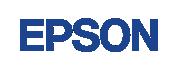
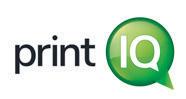
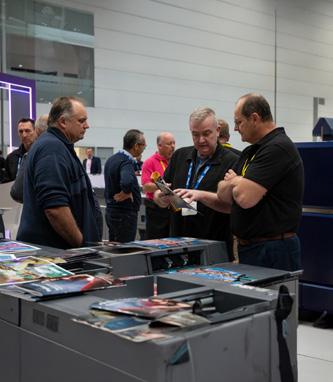
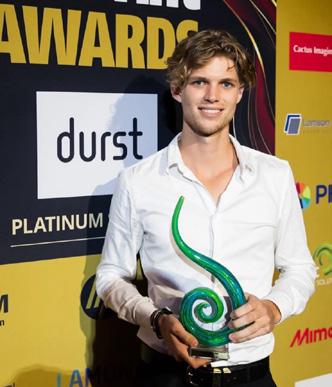
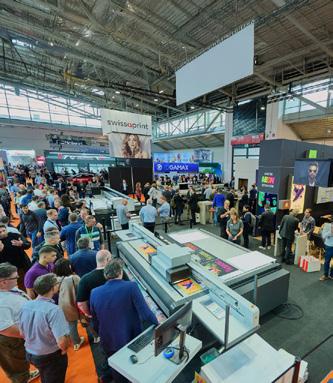
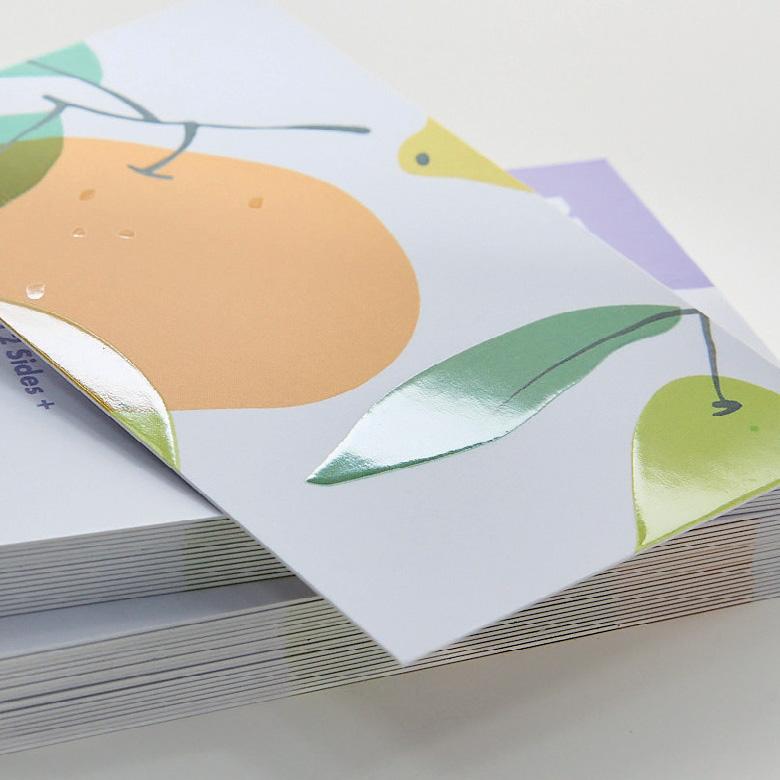
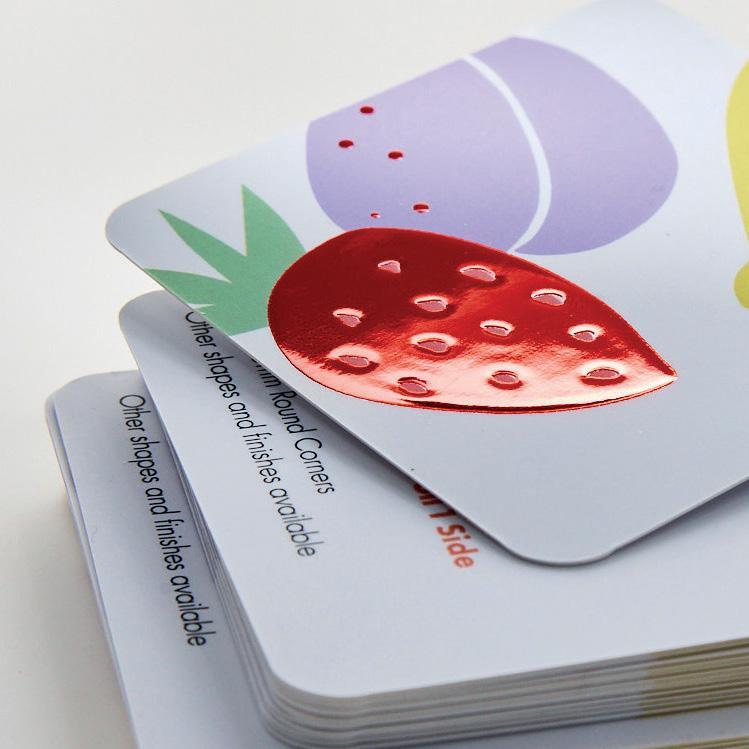
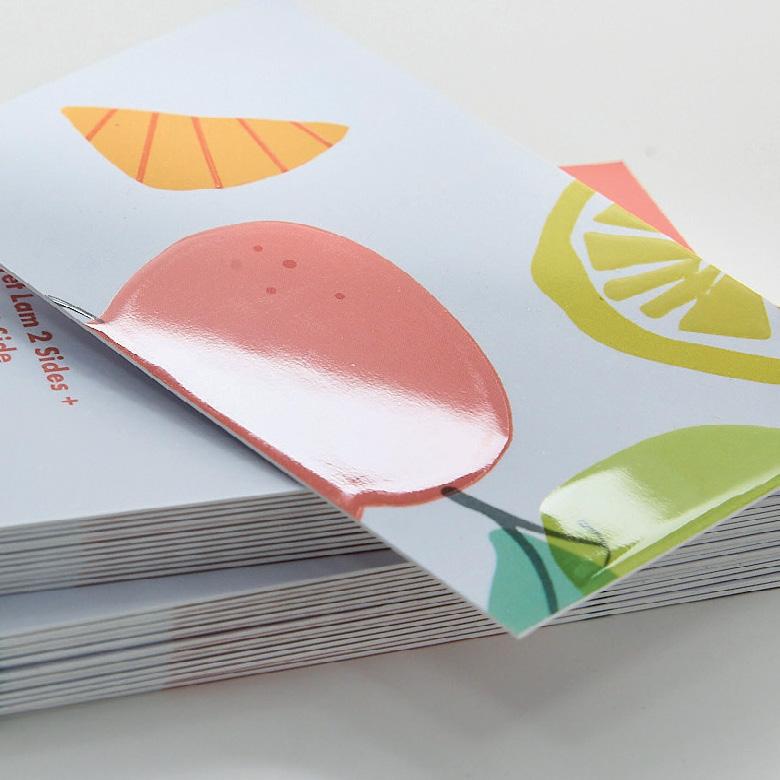
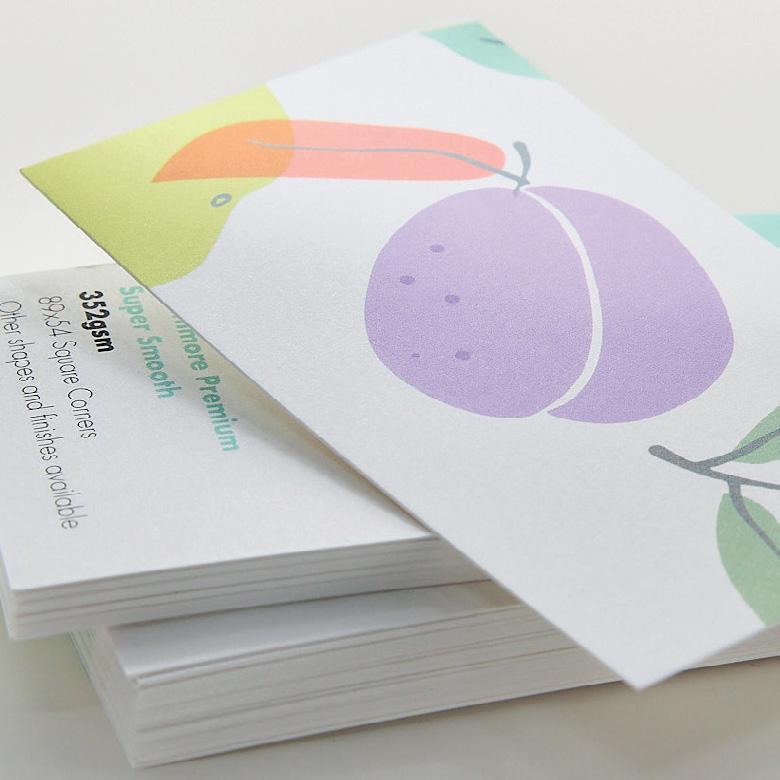

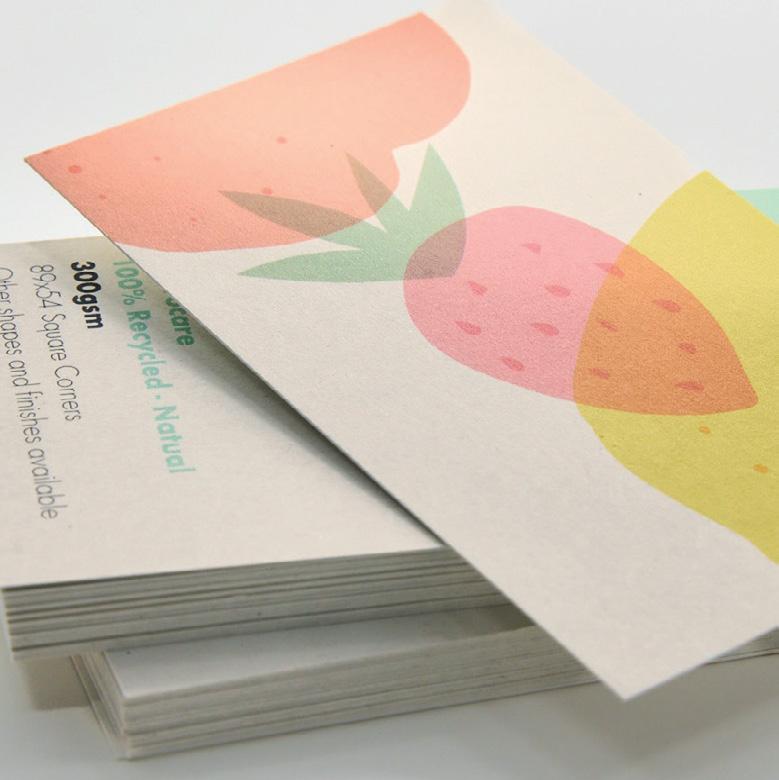
From uncoated to laminated to UV or foils - Hero Print has you covered
AUSTRALIA’S BEST TRADE PRINTER
6-12 Update
A news roundup from the world of print
14 Case study: Carbon8
Carbon8 broadens service offering following purchase of new Fujifilm Revoria PC1120
18 Downtime
Zünd celebrates the opening of its Australian headquarters and showroom
20 Star Business: SS Signs
SS Signs is gearing for growth following the re-launch of its new website and online ordering system
22 Cover story: Why PacPrint 2025 is the must-attend industry event of the year
The premier trade event for the print, sign, and graphics industries is just weeks away
26-38 PacPrint 2025 preview
See what some of the industry’s leading brands will be showcasing at PacPrint in Sydney
40 Case study: Zimmermann Industries Zimmermann Industries ramps up productivity and eyes new markets with new Mimaki flatbed
42 FESPA Global Print Expo preview
FESPA Global Print Expo is set to welcome more than 550 new and returning exhibitors from more than 36 countries
48 Case study: Corrective Services Industries
How CSI is empowering inmates with pathways in print
50 Comment: Charles Watson Navigating the new casual employee conversion regime
51 Comment: Andrew Ash
Five signs it’s time to bring a chief financial officer on board
52 ProPrint Diary
Keep up-to-date with the latest industry events
We’re now just weeks away from some of the industry’s biggest events of the year. PacPrint 2025, which is taking place at the Sydney Showground at Sydney Olympic Park is set to bring together industry leaders, innovators, and technology pioneers to showcase the latest advancements in wide-format printing, packaging, signage, workflow automation, and sustainability.
Alongside product showcases, PacPrint 2025 will feature an insightful seminar program covering an in-depth range of topics including AI and automation in print, sustainable printing practices, hybrid print solutions, as well as the future of packaging and labels.
According to the event’s organisers, a not to be missed
seminar session is the ‘Leaders in Trade’ panel, where industry experts will tackle supply chain challenges, emerging market opportunities, and the future of print technology. You can read all about what’s on at PacPrint in this edition’s cover story from page 22.
Also in this issue, we bring you a sneak peek of what some of the industry’s leading brands will be showcasing at FESPA Global Print Expo in Berlin. FESPA Global Print Expo, along with the European Sign Expo, and Personalisation Experience is expected to welcome more than 550 new and returning exhibitors from more than 36 countries, already surpassing exhibitor numbers from last year’s events.
Returning to Berlin for the first time in three years, visitors will have the opportunity to see the latest products and innovations from a rich line-up of international players including the latest trends in sustainability, print on demand, and intelligent automation. See what’s on in our special FESPA Preview from page 42.
