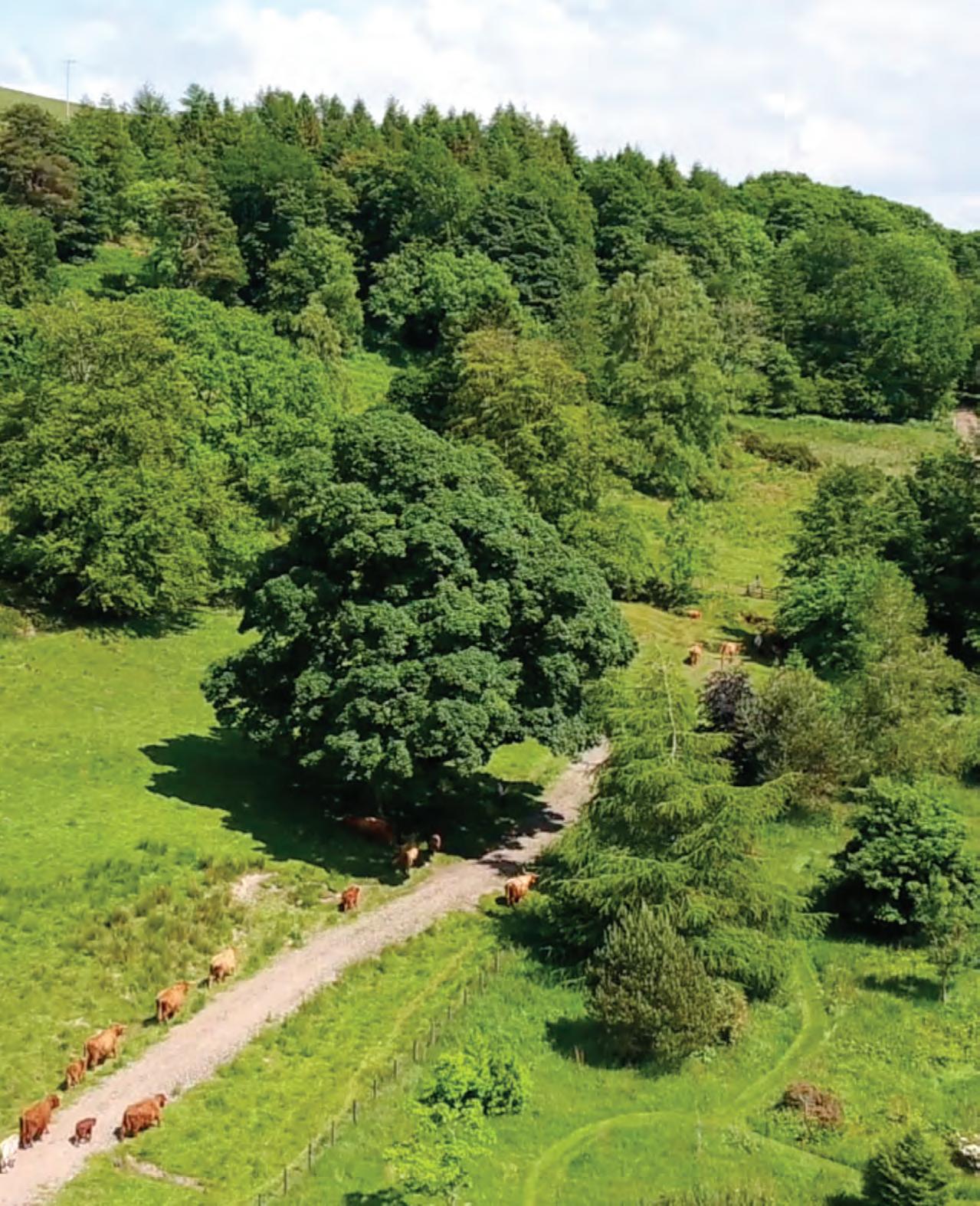
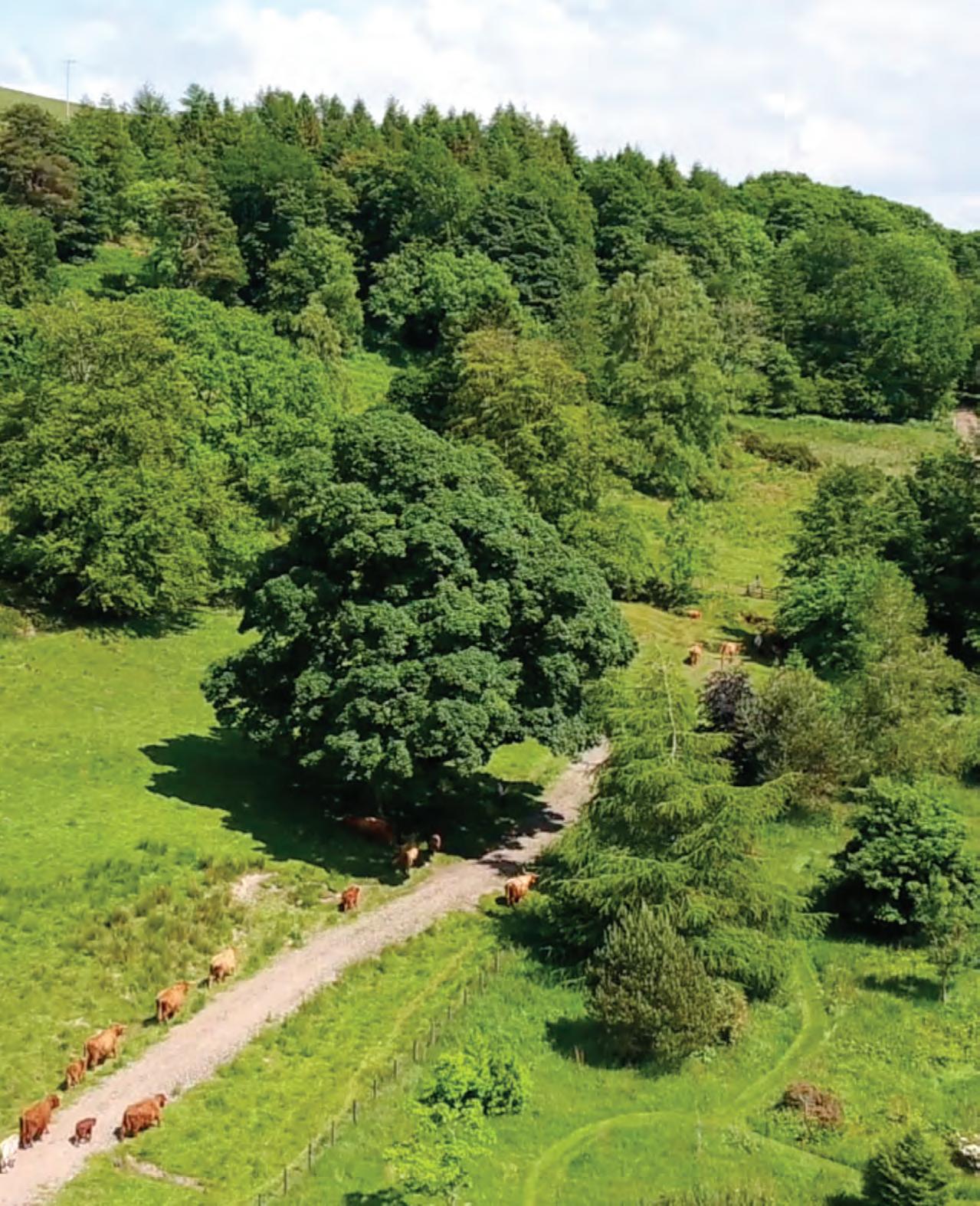
WELCOME
Lanna Deamer l.deamer@hennikgroup.comPicture this: a symbolic baton is being passed from Joe Bush to Tom St John, and with a confident grasp, it's now in my hands. As the new bearer of this imaginary, yet symbolic torch, it's my turn to take the lead and kickoff this issue with some opening thoughts. The stage is set, the anticipation is high and I'm ready to deliver an engaging start that will hopefully leave you wanting more.
Firstly, a big thank you to those who joined us at our sixth Industrial Data Summit in Birmingham at the end of April. The day brought together a diverse group of experts from the sector for a day full of thought-provoking conversations. One of the highlights was a keynote delivered by Kat Dixon, Analytics Business Partner at Babcock International, on the importance of fostering a strong digital culture, where technology is harnessed to encourage collaboration, improve efficiency and enable data-driven decisions. As Kat reminded us, it’s ultimately people who will make the difference.
As so eloquently presented during Industrial Data Summit, by our Director, Henry Anson, we’ve a range of events coming up very soon; some of you may even be reading this at one of them. Manufacturing and Engineering Week 2023 is fast approaching and the week promises to be a festival of industrial innovation, with Design Engineering Expo, Drives & Controls, Maintec and of course, Smart Factory Expo all taking place under one roof. Not only will these be incorporated but The Manufacturer team will once again be delivering SME Growth Summit, Manufacturing Digitalisation Summit as well as celebrating ten years of The Manufacturer Top 100. Truly a week not to be missed!
In the ever-changing world of business, the adoption of digital technologies has become essential for manufacturers to succeed. By utilising these tools, manufacturers can improve their operational efficiency, increase customer satisfaction and foster innovation, thereby gaining a competitive edge. Ashley Oulton, Conference Programme Manager at The Manufacturer looks ahead to Manufacturing Digitalisation Summit taking place in Birmingham on June 7-8 as part of Manufacturing and Engineering Week 2023. See page 14.
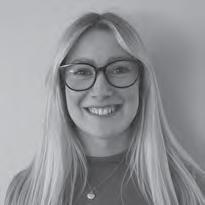
As always, the editorial team has been out and about visiting the very best of UK manufacturers and we’ve got two more factory visits and a fun day out in South Wales to tell you about. In April, leading manufacturer of measuring and production systems, Renishaw, celebrated its 50th anniversary. The Manufacturer Editor, Joe Bush, paid a visit to the company’s Miskin site to find out more about the company’s evolution.
Long time supporters of The Manufacturer MX Awards, and winner of The Manufacturer of the Year 2021, we thought it was finally time to pay Lander Tubular Products a visit at their Birmingham site. With over 140 years of history and experience since William Lander started manufacturing household wire formed goods in his attic back in 1881, the company has grown and transformed beyond his wildest dreams. See page 32.
I look forward to seeing many of you at Manufacturing and Engineering Week, please do stop by The Manufacturer Studio and say hello!
D E C @TheManufacturer
Editorial Advisory Board
The Manufacturer’s editorial advisory board provides insight and guidance to the editorial team on a regular basis, helping maintain the relevance and quality of the magazine’s content, both in print and online. The board also provides diverse and expert comment on strategic developments in manufacturing.
Board members also advise on other The Manufacturer products and online publications, such as the Annual Manufacturing Report. Membership is by invitation only, but if you would like to be considered, please email j.bush@hennikgroup.com
Andrew Churchill EXECUTIVE CHAIRMAN

JJ Churchill and The Manufacturer Top 100, Exemplar 2014
Chris White
DIRECTOR OF INDUSTRIAL POLICY Manufacturing Technology Centre
Thomas d’Arcy INNOVATION LEAD

Rolls-Royce plc. Young Manufacturer of the Year, TMMX Awards 2017
Sarah Black-Smith
HEAD OF FACTORY OPERATIONS Siemens Digital Factory, Congleton

Deirdre Fox DIRECTOR OF STRATEGIC BUSINESS DEVELOPMENT Tata Steel


Christopher Greenough
CHIEF COMMERCIAL OFFICER SDE Technology, and The Manufacturer Top 100, Exemplar 2016

Dave Mooney MANAGING DIRECTOR Drallim Industries, and The Manufacturer Top 100, shortlisted 2014

Jan Ward CEO Corrotherm, and The Manufacturer Top 100, Exemplar 2014, current Judge
David Holmes
MANUFACTURING OPERATIONS DIRECTOR MAI BAE Systems and The Manufacturer Top 100, Exemplar 2017
Paul Gadd
DEPUTY DIRECTOR, LAND & MARITIME TRANSPORT, MANUFACTURING & MATERIALS Innovate UK



Roy Haworth ENGINEERING INTEGRATION MANAGER Airbus Defence and Space, and The Manufacturer Top 100, Member 2016

Laura McBrown MANAGING DIRECTOR G&B Electronics and The Manufacturer Top 100, Member 2016

What to expect

better, sooner





28 12 things you need to know about quantum computing Digital Catapult take a look at the technology benefits for manufacturing



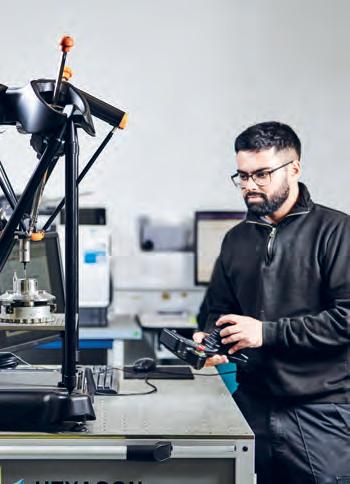
32 Tubular sells The Manufacturer pays a visit to TMMX Manufacturer of the Year 2021

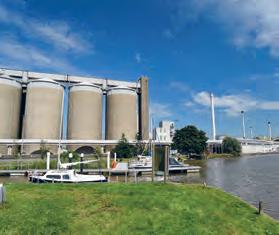









BIGGER, BETTER, SOONER
Smart Factory Expo is back for 2023 and if you’re thinking it seems like it came around fast, that’s because it has. From its new home at the NEC, Birmingham, as part of Manufacturing and Engineering (M&E) Week, Smart Factory Expo 2023 will take place on 7-8 June. And even though it’ll have only been six months or so since the last instalment, this year’s Smart Factory Expo is shaping up to be even bigger and better. The Manufacturer’s James Devonshire sat down with some key partners to learn more
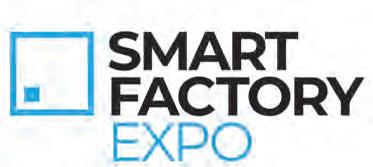
What better way to kick off my Smart Factory Expo 2023 coverage than by finding out what we can expect from Innovate UK, the UK’s national innovation agency, at this year’s event.
Innovate UK is a non-departmental government body with a mission to drive sustainable economic growth through business-led innovation, by investing in innovation and giving businesses access to support.
At Smart Factory Expo 2023, all of Innovate UK’s services will come together to deliver two core aspects of the show: Made Smarter Innovation Alley and the Innovate UK Innovation Village.
To find out more about both offerings, I caught up with Innovate UK KTN’s AnnaMarie Taylor and Matt Wasley and James Crossling from HVM Catapult.
All the pillars of UK innovation under one umbrella
The most notable difference about Innovate UK’s presence at Smart Factory Expo 2023 is its structure. In previous years, the agency’s different streams have showcased the amazing work they are each doing to drive innovation, albeit usually via separate stands and showcases.
For 2023, all the organisational elements that make up the overall Innovate UK system will come together under one umbrella in the Innovate UK Innovation Village. This will

include Innovate UK KTN, Innovate UK Edge, the High Value Manufacturing Catapult (with all of its seven centres) and Made Smarter Innovation.
Showcasing leading edge innovation in low carbon advanced manufacturing, the Innovation Village and Innovation Stage will feature companies supported by Innovate UK, investment support and funding opportunities, as well as a series of speakers who are leaders in their industry.
At the Innovation Stage, exhibition visitors can learn from inspirational speakers and partners championing and demonstrating innovation in low carbon advanced manufacturing: from the Advanced Manufacturing Research Centre’s (AMRC) open-access smart factory framework,
DIGITAL TRANSFORMATION INNOVATION VILLAGE
The Innovation Village will demonstrate innovation across four areas that Innovate UK believes are fundamental to capitalise on the huge opportunity the UK has to become a world-class destination of choice for advanced low carbon manufacturing:
• Net zero: Materials and manufacturing will be technically advanced and play a vital role in achieving the UK’s net zero target by 2050 and meeting global sustainable development goals.
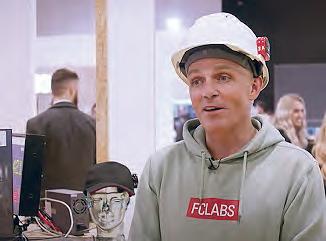
• Resilience in supply chains: Enabling companies to deal with uncertainty around changes to process, demand or supply, so the UK can create more resilient supply chains, creating more value with less cost and waste.
• Digitalisation: Innovate UK is working with manufacturing and digital industries to help the UK gain maximum advantage from the digital revolution.

• Skills and diversity: Courageous leadership, critical skills foresight, upskilling the current workforce and attracting diverse talent to drive UK manufacturing in all regions and nations.
Factory+, to the National Composite Centre’s (NCC) certification by analysis project. Apprentices from the HVM Catapult network will also talk about their careers and aspirations.
There will also be the opportunity to have your say on the Materials and Manufacturing Vision 2050, which looks at challenges and opportunities; it will outline a route to building on manufacturing capacity to make the UK a global centre for net zero sustainable production and reimagines the industry of the future.
Innovate UK’s Materials and Manufacturing Vision 2050 will be of significant importance for both our economy and society as the UK moves to establish itself as the destination of choice
for advanced low carbon manufacturing in a net zero focused world.
So why not come along and join the conversation on this crucial area of future manufacturing and learn about where Innovate UK funding will be directed going forward.
By providing access to inspiring talks, innovative companies, innovation and investment support, the Innovate UK Innovation Village represents a significant opportunity to progress your innovation aspirations.
Innovation that’s right up your alley
A regular feature at the heart of Smart Factory Expo, Made Smarter Innovation ...continued on Page 9.
ABOVE: In 2022, iov42 met with lots of different manufacturers on Innovation Alley – everyone from pharmaceutical manufacturers to companies manufacturing art
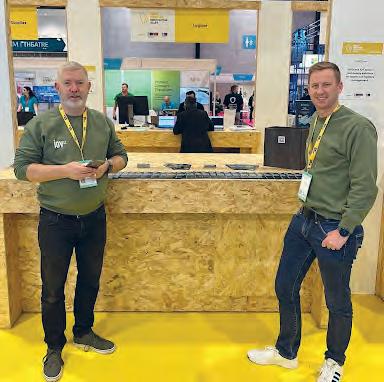
At Smart Factory Expo 2023, all of Innovate UK’s services will come together to deliver two core aspects of the show: Made Smarter Innovation Alley and the Innovate UK Innovation Village
Taylor, Innovate UK
Deloitte will focus on how digital engineering and smart manufacturing can enable your organisation to design, manufacture and operate products that are more sustainable
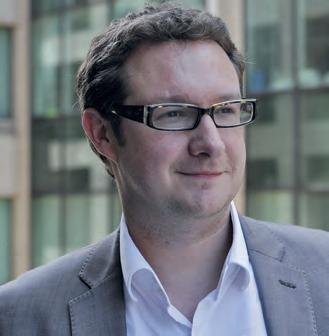
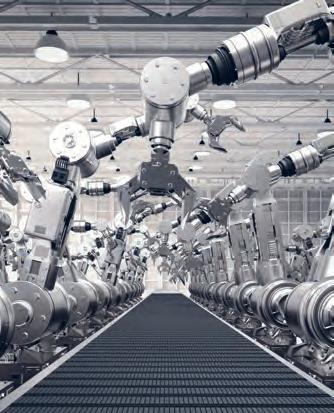
From seven smart factory sins to seven virtues
Deloitte’s ‘7 Sins of a Smart Factory Journey’ was a hit at last year’s Smart Factory Expo. The brilliant keynote by Deloitte’s UK leader for Industry 4.0, partner Nick Davis, and subsequent online article on The Manufacturer website garnered significant interest and traction.
Then there was Chip, the robot dog that captivated everyone who saw it at last year’s event, with its super-realistic movements, cute poses and book of tricks. To say we were excited to hear what Deloitte had planned for this year’s event is an understatement. We caught up with Nick (fresh back from Hannover Messe) to find out more.
Focus on sustainability
“The main theme that will run across all of our presentations and our stand this year will be sustainability”, Nick said.
“With Smart Factory Expo now a part of Manufacturing and Engineering Week, we will focus on how digital engineering and smart manufacturing can enable your organisation to design, manufacture and operate products that are more sustainable.”

The Deloitte stand will be the home of everything Deloitte. Stop by to learn about the breadth of expertise Deloitte offers; chat about your engineering and manufacturing transformation journey, experience immersive demos, hear about Deloitte’s project experience or just come to say hello and network.
Visitors to the Deloitte stand will discover how sustainability can be at the heart of product design and smart factory transformations. “We’ll cover sustainable
product design, circular ‘zero waste’ manufacturing, net zero workforce and sustainable transformation journeys,” Nick added.

Seven new sins
Deloitte will also be hosting four sessions in the Solutions Theatres over the two days. So, can we expect seven new smart factory sins, or has the focus changed for 2023?
Building on the success of last year’s ‘7 Sins of a Smart Factory Journey’, Deloitte will, on day one, reveal the ‘7 Virtues of Smart Factory’.
Nick said: “We will look at seven considerations for organisations on their sustainable engineering and manufacturing journeys and how to successfully navigate them. Later, we will talk about what product development will look like in the future as we embrace sustainability and the latest engineering practices. The session will cover material selection, circular design, durability and business models.
“On day two, we will share a client case study on reducing energy usage at a manufacturing facility, and how to get your smart factory to net zero.”
And finally, will Chip be returning?
Chip the dog will indeed be back this year and this time around he’ll have his own house. In 2022, poor old Chip was resigned to being charged in a cupboard – not exactly befitting a dog of such talent. This year, Chip will rest and charge in a bespoke dog house, further adding to the whole experience for visitors.
When it comes to innovation, as well as Chip, Deloitte will also have its virtual reality Metaverse experience, which will enable people to immersively explore its Dusseldorf, Wichita and Kyoto Smart Factories using a VR headset.
Meanwhile, a large screen will demonstrate some of Deloitte’s other innovative solutions. One such solution is GreenSpace Tech by Deloitte, which is a dynamic ecosystem that helps accelerate decarbonisation by enabling businesses to select the right technology to help to reduce investment risk.
Visitors can also expect some classic Deloitte demos on 5G, cyber security, digital transformation and more – everything you’d expect from the company’s Industry 4.0 offering.
The main theme that will run across all of our presentations and our stand this year will be sustainability
Nick Davis, partner and Industry 4.0 leader, Deloitte
Alley will be back once again this year, showcasing a host of the UK’s leading edge digital technology start-ups and scale-ups. These exciting, disruptive companies are ones to watch in the digital manufacturing space and will likely change the sector landscape over the next five to ten years.
Funded by Innovate UK and supported by Innovate UK KTN, Made Smarter Innovation Alley will feature no less than 30 game-changing innovators in the digital manufacturing space, each of which is younger than five years old or employs less than ten members of staff.
Confirmed Innovation Alley exhibitors (at time of writing) include:
• Sensor IT
• E-Nano
• TrackMyMachines
• Veribli
• FC Labs
• Clyde HSI
• iov42
• SMSTech
• Emerging Data Technologies
• CUEInterative
• DataFlowIQ
One Innovation Alley exhibitor that caught this reporter’s eye last year was FC Labs, with their incredibly powerful CoreTech technology which monitors fluctuations in mental attention. By tracking this data in real-time via two non-invasive sensors, CoreTech can flag when a potential workplace accident or incident due to human error might occur. This simple yet highly effective solution can empower individuals, teams and businesses to perform at their best, avoid accidents and injuries and improve overall health and wellbeing. Do check it out.
As well as getting to showcase their innovative solutions to manufacturers and other attendees, Innovation Alley exhibitors will also get access to Innovate UK experts, to help them hone their presentation skills and get the most out of their interactions with connections at the event. Furthermore, each Innovation Alley exhibitor will get the chance to pitch their solution(s) on the Innovation Stage to a select audience of interested individuals.
Scan the QR code to discover how iov42 found that Made Smarter Innovation Alley was a great testbed for their early stage blockchain technology.
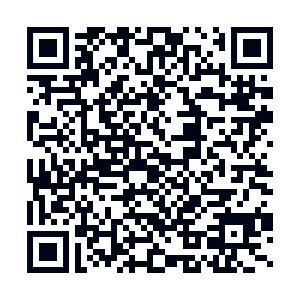
If you’re going to be at Smart Factory Expo 2023, make sure you call in on Innovation Alley and see some of the amazing solutions on show first-hand.
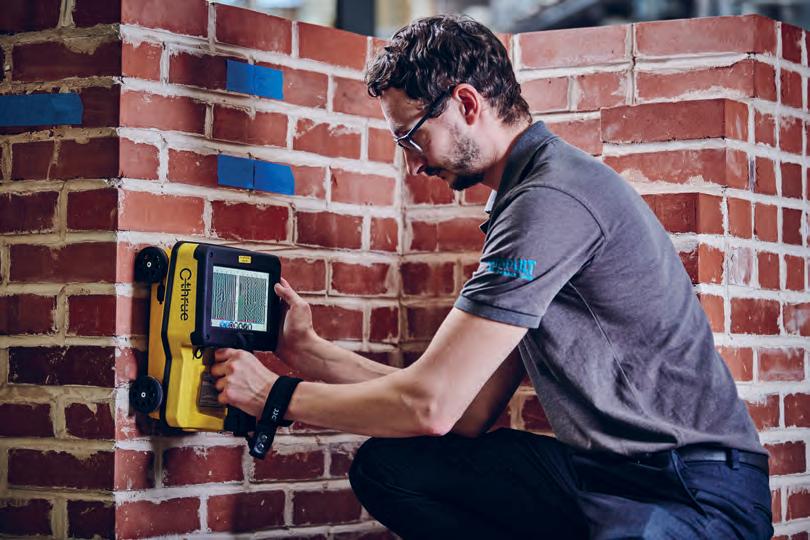
Dr Megan Ronayne, Head of Industrial Technologies and Manufacturing at Innovate UK KTN said: “Made Smarter Innovation Alley is a key event in the manufacturing calendar, showcasing the most innovative, game-changing digital technology companies that are helping to advance the global manufacturing sector. At Innovate UK KTN, collaboration is core to what we do, and it is great to play such an essential role in connecting companies on the alley to potential partners, suppliers, customers and funders.”
If you are interested in being a part of Made Smarter Innovation Alley in the future visit: bit.ly/InnovAlleySignUp.
Navigating the digital manufacturing space
As part of the High Value Manufacturing Catapult (HVMC), the Manufacturing Technology Centre (MTC) will have a presence in the Innovate UK Innovation Village. However, it will also have its own
ABOVE: The MTC is seeing more and more businesses embarking on digital transformation journeys, driven by a number of potential benefits
separate stand outside in the main Smart Factory Expo arena to showcase the specific help it can provide manufacturing organisations.
MTC Director Andy Barnes gave us a flavour of what’s in store for MTC stand visitors this June.
A digital focus
The Manufacturing Technology Centre’s big focus for Smart Factory 2023 is digital transformation and, in particular, how organisations throughout the supply chain can learn to navigate the array of technologies and capabilities within Industry 4.0 in order to unlock new efficiencies within their manufacturing organisations, realise significant business outcomes and have a positive impact on society.
“The digital manufacturing landscape is very complex and that can be pretty daunting for many businesses”, said Andy. “One of the ways we can help is by guiding businesses through it using the frameworks and roadmaps we have developed, which can be applied to specific businesses and sectors.
“To help them on that journey from where they currently are – wherever that may be in terms of maturity or commitment –towards realising some of the benefits of smart manufacturing.”
Andy added that the MTC is seeing more businesses embarking on this journey, driven both by the traditional benefits, such
as productivity gains, as well as benefits which add value to their offerings. A good example of this is manufacturers using data to start taking advantage of and generating additional revenue from servitisation.
Such an approach not only adds value to customers but also to their own business. However, it requires a certain approach to data – both legacy and new – to ensure they are not only capturing the right information but getting genuine value from it. “That’s a lot of what we’re doing now,” Andy said.
Leveraging tech to get the best out of data
Andy told us that as well as supporting industry within the UK on routes to industrial digital transformation the MTC is also focused right now on leveraging new disruptive technology, such as Artificial
Intelligence
(AI) and Machine Learning
(ML) to help businesses maximise value from their data.

By using real-time data (providing it’s being captured), organisations can look to evolve and improve their machinery to make it work harder for them. Such an approach might include adding sensors to a piece of legacy equipment so that insights into its performance, availability and other metrics can be gleaned. Improvement plans can then be drawn up to boost the machine’s performance going forward. The MTC will be showcasing such sensors at Smart Factory Expo.
In a similar vein, technological advances like digital twins are making waves in the manufacturing industry. They enable organisations of all shapes and sizes to model various aspects of their businesses, both in design and operation, such as their production line, production facility and supply chain, so they can test changes to better determine their potential impact.
Through digital models, businesses can discover what a new product introduction might look like and also what it will entail, before they make any real-world changes. This allows organisations to effectively derisk their investments, as well as be more agile and adaptable.
Specific SME support Oftentimes, we see SMEs, in particular, reluctant to take the digital plunge, whether it be because of costs, lack of skills, etc.
How can the MTC help in that regard?
Andy continued: “With such a complex digital environment, there is a hesitancy for SMEs to step foot into the landscape. But where can they go for help? “SME’s are hesitant to reach out to one of the big consultancies, simply because of their size.
“Likewise, if you contact a software vendor, there’s a good chance they’ll sell you their solution, whether it’s a good fit for you or not.”
One of the roles the MTC plays is to provide independent support to SMEs who want to take advantage of digital and working with solutions providers who can help them do so. The experience and advice its experts can offer is so valuable and relatable because they simply understand manufacturers and their pain points.
Come along to the MTC stand and talk with experts, engineers and thought leaders who have decades worth of experience between them in specific manufacturing sectors such as aerospace, defence, automotive, construction, agritech, etc. You’ll be able to see from real world examples and demonstrators how the MTC has helped businesses like yours.
You can also discover more about the MTC’s Manufacturing Training Centre, which boasts a whole range of offerings designed to help businesses both big and small overcome their upskilling challenges.
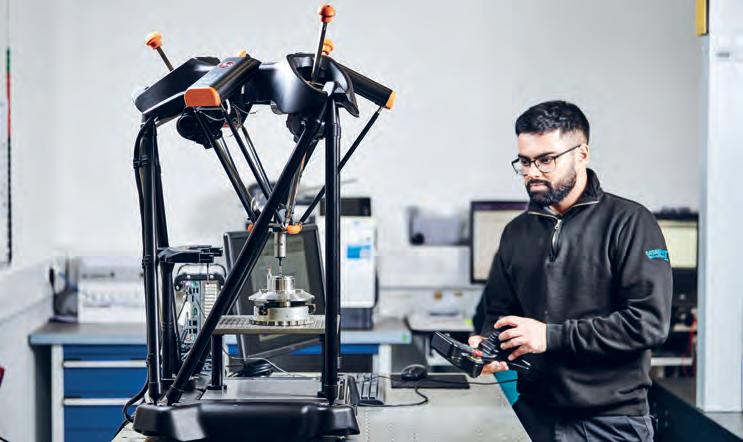
Digital transformation doesn’t need to be difficult (or necessarily cost a fortune) For many manufacturing organisations –particularly the SMEs who are the lifeblood of British industry – digital transformation presents a number of challenges. Whether it’s having the right skills to proceed, or justifying the necessary investment, digital transformation is often prohibitive for SMEs.
However, digital transformation doesn’t need to be a one time, big time effort which costs hundreds of thousands of pounds and takes years to complete. Most companies can realise tangible benefits by making a few small changes and taking it from there. It’s a reality that RS Industria Founder and Managing Director, Richard Jeffers, knows all too well.
Start simple, grow smart
“There’s a lot of hype around digital transformation. A lot of the messages focus on how it’s got to be significant and enterprise-wide but even for large companies that can be challenging,” Richard said.
The Manufacturing Technology Centre’s big focus for Smart Factory Expo 2023 is digital transformation
Andy Barnes, Director, Manufacturing Technology Centre (MTC)
“One of our key messages will be how digital transformation can be for everyone and you shouldn’t be put off by the jargon. You don’t necessarily need to become a digital specialist or data scientist to realise results.”
Start simple, grow smart is the message the RS team wants to once again portray this year, highlighting to manufacturers that you don’t need to spend large amounts of time and money to start reaping some of the benefits associated with digital transformation.
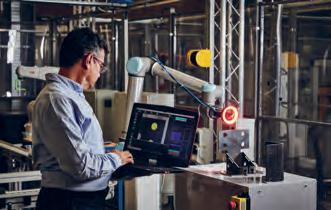
An example of how a simple change can lead to significant cost savings can be seen in RS’s work with a food and beverage manufacturer to set up alerts. It became evident that the main bearing on a high-speed canning filler was vibrating abnormally. Upon further inspection, the cause was found to be a blocked lubrication feed. This simple alert, which led to more scrutiny, saved the manufacturer somewhere in the region of £100,000.
BELOW: For 2023, RS Industria will be teaming up with other parts of RS Group in the UK and Ireland to provide a more holistic overview of how it can support organisations
A unified approach for 2023
Last year, RS Industria’s stand at Smart Factory Expo was a spectacle. From the sea of red uniforms, to the massively insightful video case studies and literature (not to mention free coffee), the amount of value on offer was incredible.
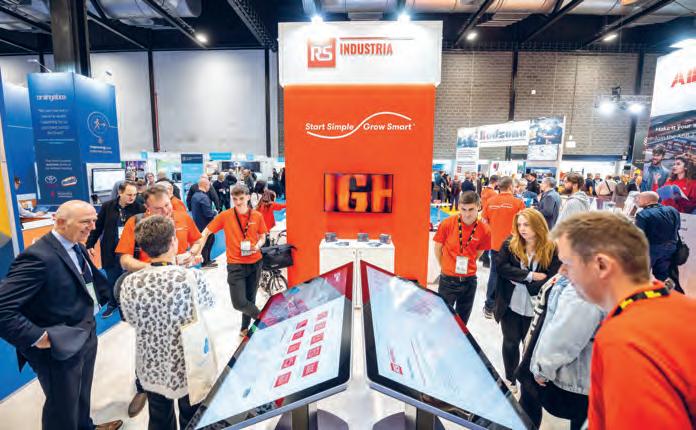
RS will be sharing a number of customer case studies, including ones involving Brompton Cycles where they’ve seen a tremendous amount of progress. Brompton spoke on RS’s behalf at Smart Factory Expo 2022; testimony to the great success the pair is realising together.
Measurement means money
As well as hosting a discussion session on advanced analytics at 11.00am on day one of the Manufacturing Digitalisation Summit (part of Smart Factory Expo), Richard will also be delivering a keynote speech. On the first day of the event at 10.25am, visitors can catch Richard’s presentation: 'Why Measurement means Money', to learn about the significant financial impact of using better information in managing factories, and the importance of communicating these high values to:
For 2023, RS Industria will be teaming up with other parts of RS Group in the UK and Ireland to provide a more holistic overview of how RS Group solutions can support organisations with numerous aspects of their digital transformation journeys and beyond.
Richard added: “In terms of the stand itself, we’ll be focusing on the practical application of digital transformation. Start with your number one problem, fix that and take it from there.”
• Gain the support of key stakeholders
• Create a sense of urgency to drive faster decision making
• Sharpen the focus on the rapid removal of barriers to implementation
Digital transformation is often so highly focused on the technology, that it can be easy to forget the core reasons for doing it.
Richard wrapped up our conversation by hinting that RS will likely make a significant announcement about their partnership with AWS. At present, RS is a certified AWS solutions provider for industrial IoT. Smart Factory Expo visitors can learn more about this partnership and find out how it can be beneficial to them.

