cost out, and M&A opportunities are exhausted, is sales excellence. Those with cost-out programs largely embedded, attention is shifting to driving revenue growth and margin improvement. The most effective businesses are focusing on:
• Customer segmentation and valuebased pricing to maximise profitability
• Data-driven sales strategies that enhance commercial decision-making
• Solution-based selling to increase customer loyalty and differentiation.
This shift suggests that commercial capability is becoming a key differentiator – businesses that invest in stronger sales execution will be well-placed to outperform competitors still focused solely on cost control.
Sustainability: Talked about but often deprioritised
Sustainability remains a consistent discussion point, but a few months into 2025, we have noticed it has taken a back seat with more immediate business pressures emerging.
Some businesses are embedding sustainability into broader efficiency programs, such as energy reduction and process optimisation, but others are pausing major initiatives to focus on financial and operational priorities. This is consistent with the historical cycle. Of course, the risk is that businesses lagging in this space will fall behind as regulation and customer expectations evolve.
The packaging sector is progressing at different speeds across this continuum of business improvement. Where does your business sit? What you do for the balance of 2025 will be decisive – it is time to reassess priorities and ensure strategic alignment for sustained success.
Peter Fotiadis is a co-founder and partner at Mattingly, an industry expert supporting businesses with strategy through to execution: strategy and growth, deals and integration, and transformation and execution.
True fit-for-purpose packaging needs to demonstrate ease of use design principles
Designing packaging that is thoughtful, intuitive, and accessible can be the difference between edible food being unnecessarily wasted, or not, in a household.
Accessible and inclusive packaging makes all the difference to so many people with limited functional abilities in the community; but yet it is often overlooked in the design process.
Key guidelines for accessible packaging include packaging that is easy to open and reclose, clear intuitive instructions, highly legible font, colours and labelling, and unique intuitive design features that eliminates the angst so many people have with packaging. True fit-for-purpose packaging needs to demonstrate ease of use design principles.
All too often, accessible packaging is not considered in the new product development stage, which in turn leads to unnecessary frustration such as opening and resealing packs, reading the ingredients or labelling, and being able to intuitively open the packaging without hurting oneself.
How many times have we all grabbed a knife to open a pack of ham, spilt food across the kitchen countertop because the pack was too hard to open, been unable to read the text on the pack (even with glasses on), or used your teeth to open a pack and then vowed to never buy that brand again?
You, as brand owners, must consider accessible design and ease of use elements in your packaging designs. Have you tested your packaging with all your target audiences? For one, can they open and close the pack?
As someone with the unique opportunity to work in many countries around the world, the best part of my job is visiting retail stores to see how each region is designing their packaging.
One of my latest trips was to Japan and I have never seen more thoughtful, accessible, and inclusive packaging designs before. The trip re-confirmed for me that Japanese embed accessible and inclusive design principles into almost all of their packaging – right from the start of the
design process – and should be a benchmark for other countries.
The thoughtful, accessible, and inclusive designs I saw truly do make life easier for everyone in society. Japanese packaging designs consider the needs of all types of people – visually impaired, people with disabilities, senior members of the community, and people that have difficulty opening and closing packaging. Japanese packaging also intuitively communicates to the consumer how to open and close the packaging. The packs display arrows, feature text explanations, and include multiple tear and notch points. The packaging is so intuitive by nature, it makes opening and closing the packaging easy.
One innovative accessible and inclusive packaging design feature in Japan is that all alcoholic beverage cans have braille on the top to indicate to the visually impaired that the beverage they have selected contains alcohol. This ensures the consumer doesn’t accidentally purchase alcohol instead of another beverage.
Next time you are in Japan, head to the milk aisle. You will notice that some milk cartons have notch points or arc-shaped indentations on the top and some do not. These notch points alert the visually impaired that the carton is a pure milk
product. Those without the indentation are not.
No more mistakes confusing shampoo with conditioner
One of the most frustrating issues many of us face when we are in the shower is working out which bottle is shampoo, and which is conditioner. This can be due to the packaging being similar in colour, shape, and design, the font being too small to read on the bottles, or the text being illegible.