Editor Claire Hibbit, chibbit@intermedia.com.au
Editor Hafizah Osman, hosman@intermedia.com.au
Design and Production Manager Sarah Vella, svella@intermedia.com.au
Managing Director James Wells, james@intermedia.com.au
Subscriptions (02) 9660 2113, subscriptions@intermedia.com.au
Printed by Hero Print Alexandria, NSW, 2015
Mailed by D&D Mailing Services Wetherill Park, NSW, 2164
Australia’s largest printer has confirmed major retailers including Coles, Bunnings, and Harvey Norman have returned to printing catalogues as well as distributing catalogues to letterboxes.
The billion-dollar ASX-listed IVE Group said it has seen major retailers including Harvey Norman and Bunnings recommence catalogue printing, while Coles has recommenced printing and distributing catalogues to letterboxes.
While delivering half-year results to analysts, IVE Group managing director Matt Aitken told shareholders about a research project his business has completed in relation to catalogues.
“This research has continued to drive strong engagement with retailers such as Bunnings and Harvey Norman coming back into the catalogue channel during the half, but most importantly Coles has returned to the letterbox channel for catalogues late in the half,” he said.
Aitken confirmed that while Coles has continued to print catalogues in-store for
Textile and fabric printer Mereton Textiles has relocated to a new facility in Penrith, western Sydney, ahead of its plans to further enhance its sustainability efforts.
“We were looking for a one-level facility that had a better workflow, larger floorspace, and more usable space,” Joe Aliano, managing director of Mereton Textiles, told ProPrint.
“Our previous factory, which was in Lambridge Place, was about 570sqm; however, there was about 100sqm of unusable space. Our new facility is 470sqm, with around 450sqm of usable space.”
Founded in 2004, family-owned and operated Mereton Textiles specialises in custom printing on natural fibre fabrics, polyesters, vinyl, and wallpapers.
The company’s services include sublimation printing for soft furnishings, residential and commercial applications, fashion, and swimwear, as well as natural fabric printing including linen, cotton, printed vinyls, laser fabric cutting artwork services, and more recently, direct to film printing, with Mereton Textiles launching its
some time, over recent months, the company has expanded its catalogue printing outside of the store to include printing and distribution for letterboxes.
“It shows to me the quality of the consumer research that we did to prove up the value of the catalogue as part of a retailer’s marketing mix and in some the additional work we are doing in that space to show how catalogues deliver in-store,” Aitken said.
“We have done a lot of qualitative and
quantitative research and have a lot of data available to us to prove the value of catalogues. It has been well received by retailers, and we have seen retailers –specifically Harvey Norman, Coles, and Bunnings entering back into that channel having been out of it for some time – really since COVID – and it would appear to be working well for them at this stage.
“We are continuing to have great conversations with retailers about the power of catalogues.”
DTF transfer product, Press & Peel, last year.
Over the past 12 months, Mereton Textiles has expanded its capacity, adding four new machines to its operations including an Oric Printer Machine (for sublimation), a DTF printer, an Epson R5000 printer, and a Monti Heat Press machine. The company is also preparing to install another machine later this year.
“Our sublimating printing will always be a staple product of our offering, but the
future for us is in natural fabrics as we continue to focus on being as sustainable as possible,” Aliano said.
“We’re continually upgrading our equipment, and we’re currently in the process of finalising a deal for a new machine that will further enhance our sustainability efforts. It’s a significant investment but we’re excited to early adopters of this new concept so watch this space.”
HP Industrial Print has awarded Currie Group the APJ HP Industrial Print Marketing Excellence Award, celebrating the company’s outstanding contributions to marketing innovation and its role in elevating the print industry across Australia and New Zealand.
The prestigious accolade highlights Currie Group’s partnership with HP, which has successfully driven awareness and consideration of HP Industrial Print technology in the region.
According to HP, through strategic initiatives and collaborative efforts, Currie Group has set new benchmarks for impactful, integrated marketing in the print industry.
DG Dimense, a Roland DG joint venture company and manufacturer of the Dimense large format three-dimensional embossing technology, has appointed Celmac Australia as a specialist national reseller for its textured printing solutions in the Australian market.
Celmac Australia managing director Wayne McIntyre said, “We are thrilled to be on board and working with DG Dimense as we get started on this new journey into textured printing solutions.
“We have wide industry experience in the sign and décor print market here in Australia and are looking forward to bringing this complementary and expansive solution to our customers and the market in general.
“We know the range of solutions that are available today and recognise that with the Dimense technology, general print service providers and specialist printers can all gain an advantage and expand their product offerings to their respective client bases. This includes adding an extra dimension to key premium sign and display applications.
“Our team here at Celmac is looking forward to receiving initial stocks and advanced training on the product over the next few weeks, to get ready to start
Rob Mesaros, CEO of Currie Group, said the award reflects Currie Group’s dedication to empowering businesses with transformative marketing strategies and solutions.
“Our partnership with HP has been a key driver in showcasing the immense potential of print technology, and this recognition inspires us to continue leading
the way in delivering value to the industry,” Mesaros said.
Matt Tangey, marketing manager at Currie Group, said the recognition from HP highlights the power of collaboration and shared vision.
“It represents our focus on engaging the market with meaningful initiatives that showcase how print technology can transform businesses. I’m proud to work alongside a team and partners who are committed to helping our customers succeed,” Tangey said.
Arnon Goldman, general manager, Asia Pacific at HP said, “Currie Group has set the standard for marketing excellence in the print industry through strategic collaboration, innovation, and an unwavering commitment to driving awareness of HP Industrial Print technology. Their always-on media presence, dynamic industry partnerships, and impactful event activations, especially around Drupa have not only elevated HP’s market presence but also redefined engagement in the sector. Currie Group’s ability to blend creativity with strategy makes them a true leader in marketing innovation.”
talking to our customers and demonstrate the new range of solutions through our Australian network of offices.”
Roland DG Corporation and vicepresident of DG Dimense Kevin Shigenoya said the team is excited to be working with Celmac Australia to help expand its solution into the Australian market.
“We are confident that Wayne McIntyre and the team have the drive and experience along with the support and service infrastructure to represent and grow the wide range of applications that our technology can produce to provide additional value to print service providers and specialist integrators alike,” he said.
The Dimense solution consists of the Dimensor S inkjet printer combined with special media that has the property of foaming when heated, a structured ink to control foaming, and CMYK water-based ink that is safe for use indoors. After
printing, the media is heated by the printer’s on-board heater, which causes areas not coated with structure ink to foam up to 1.5mm thick, creating a textured design.
Dimense also has an exclusive line of PVC-free media, with finishes including matte, suede, metallic silver, metallic gold, pearlescent, and chameleon, enabling the production of a wide variety of interior decorations, including wallpaper, as well as point-of-purchase materials.
Celmac NSW state manager Jonny Rumney said, “We are proud to be a sponsor for PacPrint 2025 and we are particularly looking forward to being able to introduce Dimense at the exhibition along with our range of other new technologies at the event. Our team will be on hand to talk to everyone and explain how Dimense can benefit their business and where Celmac can support them.”
Easy Signs USA has been named a Lehigh Valley Top Workplace in 2025.
The Lehigh Valley Top Workplaces is an annual survey, conducted in partnership with media outlet The Morning Call and Pennsylvania-based employee research and consulting firm, Energage.
For the 2025 winners list, 1130 organisations were asked to survey their employees, and based on the survey feedback, 32 earned recognition as Lehigh Valley Top Workplaces.
The survey questions cover areas such as work environment and culture, values, compensation, innovation, and leadership. Companies that are recognised have received outstanding feedback in all areas and exceeded national averages.
To qualify for the recognition, employers must have at least 35 workers in the region. Survey results are valid only if 35 per cent or more employees respond, employers with fewer than 85 employees have a higher response threshold, requiring responses from at least 30 employees.
The winners are organised by category: large (more than 500 employees in the Lehigh Valley region), mid-size (125 to 499 employees in the Lehigh Valley region) and
Grand Print Services managing director
James Sultana recently visited Vanguard’s new showroom in Las Vegas, saying it provided him with an opportunity to see the company’s breadth of solutions and the print quality of their applications.
The new 2300sqm showroom and demonstration facility has been opened in conjunction with Vanguard’s customer Chroma Imaging – a long-time supporter and user of the brand.
The demo centre features a VRK3200-HS roll-to-toll printer, a VKH900-HS hybrid printer and a VK300D-HS flatbed printer.
“The demo facility was well presented, in a clean environment. David and his staff at Chroma Imaging were very welcoming and were able to demo live jobs. I always prefer to see proper production jobs and not sampling to get a gauge for actual performance on jobs,” Sultana told ProPrint.
“It was great to be able to see multiple machines from the Vanguard large format
small (less than 124 employees in the Lehigh Valley region.
Easy Signs USA, which is led by COO Steph Wilbow, placed eighth in the small category. The company also received the Communication Award.
“The Communication Award recognised Easy Signs as a ‘Top Workplace for Communication’ across the board, not just in our category,” Wilbow told ProPrint. “This relates directly to how leadership communicates with the team. Things like open communication, giving/receiving feedback and being notified of changes are areas that Easy Signs excelled at.”
Easy Signs director Andy Fryer said the much-deserved recognition follows a “monumental sales milestone” for the US-based team.
range. I didn’t realise there was such variety of print platforms in the Vanguard range to cater for differing needs. I saw a traditional flatbed, hybrid, and roll-to-roll machine.
“We saw one machine running and inspected the other two machines. They look well-built and look like they can
“After a year of relentless challenges, we are incredibly proud of how Steph and her management team have fostered and sustained such a strong team culture, this award is well deserved,” Fryer said.
“Last month marked a monumental sales milestone for Easy Signs USA, one that took 11 years to achieve in Australia. The team achieved this while continuing to deliver the exceptional quality, service, and speed our customers have come to expect. This success is yet another testament to their dedication and we are excited to see what they can achieve in the remainder of 2025.”
Easy Signs first opened its US operations with a $US2.8 million investment for a 6700sqm in March 2022, and was recently featured on the front page of The New York Times.
handle the volumes of a busy print shop.
“Print quality of the machines looked good, and print speeds were suitable for the price point of the machine. They also look like easy machines to run and maintain.”
The VRK3200-HS roll-to-toll printer is a 3.2m true roll-to-roll UV-LED printer capable of producing almost 280 square metres per hour utilising a two-channel print head design that supports two colours at a time. The small four, eight and 12 picoliter drop size ensures tight dot placement for a vividly printed output on substrates up to 1-inch thick.
The VKH900-HS hybrid printer is a hybrid UV LED printer that combines the capabilities of the award winning VK300D-HS flatbed printer and the VKR3200-HS roll-to-roll printer. Maximising the key features of each platform, this printer has a versatile print zone of 2.5m.
The VK300D-HS flatbed printer is built on the six-time award winning VK300D series. The five-inch by 10-inch machine is a UV-LED true flatbed with a high-speed electromagnetic drive system that propels the carriage at speeds up to 1.8m per second, or 60 boards per hour.
Ball & Doggett appoints Matthew Murphy as sales manager (Victoria) – sign, display, and digital
Ball & Doggett has appointed Matthew Murphy as sales manager (Victoria) – sign, display, and digital.
In this role, Murphy will focus on strengthening partnerships, driving business development, and expanding Ball & Doggett’s presence in the sign and display market across Victoria and Tasmania.
With extensive experience in the industry, Murphy joined Ball & Doggett through the acquisition of Conect Enterprise in 2022 and has since played a key role in fostering customer relationships and delivering sales growth.
“I’m excited to step into this role and further strengthen our presence in the
sign and display market,” Murphy said.
“I look forward to working closely with our team and customers to provide innovative solutions and continue delivering exceptional value.”
Murphy will lead the sign, display, and digital sales team in Victoria and Tasmania, working collaboratively with key stakeholders to enhance Ball &
Doggett’s position in the market.
“Matt’s leadership and vision will be instrumental in driving our growth in the sign and display sector,” Rob Brussolo, general manager sign, display, and digital at Ball & Doggett, said.
“His proven track record of success and strong customer focus make him the ideal choice for this role.”
Fujifilm BI rebrands sub-brands, streamlines business for transformation
Fujifilm Business Innovation (BI) Australia (formerly Fuji Xerox Australia) has rebranded its sub-brands Fujifilm CodeBlue Australia and Fujifilm Upstream Solutions as Fujifilm IT Services and Fujifilm Process Automation respectively, in line with its streamlined and client-centric focus.
This move comes as the company has been charting a “bold new course with a strategic transformation designed to meet the evolving needs of modern businesses”.
Recognising the increasing complexity of the digital landscape, the company has repositioned itself to deliver a comprehensive suite of integrated business services that extend beyond its traditional legacy in document solutions, graphics, and printing.
The company confirmed that its stronger focus on IT services does not mean it is exiting print and graphics but strengthening its other capabilities to support the increasingly complex digital transformation requirements of customers across Australia.
This strategic transformation is also
followed by a history of key acquisitions, including Upstream Solutions (2010), CodeBlue Australia (2020), and the global acquisition of MicroChannel (2023).
The company said these acquisitions have collectively strengthened its digital capabilities and the integration of these assets has reinforced deeper collaboration across all Fujifilm Group entities in Australia, including Fujifilm Australia, Fujifilm MicroChannel, and Fujifilm Data Management Solutions.