7-8
If you’re attending Smart Factory Expo 2023, please visit the RS stand (C60) and talk with their experienced solutions engineers to discover how one simple change can begin a digital transformation journey which can deliver continuous improvement and reduce production losses – at a controlled pace and within a highly cost-effective budget.
Register for a free pass at www.mandeweek.co.uk/ manufacturing-expo-home
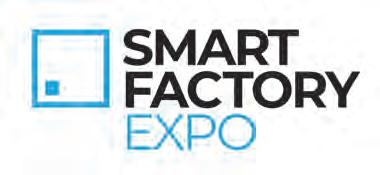
Education all areas
Readers of The Manufacturer cannot have failed to notice that Smart Factory Expo will be held at Birmingham’s NEC on 7-8 of June as part of Manufacturing & Engineering Week 2023 (www.mandeweek.co.uk)
n KEYNOTES
ABOVE: M&E Week promises to be a festival of industrial innovation
KEY TAKEAWAYS
• Manufacturing & Engineering Week will feature two Keynote Theatres and six Solutions Theatres
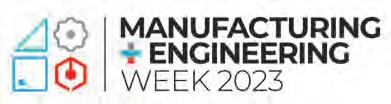
• Engineers Without Borders UK will be launching its Global Responsibility Competency Compass

• RS will be presenting findings from a recent survey of more than 1,000 maintenance professionals
• The Institute for Manufacturing (IfM) will be hosting its free educational Masterclass sessions
Smart Factory Expo (full preview article on page 6) will incorporate features such as Innovation Alley and associated events such as The Manufacturer Top 100, SME Growth Summit and the Manufacturing Digitalisation Summit. M&E Week also promises to be a festival of industrial innovation and in this article we look at some of the other elements taking place alongside Smart Factory Expo which readers might wish to plan in to their visit.
Education has always been a major part of the Smart Factory Expo experience, and this has only expanded through its integration into M&E Week. A major attraction of the show is the freeto-attend conference programme that will take place across two Keynote Theatres and six Solutions Theatres.
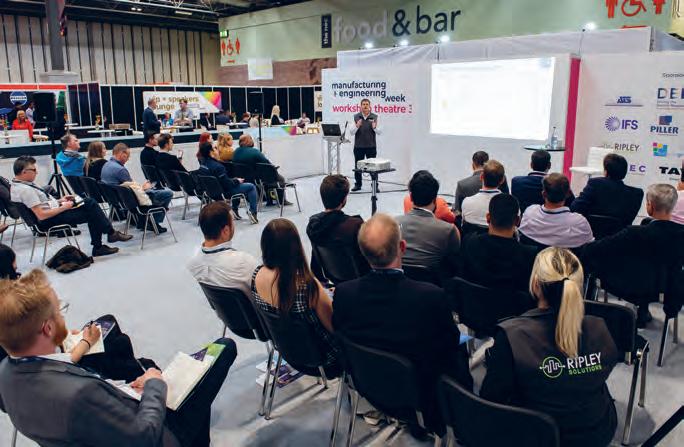
The first Keynote Theatre hosts a range of speakers and panel sessions on a wide range of relevant topics across both days of the event. The full programme can be viewed at www.mandeweek.co.uk/ conference-agenda. One keynote on 7 June that immediately catches the eye is from Katherine Bennett CBE, CEO of the HighValue Manufacturing Catapult. Speaking on the topic of Innovation as the Key to Business Transformation & Growth, the session discusses the importance of innovation to change manufacturing businesses for the better and includes examples of how Katherine has seen this working with companies that the HVMC are supporting. Also of great interest is the panel session on 8 June titled, The unstoppable rise of Digital Twins. This session, featuring Ben Wilkinson, Head of Digital Technology and Nipuni Karunaratne, Model Factory Manager, Rolls-Royce Civil Aerospace, covers Rolls-Royce’s introduction of a radical new business model in the 1990s that catalysed the development of early analytics. This grew over time into a connected ecosystem of digital twins and in this session, the panel will explore that journey and examine the cultural, behavioural and technological factors that enabled it.
The second keynote theatre is dedicated to the Maintec event. Maintec is the longest standing exhibition for the predictive maintenance, reliability and asset management industry and throughout its long history, the event has continued to focus on uptime and the tools, innovation, technology and people that support it - all topics that are dear to the hearts of The Manufacturer readers.
Delving into the Maintec Theatre agenda there are some real gems with everything from a session on the Commonwealth
SOLUTIONS THEATRES
Alongside the two keynote theatres there are, in addition, six Solutions Theatres. These theatres are again worth investigating by readers of The Manufacturer as the topics include key areas of interest: Automation & Robotics, Digital Transformation, IIoT & Connectivity, Industrial Data & AI, Innovation and Design Engineering. Additional free educational sessions are being hosted by the Institute for Manufacturing in the IfM Theatre. These Masterclasses are designed to challenge and extend the attendees' thinking in relation to some of the most pressing challenges and opportunities they face.
IfM uses research and frameworks developed at the University of Cambridge, so those attending the Masterclasses can gain practical insights and recommendations. IfM Industrial Practitioners have extensive expertise in supporting organisations across many sectors, and so are ideally placed to answer any questions and unpick problems.
The final timetable for this year’s Masterclasses will be released shortly
but previous strategic topics have included: Strategic Roadmapping, Technology and Innovation Management, Sustainability – Scope 3 Emissions, Sustainability - Reducing Energy Waste and Digital Strategy.

IfM Masterclasses require advance booking, and this can be done when registering for your ticket for Smart Factory Expo.
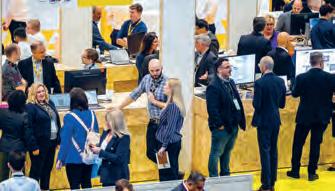
The week beginning 5 June 2023 is Manufacturing & Engineering Week with the centrepiece exhibitions, Smart Factory Expo, Design & Engineering Expo, Maintec and the Drives & Controls zone taking place at Birmingham’s NEC on 7-8 June. Other exhibitions are also taking place at the NEC during the week and these include Automechanika run by Messe Frankfurt, Med-Tech Innovation Expo and TCT 3Sixty from Rapid News Group, and Subcon from the Mark Allen Group.
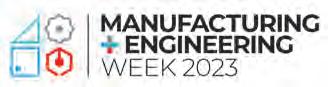
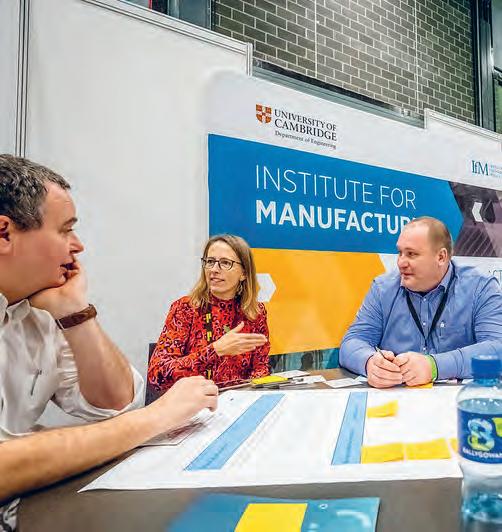
ABOVE: Innovation Alley will feature as part of Smart Factory Expo (full preview on page 6)
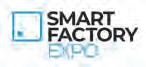
Games titled, Keeping the Games
Running, to a session on the critical role of maintenance in achieving net zero. RS is sponsoring the Maintec Theatre and will be presenting findings from a recent survey of more than 1,000 maintenance professionals as well as the Founder of RS Industria, Richard Jeffers, presenting a thoughtprovoking session on predictive maintenance as a way of life – not a technology.
In addition to hosting presentations on perennially important topics such as eliminating downtime, the theatre will also see several case studies presented as well as looking to the future of maintenance with papers and panel discussions on the role of AI and machine learning.
One conference session to mention (which is taking place in the Maintec Theatre) is from Engineers Without Borders UK. The keynote session on the afternoon of Wednesday 7 June will see the launch of a Global Responsibility Competency Compass. This session is focused on those struggling to respond effectively to the complexity, uncertainty and challenges of the age.
The action-oriented tool, developed through extensive consultation and testing, articulates the essential skills, knowledge and mindsets that engineers increasingly need to deliver the most positive impact on the four principles of global responsibility: responsible, purposeful, inclusive and regenerative. For those in manufacturing businesses who want to achieve something regarding their sustainability challenges then this session is a ‘must see’.
To register for a free pass visit:
www.mandeweek.co.uk
Digitalisation
How is it revolutionising the manufacturing industry?
In today's rapidly evolving business landscape, digitalisation has emerged as a critical driver of success for manufacturers. By leveraging digital technologies and tools, manufacturers can gain a competitive advantage by enhancing operational efficiency, improving customer satisfaction and enabling innovation. The Manufacturer’s Conference Programme Manager, Ashley Oulton, looks ahead to Manufacturing Digitalisation Summit taking place in Birmingham on June 7-8
Digitalisation is the process of integrating digital technologies into manufacturing processes, products and services to improve efficiency, reduce costs and enhance customer satisfaction. It involves the use of technologies such as the Internet of Things (IoT), artificial intelligence (AI), robotics and cloud computing to automate and optimise manufacturing processes.
Key benefit 1: Improved operational efficiency and sustainability
By automating routine tasks and leveraging data analytics, manufacturers can streamline their operations, reduce waste and errors and increase productivity. For example, IoT sensors can be used to monitor equipment performance in real-time, enabling manufacturers to proactively identify and address issues before they cause downtime or disruption and make adjustments to reduce their environmental impact.
Key benefit 2: Enhanced customer satisfaction
By leveraging digital technologies, manufacturers can gain insights into customer preferences and behaviours, enabling them to develop more targeted and personalised products and services. Digitalisation can also improve the speed and accuracy of product delivery, leading to greater customer satisfaction and loyalty.
Key benefit 3: Enable innovation by facilitating the development of new products and services
By leveraging data analytics and machine learning algorithms, manufacturers can
identify patterns and insights that can inform the development of new products and services. Additionally, digitalisation can enable the rapid prototyping and testing of new products, allowing manufacturers to bring them to market more quickly and efficiently.
What are the challenges and barriers to digitalisation?
Despite the benefits of digitalisation, manufacturers may face several challenges and barriers when implementing it in their organisations.
Challenge 1: The cost of implementing new digital technologies and systems
Digitalisation requires significant investment in hardware, software and training, which can be a significant financial burden for manufacturers, particularly small and medium-sized enterprises (SMEs).
Challenge 2: The need for a skilled workforce
Digitalisation requires a workforce with a range of skills, including data analytics, AI and machine learning. However, many manufacturers may not have the resources or expertise to recruit, train and retain such talent.

Challenge 3:

The need for a secure and reliable digital infrastructure
Manufacturers need reliable and high-speed internet connectivity, as well as robust cyber security measures, to ensure the safety and security of their digital systems and data. However, many manufacturers may not have access to such infrastructure or may lack the expertise to implement effective cyber security measures.
Challenge 4: Resistance to change among employees and stakeholders
Digitalisation requires a significant shift in mindset and culture, as well as new ways of working. Some employees may be resistant to these changes or may lack the skills or knowledge to adapt to new technologies and systems. Additionally, stakeholders such as suppliers and customers, may have their own preferences and systems, which may not align with the manufacturer's digitalisation strategy.
In conclusion, digitalisation is an essential driver of success for manufacturers in today's business landscape. By leveraging digital technologies and tools, manufacturers can improve operational efficiency, enhance customer satisfaction, enable innovation and make more sustainable decisions throughout their operations.
However, there are several challenges and barriers that organisations may face when implementing digitalisation, including the cost of implementation, the need for a skilled workforce, the need for a secure and reliable digital infrastructure and resistance to change among employees and stakeholders. Manufacturers must carefully consider these challenges and develop strategies to overcome them to fully realise the benefits of digitalisation.
Speaker's corner
Speakers and discussion leaders at Manufacturing Digitalisation Summit include:
Steve Penver, Group Head of Digital Integration, Babcock International
Clare Sibley, Head of Quality & Manufacturing Engineering, Williams Racing
Philip McNaughton, Head of Decarbonisation, British Sugar

Simon Martin, Head of Global Manufacturing, Yunex Traffic
Natalie Watson, Group Head of Sustainability, The Vita Group


Roy Pearson, NPI & Plant Engineering Manager, Gestamp
Paul Knight, Information Services & CISO, Turntide Technologies



Rashitha Jayasekara, Chief of Digital Manufacturing, Rolls Royce
Carl Haycock, UK Operations Director, Domino Printing Sciences
Alastair Henniker-Heaton, Manufacturing Systems Solution Architect, Johnson Matthey





The second annual Manufacturing Digitalisation Summit will be taking place in Birmingham on 7-8 June as part of Manufacturing and Engineering Week and several of the mentioned challenges will be discussed in our interactive roundtable discussion sessions.
Speakers and discussion leaders at the summit include senior digital, data, engineering and IT professionals from across the manufacturing industry.
Prasad Manorathna, Global Program Manager, Dover Corporation

Kallum Welch, Head of Manufacturing Engineering IS&S, Airbus

Suranjan Ghosh, Global Operations Director, Morgan Advanced Material

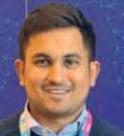
Steve Evans, Director of Research in Industrial Sustainability, IfM (University of Cambridge)
For more information on the Manufacturing Digitalisation Summit and to register your place please go to: manufacturing-digitalisation.com
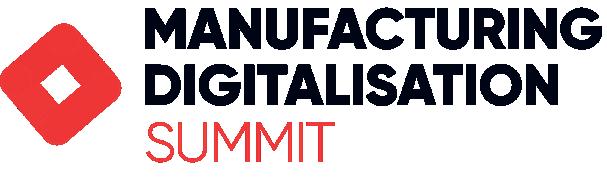
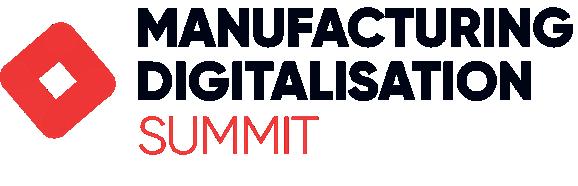
Despite the benefits of digitalisation, manufacturers may face several challenges and barriers when implementing it in their organisations
SUSTAINABILITY
At Manufacturing Digitalisation Summit, taking place at the Birmingham NEC on 7-8 June, Phil McNaughton, Head of Decarbonisation at British Sugar, will be giving a keynote around the decarbonisation challenges for larger manufacturers with dispersed industrial sites and how digitalisation can help. The Manufacturer Editor, Joe Bush, caught up with him to find out more
The sweet smell of decarbonisa
With a history that goes back more than a century, British Sugar is the sole processor of sugar beet in the UK, and the leading producer of sugar into the UK market. The organisation has four manufacturing facilities in the UK - three in East Anglia and one in Nottinghamshire – and is contracted to over 2,500 growers of sugar beet crop. The processed crop produces a range of co-products in addition to the primary sugar product, ranging from animal feed to bioethanol and electricity which is then exported to the national grid.
Can you explain more about your role at British Sugar?
PM: My role was created towards the end of the last calendar year to lead our decarbonisation activity across all areas of our business and operations; from agriculture and how we reduce the environmental footprint of farming, our factory operations and Scope 1 carbon emissions, right through to the supply chain and distribution side of our manufacturing activity.
Our focus to date has specifically been on Scope 1, but we're continuing to develop and understand our emissions around Scope 3. Scope 2 emissions are really minor for us as it only accounts for a small amount of imported electricity. My role is essentially to drive activity, coordinate and prioritise when necessary.
How big is the decarbonisation challenge for British Sugar?
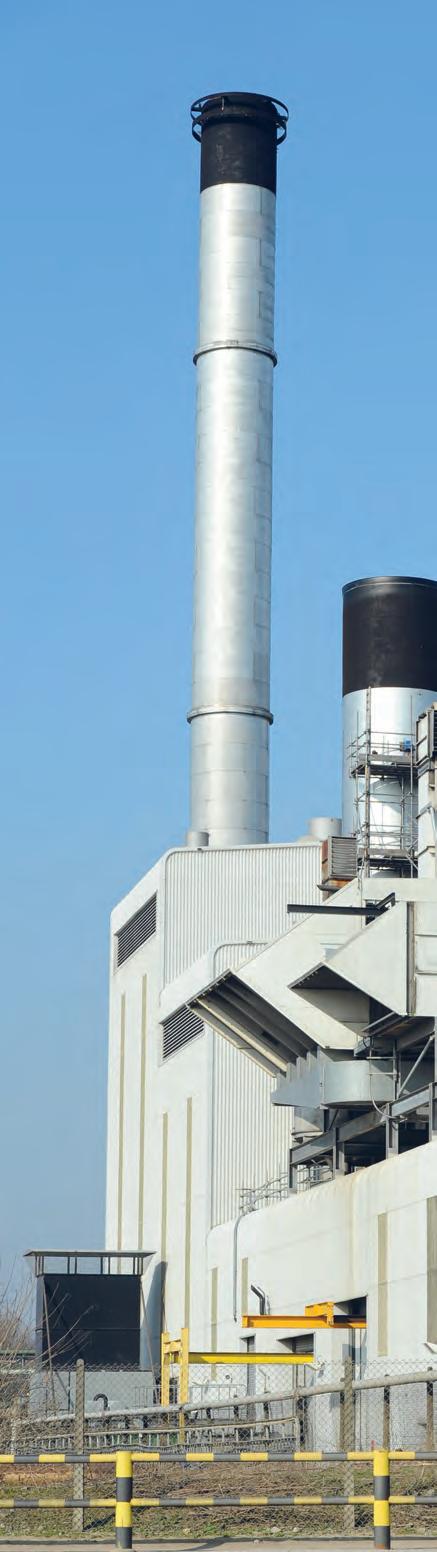
There’s no question that it is a challenge; but it's increasingly under the spotlight. Stakeholders have an increasing desire to understand how we drive our sustainability and ESG agenda, and carbon emissions are a big part of that. It's also become a much bigger question for investors in all sorts of organisations and businesses, us included.
In addition, it’s increasingly becoming a talking point with customers. The majority of the sugar that we produce goes into the industrial sector, but some does go through our sister retail business, Silver Spoon, and customers from both areas are increasingly wanting to understand firstly, what our carbon footprint is and secondly, what

we are doing to reduce our carbon and greenhouse gas emissions.
The focus on decarbonisation has increased to the point where we have included carbon reduction as part of our key strategic activities and workstreams when we reviewed them last September. And while we have activities around water reduction, packaging and plastics, carbon is seen, and has been agreed, as our priority around ESG.
How has the topic of decarbonisation changed for British Sugar over the past decade?
I've been with the business for almost 26 years and we've always had energy reduction and usage as a significant area of focus. Heat energy is a significant topic for us, driven by the fact that three quarters of sugar beet is water. Ultimately, to achieve the final solid product, that water needs to be evaporated and the product finished through a crystallisation process.
The heat energy required for that evaporation process is critical. We've made great strides over the last 40 years where we have reduced our energy demand by half. That’s been enabled through investment in new technology, efficiencies and continuous improvement activity. How's it changed more recently? Decarbonisation from a customer perspective has ramped up over the last two to three years which has been driven, ultimately, by our customers and consumers, and is only going to increase in the years to come.
Questions are now being asked in earnest around what our carbon and greenhouse gas emissions are, what do we measure? How do we measure?
And, importantly, are we improving and what are we doing to reduce emissions further? The landscape has certainly evolved, not only in terms of there being much more interest in the subject, but also around the need to articulate what our decarbonisation plan is, how it will be achieved and whether we’re on track to do so.
Head of Decarbonisation, British Sugar
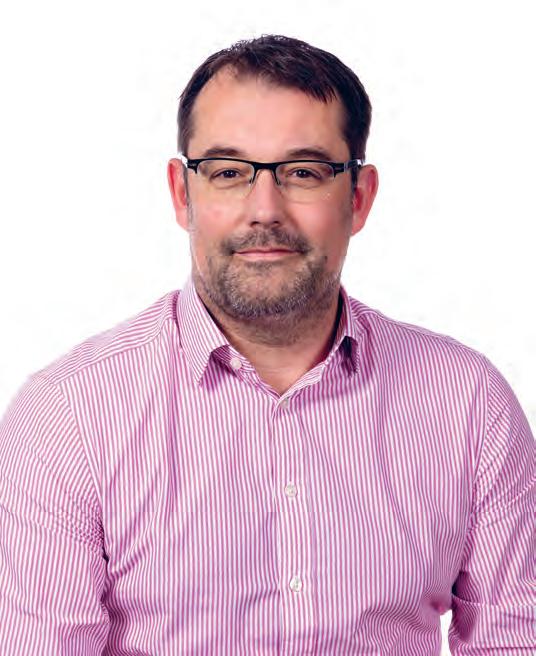
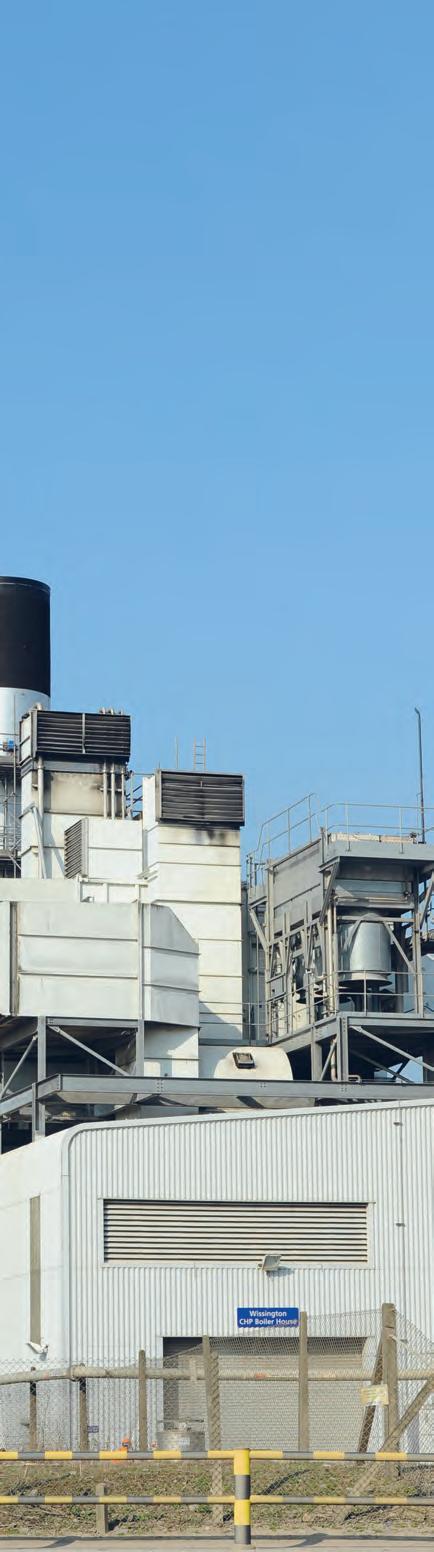
We've seen ESG and related activities becoming more important right the way through the supply chain, to consumers and supermarkets etc. What marries that desire to improve company credentials in terms of performance around ESG, is how to achieve it in a financially neutral or positive way. Opportunities exist but we need to ensure that as a business we're

While we have activities around water reduction, packaging and plastics, carbon is seen, and has been agreed, as our priority around ESG
Phil McNaughton,
investing in the right long-term solutions. A vital balance has to be struck around how you can improve on your ESG, but also maintaining good bottom line profitability to encourage that reinvestment into improvement as you go forward. There’s a lot of desire, not just in our business, but in industry more broadly, but despite that good intent, after a while those goals can become more challenging from a financial point of view.
In terms of regulation, there are a number of areas that are governed by the Environment Agency. and understanding around climate change adaptation will need to be demonstrated. The main piece of regulatory or compliance pressure for us is around the UK Emissions Trading Scheme (UK ETS); accounting for and ensuring verification of greenhouse gas emissions annually from the burning of fossil fuels.

Additionally, the financial burden associated with regulatory compliance has increased significantly over the last decade. It was a relatively small amount of
expenditure eight to ten years ago. That’s certainly one driver to decarbonise, but clearly you can't do everything overnight.
Your keynote address at Manufacturing Digitalisation Summit will be around the decarbonisation of dispersed industrial sites. Can you give a flavour of the talk and some of the key takeaways?
All four of our sites are dispersed in nature in terms of classification (dispersed being a certain distance away from a track one or track two supported government cluster). All our sites are quite a significant distance from each respective nearest cluster, so we don't anticipate any direct benefit.
We try and lobby and advocate to a number of groups, including directly with government, around support for dispersed sites, from which around half of the industrial emissions in the UK are sourced.
The advent and deployment of Industry 4.0 will evolve British Sugar; we will embrace it and it will ultimately support improvement and efficiency in our existing operations
Phil McNaughton, Head of Decarbonisation, British SugarABOVE: British Sugar also has sites in Cantley (above) and Newark (bottom right)
Some of the challenges that we have, particularly in East Anglia, are around the strength of the electricity and gas networks. If we wanted to move to electrification on-site for example, and away from natural gas usage, with the intent of being able to import more green electricity from the grid, that's a real challenge as the infrastructure isn't sufficiently developed at this moment. And that'll be the same for other industrial operators in the region.
Furthermore, around infrastructure, if I was to highlight hydrogen as an example, the infrastructure isn't developed yet in this country, and we don't really know how it’s going to look. Hydrogen will come into track one and likely, track two government supported clusters, but in terms of deploying hydrogen into areas like East Anglia and other more remote regions where dispersed sites are operating, we’re probably 20 years away.
In terms of our decarbonisation plans, our priority is to try and reduce our energy usage, primarily through steam reduction, to as low a point as we can get. Then, when we do find the right opportunities to change from natural gas, we'll do so at a point where we’re using the minimum amount of fuel possible. We've got a number of steam reduction projects which we’re progressing and developing within the business across all four sites.
We’re also looking further out at the different technologies and fuel options that will enable us to change from natural gas in the future. My position, and British Sugar’s, would be that it's likely to be a blend of fuels and technologies that we’ll need to deploy across the four sites, and maybe within the same site, in order to get to the point where we can ultimately decarbonise.
For manufacturers operating multiple and dispersed sites, what are some of the challenges when it comes to decarbonisation?