Japanese shampoo and conditioner bottles are designed differently and can be deciphered merely by touching the bottle. Shampoo bottles have textured stripes on the side and conditioner bottles have none. This is also an ideal feature for visitors to Japan who are unable to read Japanese, as well as visually impaired.
Accessible and inclusive packaging design that is intuitive, easy-to-open and innovative should be an integral part of your packaging and I encourage you to integrate this critical element into your future design processes. Your packaging could make a difference for so many people – just take Japan as an exemplar for this type of design.
Nerida Kelton is the executive director of the Australian Institute of Packaging (AIP) and vicepresident, sustainability and save food of the World Packaging Organisation (WPO).
Barrier coatings on paper-based materials or mono-plastic materials are often
considered to be two of the more sustainable packaging options, according to Smithers
As packaging manufacturers and brand owners look to develop packaging that can be labelled as ‘sustainable’, the core functionality of the packaging must be maintained.
The pack still needs to preserve the quality of its contents – providing protection both from physical damage and commonly, providing a barrier to oxygen and moisture vapour. The barrier and permeability of the pack materials is often critical in determining the shelf life of the packaged product.
The limited shelf life provided by suboptimal materials can lead to more frequent, less economic pack deliveries and greater product waste through spoilage. The use of ‘sustainable’, but compromised materials may complicate your supply chain with no overall benefit to the environment.
Sustainability options
There are several areas that are being considered for sustainable packaging. These include:
• Light-weighting through improved pack design, manufacturing process controls and transportation
• A reduction in the complexity of the materials used in a pack, making them easier to be recycled
• Producing a more durable/functional pack which can be re-used/re-filled
• Reducing the susceptibility of the product to damage or environmental deterioration, thereby reducing the barrier requirement from the packaging.
Barrier coatings on paper-based materials or mono-plastic materials are often considered to be two of the more sustainable packaging options.
They can be made to work, but their limitations in terms of barrier and permeability performance in relation to traditional multilayer structures need to be understood.
Barrier coatings
Functional and barrier coatings may be used to prevent paper-based packaging
from simply getting wet or provide some resistance to staining from greasy foods.
A more demanding requirement is to limit the ingress of oxygen or moisture vapour to extend the shelf life of the product. In essence, coatings are used to mitigate the poor performance of paper – when compared with most plastics – in applications that require some barrier performance.
Polyethylene is a popular mono-plastic material, and is an inherently good moisture barrier. In applications which require an enhanced oxygen barrier, a mono-plastic material will often need to incorporate a thin barrier layer of a second high barrier plastic, such as ethylene-vinyl alcohol copolymer (EVOH).
Care needs to be taken to ensure that the barrier layer does not undermine the recyclability credentials of the final pack.
Permeability properties
Knowing the water vapour and oxygen transmission rates of ‘sustainable’ alternative packaging materials is critical in determining their suitability for the packaging of moisture- and oxygen-sensitive products.
However, a word of caution when looking at the permeability rates quoted for barrier coated papers. The act of folding or creasing a coated paper may have a marked effect on its barrier performance unless the coating remains intact through the conversion and subsequent handling processes.
How a packaging expert can support
The Smithers team works with clients to evaluate the barrier properties, permeability characteristics and performance of their packaging materials.
This includes the following testing services for:
• Water vapour transmission rate (WVTR)
• Oxygen transmission rate (OTR)
• Physical packaging material properties
• Packaging functionality
Its ISO 17025 accredited independent laboratories provide comprehensive support for every packaging challenge.
Smithers tests to a wide variety of International Standards including ISO, ASTM, Tappi, BS and ISTA, and is also part of the Amazon APASS accreditation scheme.
The research firm finds there has been an increasing number of concerns about the potential leaching of chemicals from the plastic into products packaged with this material
Environmental organisations are increasingly highlighting the numerous health risks associated with phthalates, leading to a rise in consumer awareness and concern over the use of plastic packaging in processed food and beverage products, according to GlobalData.