Fujiifilm BI Australia chief customer officer Stephen Sims said this strategic shift not only redefines the company’s role in digital transformation but also seeks to ensure that clients receive an end-to-end solution designed with the view to futureproof their operations.
“In Australia, Fujifilm BI Australia is leading a global movement. Our evolution
is not just a rebrand – it’s a commitment to helping our clients simplify, integrate, and future-proof their operations. We endeavour to enable businesses to work smarter, faster, and more seamlessly than ever before,” Sims said.
Fujifilm BI managing director Yasuyuki Matsumoto added, “This marks a new era for Fujifilm BI Australia. By combining our consulting expertise, technology, and managed services, we aim to provide an integrated approach to digital transformation. Our clients demand a trusted partner to navigate complex challenges, and we believe we are uniquely positioned to deliver real impact”.
The company also recently announced the local Fujifilm Graphics Systems (FFAU), and Fujifilm BI Australia sales teams will soon merge, creating a single, go-tomarket sales team.
Experience One Fujifilm at PacPrint 2025, stand B62. The one decision that makes the rest easy.
Put a smile on your face when you discover a world of possibilities. Meet the new mid-range 5-colour production presses, the Revoria Press™ EC2100S and Revoria Press™ SC285S. Compact and powerful presses designed for quality, efficiency, and versatility. From analogue to the latest digital presses, mono and colour print engines, and integrated workflows – we have it all. Join us and take your business to the next level with One Fujifilm. Because when print is simple and successful, everyone smiles. It’s worth the visit.
Matching its business philosophy, ‘we can produce anything you can dream of’, Sydneybased printing company, Carbon8 has invested in a new Fujifilm Revoria PC1120.
Multi-award-winning Sydney-based printing company, Carbon8, has a reputation in the market for working with high end clients to deliver premium printing products.
Known as a committed advocate of HP Indigo, it came as a surprise that the business recently decided to invest in a Fujifilm Revoria PC1120.
Carbon8 co-owner Peter Musarra first viewed the Revoria at drupa in 2024, but it was not until later in the year that the business case became obvious.
“Leading into Christmas, the volume of work coming into Carbon8 led to multiple shifts of overtime on the Indigo platform,” Musarra told ProPrint
“A large portion of the work on the Indigo really should not have been run at that cost and we realised it was time we needed to add a different engine to the stable.
“Of course, one solution was to invest in another version of the same engine that we already had in our business, but after examining our needs and the available machines in the market, we decided to look at a completely different engine that provided us with some diversification.
“Not only was the Revoria a cost-effective option, but it also provided additional financial benefits and efficiencies within our business.The Revoria has allowed us to offer a broader range of services, and most importantly, a more cost competitive offering One of the first things the Revoria helped us achieve was the reduction in overtime, as we no longer needed to run our two sheet-fed Indigos late into the night.
“Suddenly, we were able to create more output under the same roof, in the same shift. Some of our staff were the strongest supporters for the Revoria as they could see that this would improve the profitability, viability and sustainability of our entire business.”
Carbon8 co-owner Kenneth BeckPedersen provided a specific case study to explain the benefits of the new Revoria machine.
“Not only was the Revoria a costeffective option, but it also provided additional financial benefits and efficiencies within our business. The Revoria has allowed us to offer a broader range of services, and most importantly, a more cost competitive offering.”
“There is one catalogue job we have every six weeks that would take 14 or 15 hours on the A3 Indigo machine. This is now on the Revoria and takes 12 hours. It is a simple job on coated stock that is suited to the Revoria, and the client is just as happy with the results.
“This same client was pressuring us to do the work at a better price, and the beauty of having the Revoria is we have delivered a seven per cent reduction in the cost of
the job for the client even though our overall profitability for the job increased. As a result, we have renewed this contract for a further two years and the client loves the results from the Revoria,” BeckPedersen said.
“Our business can change from week to week. Sometimes we are printing business cards, the next week it could be menus for a chicken shop, or suddenly a bunch of black and white novels. The best thing about the Revoria is that it can handle all of this work, as well as multi-page brochures. It works with textured paper and can also print envelopes. The quality and consistency is exactly what we require for this diverse range of regular work that we are no longer outsourcing or pricing too high.
“There is a segment of our work where the Revoria technology is probably better than the Indigo for our business. Running certain jobs on the Indigo is like delivering a pizza in a Maserati. The Revoria is also far less demanding from an operator perspective so we can have the two Indigos and the Revoria running without an additional full-time operator,” BeckPedersen said.
Musarra estimates up to 30 per cent of Carbon8’s existing work could eventually be transferred to the Revoria, but the new machine has also provided the business with access to more opportunities.
“At Carbon8, we are not about delivering the cheapest product, but there is plenty of work and market credibility that is being lost by printers at the moment that let people down. There is a substantial volume of work out there that has become available from companies either going out of business or those that don’t have the
dedication to deliver on time and making it beautiful – no matter how simple the job may be,” Musarra said.
“Our business model always is and always will be high margin work to the high-end of town, but we realised we were missing out on work at a lower price point that we either outsourced or turned away. We are now able to provide a much broader range of products that are much more costeffective for our customer base. If clients come to us and say they have budget constraints, we can now say we have options to save them money and we can also provide a wider catchment of clients with a broader set of services.
“The Revoria matched our business philosophy, which is ‘we can produce anything you can dream of’ – and like most printing businesses we don’t like saying no to our clients. With the Revoria we now have access to additional applications including speciality inks that also feeds back into our super premium reputation and our ability to deliver that ‘magic’ to the top end of town.”
“The Revoria matched our business philosophy, which is ‘we can produce anything you can dream of’ – and like most printing businesses we don’t like saying no to our clients. With the Revoria we now have access to additional applications including speciality inks that also feeds back into our super premium reputation and our ability to deliver that ‘magic’ to the top end of town.
“While the Revoria is less complicated, it is still able to deliver several creative advantages over the Indigo that we have been able to use such as white, silver,
clear, and vibrant pink as well as the ability to print a long sheet. This versatility is the reason why this machine won out against its competitors in the same category. We needed one product that could hit 100 per cent of this regular work, and as an entire package it was the best machine in the market compared to competitors and was at a price that worked for our business, and we may end up with a couple more Revorias in the future,” Musarra said.
“I still believe the HP Indigo is the quintessential premium digital reproduction engine in the market, but uptime remains an issue. The uptime of the Indigo does not compare to the less complicated Revoria engine that continues to get the work done and when there has been a service issue, it has always been resolved by Fujifilm in a few hours, never days.
“The Fujifilm team involved in educating our team on the machine were very thorough and throughout the entire sales process we felt as though it was a genuine collaboration rather than just a hard sales pitch as our needs were considered at all times.
“We knew that Fujifilm wanted to make this machine work for us and this genuine collaboration has been very refreshing and it is a good start for the longevity of our relationship. We have been sold machines in the past where we were the favourite for only a short amount of time, but the Fujifilm service and customer relationship has been second to none and we feel as though we are in this together.”
Ryan Julleza, NSW account manager, Fujifilm Graphic Systems, said, “We’re privileged to showcase the capabilities of our Revoria PC1120 to Kenneth and Peter, gaining insight into their needs and demonstrating the value it can bring to their operations through the high-quality prints it produces using special colours such as white, pink, gold, and silver. We’re glad to have brought smiles to Carbon8.”
Roger Labrum, analogue sales and marketing manager, Fujifilm Graphic Systems, said, “With the installation of the Revoria PC1120 at a top tier, high value and immensely innovative print house like Carbon8, we have created a partnership that will deliver substantial growth, resilience, and sustainability within their business.
“The Revoria PC1120 is the ideal product to complement existing digital technology within Carbon8 and provides additional value propositions and opportunities for business development. The Fujifilm team is looking forward to working closely with Carbon8 to support their expanding business and maximising the creativity of their clients’ projects and experiences.”
Imagination Graphics recently hosted its regular barbeque networking event for staff, customers, and suppliers at Marrickville in inner west Sydney.
For more than 25 years, Imagination Graphics’ regular barbeque has been a highly anticipated tradition on the print calendar.
Recently held at Imagination Graphics’ premises, the event was an opportunity for staff, customers, and suppliers to connect.
“We have been hosting these barbeques for more than 25 years. They are mainly for the staff, but I also invite suppliers and our end-customers to come along as well,” said Imagination Graphics owner, Emmanuel ‘Budgie’ Buhagiar.
Located in an industrial estate in the inner
west of Sydney, nestled between the most popular craft breweries in Sydney, Imagination Graphics offers digital printing, offset printing as well as graphic and web design services.
“At Imagination Graphics, we have built our business on friendships and relationships. We are an easy-going family-owned business and not a highpressure sales environment because we thrive on service,” Buhagiar said.
Utilising the flagship Konica Minolta KM-1, Imagination Graphics produces a wide range of print from annual reports, hardcover books, brochures, magazines,
posters as well as short-run work for many major businesses.
“In 2025, Imagination Graphics’ main priority will be streamlining the way we work and making the business more efficient. As always, we will continue to strive and offer our clients a better service and work more closely with them,” Buhagiar said.
“In addition, we will be looking at furthering our sustainability practices. Imagination has been doing its best to be as sustainable as possible, but we aim to look for new and better ways to improve our practices.”
One year on from launching as a local subsidiary, Zünd Australia welcomed customers, partners, and suppliers to the official grand opening of its purpose-built showroom.
Zünd Australia has officially opened its local headquarters in Melbourne, located at Unit 4, 136 Keys Road, Cheltenham.
To mark the occasion, Zünd Systemtechnik AG owner and CEO Oliver Zünd travelled to Australia for the first time to officiate the opening, describing the launch as a “truly remarkable milestone” in the company’s history.
Zünd Australia first started operations in March 2024 and moved into the new Cheltenham premises in September 2024. Since then, the business has been setting up its new purpose-built showroom with new Zünd machines and technology.
“Thank you all for joining us to celebrate this special occasion,” Zünd Australia managing director, Dale Hawkins, told attendees at the official opening.
“This month marks the first anniversary of Zünd Australia, so we are still fairly young. But Zünd itself has been around in Australia for much longer. In fact, we have customers that have had some of their machines for 20 years.
“In our first year, the Zünd Australia team – with the support of Zünd Switzerland –has already achieved so much. I want to thank the Australian team of William, Predrag, and Edwin. These guys truly are
the A team when it comes to digital cutting, and it has been an honour to work alongside such a talented group of people.
“I would also like to extend a heartfelt thank you to our Zünd customers. We have fantastic customers here and some big players that have multiple Zünd machines. You are our family, our friends, our partners, and our promoters and we are so grateful for your trust and your support.”
Hawkins also thanked Oliver Zünd.
“It’s no small feat to start a business 16,000 kilometres away and we’re so grateful to have your confidence as we continue to service Zünd customers and grow Zünd Australia,” Hawkins said.
Oliver Zünd said the launch of Zünd Australia is more than just an expansion, but a commitment to supporting Australian businesses and the future of smart manufacturing.
“I would like to extend my deepest gratitude to Dale, William, Predrag, and Edwin for their dedication and hard work in bringing Zünd Australia to life. Your contributions have been invaluable. I also want to express my sincere appreciation to our customers. Your trust, support, and belief in us were instrumental in making this vision a reality,” he said.
“For three decades, Zünd has been at the forefront of cutting-edge digital cutting technology, redefining efficiency, precision, and automation across industries such as graphics, packaging, textiles, and manufacturing. We are incredibly proud of the impact our technology has had on businesses worldwide and today marks a significant step in bringing the same expertise closer to the Australian market.
“But the launch of Zünd Australia is more than just an expansion. It is a commitment – a commitment to local businesses, to Australian industries, and to the future of smart manufacturing. We are here to empower businesses with state-of-the-art solutions, delivering not just world class products but also personalised service, localise support, and industry leading expertise.
“At Zünd, sustainability is at the heart of everything we do. Our technology is designed to optimise material usage, reduce waste, and maximise efficiency helping businesses operate with both economic and environmental responsibility.
“As we establish our footprint in Australia, we remain committed to driving process that is both innovative and sustainability. Today, is the beginning of an exciting journey and with the strength of our local team and the trust of our valued customers, we look forward to shaping the future of digital cutting technology in Australia.”
The 150sqm showroom features two fully operational cutting systems: a G3 L-2500 1800 x 2500 model and an S3 M-1200 model with an extension table. It is also available for customers to experience in-house demonstrations and user training. The building includes the offices for Zünd Australia.
The event featured live demonstrations of the G3 L-2500 and S3 M-1200 – showcasing the multitude of applications, tools, and consumables available for the machines.
The event concluded with a celebratory after-party at the nearby 2 Brothers Brewery, where customers, partners, and the Zünd team gathered for networking and informal discussions.
Following a transformative year in 2024 installing the first DigiTech printer in Australia, 2025 is shaping up to be even bigger for SS Signs, with the launch of its revamped website and online ordering system.
SS Signs has launched a new website and ordering system, allowing customers to design, customise, and purchase signage online.
SS Signs operations manager Luke Lambourne said the website upgrade was designed to streamline the ordering process for customers.
“By eliminating manual order processing, SS Signs has increased efficiency, reduced lead times, and improved workflow,” Lambourne told ProPrint
The revamped website also expands SS Signs’ product range to include statutory signage, custom stickers, beer boxes, LED neon signs, and more.