To an extent it depends on where your sites are located and if they are genuinely dispersed. For those that are, there are challenges around availability through networks of alternative fuels. So, if you are a dispersed site, and you're getting
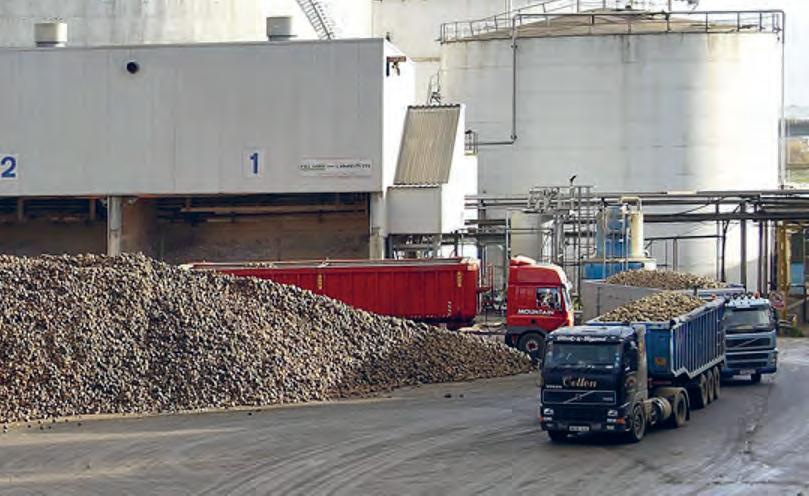

on with fuel switching today, and in the years to come, you're likely to be doing it off grid. And you're probably tying up with a third-party who is offering that deployment for you on a variety of different levels of ownership.
That again depends on location, appetite and whether you've got other significant energy users in the same area that might join forces with you to make that type of investment and project more attractive for yourself and any thirdparties you may be working with.
Quite frankly, the more remote you get, the more challenging this becomes. And while there are end of pipe technologies, such as carbon capture and storage, we're fairly agnostic on that, because it doesn't genuinely reduce the burning of fossil fuels and emitted carbon.
Our position would be that, as a first port of call, we want to try and reduce the quantity of fossil fuels we're burning to reduce our greenhouse gas emissions at source, rather than having to adopt a technology that might capture the carbon and put it into storage.
What part can technology and digitalisation play to help address this?
We’re just starting to discover some of the options and opportunities that Industry 4.0 may offer and we’re collaborating with an external partner to help us do that.
We've identified six areas of work activity and assigned leaders to each one. Through the increasing level of automation that we've deployed across our sites in recent years, providing operators the ability to control the plant remotely on digital equipment, we're now set up with a much better infrastructure. We're now trying to test and work out how we take maximum advantage of that to improve the consistency of site operations, and look for opportunities that can be deployed across all sites that gives us the best options for repeatability and consistency.
We're learning in this space, but I think there’s a massive opportunity both in terms of generating better data and how we use it to improve, but also, how that data is used specifically for energy performance. We will identify opportunities, we just don't know what they are yet, but we're fairly confident they will come.
How is the company using renewable energy sources?
It’s currently quite limited because of the size of energy demand that we have. However, there are a couple of areas that are worth highlighting. We have a 5MW anaerobic digestion plant at our Bury St Edmonds site. Pressed pulp, which is what remains after we’ve extracted sugar out of the sugar beet, is then fed into that anaerobic digestion plant. The green electricity generated is injected directly into the network.
The majority of our pressed pulp is dried, pelleted and then sold into the animal feed market in the UK, and therein lies one of our internal conflicts. That actually generates revenue for us with one of our sister businesses. However, going forward, if we want to put that material into anaerobic digestion instead, we will have to give up that revenue and find how that imbalance is addressed elsewhere.
We also have a couple of small solar PV installations. Again, solar PV is one of the areas and potential projects that we are currently reassessing because technologies change in terms of their viability and what’s available.
It is also worth underlining the credentials that we have around good quality, combined heat and power (CHP) plants. All of our sites have a CHP scheme, and obviously, for an overall electricity and heat supply, that maximises the efficiency and utilisation of that input fuel.
A standalone power station generating electricity would be at a much lower overall efficiency than our CHP schemes deliver in terms of useful heat and electricity, which is pushing around 80%.
What does British Sugar’s decarbonisation and digitalisation future look like?
The advent and deployment of Industry 4.0 will evolve at British Sugar; we will embrace it and it will ultimately support improvement and efficiency to a greater level in our existing operations and our continuous improvement. That will help us from an energy utilisation point of view.
I think it might also help identify opportunities where we can look for investment and highlight areas where there is lower performance. In terms of marrying that with a decarbonisation future, I think there's lots of known technology, particularly within the sugar arena, that we might consider deploying that will help us ultimately reduce energy and decarbonise.
I can see that Industry 4.0 will also help support alternative, lower carbon emitting fuels. When we start to look at alternatives, I would expect digitalisation to be a part of that process. I can also see us having to be much more flexible in terms of switching between different
fuels, particularly as we transition from a carbon emitting business in terms of the fossil fuel that we're burning, to ultimately one where we're using clean fuels and we've decarbonised.
That's clearly a few years and decades away but digitalisation will help us through that period and to optimise the decarbonisation aspect of the business. It will also help us to marry that with the commercial and financial side of balancing what fuel to use, when and how to generate electricity, and potentially continue to export some of that energy to the grid.
It's a challenge, because we're not quite sure how we’re going to get there but I'm absolutely certain that digitalisation will have a part to play in how we go forward and we will understand that better over the next two or three years.
KEY TAKEAWAYS
• British Sugar is a significant user of natural gas and there is a high heat and electricity demand from each of its four sites in the UK
• Carbon reduction is now a part of British Sugar’s key strategic activities and workstreams
• Over the last 40 years British Sugar has reduced its energy demand by half via investment in new technology, efficiencies and continuous improvement activity
• The importance of decarbonisation from a customer perspective has increased over the last two to three years
• Industry 4.0 technologies have created an improved infrastructure for decarbonisation at British Sugar
Manufacturing digitalisation Summit will take place at the NEC, Birmingham on 7-8 June. To register your place visit: manufacturingdigitalisation.com
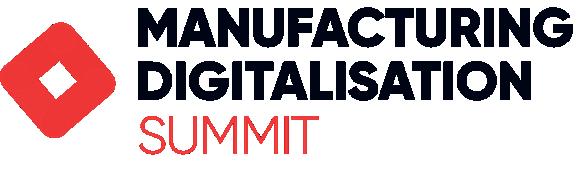
In terms of decarbonisation, we're not quite sure how we’re going to get there yet, but I'm absolutely certain that digitalisation will have a part to play in how we go forward
Phil McNaughton, Head of Decarbonisation, British Sugar
DISCOVER TECHNOLOGY BREAKTHROUGHS AT THE MADE SMARTER INNOVATION ALLEY
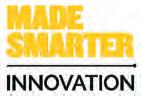
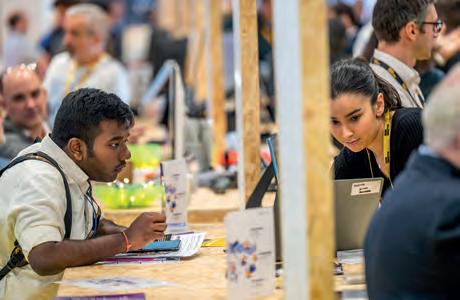
MADE SMARTER INNOVATION ALLEY:
Located at the very heart of Smart Factory Expo (7-8 June 2023, NEC, Birmingham), Made Smarter Innovation Alley is the largest showcase of leading edge digital technology start-up and scale-up in the UK that will change the landscape of manufacturing over the next 5-10 years.
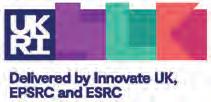
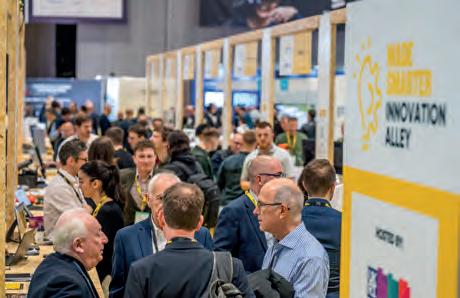
Funded by Innovate UK and supported by Innovate UK KTN, the Alley is open to university spin-outs, start-ups and scale-ups who are less than 5 years old, employ less than 10 members of staff and have an innovative digital product or service targeting manufacturers.
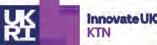
Meet 40+ companies with innovative digital manufacturing technologies in AI, machine learning, additive manufacturing, sensors and blockchain, robotics, immersive technologies and IIOT across multiple industry sectors including medtech, chemistry, defence, nuclear, automotive, aerospace, food and drink and others.
DON’T ALSO MISS:
Visit the Innovation Village to connect with the Innovate UK innovation ecosystem and be inspired through funding, collaboration, investment, and leading-edge research to support the aspirations of the UK’s manufacturing industry.
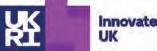
Meet and engage with early-stage companies and their founders to uncover bleeding-edge disruptive technology that could be gamechanging for you, your product and your business in the future.
REGISTER A FREE PASS TO ATTEND www.mandeweek.co.uk
Funded by:
Supported by:
A PERFECT 10 FOR THE
This year sees The Manufacturer celebrate the tenth anniversary of the Top 100; the awards programme which celebrates the inspiring individuals who are shaping the manufacturing sector in the UK
From Young Pioneers and Unsung Heroes to Inspiring Leaders and Innovators, the Top 100 is a showcase of the very best talent the sector has to offer, as judged by an esteemed panel featuring leaders of industry, academic institutions and manufacturing associations.
In this article, The Manufacturer Editor, Joe Bush, takes a trip down memory lane for a catch up with three of the original 20 Exemplars from the very first Top 100 intake in 2014: Jan Ward CBE, Founder of Corrotherm, a supplier of seamless pipes, tubes, fittings and flanges; Richard Lloyd, General Manager of wines and spirits company, Accolade Wines; and Adrian Maxwell, Managing Director of cappuccino and espresso coffee machine manufacturer, Fracino.

What was it like to be named as an Exemplar in the first ever Top 100?
JW: It was a lovely surprise because I wasn't expecting it. There's a sense of achievement because you've been recognised for the work you do, but being named in the Top 100 is also a really good way to link up with other people.
You've got something in common with others named in the same cohort. You get talking and it actually leads to business opportunities and access to information that you can use to improve your business. It was also great to see manufacturing acknowledged and the profile of the sector being raised in the public domain.
RL: To be in the first year to be selected in the Top 100 was amazing, but to then be named in the Exemplar group was incredibly flattering; it's something I've always cherished. I've attended most years since and seen the calibre of people that have been added. It was just magical to be there from the start.
It’s always good to have some external recognition as a verification of your standing. Being an Exemplar in the Top 100 also gives you an air of credence when you’re in a group of people and part of dynamic business discussions.
AM: It is very prestigious to be in the Top 100; it has helped us win other awards and market the company. Before being nominated we were fairly unknown, now we’re being consulted around policy, which is absolutely incredible – government are actually looking to us. Being recognised by The Manufacturer was a catalyst for that and it really helped us promote the business and push it forward.

In addition, it’s really helped us from the perspective of being in a global market. Recognitions like this give us extra kudos and credibility with potential customers. We didn’t export a single product until 2009; now our export market represents around 35-40% of our turnover.
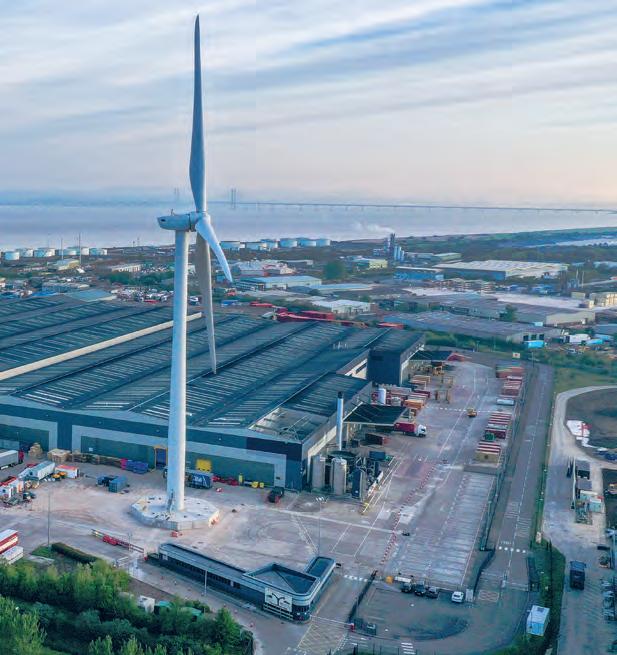
JW: The Top 100 programme is more important to the sector now than ever before. It's absolutely vital as we can see all too clearly how unstable the UK economy can become if it’s totally reliant on services, which it has been. The Top 100 is key to promoting the industry and encouraging youngsters to get involved; to show that working in manufacturing can be successful and enjoyable.
What impact has The Top 100 had on your career?
RL: There have been some big milestones that have come about from our relationship with The Manufacturer. We always attend their events as a group because it’s really important to hear different views, ideas and see different technology; we can discuss, meet people and discover what works for us.
We’ve introduced 3D printing of our spare parts, AI and machine learning, totally off the back of being at The Manufacturer events and meeting other suppliers and likeminded businesses. Our business has evolved with technology and for me, The Manufacturer and The Manufacturer Top 100 has provided the platform to help us grow.
JW: Being in the Top 100, using the network and attending events hosted by The Manufacturer has opened up a number of opportunities for me to meet and talk to other people and companies. That collaboration is really useful.

As manufacturers, we're naturally curious, but that is enhanced by being part of the Top 100 as there’s nothing like the face-toface sparking of ideas across platforms and people. The other huge bonus of being a Top 100 Exemplar is that it has enabled me to see other factories, which is my favourite thing to do.
The programme brings you together with people that you wouldn't necessarily have met under normal circumstances. It enables you to get involved and understand more about what others are doing in areas beyond your sector, but which can still influence what you do.
I also like the fact that the Top 100 puts forward people that wouldn't necessarily be acknowledged – the Young Pioneer and Unsung Hero categories for example; the people that work in the
Our business has evolved with technology and for me, The Manufacturer Top 100 has provided the platform to help us grow
Richard Lloyd, General Manager, Accolade Wines
background to keep production rolling, doing the jobs that are not necessarily high profile. It's not all about the chief executives and members of the board.
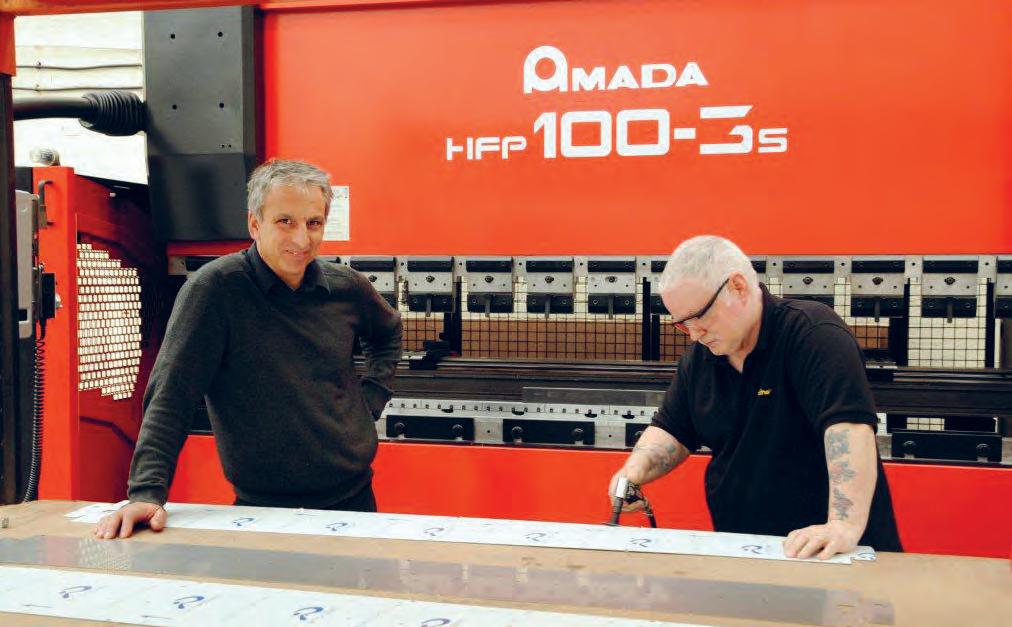
When you get the title of being in the Top 100, it puts you on the same level as everyone else in that year’s intake. People from a large automotive OEM, for example, wouldn't necessarily be speaking to a small manufacturer from the Midlands. But when you're in the Top 100, you all come together.
AM: I still like to be very hands-on, although I don’t have as much time to do so as I once did. I oversee and run the business, and I have a core team that run each department and report into me. I’ve constantly learned new skills as the business has grown,
and I always listen. That’s something my father taught me. You don’t have to agree with what’s being said, but as long as you’re listening, you’re always learning.
RL: I’ve become more of a generalist since being included in the Top 100. I’m lucky now that I have full supply chain end-to-end responsibility. The huge advantage of that is having the skill set to be able to bring a group of different functions together and make sure they are optimised as a whole.
When looking after just one function, you’re very focused on optimising that one area, and rightly so. But my career has now become one of building a leadership team and making sure we provide that end-to-end supply chain offering for our customers.
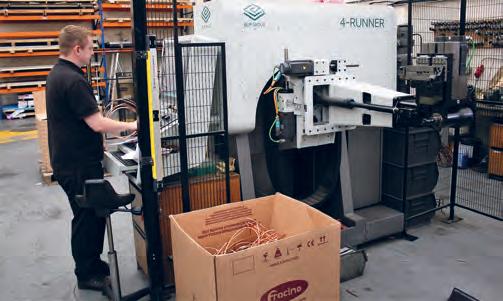
The Top 100 has really helped us from the perspective of being in a global market. These recognitions give us extra kudos and credibility with potential customers
Adrian Maxwell (above left), Managing Director, FracinoBELOW: The fabrication of copper tubing at Fracino
How has the landscape of manufacturing changed in the last decade?
JW: Automation and digitalisation have been huge. However, in truth I'm disappointed it hasn't come further. But I am aware of the barriers that exist for small businesses and how hard it is to find the necessary skills to enable the rollout of such technology. That demographic of people and the infrastructure that will enable this to happen, is not going to grow quickly, and perhaps the two years of the pandemic and the aftermath has caused further delays. Small businesses know that it's something they should be doing but they can sometimes get overwhelmed. So again, talking to other Top 100 members helps to gauge some perspective and see what can be done. And there are offers of help as well.
The bigger companies will try to assist smaller businesses or introduce them to people that can. There’s certainly a desire for digital transformation by most small manufacturers, and they are aware of the fact, particularly with labour shortages, that automation and digital is the way to go.
There's also a very robust discussion being had around what can be achieved with net zero. There are lots of things that people can do, but they all cost money. So sharing information about how this can be done cheaper and more incrementally is key.
It's a case of trying to work out what's affordable for you so you can take those small steps, because it's not possible for everyone to leap into it and convert everything straightaway, especially if you have inherited assets that are quite old. However, the Top 100 gives you the opportunity to sit down and talk with people who are perhaps further along the journey and offer ideas of what you can be doing yourself.
RL: Sustainability has grown massively. That’s why we’re now a carbon net neutral facility; we have the country’s largest wind turbine, we 3D print machine parts using one of our waste streams and we move all our vehicles around the site on hydrated vegetable oil (HVO).
We have had to evolve our offering and the way we work. The cost pressures that have grown recently have meant that productivity improvements are more important than ever. Our ability to embrace technology and take cost out where we can has been critical, but the core purpose of delivering value for our customers has ultimately, remained unchanged.
We embraced sustainability and found it has had an economic benefit. Our 2.5MW wind turbine, which was put up in 2019, provides 50% of our electricity for the site. And when you compare the cost of that electricity against the grid, it’s about a quarter of the price.
There’s been a number of different pressures but, if you keep embracing new technology and partner with businesses that help you optimise and drive forward, you can stay ahead of the game. The initiatives we’ve rolled out mean we are more resilient to some of the external factors impacting the sector.
AM: We’ve been working on environmental issues for quite a long time. We installed solar panels around eight years ago, and at the time were able to take advantage of the buy-intariffs. That means we can use all the power we generate and get paid for it, which is absolutely wonderful.
That was a 25 year contract so it is still ongoing. The solar panels are paid for following our initial outlay of around £40,000. That demonstrated foresight on our part and you can’t underestimate the importance of reinvestment; it really is a no brainer – particularly at the moment with the current energy
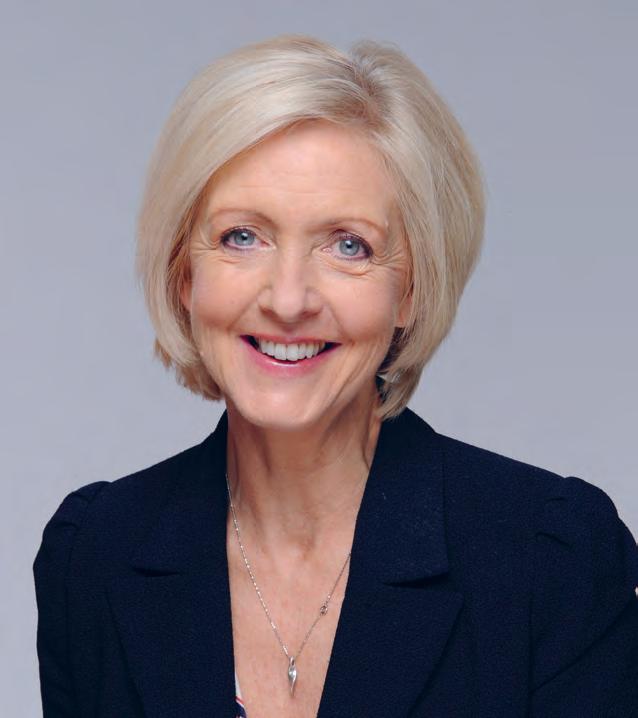
The Top 100 programme is more important to the sector now than ever before. It’s key to promoting the industry and encouraging youngsters to get involved; to show that working in manufacturing can be successful and enjoyable
Jan Ward CBE, Founder, Corrotherm
crisis – so the measures we implemented a few years ago have been an absolute godsend.
We also recycle all our metal and our machines themselves are 96% recyclable. We recycle all our own cardboard and reuse all our own waste. We recycle everything we possibly can, even down to our own oil.
A key purpose of the Top 100 is to raise awareness of the sector and help reduce the skills gap. How has this particular problem shifted since 2014?
AM: We see evidence of the huge skills shortage across many facets of the industry. If we need something done that’s physical or practical, we’re finding that the vast majority of people available are from an older age group.
We do have young people but we find that we really have to pull them along as often, they’re not that keen on the work. I blame the education system to a certain extent as young people are pushed into and coached for exams, which doesn’t provide them with the practical skills needed for a career in manufacturing - they can't think around a problem and often don't know how to communicate.
Of course, we find some young people who aren't very good at school and struggle with academia, but they've got great practical skills. They’re the ones we try and get hold of quickly because they are unusual. The education system needs to recognise that we’re not going to be able to fill the skills gap unless we have those practical courses.
CNC machinists are so hard to find. We have someone who’s semi-retired that's running our machines; we are struggling and are just managing with what we've got. Something needs to change. And I think it probably needs to start at school, because education tends to portray ‘engineer’ as a dirty word.
It’s a completely different sector now. You can be working with some pretty high-tech pieces of equipment and machinery, producing some amazing finished products. However, there’s still not the right links between school and industry to bring the two together.

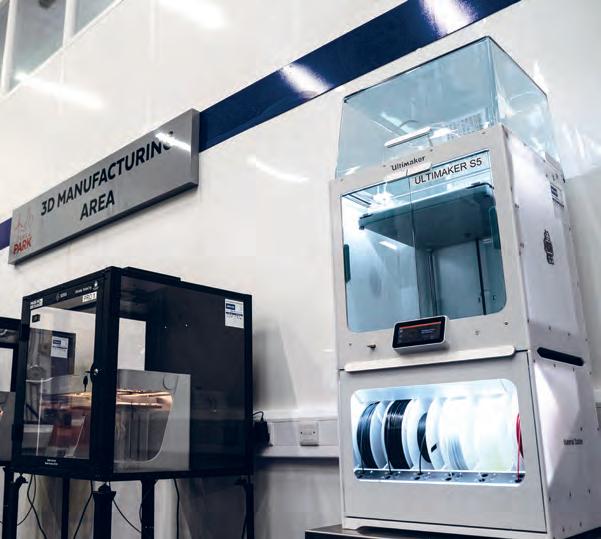
JW: Unfortunately, I don't think that the skills gap has changed much in terms of the volume of people coming into the sector. We haven't had the big influx into the industry that would have been desirable. And we’ve also had the retirement issue that we knew was coming and is still ongoing.
COVID certainly made that worse – an estimated half a million early retirees left the labour force due to the pandemic and I suspect quite a high number of those came from manufacturing.
The sector is performing a lot better than it was a decade ago and I don't think the gender gap is as big a problem as it once was. However, the main issue is still around attraction and the pull of other sectors has made it harder to recruit young people.
I don't think the industry has done a bad job of putting itself out there, but the skills piece is still not where it needs to be and we're not getting the feed of people with the right level of skills coming into the sector, particularly in mathematics and physics. So companies are having to take pretty raw recruits and train them themselves.
All of that said, I do think that going digital and the adoption of automation has helped to recruit more young people by
quashing that image of the sector being all about oily rags and overalls, and showing youngsters that are training now and thinking about degrees, the truth about the industry.
We need the universities to step up and show what is possible in manufacturing. Unfortunately, teachers and parents are often way behind the times when it comes to knowing what manufacturing is about. Parents generally don't understand what real, modern manufacturing means in terms of a career and it's up to the institutions to get that message across.
However, I’m afraid that many universities are behind the curve. Many of the engineering departments are not well funded, don't have the necessary equipment, and are therefore, not up to speed with what's going on. The universities are also failing to recruit the right sort of people. Former manufacturers need to be doing the teaching; giving it to professors that have only ever been in academia is not good for manufacturing.
In the past, I’ve found resistance to modern methods when I've visited universities (3D printing for example). If it’s a technology that’s not understood, then it’s not going to be wanted in the university department. There are notable exceptions of course - places like Brunel, Manchester and some of the Scottish universities especially. But I think in general, there's a very big gap between what the lecturers know and want to do, and what's actually needed by industry.
2023
The Manufacturer Top 100 Awards ceremony will take place on 7 June as part of Manufacturing & Engineering Week. Visit www.mandeweek.co.uk/ manufacturing-expo-home to register.
MORE NEWS.
MORE MEDIA .
MORE INSIGHT.
DIGITAL BRIEFING
The Manufacturer Digital Briefings are published twice weekly for the latest information, innovations & insights in manufacturing, sign up now.
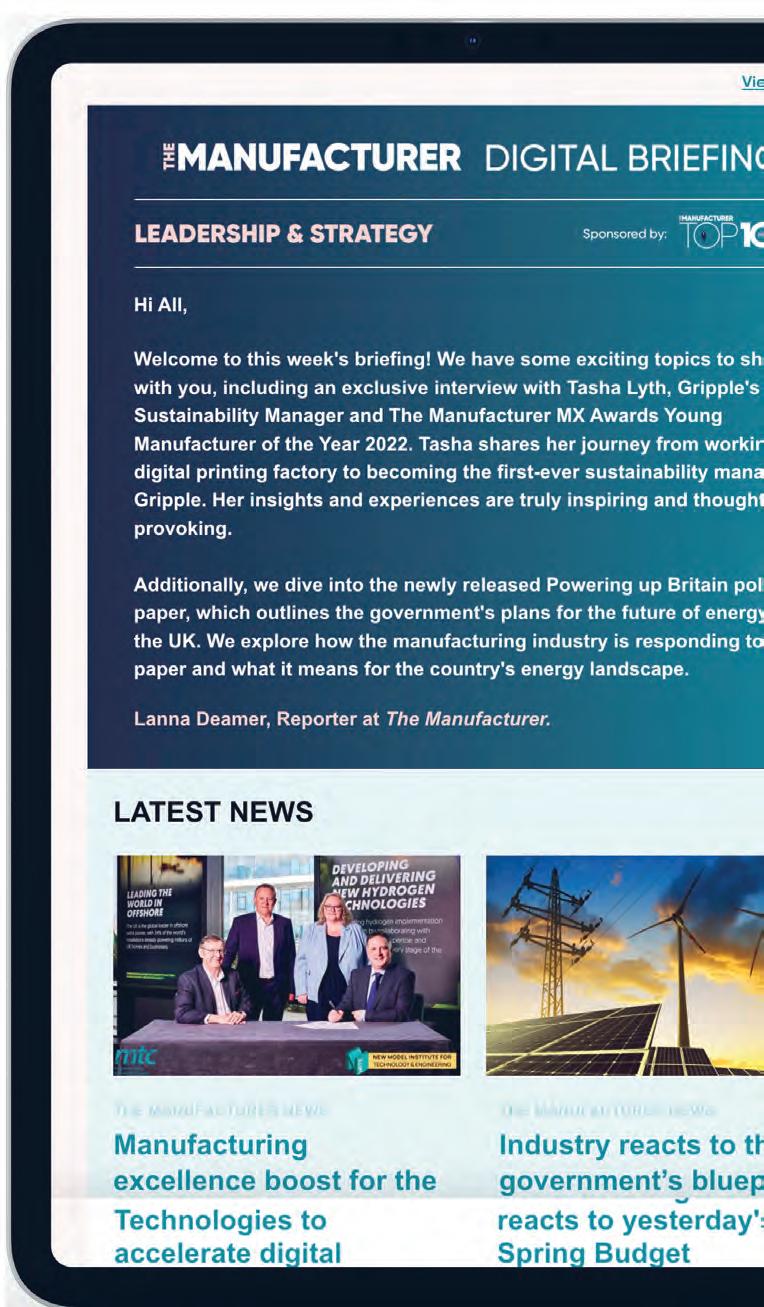
For many, quantum computing may appear to have parallels with nuclear fusion: a technology with great potential but with no provable benefits despite decades of costly research.

However, beyond the hype and the theory, there will be plenty of real-life, tangible opportunities for manufacturers to solve critical business challenges more quickly and cheaply, and it is important to be aware of the threat that quantum computing offers to some encryption schemes. There’s already lots to read online and plenty of organisations, including Digital Catapult, that can help manufacturers dip their toes into the quantum water.
1. Why do we need quantum computing? Despite the massive increase in computing power which defines our modern world, there are still some tasks classical computers can’t handle well. For example, developing a room temperature
things you need
to know about quantum
LEFT: Despite the massive increase in computing power which defines our modern world, there are still some tasks classical computers can’t handle well
superconductor would help solve the world’s energy problems yet research is blocked, in part, because classical computers can’t simulate quantum systems with many entangled particles.
Medical research also suffers because classical computers can’t simulate large molecules accurately. Optimisation and machine learning algorithms are sometimes limited by computing resource constraints. Quantum computers will, it’s believed, solve some of these difficult problems in the future, due to their fundamentally different computing paradigm.
2. How will quantum computing affect my industry?
Today’s Noisy Intermediate Scale Quantum (NISQ) devices have, at most, a few hundred qubits, and these are very error prone. In the current NISQ era, Variational Quantum Algorithms (VQA), where a quantum computer is ‘trained’ by a classical computer, are likely to be used for a wide range of functions:
• Optimisation: Solving a wide range of real-world problems such as finding the best configuration for telecoms networks, optimal vehicle routing for last mile delivery, optimising supply chains and factory flows.
• Machine learning: Particularly for anomaly detection to find manufacturing faults.

• Computational fluid dynamics: Calculating fluid flows around vehicles to make them more aerodynamic.
The ‘holy grail’ of modern research is to build a large, universal, error corrected quantum computer, which could in principle run any quantum algorithm; with many positive societal impacts including revolutionising the challenge of climate change by discovering new materials for solar cells, batteries and even room temperature superconductors.
3. Which industries will benefit the most in the short-term?
Multiple industries with complex supply chains will benefit from the ability to carry out better optimisations than are possible classically, and these are likely to be the first commercial use cases, with quick and significant paybacks.
At Digital Catapult, we’re supporting sectors including energy, construction, automotive, transportation, advanced manufacturing, material science and telecoms to determine how companies in those sectors will gain a competitive advantage by understanding the future benefits and applications of secure quantum computing for their industry, upskilling their employees and encouraging innovation. For example, quantum computers are being used to develop next-generation batteries, and the aerospace industry will benefit from digital twins enabled by quantum fluid dynamics simulations.
4. How does quantum translate into economic opportunity?
Many businesses will benefit from improved quantum chemistry, fluid dynamics, machine learning and optimisation. These businesses will need to purchase not just a quantum computer, or cloud access to a quantum computer, but ‘the complete product’. They may need to purchase consultancy, to understand which problems are amenable to quantum computing, quantum software and the rights to use quantum algorithms.
The quantum computer manufacturer will themselves need to source essential supply chain components such as dilution refrigerators, lasers, semiconductor nanostructure design and manufacture and microwave generators, and depend on scientific research. All of these transactions provide an economic opportunity and build a quantum eco-system.
5. What is a quantum computer?
Quantum computers depend on quantum effects only relevant at small scales, that we don’t see in our day-to-day lives. For example, a normal egg-timer starts off full, and then gradually empties as the sand drains out. The quantum equivalent, at the atomic scale, is completely different. A radiation pulse will cause an atom to transition between excited and ground quantum states, like the egg timer.
Because in quantum mechanics energy comes in lumps, or ‘quanta’, after a pulse of appropriate length, the atom is found with equal probability in the excited state or in the ground state. The pulse has placed the atom in a ‘quantum superposition’ where it is in both the excited and ground states at the same time. The atom can be considered to be a ‘qubit’ - the quantum equivalent of the classical computing bit.
6. How is quantum computing different from normal computing?
A bit used on normal, or ‘classical’ computing, is only ever in one of two binary states, 0 or 1. Because of superposition, a qubit holds much more information. In a quantum computer, parallel processing over many qubits in superposition can give huge benefits over classical computers for some computations problems.
7. What is quantum supremacy and why does it matter?
Google claimed quantum supremacy when a superconducting quantum device with 53 qubits carried out a computation that could not be performed on a classical computer. The use of the word supremacy is now generally considered inappropriate because of its political connotations.
The computation had no business value and the error rates were high: nonetheless, this important demonstration hinted at
Quantum computing will give manufacturers the opportunity to solve critical business challenges quicker and cheaper
Daniel Goldsmith, Quantum Technologist, Digital Catapult
future quantum business advantage, where it will be cheaper or more convenient to use quantum computations for some applications.
8. How far are quantum computers from being commercially viable — or actually being able to make an impact?
Most experts believe that quantum computers are three to eight years away from being commercially viable for some applications, and that universal, fault tolerant computers are at least a decade
away. Some would say that quantum computers are already making an impact. There is at least one large company that has not fully operationalised a quantum optimisation programme, yet finds it helpful to run the algorithm daily to gain valuable insights into the best way to configure equipment routings through the maintenance organisation.
9. Who will quantum computing capabilities be available to in the near future?