The use of phthalates in plastic packaging is facing increased scrutiny due to a growing body of research that underscores significant health risks linked to these chemicals. This concern has led to legal action by environmental organisations such as Earthjustice and the Environmental Defense Fund against the FDA over its alleged refusal to address regulation concerning the issue.
One notable health risk associated with plastics is their propensity to absorb flavours, colours, and odours, which consequently raises concerns about the potential leaching of harmful chemicals into food and beverage products packaged with this material.
GlobalData packaging consultant and analyst Chris Rowland said, “The European Union has implemented a ban or imposed restrictions on certain phthalate compounds that come into contact with food, a regulatory move adopted by other nations such as the UK and Canada.
“To future-proof their packaging capabilities, FMCG companies could explore innovative alternatives, including paper or plant-based materials.
“While initially this shift may entail higher costs, the growing consumer awareness of health risks associated with plastic packaging, coupled with a rising preference for sustainable packaging solutions and the tightening of global regulations on plastic packaging use, suggests that a failure to adapt could lead to a long-term competitive disadvantage.”
According to the latest consumer survey by GlobalData for Q4 2024, more than 50 per cent of consumers are “extremely” or “quite concerned” about the amount of processed food they eat or give to others in the “meat”, “pre-packaged meals”, and “food/drinks for children” categories.
“Consumers who are concerned about their physical fitness and dietary intake of processed foods tend to be more open to alternatives to plastic packaging,” Rowland said.
“Consequently, an opportunity may arise for consumer-packaged goods manufacturers to respond to these concerns, by providing packaging free from phthalates, prominently displaying this feature on the packaging, and working with their packaging suppliers to pioneer innovations in paper and biodegradable packaging for processed foods.”
At present, “phthalate-free” claims are predominantly associated with products within the personal care category, including soaps, cosmetics, and skincare products.
Additionally, certain niche food producers are making strides by advocating for packaging that is plastic-free, biodegradable, and recyclable.
A case in point is Pheasants Hill Farm in the UK, which markets a range of food products, including steaks, mince, and burgers, in plastic-free pouches. These pouches are constructed from plantbased materials, which are claimed to be biodegradable, compostable, and ocean-friendly.
Numerous packaging formats are now being presented as safer and more environmentally friendly alternatives to phthalate-containing plastic packaging. For example, mushroom packaging employs mycelium – the root structure of mushrooms – to bind agricultural waste into biodegradable packaging materials.
This method is not only more sustainable but also provides natural insulation and protection for fragile goods. Seaweed is another material gaining popularity in the packaging industry because of its biodegradable properties and its ability to decompose without leaving harmful residues.
“The health and environmental concerns associated with plastic packaging are significant and complex. Addressing these issues necessitates a collaborative effort from consumers, businesses, and regulators to adopt sustainable practices and alternative materials. By adopting paper-based packaging and other alternative materials, brands can align with consumer preferences, comply with regulations, and demonstrate their commitment to health, well-being, and sustainability,” Rowland said.
AIP Australasian Packaging Conference May 6-7, 2025 Sydney, Australia aipack.com.au
Labelexpo Southeast Asia May 8-10, 2025 Bangkok, Thailand labelexpo-seasia.com
China Print 2025 May 15-19, 2025 Beijing, China printchina.com
PacPrint 2025 May 20-23, 2025 Sydney, Australia pacprint.com.au
IPACK-IMA Milano May 27-30, 2025 Milan, Italy ipackima.com
ProPak Asia 2025 June 11-14, 2025 Bangkok, Thailand propakasia.com
Smart Packaging World Congress June 19-20, 2025 Amsterdam, Netherlands events.awa-bv.com/AIPIAWC25
Industrial Transformation Australia July 22-24, 2025 Sydney, Australia industrialtransformation.com.au
Labelexpo Europe 2025 September 16-19, 2025 Barcelona, Spain labelexpo-europe.com
Pack Print International September 17-20, 2025 Bangkok, Thailand pack-print.de