“With our new website and ordering system, customers can now instantly design, customise, and purchase signage online, eliminating back-and-forth emails and delays,” Lambourne said.
“We’ve also introduced client catalogues, allowing businesses to reorder their standard items effortlessly and have them produced within 24 hours. This upgrade streamlines the entire process, making ordering faster, easier, and more efficient than ever before. This launch marks a significant step forward in automation, convenience, and growth for SS Signs in 2025.”
Lambourne said the website is constantly evolving, with plans to release a new product every month.
“Right now, we’re producing braille signage to a high standard, and a full braille catalogue will soon be available on the website. Expect continuous improvements as we grow,” he added.
The launch follows SS Signs’ expansion to a state-of-the-art signage facility in Cleveland, Brisbane – increasing its footprint to more than 3500sqm. SS Signs plans to expand its footprint by another 1500sqm by the end of 2025 to further enhance its capabilities.
“The move was essential to support our growth and production demands, providing space for a 16m spray booth, a steel fabrication area with a 5-tonne overhead gantry crane, plastic fabrication, letter bending, three routers, steel folding, and water cutting,” Lambourne said.
“Our new facility includes a dedicated production space, capacity to wrap up to 20 cars, cranes, or boats, a full warehouse, and room for eight graphic designers.”
The facility also houses the first DigiTech printer in Australia – the DigiTech TruFire LTX2, which is also paired with an Aristo 6m long cutter.
Designed and built in the US, the flatbed UV printer, with its focus on innovative design, high precision and print quality, is a welcome addition to the Australian print market. With the TruFire LT/X2 model, the operator can change sheets of media in under 10 seconds with the standard autounloader. The printer is made for large print shops that require fast, efficient, all-day production.
According to Lambourne, the new additions have increased production efficiency by more than 20 per cent. Recently, the Digitech delivered 2500 corflute signs with one operator in one eight-hour shift. A few months after its installation, SS Signs hosted a successful open house in partnership with Celmac, at its Cleveland facility to showcase the DigiTech in action to the wider industry.
SS Signs also recently expanded its capabilities with key equipment purchases, including a guillotine that has the ability to cut up to 6mm steel, a bender for 6mm steel, and “one of the safest aluminium extrusion cutting saws available in Australia”.
The company also grew its vehicle and access equipment fleet, adding two scissor lifts, a cherry picker, a tilt truck with a 13-tonne capacity, and a 60-foot knuckle boom.
“Owning our access equipment has been a game-changer,” said Lambourne.
This year, the company has its sights also set on growing its footprint in Melbourne, where it currently operates roll over tables, the HP365, the HP R2000, laminators, Multicam cutter and router, and steel and aluminium fabrication capabilities.
“Growing our Melbourne operations is a key priority. While the region has seen some progress, we are implementing strategies to scale much more rapidly. This includes increasing our marketing efforts, expanding our client base, and focusing on building a stronger presence in Melbourne’s signage market,” Lambourne said.
“We plan to work with all our national partners out of Melbourne such as Sigma, Tesla and Snap Fitness. This will help save costs of travelling and freighting goods.”
This year, the signage company is looking to increase its fleet of machines in both Melbourne and Brisbane.
“For Melbourne, we’re looking at another DigiTech flatbed, which would make us the first company to own the first and second DigiTech flatbeds in Australia. It is an awesome machine – thanks Celmac! While in Queensland, we’re looking for a high-
speed hybrid machine for redundancy purpose to back up our dedicated machinery.
“We’re also always on the lookout for staff in production, graphic design, vehicle wrap and install – we need more people with the business expansion.”
A third-generation printer, Lambourne was last year named an Emerging 50 winner at the annual ProPrint Awards and is an advocate for engaging more young people in the print industry.
“As someone who’s grown up surrounded by the print industry, with both my father and grandfather being well-known figures, I’ve had the privilege of learning from some of the best in the business. At just 21, I’m proud to continue their legacy while carving my own path,” he said.
“What I love most about the print industry is seeing our work come to life. I love that no day is ever the same. There’s always something new to be learnt, or a new challenge to take on. I am very lucky to be the operations manager and that I am able to oversee the entire production process from graphic design, print, finishing, cutting, plastic fabrication, paint, and metal fabrication.
“It’s important that we continue to encourage fresh talent to the industry.
The young talent that we have in our business is amazing; I would nearly go to say it is the core of our business, and we want to continue to provide pathways for young people in print.”
With just a few weeks to go until PacPrint 2025, excitement is mounting as the premier trade event for the print, sign, and graphics industries prepares to open its doors.
Taking place at the Sydney Showground, Sydney Olympic Park, from 20-23 May, PacPrint 2025 will bring together industry leaders, innovators, and technology pioneers to showcase the latest advancements in wide-format printing, packaging, signage, workflow automation, and sustainability.
Leading brands including Roland DG, Epson, Spicers, Screen GP Australia,
Fujifilm, Mimaki, Mutoh, Konica Minolta, and HP will unveil cutting-edge solutions that are set to redefine efficiency, enhance creativity, and drive sustainability in print and graphic communications.
With a packed exhibition floor, live demonstrations, and an insightful industry forum, PacPrint 2025 is the must-attend event of the year for print professionals.
Exhibitor highlights
Roland DG: Pioneering print versatility
As a platinum sponsor of PacPrint 2025, Roland DG is taking innovation to the next level with a showcase dedicated to Direct-to-Film (DTF), Direct-to-Object (DTO), and advanced signage printing. Visitors will get an exclusive look at the TY-300 DTF Production Transfer Printer, a “breakthrough” in garment decoration technology, featuring an optional Shaker/Heater Unit for automated production with superior image quality and colour vibrancy.
The TrueVIS XP-640 64-inch eco-solvent inkjet printer, a newly launched highspeed, high-precision wide-format solution, will also be on display, demonstrating how businesses can increase productivity while achieving outstanding print quality. Alongside its renowned TrueVIS wide-format printers, Roland DG will also introduce groundbreaking DTO UV printers, allowing direct printing onto three-dimensional substrates, unlocking new creative possibilities for customisation.
Epson: The power of precision and sustainability
Epson is set to stay true to its bold “Come Alive with Epson” theme at Stand C48. A key highlight will be the SureColor S9160, an industry-leading eco-solvent signage printer boasting the widest colour gamut in Epson’s history. Designed for highimpact, durable prints, this solution is ideal for retail, promotional materials, and outdoor signage.
Beyond signage, Epson will also showcase its DTFilm solutions, alongside highdefinition photo, merchandise, and label printing technologies. Epson’s focus on sustainability will be front and centre, with demonstrations of waste-reducing ink systems, energy-efficient print technologies, and recyclable packaging innovations.
“Sustainability is a core focus for Epson globally,” said Priscilla Dickason, corporate marketing manager, Epson Australia.
“From our heat-free printing technology to our recyclable ink systems, we’re committed to helping businesses adopt environmentally responsible print solutions without compromising performance.”
Spicers: A new industry experience
– The Spicers Precinct
Spicers is set to transform the PacPrint 2025 experience with the launch of The Spicers Precinct, a multi-dimensional showcase of print, fine art, architectural products, and packaging innovations.
This immersive hub will include:
• The Pop-Up Gallery, featuring premium print substrates from Hahnemühle Photo & Fine Art, Bauhaus, and Chromalux.
• The 3M Architectural Showcase, highlighting innovative interior and exterior applications using Di-Noc and Glass Finishes.
• Live technology demonstrations, including:
• Mimaki UCJV330-160: A nextgeneration print-and-cut UV LED printer
• Roland DG TY-300 DTF Printer: A breakthrough DTF solution
• Neolt XY DTF Cutter: Advanced precision cutting technology
• RollsRoller 540/170 Signature Plus: A state-of-the-art flatbed applicator
In addition, Spicers will spotlight its Environs range, a collection of eco-friendly substrates and sustainable solutions for commercial print, labels, and packaging.
Screen GP Australia: A leader in digital print evolution
Screen GP Australia, a PacPrint exhibitor since the 1980s, is returning in 2025 with a focus on high-volume inkjet innovations for commercial print, labels, packaging, and pharmaceutical applications.
Visitors will get an up-close look at:
• Truepress Jet L350UV Series, a market-leading UV inkjet press known for exceptional label production quality
• Truepress PAC 520, a sustainable packaging solution designed for recyclable, paper-based wraps
• Truepress PAC 830F, a game-changing flexible packaging solution, producing short-run, full-colour pouches and bags with sustainable ink technology
• Truepress Jet 560HDX, a 560mm web inkjet press delivering offset-quality prints.
Visitors can also experience Screen’s EQUIOS workflow system, with live demonstrations of automated print management tools.
While wide-format printing is a major focus, PacPrint 2025 will also feature innovations in workflow automation, packaging, and sustainability.
• Accura MIS, CERM, M-Power Software, and Quote & Print Software will present advanced automation systems designed to reduce production costs and improve efficiency.
• Finance@work will provide tailored financing solutions, helping businesses invest in new technologies.
• Sustainability initiatives will take centre stage, with exhibitors showcasing biodegradable substrates, water-based inks, and energy-efficient printing technologies.
Alongside product showcases, PacPrint 2025 will feature an insightful seminar program covering:
• AI and automation in print
• Sustainable printing practices
• Hybrid print solutions
• The future of packaging and labels.
A highlight will be the Leaders in Trade panel, where industry experts will tackle supply chain challenges, emerging market opportunities, and the future of print technology.
• Unparalleled access to innovation
– See the latest in print technology, digital automation, and sustainable solutions
• Live demonstrations – Experience cutting-edge printing, finishing, and workflow solutions in action
• Networking opportunities – Connect with industry leaders, experts, and potential business partners
• Exclusive product launches
– Be among the first to discover groundbreaking technologies shaping the industry’s future.
PacPrint 2025 runs from 20-23 May at the Sydney Showground, Sydney Olympic Park. Be part of the industry’s most anticipated event and stay ahead in a rapidly evolving market.
Register today and take a front-row seat to the innovations shaping the future of print. For more information about exhibiting at PacPrint 2025, contact the events team at exhibitions@visualconnections.org.au or call +61 2 9868 1577. For the latest updates, visit www.pacprint.com.au. Event information was correct at the time of publication.
Epson will make a bold statement at PacPrint 2025 with its vibrant ‘Come Alive with Epson’ theme, inviting visitors to experience the power of colour, precision, and sustainability firsthand.
Located at stand C48, Epson’s showcase will feature cutting-edge printing technology, including the brand-new SureColor S9160, its industry-leading signage printer with the broadest colour gamut ever seen in an Epson eco-solvent model and the very latest DTFilm solutions.
“The SureColor S9160 is a game-changer for the signage and display market,” said Priscilla Dickason, corporate marketing manager, Epson Australia.
“It delivers unparalleled colour accuracy and vibrancy, making it the ideal choice for businesses looking to produce highimpact, durable prints.”
The SureColor S9160 aims to deliver exceptional image quality, an expanded colour gamut, productivity and a compact, user-friendly design.
It is equipped with Epson’s latest user-replaceable 2.64-inch PrecisionCore MicroTFP printhead, and features an integrated temperature sensor, nozzle verification technology and nozzle replacement.
These advancements ensure reliable image quality and consistent colour output while significantly boosting productivity.
The SureColor S9160 utilises an advanced 11-colour ink set, including red, orange and an all-new green, as well as opaque white ink, which can be used on clear or dark substrates to add versatility and enhance colour.
This expanded ink set delivers a broad colour gamut and enables vibrant and accurate prints on a variety of media types, including vinyl, canvas, film, wallpaper and other roll media up to 1626mm.
In addition to the SureColor S9160, visitors to the Epson stand will witness the latest innovations spanning photo, signage, merchandise, and label printing.
Whether it’s high-definition photographic reproductions, eye-catching promotional materials or durable, customised labels, Epson will demonstrate a suite of solutions that offer unmatched versatility at the show.
“We will demonstrate the true possibilities of Epson technology, how we have a solution for every requirement and how from retail displays to commercial signage, our products empower businesses to create stunning visuals that add value, captivate audiences and drive engagement,” Dickason said.
Alongside dazzling colours and highquality prints, sustainability is a core focus for Epson at PacPrint 2025. The company will demonstrate how it continues its commitment in this space with advancements in waste reduction, eco-friendly packaging, and energyefficient print solutions.
Epson products leverage innovative ink systems, energy efficiency and sustainability certifications to align with the company’s commitment to reducing environmental impact in the ICT sector.
“Sustainability is a global Epson initiative. It’s something we take very seriously. As a result, we are constantly innovating to reduce environmental impact, whether through our heat-free printing technology, recyclable ink systems or our commitment to responsible sourcing,” said Dickason.
Epson’s eco-conscious product lineup is designed to help businesses minimise waste and energy consumption while maintaining the best possible print quality.
With that in mind attendees at PacPrint25 will have the opportunity to explore how Epson’s technology aligns and complements with the growing demand for environmentally responsible printing solutions.
With thousands of visitors expected at PacPrint 2025, the Epson stand is always one of the highlights and a must-visit for anyone looking to explore the future of print technology.
“Epson solutions at the show will demonstrate game-changing colour capabilities, high-performance printing and sustainable innovations,” Dickason said.
“PacPrint is always an excellent platform for us to engage with print professionals, demonstrate our latest innovations, and showcase how Epson is helping and adding value to the industry. We are looking forward to welcoming visitors to our stand and showing them how their print requirements can truly ‘Come Alive with Epson’.”