Anyone can access a quantum computer at present. For example, using Qiskit it is possible to program a quantum circuit with a few lines of python code and submit this on a small IBM device. Large cloud computing vendors, such as Amazon Braket and Microsoft Azure enable cloud access to quantum hardware vendors, and manufacturers like D-Wave, and others, sell access to their devices. Digital Catapult is running a quantum technology access programme later this year.
10. How is the UK positioned to compete in the quantum computer industry?
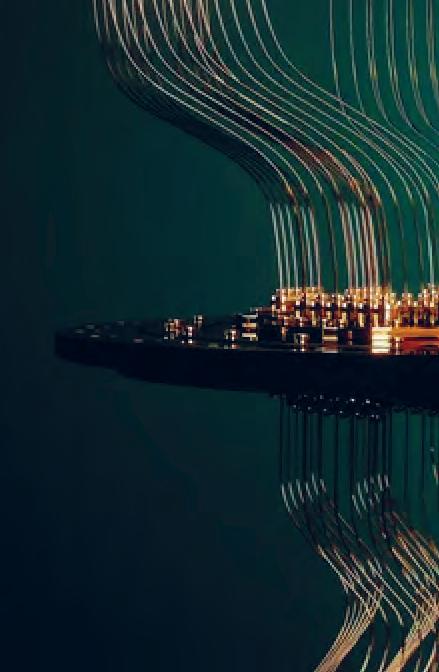
The UK made an early start in funding quantum research, with total investment exceeding £1bn since 2014, and in March 2023 announced a new ten year National Quantum Strategy and committed to £2.5bn to developing quantum technologies in the UK over the ten years from 2024. The National Quantum Computing Centre (NQCC) reports that the UK is joint fourth in quantum programme delivery and second in quantum technology commercialisation globally.
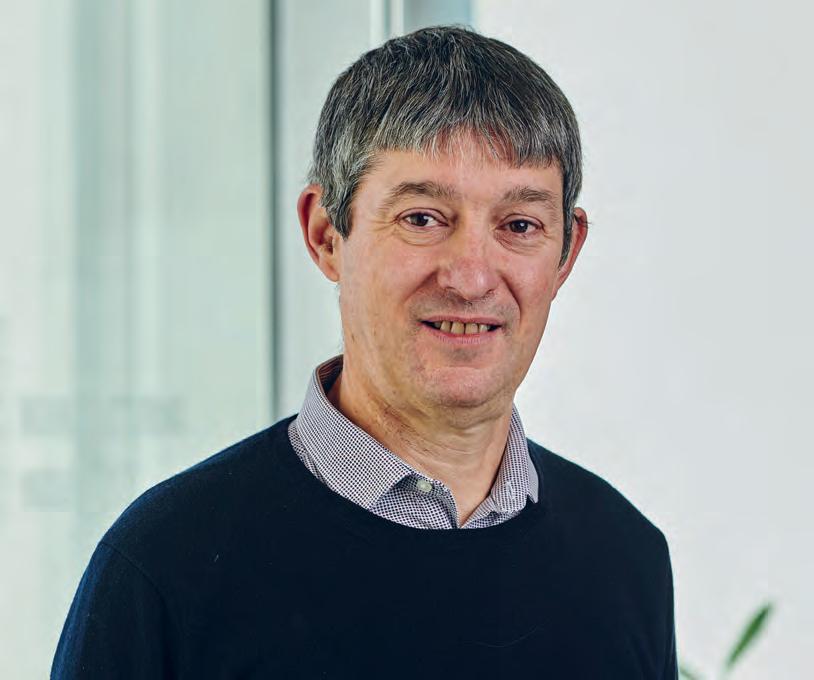
Although the global quantum computing industry is dominated by large, extremely well funded, US companies, there are several significant UK quantum computing companies.
Orca has built a photonic computer and Oxford Quantum Circuits has built an eight qubit superconducting computer which is available on Amazon Braket. Phasecraft, Riverlane, Kuano and Feynman Solutions specialise in quantum software and
Digital Catapult will be running a quantum technology access programme during summer 2023
Daniel Goldsmith, Quantum Technologist, Digital Catapult
quantum algorithms. Oxford Ionics, SeeQC, Universal Quantum, Quantum Motion and Duality carry out important fundamental research. Quantinuum is a merger of Cambridge Quantum’s advanced software development with Honeywell’s hardware.
11. Are there potential negative consequences of quantum like those we see with AI?
Shor’s 1994 quantum factorisation algorithm shocked the research community by suggesting an impressive ‘quantum speed-up’ that could undermine RSA encryption.
Although the large, universal, fault tolerant devices needed to run the full algorithm are probably decades away, there are hints that a variation on this algorithm might break RSA encryption much sooner. The combined development and lifespan of Internet of Things (IoT) devices like modern cars can be very long, and if an RSA encryption algorithm is hardwired in the chip, there is risk that devices could still be in the field
when quantum computers arrive that can break the encryption.
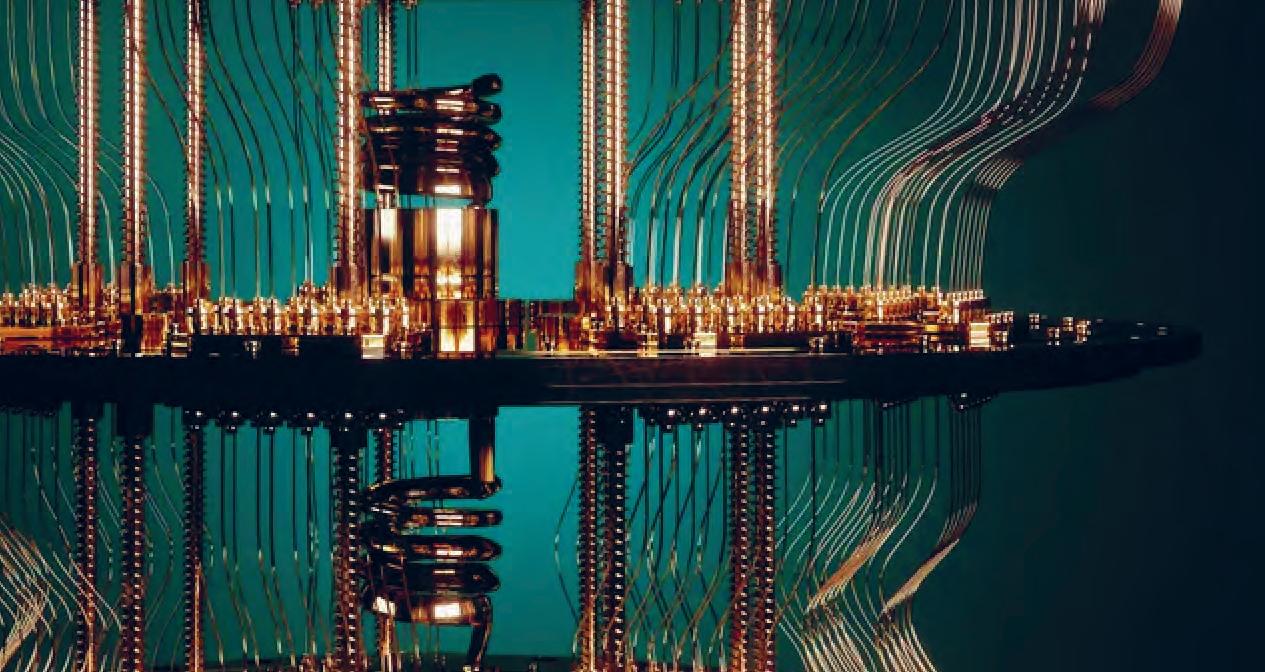
12. How do we prevent/mitigate the possible negative consequences?
Any industry that depends on RSA or similar schemes to protect business secrets should be aware of the risk of ‘store now, break later’ attacks. There is a strong case to develop a strategy to implement quantum safe encryption in software and hardware.
Like any new technology it will take decades for the full impact of quantum computing to be seen. In the long-term, quantum computing will profoundly shape our future with impacts as dramatic as the invention of flight or the silicon chip. It is very likely that in the next decade we will start to see quantum computers carry out computations simply not feasible on classical computers. The UK is well positioned to take advantage of this new technology because of its early strategic investment and continued government support.
Quantum technology access programme
As part of the Data Centre of the Future, led by Orca Computing, Digital Catapult will be running a quantum technology access programme during summer 2023 in which companies in the energy, construction, automotive, transportation, advanced manufacturing, material science and telecoms sectors can receive free education and training on quantum computing, advice from quantum scientists on appropriate algorithms for their business, and hands on time on simulators and the ORCA PT-1 quantum computer. Email quantum@digicatapult.org. uk for more information and to register interest in the programme

TUBULAR SELLS
Moving the world through power and strength in tubular products
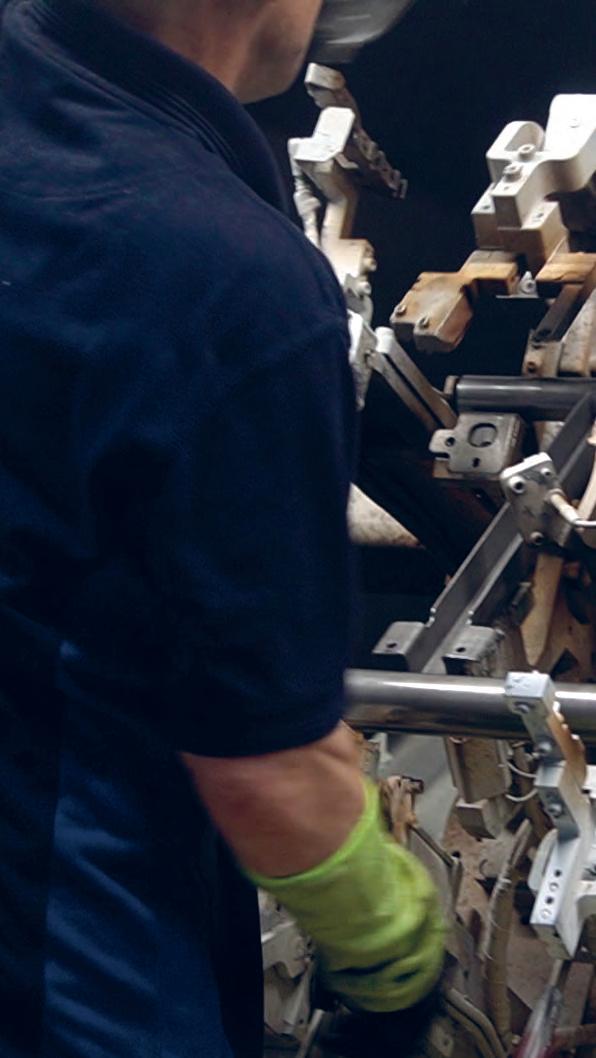
With over 140 years of history and experience since William Lander started manufacturing household wire formed goods in his attic back in 1881, Lander Tubular Products has grown and transformed beyond his wildest dreams. The Manufacturer’s Lanna Deamer recently paid a visit to the company’s global headquarters, and its largest manufacturing facility, in Birmingham
Lander Tubular Products is an engineering and fabrication manufacturer specialising in tube manipulation and CNC tube bending of metal and plastic pipe and tube assemblies. The company manufacture products for the global automotive, commercial vehicle, off highway and industrial sectors. Lander manufacture a product range that covers multiple applications for the transfer of fluids or air within different systems, as well as structural support components which provide stability and safety to the end user.
Walking up to the building entrance, my colleague Tom St John and I both turned to each other and asked if we’d been here before. Something about the building felt so familiar. Although we know the Lander team well and everything felt like a weird case of déjà vu, this was our first time visiting the Birmingham site. Long time entrants of The Manufacturer MX (TMMX) Awards, we were greeted by a mini shrine to the awards. Walking upstairs to the conference
room, the walls were lined with certificates from the years of entering our prestigious programme.
We were welcomed by Len Palmer, Managing Director of Lander Tubular Products who commented on the awards wall: “As you know, we’re long-time supporters of The Manufacturer MX Awards but we had a year off last year after winning The Manufacturer of the Year award in 2021. We’re excited to say that we’ll be back entering the awards this year.
“We’ve been entering the awards for years, and we’ve always found it to be a very powerful exercise for us internally, but also peer review when it comes to the judging process. We first started applying in 2016, with a view to benchmarking ourselves and subsequently, every year since then, we’ve either picked up an award or been very close!
“Year-on-year, we’ve tried to take all the feedback and advice given during the judging process, apply it to the business and then see if we can progress. The

achievement of Manufacturer of the Year in 2021 was a culmination of the progression we’ve annually been taking on board, the feedback and seeing ourselves measured against peer groups in other sectors. It has been a really powerful tool for us to drive continuous improvement activities in our business. This year another part of Lander will be going through the entry process to give them a chance to learn and take on what we’ve gained over the years.”
Where the magic happens
Although familiar with the Lander team, both Tom and I still couldn’t quite get our heads around what Lander actually manufacture, so we were eager to get on the shop floor. The Birmingham plant houses the central group functions including engineering, purchasing, sales, IT, HR and group finance. At over 10,000 square metres, it is the company’s largest manufacturing facility by size and is configured to support medium to high volume products, mainly for the automotive
and off highway sectors. The facility is also the base for the plastic servo bending machine and the product development centre.
Tube bending is at the core of Lander’s capabilities; the manufacturer has more than 60 CNC tube bending machines across the group with the ability to bend tubes in diameters from ø4mm up to ø152mm. There were several multi-stack CNC bending machines on display which mean the team can produce complex compound bends where there is very
LEFT: Lander manufacture products for the global automotive, commercial vehicle, off highway and industrial sectors
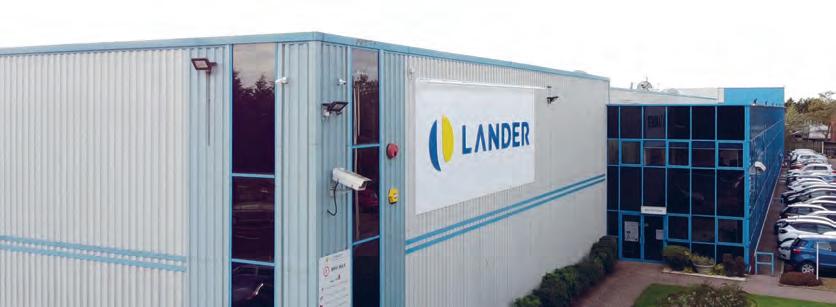
little straight length of tube between bends. I was told that this is often seen in automotive applications where there are very tight package spaces for tubes to be routed through.
“We can produce all different kinds of beaded end form on tube, from single beads for the attachment of hoses and double beads to allow for a hard stop for a hose joint. We also produce complex quick connector end forms for the attachment of snap fit plastic quick connectors and rolled end forms which have a very tight tolerance and are used to join to applications such as turbochargers,” explained Simon Walker, Operations Director at Lander Tubular Products.
The metal joining capabilities enable Lander to offer its customers a variety of solutions from simple manual MIG and automated MIG welding, to manual TIG, and aluminium soldering.
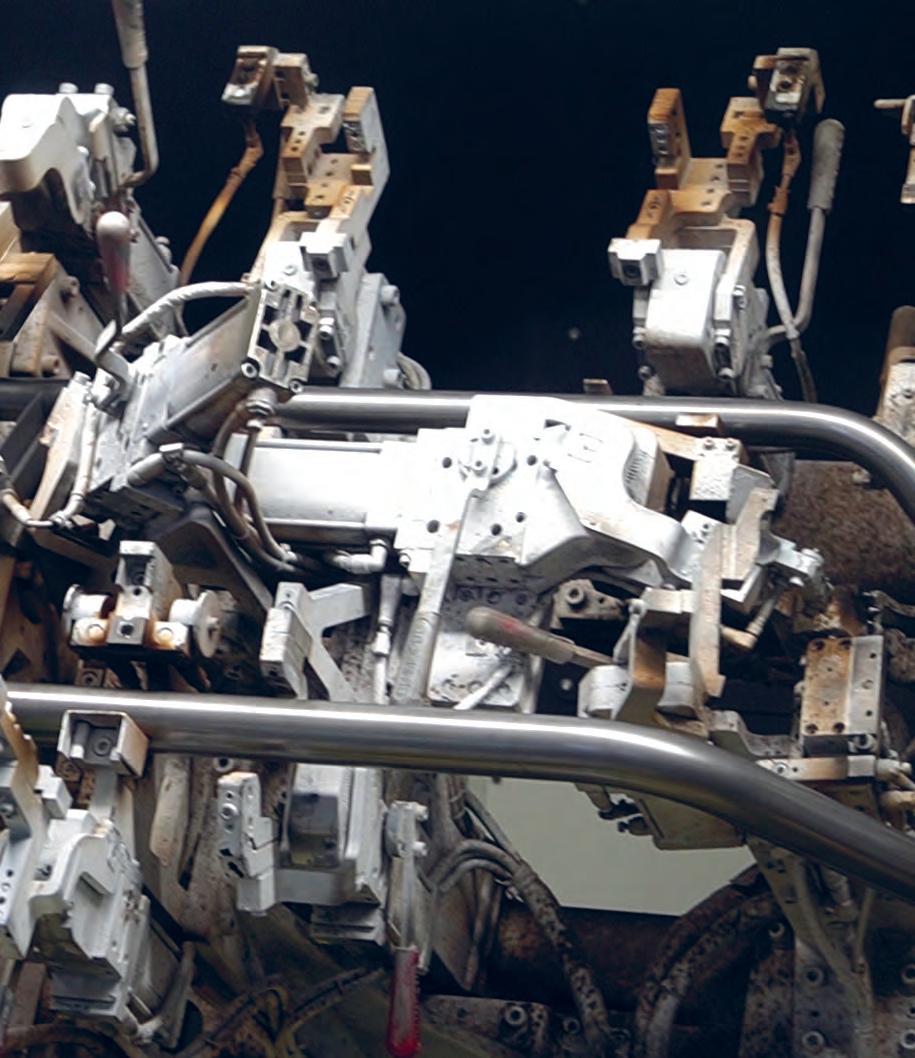
Lander has an in-house mild steel brazing furnace which means the team can provide customers with brazing services to deliver high quality joining solutions on steel products where brackets are featured. Simon explained that brazing helps to ensure that the joint between the tube and the brackets have good integrity in order to maximise longevity.
Once products have been through the manufacturing process, where applicable
BELOW: Lander’s global headquarters in Birmingham

We’re always keen to promote manufacturing as a career path and as such, we have partnered with local colleges to help recruitment within our programme
Len Palmer, Managing Director, Lander Tubular Products
ABOVE: At over 10,000 square metres, Lander’s Birmingham site is the largest manufacturing facility by size and is configured to support medium to high volume products
LANDER’S SMART MANUFACTURING ETHOS
the team leak test and gauge the product to validate it. The standard testing system for smaller diameter tubes is air decay which is highly accurate for detecting any leaks. The team also use air underwater testing as an alternative method.
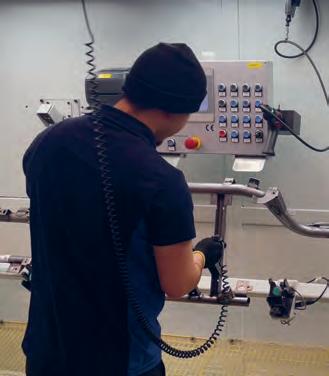
Once the part has been leak tested, the team will gauge it to ensure that all components are in place and the geometry of the part is correct. Where possible, pokayokes are built into Lander’s gauges in the form of camera vision systems and sensors to check components are present. Only when the part has been validated will the system print a pass label.
Created in-house by a cross-functional team, Lander’s Apollo system uses the latest IoT (Internet of Things) and PLC technology to get information from many different sources (machine controllers, environmental, ERP and HR systems) to provide realtime feedback to operators and team leaders. Additionally, this data is recorded in a data warehouse solution that can be interrogated by an easy-to-use webbased portal to view historical trends and data or even make ad-hoc queries without the need for IT intervention.
Pal Kayla, Controls and Instrumentation Engineer at Lander Tubular Products said: “We started our smart factory adventure after a visit to Smart Factory Expo which gave us plenty of ideas. We then
Connected: Processes, machines and teams are connected to shorten the time required to analyse and react to data
Optimised: Continual analysis of process performance in real-time to increase machine uptime and productivity
Agile: Flexible manufacturing systems allow Lander to re-configure factory layouts to implement products in real-time

Transparent: Visibility for Lander’s teams across all operations to shorten decision making times
Proactive: Automated stock replenishment, error monitoring and safety protection
KEY TAKEAWAYS
• Lander’s people are at the heart of the business
• The company’s core values are closely linked to the apprenticeship programme

• Showing world-class, modern manufacturing facilities will help break down barriers and misconceptions held about the industry
developed our own in-house OEE real-time data monitoring system. We still have a lot to explore in digitising our shop floor."
Apprenticeships
People are well and truly at the heart of Lander’s business. In June 2022, the company was ranked number one in the National Apprenticeship Service's Top 50 SME Apprentice Employers. The programme was first developed in 2016 to help make the best use of the organisation’s strengths and to take the opportunity to reduce the skills shortage in the business.
In normal times, Lander aims to recruit between 10 to 15 apprentices every eight weeks. They are recruited through a training provider who then identify 25 candidates to start their pre-apprenticeship programme for four weeks, where they undertake initial training and development at college.
They are also assessed on their behaviours during this process. When they have completed the pre-apprenticeship, they attend an assessment day on-site at Lander and the company selects candidates to start one week of work experience. At the end of the week, they are assessed again and those that have met the criteria are offered placements on the programme in the form of an 18-month contract and start their apprenticeship with six weeks in the on-site Lander Academy.
They will then graduate at the end of those six weeks and begin working in manufacturing for the duration of their first year. Lander has continued to drive the quality of the programme to meet business and apprentice needs, ensuring they have the best opportunity to learn while earning and to successfully achieve
ABOVE: In June 2022, Lander was ranked number one in the National Apprenticeship Service's Top 50 SME Apprentice Employers
their apprenticeship. Apprentices start their journey within manufacturing and have the opportunity to develop into specialist roles that become available within the business.
We spoke with previous apprentice, Joe McCarthy, who is now a Production Engineering Improver. He said: “I started my apprenticeship in manufacturing engineering back in 2018. The thing I enjoyed the most about my apprenticeship was learning new skills such as PLC programming and how different computers and systems work.
“The life skills I have learned are communication, problem solving as well as listening skills. All of them help with my current job role. My average day now involves developing new systems for the business, such as a new Andon system. I also update and further develop the current systems we have in operation.
“For anyone looking to start an apprenticeship, I would advise them to learn as much as possible and be keen. Lander has a friendly workplace environment which makes a big difference, but not only that, if you show a willing attitude then you’ll be given more opportunities and the chance to progress your career.”
Len added: “We’re always keen to promote manufacturing as a career path and as such, we have partnered with local colleges to help recruitment within our programme. We are also constantly reaching out to schools to get children
involved from a young age – it’s a great way for us to grow our talent.
“On a more personal level, it’s one of the most rewarding things I’ve ever done because I feel a sense of duty to help the next generation. Most of the directors in the business have been part of apprenticeship programmes at some point in the past. The programme we offer is one of the most unique things about us, and we received a lot of brilliant feedback about the way we engage our apprentices from the TMMX judging panel. Apprentices effectively do a much better job at describing the company culture than any senior management.
“We love running open days for young people and their parents to have a look around our plant. Showing that we have a modern, world-class manufacturing facility
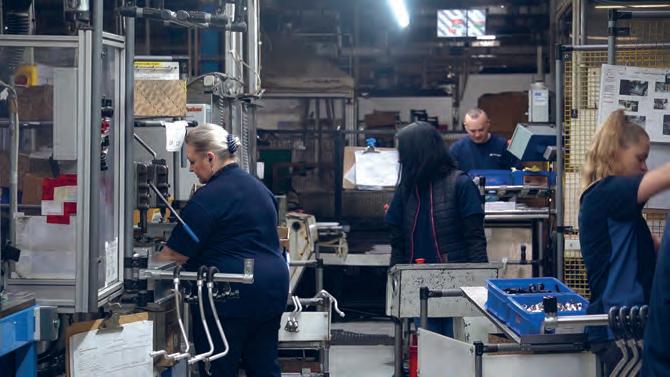
THE LANDER FAMLY
Apprentices are made to feel welcome and part of the team as soon as they arrive.
Passion for perfection: The company instil in its apprentices the importance of achieving the best that they can with their support. Take responsibility: Apprentices are enabled to suggest improvements, report concerns and accept when things go wrong - it’s all about learning and developing.
Yesterday’s gone: Apprentices know that if they make a mistake, they should learn from it and move forward.
Great is just not good enough: Apprentices understand very quickly why quality is important and how it impacts business performance.
Freedom to fail: Apprentices know that if they fail in one role, there is an opportunity to look at other areas of the business.
Free speech: Apprentices are encouraged to speak up and let leadership know what they think. Have a blast: Apprentices are encouraged to socialise and join in the sporting activities held outside of Lander, and to participate in various charity events throughout the year.
helps break down those initial barriers and misconceptions that people often have of plants such as this. They are still considered to be very dirty, old-fashioned places but they’re the complete opposite.”
Although Lander's core values were visibly displayed on the shop floor, their true reflection could be seen in the company's actions. These values were not just empty words but were also closely linked to the apprenticeship programme.
Scan QR code to view a video of the visit to Lander
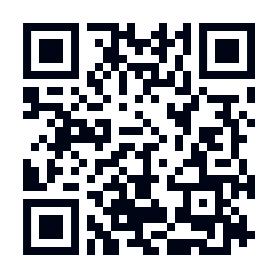

The apprenticeship programme we offer is one of the most unique things about us, and we received a lot of brilliant feedback from the TMMX judging panel
Len Palmer, Managing Director, Lander Tubular Products
Charging ahead!
Autocraft EV Solutions has pioneered how to repair and remanufacture
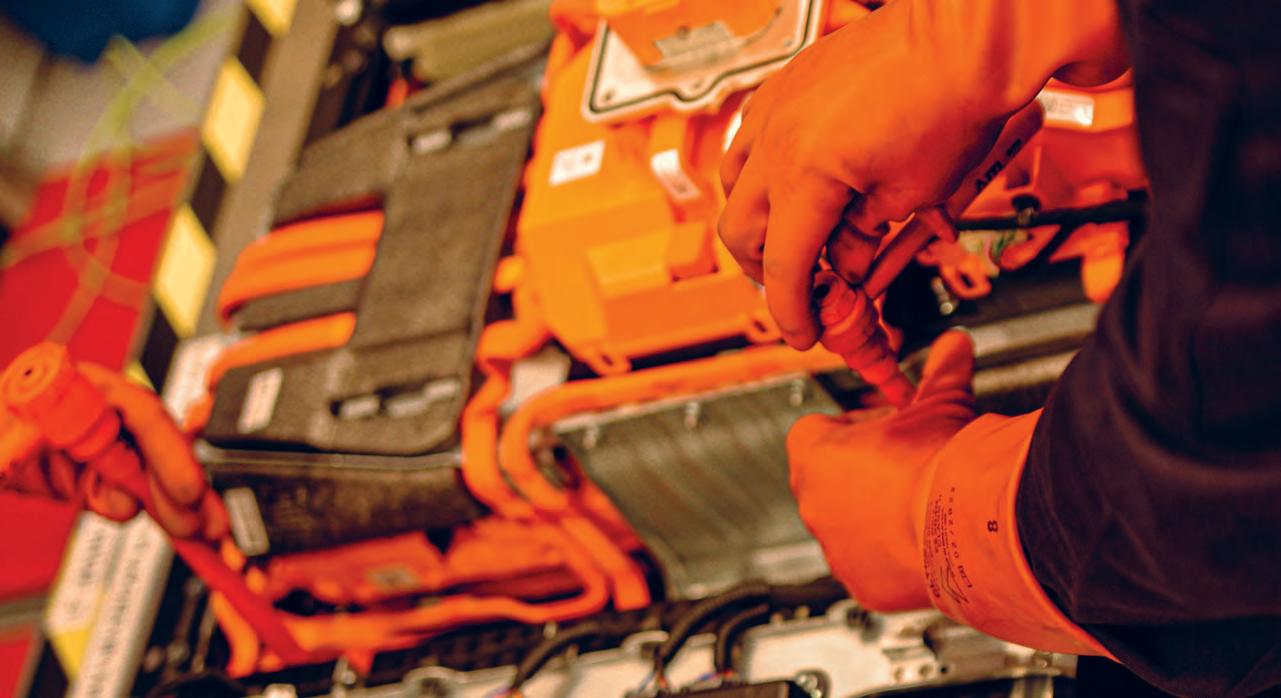
EV batteries at scale, safely and sustainably. Doing so unlocks enormous opportunities for the company while reinforcing the UK’s international standing for engineering innovation.
There are now more than one million cars on UK roads that come with a plug (fully electric or plug-in hybrid). More than 265,000 battery electric cars were registered in 2022 alone, up 40% from the previous year. All signs point to this rapid growth being sustained if not exceeded over the coming decade.
Several factors are driving the surging popularity of electric vehicles. Chief among them is that EVs produce no harmful emissions at the tailpipe and are therefore seen as crucial to achieving net zero ambitions. Yet, the mining and manufacturing processes involved in battery production do emit CO2, alongside other environmental impacts.
Jonny Williamson reportsTypically, the manufacture of an EV produces nearly double the amount of carbon emissions as an internal combustion engine (ICE) vehicle. Depending on the EV in question, it will take between 20,000 and 55,000 miles for it to ‘break-even’ on CO2 emissions. If an EV battery fails or is believed to have failed prematurely, then the carbon benefits of EVs are eroded.
It is therefore vitally important to maximise the life of a battery. Achieving this fully relies on being able to quickly, safely and robustly test and repair them. A lack of such capabilities has seen industry and governments prioritise recycling, forgoing the substantial environmental and economic opportunities provided by repair and remanufacturing. Until now.
Problem into opportunity
EV batteries are the same as those in your smartphone and other electronic devices in that their capacity diminishes over time. Where they differ, however, is that they have multiple modules, making it possible to replace defective modules where there is an issue. For an EV, this degradation normally happens after 600 charge/ discharge cycles or about 150,000 miles, but a fault can cause it to happen much sooner. As the number of EVs on our roads continues to rise, it only takes a very small percentage failure rate of batteries to create huge demand for EV battery repair.
Once a battery is unable to fulfil its initial EV application, it can still perform a less demanding secondary application. The
most common is stationary power storage for industrial or residential renewable energy. The other preferred end-of-life option is recycling (incinerating) the battery to recover the precious materials contained within, such as lithium, cobalt and nickel graphite.
While repurposing and recycling have an important role to play, they both ignore the intrinsic value that remains in most batteries.
A battery, much like a chain, is only as strong as its weakest part. Modules inside an EV battery age differently and only a certain amount will be unusable at the end of a battery’s life. Identifying and replacing damaged or underperforming modules means a battery can be returned to its original performance limits. What’s more, this remanufacturing
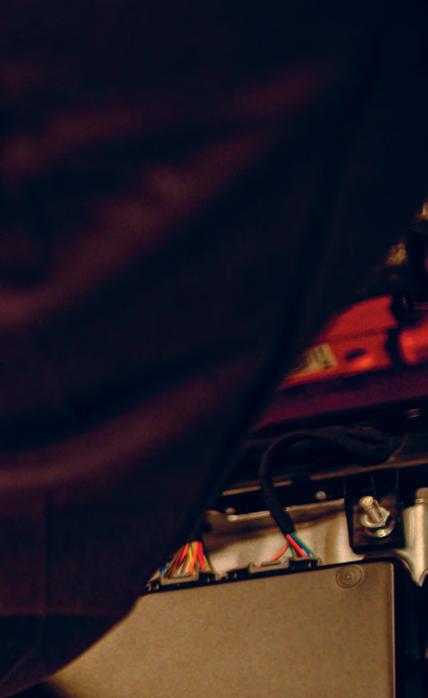
process can be done multiple times over.
In so doing, it ensures repairable batteries aren’t being prematurely sent for repurposing and recycling and provides greater confidence to consumers, especially concerning used electric cars. Although recycling is good, remanufacturing is more than 50% better for the environment compared to pure recycling across water, electricity, CO2 and waste to landfill.
Sounds fantastic, but remanufacturing is routinely disregarded due to a widespread belief that it can’t be done at scale, safely and sustainably. What Autocraft EV Solutions, part of Autocraft Solutions Group, has achieved behind the most unassuming of facades proves otherwise.
The Grantham-headquartered company now sits at the centre of a multi-billionpound market for testing, repairing, remanufacturing and repurposing EV batteries.
Autocraft Solutions Group