Visitors to PacPrint 2025 will discover how Fujifilm helps businesses optimise their print operations and applications with innovative products and tailored support.
Graphic communications functions of both FUJIFILM Business Innovation (BI) Australia and FUJIFILM Australia are proud to unite as One Fujifilm, strengthening its position as one of the leading complete solutions partners in the commercial printing industry across Australia and New Zealand.
“Centralising this business means we can more effectively offer customers our entire portfolio of Graphic Communications products and services, maximising value and the experience,” said Yoshitaka Nakamura, senior general manager, graphic communications, and head of Oceania, FUJIFILM BI Australia.
This integration of the graphic communications functions marks an exciting new chapter, demonstrating Fujifilm’s complete solutions portfolio, spanning analogue plates and specialty inks to cutting-edge digital print technologies and advanced workflow software.
Visitors to PacPrint 2025 will discover how Fujifilm helps businesses optimise their print operations and applications with innovative products, and tailored support. Whether they’re seeking to enhance efficiency, expand capabilities, or deliver vibrant results, Fujifilm works closely with them, so they won’t need to look anywhere else.
colour channels. These can be populated with ink sets that best suit your application needs, including CMYK, white, clear and a jettable primer, seeking to ensure optimal adhesion to industrial media types.
Fujifilm’s latest addition to the processless portfolio, the Superia ZX, is its most advanced printing plate to date, with higher durability, robust scratchresistance, and better visibility.
The tradeshow is also a chance to see Fujifilm’s newly launched mid-range 5-colour production presses, the Revoria Press™ EC2100S and Revoria Press™ SC285S. Compact in size with the newly developed Vertical Toner Development Technology and Automated Print Inspection System, these are powerful presses designed for quality, efficiency, and versatility – a feature of the flagship award winning model, the Revoria Press™ PC1120.
The Acuity series supports high-quality large format printing across a variety of materials. Whether a user is producing banners, highimpact posters, or vibrant retail displays, they need a versatile and powerful solution that assists with delivering exceptional quality on a grand scale.
With its compact yet powerful design, the Acuity Prime Hybrid is ideal for industrial offices with limited space, while offering the flexibility to configure 4,5, 6, or 7
The Revoria Press™ PC1120 aims to set new standards in premium print effects, supporting the use of specialty toners such as white, gold, silver, clear and pink. It seeks to provide confidence in delivering stunning colour enhancements, precision finishing, and versatile applications to elevate every print.
“With its combination of image quality, productivity, and specialty colour printing, we believe the Revoria Press™ series has redefined what’s possible in production printing,” Nakamura said.
“Now, with the latest advancements, we are excited to see how these next-generation machines will further transform businesses in the region, helping with unlocking new levels of efficiency, creativity, and competitive edge.”
Managing multiple devices, whether offset or digital, may be complex and time-consuming. That’s where Fujifilm’s proprietary, fully integrated workflow solution comes in – bringing all print operations into an integrated, connected environment.
Automate job management with the Revoria XMF™ PressReady and XMF Workflow. With this functionality, users can easily centralise printer and job management through a single platform to help achieve greater efficiency and control.
Fujifilm believes high-quality printing starts with high-quality chemistry. That’s why Fujifilm manufactures press chemicals right here in Australia, tailored to the Australasian market and sold directly to consumers nationwide.
From fountain solutions and UV coatings to ink testing, colour matching and blanket supply, its Melbourne-based factory provides a full suite of solutions to both analogue and digital platforms.
With bespoke chemistries available for specific projects or equipment, Fujifilm’s expert team seeks to ensure customers’ needs are met with precision and speed.
Join Fujifilm as it redefines commercial printing and explore the various possibilities of its complete analogue-to digital solutions. Together, Fujifilm is delivering not just exceptional technology but also delivering on its group purpose –giving our world more smiles – for users and their customers
Experience One Fujifilm at PacPrint 2025, Stand B62.
Experience One Fujifilm at PacPrint 2025, stand B62. The one decision that makes the rest easy.
Put a smile on your face when you discover a world of possibilities. Meet our expert team and explore cutting-edge technologies designed to make print smarter and more profitable. From analogue to the latest digital presses, mono and colour print engines, and integrated workflows – we have it all. Join us and take your business to the next level with One Fujifilm. Because when print is simple and successful, everyone smiles. It’s worth the visit.
experience the future of print firsthand.”
and tap into the growing demand for high-quality, custom labels.
workflow automation, our team is ready to help you unlock new possibilities.”
PacPrint 2025 will mark the first time the swissQprint Generation 5 Nyala is on show in Australia, with visitors set to see why the machine continues to set the industry benchmark.
At PacPrint 2025, Pozitive will showcase some of its latest advancements in print and finishing technology, bringing together high-end printing, precision cutting, and workflow automation in a fully integrated production environment.
A key highlight will be the first-ever Australian appearance of the swissQprint Gen 5 Nyala, alongside Summa’s flatbed and roll cutting solutions. Pozitive will demonstrate workflow automation using PrintFactory and Caldera RIP software, showcasing how these technologies improve efficiency and precision.
Beyond equipment, Pozitive will be showcasing a range of consumables from Ritrama and B-Flex, covering everything from printable media to heat transfer vinyl, making its stand a must-visit for businesses in signage, packaging, and commercial print.
swissQprint Nyala 5 – Australian debut
As one of the most advanced UV flatbed printers on the market, the latest Nyala model delivers exceptional print quality, speed, and versatility.
Designed for high-end signage, packaging, and specialty graphics, the Nyala is known for its precision printing quality, high productivity, and exceptional energy efficiency. It has also been Europe’s best-selling flatbed printer in its class for 10 consecutive years, reinforcing its reputation as a trusted solution for professionals worldwide.
Further highlighting its build quality and longevity, the Nyala comes with a 36-month manufacturer’s warranty, a testament to swissQprint’s confidence in its engineering and long-term reliability. With swissQprint’s reputation for precision and durability, visitors to PacPrint will have the opportunity to see firsthand why the Nyala continues to set the industry benchmark.
Pozitive will run live demonstrations of a complete print and finishing workflow, showing how each machine integrates for seamless production.
Visitors can see:
• swissQprint Gen 5 Nyala – Highquality UV flatbed printing for signage, packaging, and specialty applications.
• Summa F Series F1612 – A flatbed cutter designed for precise finishing of rigid boards and roll stock, including cutting, routing, and creasing.
• Summa S One and S3 Vinyl Cutters – High-speed roll stock cutting, ideal for contour-cut graphics and printand-cut applications.
• PrintFactory and Caldera RIP Software – RIP software that ties everything together, reducing manual handling and improving accuracy with advanced automation functions.
By combining high-end printing with precise cutting and smart automation, Pozitive’s demonstration will offer a practical look at how businesses can speed up production while maintaining exceptional quality.
In addition to showcasing the latest equipment, Pozitive will showcase premium Ritrama and B-Flex consumables for signage, textiles, and specialty applications.
• Ritrama Printable Media and Specialty Films – A comprehensive range of monomeric, polymeric, and cast printable media, designed for vibrant, high-quality prints across various applications. The lineup also includes floor graphics, wallpaper, and window etch films, providing durable and versatile solutions for signage, interior decor, and promotional displays.
• Ritrama Platinum Series – A highperformance collection of coloured sign vinyl, offering long-lasting durability and strong adhesion, making it ideal for vehicle graphics, retail signage, and outdoor branding.
• B-Flex Heat Transfer Vinyl (HTV) –Covering CAD-Cut coloured HTV, Printable HTV, and Direct-to-Film (DTF) solutions, B-Flex delivers highquality heat transfer materials for apparel, uniforms, and promotional textiles. Known for its easy weeding, strong adhesion, and vibrant colours, B-Flex ensures professional-grade results on a wide range of fabrics.
Show specials and networking opportunities
PacPrint visitors can also take advantage of exclusive show specials, with special pricing on select equipment and consumables.
In addition to connecting with Pozitive’s expert team, visitors will have the opportunity to engage with international guests, including Adriano Gut from swissQprint and Andrea Sottana from B-Flex Italia. Their presence will provide a unique chance to gain insights directly from the manufacturers, discuss industry trends, and explore the latest advancements in UV printing and heat transfer technology. The Pozitive stand offers a key networking hub for industry professionals to share insights and stay ahead of trends.
Visit the Pozitive at Stand C72 for live demos, expert discussions, and hands-on insights into print and finishing solutions.
Discover how printIQ can revolutionise your print business, streamline operations, and position you for success at PacPrint 2025.
In today’s competitive print landscape, printIQ stands as the market-leading management information system (MIS), delivering unparalleled visibility and efficiency across print workflows.
This modular, cloud-based solution encompasses everything from estimating and ordering to production and delivery, enabling print businesses to scale operations without costly workarounds.
Serving sectors including commercial print, wide and large format, labels, and packaging, printIQ measurably improves visibility, efficiency, communication, and profitability for print service providers of all sizes.
What truly sets printIQ apart is its comprehensive automation capabilities, powered by innovative technology and backed by dedicated developers and support staff based in Australia and New Zealand:
• Robust API capabilities enable seamless integration with existing systems and third-party solutions
• New SaaS offering for pre-press automation workflows with CYANFix as a partner, streamlining preproduction tasks
• IQ Link module enables automated outsourcing workflows between printIQ customers, creating a networked production ecosystem
• HP Siteflow module enhances production efficiency for digital print environments
These automation tools eliminate manual touchpoints throughout the production process, significantly reducing the risk of errors. By automating routine tasks, printIQ frees staff to focus on value-adding activities that drive business growth.
The system’s ability to integrate with existing workflows means print businesses can implement automation incrementally, targeting high-impact areas first before expanding to full workflow automation. This practical approach ensures minimal disruption while delivering immediate efficiency gains.
At printIQ’s core is its revolutionary simplified quoting functionality – a major market differentiator that transforms how print businesses operate. By moving production knowledge directly into the platform, printIQ democratises the quoting process, allowing anyone in the organisation to generate accurate quotes without extensive technical expertise.
This innovative approach removes traditional bottlenecks by reducing quoteto-production timelines from days to minutes, while maintaining consistent pricing across the business. The system’s intelligence ensures that every quote reflects accurate costings, appropriate margins, and optimal production methods.
printIQ’s automation capabilities reach new heights through its strategic partnership with Infigo’s web-to-print platform. This powerful integration creates a seamless end-to-end system that maximises automation across the entire print production process, from online ordering through to delivery.
Built on a shared philosophy of innovation and customer success, this partnership delivers a solution that not only solves today’s challenges but anticipates tomorrow’s opportunities. The integration enables:
• Live pricing with printIQ: Creating estimates through SKU-based mapping or custom quoting, providing flexibility for both standardised and bespoke print jobs
• Product synchronisation: Products created in printIQ are automatically added to Infigo storefronts, with support for multiple storefronts and hierarchical category mapping
• Real-time inventory updates: Stock levels from printIQ display in real-time on Infigo storefronts, ensuring customers always see accurate availability
• Bi-directional communication: Uploaded artwork is directly pushed into printIQ, automatically creating job folders with all necessary production information
• Advanced custom quoting: Generating bespoke quotes based on properties such as size, stock, colour, and pages without requiring pre-built products, supporting truly tailored solutions
Experience printIQ at PacPrint
Visit Stand A78 at PacPrint to experience firsthand how printIQ transforms print operations and drives profitability in today’s challenging market. The printIQ team is proud to sponsor Infigo’s presence at its stand, where our combined teams will showcase the power of printIQ’s MIS integrated with Infigo’s web-to-print solution.
The joint presentation showcases printIQ’s commitment to delivering the ultimate automation solution to the ANZ print market. printIQ’s Australian and New Zealand-based development and sales teams will be on-hand to discuss how printIQ can be tailored to your specific business requirements and production environment.
Don’t miss this opportunity to discover how printIQ can revolutionise your print business, streamline operations, and position you for success. With printIQ and our strategic partnerships, you’re not just investing in software, you’re securing the future of your print business through intelligent automation that drives efficiency, quality, and growth.
Attendees to the centrally located Screen GP Australia stand will see how it is changing the high-volume digital printing sector for commercial print, labels, packaging, pharmaceutical inserts, direct mail marketing, and much more.
Screen GP Australia, a loyal PacPrint exhibitor since the 1980s, will be showcasing Screen’s latest innovations at this year’s highly anticipated PacPrint in May.
Screen GP Australia managing director Peter Scott recently returned from Hunkeler Innovationdays in Switzerland, where Screen was a major exhibitor.
“Although we will not have equipment on the stand at PacPrint, we will be showing numerous examples and videos of how Screen is changing the high-volume digital printing sector for commercial print, books and magazines, labels, packaging, pharmaceutical inserts, direct mail marketing and more,” Scott said.
“Hunkeler Innovationdays was a real eyeopener for me and many visitors and clearly showed that the progress of inkjet as a major print process is unstoppable.”
The print samples to be presented at PacPrint 2025 will cover labels – where Screen, through its partner Jet Technologies, has a major foothold in Australia and New Zealand with the Truepress L350UV series – to other forms of packaging production such as the innovative Truepress PAC 520 – designed to produce recyclable, sustainable paperbased wraps and packs that replace micro-plastic producing hydrocarbonsourced plastics.
Although paper is re-emerging as a desirable, sustainable packaging medium, the need for certain plastics is still strong
in liquid and food packaging. With this in mind, Screen will have several samples of production from its Truepress PAC830F, a mighty 830mm web machine that is more than 21 metres long!