Autocraft has been a trusted powertrain manufacturing partner to OEMs since the 1970s and as far back as 2006, the company saw the requirement for EV battery remanufacture and repair.
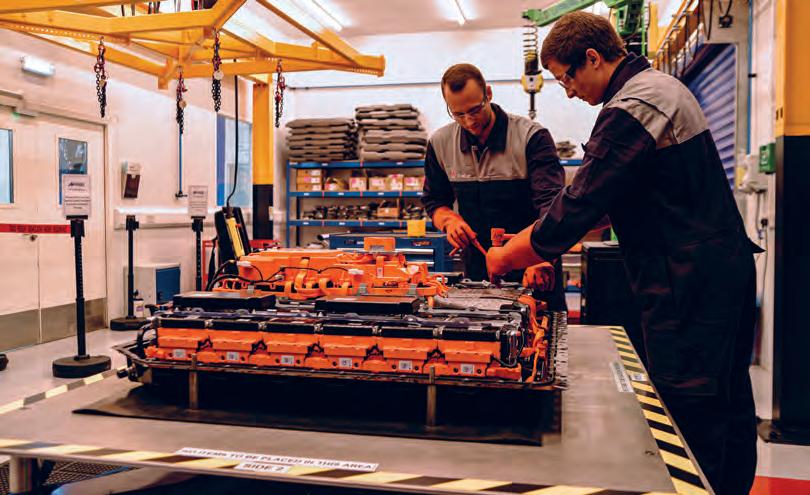
That same year, Autocraft started to produce small volume and prototype battery packs for several niche vehicles. The packs were very low-tech and lowpower compared with modern packs, but the same base chemistries and use of cylindrical cells gave Autocraft a ten year head-start on other companies and put it on the road to where it is today.
The arrival of Mike Hague-Morgan has been equally important to that journey. Known as something of a problem solver for automotive tier 1 companies, in 2008 Mike was parachuted in to turn the loss-making company into profit. Seeing the potential of the company, Mike led an MBO in 2010 and the company was reborn.
Under the direction of Mike and his senior leadership team, the vertically integrated Autocraft Solutions Group was formed following the purchase of Vertex Engineering Solutions (Birmingham) in 2015 and Autocraft Machining Solutions (Wellingborough) in 2018.
Since the MBO, the company has grown from £7m to £70m turnover, and from sub100 to more than 460 employees. Autocraft has also adopted at least one major new technology every year since 2013, including becoming paperless and introducing its own unique augmented reality assembly systems and cloud-based data analysis.
It has also continued to invest heavily in its EV capability, becoming one of the only companies in the world that can
Repurposing and recycling are all well and good but they still mean a new battery being manufactured to go back in the car
Mike Morgan, Co-Owner & Executive Director, Autocraft EV SolutionsABOVE: Autocraft has a decade-long head-start on many other battery companies, combined with 40 years of experience in engine and transmission assembly RIGHT: Since 2020, Autocraft has repaired/remanufactured more than 2,000 EV battery packs for multiple wellknown automotive brands
both test and repair and remanufacture EV battery packs.
REVIVE
REVIVE is Autocraft’s unique and patented process of identifying the state-of-health (SOH) of EV batteries and the subsequent repair and remanufacture of degraded modules. The beauty of REVIVE lies in its flexible yet scalable structure:
• REVIVE Triage is a fleet of highly-mobile on-the-road vans for fast response, non-invasive testing to identify electrical faults and failed modules down to the cell level. Many electrical faults can be fixed at the roadside, however, where this is not possible, batteries with module or cell faults are transported to an Autocraft EV Battery Service Centre for full repair. REVIVE Triage is also able to make damaged (red) packs safe for onward transport.
• REVIVE Workshops are fixed Autocraft EV Battery Service Centres for full triage, repair and remanufacture. These facilities can be strategically located on a customer’s site or near to any
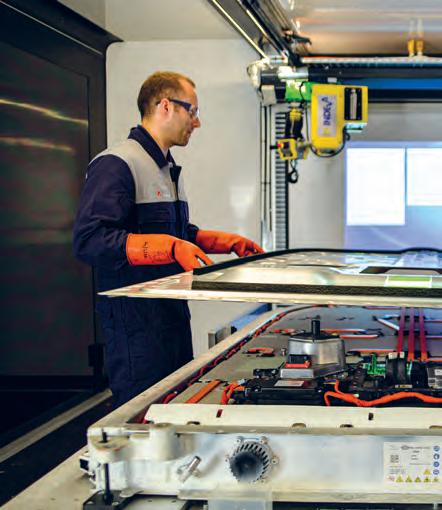
location with a high concentration of EVs to maximise battery repair throughput so are ideal for those requiring volume processing.
• REVIVE Mobile takes a REVIVE Workshop and condenses it into a 30ft expandable container that can be deployed anywhere from an HGV trailer. These Mobile centres enable Autocraft to provide global coverage to safely test and discharge a specific batch of batteries before dismantling for recycling, allowing Autocraft to establish an initial presence in a new location as it expands.
“The weight and legislation associated with shipping batteries to the UK compared to engines means the business model for batteries is different,” explained Mike. “You need to be much closer to the market or end-user and that’s where REVIVE Mobile comes in.”
Autocraft currently has one REVIVE Mobile facility, but scalability was front of mind from the very beginning. Everything within the container has been manufactured in-house, from the bespoke control cabinet and mains invertor to the sophisticated testing rig and tool board. A bill of material was also drawn up during its construction detailing everything down to the fixtures used and the length of wires in each loom.
“We knew this was going to be one of many, so we aimed to make it as quick and easy to replicate as possible,” Mike added. “A team of three to four people, using the work instructions and modular subassemblies made at our other facilities or by supply partners, can build one of these in four weeks.”
4IR to deliver 5R Speed is equally crucial to scaling Autocraft’s offering, especially when it comes to testing.
Most of Autocraft’s competitors conduct fairly rudimentary static testing energy for capacity loss and resistance rise (energy inminus energy out = capacity loss).
As packs stop charging when a single cell reaches its upper limit, static testing only tells you the state of charge of the worst-performing cells or module. Accepted methods for static testing also take around 24 hours for each test, too long for a production environment.
Autocraft has developed a unique dynamic test that draws on its extensive experience working with battery packs to quickly identify outlier cells requiring further investigation. This can be done thanks to a digital twin for each battery pack, built up of years of data collection and analysis.
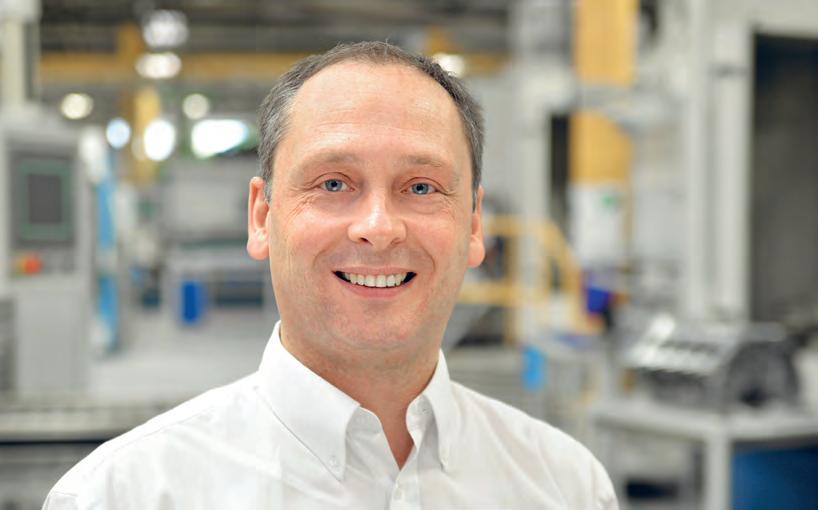
“Our testing equipment pinpoints the root cause of failure so we can accurately address any faults and prevent the issue from spreading. This also helps to maximise the life of the battery or at the very least, gauge when a pack is no longer suitable for automotive use. To the best of our knowledge, no other company in the world can do this,” Mike commented.
Technology also underpins Autocraft’s health and safety processes, including a LIDAR system that stops the process if technicians enter a red zone and a camerabased system to monitor whether the correct PPE is being worn (all electrical systems are shut down until this is the case).
Battery fires are of particular concern. Here, once again, Autocraft is leading the way. Its patented battery ejection and suppression system quickly identifies, ejects, covers, and secures any pack experiencing a thermal event.
The system has been championed by both fire authorities and manufacturers, with several customers adopting the system and
Our understanding of battery technology is always evolving
Mike Morgan, Co-Owner & Executive Director, Autocraft EV Solutions
ABOVE: EV batteries are wired in series, like Christmas lights, so when one cell or module fails it brings down the performance of the whole pack
there are calls for it to become the de facto standard.
Safety and testing systems are all linked to Autocraft’s exclusive Augmented Reality Interactive Assembly (ARIA) system. Through overhead projection and voice commands, ARIA fully guides technicians throughout the EV battery repair and remanufacture process. Camera recognition continuously checks parts are removed, stored, and fitted correctly.
Green lights clearly indicate the parts and tools to be taken next in the sequence and Wi-Fi enabled tooling communicates with ARIA to guarantee every fixing is torque controlled and recorded, eliminating operator error.
“ARIA is a new but proven technology that gives Autocraft a significant competitive advantage,” said Mike. “It’s just one example of how modern industrial technologies are helping us to optimise the delivery of our 5R solution - recovery, repair, remanufacture, reuse, and recycle.”
KEY TAKEAWAYS
• Battery cells account for around a third of the cost of an all-electric vehicles
• Remanufacturing battery packs retains more value and delivers substantial environmental savings compared to pure recycling
• Autocraft EV Solutions is a market leader in the repair, remanufacture, and assembly of EV batteries, electric drive units, and power electronics
• Since an MBO in 2010, Autocraft has grown from £7m to £70m turnover
• The company has developed a myriad of unique and patented manufacturing technologies
Although these processes and systems have all been developed in-house, Mike readily admits that Autocraft couldn’t have achieved what it has without the support and funding from strategic
partners. These include the Advanced Propulsion Centre, Coventry University, Innovate UK, KTN, Made Smarter, Warwick Manufacturing Group, and numerous customers.
Uniquely placed
The rapid growth of the EV market is translating to equally rapid growth for Autocraft. The company’s first overseas expansion, an EV battery repair facility in the Netherlands, is currently being developed. Similar centres are expected to be announced for North America and Asia in the next 24 months.
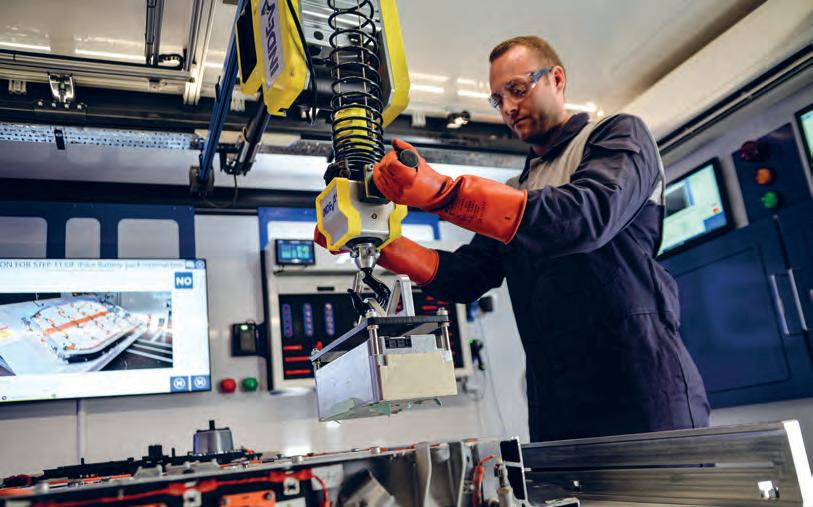
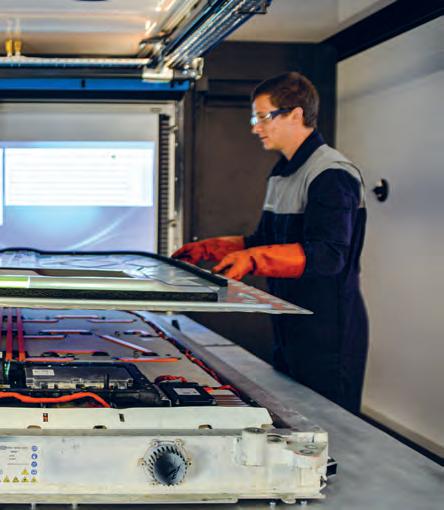
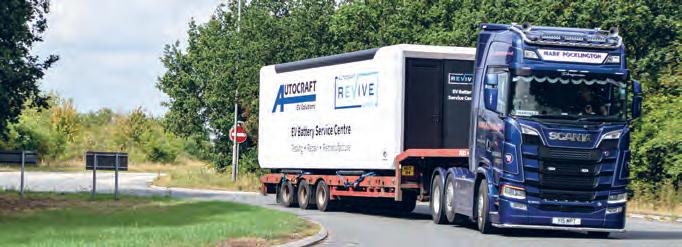
“Remanufacturing has become a lot more commercially desirable for several reasons, including the ever-rising cost of commodities driving focus away from virgin materials, and the waiting lists for new cars resulting in cars being kept on the road for longer,” concluded Mike.
“We see our solution being instrumental in helping consumers adopt EVs faster because it will give them reassurance of the future cost of ownership. We believe it will revolutionise both EV and hybrid ownership by giving drivers the confidence that failures of their battery packs when out of warranty, will no longer lead to the premature writing off of an otherwise perfectly good vehicle.
“What’s more, some of our customers had hundreds of broken or surplus EV batteries in warehouses and were facing eye-watering costs of disposal. We stepped in and changed them from being a liability to a massive profit opportunity.”
2023 EVENTS
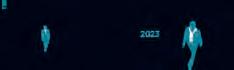
Celebrating the best in manufacturing and engineering excellence and innovation.
Manufacturing & Engineering Week brings the entire community together for a festival of innovation featuring a dynamic, interactive series of digital and live events to inspire, inform and entertain.
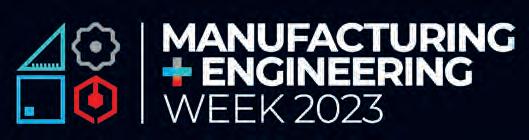
7 LIVE CO-LOCATED EVENTS:
INDUSTRY’S BIGGEST DIGITAL MANUFACTURING
SHOW
For the eighth year, Smart Factory Expo brings together all the technologies enabling the digital manufacturing revolution –creating a carefully-curated shop window for manufacturers at all stages of their digital journey.
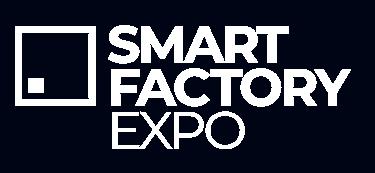
Source the very best innovative solutions on offer, including the latest technology offerings from start-ups, alongside established brands and companies that truly support and advance the manufacturing sector.
ENHANCED PRODUCTIVITY, EFFICIENCY & SUSTAINABILITY
Join senior manufacturing leaders to plan a sustainable digitalisation strategy. Investigate key challenges, such as supply chain resilience, digital integration, data insights, IoT energy efficiency, and workforce upskilling.
manufacturing-digitalisation.com
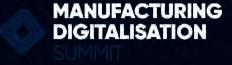
For product designers and engineering professionals from all tiers of the supply chain looking for the latest solutions to reduce costs, streamline & optimise future design and engineering strategy.
CEREMONY: 7 JUNE
Bringing together key suppliers of drives, power transmission & motion control equipment. Representing the multi-tasking culture of today’s design engineer, covering critical areas such as energy efficiency, machine safety, drives, motion control, robotics and automation plus more all under one roof.
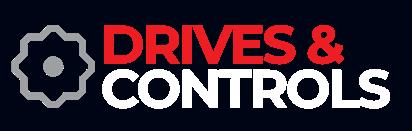
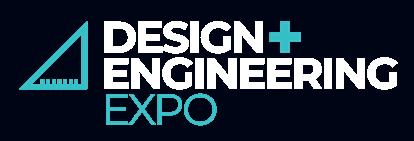
7-8 JUN 2023
NEC Birmingham
SME GROWTH
SUMMIT
COLLABORATE. LEARN. GROW.
A crash course in growth for SME manufacturers. Linking platforms and tech to drive strategy, product, and workforce development. Boost revenue, profitability, and overcome growing pains in just two days.
For businesses with a turnover <£100m.
manufacturing-growth.co.uk
INDUSTRY’S CHANGE-MAKERS
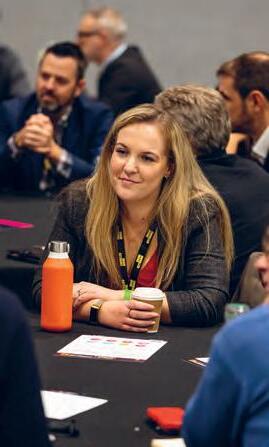
The Manufacturer Top 100 are the very best UK manufacturing has to offer. Now in it’s tenth year, we want to continue to showcase the people who make a truly exceptional contribution to the sector every day. Join us for the reveal of this year’s cohort at a glittering drinks reception honouring industry’s movers and shakers!
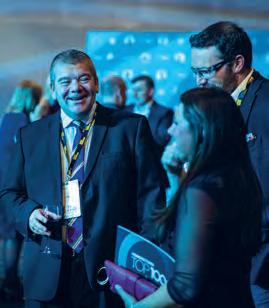
themanufacturertop100.com
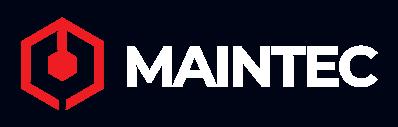
The UK’s longest standing event dedicated to the maintenance, reliability & asset management industry, attracting major buyers from the industrial, buildings, transport & supply chain maintenance sectors.
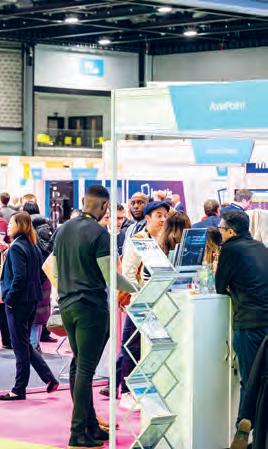
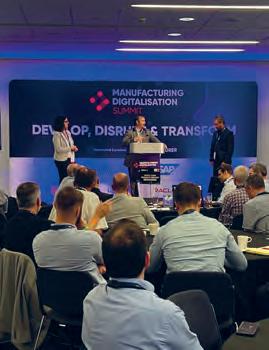
15
Liverpool
2023 EVENTS
Liverpool
CELEBRATING MANUFACTURING EXCELLENCE
The reveal of the Best of British manufacturers - 700 industry professionals will enjoy a three course dinner, guest speakers, live entertainment and a lively awards ceremony.

Delivered by The Manufacturer in partnership with the Institution of Mechanical Engineers (IMechE), The Manufacturer MX Awards have a combined heritage of over 50 years and are widely regarded as the gold standard in industry awards.

themanufacturermxawards.com
ENTRY DEADLINE: 7 JULY
14-15
Liverpool
SME GROWTH SUMMIT
COLLABORATE. LEARN. GROW.
Join the 2nd 2023 SME Manufacturing Leaders’ Summit with a focus on people and processes, completing the June event’s syllabus. Get actionable insights from roundtable debates and plenary keynotes to take away and deploy into your business.
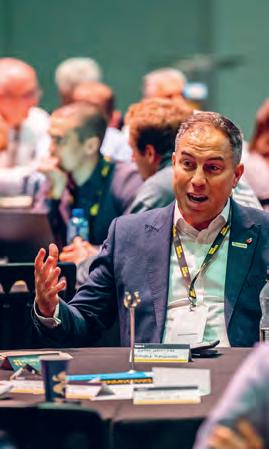
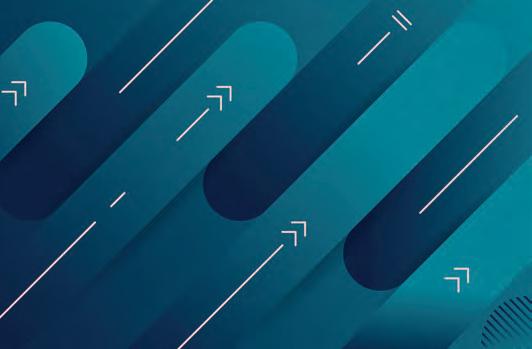
manufacturing-growth.co.uk
MONTHLY
Virtual
PEER TO PEER NETWORKING
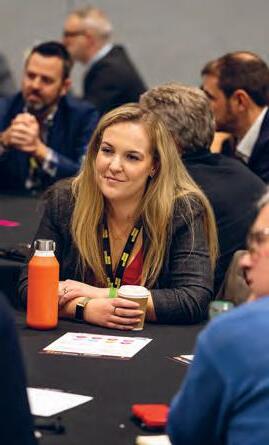
The home for directors and C-Suite of manufacturing businesses interested in networking with their peers.
Regular virtual roundtable discussions over a glass of wine, focussed on key business issues to drive efficiency, sustainability, and innovation.
Apply to join: directorsforum@ hennikgroup.com
SUSTAINABLE GROWTH THROUGH DIGITALISATION
Get world-class content on manufacturing from top speakers worldwide. Covering key strategic, business, and technical challenges in just 2 days, with plenty of networking opportunities. The 2023 Manufacturing Leaders’ Summit is a must-attend event.
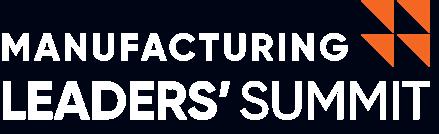
Contact events@hennikgroup.com for more information.
BETTER DATA, BETTER INSIGHTS, BETTER DECISONS.
Data-minded manufacturing leaders will be coming together for the sixth year to discuss the role of data and analytics in manufacturing. They will be exchanging views on the best practices for collecting, managing, and leveraging data to enable factories and businesses to be more efficient and cost-effective - which is critical in the current economy.
industrial-data.uk
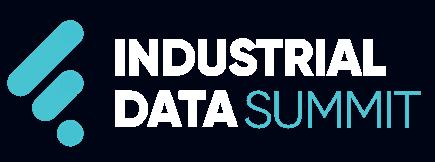
IMMERSIVE, INTERACTIVE & BESPOKE DIGITAL LEAD GEN
Concise deep dives in to specific topics led by industry specialists. Watch a back catalogue of practical how-to webinars on demand, or watch live and ask questions to stay on top of the latest trends and technologies with our fortnightly schedule.
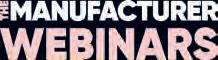
themanufacturer.com/webinars
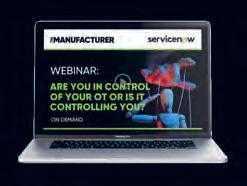
PIVOT PIONEERS
As runners up in The Manufacturer of the Year category at The Manufacturer MX (TMMX) Awards, you’d expect Druck to be an impressive business. Part of the global energy technology company, Baker Hughes, Druck designs, develops and manufactures pressure sensing devices and instruments, software and services.
The facility we visited at Groby in Leicester, is considered by Baker Hughes as something of a jewel in its crown, an advanced manufacturing and design centre of excellence. Like many facilities in the country, it suddenly appears out of nowhere. One minute you’re driving through a housing estate, next minute you’re at the gate; it almost rushes up out of the ground.
At this site pressure sensors are manufactured; very accurate, precise and stable products. These are typically used in harsh environments as well as
in critical applications and in precise instrumentation across a variety of different applications.
A nice touch at this facility, is that every function is on display. All the way through from sourcing, manufacturing, purchasing, planning, marketing and product management. Employees can see how the products are made and the engineer who designs the product can see the full lifecycle, from the silicon to the sensor to the instrument – all the way through the supply chain.
These products are sold into a great number of different markets.
Dave Watson, who leads on Product Management, Marketing and Strategy explained: “We serve industries from aerospace, 50,000 feet in the air, to the bottom of the ocean in subsea markets and everything in between. We supply oil and gas topside, we supply power generation, semiconductors and we’re in the automotive industry.”

He continued, “We also supply the environmental monitoring spaces, which includes clean drinking water. The last glass of tap water that you drank was facilitated by Druck sensors in natural water monitoring and in reservoirs.
“We also have sensors in weather stations, monitoring barometric pressure measurement. The weather forecasts that you can get as an app on your phone are facilitated by Druck sensors.”
The products sold into aerospace include sensors that facilitate safe flight. They’re used in aircraft engines and environmental control systems. We can also thank Druck for the clean air that we breathe on commercial planes.
The issue though, is that some of these industries have taken a hit in recent years. So, how did the business turn this to its advantage?
Druck: a history
Before we get into more of that, let’s take a look at where the company started. Druck was established in 1972 by two creative entrepreneurs, Mike Bertioli and John Salmon. As innovative an engineer as he was a businessman, Mike was the inventor of the world's very first piezoresistive pressure sensor made from silicone back in the 1960s.
John was also an engineer, but as we were told by Druck Vice President,

We moved a lot of our products from aviation to industrial, and now we're seeing a real boom in our industrial portfolio
Gordon Docherty, Vice President, Druck
In a landscape of recent uncertainty and turmoil for manufacturers, the pressure is on. Many businesses have had to explore fresh markets and new roads to success. The Manufacturer’s Tom St John went to visit a business that embodies this spirit of endeavour; pivot pioneers, DruckTom St John, Multimedia Editor, The Manufacturer
Gordon Docherty, he was someone: “who really loved the customer aspects and the application.” Gordon went on to state: “I think when you’re starting up any business, having a great product and placing the customer in the market is a real recipe for success.”
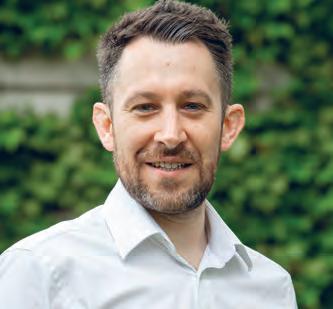
Druck is the German word for pressure, and Mike and John chose this as the name for the business because of the association with German high quality and precision.

“Eighty percent of our products are industrial products,” explained Gordon. “And we have a class 100 cleanroom, where all our silicon chips are made.” It was in front of this cleanroom that we were chatting with Gordon, to a backdrop of laboratory engineers clad in blue protective clothing.
“As you'll see behind me,” gestured Gordon, “this is an example of our cleanroom where we produce over a million chips per year. Back in the day, Mike and John had a makeshift laboratory in Mike’s laundry room. We now have this multimillion-dollar investment that was put into the business to really increase the quality of our pressure sensor products.”
Last year, Mike and John called it quits, in a sale that valued Druck’s capital at £229m, of which they each picked up £58m. Not bad for two blokes who started out in a laundry room in Leicester.
Under pressure
We were led around the Druck facility (donning full, glorious PPE) and at various stop points were introduced to different people who gave us a broad insight into life at Druck. What we’re always eager to learn, is how UK manufacturers have navigated the last few years of unrest. Like so many in the sector, Druck has found solutions to the hardships.
As Gordon put it: “We've managed to really pivot.” A word we’ve heard so often. Druck was able to keep facilities open throughout the COVID-19 pandemic, both in the UK and in China. But, as a business supplying to aviation, this period caused some obvious challenges, meaning that Druck had to explore some alternatives.
“People weren’t flying on planes in great quantities, which of course saw the demand for pressure sensors reduce,” said Gordon. “We had to pivot into new markets and new industries. As the aviation industry was dipping, the semiconductor industry was really taking

off. People wanted more computers, more phones and more tablets. People were working from home. And obviously, electric vehicle growth has been on the up more recently as well.”
He continued: “We’ve got a number of very strong pressure sensor products that we use in the semiconductor industry. We moved a lot of our products from aviation to industrial, and now we're seeing a real boom in our industrial portfolio. That’s been a real success for us.”
Druck has also felt the disruption of supply chains due to world issues, the conflict in Ukraine being an exacerbator. While it’s seen boosts in electrical and semiconductor markets, component supplies have been, and continue to be, widely reported issues in this sector. A lot of the metals that originate from those affected regions often go into the chips and the electronic components that Druck use.
This has been a task for Claire Aitchison to tackle, as it’s her responsibility to oversee supply chain management as Executive Operations Lead, and believes that despite the component shortages, the business has managed well. She puts this success down to having a world class sourcing team and a technology team that is well connected to Druck’s products.
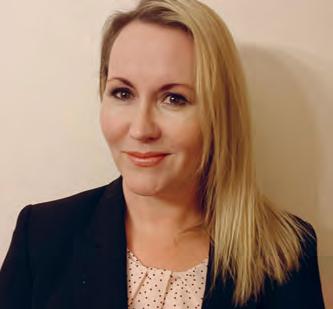
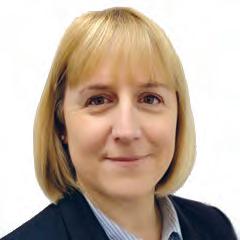
“We've been able to find alternative components to use when they have been in short supply,” said Claire. “Our sourcing team has moved heaven and Earth to find pockets of components that have driven our ability to keep our lead times competitive.
She continued: “However, those solutions don’t come free of cost, and that’s been a real challenge to the business. Some of this we've had to pass on to our customers as price impact, and some of it we've had to absorb within the business. This has been the real impact for us from the hugely disrupted supply chains of the last few years.”
Don’t wait to automate
Gordon also cited further costs due to the ongoing conflict in Ukrainehyperinflation and rises in energy prices. In this instance, the business has tried hard not to pass this price rise onto its customers. “We can't do this,” Gordon stated. “As a result, we've had to invest in automation, and really looking at ways in which we can improve the productivity and efficiency of how we build products.”
KEY TAKEAWAYS
• The high performance, high stability and high reliability element of Druck products make them suitable for a wide range of industries
• Clearly, investment in supply chain solutions has been substantial but needed to maintain competitive lead times
• Good employee engagement in sustainable initiatives only ever seems to lead to positive outcomes
• Druck was very nearly Manufacturer of the Year and almost took home Young Manufacturer of The Year at our TMMX Awards. Ones to watch this year, I suspect
Gordon again pointed to the cleanroom behind him, where lab coat-cladded personnel were busy about their work. “What we've got behind me is a good example of more automated processes. Previously, we used to inspect all our silicon chips manually using optical inspection products.
“Now, we've got automated optical inspection products, where we're using machine learning and artificial intelligence to inspect the chips. This is resulting in much higher quality and throughput. We’ve also moved several of our highly skilled operators, who would normally do that inspection, into other areas of our cleanroom to boost production there.”