“Needless to say, having such a huge machine at a trade show is out of the question – even at drupa we exhibited just a unit of the PAC 830F. Nevertheless, interest here is strong and we will show some stunning examples at PacPrint; flexible pouches and bags in full colour, printed in short runs without using plates. Plus, the inks are water-based and sustainable,” Scott said.
On the commercial print side, book, brochure, and magazine work from the
Truepress Jet 560HDX will put to rest any doubts that inkjet can match offset quality.
“The 560HDX was a star at Hunkeler Innovationdays. Printing on standard offset paper media and finished on Hunkeler lines across a 560mm web, the colour and resolution is amazing, as any visitor to our stand at PacPrint will see. Of course, the advantage of printing high value digital is economy, with no plates and minimum wastage; versatility, the ability to run several jobs in one print run with no interruptions; versioning and personalisation – variable data managed through our EQUIOS workflow.”
Attracting equal attention was the Truepress Jet 520NX-AD (Advanced Drying) a 225 metres/min speed machine configured for both CMYK colour and Mono (K only) print, with the ability to ‘park’ the CMY printheads and save ink. Screen will have samples from this machine, including pharmaceutical multi-folded leaflets using finishing by partner company Ibis, UK. This feature extends to ‘lablets’ – labels that combine with a multi-page information pamphlet when unfolded.
“The Screen Stand E48, centrally located at PacPrint, will be a good place to stop, have a good coffee, chat about the trends that are changing our industry on the commercial print and packaging levels –and witness the real-world end results. There will also be working demonstrations of software and EQUIOS workflow and, for our CtP customers, updates on the latest 4pp, 8pp and VLF setters. I warmly welcome all visitors to call by.”
Redefine Commercial Printing Standards and elevate production with Next-Gen High-Speed Inkjet
PRODUCTIVITY
•High productivity
•560mm paper width
•High machine uptime
QUALITY
•New Inkjet 1200dpi PHs
•New saturated ink SC2
•Enhanced image quality
USABILITY
• Energy-efficient drying
•Easy operation
•Offset-coated papers
AGILITY
•Optimised integration
•Precision paper sensing
•Complete New Platform
At PacPrint 2025, Neschen will introduce two new, highly anticipated models: the CL 1650 SW and the PhotoLam 650.
Stick On Signs will soon showcase two new Neschen laminators at PacPrint 2025, bringing decades of laminating excellence to Australian print shops, photographers, and wide-format graphics producers.
The highly anticipated models are the CL 1650 SW and the PhotoLam 650.
The CL 1650 SW is a heat-assist laminator designed for mid-to-large print shops that require high-volume capabilities. It features an adjustable heat-assist top roller (up to 70°C), enabling better lamination quality, especially with sensitive or thicker materials.
This machine also offers roll-to-roll operation, pneumatic pressure control, and electrical nip adjustment for precise and efficient lamination. With a speed of up to 8m/min, it ensures maximum productivity without compromising on quality.
Additional features such as safety light bars, foot switches, and dual control panels, ensure the CL 1650 SW operates seamlessly, while swing-out shafts make loading and unloading more efficient, significantly reducing downtime.
The PhotoLam 650 is designed specifically with photographers in mind, particularly for those working with pressure-sensitive adhesive materials. This laminator offers high flexibility and performance tailored to the photo industry.
The PhotoLam 650 has a 650mm processing width, allowing for a variety of media to be laminated with ease. A maximum speed of 2 metres per minute, along with manual adjustments for pressure and speed, ensures optimum results for each job.
The 20mm nip opening accommodates a wide range of substrates, from thin papers to thicker materials. Its robust, free-standing design guarantees stability, making it a reliable choice for those looking to produce high-quality photo laminations. With the ability to laminate with protective films or double-sided adhesive mounting films in a single operation, the PhotoLam 650 streamlines
The new PhotoLam 650 is designed specifically with photographers in mind, particularly for those working with pressure-sensitive adhesive materials
production, increases profitability, and enhances the quality and durability of photographic work.
Crafted in Europe, Neschen laminators are designed and built to uphold the highest quality standards, ensuring long-term reliability and peak performance. The construction of each machine features a high-torsion stiffness chassis, along with precisely parallel rollers and shafts, ensuring accurate and consistent lamination results. This meticulous design also serves to extend the machine’s lifespan, reduce costly errors, and minimise material waste.
Each machine’s heavy-duty, 140mm diameter rollers play a key role in enhancing lamination precision. These large rollers ensure better pressure distribution across a wider surface area, allowing for even
lamination with minimal risk of issues such as creasing, twisting, or shrinking. This robust and precise engineering makes Neschen laminators the preferred choice for professionals across Australia.
Stick On Signs said it is excited to showcase the full Neschen laminator lineup at the upcoming tradeshow, offering solutions for every business need – from entry-level to high-volume production. Among the range is the affordable Ecolam 1650, a laminator designed for budget-conscious users, offering a perfect balance of quality and cost-efficiency.
The Hotlam 1650 DoubleH provides superior performance, versatility, and speed for high-demand, high-volume production environments.
Neschen’s extensive range demonstrates the company’s commitment to meet the needs of diverse applications, from smaller print shops to larger commercial operations.
As PacPrint 2025 approaches, Stick On Signs is excited to showcase the next generation of laminating technology from Neschen. With a strong commitment to innovation, precision engineering, and operator-focused design, Neschen continues to push the boundaries of laminating excellence.
“By visiting the Stick On Signs booth, you’ll get the opportunity to see the full range of Neschen laminators in action,” the company said.
“Whether you’re looking to upgrade your existing laminating processes or invest in your first machine, Stick On Signs is the perfect place to discover how Neschen solutions can transform your workflow. Don’t miss this opportunity to experience firsthand the future of professional laminating with Neschen – where performance, precision, and reliability come together.”
Zimmermann Industries has hit a major milestone in its production capabilities following the company’s recent purchase of a Mimaki JFX600-2513 UV LED flatbed inkjet printer.
Zimmermann Industries has boosted its capacity by 400 per cent following its purchase of a Mimaki JFX600-2513 UV LED flatbed inkjet printer.
Installed at Zimmermann Industries’ facility in Lilydale, Victoria, in December, the new addition to the production line marks a significant leap forward for the company, by enhancing its efficiency, output, and expansion into new markets.
“Since the installation, we’ve been flat out,” Steen Zimmermann, owner and director of Zimmermann Industries told ProPrint
“We’ve done more work in a month than what our previous printer did in a whole year.”
Founded by Steen Zimmermann in 2007, Zimmermann Industries is a leading turn-key fabricated and electronic signage supplier, and has worked with major retail brands including Reebok, Focus on Furniture, Lovisa, and Mecca.
The purchase of the JFX600-2513 continues Zimmermann’s longstanding relationship with Mimaki Australia, with the new machine replacing a second-hand Mimaki printer purchased two years ago. The new addition takes the total number of Mimaki machines owned by Zimmermann throughout its 18-year history to seven.
“We’ve only ever had Mimaki. We bought our previous machine to get into the
flatbed market and we got it second hand because, at the time, we didn’t have the work to warrant the investment of a brand-new machine,” Zimmermann said.
“I never thought we would go from a second-hand $40,000 machine to a brand new machine. I thought there would be a mid-point in there. But, after looking at the increasing volume of work our clients needed from us, we knew we needed more capacity. So, when we started the process of looking for a new machine, it just made sense to go with what we knew.
“We did look at other printers, but Mimaki came out on top in terms of speed, quality, and durability of ink. Not only that, the JFX600-2513 offered everything we needed. We felt that with some of the other machines, we would have to compromise on one feature to get another. The JFX600-2513’s speed is also unbelievable – it’s up to 16 times faster than our previous machine.
“There are only three JFX600-2513 machines in Australia and we’re the only one with this configuration in Australia. The Mimaki team flew us to their showroom in Sydney to see the machine, and we also visited a printer based in Albury who also has a JFX600-2513, where we did durability tests.
“Overall, it was about six months of due diligence by us before we bought it. It was a big leap to even buy the first one and
that was second-hand, so we wanted to be certain this was the right fit for us, and it has paid off.
“From start to finish, the Mimaki team have been great. It was a two-week set up. Once we got it off the truck, Mimaki did everything and trained up our team. Whenever we need support, they are there. There are cheaper and more expensive machines out there in the market, but I don’t think the others have the tech support that Mimaki has.”
The ability to print bespoke architectural decor with the JFX600-2513 has also significantly enhanced Zimmermann Industries’ presence in the decor market.
“We’ve been developing our texture printing for the past two years, and it’s an area that we’re really focused on. We’re now starting to do more surface printing such as display walls in retail and trade showrooms,” Zimmermann said.
“For example, instead of using wallpaper or tiles for a wall display of taps and fittings in a plumbing supplies store, we’re now replicating that with texture printing. So, the texture software of the JFX6002513 was another major drawcard for us. It allows us to offer a range of services to clients now, depending on what they need and their budget.
“We’re currently working with a retailer on the opening of their new flagship store. They are in a heritage building and tiles were damaged prior to them moving in. They can’t replace the new tiles in time for the launch, so we are printing replicas as an interim solution and then they will replace with custom made tiles after launch.
“The interest from brands once they realise what we can do with has skyrocketed. We get new jobs every week. It has opened a lot of other avenues for us that we couldn’t do before. It’s the same skillset by our team and the same capacity that we have; it’s just adding more value to what we can offer.”
Up to 70% more productive
PVC production at 18 m2/h with 2 head staggered array.
2.5D printing on Roll-to-Roll printer
RasterLink7’s 2.5D texture Maker feature can easily create 2.5D printing data.
2.5 times more nozzles and 4 pl droplets produce smoother skin tones and better saturation at high speed.
Clear ink expands design opportunities and produces more profitable output.
RasterLink7’s Ink Saving Function reduces ink consumption while maintaining colour balance.
Up to three media rolls can be mounted, and the media can be changed by simply turning the handle.
Print more with less maintenance
The cloth wiper, automatic adjustment (DAS), W motor winding, and V-shape cut make operations more efficient.
Check the printing operating status and ink usage at a glance.
From 6- 9 May 2025, at the Messe Berlin, Germany, FESPA Global Print Expo and its co-located events, European Sign Expo and Personalisation Experience, will become the stage for print professionals to discover a wealth of products and solutions in speciality print, signage, and personalisation.
FESPA Global Print Expo, European Sign Expo, and Personalisation
Experience is set to welcome more than 550 new and returning exhibitors from more than 36 countries, already surpassing exhibitor numbers from last year’s events.
Returning to Berlin for the first time in three years, visitors will have the opportunity to see the latest products and innovations from a rich line-up of international players in the speciality print space including the latest trends in sustainability, print on demand, and intelligent automation.
“This year’s events are set to be a pivotal platform in 2025 for our global community,” said Michael Ryan, head of FESPA Global Print Expo.
“Eight halls full of innovation await professionals from the speciality print market, where they can discover a plethora of on-demand technologies for
specialist print applications. With over 550 exhibitors, FESPA Global Print Expo and its co-located events will be the meeting point for visionaries in 2025.”
Agfa to feature new inkjet “power beasts”
Agfa is set to continue its innovation momentum at FESPA 2025, where it will unveil its latest high-performance inkjet printing solutions.
Over the past year, Agfa has significantly expanded and modernised its inkjet portfolio, introducing four new inkjet printing solutions: the hybrid Anapurna Ciervo H3200 and Jeti Bronco S printers, the roll-to-roll Jeti Condor, and the SpeedSet Orca inkjet press.
Additionally, Agfa has enhanced automation features, such as robotics and a new autoloader, for the Jeti Tauro hybrid printer and Onset Grizzly flatbed printer. These innovations have been widely
accepted by the market, demonstrating their alignment with industry demands.
“At Agfa, innovation moves faster than anywhere else in the inkjet printing realm,” said Arnaud Calleja, vice-president of digital printing solutions.
“In just over a year, we have nearly completely renewed our inkjet printing portfolio. Every solution is designed in close collaboration with our customers, addressing their challenges and opportunities.”
Agfa’s advancements are brought together under the ‘Powerful by Nature’ theme, reflecting the strength, versatility, and performance of its products. At FESPA, Agfa will unveil three new powerful additions to further help print service providers take on emerging challenges.
Agfa’s booth will also showcase inspiring print applications and highlight how its solutions cater to diverse markets while contributing to a more sustainable printing industry.
“Agfa empowers businesses to meet growing demands for sustainable prints while offering long-term reliability,” Calleja said.
Visit Agfa at FESPA Berlin (Hall 27, Booths D70 and D60) to explore the latest in inkjet printing innovation and sustainability.
Canon Production Printing to showcase ‘The Power to Move’
Canon Production Printing will be showcasing ‘The Power to Move’ – where bold, high-impact print creates emotional connections, delivers real business momentum, and transforms spaces into unforgettable brand experiences.
Under the theme ‘The Power to Move’, Canon Production Printing will demonstrate how its combination of technology innovations, expert teams, support services, and collaboration empowers print service providers (PSPs) to transform their businesses. Attendees will get insights into the industry’s trends and opportunities and be inspired by show-stopping applications and new technologies.
Visitors will experience the world-class portfolio of wide format print production technologies, and see how Canon works with expert software, finishing, and media partners to integrate these into solutions tailored to each customer’s needs.