In this situation, it’s clear that investment in automation was needed. Taking on initial cost for long-term benefits in production. Leila O’Shea, Advanced Manufacturing Engineering Manager at Druck, further highlighted the importance of automated, tech-centric processes.
“We produce hundreds of different variations and configurations of our silicon. Advanced automation within our silicon cleanroom has enabled us to triple our efficiencies through our silicon processing.”
She continued: “All of our processes are measured, monitored and data is captured. We have a team of process experts and engineers that will take that data and use the relevant tools to analyse it and look for continuous improvements.
“In doing this, we can look for quality improvement for our products, improved health and safety for our operators, efficiency in labour and capacity through our manufacturing lines. This in turn then gives

Entries for The Manufacturer MX (TMMX) Awards (in partnership with the Institution of Mechanical Engineers) are open now. Enter today. themanufacturermxawards.com
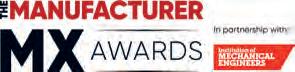
our customers a repeatable and precision performance product that they need.”
The talent puzzle
The products that Druck manufacture, as already mentioned, are high precision. They require specialist engineers and there is little room for error for cleanroom technicians.
This begs the question then, where does the business find its skills for the present and the future? Particularly in an industrywide landscape of talent shortage.
Gordon pointed out, optimistically: “Druck has always had success in attracting strong talent to the business. We're very lucky that we've got highly talented, highly capable people that want to come and work for us.”
He continued: “I think our apprenticeship programme has been the platform for this recently. We work very closely with Loughborough College. Over the last few years, we've brought in a number of apprentices who have done exceptionally well. In fact, one of our apprentices, Jack Barnes, was nominated last year for Young Manufacturer of the Year at The Manufacturer MX (TMMX) awards.”
Druck also organises internships with universities; in its local area and globally the business allows students to undertake a year of work experience. While this is beneficial to the student, Gordon believes it elevates Druck as well, as he spoke glowingly about, “young minds that think up
BELOW: Druck has a class 100 cleanroom, where all its silicon chips are made
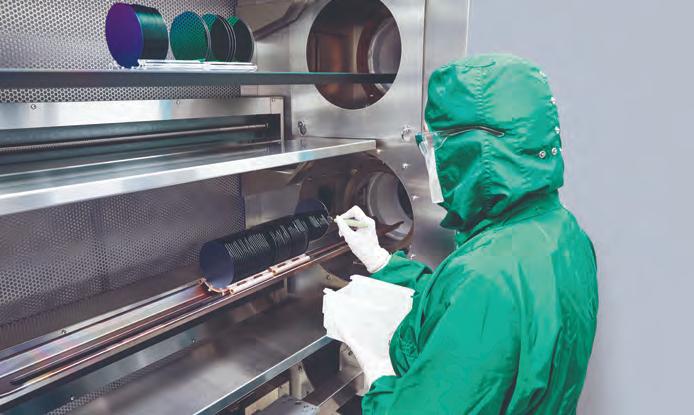
new ideas and push us to think differently.”
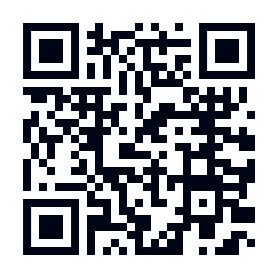
Talent attraction is one part of the puzzle, talent retention is another. At its Leicester site, Druck has a number of long serving employees, but the 20+ years of service trend is one that businesses aren’t seeing as much of these days, with younger people more likely to change jobs.
In a bid to imbed talent by making them feel valued, the company has gone down the mentorship route. This involves pairing employees, some of them with 30-40 years of Druck experience under their belts, with younger members of staff.
Gordon explained: “This also drives the capability levels really high within the business. Although it's a global business, we really work as a family and as one team, and all of our people learn and grow together.
“I think this comes back to working at a facility where you’re able to see the entire lifecycle of the product - being built from the start, from the silicon to the sensor to the instrument. That really does build up a lot of excellent capability and knowledge of how we work.”
Push to net zero

Baker Hughes, the Druck parent company, has a vision to be net zero by 2050. Druck has set its own benchmark to halve its carbon footprint by 2030. This would indicate “a very active plan,” as Claire put it, on environmental progress. It’s a plan that Druck has been moving on since 2012.
“We understand our carbon footprint, we know the key drivers to reduce it and our usage of energy,” Claire explained.
“We have an active programme looking at energy usage, our machinery and our test procedures, which all use carbon dioxide and which we're looking to convert into a different gas.”
Claire also mentioned the importance of having good employee engagement when it comes to sustainability. She added: “It's not just about the hard-line business processes, our employees are passionate about the environment as well.
“We engage with our people; we have good recycling processes and, as a result, we've removed all single use plastics from the site. We’ve also changed all our lightbulbs for LEDs; all examples of those good ideas that come from people.”
Allowing people to do their part and feel involved in their company’s strategy is often seen as critical. Druck is taking this into account, as Claire explained it as being: “The corporate angle of really looking at our manufacturing process and making sure that’s on track to hit the company targets.”
Another shining exemplar
It feels like we’ve written similar conclusions in previous articles, but once again, we’ve spotlighted an example of real ingenuity in the face of turmoil. To transition into new markets so seamlessly is obviously easier when selling high quality products, but it’s the adaptation of Druck’s product positioning in relation to those different levels of market growth which is impressive.
Like many, it’s experienced the recent challenges around supply, but Druck has seen the opportunity for great growth potential and has seized it, by tapping into the rise in demand of semiconductors and the growth in chip demand through consumer electronics.
Here we have another UK manufacturer that didn’t falter through hard times, but strategically dragged itself into new markets to stay competitive and profitable, while retaining talent, investing smartly in automation and taking action on environmental goals.
Advanced automation within our silicon cleanroom has enabled us to triple our efficiencies through our silicon processing
Leila O’Shea, Advanced Manufacturing Engineering Manager, Druck
Thinking about making a career move? Key things to consider
Have you ever felt that you needed a new career challenge, but weren’t sure where to start? If so, you are not alone. Every year, thousands of professionals change jobs in the hope of finding not only extra financial remuneration, but also more fulfilment, better worklife balance and much more. Lauren Wise, Managing Consultant, Michael Page Manufacturing, explains more

As a part of Michael Page Manufacturing, I specialise in recruiting leadership professionals for engineering and manufacturing businesses. Speaking with manufacturing leaders every day, I have learned first-hand just how difficult navigating the job market is. Job titles can be ambiguous, salaries are not always disclosed, and you can’t always get a feel for a company or a role based solely on a 300 word job advert.
While renumeration is key, there are many other factors to consider when deciding on a new role. However, all too often, candidates don’t thoroughly investigate them until later in the recruitment process, when they've already invested time in researching the company, attending interviews and potentially even preparing presentations.
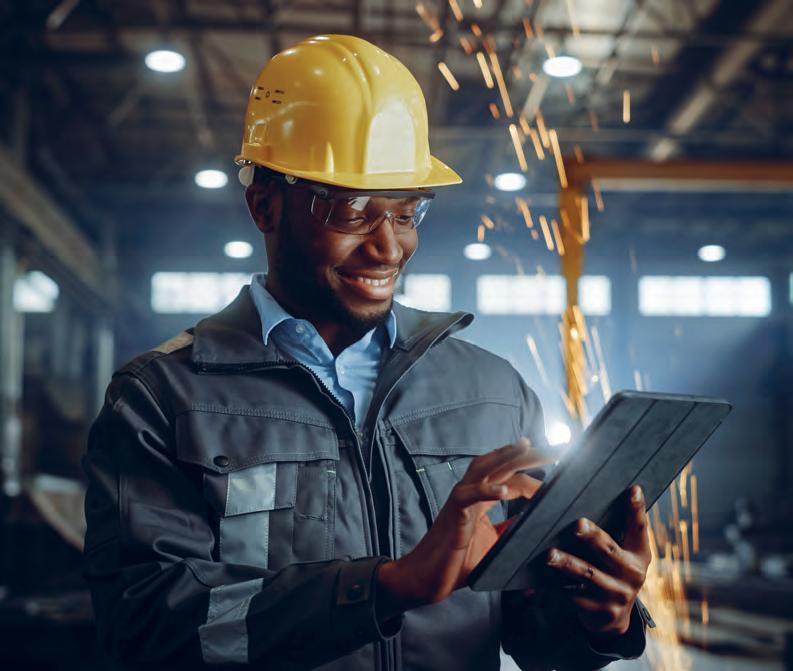
That’s why I’d like to share my top tips for what to consider when looking for a new role, so that you can save time and hopefully land that perfect position first time around.
Step 1: Decide what you’re looking for
It can be surprisingly difficult to nail down exactly what you’re looking for in a new role – and even whether you need to move at all.
The first thing to do is decide what could be improved in your current circumstances, whether it’s a higher salary, a more senior role or additional training. These opportunities may even already be available at your current employer, and it’s worth asking for them. Requesting a pay rise or a promotion isn’t easy, but it’s
a conversation your boss would probably rather have now than after you’ve handed in your notice.
If after these conversations you’ve decided that the right opportunity is not available with your existing company, then it’s onto Step 2, and how to find that perfect job.
Step 2: Take a targeted approach
Think about where you see yourself in two, five and even ten years. What do you want out of your career in the longer-term, and what roles could get you there? There is rarely only one path to your ideal career destination, so be sure to consider the options you’d be open to and investigate roles in that space.
Secondly, consider the minimum salary and maximum commute you’d be happy with, and don’t engage with opportunities outside of these guidelines. The role itself might be great, but if it doesn’t allow you to afford your lifestyle, then it won’t work for you. However, think realistically about your expectations, as sometimes a role with a lower salary but a shorter commute could be just as suitable.
Next, carefully select the sort of roles, companies and industries you’re interested in. Don’t send your CV to every role in the
salary range and commuting distance you’ve decided you’re happy with. Instead, take the time to pinpoint opportunities you’re passionate about.
Step 3: What to say in an interview

It might be tempting to say what the interviewer wants to hear, but in this situation, honesty is the best policy. Many of the candidates we talk to are looking for something new because their current role isn’t what they thought it would be. If the interviewer is honest about the opportunity and the interviewee is transparent about what they’re looking for, then neither party should be going through the recruitment process again in three to six months.
It’s also important to remember that an interview is a two-way street. Make sure you seem interested in the company and role, but feel free to also ask questions about the company’s approach on things that matter to you.
Step 4: You’ve got the offer, now what?
If you’ve followed Steps 1-3 and have been honest with yourself, your prospective employer and any recruitment agents involved, then this is the easy part.
Any offer you receive ought to match the discussions you’ve had throughout the process, so there shouldn’t be too much to consider. However, you don’t want to rush this decision. So, up until this point, have conversations with family and friends about how you’d feel if the offer came your way. This will make you feel confident in your decision, regardless of whether it is an acceptance or a rejection.
Once you’ve accepted an offer, the next stage will likely be to hand in your notice. This isn’t always easy; your current company may even make a counteroffer to get you to stay. However, if you’ve

had the conversations mentioned in Step 1, then it shouldn’t matter whether they offer more money, a relocation or a promotion. If it took your resignation for your employer to make these offers, then accepting them probably won’t be the right move in the long run. In our experience, most candidates who accept counteroffers normally restart their job search within six months..
Of course, sometimes you’ll go through an interview process and feel like the perfect fit for the job, but won’t receive an offer. Naturally you’ll be disappointed – but try to use this as a development opportunity. Understand why you weren’t offered the role and take the learning forward.
Maintaining career satisfaction
When it comes to maintaining career satisfaction for the long-term, my advice would be to evaluate what you enjoy about your role, and what you don’t. Don’t hesitate to have an open conversation with your employer about measures to improve your engagement, and how this will benefit the company. Nobody goes to work to do a bad job, so find what makes you happy and be good at it.
Interested in finding your next opportunity?
At Michael Page Manufacturing, we specialise in connecting professionals across manufacturing, engineering, procurement and supply chain with top employers. If you are looking for a new opportunity, please get in touch with me on the details below:
Lauren Wise, Managing Consultant, Michael Page Engineering and Manufacturing
E: laurenwise@michaelpage.com
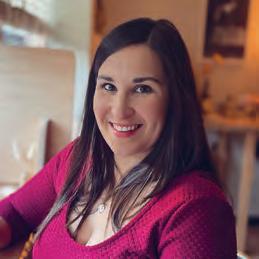
Nobody goes to work to do a bad job, so find what makes you happy and be good at it
Lauren Wise, Managing Consultant, Michael Page Manufacturing
UK MANUFACTURING SUCCESS STORY REACHES A HALF CENTURY
50 NOT OUT
In April, leading manufacturer of measuring and production systems, Renishaw, celebrated its 50th anniversary. The Manufacturer Editor, Joe Bush , paid a visit to the company’s Miskin site in South Wales to find out more about the company’s evolution
Renishaw began its journey back in 1973 when now Executive Chairman, Sir David McMurtry, worked as an Assistant Chief of Engine Design for Rolls-Royce. At the time the company was experiencing a dimensional measurement issue in relation to the manufacture of the Olympus engines that powered the supersonic Concorde aircraft.
McMurtry had a reputation as a great innovator and troubleshooter (in fact, by the time he left Rolls-Royce, he was named on almost 50 patents), and his ingenuity
brought about the creation of a prototype touch-trigger probe for co-ordinate measuring machines (CMMs).
The probe not only solved the problem for Rolls-Royce, but also similar challenges being faced by many precision manufacturers around the world, ultimately allowing measurement on CMMs to be automated for the first time.
Following a conversation with John Deer, now Renishaw’s Non-Executive Deputy Chairman, the pair recognised the wider commercial opportunities for the invention and Rolls-Royce agreed to license the
ABOVE: In summer 2022, Renishaw announced a significant new investment at its Miskin site in South Wales, to increase manufacturing capacity and to help meet its net zero emissions targets
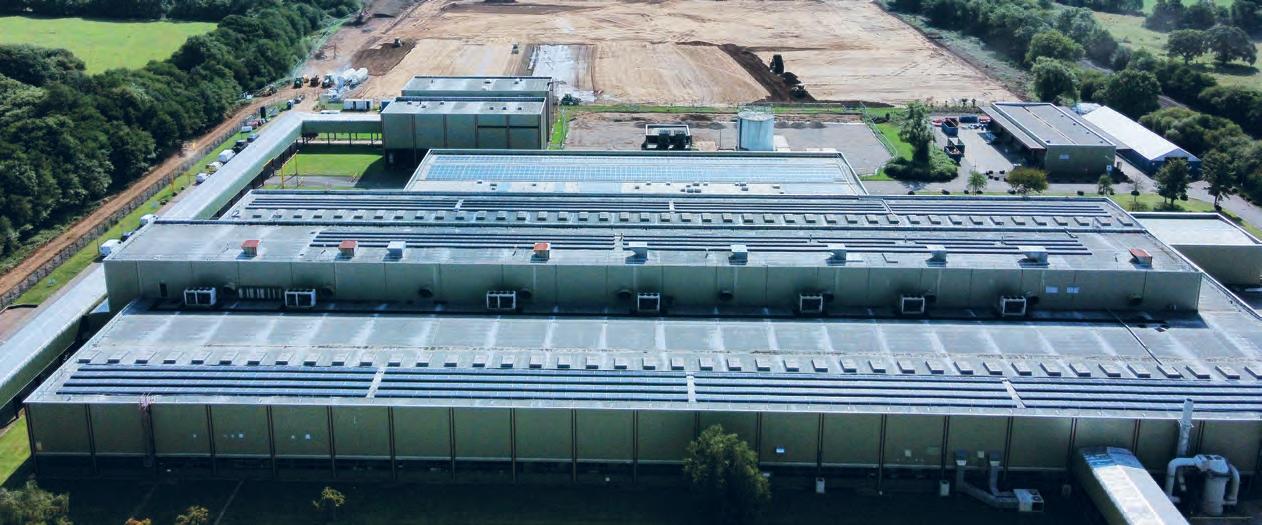
patent to them but would only do so if they had a limited liability company. For expediency, the pair purchased an ‘off-theshelf’ company and on 4 April 1973, the first Renishaw company, Renishaw Electrical Ltd., was registered.

Although today, a significant amount of Renishaw’s business is still derived from contact and non-contact measurement systems for CMMs and machine tools, the company now supplies a wide range of metrology systems for calibration, position feedback and gauging, plus associated accessories including styli and fixturing. The company has also applied its core expertise in measurement, manufacturing and process control to develop systems for non-destructive testing using Raman spectroscopy, robots and drug delivery systems for brain surgery, and is also a technology leader in the field of metal additive manufacturing (3D printing).
Learning curve
Skilled craftsmen and tool makers made up what was a very traditional CNC environment at Renishaw in the early days. The company is a high variety/ low volume manufacturer and so has a range of different batches of work moving through the factory. In the 1970s and 1980s, this meant extended set times, combined with high quantities of parts, meaning the company’s set to run ratio was high.
“This didn't meet the rate with which we were consuming these components in assembly,” said Paul Maxted, Renishaw’s Director of Industrial Metrology Applications. “We were therefore, tying up lots of machines that were making parts which weren't being used.

“We also had a traditional approach to quality, with a co-ordinate measuring machine (CMM) in the corner of the factory with a traditional inspector who had the responsibility to make sure our quality was being maintained. This made him the busiest person in the factory and created a bottleneck. We also had frequent unplanned quality investigations, and these unforeseen issues were adding cost to us as a business.”
Because Renishaw was designing products that were right on the limits of machine capability at the time, the company also had excessive batchby-batch modification of processes that required regular tinkering from the manufacturing engineering teams.
All these challenges were thrown up at the same time as the company was growing and with it, a requirement for increased capacity. A wide portfolio that included a variety of parts for different products led to high levels of inventory
and cost, meaning the company had to become more responsive to assembly demand.

An influx of automation
Renishaw has been on a journey of mass automation adoption since its early days, and this has helped the company
deploy machine tools that allow for one hit machining, thus simplifying scheduling throughout the factory.
The adoption of automation systems for part transfer has also allowed Renishaw to leave machines running for long periods with no manual intervention or requirement for raw materials to be replenished. Crucially, the company has also introduced automation in the factory around part setting, batch set up, monitoring processes and the verification of parts.
“It’s been a journey, a key part of which has been rationalising the things we do in the factory,” said Paul. “We've got lots of similar machines which means scheduling is much easier. We’ve also standardised our approach to the machining techniques we use.
“There's very little new process development that goes on - we're just reusing our best practices again and again. This allows us to reduce the amount of time it takes to develop new machining processes for new products.”
Renishaw use a combination of technologies that can be applied to the automation synergy process. Machine performance assessment, on-machine probing and new machine gauging systems allow for closed loop process control, which in turn allows the movement of parts, the interpretation of inspection results and adjustment processes without skilled resources or any manual intervention.
“We manufacture over 70,000 different components and sell over 30,000 combinations of products,” said Gareth Hankins, Head of Group Manufacturing. “In terms of volume and demand, we have a handful of products that we make in the thousands each month, while others are just one-offs.
“So, we have a very broad, medium to low volume manufacturing problem, which makes us quite different. And if we didn't adopt technology around the methods we use to manufacture parts, I can’t begin to think what life would be like. It's enabled us to grow.”
Productive Process Pyramid
To identify and control processes around the factory - before, during and after machining – Renishaw introduced its Productive Process Pyramid. This four-step journey begins with Process Foundation; prior to machining, control of variability and
We can experience significant shifts in volume at very short notice, so standardisation and rationalisation of equipment is absolutely fundamental to our ability to meet the needs of the business
Gareth Hankins, Head of Group Manufacturing, Renishaw
KEY TAKEAWAYS
• Renishaw was founded in 1973 when Executive Chairman, Sir David McMurtry, began tackling a measurement issue when building engines for the original Concorde aircraft
• Today, Renishaw employs 5,200 people in 36 countries, including 3,400 in all its sites in the UK
• The company supply contact and non-contact measurement products, and a wide range of technologies to support manufacturing, medical and science industries
• Key drivers in Renishaw’s five year strategic plan are Harmonisation, Agility, Productivity and Evaluation
• Renishaw is constructing two new halls adding increased manufacturing space with sustainability at its core
source of variation in the factory needs to be considered.
This can vary from machine capability, quality of tools, consistency of tool build and good housekeeping around the factory, which would normally require experienced people. All the procedures, work instructions and checklists need to be in place to guarantee that the factory is operating in a consistent manner.
The second step in the pyramid deals with Process Setting; as each batch on a machine is set, factors to consider include
critical alignments, setting tools, setting up workpieces and understanding the condition of materials.
That moves on to In-Process Control which covers monitoring, tool wear, drift on the machine, thermal effects of the machining process and tool breakage detection. At the very top of the pyramid Renishaw has Post-Process Monitoring which is the verification of operations of parts.
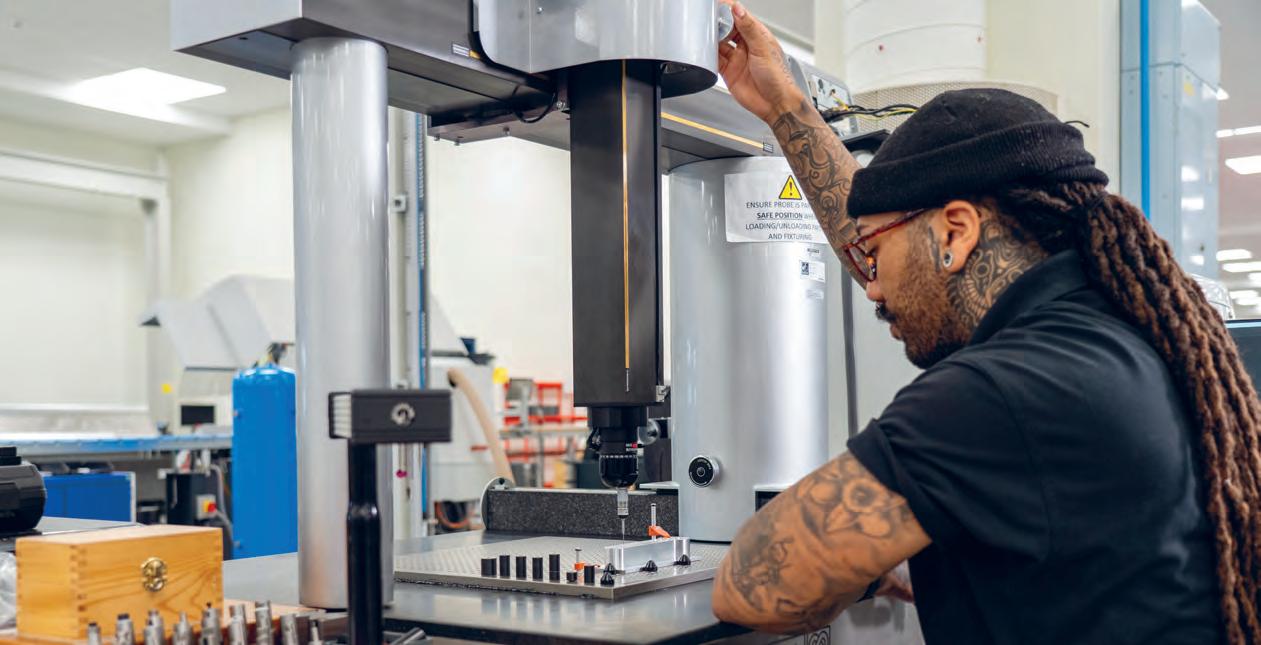
Paul added: “What makes us unique is that we offer technologies, software and applications experience across all these layers, from machine calibration systems through to final part inspection. And there has been a real benefit to integrating metrology into our CNC machining processes. Indeed, lessons we've learned in our own factory can be applied to our customers and have become products in their own right, which we have then taken to market.
“Our journey has allowed us to learn how to control processes (and set limits on them), configure systems and understand what to do when something goes wrong. All that learning is baked into our intelligent process control software.”
Bringing metrology to the shopfloor
Paul added that increased demands from customers have created a need for actionable data in real-time which has seen metrology deployed on the shopfloor. Previously, there would have been delays around data, both in terms of its collation
ABOVE: Over the last 50 years Renishaw has evolved from crafted manufacturing to technology-enabled precision machining at scale
and the decision making needed to act on it. Meanwhile, products would continue to be manufactured in the factory. Paul continued: “Sample routine quality inspections for 1-100 or 1-200 is fine when things are going well. However, if things go badly, this becomes a huge issue for an organisation.
“You then need to establish how many parts have been affected, where the occurrence happened, how many parts need to be remeasured or reworked, and where you need to assign concessions and associated design resources to approve and deviations.
“This is a widespread issue in the industry so by bringing metrology closer to the point of manufacture we are able to react much more quickly, bring processes under control and lessen the impact of quality issues. We can then reduce the cost involved in our quality operations. We also find that this creates increased confidence in the part as it goes through the factory.”
Global manufacturing challenges
The challenges of recent years have meant that manufacturers are having to be far more flexible in their operations, exacerbated by a marked increase in demand from customers and a change in product mix.
Automotive, for example, has seen factories manufacture internal combustion engines, hybrids and battery electric vehicles, all through the same line. Customers want new things, and they want them more regularly, meaning products need to be updated more frequently than before.
From Renishaw’s point of view, this has seen the introduction of an increased level of flexibility in machining processes and inspection to cope with this change in demand. Increased legislation and emissions targets have also created a need to continuously evolve new designs to make products more efficient.
“Methods of manufacturing products and inspection systems can no longer be fixed,” added Paul. “They both need a flexible approach if you want to scale, either from a volume or geographical perspective.”
“Our business has become pretty volatile when compared to a few years ago,” Gareth continued. “We were traditionally selling into OEMs in the machine tool sector, however, now our business is driven more by end users and influenced by what's happening further in the selling chain.”
This has seen Renishaw’s manufacturing model based further around the need to be agile and the capacity to scale in various different scenarios. “We can experience significant shifts in volume at very short notice,” said Gareth. “So, standardisation and rationalisation of equipment is absolutely fundamental to our ability to meet the needs of the business and scale and adapt to changing scenarios.”
Data use

As metrology equipment has been rolled out on the shop floor, and integrated into automation, process control has become increasingly close knit. The data that results can be utilised to keep processes running and for validation. However, it can also provide visualisation into what's going on in the factory.
Paul added: “Just taking a part from a machine shop and looking at the final inspection results is no longer enough. People need to understand exactly how parts have evolved as they’ve gone through the factory, at each stage or machining operation. That data gives the insights that enables you to investigate and prove the quality of processes on the shop floor.”
The company has recently launched Renishaw Central, a data collection
system that allows data consolidation from Renishaw and third-party devices. The system provides all the process history of the part as it's gone through the factory. For industries such as medical and aerospace, this is vitally important as it offers a complete audit trail of the part.
“In the wider scheme, we're going to see this data being fed back into product design and PLM systems; gathering data, looking at it over a period of time, and using it to improve processes and product designs on an ongoing basis,” Paul continued.
Legacy and future commitments
Over the last 50 years Renishaw has evolved from crafted manufacturing to technology-enabled precision machining at scale. This transformation has enabled far higher levels of process capability and accuracy in manufacturing which has helped to reduce waste, scrap or rework in the factory; achieve high levels of productivity and efficiency; allow automation in factories; and reduce the requirement for skilled intervention.
Paul added: “Most importantly, however, our evolution has allowed us to improve product performance, efficiency and reliability of things that we see all around us, every day, and that’s what we’re all about. Think of the increase in reliability and efficiency of cars - they rarely leak oil anymore, and that’s because of higher precision manufactured parts working to much closer tolerances.”
While this year Renishaw is celebrating its past achievements, the company is also focused on ensuring the continuing success of the business through investments in people, product development and production capacity; all underpinned by a commitment to be a more sustainable organisation.
In summer 2022, the company announced a significant new investment at its Miskin site in South Wales, to increase manufacturing capacity and to help meet its net zero emissions targets. An investment of around £65m will see a phased development of 400,000 sq ft of additional low carbon buildings at the 193-acre site to the west of Cardiff, consisting of two new production halls and an employee welfare facility.

Gareth continued: “Our Miskin site, which we acquired from Bosch in 2012, is now the largest manufacturing facility within the group. We started manufacturing in 2013 and gradually refurbished the space to a point where we now have two production halls; one looking after product assembly the other component manufacturing. We’re currently around 75% full and the acquisition of the new site has allowed us to take care of strategic risk management by splitting capacity and adding resiliency into the supply chain.”
The existing production halls will also be refurbished to reduce their greenhouse gas (GHG) emissions. This investment will almost double the footprint of the site. The additional capacity will allow for increases to machining operations and the
Just taking a part from a machine shop and looking at the final inspection results is no longer enough. People need to understand exactly how parts have evolved as they’ve gone through the factory
Paul Maxted, Director of Industrial Metrology Applications, Renishaw
assembly of products already built at the site, including Renishaw’s world-leading metal additive manufacturing (3D printing) machines.
Gareth added: “In the last couple of years, we’ve tried to be more joined up in our strategic thinking – to make sure we evolve and use the latest technology, thus increasing our agility and guaranteeing we can react to all the different market drivers – that’s fundamental to what we do.”









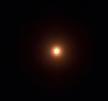


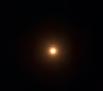


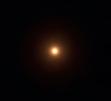
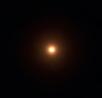












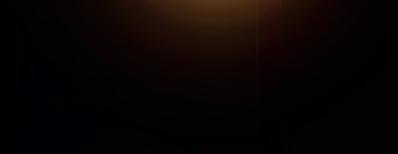
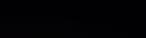
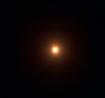
A key topic on Gareth’s agenda is manufacturing productivity, vital to which is establishing common methods and reasoning for decisions taken around business processes right the way across the organisation, and making sure effort is not duplicated and wasted.
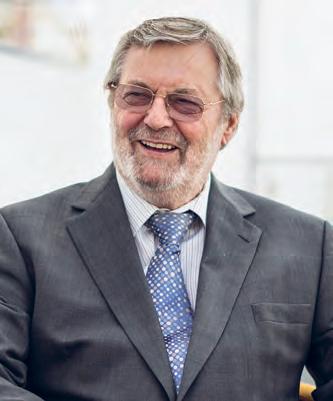
He added: “We're trying to harmonise where possible, because engineers are inventive souls by nature. What we have learned is that when processes are separated, it is inevitable that they will be done differently after a certain period of time; a result of someone implementing a good idea to improve part of a process which isn’t then standardised across the sites. We're trying to be more mindful of that as we grow.”











Gareth added that the decision to double the capacity of the Miskin site, which is vital for the organic growth of the business, was a fairly easy one when the company’s aspirations for the next five years are taken into consideration.
The plan is to have the first building completed by the end of this year, with manufacturing assembly moving in soon after. The vision for the second building is around component manufacturing, giving the company further options to split processes where required and increase resilience.
Future talent


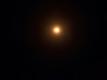



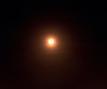
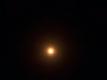

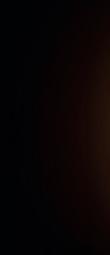

A key aspect of investing for future success lies in Renishaw’s ability to retain and recruit skilled individuals across many business disciplines. The company has a strong track record of growing its own talent pool, having started an apprenticeship programme in 1979 and recruiting apprentices every year since that time, even during business downturns. The 50th year will again see a significant investment in future talent, with the aim to recruit around 100 graduates and 60 apprentices in the UK.
However, the hard work starts years before a young person will ever be employed by Renishaw. A science, technology, engineering and manufacturing
(STEM) education outreach programme is run in the South West of England and South Wales by four employees who are dedicated to engagement with both primary and secondary schools.
Following the success of a dedicated education centre at the Miskin site, Renishaw has also opened a STEM education centre at its HQ site in Gloucestershire, which will support students with their science, technology, engineering and maths studies.
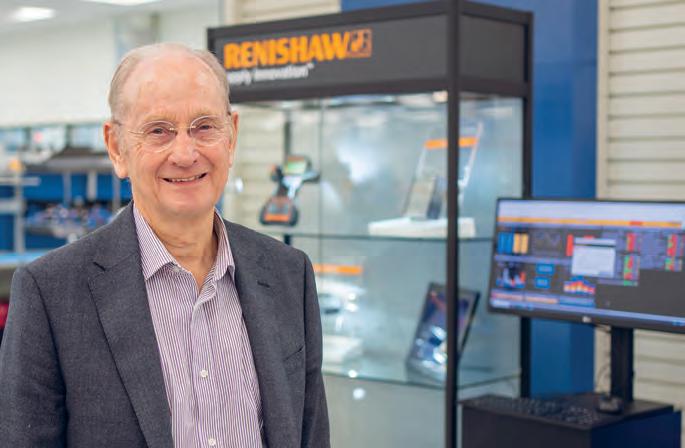
Sustainability targets
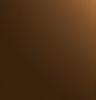

In 2022, Renishaw announced that in addition to its commitment to achieve a science-based net zero GHG emissions target for all its business operations by 2050, it would also achieve net zero for Scopes 1 and 2 emissions by 2028. Both these targets will be validated and monitored by the Science Based Targets initiative (SBTi). A

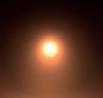



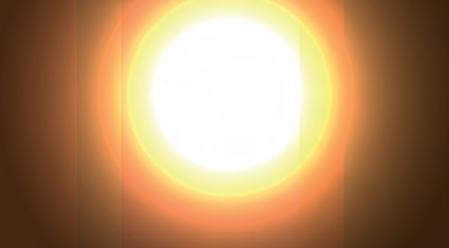
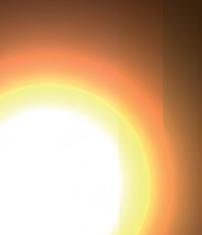
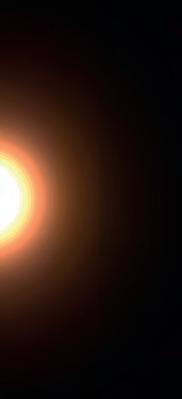
vital consideration for the new construction programme at the Miskin site is to ensure that this new target can be achieved.
Therefore, the new facilities will be built with the latest technologies and materials to ensure that they will be net zero in operation, and the build also aims to minimise the amount of embodied carbon within the building materials used in construction.
Gareth added: “What we are setting out to do with these new buildings, and overall for this site, is to be able to look people in the eye and certify ourselves as being net zero. All the buildings we're putting up throughout the group have the same target. I've been involved with a lot of buildings over the years, but the difference with this one is we engaged consultants from the start and so sustainability has been built in.”
By the end of 2024, Renishaw also aims to have included new energy efficient cladding and replaced existing heating systems in the two existing production halls.
These sustainability investments complement initiatives at Renishaw’s other global sites, including large investments in roof-mounted solar panels, new car port solar panels, EV charging points to support the company’s move to ultra-low emission (ULEV) fleet vehicles and a new ULEV salary sacrifice scheme, initially for its UK employees, and feasibility studies to assess the viability of wind power.
Gareth added: “The vision within 18 months is for this site to be fully net zero. Part of that journey will be about creating momentum across the group as, with all the properties we own around the world, each will be at differing stages of this journey.
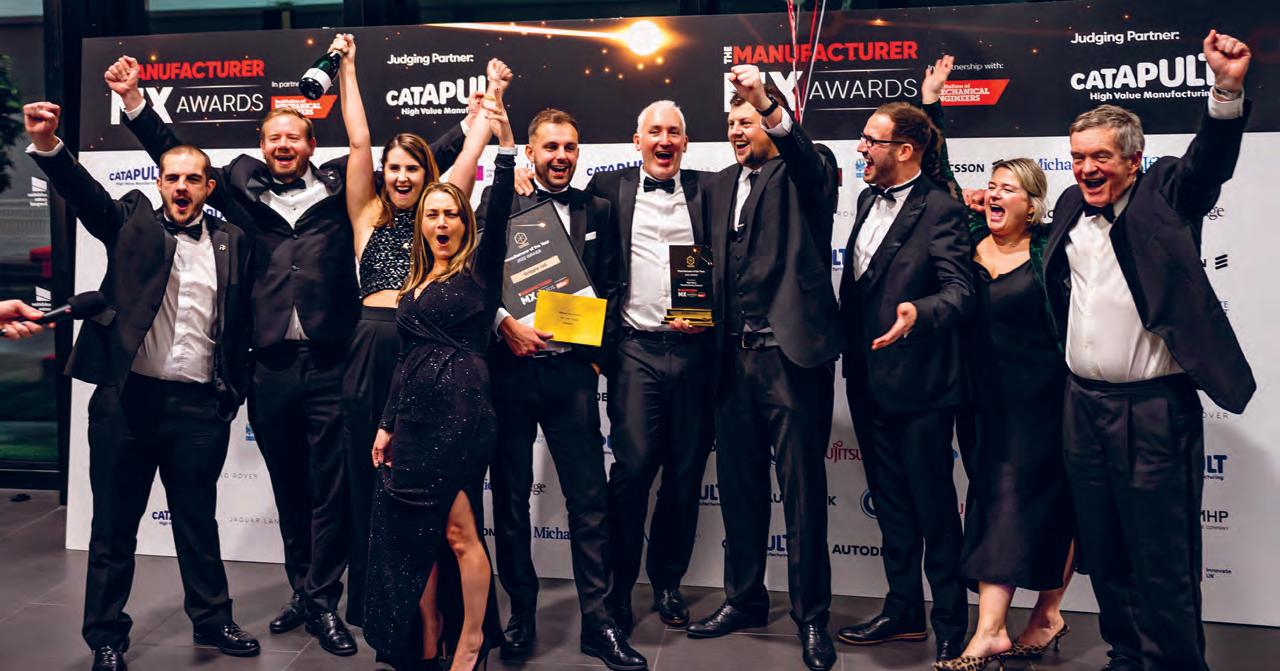



“Therefore, if we can first achieve net zero at one site, we can then share that knowledge with others in the rest of the group and create that impetus. For a company of our size, we've got certain commitments in this space which we need to achieve over the next few years.”