Canon Production Printing will also showcase its market-defining wide format printers – from the Arizona flatbed range with FLXflow and the Colorado M-series roll-toroll printers with UVgel technology, coupled
with the Neolt Packaging Factory which can power through the most demanding workloads and challenging media. Canon is proudly distributed and serviced by Currie Group.
EFI is set to showcase the future of digital printing at the tradeshow, where visitors to Stand 3.2-A20 will have the opportunity to explore its latest advancements in digital inkjet technology, designed to help businesses expand capabilities, enter new markets, and drive profitability.
On display will be a range of highperformance solutions, including the EFI Pro 30f+, a flatbed LED printer offering superior image quality, production-level efficiency, and more print capabilities to accelerate business growth.
The EFI VUTEk M3h, a 3.2m hybrid flatbed/ roll-fed LED printer, delivers higher volumes, faster turnarounds, and lower operating costs. For those looking for premium imaging and versatile production capabilities, the EFI VUTEk Q3h XP offers high-speed hybrid LED technology.
Additionally, the EFI VUTEk X3r roll-to-roll LED printer supports unattended printing, delivers a complete print-to-finished graphic workflow system, and takes image quality at production-level speeds to a new level.
Beyond live demonstrations, visitors can explore EFI’s applications and samples area, learn about its advanced textile printing solutions, and discover super-high-speed printers for packaging, signage, and display production. EFI is proudly distributed and serviced by Currie Group.
Key products Elitron will be exhibiting at FESPA Global Print Expo include the Kombo THC 32.20 and the Spark C 19.16. The Kombo THC 32.20 is a multi-tool, conveyor cutting system with two cutting
heads for maximum production flexibility. The Spark C 19.16 is a multi-tool, compact cutting system for a multitude of roll and sheet material applications.
The Kombo THC will be equipped with the loading table and the NEW EFS (Elitron Feeding System) for loading automation, together with the SDS Seeker System which reads and centres the print reference marks and reads any bar codes from the underside, for immediate loading of the relative cutting files. Elitron is proudly distributed and serviced by Currie Group.
Kongsberg Precision Cutting Systems delivers one of the best in class digital cutting solutions to packaging, signage, display, and manufacturing businesses worldwide.
At FESPA Global Print Expo 2025, at Stand 27-C20, Kongsberg PCS, through its new campaign, ‘Shaping Your Future Together’, will be drawing upon its deep materials engineering heritage and expertise to showcase the diverse and scalable
creative applications that are possible when its expertly engineered cutting tables, partnerships, and unique operating software combine.
As well as showcasing the ultra-versatile C24 and award-winning Ultimate tables, with proven capabilities of helping customers make the most of their potential, Kongsberg PCS will be showcasing the new iPC 3.1 operating software – unique to Kongsberg tables.
Designed for increased versatility and high uptime, the iPC 3.1 operator software delivers a major leap in productivity and ease of use. With an overall improved and intuitive user interface, the new update allows new features including dynamic nicks, which allow operators to easily add and modify nicks directly within iPC 3.1, enabling smarter and more efficient operations without the need for third party software.
Kornit Digital will showcase its Apollo system at FESPA 2025. This next-generation direct-to-garment (DTG) solution is designed to transform high-volume apparel production with unprecedented speed, automation, and sustainability.
The Kornit Apollo delivers up to 400 garments per hour, seamlessly integrating printing and curing in a fully automated workflow. By minimising manual intervention, Apollo reduces labour costs while ensuring consistent, high-quality output. Supporting diverse fabric types, from cotton to polyester blends, it meets the needs of fashion brands, print service providers, and promotional product businesses.
Equipped with Kornit’s Eco Rapid NeoPigment inks, Apollo ensures vibrant colours, soft hand feel, and long-lasting durability while adhering to the strictest environmental standards. Its water-based, GOTS-certified inks eliminate pretreatment and post-washing, cutting down on waste and resource consumption.
One of Apollo’s innovations is its ability to enable on-demand mass production, helping brands reduce inventory, eliminate overproduction, and respond quickly to consumer trends. Early adopters, such as Germany’s Print Palace Textildruck, have already leveraged Apollo to transition from traditional screen
printing to a more flexible, cost-efficient digital model.
At FESPA 2025, visitors will experience live demonstrations of Apollo, witnessing its efficiency, precision, and ease of operation. Kornit’s innovative All-Inclusive Click (AIC) model further simplifies adoption by offering predictable costs and lowering investment barriers.
Summa is gearing up for an exciting presence at FESPA 2025. With a dynamic lineup of innovations, including a major product launch, Summa is ready to showcase six of its cutting-edge solutions.
Attendees will get an up-close look at the L Series laser cutters, the S Series vinyl cutters, the F Series flatbed cutters, and the brand-new V Series flatbed cutters –each designed to redefine precision and efficiency in digital cutting.
A standout highlight on the Summa stand will be the S3 TC75 vinyl cutter, optimised for Direct-to-Film (DTF) applications. Understanding the industry’s need for flawless processing, Summa has developed a frictionless roll feed system to prevent scratches and roller marks that often occur when handling PET film. This dedicated DTF bundle also features Summa’s proprietary tangential cutting technology, advanced camera technology, and the intuitive GoSign production
software. The S Class 3-DTF Bundle is designed to meet the highest demands of DTF cutting, ensuring precision, low friction, and unparalleled reliability.
Another key attraction will be the introduction of the V Series flatbed cutters, the result of Summa’s strategic acquisition of Italy-based Valiani. By merging Summa’s precision cutting expertise with Valiani’s deep-rooted knowledge in packaging applications, the V Series delivers outstanding accuracy for cutting and folding carton materials. This makes it an essential solution for packaging professionals, catering to everything from prototype development to short and medium production runs.
However, the most anticipated moment at FESPA 2025 will be Summa’s world premiere of a brand-new cutter. While details remain under wraps, visitors to the Summa stand at FESPA will be the first to witness this new advancement in digital cutting. This innovation is poised to redefine industry standards and offer professionals an unparalleled competitive edge.
swissQprint to showcase the future of large format printing
Visitors to FESPA 2025 will discover the new swissQprint flatbed range. A completely redesigned mechanical foundation, 23 per cent higher output, and 10 colour channels for extended versatility are the prime features. Also in the spotlight will be the Karibu roll-to-roll printer and a wideranging application gallery.
Supported by its worldwide distribution network, swissQprint will be showing visitors in Hall 27, Stand C60, how it can reposition their business and operate with high profitability.
Two printers represent the new generation of machines with which swissQprint heralded a new era in flatbed printing this January: The Nyala model, now in the 5th generation and 23 per cent faster than its predecessor, as well as the high-end Kudu flatbed printer, now with a maximum output of 341 m²/h.
“These printers’ combination of productivity and precision is best seen to be believed,” said Adriano Gut, key account manager at swissQprint.
“The same is true of their multifunctionality and versatility. In addition to various add-on options,
they offer 10 freely configurable colour channels.”
The dedicated roll-to-roll printer, Karibu, is also set to surprise with its unique features aimed at high efficiency along with exceptional capabilities such as varnish embellishment and haptic prints that would normally be expected only from flatbed printing.
Attendees will discover a colourful variety of inspiring flatbed and roll-to-roll printing applications – neon printing included – at printing demonstrations as well as in themed application worlds.
Mimaki to present extensive lineup of product innovation
Mimaki is poised for an exciting and innovation-packed FESPA Global Print Expo as the company celebrates its 50th anniversary.
The Mimaki Tx330-1800 is one of the new solutions being demonstrated at Mimaki’s stand, a direct-to-textile printer allowing for seamless printing on both fabric and paper.
With the Tx330-1800, the operator can easily switch the printing mechanism according to the base material (fabric or transfer paper) to be printed, enabling the production of mainly fabric signs and interior fabrics in short-run.
In addition, the Tx330-1800 can also print on wallpaper and poster paper, contributing to improved proposals for total coordination, including the interior design of stores and event booths, for those who have mainly been producing fabric signages.
The display of Mimaki solutions will also include the JFX600-2531, UCJV330160, UJF-MKII e, and TxF300-75, celebrating the wide-ranging, creative application possibilities enabled by Mimaki technology.
The extensive product portfolio being showcased exemplifies Mimaki’s continuous drive to enable its customers to thrive, adapt, and lead the market in new directions.
Neolt Factory will showcase the 3.3m XY Plus and the Neolt Jumbo Unwinder Model 4.
The Neolt Jumbo Unwinder Model 4, seamlessly integrated with Canon printers and the XY Plus cutter with table and stacker, offers a complete solution for fully automated printing and cutting workflows. It features:
• Higher print volumes: Continuous roll feeding ensures uninterrupted operation
• Seamless workflow: Perfect synchronisation between unwinder, printer, and cutter
• Precision and speed: The XY Plus cutter delivers accurate cuts while the stacker ensures a smooth output process
• Reduced manual handling: Minimise errors and labour costs with a fully automated system.
This setup enhances productivity, reduces downtime, and allows businesses to meet increasing market demands with ease.
Neolt Factory’s innovative packaging line is designed to maximise productivity while minimising costs, powered by a 500kg jumbo roll feed. This solution sets new standards for efficiency and sustainability in the packaging industry.
Other solutions on include:
• XY DTF Cutter automatic cutter for DTF media from roll or online with the printer
• Sword ELS vertical cutter with motorised spindle for cut media like Dibond and Plex
• Neoweld welding machine for banners
• NeoEyelet
• Shield pneumatic laminators
Neolt Factory is proudly distributed and serviced by Currie Group.
At Booth B30 in Hall 27, Zünd will demonstrate how a combination of
powerful cutting technology, intelligent software, and innovative solutions for automated material handling can make digital cutting efficient and versatile.
Visitors will have a chance to experience the extensive versatility of Zünd cutting technology through the example of a Zünd S3 cutter configured for cutting rolled goods as well as challenging board materials.
No less versatile and powerful, its big brother, the Zünd G3, will also be demonstrating live its many capabilities. This cutting solution includes fully automated, robotic material handling, and parts removal with the PortaBase 175 system – the 175 designation refers to the robotic arm’s reach of 69-inches.
As a system provider, Zünd follows a holistic approach that goes well beyond the sale of its products. The focus is on customised total solutions for specific customer requirements, developed with the highest degree of technical expertise.
In addition to hardware and software, this comprehensive approach encompasses a broad range of services both before and after the sale – from maintenance and repair to high-quality original consumables and a variety of after-sales support services.
Customers across the world depend on the reliability of Zünd cutting solutions. They trust the Swiss-based, family-owned business because they can rely on innovative solutions tailored to their specific needs.
The product portfolio from Zünd is also notable for its exceptional modularity. This makes it possible to quickly and conveniently add new capabilities to cutters as production requirements change – whether by adding additional tools, new software functions, or more advanced material-handling solutions. From smart entry-level models to maximally scalable industrial solutions, Zünd covers the entire spectrum of customer requirements.
FESPA Global Print Expo attendees will be among the first to discover what’s next from Durst, with industry-leading innovations set to be unveiled.
Durst is set to showcase its latest innovations ‘Out of the Box’ – from cutting-edge printing technology to powerful software, high-performance inks, and expert services.
“Whether you are looking to optimise your workflow, increase productivity, or discover new applications, our solutions are designed to take your business to the next level,” said Matt Ashman, managing director of Durst Oceania.
“Join us at FESPA to explore the entire ecosystem –Made in Durst.”
Among the highlights will be the P5 X, the newest and long-awaited addition to the P5 family which reflects Durst’s dedication to innovation, quality, and reliability.
The P5 X is a ‘true flatbed’ with roll-to-roll capability to fill a mid-market position in the company’s P5 large-format printing portfolio.
“The P5 X is a testament to our commitment to continuous growth in the large-format printing (LFP) sector,” said Christoph Gamper, CEO and co-owner of Durst Group.
“We continue to push boundaries with new technologies, expanding our capabilities to meet our customers’ evolving needs.”
Ashman added, “The P5 X complements the other products in the P5 portfolio and is the true flatbed machine that everyone had been asking for from Durst for some time.
“The market needs a machine like this with the flexibility, reliability, and functionality that Durst customers have come to expect.”
Designed for high-end applications such as bespoke visual communications, largescale decoration, and specialty packaging, the P5 X is built to meet the highest standards while also being accessible to those wanting to enter the “Champions League” of digital printing.
Other products to be showcased include:
• The P5 350 HS D4
The Durst high-speed workhorse, with enhanced performance, throughput and efficiency
• A groundbreaking innovation for sublimation printing
Super-wide sublimation printing
solution with integrated inline fixation
• New Durst printer series for fabrics printing
Expanding the product offering for indoor and outdoor applications with water-based ink
• New ink generation
High-yield inks for brilliant colours and durability, tailored for a wide range of substrates and applications compliant with the European standards
Visitors to the Dust booth at FESPA Global Print Expo can also learn more about its powerful software solutions that streamline processes, optimise production, and reduce costs, including:
• AI-powered tools: Durst will introduce new AI-driven solutions designed to assist users at every step, simplifying processes and enhancing their experiences.
• Durst Workflow: The new version of Durst Workflow features an enhanced automation package that enables users to automatically process jobs from file submission to printer. It’s designed to boost efficiency, save time, and reduce costs.
• Durst Analytics: Discover how Durst Analytics now moves to the cloud, with new functionalities designed to further enhance a user’s experience. Make data-driven decisions with realtime monitoring and performance insights for maximum uptime and automated production.