“This was a fantastic night for Gripple and for manufacturing in South Yorkshire!






























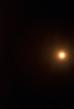










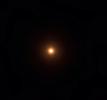
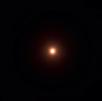
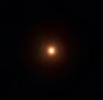
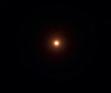

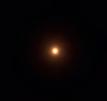
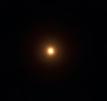

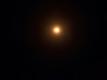
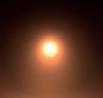
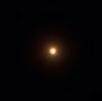
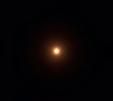


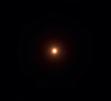

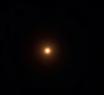
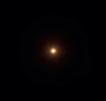
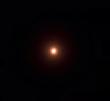
































































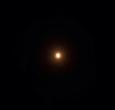





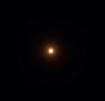

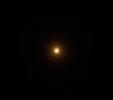

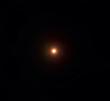


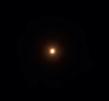

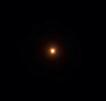

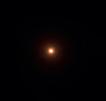
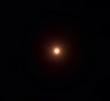

































































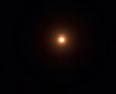






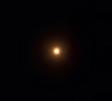
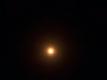


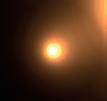

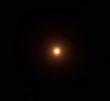




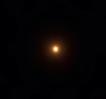


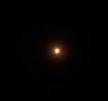
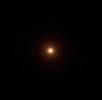

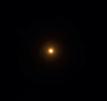

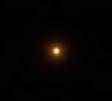

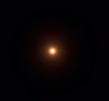





















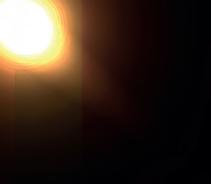
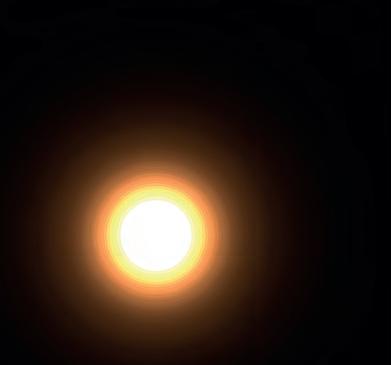
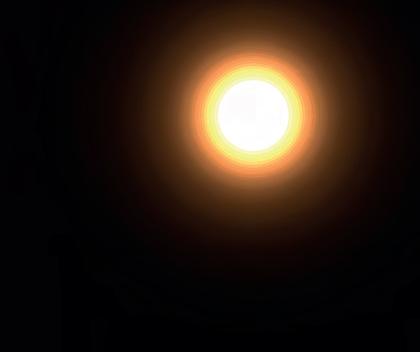


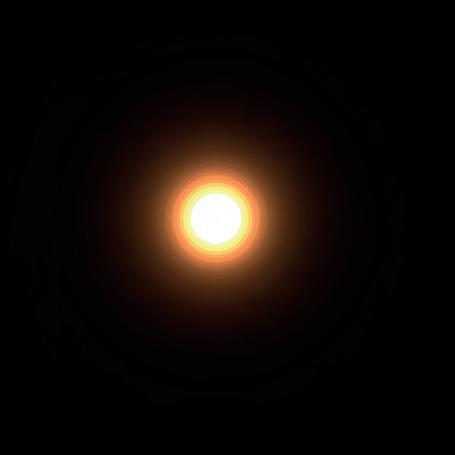
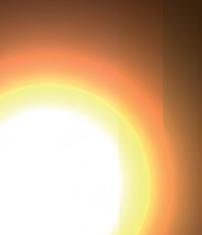
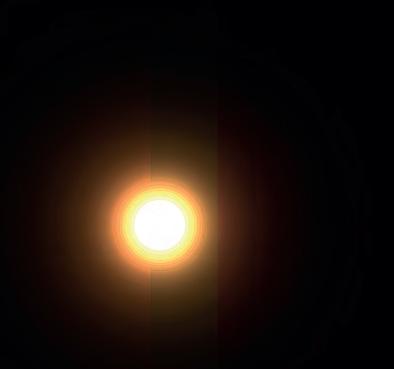
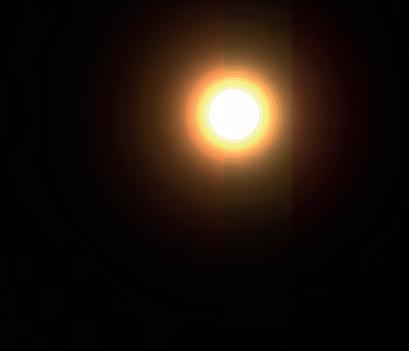



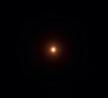



The Manufacturer MX Awards are the most prestigious manufacturing awards in the country. The entry process and judging criteria are, quite rightly, rigorous and the judges really do put you to the test when they visit. We are so pleased with the feedback we received and will use this to continually improve our operations.”
ENTRY DEADLINE: 7 JULY





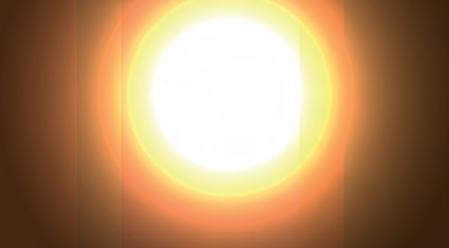
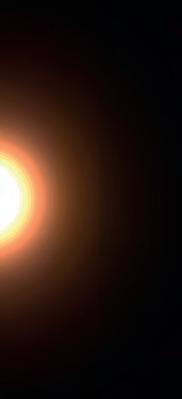
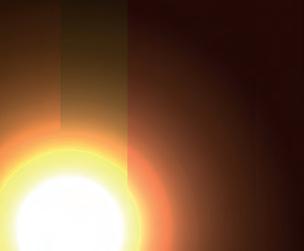
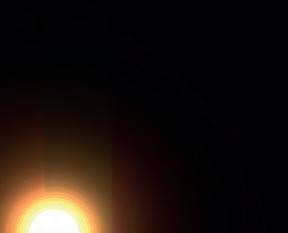
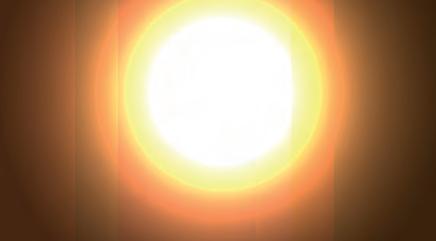

The Manufacturer MX Awards consist of ten categories and two overall winners. You can submit for as many categories as you like and entry is free.
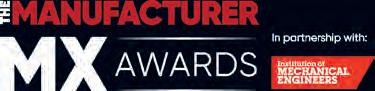
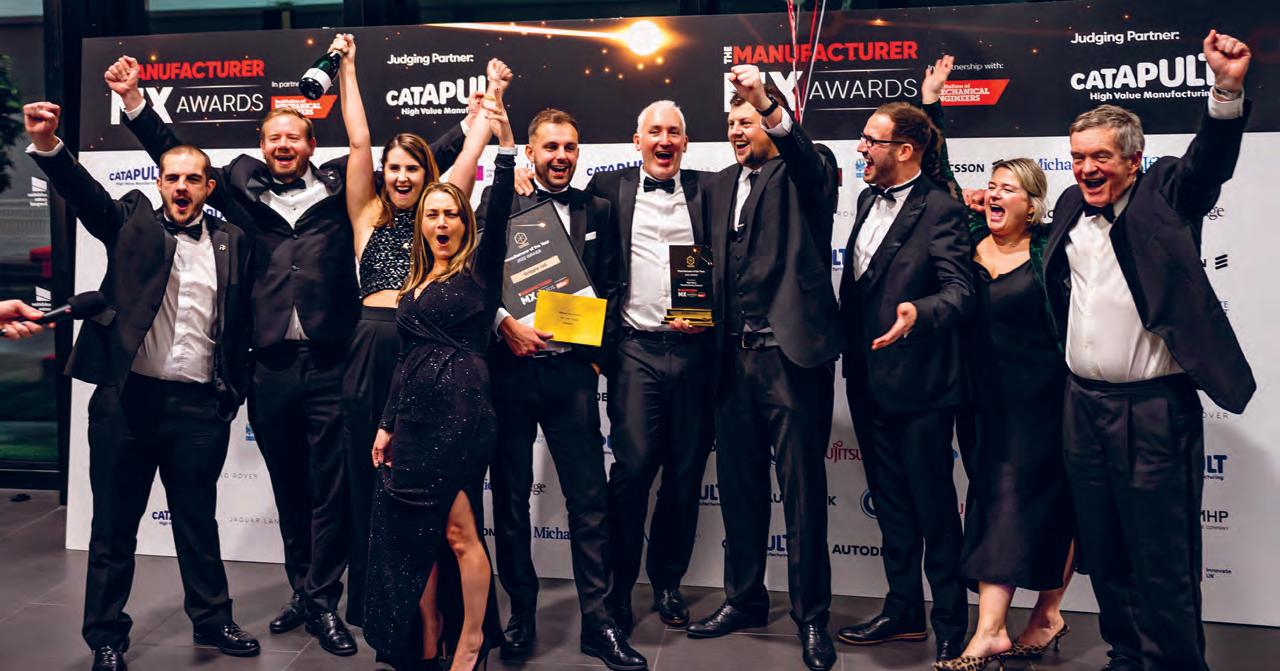




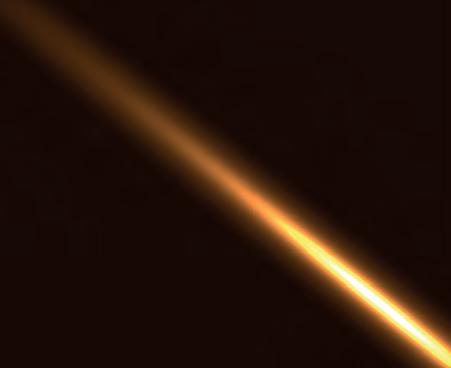
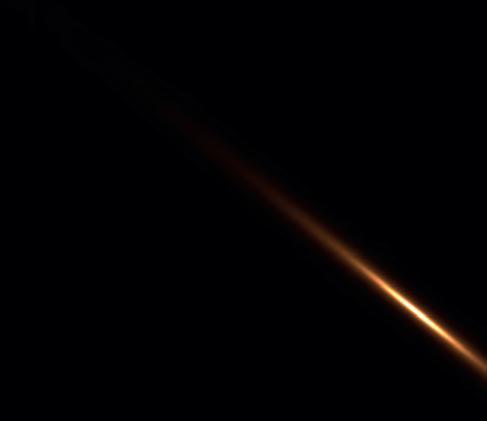
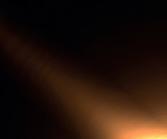
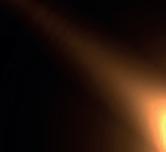
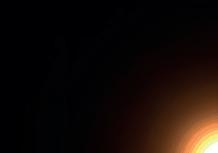
Search: TMMX Awards










































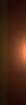






































































































































































































































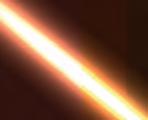

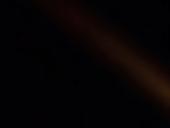
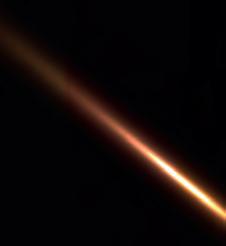




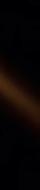
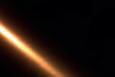
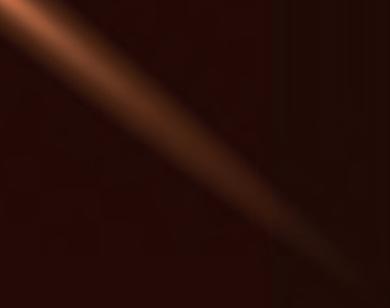
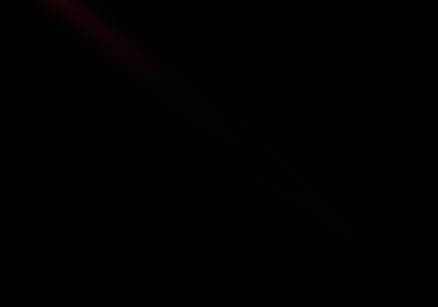
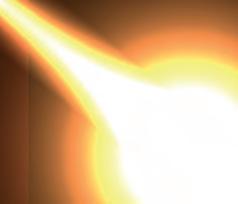
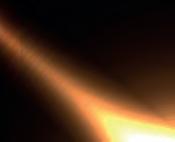
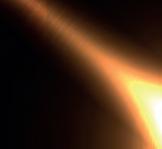










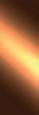









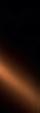
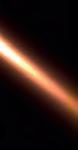
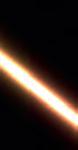

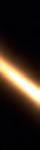

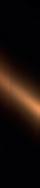

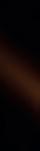
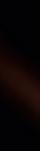
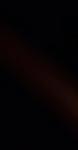

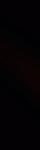
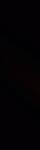

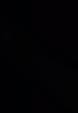

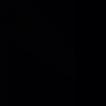
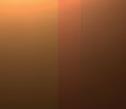

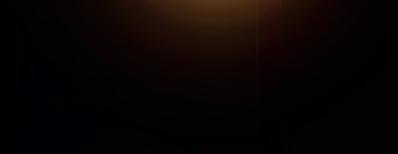



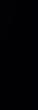

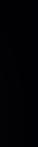
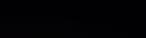
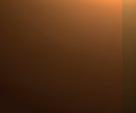



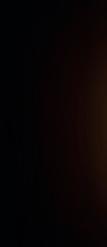
5 STEPS TO NAVIGATING NET ZERO

Climate business expert Nigel Topping recently stated that if governments were to make bolder policy decisions and take urgent action, the world could reach net zero by the early 2040s. Some sectors, he argues, could even be net zero by the end of the 2030s.
However, an independent review carried out by Tory MP Chris Skidmore on the UK government’s delivery of net zero, has found that the UK is falling behind in the race to curb emissions. The review makes 129 recommendations including the development of a policy proposal to incentivise on-site generation in manufacturing by Q2 2024 to increase adoption across the sector.
Having spoken with multiple business leaders within the manufacturing community – an industry that accounts for around 12% of the country’s total emissions – there’s a clear demand for greater clarity and certainty from the government and local authorities.
Rising costs and severe labour shortages have disrupted many manufacturers’ net zero strategies. Now, with the UK facing continued economic uncertainty, businesses around the country remain in survival mode, further delaying any progress from being made.

Yet, the likelihood is that manufacturers will still have some time left to wait before any additional financing and support is made available. All the while global
to reach net zero
warming is rapidly approaching a tipping point from which there is no return. This means that we need an ‘act now to go further and faster later’ approach.
Outlined below are some of the first steps manufacturers should take as they look to start, or restart, their journey to net zero. This can be used as part of a wider net zero checklist that businesses will need to integrate between now and the 2050 deadline.
1. Measurement and benchmarking
The first steps on the journey to net zero will look different for every manufacturer. It's important that you find an action plan tailored specifically to your needs that works within your budget restrictions.
As the manufacturing industry faces increasing pressure to reduce emissions, Drax’s Paul Miller outlines five steps manufacturers can take
As a first step, you should look to use a carbon calculating service to measure your carbon footprint. This will allow you to identify sources of emissions and any potential cost savings. It will also allow you to create a benchmark to work against.
By measuring your progress over time, you can start to demonstrate your sustainability credentials and activities to your customers and stakeholders, including new business tenders.
2. Internal and external communication
Communication is key when it comes to net zero strategies. And this is something you can do right away.
Firstly, it's important that you make sure that all your staff, from the board down to the factory floor, are fully onboard and feel part of the journey. Likewise, you should ensure stakeholders and customers know about your commitments, sharing any successes and shortcomings with them along the way.
You should also take care to upskill your employees with net zero values and any expertise they need to support new procedures or technologies such as data analysis or electric driving.

3. Renewable energy
Switching to a renewable energy supplier is an efficient way to reduce Scope 2 carbon emissions. Certain suppliers will
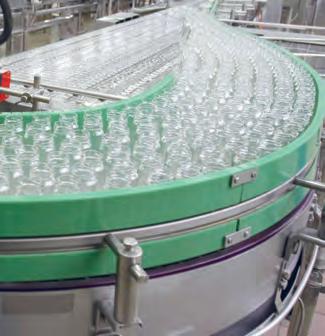
also be able to provide customers with Renewable Energy Certificates (RECs) which allow you to substantiate your green credentials.
Another cost efficient way to reduce energy usage is to install LED lighting and insulation throughout your premises.
LEFT: Net zero offers the UK a historic opportunity to grow its economy and protect the planet at the same time
LED bulbs use up to 90% less energy than conventional halogen bulbs, while insulation can help you to significantly save on money and carbon emissions. And while not every business will have the upfront capital expenditure required for on-site generation right now, it’s worth remembering that this is a great opportunity for manufacturers to create new revenue streams through the use of a Power Purchase Agreement.
4. Smart meters
Smart meters are a fundamental part of the net zero puzzle. They allow businesses to leverage the goldmine of data at their fingertips. And with the right expertise, you can turn that data into intelligent conversations about sustainability, health and safety, and competitor analysis. These are a no brainer for manufacturers who want to improve operational efficiency, security and profitability.
5. Asset optimisation
My final recommendation for manufacturers looking to advance their net zero strategies and save money in the process is to look into advanced electric asset optimisation. This allows you to make full use of your existing infrastructure, switching it up/down or on/ off during certain times to reduce energy consumption. Not only is this an efficient way to save money, but it also goes a long way to reduce your carbon emissions.
Act now to go further and faster later
To echo Chris Skidmore, net zero offers the UK a historic opportunity to grow its economy and protect the planet at the same time. While a full net zero strategy requires long-term investment which may seem unfeasible within the current economic climate, these incremental steps will allow businesses to get ahead and set themselves up for success in the years to come.
As one of the leading contributors to carbon emissions in the UK, the manufacturing sector has an important role in helping the UK meet its goal. Our online checklist is designed to guide you through the process, helping you save money by maximising your efficiencies and minimising your carbon footprint simultaneously.
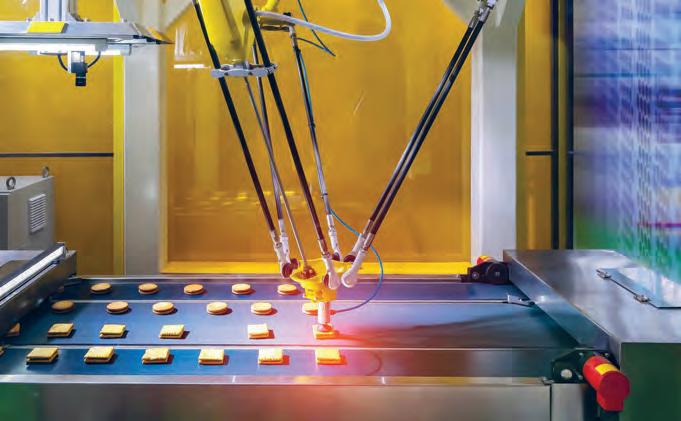
Rising costs and severe labour shortages have disrupted many manufacturers’ net zero strategies
ENGINEERING SUPERHEROES

HELPING AN AEROSPACE COMPANY SPREAD ITS WINGS
Yorkshire-based engineering company Produmax, global experts in flight control components and assemblies, won The Manufacturer MX (TMMX) Leadership & Strategy award in November 2022. The company’s collaborative journey with IfM Engage has been crucial in helping it succeed in a volatile global market and build resilience for the future
IfM Engage, the knowledge-transfer arm of the Institute for Manufacturing (IfM), began working with Otleybased engineering company Produmax in 2014 as part of the Sharing in Growth (SiG) programme, which supports UK manufacturing and engineering companies to increase cost competitiveness, grow capability and sustainability.
With a £5m turnover, Produmax was one of the smallest SiG beneficiaries at that time. However, with plans to move the whole organisation to a new stateof-the-art factory in nearby Shipley, the
company had high ambitions to grow, develop its capabilities and nurture its workforce. In 2014, IfM Engage began working collaboratively with SiG to develop Produmax’s strategy for doubling turnover to £10m by 2020.
Tools and approaches included:
• The Prioritisation Diagnostic tool to understand strategic business priorities, identify a manageable number of objectives and get buy-in from the management team to address objectives.

• Strategy Development workshops to investigate and understand the internal and external environment for the company, explore a range of potential strategic options and then decide upon a future action plan. Following these workshops, Produmax's senior leadership team was inspired to become ‘Engineering Superheroes’ who would commit to engaging and inspiring their wider team so they could further develop their skills and contribute to growing the business.
• Strategy Refresh workshops in 2017 to further develop the strategic landscape for the company. These workshops involved identifying and prioritising external drivers, market-facing opportunities and developing an objective and transparent framework (Mapping Opportunity v Feasibility) to evaluate and build topic roadmaps for a portfolio of the company’s prioritised options. The Opportunity v Feasibility framework and topic roadmapping were then drawn upon again in 2018 and 2019 to further evaluate and build Produmax’s portfolio.
Be future positive
Many businesses and organisations are looking to the future. And how to power that future sustainably. At Drax, we have a range of unique products and services to help you meet both your commercial goals and your sustainability goals.
Because we believe in a future where reducing emissions and managing costs isn’t an ‘either or’, but a ‘both’.
Discover the power of a great partnership. Search ‘Drax. Be future positive’
“Each individual engagement with IfM Engage was relatively short, with minimum disruption of the management’s day-today operations,” said Duncan Hurlstone, an Industrial Associate with IfM Engage who has worked closely with Produmax since the beginning. .
“This is one of the key benefits of using our highly developed, collaborative
approaches with companies. Time commitments are minimal, but the impact is long-lasting.”
By the end of 2019, the company was well on its way to achieving the targets it had set back in 2014. “Then, of course, COVID came along,” added Duncan.
“Although this kind of disaster scenario was considered as part of its resilience
planning, Produmax, as with most of us, hadn’t actually expected it to happen in real life.”

Navigating a new landscape
The impact of the COVID-19 pandemic was devastating for the aviation and aerospace industry, with demand for new aircraft (including Boeing, a major Produmax client) almost coming to a complete standstill. The impact on Produmax was both immediate and profound.
“COVID was very difficult. We were exposed across all platforms; effectively victims of our earlier success. As a result, our turnover quickly fell, dropping back by over 60%,” said Mandy Ridyard, Produmax’s Financial Director.
“The challenge became inverted (from building our capability to deliver our growing order book) to fully utilising our newly grown capability and capacity. At the same time, we were determined to play our part in helping the UK through COVID and maintain staff morale as much as possible.”
Mandy credits the knowledge transfer, expert input plus the strategic tools and guidance provided by IfM Engage as being critical in helping the company to get back on its feet.
“Our team revisited the strategy development and refresh work we had done together with Duncan and IfM Engage and used it to actively consider the new external context and critical drivers/challenges.
“We proactively targeted space, energy, civil aerospace and defence sectors. This diversification allowed us to rebuild revenues and mitigate risk across a wider portfolio of products and customers.
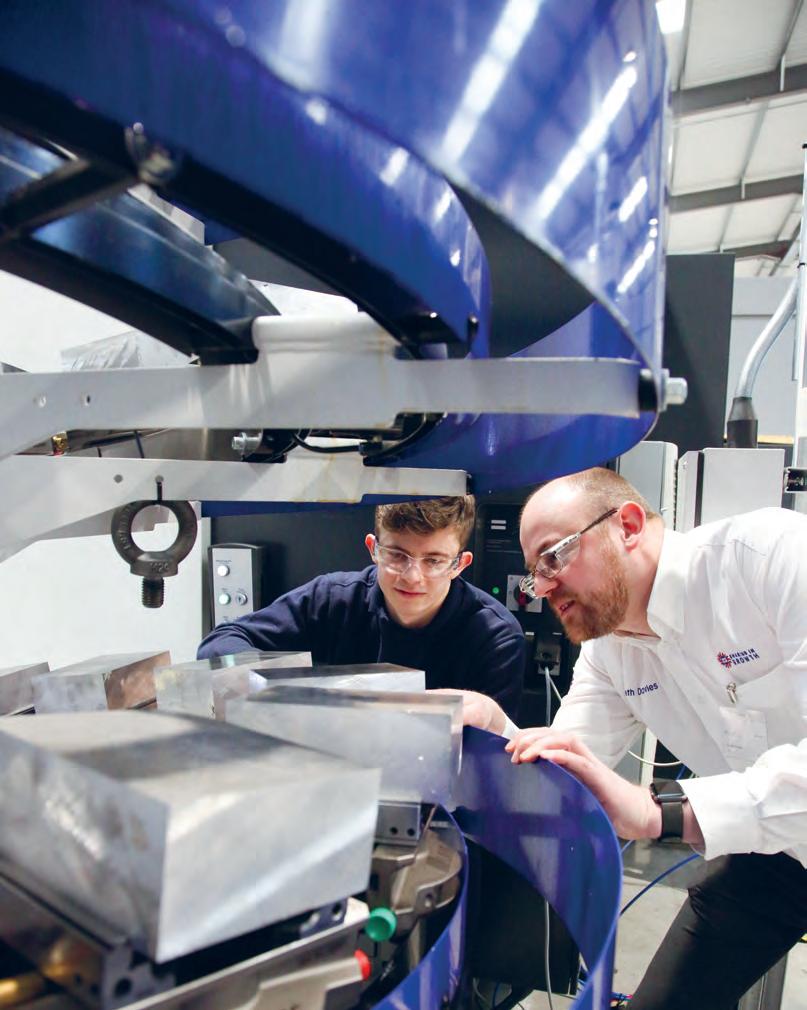
“This refined strategy to build Produmax resilience has increased our customer base three-fold. We have also spread our market exposure to a balanced mix of platforms and sectors that align nicely with the evolving strategic criteria that we first developed and adopted in our work with IfM in our first strategy refresh workshop back in 2017.”
Duncan added that developing the strategic landscape with IfM Engage
There are many people who talk about the need for organisations to be able to ‘pivot’ when required – well, Produmax did that brilliantly
Duncan Hurlstone, Industrial Associate, IfM Engage
helped Produmax to understand the big picture as well as the real and present implications for the business.
He said: “The ‘Opportunity-FeasibilityEvaluation’ approach helped prioritise key opportunities and challenges that still aligned with their overall strategic ambition. ‘Topic Roadmapping’ helped to plan and implement what they decided to do to pursue this ambition.
“There are many people who talk about the need for organisations to be able to
ABOVE: The company has won multiple awards for its work such as SiG Award 2017, MAKE UK SME of the Year 2020 and Manufacturer of the Year 2022 and The Manufacturer MX (TMMX) Leadership & Strategy award 2022
‘pivot’ when required – well Produmax did that brilliantly. It actively deployed and built upon its developed core capabilities to help the company navigate these new challenges and adjust its direction through targeted diversification and to grow again.”
Tools have become part of our DNA
By the end of 2022, Produmax’s revenue had been rebuilt by nearly 90%, with a further 40% growth for this coming year projected. Today, the company exports 70% of its production to the US, Canada, Japan, Morocco, the Philippines and Italy.
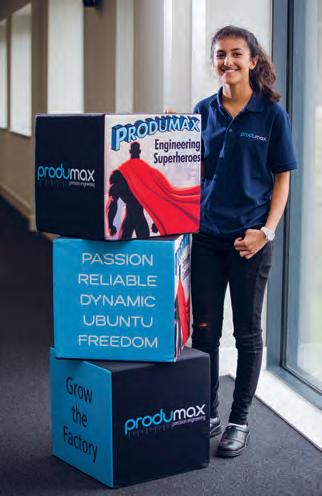
The company has won multiple awards for its work such as SiG Award 2017, MAKE UK SME of the Year 2020 and Manufacturer of the Year 2022. Most recently, in recognition of the company’s breadth and depth of leadership and management skills, as well as a clear, well-communicated business strategy, the company was awarded The Manufacturer MX Leadership & Strategy award last November.
"The results speak for themselves; turnover is up by almost 70% and we have had an increase in people of almost 80%. In this time, we have opened a second factory and built a satellite facility focussed on additive manufacturing at the Digital Manufacturing Centre at Silverstone," added Mandy.
LEADERSHIP & STRATEGY
KEY TAKEAWAYS
• Building on core capabilities can help navigate new challenges and succeed in a volatile global market
• Using collaborative tools and approaches can have a lasting impact, with minimal time commitment needed
• Strategy development tools can help companies understand internal and external environments and identify strategic options

• Team engagement and collaboration are essential for success
• Revisiting strategy via refresh sessions can help build topic roadmaps for the company’s prioritised options
“We will continue to build upon what we have learned to equip ourselves for the new challenges and opportunities that undoubtedly lie ahead.”
Reflecting on the company’s engagement with the IfM, Duncan added: “Ever since day one, the team at Produmax has actively engaged with the approaches we have worked on together. Their insatiable thirst for proactively applying what has been learned but also building upon this further is truly inspiring. It also demonstrates how IfM Engage’s highly collaborative tools and approaches have a lasting positive impact, without the delivery sapping too much valuable time from the management team along the way.”
To discover how IfM Engage approaches might help your organisation with the challenges of today and the future visit engage.ifm.eng.cam.ac.uk
ABOVE: Produmax's senior leadership team was inspired to become ‘Engineering Superheroes’ who would commit to engaging and inspiring their wider team

“The tools and approaches we worked on with the IfM Engage and the SiG team have become part of our Produmax DNA,” Mandy continued. “This has enabled us to adapt our strategy to address critical challenges as they present themselves.
Entries for The Manufacturer MX (TMMX) Awards (in partnership with the Institution of Mechanical Engineers) are open now. Enter today. themanufacturermxawards.com
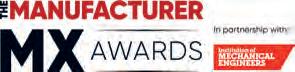
The tools and approaches we worked on with the IfM Engage and the SiG team have become part of our Produmax DNA
Mandy Ridyard, Financial Director, Produmax
Data lessons
The sixth annual Industrial Data Summit took place at Villa Park, Birmingham, on 26 April where the UK’s most senior manufacturing data professionals came together to talk data and analytics in their businesses
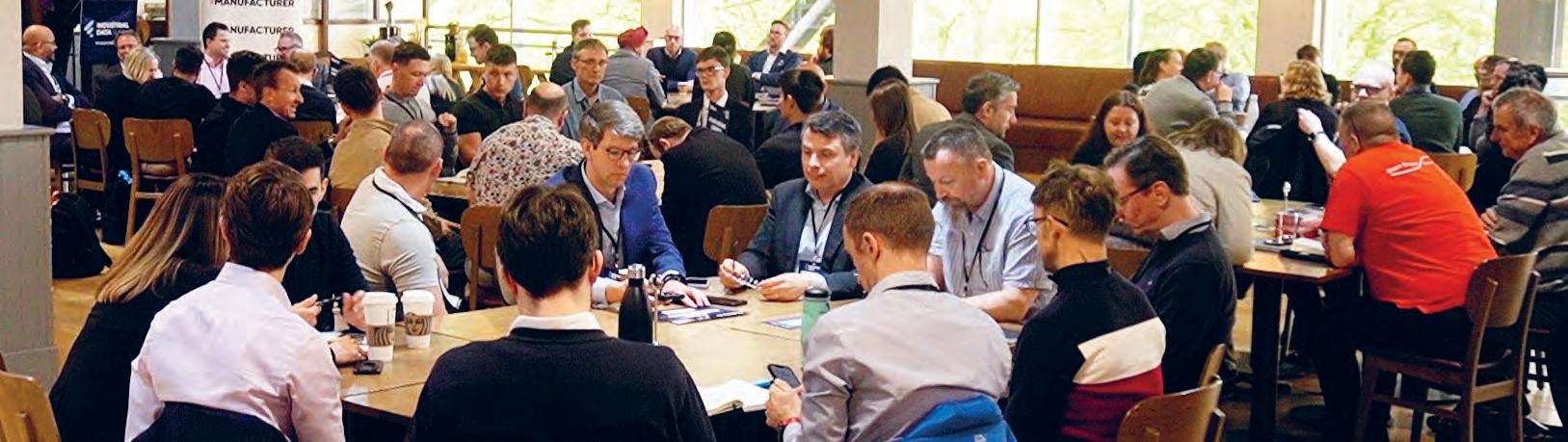
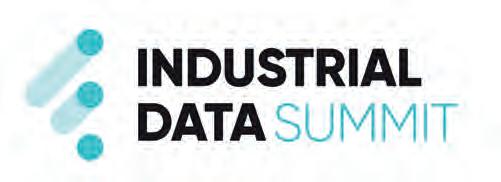
In the day’s opening keynote, Rob Clifford, Head of Digital and Data, BAE Systems, spoke about applying lessons from digital transformation in the public sector to the manufacturing industry. The manufacturing sector is the latest domain to embrace the digital and data transformation ethos. While there is ground to make up, there’s also huge opportunity to accelerate change by learning from successes and failures in other sectors.
The Manufacturer spoke to Rob around the topic of cyber security within manufacturing. The full interview can be seen in the Jan/Feb issue of The Manufacturer magazine.
We often talk around the importance of people here at The Manufacturer and the second keynote of the day saw Kat Dixon, Analytics Business Partner at Babcock International, discuss the realities of creating a data-driven culture, warning that businesses often have a tendency to dive into the technicalities of digital transformations. However, no amount of new technology is going to work without first having the right foundations and organisational culture. A full interview with Kat can be found in our Mar/Apr issue.
In this article, however, we look at the findings from the summit’s eight discussion tables, where the table hosts share the popular discussion topics of the day and their key takeaways.
Discussion Session: AI and Machine Learning
Tom Vaughan, Solutions Engineer, Peak AI
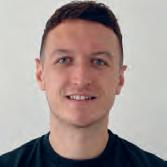
Four key points came out of our discussions. Number one was to identify the process and see where it can be improved. In order to get to an AI and machine learning base, you first need to understand the process you're trying to improve; establish what the challenge is across the business and the process improvement that can take place.
Number two was data strategy and systems. What is the quality of data and systems you currently use? Are they interconnected or are they siloed? And do you have the foundation layer to be able to bring in an AI or machine learning model?
Quite a large part of the discussion, spoken about passionately, was the change management side of data. When bringing in AI and machine learning, it’s important to remember that it’s not there to replace people, it's there to enhance people.
We heard some great examples of where machine learning could be deployed within a business. The best results have been where machine learning perhaps performs the algorithm and builds the model, but then allows people to make the final strategic decision.
Finally, topic four was around the AI and machine learning models themselves and how to get an effective AI and machine learning model within your business. That involves the three previous elements - process improvement, having a great data strategy and change management.