• Smart Shop: An intuitive and fully integrated e-commerce solution dedicated to the digital printing industry, it enables seamless order processing, automated production, enhanced price calculation, and powerful personalisation tools to elevate business.
• Lift ERP: From order entry to final invoicing, Lift ERP connects a user’s entire workflow, providing end-to-end efficiency.
ProPrint recently toured the printing facilities of Corrective Services Industries (CSI) – the commercial arm of Corrective Services NSW – to understand how it works with the local printing industry and also empowers inmates to gain employment and skills.
Corrective Services Industries (CSI) – the commercial arm of Corrective Services NSW – employs more than 5000 people in custody across 120 business units within 14 different industries across 29 correctional centres.
For more than 30 years, CSI has empowered inmates to gain employment skills and qualifications while in custody as well as provide work release programs and pathways to employment.
ProPrint recently visited Long Bay Correctional Complex in Sydney to understand how CSI operates in one of its industries – producing print and signage work and how it integrates with the local printing industry.
The equipment used within CSI’s printing facilities at Long Bay features a number of brands familiar to the printing industry including HP, Zünd, Epson, Roland DG, and Mimaki and is located within a facility in the Correctional Complex.
Through its print operations, CSI provides an extensive range of products and services for the day-to-day operation of NSW correctional centres and also manufactures and supplies sign and print work in partnership with the private sector and government.
“We specialise in overflow and import replacement work, supporting Australian businesses to keep manufacturing onshore,” said CSI marketing manager, Donna Elayadi.
“Our clients are varied, but they all have one goal in common: by working with CSI, they contribute to creating safer communities for us all.”
CSI programs provide work readiness capability for people in custody to enhance their opportunities to gain employment post-release, reducing recidivism and enhancing community safety.
“CSI business units replicate the realworld working environment that allows people in custody to participate in work programs providing opportunities to learn new skills and gain employment experience,” Elayadi said.
“Providing people in custody with the opportunity to participate in meaningful work and develop skills they can use in the community significantly enhances the opportunity for post-release employment.
“It also empowers inmates to gain employment skills and qualifications while in custody. We continue to surpass industry benchmark performance for
correctional industries globally with innovation at the forefront. We treat land, resources, and people with great respect,” she said.
All work completed by CSI is managed by trade qualified overseers, including ProPrint Awards Printer 50 finalist Angelo Varnakulasingham and his team.
“The CSI Standards of Customer Service Management provide a total commitment to servicing customer needs,” Elayadi said.
“CSI staff at all levels, are committed to fulfilling customer needs in a friendly, responsive, and professional manner. Serving the customer is the most important part of our business.
“Our widespread industry facilities and job ready workforce means that we have robust contingency plans in place for the fulfilment of orders. Our warehousing and logistics services can facilitate long-and short-term storage solutions, as well as deliveries across New South Wales and interstate.”
CSI currently works with more than 100 employers across NSW to provide skilled individuals eager to work and find pathways to employment. Companies from within the local printing industry who are interested in finding out more can contact business manager operations David Rickwood on 02 4582 2420.
Are you looking to partner with an Australian company with a large workforce to complement your business?
With expansive operations, warehousing, logistics and labour force capability across metro and regional NSW, we provide high quality manufacturing, printing, assembly and other service solutions to Government and private sector.
By partnering with CSI, your organisation empowers people and contributes to safer communities for everyone. We specialise in import replacement work, supporting Australian businesses to keep manufacturing onshore.
Speak to our team today to find out more.
This document contains statements related to our current and future operations and is subject to change without notice. All diagrams, drawings, products, machinery, and any other types of images in this document are for display purposes only.
Compliance to AS/NZS ISO 9001:2015 Quality Management Certification, applies to select Business Units. While the information in this document has been presented with all due care, the Department of Communities and Justice does not guarantee or warrant, and accepts no legal liability whatsoever arising from or connected to, the accuracy, reliability, currency or completeness of any material contained in this document. Enquiries relating to this document should be directed to csi@dcj.nsw.gov.au or 02 4582 2420.
For further information
Call 02 4582 2420
Email csi@dcj.nsw.gov.au
Visit csi.nsw.gov.au
Casuals have a new pathway to fulltime or part-time (permanent) employment under the National Employment Standards (NES).
Previously, employers had an obligation to offer casual Award covered employees the opportunity to convert from casual to permanent employment after six or 12 months of service where certain criteria are met.
However, since 26 February 2025, casual employee conversion now operates under an ‘employee choice pathway’ thereby dispensing with the need for an employer to instigate offering conversion to permanent employment status.
Under the new ‘employee choice pathway’ a casual employee can give written notice (the ‘notification’) to their employer requesting they convert to permanent employment status if they have been employed for at least six months, and believe they no longer meet the requirements of the casual employee definition.
A casual employee cannot provide the notification if they:
• have had a previous notification for conversion rejected in the previous 6 months; or
• are currently engaged in a related dispute.
A business that receives a notification must consult with the employee and provide them with a written response within 21 days. If the request is accepted the business must provide information setting out the employee’s new status (full-time or part-time), their new hours of work, and the date the change
The employee choice pathway allows eligible casuals to notify their employer in writing of their intention to change to permanent employment
commences (the first day of the first full pay period commencing after the response unless otherwise agreed).
An employer can only refuse the conversion request if the employee:
• still meets the definition of casual employee;
• there are fair and reasonable operational grounds for not accepting the notification, such as:
• substantial changes would be required to the way in which work in the employer’s business is organised;
• there would be significant impacts on the employer’s business operations; or
• substantial changes to the employee’s employment conditions would need to be made to ensure that the employer does not contravene an Award or enterprise agreement that would apply to the employee as a permanent employee.
In keeping with the revised legislative definition of ‘casual employee’ in the Fair Work Act, an employment relationship is considered casual if the employment relationship is characterised by:
• no firm advance commitment to continuing and indefinite work; and
• the employee would be entitled to a casual loading or a specific rate of pay for casual employees under an Award or contract of employment.
Where an employer and employee are unable to reach agreement, the issue can be escalated to the Fair Work Commission.
Although the Commission will initially seek to resolve the dispute by informal conferencing, the Commission can arbitrate with a binding decision. This includes that the employee will continue to be treated as a casual or alternatively as a permanent employee.
Additionally, the employee choice pathway is a workplace right and casual employees may be protected under the General Protections provisions of the Act. Any deliberate actions by an employer to avoid their obligations can be dealt with accordingly.
Please note that these changes do not come into effect for small businesses until 26 August 2025. Further, a small business employee must have been employed for 12 months employment, rather than six months, prior to providing a notification to their employer.
As part of your related consultative discussions with the casual employee, remember to advise them that if they become permanent (part-time or full-time) they will commence accruing personal and annual leave entitlement, however, will no longer receive the casual loading if they become a permanent employee. This consideration can result in an employee deciding to withdraw their request due to a perceived reduction in pay.
In dealing with this issue, businesses should ensure that their operational needs are proactively considered. Businesses should undertake an assessment of the real substance, the practical reality, and the true nature of whether each casual employee continues to meet that definition under the Fair Work Act.
Charles Watson is GM – IR, Policy, and Governance at the Visual Media Association
This article is of a general nature and guidance only and does not constitute legal advice.
As a business owner, you likely wear a lot of hats. You juggle sales, marketing, operations, and customer service. Maybe you even manage your own finances, tracking cash flow, balancing the books, and making sure everything adds up.
But as your business grows, you might start to feel like you’re sinking in spreadsheets or that you can’t quite keep up with the financial decisions that are starting to pile up. That’s when the idea of bringing in a CFO starts to feel less like a distant dream and more like a reality.
But how do you know when it’s time to hire a CFO? Is it worth the investment? Let’s dive into the signs that it’s time to engage a CFO and the benefits of having one on board.
1. You’re too busy to focus on your business’ financial health
At the early stages, it’s common for business owners to manage their finances themselves. But as the business grows, you might find that it isn’t just time-consuming – it’s taking your focus away from running the business. If you find yourself scrambling through financial statements at the last minute, or feeling overwhelmed by cash flow issues, it could be time to get expert help.
It’s not uncommon for business owners to feel like they’re constantly putting out financial fires instead of planning ahead. A CFO can take over the heavy lifting, giving you the time and space to focus on what you do best – growing the business.
2. You’re facing complex financial decisions
As your business expands, so do the financial complexities. You might be considering taking on debt, structuring a deal, or navigating new regulations, and you realise you’re not sure which direction to take. For example, should you seek outside funding, or are you better off bootstrapping for a bit longer? What’s the best way to structure compensation packages for your
A CFO can be your financial strategist, helping you plan for the future
growing team? These decisions are critical, and having a financial expert guiding you through them can make all the difference.
A CFO doesn’t just manage financial reports – they help you make the right strategic decisions for the business, based on real-time financial data and projections. They help you understand what risks you’re facing and where the opportunities are.
3. You’re dealing with unpredictable cash flow
It’s a common problem: You have great sales, but when it comes time to pay suppliers or employees, the cash just isn’t there. Cash flow issues can make even the most successful businesses feel like they’re on the edge of a cliff. If you’re constantly stressed about managing the timing of expenses and income, a CFO can help you set up systems and strategies to ensure more consistent cash flow.
A CFO can help you forecast your financial future more accurately and implement systems that improve your liquidity, making sure you have the cash you need to run smoothly.
4. You’re ready to scale, but don’t have a financial strategy in place
You know your business is ready to grow, but the path to expansion is unclear. You might be considering
opening new locations, launching a new product line, or expanding your marketing efforts. But you’re unsure how much capital you’ll need, how to structure the growth, or whether it’s sustainable long-term.
A CFO can be your financial strategist, helping you plan for the future. They can help analyse the numbers, set financial targets, budgets, and projections that support your expansion plans. Having someone with a big picture understanding of your financial landscape can help you scale smarter and more confidently.
5. You’re facing increased regulatory and compliance demands
As businesses grow, so does the need for compliance. Whether it’s tax laws, financial regulations, or industryspecific requirements, keeping up with everything can quickly become a fulltime job. A CFO brings expertise in managing compliance, ensuring that your business stays on the right side of regulations, and minimising risks associated with penalties and audits.
Engaging a CFO doesn’t have to be an overwhelming decision. If you find yourself asking, “When should I hire a CFO?” it’s likely you’re close to needing one. If you don’t want to jump straight in, you can always engage a fractional CFO (someone that fulfils the role on a parttime or flexible basis). Whether it’s to fix cash flow issues, navigate expansion, or just to get a clearer picture of where your business stands, a CFO can help provide that clarity.
At the end of the day, it’s about recognising when you need help and trusting an expert to guide you. You’ve built your business with passion and drive. Now, it’s time to bring in the financial expertise that can help you take it to the next level.
Andrew Ash is a business advisor, fractional CFO, and tax agent. He can be contacted at pfbconsulting@outlook.com or 0412 055 814.
Berlin, Germany
Beijing, China
Sydney, Australia
Print4All 2025
Labelexpo Europe 2025
Pack Print International
The Print Show & The Sign Show
ProPrint Awards
Printing United 2025
Milan, Italy
Barcelona, Spain
Bangkok, Thailand
Birmingham, UK
Sydney, Australia
Florida, US DATE
Hosting an event? Send an email to the editor Claire Hibbit chibbit@intermedia.com.au with the details
• Near total coverage of roller requirements for the graphic arts sector
• Wide range of rollers for printing and packaging, laminating, gluing, transport and nip
• Specialised services for non-standard applications
• In-house expertise to help you achieve your production goals
For enquiries, please contact: Carmen Ciappara, National Sales Manager Direct: 02 9833 4314 or 0410 582 450 | Email: carmen@proprint.com.au
Mimaki JFX 200-2513
CMYK + WWClCl Inks
Max Print 2500x1300mm In great working order MAKE AN OFFER
Mimaki CF-22 Cutting Table 2500x1220mm Plotting Area
Single Phase 240V In excellent condition MAKE AN OFFER
Autobond Mini 52SD-T
Max sheet size: 52 x 74 cm
150 gsm to 650 gsm
Small footprint (10’ x 4’) MAKE AN OFFER
2010 Isuzu NLR 200 205,000kms, Electric Windows, Tinted Windows, Freshly painted cab. $22,000 + GST
Call Print Storm on (02) 6372 7599 or email paul@printstorm.com.au
Volunteer or Sponsor help us grow!
Come and see the extensive expansion and renovations.
Need a venue for a function? Talk to us we can help.
Visit https://www.printingmuseum.org.au/
Revolutionise Your Bookbinding with Our State-of-the-Art Hard Case Solutions.
Print Logistics is proud to offer cutting-edge, hard case binding technology that delivers a new level of durability and sophistication. Our innovative process involves expert casing of the hardcover, resulting in a final product that exceeds the competition in both robustness and elegance.
Elevate your publications, specialty books, and projects to new heights with our superior hard case binding solutions, perfect for customers who refuse to compromise on quality.
• Fast turnaround times
• Competitive trade-only pricing
• Privileged communication
• Family owned and run
• Variety of customisation options to meet your specific needs
“We’ve relied on Print Logistics for years and couldn’t be happier with their service. Their professionalism, precision, and dedication to confidentiality make them invaluable partners. We highly recommend Print Logistics for exceptional printing and binding services.” Principle Design
Print is perception and we treat it accordingly.
Contact Us Today
Phone: 1300 659 029
Email: contactus@printlogistics.com.au Visit: www.printlogistics.com.au