Discussion Session: Data Strategy
Jennifer Belissent, Principal Data Strategist, Snowflake
One of the big issues that we discussed was what is a data strategy? We started with the idea that perhaps a data strategy doesn't exist on its own - it's an element or an enabler of a larger business strategy.
So, when thinking of wider business objectives, manufacturers need to ask what they are trying to do as an organisation; whether it's to reduce cost, increase revenues, improve customer experience or reduce risk. What needs to be done with data then flows from that, enabling the whole data value chain from data use through to investments in the pillars of people, process and technology.
It's not just about having a data strategy that encompasses technology, it's about the people and the processes that we need to set up. Therefore, we
Discussion Session: Data Governance
Niall Buswel, Procurement
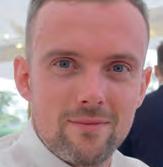
Data Lead, Jaguar Land Rover
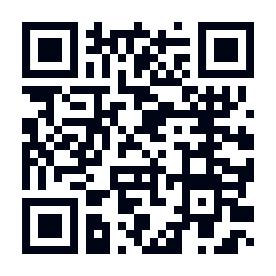
It was very valuable to hear what everyone collectively has been going through and it was reassuring to know that we’re generally facing the same challenges. Even though the main topic was data governance, we also spent a lot of time talking about data quality and how organisations are approaching that.
As well as discussions around ownership and stewardship of data, we also spoke about the standards and policies around data governance and how we get business buy in, throughout the organisation, from the top floor to shop floor.
Another theme focused on delivering value. You can have all the best policies and data quality metrics in place, but how do you showcase that to the senior leadership team and the wider business? How is it impacting day-to-day operations and how are you delivering value for others throughout the organisation?
also spoke about where you start; a number of people highlighted the fact that they had a data strategy but were unsure of how to implement it.
We discussed how to identify data champions; whether it's from parts of the organisation that are more data mature, or people within the organisation that have an affinity to data and really want to experiment and innovate. From there broader communities can be developed, creating a snowball effect. These champions should be given the opportunity to share what they've done and to showcase their work as a means of professional development.
We also spoke about what else is required to scale i.e., the communications element of a data strategy, and how you spread the word on what data is in the organisation, so everyone understands their role; whether it's capturing, protecting or using data.
We spoke about getting more people involved in this data-driven culture. The ‘D’ in chief data officer doesn't just stand for ‘data’, it stands for diplomacy as well, because it's about bridging gaps within different organisations and rationalising the requirements across the business.
Discussion Session: IoT and Sensors
Matt Mould, Partner, Storm Reply
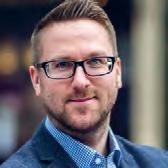
We learned a lot about where people are in their journey with IoT and the good news is there are similarities in terms of where everyone’s at. One universal complexity seems to be a wide, disparate collection of machines that have to be understood to satisfy leaders that a plant is operationally efficient, and that energy is being tracked. The challenge, however, is that a lot of separate vendors own the machines that need to be changed.
We also tackled the issue of talent attraction in this space. Manufacturing was referred to as the backbone of the country, yet it is operating in the background. Therefore, attracting the talent to compete with other, more recognisable industries, is also a challenge.
We also debated why we extract data from machines and why we integrate data from other systems? But these questions need to be answered in the context of the business case to enable investment in this space, particularly with IoT and sensors. Because the impact on the bottom line isn’t always immediately obvious.
Discussion Session: Data Collaboration
Sean
Robinson, Manager, Software Solutions, Novotek UK & Ireland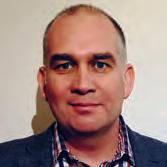
Our discussions kept returning to working backwards from goals that matter to leadership, and then translating that to things that are very specific. It's a lot easier to get people to collaborate around something that's understood (such as launching a new product, changing a product definition or even building a new factory), than it is to collaborate around data for a more nebulous goal that may be seen as detached from day-to-day business operations.
Some of the cultural challenges around that collaboration relate to people feeling a sense of ownership and protectiveness for their system. It was interesting to note how few people were able to say that they had clear data owners.
That links back to keeping data specific; know what you're doing in support of the organisation's goals and strategy, but then understand how collaboration has to happen. From there you can create a culture that's more capable to think about specific improvement initiatives or more detached exercises, because there will be a higher level of trust.
Security was supposed to be a big part of our discussion table. I would argue that what we ended up concluding was that more often than not, the technical security aspects of enabling collaboration, even around sensitive data, are less of a barrier than culture.

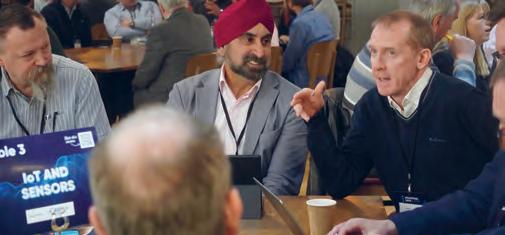
You need people who are domain experts in what really matters. Overly rigid rules can be enacted if no one truly knows what is safe and what should be available for both internal and external collaboration. Therefore, the technical aspect of data can play a secondary role to an overzealous culture.
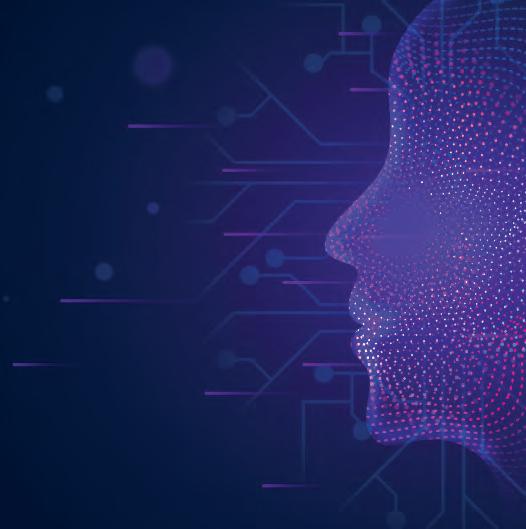
Discussion Session: Predictive and Advanced Analytics
Richard Jeffers, Founder and
Managing Director, RS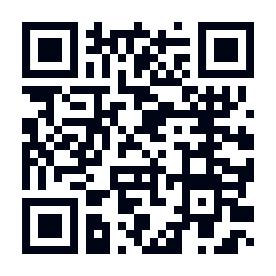

Industria
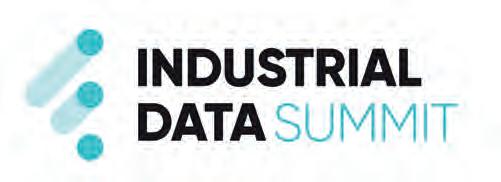
There were four recurring themes on our table. The first was around the importance of starting with the problem at hand rather than falling in love with the technology. It's not about deploying data science for the sake of it. Linked to that is the fact that you can do a lot with some relatively unsophisticated tools - statistics can take you a long way before you need to move into AI and machine learning. To solve any of these problems, you need to bring together the people who understand data and the maths with the people who understand the domain; you've got to have people who are embedded into the problem, as well as people who are embedded into the technology.
The most important discussion point was around culture change because people have to respond to the alerts and insight that come from the data and use that to drive improvement activity in the business. The maths won't actually deliver any business value without cultural change.
Discussion Session: Data Collection and Integration
Mike Kiersey, Head of EMEA Technology Organisation, Boomi

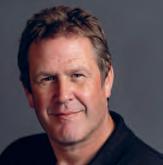
We touched on just about every aspect of data as part of our conversations, and there was some great sharing of best practices and ideas, particularly around keeping things simple, starting small and growing from there. Businesses can go quite broad with data, very fast, but that won’t necessarily yield the desired results.
Much like the second keynote address, we also touched on culture and data literacy. Do people really understand why they're making data-driven changes and who is leading the way on that journey? Do we really know what and how much data we need and how long we need to keep it? And how do we make it easy for people to access, organise and use?

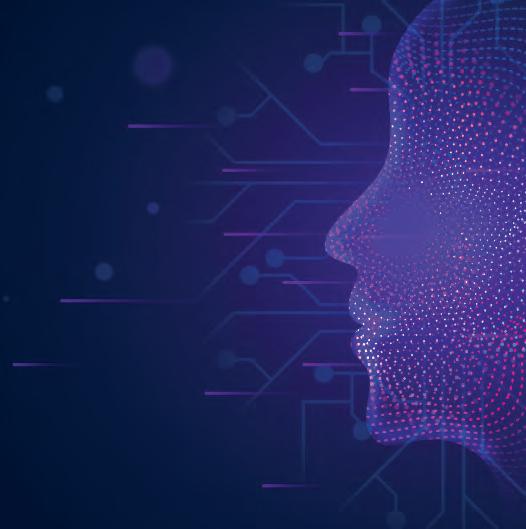
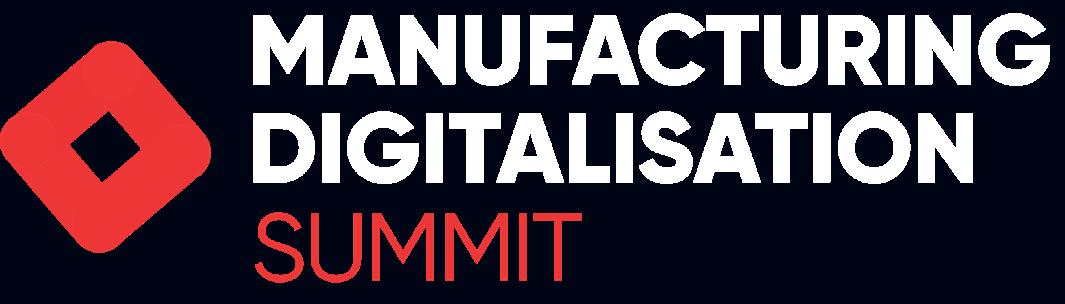
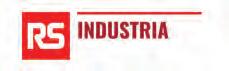

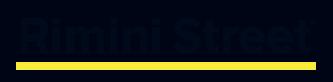

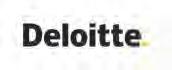

Discussion Session: Data Leadership
Phil Ware, Digitalisation Manager, Edwards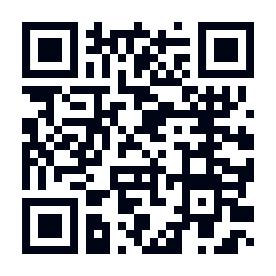
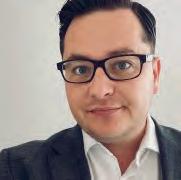
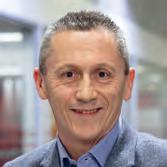

We looked at building a strong datadriven culture, implementing robust data management practices and developing a strategic approach to leverage data to achieve business objectives. I think the last one answers all the other questions. If you know where you're going, you know what you're looking for and you can communicate that. That drives your data strategy all the way through the business. Everyone understands what you're trying to do and why you need the data, and they want to find out what data you need.
Cross collaboration was a common theme; getting people who work in different areas to understand data from different parts of the business, creating a data flow. Knowing what to do with a piece of data and how it impacts the customer is critical.
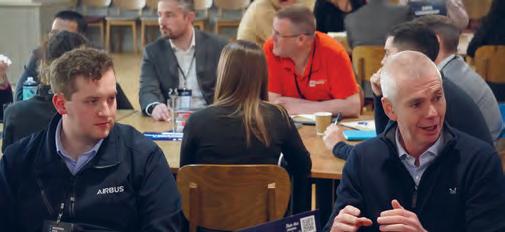
Leadership was also highlighted; the senior team need to drive down. If not, the shop floor can still drive back up. Get good information and feed that upwards to drive culture change at the top.
Rob Clifford, Head of Digital and Data, BAE Systems
Being a data leader doesn't mean you do it all yourself. It takes bravery, intellectual curiosity, but doesn't require you to be a data ninja. It's more important that you create the conditions for other people to succeed and give them the cover that they need from senior teams if it doesn't go the way it should. That's what the real leadership part is. And it may be cliché but those are the leaders we all enjoy working with.
What you said about IDS
Kat Dixon, Analytics Business Partner, Babcock International
"Summits like this give you the opportunity to learn from other businesses – their experiences, successes and failures. It’s encouraging to know you’re not alone and not the only person facing a certain challenge. It’s great to meet people who have a similar mindset and have the same priorities. You can feel quite lonely in business as the data person, so coming together and sharing best practices in this way is really important."
Jennifer Belissent, Principal Data Strategist, Snowflake
"The discussion tables at Industrial Data Summit are a really fabulous mechanism for allowing peers to exchange and share their experiences. It’s a very open environment in which they can express the challenges they face and get input from others to test out different ideas and get feedback on strategies that they might be thinking about but have not yet implemented."
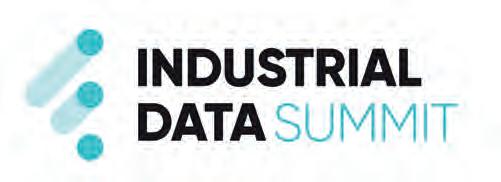
Rob Clifford, Head of Digital and Data, BAE Systems
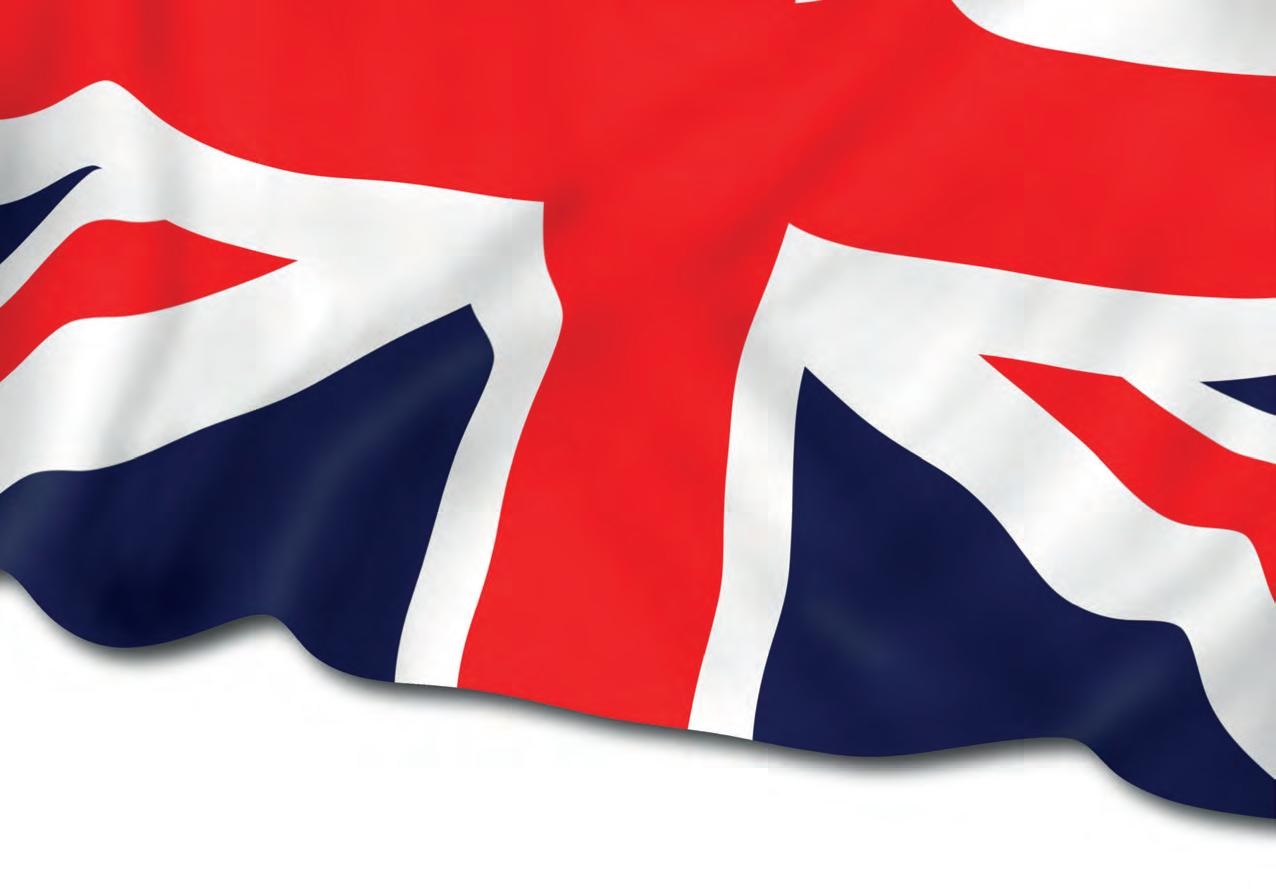
"It’s been great to hear from everyone around what data means to them, how it’s being dealt with in different businesses and what’s been seen in terms of good and bad. Hearing stories from colleagues and peers can offer reassurance because we’re on the same journey together."
Sean Robinson, Manager, Software Solutions, Novotek UKI
"A phrase we heard a lot on the roundtables was ‘group therapy’. That may sound fuzzy, but I think it’s important that people realise they’re not alone. If you know others are facing the same challenges it can actually have a positive impact on your morale and allows you to go back to work knowing that you’re not the laggard and haven’t already lost the race. "
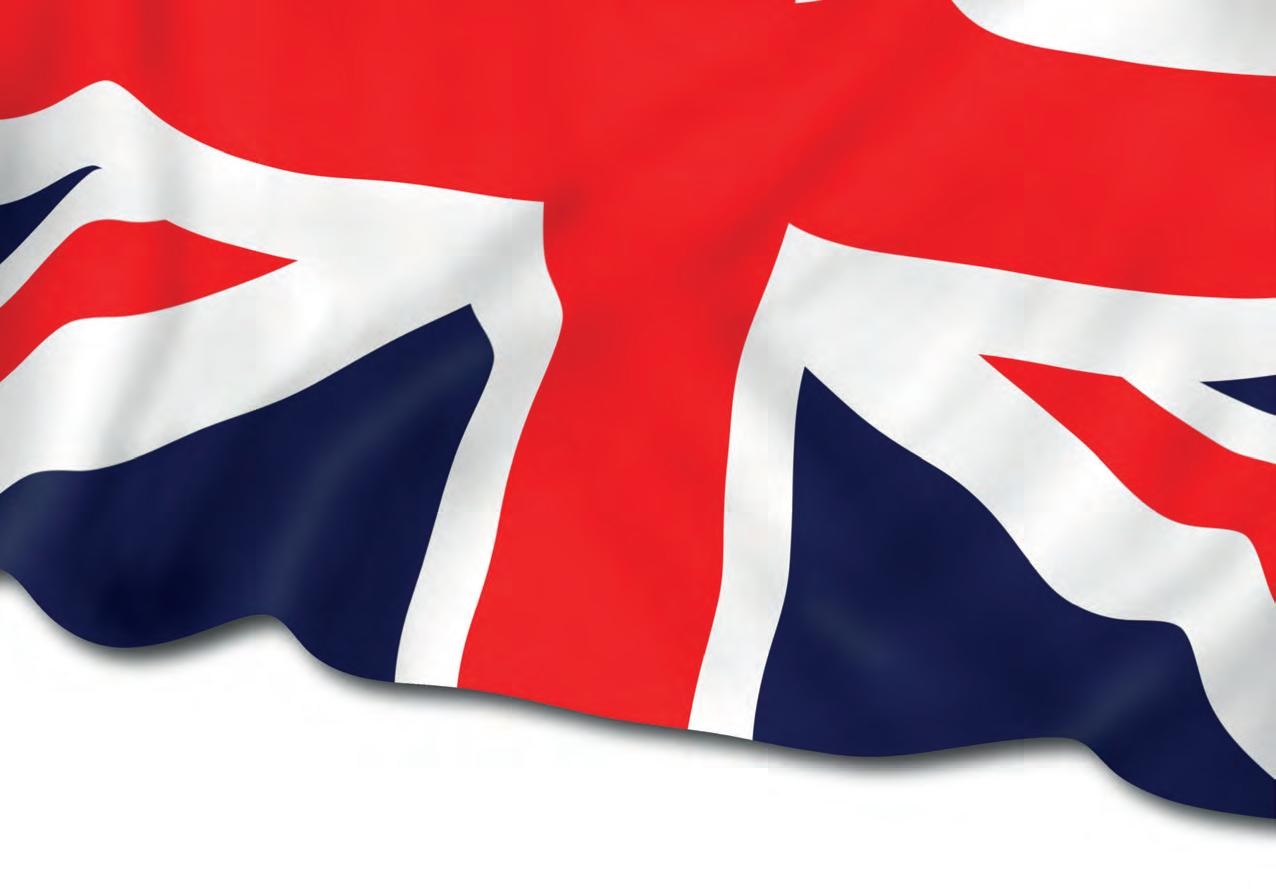
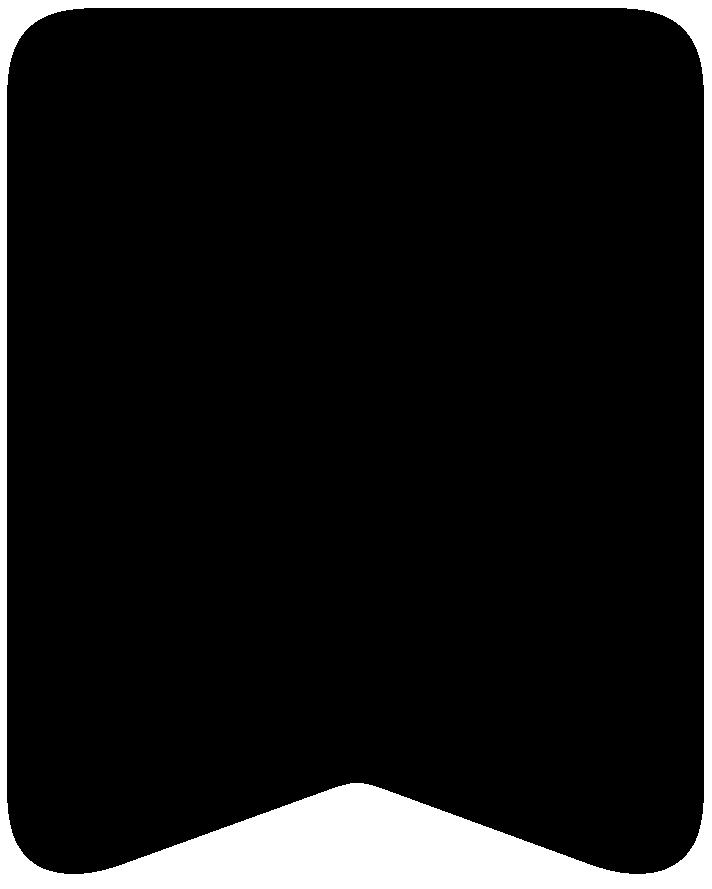
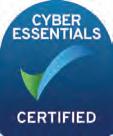
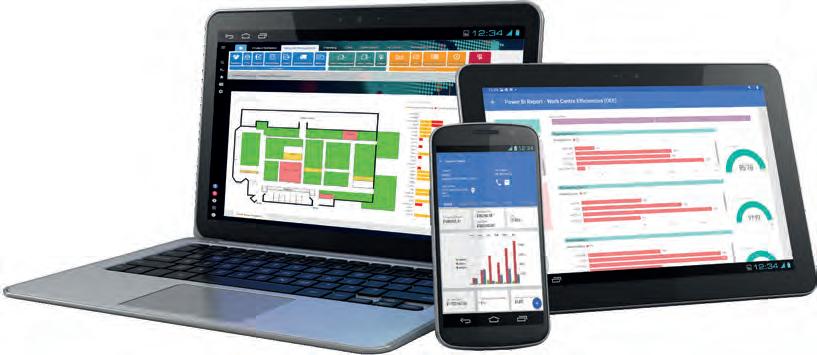
CRM way y














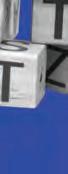
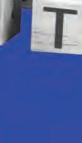


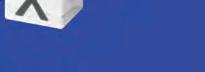
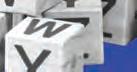

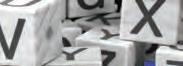
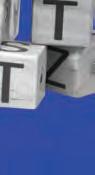


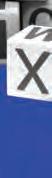
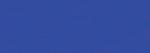
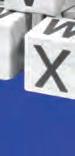

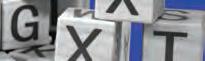
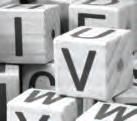
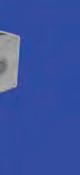
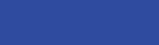

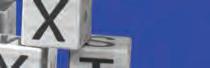
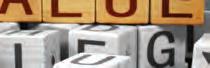

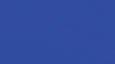
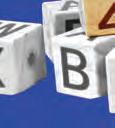

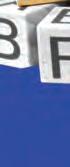
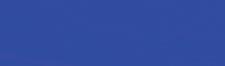
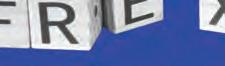
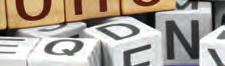

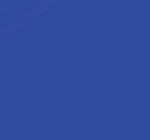
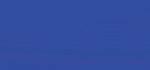
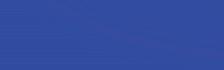
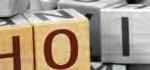


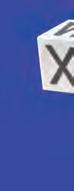
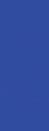

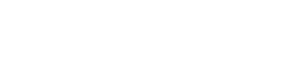
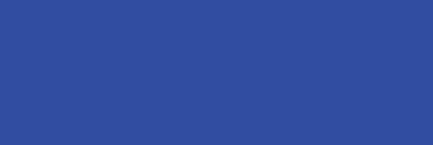

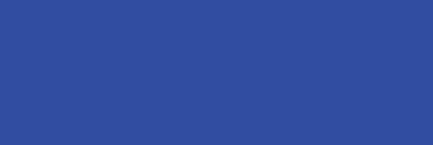

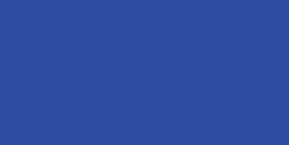
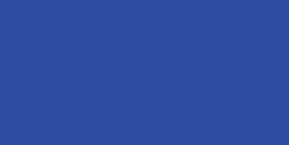
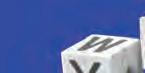
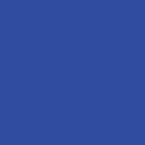

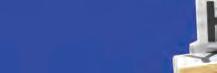

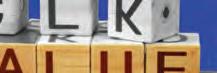
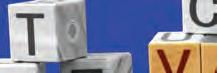
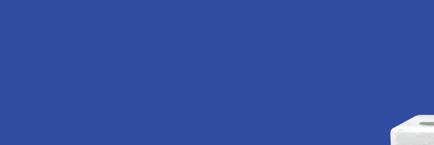
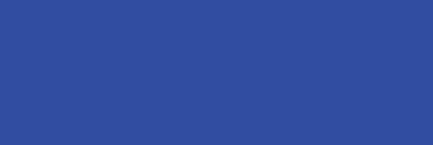
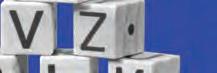
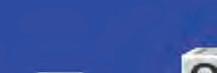

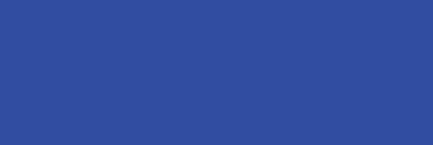
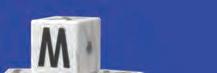
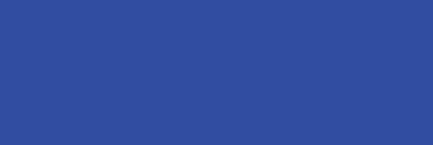

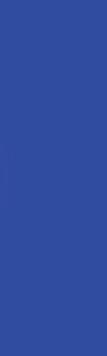
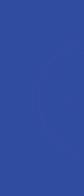